Open Access
ARTICLE
Study on the Preparation Process Optimization of Plywood Based on a Full Biomass Tannin-Sucrose Wood Adhesive
College of Forestry, Guizhou University, Guiyang, 550025, China
* Corresponding Authors: Min Tang. Email: ; Feiyan Gong. Email:
Journal of Renewable Materials 2023, 11(8), 3245-3259. https://doi.org/10.32604/jrm.2023.027461
Received 31 October 2022; Accepted 28 November 2022; Issue published 26 June 2023
Abstract
Biomass adhesive is conducive to decreasing the dependence of the wood adhesive industry on synthetic resin based on fossil resources and improving the market competitiveness of adhesives. It is also a critical breakthrough to realize the goal of carbon peaking and carbon neutrality in the wood industry. In this study, a full biomass wood adhesive composed of tannin and sucrose was developed and applied successfully to the preparation of plywood. The preparation technique of plywood was optimized, and the chemical structure, curing performance, crystallization property and thermal performance of the adhesive were investigated. Results showed that: (1) hot-pressing temperature played a decisive role in the performances of tannin-sucrose composite adhesives and it also had a very significant influence on the water resistance of plywood. (2) The preparation of tannin-sucrose composite adhesive was a process in which sucrose was transformed into furan aldehydes and then made cross-linking reaction with tannin. These composite adhesives could only get good bonding performances when the curing temperature was above 210°C. (3) The optimal plywood preparation technique was: hot-pressing temperature of 220°C, hot-pressing time of 1.2 min/mm, m(tannin):m(sucrose) of 60:40, and adhesive loading of 160 g/m2. The wet bonding strength in boiling water of the prepared plywood was 0.83 MPa, meeting the strength requirements of Type-I plywood in the standard of GB/T 17657-2013. (4) The curing temperature of tannin-sucrose composite adhesive was further decreased by lowering the temperature during the transformation of sucrose into 5-HMF, which was a key in subsequent research.Keywords
The production process of wood products consumes less energy and has a low carbon emission level. Compared with traditional building materials such as steel, glass and cement, wood products have obvious advantages in energy saving and carbon reduction [1–4]. The CO2 emissions per 1 t production of cement, steel and glass are about 1220, 6470 and 1870 kg, respectively, but the CO2 emissions per 1 m³ of wood processing are only 30.3 kg [5,6]. With progress in reform and normalization of supervision over environmental protection in recent years, China’s wood industry is undergoing a critical stage of transformation and updating. The low-end background production capacity exits the market gradually and the industrial structure continues to develop toward low carbonization [7,8]. Under the goal of carbon peaking and carbon neutrality, China’s wood industry will surely accelerate green low-carbonization technological reform, transformation and updating.
Wood adhesive is the key material of the wood industry. Most adhesives produced around the world are used in the wood industry and the consumption of wood adhesives has become an important symbol to measure the national technological development level of the wood industry [9–11]. At present, formaldehyde-based adhesives still take the dominant role in the wood industry. It may release formaldehyde during the preparation and use of formaldehyde-based adhesives as well as the processing and use of wood-based panels prepared by formaldehyde-based adhesives, thus threatening environmental and human health [12–14]. With the continuously rising price of petrochemical products and strengthening public consciousness of environmental protection, the development and application of bio-based wood adhesives have attracted more and more attention. Relevant studies have reported tannin-based adhesives [15–17], soybean protein-based adhesives [18–20], starch-based adhesives [21,22], lignin-based adhesives [23–25], and so on. Among them, tannin-based adhesives are studied and used the most successfully, and they have been applied to industrial production successfully in some countries.
Tannin has a polyphenol structure which is similar to the structure of phenol. So, tannin can replace phenol in phenol-formaldehyde resin partially or wholly, and then react with formaldehyde. The tannin-based adhesive is another critical application field of tannin except for the leather industry, and it even has been used successfully for industrial production in South African countries rich in tannin resources. Common tannin-based adhesives can be prepared in a simple method and it only requires adding formaldehyde before hot-pressing. However, the prepared tannin-based adhesives have a low cross-linking degree, low bonding strength, poor water resistance, and so on. This is mainly because tannin has a low degree of polycondensation with formaldehyde due to its high molecular weight, but the system viscosity increases and the liquidity decline significantly. To solve these problems, many scholars replaced the short molecular-chain formaldehyde with the long molecular-chain bond bridge extender. Phenol-formaldehyde resin, urea-formaldehyde resin, melamine-formaldehyde resin and hydroxymethyl phenol are widely studied [26–30]. However, such cross-linking agents used toxic and volatile formaldehyde, thus decreasing the advantages of tannin-based adhesives in environmental protection. Hence, the environmental protection performance of the bond bridge extender is critical to prepare environmental-friendly tannin-based adhesives. Associated studies mainly focus on epoxy resin, polyamides, isocyanate, polyurethane, and so on [31–35]. Thus, the cured tannin-based adhesives are more compact and tighter, and their bonding performances and water resistance are improved significantly. But these modifiers are still the bases of petrochemical products and the large-scale introduction of these modifiers is also against the initial R&D intention of tannin-based adhesives. They are still not absolute full biomass tannin-based adhesives.
