Open Access
ARTICLE
Curing Process of Phenol Formaldehyde Resin for Plywood under Vacuum Conditions
1
College of Furnishings and Industrial Design, Nanjing Forestry University, Nanjing, 210037, China
2
School of Forestry & Landscape Architecture, Anhui Agricultural University, Hefei, 230036, China
3
College of Materials Science and Engineering, Nanjing Forestry University, Nanjing, 210037, China
* Corresponding Authors: Xiaoning Lu. Email: ; Juwan Jin. Email:
Journal of Renewable Materials 2023, 11(9), 3447-3461. https://doi.org/10.32604/jrm.2023.027430
Received 29 October 2022; Accepted 01 February 2023; Issue published 20 July 2023
Abstract
The study characterized the curing behaviors of phenol formaldehyde (PF) resin under different vacuum degrees and explored the properties of 9-ply plywood panels hot-pressed under both vacuum and atmospheric conditions. The changes in core temperature and moisture content of the plywood mats during hot pressing were investigated as well. It was found that the gel times and gel temperatures of PF resin decreased with the increase of vacuum degree using a self-made device. FTIR spectra indicated the degree of polycondensation of hydroxymethyl gradually increased with the increase in temperature. It was also observed that a higher degree of vacuum led to a slower polycondensation reaction rate of PF resin. During different hot-pressing processes, the bonding strengths in the innermost and uppermost gluelines of the vacuum hot-pressed plywood panels were up to 30%–50% higher than their counterparts of conventional hot-pressed products. A less difference in the bonding strengths between these two gluelines was also observed for vacuum hot-pressed products. In addition, the core of vacuum hot-pressed plywood was found to have a greater heating rate and higher temperature at the final stage of hot pressing, which was beneficial to cure the PF resin. The results from this study indicate a promising potential of introducing a vacuum during hot pressing to improve the quality and productivity of plywood products and provide a basis for adopting vacuum to hot press wood composites.Keywords
Plywood is a panel product consisting of wood veneers, which makes it practical to produce stronger, more stable, and more durable products than particleboard or medium-density fiberboard. Thus, plywood is not only a good material for furniture making. More importantly, plywood products bonded with phenolic formaldehyde (PF) resin are traditionally and currently dominant panel products for heavy-duty end-uses such as construction sheathing, container flooring, and concrete forms [1,2].
In the production of plywood, hot pressing is the most critical process that directly affects product quality, productivity, energy consumption, and cost. Hence, manipulation of key hot-pressing parameters, including hot press temperature, pressure, and time, to achieve an optimal balance between the quality and production cost of plywood products is the key to hot pressing process [3]. Compared with the hot press temperatures for pressing particleboard and fiberboard, the temperature for pressing plywood is much lower when similar resin adhesives are used. This is because a lower hot press temperature results in lower internal gas pressures. And therefore less risk of blisters and lower energy costs. For instance, the press temperature for plywood bonded with urea formaldehyde resin ranges from 100°C to 120°C. Even PF resins that need more energy to initiate cure, the typical temperature for pressing PF-bonded plywood products is set to around 160°C only [4]. Though using the lower temperature for pressing plywood presents the above-mentioned merits, it inevitably leads to a slower heating rate in the core of the plywood mat and, therefore, a longer time to heat the innermost glueline to the temperature required for resin polymerization. Consequently, lower press temperatures result in longer times to cure the resins, and thus, longer press time reduces plywood production productivity. Therefore, how to increase the heating rate of the core and how to cure the resin quickly are of great importance and have become critical goals for optimizing the hot-pressing process of plywood products.
One promising approach to achieve the goals is hot pressing plywood with the help of a vacuum, i.e., vacuum hot pressing. Hong et al. studied the influence of vacuum hot pressing on plywood’s bonding quality and heat transfer performance. Their results reported that the core temperature of vacuum pressed plywood mats at the end of hot pressing were about 20°C to 30°C significantly higher and the PF adhesive cured more quickly under vacuum hot pressing compared to conventional hot pressing. Moreover, they observed that the vacuum hot-pressing method had significantly improved the bonding strength of plywood by 48.37% [5,6].
More needs to be explored to further develop the vacuum hot-pressing technology for plywood. One key topic to be investigated is the curing process and characteristics of resin under vacuum conditions since the curing behavior of resin directly affects both the hot-pressing procedure and the quality of the plywood products. The cure of PF resins is complex due to the interaction between the chemical kinetics and changes in their physical properties [7–12]. One method to investigate the cure of PF resins is to determine their gel times and temperatures. Gel time is the temporal duration required for the liquid resin transition from sol to gel state, occurring at the beginning of the hot-pressing process. Gelation has a great influence on molecular flow, such as reaction rate, processing difficulty, and so on [13,14]. It is important to relate the gelation to the reaction time at different cure temperatures so that desired properties can be controlled. Gel time is one of the important factors affecting resin curing. As for characterizing the curing behavior of PF resin, Fourier transforms infrared spectroscopy (FTIR) is an appropriate tool to be adopted. FTIR is one of the most important means to characterize polymers and has been established as a powerful tool for the study of material [15–17], macromolecules, and so on [18–20]. FTIR analyses are the bases for evaluating and providing atomic bonding information by analyzing the intensity and position of the peaks in the spectra.
