Open Access
REVIEW
Advanced Thermochemical Conversion Approaches for Green Hydrogen Production from Crop Residues
Department of Mechanical Engineering, Ekiti State University, Ado Ekiti, Nigeria
* Corresponding Author: Omojola Awogbemi. Email:
(This article belongs to the Special Issue: Special Issue in Celebration of JRM 10 Years)
Journal of Renewable Materials 2024, 12(1), 1-28. https://doi.org/10.32604/jrm.2023.045822
Received 08 September 2023; Accepted 09 November 2023; Issue published 23 January 2024
Abstract
The huge volumes of crop residues generated during the production, processing, and consumption of farm products constitute an ecological nuisance when ineffectively managed. The conversion of crop residues to green hydrogen is one of the sustainable management strategies for ubiquitous crop residues. Production of green hydrogen from crop residue sources will contribute to deepening access to clean and affordable energy, mitigating climate change, and ensuring environmental sustainability. However, the deployment of conventional thermochemical technologies for the conversion of crop residues to green hydrogen is costly, requires long residence time, produces low-quality products, and therefore needs to be upgraded. The current review examines the conventional, advanced, and integrated thermochemical conversion technologies for crop residues for green hydrogen production. After a brief overview of the conventional thermochemical techniques, the review delves into the broad narration of advanced thermochemical technologies including catalytic pyrolysis, microwave pyrolysis, co-pyrolysis, hyropyrolysis, and autothermal pyrolysis. The study advocates the deployment of integrated pyrolysis, anaerobic digestion, pyrolysis, and gasification technologies will ensure scalability, decomposition of recalcitrant feedstocks, and generation of high grade green hydrogen. The outlook provides suggestions for future research into cost-saving and sustainable integrated technologies for green hydrogen production towards achieving carbon neutrality and a circular bio-economy.Keywords
Nomenclature
AD | Anaerobic digestion |
USD | United States Dollar |
GHGs | Greenhouse gases |
EHI | Effective hydrogen index |
CH4 | Methane |
CO | Carbon monoxide |
CO2 | Carbon dioxide |
HR | Heating rate |
MA | Microwave absorber |
CFBR | Continuous fixed bed reactor |
| Metric tons |
MMT | Million metric tons |
The ever-growing global population, lifestyle changes, improved socioeconomic activities, and increased demand for food and other industrial raw materials have put more pressure on the agricultural sector to produce more food. There has been an astronomical increase in food production to meet the growing food demand. Food producers, farmers, agriculturists, and other stakeholders have invested enormous human and financial resources in improved seedlings, increased usage of fertilizers, herbicides, and other chemicals, and engaged in mechanized farming and other innovative agricultural practices to substantially increase food production. The global per capita production of wheat, rice, and potatoes increased from 222.36 million tons (Mt), 215.65, and 270.55 MT in 1961 to 587.65, 598.67, and 322.77 Mt in 2000 and further to 770.88, 787.29, and 376.16 Mt in 2021 [1]. During the same period, the global population increased from 3.068 billion in 1961 to 6.149 billion in 2000, and further to 7.909 billion in 2021 [2]. With the projected increase in the global population, food production is expected to continue to increase to avoid a catastrophe famine. Fig. 1 shows the per capita food production for some common food items and the global population.
Figure 1: Per capita production of some common food (Billion tons) and global population (Billion)
With the increase in food production, there is a commensurate rise in waste generation particularly in the agricultural sector. The global waste generation which was nearly 2.02 billion tons in 2016 has been predicted to rise to 2.58 billion tons by 2030 and 3.4 billion tons by 2050. The East Asia and the Pacific and the South Asia regions are the greatest contributors to global waste generation (Fig. 2) [3]. The twin factors of population growth and socioeconomic development are the major contributors to waste generation. Food and green waste accounts for about 44% of the global waste while 38% is plastic, paper, glass, and metal. Only about 40% of global waste is disposed to landfills while 19% undergoes material recovery through recycling and composting. In Sub-Sahara Africa, close to 70% of waste generated is disposed of indiscriminately and subjected to open burning thereby exacerbating air pollution and impacting air quality [3]. A lot of financial resources has been expended in ensuring effective waste management, globally. The global waste management which was around USD 1060.07 in 2022 has been predicted to become USD 1782.5 billion by 2030 [4]. The huge financial resources committed to ensuring effective waste management by governments, international bodies, and stakeholders underscore its importance to our existence. Effective management of global waste will contribute to ensuring sanitation, improvement of air quality, and reduction of air-borne diseases. Inappropriate waste disposal coupled with ineffective waste management strategies creates an unclean environment, results in surface and underground water pollution, and cultivates breeding habitats for mosquitoes, pests, rodents, flies, and other disease-causing pathogens [5].
Figure 2: Global waste generation by region
Generally, agricultural wastes are materials discarded along the value chain of the agricultural production process. Due to the increase in food production and processing activities, globally, a huge volume of agricultural waste is generated daily. The global average of agricultural waste generation is 3.35 Kg/capita/day and is second only to industrial waste [3]. Agricultural waste can be classified as crop residues, industrial processing wastes, animal wastes, and fruit waste (Fig. 3) [5]. Crop residues are forms of agricultural waste ruminants or leftover materials in the agricultural feeds after the crops have been harvested. They also include the waste materials discarded during the consumption and processing of agricultural products. Common examples of crop residues include straws, peels, bagasse, stubbles, shells, leaves, husks, cobs, stalks, and seed pods [6]. Some of the crop residues are toxic, non-biodegradable, and fire-resistant. Ineffective disposal and management of crop residues impact soil fertility and plant health, constitute a nuisance, provide breeding grounds for microorganisms and pests, contribute to pollution, and exacerbate bush burning. Notwithstanding these challenges, crop residues are potential raw materials for biofuels and chemicals, and can be converted to heat, electricity, and other valuable products. To achieve this, mechanical, thermal, chemical, and biological techniques have been applied to transform diverse crop residues into useful products. While thermal conversion involves the use of heat to convert crop residues to renewable fuels and heat, the biological conversion method explores the use of fungi, bacteria, and enzymes to transform crop residues into chemicals, biofuels, and other products. In the chemical conversion technique, acids and other chemicals are applied to change crop residues to useful commodities [7]. To further enhance the effectiveness of these methods, a combination of two or more methods is used for crop residue conversion.
Figure 3: Classification of agricultural wastes. Adapted with permission from reference [5], Copyright ©2022, Elsevier B. V
Thermochemical (thermal + chemical) conversion is arguably one of the more effective and efficient techniques in transforming crop residue into heat, liquid, solid, and gaseous renewable fuels. During the process, a combination of heat and chemicals is used to break the recalcitrant internal structure of the various crop residues. The thermochemical conversion techniques involve complex multiple and simultaneous reactions and the outcome of the process depends on the type and state of feedstock, reactor, temperature, heating rate and duration, choice of catalysts/chemicals, and mode of operation. Besides, the thermochemical conversion technique is easy to achieve, scalable, and can handle varieties of feedstock matrix. These make the thermochemical conversion technique the most deployable method for biomass conversion.
One of the products of the thermochemical conversion of crop residues is green hydrogen. Green hydrogen, also known as biohydrogen, is the production of hydrogen from renewable sources such as biomass, microalgae, and waste. The global hydrogen production which was about 60 million metric tons (MMT) in 2018 has been projected to become 300 MMT by 2030 going by the current trend [8]. The demand for green hydrogen is boosted by the transition from fossil-based fuels to clean energy sources and the avalanche of utilization pathways for green hydrogen. The ability of green hydrogen to significantly cut carbon emissions and slow down climate change has led to increased demand and investment in its production and utilization. Australia, the United States, Spain, Canada, and Chile are the top five green hydrogen-producing nations and are expected to jointly produce 9084.5 thousand tons of green hydrogen by 2030 [9]. The global green hydrogen market share which was USD 4.02 billion has been predicted to become USD 33.72 billion by 2027, and further to USD 130.49 billion by 2030 [10]. Fig. 4 shows the top five green hydrogen producers and the global market share of green hydrogen. Unlike hydrogen produced from fossil-based sources, green hydrogen has no carbon emissions, reduces global warming, and contributes to carbon neutrality and environmental sustainability. However, hydrogen is volatile, explosive, and expensive to produce, transport, and store. The technology for producing green hydrogen is relatively immature and requires sustained investment and manpower development. The choice of crop residue are raw materials for green hydrogen production will help reduce the production cost and pump price, and popularize its use for various applications.