Zhao et al. reported a tannin-sucrose adhesive used to prepare particleboard [36–38]. According to Zhao’s results, one of the essential processes for biomass transformation and utilization of sucrose lay in sucrose-catalyzed conversion and synthesis of furan aldehydes like hydroxymethyl furfurals. Accordingly, it was thought that the successful preparation of tannin-sucrose adhesives derived from the reaction between tannin and hydroxymethyl furfurals (Fig. 1). Although Zhao’s study fully indicated that tannin-sucrose adhesives could successfully prepare particleboard, plywood and particleboard were not totally the same in terms of requirements for adhesives, including molecular weight, polycondensation degree, crosslinking density, adhesive loading, and so on. This paper mainly explores the feasibility of preparing plywood with tannin-sucrose composite adhesive and the preparation technology. Influences of factors on bonding performances of plywood prepared by tannin-sucrose composite adhesives were investigated. Moreover, the appropriate preparation technique of plywood was determined, aiming to lay foundations for the R&D of fully biomass-based wood adhesives.
Figure 1: The possible reaction scheme between sucrose and tannin
Waxberry tannin (160 mesh, industrial grade) was purchased from Guangxi Wuming Tannin Extract Factory (China). Sucrose (purity of 99.0%, analytically pure) was from Chengdu Jinshan Chemical Reagent Co., Ltd., China. Sodium dodecyl benzene sulfonate (purity of >90.0%, analytically pure) was from Tianjin Fengchuan Chemical Reagent Science and Technology, Ltd., China. Distilled water was prepared in the laboratory. Poplar veneer with a moisture content of 8%~10% and a size of 400 mm (length) × 400 mm (width) × 1.5 mm (thickness), was brought from Shuyang, Jiangsu Province, China.
2.2 Preparation of Tannin-Saccharose Composite Adhesives as Well as Preparation and Bonding Strength Test of Plywood
Under room temperature, distilled water, tannin and sucrose were added into a round-bottomed three-mouth flask which was equipped with a mechanical stirring rod, thermometer and condenser pipe. They were stirred to a slurry, to which 0.3 g sodium dodecyl benzene sulfonate was added and stirred for another 5 min. Solid contents, viscosity and pH of adhesives were tested in accordance with the standard of GB/T 14074-2017 (Table 1). Three-layer Poplar plywood with a breadth of 400 mm × 400 mm was prepared in the laboratory. Hot-pressing temperature, hot-pressing time, adhesive loading, and m(tannin):m(sucrose) were chosen as four factors in the test and the bonding strength in boiling water was used as the assessment index. On this basis, the experiment was designed according to the orthogonal table L16 (44) (Table 2). The prepared plywood was cut into 100 mm × 25 mm specimens and the bonding strength in boiling water was tested according to test methods for I-class plywood in the national standard of GB/T 17657-2013. The average strength of 8–10 specimens was used as the final value.
2.3 Property Characterization of Tannin-Sucrose Composite Adhesives
The tannin-sucrose composite adhesives were put in a piece of tin foil paper which was then dried absolutely in a constant-temperature ventilation oven (60°C~70°C). The adhesives were taken out and then put into a pulverizer for grinding, and then filtered by a 200-mesh sieve, thus getting adhesive powder (to test the curing performance of tannin-sucrose composite adhesives). The above adhesive powder was collected and dried in a constant-temperature (200°C, 210°C, 220°C and 230°C) ventilation oven for 12 min. Later, the powder was taken out (to test the chemical structure, crystallization properties and thermal performance of tannin-sucrose composite adhesives).
The DSC 204 F1 differential scanning calorimetry (NETZSCH, Germany) was applied to test the curing performance of tannin-sucrose composite adhesives under the conditions of N2 protection, temperature 30°C~400°C, and temperature rising rate of 10 °C/min. The Varian 1000 (USA) infrared spectrometer was used to test the chemical structure of tannin-sucrose composite adhesives under the conditions of wave number of 400~4000 cm−1, resolution of 4 cm−1, scanning number of 32, indoor temperature of 22°C~25°C, and relative humidity of ≤60%. The TTR XRD (Tokyo, Japan) was used to test the crystallization of tannin-sucrose composite adhesives under conditions of Cu target (λ = 0.154060 nm), 2θ scanning interval of 5~80°, step length of 0.02°, scanning rate of 5°/min, tube current of 120 mA, and tube voltage of 40 kV. The TG 209 F3 thermogravimeter (NETZSCH, Germany) was used to test the thermal stability of tannin-sucrose composite adhesives under test conditions of N2 protection, temperature of 30°C~700°C, and temperature rising rate of 10 °C/min.
