Open Access
ARTICLE
Characterization of Formacell Lignin Derived from Black Liquor as a Potential Green Additive for Advanced Biocomposites
1
Agricultural Product Technology Department, Faculty of Agriculture, The University of Lampung, Jl. Sumantri Brojonegoro No. 1,
Bandar Lampung, Indonesia
2
Department of Forest Product, Faculty of Forestry, Universitas Sumatera Utara, Kampus USU Padang Bulan, North Sumatra,
Indonesia
3
JATI-Sumatran Forestry Analysis Study Center, Jl. Tridharma Ujung No. 1, Kampus USU, Medan, North Sumatra, Indonesia
4
Research Center for Biomass and Bioproducts, National Research and Innovation Agency (BRIN), Jl. Raya Bogor, Cibinong,
Indonesia
5
Faculty of Forest Industry, University of Forestry, Sofia, Bulgaria
6
Department of Wood Industry, Faculty of Applied Sciences, Universiti Teknologi MARA (UiTM), Cawangan Pahang Kampus
Jengka, Lintasan Semarak, Bandar Jengka, Malaysia
7
Institute of Tropical Forestry and Forest Products, Universiti Putra Malaysia, Selangor, Malaysia
8
Research Collaboration Center for Marine Biomaterials, Jl. Ir. Sukarno, Jatinangor, Sumedang, West Java, Indonesia
9
Advanced Engineering Materials and Composites Research Centre, Department of Mechanical and Manufacturing Engineering,
Universiti Putra Malaysia, Selangor, Malaysia
* Corresponding Author: Sri Hidayati. Email:
(This article belongs to the Special Issue: Advances in Eco-friendly Wood-Based Composites: Design, Manufacturing, Properties and Applications)
Journal of Renewable Materials 2023, 11(6), 2865-2879. https://doi.org/10.32604/jrm.2023.027579
Received 04 November 2022; Accepted 19 December 2022; Issue published 27 April 2023
Abstract
Black liquor is obtained as a by-product of the pulping process, which is used to convert biomass into pulp by removing lignin, hemicelluloses and other extractives from wood to free cellulose fibers. Lignin represents a major constituent in black liquor, with quantities varying from 20% to 30%, of which a very low share is used for manufacturing value-added products, while the rest is mainly burned for energy purposes, thus underestimating its great potential as a raw material. Therefore, it is essential to establish new isolation and extraction methods to increase lignin valorization in the development of bio-based chemicals. The aim of this research work was to determine the effect of KOH or ethanol concentration as an isolation agent on lignin yields and the chemical characteristics of lignin isolated from formacell black liquor of oil palm empty fruit bunch (OPEFB). Isolation of lignin was carried out using KOH with various concentrations ranging from 5% to 15% (w/v). Ethanol was also used to precipitate lignin from black liquor at concentrations varying from 5% to 30% (v/v). The results obtained showed that the addition of KOH solution at 12.5% and 15% concentrations resulted in better lignin yield and chemical properties of lignin, i.e., pH values of 3.86 and 4.27, lignin yield of 12.78% and 14.95%, methoxyl content of 11.33% and 10.13%, and lignin equivalent weights of 476.25 and 427.03, respectively. Due to its phenolic structure and rich functional groups that are favorable for modifications, lignin has the potential to be used as a green additive in the development of advanced biocomposite products in various applications to replace current fossil fuel-based material, ranging from fillers, fire retardants, formaldehyde scavengers, carbon fibers, aerogels, and wood adhesives.Graphic Abstract
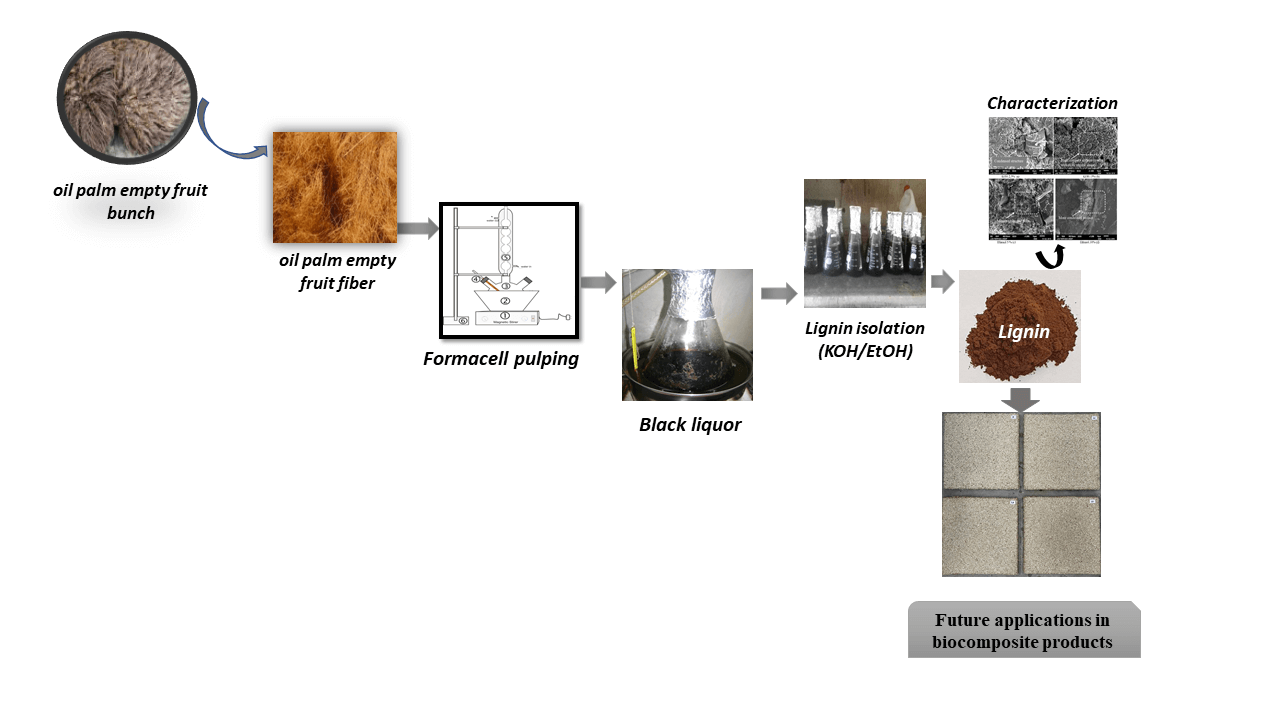
Keywords
Global challenges such as food security and environmental threats can be treated by applying the circular bioeconomy principles, including sustainable conversion of biomass components into bio-based products as green alternatives to their petroleum-based counterparts, thus closing the material resource loops [1]. Black liquor (BL) is liquid waste left over from cooking pulp, aimed at removing lignin, hemicelluloses, and other extractable constituents from wood in order to free the cellulose fibers. Lignin is the main organic substance in BL, reaching 45% dry weight [2]. About 150 billion tons of BL are released from the pulp and paper industry, where every 1 ton of pulp production will produce 7 tons of BL [3]. Considering the increased production of bioethanol, this availability is projected to reach 225 million tons annually in 2030 [4–6]. However, only 2%–5% of BL has been valorized into biomaterial [7], and the rest for energy purposes [8–10]. Hence, it is important to develop new techniques aimed at increasing the valorization of lignin as a renewable feedstock in various value-added industrial applications. Lignin is a complex polyphenol compound with a complex three-dimensional chemical structure that is difficult to decompose naturally, so it has the potential to cause water pollution if discharged into the environment [11]. Lignin has a highly aromatic structure that is stable to heat and has high carbon content. In addition, lignin contains various functional groups, e.g., aliphatic, phenolic, methoxyl, and carbonyl hydroxyl groups, allowing its modification. Thus, it can be used in many functional applications such as biomass-based fuels, adhesives, flame retardants, dispersants, and surfactant formulations, as antioxidants in plastics and rubbers, dyes, synthetic floors, thermosets, paints, food packaging, filler in adhesives, seed coatings, automotive devices, 3D printing, and fuels for highway maintenance [12–17]. However, the utilization of lignin is still limited on an industrial scale due to the inhomogeneity of structure.
