Open Access
REVIEW
Gasification of Organic Waste: Parameters, Mechanism and Prediction with the Machine Learning Approach
1 Yibin Research Institute, Southwest Jiaotong University, Yibin, China
2 Office of Domestic Cooperation and Educational Training Management, Southwest Jiaotong University, Chengdu, China
3 School of Computer Science and Technology, Xidian University, Xi’an, China
4 Faculty of Geosciences and Environmental Engineering, Southwest Jiaotong University, Chengdu, China
* Corresponding Author: Feng Gao. Email:
Journal of Renewable Materials 2023, 11(6), 2771-2786. https://doi.org/10.32604/jrm.2023.027325
Received 24 October 2022; Accepted 11 November 2022; Issue published 27 April 2023
Abstract
Gasification of organic waste represents one of the most effective valorization pathways for renewable energy and resources recovery, while this process can be affected by multi-factors like temperature, feedstock, and steam content, making the product’s prediction problematic. With the popularization and promotion of artificial intelligence such as machine learning (ML), traditional artificial neural networks have been paid more attention by researchers from the data science field, which provides scientific and engineering communities with flexible and rapid prediction frameworks in the field of organic waste gasification. In this work, critical parameters including temperature, steam ratio, and feedstock during gasification of organic waste were reviewed in three scenarios including steam gasification, air gasification, and oxygen-riched gasification, and the product distribution and involved mechanism were elaborated. Moreover, we presented the details of ML methods like regression analysis, artificial neural networks, decision trees, and related methods, which are expected to revolutionize data analysis and modeling of the gasification of organic waste. Typical outputs including the syngas yield, composition, and HHVs were discussed with a better understanding of the gasification process and ML application. This review focused on the combination of gasification and ML, and it is of immediate significance for the resource and energy utilization of organic waste.Keywords
Organic waste like lignocellulosic biomass, sewage sludge, and municipal solid waste contains rich carbon resources, and the high-value utilization is direct to the realization of carbon neutrality [1,2]. In recent years, a variety of high-value utilization approaches have emerged for energy or resource recovery. To efficiently valorize organic waste, thermochemical pathways have been widely studied due to the huge potential to convert organic waste into bioenergy [3]. Among these conversion techniques, gasification shows great potential due to its high efficiency and flexibility, and feedstock species, carrier environment, and thermal parameters are the main factors. With the moisture in feedstock or the load of the water, gasification can be divided into hydrothermal gasification and conventional gasification, while the former can use water as a reaction medium for syngas production, and the latter one is dominated by molecular rearrangement and gas release [4,5]. Generally, organic waste gasification produces high-value gases such as CO, CH4, and H2 [6]. However, the thermal-conversion mechanism is very complex due to the fact that diverse molecular rearrangement reactions and condensation reactions happen during the process [7,8].
In addition to the pyrolysis environment and parameters, lignocellulose materials differ from biowaste like sludge and algae, and this makes the products with various yields, HHVs, and components, while gasification is limited by the experiments and it is cost-effective [9]. Thus, accurate prediction of the components and mass distribution is a subject of great industrial significance. Considering this, it is necessary to have a basic understanding of the conversion process and to predict the gasification products. In recent years, studies have tried to explore the effect of parameters on the gasification of various biomass through experimental methods. Several works used Aspen Plus or CFD models to investigate the equilibrium and kinetic models of gasification [10,11]. However, with the development of artificial intelligence and the improvement of modern computer computing power, machine learning (ML) methods like artificial neural networks have been widely used in medical, environmental, and electrical fields, bringing new methods for the accurate prediction of biomass pyrolysis products [12,13]. ML is regarded as one of the most critical pathways, and it can be conducted by accurate prediction based on big data [14]. Therefore, a new area and direction of development emerged in recent years. ML means that algorithms build a model depending on the data of samples, namely training data, and then predictions or decisions can be made without being explicitly programmed [15]. For organic waste upgrading, ML models have great potential to accurately describe this complex process regardless of experiments with a reactor. However, at present, most studies use a variety of models for predication, but lack comparison in the same scenario, especially in the gasification process which also has not been fully explored about the mechanism and product distribution law, and this needs to improve the accuracy and understanding of the ML models in the future. This work will develop a better understanding of gasification mechanisms and the influence of parameters, as well as build reasonable models for the prediction of the gas product.
In this work, critical parameters, gasification mechanism, and product distribution from organic waste gasification were systematically reviewed, with three typical gasification techniques and the involved mechanism. The gasification process of organic waste and several popular ML techniques like regression analysis, artificial neural networks, decision trees, and related methods were discussed, which are expected to revolutionize data analysis and modeling of the gasification of organic waste including main outputs like the syngas yield, gas composition, and HHV. Moreover, current challenges and future perspectives of ML applications in organic waste gasification were discussed.
