Open Access
ARTICLE
Carbon Capture from Flue Gas Based on the Combination of Non-Contact Hydrophobic Porous Ceramic Membrane and Bubbling Absorption
College of Materials Science and Engineering, Nanjing Tech University, Nanjing, 211816, China
* Corresponding Authors: Jiang Jin. Email: ; Hua Zhang. Email:
(This article belongs to the Special Issue: Porous Materials for Sustainable Development)
Journal of Renewable Materials 2023, 11(7), 3143-3153. https://doi.org/10.32604/jrm.2023.027396
Received 01 November 2022; Accepted 23 December 2022; Issue published 05 June 2023
Abstract
A hybrid system combined with a non-contact membrane and bubbling absorption is proposed to capture CO2 from flue gas. The non-contact way of membrane and liquid absorbent effectively avoids the reduction of gas diffusion flux through the membrane. High-porosity ceramic membranes in hybrid systems are used for gas-solid separation in fuel gas treatment. Due to the high content of H2O and cement dust in the flue gas of the cement plant, the membrane is hydrophobically modified by polytetrafluoroethylene (PTFE) to improve its anti-water, anti-fouling, and self-cleaning performances. The results show that the diffusion flux of CO2 through the membrane is still higher than 7.0 × 10−3 mol/m2 s (20% CO2 concentration) even under the influence of water and cement dust. In addition, slaked lime selected as the absorbent is cheap and the product after bubbling absorption is nano-scale light calcium carbonate. To sum up, the hybrid system combining non-contact membrane and bubbling absorption is expected to be used to capture carbon dioxide from the flue gas of the cement plant.Keywords
The global climate has rapidly deteriorated in recent years due to the greenhouse effect, mostly caused by excessive carbon dioxide emissions. It is vitally necessary to reduce carbon emissions since the average amount of CO2 in the atmosphere is rising at an alarming pace of 3 ppm per year, already reaching 418 ppm by July 2022 [1]. In order to reduce CO2 emissions, efficient and economic separation and recovery of CO2 from the flue gas after combustion has become one of the main contents of sustainable development in the future. Research on the combustion process stage is currently devoted to chemical cycle combustion (CLC) [2]. Considering that some industrial environments cannot promote the carbon capture process from the combustion process stage, recent carbon reduction research focuses on the development of post-combustion carbon capture technology [3]. The applicability of the technology and the feasibility of installation make it more promising for industrial applications in the flue gas treatment process [4]. However, due to the high content of carbon dioxide (20%~30%), cement dust, and water in the cement plant’s flue gas, the development of post-combustion carbon capture technology is limited [5]. Considering the economics of CO2 capture projects in the cement industry, we should consider the complexity of the carbon capture process, the absorbent cost, and the products’ economic benefits [6].
In post-combustion carbon capture technology, membrane technology has shown the advantages of low energy consumption, simple equipment, etc. At present, there are extensive studies on gas-liquid contact membrane systems, and the characteristics of this system refer to direct contact between adsorbent and membrane material [7,8]. A gas-liquid contact membrane system is a hybrid system that combines membrane and absorbent absorption [9]. The absorbent carries out the selective absorption of CO2 from the flue gas in this system [3]. Compared to conventional absorption devices, the hybrid system has the features of operational flexibility, easy scale-up, and modularity. It was considered a promising alternative to conventional technologies for CO2 removal [10,11]. In hybrid systems, demands are placed on the performances of membrane materials, such as low diffusion resistance and good thermal and chemical stability, especially in industrial environments. For example, cement plants and membrane materials’ thermal stability need special attention. Porous ceramic membranes have the potential to be used for capturing CO2 in high-temperature flue gases due to their high mechanical strength, thermal stability, and chemical stability [12–14].