Figure 4: Global green hydrogen production and market value
The subject matter of the conversion of crop residues to various products is not new. In recent research, Fricler et al. [11], Karaeva et al. [12], and Mo et al. [13] carried out the thermochemical conversion of various crop residues to biochar, oil, and gaseous fuels. The experimental, simulation, and environmental evaluation of the process confirm the effectiveness of pyrolysis in converting crop residue to biofuels. In similar studies, sugarcane bagasse, rice husk, maize cob, and bean straw were separately converted to biofuel, methanol, activated carbon, and other useful commodities through the instrumentality of the thermochemical process. The outcomes of the studies show the combination of thermochemical conversion technique and crop residue as feedstock provides a feasible approach for low-cost and eco-friendly production of bioenergy, biofuels, chemicals, and other high-value products and alignment to achieving carbon neutrality [14–16]. The recent efforts by Pocha et al. [17] and Osman et al. [18] in converting crop residues to biohydrogen yielded positive results with good conversion efficiency, high-quality product, and a further testament to the feasibility of the process. High-quality review articles published on the thermochemical conversion of crop residues to biohydrogen, bioenergy, chemicals, and other useful commodities showcased the processes, technologies, challenges, and prospects of the process [6,19,20]. However, in the opinion of the authors, there are still recognizable gaps in the research domain that necessitate the current intervention. It is the considered opinion of the authors that the conventional thermochemical techniques are becoming insufficient to allow for effective conversion of crop residues so diverse in terms of type, composition, and characteristics. Therefore, advanced and integrated thermochemical approaches for converting crop residues to green hydrogen need to be brought to the fore and highlighted. This forms the novelty of this work.
1.2 Motivation, Aim, and Objectives
Despite the myriads of work done in the research domain, the pertinent question to ask is whether conventional thermochemical techniques are sufficient to fully degrade and convert crop residues to bioenergy and other useful products. This forms the motivation for the current work. The current study aims to interrogate the application of advanced and integrated thermochemical techniques for the conversion of diverse crop residue to green hydrogen. The objectives of this review are to (i) present a brief overview of the conventional thermochemical process, (ii) introduce some advanced thermochemical techniques for effective conversion of crop residues to green hydrogen, and (iii) introduce novel integrated approaches for converting crop residue to green hydrogen. The current study is limited to a desktop review of thermochemical technologies for converting crop residues to green hydrogen using information extracted from relevant recently published journals, book chapters, and conference proceedings. The production costs, techno-economic analysis, and life cycle assessments of the various thermochemical technologies for the conversion of crop residues to green hydrogen are beyond the scope of the current study. The outcome of this review will open a new vista and stimulate further research interests among the scientific communities in the conversion of biomass to bioenergy and contribute to increased production and utilization of renewable fuels towards achieving carbon neutrality.
This review is subdivided into sections. The section on conventional thermochemical techniques will give a brief overview of the process, benefits, and drawbacks of various conventional pyrolysis techniques. The section on advanced thermochemical techniques will dwell on catalytic pyrolysis, co-pyrolysis, microwave-assisted pyrolysis, hydropyrolysis, and autothermal pyrolysis for converting crop residues to green hydrogen. The deployment of integrated thermal, chemical, and biological technologies for the conversion of crop residues to green hydrogen is briefly introduced and discussed. Finally, the implications and prospects section will highlight the benefits of the thermochemical conversion of crop residues to green hydrogen and suggest some future research directions.
2 Selection and Composition of Crop Residue for Thermochemical Conversion
Just like other biomass, crop residues can be converted to other usable forms by the application of mechanical, thermal, chemical, and biological techniques. Though there are no criteria for selecting crop residue for conversion, the material must be readily available, low cost, easily convertible either by heat, chemical, or microorganisms, and inflict no bodily harm on human operators. The crop residue for possible conversion must not interfere with the food chain, and guarantee high conversion efficiency and product yield. All legal, ethical, institutional, and sociocultural issues must be sorted before the crop residues are accepted for conversion. Generally, crop residues such as bagasse, straws, husk, peels, shells, cobs, stovers, and stubbles are easily degraded by the application of thermochemical techniques at diverse temperatures, residence times, chemical dosages, etc., [5,6].
Crop residues are composed of mainly cellulose, hemicellulose, lignin, and other extractives such as ash, sugar, pectin, and protein. For effective conversion, the complex structures of the crop residue are degraded into simple monomers before they are converted to different configurations. The degree of degradability of crop residue is determined by the structural composition of each crop residue. Biomass with high lignin and cellulose are not easily degraded and therefore not easily converted while those with high content of sugar and starch demonstrate high digestibility and are easily converted [13,14,18]. Table 1 shows the cellulose, hemicellulose, and lignin compositions and global production of some crop residues.
3 Conventional Thermochemical Technologies
Conventional thermochemical techniques are the methods involving biomass degradation in a controlled environment maintained at elevated temperatures. During the process which can occur with or without oxygen, intermolecular bonds between adjacent carbon, hydrogen, and oxygen molecules are obliterated and the release of stored energy is accomplished. Though combustion and liquefaction are also thermochemical processes, gasification, and pyrolysis are the most commonly used conversion techniques for lignocellulosic biomass, including crop residues.
Gasification is the application of heat and chemicals, usually called gasifying agents for the conversion of crop residues, lignocellulosic biomass, and other carbonaceous materials into biofuels, bioenergy, and other value-added chemicals. There are usually four overlapping processes of drying, pyrolysis, combustion, and reduction involved in gasification. During the process, the reactor, usually called the gasifier, is maintained at an elevated temperature above 700°C in the presence of a selected gasifying agent [21]. Common gasifying agents include steam, air, etc., [22]. The drying stage is a form of pretreatment for the removal of moisture, preparatory to thermal degradation. During drying, the feedstock is heated to between 100°C and 200°C which is insufficient to cause thermal decomposition feedstock. Drying prevents fluidization and agglomeration and improves the digestibility of the recalcitrant wet feedstock.
The pyrolysis stage occurs at controlled temperatures between 200°C and 700°C in the absence of oxygen and allows the thermal decomposition of the crop residues. The combustion stage is the oxidation of the feedstock at between 700 and 1500, during which water, carbon dioxide (CO2), and carbon monoxide (CO) are liberated. The products of the reduction stage react with the solid residue to produce CO, methane, hydrogen, and other byproducts like CO, acetylene, and ethylene [5,23]. Advancements in technologies have led to optimization of the gasification process to achieve optimal process parameters, improved conversion efficiency, enhanced reactor design and performance, selection and deployment of effective gasifying agents, and better product quality [24]. The gasification technique remains an effective, low-cost, easily achievable, and sustainable strategy for the conversion of crop residues and other lignocellulosic biomass into green hydrogen. Notable classification of gasification includes air gasification, oxy-blown gasification, steam blown gasification, and supercritical water gasification.
In the air gasification technique, air is used as the gasifying agent. Though the air is readily available and has no impact on the ecosystem, the use of air as a gasifying agent reduces green hydrogen generation and leads to low product quality. The air gasification process requires feedstock drying and other pretreatment operations and leads to the generation of CO, CO2, sulfur, and nitrogen oxide [25,26].
Oxy-blown gasification involves the use of pure oxygen as a gasifying agent. During the process, a higher process temperature is achieved which leads to a higher generation of hydrogen and a lower generation of CO2 and CH4 when compared with the air gasification process. However, more CO is generated during the process. Besides, the process requires higher temperature, more expensive, and a reduction in the overall process efficiency [27,28].
The steam-blown gasification uses steam as the gasifying agent. The use of steam ensures improved hydrogen production and reduced tar production. There is evidence of improved energy and exergy efficiencies in the systems. However, 25%–40% CO, 8%–20% CO2, and 6%–15% CH4 are generated [29,30]. Supercritical water gasification involves the use of liquid water as a gasifying agent. During the process, the operating temperature and pressure are raised above the supercritical point of water. The supercritical water gasification requires no prior drying of the feedstock and helps eliminate the cost of feedstock drying. However, the gasification process is associated with high temperature, high pressure, high energy consumption, and risk of fire and explosion. Similarly, there is a high generation of CO, CO, CO2, CH4, and other toxic gases during the gasification process. These impact the environment and negate efforts at achieving net-zero carbon and a sustainable environment [31]. The numerous challenges associated with the gasification process make an improvement and upgrading in technology inevitable. Table 2 shows some of the benefits and drawbacks of gasification technologies.
Pyrolysis is believed to be the oldest and most commonly applied thermochemical technique for the conversion of lignocellulosic biomass into useful products. Commonly used conventional pyrolysis techniques include slow pyrolysis, intermediate pyrolysis, fast pyrolysis, and flash pyrolysis. The categorization of the conventional pyrolysis process is due to the operations parameters such as temperature, heating rate, feedstock size, residence time, etc., [34].
The slow pyrolysis process occurs in a drum reactor or rotary kiln maintained at moderate temperatures of between 300°C and 700°C. The heat is applied slowly at less than 1°C/s for a residence time of more than 300 s. The products of the slow pyrolysis process are usually biochar (35%–45%), bio-oil (25%–35%), and syngas (20%–30%) [35]. Feedstocks such as woody biomass, microalgae, and agricultural waste must be cut or chopped to between 2–50 mm size before inserting them into the reactor [36]. The slow pyrolysis conversion process can only operate at moderate temperatures and there is a limit to the type and size of feedstock it can handle.
