Open Access
ARTICLE
Effect of Amine Type on Lignin Modification to Evaluate Its Reactivity in Polyol Construction for Non-Isocyanate Polyurethanes (NIPU)
1 Department of Wood Science and Technology, Faculty of Natural Resources, Tarbiat Modares University, Tehran, Iran
2 Department of Resin and Additives, Institute for Color Science and Technology, Tehran, Iran
3 LERMAB, University of Lorraine, Blvd des Aiguillettes, Nancy, France
* Corresponding Authors: Antonio Pizzi. Email: ; Fatemeh Hassani Khorshidi. Email:
Journal of Renewable Materials 2023, 11(5), 2171-2189. https://doi.org/10.32604/jrm.2023.027835
Received 17 November 2022; Accepted 13 December 2022; Issue published 13 February 2023
Abstract
Polyols are groups of organic compounds which contain carbon and are randomly linked to other atoms, especially carbon-carbon and carbon-hydrogen. These compounds are mainly used as reactants to make other polymers. Among biopolymers, lignin is regarded as the base of a new polymer in polyol construction. The present study aimed to investigate the effects of amine type (diethylenetriamine and ethylenediamine) on the modification of lignin-based polyols, so as to provide an alternative to petroleum polyols and, in turn, increase functional groups and reduce their harm to humans’ health and the environment. To this aim, first, lignin was extracted from raw liquor. Next, the extracted lignin was reacted with diethylenetriamine (DETA) and ethylenediamine (EDA). Finally, the Mannich method was used for the reaction between amine lignin and propylene carbonate. The results of the Fourier Transform Infrared (FTIR) spectroscopy analysis showed that modification with DETA led to more structural change in lignin and peak 1100 indicates the presence of C–O bond related to urethane bonds in modified lignin. Moreover, adding propylene carbonate to aminated lignin did not result in much change in the results of the FTIR analysis. Additionally, urethane bonds can be seen in the results of GPC at 400°C–500°C. Furthermore, a slight decrease in thermal stability was observed in lignin modified with amine and propylene carbonate, compared to the raw lignin sample.Graphic Abstract
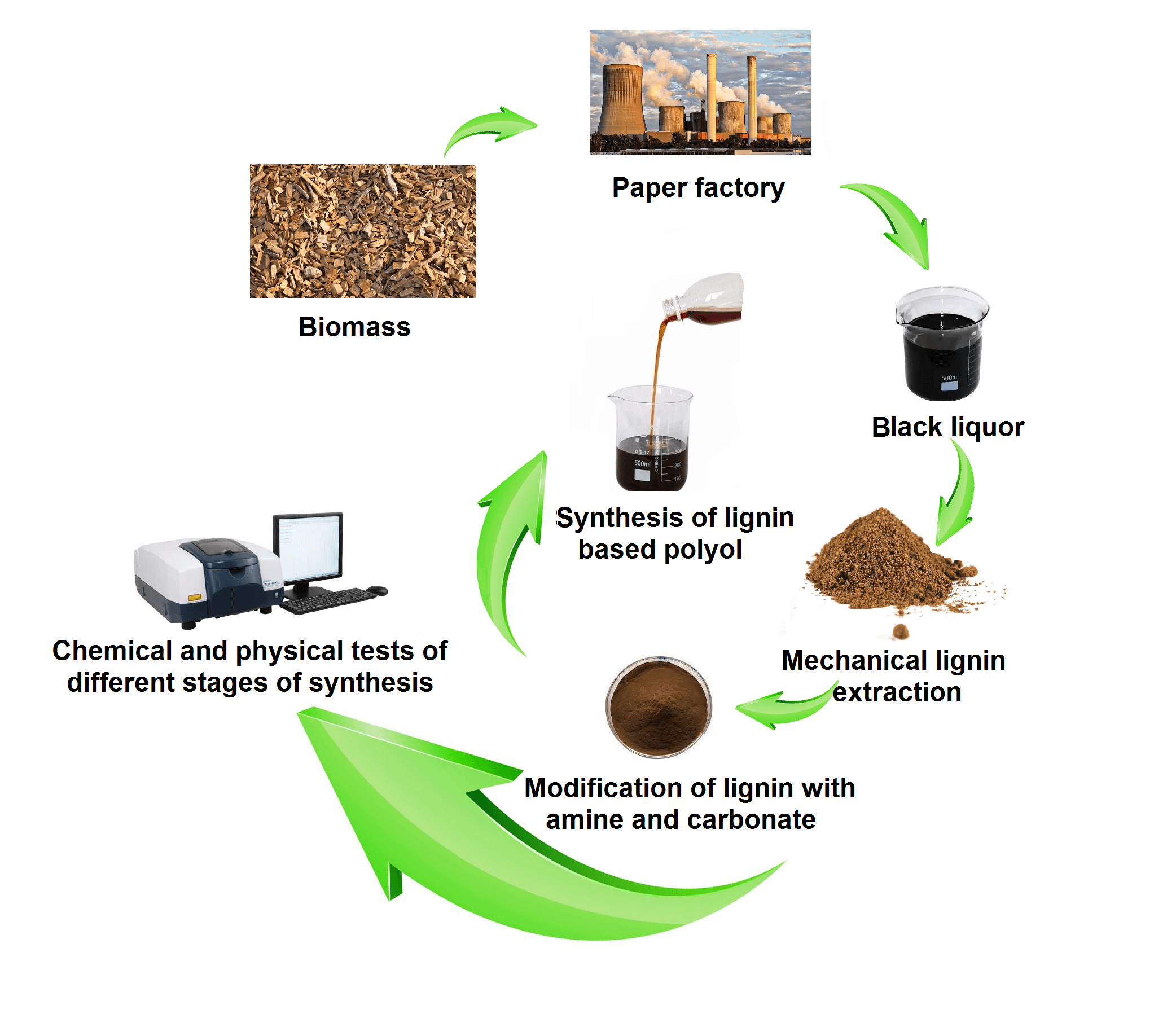
Keywords
Polyols belong to the group of organic compounds which contain carbon and are randomly attached to other atoms, especially carbon-carbon and carbon-hydrogen. These compounds, with several hydroxyl functional groups, are available for organic reactions and are principally used as reactants to make other polymers.
They can be categorized according to their ultimate application. Polyols with higher molecular weights (between 2000 and 10,000 g/mol) are applied to make more flexible polyurethanes, whereas polyols with lower molecular weights are used to make stiffer products. Luo et al. [1] and Chen et al. [2] stated in their research that lignin is a good candidate for polymerization and chemical modification to prepare stable polyurethane materials.