To avoid introducing additional mass transfer resistance, the membrane used in gas-liquid contact membrane systems should provide an effective barrier between the flue gas and the absorbent [15]. Therefore, the surface of the ceramic membrane in this system usually needs to be hydrophobically modified [16–18]. The surface contact angle between the liquid and the solid decreases as the temperature increases. Even if a hydrophobic modifier modifies the membrane, the surface of the gas-liquid contact membrane is easily wetted at high temperatures. The wetting of membranes has been limiting the further development of gas-liquid contact membrane systems [19–22]. A hybrid system with a combination of non-contact membranes and bubbling absorption is proposed to address the problem of contact membranes. On the one hand, the non-contact approach between the membrane and the liquid absorbent expands the selection of the membrane. On the other hand, the non-contact approach effectively avoids the decrease of gas diffusion flux through the membrane due to the wetting of the membrane by the liquid absorbent.
In addition, gas-liquid systems require attention to the choice of absorbent. At present, amine solvents are the most studied CO2 absorbents [23–27]. Although the carbon capture rate of amine solvents is high, the amine desorption process has the problems of high cost, high energy consumption, and low economic efficiency [28,29]. This greatly limits the development of gas-liquid contact membrane systems [30,31]. In order to minimize the cost of the carbon capture process, Ca(OH)2 solution (slaked lime) was chosen as the absorbent for this work. Furthermore, appropriate absorption methods are also important for the entire carbon capture process. Compared to CO2 absorption methods such as spray absorption and reflux tower absorption, the bubbling absorption method has the advantages of small unit size and high operational flexibility. The carbon dioxide reacts with absorbent in a bubbling carbonization unit.
The membrane material in this work is high porosity ceramic membrane, which is hydrophobically modified with PTFE. The diffusion flux of CO2 through the membrane, anti-water, anti-fouling and self-cleaning performances are discussed in detail. Furthermore, several bubbling absorption methods are compared, and the products are characterized to assess the feasibility and suitability of the hybrid system proposed in this paper.
2.1 Fabrication and Characterization of Hydrophobic High Porosity Ceramic Membranes
The fabrication procedure of high porosity ceramic membranes (HPCM) was described in previous works [32]. Alumina fiber, pore-making agent, glass powder, deionized water, and carboxymethyl cellulose was mixed thoroughly and pressed into the cylindrical body (ϕ 32 mm × 3 mm). The green body was sintered at 1300°C for 1 h.
Polytetrafluoroethylene dispersion (PTFE, 60 wt.%) was used for the surface modification of HPCM. The HPCM were soaked in PTFE dispersion (5, 10, 20, 30, 40 wt.%) for 30 min, dried at 70°C for 1 h and cured at 260°C for 2 h. The samples were labeled as 5-PTFE-HPCM, 10-PTFE-HPCM, 15-PTFE-HPCM, 20-PTFE-HPCM, 30-PTFE-HPCM, and 40-PTFE-HPCM.
The microstructure and morphology of high porosity ceramic membrane (HPCM) and hydrophobic modified high porosity ceramic membrane (PTFE-HPCM) were characterized by scanning electron microscopy (SEM, JSM-6510, JEOL, Ltd., Tokyo, Japan). The distribution of elements on the surface of the ceramic membrane was analyzed using an energy dispersive spectrum (EDS). (JEOL Ltd., Tokyo, Japan) The hydrophobicity of PTFE-modified samples was characterized based on the water contact angle (CA), which was measured using the contact angle system DSA 100 (KRÜSS GmbH, Hamburg, Germany). The thermal stability of the hydrophobic layer was characterized by a thermogravimetric analyzer (TG, NETZSCH-STA-449-F5, Germany).
2.2 Determination of CO2 Diffusion Flux through the Ceramic Membrane
The schematic diagram for detecting the diffusion flux of carbon dioxide through the ceramic membrane is shown in Fig. 1. A mass flow controller controls the CO2 concentration on both sides of the membrane. The diffusion flux of CO2 through the membrane is calculated as follows (1):
Figure 1: Schematic diagram of experimental device and diffusion principle
where ρ is the gaseous CO2 density under standard conditions (g/L), V is the volume of CO2 (L), M stands for molar mass of CO2 (g/mol), S is the effective area of the ceramic membrane (m2) and t is the effective diffusion time (s).