A lignin component is a phenylpropane unit with several different methoxy groups [18]. Chemical structures of lignin are identified by the presence of polypropene units such as p-hydroxyphenyl (or p-coumaryl alcohol), guaiacyl (or coniferyl alcohol), and syringyl (or sinapyl alcohol), and their percentage vary depending on the botanical origin. Polypropane units can be chemically bonded in different bonding patterns where the β-O-4 aryl glycerol ether bond is the primary linkage [19]. However, the technical lignin’s structure differs from the native lignin and depends on the pulping method used. Besides, the source of raw materials and isolation method, including the type of chemical used and temperature, play critical roles in the physicochemical properties of lignin [20].
Lignin can be extracted in powder form from BL with proper chemical treatment and screening process [21]. Precipitation of lignin in the BL occurs due to the condensation reaction on the lignin constituent units, which were initially soluble and will be polymerized and form large molecules [22]. Base, acid, and organic solvents are common solutions to isolate lignin from BL. The process of lignin separation using organic solvents is known as the alcell or organosolv process [23]. This method is popular for breaking down lignin fractions [24]. The benefits of this method include obtaining lignin with a low molecular weight that is free of sulfur, and its application can be improved through fractionation or chemical modification [25], but organosolv fractionation is laborious work [26]; hence, acid and base deposition methods are more feasible. However, this method depends on the pH of the liquor, residence time, and temperature [22]. Some acids such as H2SO4, phosphoric acid (H3PO4), or HCl have been reported in isolating lignin from base BL, such as from the kraft process [27]. Meanwhile, lignin from formacell BL, BL derived from acetic acid, or formic acid as cooking liquid can be released by different alkalis, especially KOH, Ca(OH)2, and NaOH [20]. KOH, a strong base, is stronger than NaOH, and its use is expected to result in higher lignin yield.
Based on Miller et al. [28], a strong base (e.g., NaOH and KOH) provides a higher result in lignin yield than a weak base, and it would be a promising technique for depolymerizing lignin. The concentration of base is important to measure because it will influence selectivity, chemical-physical properties, and lignin yield [20,29]. Recently, Hidayati et al. evaluated the effect of NaOH concentration on lignin properties [20] while the disadvantage of NaOH was monoaromatic re-condensation led to the higher molecular weight of lignin [30]. Consequently, an alternative base such as KOH and ethanol is needed to overcome this problem. To date, no one reported lignin isolation from formacell BL using different concentrations of KOH and ethanol. Therefore, this study aimed to determine the effect of KOH and ethanol concentrations on the yield and chemical characteristics of lignin isolated from formacell BL of oil palm empty fruit bunch (OPEFB).
Black liquor used in this research is a by-product of the formacell pulping of OPEFB, as reported by Hidayati et al. [31]. The pulping conditions are presented in detail in the next section. OPEFB was obtained from PTPN Business Unit VII Central Lampung Bekri, Indonesia. Meanwhile, KOH, NaCl, NaOH, HCl, and ethanol were supplied by Merck (Darmstadt, Germany).
The formacell pulping was conducted in the autoclave at a liquor-to-particle ratio of 15:1 for 1 h at 130°C. This ratio of liquor to OPEFB particle ratio was used based on our initial experimental trials in the laboratory, considering the volumetric of OPEFB as a typical example of non-woody biomass. In this ratio, the OPEFB particles can be immersed completely in the chemical liquor. The ratio solvent of acetic acid and formic acid was 85:15 with the addition of HCl of 0.5% as the catalyst. The cooking liquor was collected after filtration and washing the completed softened OPEFB with fresh water at room temperature. This formacell BL was used for the next step.
The formacell BL obtained from the pulping process of 100 mL contained a total solid content of around 25.10%. There are two methods for lignin isolation from formacell BL of OPEFB. The first one, i.e., the isolation of lignin from BL was conducted using KOH with a concentration of 2.5%, 5%, 7.5%, 10%, 12.5%, and 15% (w/v). The second isolation technique used ethanol at concentrations of 5%, 10%, 15%, 20%, 25% and 30% (v/v). As much as 100 mL of the KOH or ethanol solution was added into 100 mL BL, then stirred and measured the pH of the liquor was. The solution was allowed to stand for 10 h, then centrifugated for 20 min at 2500 rpm, and then separated using filter paper. The precipitated lignin was then oven-dried at 50°C–60°C for 24 h. Dried lignin was crushed manually to produce fine lignin powder (Fig. 1). The experiment was conducted in triplicate.
Figure 1: Flowchart of lignin isolation process using KOH/Ethanol
The data were calculated and presented in average and standard deviation tables and graphs. Observations made were pH value, the yield of lignin, lignin methoxyl content, the equivalent weight of lignin, analysis of lignin with Fourier Transform Infra-Red spectroscopy (FTIR) spectrophotometer (Cary 630 FTIR, Agilent, Australia), and lignin morphology using a scanning electron microscope (SEM) (JEOL JSM 6510 LA, Japan).