Gondaliya et al. [3], in their research, used lignin as a partial polyol substitute in flexible polyurethane foam. In the research of Saražin et al. [4] non-isocyanate polyurethane a wood adhesive was produced from organosolv lignin, which is a bio-sourced raw material, produced in large quantities as a by-product of the paper industry.
The use of polyols has several advantages: a) high solubility of simple metal salts (similarl to water) which are used as raw materials for the synthesis of many nanomaterials; b) high boiling points up to 320°C; c) utilization of coordination properties to functionalize the surface or create colloidal stability in different nanoparticles; d) very high adaptability, which means that they can be used for some specific syntheses, from the lower molecular weight polyols such as ethylene glycol to the higher molecular weight compounds such as polyethylene glycol.
Noteworthy is the fact that some polyols also have low toxicity, high biodegradability, and biocompatibility. Some polyols are FDA-approved, and some others are known as green solvents [5].
Biodegradable polyols are polymers that decompose after serving their purpose through a bacterial decomposition process. This decomposition leads to the formation of by-products such as CO2, N2, water, biomass, and mineral salts. These polymers form either naturally or are synthesized and are mainly composed of esters, amides, and ethers functional groups. Their properties and decomposition mechanisms are determined based on their exact structures. It should also be stated that these polymers are often synthesized through compression reactions, open-ring polymerization, and metal catalysts. There are many examples and applications of degradable polymers.
Biodegradable polymers are classified into four main categories based on their source of production:
A) Agricultural biomass products such as starch, cellulose, chitosan, lignin, and proteins are major sources of renewable biodegradable polymers that can be extracted directly;
B) Biodegradable polymers produced from the activity of micro-organisms such as polyhydroxy alkanoates;
C) Polymers resulting from biotechnological processes such as polylactides, which are widely used in medicine and pharmacy; and
D) Polymers derived from petrochemical monomers such as caprolactones [6,7].
Of the above-mentioned biopolymers, lignin is considered to be a polymer source in the production of polyols. Lignin, as a very important renewable material, is the second most abundant biopolymer on earth after cellulose and has a heterogeneous and amorphous structure, with many hydroxyl groups and aromatic rings.