The structural parameters of the two ceramic membranes used in the experiment are shown in Table 1. The diffusion fluxes of carbon dioxide through the two membranes were measured separately.
In order to discuss the effect of water on the diffusion flux of carbon dioxide through the membrane, a combination of a heating device and a steam generator was used to control the content of H2O in the inlet gas during the experiment.
The self-cleaning performance of the ceramic membrane was studied by simulation experiment. The details of the simulation experiment are as follows: The surface of ceramic membrane was coated with cement dust and then cleaned with H2O, and the procedure was repeated several times to simulate working conditions. During the experiment, the diffusion flux of carbon dioxide through the membrane was detected to evaluate the change of self-cleaning performance of ceramic membrane.
2.3 Bubbling Absorption Experimental
Carbon dioxide passes through the ceramic membrane and is pumped into the unit of bubbling absorption. After the bubbling absorption unit has purified the gas mixture to remove CO2, the remainder is vented back to position B in Fig. 1 to maintain an isobaric environment on both sides of the ceramic membrane. Isobaric conditions prevent large amounts of cement dust and other contaminants from entering the pores of the ceramic membrane under pressure. This avoids the reduction of the diffusion flux of carbon dioxide through the porous ceramic membrane. And the service life of the ceramic membrane is greatly extended.
In order to find a better bubbling absorption method, three different bubbling absorption methods were compared. The experiment was carried out at room temperature with clarified lime water as the absorbent, a bubbling rate of 20 L/min and a CO2 concentration of 20%. The bubbling absorption methods are described as follows and the details are shown in Fig. 2. Method A (straight-through): Mixed gas (20%CO2, 80%N2) directly enters the absorbent through the pipeline; Method B (mechanical pump agitation): The gas mixture and the absorbent are fed together into the mixing tank, where the contact area between the gas mixture and the absorbent is greatly increased by the stirring action of the mechanical pump; Method C (ceramic single-tube aeration): The mixed gas enters the carbonization tank in the form of small bubbles after passing through the membrane hole of the porous ceramic single tube.
Figure 2: Diagram of the three different types of bubbling absorption
3.1 Effect of Hydrophobic Modification on the Performance of HPCM
As shown in Fig. 3a, the diffusion flux of CO2 through the HPCM is significantly higher than the diffusion flux of CO2 through the LPCM. Therefore, subsequent experiments are mainly carried out on HPCM.
Figure 3: Effect of (a) porosity and (b) modifier concentration on the diffusion flux of CO2 through membrane, (c) surface contact angle of membrane
Fig. 3b shows that the diffusion flux of CO2 through membrane decreases with the increase of hydrophobic modifier concentration. The modifier of less than 10% has little effect on the diffusion flux of CO2 through the ceramic membrane. When the modifier concentration exceeds 10%, the diffusion flux starts to drop steeply. Obviously, the addition of modifier will introduce additional diffusion resistance to the membrane. When the modifier concentration is too high, excess modifier accumulates in the membrane’s pores, introducing additional mass transfer resistance. According to the data in Fig. 3b, less than 10% modifier is suitable for hydrophobic modification of HPCM. As shown in Fig. 3c, the ceramic membrane obtained good hydrophobicity after hydrophobic modification. The surface contact angle of 10-PTFE-HPCM is as high as 135°. It can be seen from Fig. 3b that the CO2 concentration also significantly affects the diffusion flux of CO2 through the membrane. Considering that the CO2 concentration in the cement plant flue gas is about 20%~30%, the CO2 concentration of subsequent experiments is controlled at 20%.