The purposes of this study were to determine gel times and temperatures of PF resin under different vacuum degrees and to characterize the chemical structure characteristics of PF resins cured under vacuum conditions, aiming at providing a fundamental basis for further developing the technology of vacuum hot pressing for PF-bonded plywood production. Moreover, to optimize the process of vacuum hot pressing for plywood, we also investigated the changes in the core temperature and moisture contents during vacuum hot pressing and compared the bonding strength values of typical plywood products pressed under both conventional and vacuum hot pressing.
Rotary-cut poplar (P. × canadensis Moench cv. ‘I-72/58’) veneers with a nominal thickness of 1.68 mm were obtained from Xuzhou, Jiangsu Province (China). They were cut into pieces of 330 mm × 330 mm (length × width), and those pieces of defect-free and uniform thickness were selected for making plywood panels. The average veneer crack degree and moisture content were about 40% and 10 ± 2%, respectively. The commercial plywood PF resin 14L960 (Nanjing Dynea Co., Ltd., China), with a solid content of 42% and a viscosity 80–100 cPa·s (at 25°C), was used for this study.
2.2 Method for Determining Gel Time of PF Resin
Various methods for determining gel time have been reported, including the pouring cup, rotational viscometer, and rheological technology via changing dynamic mechanical properties under conventional conditions [21–24]. However, most experimental devices are not suitable for being placed in a vacuum environment.
In this study, a self-made device for measuring the gel time of PF resin was developed. Fig. 1 gives the diagram of this device. Basically, there are three major components in this device: the core component based on the open-source hardware Arduino Uno development board; ATmega 328P single-chip microcomputer (MCU) as the core processor of data acquisition and processing using, and the external hardware consisting of voltage measurement module, temperature measurement module, and display module. The voltage measurement module tests the voltage value of the given resistance on the series circuit, which is used to judge the viscosity state of the PF resin solution and determine the gelation. The series circuit composes of a known value resistor, a DC motor with a propeller (12 V, 0.2 W, maximum torque: 3 kg∙cm), a DC power, and a pressure regulator. The temperature measurement module introduces the MCU to drive the MAX 6675 module, which acquires the PF resin solution temperature with a K-type thermocouple.
Figure 1: Diagram of the self-made device for determination of the gel time
According to the knowledge of electricity and mechanics, the expressions of thrust, resistance torque, and propeller power when the propeller is rotated are shown as follows:
where F is the thrust generated by the propeller; M is the resistance torque of the propeller; P is the power of the propeller; η is the viscosity of PF resin; n is the rotating speed of the propeller; D is the diameter of the propeller; KF and KM represent the propeller thrust coefficient and a torque coefficient, respectively. In the steady state, they are all constants; in the dynamic state, they all change with the advance ratio J.
For the DC motor in series circuit,
where I is the current of a series circuit; R0 is a 10 Ω resistor; U0 is the voltage of the resistor; V is the voltage value of the resistor shown in the digital voltmeter. According to formula (4), there is a positive correlation between V and η when the DC motor runs at low speed and remains stable.
During the testing for determining the gel time (when the resin temperature reach 50°C, the test begins timing), PF resin undergoes polycondensation reaction. As the reaction progresses, V (the voltage value on the measuring circuit) rises with the increase of η (the viscosity of the PF resin samples). When the propeller stops stirring, and the V value does not increase anymore, the resin sample is considered gelated. The time from the application of the heat until the propeller stops stirring is referred to as the approximate gel time, and the temperature at this point is taken as the gel temperature.
A sample of 20 ml PF resin was placed in a reverse mouth test tube, which was fixed in a constant temperature oil bath with a digital temperature display. Then, a propeller and a K-type thermocouple were inserted into PF sample in the tube. During the testing, samples were heated and cured under different vacuum conditions in an oven. The vacuum degree conditions were 0, −0.085, −0.090, and −0.095 MPa, respectively.