Lignin yield was calculated based on the method according to Sluiter et al. [32], as presented in Eq. (1).
Notation:
a = weight of isolated lignin;
b = weight of lignin in black liquor.
2.5 Methoxyl Content of Lignin
The methoxyl content of lignin was determined by using the ASTM 15120-81 method [33]. As much as 0.5 g of lignin was added to 5 mL of ethanol, following addition to 100 mL of distilled water containing 1 g of NaCl, and made in the form of suspension. Neutralization was performed using 0.1 N NaOH, given 6 drops of phenolphthalein (pp) indicator, and then 25 mL of 0.25 N NaOH was added and homogenized in a closed state for 30 min at room temperature. After that, 25 mL of 0.25 N HCl was added and titrated with 0.1 N NaOH until the end of the lasting color change (at least 30 s). The methoxyl content of lignin was calculated according to Eq. (2) as follows:
Isolated lignin equivalent weight was calculated using the method of Brauns et al. [34]. 0.5 g lignin was put into 250 mL Erlenmeyer and moistened with 5 mL ethanol. The mixture is spiked with 1 g of NaCl which is then added with 100 mL of distilled water and 6 drops of phenolphthalein indicator. The solution was then titrated with 0.1 N NaOH until pH 7.5. The equivalent weight of isolated lignin was calculated by using Eq. (3).
2.7 FT-IR Analysis of Isolated Lignin
As much as 1 mg isolated lignin was added with 150 mg KBr, pelletized, and then the samples were analyzed by FT-IR spectrophotometer (Cary 630 FTIR Agilent). The analysis was set at a wavenumber of 4000 to 400 cm−1 (wavelength of 2.5–25 πm).
Morphology of isolated lignin was carried out using Scanning Electron Microscope (SEM) (JEOL JSM 6510 LA) with 1000 × magnification.
The pH of BL from formacell pulping OPEFB is 0.59 ± 0.01, indicating that the liquor is acidic; thus, base or ethanol can be used to precipitate lignin from BL. To speed up the reaction, solvents such as acetic acid and formic acid are used in the formacell pulping process, along with HCl as a catalyst [31]. This process causes the pH of the formacell BL to become very acidic. Zhuang et al. [35] stated that formic acid and acetic acid could delignify lignin because of their acidic nature, so they can degrade lignin well. In another study, a combination of formic acid, acetic acid, and water achieved more than 50% lignin depolymerization in biomass [36]. The pH of the BL will be affected by the addition of KOH solution. According to the research, the pH value obtained from formacell pulping added with KOH solution ranged from 2.43 ± 0.07 to 4.27 ± 0.35 (Table 1), while the addition of ethanol concentrations can slightly increase the pH value from 1.0 ± 0.01 to 1.29 ± 0.03. According to the findings, KOH has a greater effect on increasing pH than ethanol due to the strong base property of KOH.
The pH steadily increased as an up-surging concentration of KOH, where the lowest pH, 2.43 ± 0.07, was obtained from 2.5% KOH, and the highest was a pH of 4.27 ± 0.35 from KOH 15%. Increasing the concentration of KOH solution causes more OH− ions in the BL so that the pH of the solution becomes more alkaline. It can also be explained that KOH is a strong base. The stronger the base, the more OH ions are released, increasing the pH of the solution and making it more alkaline. Ethanol has a higher pKa than KOH, indicating a weaker acid. Unlike KOH, increasing the ethanol concentration slightly increased the pH, with the lowest being 1 and the highest being 1.29 after adding 5% and 30%, as shown in Table 1.
The lignin yield from adding KOH solution at various concentrations in isolation of BL ranged from 3.57 ± 0.38 to 14.95 ± 1.10 (Table 1). In comparison, ethanol isolation resulted in lower lignin yields of about 0.51 ± 0.00 to 1.06 ± 0.00. The highest lignin yield was produced at a concentration of 15% KOH solution (14.95% ± 1.10). Increasing the concentration of KOH solution caused the lignin yield to increase. It can be affected by the increasing concentration of an alkaline solution (KOH) that facilitates easier breaking of lignin bonds with other compounds, and a condensation reaction occurs in the lignin constituent units [37]. It is also supported by Sundin [38] who stated that lignin deposition from BL due to the protonation of phenol groups on lignin molecules caused by the addition of OH− ions from KOH. It reduces the electrostatic force between lignin molecules, resulting in the deposition of lignin and reduced solubility. The more OH− ions, the more lignin deposits will form. The deposit lignin increase occurred because of an increase in ionic strength and protonation. The protonation of the phenolic group in lignin leads the lignin nucleus to form aggregates when the pKa value of lignin is reached [39].
The lignin yield with KOH liquor treatment is higher than that of NaOH, as reported by Hidayati et al. [20]. Lignin was isolated from formacell BL of OPEFB by using NaOH, producing lignin yields ranging from 1.48% to 5.67%. It might be caused by the stronger base of KOH than NaOH. As seen in the periodic system, the metal Na+ and K+ are included in Group 1A. This is also related to the lower nature of alkali metal bases; the stronger, the lower the metal, the more easily reduced. Besides pH, temperature and ionic strength also affect lignin solubility. The molecular weight distribution in lignins is related to yield [40]. Both molecular weight and the ratio of phenols to aromatic units contribute to the solubility of lignin [40]. The changes in lignin yield in isolation by adding ethanol concentration are very low. The very low electronegativity of ethanol can suggest the presence of carbon compounds that cannot precipitate lignin properly. In the absence of sulfide, delignification was slower in the Alcell process.
As opposed to KOH precipitation, increasing ethanol concentrations leads to almost 0% lignin recovery. This result was in agreement with the precipitation of lignin from Miscanthus x giganteus, where after the addition of 75% of ethanol, there was no lignin precipitated [41]. In the low concentration of ethanol, lignin precipitation is carried out by diluting liquor with water, and the solubility of lignin decreases, resulting in more lignin being recovered. In other words, when the water content in the ethanol is limited, most of the lignin is soluble in the system, and hence the aggregate is not formed.
