Open Access
ARTICLE
Effect of Fibre Size on Mechanical Properties and Surface Roughness of PLA Composites by Using Fused Deposition Modelling (FDM)
1
Fakulti Kejuruteraan Mekanikal, Universiti Teknikal Malaysia Melaka, Hang Tuah Jaya, Durian Tunggal, Melaka, 76100, Malaysia
2
Fakulti Teknologi Kejuruteraan Mekanikal dan Pembuatan, Universiti Teknikal Malaysia Melaka, Hang Tuah Jaya, Durian Tunggal,
Melaka, 76100, Malaysia
3
Centre for Advanced Research on Energy, Universiti Teknikal Malaysia Melaka, Hang Tuah Jaya, Durian Tunggal, Melaka, 76100,
Malaysia
* Corresponding Author: Nadlene Razali. Email:
(This article belongs to the Special Issue: Bio-Fibres, Biopolymers and Biocomposites – Design for Sustainability, Life Cycle Analysis, Concurrent Materials and Conceptual Design Selection)
Journal of Renewable Materials 2023, 11(8), 3261-3276. https://doi.org/10.32604/jrm.2023.028280
Received 09 November 2022; Accepted 20 December 2022; Issue published 26 June 2023
Abstract
Natural fibre as a reinforcing agent has been widely used in many industrial applications. Nevertheless, several factors need to be considered, such as the size and weight percentage of the fibre used in binding. Using fused deposition modelling (FDM), this factor was investigated by varying the size of natural fibre as the responding variable with a fixed weight percentage of kenaf fibre. The process of modifying the natural fibre in terms of size might increase the dispersion of kenaf fibre in the polymer matrix and increase the adhesion bonding between the fibre and matrix of composites, subsequently improving the interfacial bonding between these two phases. In this paper, the effect of fibre size was evaluated by performing the mechanical test, Scanning Electron Micrograph (SEM) to observe the morphology of the composites, and also by surface analysis. The surface roughness was visualised using a 3D profilometer and the figure was illustrated as colour shading in the image. The composite with fibre size ≤100 μm displayed better tensile and flexural strength, compared to other sizes. In conclusion, by reducing the size of the fibre, the composites could develop high strength performance for industrial applications.Keywords
The combination of cellulose fibre and polymer matrix has attracted many researchers to develop new techniques to produce effective composite materials. Natural fibre has been explored to replace synthetic fibre as the filler in the composite’s platform [1]. A composite is a material that is made up of two or more different types of materials that are mixed and have varied qualities. Polymers are frequently used in construction as primary materials because of their high strength and quick setting characteristics [2].
The natural fibre is known for its strength and is one of the best replacements for synthetic fibre and artificial fibre in manufacturing because it is lightweight, biodegradable, and safe [3]. Table 1 summarizes characteristic values for the density and mechanical properties, of natural (plant), synthetic fibres and glass fibres.
The natural fibre is safer than synthetic fibre, and its unique properties, such as low density, low cost, low energy consumption, biodegradability, high specific strength, and high vibration absorption, caused many academics to express an interest in learning more about it as a filler [4]. The concern towards the environment urges industries to produce “green materials” as their main filler. While natural fibre is biodegradable, renewable, nontoxic, sustainable, and environment friendly [5]; its drawbacks, are such as excessive moisture absorption, low processing temperature, low durability, and incompatibility between fibre and polymer matrix [6]. Some of the commonly available natural fibres are kenaf, pineapple leaf fibre (PALF), coir, hemp, wood, jute and sisal.
To resolve the incompatibility problem between fibre and polymer matrix, Jamadi et al. [3] stated that surface modification by alkaline treatment can enhance the bonding between these two phases. Subsequently, to obtain an accurate result in mechanical strength, the right amount of immersion time and concentration need to be studied. The surface modification is a step to remove any impurities such as wax or oil and enhance the surface roughness of the fibre surface. In addition, this paper observed that the wettability problem could be resolved by using silane as a coupling agent. This approach can improve the natural fibre and polymer matrix’s interlocking adherence [7].