3.1 Analysis of Curing Performances of Tannin-Sucrose Composite Adhesives
The results of curing performances of tannin-sucrose composite adhesives are shown in Fig. 2. Obviously, there was a broad exothermic peak at 150°C, which was attributed to water evaporation, partial sucrose pyrolysis and volatilization of micro-molecule in the adhesive system. There was a significant sharp absorption peak at 203.3°C, which was caused by cross-linking reaction between tannin and sucrose. The initial and end reaction temperatures of this peak were 197.7°C and 226.7°C, indicating that the cross-linking reaction was relatively quick, which also showed that it needed a high temperature for cross-linking of tannin-sucrose composite adhesives. Hence, the subsequent orthogonal test temperature factor was chosen 200°C~230°C.
Figure 2: DSC curve of tannin-sucrose adhesive
3.2 The Results and Analysis of the Orthogonal Experiment
The results of bonding strength in boiling water of plywood prepared based on tannin-sucrose composite adhesives under different technological conditions as well as analysis results of range and variance is shown in Tables 3 and 4. Concerning the influences of four factors on bonding strength in boiling water of plywood, there was an order: hot-pressing temperature » m(tannin):m(sucrose) > hot-pressing time ≥ adhesive loading. Specifically, hot-pressing temperature influenced bonding strength in boiling water of plywood the most significantly and played a decisive role in the good bonding performance of plywood. The plywood prepared under the hot-pressing temperature of 200°C series had no water resistance, while the plywood prepared under 210°C series increased the wet bonding strength significantly. The bonding strength in boiling water of plywood prepared under 220°C series and 230°C series could meet the national standard requirements.
Wood failure could be used to evaluate the bonding stability and reliability of plywood. The plywood prepared under the hot-pressing temperature of 200°C series had no water resistance, and the wood failure was 0. The wood failure plywood prepared under 210°C series was 15%~22%, indicating that the stability of the bonding strength was improved to some extent. The wood failure of plywood prepared under 220°C series and 230°C series were 42%~55% and 75%~88%, indicating the high bonding reliability of plywood.
3.3 Effects of Hot-Pressing Temperature on Bonding Strength in Boiling Water of Plywood
Effects of hot-pressing temperature on bonding strength in boiling water of plywood are shown in Fig. 3. The bonding strength in boiling water of plywood prepared under 200°C was 0, while that of plywood prepared under 210°C, 220°C and 230°C were increased to 0.67, 0.97 and 1.06 MPa, respectively (meeting requirements on the strength of I-class plywood in the standard of GB/T 17657-2013, ≥0.70 MPa). The bonding strength was positively related to hot-pressing temperature. With the increase of hot-pressing temperature, plywood was heated more quickly and the heat transfer was more uniform, thus accelerating the thermal motion among molecules, which were conducive to the spreading, diffusion and infiltration of adhesives on the wood surface, and the curing of adhesives was more uniform.
Figure 3: Effects of hot-pressing temperature on bonding strength in boiling water of plywood
According to the results of Zhao et al. [36–38], the key for tannin-sucrose composite adhesives to get good bonding performances was that sucrose was transformed into synthetic furan aldehyde products like hydroxymethylfurfural (5-HMF). Moreover, the temperature played a decisive role in the formation of 5-HMF. The higher hot-pressing temperature was more beneficial for the transformation of 5-HMF and it was more beneficial for the improvement of cross-linking degree and cross-linking density of the adhesives. The bonding strength and water resistance also increased accordingly. Additionally, with the increase of hot-pressing temperature, (1) some cellulose and semi-cellulose of wood could degrade and produce components with cross-linking effect, which could further improve bonding performances; (2) the thermoplastic lignin intertwined on the bonding interface to some extent, which also had some contributions to the improvement of bonding performances. Although a high hot-pressing temperature was conducive to the formation of 5-HMF and improved bonding performances, it was easy to cause caramel color on the plywood surface, increase energy consumption during preparation and compression ratio of plywood, and decrease utilization of woods [39,40]. The future research shall focus on: (1) The introduction of catalyst into the adhesive system and achieving high transformation of 5-HMF under a low hot-pressing temperature; (2) Sucrose was converted into 5-HMF beforehand and then cross-linked with tannin. But for this experiment, 220°C was an appropriate hot-pressing temperature.
3.4 Effects of Hot-Pressing Time on Bonding Strength in Boiling Water of Plywood
Effects of hot-pressing time on bonding strength in boiling water of plywood are shown in Fig. 4. The bonding strength was 0.62 MPa when the hot-pressing time was 1.0 min/mm. With the increase of hot-pressing time, bonding strength increased gradually and reached the maximum (0.71 MPa) at 1.2 min/mm. As the hot-pressing time continued to grow to 1.4~1.6 min/mm, the bonding strength began to decrease. Due to the high viscosity and large contact angle with the wood surface, tannin-sucrose composite adhesives were challenging to wet and took some time to spread and infiltrate. Besides, heat is transferred from the surface to the core of plywood during hot-pressing. It took some time to produce furan aldehydes and realized cross-linking curing of adhesives. However, excessive long hot-pressing time could lead to excessive curing of adhesives, thus making the bonding layer brittle and even causing thermal decomposition of cured adhesive and wood. Finally, the bonding strength declined. Hence, the appropriate hot-pressing time of tannin-sucrose composite adhesives was determined at 1.2 min/mm.