2 Gasification of Organic Waste
2.1 Typical Gasification Techniques
Generally, gasification can be divided into steam gasification, air gasification, and oxygen-riched gasification, based on the agent used during the process. Among these techniques, steam gasification can generate the highest stoichiometric yield of H2. Since the properties of water change dramatically when a supercritical point (22.1 MPa and 374°C) is reached, water can be oxidant. Under this environment, organic components react with oxygen molecules of water, while CO2 can be produced by a reaction between CO and steam [16]. Steam gasification is regarded as one efficient way to produce H2, while the cost of this method is several folds higher than that of other gasification techniques due to that the steam reforming reactions require more heat to perform. However, this method is suitable for high-moisture feedstock like sewage sludge, algae, and manure. As for air gasification, the advantage is that the reaction agent can be easily obtained from nature, which had high gasification efficiency and it is the most economic one of all gasification techniques. It suggested that the HHV of syngas can be significantly influenced by the temperature and equivalence ratio during air gasification [16]. One obvious drawback of air gasification is that the air injection also brings more N2 into a reactor, which may lead to a low heating value (3~8 MJ/m3) of syngas and this also results in a difficult separation of N2 [17]. Generally, medium heating value gas can be obtained from oxygen-riched gasification. Wang et al. [18] reported that the concentrations of H2 and CO2 in the syngas showed a sharp reduction with the increase of the O/C, while the CO concentration remained constant. The tendency of gas components from both oxygen-riched gasification and air gasification is similar to the variations of equivalence ratio. The solid residue and tar can be fully combustion combined with extra heat. However, oxygen-riched gasification needs high capital costs due to the requirement of pure oxygen. Typical gasification sets including steam gasification, air gasification, and oxygen-riched gasification are shown in Fig. 1, and the comparison is shown in Table 1. It can be observed the agent supply, purging, heating, and cooling are the main units, which support the operation of the gasifier.
Figure 1: Typical gasification techniques and set including steam gasification (A), air gasification (B), and oxygen-riched gasification (C) [18–20]
A deep understanding of the gasification mechanism is essential to the applications of ML as a prediction tool. Thus, this section mentioned the details of gasification. Generally, the objective of gasification is to convert organic waste into gaseous products under a low-oxygen environment, which is also called syngas, combustible gas with CO, H2, or CH4 as the main component [21,22]. This process also produces condensable tars and oils. The chemistry involved in the gasification is very complex, and a series of cracking, molecular rearrangement, etc. happen during gasification, and the air, steam, or oxygen can be used as the reaction agent in which a thermochemical reaction occurs since organic waste contains these components above [23].
The whole process can be divided into four stages (drying, pyrolysis, oxidation, and reduction), which are happened at a temperature range of 200°C–300°C, 300°C–400°C, and 1000°C–1200°C, respectively. During the drying process, moisture contained in the feedstock can be removed to approximately 5%. The pyrolysis process, namely devolatilization, can significantly decrease the volatile matter since most of the feedstock is converted into biochar, while the volatile gas can be condensed to tar under a low-temperature range [24]. During the oxidation stage, the main products are CO2 and water because of the carbonized production reaction and oxidized hydrogen, then this process releases a lot of heat. As for the reduction stage, since the low oxygen content, reduction reactions happen and most of these reactions like methane reaction and shift reaction are endothermic [25]. In Fig. 2, we summarized the mechanism and reactions that happened during steam gasification which included other gasification species based on the endothermic and exothermic properties. Additionally, a large number of studies focused on the production of fuels or value-added chemicals from gasification of low or negative-value organic waste, while it is essential to consider the energy cost due to the separation and catalysts when considering industrial scale.
Figure 2: Typical gasification mechanism from organic waste during steam gasification
2.3 Gasification Parameters and Effect on the Distribution of the Products
The types of organic waste are directly related to gasification. The main species of organic waste used in the presented works include lignocellulose materials, algae, MSW, sewage sludge, and manure. The dominant components are cellulose, lignin, hemicellulose, protein, and lipid. Thermal-stable components like lignin can collapse at a relatively higher temperature, so the intrinsic nature of organic waste like biomass must be cracked before the step of gas generation. Interestingly, moisture contained in the organic waste can be direct as reaction media, so sewage sludge or algae can be properly converted under a stem gasification environment. The size of the feedstock can significantly influence gas production. Since small particles have better heat and mass transfer, the gasification process can be effectively improved. In Lv et al.’s work [26], a larger feedstock size was not favored for the gasification due to the incomplete crack of large particles, and more biochar was produced. This tendency was also proved by Hernández et al.’s work, which suggested that a low biomass size can decrease the tar yield, and the gasification efficiency was also enhanced [27].
Temperature represents one critical factor during gasification. This factor can significantly affect the water properties like ionic concentration, then the type of reactions can be determined. Since most of the reactions are endothermic, an increase in temperature can decline the yield of biochar and tar, and the production of components with low molecules increases the efficiency of gasification. Especially, methane is relatively stable at a temperature range of 300°C~600°C due to its highly endothermic, while methane will decompose or reform with hydrocarbon at a temperature above 600°C [24]. Nevertheless, the yield of H2 usually increases with increasing temperature, which is highly related to the decomposition of methane and hydrocarbon. In addition, the filling ratio, namely the mass of steam/feedstock ratio, is another factor influencing the gas yield and HHV. A high organic waste ratio will generate more solid residue and methane because a solid-solid conversion dominates the organic waste gasification. With an excessive steam ratio, the production of H2 is favorable, and more tar can be formed. Considering this, a good balance of stem ratio should be controlled. Catalysts also play a critical role during gasification, and this discussion can be found in others’ work [17]. In Fig. 3, the distribution of the gas composition with a stem/feedstock ratio is summarized including typical air gasification and steam gasification. As observed, the CH4 ratio is relatively stable as discussed above, while the yield of H2 and CO2 shows an obvious increase and the tendency of CO content is adverse. This suggests that the load of the feedstock is one critical factor and strategy adjustment of steam/feedstock is essential.