It was noted that increasing the alkaline concentration can damage the natural fibres, resulting in decreased mechanical and physical properties. In conclusion, alkaline treatment is the most effective treatment compared to others because an alkaline solution can stand for a long period and has a lasting effect on the mechanical behaviour of the natural fibres, especially on their strength and stiffness and surface treatment can be improved the properties of the composites itself [8–13]. The optimum concentration for alkaline treatment is 6 wt%, consistent with the literature review shown in Table 2. The hydrophilic properties of the kenaf fibre can be reduced and enhance the interfacial bonding between fibre and polymer itself.
Natural fibre reinforced composite has been used in several industries such as automotive, aerospace, and sports to substitute glass and carbon as their main reinforcement agent. The natural fibre is also used as a reinforced polymer composite in gears, bearings, clutches, and many other mechanical components due to its excellent mechanical qualities.
Aida et al. [6] listed several factors that might affect the effectiveness of the composites such as: (a) the variety of fibre size, (b) aspect ratio size, (c) particle size and shape, (d) particle surface area, (e) fibre orientation, (f) volume of fibre, and (g) chemical composition. Their study found increasing fibre size produces higher tensile strength and elasticity of composites. Additionally, increasing the fibre content could improve the composites’ strength and stiffness. The aspect ratio size shows that an increase in fibre content increases tensile modulus but decreases tensile and flexural strength. They concluded increasing the fibre content with poor dispersion would reduce composite strength, and increasing the fibre length would increase composite strength and elasticity but diminish toughness and strain [14–17].
Zhang et al. [18] investigated that fibre length and dispersion would give some effect towards a good result. In conclusion, the data indicated that as the glass fibre length increased, the strength also increased due to a good dispersion within the polymer matrix. The previous study also showed that if the fibres were not well distributed, it could lead to low mechanical properties.
Cuvalvi et al. conducted a test that observed the effect of the fibre volume ratio. The data showed an inclination of tensile strength as the fibre content to volume ratio increased at a certain point but showed a declination if the content/volume ratio constantly increased [19]. This can be concluded that the fibre content might affect the composites if the fibre volume was low due to the low distribution of fibre and the force that transferred towards the composites might not contribute well. However, if the fibre volume was higher, it might also affect the properties due to the bonding between the matrix and fibre was not properly embedded. Therefore, the optimum volume ratio needs to be further studied in order to obtain a good result [19].
Additive manufacturing (AM), such as fused deposition modelling (FDM), is one of the technologies that can reduce cost while producing goods with geometrical and complicated features. This method requires a layer-by-layer process by using 3D printing fed through CAD file generation. FDM as shown in Fig. 1 has become increasingly popular in industrial applications such as biomedical, mechanical, and electrical manufacturing in recent years [16,20–22].
Figure 1: FDM process diagram [7]
The goal of this study is to evaluate how the diameters of natural fibres affect the mechanical characteristics and surface roughness of kenaf fiber reinforced PLA composites. Four different sizes (≤100, 100, 250 and 300 μm) were investigated. Whilst the study focuses on both performance and quality, the printed surfaces were also examined utilizing 2D and 3D image analyzers.
Kenaf fibre powder (unsieved) was supplied locally from Lembaga Kenaf dan Tembakau Negara (LKTN). Poly Lactic Acid (PLA) pellets and Silane (Aminopropyltriethoxysilane Agent) were obtained from Mecha Solve Engineering (Selangor, Malaysia).
In this experiment, kenaf fibre powder with random size (unsieved) within 100–650 µm was treated with alkaline treatment. The kenaf fibres were immersed in sodium hydroxide solution with a fixed concentration of 6 wt% for 24 h [23]. After alkaline treatment, the kenaf fibres were washed thoroughly with running water and dried in an oven at a temperature of 110°C for 24 h. Fig. 2 shows the rinsed fibre after alkaline treatment.
Figure 2: Alkaline treatment
The surface is then treated with the silane coupling agent method. In this treatment, 1.0 wt% APS (aminopropyltriethoxy silane) was dissolved in a solution containing 70% methanol and 30% water. After that, the solution was stirred for 30 min. The kenaf fibre that had already undergone the alkaline treatment was then soaked in silane solution for 3 h before being dried in an oven at 110°C for 24 h to remove all moisture from the fibre. Table 3 details the chemical treatment used in this experiment, while Fig. 3 shows fibre in silane treatment and Fig. 4 depicts the drying process in the oven.
