Open Access
ARTICLE
Plasticizing Effect of Camellia oleifera Seed-Oil-Based Plasticizer on PVC Material Modification
1 College of Horticulture and Landscape Architecture, Zhongkai University of Agriculture and Engineering, Guangzhou, 510225, China
2 Guangdong Provincial Key Laboratory of Silviculture, Guangdong Academy of Forestry, Guangzhou, 510225, China
3 Institute of Chemical Industry of Forest Products, Chinese Academy of Forestry (CAF); Key Laboratory of Biomass Energy and Material, Co-Innovation Center of Efficient Processing and Utilization of Forest Resources, Nanjing Forestry University; Key and Open Laboratory of Forest Chemical Engineering, SFA, National Engineering Laboratory for Biomass Chemical Utilization, Nanjing, 210042, China
4 College of Chemistry and Chemical Engineering, Zhongkai University of Agriculture and Engineering, Guangzhou, 510225, China
* Corresponding Authors: Yongquan Li. Email: " />; Qiaoguang Li. Email:
" />
# Qinghua Lao and Hui Zhang contributed equally to this work
Journal of Renewable Materials 2023, 11(7), 3025-3041. https://doi.org/10.32604/jrm.2023.026646
Received 17 September 2022; Accepted 30 November 2022; Issue published 05 June 2023
Abstract
In this study, as the plasticizer, Camellia oleifera seed-oil-based cyclohexyl ester (COSOCE) was prepared by the reaction of cyclohexene oxide and refined C. oleifera seed oil (RCOSO) obtained by acidification hydrolysis after saponification. In addition, the structure of the target product was confirmed by Fourier transform infrared (FTIR) spectroscopy, nuclear magnetic resonance (NMR) spectroscopy, and Raman spectroscopy. COSOCE was used as plasticizer-modified polyvinyl chloride (PVC) membranes. The structure of the COSOCE-modified PVC membranes were characterized by Raman spectroscopy and scanning electron microscopy (SEM). The properties of the COSOCE-modified PVC membrane were characterized by contact angle measurements, universal testing machine, thermogravimetric analysis (TGA), and differential scanning calorimetry (DSC). The results revealed that (1) The COSOCE-modified PVC membranes exhibit a good microscopic morphology. Combined with energy-dispersive X-ray spectroscopy (EDS) and contact angle measurement results, the COSOCE-modified PVC membranes are confirmed to be a hydrophilic material. (2) The modified PVC membrane with 60% COSOCE exhibited the best mechanical properties. The tensile strength reached 23.56 ± 2.94 MPa. (3) COSOCE-modified PVC material exhibited better thermal stability, with a loss rate of less than 75% at the end of the first decomposition stage. Compared with that of the dioctyl-phthalate (DOP)-modified PVC membrane, the initial decomposition temperature of PVC was increased by 1.17°C–8.17°C, and the residual rate was increased by 0.67%–5.75%. The carbon–carbon double bond in the COSOCE molecular structure can remove the free radicals generated during the degradation of PVC material and slow down the decomposition rate of PVC. In addition, the double bond can be cross-linked partially with the PVC molecular chain containing the conjugated polyene structure, thereby increasing the movement resistance of the PVC molecular chain segment. Hence, COSOCE can replace DOP as a PVC plasticizer.Keywords
Nomenclature
COSOCE | Camellia oleifera seed-oil-based cyclohexyl ester |
RCOSO | Refined Camellia oleifera seed oil |
PVC | Polyvinyl chloride |
SEM | Scanning electron microscopy |
TGA | Thermogravimetric analysis |
DTG | Derivative thermogravimetric |
DSC | Differential scanning calorimetry |
DOP | Dioctyl phthalate |
DOA | Dioctyl adipate |
ESO | Epoxy soybean oil |
Polyvinyl chloride (PVC) is one of the most widely used plastic products worldwide [1,2] PVC-derived plastic products exhibit advantages such as material processability, relatively low costs, and immense versatility [3]. However, owing to the high glass transition temperature of PVC, it is used in a brittle glass state at the daily use temperature. To improve the mechanical and thermal properties of PVC materials, plasticizers are added during production [4,5]. Currently, dioctyl phthalate (DOP), dioctyl terephthalate, dihexyl phthalate, and diisononyl phthalate plasticizers are mainly used [1]. However, conventional plasticizers exhibit slow degradation rates [6,7]. Moreover, the widely used phthalate ester plasticizer, i.e., DOP, spreads on the material surface, which can adversely affect animals and the environment [8]. Bio-based plasticizers with the advantages of low toxicity or non-toxicity can be used in food packaging materials or other industries that necessitate strict safety and health requirements [9–13]. At the same time, bio-based plasticizers are derived from renewable and environmentally friendly resources [6,14,15], these materials have become the focus of the plastic and plasticizer industry [16].