The intermediate pyrolysis process operates at a temperature of about 500, residence time of less than 4 s, and processing duration of between 30 and 1500 s. The products of the intermediate pyrolysis include liquid (40%–60%), gas (20%–30%), and solid residue (16%–25%) [37]. This technique is still not fully developed and standardized. Besides, there is a need to optimize the process parameters for effective operation [36]. Fast pyrolysis usually takes place in a fixed bed or fluidized bed reactors heated to temperatures between 450°C and 800°C and for a residence time of 0.5–10 s. The fast pyrolysis process yields 60% bio-oil, 20% biochar, and 20% syngas [38].
Flash pyrolysis thermochemical conversion of biomass usually occurs in a fluidized bed reactor, heated at a heating rate of about 1000°C/s to temperatures between 800°C–1200°C and a residence time of less than 2 s. The high operating temperature and heating rate enhance bio-oil formation but less biochar. However, the high energy cost of attaining the high temperature needed for this process is a major constraint to its wide acceptability [5,39].
Conventional thermochemical conversion technologies including gasification and pyrolysis processes are easy to operate, require no sophisticated equipment, and can be scaled up. Also, conventional thermochemical techniques can handle woody biomass, crop residues, microalgae, and municipal wastes and therefore can be used by local communities to convert their wastes to bioenergy and other commodities [40]. However, the technologies have not been effectively upgraded for industrial and commercial applications. Besides, the conventional pyrolysis process is not eco-friendly and impacts the environment due to the generation of toxic gases such as CH4, CO, CO2, etc., as by-products which exacerbates environmental pollution and global warming [41]. Conventional pyrolysis technologies have numerous challenges and require the injection of innovative ideas and system upgrades. Table 3 compiles the benefits and drawbacks of major conventional pyrolysis technologies.
4 Advanced Thermochemical Technologies
Due to many inadequacies of conventional thermochemical technologies, advanced thermochemical technologies were developed to improve product yield, product quality, and conversion efficiency. Most of the advanced technologies are products of the optimization of process parameters and consistent improvement on conventional conversion technologies. Other benefits of advanced thermochemical conversion include reduction in pretreatment, robustness, scalability, and use of innovative technologies. Notable advanced thermochemical technologies for biomass conversion include catalytic pyrolysis, co-pyrolysis, microwave-assisted pyrolysis, hydropyrolysis, and autothermal pyrolysis.
Catalytic pyrolysis is an improvement on the conventional pyrolysis techniques for the conversion of biomass to green hydrogen. The process combines the use of heat and chemicals (usually catalysts) for the decomposition of crop residues to enhance product yield. During the process, the heat applied helps in decomposing the biomass while the catalysts help to modify the composition of the thermally degraded materials and convert them to the desired products. Catalytic pyrolysis can occur in-situ or ex-situ.
In-situ catalytic pyrolysis involves direct mixing of the catalytic materials with the feedstock in the reactor. The mixing of the catalysts and the feedstock in the reactor facilitates interaction between the reactants resulting in a higher conversion rate, improved product yield, and reduction in tar formation. However, improper mixing of the reactants or ineffective catalysts can impact feedstock conversion and product yield [43,44]. In the ex-situ catalytic pyrolysis process, the reactor is designed such that the biomass and the catalyst are introduced at different times during the pyrolysis process. While the catalyst is usually placed downstream of the reactor, the biomass is introduced from the hopper and heated to the required temperature before it gets to the location of the catalyst. The interaction of the heated feedstock with the catalyst enhances product formation and ensures minimum residence time [45]. In recent studies, conventional fast and flash pyrolysis have been upgraded to catalytic fast pyrolysis (Fig. 5a) and catalytic flash pyrolysis (Fig. 5b) to improve conversion efficiency, product yield, and quality [46].
Figure 5: Schematic representation of (a) catalytic fast pyrolysis [47] and (b) catalytic flash pyrolysis [48]
The choice of the catalyst is crucial to the catalytic pyrolysis process since the success and effectiveness of the entire process substantially depend on the applied catalyst. Notable catalysts used for the catalytic pyrolysis of crop residue include alkali and alkaline earth metals alkaline metals, zeolites, iron oxide, activated carbon, magnetite, red mud, etc. The catalytic pyrolysis technique is an improvement on conventional pyrolysis for the conversion of crop residue to green hydrogen. Advantages of the application of catalytic pyrolysis include the production of high-quality hydrogen, low operating temperature, low energy consumption, improved synthesis of hydrogen, and drastic reduction in impurities [49]. However, the high cost of catalysts, unpredictable behavior of some catalysts, high coke formation, and increased production costs are militating against its wide and commercial applications [41]. The formation of tar as a byproduct of catalytic pyrolysis and the disposal of spent catalysts constitutes a major pollutant to air and underground water. The emission of CO, NOx, SO2, and other GHGs exacerbates global warming and environmental degradation [5,47]. Further research is needed to devise means of bringing down the processing temperature, prevent product contamination, and devise effective means of disposing of the spent catalyst to allow for scalability and industrial application.
Over the past few years, catalytic pyrolysis has been deployed for the production of green hydrogen from some crop residue. Lu et al. [50] experimented with catalytic pyrolysis for the production of green hydrogen from wheat straw using Ni/Ca-promoted Fe catalyst in a fixed-bed reactor. The authors reported 91.19 mL/g representing 37.05% green hydrogen production due to the effectiveness of the catalysts. A similar study by Yue et al. [51] on the conversion of corn cob to green hydrogen over Ni/CaO bifunctional catalyst in a quartz reactor maintained at 600°C. The green hydrogen of 450.15 mL/g was reported after 30 min reaction time. The outcome of other research confirmed the effectiveness of catalytic pyrolysis in converting crop residues to green hydrogen with the aid of appropriate catalysts [52,53]. Apart from green hydrogen, catalytic pyrolysis technology has been developed for the production of biobased benzene, toluene, xylene, and other useful commodities.
It has been observed that not all feedstock produces a high green hydrogen yield after conversion. The idea of co-pyrolysis is to add two feedstocks together for pyrolysis. The co-pyrolysis approach relies on the principle of synergetic interactions to improve the conversion efficiency of feedstock and hydrogen production. Though this technique can be applied with most feedstocks, the method intends to co-pyrolyze a low-yielding feedstock with a high-yielding feedstock [54]. A low-yielding feedstock is a feedstock with a low value of effective hydrogen index (EHI). The EHI of a feedstock depends on the number of moles of carbon (C), hydrogen (H), nitrogen (N), oxygen (O), and sulphur (S) in the feedstock, and can be calculated thus Eq. (1) [55]. For example, a biomass with low EHI should be considered as a co-feedstock with another biomass with high EHI.
The main purpose of co-pyrolysis is to achieve synergistic product enhancement, increase product yield for low EHI biomass, and ensure no biomass is left out of the waste-to-fuel conversion basket. Co-pyrolysis is cost-effective, needs no modification of the existing reactor, and can handle diverse biomass. For wet feedstocks, a co-feedstock with low moisture content should be selected to ensure synergetic interaction and effective conversion. However, the properties and composition of biomass may impede co-feedstock interaction and may cause negative synergistic interactions [56,57].
Fakayode et al. [57], Ahmed et al. [58], and Lin et al. [59] in their separate works have provided updated information on the performance, process parameters, operation, product quality, and enhancement of co-pyrolysis technology for the conversion of diverse feedstocks to bioenergy and other useful products. The reported works of Hu et al. [60], and Tang et al. [61] demonstrated that the addition of a suitable co-feedstock enhanced conversion efficiency and green hydrogen yield. Co-pyrolysis also produces an increment in the proportion of gaseous products and high-quality hydrogen. The major challenge with this technology is the inability to scale up to commercial and industrial stages. There is also increased emission of unwanted gases from the conglomerate of the feedstock. The deployment of co-pyrolysis is also associated with high energy costs, increased energy consumption, and the generation of more waste and other unwanted materials. The inappropriate disposal of this waste populates dumpsites and contributes to environmental pollution. The composition, moisture content, and properties of the diverse feedstocks used in the co-pyrolysis process have limited its effective operations [57,58]. A new design is that will make provision for a separate pre-treatment unit before the process can be scalable and the much-needed industrial patronage. There is a need for a techno-economic analysis of the process to ensure the effectiveness of the process at affordable costs.
4.3 Microwave-Assisted Pyrolysis
The conventional pyrolysis technology transmits heat from the carrier gas to the biomass surface by convection and to the inner part of the feedstock by conduction. However, due to the low thermal conductivity of some biomass, a thermal gradient is developed within the biomass from the outer sauce to the inner particles of the biomass [37]. This attendant heat loss significantly impacts the process, slows down biomass conversion, and increases residence time. In microwave-assisted pyrolysis, heat penetrates the inner part of the feedstock and transforms the heat into microwave thermal energy, thereby enhancing the thermal decomposition of the feedstock. Also, microwave-assisted pyrolysis technology prevents heat loss and lower heating rates experienced with wet feedstock in conventional pyrolysis methods [62]. However, the effectiveness of the process depends on the type and properties of the feedstock and the microwave interactions. Also, the addition of catalysts and microwave absorbers enhances the effectiveness of the microwave-assisted pyrolysis process and contributes to hydrogen yield and quality [63]. The microwave-assisted pyrolysis usually takes place in a microwave oven equipped with microwave dielectric heating to ensure improved heating rate and interaction between the biomass and the heated gas. Fig. 6 shows the schematic diagram of a microwave-assisted pyrolysis equipment.
