Open Access
ARTICLE
Hydrolysable Chestnut Tannin Extract Chemical Complexity in Its Reactions for Non-Isocyanate Polyurethanes (NIPU) Foams
1 LERMAB, Faculty of Science and Technology, University of Lorraine, Vandoeuvre les Nancy, 54506, France
2 LERMAB, University of Lorraine, Epinal, 88051, France
* Corresponding Authors: Antonio Pizzi. Email: ; Christine Gerardin-Charbonnier. Email:
Journal of Renewable Materials 2023, 11(6), 2823-2848. https://doi.org/10.32604/jrm.2023.027651
Received 08 November 2022; Accepted 15 November 2022; Issue published 27 April 2023
Abstract
Non-isocyanate polyurethane (NIPU) foams from a commercial hydrolysable tannin extract, chestnut wood tannin extract, have been prepared to determine what chemical species and products are taking part in the reactions involved. This method is based on two main steps: the reaction with dimethyl carbonate and the formation of urethane bonds by further reaction of the carbonated tannin with a diamine-like hexamethylene diamine. The hydroxyl groups on the tannin polyphenols and on the carbohydrates intimately linked with it and part of a hydrolysable tannin are the groups involved in these reactions. The carbohydrate skeleton of the hydrolysable tannin is also able to participate through its hydroxyl groups to the same two reactions rendering the whole molecular complex able to react to form NIPUs. The analysis by Matrix-Assisted Laser Desorption Ionization (MALDI-TOF) mass spectrometry and 13C Nuclear Magnetic Resonance (13C NMR) to further investigate the reaction mechanisms involved revealed the unsuspected complexity of chestnut hydrolysable tannin, with different fragments reacting in different manners forming a hardened network of considerable complexity. As the morphology and performance of these types of foams changes slightly with the change in the amount of glutaraldehyde and hexamine hardeners, the best performing foam formulation previously determined was scanned by SEM and analysed chemically for the structures formed.Graphic Abstract
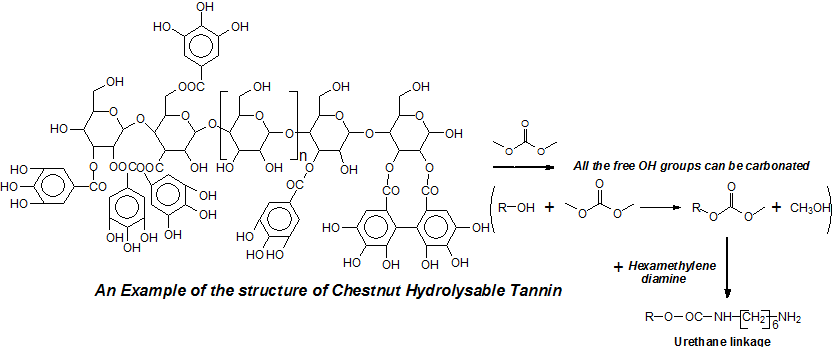
Keywords
Hydrolysable tannins are phenolic organic compounds that have been used, although rarely, in materials development research because of their low reactivity and structure when compared to condensed tannins [1–4]. While they are very valuable for leather tanning due to the low color they impart to the finished leather, they are nonetheless produced in a less than 10% proportion of the present commercial tannins market [5]. They are found in smaller quantities also in plants and secondary plant metabolites.
The structure of condensed tannin is phenolic, the hydrolysable tannins commercialized being in general a mixture of esters of sugar, mainly glucose, with simple phenols such as gallic and digallic acids and also with more complex structures such as ellagic acid [6–8]. Because of their different structure from condensed tannins, they have not been used with reactions with aldehydes in the same reactions as condensed tannins. They are composed mainly of pentagalloyl glucose (I) and its rearrangements forming castalagin (II) and castalin (III) [9].
One of the problems unresolved as regards their structure is how are enchained the pentagalloyl glucose units in the tannin in its natural state and in its extracted form where they constitute at least 30% of the commercial extract [6,10]. On this subject only three articles exist in the literature [6–8].