The microstructure and morphology of HPCM and 10-PTFE-HPCM were observed by scanning electron microscopy as shown in Figs. 4a, 4b. The surface of the ceramic fiber in HPCM is smooth, while the surface of the ceramic fiber in HPCM appears to have a lot of granular attachments. As shown in Figs. 4b, 4c, SEM images and EDS elemental mapping of fluorine show that the attachment is PTFE. In addition, Figs. 4a, 4b, 4d and 4e show that the pores begin to be blocked with the modifier as the modifier concentration increases.
Figure 4: SEM images of (a) HPCM, (b) 10-PTFE-HPCM, (c) EDS mapping of F element for 10-PTFE-HPCM, (d) 20-PTFE-HPCM, (e) 30-PTFE-HPCM
3.2 Effect of H2O in Flue Gas on CO2 Gas Diffusion Flux
Fig. 5a shows the effect of H2O in the flue gas on the diffusion flux of CO2 through the ceramic membrane. When the experimental temperature (150°C) is reached, H2O is introduced into the gas mixture and the diffusive flux of CO2 through the membrane is examined. Fig. 5a shows that the diffusive flux of CO2 through the membrane decreases significantly when H2O is introduced into the gas mixture. It has been analyzed that the diffusion process is introduced with additional mass transfer resistance due to the membrane being easily wetted. The diffusion flux of carbon dioxide through the 5-PTFE-HPCM first decreases and then stabilizes. This may be due to the poor hydrophobicity of the surface, which leads to partial wetting of the membrane and additional mass transfer resistance. However, the diffusion flux of carbon dioxide through 10-PTFE-HPCM remained constant and stabilized at 9.7 × 10−3 mol/m2. Therefore, the subsequent experiments were mainly carried out on 10-PTFE-HPCM.
Figure 5: (a) Effect of H2O in flue gas on CO2 gas diffusion fluxes of HPCM and 10-PTFE-HPCM, (b) thermogravimetric curve of 10-PTFE-HPCM
Fig. 5b shows the thermogravimetric curves of 10-PTFE-HPCM from room temperature to 800°C. The quality of the sample is basically stable before 400°C. In the process of industrial application, the flue gas temperature generally does not exceed 250°C. Therefore, PTFE-HPCM can be used in high-temperature environments under industrial conditions.
3.3 Anti-Fouling and Self-Cleaning Performances of Ceramic Membranes
As shown in Fig. 6, the simulation experiment of membrane self-cleaning performance illustrates ceramic membranes’ anti-water and anti-fouling performances. The surface of both HPCM and 10-PTFE-HPCM was covered with cement dust. After spraying a drop of water on the HPCM, the surface of the HPCM is wetted. Cement dust and water attach to the surface of the ceramic membrane together, forming a layer of dirt. However, the complete liquid droplet formed on the membrane surface when above operation was repeated for 10-PTFE-HPCM. As the water drops roll, the cement dust is carried away by the water droplet and the surface of the ceramic membrane is cleaned. Therefore, hydrophobic modification can significantly improve ceramic membranes’ anti-water and anti-fouling performances.
Figure 6: The pictures of the self-cleaning performance simulation experiment on HPCM and 10-PTFE-HPCM
Fig. 7a shows the effect of cement dust covering and water cleaning on the diffusion flux of CO2 through membrane. After the ceramic membrane is covered with cement dust several times, the diffusion flux of CO2 through the membrane starts to decrease slightly. The diffusion flux of CO2 through the HPCM decreases rapidly when the cleaning by water starts. However, the diffusion flux of CO2 through the 10-PTFE-HPCM under same conditions remained essentially stable at 7.07 × 10−3 mol/m2s. These results indicate that the modified ceramic membrane has superior self-cleaning performances.
Figure 7: The anti-water, anti-fouling, and self-cleaning performances of ceramic membranes
As shown in Fig. 7b, after contamination of the unmodified ceramic membrane, the recovery effect of the diffusion flux of CO2 through ceramic membrane was still poor even after the ceramic membrane was rinsed and dried in time. However, when the modified ceramic membrane was rinsed and dried in time, the diffusion flux of CO2 through the modified ceramic membrane recovered remarkably. It is further shown that the performance of anti-water, anti-fouling, and self-cleaning of hydrophobic modified ceramic membranes is significantly improved. The PTFE-HPCM has the characteristics of strong applicability and wide application range, which is expected to be used in carbon capture membrane technology.