Based on known lignin properties, among the various methods for its chemical modification, amination is one of the most promising ones because amino groups can be ionized under acidic conditions [8]. Amines are organic bases, to which a central nitrogen atom and one, two, or three alkyl groups are attached, named type one amine, type two amine, and type three amine, respectively. Amines are usually extracted from ammonia replacing the hydrogens linked to alkyl groups. Diethylenetriamine (DETA) and ethylenediamine (EDA) are among the amines used to aminate organic compounds, including lignin. The formation of amine groups is rather simple and increases the structural strength and resistance to hydrolysis of polyols.
The second method used to modify lignin is to react it with propylene carbonate. Due to its high vapor pressure, toxicity, flammability, and carcinogenicity, the use of propylene oxide in lignin modification reactions are not advisable. Therefore, with these considerations in mind, the organic five-membered ring of propylene carbonate is instead preferable to propylene oxide for its use in reactions. This organic material is known as a compound with low toxicity, and low vapor pressure, biodegradability, solubility, and a high boiling [9].
The purpose of the two-stage modification of lignin with propylene carbonate is to improve its solubility and increase its reactivity. In this reaction, lignin is first reacted with the amine. The aminated product is next reacted with propylene carbonate and end hydroxyl groups are developed [10].
Xue et al. [11] proposed an innovative type of solvent-free and catalyst-free process to obtain a hybrid non-isocyanate polyurethane (HNIPU). The researchers used ethylenediamine (EDA), diethylenetriamine (DETA), triethylenetetramine (TETA) and tetraethylenepentamine (TEPA) in reaction with ethylene carbonate (EC) to obtain four bi(hydroxyethyloxycarbonylamine)alkane (BHA)s. The results of TGA thermal analysis and DTG derivative thermogravimetry showed that the obtained HNIPUs had good thermal stability and can, thus, be considered heat resistant coatings.
In another study, Hu et al. [12] investigated an environmentally-friendly and non-toxic route for the synthesis of lignin-based non-isocyanate polyurethane networks. Specifically, the NH2-terminated polyhydroxy urethane prepolymer was first synthesized from the 6-membered cyclic bicarbonate BCC and diamine through a ring-opening reaction. Subsequently, lignin-based non-isocyanate polyurethanes were synthesized. The structural, mechanical, and thermal properties of NIPU were determined. DMA analysis and TGA thermal analysis results showed that tensile strength, Young’s modulus, toughness, storage modulus, glass transition temperature, and thermal stability of lignin-based NIPUs gradually increased in parallel with the increase in lignin content.
Non-isocyanate polyurethanes (NIPU) have been in the spotlight of many researchers for quite some time now [13–17]. The more established route to prepare them is through the preparation and use of cyclic carbonates [18–22]. More recently a rather easier route using a simple aliphatic carbonate, namely dimethyl carbonate, has been found [23–27]. All of these routes are different from the classical approach using isocyanates, even if using natural polyols [28]. The dimethyl carbonate route has led to applicable NIPUs as adhesives and coatings and has been pursued with some success, and moreover by using a number of biomaterials [29–33]. The route presented in this paper is another, different, alternative approach to preparing NIPUs from biosourced materials such as lignin.
With respect to the above-mentioned points, the present study investigated the modification of lignin with DETA, EDA, and propylene carbonate in the manufacture of basic lignin polyols to provide an alternative to petroleum polyols and finally to find an alternative route to the preparation of non-isocyanate polyurethanes (NIPU). This can increase the number of functional groups and reduce the harmful effects on health and the environment.
2.1 Extraction of Lignin from Liqueur
First, some liqueur was supplied from Mazandaran Wood and Paper Factory. The production method of paper pulp in this factory was a mechanical pulping process. Next, to prepare the required lignin, the researchers added 20-percent sulfuric acid to a liter of liqueur with a PH of about 12 to 13, which resulted in a mixture with a PH of 2–3, causing the lignin to precipitate. This precipitated lignin was then dried in an oven at a temperature of about 40°C. Finally, the resulting powder was washed three times again with methanol. The residual amount and lignin extraction efficiency were measured according to the method introduced in [34].
2.2 Modification of Lignin with Amine (DETA and EDA)
To aminate lignin, the researchers first heated 10 g of the extracted lignin and 3 g of the DETA in 50 cc of methanol solution and 50 cc of xylene solution at a ratio of 1:1 at 75°C for 6 h. After the completion of the reaction, the reaction mixture was cooled to ambient temperature, and the resulting precipitate was first passed through the polyester sulfone membrane with a pore size of 0.22 μm and then washed with methanol. The solid residue, the aminated lignin, was then washed 4 times with methanol solution and was finally dried in a vacuum oven at 30°C. The same steps were repeated to modify the lignin with ethylenediamine.