Figure 4: Effects of hot-pressing time on bonding strength in boiling water of plywood
3.5 Effects of Adhesive Loading on Bonding Strength in Boiling Water of Plywood
Effects of adhesive loadings on bonding strength in boiling water of plywood are shown in Fig. 5. Clearly, the maximum bonding strength was 0.72 MPa when the adhesive loading was 140 g/m2, indicating that adhesives could be coated on plywood uniformly at this moment. When the adhesive loading increased to 160~200 g/m2, the bonding strength was 0.65~0.69 MPa, which was decreased to some extent. According to the bonding theory, the bonding layer became thinner and the bonding performances were better after adhesives formed a layer of uniform film on the wood surface. On the one hand, excessive adhesive loading could make adhesives spill over during hot-pressing, thus causing some waste of adhesives. On the other hand, it could increase the thickness of the curing bonding layer, making the cohesion of the bonding layer more diminutive than the bonding force between adhesives and the wood, which caused significant curing stresses of adhesives, and thereby influenced the bonding strength to some extent [41,42]. Although adhesive loading had insignificant influences on the bonding performances of plywood in this experiment, the appropriate resin content was determined at 160 g/m2 in this study with consideration of the increased liquidity and infiltration of adhesives during the hot-pressing.
Figure 5: Effects of adhesive loading on bonding strength in boiling water of plywood
3.6 Effects of Mass Ratio of Tannin to Sucrose on Bonding Strength in Boiling Water of Plywood
Effects of m(tannin):m(sucrose) on bonding strength in boiling water of plywood are shown in Fig. 6. Clearly, the bonding strength remained constant when m(tannin):m(sucrose) was 60:40, 50:50 and 40:60, and it began to decrease at 30:70. The pH of the adhesive system also played an essential role in the transformation of sucrose into furan aldehydes, except for temperature. Tannin presented some acidity in an aqueous solution and it could promote transformation into furan aldehydes to some extent. With the reduction of tannin and sucrose, the acidity of the system decreased and the transformation rate of furan aldehydes reduced accordingly. Additionally, the curing of adhesives was influenced if excessive micromolecular sucrose was scattered in the adhesive system, thus decreasing the bonding strength. So, the appropriate m(tannin):m(sucrose) was determined at 60:40.
Figure 6: Effects of mass ratio of tannin to sucrose on bonding strength in boiling water of plywood
Plywood was prepared by choosing the optimal technological parameters: Hot-pressing temperature of 220°C, hot-pressing time of 1.2 min/mm, adhesive loading of 160 g/m2, and m(tannin):m(sucrose) of 60:40. The bonding strength in boiling water of plywood prepared under these optimal conditions was 0.83 MPa (meeting requirements for I-class plywood in the standard of GB/T 17657-2013).
3.7 Analysis of the Chemical Structure of Tannin-Sucrose Composite Adhesives
The FT-IR curves of cured tannin-sucrose composite adhesives under different curing temperatures are shown in Fig. 7, and the structural attribution is shown in Table 5. The control group was a mixture of tannin and sucrose. The wavenumber peak at 1622.6 cm−1 was the skeleton carbon absorption peak on the benzene ring of tannin [26,29], and 843.6 cm−1 was the C-H bending vibration absorption peak on the aromatic ring of tannin. The wavenumber peak at 1137.4 cm−1 was assigned to glycosidic linkage (C–O–C) of sucrose, and 929.9 and 989.9 cm−1 were attributed to the hydroxymethyl of pyranose ring of sucrose, and 1049.8 cm−1 was the ether bond absorption peak of the sucrose.
Figure 7: FT-IR curves of cured tannin-sucrose adhesives at different temperatures
FT-IR curves of curing products of tannin-sucrose composite adhesives under different temperatures were significantly different from that of the blank control group. The wavenumber at 1137.4, 989.9 and 929.9 cm−1 disappeared. This indicated the depolymerization of the hexatomic pyranose ring of sucrose. The new absorption peaks produced at 1706.1, 1515.8 and 774.7 cm−1 resulted from the characteristic of C=O, C=C stretching vibration and unsubstituted CH=CH of furan aldehydes such as furfural and 5-HMF. The ether bond at the curing temperature of 200°C was shifted to 1038.6 cm−1. The ether bond peaks at 210°C, 220°C and 230°C were further shifted to 1033.0 cm−1. The shifts of the ether bond signal in the heterocyclic ring as the temperature increases, were possibly attributed to heterocyclic rearrangement after unfolding or reaction with tannin [36–38]. The decrease and disappearance at 843.6 cm−1, indicated that tannin reacted with sucrose and a high curing temperature requirement for the cross-linking reaction of tannin-sucrose adhesive. However, it was difficult to ensure the reaction of tannin with furfural or 5-HMF by FT-IR only. Therefore, other chemical analysis methods will be carried out in our further research to verify the mechanism.