Figure 3: Influence of the steam/biomass ratio on the gas composition for the air and steam gasification of biowaste feedstock [28–31]
3 Machine Learning Applications in Gasification
3.1 Application Scenario of Machine Learning Methods
Several ML pathways have been widely used for modeling gasification, and a variety of predictions with different accuracy can be found in these works. Here, we mainly described regression analysis, artificial neural networks, decision trees, and related methods. Among them, regression analysis is popular to model the gasification process. Regression analysis represents one typical statistical way that models the connection between dependent variables, namely the object variable, and an independent variable with more. In detail, regression analysis can help researchers to recognize how the values of independent variables correspond to changes in the independent variables, while the other variables remain fixed. It can predict continuously values like mass balance, yield, and one of the typical components of organic waste gasification [32]. A simple process of the machine learning method in the field of gasification was shown in Fig. 4.
Figure 4: The principle process of the machine learning method in the field of gasification
3.2 Typical Machine Learning Techniques
Generally, regression is a discovery of correlations between variables, which can predict continuous output data depending on other variables. It can be conducted for forecasting, time series modeling, and exploring relationships among these variables. Especially, linear regression is one simple method that reveals the linear relationship between an independent variable and the dependent variables. Additionally, logistic regression and polynomial regression, etc. are other typical regression methods. The former is generally used as a classification algorithm, and only solves binary classification problems and probability can be obtained [33]. Meanwhile, the sigmoid function or logistic function is generally adopted by logistic regression methods. Polynomial regression represents one linear regression model, in which the regression function is linear corresponding to the regression coefficient [34]. With polynomial regression, the regression model can be fitted better.
The artificial neural network is a common nonlinear algorithm model in machine learning, which is inspired by the biological neural networks from a human brain. This idea was generated in the 1960s [35]. Actually, an artificial neural network is also regarded as a universal function approximator. The detail of the running process of the neural networks mainly concludes the prediction of relevant dependent variables according to independent variables, and the model is nonlinear and calculated by the machine when the prediction function is considered [35]. The independent variables and dependent variables can be added to the model (input layer), and the data goes into a black box (hidden layer), which will train the data repeatedly and discover corresponding patterns, and then a model can be built in the box where the independent variables and dependent variables are intertwined [36]. One point that should be pointed out is that the black box is short of interpretability for artificial neural networks, which needs more work in the future [36]. In Fig. 5, a brief single-layer perceptron structure was presented.
Figure 5: A simple single-layer perceptron structure with I and O representing corresponding inputs and outputs, where W means the weights in two neurons and B is denoted as the bias terms [36]
Decision tree represents another basic machine learning method for classification and regression, and its model presents a tree structure. Fig. 6 showed a brief of the decision tree and random forest methods. For classification issues, it can be regarded as one probability distribution based on the feature space and class space [37]. The advantages of the decision tree are strong interpretability and fast classification. According to the principle of minimizing loss function, a decision tree can be developed for training. During classification, the rule is developed by the path from a root node to a leaf node, which is used for matching classification, and the features of internal nodes on the path [38]. Decision tree training generally includes feature selection, tree generation, and tree pruning [38]. Only the local optimum is considered when a decision tree is generated, whereas the global optimum is considered for the pruning of the decision tree [39]. Generally, decision tree shows advantages with high speed and relatively low demand computation, and it is easy to be transformed into classification rules [40]. Herewith, the strong interpretability makes it easy to be controlled. However, rapid training may lead the overfitting and high variance, which should not be neglected in practice. In addition to decision, the support vector machine represents another type of algorithm, which is popular for solving binary classification problems, and this method is suitable for other classification and regression tasks. In the next section, the application of ML methodology in the gasification of organic waste will be presented.
Figure 6: A brief of the decision tree and random forest methods. Single decision trees are shown in a blue box. The highlighted branches with green color give a pathway of a tree’s prediction
3.3 Machine Learning Applications in the Gasification of Organic Waste
To obtain gasification products with high yield and HHVs, etc., researchers usually estimate the actual and model results from supervised machine learning algorithms data [41]. Multi-output and single-output models are conducted by researchers, and machine learning methods are more suitable for a particular organic waste gasification scenario which can be developed by comparison. With this, the modeling process is always conducted by selecting the feedstock species like lignocellulose content, and gasification parameters like temperature, residence time, CO2/N2 environment, and solid ratio, which are generally used as input data. The gasification yield of gas like H2, gas composition, HHVs, etc. are set as out value. For example, Zhao et al. [42] applied a random forest model, artificial neural network, and support vector machine models in supercritical water gasification for the prediction of H2 yield, and modeling results suggested that high oxygen-containing feedstock was advantageous for H2 recovery efficiency. In addition to the yield of gas production, composition analysis is essential. Mutlu et al. [43] used binary least squares support vector machine and multi-class random forests classifiers to predict the gas composition and calorific value from organic waste gasification, and temperature distribution was proved to be critical for the models’ prediction of gasification products. In Bahadar et al.’s work [44], the gasification temperature was found to be the critical factor for hydrogen-rich syngas from a co-gasification of biomass/lignite which was predicted by machine learning algorithms with configured and trained datasets. Additionally, the quantization of the training dataset is important, since this is the main reason for the formation of errors. Ögren et al. [45] compared the applications of gaussian process regression and artificial neural networks in a laboratory-scale flat-flame burner and a pilot-scale of biomass gasification respectively, while the results suggested that a large dataset led an irreducible error based on the variance of the training dataset, and limited made the gaussian process regression better.