Figure 6: Schematic diagram of a microwave-assisted pyrolysis [62]
Several researchers have experimented with the application of microwave-assisted pyrolysis for the conversion of biomass to biofuels and other useful products and reported that microwave heating is an advanced technology when compared with conventional heating technologies due to its ease of operation, improved heating rate, and ability to handle wet feedstocks [63,64]. The thermochemical conversion of wet sugarcane bagasse to green hydrogen shows the effectiveness of microwave-assisted pyrolysis in achieving good conversion efficiency, improved heating rate, and quality green hydrogen [65,66]. In the conversion of olive pruning residues to different products, Bartoli et al. [67] reported the efficacy of microwave-assisted pyrolysis in achieving improved hydrogen production when compared with conventional pyrolysis. However, improved reactor design, optimization of process parameters, and introduction of innovative technologies are needed to improve the process. Microwave-assisted pyrolysis is also associated with increased environmental pollution and the generation of more GHGs. The high temperature required during the process requires higher energy consumption and aggravates production costs. Currently, there is a limitation in the type of feedstock that can be processed by microwave-assisted pyrolysis and the technology is not fully demonstrated at the industrial level [64,66]. Consequently, well-coordinated research is needed to upgrade the technology for industrial applications.
Hydropyrolysis is an entirely new thermochemical conversion technology performed under a high-pressure hydrogen atmosphere and rapid heating rate to achieve fast thermal decomposition of biomass. The process is completely different from conventional pyrolysis due to the use of a high-pressure hydrogen atmosphere. The process is usually achieved in a high-pressure reactor (Fig. 7). The early hydropyrolysis process was designated slow pyrolysis and was characterized by slow heating rates and long holding durations. But advancements in scientific innovations have resulted in fast hydropyrolysis characterized by higher heating rates (as high as 500°C/s), and the development of non-catalytic and catalytic fast pyrolysis technologies [68]. The advantages of the deployment of hydropyrolysis technology include inhibition of coking, reduction of char formation, better process stability, and prevention of formation of unwanted olefins, and polynuclear aromatics. Hydropyrolysis technology also offers an economically sustainable pathway for the conversion of diverse feedstocks to bioenergy, special chemicals, fungible hydrocarbons, and other commodities [69,70]. However, the high cost of catalyst materials, high-pressure requirement, and need for an external hydrogen source as input to the reactor are some of the major drawbacks of the hydropyrolysis process. The high hydrogen consumption during the process, the need for special equipment, and well-trained personnel may significantly add to the processing cost and prevent high-scale implementation. To scale this hurdle, the addition of appropriate catalysts, adoption of co-pyrolysis, and development of an integrated hydroconversion and hydropyrolysis process are suggested [37,70].
Figure 7: Schematic diagram of a hydropyrolysis process [71]
The conversion of rice straw, pine wood, and wheat straw to hydrogen and other products was effected through hydropyrolysis technology, confirming the deployment of the advanced technology for high-quality hydrogen production [72,73]. One of the latest innovations in hydropyrolysis technology is the deployment of an integrated hydroconversion and hydropyrolysis process and co-pyrolysis of feedstocks. However, the high temperature and pressure required for an effective process significantly increase energy consumption and exacerbate the risk of fire and explosion, thereby compromising the safety of the operator. Though the technology produces high-quality products, the release of unwanted gases into the atmosphere is a major drawback.
One of the major challenges of conventional thermochemical conversion technologies is the heat transfer limitation due to the endothermic nature of the reactors and the difficulties in technology scale-up. The autothermal pyrolysis technology is, therefore, one of the advanced technologies to overcome these limitations and ensure easy commercialization of the pyrolysis technology. The biomass autothermal pyrolysis reactor allows the heat from the feedstock or pyrolyzed products to form part of the heat in the process, thereby upgrading heat sources. Similarly, the process enhances the scalability of the pyrolysis process by ensuring chemical reactions during the process proceed optimally. During the process, limited oxygen is introduced into the rector to enhance the interactions between the oxidative oxygen-char and oxygen volatiles, and enrich the products [74,75]. The schematic diagram of the autothermal pyrolysis process is shown in Fig. 8.
Figure 8: Schematic diagram of a biomass autothermal pyrolysis reactor. Adapted with permission from reference [76], Copyright ©2021, America Chemical Society
The thermochemical decomposition of crop residues such as corn stover and oat straw through the autothermal pyrolysis technology was demonstrated and found effective and generated quality products [77,78]. Recent studies show that autothermal pyrolysis technology was utilized to achieve partial oxidative reactions to support waste conversion and promote bioenergy utilization. The advancement in autothermal pyrolysis technology has led to the commercialization of the technology due to the capability of the technology to decompose feedstock from diverse sources and configurations. The introduction of digital tools such as machine learning, artificial neural networks, and other modelling tools. in real-time process monitoring and optimization, product yield prediction, production metering, life-cycle assessment, and techno-economic analysis will accelerate scalability, and bridge the knowledge gaps in the autothermal pyrolysis technology [79,80]. Table 4 summarizes the production of green hydrogen from diverse crop residues using advanced thermochemical conversion technologies.
Compared with other hydrogen production methods such as biological, electrolysis, and direct solar water splitting, the synthesis of green hydrogen using advanced thermochemical conversion techniques is sustainable, scalable, and a viable waste management strategy. The biological method involving microorganisms and sunlight to convert water and organic matter to green hydrogen is eco-friendly, non-toxic, and requires low energy consumption but suffers from a lack of scalability and industrial utilization. The electrolysis and direct solar water splitting techniques guarantee green hydrogen production with minimal GHG emissions and moderate production conditions. However, the use of water for hydrogen production impacts water supply, endangers aquatic ecosystems, and poor product quality. Table 5 compares the advanced thermochemical conversion techniques with biological, electrolysis, and water-splitting hydrogen production.
5 Integrated Conversion Technologies
There is an urgent need to further upgrade the technologies to ensure accelerated biomass conversion for green hydrogen synthesis. This call is borne out of the seeming drawbacks of the existing single conversion approaches. The need to adopt multi-faceted cost-saving and low-energy conversion technologies to enhance the production process and improve product quality has further made this upgrade a necessity. The integration of thermal, chemical, and biological technologies will reduce production costs, promote the circular economy, enhance efforts at resource recovery from waste, and eliminate the drawbacks associated with each technology. Table 6 shows the benefits and drawbacks of major integrated thermal, chemical, and biological technologies.
5.1 Integrated Thermal and Biological Technologies
Thermal (pyrolysis) and biological (anaerobic digestion) technologies have been integrated as low-cost and effective approaches to systematically decompose lignocellulosic biomass for rapid bioenergy production and resource recovery. The combination of pyrolysis and anaerobic digestion (AD) will degrade feedstocks with high concentrations so lignin and other recalcitrant compounds recalcitrant compounds n enhance the formation of useful products. Through the integrated pyrolysis-AD technologies, wastes from divergent sources and configurations are digested in a single process thereby facilitating waste management, effective recovery and utilization of resources, and optimal production and application of bioenergy, chemicals, and other byproducts [94,95]. The integrated AD-pyrolysis is a sustainable pathway for biomass degradation, bioenergy generation from digestate, and heat and power generation. Fig. 9 shows the concept of an integrated AD-pyrolysis system.
Figure 9: Conceptual view of integrated AD-pyrolysis system [96]
To demonstrate the integration of AD and pyrolysis system, Moško et al. [97] combined pyrolysis and AD for the conversion of sewage sludge to useful products for effective and low-cost waste management. During the process, sewage sludge was pyrolyzed in a fixed bed reactor after an AD process. The resulting AD sludge chars were used for various applications and the process was able to eliminate about 98% of the pollutants. In another study, integrated AD and pyrolysis were deployed to convert food waste to biofuel and other products. The food waste was first fermented in an AD reactor for methane generation while the undigested slurry was later pyrolyzed and converted to biochar. The integrated approach has potential for industrial applications and circular-bio-economy [98]. Various modelling and optimization tools have been deployed to carry out the energy, exergy, and performance evaluation of the integrated AD-pyrolysis process. The conclusion of the investigation shows that the integration of pyrolysis and AD reduces the reaction time, lowers energy costs, promotes both exergy and energy efficiencies, and accelerates bioenergy production [99]. Table 7 compiles the outcomes of some integrated AD-pyrolysis processes. More studies are required for the conversion of recalcitrant crop residues to green hydrogen to facilitate efforts at promoting carbon neutrality.