2.3 Modification of Amino Lignin with Propylene Carbonate (PC)
The Mannich method was used for the reaction between amino lignin and propylene carbonate. As shown in Figs. 1 and 2. In this process, 9 g of amino lignin was dissolved with 10 g of PC and 150 cc of chloroform. Subsequent to this, a certain amount of DBTDL catalyst was added to the reaction mixture. The reaction proceeded for 6 h at 65°C at atmospheric pressure. When the reaction was completed, the reaction mixture was cooled to ambient temperature and the precipitate was first passed through the polyester sulfone membrane with a pore size of 0.22 μm and then washed with methanol. The product was next dried in a vacuum oven at 30°C. All the chemicals used in this research were obtained from the German brand Merck Schuchardt.
Figure 1: The first step is the reaction of ethylene diamine with unsaturated areas on lignin and the second step is the reaction of propylene carbonate with the amines formed in the first step
Figure 2: The first step is the reaction of diethylenetriamine with unsaturated areas on lignin and the second step is the reaction of propylene carbonate with the amines formed in the first step
2.4 Fourier Transform Infrared (FTIR) Analysis
Fourier transform infrared analysis was performed using the Bruker Vertex 80 system, manufactured by Arvin Bonyan Tajhiz according to ASTM D8036-16 to study changes in lignin functional groups [35]. KBr tablet samples were prepared with a concentration of 1% of the weight of lignin extracted from liqueur (L1), amino lignin (L2), and amino lignin of propylene carbonate (L3). To remove moisture from the samples, they were first dried in the open air and then for 6 h at 100°C in the oven. Next, by irradiating electromagnetic waves in the range of 400 to 4000 cm−1 with a resolution of 1 cm−1, the researchers recorded the FTIR sample spectrums.
2.5 Gel Permeation Chromatography (GPC)
The gel permeation chromatography test was performed according to ASTM D6579-11 to determine the molecular mass and separate the molecules of the amino carbonate lignin powder sample (L3) [36]. The separation of amino lignin polymers modified with polypropylene carbonate in the organic solvent tetrahydrofuran (THF) was conducted through the stationary phase of polystyrene. Lignin was dissolved in THF and injected into the column. Tetrahydrofuran was used as the mobile phase at a rate of 1 min/mL.
2.6 Measurement of Acid Number
The acid number of lignin was determined according to ASTM D4662-08 [37]. To this aim, the researchers dissolved 2 g of lignin in 50 ml of ethanol solution. The mixture was then titrated with a normal solution of 0.1 N sodium hydroxide. The acid number of the sample was then calculated using the following equation:
where C represents the titration volume of sodium hydroxide solution at the equivalence point (mL), B denotes the bulk solution volume (mL), n is the normality of sodium hydroxide solution (mL), and W refers to the sample weight (g).
The hydroxyl number of lignin modified with amine and polycarbonate was determined according to ASTM D4274-05 [34,38]. One gram of modified lignin and 10 ml of sterilization reagent (150 g of anhydridaphthalic, 100 g of pyridine, and 900 g of dioxane) were poured into Erlenmeyer, covered with aluminum foil, and then placed in a 100°C hot water bath for 30 min. After cooling the solution to room temperature, the researchers added 20 ml of dioxane and 5 ml of distilled water to it. Using a pH meter, the researchers titrated the mixture with a standard solution (sodium hydroxide 1 N). The hydroxyl number of the sample was then calculated using the following equation:
where b is the volume of sodium hydroxide solution required for sample titration (mL), a represents the bulk solution volume (mL), n is the normality of sodium hydroxide solution (mL), and W denotes the sample weight (g).
TGA-DTA thermal analysis (Thermal Gravimetric Analysis-Differential Thermal Analysis) is one of the widely used methods in material analysis. TGA-DTA thermal analysis measures the changes, due to heat, in the sample and provides the user with a graph. Thermal analysis was performed by Perkin Elmer Pyris Diamond device with a thermal gradient of 5 °C/min.
By interpreting TGA-DTA thermal analysis, one can find out the thermal stability, i.e., reaction content in a chemical substance.
Structural changes of lignin, extracted from raw liquor, before and after its reaction with DETA and EDA are shown in Figs 3 and 4. In order to study the resulting FTIR spectra more accurately, the total amine depletion index of lignin was determined using the method of El-Mansouri et al. [39] and according to Eqs. (3) to (5) below.