3.8 Analysis of Crystallization Properties and Thermal Performance of Tannin-Sucrose Composite Adhesives
The crystallization properties test results of curing products of tannin-sucrose composite adhesives under different temperatures are shown in Fig. 8. The degree of crystallization reflected the degree of ordered molecular arrangement and it also could reflect the degree of cross-linking reaction between tannin and sucrose to some extent [43,44].
Figure 8: XRD curves of cured tannin-sucrose adhesives at different temperatures
Based on the above analysis, the temperature had significant influences on the transformation of sucrose into furan aldehydes. When the curing temperature was 200°C, the transformation rate of furan aldehydes was low and its cross-linking reaction with tannin was insufficient, accompanied by the minimum degree of crystallization (7.72%). The degrees of crystallization of curing products were 18.16% and 33.13% under 210°C and 220°C, indicating the high transformation rate of furan aldehydes and sufficient cross-linking reaction with tannin. The cross-linking density and degree of crystallization increased obviously. Generally speaking, cross-linking and crystallization are contradictory processes for high-molecular polymers. The excessive cross-linking reaction may hinder the directed arrangement of molecules, thus decreasing the degree of crystallization [45,46]. Although the transformation rate of furan aldehydes could be further increased at 230°C, the degree of crosslinking reaction with tannin was too high and the cross-linking density was excessively high, thus decreasing the degree of crystallization. Besides, the decomposition of cured adhesives could also influence the degree of crystallization greatly as the curing temperature was increased.
Thermal performance results of cured tannin-sucrose composite adhesives under different temperatures are shown in Figs. 9 and 10. Mass loss in the 30°C~150°C stage was mainly caused by water evaporation of adhesives in the adsorption air. The adhesive suffered a great mass loss since 200°C and the residual mass was constant until 700°C. The temperatures for maximum mass thermal weight loss of cured tannin-sucrose composite adhesives when the curing temperature was 200°C, 210°C, 220°C and 230°C were 288.4°C, 298.4°C, 304.5°C and 290.3°C, respectively. The variation trend was consistent with XRD results. The XRD and TG/DTG test results further proved that cross-linking structure was established in tannin-sucrose composite adhesives. To ensure the degree of cross-linking reaction and thermal stability of cured adhesives, the curing temperature of tannin-sucrose composite adhesives should not be higher than 220°C.
Figure 9: TG curves of cured tannin-sucrose adhesives
Figure 10: DTG curves of cured tannin-sucrose adhesives
Biomass adhesive is a vital breakthrough to realize the goal of carbon peaking and carbon neutrality in the wood industry. In this study, a kind of fully biomass wood adhesive composed of tannin and sucrose was developed and used successfully in the preparation of plywood. Results showed that:
(1) Hot-pressing temperature played a decisive role in the performances of tannin-sucrose composite adhesives. It had very significant influences on the water resistance of plywood. Hot-pressing time, adhesive loading and m(tannin):m(sucrose) had insignificant influences on the water resistance of plywood.
(2) The preparation of tannin-sucrose composite adhesive was a process in which sucrose was transformed into furan aldehydes and then made cross-linking reaction with tannin. The transformation of sucrose into 5-HMF required a very high temperature. Therefore, the tannin-sucrose composite adhesives could only get good bonding performances when the curing temperature was above 210°C. However, on the one hand, excessive curing temperature might induce the degradation of adhesives. On the other hand, it could decrease cross-linking density and thermal stability of adhesives.
(3) The optimal plywood preparation technique based on tannin-sucrose composite adhesive was: hot-pressing temperature of 220°C, hot-pressing time of 1.2 min/mm, m(tannin):m(sucrose) of 60:40, and adhesive loading of 160 g/m2. The wet bonding strength in boiling water of the prepared plywood was 0.83 MPa, meeting the strength requirements of Type-I plywood in the standard of GB/T 17657-2013.
(4) In the following work, we will consider using catalysis to reduce the curing temperature of tannin-sucrose composite adhesive and sucrose was converted into furan aldehydes beforehand and then cross-linked with tannin.
Acknowledgement: The authors thank the anonymous reviewers for their invaluable comments and suggestions to improve the quality of this paper.
Funding Statement: The authors received no specific funding for this study.
Conflicts of Interest: The authors declare that they have no conflicts of interest to report regarding the present study.