Figure 3: Silane treatment
Figure 4: Drying process
Composites were created by combining kenaf fibre and matrix using the law of mixture. The weight of each element was calculated by using Eq. (1) as shown in Table 4. Han et al. discovered that 2.5 wt% fibre in PLA was optimal for FDM [24].
Weight percentage of element,we×Weight of composites=Weight of elements (1)
Sieve analysis was one of the methods used to ascertain the particle size of the kenaf fibre powder distribution. By pouring kenaf fibre powder through a wire mesh sieve, specific size ranges were then determined using the sieve analysis method. The required weight of kenaf fibre powder was obtained using this method, which involved using a sieve stack that was placed on a sieve shaker for 30 min. The vibration used made it easier for the fibre particles to reorient themselves as they passed through the sieve. On the other hand, the sieve also aided in breaking up the fibre’s tendency to clump together, enabling better distribution. By doing this, the kenaf fibre powder that passed through the sieve was deemed to be within the wire mesh sieve’s specification range. The four different sizes under investigation were ≤100, 100, 250, and 300 μm.
Twin screw extruders with constant pulling speed and constant filament size have been utilized to make filament composites for various fibre sizes. Fig. 5 depicts the twin screw extruder and the extrusion parameter is shown in Table 5.
Figure 5: Twin screw extruder
The Flashforge 3D printer was used to extrude the sample. The solid has been put up with a 100% infill in a line shape. Following that, the nozzle temperature was set at 210°C, and the bed temperature was set at 60°C, as PLA polymer did not require high temperatures. The nozzle size that had been used to print the composites’ samples is 0.8 mm (0.031 in). Fig. 6 represents the schematic diagram of the 3D printer and Fig. 7 shows the printed tensile test coupons.
Figure 6: Schematic 3D printer
Figure 7: Tensile test specimens
To evaluate the mechanical properties of the biodegradable composites, the tensile test was applied. Some of the properties that can be obtained after performing the tensile test include young’s modulus and tensile strength. The testing was carried out by following the ASTM D638 standard and five samples have been taken for each fibre size to find the average results. The tensile properties of composites were determined using the Universal Testing Machine model Instron 887, manufactured in Norwood, Massachusetts, United States.
The flexural test was conducted according to the ASTM D790 standard and five samples have been taken for each parameter to find the results average. The crosshead speed is 1 mm/min with a load cell of 5 kN tested using the Universal Testing Machine model Instron 5585 manufactured in Norwood, Massachusetts, United States. The sample size is 100 mm × 10 mm × 3 mm with a span length of 80 mm.
Eq. (2) can be used to determine flexural stress.
σ=3PL2bd2 (2)
where, σ is the flexural strength , P is the maximum force at break (N), L is the support span (mm), b is the width of the sample (mm), and d is the depth of the sample (mm).
Morphological tests were carried out on the cracked surface tensile test sample and a scanning electron microscope (SEM) for the four separate samples with diameters of ≤100, 100, 250, and 300 μm. Platinum coating was used to improve the resolution. JSM-6010PLUS/LV Scanning Electron Microscope made by Jeol Ltd., Tokyo, Japan.
The surface structure detail was obtained by using the Low Power Microscope, Zeiss Axioskop 2 with 50x lens which was manufactured in Germany.
3.4 Profilometer Surface Roughness
A 3D Profilometer was performed to obtain the surface roughness of the composites’ surface. The 3D surface roughness was observed by using Shodensha GR3400 with a 50x lens.
Mechanical testing was used to investigate the tensile and flexural strength of the materials, as well as the elastic modulus. Interfacial bonding is one of the factors that might influence the strength of composites. Good results could be obtained with good stress distribution [18]. The results could reveal whether the sample has good or poor interfacial bonding. The tensile test can be used to determine the elastic modulus, maximum tensile strength, and strain to failure [23]. By adding fibre and improving fibre quality, the contact area between the two phases also can be enhanced. As the ideal amount of fibre is reached, the ductility of the composites will increase, but if the amount of fibre is greater, both the ductility and the strength of the composites may decrease.