3.3 Methoxyl Content in Lignin
Methoxyl is one of the chemical groups in lignin for identifying one of the characteristics of lignin. The methoxyl group in each type of lignin has different content because of the different structures of lignin types. Determining methoxyl contents gives information about the average C9 units in lignin, and eventually, the unsaturated side chain and average oxygen content can be calculated [42]. The methoxyl content in KOH lignin ranged from 10.13% ± 1.92 to 13.06% ± 0.9, whereas the use of ethanol concentrations results in methoxyl contents between 11.99 ± 0.02 to 17.03 ± 0.42 (Table 1). The highest methoxyl content in lignin was acquired from isolated lignin by adding a 2.5% KOH solution. Increasing the concentration of KOH and ethanol solution leads to a decrease in the methoxyl content of isolated lignins. This may be due to the use of KOH as a strong base as a precipitating solution, which allows some methoxyl groups to degrade and transform into other compounds. This decrease in methoxyl content can be influenced by the disruption of structural stability in lignin caused by the addition of KOH. Furthermore, according to the pathway proposed by Yin et al. the removal of the methoxy group in lignin created a higher hydroxyl group of lignin by KOH solution. The presence of potassium in lignin isolation decreased the methoxyl content due to cleavage Cα―Cβ through Cβ―O bond. This cleavage leads to the removal of side chains such as methoxyl. The mechanism of this reaction has been proved by Yin et al. [43].
The various methoxyl content in lignin depends on the source of lignin and the delignification process used. Generally, high methoxyl content will inhibit lignin reactivity during use in the resin field. Lignin has phenolic hydroxyl groups that are typically linked to nearby phenyl propane units, allowing lignin to connect with formaldehyde in a way analogous to phenol and formaldehyde [44]. Molecular weight and lignin purity are important factors during the production of biocarbon fibers [44,45].
In the case of lignin application as an adhesive raw material, the low methoxyl content is more beneficial because it will increase the reactivity of aromatic nuclei in lignin [46]. It will facilitate the reaction of methylation or hydroxymethylation with adhesive-forming reactants such as NaOH and formaldehyde, hinting at the ease of gel formation. Recently, Gendron et al. compared four types of lignin for green adhesive, where the lowest methoxyl content of lignin had the highest water solubility and shear resistance as an adhesive [47].
The lignin standard of Indulin AT has a methoxyl content of around 13.5%–14.5% [48], so the methoxyl contents in isolated lignin in this study are still lower. Meanwhile, compared to methoxyl content by Hidayati et al. [20] with a value of 14.61%–20.77% by using NaOH as precipitating solution, the results of this study are also lower. These results are probably influenced by the use of KOH, which is classified as a strong base with a higher reactivity than NaOH, as seen from the periodic system. The influence of harsh chemicals and temperature during isolation causes the structure of lignin to undergo many changes, including the methoxyl group. The methoxyl group is degraded and transformed into other degradation compounds such as aromatic hydrocarbon and phenolic types, resulting in lower methoxyl content [49].
3.4 The Equivalent Weight of Lignin
The determination of the equivalent weight of lignin is intended to determine the molecular weight of lignin to identify lignin degradation and condensation reactions. The molecular weight of lignin is an important property that influences biomass recalcitrance and lignin value. Determination of the molecular weight of lignin in the original biomass depends on the source of the raw material used, chemicals used for isolation, and purification methods [50,51]. Based on the results, the equivalent weight of lignin from the KOH solution ranged from 427.03 ± 74.20 to 1372.94 ± 269.73, whereas the addition of ethanol concentration resulted in molecular weights ranging from 449.88 ± 1.9 to 2123.03 ± 27.5 (Table 1).
Increasing the concentration of KOH solution resulted in a decrease in lignin equivalent weight, so the lowest value at 15% KOH solution concentration was 427.03 ± 74.20. This might be attributed to the increasing addition of a KOH solution as a strong base will degrade a portion of lignin into a derivative compound with shorter chains. It can degrade lignin resulting in a low equivalent weight. According to Patil et al., lignin depolymerization has two routes: harsh and moderate, resulting in different lignin structures [52]. The average molecular weight of lignin decreases with increasing precipitation of lignin yield by KOH. It was shown that increasing the amount of lignin with lower molecular weight deposited a high yield of lignin. Lignin is degraded into smaller fragments so that there are more phenolic groups with lower molecular weights [53]. Increasing salt concentration can lower the product’s molecular weight [54,55].
According to Gellerstedt [56], the termination of methyl aryl ether bonds from the aromatic ring of lignin resulted in decreased methoxyl content and low molecular weight of lignin due to the lignin degradation process. Based on several previous studies, lignin molecular weight values were obtained, namely 2500–14,000 [57], and 1327.64–1787.23 [20]. In contrast, the equivalent weight of Indulin AT reached 3357–3366 [58]. This shows that the equivalent weight value of lignin varies greatly.
Lignin that has a high molecular weight can be used as a matrix in polyolefin composites, because a higher molecular mass of lignin has a better affinity with the matrix [59], while lignin with a lower molecular weight can be used for the development of phenol-formaldehyde resins, antioxidants, adhesives, and paints due to their higher reactivity than high molecular weight lignin [59].
Differences in elemental composition, functional group types, proportions, and molecular weight in lignin molecules provide opportunities to use lignin in a variety of value-added applications. Some factors that influence the molecular weight of lignin are the diversity of lignin isolation procedures, macromolecular degradation during isolation, the effect of condensation mainly on acidic conditions, the apparent polydispersity of dissolved lignin, inadequate determination methods used to characterize the isolated lignin, and uncertainties in the properties of lignin. Because lignin is heterogeneous and inconstant, characterizing native lignin is also difficult [60].
The molecular weight of lignin is very important in the development of such polymeric products; similarly, low-molecular-weight lignin isolated from wheat straw by acetic acid pulping is an ideal feedstock for adhesive manufacturing [61]. Doherty et al. [62] stated that lignin from the soda process of wheat plants ranges from 1700 with a methoxyl content of 16. The organosolv pulping process at bagasse produces a molecular weight of around 2000 and a methoxyl content of 15.1. Lignin produced in the isolation process using alcohol or alcell process has a low molecular weight (Mw < 900) with low polydispersity, no sulfur, and low ash content, although the value depends on the analytical method. There is also a molecular weight of 2580 g mol−1 with a polydispersity of 4.3. Sameni et al. compared four types of lignin from different isolation methods, where the highest Mw (13488) was obtained from the steam explosion process with a methoxyl content of 0.69. Meanwhile, with the same methoxyl content, the lowest Mw (2565) was derived from the kraft process [57]. Yun et al. reported that organosolv fractionation from native lignin decreased its molecular weight from 5070 to 1810 [23].