3.4 Comparative Analysis of Different Bubbling Carbonization Absorption Modes
Table 2 shows the production formation rates of the product (CaCO3) for the different bubbling absorption methods. The fastest production formation rate of the product was achieved by method B. This is due to the large gas-liquid contact area and reaction time in the absorption process. The stirring effect of the mechanical pump also reduces the product agglomeration. Therefore, the mechanical pump stirring method is more suitable for the absorption of carbon dioxide in gas mixtures.
In addition, the effect of cement dust on the purity of the absorption product can be ignored during the bubbling absorption stage, because the gas mixture first passes through the ceramic membrane and the cement dust has been removed.
3.5 Characterization of Absorption Products
After extraction and drying, the product is calcium carbonate with high whiteness as shown in Figs. 8a, 8b. The XRD pattern of the product (CaCO3) of method B is shown in Fig. 8a. It matches well with calcite (PDF 85-1108). The SEM image of the absorption sample is shown in Fig. 8c. Most of the crystals are cubes with particle sizes ranging from 50 to 200 nm. These results indicate that the product obtained by method B is qualified for nano-scale light calcium carbonate.
Figure 8: (a) XRD, (b) Physical and (c) SEM images of products
In this study, CO2 first passes through PTFE-HPCM and then is sent to the bubble absorption unit to complete purification and absorption. The suitability and feasibility of the proposed hybrid system (non-contact PTFE-HPCM combined with bubbling absorption) for carbon capture in the flue gas were analyzed and evaluated. The conclusions are summarized as follows:
1. PTFE-modified HPCM has good anti-water and anti-fouling performances. The concentration of 10 wt.% modifier has a low effect on the diffusion flux of CO2 through the membrane, and the membrane (10-PTFE HPCM) with this modified concentration has good hydrophobicity. Even under contaminated conditions, the diffusion flux of CO2 through the membrane can be maintained at around 7.0 × 10−3 mol/m2s.
2. The 10-PTFE-HPCM has good self-cleaning performances, with a stable diffusion flux of CO2 through the membrane of 7.0 × 10−3 mol/m2s~7.34 × 10−3 mol/m2s within 5 h.
3. The mechanical pump stirring method among the different bubbling absorption methods had a high product formation rate (5.41 g/min) with a product of 50~200 nm nano-scale light calcium carbonate. The whole CO2 capture and absorption process is environmentally friendly and has low energy consumption.
In conclusion, a hybrid system combining non-contact membrane and bubbling absorption developed in this work is feasible for CO2 capture in flue gas, especially for CO2 capture in cement plant flue gas, and is considered as a potentially effective carbon capture technology.
Funding Statement: The authors received no specific funding for this study.
Conflicts of Interest: The authors declare that they have no conflicts of interest to report regarding the present study.