5.2 Integrated Pyrolysis and Gasification Technologies
Ordinarily, gasification consists of multiple overlapping processes such as heating, drying, pyrolysis oxidation, and gasification. However, a major drawback in the gasification techniques is the interaction between the char and volatiles in the reactor which often obstructs the process, contaminates the product, and impacts the conversion efficiency. One way of mitigating this is to separate the pyrolysis and the gasification processes [106]. This is what the integrated pyrolysis and gasification technology aims to achieve (Fig. 10). During the process, biomass is converted to slurry consisting mainly of char and oil in the pyrolysis reactor. The generated slurry is transported into the gasifier for final conversion into biofuel and other products [37]. However, the challenges of economic viability, the impact of the char and oil on the product, and transportation between the reactor and the gasifier need further investigation.
Figure 10: Integrated pyrolysis and gasification technology [106]
Few researchers have investigated the combined effect of pyrolysis and gasification on biomass for hydrogen production. The deployment of slow pyrolysis and steam gasification effectively converted lignocellulosic biomass into quality and high-purity hydrogen and other useful commodities. The conversion efficiency was higher than the conventional non-integrated pyrolysis method [107]. The technical and economic assessment of integrated biomass pyrolysis and gasification of rice straw was successful with the production of syngas and other valuable products. The process was energy efficient with increased life of the equipment [108]. In a similar study, Hwange et al. [109] demonstrated the conversion of latch sawdust to syngas was carried out effectively with significant improvement in product quality and reduction in tar formation. Table 8 compiles the outcomes of other integrated pyrolysis and gasification processes for biomass conversion.
6 Implications and Future Perspectives
The huge volume of crop residues is generated from the farming site and during the processing and consumption of fruits and other farm produce. These crop residues are termed wastes and therefore discarded since they can no longer be used in their current form. The inappropriate disposal of these crop residues impacts sanitation, attracts and provides breeding habitats for flies, rodents, and other disease-causing pathogens, and constitutes environmental hazards. Indiscriminately dumped crop residues in the farming sites attract termites and other insects, increase soil acidity, contaminate water bodies, and exacerbate bush burning and deforestation. The conversion of these wastes to green hydrogen will contribute to increasing renewable energy penetration, supports carbon neutrality, and further popularize waste-to-energy initiative. The deployment of crop residues as feedstock for green hydrogen production will increase the production and consumption of green hydrogen and ensure the application of green hydrogen as transportation engine fuels and for heat and electricity generation. Advanced thermochemical technologies are more effective, consume less energy, and produce high-purity products. The introduction of integrated pyrolysis and AD and pyrolysis and gasification technologies reduces the challenges and shortcomings of the individual technology and increases the conversion efficiency at lower costs. Integrated technologies also ensure that wet feedstocks from diverse sources, recalcitrant crop residues, and a combination of crop residues and other wastes can be easily degraded and converted to green hydrogen and other useful commodities.
The thermochemical technologies for the pretreatment and conversion of crop residues are still expensive and energy-dependent. This is one of the drawbacks and a major setback for the process. A techno-economic analysis is desirable to reduce energy consumption and production costs. The processes for the collection, sorting, transportation, pretreatment, and degradation of crop residues emit carbon and other unwanted gases and can be hazardous to workers. There is an urgent need to conduct a life cycle assessment to determine safe and carbon neutral pathways for their processing and conversion. The conversion of crop residues to green hydrogen is still faced with GHG emissions, high energy consumption, and other technical challenges. Future collaborative research should focus on developing low-energy consumption techniques, optimization of process parameters, redesigning of reactors, and development of eco-friendly approaches for advanced and integrated approaches. Bearing in mind the challenges in the production process monitoring, handling, transporting, and storage of hydrogen, the use of innovative technologies such as modelling optimization tools, machine learning, robotic technology, smart metering, artificial intelligence, etc., are desirable. Upgrading the production of green hydrogen from crop residues into industrial and commercial standards is capable of contributing to efforts at meeting the global clean and affordable energy demands.
This study agrees with the outcomes of previous studies that thermochemical technologies are a feasible and effective route for the conversion of crop residues to green hydrogen. However, conventional pyrolysis and gasification conversion technologies are slow, consume energy, emit carbon, and produce low-quality green hydrogen. Besides, most conventional biomass conversion technologies cannot be upgraded and scaled up to industrial standards. Advanced thermochemical technologies such as catalytic pyrolysis, co-pyrolysis, microwave pyrolysis, hydropyrolysis, and autothermal pyrolysis ensure scalability, generate high-purity products, and guarantee improved hydrogen yield. Integrated approaches such as pyrolysis and AD and pyrolysis and gasification are innovative and cost-effective conversion technologies that will revolutionize green hydrogen production from crop resides. The capacity of integrated thermal, biological, and chemical technologies is not limited to crop residues but can be extended to plastic waste, municipal waste, food waste, and non-biodegradable raw materials. Integrated conversion technologies will promote circular bio-economy and other waste-to-energy initiatives.
Acknowledgement: The authors acknowledge the support of the authority of the Faculty of Engineering, Ekiti State University for providing a conducive atmosphere for this work.
Funding Statement: The authors received no specific funding for this study.
Author Contributions: Omojola Awogbemi: Conceptualization, draft manuscript preparation, reviewing, project administration, software supply, corresponding author; Ayotunde Adigun Ojo: Reviewing, data collection, analysis and interpretation of results, project administration, software supply; Samson Adedayo Adeleye: Reviewing, data collection, analysis and interpretation of results, project administration, software supply.
Availability of Data and Materials: Not applicable.
Conflicts of Interest: The authors declare that they have no conflicts of interest to report regarding the present study.
References
1. Ritchie, H., Rosado, P., Roser, M. (2023). Agricultural production. https://ourworldindata.org/agricultural-productionHannah (accessed on 20/08/2023) [Google Scholar]
2. World population by year. https://www.worldometers.info/world-population/world-population-by-year (accessed on 20/08/2023) [Google Scholar]
3. World Bank (2018). What a waste 2.0: A global snapshot of solid waste management to 2050. https://openknowledge.worldbank.org/entities/publication/d3f9d45e-115f-559b-b14f-28552410e90a (accessed on 20/08/2023) [Google Scholar]
4. Management market. https://www.precedenceresearch.com/waste-management-market# (accessed on 20/08/2023) [Google Scholar]
5. Awogbemi, O., Kallon, D. V. V. (2022). Valorization of agricultural wastes for biofuel applications. Heliyon, 8(10), e11117. [Google Scholar] [PubMed]
6. Awogbemi, O., Kallon, D. V. V. (2023). Application of biochar derived from crops residues for biofuel production. Fuel Communications, 15, 1000883. [Google Scholar]
7. Kumar Sarangi, P., Subudhi, S., Bhatia, L., Saha, K., Mudgil, D. et al. (2023). Utilization of agricultural waste biomass and recycling toward circular bioeconomy. Environmental Science and Pollution Research, 30(4), 8526–8539. [Google Scholar] [PubMed]