Generally, the line-regression method is inadequate for modeling the gasification process, and other regression methods like polynomial regression and stepwise regression are relatively suitable for higher dimensionality data. For example, in Ayodele et al. and coworker’s study [46], a non-linear response quadratic model with inbuilt algorithms was proved to be best for the prediction of hydrogen production from co-gasification of coconut shell and oil palm waste, while the support vector machine incorporated with linear kernel lead a low R2 performance of 0.3~0.7. Few works used a decision tree-based method to model the gasification and predict the yield of gas compared to the artificial neural networks. Although a simple tree decision can be conducted easily, it still possesses the same black-box nature as an artificial neural network, and its interpretability is relatively higher than that of the artificial neural network [47]. One most recent work compared six models for supercritical water gasification of coal, and their work showed that the decision tree had a better prediction performance of gas yield than the artificial neural networks [47]. Several studies used support vector machines to finish the classification tasks, but they also can be applied to the modeling of the gasification process, since support vector machines resulted in a better value of both RMSE and R2 compared to the artificial neural network. With this, the gas components or the corresponding distribution can be favored. For instance, Aguado et al. [48] successfully predicted the hydrogen concentration from an air-blown downdraft fixed-bed gasifier, and the modeling result was consistent with the artificial neural network. However, in Hossain et al.’s work [49], the support vector machine showed poor performance during the modeling of H2 production with any incorporation of kernel functions. This work was conducted with a biological process instead of gasification, since the parameters was more complex than gasification.
In Table 2, we presented recent works about ML methods and their corresponding applications in the field of organic waste gasification. It can be observed that R2 reached a value close to 1 meaning high fitting results. Most works focus on the high yield of H2 and the HHV of gas products, which suggests that ML application in energy recovery can be very successful since gasification of organic waste requires high energy input and a good optimization of energy balance is essential. Generally, the popular applications of ML in organic waste gasification include artificial neural networks, followed by support vector machines, decision trees, and gradient tree boosting. Typical input variables adopted by the ML tool are the elemental composition, proximate analysis of feedstock, and gasifying agent, and gas compositions including CO, CO2, H2, and CH4, mass yield, and HHV are the most comment used as output data [58].
The numbers of input and out data were generally not beyond ten in these works, while the data size was different due to the difference in samples and collection methods. The data size also played a critical role in an accurate prediction. These works used more than three models to predict the output parameters, and similar results from the ML models were accepted. Among these input factors, although a large number of studies considered the effect of temperature and residence time, few works focused on parameters like heating rates and environmental pressures with the air and N2. Unlike traditional methods of stoichiometric and nonstoichiometric equilibrium, in which the results significantly rely on the chemical reactions and equilibrium conditions, approaches of ML are more autonomous to finish the modeling process.
Finally, in Fig. 7, we presented typical samples for the ML application models for different target variables. In summary, it will be convenient for researchers to select ML models based on adaptability, advantage, and drawbacks in the gasification field. When the target is set to solve complicated non-linear environmental problems, the artificial neural network is highly adaptive and fault tolerant, but the nature of the “black box” and overfitting make is limited. Several researchers use support vector machines to avoid local optimum and dimensionality problems, and the accuracy can be improved, while it is sensitive to the missing data. Even if low overfitting can be expected from the support vector machine method, the training efficiency during the interpolation of large-scale data is low. Meanwhile, a similar situation in both the random forest model and the genetic algorithm is the low calculation speed, but the genetic algorithm can be easily incorporated with other types of models. In addition, though the decision tree has a higher learning rate and interpretability, the data can be easily overfitted as the support vector machine method. In summary, from the perspectives of data size, setting of input and output parameters, process optimization, and estimation of the performance of and quality of products, a suitable ML model for organic waste gasification should be developed. Because of the high complexity of organic waste, the mechanism of the gasification process is still under exploration in a view of thermal chemistry, the selection of a certain parameter and ML model, or the characteristics of the product to be evaluated, which are facing challenges.
Figure 7: Representative examples of ML application for organic waste gasification [42,46,53,59,60]: (a) random forest and support vector machine as yield and compositions; (b) artificial neural network derived ML models for the prediction of biomass pyrolysis kinetics; (c) H2 production prediction during hydrothermal gasification using random forest model outperformed gaussian process regression, artificial neural network and support vector machine models; (d) genetic algorithm based ML models for prediction, analysis, and evaluation of H2 yield with elemental and proximate analysis; (e) support vector machine, Gaussian process regression, sequential quadratic programming algorithms for predication Hydrogen-rich syngas production with factors of temperature, catalysts loading and blending ratio
In this work, the detailed process parameters including temperature, steam ratio, and feedstock during gasification of organic wastes were reviewed, with three typical gasification techniques including air gasification, and the involved mechanism were elaborated. Additionally, parameters affecting the product distribution were discussed, which provided references for the ML application. We also presented the details of ML methods like regression analysis, artificial neural networks, decision trees, and related methods, which are expected to revolutionize data analysis and modeling of the gasification of organic waste. Main outputs including the syngas yield, gas composition, and HHV can be predicted with a better understanding of the gasification process and ML application. A combination of gasification and ML is of great significance for the resource and energy utilization of organic waste, and a reference for industrial application can be provided.