3.5 Lignin Analysis with FT-IR Spectrophotometer
FTIR was performed to analyze differences in the functional groups of lignin in the sample (Figs. 2 and 3). FTIR spectra analysis showed that the peak in the aromatic ring vibrations decreased with the absorption band at 1446 cm−1 (a) and 1408 cm−1 (b), especially in the treatment using the highest concentration of KOH (Fig. 2) and ethanol (Fig. 3). There are similarities in the wavelength of 3500 to 3109 cm−1 which refer to the presence of hydrogen bonds in the hydroxyl group (alcohol and phenolic). A wavelength absorption of 1587 and 1513 cm−1 indicates the aromatic lignin skeletal vibration [60]. Wavenumbers at 1460 to 1420 cm−1 are associated with stretching wavelengths of CH (methyl and methylene) and CH deformation with aromatic ring stretching fields [63]. The peaks observed in the range of 1220 to 1270 cm−1 in all spectra may refer to the C-H deformation vibrations of the guaiacyl [64]. The bands at 1300 cm−1 (syringyl) and 1200 cm−1 (guaiacyl) indicate the presence of both syringyl and guaiacyl in lignin’s chemical structure as the unique peaks of lignin precursor [65]. A similar peak was also found in kraft lignin isolated from Acacia mangium black liquor [27]. In general, peaks in Figs. 2 and 3 show that the treatment using KOH had a sharper peak than that of ethanol treatment. However, no difference in the peaks resulting from these two treatments was determined. Hidayati et al. [20] reported the experiment in isolated lignin from formacell BL of OPEFB using NaOH with the wave number of isolated lignin for guaiacyl lignin at around 1273.02 cm−1.
Figure 2: The FT-IR spectra of lignin using KOH isolation
Figure 3: The FT-IR spectra of lignin using ethanol isolation
Scanning Electron Microscope (SEM) was used to observe the size and morphology of lignin. In this study, SEM images were taken from the lowest and the highest concentration of KOH and ethanol as representative lignin morphology. As seen in Fig. 4, increasing the concentration of KOH acid from 2.5% to 15% showed differences in lignin morphology. Lignin isolation using 15% KOH (Fig. 4b) produced a more compact formation and morphology compared to lignin produced by isolation using 2.5% KOH concentration (Fig. 4a). In stark contrast, in treatment using ethanol appears that treatment with a 5% ethanol concentration resulted in a more condensed form and morphology than those using a 30% concentration. This result was in accordance with the findings reported by Solihat et al. [27] and Hamzah et al. [41], where increasing ethanol concentration created more rupture and amorphous lignin surface.
Figure 4: Morphological images of isolated lignin (a) KOH 2.5%, (b) KOH 15%, (c) ethanol 5%, (d) ethanol 30% with 1000 × magnification
3.7 Prospective Application of Formacell Lignin as Advanced Biocomposite Products
The lignin molecule contains a variety of active functional groups, including aliphatic hydroxyl (Al-OH), phenolic hydroxyl (Ph-OH), carboxyl (-COOH), carbonyl (-C=O), and methoxy groups (-OCH3), which determine its properties, chemistry, and reactivity of lignin. Lignin’s chemical properties enable it and its derivatives to be used as high-value materials. The lignin molecule can be used in a variety of value-added applications due to differences in molecular weight, elemental composition, and the types and proportions of functional groups. Currently, Saražin et al. investigated the potency of organosolv lignin-based non-isocyanate polyurethane for wood adhesive and the result demonstrated satisfactory mechanical properties [66] and its curing kinetics for interior furniture showed that it was more suitable than urea-formaldehyde (UF) adhesive [67]. Sulfur-free lignin is produced by isolating lignin from the formacell process. Most value-added applications prefer lignin with a lower percentage of sulfur and ash. For example, sulfur-free lignin is preferred for use in aerogel composites. Jõul et al. reacted lignin isolated by organic acid with 5-methylresorcinol-formaldehyde to create aerogel and according to the data, formacell lignin had good reactivity to create a high surface area of aerogel [68]. According to Talabi et al. lignin with rich hydroxyl carbon, low molecular weight, and less in the methoxyl group was suitable for lignin-based-formaldehyde resin with a 73% graphitization level [69], and hence formacell lignin with higher KOH and ethanol concentrations are appropriate for this application. Meanwhile, the high molecular weight of lignin is preferred as a matrix in carbon fiber composites because it improves the mechanical performance of the fiber.
A strong base, such as KOH, was used to successfully isolate lignin from oil palm empty fruit bunch (OPEFB) formacell BL. Some identified lignin peaks can be found in the FTIR spectra, with no significant difference between lignins isolated with KOH and ethanol. The addition of KOH solution at 12.5% and 15% concentrations is the more effective method for isolating lignin from formacell BL. At this condition, isolated lignins have pH values of 3.86 and 4.27, lignin yield of 2.78% and 14.95%, methoxyl content of 11.33% and 10.13%, and lignin equivalent weights of 476.25 and 427.03, respectively. The lignin produced by the isolation process using KOH and ethanol was characterized by the low methoxy content and a low molecular weight that created its higher reactivity. According to these properties, lignin derived from formacell is suitable for developing green, bio-based additives in biocomposite applications such as wood adhesives from non-isocyanate polyurethane, coatings, lignin-based-formaldehyde resins, formaldehyde scavengers, composite fillers, and other value-added industrial applications.
Acknowledgement: Authors acknowledge the Ministry of Education and Culture of the Republic of Indonesia for the financial support through the Basic Research Fund for the 2017/2018 Fiscal Year. The authors also acknowledge Advanced Characterization Laboratories Cibinong—Integrated Laboratory of Bioproduct, National Research, and Innovation Agency through E-Layanan Sains, Badan Riset dan Inovasi Nasional for the facilities, scientific and technical support form. This work was also supported by the Project “Development, Properties, and Application of Eco-Friendly Wood-Based Composites”, No. HИC-Б-1145/04.2021, carried out at the University of Forestry, Sofia, Bulgaria. The authors would like to acknowledge the Fundamental Research Grant Scheme (FRGS 2018-1), Reference Code: FRGS/1/2018/WAB07/UPM/1 provided by the Ministry of Higher Education, Malaysia.
Funding Statement: The authors received no specific funding for this study.
Conflicts of Interest: The authors declare that they have no conflicts of interest to report regarding the present study.