Figure 3: FTIR spectrum of lignin (blue: before amination with DETA and red: after amination with DETA)
Figure 4: FTIR spectrum of lignin after amination with EDA
where KOH shows the total amount of hydroxyl groups, KOHar indicates the amount of aromatic phenolic hydroxyl groups, KOHal refers to the amount of aliphatic hydroxyl groups, and Amin index is the amination index. The assignement of the different FTIR signals are shown in Table 1 and the calculated results are given in Tables 2 and 3
Fig. 3 shows that in lignin aminated with DETA, the wave intensity at peaks of 3200–3400 cm−1, which are related to the hydroxyl groups of lignin, is reduced, and the wavelength of 1460 cm−1, which belongs to the hydrocarbon groups, has somewhat increased.
Fig. 4 reveals that in lignin aminated with EDA, unlike its modification with DETA, the wave intensity at peaks of 3200–3400 cm−1 does not change significantly.
The results of the FTIR test of lignin aminated with DETA and EDA indicate that the wave intensity at 1710–1715 cm−1 peaks, relating to the carbonyl and carboxylic groups, and the peaks in the 700–800 cm−1 range, which belong to the aromatic rings and alkene hydrocarbons of methylene groups, are completely eliminated.
The results also show that the peaks in the range of 1035–1130 cm−1, which belong to the groups of hydrocarbons in syringyl and carbon monoxides in secondary alcohols and aliphatic ethers, the wave intensity in the peaks of 1425–1605 cm−1, belonging to the aromatic ring, the peaks in the range of 1330–1340 cm−1, relating to the carbon monoxide and hydroxide groups, and the 1035–1130 cm−1 peaks, which belong to the carbon monoxide group in aliphatic ethers, have been completely removed after the modification of lignin with DETA and EDA.
The wave intensity at 1710–1715 cm−1 peaks in the lignin modified with both amines belonging to the carbonyl and carboxylic groups is reduced and almost eliminated. Reducing the adsorption intensity ratio of the carbonyl group is a measure of crosslink density. Decreased carbonyl group uptake indicates an increase in adverse reactions [38]. It can be said that with decreasing crosslinking in polyols, their solubility increases [40] In parallel, peaks of 1035–1130, which belong to the carbon monoxide group in aliphatic ethers, decrease. The reduction of ether junctions reduces the molecular weight of lignin, which ultimately improves the reactivity potential of lignin [41].
As can be seen in the spectra, the integrals and peak positions of the alcoholic and phenolic hydroxyl groups in the 3200–3400 cm−1 spectra of DETA-modified lignin differ from those of unmodified lignin. These spectra reveal the reaction of DETA amines with lignin. The main drawbacks of this method are related to the amination reaction of lignin, which is often incomplete and in which a small number of hydroxyl groups remain unaminated [39]. Although this behavior has been observed by other researchers, it has been ignored [39].
As is shown in Table 1 [42], the total number of hydroxyl groups of lignin decreases after reaction with DETA. The amination index is 1.75, while the total number of hydroxyl groups after modification with EDA remains unchanged; El Mansouri et al. [43] proved that increasing the lignin modification time to more than 10 h slightly reduces the number of aromatic hydroxyl groups, possibly due to secondary reactions of lignin condensation.
The amination of lignin with DETA significantly reduces the amine content of aliphatic hydroxyl groups, which indicates that lignin has been aminated. One of the increasing applications of lignin is its use in the structure of synthetic polymers and in the manufacturing of various composites; if lignin is used as part of polyols, the more amino groups it has, the better and stronger the reaction will be with the formation of C–N bonds. The reaction of amino lignin with polycarbonate, while producing hydroxyl groups, also leads to the production of amide bonds, which can play an important role in improving polyol properties.
Furthermore, structural changes of lignin aminated with DETA before and after modification with propylene carbonate are displayed in Fig. 5 As can be seen, the spectral patterns of both samples before and after modification are very similar to propylene carbonate. Fig. 5, in turn, shows that the structure of DETA-aminated lignin remains almost unchanged after modification with propylene carbonate. However, the intensity of the 1330–1340 cm−1 peak belonging to the hydroxide and hydrocarbon groups in aminated lignin reacted with propylene carbonate increases slightly.
Figure 5: FTIR spectrum of DETA-aminated lignin with propylene carbonate (blue: before modification with propylene carbon and red: after modification with propylene carbon)
Fig. 6 indicates the structure of EDA-aminated lignin after the reaction with propylene. According to this figure, the intensity of the 1458 cm−1 wave in the amino lignin modified with propylene carbonate, corresponds to the C–H groups of the methylene group.