Fig. 8 shows the tensile stress and tensile modulus for the fibre composites of various sizes and a constant weight percentage of 2.5 wt%. The tensile stress for ≤100, 100, 250 and 300 μm showed values of 45.48, 43.35, 39.89 and 38.63 MPa, respectively and concluded that ≤100 μm fibre size indicated good strength compared to the other fibre size composites. The lowest size of fibre also showed the highest elasticity (1.10 GPa). It can be observed that the tensile modulus is proportioned to tensile strength. These results confirm that a smaller size of fibre gives good fibre dispersion and distribution in the polymer matrix which increases the mechanical properties. Yeh et al. [25] stated that the fibre aspect ratio would give a great impact on the mechanical properties. The 300 μm size showed the lowest tensile values. Since the fibre used in this experiment are in a powder state, or isotropic, there is no need for it to have a specific orientation.
Figure 8: Kenaf reinforced PLA composites tensile properties at varying fibre size
The flexural strength for samples ≤100, 100, 250 and 300 μm, are 64.53, 63.67, 59.71, and 49.02 MPa, respectively. Fig. 9 shows samples with a size of ≤100 μm obtained the highest flexural strength, whereas the highest flexural elasticity was produced from the sample size of 100 μm (1.85 GPa). However, 300 μm achieved the lowest strength as compared to other fibre sizes. The flexural modulus in general indicated an increasing trend as the strength increased. The lowest fibre size obtained the highest strength due to its ability to distribute and disperse well into the polymer matrix as compared to the larger sizes. For this reason, when the load was applied, the force could be well distributed in the composites.
Figure 9: Kenaf reinforced PLA composites’ flexural properties at varying fibre size
From the tensile and flexural strength results, it can be concluded that a smaller fibre size is better than a larger fibre size. A smaller size has a higher surface area to increase the bonding between the two phases and can distribute well without agglomeration thus increasing the inner strength of the composites [22]. The trend of strength that gradually decreases as the size of the fibre is increasing might be due to voids or impurities of the fibre itself.
To analyze the micrograph of the composites, the cracked surfaces from the tensile test were viewed under SEM. Fig. 10 depicts the shattered surfaces of composites. Fig. 10a shows the tensile fractured surface of a ≤100 μm fibre. Fibre pull-out was noticed in the micrograph, proving that the fibres were properly blended and distributed in the polymer matrix. Additionally, some fibre was still present, showing that the matrix and fibre had a strong interfacial connection. This suggested that effective surface treatment would increase the composite’s strength. The micrograph showed good tensile strength results, showing that among the fibre sizes ≤100 μm was the best.
Figure 10: Scanning Electron micrograph (a) ≤100 μm; (b) 100 μm; (c) 250 μm; (d) 300 μm
Fig. 10b shows the tensile fracture surface for 100 μm size. It could be seen that there were some voids and cracks on the surface, larger fibre pull-out, and the distribution of fibre was slightly less as compared to Fig. 10a. The tensile fracture surface of 250 μm fibre size in Fig. 10c shows bigger fibre holes and fibre gaps between the fibre and matrix, whereas Fig. 10d illustrates the tensile fracture surface of 300 μm fibre size with larger fibre holes, cracks, and fibre distribution on the polymer. In conclusion, a larger fibre size had minimal interaction as a crack barrier in comparison to a smaller size. 300 μm fibre size contained plenty of fibre pull-out in contrast to the smaller fibre size.
The printed surface of kenaf fibre composites was investigated by using a Low Power Microscope, Zeiss Axioskop 2 using a 50x magnifying lens. The samples were taken with the same printing parameter with different sizes of kenaf fibre as shown in Fig. 11. According to the 2D image analyzer, the ≤100 μm size in Fig. 11a had the smoothest printed surface when compared to other fibre sizes.
Figure 11: Image analyzer for printed surface (a) ≤100 μm; (b) 100 μm; (c) 250 μm; (d) 300 μm
Ra is the average value of surface roughness obtained while Rz is the highest peak. The average value was taken at five different points per sample using the 3D profilometer. The surface illustration is shown in Fig. 12. The numerical results of surface roughness are tabulated in Table 4, the surface roughness trend changes according to the fibre size.