Meanwhile, plant oil has become a hot research topic in recent years due to its abundant sources and low toxicity as well [17]. Epoxidized soybean oil (ESO) has been successfully established as a green additive, which exhibits a dual function of a compatibilizer and a plasticizer. Dutta et al. [18] prepared PVC/rice husk ash (RHA) nanocomposites using ESO as the green additive. The introduction of 1 phr of ESO into the composites leads to improvement of tensile properties by 97%, flexural properties by 90%, the shore D value by 91%, and the limiting oxygen index values (indicator for flame retardancy) by 66.6%. The acid resistance, alkali resistance, and water vapor resistance of the nanocomposites after 168 h are 0.09, 0.11, and 0.35, respectively. Ma et al. [8] synthesized a highly branched and non-toxic plasticizer CHE-12 derived from natural cashew shell oil by facile one-pot solvent-free synthesis. CHE-12 exhibits a toxic dose of 5000 mg/kg; hence, it is a non-toxic plasticizer. PVC materials plasticized using CHE-12 exhibit more superior thermal stability, plasticizing property, migration stability, and compatibility than those plasticized with DOP. Feng et al. [19] obtained a new type of a high-stability bio-based plasticizer by a four-step reaction using ricinoleic acid as the main raw material. Compared with those of the PVC material plasticized using dioctyl adipate (DOA) and DOP, the initial degradation temperature of ricinoleate-plasticized material is 40°C higher. Compared to DOA and DOP, ricinoleate exhibits better comprehensive performance, plasticizing efficiency, mechanical properties, migration stability, and thermostability. All of the results demonstrated that ricinoleate can be used as a substitute for DOA or DOP, providing a new approach for the rational use of renewable resources to prepare environmentally friendly plasticizers. Rozaki et al. [20] synthesized an oil-modified polyester to function as a plasticizer for PVC; as a result, the glass transition temperature of PVC is reduced to 65°C on average under 20% load. That PVC films exhibit a higher heat stability, an increased decomposition activation energy, and a lower toxicity than those of commercial plasticizers.
Meanwhile, Camellia oleifera Abel. is a unique edible oil woody plant with a long history in Chinese farming culture. In 2015, the planting area of C. oleifera reached 400,000 hectares, with a seed output of about 2.2 million tons [21,22]. C. oleifera seed oil by expelling contains a large amount of unsaturated fatty acids; in particular, its oleic acid content is greater than 80% [22]. Benzene rings are absent, but unsaturated double bonds are present in unsaturated fatty acids; hence, its derivatives are suitable as plasticizer raw materials to modify PVC materials. To obtain an oil-based plasticizer of C. oleifera oil with good properties, PVC material was modified using COSOCE as the plasticizer, and the mechanical properties and thermal stability of the modified PVC material were investigated and compared with those of DOP. Furthermore, the application of C. oleifera seed oil was explored using commercial C. oleifera seed oil as the raw material, with the aim to explore the potential value of the waste generated during production, and prepared the regenerative application and deep processing technology of C. oleifera.
Organic C. oleifera seed oil was kindly supplied by Guangdong Baohua Agricultural Science and Technology Co., Ltd. (China). Potassium hydroxide (KOH), hydrochloric acid (HCl), and ethanol (C2H5OH) were purchased from Tianjin Damao Chemical Reagent Co., Ltd. (China), Guangzhou Chemical Reagent Factory (China), and Shanghai Titan Scientific Co., Ltd. (China), respectively. Cyclohexene oxide, benzyltriethylammonium chloride (TEBAC), and tetrahydrofuran were purchased from Shanghai Macklin Biochemical Co., Ltd. (China). DOP and polyvinyl chloride (PVC, K-value 72–71) were purchased from Shanghai Aladdin Biochemical Technology Co., Ltd. (China). All chemicals were used as received without further purification.
2.2 Synthesis of Refined C. oleifera Seed Oil (RCOSO)
First, 26.4 g of potassium hydroxide was blended in ethanol and poured into a conical flask containing 100 g of organic C. oleifera seed oil. Second, the mixture was maintained at ~60°C for 2 h. Next, 140 mL of a 10% HCl solution and 100 mL of ethanol were added into the conical flask, and the mixture was maintained at 60°C for another 3 h. The mixture was left standing, and the top layer of the mixture was rotated to permit evaporation. The solution was stored at ~110°C for 2 h in a thermostatic dry box with an air blower (Yiheng, China), affording the RCOSO products.
2.3 Synthesis of C. oleifera Seed Oil-Based Cyclohexyl Ester (COSOCE)
In a three-necked flask equipped with a stirrer and a thermometer, 10.00 g of cyclohexene oxide, 14.70 g of RCOSO, and 0.23 g of TEBAC were added. The mixture was maintained at ~115°C for 2 h, affording a light yellow and viscous COSOCE. Fig. 1 shows the preparation reaction formula.
Figure 1: Synthetic route of COSOCE
2.4 Synthesis of COSOCE-Modified PVC Membrane
According to the formulations of PVC-modified films shown in Table 1, different contents of COSOCE were used to prepare PVC-modified films, and the plastic film prepared by the modification of PVC material using the DOP plasticizer was used as the control.