Figure 6: FTIR spectrum of EDA-aminated lignin with propylene carbonate (red: before modification with propylene carbonate and blue: after modification with propylene carbonate)
As stated above, the bonding of propylene carbonate with does confirm the presence of these bonds and the CO2 resulting from this reaction. Peak 1100 also indicates the amine in lignin causes the formation of urethane bonds. The presence of the 1650–1750 cm−1 peaks does indicate the presence of C–O groups belonging to urethane bonds. Moreover, the peak 3200 cm−1 shows NH tensile vibrations, and the 1350 cm−1 peak indicates NH flexural vibrations in lignin modified with both amines and PC.
The large hydrodynamic volume of the lignin molecule can be determined using gel permeation chromatography (GPC). Next, using the calibrated column, one can compute the number average molecular weight (Mn) and the weight average molecular weight (Mw). As a result, the molecular weight distribution can also be calculated. When working with GPC, it is very important to prevent the accumulation of lignin molecules in the solvent, which constitutes a serious challenge [44].
The results of GPC analysis of lignin modified with DETA and propylene carbonate are shown in Table 4 and Figs. 7 and 8. Also, Table 5 shows the molecular weights of conifer and broadleaf lignin obtained from the GPC analysis [45].
Figure 7: GPC test diffusion spectrum of lignin modified with DETA and propylene carbonate
Figure 8: Normal distribution of GPC test diffusion spectrum of lignin modified with DETA and propylene carbonate
The number average molecular weight of amino lignin modified with propylene carbonate was found to be 16652 Daltons, while the weight average molecular weight was 15765 Daltons, and the polydispersity index of modified lignin was calculated to be 1.05 (see Table 5) [43,44,46].
To obtain the molar value of hydroxyl groups per gram of modified lignin, it is necessary to calculate the weight of the groups (MAP) added to lignin, namely DETA and propylene carbonate [21].
In Eq. (6), the molecular weight of propylene carbonate amine groups is added, which equals 112.17 + 102.09 g/mol. The number 1 in (MAP-1) indicates the proton removed from OH lignin during the amination reaction.
MPAL is the weight of propylene-carbonated amino lignin, and N’OH/mAP is the molar of hydroxyl groups per weight of lignin amine propylene carbonate. By rearranging Eq. (1), one arrives at Eq. (2). In this case, the molar of hydroxyl groups is calculated per gram of propylene-carbonated amino lignin:
Using N’OH/mAP, as well as Eqs. (6) and (7), the researchers calculated the number of hydroxyl groups of lignin per 1 mol of chain and the mean numerical molecular weight of lignin:
In Eqs. (6) and (7), Mn.AP represents the molecular weight of propylene-carbonated amino lignin, nOH/nL is the molar of lignin hydroxyl groups per 1 mol of lignin chains, and MnL is the mean numerical molecular weight of lignin. Table 6 shows the weight average molecular weights, the number average molecular weights, and molecular weight distributions of propylene-carbonated amino lignin, together with the results of calculations for the numerical molecular weight of lignin and moles of lignin hydroxyl groups per mole of lignin chains.
Rajendran et al. [47] mixed a combination of adipic acid with different glycols four times for polyol synthesis and used zinc acetylacetonate as a catalyst. The reaction was carried out for 3 h at 220 mmHg until the acid number dropped below 1. The obtained polyol had an acid number of 0.2, a hydroxyl number of 56, and a mean molecular mass of 2000.
Murayama et al. [48] synthesized a type of polyester polyol using adipic acid and 2, 4-diethyl-1 and 5-pentane diol in an inert nitrogen atmosphere. The obtained polyester polyol had an acid number of 0.2, a hydroxyl number of 56, and a mean molecular mass of 2000.
Allauddin et al. [49] synthesized a polyol with a hydroxyl number of 240 using the reaction of adipic acid and isophthalic-anhydride. In this reaction, a 2-liter 4-port reactor, a mechanical stirrer, and a nitrogen source were used. The reaction continued for several hours until the acid number dropped below 5. The obtained polyol molecular mass was 2687.
To prepare a polyurethane, Cook [50] synthesized a linear polyol using dimethylglutarate and diethylene glycol. The reaction was performed under nitrogen-free atmosphere, and the reaction temperature rose from 170°C to 215°C. In this reaction, the catalyst was tin-2-ethylhexanoate. The obtained polyol was black and viscous and had an acid number of 0.25, a hydroxyl number of 53.9, and a molecular mass of 2072.