Some carbohydrate chains in which a number of galloyl residues esterified on the carbohydrates have been lost in the extraction process also occur in commercial chestnut tannin extract, as well as smaller molecular species [7,8]. To take advantage of the potential of this type of tannin, with its abundance in hydroxyl groups, an approach such as the preparation of Non-Isocyanate Polyurethane (NIPU) has been used [11,12], an approach being used also for other biomaterials [13,14]. The application of this approach to prepare biomaterials based on hydrolysable tannins has made it possible to start using them in materials research such as for adhesives [2] and insulating foams and other polymers [15].
Recently, a kind of rigid thermal insulating foam has been prepared using chestnut tannin [15]. The technique of preparing tannin-furanic foams is not adapt to form a foam with hydrolysable tannins due to their phenolic sites low reactivity. Thus, the non-isocyanate polyurethane approach based on their abundance in hydroxyl groups was used and the initial results of thermal and mechanical resistance were found to be acceptable [15].
Non-Isocyanate polyurethane foams from hydrolysable tannin with varying proportions of glutaraldehyde and citric acid and hexamine have been prepared (Table 1). The energy for foam expansion comes from the reaction between citric acid with the amino group of hexamethylene diamine with glutaraldehyde having the role of cross-linking agent [15–17]. FTIR characterization proved the existence and formation of urethane bonds.
Based on these initial analyses, density and compressive strength appeared to be independent from each other for some foams. Coherence was supposed to exist between foam density and its mechanical strength. However, at almost the same densities for the different types of foam formulations, one of them showed instead a remarkably higher strength compared to the other foams. The present work presents (i) a scanning electron microscope (SEM) characterization of the different foams cell structures to explain their mechanical behavior. Furthermore (ii) an in depth complementary analysis by MALDI ToF and 13C NMR were carried out of the foam with the best cell structure and highest compressive strength, to explain the type of very complex oligomers mix formed and contributing to the hardened foam network, this being the first time this type of study is carried out on a finished hydrolysable tannin NIPU foam, and (iii) as the manner in which pentagalloyl glucose units are linked is not really explained in the literature with only two articles [7,8] addressing this problem drawing different conclusions this was also studied.
Commercial chestnut (Castanea sativa) wood tannin extract was obtained from Silva Chimica (S.Michele Mondovi, Italy). Retail products, including dimethyl carbonate (DMC, anhydrous, ⩾99%), hexamethylene diamine (HDMA, technical grade, 70% water solution), glutaraldehyde, citric acid, and hexamethylene tetramine were obtained from Sigma-Aldrich (St.Louis, Missouri, USA).
2.2 Preparation of Chestnut Tannin Extract Non-Isocyanate Polyurethane (NIPU) Resin and Foams
The NIPU foam preparation is based on three phases:
A) Preparation of the NIPU resin
B) Preparation of a flexible foam or a homogeneous mixture from the NIPU resin
C) Heat to cure and harden the foam obtained
Tannin-based NIPU resins were prepared by the same procedure used and reported previously [14–18]. Briefly, distilled water was charged into a three-neck round flask with magnetic stirrer and thermometer immersed in an oil bath condition. Then, chestnut tannin extract was added and sufficiently mixed till a homogenous mixture was obtained. Thereafter, DMC was added into the flask and the mixture heated to 65°C and kept at this temperature for 1 h. Finally, HDMA was added under continuous mechanical stirring and maintained at 90°C for 2 h. The reactions were tried by heating them either in an oil bath or without an oil bath. The resin so obtained was cooled down to room temperature and recorded as tannin NIPU. The relative proportions of the reactive used are shown in Table 1.
To complete this study, four types of foam were prepared (Table 2). The formulations to prepare the resin and the foams come from recent research [16–18]. In addition, initial observations such as density and compressive strength are mentioned to be able to distinguish foams by their physical characteristics.