The test for the PF sample under the vacuum degree of 0 MPa (i.e., atmospheric pressure), which was regarded as the control sample, was conducted according to China National Standard for Plastics-PF resins-Determination of gel time (GB/T 33315-2016) at the oil bath temperature of 130°C. The determined gel time of the control sample was 60 min when the temperature rose from 50°C to 105°C (i.e., gel temperature). And at the point when the propeller stopped stirring in the control sample, the measured voltage value of the given resistance on the measuring circuit was 263 (
For the testing under the other three vacuum conditions, the propeller stirring speed and the temperature of the oil bath was set at 2~3 rpm and 100°C, respectively. Each set of the PF sample temperature in the tube and voltmeter data were recorded every 30 s. The testing was repeated five times for each vacuum condition.
2.3 Preparation of PF Samples for FTIR
We measured 2 ml of PF resin and placed it in a quartz crucible as one of the samples. In order to compare the effects of different curing conditions, i.e., atmospheric and vacuum conditions, we prepared two groups of samples: one group was cured at atmospheric pressure for 50 min at 105°C (gel temperature), 120°C, 140°C; another group was cured under vacuum conditions. Considering the influences of vacuum, gel time, and temperature, the vacuum degree of the drying oven was set at −0.085, −0.090, −0.095 MPa, respectively, and then the PF sample was cured at 80°C, 100°C, 120°C and 140°C for 50 min.
The cured PF resin samples were characterized by Fourier transform infrared spectroscopy (FTIR, VERTEX 80 V, Bruker Co., Ltd., Karlsruhe, Germany). The spectra were recorded by the KBr pellet technique in the solid state, with 32 spectra accumulated at a resolution of 2 cm−1 from the 4000 to 400 cm−1 wavenumber range [4,11]. The uncured PF resin was used as the control sample. We measured an appropriate amount of resin and dropped it on KBr. The sample dried 3 h with an infrared lamp (nearly 100°C) to remove moisture for FTIR analysis. The spectra were obtained with respect to a background that was previously recorded on air and under the same measurement conditions.
PF resin adhesive was applied to both surfaces of each even veneer ply at different spread quantities (200, 240 g∙m−2) with a hand roller spreader. The resinated veneer pieces and those pieces without resin adhesive were assembled perpendicular to each other to form plywood mats of 9-ply.
One set of mats were hot pressed using vacuum press equipment at the vacuum degree ranging from −0.090 to −0.095 MPa. The assembled mats were pressed into plywood panels with a thickness of 15.12 mm under 160°C and 0.8 MPa for 60 s∙mm−1.
For comparison, another set of mats was pressed into plywood panels of the same thickness using a conventional hot-pressing method at the same pressing temperature, time, and pressure. The replicates of plywood panels for each condition were five.
2.5 Measurement of the Core Temperature and Moisture of Mat
In this research, we adopted a thermocouple sensor (Type T/copper-constant), a humidity sensor, and a data collector to monitor and record the mat’s core temperature and moisture content under the hot pressing. The time interval for reading the temperature and moisture set by the data recorder was 2 s. Measurement started when the platen pressure reached the mat surface.
2.6 Testing of Bonding Strength
According to China National Standard for Type I Plywood (GB/T 9846-2015), the bonding strength of the plywood was tested with a universal mechanical testing machine (AG-IC, Shimadzu (China) Co., Ltd., China). Ten replicates for each condition were performed.
Fig. 2 gives the gel times of PF resin samples measured with the self-made device under different vacuum degrees. At the initial stage, due to heat conduction, the temperature of PF resin sample increased rapidly under vacuum conditions and soon reached a stable temperature platform of the boiling point of water and lasted for more than ten minutes. For example, the sample reached a stable platform at about 63.5°C under the vacuum of −0.085 MPa, about 58.5°C at −0.090 MPa, and around 53.5°C at −0.095 MPa. At this stage, the increase in temperature led to the weakening of intermolecular force. However, with the continuous evaporation of water and the increase in the solid content (SC) of resin, there was little change in viscosity and voltage data. Subsequently, when there was little water in the sample, the temperature started to rise slowly. PF resin began to cross-link, and the voltage value increased sharply. Since PF resin would change from sol to gel, the voltage value would continue to rise until it reached the threshold value.
Figure 2: Measured temperature and voltage of PF resin samples during the testing of gel times
The gel time data of PF resin adhesive under different vacuums were presented in Table 1. The results showed that the gel temperature was higher than the boiling point of water. The tested gel times ranged from 57.5 min at 61°C under a vacuum of −0.095 MPa to 65 min at 75°C under a vacuum of −0.085 MPa. Because of the large temperature difference between the resin in the test tube and the oil bath, the heat convection was faster, which led to faster gelation time. PF resin could cure at a lower temperature under vacuum conditions. And the lower vacuum degree, the lower gel temperature, and the shorter gel time of the PF resin. This indicates a great potential for introducing the vacuum during hot pressing to achieve a possible reduction in the curing time of the resin, and thus the reduction of hot-pressing time and the increase in the productivity.