References
1. Wei, Y., Chen, K., Kang, J., Chen, W., Wang, X. et al. (2022). Policy and management of carbon peaking and carbon neutrality: A literature review. Engineering, 14(7), 52–63. https://doi.org/10.1016/j.eng.2021.12.018 [Google Scholar] [CrossRef]
2. Feng, B. (2021). Goals of “Peak CO2 emissions and carbon neutrality” reshape the oil and gas industry. China Oil & Gas, 28(2), 41–47. [Google Scholar]
3. Li, J., Li, G. (2021). Carbon neutrality: Opportunities and challenges for development transformation in China. Environment and Sustainable Development, 46(1), 50–57. https://doi.org/10.19758/j.cnki.issn1673-288x.202101050 [Google Scholar] [CrossRef]
4. Xu, W.(2021). Study on the pathway of improving carbon sink capacity of wood forest products under the background of “Carbon Neutralization”. China Forest Products Industry, 58(9), 81–83. https://doi.org/10.19531/j.issn1001-5299.202109015 [Google Scholar] [CrossRef]
5. Zhang, Y., Huang, A., Ye, K. (2010). Outlook on development of China wood industry from low-carbon economy point of view. China Wood Industry, 24(2), 17–20. https://doi.org/10.19455/j.mcgy.2010.02.006 [Google Scholar] [CrossRef]
6. Chen, W. (2014). Analysis on forestry carbon sequestration market in China based on carbon neutral (Ph.D. Thesis). Beijing Forestry University, Beijing, China. [Google Scholar]
7. Wang, S. (2022). Study on the response mechanism and pathways of coal production to CO2 emissions mitigation under carbon peaking and carbon neutrality (Ph.D. Thesis). China University of Mining and Technology, Beijing, China. [Google Scholar]
8. Li, Q., Zhang, K. (2021). The path for green development and utilization of energy in China. Strategic Study of Chinese Academy of Engineering, 23(1), 101–111. https://doi.org/10.15302/J-SSCAE-2021.01.012 [Google Scholar] [CrossRef]
9. Pizzi, A. (2003). Handbook of adhesive technology. New York: Marcel Dekker. [Google Scholar]
10. Xi, X., Pizzi, A., Frihart, C. R., Lorenz, L., Gerardin, C. (2020). Tannin plywood bioadhesives with non-volatile aldehydes generation by specific oxidation of mono-and disaccharides. International Journal of Adhesion and Adhesives, 98, 102499. https://doi.org/10.1016/j.ijadhadh.2019.102499 [Google Scholar] [CrossRef]
11. Gan, W., Liu, J., Zhang, J., Fang, J., Hou, Z. et al. (2022). Research progress on utilizing liquefaction of lignin to modify phenolic resin. Journal of Forestry Engineering, 7(3), 11–19. https://doi.org/10.13360/j.issn.2096-1359.202107042 [Google Scholar] [CrossRef]
12. Jiang, S., Hu, M., Zhou, X., Duan, Z., Du, G. et al. (2022). Effects of highly branched polyurea on the water resistance and formaldehyde emission of urea-formaldehyde adhesive. Journal of Forestry Engineering, 7(1), 107–114. https://doi.org/10.13360/j.issn.2096-1359.202107026 [Google Scholar] [CrossRef]
13. Liang, J., Li, Q., Wu, Z., Du, G., Li, T. et al. (2020). Competitive polycondensation of model compound melamine-urea-formaldehyde (MUF) resin system by 13C NMR. Journal of Bioresources and Bioproducts, 5(1), 60–66. https://doi.org/10.1016/j.jobab.2020.03.007 [Google Scholar] [CrossRef]
14. Zhang, B., Wu, Z., Liang, J., Yu, L., Xi, X. et al. (2022). Effects of polyethylene glycol on the flexibility of cold-setting melamine-urea-formaldehyde resin. European Journal of Wood and Wood Products, 80(4), 975–984. https://doi.org/10.1007/s00107-022-01801-x [Google Scholar] [CrossRef]
15. Osman, Z., Pizzi, A. (2002). Comparison of gelling reaction effectiveness of procyanidin tannins for wood adhesives. European Journal of Wood and Wood Products, 60(5), 328. https://doi.org/10.1007/s00107-002-0289-x [Google Scholar] [CrossRef]
16. Zhang, J., Liu, B., Zhou, X., Essawy, H., Zhao, C. et al. (2022). Gelatinized starch-furanic hybrid as a biodegradable thermosetting resin for fabrication of foams for building materials. Carbohydrate Polymers, 298(2), 120157. https://doi.org/10.1016/j.carbpol.2022.120157 [Google Scholar] [PubMed] [CrossRef]