2.3 Scanning Electron Microscopy (SEM)
The microscopy structure and morphology of the foams were examined using scanning electron microscopy (SEM, Hitachi TM-3000) (Milexia, Paris, France). The sample was cut into a 0.2 cm2 cross-section. A thin metallic coating was sputtered on top of the foams.
2.4 Matrix Assisted Laser Desorption Ionization Time-of-Flight Mass Spectrometry (MALDI-TOF)
5 mg of sample powder was dissolved in 1 mL of a 50:50 v/v acetone/water solution. Then, 10 μL of a 2,5-dihydroxy benzoic acid (DHB) matrix was added to 10 mg of the sample solution. Furthermore, 2 μL of a NaCl solution 0.1 M in 2:1 v/v methanol/water was applied and pre-dried on the sample support plaque, followed by adding 1 μL of the sample solution. The plaque was then dried again. The standardization of the MALDI spectrometer was done with red phosphorous. The spectrometer was an Axima-Performance from Shimadzu Biotech (Kratos Analytical Shimadzu Europe, Ltd., Manchester, UK). The tuning mode was linear polarity-positive. A total of 1000 transients for each sample were done, with two shots accumulated per profile. The spectrum precision is ±1 Da.
2.5 Solid State CP MAS 13C NMR
Solid state Cross Polarization-Magic Angle Spinning CP MAS 13C NMR was used to characterize the cured foam. As foam B showed the best physical results physique, it was chosen for this analysis. The spectrometer used was an AVANCE II 400 MHz spectrometer (Brüker, Billerica, MA, USA). Furthermore, 100.6 MHz was the frequency used at a 12-kHz sample spin, and the recycling delay was 1 s, depending on the 1H spin-lattice relaxation times (t1) estimated with the inversion-recovery pulse sequence and a contact time of 1 ms. The decoupling field was 78 kHz, with 15,000 being the number of transients. Tetramethyl silane (TMS) was used as the shift control. The spectra precision was ±1 ppm. Spinning sideband suppression was used.
3.1 Scanning Electron Microscopy (SEM) Analysis
The results of scanning electron microscopy are shown in Figs. 1 and 2. Comparing foams A and B, which have the same formulation, but with the only difference being in the amount of glutaraldehyde, it is visible that the cell structure of foam B is more arranged, and the cells are better formed and more closed. Thus, the addition of glutaraldehyde appears to have improved cell formation yielding less perforated open cells when compared to foam A. As the foams with a higher amount of glutaraldehyde are much denser, it can be concluded that there is a reasonable reaction between tannin and glutaraldehyde and that cross-linking is more completed. For this reason, formulation D while having the same amount of hexamine as C, has a higher amount of glutaraldehyde and its cells are thus less fractured. The addition of glutaraldehyde can increase the viscosity and speed-up foam formation, and for this reason, foams containing more glutaraldehyde are slightly denser and have higher molecular weights [15,16]. The addition of hexamine may accelerate foam formation, leading to faster formation of foams C and D rather than for B. Still, a kind of cell fracture appeared, which can be attributed to the higher rate of reaction. This excessive speed does not allow the cells to complete the formation of their structure or starts to break down the cell walls. Conversely, in formulation D, by increasing the amount of glutaraldehyde, the cross-linking has improved which can be attributed to a better balanced rate of foam formation, and as it is visible in Fig. 1, foam D is less fractured than foam C, its cells being less fractured. However, the addition of glutaraldehyde and hexamine has decreased the cells size and the rate of cells formation.
Figure 1: SEM images of chestnut tannin extract-based non-isocyanate polyurethane (NIPU) bio-foams
Figure 2: SEM images of chestnut tannin extract-based non-isocyanate polyurethane (NIPU) bio-foams
The preparation of non-isocyanate urethane linkages, which is the essential reaction, comprises several processes.