First, a flask equipped with a stirrer was filled with PVC, plasticizer, and tetrahydrofuran. Second, the mixture was maintained at 40°C, and PVC was slowly poured into the mixture until it completely reacted. Next, it was placed in a thermostatic dry box with an air blower at 40°C for drying, affording the modified PVC membrane.
2.5 Characterization and Measurements
First, potassium bromide powder was placed in a tablet press and maintained at a pressure of 10 MPa for 1–2 min to prepare 0.2–0.5-mm translucent thin sections. Sample of 1/120 mass potassium bromide sheet was coated evenly on the potassium bromide sheet and baked with a tungsten filament lamp for ~1 min. Fourier transform infrared (FTIR) spectra of the samples were recorded in the wavenumber range of 4000–400 cm–1.
1H NMR spectra of cyclohexene oxide, RCOSO, and COSOCE were recorded at 40°C on an AV400 spectrometer (Bruker, Germany) at a frequency of 400.13 MHz, and 13C NMR spectra were recorded at a frequency of 100.61 MHz. Deuterochloroform (CDCl3) was used as the solvent. The chemical shift values were referenced to the signals of CDCl3.
Cyclohexene oxide, RCOSO, COSOCE, and modified PVC materials were placed on clean slides and tested under a confocal Raman spectrometer (Thermo Scientific, China).
The modified PVC materials were sprayed with gold for 30 s, and the morphology of the samples were observed by scanning electron microscopy (ZEISS, Germany).
The element composition of modified PVC materials were analyzed by X-ACT energy-dispersive X-ray spectroscopy.
The hydrophilicity of the modified PVC materials was characterized by static contact angle measurements using a precision Kruss drop shape analyzer (Biolin, Sverige) at 25°C. The contact angle measurements were conducted in triplicate, and an average value was obtained.
Three dumbbell-shaped modified PVC samples with specifications of 4 mm × 50 mm were prepared and examined on a universal testing machine (Suns, China). Samples were characterized at 25°C at a rate of 10 mm/min, and the average of three temporal measurements was reported.
In a thermogravimetric analyzer (Mettler Toledo, USA), 3–5 mg of the modified PVC material was heated from 30°C to 600°C under nitrogen at a heating rate of 10 °C/min.
For differential scanning calorimetry (TA Instruments, USA) measurements, 5–10 mg of the modified PVC material was heated from −20°C to 110°C under nitrogen at a flow rate of 20 mL/min and a heating rate of 10 °C/min.
3.1 Characterization of COSOCE
Fig. 2 shows the FTIR spectra of cyclohexene oxide, RCOSO, and COSOCE. From spectra a and c in Fig. 2, the band corresponding to the epoxy groups at 965 cm−1 disappeared [1], a new band corresponding to the hydroxyl group at 3444 cm−1 were observed [3,23,24], and the band corresponding at 1734 cm−1 was the ester base in spectra c [24,25]. Indicating that esterification is completed. In addition, the band corresponding to the carboxyl peak at 1712 cm−1 was observed [26–28]. The FTIR analysis results revealed that the final product of COSOCE is successfully synthesized.
Figure 2: FTIR spectra: (a) Cyclohexene oxide, (b) RCOSO, and (c) COSOCE
Figs. 3 and 4 show the 1H NMR and 13C NMR spectra of cyclohexene oxide, RCOSO, and COSOCE. No. 0 corresponded to the solvent peak of CDCl3. In the 1H NMR spectrum of cyclohexane epoxy, the peak at 3.02 ppm corresponded to the proton signal of the No. 1 carbon atom on the epoxy group, and the clusters of peaks observed at 1.67–1.90 ppm and 1.09–1.39 ppm corresponded to the proton signals of the No. 2 and No. 3 carbon atoms. Compared with them, in the 1H NMR curve of COSOCE, the proton signal of the No. 1 carbon atom disappeared, while the proton signals of No. 2 and No. 3 carbon atoms and the methylene on the carbon atom shifted [29]. The above results confirm the successful reaction of the epoxy group. In the 1H NMR spectrum of RCOSO, the peak at 11.19 ppm corresponded to the proton signal of the hydroxyl group (No. 10), and disappeared completely in the 1H NMR spectrum of COSOCE which mean that the RCOSO was completely esterified. Infrared characterization also proves this result. Besides, in the 1H NMR spectrum of COSOCE, the peak at 5.29 ppm corresponded to the C=C proton signal peak (No. 4), which was consistent with the proton signal peak of the hydroxyl group. The peaks at 2.28, 1.98, 1.58, 1.27, 0.85 ppm corresponding to the proton signals of carbon atoms Nos. 5, 6, 7, 8, and 9, respectively. In summary, the 1H NMR analysis results of the products are consistent with the actual structure of COSOCE.