3.2 Chemical Characteristics of PF Resin Powder Measured by FTIR
FTIR can not only qualitatively detect the types of functional groups but also be applied quantitatively to analyze the reaction of functional groups by measuring the changes in peaks height and peak areas [25,26]. In this study, according to the internal standard method, benzene ring skeleton vibration at 1606 cm−1 peaks without obvious shift and affected by vacuum and temperature changes during the curing process were selected as the reference peak. In order to quantify and compare the polycondensation reaction degree of PF resin samples cured under different conditions, the FTIR spectra of PF adhesive powder solidified under different vacuum degrees were normalized by the peak of benzene ring skeleton vibration.
After baseline correction and normalization, the infrared spectrum of the control sample is shown in Fig. 3. A wide transmittance band near 3450 cm−1 was assigned to the telescopic vibration of OH groups, and a peak near 1640 cm−1 was attributed to C=O stretching vibration. Significant peaks were observed near 1606 cm−1due to C=C vibration of the benzene ring skeleton, and the band at 1016 cm−1 belonged to C–O stretching vibration of CH2OH groups, while bands at 2890, 2850, and 1450 cm−1 were related to the C–H of CH2 groups. The peak at 886 and 800 cm−1 was the stretching vibration of C-H [27]. Bands assignment of FTIR is shown in Table 2.
Figure 3: FTIR spectra of control sample at atmospheric pressure
Fig. 4 displays the FTIR spectra from 4000 to 500 cm−1 of PF resin samples solidified under atmospheric pressure and different vacuum degrees and temperatures. The PF resin contains a lot of hydroxyl groups and hydroxymethyl groups. There was an obvious wide absorption peak (OH bond) at 3450 cm−1 and an obvious absorption peak (C-O stretching vibration of CH2OH group) at 1016 cm−1. In the curing reaction of PF resin, the main active group is hydroxymethyl. PF resin goes through three distinct stages as it cures. It is common to classify PF resins as A-stage (resloe), B-stage (resitol), and C-stage (resite) resins (Fig. 5) [28,29]. An A-stage resin corresponds to a mixture of monohydric, dibasic, and ternary hydroxymethyl phenols, sometimes containing a certain amount of dimers (molecular weight < 1000). Therefore, the monomers can easily continue to react under appropriate conditions, and more hydroxymethyl bridges are generated by polymerization, forming B-grade resin, which is obviously condensed but not cured. When resitol resin is heated, it is polycondensed again, and the final C-stage is produced. C-stage resin is cured or cross-linked phenolic.
Figure 4: FTIR spectra of PF samples solidified under different vacuum degrees
Figure 5: Curing mechanisms for PF resin
As shown in Figs. 6A–6C, under the same vacuum degree, the peak intensity of hydroxymethyl bond (-CH2OH) at 1016 cm−1 gradually decreased with the increase in temperature. When the curing temperature of the sample was 80°C, the peak intensity of PF resin was close to that of the control sample, and the polycondensation degree of hydroxymethyl was small. When the curing temperature was 140°C, the peak intensity was the lowest, and the polycondensation degree of hydroxymethyl was the highest. Therefore, the higher the temperature, the higher the degree of polycondensation under the same vacuum degree.
Figure 6: FTIR spectra of C-O bonds in hydroxyl groups with temperature and vacuum variation
As demonstrated in Fig. 6D, when the curing temperature of the sample was 80°C, the peak intensity at 1016 cm−1 under a vacuum of −0.085 MPa was higher than that of under a vacuum of −0.090 and −0.095 MPa. Under the vacuum of −0.085 MPa, the temperature of 80°C just exceeded the gel temperature in Table 1 and polycondensation degree of hydroxymethyl was less than that of the other two vacuum conditions. However, when the curing temperature reached 100°C, the peak intensity of hydroxymethyl bond under a vacuum of −0.085 MPa was significantly lower than that of under a vacuum of −0.090 and −0.095 MPa. The same result was obtained in the subsequent heating process. The results showed that the lower the degree of vacuum, the faster the polycondensation reaction rate at the same temperature. When the curing temperature rose to 140°C, the absorption peak intensity under vacuum of −0.085 and −0.090 MPa was very close to the peak intensity under atmospheric pressure, indicating free hydroxymethyl groups of PF resin reduced, and the polycondensation reaction was coming to an end.
In the fingerprint region of 650~910 cm−1, the intensity of absorption peaks can be used to characterize the substituted position of the phenolic aromatic ring of PF resin. Fig. 7 clearly showed that there were weak absorption peaks at 885 cm−1 and relatively strong peaks at 800 cm−1. According to the literature [30], the absorption peak at 885 cm−1 may be the vibration of isolated hydrogen atoms on the benzene ring skeleton, and the absorption peak at 800 cm−1 may be caused by the vibration of three adjacent hydrogen atoms on the benzene ring skeleton. With the increase in temperature, the peak intensity at 800 cm−1 is obviously higher than that at 885 cm−1. Therefore, in the curing reaction of PF resin under vacuum conditions, hydroxymethyl would preferably replace the active hydrogen on the 2, 6 ortho-position of the benzene ring. Therefore, the polycondensation reaction between hydroxymethyl groups can be shown in Fig. 8.