The first step is the reaction between the gallic acid and/or ellagic acid groups of chestnut tannin with the dimethyl carbonate. The second step is the reaction of this mix of compounds formed in the previous reaction with a diamine, in our case with hexamethylene diamine: Because they are polyols, it is also probable that some of the carbohydrates that are intimately linked to the polyphenols in the tannin are affected by carbonation and thus participate to the formation of non-isocyanate polyurethanes once reacted as well with hexamethylene diamine. The MALDI ToF analysis of all the species formed by the reactions or already present in the tannin is shown in Table S1 in Appendix A.
In reality this simplicity of reaction is only apparent as a complex series of reactions with a number of the chemical species present are possible and many different products are hence formed. It must be considered that the extraction process of a tannin such as chestnut leads to the formation of all sorts of fragments of different molecular weight, rendering the environment rather complex. The first point to consider is to see if gallic acid moieties are carbonated by the dimethyl carbonate (DMC) and then if the reaction with the diamine occurs. That this does occur with ease is shown by all the species at 254, 309, 411, 447, and 475 Da (Fig. 3). The second point to see is if the carbonated gallic acid moieties do react with the hexamethylene diamine. Many species have been identified where this is the case, namely at 477, 529, 670, 731, 753, 817, 838, 896, 953, 1037 Da, such as the species at 1037 Da clearly demonstrating the participation of gallic acid residues to the NIPU formation (IV) (Fig. 3).
Figure 3: MALDI ToF spectra of chestnut tannin extract non-isocyanate polyurethane (NIPU) bio-foam: (a) 100–500 Da range, (b) 400–600 Da range, (c) 500–1000 Da range, (d) 800–1000 Da range, (e) 1000–1200 Da range, (f) 1200–1400 Da range, (g) 1600–2000 Da range, (h) 2000–250,000 Da range
It must be equally pointed out that some of these peaks can be represented with NIPU being formed with the glucose residues that are inherent part of this tannin before and after extraction, namely the peaks at 529, 670, 810, 953, 1020 and 1037 Da (V) (Fig. 3) [18,19].
And moreover, mixed species in which both gallic acid and glucose participate in the non-isocyanate polyurethane formed also occur, such as those at 1242 and 1264 Da (Fig. 3), such as (VI).
Species I, II and III also show that DMC + hexamethylene diamine are able to form urethane cross-links between gallic acid residues, between glucoses and jointly between gallic acid and glucose residues.
All these compounds are in reality formed with small residues in the tannin extract, namely gallic acid and glucose that have been separated by the extraction process from the main structures of the tannin itself. Thus, it is essential to find out how the set of reactions to form NIPU do occur with big oligomers such as pentagalloyl glucose, the real repeating unit of the chestnut tannin polymer in nature. The reactions also occur with ease with pentagalloyl glucose, such as shown by the species peaks at 1275, 1299, 1524, 1635, 1712, 1747 Da and particularly 2044 Da, this last one showing cross-linking of two pentagalloyl glucose units by formation of two non-isocyanate polyurethane linkages by reaction with DMC and hexamethylene diamine (Fig. 3) (VII).
To proceed further the structure of the polymer formed by just pentagalloyl glucose units is not really sure and is unreported in the literature. Only two early articles [6,7] gave an explanation both of which could well be true as, while corresponding to the MALDI results obtained then, is possibly not the only type of linkages between the units, given the structural complexity of this tannin. There are several different ways that the pentagalloyl glucoses can be linked.
1. Through a linkage directly between aromatic rings through ArC-Car of the two units as for example as between gallic residues in ellagic acid (VIII).
2. Through a bridge ArC-O-CAr as in one of the only two articles on this subject [6], leaving all the 3 × OHs of the receiving gallic acid free so with the O bridge being formed between a -OH and the meta position of a gallic residue. This however at first sight seems unlikely as it would entail the elimination of just 2Hs, notwithstanding that in the article the MW of the trimer so formed corresponds to what expected from such a structure (IX).
3. Third, and possibly more probable as a linkage ArC-O-CAr in which the -OH of the gallic acid donor and of the gallic acid receiver for such bridge are both involved by elimination of a H2O molecule (X).