Figure 3: 1H NMR spectra of cyclohexene oxide, RCOSO, and COSOCE
Figure 4: 13C NMR spectra of cyclohexene oxide, RCOSO, and COSOCE
In the 13C NMR spectrum of cyclohexene oxide, the peak at 51.92 ppm corresponded to the signal of the No. 1 carbon adjacent to the epoxy group, and this signal shifted toward 34.51 and 72.42 ppm. The peaks located at 24.35 and 19.33 ppm corresponded to the carbon signals of the methylene group (No. 2) on cyclohexene oxide, which were also shifted in the 13C NMR spectrum of COSOCE. In the 13C NMR spectrum of RCOSO, the carboxyl group (No. 3) characteristic peak located at 180.25 ppm, and shifted toward 174.01 ppm in COSOCE. In the 13C NMR curve of COSOCE, peaks characteristic of the double bond (No. 4) [30], and methyl groups (No. 6) in COSOCE were observed at 129.87, and 14.04 ppm, respectively, and the peaks observed at 22.64–34.51 ppm corresponded to the carbon signals of the methylene group on the carbon chain (No. 5) of COSOCE. In summary, the epoxy group of cyclohexene oxide had open loop reactions, and the carboxyl group of RCOSO product an ester group. Based on the results obtained from the 1H NMR and 13C NMR analysis of cyclohexene oxide, RCOSO, and COSOCE, the product of RCOSO and cyclohexene oxide was COSOCE.
Fig. 5 shows the Raman spectra of cyclohexene oxide, RCOSO, and COSOCE. From the Raman spectra of cyclohexene oxide (a) and COSOCE (c), peaks characteristic of the epoxide groups disappeared at 611–989 cm–1 (gray area). In the Raman spectrum between RCOSO (b) and COSOCE (c), the peak at 1655 cm–1 corresponded to that characteristic of C=C bonds, and the new peak observed at 2934 cm–1 corresponded to that characteristic of the ester group. According to the above analysis, COSOCE is successfully produced by the reaction of RCOSO and cyclohexene oxide.
Figure 5: Raman spectra: (a) Cyclohexene oxide, (b) RCOSO, and (c) COSOCE
3.2 Characterization of Modified PVC Materials with Different Formulations
Fig. 6 shows the chemical structural formulas of DOP and COSOCE. The carbon ring structures were represented by pink. DOP comprises a benzene ring as its carbon ring, while COSOCE comprises cyclohexane as its carbon ring. The ester groups were represented by blue. DOP contains two ester functional groups connected in a benzene ring, but COSOCE contains only one ester group. The long carbon-chain structures were represented by red. DOP and COSOCE contain different amounts of carbon in their ester chains, while compared to DOP, COSOCE contains a C=C bonds in its ester chain. The results revealed that the structures of COSOCE and DOP are similar; hence, COSOCE can be used to replace DOP for PVC plasticizing.
Figure 6: Chemical structures: (a) DOP and (b) COSOCE
Fig. 7 shows the Raman spectra of modified PVC materials with different formulations. In the Raman spectrum of modified PVC materials, the peak characteristic of ester was observed at 2937 cm–1 [14], and the signal of H1 was stronger than those of H2, H3, and H4 (Fig. 7). In the Raman spectra of H2, H3, and H4, the peaks characteristic of C=C were observed at 1654 cm–1. The Raman spectra results are consistent with the expected results, and COSOCE at different concentrations are successfully introduced into PVC materials.
Figure 7: Raman spectra of modified PVC materials with different formulations
Fig. 8 shows the SEM images of modified PVC materials with different formulations. By the modified PVC materials as mixtures, those mixing degree were not the same, the compatibility between the components were not the same, resulting different structure of them. For the above reasons, the SEM images of them were something different. The surfaces of the modified PVC materials with four formulations were relatively smooth (Fig. 8). The H1 surface did not exhibit any clear granular shape, but stripe folds. H2, H3 and H4 had rough surface but uniform texture. The results revealed that the compatibility of COSOCE with PVC is less than that of DOP, but COSOCE can be used as a plasticizer to prepare PVC materials.
Figure 8: SEM images of modified PVC materials with different formulations
3.3 Performance Test Results of Modified PVC Materials with Different Formulations
Fig. 9 shows EDS images and analysis results of modified PVC materials with different formulations: C, Cl, and O were detected in films with different formulations (Fig. 9). The O content of modified PVC materials prepared using the COSOCE plasticizer was less than that using DOP (H1: 8.07%). Specific data were as follows: The O contents of H2, H3, and H4 were 3.63%, 5.28%, and 4.05%, respectively. The DOP molecular structure comprised two ester groups, while only one ester group was present in COSOCE. Therefore, the content of O in H1 is significantly greater than that in H3 in the two plasticizers with the same addition amount, and EDS analysis results are consistent with expected results.