References
1. National Oceanic and Atmospheric Administration, NASA. (2022). Carbon dioxide-climate change: Vital signs of the planet. https://climate.nasa.gov/vital-signs/carbon-dioxide [Google Scholar]
2. Gong, Y., Wang, X., Chen, D., Al-Qadri, B. M. H. (2021). Retrospect and prospect of carbon stripper technology in solid-fuel chemical looping combustion. Fuel Processing Technology, 221, 106920. [Google Scholar]
3. Chao, C., Deng, Y., Dewil, R., Baeyens, J., Fan, X. (2021). Post-combustion carbon capture. Renewable and Sustainable Energy Reviews, 138, 110490. [Google Scholar]
4. Abdolahi-Mansoorkhani, H., Seddighi, S. (2020). CO2 capture by modified hollow fiber membrane contactor: Numerical study on membrane structure and membrane wettability. Fuel Processing Technology, 209(12), 106530. [Google Scholar]
5. Pedraza, J., Zimmermann, A., Tobon, J., Schomäcker, R., Rojas, N. (2021). On the road to net zero-emission cement: Integrated assessment of mineral carbonation of cement kiln dust. Chemical Engineering Journal, 408, 127346. [Google Scholar]
6. Paltsev, S., Morris, J., Kheshgi, H., Herzog, H. (2021). Hard-to-abate sectors: The role of industrial carbon capture and storage (CCS) in emission mitigation. Applied Energy, 300(1), 117322. [Google Scholar]
7. Lee, H. J., Kim, M. K., Park, J. H. (2020). Decompression stripping of carbon dioxide from rich monoethanolamine through porous hydrophobic modified ceramic hollow fiber membrane contactor. Separation and Purification Technology, 236(1–2), 116304. [Google Scholar]
8. Saud, I. H., Othman, M. H., Hubadillah, S. K., Aziz, M. H., Pauzan, M. A. et al. (2020). Superhydrophobic ceramic hollow fibre membranes for trapping carbon dioxide from natural gas via the membrane contactor system. Journal of the Australian Ceramic Society, 57(3), 705–717. [Google Scholar]
9. Chuah, C. Y., Kim, K., Lee, J., Koh, D., Bae, T. (2020). CO2 absorption using membrane contactors: Recent progress and future perspective. Industrial & Engineering Chemistry Research, 59(15), 6773–6794. [Google Scholar]
10. Paris, J. M., Roessler, J. G., Ferraro, C. C., DeFord, H. D., Townsend, T. G. (2016). A review of waste products utilized as supplements to Portland cement in concrete. Journal of Cleaner Production, 121, 1–18. [Google Scholar]
11. Sheng, M., Dong, S., Qiao, Z., Li, Q., Yuan, Y. et al. (2021). Large-scale preparation of multilayer composite membranes for post-combustion CO2 capture. Journal of Membrane Science, 636, 119595. [Google Scholar]
12. Chen, T., Xu, Y., Zhang, Y., Gong, Y., Zhang, Y. et al. (2022). Double-layer ceramic-carbonate hollow fiber membrane with superior mechanical strength for CO2 separation. Journal of Membrane Science, 658(24), 120701. [Google Scholar]
13. Dong, B., Yang, M., Wang, F., Wang, J., Hao, L. et al. (2019). Production and characterization of durable self-cleaning and engineering porous Al2O3/CaAl12O19 ceramic membranes. Journal of the American Ceramic Society, 102(7), 3879–3886. [Google Scholar]
14. Liang, D., Huang, J., Zhang, H., Fu, H., Zhang, Y. et al. (2021). Influencing factors on the performance of tubular ceramic membrane supports prepared by extrusion. Ceramics International, 47(8), 10464–10477. [Google Scholar]
15. Yuan, K., Li, H., Jin, X., Li, C., Wang, X. et al. (2022). Electrospun flexible calcium zirconate fiber membrane with excellent thermal stability and alkali resistance. Ceramics International, 48(9), 12408–12414. [Google Scholar]
16. Kim, S., Scholes, C. A., Heath, D. E., Kentish, S. E. (2021). Gas-liquid membrane contactors for carbon dioxide separation: A review. Chemical Engineering Journal, 411(2), 128468. [Google Scholar]
17. Chen, X., Dai, C., Zhang, T., Xu, P., Ke, W. et al. (2022). Efficient construction of a robust PTFE/Al2O3 hydrophobic membrane for effective oil purification. Chemical Engineering Journal, 435, 134972. [Google Scholar]