References
1. Rana, A. K., Guleria, S., Gupta, V. K., Thakur, V. K. (2023). Cellulosic pine needles-based biorefinery for a circular bioeconomy. Bioresource Technology, 367, 128255. https://doi.org/10.1016/j.biortech.2022.128255 [Google Scholar] [PubMed] [CrossRef]
2. Speight, J. G. (2019). Chapter 13—Upgrading by gasification. In: Speight, J. G. (Ed.Heavy oil recovery and upgrading, pp. 559–614. USA: Gulf Professional Publishing. [Google Scholar]
3. Bajpai, P. (2018). Chapter 12—Pulping fundamentals. In: Bajpai, P. (Ed.Biermann’s handbook of pulp and paper. Third Edition, pp. 295–351. Netherlands: Elsevier. [Google Scholar]
4. Epa, U. (2018). Inventory of US greenhouse gas emissions and sinks. In: The air pollution consultant. New York: United States Environmental Protection Energy. [Google Scholar]
5. Luo, H., Abu-Omar, M. (2017). Chemicals from lignin. In: Abraham, M. A. E. (Ed.Encyclopedia of sustainable technologies, pp. 573–585. Netherlands: Elsevier. [Google Scholar]
6. Bajwa, D. S., Pourhashem, G., Ullah, A. H., Bajwa, S. G. (2019). A concise review of current lignin production, applications, products and their environmental impact. Industrial Crops and Products, 139(9), 111526. https://doi.org/10.1016/j.indcrop.2019.111526 [Google Scholar] [CrossRef]
7. Nadda, A., Sharma, S. (2020). Lignin biosynthesis and transformation for industrial applications. German: Springer Nature Publishing. [Google Scholar]
8. Tribot, A., Amer, G., Abdou Alio, M., de Baynast, H., Delattre, C. (2019). Wood-lignin: Supply, extraction processes and use as bio-based material. European Polymer Journal, 112(1), 228–240. https://doi.org/10.1016/j.eurpolymj.2019.01.007 [Google Scholar] [CrossRef]
9. Naqvi, M., Yan, J., Dahlquist, E. (2010). Black liquor gasification integrated in pulp and paper mills: A critical review. Bioresource Technology, 101(21), 8001–8015. https://doi.org/10.1016/j.biortech.2010.05.013 [Google Scholar] [PubMed] [CrossRef]
10. Wild, P., Huijgen, W., Gosselink, R. (2014). Lignin pyrolysis for profitable lignocellulosic biorefineries. Biofuels, Bioproducts and Biorefining, 8(5), 645–657. https://doi.org/10.1002/bbb.1474 [Google Scholar] [CrossRef]
11. Zabel, R. A., Morrell, J. J. (2020). Chemical changes in wood caused by decay fungi. In: Wood microbiology, pp. 215–244. USA: Academic Press. [Google Scholar]
12. Podkościelna, B., Goliszek, M., Sevastyanova, O. (2017). New approach in the application of lignin for the synthesis of hybrid materials. Pure and Applied Chemistry, 89(1), 161–171. https://doi.org/10.1515/pac-2016-1009 [Google Scholar] [CrossRef]
13. Dai, P., Liang, M., Ma, X., Luo, Y., He, M. (2020). Highly efficient, environmentally friendly lignin-based flame retardant used in epoxy resin. ACS Omega, 5(49), 32084–32093. https://doi.org/10.1021/acsomega.0c05146 [Google Scholar] [PubMed] [CrossRef]
14. Santiago Medina, F., Basso, M. C., Pizzi, A. P., Delmotte, L. (2017). Polyurethanes from kraft lignin without using isocyanates. Journal of Renewable Materials, 6(4), 413–425. https://doi.org/10.7569/JRM.2017.634172 [Google Scholar] [CrossRef]
15. Cheng, C., Sun, W., Hu, B., Tao, G., Peng, C. (2020). Analysis of the mechanism and effectiveness of lignin in improving the high-temperature thermal stability of asphalt. Journal of Renewable Materials, 8(10), 1243–1255. https://doi.org/10.32604/jrm.2020.012054 [Google Scholar] [CrossRef]
16. Karthäuser, J., Biziks, V., Mai, C., Militz, H. (2021). Lignin and lignin-derived compounds for wood applications-a review. Molecules, 26(9), 2533. https://doi.org/10.3390/molecules26092533 [Google Scholar] [PubMed] [CrossRef]
17. Savov, V., Valchev, I., Antov, P., Yordanov, I., Popski, Z. (2022). Effect of the adhesive system on the properties of fiberboard panels bonded with hydrolysis lignin and phenol-formaldehyde resin. Polymers, 14(9), 1768. https://doi.org/10.3390/polym14091768 [Google Scholar] [PubMed] [CrossRef]
18. Windeisen, E., Wegener, G. (2016). Lignin as building unit for polymers. In: Reference module in materials science and materials engineering. Netherlads: Elsevier. [Google Scholar]
19. Abdelaziz, O. Y., Brink, D. P., Prothmann, J., Ravi, K., Sun, M. (2016). Biological valorization of low molecular weight lignin. Biotechnology Advances Journal, 34(8), 1318–1346. https://doi.org/10.1016/j.biotechadv.2016.10.001 [Google Scholar] [PubMed] [CrossRef]
20. Hidayati, S., Zuidar, A., Satyajaya, W., Murhadi, M., Retnowati, D. (2018). Isolation and characterization of formacell lignins from oil empty fruits bunches. IOP Conference Series: Materials Science and Engineering, vol. 344, pp. 1–14, 012006. Brisbol, British. [Google Scholar]
21. Ammar, M., Mechi, N., Slimi, H., Elaloui, E. (2017). Isolation and purification of alfa grass kraft lignin from industrial waste. Current Trends in Biomedical Engineering & Biosciences, 6(2). https://doi.org/10.19080/CTBEB.2017.06.555685 [Google Scholar] [CrossRef]
22. Andeme Ela, R. C., Spahn, L., Safaie, N., Ferrier, R. C., Ong, R. G. (2020). Understanding the effect of precipitation process variables on hardwood lignin characteristics and recovery from black liquor. ACS Sustainable Chemistry & Engineering, 8(37), 13997–14005. https://doi.org/10.1021/acssuschemeng.0c03692 [Google Scholar] [CrossRef]
23. Yun, J., Wei, L., Li, W., Gong, D., Qin, H. (2021). Isolating high antimicrobial ability lignin from bamboo kraft lignin by organosolv fractionation. Frontiers in Bioengineering and Biotechnology, 9, 683796. https://doi.org/10.3389/fbioe.2021.683796 [Google Scholar] [PubMed] [CrossRef]