Figure 9: EDS analysis of modified PVC materials with different formulations
Figs. 10 and 11 show the contact angle test photographs and analysis of modified PVC materials with different formulations. The contact angles of modified PVC materials were less than 90°C (Fig. 11), indicating that modified PVC materials with four formulations are hydrophilic materials [31]. The water contact angles of PVC materials modified using COSOCE were less than those of PVC materials modified using DOP, and the contact angles increased in the order of H2, H3, and H4. The contact angle of modified PVC materials were related to the addition of COSOE, and increased with the increase of COSOE. It shown that the hydrophilicity of the modified PVC materials were improved, which was caused by the introduction of more hydrophilic hydroxyl groups by the esterification reaction [32,33].
Figure 10: Photographs of the contact angles of modified PVC materials with different formulations
Figure 11: Contact angle analysis of modified PVC materials with different formulations
Fig. 12 shows the tensile test analysis results of modified PVC materials with different COSOCE Mass ratio. The tensile strength of PVC materials modified with different COSOCE concentrations increased in the order of H1, H4, H2, and H3; the tensile strength values were 28.19 ± 1.65, 23.56 ± 2.94, 23.15 ± 0.93, and 18.27 ± 1.93 MPa, respectively, and the corresponding elongation-at-break values were 238.01% ± 84.56%, 95.15% ± 21.84%, 74.77% ± 22.25%, and 79.77% ± 8.91%, respectively. The results revealed that the PVC materials modified with DOP were better than COSOCE. However, COSOCE is a bio-based plasticizer, which has the function of green environmental protection, and it improves the mechanical properties of PVC to some extent. Although the overall mechanical properties are not as good as those of DOP. When PVC is applied with low mechanical properties, but requires environment-friendly plasticizer, it has potential application scenarios.
Figure 12: Mechanical properties of modified PVC materials with different formulations
Figs. 13 and 14 show the TG curves and derivative thermogravimetric (DTG) curves of PVC films with different formulations, respectively, and Table 2 shows the characteristic parameters of the curves. As can be observed in Figs. 13 and 14 and Table 2, the mass loss ratios of H2, H3, and H4 were less than that of H1, and their residual rates were greater than that of H1 within the range of 30°C–600°C, and decreasing by 3.90%–5.75% at 600°C. The data revealed that PVC material modified using the COSOCE plasticizer exhibits better heat resistance. At 30°C–180°C, the modified PVC materials did not exhibit mass loss; hence, in this temperature range, the four modified PVC materials exhibit stable thermal performance. The temperature range of 180°C–400°C corresponded to the first decomposition stage of modified PVC materials, at which thermal decomposition was more rapid, with a higher mass loss. The WP1 (Mass ratio lost at the end of the first decomposition stage) of H1 was greater than 75%, reaching 78.00%, while those of H2, H3, and H4 were less than 75%, decreasing by 5.87%–11.27%. The rapid decomposition of the modified PVC materials in the first stage was mainly related to the formation of HCl after the dissociation of the C–Cl bond. At the same time, the double bond formed on the PVC chain induced the dissociation of several C–Cl bonds, forming a polyene structure and generating a large number of macromolecular free radicals and Cl atoms. The above two reasons caused the continuous decomposition of the modified PVC materials [34]. The temperature range of 400°C–560°C corresponded to the second thermal decomposition stage, which was mainly attributed to the cross-linking of the polyene structure and decomposition of carbon residues [34,35].
Figure 13: TGA curves of modified PVC materials with different formulations
Figure 14: DTG analysis of modified PVC materials with different formulations
As can be observed from Table 2, the T5 and T10 of COSOCE-plasticized PVC materials decreased in the order of H2, H4, and H3, which were 1.17°C–8.17°C and 6.51°C–10.34°C greater than those of H1, respectively. This may be related to the synergistic effect of the molecular volume and COSOCE structure on the orientation of functional groups in PVC materials.
Among the modified PVC materials with different formulations, the TP1 of COSOCE-modified PVC materials decreased in the order of H4, H2, and H3, which were 7.33°C–9.33°C less than that of H1. The VP1 of the modified VC materials decreased in the order of H4, H3, and H2, which were 0.07%/°C–0.17%/°C less than that of H1.
In conclusion, the thermal stability of PVC modified using COSOCE is better than that using DOP, and the thermal stability of 60% COSOCE is better. This result was possibly related to the presence of a large amount of unsaturated fatty acids in COSOCE prepared from C. oleifera seed oil, containing C=C double bonds [36]. In the first thermal decomposition stage, the free radicals generated during the degradation of PVC materials are removed by the C=C double bonds, which slowed down the continuous decomposition rate of PVC materials [19,31,34,37]. In the second decomposition stage, a partial cross-linking reaction occurred with the PVC molecular chain containing the conjugated polyene structure, which increased the movement resistance of the PVC molecular chain segment. Owing to the aforementioned reasons, the thermal stability of PVC materials is improved.
Fig. 15 shows DCS curves of modified PVC materials with different formulations. As can be observed in Fig. 15a glass transition temperature and decomposition exothermic peak for the modified PVC materials with four formulations were not observed at −20°C to 110°C. The results revealed that the PVC materials modified using synthesized COSOCE are stable and can be used at ≤100°C for a long time.