8. Global hydrogen production 2018 & 2030. https://www.statista.com/statistics/1121207/global-hydrogen-production/ (accessed on 20/08/2023) [Google Scholar]
9. Hydrogen insight. https://www.hydrogeninsight.com/production/exclusive-which-ten-countries-will-be-the-biggest-producers-of-green-hydrogen-in-2030-/2-1-1405571 (accessed on 20/08/2023) [Google Scholar]
10. Green Hydrogen Market. https://www.precedenceresearch.com/green-hydrogen-market (accessed on 20/08/2023) [Google Scholar]
11. Fricler, V. Y., Nyashina, G. S., Vershinina, K. Y., Vinogrodskiy, K. V., Shvets, A. S. et al. (2023). Microwave pyrolysis of agricultural waste: Influence of catalysts, absorbers, particle size and blending components. Journal of Analytical and Applied Pyrolysis, 171, 105962. [Google Scholar]
12. Karaeva, J. V., Timofeeva, S. S., Kovalev, A. A., Kovalev, D. A., Gilfanov, M. F. et al. (2022). Co-pyrolysis of agricultural waste and estimation of the applicability of pyrolysis in the integrated technology of biorenewable hydrogen production. International Journal of Hydrogen Energy, 47(23), 11787–11798. [Google Scholar]
13. Mo, W., Xiong, Z., Leong, H., Gong, X., Jiang, L. et al. (2022). Processes simulation and environmental evaluation of biofuel production via co-pyrolysis of tropical agricultural waste. Energy, 242, 123016. [Google Scholar]
14. Su, G., Zulkifli, N. W. M., Ong, H. C., Ibrahim, S., Yu, K. L. et al. (2023). Carbon-negative co-production of methanol and activated carbon from bagasse pyrolysis, physical activation, chemical looping, and methanol synthesis. Energy Conversion and Management, 293, 117481. [Google Scholar]
15. Okot, D. K., Bilsborrow, P. E., Phan, A. N., Manning, D. A. C. (2023). Kinetics of maize cob and bean straw pyrolysis and combustion. Heliyon, 9(6), e17236. [Google Scholar] [PubMed]
16. Zaidi, A. A., Khan, A., AlMohamadi, H., Anjum, M. W., Ali, I. et al. (2023). Catalytic pyrolysis of rice husk over defect-rich beta zeolites for biofuel production. Fuel, 348, 128624. [Google Scholar]
17. Pocha, C. K. R., Chia, W. Y., Silvanir, T. A., Khoo, K. S., Chew, K. W. (2023). Thermochemical conversion of different biomass feedstocks into hydrogen for power plant electricity generation. Fuel, 340, 127472. [Google Scholar]
18. Osman, A. I., Lai Z. Y., Farghali, M., Yiin, C. L., Elgarahy, A. M. et al. (2023). Optimizing biomass pathways to bioenergy and biochar application in electricity generation, biodiesel production, and biohydrogen production. Environmental Chemistry Letters, 21, 2639–2705. [Google Scholar]
19. Khan, A., Niazi, M. B. K., Ansar, R., Jahan, Z., Javaid, F. et al. (2023). Thermochemical conversion of agricultural waste to hydrogen, methane, and biofuels: A review. Fuel, 351, 128947. [Google Scholar]
20. Awogbemi, O., Kallon, D. V. V., Aigbodion, V. S. (2022). Pathways for sustainable utilization of waste chicken eggshell. Journal of Renewable Materials, 10(8), 2217–2246. https://doi.org/10.32604/jrm.2022.019152 [Google Scholar] [CrossRef]
21. Dafiqurrohman, H., Safitri, K. A., Setyawan, M. I. B., Surjosatyo, A., Aziz, M. (2022). Gasification of rice wastes toward green and sustainable energy production: A review. Journal of Cleaner Production, 366, 132926. [Google Scholar]
22. Mousavi Rabeti, S. A., Khoshgoftar Manesh, M. H., Amidpour, M. (2023). Techno-economic and environmental assessment of a novel polygeneration system based on integration of biomass air-steam gasification and solar parabolic trough collector. Sustainable Energy Technologies and Assessments, 56, 103030. [Google Scholar]
23. Seo, J. Y., Tokmurzin, D., Lee, D., Lee, S. H., Seo, M. W. et al. (2022). Production of biochar from crop residues and its application for biofuel production processes—An overview. Bioresource Technology, 361, 127740. [Google Scholar] [PubMed]
24. Li, J., Li, L., Tong, Y. W., Wang, X. (2023). Understanding and optimizing the gasification of biomass waste with machine learning. Green Chemical Engineering, 4(1), 123–133. [Google Scholar]
25. Inayat, M., Sulaiman, S. A., Shahbaz, M., Bhayo, B. A. (2020). Application of response surface methodology in catalytic co-gasification of palm wastes for bioenergy conversion using mineral catalysts. Biomass and Bioenergy, 132, 105418. [Google Scholar]
26. Sansaniwal, S. K., Rosen, M. A., Tyagi, S. K. (2017). Global challenges in the sustainable development of biomass gasification: An overview. Renewable and Sustainable Energy Reviews, 80, 23–43. [Google Scholar]
27. Pandey, B., Prajapati, Y. K., Sheth, P. N. (2019). Recent progress in thermochemical techniques to produce hydrogen gas from biomass: A state of the art review. International Journal of Hydrogen Energy, 44(7), 25384–25415. [Google Scholar]
28. Bhattacharya, A., Bhattacharya, A., Datta, A. (2012). Modeling of hydrogen production process from biomass using oxygen blown gasification. International Journal of Hydrogen Energy, 37(24), 18782–18790. [Google Scholar]
29. Wu, Y., Yang, W., Blasiak, W. (2014). Energy and exergy analysis of high temperature agent gasification of biomass. Energies, 7(4), 2107–2122. [Google Scholar]
30. Del Grosso, M., Cutz, L., Tiringer, U., Tsekos, C., Taheri, P. et al. (2022). Influence of indirectly heated steam-blown gasification process conditions on biochar physico-chemical properties. Fuel Processing Technology, 235, 107347. [Google Scholar]
31. Boukis, N., Stoll, I. K. (2021). Gasification of biomass in supercritical water, challenges for the process design—Lessons learned from the operation experience of the first dedicated pilot plant. Processes, 9(3), 455. [Google Scholar]
32. Wang, Q., Zhang, X., Cui, D., Bai, J., Wang, Z. et al. (2023). Advances in supercritical water gasification of lignocellulosic biomass for hydrogen production. Journal of Analytical and Applied Pyrolysis, 170, 105934. [Google Scholar]
33. Chen, J., Wang, Q., Xu, Z., Jiaqiang, E., Leng, E. et al. (2021). Process in supercritical water gasification of coal: A review of fundamentals, mechanisms, catalysts and element transformation. Energy Conversion and Management, 237, 114122. [Google Scholar]
34. Sun, J., Norouzi, O., Mašek, O. (2022). A state-of-the-art review on algae pyrolysis for bioenergy and biochar production. Bioresource Technology, 346, 126258. [Google Scholar] [PubMed]
35. Chandra, S., Medha, I., Tiwari, A. K. (2023). The role of modified biochar for the remediation of coal mining-impacted contaminated soil: A review. Sustainability, 15(5), 3973. [Google Scholar]
36. Jerzak, W., Gao, N., Kalemba-Rec, I., Magdziarz, A. (2022). Catalytic intermediate pyrolysis of post-extraction rapeseed meal by reusing ZSM-5 and Zeolite Y catalysts. Catalysis Today, 404, 63–77. [Google Scholar]
37. Vuppaladadiyam, A. K., Vuppaladadiyam, S. S. V., Awasthi, A., Sahoo, A., Rehman, S. et al. (2022). Biomass pyrolysis: A review on recent advancements and green hydrogen production. Bioresource Technology, 364, 128087. [Google Scholar] [PubMed]
38. Yang, C., Li, R., Zhang, B., Qiu, Q., Wang, B. et al. (2019). Pyrolysis of microalgae: A critical review. Fuel Processing Technology, 186, 53–72. [Google Scholar]
39. Ighalo, J. O., Iwuchukwu, F. U., Eyankware, O. E., Iwuozor, K. O., Olotu, K. et al. (2022). Flash pyrolysis of biomass: A review of recent advances. Clean Technologies and Environmental Policy, 24(8), 2349–2363. [Google Scholar]
40. Ruiz, B., Fuente, E., Pérez, A., Taboada-Ruiz, L., Sanz, J. M. et al. (2023). Employment of conventional and flash pyrolysis for biomass wastes from the textile industry with sustainable prospects. Journal of Analytical and Applied Pyrolysis, 169, 105864. [Google Scholar]
41. Qiu, B., Xao, X., Wang, J., Liu, Y., Li, S. et al. (2022). Research progress in the preparation of high-quality liquid fuels and chemicals by catalytic pyrolysis of biomass: A review. Energy Conversion and Management, 261, 115647. [Google Scholar]
42. Mishra, K., Singh Siwal, S., Kumar Saini, A., Thakur, V. K. (2023). Recent update on gasification and pyrolysis processes of lignocellulosic and algal biomass for hydrogen production. Fuel, 332, 126169. [Google Scholar]
43. Azizi, K., Keshavarz Moraveji, M., Arregi, A., Amutio, M., Lopez, G. et al. (2020). On the pyrolysis of different microalgae species in a conical spouted bed reactor: Bio-fuel yields and characterization. Bioresource Technology, 311, 123561. [Google Scholar] [PubMed]
