Open Access
ARTICLE
Chemically Modified Sugarcane Bagasse for Innovative Bio-Composites. Part One: Production and Physico-Mechanical Properties
1 Department of Wood and Paper Science and Technology, Faculty of Natural Resources, University College of Agriculture and Natural Resources, University of Tehran, Karaj, 3158777871, Iran
2 CIRAD, UPR BioWooEB, Montpellier, F-34398, France
3 BioWooEB, University of Montpellier, CIRAD, Montpellier, F-34398, France
* Corresponding Authors: Peyman Ahmadi. Email: ; Davood Efhamisisi. Email:
Journal of Renewable Materials 2024, 12(10), 1715-1728. https://doi.org/10.32604/jrm.2024.054076
Received 18 May 2024; Accepted 21 August 2024; Issue published 23 October 2024
Abstract
Sugarcane bagasse is an agro-waste that could replace timber resources for the production of bio-composites. Composite boards such as particleboard offer an issue for the use and recycling of poor quality timber, and these engineered products can overcome some solid wood limitations such as heterogeneity and dimension. Bagasse offers an alternative to wood chips for particleboard production but present some disadvantages as well, such as poor physico-mechanical properties. To address these issues, bagasse fibers were treated with an innovative natural resin formulated with tannin and furfural. Impregnated particles with different concentrations of resin (5%, 10%, and 15% m/m) were exposed to temperatures of 40°C, 60°C, 80°C, and 100°C for resin curing. Various types of tannin-based adhesives, including tannin formaldehyde, tannin/formaldehyde-furfural, and tannin hexamine, were utilized for bonding the treated bagasse particles. The resultant panels were assessed for their physical and mechanical properties and compared to those produced using Melamine-Urea-Formaldehyde (MUF) adhesive. The density of the panels varied from 650 to 730 kg/m3 depending on the resin concentration. The values for both modulus of elasticity and modulus of rupture increased as the resin concentration increased. The internal bonding values exhibited an increase with resin concentration up to a critical point, after which a decreasing trend was observed. The water absorption and thickness swelling were significantly reduced with an increase in resin concentration. However, the panels produced using MUF adhesive yielded the most favorable physico-mechanical properties. Additionally, the panels made with tannin-based adhesives met the minimum requirements specified in the standard EN 312 (specifications for uncoated resin-bonded particleboards) for application in dry conditions. The analysis of formaldehyde emissions indicated that panels produced with tannin-based adhesives exhibited significantly lower emissions compared to those made with MUF. The tannin/furfural resin showed great potential for improving the quality of bagasse particleboard using tannin-based adhesives.Graphic Abstract
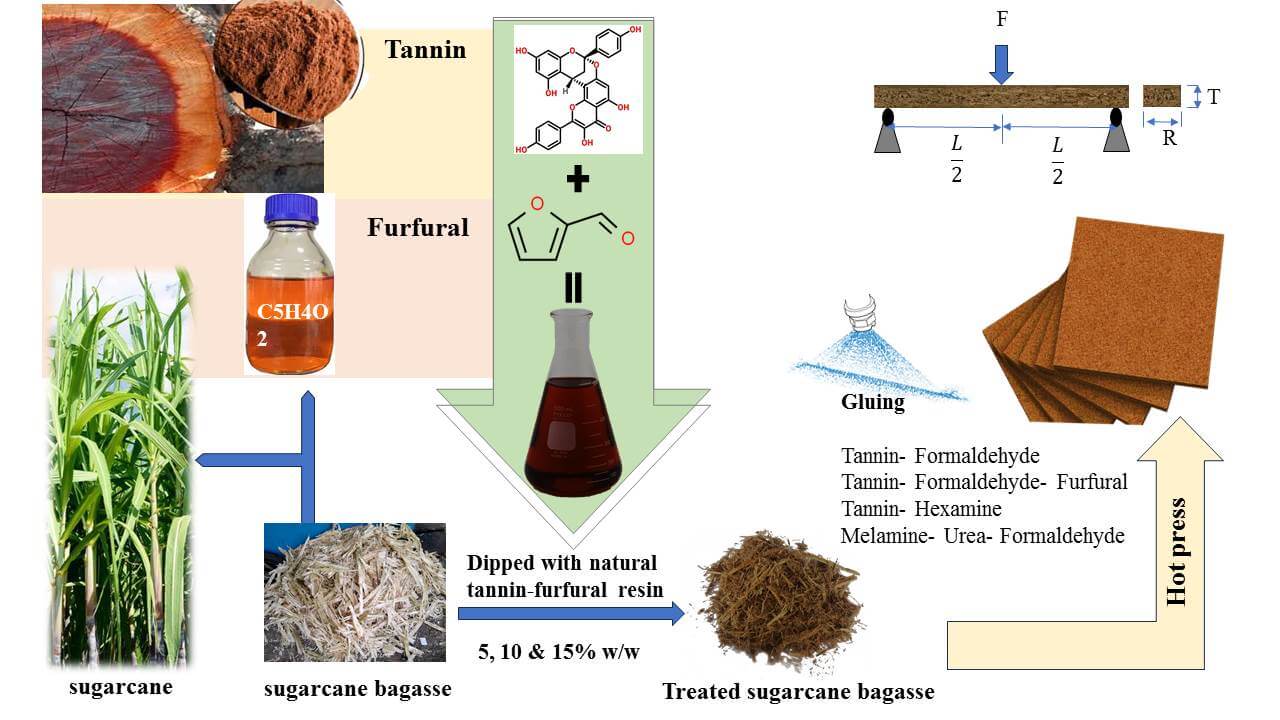
Keywords
Cite This Article
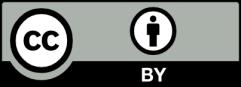
This work is licensed under a Creative Commons Attribution 4.0 International License , which permits unrestricted use, distribution, and reproduction in any medium, provided the original work is properly cited.