Figure 15: DSC analysis of modified PVC materials with different formulations
(1) PVC materials modified using COSOCE exhibited a good surface morphology. Combined with EDS analysis and contact angle measurement results, COSOCE-modified PVC was confirmed to be a hydrophilic material. Hence, COSOCE can be used as a plasticizer for PVC materials.
(2) The PVC material modified using 60% COSOCE exhibited the best mechanical properties, and its tensile strength reached 23.56 ± 2.94 MPa.
(3) The mass loss ratios of H2, H3, and H4 were less than that of H1, and their residual rates were greater than that of H1 within the range of 30°C–600°C, and decreasing by 3.90%–5.75% at 600°C. The T5 and T10 of COSOCE-plasticized PVC materials decreased in the order of H2, H4, and H3, which were 1.17°C–8.17°C and 6.51°C–10.34°C greater than those of H1, respectively. Hence, PVC materials modified using the COSOCE plasticizer exhibit better heat resistance and demonstrate potential for use as a PVC plasticizer.
(4) At 20°C to 110°C, COSOCE-modified PVC materials did not exhibit a glass transition temperature and decomposition exothermic peak; hence, it can be used at ≤100°C for a long time.
COSOCE, a natural plasticizer made from C. oleifera seed-oil, has a simple production process. Compared with DOP, it has no obvious improvement in mechanical properties, but it has more advantages in hydrophilicity and thermal stability. More importantly, it is green, and friendly with biological and environmental, which is in line with the concept of green sustainable development. Therefore, COSOCE has the potential to replace DOP.
Funding Statement: The authors express their gratitude for the financial support from the National Natural Science Foundation of China (32101475), the Yuemu Technology Plan Project (YMKJ202201).
Conflicts of Interest: The authors declare that they have no conflicts of interest to report regarding the present study.
References
1. Ma, Y., Song, F., Yu, J., Wang, N., Jia, P. et al. (2022). Combining renewable eleostearic acid and eugenol to fabricate sustainable plasticizer and its effect of plasticizing on PVC. Journal of Polymers and the Environment, 30(5), 2099–2108. https://doi.org/10.1007/s10924-021-02341-w [Google Scholar] [CrossRef]
2. Zampino, D., Mancuso, M., Zaccone, R., Ferreri, T., Borzacchiello, A. et al. (2021). Thermo-mechanical, antimicrobial and biocompatible properties of PVC blends based on imidazolium ionic liquids. Materials Science and Engineering: C, 122, 111920. [Google Scholar] [PubMed]
3. Tüzüm Demir, A. P., Ulutan, S. (2012). Migration of phthalate and non-phthalate plasticizers out of plasticized PVC films into air. Journal of Applied Polymer Science, 77. https://doi.org/10.1002/app.38291 [Google Scholar] [CrossRef]
4. Bouchoul, B., Benaniba, M. T. (2021). Assessment of derived sunflower oil as environmentally friendly plasticizers in poly vinyl chloride. Polímeros, 31(3). https://doi.org/10.1590/0104-1428.20210015 [Google Scholar] [CrossRef]
5. You, J., Jiang, Z., Jiang, H., Qiu, J., Li, M. et al. (2022). A plasticizing-foaming-reinforcing approach for creating thermally insulating PVC/polyurea blend foams with shape memory function. Chemical Engineering Journal, 450(15), 138071. https://doi.org/10.1016/j.cej.2022.138071 [Google Scholar] [CrossRef]
6. Nilsen Nygaard, J., Fernández, E. N., Radusin, T., Rotabakk, B. T., Sarfraz, J. et al. (2021). Current status of biobased and biodegradable food packaging materials: Impact on food quality and effect of innovative processing technologies. Comprehensive Reviews in Food Science and Food Safety, 20(2), 1333–1380. https://doi.org/10.1111/1541-4337.12715 [Google Scholar] [PubMed] [CrossRef]
7. Priyadarshi, R., Rhim, J. (2020). Chitosan-based biodegradable functional films for food packaging applications. Innovative Food Science & Emerging Technologies, 62(2), 102346. https://doi.org/10.1016/j.ifset.2020.102346 [Google Scholar] [CrossRef]
8. Ma, Y., Song, F., Hu, Y., Kong, Q., Liu, C. et al. (2020). Highly branched and nontoxic plasticizers based on natural cashew shell oil by a facile and sustainable way. Journal of Cleaner Production, 252(2), 119597. https://doi.org/10.1016/j.jclepro.2019.119597 [Google Scholar] [CrossRef]