4. As can be seen from the long carbohydrate oligomer chains on which less or much less galloyl residues are linked, the possibility that in the commercial chestnut tannin extract the repeating units might not be pentagalloyl glucose but a lesser number of galloyl residues on glucose and that such units are linked by just glucose to glucose by glycosidic bridges. It may also be that such a configuration is generated by the extraction process. This type of configuration has already been shown to exist in commercial chestnut tannin extract [7,8], as for example structure (XI) at 1437 Da (Fig. S1 in Appendix A), and all its isomers.
While of these four possibilities the first type of link exists in ellagic acid and the third is most logical for an enzymatic driven reaction in the native tannin, there is clear evidence that the other two are well present as well, adding to the complexity of chestnut tannin extract.
Thus, for the first linkage possibility, in the spectra present the peaks at 1861 and 2001 Da pertain to pentagalloyl glucose dimer alone and with a NIPU linkage. For the second possible link between units the peaks at 1898, 2018 and 2302 Da belong to it, pertaining to a pentagalloyl glucose dimer alone, with one NIPU linkage, and with 3 NIPU linkages, respectively. For the third possibility the peaks at 1898 and 2001 Da are also interpreted in the same manner as the first type of possibility. Thus, it is not possible to distinguish between the first and the third type of linkage between the units. It is only possible to state that the type 2 does clearly exists [6], and that either the first or the third exist, or possibly both. The fourth type of inter-unit linkage definitely exists [7,8,18,19] as shown in Fig. 3 by the peaks at 1231 Da (1 galloyl residue + 8 stripped glucose residues chain), 1365 Da (1 galloyl residue + 9 stripped glucose residues chain), 1437 Da (4 galloyl residues + 6 stripped glucoses chain), 1762 Da (1 galloyl residue + 12 stripped glucose residues chain), 1892 Da (7 galloyl residues + 5 glucose residues chain) (V), 2035 Da (7 galloyl residues + 5 glucose residues chain + 1 × NIPU) (XII).
A reaction scheme of what does occur with a kind of configuration can be better explained with the example given in Fig. 4 for one configuration of glucose chains linked by glycoside bridges with a variable number of galloyl residues linked to it between 0 and 4.
Figure 4: Reaction scheme showing that all the free-OH groups in a glucose chain with the glucoses linked by glycosidic linkages with on each glucose either no galloyl residue attached or with a variable number of galloyl residues attached can be first carbonated and the carbonate group reacted with a diamine to form a urethane linkage
Several peaks of significance are visible in the CP-MAS 13C NMR spectrum in Fig. 5 [20,21]. First of all the broad peak at 180 ppm is just due to overlap of carboxylic group from gallic acid and citric acid, this latter used as catalyst, and quinone structures due to oxidation of phenolic hydroxyls while the phenolic part of the hydrolysable tannin is undergoing the different reaction leading to the NIPU resin and finally the foam. The evident width of the majority peaks already indicates that the material in the foam is polymerized. The very small peak at 168 ppm is assigned to the free C=O of gallic acid. The more marked peak at 159 ppm is assigned to the C=O group of the NIPU hydroxyurethane linkages -NH-CO-O-R formed confirming that non-isocyanate urethane linkages have been formed. The wide peak at 144 ppm belongs to the aromatic carbons of the two non-vicinal phenolic hydroxyl groups of gallic acid residues. The width of this peak also attests of the complexity of the variety of environments in which gallic acid finds itself as seen above by MALDI ToF analysis. The barely visible shoulder centered at 137 ppm central belongs to the aromatic carbon of the central hydroxyl group of gallic acid, thus the only one doubly vicinal of the other two hydroxyls. There is a very small peak at 120 ppm which belongs to the aromatic carbon attached to the C=O of gallic acid carboxyl group. The small but wide peak is composed of two shifts at 109 and 106 ppm and are assigned to the unsubstituted aromatic carbons of gallic and ellagic acids. The shift range between 50 and 90 ppm mainly belongs