Figure 7: FTIR spectra of C-H bonds on phenol aromatic rings
Figure 8: Polycondensation reactions between hydroxyl methyl groups
Absorption peaks at 1060 cm−1 (C-O stretching vibration of ether bond) can hardly be found at 80°C~140°C in Fig. 9. The peak intensity of 1270 cm−1 (Phenolic OH and ether bond stretching vibration) continued to decrease with the rising temperature, the absorption carbon peak at 1640 cm−1 rose rapidly at the same time. Because hydroxyl groups were relatively stable compared with ether bonds, when the temperature was raised and vacuum was applied, the dibenzyl ethers were converted to something else, most likely to methylene linkages and formaldehyde [29,31], as shown in Fig. 8.
Figure 9: Partial FTIR spectra of PF resin from 1700 to 1000 cm−1
Consequently, the results of FTIR analysis showed that temperature had a positive effect on the curing reaction of PF resin. With the increase in temperature, the degree of polycondensation of hydroxymethyl gradually increased. While the vacuum degree had a negative effect on the curing reaction of phenolic resin, the higher the vacuum degree, the slower the polycondensation rate of phenolic resin, but the structure of final cured PF resins had no obvious changes.
3.3 Bonding Quality of Plywood
Fig. 10 illustrates the bonding strength values of all plywood panels hot-pressed via both vacuum and conventional pressing methods. Bonded with the same amount of PF resin, the bonding strength of vacuum hot-pressed plywood was higher than that of conventional hot-pressed plywood. The bonding strength of the innermost glueline in plywood vacuum hot-pressing was 50% higher than that of conventional hot-pressing conditions. The bonding strength of the uppermost glueline in vacuum hot-pressed plywood was up to 30% higher than that of conventional hot-pressed one. Under the hot-pressing pressure of 0.8 MPa and a vacuum degree of −0.090 to −0.095 MPa, the bonding strength of plywood reached the maximum value of 2.15 MPa when the PF resin spread quantity was 240 g∙m−2. In addition, the bonding strength of the innermost and uppermost gluelines when the PF resin spread quantity was 240 g∙m−2 was higher than that of the conventional hot-pressed plywood when the PF resin spread quantity was 280 g∙m−2 (1.75 and 1.37 MPa for the innermost and uppermost gluelines, respectively). To optimize the vacuum hot pressing technology for plywood, more future work is required to systematically investigate the effects of hot pressing parameters, including different adhesive spread levels, vacuum degree, hot-pressing time and hot-pressing temperature, on the bonding strength.
Figure 10: Bonding strength of plywood panels
Under a hot-pressing temperature and pressure, the needed hot-pressing time depends on the required curing time of the inner most glueline in the mat that is farthest away from the hot platen. The thicker the assembled mat, the longer the time to heat the core up to the adhesive cure time. Fig. 11 shows the temperature and moisture changes in the core of the 9-ply mats during different hot-pressing processes. The three stages of the core temperature behavior were observed during the conventional hot-pressing process. First, the temperature of the core rose rapidly because the heat transferred from the hot platen to the mat was used to heat veneer and glue. Then, the temperature of the central layer reached 100°C~103°C within 2 to 3 min. As the moisture of the veneer absorbs a lot of heat and evaporates, the temperature will be stable for nearly 10 min. Finally, with the decrease of moisture in the center layer, the temperature of the core only slowly raised to above 120°C at the end of hot pressing [32]. It took nearly 600 s to raise the temperature of the core to Tg-c (gel temperature of PF resin under atmospheric pressure), which was about 105°C as shown in Table 1. This indicated that the curing time of PF resin was short, the curing temperature was low, and many hydroxyl groups may not be fully cured under the condition of high MC (moisture content) for a long time and may form more small molecules.
Figure 11: Core temperature and moisture content of the plywood mats during different hot-pressing processes
Under the vacuum hot-pressing process, the heating rate of the core layer in 9-ply veneer mats was basically the same as that of the conventional pressed mat at the initial stage. When the mat surface temperature was heated to 60°C–70°C (the boiling point of water under vacuum), the moisture in the surface veneer layer absorbed a large amount of heat, and the heating rate of the core began to slow down, and it took about 2 min until the core was heated up to the boiling point. Because the moisture inside the mat could reach the boiling point at a lower temperature, the surface temperature of the mat was higher, and the moisture evaporated faster than the core. With the help of a vacuum pump, the plywood mat formed a moisture gradient with the high inside and low outside, which accelerated the migration of moisture inside of the mat to the outside, and moisture was continuously discharged from the plywood mat, resulting in the MC of the core dropping much faster and being lower than that of the mat under conventional hot pressing. Therefore, the duration of the stable temperature under vacuum hot pressing was obviously shortened. In the subsequent stage, the temperature heating rate of the core of the mat under vacuum hot pressing was obviously higher. And in a short time, after 10 min, the core temperature exceeded that of the mat under conventional hot pressing and reached over 140°C at the end of hot pressing.