Figure 12: Kenaf reinforced PLA composites 3D profilometer at varying fibre size
Campbell et al. [26] and Reddy et al. [27] concluded it is difficult to capture surface roughness since the layer thickness of the printed surface could affect the reading and further study is needed in this method. In a nutshell, it can be concluded that in the current study, a smaller fibre size could produce a better surface finish as compared to larger fibre sizes since the only different parameter in the samples is the fibre size [28] and fibre size also improve the mechanical properties as mentioned above [29,30]. Figs. 13 and 14 show that the highest surface roughness and tallest peaks on the surface by referring to Table 6, were obtained for the fibre size of 300 μm.
Figure 13: Mean value of surface roughness, Ra varying fibre size
Figure 14: Peak point on the surface, Rz varying fibre size
The study was carried out by combining kenaf fibre with thermoplastic PLA and observing the mechanical properties of the composites. Four different sizes of fibres were studied (≤100, 100, 250 and 300 μm). According to the findings ≤100 μm size achieved the highest strength when compared to other fibre sizes. Because the stress could be distributed evenly on the surface, the tensile and flexural strength could be enhanced due to strong interfacial bonding as the composition of composites achieved the optimum concentration and fibre size. This experiment also demonstrated that increasing the size of a filler can affect internal strength. It can be concluded that fibre size influences mechanical properties. Therefore, the optimum tensile and flexural strengths were obtained at a fibre size of ≤100 μm. The surface profilometer analysis proved that the smaller size could help in a better surface finish. The correct size of the filler for natural fibre is one of the important factors to consider since it efficiently provides sufficient bonding to achieve a high internal strength for application development.
Acknowledgement: The author would like to thank Universiti Teknikal Malaysia, Melaka, for facilities for this research and the Ministry of Education Malaysia for funding this research.
Funding Statement: The result was obtained through the financial support of the Ministry of Education Malaysia under Grant Number RACER/2019/FKM-CARE/F00408. This paper’s publication also funded by UTeM Incentive Jurnal Q00049/JURNAL/2020/FKM.
Conflicts of Interest: The authors declare that they have no conflicts of interest to report regarding the present study.
References
1. Sood, M., Dwivedi, G. (2018). Effect of fiber treatment on flexural properties of natural fiber reinforced composites: A review. Egyptian Journal of Petroleum, 27(4), 775–783. https://doi.org/10.1016/j.ejpe.2017.11.005 [Google Scholar] [CrossRef]
2. Elkazaz, E., Crosby, W. A., Ollick, A. M., Elhadary, M. (2020). Effect of fiber volume fraction on the mechanical properties of randomly oriented glass fiber reinforced polyurethane elastomer with crosshead speeds. Alexandria Engineering Journal, 59(1), 209–216. https://doi.org/10.1016/j.aej.2019.12.024 [Google Scholar] [CrossRef]
3. Jamadi, A. H., Nadlene, R., Petrů, M., Mastura, M. T., Muhammad, N. et al. (2021). Effect of chemically treated kenaf fibre on mechanical and thermal properties of PLA composites prepared through fused deposition modeling (FDM). Polymers, 13(19), 3299. https://doi.org/10.3390/polym13193299 [Google Scholar] [PubMed] [CrossRef]
4. Singh, H., Singh, T. (2019). Effect of fillers of various sizes on mechanical characterization of natural fiber polymer hybrid composites: A review. Materials Today: Proceedings, 18(7), 5345–5350. [Google Scholar]