24. Zijlstra, D. S., de Santi, A., Oldenburger, B., de Vries, J., Barta, K. (2019). Extraction of lignin with high β-o-4 content by mild ethanol extraction and its effect on the depolymerization yield. Journal of Visualized Experiments, (143). https://doi.org/10.3791/58575 [Google Scholar] [PubMed] [CrossRef]
25. Li, T., Takkellapati, S. (2018). The current and emerging sources of technical lignins and their applications. Biofuels, Bioproducts and Biorefining, 12(5), 756–787. https://doi.org/10.1002/bbb.1913 [Google Scholar] [PubMed] [CrossRef]
26. Thoresen, P. P., Matsakas, L., Rova, U., Christakopoulos, P. (2020). Recent advances in organosolv fractionation: Towards biomass fractionation technology of the future. Bioresource Technology, 306(1), 123189. https://doi.org/10.1016/j.biortech.2020.123189 [Google Scholar] [PubMed] [CrossRef]
27. Solihat, N. N., Santoso, E. B., Karimah, A., Madyaratri, E. W., Sari, F. P. (2022). Physical and chemical properties of Acacia mangium lignin isolated from pulp mill byproduct for potential application in wood composites. Polymers, 14(3), 491. https://doi.org/10.3390/polym14030491 [Google Scholar] [PubMed] [CrossRef]
28. Miller, J. E., Evans, L., Littlewolf, A., Trudell, D. E. (1999). Batch microreactor studies of lignin and lignin model compound depolymerization by bases in alcohol solvents. Fuel, 78(11), 1363–1366. https://doi.org/10.1016/S0016-2361(99)00072-1 [Google Scholar] [CrossRef]
29. Roy, R., Rahman, M. S., Amit, T. A., Jadhav, B. (2022). Recent advances in lignin depolymerization techniques: A comparative overview of traditional and greener approaches. Biomass, 2(3), 130–154. [Google Scholar]
30. Ahmad, Z., Mahmood, N., Yuan, Z., Paleologou, M., Xu, C. C. (2018). Effects of process parameters on hydrolytic treatment of black liquor for the production of low-molecular-weight depolymerized kraft lignin. Molecules, 23(10), 2464. [Google Scholar] [PubMed]
31. Hidayati, S., Zuidar, A. S., Satyajaya, W. (2017). Effect of acetic acid: Formic acid ratio on characteristics of pulp from Oil Palm Empty Fruit Bunches (OPEFB). ARPN Journal of Engineering and Applied Sciences, 12, 3802–3807. [Google Scholar]
32. Sluiter, A., Hames, B., Ruiz, R., Scarlata, C., Sluiter, J. (2010). Determination of structural carbohydrates and lignin in biomass. In: Laboratory analytical procedure (TP-510-42618). Colorado (USANational Renewable Energy Laboratory. [Google Scholar]
33. ASTM (1981). Methoxyl content of pulp and wood. In: ASTM D15120-81. USA: American National Standards Institute. [Google Scholar]
34. Brauns, F., Brauns, D. (1960). The chemistry of lignin: Covering the literature for the years 1949–1958. 1st EditionCambridge, Massachusetts: Academic Press. [Google Scholar]
35. Zhuang, J., Lin, L., Liu, J., Luo, X., Pang, C. (2009). Preparation of xylose and kraft pulp from poplar based on formic/acetic acid/water system hydrolysis. BioResources, 4(3), 1147–1157. [Google Scholar]
36. Ma, Q., Li, Z., Guo, L., Zhai, H., Ren, H. (2021). Formation of high carbohydrate and acylation condensed lignin from formic acid-acetic acid-H2O biorefinery of corn stalk rind. Industrial Crops and Products, 161, 113165. [Google Scholar]
37. Dinh Vu, N., Thi Tran, H., Bui, N. D., Duc Vu, C., Viet Nguyen, H. (2017). Lignin and cellulose extraction from vietnam’s rice straw using ultrasound-assisted alkaline treatment method. International Journal of Polymer Science, 2017(2), 1063695. https://doi.org/10.1155/2017/1063695 [Google Scholar] [CrossRef]
38. Sundin, J. (2000). Precipitation of kraft lignin under alkaline conditions. In: Department of pulp and paper chemistry and technology. Swedish: Royal Institute of Technology. [Google Scholar]
39. Jardim, J. M., Hart, P. W., Lucia, L. A., Jameel, H., Chang, H. M. (2022). The Effect of the kraft pulping process, wood species, and pH on lignin recovery from black liquor. Fibers, 10(2), 1–12. https://doi.org/10.3390/fib10020016 [Google Scholar] [CrossRef]
40. Zhu, W., Theliander, H. (2015). Precipitation of lignin from softwood black liquor: An investigation of the equilibrium and molecular properties of lignin. BioResources, 10(1), 1696–1714. https://doi.org/10.15376/biores.10.1.1696-1715 [Google Scholar] [CrossRef]
41. Hamzah, M. H., Bowra, S., Cox, P. (2020). Effects of ethanol concentration on organosolv lignin precipitation and aggregation from Miscanthus x giganteus. Processes, 8(7), 845. https://doi.org/10.3390/pr8070845 [Google Scholar] [CrossRef]
42. Ma, R., Zhang, X., Wang, Y., Zhang, X. (2018). New insights toward quantitative relationships between lignin reactivity to monomers and their structural characteristics. ChemSusChem, 11(13), 2146–2155. https://doi.org/10.1002/cssc.201800550 [Google Scholar] [PubMed] [CrossRef]
43. Yin, L., Leng, E., Fang, Y., Liu, T., Gong, X. (2020). Effects of KCl, KOH and K2CO3 on the pyrolysis of Cβ-O type lignin-related polymers. Journal of Analytical and Applied Pyrolysis, 147, 104809. [Google Scholar]
44. Ghorbani, M., Liebner, F., Herwijnen, H. W. G. V., Pfungen, L., Krahofer, M. (2016). Lignin phenol formaldehyde resoles: The impact of lignin type on adhesive properties. BioResources, 11(3), 6727–6741. [Google Scholar]
45. Syahmani (2017). Isolasi, sulfonasi dan asetilasi lignin dari tandan kosong sawit dan studi pengaruhnya terhadap proses pelarutan urea (Master Thesis). Bandung: Faculty of Math and Science Institut Teknologi Bandung. [Google Scholar]
46. Pizzi, A., Mittal, K. L. (2010). Wood adhesives. London: CRC Press. [Google Scholar]
47. Gendron, J., Stambouli, I., Bruel, C., Boumghar, Y., Montplaisir, D. (2022). Characterization of different types of lignin and their potential use in green adhesives. Industrial Crops and Products, 182, 114893. [Google Scholar]