Under vacuum hot pressing, PF resin could be cured at a lower temperature, about 60°C~65°C, and the core reached the Tg-v (gel temperature of PF resin under vacuum condition) within 300 s and had a higher temperature at the last period of the hot pressing cycle. Compared with conventional hot pressing at the same pressing pressure, temperature, and time, PF resin in the mat under vacuum hot pressing had a long time to cure, and therefore more hydroxymethyl groups participated in the reaction at a higher temperature. As shown in Fig. 10, the bonding strengths of the innermost and uppermost gluelines were approximately the same for the vacuum hot-pressed products, whereas the strength difference in these two gluelines were relatively larger for the conventional hot-pressed products. In the conventional hot-pressing process, the PF molecules were polymerized at about a temperature of 100°C for a long time. The polycondensation degree of CH2OH groups was not high. Therefore, there were possibly many small molecules, and the distribution of large molecules was uneven, resulting in poor uniformity in bonding strength. In contrast, under the vacuum hot-pressing process, CH2OH groups had a high degree of polycondensation, which could lead to more macromolecules with uniform distribution and good uniformity. This could be one of the reasons why the bonding strength of vacuum hot-pressed plywood panels was higher than that of conventional hot-pressed ones.
The curing behaviors of PF resin during vacuum hot pressing remain unclear. This study investigated the gel time and FTRP spectra of PF resin, the core temperatures and moisture of plywood mats during hot pressing, and the plywood bonding strength. Major conclusions can be addressed here:
1. It can be concluded that PF resin can be cured at a lower temperature under vacuum conditions. Within the investigated range of vacuum values, the lower the vacuum degree, the lower the gel temperature and the shorter gel time of PF resin.
2. Under the same vacuum degree, FTIR results determined that the absorption peak intensity of hydroxymethyl bond at 1016 cm−1 gradually decreased with the increase in temperature, and the polycondensation degree of hydroxymethyl increased with the increase in temperature degree. The higher the degree of vacuum, the slower the polycondensation reaction rate of PF resin at the same solidification temperature. In the curing process, hydroxymethyl and hydrogen substitution reaction on the benzene ring was ortho-preferred under vacuum conditions.
3. The bonding strength of vacuum hot-pressed plywood was higher than that of conventional hot-pressed plywood. The bonding strength in the innermost glueline and that in the uppermost glueline in hot-pressed plywood panels were 50% and up to 30% higher than their counterparts of conventional hot-pressed plywood ones, respectively.
4. It was demonstrated that the core in vacuum hot-pressed plywood mat had a faster heating rate and a higher final temperature than that of the conventional ones, which helped to cure PF resin reactively quickly and completely, which was beneficial to good bonding between veneer layers.
5. Adopting a vacuum during hot pressing provides a great possibility for shortening hot pressing time and improving both the quality and productivity of plywood products.
6. The research outcome of this study could provide a technical basis for introducing vacuum for hot pressing of wood composite products.
7. Future works can focus on systematically investigating the effects of vacuum hot-pressing parameters on the bonding strength and optimizing a new vacuum system for hot-pressing plywood products.
Acknowledgement: All authors contributed equally to this work.
Funding Statement: The authors received no specific funding for this study.
Conflicts of Interest: The authors declare that they have no conflicts of interest to report regarding the present study.