Organic waste gasification is an effective and sustainable way for energy utilization, and the advantages are exploited to the hilt with adjustment and optimization of process parameters. ML has shown excellent application performance in the field of organic waste gasification including product distribution and HHV. Nevertheless, ML application in gasification faces huge challenges. Since every modeling strategy is distinct and the running way is different, enough data should be considered when model training and validation are developed. Sufficient samples should be provided when high dimensional datasets are conducted to avoid overfitting, which means a low efficient training. Future challenges are given below:
(a) Though significant works have successful applications of these ML models for a thermal conversion process, these models are really different and lack comparability, which hinders their practical application.
(b) Additionally, although the high accuracy, models should enhance the interpretability, because the involved internal principle like black box form artificial neural network is confusing for researchers, and the gray-box modeling method coupled with a partial theory-driven model and first principal model with the data-driven model are expected.
(c) Moreover, it is important to estimate the role of the variable contained in the gasification. Few works focused on catalyst loading and optimization during gasification. More works should consider the ML application in catalyst-assisted gasification processes regardless of the species and efficiency in the future. The solid residue and tar should be considered in the data set.
Funding Statement:: This work is supported by Sichuan Science and Technology Program (2021JDR0343), and the Project Fund of Chengdu Science and Technology Bureau (2019-YF09-00086-SN).
Conflicts of Interest: The authors declare that they have no conflicts of interest to report regarding the present study.
References
1. Liedel, C. (2020). Sustainable battery materials from biomass. ChemSusChem, 13(9), 2110–2141. https://doi.org/10.1002/cssc.201903577 [Google Scholar] [PubMed] [CrossRef]
2. Murphy, J. D., McKeogh, E., Kiely, G. (2004). Technical/economic/environmental analysis of biogas utilisation. Applied Energy, 77(4), 407–427. https://doi.org/10.1016/j.apenergy.2003.07.005 [Google Scholar] [CrossRef]
3. Li, D. C., Jiang, H. (2017). The thermochemical conversion of non-lignocellulosic biomass to form biochar: A review on characterizations and mechanism elucidation. Bioresource Technology, 246(6), 57–68. https://doi.org/10.1016/j.biortech.2017.07.029 [Google Scholar] [PubMed] [CrossRef]
4. Liakakou, E. T., Vreugdenhil, B. J., Cerone, N., Zimbardi, F., Pinto, F. et al. (2019). Gasification of lignin-rich residues for the production of biofuels via syngas fermentation: Comparison of gasification technologies. Fuel, 251(1), 580–592. https://doi.org/10.1016/j.fuel.2019.04.081 [Google Scholar] [CrossRef]
5. Vilas-Boas, A. C. M., Tarelho, L. A. C., Kamali, M., Hauschild, T., Pio, D. T. et al. (2021). Biochar from slow pyrolysis of biological sludge from wastewater treatment: Characteristics and effect as soil amendment. Biofuels, Bioproducts and Biorefining, 15(4), 1054–1072. https://doi.org/10.1002/bbb.2220 [Google Scholar] [CrossRef]
6. Hanchate, N., Ramani, S., Mathpati, C. S., Dalvi, V. H. (2021). Biomass gasification using dual fluidized bed gasification systems: A review. Journal of Cleaner Production, 280(6), 123148. https://doi.org/10.1016/j.jclepro.2020.123148 [Google Scholar] [CrossRef]
7. Wang, C., Jin, H., Feng, H., Wei, W., Cao, C. et al. (2020). Study on gasification mechanism of biomass waste in supercritical water based on product distribution. International Journal of Hydrogen Energy, 45(52), 28051–28061. https://doi.org/10.1016/j.ijhydene.2020.02.146 [Google Scholar] [CrossRef]
8. Brand, S., Hardi, F., Kim, J., Suh, D. J. (2014). Effect of heating rate on biomass liquefaction: Differences between subcritical water and supercritical ethanol. Energy, 68(1), 420–427. https://doi.org/10.1016/j.energy.2014.02.086 [Google Scholar] [CrossRef]
9. Han, T., Ding, S., Yang, W., Jönsson, P. (2019). Catalytic pyrolysis of lignin using low-cost materials with different acidities and textural properties as catalysts. Chemical Engineering Journal, 373(7), 846–856. https://doi.org/10.1016/j.cej.2019.05.125 [Google Scholar] [CrossRef]
10. Davis, R., Aden, A., Pienkos, P. T. (2011). Techno-economic analysis of autotrophic microalgae for fuel production. Applied Energy, 88(10), 3524–3531. https://doi.org/10.1016/j.apenergy.2011.04.018 [Google Scholar] [CrossRef]