In the present work, the results of gel permeation chromatography of modified lignin and the mean molecular weight of lignin extracted from liquor showed that lignin was converted into a lower molecular weight after modification. Comparison of the results with previous research also indicated that the basic lignin polyol prepared in this work had a lower molecular weight than the existing synthetic and natural polyols, which can be due to the mechanical degradation of lignin during its preparation and modification. Due to alkaline hydrolysis and rupture of aryl ether bonds during de-lignification, the lignin in the black liquor resulting from the pulping process had a lower molecular weight and a higher number of active functional groups, such as phenolic and aliphatic hydroxyl groups, in comparison with the lignocellulosic raw material. Therefore, they had aquired a greater potential for reaction [51].
The first characteristic of polyols is the presence of terminal hydroxyl groups for the reaction and production of various products. The hydroxyl number is a standard measure for quality control of polyols. This number is also used in determining the polymer formulation of polyurethane systems [52].
In this work, the hydroxyl number was determined through the modification of lignin with DETA and propylene carbonate and through the modification of lignin with EDA and propylene carbonate. In the former case, the hydroxyl number was calculated to be 848 (mgKOH/g), and in the latter case, this number was 2220 (mgKOH/g), which showed an increasing trend.
Mahmood et al. [53] research project involved producing polyols based on lignin kraft (KL) with a relatively high hydroxyl number. In this study, they prepared polyols with a hydroxyl number of 352 (mgKOH/g) and a molecular weight of 3310 (g/mol). These polyols were derived from lignin kraft by direct hydrolysis using NaOH as a catalyst and without any organic solvents.
In another study, Perez-Arce et al. [54] prepared and analyzed a family of lignin-based polyols using a new synthetic approach. This approach involved the polymerization reaction of the cationic ring opening of oxidants in the presence of tetrahydrofuran, as a solvent and a monomer, and organosol lignin. The hydroxyl number ranged from 53 to 253 (mgKOH/g), and the mean molecular weight ranged from 2730 to 30258 g/mol.
Li et al. [55] used alkaline lignin as a by-product manufactured during bioremediation in the production of polyurethane foams. The results indicated that the produced polyester had better thermal stability and higher compressive strength than petroleum-based polyurethanes. The hydroxyl number of these polyols was 420 (mgKOH/g).
Cross et al. [56] prepared polyester polyol using 1, 2-propylene glycol, trimethylol propane, phthalic anhydride. The resulting product had an acid number of about 5 and a hydroxyl number of 78.
Vogt et al. [57] using adipic acid and diethylene glycol, synthesized polyols that were linear. In this reaction, taking 14 h, a tetraalkyl titanate-tin-alkanate catalyst was used. The resulting polyol had an acid number of 0.6 and a hydroxyl number of 46.
As can be seen, the lignin-based polyols prepared in this process had a much higher hydroxyl number than the petroleum-based polyols, as well as other similar lignin-based polyols, the same as in Tables 7 to 8 [58,59]. Therefore, it can be said that the lignin-based polyols modifed with DETA and polypropylene carbonate has a higher reactivity potential than other polyols used for the same purpose (Table 9).
3.4 Thermogravimetric Heat Analysis (TGA)
The amount of weight loss of the samples is displayed in the following figures and Table 10. As can be seen, the graphs of crude lignin and lignin modified with amine and propylene carbonate are almost identical in both forms. Moreover, the thermal degradation of crude lignin and modified lignin takes place in one step, which can be divided into three regions. In the first and second regions, the degradation and weight loss in crude lignin starts at about 100°C and then increases. In turn, the third region, which starts at 600°C, involves the complete degradation of unmodified lignin to ash.
The first stage of weight loss of lignin is attributed to the evaporation of water and other volatile compounds, and the second stage of thermal decomposition is attributed to the disintegration of syringyl, guaiacyl, and p-hydroxyphenyl polymer units [60]. It should also be noted that the degradation and weight loss in modified lignin starts from the very beginning. However, its rate decreases slightly, compared to that in crude lignin. As stated previously, aminated lignin is completely reduced to ash at 600°C.
When lignin is pure or carbohydrate-free, losses occur due to water evaporation, and light gases because of the separation of β-O-4 bonds in the lignin structure and CO2 release because of the disintegration of weak ester bonds in the aminated propylene-carbonate lignin [60].
The abundance of these bonds in lignin determines its thermal stability [61]. In fact, the higher the ratio of β-O-4 bonds, the greater its stability. C-C bonds are also degraded at 200°C to 400°C in modified lignin, and the propylene glycol structures are removed. Also, urethane bonds formed through the combination of PC and amine with lignin are destroyed at a temperature of 400°C–500°C.