References
1. Lu, X., Pizzi, A. (1998). Interior MDI/pine tannin plywood adhesives without formaldehyde. Holz als Roh-und Werkstoff, 56(1), 78. https://doi.org/10.1007/s001070050267 [Google Scholar] [CrossRef]
2. Bekhta, P., Sedliačik, J., Jones, D. (2018). Effect of short-term thermomechanical densification of wood veneers on the properties of birch plywood. European Journal of Wood and Wood Products, 76(2), 549–562. https://doi.org/10.1007/s00107-017-1233-4 [Google Scholar] [CrossRef]
3. Bekhta, P., Salca, E. A. (2018). Influence of veneer densification on the shear strength and temperature behavior inside the plywood during hot press. Construction and Building Materials, 162(10), 20–26. https://doi.org/10.1016/j.conbuildmat.2017.11.161 [Google Scholar] [CrossRef]
4. Irle, M., Barbu, M. C., Niemz, P., Carvalho, L., Paul, W. et al. (2010). Wood-based panel technology: An introduction for specialists. London: Brunel University Press. [Google Scholar]
5. Hong, L., Shu, B., He, Q., Ju, Z., Zhang, H. et al. (2021). Improving the properties of fast-growing Chinese fir by vacuum hot pressing treatment. Journal of Renewable Materials, 9(1), 49–59. https://doi.org/10.32604/jrm.2021.013833 [Google Scholar] [CrossRef]
6. Hong, L., He, Q., Ju, Z., Zhang, H., Brosse, N. et al. (2020). Effect of vacuum hot pressing on the bonding quality and heat transfer performance of plywood. European Journal of Wood and Wood Products, 78(3), 441–447. https://doi.org/10.1007/s00107-020-01531-y [Google Scholar] [CrossRef]
7. Lange, J., Altmann, N., Kelly, C. T., Halley, P. J. (2020). Understanding vitrification during cure of epoxy resins using dynamic scanning calorimetry and rheological techniques. Polymer, 41(15), 5949–5955. https://doi.org/10.1016/S0032-3861(99)00758-2 [Google Scholar] [CrossRef]
8. Dorieh, A., Ayrilmis, N., Pour, M. F., Movahed, S. G., Kiamahalleh, M. V. et al. (2022). Phenol formaldehyde resin modified by cellulose and lignin nanomaterials: Review and recent progress. International Journal of Biological Macromolecules, 222(14), 1888–1907. https://doi.org/10.1016/j.ijbiomac.2022.09.279 [Google Scholar] [PubMed] [CrossRef]
9. Asim, M., Saba, N., Jawaid, M., Nasir, M., Pervaiz, M. et al. (2018). A review on phenolic resin and its composites. Current Analytical Chemistry, 14(3), 185–197. https://doi.org/10.2174/1573411013666171003154410 [Google Scholar] [CrossRef]
10. Çetin, N. S., Özmen, N. (2002). Use of organosolv lignin in phenol-formaldehyde resins for particleboard production: I. Organosolv lignin modified resins. International Journal of Adhesion and Adhesives, 22(6), 477–480. https://doi.org/10.1016/S0143-7496(02)00058-1 [Google Scholar] [CrossRef]
11. Younesi-Kordkheili, H. (2022). Maleated lignin coreaction with phenol-formaldehyde resins for improved wood adhesives performance. International Journal of Adhesion and Adhesives, 113, 103080. https://doi.org/10.1016/j.ijadhadh.2021.103080 [Google Scholar] [CrossRef]
12. Wang, J., Jiang, N., Guo, Q., Liu, L., Song, J. (2006). Study on the structural evolution of modified phenol-formaldehyde resin adhesive for the high-temperature bonding of graphite. Journal of Nuclear Materials, 348(1–2), 108–113. https://doi.org/10.1016/j.jnucmat.2005.09.008 [Google Scholar] [CrossRef]
13. Laiveniece, L., Morozovs, A. (2016). Impact of water on rheological behavior of polyurethane glues. Rural Sustainability Research, 35(330), 7–18. https://doi.org/10.1515/plua-2016-0002 [Google Scholar] [CrossRef]
14. Kim, S., Kim, H. S., Kim, H. J., Yang, H. (2008). Fast curing PF resin mixed with various resins and accelerators for building composite materials. Construction and Building Materials, 22(10), 2141–2146. https://doi.org/10.1016/j.conbuildmat.2007.07.007 [Google Scholar] [CrossRef]
15. Zhang, H., Wang, X., Li, Y. (2018). Measuring radiative properties of silica aerogel composite from FTIR transmittance test using KBr as diluents. Experimental Thermal and Fluid Science, 91, 144–154. https://doi.org/10.1016/j.expthermflusci.2017.10.010 [Google Scholar] [CrossRef]
16. Toscano, G., Maceratesi, V., Leoni, E., Stipa, P., Laudadio, E. et al. (2022). FTIR spectroscopy for determination of the raw materials used in wood pellet production. Fuel, 313(7), 123017. https://doi.org/10.1016/j.fuel.2021.123017 [Google Scholar] [CrossRef]