11. Kaczor, Z., Buliński, Z., Werle, S. (2020). Modelling approaches to waste biomass pyrolysis: A review. Renewable Energy, 159, 427–443. https://doi.org/10.1016/j.renene.2020.05.110 [Google Scholar] [CrossRef]
12. Zhong, S., Zhang, K., Bagheri, M., Burken, J. G., Gu, A. et al. (2021). Machine learning: New ideas and tools in environmental science and engineering. Environmental Science Technology, 55(19), 12741–12754. [Google Scholar] [PubMed]
13. Ayodele, B. V., Mustapa, S. I., Kanthasamy, R., Zwawi, M., Cheng, C. K. (2021). Modeling the prediction of hydrogen production by co‐gasification of plastic and rubber wastes using machine learning algorithms. International Journal of Energy Research, 45(6), 9580–9594. https://doi.org/10.1002/er.6483 [Google Scholar] [CrossRef]
14. Onsree, T., Tippayawong, N. (2021). Machine learning application to predict yields of solid products from biomass torrefaction. Renewable Energy, 167(2), 425–432. https://doi.org/10.1016/j.renene.2020.11.099 [Google Scholar] [CrossRef]
15. Koza, J. R., Bennett, F. H., Andre, D., Keane, M. A. (1996). Automated design of both the topology and sizing of analog electrical circuits using genetic programming. Artificial Intelligence in Design, 96, 151–170. https://doi.org/10.1007/978-94-009-0279-4 [Google Scholar] [CrossRef]
16. Lucas, C., Szewczyk, D., Blasiak, W., Mochida, S. (2004). High-temperature air and steam gasification of densified biofuels. Biomass and Bioenergy, 27(6), 563–575. https://doi.org/10.1016/j.biombioe.2003.08.015 [Google Scholar] [CrossRef]
17. Parthasarathy, P., Narayanan, K. S. (2014). Hydrogen production from steam gasification of biomass: Influence of process parameters on hydrogen yield—A review. Renewable Energy, 66, 570–579. https://doi.org/10.1016/j.renene.2013.12.025 [Google Scholar] [CrossRef]
18. Wang, L., Du, X., Chen, J., Wu, Z. (2021). Numerical study on characteristics of biomass oxygen enriched gasification in the new gasifier on an experimental basis. Renewable Energy, 66(30), 570–579. https://doi.org/10.1016/j.renene.2021.07.098 [Google Scholar] [CrossRef]
19. Romero Millán, L. M., Sierra Vargas, F. E., Nzihou, A. (2021). Unraveled mechanisms in energy production from bioresources using steam gasification. Fuel, 287, 119527. https://doi.org/10.1016/j.fuel.2020.119527 [Google Scholar] [CrossRef]
20. Cao, Y., Bai, Y., Du, J. (2021). Air-gasification of pine sawdust using dolomite as in-bed material: Effects of gasification conditions on product characteristics. Journal of the Energy Institute, 95, 187–192. https://doi.org/10.1016/j.joei.2021.01.010 [Google Scholar] [CrossRef]
21. Materazzi, M., Taylor, R., Cairns-Terry, M. (2019). Production of biohydrogen from gasification of waste fuels: Pilot plant results and deployment prospects. Waste Management, 94(2–3), 95–106. https://doi.org/10.1016/j.wasman.2019.05.038 [Google Scholar] [PubMed] [CrossRef]
22. Paida, V. R., Brilman, D. W. F., Kersten, S. R. A. (2019). Hydrothermal gasification of sorbitol: H2 optimisation at high carbon gasification efficiencies. Chemical Engineering Journal, 358(15), 351–361. https://doi.org/10.1016/j.cej.2018.10.008 [Google Scholar] [CrossRef]
23. He, C., Chen, C. L., Giannis, A., Yang, Y., Wang, J. Y. (2014). Hydrothermal gasification of sewage sludge and model compounds for renewable hydrogen production: A review. Renewable and Sustainable Energy Reviews, 39, 1127–1142. https://doi.org/10.1016/j.rser.2014.07.141 [Google Scholar] [CrossRef]
24. Puig-Arnavat, M., Bruno, J. C., Coronas, A. (2010). Review and analysis of biomass gasification models. Renewable and Sustainable Energy Reviews, 14(9), 2841–2851. https://doi.org/10.1016/j.rser.2010.07.030 [Google Scholar] [CrossRef]
25. McKendry, P. (2002). Energy production from biomass (part 1Overview of biomass. Bioresource Technology, 83(1), 37–46. https://doi.org/10.1016/S0960-8524(01)00118-3 [Google Scholar] [PubMed] [CrossRef]
26. Lv, P. M., Xiong, Z. H., Chang, J., Wu, C. Z., Chen, Y. et al. (2004). An experimental study on biomass air-steam gasification in a fluidized bed. Bioresource Technology, 95(1), 95–101. https://doi.org/10.1016/j.biortech.2004.02.003 [Google Scholar] [PubMed] [CrossRef]
27. Hernández, J. J., Aranda-Almansa, G., Bula, A. (2010). Gasification of biomass wastes in an entrained flow gasifier: Effect of the particle size and the residence time. Fuel Processing Technology, 91(6), 681–692. https://doi.org/10.1016/j.fuproc.2010.01.018 [Google Scholar] [CrossRef]
28. Cao, Y., Bai, Y., Du, J. (2021). Air-steam gasification of biomass based on a multi-composition multi-step kinetic model: A clean strategy for hydrogen-enriched syngas production. Science of the Total Environment, 753(2), 141690. https://doi.org/10.1016/j.scitotenv.2020.141690 [Google Scholar] [PubMed] [CrossRef]