44. Vuppaladadiyam, A. K., Memon, M. Z., Ji, G., Raheem, A., Jia, T. Z. et al. (2018). Thermal characteristics and kinetic analysis of woody biomass pyrolysis in the presence of bifunctional alkali metal ceramics. ACS Sustainable Chemistry & Engineering, 7(1), 238–248. [Google Scholar]
45. Shi, X., Li, P., Wang, X., Song, J., Fang, S. et al. (2022). Enhancement of the production of aromatics and bio-syngas from microwave ex-situ pyrolysis based on Zn/Zr modified biochar and multi-catalysts. Energy, 261, 125307. [Google Scholar]
46. Nzihou, A., Stanmore, B., Lyczko, N., Minh, D. P. (2019). The catalytic effect of inherent and adsorbed metals on the fast/flash pyrolysis of biomass: A review. Energy, 170, 326–337. [Google Scholar]
47. Xia, S., Wang, C., Chen, Y., Kang, S., Zhao, K. et al. (2022). Sustainable aromatic production from catalytic fast pyrolysis of 2-methylfuran over metal-modified ZSM-5. Catalysts, 12(11), 1483. [Google Scholar]
48. Imran, A., Bramer, E. A., Seshan, K., Brem, G. (2016). Catalytic flash pyrolysis of biomass using different types of zeolite and online vapor fractionation. Energies, 9(3), 187. [Google Scholar]
49. Lee, J., Kwon, E. E., Park, Y. K. (2020). Recent advances in the catalytic pyrolysis of microalgae. Catalysis Today, 355, 263–271. [Google Scholar]
50. Lu, Q., Li, W., Zhang, X., Liu, Z., Cao, Q. et al. (2020). Experimental study on catalytic pyrolysis of biomass over a Ni/Ca-promoted Fe catalyst. Fuel, 263, 116690. [Google Scholar]
51. Yue, W., Ma, X., Yu, Z., Liu, H., Li, M. et al. (2023). Ni-CaO bifunctional catalyst for biomass catalytic pyrolysis to produce hydrogen-rich gas. Journal of Analytical and Applied Pyrolysis, 169, 105872. [Google Scholar]
52. Yang, S., Chen, L., Sun, L., Xie, X., Zhao, B. et al. (2021). Novel Ni-Al nanosheet catalyst with homogeneously embedded nickel nanoparticles for hydrogen-rich syngas production from biomass pyrolysis. International Journal of Hydrogen Energy, 46(2), 1762–1776. [Google Scholar]
53. Deng, J., Zhou, Y., Zhao, Y., Meng, L., Qin, T. et al. (2022). Catalytic pyrolysis of pine needle biomass over Fe–Co–K catalyst for H2-rich syngas production: Influence of catalyst preparation. Energy, 244, 122602. [Google Scholar]
54. Wang, Z., Burra, K. G., Lei, T., Gupta, A. K. (2021). Co-pyrolysis of waste plastic and solid biomass for synergistic production of biofuels and chemicals–A review. Progress in Energy and Combustion Science, 84, 100899. [Google Scholar]
55. Xie, Q., Addy, M., Liu, S., Zhang, B., Cheng, Y. et al. (2015). Fast microwave-assisted catalytic co-pyrolysis of microalgae and scum for bio-oil production. Fuel, 160, 577–582. [Google Scholar]
56. Vuppaladadiyam, A. K., Liu, H., Zhao, M., Soomro, A. F., Memon, M. Z. et al. (2019). Thermogravimetric and kinetic analysis to discern synergy during the co-pyrolysis of microalgae and swine manure digestate. Biotechnology for Biofuels, 12, 1–18. [Google Scholar]
57. Fakayode, O. A., Wahia, H., Zhang, L., Zhou, C., Ma, H. (2023). State-of-the-art co-pyrolysis of lignocellulosic and macroalgae biomass feedstocks for improved bio-oil production–A review. Fuel, 332, 126071. [Google Scholar]
58. Ahmed, M. H. M., Batalha, N., Mahmudul, H. D. M., Perkins, G., Konarova, M. (2020). A review on advanced catalytic co-pyrolysis of biomass and hydrogen-rich feedstock: Insights into synergistic effect, catalyst development and reaction mechanism. Bioresource Technology, 310, 123457. [Google Scholar] [PubMed]
59. Lin, X., Lei, H., Wang, C., Qian, M., Mateo, W. et al. (2023). The effects of pore structures and functional groups on the catalytic performance of activated carbon catalysts for the co-pyrolysis of biomass and plastic into aromatics and hydrogen-rich syngas. Renewable Energy, 202, 855–864. [Google Scholar]
60. Hu, Y., Wang, S., Li, J., Wang, Q., He, Z. et al. (2018). Co-pyrolysis and co-hydrothermal liquefaction of seaweeds and rice husk: Comparative study towards enhanced biofuel production. Journal of Analytical and Applied Pyrolysis, 129, 162–170. [Google Scholar]
61. Tang, Y., Dong, J., Zhao, Y., Li, G., Chi, Y. et al. (2022). Hydrogen-rich and clean fuel gas production from co-pyrolysis of biomass and plastic blends with CaO additive. ACS Omega, 7(41), 36468–36478. [Google Scholar] [PubMed]
62. Mohabeer, C., Guilhaume, N., Laurenti, D., Schuurman, Y. (2022). Microwave-assisted pyrolysis of biomass with and without use of catalyst in a fluidised bed reactor: A review. Energies, 15(9), 3258. [Google Scholar]
63. Zhang, Y., Cui, Y., Liu, S., Fan, L., Zhou, N. et al. (2020). Fast microwave-assisted pyrolysis of wastes for biofuels production—A review. Bioresource Technology, 297, 122480. [Google Scholar] [PubMed]
64. Luo, J., Ma, R., Lin, J., Sun, S., Gong, G. et al. (2023). Review of microwave pyrolysis of sludge to produce high quality biogas: Multi-perspectives process optimization and critical issues proposal. Renewable and Sustainable Energy Reviews, 173, 113107. [Google Scholar]
65. Lin, B. J., Chen, W. H. (2015). Sugarcane bagasse pyrolysis in a carbon dioxide atmosphere with conventional and microwave-assisted heating. Frontiers in Energy Research, 3, 1–6. [Google Scholar]
66. Parvez, A. M., Wu, T., Afzal, M. T., Mareta, S., He, T. et al. (2019). Conventional and microwave-assisted pyrolysis of gumwood: A comparison study using thermodynamic evaluation and hydrogen production. Fuel Processing Technology, 184, 1–11. [Google Scholar]
67. Bartoli, M., Rosi, L., Giovannelli, A., Frediani, P., Frediani, M. (2020). Characterization of bio-oil and bio-char produced by low-temperature microwave-assisted pyrolysis of olive pruning residue using various absorbers. Waste Management & Research, 38(2), 213–225. [Google Scholar]
68. Oh, S., Lee, J., Lam, S. S., Kwon, E. E., Ha, J. M. et al. (2021). Fast hydropyrolysis of biomass Conversion: A comparative review. Bioresource Technology, 342, 126067. [Google Scholar] [PubMed]
69. Jindal, M., Kumar, A., Kaur, R., Chandra Sekhar Palla, V., Bhaskar, T. (2022). Flash hydropyrolysis of cotton stalks: Role of temperature, metal loading, pressure for enhancement of aromatics. Bioresource Technology, 351, 127047. [Google Scholar] [PubMed]
70. Lonchay, W., Bagnato, G., Sanna, A. (2022). Highly selective hydropyrolysis of lignin waste to benzene, toluene and xylene in presence of zirconia supported iron catalyst. Bioresource Technology, 361, 127727. [Google Scholar] [PubMed]
71. Sarkar, J. K., Wang, Q. (2020). Characterization of pyrolysis products and kinetic analysis of waste jute stick biomass. Processes, 8(7), 837. [Google Scholar]
72. Chen, H., Cheng, H., Zhou, F., Chen, K., Qiao, K. et al. (2018). Catalytic fast pyrolysis of rice straw to aromatic compounds over hierarchical HZSM-5 produced by alkali treatment and metal-modification. Journal of Analytical and Applied Pyrolysis, 131, 76–84. [Google Scholar]
73. Estrada Leon, A., Ramamurthy, R., Ghysels, S., Niazi, S., Prins, W. et al. (2023). Analytical (hydro)pyrolysis of pinewood and wheat straw in chloride molten salts: A route for 2-methyl furan production. Fuel Processing Technology, 250, 107917. [Google Scholar]
74. Huang, Y., Li, B., Liu, D., Xie, X., Zhang, H. et al. (2020). Fundamental advances in biomass autothermal/oxidative pyrolysis: A review. ACS Sustainable Chemistry & Engineering, 8(32), 11888–11905. [Google Scholar]
75. Li, B., Song, M., Xie, X., Wei, J., Xu, D. et al. (2023). Oxidative fast pyrolysis of biomass in a quartz tube fluidized bed reactor: Effect of oxygen equivalence ratio. Energy, 270, 126987. [Google Scholar]
76. Olafasakin, O., Chang, Y., Passalacqua, A., Subramaniam, S., Brown, R. C. et al. (2021). Machine learning reduced order model for cost and emission assessment of a pyrolysis system. Energy & Fuels, 35(12), 9950–9960. [Google Scholar]
77. Polin, J. P., Carr, H. D., Whitmer, L. E., Smith, R. G., Brown, R. C. (2019). Conventional and autothermal pyrolysis of corn stover: Overcoming the processing challenges of high-ash agricultural residues. Journal of Analytical and Applied Pyrolysis, 143, 104679. [Google Scholar]
78. Mlonka-Mędrala, A., Evangelopoulos, P., Sieradzka, M., Zajemska, M., Magdziarz, A. (2021). Pyrolysis of agricultural waste biomass towards production of gas fuel and high-quality char: Experimental and numerical investigations. Fuel, 296, 120611. [Google Scholar]