9. Gerassimidou, S., Martin, O. V., Chapman, S. P., Hahladakis, J. N., Iacovidou, E. (2021). Development of an integrated sustainability matrix to depict challenges and trade-offs of introducing bio-based plastics in the food packaging value chain. Journal of Cleaner Production, 286(4), 125378. https://doi.org/10.1016/j.jclepro.2020.125378 [Google Scholar] [CrossRef]
10. Ögmundarson, Ó., Sukumara, S., Laurent, A., Fantke, P. (2019). Environmental hotspots of lactic acid production systems. Global Change Biology Bioenergy, 12(1), 19–38. https://doi.org/10.1111/gcbb.12652 [Google Scholar] [CrossRef]
11. Dong, F., Yang, X., Guo, L., Wang, Y., Shaghaleh, H. et al. (2022). Self-healing polyurethane with high strength and toughness based on a dynamic chemical strategy. Journal of Materials Chemistry A, 10(18), 10139–10149. https://doi.org/10.1039/D2TA00802E [Google Scholar] [CrossRef]
12. Sun, P., Wang, S., Huang, Z., Zhang, L., Dong, F. et al. (2022). Water-resistant, strong, degradable and recyclable rosin-grafted cellulose composite paper. Green Chemistry, 24(19), 7519–7530. https://doi.org/10.1039/D2GC02372E [Google Scholar] [CrossRef]
13. Jariyasakoolroj, P., Leelaphiwat, P., Harnkarnsujarit, N. (2020). Advances in research and development of bioplastic for food packaging. Journal of the Science of Food and Agriculture, 100(14), 5032–5045. https://doi.org/10.1002/jsfa.9497 [Google Scholar] [PubMed] [CrossRef]
14. Wang, S., Yu, L., Wang, S., Zhang, L., Chen, L. et al. (2022). Strong, tough, ionic conductive, and freezing-tolerant all-natural hydrogel enabled by cellulose-bentonite coordination interactions. Nature Communications, 13(1), 3408. https://doi.org/10.1038/s41467-022-30224-8 [Google Scholar] [PubMed] [CrossRef]
15. Wang, S., Sun, P., Xu, X., Liu, H., Wang, D. et al. (2022). Rosin-based Si/P-containing flame retardant toward enhanced fire safety polyurethane foam. Advanced Engineering Materials, 24(4), 2101044. https://doi.org/10.1002/adem.202101044 [Google Scholar] [CrossRef]
16. Liu, X., Yang, X., Wang, S., Wang, S., Wang, Z. et al. (2021). Fully bio-based polyhydroxyurethanes with a dynamic network from a terpene derivative and cyclic carbonate functional soybean oil. ACS Sustainable Chemistry & Engineering, 9(11), 4175–4184. https://doi.org/10.1021/acssuschemeng.1c00033 [Google Scholar] [CrossRef]
17. Sharma, V., Kundu, P. P. (2006). Addition polymers from natural oils—A review. Progress in Polymer Science, 31(11), 983–1008. https://doi.org/10.1016/j.progpolymsci.2006.09.003 [Google Scholar] [CrossRef]
18. Dutta, N., Bhadra, B., Gogoi, G., Kumar Maji, T. (2021). Development of polyvinyl chloride/waste rice husk ash/modified montmorillonite nanocomposite using epoxidized soybean oil as green additive substituting synthetic plasticizer and compatibiliser. Cleaner Materials, 2(4), 100033. https://doi.org/10.1016/j.clema.2021.100033 [Google Scholar] [CrossRef]
19. Feng, S., Zhang, P., Jiang, P., Zhang, Z., Deng, J. et al. (2022). Synthesis and application of high-stability bio-based plasticizer derived from ricinoleic acid. European Polymer Journal, 169(7), 111125. https://doi.org/10.1016/j.eurpolymj.2022.111125 [Google Scholar] [CrossRef]
20. Rozaki, N. Z., Gan, S., Ang, D. T. (2017). Environmentally friendly oil-modified polyesters as polymeric plasticizers for poly(vinyl chloride). Journal of Polymers and the Environment, 25(2), 286–295. https://doi.org/10.1007/s10924-016-0810-7 [Google Scholar] [CrossRef]
21. Lin, P., Wang, K., Zhou, C., Xie, Y., Yao, X. et al. (2018). Seed transcriptomics analysis in Camellia oleifera uncovers genes associated with oil content and fatty acid composition. International Journal of Molecular Sciences, 19(1), 118. [Google Scholar] [PubMed]
22. Liu, L., Feng, S., Chen, T., Zhou, L., Yuan, M. et al. (2021). Quality assessment of Camellia oleifera oil cultivated in Southwest China. Separations, 8(9), 144. [Google Scholar]
23. Yang, X., Ren, C., Liu, X., Sun, P., Xu, X. et al. (2021). Recyclable non-isocyanate polyurethanes containing dynamic covalent network derived from epoxy soybean oil and CO2. Materials Chemistry Frontiers, 16(5), 6160–6170. [Google Scholar]
24. Qian, Y., Dong, F., Guo, L., Xu, X., Liu, H. (2021). Two-component waterborne polyurethane modified with terpene derivative-based polysiloxane for coatings via a thiol-ene click reaction. Industrial Crops and Products, 171, 113903. [Google Scholar]