17. Sawicz-Kryniger, K., Niezgoda, P., Stalmach, P., Starzak, K., Wysocka, A. et al. (2022). Performance of FPT, FTIR and DSC methods in cure monitoring of epoxy resins. European Polymer Journal, 162(65), 110933. https://doi.org/10.1016/j.eurpolymj.2021.110933 [Google Scholar] [CrossRef]
18. Bouyanfif, A., Liyanage, S., Hequet, E., Moustaid-Moussa, N., Abidi, N. (2019). FTIR microspectroscopy reveals fatty acid-induced biochemical changes in C. elegans. Vibrational Spectroscopy, 102(2), 8–15. https://doi.org/10.1016/j.vibspec.2019.03.002 [Google Scholar] [CrossRef]
19. Ferreira, A. C., Diniz, M. F., Ferreira, A. C. B., Sanches, N. B., Mattos, E. D. C. (2020). FT-IR/UATR and FT-IR transmission quantitative analysis of PBT/PC blends. Polymer Testing, 85(1), 106447. https://doi.org/10.1016/j.polymertesting.2020.106447 [Google Scholar] [CrossRef]
20. Al-Lafi, A. G., AL-Naser, I. (2022). Application of 2D-COS-FTIR spectroscopic analysis to milk powder adulteration: Detection of melamine. Journal of Food Composition and Analysis, 113(8), 104720. https://doi.org/10.1016/j.jfca.2022.104720 [Google Scholar] [CrossRef]
21. Mijović, J., Kenny, J., Nicolais, L. (1993). Comparison of kinetic and rheological evaluation of gel time for an amine-epoxy system. Polymer, 34(1), 207–209. https://doi.org/10.1016/0032-3861(93)90307-V [Google Scholar] [CrossRef]
22. Hua, R. (1996). Application of viscoanalyser in analysis of epoxy resin curing course. Analysis and Testing Technology and Instruments, 2(4), 24–28. [Google Scholar]
23. Chatterjee, B. K., Roy, S. C. (2005). Viscosity divergence and gelation. Radiation Physics and Chemistry, 74(6), 419–425. https://doi.org/10.1016/j.radphyschem.2005.08.006 [Google Scholar] [CrossRef]
24. Kariz, M., Kuzman, M. K., Sernek, M. (2013). The effect of the heat treatment of spruce wood on the curing of melamine-urea-formaldehyde and polyurethane adhesives. Journal of Adhesion Science and Technology, 27(17), 1911–1920. https://doi.org/10.1080/01694243.2013.764809 [Google Scholar] [CrossRef]
25. Li, Y., Li, F., Yang, X., Guo, L., Huang, F. et al. (2018). Quantitative analysis of glycated albumin in serum based on ATR-FTIR spectrum combined with SiPLS and SVM. Spectrochimica Acta Part A: Molecular and Biomolecular Spectroscopy, 201, 249–257. https://doi.org/10.1016/j.saa.2018.05.022 [Google Scholar] [PubMed] [CrossRef]
26. Gil, M. L. A., Luna, M., Zarzuela, R., García-Moreno, M. V. (2020). Quantitative determination of the penetration of a silica-based consolidant in a limestone by FTIR spectroscopy. Vibrational Spectroscopy, 110, 103109. https://doi.org/10.1016/j.vibspec.2020.103109 [Google Scholar] [CrossRef]
27. Tejado, A., Peña, C., Labidi, J., Echeverria, J. M., Mondragon, I. (2007). Physico-chemical characterization of lignins from different sources for use in phenol-formaldehyde resin synthesis. Bioresource Technology, 98(8), 1655–1663. https://doi.org/10.1016/j.biortech.2006.05.042 [Google Scholar] [PubMed] [CrossRef]
28. Granado, L., Tavernier, R., Foyer, G., David, G., Sylvain, C. (2018). Comparative curing kinetics study of high char yield formaldehyde- and terephthalaldehyde-phenolic thermosets. Thermochimica Acta, 667, 42–49. https://doi.org/10.1016/j.tca.2018.06.013 [Google Scholar] [CrossRef]
29. Detlefsen, W. D. (2002). Phenolic resins: Some chemistry, technology, and history. Adhesion Science and Engineering, 2(2), 869–945. https://doi.org/10.1016/B978-044451140-9/50020-2 [Google Scholar] [CrossRef]
30. Pan, Y., Zhao, Y., Zhang, F. (2000). IR fingerprint spectrum and its analyze method. Modern Instruments, 1, 1–13. [Google Scholar]
31. Wu, Y., Huang, Z. (1981). Study of curing process of resole type phenol-formaldehyde resins by infra-red spectroscopy. Acta Polymerica Sinica, 6, 403–408. [Google Scholar]
32. Lu, X., Pizzi, A. (1998). Curing conditions effects on the characteristics of thermosetting adhesives-bonded wood joints—Part 1: Substrate influence on TTT and CHT curing diagrams of wood adhesives. Holz Roh-Werkst, 56(6), 401. https://doi.org/10.1007/PL00002611 [Google Scholar] [CrossRef]
Cite This Article
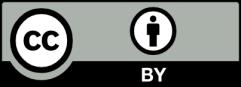
This work is licensed under a Creative Commons Attribution 4.0 International License , which permits unrestricted use, distribution, and reproduction in any medium, provided the original work is properly cited.