79. Akinpelu, D. A., Adekoya, O. A., Oladoye, P. O., Ogbaga, C. C., Okolie, J. A. (2023). Machine learning applications in biomass pyrolysis: From biorefinery to end-of-life product management. Digital Chemical Engineering, 8, 100103. [Google Scholar]
80. Huttunen, M., Kallio, S. (2023). Evaluation of dynamic responses of a BFB boiler furnace by means of CFD modelling. Digital Chemical Engineering, 7, 100095. [Google Scholar]
81. Sharma, R. K., Nazari, M. A., Haydary, J., Singh, T. P., Mandal, S. (2023). A review on advanced processes of biohydrogen generation from lignocellulosic biomass with special emphasis on thermochemical conversion. Energies, 16(17), 6349. [Google Scholar]
82. Siwal, S. S., Sheoran, K., Saini, A. K., Vo, D. V. N., Wang, Q. et al. (2022). Advanced thermochemical conversion technologies used for energy generation: Advancement and prospects. Fuel, 321, 124107. [Google Scholar]
83. Pocha, C. K. R., Chia, R., Silvanir, W. Y., Kurniawan, T. A., Khoo, K. S. et al. (2023). Thermochemical conversion of different biomass feedstocks into hydrogen for power plant electricity generation. Fuel, 340, 127472. [Google Scholar]
84. Osman, A. I., Deka, T. J., Baruah, D. C., Rooney, D. W. (2020). Critical challenges in biohydrogen production processes from the organic feedstocks. Biomass Conversion and Biorefinery, 13, 8383–8401. [Google Scholar]
85. Ramprakash, B., Lindblad, P., Eaton-Rye, J. J., Incharoensakdi, A. (2022). Current strategies and future perspectives in biological hydrogen production: A review. Renewable and Sustainable Energy Reviews, 168, 112773. [Google Scholar]
86. Chakrabarty, P., Alam, K. C. A., Paul, S. K., Saha, S. C. (2024). Hydrogen production by electrolysis: A sustainable pathway. In: Khan, M. M. K., Azad, A. K., Oo, A. M. T. (Eds.Hydrogen energy conversion and management, pp. 81–102. Netherlands: Elsevier. [Google Scholar]
87. Veeramani, K., Janani, G., Kim, J., Surendran, S., Lim, J. et al. (2023). Hydrogen and value-added products yield from hybrid water electrolysis: A critical review on recent developments. Renewable and Sustainable Energy Reviews, 177, 113227. [Google Scholar]
88. Zhao, Y., Niu, Z., Zhao, J., Xue, L., Fu, X. et al. (2023). Recent advancements in photoelectrochemical water splitting for hydrogen production. Electrochemical Energy Reviews, 6(1), 14. [Google Scholar]
89. Ge, M., Yang, M. C., Wang, L. S., Ma, X. G. (2023). Photocatalytic hydrogen generation from overall water splitting with direct Z-scheme driven by two-dimensional InTe/Bismuthene heterostructure. International Journal of Hydrogen Energy, 48(1), 138–146. [Google Scholar]
90. Tayibi, S., Monlau, F., Bargaz, A., Jimenez, R., Barakat, A. (2021). Synergy of anaerobic digestion and pyrolysis processes for sustainable waste management: A critical review and future perspectives. Renewable and Sustainable Energy Reviews, 152, 111603. [Google Scholar]
91. Wang, W., Chang, L. S., Lee, D. J. (2023). Anaerobic digestate valorization beyond agricultural application: Current status and prospects. Bioresource Technology, 373, 128742. [Google Scholar] [PubMed]
92. Nguyen, V. G., Nguyen-Thi, T. X., Phong Nguyen, P. Q., Tran, V. D., Ağbulut, Ü. et al. (2023). Recent advances in hydrogen production from biomass waste with a focus on pyrolysis and gasification. International Journal of Hydrogen Energy, 48(101), 40216–40227. [Google Scholar]
93. Choi, H. Kim, Y., T., Tsang, Y. F., Lee, L. (2023). Integration of thermochemical conversion processes for waste-to-energy: A review. Korean Journal of Chemical Engineering, 40, 1815–1821. [Google Scholar]
94. Kobayashi, T., Kuramochi, H. (2023). Catalytic pyrolysis of biomass using fly ash leachate to increase carbon monoxide production and improve biochar properties to accelerate anaerobic digestion. Bioresource Technology, 387, 129583. [Google Scholar] [PubMed]
95. Singh, R., Paritosh, K., Pareek, N., Vivekanand, V. (2022). Integrated system of anaerobic digestion and pyrolysis for valorization of agricultural and food waste towards circular bioeconomy: Review. Bioresource Technology, 360, 127596. [Google Scholar] [PubMed]
96. Sevillano, C. A., Pesantes, A. A., Peña Carpio, E., Martínez, E. J., Gómez, X. (2021). Anaerobic digestion for producing renewable energy—the evolution of this technology in a new uncertain scenario. Entropy, 23(2), 145. [Google Scholar] [PubMed]
97. Moško, J., Pohořelý, M., Cajthaml, T., Jeremiáš, M., Robles-Aguilar, A. A. et al. (2021). Effect of pyrolysis temperature on removal of organic pollutants present in anaerobically stabilized sewage sludge. Chemosphere, 265, 129082. [Google Scholar] [PubMed]
98. Yang, Z., Liu, Y., Zhang, J., Mao, K., Kurbonova, M. et al. (2020). Improvement of biofuel recovery from food waste by integration of anaerobic digestion, digestate pyrolysis and syngas biomethanation under mesophilic and thermophilic conditions. Journal of Cleaner Production, 256, 120594. [Google Scholar]
99. Ebrahimi, A., Houshfar, E. (2022). Thermodynamic analysis and optimization of the integrated system of pyrolysis and anaerobic digestion. Process Safety and Environmental Protection, 164, 582–594. [Google Scholar]
100. Giwa, A. S., Chang, F., Xu, H., Zhang, X., Huang, B. et al. (2019). Pyrolysis of difficult biodegradable fractions and the real syngas bio-methanation performance. Journal of Cleaner Production, 233, 711–719. [Google Scholar]
101. Song, X. D., Chen, D. Z., Zhang, J., Dai, X. H., Qi, Y. Y. (2017). Anaerobic digestion combined pyrolysis for paper mill sludge disposal and its influence on char characteristics. Journal of Material Cycles and Waste Management, 19, 332–341. [Google Scholar]
102. Li, H., Feng, K. (2018). Life cycle assessment of the environmental impacts and energy efficiency of an integration of sludge anaerobic digestion and pyrolysis. Journal of Cleaner Production, 195, 476–485. [Google Scholar]
103. Deng, C., Lin, R., Kang, X., Wu, B., O’Shea, R. et al. (2020). Improving gaseous biofuel yield from seaweed through a cascading circular bioenergy system integrating anaerobic digestion and pyrolysis. Renewable and Sustainable Energy Reviews, 128, 109895. [Google Scholar]
104. Wang, Z., Chen, C., Zhang, X., Li, J., Wu, W. et al. (2023). An operation strategy towards efficient energy recovery from integrated anaerobic digestion and pyrolysis of corn stalk. Resources, Conservation and Recycling, 188, 106710. [Google Scholar]
105. Wang, S., Wen, Y., Shi, Z., Nuran Zaini, I., Göran Jönsson, P. et al. (2022). Novel carbon-negative methane production via integrating anaerobic digestion and pyrolysis of organic fraction of municipal solid waste. Energy Conversion and Management, 252, 115042. [Google Scholar]
106. Glushkov, D., Nyashina, G., Shvets, A., Pereira, A., Ramanathan, A. (2021). Current status of the pyrolysis and gasification mechanism of biomass. Energies, 14(22), 7541. [Google Scholar]
107. Parthasarathy, P., Sheeba, K. (2015). Combined slow pyrolysis and steam gasification of biomass for hydrogen generation—A review. International Journal of Energy Research, 39(2), 147–164. [Google Scholar]
108. Im-orb, K., Wiyaratn, W., Arpornwichanop, A. (2018). Technical and economic assessment of the pyrolysis and gasification integrated process for biomass conversion. Energy, 153, 592–603. [Google Scholar]
109. Hwang, J. G., Choi, M. K., Choi, D. H., Choi, H. S. (2021). Quality improvement and tar reduction of syngas produced by bio-oil gasification. Energy, 236, 121473. [Google Scholar]
110. Ai, N., Chen, L., Fu, Y. (2022). A novel analysis on pyrolysis and gasification process of rice straw feedstock. Sustainable Energy Technologies and Assessments, 51, 101866. [Google Scholar]
111. Ramirez, J. A., Rainey, T. J. (2019). Comparative techno-economic analysis of biofuel production through gasification, thermal liquefaction and pyrolysis of sugarcane bagasse. Journal of Cleaner Production, 229, 513–527. [Google Scholar]
112. Ge, S., Yek, P. N. Y., Cheng, Y. W., Xia, C., Wan Mahari, W. A. et al. (2021). Progress in microwave pyrolysis conversion of agricultural waste to value-added biofuels: A batch to continuous approach. Renewable and Sustainable Energy Reviews, 135, 110148. [Google Scholar]
Cite This Article
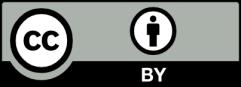
This work is licensed under a Creative Commons Attribution 4.0 International License , which permits unrestricted use, distribution, and reproduction in any medium, provided the original work is properly cited.