to carbohydrates groups. In this range the peak centered on 72 ppm and the peaks at 80 ppm, the shoulder at 90 ppm and the peak at 68 ppm are all assigned to the carbons of the pyranose heterocycle ring in pentagalloyl glucose confirming that a marked amount of the glucose is in its pyranose cycle form, thus belonging to pentagalloyl glucose and other galloyl glucoses rather than in the open sugar structure form present in rearrangement products such as castalagin or castalin. The 56 ppm shift while generally assigned in general to carbohydrates is really assigned to the presence of sugar chains linked by glycosidic bonds [22–25] indicating a further manner in which galloyl glucoses with a different number of galloyl residues can be linked through the carbohydrate chain as well [7,8]. It reflects the reality of the MALDI ToF analysis peaks at 826, 977, 1231, 1365, 1437, 1762, 1819, and 1892 Da of long sugar chains oligomers with just very few galloyl residue linked to them [7,8]. These are species where the galloyl residue esters to the carbohydrates have been cleaved with only very few of them remaining attached to the main, skeletal carbohydrate chain. The C-O- of the chestnut extract carbohydrates is represented by the peak at 40 ppm. The small peak at 45 ppm is assigned to the -CH2- groups of citric acid. The dominant peak at 30 ppm is assigned to -CH- and -CH2- belonging to both open and ring carbohydrates and to the linear -CH2- groups of the diamine aliphatic chains in the NIPU urethanes formed, predominating in the NIPU resin.
Figure 5: CP-MAS 13C NMR of non-isocyanate polyurethane (NIPU) chestnut tannin extract bio-foam
Finally it is worth to notice that among all the types of oligomers observed in the foam there are a few more that have been observed in the system such as flavogallonic acid or valoneic acid [6] linked to a pentagalloyl glucose, at respectively 1390 and 1426 Da, and glucose esters of citric acid hardener such as the species at 699 Da (XIII).
This confirms that, even under the reaction conditions of a bio-foam, citric acid is not only the catalyst of the foaming reaction but also cross-links the hydrolysable tannin, especially by reacting with the carbohydrate fraction linked to the polyphenolic part of the tannin extract. The reaction of citric acid with carbohydrates monomers and oligomers has already been studied in depth previously [26].
This shows the complex system in hydrolysable tannin extracts in which a tannin foams needed to be developed (Table S1 in Appendix A).
The analysis work presented here shows the multitude of species initially present in commercial chestnut wood tannin extract as well the complex chemical species environment formed during the preparation of this hydrolysable tannin NIPU foams. The instrumental chemical analysis has shown that gallic acid and gallic acid residues linked to carbohydrates are cross-linked by the reaction with dimethyl carbonate and diamine, but that the same cross-linking occurs between the glucose residues which are an inherent part of the tannin itself, as well as mixed cross-linking of gallic acid residues and glucose residues. Such reactions occurs both with the lower molecular weight species formed by cleavage of the tannin polymer during its extraction process, but more interestingly also between gallic acid esterified glucose chains and the glucoses of equivalent carbohydrate chains. The analysis confirms the formation of non-isocyanate polyurethane bridges between all these species. It also confirms that citric acid is not only the catalyst of foaming, but that it reacts covalently and participate to the cross-linking of the total foam system by esterifying glucose residues in the hydrolysable tannin, and possibly also some of the phenolic material. As regards the way in which galloyl glucoses are linked to each other, all the 4 manner possible, including the two already mentioned in the literature, appears to occur but with the likely predominance of long glucose chains linked by glycosidic bridges and with gallic acid and ellagic acid residues esterifying to different degrees the glucoses in the chain.
Funding Statement: The authors received no specific funding for this study.
Conflicts of Interest: The authors declare that they have no conflicts of interest to report regarding the present study.