48. Hu, Z., Du, X., Liu, J., Chang, H. M., Jameel, H. (2016). Structural characterization of pine kraft lignin: Biochoice lignin vs Indulin AT. Journal of Wood Chemistry and Technology, 36, 1–15. [Google Scholar]
49. Shen, D., Liu, G., Zhao, J., Xue, J., Guan, S. (2015). Thermo-chemical conversion of lignin to aromatic compounds: Effect of lignin source and reaction temperature. Journal of Analytical and Applied Pyrolysis, 112, 56–65. [Google Scholar]
50. Tolbert, A., Akinosho, H., Khunsupat, R., Naskar, A., Ragauskas, A. (2014). Characterization and analysis of the molecular weight of lignin for biorefining studies. Biofuels, Bioproducts and Biorefining, 8(6), 836–856. https://doi.org/10.1002/bbb.1500 [Google Scholar] [CrossRef]
51. da Silva, S. H. F., Gordobil, O., Labidi, J. (2020). Organic acids as a greener alternative for the precipitation of hardwood kraft lignins from the industrial black liquor. International Journal of Biological Macromolecules, 142, 583–591. https://doi.org/10.1016/j.ijbiomac.2019.09.133 [Google Scholar] [PubMed] [CrossRef]
52. Patil, V., Adhikari, S., Cross, P., Jahromi, H. (2020). Progress in the solvent depolymerization of lignin. Renewable and Sustainable Energy Reviews, 133, 110359. https://doi.org/10.1016/j.rser.2020.110359 [Google Scholar] [CrossRef]
53. Norgren, M., Lindström, B. (2000). Dissociation of Phenolic groups in kraft lignin at elevated temperatures. Holzforschung, 54(5), 519–527. https://doi.org/10.1515/HF.2000.088 [Google Scholar] [CrossRef]
54. Roberts, V. M., Stein, V., Reiner, T., Lemonidou, A., Li, X. (2011). Towards quantitative catalytic lignin depolymerization. Chemistry–A European Journal, 17(21), 5939–5948. https://doi.org/10.1002/chem.201002438 [Google Scholar] [PubMed] [CrossRef]
55. Ding, N., Liu, H., Sun, Y., Tang, X., Lei, T. (2021). Lignin degradation in cooking with active oxygen and solid Alkali process: A mechanism study. Journal of Cleaner Production, 278(12), 123984. https://doi.org/10.1016/j.jclepro.2020.123984 [Google Scholar] [CrossRef]
56. Gellerstedt, G. (2009). Chemistry of chemical pulping. In: Ek, M., Gellerstedt, G., Henriksson, G. (Eds.Chemistry of chemical pulping in the pulp and paper chemistry and technology: Pulping chemistry and technology. Germany: De Gruyter. [Google Scholar]
57. Sameni, J., Krigstin, S., Sain, M. (2016). Characterization of lignins isolated from industrial residues and their beneficial uses. BioResources, 11(4), 8435–8456. https://doi.org/10.15376/biores.11.4.8435-8456 [Google Scholar] [CrossRef]
58. Santoso, A. (1995). Characterization of lignin isolates and efforts to make them as plywood adhesive (Master Thesis). Institut Pertanian Bogor: Bogor. [Google Scholar]
59. Borregaard (2001). Dye dispersants, vol. 869. S.E.A. Singapore: Borregaard Lignotech. [Google Scholar]
60. Wang, H., Pu, Y., Ragauskas, A., Yang, B. (2019). From lignin to valuable products-strategies, challenges, and prospects. Bioresource Technology, 271(2), 449–461. https://doi.org/10.1016/j.biortech.2018.09.072 [Google Scholar] [PubMed] [CrossRef]
61. Pan, X., Sano, Y. (2005). Fractionation of wheat straw by atmospheric acetic acid process. Bioresource Technology, 96(11), 1256–1263. https://doi.org/10.1016/j.biortech.2004.10.018 [Google Scholar] [PubMed] [CrossRef]
62. Doherty, W. O. S., Mousavioun, P., Fellows, C. M. (2011). Value-adding to cellulosic ethanol: Lignin polymers. Industrial Crops and Products, 33(2), 259–276. https://doi.org/10.1016/j.indcrop.2010.10.022 [Google Scholar] [CrossRef]
63. Lu, Y., Lu, Y. C., Hu, H. Q., Xie, F. J., Wei, X. Y. (2017). Structural characterization of lignin and its degradation products with spectroscopic methods. Journal of Spectroscopy, 2017, 1–15. https://doi.org/10.1155/2017/8951658 [Google Scholar] [CrossRef]
64. Kim, D., Cheon, J., Kim, J., Hwang, D., Hong, I. (2017). Extraction and characterization of lignin from black liquor and preparation of biomass-based activated carbon therefrom. Carbon Letters, 22, 81–88. [Google Scholar]
65. Watkins, D., Nuruddin, M., Hosur, M., Tcherbi-Narteh, A., Jeelani, S. (2015). Extraction and characterization of lignin from different biomass resources. Journal of Materials Research and Technology, 4(1), 26–32. https://doi.org/10.1016/j.jmrt.2014.10.009 [Google Scholar] [CrossRef]
66. Saražin, J., Pizzi, A., Amirou, S., Schmiedl, D., Šernek, M. (2021). Organosolv lignin for non-isocyanate based polyurethanes (NIPU) as wood adhesive. Journal of Renewable Materials, 9(5), 881–907. https://doi.org/10.32604/jrm.2021.015047 [Google Scholar] [CrossRef]
67. Saražin, J., Poljanšek, I., Pizzi, A., Šernek, M. (2022). Curing kinetics of tannin and lignin biobased adhesives determined by DSC and ABES. Journal of Renewable Materials, 10(8), 2117–2131. https://doi.org/10.32604/jrm.2022.019602 [Google Scholar] [CrossRef]
68. Joul, P., Ho, T. T., Kallavus, U., Konist, A., Leiman, K. (2022). Characterization of organosolv lignins and their application in the preparation of aerogels. Materials, 15(8), 12861. https://doi.org/10.3390/ma15082861 [Google Scholar] [PubMed] [CrossRef]
69. Talabi, S. I., da Luz, A. P. D., Pandolfelli, V. C., Lima, V. H., Botaro, V. R. (2020). Graphitization of lignin-phenol-formaldehyde resins. Materials Research, 23(2), e20190686. https://doi.org/10.1590/1980-5373-mr-2019-0686 [Google Scholar] [CrossRef]
Cite This Article
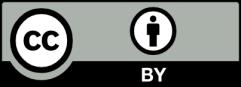
This work is licensed under a Creative Commons Attribution 4.0 International License , which permits unrestricted use, distribution, and reproduction in any medium, provided the original work is properly cited.