5. Mohamed, W. Z. W., Baharum, A., Ahmad, I., Zakaria, N. E. (2018). Effects of fiber size and fiber loading on mechanical properties and morphology of thermoplastic mengkuang reinforced natural rubber and high density polyethylene composites. BioResources, 13(2), 2945–2959. [Google Scholar]
6. Aida, H. J., Nadlene, R., Mastura, M. T., Yusriah, L., Sivakumar, D. et al. (2021). Natural fibre filament for Fused Deposition Modelling (FDMA review. International Journal of Sustainable Engineering, 14(6), 1988–2008. https://doi.org/10.1080/19397038.2021.1962426 [Google Scholar] [CrossRef]
7. Farhan, M., Siddiqui, M. A. (2018). Raw natural fiber reinforced polystyrene composites: Effect of fiber size and loading. Materials Today: Proceedings, 5(2), 5908–5917. [Google Scholar]
8. Mohamed, S. A. N., Zainudin, E. S., Sapuan, S. M., Azaman, M. D., Arifin, A. M. T. (2018). Introduction to natural fiber reinforced vinyl ester and vinyl polymer composites. In: Natural fibre reinforced vinyl ester and vinyl polymer composites, pp. 1–25. Cambridge, United Kingdom: Woodhead Publishing. https://doi.org/10.1016/B978-0-08-102160-6.00001-9 [Google Scholar] [CrossRef]
9. Fiore, V., Di Bella, G., Valenza, A. (2015). The effect of alkaline treatment on mechanical properties of kenaf fibers and their epoxy composites. Composites Part B: Engineering, 68, 14–21. [Google Scholar]
10. Oushabi, A., Sair, S., Oudrhiri Hassani, F. O., Abboud, Y., Tanane, O. et al. (2017). The effect of alkali treatment on mechanical, morphological and thermal properties of date palm fibers (DPFsStudy of the interface of DPF-Polyurethane composite. South African Journal of Chemical Engineering, 23(3), 116–123. https://doi.org/10.1016/j.sajce.2017.04.005 [Google Scholar] [CrossRef]
11. Mahjoub, R., Yatim, J. M., Sam, A. R. M., Hashemi, S. H. (2014). Tensile properties of kenaf fiber due to various conditions of chemical fiber surface modifications. Constructions and Building Materials, 55(4), 103–113. https://doi.org/10.1016/j.conbuildmat.2014.01.036 [Google Scholar] [CrossRef]
12. Edeerozey, A. M. M., Akil, H., Azhar, A. B., Ariffin, M. I. Z. (2007). Chemical modification of kenaf fibers. Materials Letter, 61(10), 2023–2025. https://doi.org/10.1016/j.matlet.2006.08.006 [Google Scholar] [CrossRef]
13. Sreenivasan, V. S., Ravindran, D., Manikandan, V., Narayanasamy, R. (2012). Influence of fibre treatments on mechanical properties of short Sansevieria cylindrica/polyester composites. Material and Design, 37(16), 111–121. https://doi.org/10.1016/j.matdes.2012.01.004 [Google Scholar] [CrossRef]
14. Rahim, T. N. A. T., Abdullah, A. M., Akil, H. M. (2019). Recent developments in fused deposition modeling-based 3D printing of polymers and their composites. Polymer Reviews, 59(4), 589–624. https://doi.org/10.1080/15583724.2019.1597883 [Google Scholar] [CrossRef]
15. Natarajan, S. M., Senthil, S., Narayanasamy, P. (2022). Investigation of mechanical properties of FDM-processed acacia concinna-filled polylactic acid filament. International Journal Polymer Science, 2022, 1–8. [Google Scholar]
16. Mastura, M. T., Nadlene, R., Jumaidin, R., Kudus, S. I. A., Mansor, M. R. et al. (2022). Concurrent material selection of natural fibre filament for fused deposition modeling using integration of analytic hierarchy process/analytic network process. Journal Renewable Material, 10(5), 1221–1238. https://doi.org/10.32604/jrm.2022.018082 [Google Scholar] [CrossRef]
17. Rafiee, M., Abidnejad, R., Ranta, A., Ojha, K., Karakoç, A. et al. (2021). Exploring the possibilities of FDM filaments comprising natural fiber-reinforced biocomposites for additive manufacturing. AIMS Material Science, 8(4), 524–537. https://doi.org/10.3934/matersci.2021032 [Google Scholar] [CrossRef]
18. Zhang, D., He, M., Yu, J. (2017). Effect of fiber length and dispersion on properties of long glass fi ber reinforced thermoplastic composites based on poly(butylene terephthalate). RCS Advances, 7, 15439–15454. https://doi.org/10.1039/C7RA00686A [Google Scholar] [CrossRef]