References
1. Kulvik, E. (1976). Chestnut wood tannin extracts in plywood adhesives. Adhesives Age, 19(3), 19–21. [Google Scholar]
2. Spina, S., Zhou, X., Segovia, C., Pizzi, A., Romagnoli, M. et al. (2013). Phenolic resin adhesives based on chestnut (Castanea sativa) hydrolysable tannins. Journal of Adhesion Science and Technology, 27(18–19), 2103–2111. https://doi.org/10.1080/01694243.2012.697673 [Google Scholar] [CrossRef]
3. Lagel, M. C., Pizzi, A., Giovando, S., Celzard, A. (2014). Development and characterisation of phenolic foams with phenol-formaldehyde-chestnut tannins resins. Journal of Renewable Materials, 2(3), 220–229. https://doi.org/10.7569/JRM.2014.634113 [Google Scholar] [CrossRef]
4. Giovando, S., Pizzi, A., Pasch, H., Pretorius, N. (2013). Structure and oligomers distribution of commercial tara (Caesalpina spinosa) hydrolysable tannin. ProLigno, 9(1), 22–31. [Google Scholar]
5. Caller, L. (1989). Le fabbriche italiane di estratto di castagno. San Michele Mondovi (CNItaly: Silva Chimica. [Google Scholar]
6. Pasch, H., Pizzi, A. (2002). On the macromolecular structure of chestnut ellagitannins by MALDI-TOF mass spectrometry. Journal of Applied Polymer Science, 85(2), 429–437. https://doi.org/10.1002/(ISSN)1097-4628 [Google Scholar] [CrossRef]
7. Pizzi, A., Pasch, H., Rode, K., Giovando, S. (2009). Polymer structure of commercial hydrolysable tannins by MALDI-TOF mass spectrometry. Journal of Applied Polymer Science, 113(6), 3847–3859. https://doi.org/10.1002/app.30377 [Google Scholar] [CrossRef]
8. Radebe, N., Rode, K., Pizzi, K., Giovando, S., Pasch, H. (2013). MALDI-TOF-CID for the microstructure elucidation of polymeric hydrolysable tannins. Journal of Applied Polymer Science, 128, 97–107. https://doi.org/10.1002/app.38156 [Google Scholar] [CrossRef]
9. Fengel, D., Wegener, G. (1984). Wood: Chemistry, ultrastructure, reactions. Berlin: de Gruyter. [Google Scholar]
10. Tang, H. R., Hancock, R. A., Covington, A. D. (1991). Studies on commercial tannin extracts. Proceedings of the XXI Congress of the International Union of Leather Trade Chemists, pp. 1503–1527. Barcelona, Spain. [Google Scholar]
11. Thébault, M., Pizzi, A., Dumarçay, S., Gerardin, P., Fredon, E. et al. (2014). Polyurethanes from hydrolysable tannins obtained without using isocyanates. Industrial Crops and Products, 59, 329–336. https://doi.org/10.1016/j.indcrop.2014.05.036 [Google Scholar] [CrossRef]
12. Pizzi, A. (2019). Tannin-based biofoams. Journal of Renewable Materials, 7(5), 477–492. https://doi.org/10.32604/jrm.2019.06511 [Google Scholar] [CrossRef]
13. Sahimim, W., Boer, F. D., Chapuis, H., Obonou-Akong, F., Pizzi, A. et al. (2022). Feasibility study of the synthesis of isocyanate-free polyurethanes from catechin. Journal of Renewable Materials, 10(5), 1175–1184. https://doi.org/10.32604/jrm.2022.016365 [Google Scholar] [CrossRef]
14. Sarazin, J., Pizzi, A., Amirou, S., Schmidt, D., Sernek, M. (2021). Organosolv lignin non-isocyanate based polyurethanes (NIPU) as wood adhesive. Journal of Renewable Materials, 9(5), 881–907. https://doi.org/10.32604/jrm.2021.015047 [Google Scholar] [CrossRef]
15. Azadeh, E., Chen, X., Pizzi, A., Gérardin, C., Gérardin, P. et al. (2022). Self-blowing non-isocyanate polyurethane foams based on hydrolysable tannins. Journal of Renewable Materials, 10(12), 3217–3227. https://doi.org/10.32604/jrm.2022.022740 [Google Scholar] [CrossRef]