25. Dong, F., Qian, Y., Xu, X., Shaghaleh, H., Guo, L. et al. (2021). Preparation and characterization of UV-curable waterborne polyurethane using isobornyl acrylate modified via copolymerization. Polymer Degradation and Stability, 184, 109474. [Google Scholar]
26. Zhao, T., Yuan, W., Li, Y., Weng, Y., Zeng, J. (2018). Relating chemical structure to toughness via morphology control in fully sustainable sebacic acid cured epoxidized soybean oil toughened polylactide blends. Macromolecules, 51(5), 2027–2037. https://doi.org/10.1021/acs.macromol.8b00103 [Google Scholar] [CrossRef]
27. Qian, Y., Dong, F., Guo, L., Xu, X., Liu, H. (2021). Terpene derivative-containing silicone two-component waterborne polyurethane for coatings. Progress in Organic Coatings, 153(6), 106137. https://doi.org/10.1016/j.porgcoat.2021.106137 [Google Scholar] [CrossRef]
28. Fan, X., Yang, X., Wang, S., Wang, S., Xu, X. et al. (2021). Modified cellulose nanocrystals are used to enhance the performance of self-healing siloxane elastomers. Carbohydrate Polymers, 273(1), 118529. https://doi.org/10.1016/j.carbpol.2021.118529 [Google Scholar] [PubMed] [CrossRef]
29. Pan, S., Hou, D., Chang, J., Xu, Z., Wang, S. et al. (2019). A potentially general approach to aliphatic ester-derived PVC plasticizers with suppressed migration as sustainable alternatives to DEHP. Green Chemistry, 21(23), 643–644. https://doi.org/10.1039/C9GC03077H [Google Scholar] [CrossRef]
30. Liu, D., Shen, Y., Jiang, P., Thin Wai, P., Zhang, Z. et al. (2021). An efficient cold-resistant strategy: Synthesis and application of green cold-resistant bio-based plasticizer for poly(vinyl chloride). European Polymer Journal, 142, 110154. https://doi.org/10.1016/j.eurpolymj.2020.110154 [Google Scholar] [CrossRef]
31. Law, K. (2014). Definitions for hydrophilicity, hydrophobicity, and superhydrophobicity: Getting the basics right. The Journal of Physical Chemistry Letters, 5(4), 686–688. https://doi.org/10.1021/jz402762h [Google Scholar] [PubMed] [CrossRef]
32. Chen, R., Mao, L., Matindi, C. N., Liu, G., He, J. et al. (2022). Tailoring the micro-structure of PVC/SMA-g-PEG blend ultrafiltration membrane with simultaneously enhanced hydrophilicity and toughness by in situ reaction-controlled phase inversion. Journal of Membrane Science, 653, 120545. https://doi.org/10.1016/j.memsci.2022.120545 [Google Scholar] [CrossRef]
33. Aji, M. M., Narendren, S., Purkait, M. K., Katiyar, V. (2020). Utilization of waste polyvinyl chloride (PVC) for ultrafiltration membrane fabrication and its characterization. Journal of Environmental Chemical Engineering, 8(2), 103650. https://doi.org/10.1016/j.jece.2019.103650 [Google Scholar] [CrossRef]
34. Chen, J., Liu, Z., Nie, X., Jiang, J. (2018). Synthesis and application of a novel environmental C26 diglycidyl ester plasticizer based on castor oil for poly(vinyl chloride). Journal of Materials Science, 53(12), 8909–8920. https://doi.org/10.1007/s10853-018-2206-7 [Google Scholar] [CrossRef]
35. Abd El-Kader, M. F. H., Awwad, N. S., Ibrahium, H. A., Ahmed, M. K. (2021). Graphene oxide fillers through polymeric blends of PVC/PVDF using laser ablation technique: Electrical behavior, cell viability, and thermal stability. Journal of Materials Research and Technology, 13(13), 1878–1886. https://doi.org/10.1016/j.jmrt.2021.05.024 [Google Scholar] [CrossRef]
36. Kwon, C. W., Chang, P. (2021). Influence of alkyl chain length on the action of acetylated monoglycerides as plasticizers for poly(vinyl chloride) food packaging film. Food Packaging and Shelf Life, 27(4), 100619. https://doi.org/10.1016/j.fpsl.2020.100619 [Google Scholar] [CrossRef]
37. Qu, H., Liu, X., Xu, J., Ma, H., Jiao, Y. et al. (2014). Investigation on thermal degradation of poly(1,4-butylene terephthalate) filled with aluminum hypophosphite and trimer by thermogravimetric analysis-fourier transform infrared spectroscopy and thermogravimetric analysis-mass spectrometry. Industrial & Engineering Chemistry Research, 53(20), 8476–8483. https://doi.org/10.1021/ie404297r [Google Scholar] [CrossRef]
Cite This Article
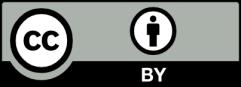
This work is licensed under a Creative Commons Attribution 4.0 International License , which permits unrestricted use, distribution, and reproduction in any medium, provided the original work is properly cited.