29. Gai, C., Guo, Y., Liu, T., Peng, N., Liu, Z. (2016). Hydrogen-rich gas production by steam gasification of hydrochar derived from sewage sludge. International Journal of Hydrogen Energy, 41(5), 3363–3372. https://doi.org/10.1016/j.ijhydene.2015.12.188 [Google Scholar] [CrossRef]
30. Ning, S., Jia, S., Ying, H., Sun, Y., Xu, W. et al. (2018). Hydrogen-rich syngas produced by catalytic steam gasification of corncob char. Biomass and Bioenergy, 117(68), 131–136. https://doi.org/10.1016/j.biombioe.2018.07.003 [Google Scholar] [CrossRef]
31. Yong, Y. S., Abdul Rasid, R. (2021). Process simulation of hydrogen production through biomass gasification: Introduction of torrefaction pre-treatment. International Journal of Hydrogen Energy, 136, 105530. https://doi.org/10.1016/j.ijhydene.2021.07.010 [Google Scholar] [CrossRef]
32. Ateş, F., Erginel, N. (2012). The regression analysis of fast pyrolysis product yields and determination of product quality. Fuel, 102, 681–690. [Google Scholar]
33. Dai, C., Li, Y. P., Huang, G. H. (2011). A two-stage support-vector-regression optimization model for municipal solid waste management—A case study of Beijing, China. Journal of Environmental Management, 92(12), 3037–3203. [Google Scholar]
34. Elmaz, F., Yücel, Ö., Mutlu, A. Y. (2020). Predictive modeling of biomass gasification with machine learning-based regression methods. Energy, 191, 116541. [Google Scholar]
35. Schmidhuber, J. (2015). Deep learning in neural networks: An overview. Neural Networks, 61, 85–117. [Google Scholar] [PubMed]
36. Ascher, S., Watson, I., You, S. (2022). Machine learning methods for modelling the gasification and pyrolysis of biomass and waste. Renewable and Sustainable Energy Reviews, 155(80), 111902. https://doi.org/10.1016/j.rser.2021.111902 [Google Scholar] [CrossRef]
37. Mori, N., Debeljak, B., Škerjanec, M., Simčič, T., Kanduč, T. et al. (2019). Modelling the effects of multiple stressors on respiration and microbial biomass in the hyporheic zone using decision trees. Water Research, 149, 9–20. https://doi.org/10.1016/j.watres.2018.10.093 [Google Scholar] [PubMed] [CrossRef]
38. Hastie, T., Tibshirani, R., Friedman, J. (2009). Elements of statistical learning. 2nd. Berlin: Springer. [Google Scholar]
39. Hannan, M. A., Arebey, M., Begum, R. A., Basri, H. (2012). An automated solid waste bin level detection system using a gray level aura matrix. Waste Management, 32(12), 2229–2238. https://doi.org/10.1016/j.wasman.2012.06.002 [Google Scholar] [PubMed] [CrossRef]
40. Yu, Z., Yousaf, K., Ahmad, M., Yousaf, M., Gao, Q. et al. (2020). Efficient pyrolysis of ginkgo biloba leaf residue and pharmaceutical sludge (mixture) with high production of clean energy: Process optimization by particle swarm optimization and gradient boosting decision tree algorithm. Bioresource Technology, 304(15), 123020. https://doi.org/10.1016/j.biortech.2020.123020 [Google Scholar] [PubMed] [CrossRef]
41. Umenweke, G. C., Afolabi, I. C., Epelle, E. I., Okolie, J. A. (2022). Machine learning methods for modeling conventional and hydrothermal gasification of waste biomass: A review. Bioresource Technology Reports, 17(45), 100976. https://doi.org/10.1016/j.biteb.2022.100976 [Google Scholar] [CrossRef]
42. Zhao, S., Li, J., Chen, C., Yan, B., Tao, J. et al. (2021). Interpretable machine learning for predicting and evaluating hydrogen production via supercritical water gasification of biomass. Journal of Cleaner Production, 316, 128244. https://doi.org/10.1016/j.jclepro.2021.128244 [Google Scholar] [CrossRef]
43. Mutlu, A. Y., Yucel, O. (2018). An artificial intelligence based approach to predicting syngas composition for downdraft biomass gasification. Energy, 165(1), 895–901. https://doi.org/10.1016/j.energy.2018.09.131 [Google Scholar] [CrossRef]
44. Bahadar, A., Kanthasamy, R., Sait, H. H., Zwawi, M., Algarni, M. et al. (2022). Elucidating the effect of process parameters on the production of hydrogen-rich syngas by biomass and coal co-gasification techniques: A multi-criteria modeling approach. Chemosphere, 287, 132052. https://doi.org/10.1016/j.chemosphere.2021.132052 [Google Scholar] [PubMed] [CrossRef]
45. Ögren, Y., Tóth, P., Garami, A., Sepman, A., Wiinikka, H. (2018). Development of a vision-based soft sensor for estimating equivalence ratio and major species concentration in entrained flow biomass gasification reactors. Applied Energy, 226, 450–460. https://doi.org/10.1016/j.apenergy.2018.06.007 [Google Scholar] [CrossRef]