17. Zhang, J., Xi, X., Liang, J., Pizzi, A., Du, G. et al. (2019). Tannin-based adhesive cross-linked by furfuryl alcohol-glyoxal and epoxy resins. International Journal of Adhesion and Adhesives, 94(1), 47–52. https://doi.org/10.1016/j.ijadhadh.2019.04.012 [Google Scholar] [CrossRef]
18. Yuan, C., Chen, M., Luo, J., Li, X., Gao, Q. et al. (2017). A novel water-based process produces eco-friendly bio-adhesive made from green cross-linked soybean soluble polysaccharide and soy protein. Carbohydrate polymers, 169, 417–425. https://doi.org/10.1016/j.carbpol.2017.04.058 [Google Scholar] [PubMed] [CrossRef]
19. Xu, C., Xu, Y., Chen, M., Zhang, Y., Li, J. et al. (2020). Soy protein adhesive with bio-based epoxidized daidzein for high strength and mildew resistance. Chemical Engineering Journal, 390, 124622. https://doi.org/10.1016/j.cej.2020.124622 [Google Scholar] [CrossRef]
20. Xu, F., Dong, Y., Zhang, W., Zhang, S., Li, L. et al. (2015). Preparation of cross-linked soy protein isolate-based environmentally-friendly films enhanced by PTGE and PAM. Industrial Crops and Products, 67, 373–380. https://doi.org/10.1016/j.indcrop.2015.01.059 [Google Scholar] [CrossRef]
21. Bartolome, M., Schwaiger, N., Flicker, R., Seidl, B., Kozich, M. et al. (2022). Enzymatic synthesis of wet-resistant lignosulfonate-starch adhesives. New Biotechnology, 69, 49–54. https://doi.org/10.1016/j.nbt.2022.03.003 [Google Scholar] [PubMed] [CrossRef]
22. Chen, X., Sun, C., Wang, Q., Tan, H., Zhang, Y. (2021). Preparation of glycidyl methacrylate grafted starch adhesive to apply in high-performance and environment-friendly plywood. International Journal of Biological Macromolecules, 194, 954–961. https://doi.org/10.1016/j.ijbiomac.2021.11.152 [Google Scholar] [PubMed] [CrossRef]
23. Xia, Z., Li, J., Zhang, J., Zhang, X., Zheng, X. et al. (2020). Processing and valorization of cellulose, lignin and lignocellulose using ionic liquids. Journal of Bioresources and Bioproducts, 5(2), 79–95. https://doi.org/10.1016/j.jobab.2020.04.001 [Google Scholar] [CrossRef]
24. Li, R., Gutierrez, J., Chung, Y., Frank, C., Billington, S. et al. (2018). A lignin-epoxy resin derived from biomass as an alternative to formaldehyde-based wood adhesives. Green Chemistry, 20(7), 1459–1466. https://doi.org/10.1039/C7GC03026F [Google Scholar] [CrossRef]
25. Zhang, N., Li, Z., Xiao, Y., Pan, Z., Jia, P. et al. (2020). Lignin-based phenolic resin modified with whisker silicon and its application. Journal of Bioresources and Bioproducts, 5(1), 67–77. https://doi.org/10.1016/j.jobab.2020.03.008 [Google Scholar] [CrossRef]
26. Zhang, J., Liang, J., Du, G., Zhou, X., Wang, H. et al. (2017). Development and characterization of a Bayberry tannin-based adhesive for particleboard. BioResources, 12(3), 6082–6093. https://doi.org/10.15376/biores.12.3.6082-6093 [Google Scholar] [CrossRef]
27. Wang, X., Wu, Z., Dong, J., Lei, H., Zhang, B. et al. (2017). Preparation and performance of tannin-based adhesive crosslinked by hydroxymethyl phenol. Journal of Northwest Forestry University, 32(1), 234–238. [Google Scholar]
28. Dong, J., Wu, Z., Lei, H., Su, L., Wang, X. et al. (2018). Bonding performance of tannin-phenol-formaldehyde resin. Journal of Forest and Environment, 38(1), 118–122. https://doi.org/10.13324/j.cnki.jfcf.2018.01.019 [Google Scholar] [CrossRef]
29. Wang, X., Wu, Z., Lei, H., Wu, J., Su, L. et al. (2017). Study on tannin based adhesive prepared by glyoxal. China Adhesives, 26(2), 39–42. https://doi.org/10.13416/j.ca.2017.02.010 [Google Scholar] [CrossRef]
30. Yuniarti, K., Santoso, A., Pari, R. (2020). The effect of drying temperatures and tannin-adhesive types on bending properties and shear strength of glued Eucalyptus pellita board. IOP Conference Series: Earth and Environmental Science, 460(1), 12015. https://doi.org/10.1088/1755-1315/460/1/012015 [Google Scholar] [CrossRef]
31. Li, K., Geng, X., Simonsen, J., Karchesy, J. (2004). Novel wood adhesives from condensed tannins and polyethylenimine. International Journal of Adhesion & Adhesives, 24(4), 327–333. https://doi.org/10.1016/j.ijadhadh.2003.11.004 [Google Scholar] [CrossRef]