18. Cui, Q., Shang, Y., Fei, Z., Tu, T., Yan, S. (2022). Hydrophobic-hydrophilic janus ceramic membrane for enhancing the waste heat recovery from the stripped gas in the carbon capture process. ACS Sustainable Chemistry & Engineering, 10(12), 3817–3828. [Google Scholar]
19. Guo, X., Wang, H., Tian, R., Yin, H., Qiu, Y. et al. (2022). Optimization of preparation process and characterization for hydrophobic α-Al2O3 ceramic membrane. Materials Chemistry and Physics, 276(16), 125280. [Google Scholar]
20. Wang, J., Li, X., Fan, M., Gu, J., Hao, L. et al. (2017). Porous β-Sialon planar membrane with a robust polymer-derived hydrophobic ceramic surface. Journal of Membrane Science, 535, 63–69. [Google Scholar]
21. Chang, P. T., Baharuddin, I. M., Ng, Q. H., Teoh, G. H., Ahmad, A. L. et al. (2022). Creating membrane-air-liquid interface through a rough hierarchy structure for membrane gas absorption to remove CO2. International Journal of Energy Research, 46(1), 5067–5082. [Google Scholar]
22. Li, L., Ma, G., Pan, Z., Zhang, N., Zhang, Z. (2020). Research progress in gas separation using hollow fiber membrane contactors. Membranes, 10(12), 380. [Google Scholar] [PubMed]
23. Qi, W., Fu, K., Chen, X., Qiu, M., Fan, Y. (2022). Falling liquid-film on hydrophilic porous ceramic membrane for boosting CO2 absorption. Separation and Purification Technology, 303, 122238. [Google Scholar]
24. Xue, K., Fu, H., Chen, H., Zhang, H., Gao, D. (2022). Investigation of membrane wetting for CO2 capture by gas-liquid contactor based on ceramic membrane. Separation and Purification Technology, 304, 122309. [Google Scholar]
25. Magnone, E., Lee, H. J., Shin, M. C., Park, J. H. (2021). A performance comparison study of five single and sixteen blended amine absorbents for CO2 capture using ceramic hollow fiber membrane contactors. Journal of Industrial and Engineering Chemistry, 100(2–3), 174–185. [Google Scholar]
26. Chai, S. Y. W., Ngu, L. H., How, B. S. (2022). Review of carbon capture absorbents for CO2 utilization. Greenhouse Gases: Science and Technology, 12(3), 394–427. [Google Scholar]
27. Helmlinger, L., Zhu, Y., Gensel, J., Neumeyer, T., Thäter, S. et al. (2017). Application of amine-functionalized cellulose foam for CO2 capture and storage in the brewing industry. Journal of Renewable Materials, 6(3), 219–225. [Google Scholar]
28. Jiang, W., Li, X., Gao, G., Wu, F., Luo, C. et al. (2022). Advances in applications of ionic liquids for phase change CO2 capture. Chemical Engineering Journal, 445(5948), 136767. [Google Scholar]
29. Jin, X., Ren, E., Yang, E. (2022). Effect of solvents on the phase separation behavior and CO2 capture performance of MEA-based nonaqueous absorbents. Energy & Fuels, 36(13), 6965–6973. [Google Scholar]
30. Bello, A., Idem, R. O. (2005). Pathways for the formation of products of the oxidative degradation of CO2-loaded concentrated aqueous monoethanolamine solutions during CO2 absorption from flue gases. Industrial & Engineering Chemistry Research, 44(4), 945–969. [Google Scholar]
31. Zarogiannis, T., Papadopoulos, A. I., Seferlis, P. (2020). Efficient selection of conventional and phase-change CO2 capture solvents and mixtures based on process economic and operating criteria. Journal of Cleaner Production, 272(23), 122764. [Google Scholar]
32. Li, K., Zhou, T., Xu, X., Han, C., Zhang, H. et al. (2022). PTFE-modified Mn-Co-based catalytic ceramic filters with H2O resistance for low-temperature NH3-SCR. Sustainability, 14(9), 5353. [Google Scholar]
Cite This Article
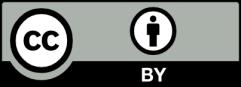
This work is licensed under a Creative Commons Attribution 4.0 International License , which permits unrestricted use, distribution, and reproduction in any medium, provided the original work is properly cited.