46. Ayodele, B. V., Mustapa, S. I., Kanthasamy, R., Mohammad, N., AlTurki, A. et al. (2022). Performance analysis of support vector machine, gaussian process regression, sequential quadratic programming algorithms in modeling hydrogen-rich syngas production from catalyzed co-gasification of biomass wastes from oil palm. International Journal of Hydrogen Energy, 47(98), 41432–41443. https://doi.org/10.1016/j.ijhydene.2022.05.066 [Google Scholar] [CrossRef]
47. Liu, S., Yang, Y., Yu, L., Zhu, F., Cao, Y. et al. (2022). Predicting gas production by supercritical water gasification of coal using machine learning. Fuel, 329(3), 125478. https://doi.org/10.1016/j.fuel.2022.125478 [Google Scholar] [CrossRef]
48. Aguado, R., Casteleiro-Roca, J. L., Vera, D., Calvo-Rolle, J. L. (2022). A hybrid intelligent model to predict the hydrogen concentration in the producer gas from a downdraft gasifier. International Journal of Hydrogen Energy, 47(48), 20755–20770. https://doi.org/10.1016/j.ijhydene.2022.04.174 [Google Scholar] [CrossRef]
49. Hossain, S. S., Ayodele, B. V., Ali, S. S., Cheng, C. K., Mustapa, S. I. (2022). Comparative analysis of support vector machine regression and gaussian process regression in modeling hydrogen production from waste effluent. Sustainability, 14(12), 1–14. https://doi.org/10.3390/su14127245 [Google Scholar] [CrossRef]
50. Kardani, N., Zhou, A., Nazem, M., Lin, X. (2021). Modelling of municipal solid waste gasification using an optimised ensemble soft computing model. Fuel, 289(11), 119903. https://doi.org/10.1016/j.fuel.2020.119903 [Google Scholar] [CrossRef]
51. Ozbas, E. E., Aksu, D., Ongen, A., Aydin, M. A., Ozcan, H. K. (2019). Hydrogen production via biomass gasification, and modeling by supervised machine learning algorithms. International Journal of Hydrogen Energy, 44(32), 17260–17268. https://doi.org/10.1016/j.ijhydene.2019.02.108 [Google Scholar] [CrossRef]
52. Xing, J., Luo, K., Wang, H., Gao, Z., Fan, J. (2019). A comprehensive study on estimating higher heating value of biomass from proximate and ultimate analysis with machine learning approaches. Energy, 188(3), 116077. https://doi.org/10.1016/j.energy.2019.116077 [Google Scholar] [CrossRef]
53. Haq, Z. U., Ullah, H., Khan, M. N. A., Naqvi, S. R., Ahsan, M. (2022). Hydrogen production optimization from sewage sludge supercritical gasification process using machine learning methods integrated with genetic algorithm. Chemical Engineering Research and Design, 184, 614–626. https://doi.org/10.1016/j.cherd.2022.06.020 [Google Scholar] [CrossRef]
54. Elmaz, F., Yücel, Ö. (2020). Data-driven identification and model predictive control of biomass gasification process for maximum energy production. Energy, 195(11), 117037. https://doi.org/10.1016/j.energy.2020.117037 [Google Scholar] [CrossRef]
55. Sezer, S., Kartal, F., Özveren, U. (2021). Prediction of chemical exergy of syngas from downdraft gasifier by means of machine learning. Thermal Science and Engineering Progress, 26(14), 101031. https://doi.org/10.1016/j.tsep.2021.101031 [Google Scholar] [CrossRef]
56. Sezer, S., Özveren, U. (2021). Investigation of syngas exergy value and hydrogen concentration in syngas from biomass gasification in a bubbling fluidized bed gasifier by using machine learning. International Journal of Hydrogen Energy, 46(39), 20377–20396. https://doi.org/10.1016/j.ijhydene.2021.03.184 [Google Scholar] [CrossRef]
57. Kargbo, H. O., Zhang, J., Phan, A. N. (2021). Optimisation of two-stage biomass gasification for hydrogen production via artificial neural network. Applied Energy, 302, 117567. https://doi.org/10.1016/j.apenergy.2021.117567 [Google Scholar] [CrossRef]
58. Li, J., Pan, L., Suvarna, M., Wang, X. (2021). Machine learning aided supercritical water gasification for H2-rich syngas production with process optimization and catalyst screening. Chemical Engineering Journal, 426(18), 131285. https://doi.org/10.1016/j.cej.2021.131285 [Google Scholar] [CrossRef]
59. Tang, Q., Chen, Y., Yang, H., Liu, M., Xiao, H. et al. (2021). Machine learning prediction of pyrolytic gas yield and compositions with feature reduction methods: Effects of pyrolysis conditions and biomass characteristics. Bioresource Technology, 339(7), 125581. https://doi.org/10.1016/j.biortech.2021.125581 [Google Scholar] [PubMed] [CrossRef]
60. Balsora, H. K., Kartik, A., Dua, V., Joshi, J. B., Kataria, G. et al. (2022). Machine learning approach for the prediction of biomass pyrolysis kinetics from preliminary analysis. Journal of Environmental Chemical Engineering, 10(3), 108025. https://doi.org/10.1016/j.jece.2022.108025 [Google Scholar] [CrossRef]
Cite This Article
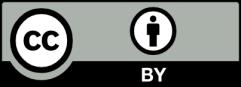
This work is licensed under a Creative Commons Attribution 4.0 International License , which permits unrestricted use, distribution, and reproduction in any medium, provided the original work is properly cited.