16. Chen, X., Xi, X., Pizzi, A., Fredon, E., Zhou, X. et al. (2020). Preparation and characterization of condensed tannin non-isocyanate polyurethane (NIPU) rigid foams by ambient temperature blowing. Polymers, 12(4), 750. https://doi.org/10.3390/polym12040750 [Google Scholar] [PubMed] [CrossRef]
17. Chen, X., Pizzi, A., Xi, X., Zhou, X., Fredon, E. et al. (2021). Soy protein isolate non-isocyanates polyurethanes (NIPU) wood adhesives. Journal of Renewable Materials, 9(6), 1045–1057. https://doi.org/10.32604/jrm.2021.015066 [Google Scholar] [CrossRef]
18. Xi, X., Pizzi, A., Delmotte, L. (2018). Isocyanate-free polyurethane coatings and adhesives from mono- and di-saccharides. Polymers, 10, 402. https://doi.org/10.3390/polym10040402 [Google Scholar] [PubMed] [CrossRef]
19. Xi, X., Pizzi, A., Gerardin, C., Du, G. (2019). Glucose-based non-isocyanate polyurethane biofoams. Journal of Renewable Materials, 7(3), 301–312. https://doi.org/10.32604/jrm.2019.04174 [Google Scholar] [CrossRef]
20. Pretsch, E., Clerc, T., Seibl, J., Simon, W. (1989). Tables of spectral data for structure determination of organic compounds: 13C-NMR, 1H-NMR, IR, MS, UV/VIS. Second editionBerlin: Springer-Verlag. [Google Scholar]
21. Wehrli, F. W., Wirthlin, T. (1978). Interpretation of 13C NMR spectra. London: Heyden. [Google Scholar]
22. Drovou, S., Pizzi, A., Lacoste, C., Zhang, J., Abdalla, S. et al. (2015). Flavonoid tannins linked to long carbohydrate chains–MALDI ToF analysis of the tannin extract of the African locust bean. Industrial Crops and Products, 67, 25–32. https://doi.org/10.1016/j.indcrop.2015.01.004 [Google Scholar] [CrossRef]
23. Konai, N., Raidandi, D., Pizzi, A., Meva’a, L. (2017). Characterisation of Ficus sycomorus using ATR-FTMIR, MALDI-TOF MS and 13C NMR methods. European Journal of Wood and Wood Products, 75(5), 807–815. https://doi.org/10.1007/s00107-017-1177-8 [Google Scholar] [CrossRef]
24. Santos Ucha, J., Antorrena, G., Freire, S., Pizzi, A., Gonzalez-Alvarez, J. (2017). Environmentally friendly wood adhesives based on chestnut (Castanea sativa) shell tannins. European Journal of Wood and Wood Products, 75(1), 89–100. https://doi.org/10.1007/s00107-016-1054-x [Google Scholar] [CrossRef]
25. Cesprini, E., de Iseppi, A., Giovando, S., Tarabra, E., Zanetti, M. et al. (2022). Chemical characterization of cherry (Prunus avium) extract in comparison with commercial mimosa and chestnut tannins. Wood Science and Technology, 56, 1455–1473. https://doi.org/10.1007/s00226-022-01401-1 [Google Scholar] [CrossRef]
26. Del Menezzi, C., Amirou, S., Pizzi, A., Xi, X., Delmotte, L. (2018). Reactions with wood carbohydrates and lignin of citric acid as a bond promoter of wood veneer panels. Polymers, 10, 833. https://doi.org/10.3390/polym10080833 [Google Scholar] [PubMed] [CrossRef]
Appendix A
Figure S1: MALDI ToF Spectra of chestnut tannin extract non-isocyanate polyurethane (NIPU) bio-foam in the 1400–1800 Da range
Cite This Article
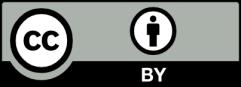
This work is licensed under a Creative Commons Attribution 4.0 International License , which permits unrestricted use, distribution, and reproduction in any medium, provided the original work is properly cited.