19. Çuvalci, H., Erbay, K., İpek, H. (2014). Investigation of the effect of glass fiber content on the mechanical properties of cast polyamide. Arabian Journal for Science and Engineering, 39(12), 9049–9056. https://doi.org/10.1007/s13369-014-1409-8 [Google Scholar] [CrossRef]
20. Yusof, N. S. B., Sapuan, S. M., Sultan, M. T. H., Jawaid, M. (2020). Manufacturing process selection of ‘green’ oil palm natural fiber reinforced polyurethane composites using hybrid TEA criteria requirement and AHP method for automotive crash box. Journal of Renewable Materials, 8(6), 647–660. https://doi.org/10.32604/jrm.2020.08309 [Google Scholar] [CrossRef]
21. Bi, X., Huang, R. (2022). 3D printing of natural fiber and composites: A state-of-the-art review. Materials and Design, 222, 111065. [Google Scholar]
22. Ismail, K. I., Yap, T. C., Ahmed, R. (2022). 3D-printed fiber-reinforced polymer composites by fused deposition modelling (FDMFiber length and fiber implementation techniques. Polymers, 14(21), 4659. https://doi.org/10.3390/polym14214659 [Google Scholar] [PubMed] [CrossRef]
23. Shirazi, M. G., Rashid, A. S. A., Nazir, R. B., Rashid, A. H. A., Kassim, A. et al. (2019). Investigation of tensile strength on alkaline treated and untreated kenaf geotextile under dry and wet conditions. Geotextiles and Geomembranes, 47(4), 522–529. https://doi.org/10.1016/j.geotexmem.2019.01.016 [Google Scholar] [CrossRef]
24. Han, S. N. M. F., Mastura, M. T., Mansor, M. R. (2019). Thermal and melt flow behaviour of kenaf fibre reinforced acrylonitrile butadiene styrene composites for fused filament fabrication. Defence S&T Technical Bulletin, 12(2), 238–246. [Google Scholar]
25. Yeh, S., Hu, C., Bangun, M., Kuo, C. (2021). Effect of fiber size, cyclic moisture absorption and fungal decay on the durability of natural fiber composites. Constructions and Building Materials, 286(12), 122819. https://doi.org/10.1016/j.conbuildmat.2021.122819 [Google Scholar] [CrossRef]
26. Campbell, R. I., Martorelli, M., Lee, H. S. (2002). Surface roughness visualisation for rapid prototyping models. Computer-Aided Design, 34(10), 717–725. https://doi.org/10.1016/S0010-4485(01)00201-9 [Google Scholar] [CrossRef]
27. Reddy, V., Flys, O., Chaparala, A., Berrimi, C. E., Amogh, V. et al. (2018). Capacity optimization between used capacity and operational efficiency study on surface texture of fused deposition modeling study on surface texture of fused deposition modeling. Procedia Manufacturing, 25(3), 389–396. https://doi.org/10.1016/j.promfg.2018.06.108 [Google Scholar] [CrossRef]
28. Pérez, M., Medina-Sánchez, G., García-Collado, A., Gupta, M., Carou, D. (2018). Surface quality enhancement of fused deposition modeling (FDM) printed samples based on the selection of critical printing parameters. Materials, 11(8), 1382. https://doi.org/10.3390/ma11081382 [Google Scholar] [PubMed] [CrossRef]
29. Hassine, B., Ahmed, K., Patrick, P., Alain, C. (2009). Effects of fiber characteristics on the physical and mechanical properties of wood plastic composites. Composites Part A: Applied Science and Manufacturing, 40(12), 1975–1981. https://doi.org/10.1016/j.compositesa.2009.06.003 [Google Scholar] [CrossRef]
30. Singha, A. S., Rana, R. K. (2012). Natural fiber reinforced polystyrene composites: Effect of fiber loading, fiber dimensions and surface modification on mechanical properties. Materials and Design, 41(16), 289–297. https://doi.org/10.1016/j.matdes.2012.05.001 [Google Scholar] [CrossRef]
Cite This Article
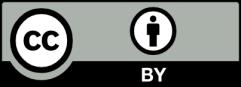
This work is licensed under a Creative Commons Attribution 4.0 International License , which permits unrestricted use, distribution, and reproduction in any medium, provided the original work is properly cited.