32. Sun, G., Sun, H., Liu, Y., Zhao, B., Zhu, N. et al. (2007). Comparative study on the curing kinetics and mechanism of a lignin-based-epoxy/anhydride resin system. Polymer, 48(1), 330–337. https://doi.org/10.1016/j.polymer.2006.10.047 [Google Scholar] [CrossRef]
33. Meikleham, N. E., Pizzi, A. (1994). Acid-catalyzed and alkali-catalyzed tannin-based rigid foams. Journal of Applied Polymer Science, 53(11), 1547–1556. https://doi.org/10.1002/app.1994.070531117 [Google Scholar] [CrossRef]
34. Ghahri, S., Pizzi, A. (2018). Improving soy-based adhesives for wood particleboard by tannins addition. Wood Science and Technology, 52(1), 261–279. https://doi.org/10.1007/s00226-017-0957-y [Google Scholar] [CrossRef]
35. Nacas, A. M., Ito, N. M., de Sousa Jr, R. R., Spinacé, M. A., Dos Santos, D. J. (2016). Effects of NCO:OH ratio on the mechanical properties and chemical structure of Kraft lignin-based polyurethane adhesive. The Journal of Adhesion, 1(2), 18–29. https://doi.org/10.1080/00218464.2016.1177793 [Google Scholar] [CrossRef]
36. Zhao, Z., Umemura, K. (2014). Investigation of a new natural particleboard adhesive composed of tannin and sucrose. Journal of Wood Science, 60(4), 269–277. https://doi.org/10.1007/s10086-014-1405-3 [Google Scholar] [CrossRef]
37. Zhao, Z., Umemura, K. (2015). Investigation of a new natural particleboard adhesive composed of tannin and sucrose. 2. Effect of pressing temperature and time on board properties, and characterization of adhesive. BioResources, 10(2), 2444–2460. https://doi.org/10.15376/biores.10.2.2444-2460 [Google Scholar] [CrossRef]
38. Zhao, Z., Umemura, K., Kanayama, K. (2015). Effects of the addition of citric acid on tannin-sucrose adhesive and physical properties of the particleboard. BioResources, 11(1), 1319–1333. https://doi.org/10.15376/biores.11.1.1319-1333 [Google Scholar] [CrossRef]
39. Wu, Z., Deng, X., Li, L., Xi, X., Tian, M. et al. (2021). Effects of heat treatment on interfacial properties of Pinus massoniana wood. Coatings, 11(5), 543. https://doi.org/10.3390/coatings11050543 [Google Scholar] [CrossRef]
40. Tian, M., Zhang, B., Wu, Z., Yu, L., Li, L. et al. (2021). Effects of steam heat-treatment on properties of Pinus massoniana wood and its bonding performance. Journal of Renewable Materials, 9(4), 789–801. https://doi.org/10.32604/jrm.2021.013844 [Google Scholar] [CrossRef]
41. Luo, J. (2018). Cross-linking architecture regulation and reinforcement mechanism of soy protein-based adhesive (Ph.D. Thesis). Beijing Forestry University, Beijing, China. [Google Scholar]
42. Song, J., Tian, H., Lei, H., Xu, G., Wang, J. et al. (2022). Modification of urea-formaldehyde resin by nano MnO2. Journal of Forestry Engineering, 7(2), 91–96. https://doi.org/10.13360/j.issn.2096-1359.202107016 [Google Scholar] [CrossRef]
43. Deng, X., Wu, Z., Zhang, B., Lei, H., Liang, J. et al. (2022). A new wood adhesive based on recycling Camellia oleifera cake-protein: Preparation and properties. Materials, 15(5), 1659. https://doi.org/10.3390/ma15051659 [Google Scholar] [PubMed] [CrossRef]
44. Zhang, M., Zhang, Y., Chen, M., Gao, Q., Li, J. (2018). A high-performance and low-cost soy flour adhesive with a hydroxymethyl melamine prepolymer. Polymers, 10(8), 909. https://doi.org/10.3390/polym10080909 [Google Scholar] [PubMed] [CrossRef]
45. Li, C., Lei, H., Wu, Z., Xi, X., Du, G. et al. (2022). Fully biobased adhesive from glucose and citric acid for plywood with high performance. ACS Applied Materials & Interfaces, 14(20), 23859–23867. https://doi.org/10.1021/acsami.2c02859 [Google Scholar] [PubMed] [CrossRef]
46. Li, T., Zhang, B., Jiang, S., Zhou, X., Du, G. et al. (2020). Novel highly branched polymer wood adhesive resin. ACS Sustainable Chemistry & Engineering, 8(13), 5209–5216. https://doi.org/10.1021/acssuschemeng.9b07732 [Google Scholar] [CrossRef]
Cite This Article
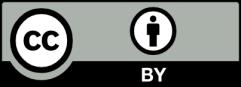
This work is licensed under a Creative Commons Attribution 4.0 International License , which permits unrestricted use, distribution, and reproduction in any medium, provided the original work is properly cited.