3.5 DTG Lignin Mass Loss Derivative
The derivative curve of lignin mass loss as a function of temperature, obtained at a heating rate of 15 °C/min, is displayed on the TGA curve in the figure which is shown in Figs. 9 and 10.
Figure 9: Thermogravimetric spectrometry test: blue (lignin), green (lignin modified with DETA and propylene carbonate)
Figure 10: Thermogravimetric spectrometry test: blue (lignin), green (lignin modified with EDA and propylene carbonate)
In the temperature range studied, the DTG diagram shows several peaks. The first case, at very low temperatures, is related to dehydration. The peak is relatively sharp at a maximum of 340°C. The peak is surrounded on both sides by shoulders.
Most of the research works reported in the literature generally show two peaks in the DTG [62–64]. To the researcher’s best knowledge, only Watkins et al. [65] reported the presence of combs at 450°C, and Manara et al. [66]. They reported the presence of peaks at higher temperatures in the form of a broad band. Kim et al. [62] stated that these peaks are formed due to dehydration. In these peaks, β-O-4 bond breakage, C-C bond breakage, β-β bond breakage and polymerization reactions take place. The clarity and intensity of the peak related to the decomposition of β-O-4 bonds depend on the ratio of these bonds in lignin [21].
In modified lignin, degradation started at lower temperatures and lignin has completely lost its weight at 600 degrees.
They also showed that lignin without β-O-4 completely decomposed at 200°C–300°C. However, lignin with a lower frequency of β-O-4 bonds compared to C-C bonds is more resistant. In the case of lignin, where the ratio of β-O-4 bonds is equal to C-C bonds, peaks occur with relatively equal intensities.
In modified lignin, however, degradation begins at lower temperatures, and lignin completely loses its weight at 600°C. With the addition of amine and propylene carbonate, a slight decrease in thermal stability is observed for modified lignin samples, compared to crude lignin samples. These results can be attributed to the low molecular weight of modified lignin. The presence of oligomers in the modified lignin samples and the absence of significant intermolecular interactions in this case cause the samples to degrade at lower temperatures. The results obtained from GPC also confirm the reduction of molecular weight of the copolymers in the modified lignin samples, compared to the pure polymer.
1. The results of the FTIR analysis showed that peak 1100 indicates the presence of C-O bond related to urethane bonds in modified lignin.
2. The results of GPC of lignin modified showed that lignin was converted to a lower molecular weight after modification. This could be due to the mechanical degradation of lignin during its preparation and modification.
3. The lignin-based polyol prepared in this process has a much higher hydroxyl number than oil-based polyols. Therefore, it can be said that it has a high reactivity potential.
4. Urethane bonds formed by the combination of PC and amine with lignin can be seen in the results of GPC at 400°C–500°C.
Funding Statement: The authors received specific funding for this study from Tarbiat Modares University of Tehran, Iran.
Conflicts of Interest: The authors declare that they have no conflicts of interest to report regarding the present study.
References
1. Luo, S., Gao, L., Guo, W. (2020). Effect of incorporation of lignin as bio-polyol on the performance of rigid lightweight wood–polyurethane composite foams. Journal of Wood Science, 66(23), 1820–1828. DOI 10.1186/s10086-020-01872-5. [Google Scholar] [CrossRef]
2. Chen, Y., Zhang, H., Zhu, Z. (2020). High-value utilization of hydroxymethylated lignin in polyurethane adhesives. International Journal of Biological Macromolecules, 152, 775–785. DOI 10.1016/j.ijbiomac.2020.02.321. [Google Scholar] [CrossRef]
3. Gondaliya, A., Nejad, M. (2021). Lignin as a partial polyol replacement in polyurethane flexible foam. Molecules, 26(8), 2302. DOI 10.3390/molecules26082302. [Google Scholar] [CrossRef]
4. Saražin, J., Pizzi, A., Amirou, S., Schmiedl, D., Šernek, M. (2021). Organosolv lignin for non-isocyanate based polyurethanes (NIPU) as wood adhesive. Journal of Renewable Materials, 9(5), 881–907. DOI 10.32604/jrm.2021.015047. [Google Scholar] [CrossRef]
5. Dong, H., Chen, Y., Feldmann, C. (2015). Polyol synthesis of nanoparticles: Status and options regarding metals, oxides, chalcogenides, and non-metal elements. Green Chemistry, 17(8), 4107–4132. DOI 10.1039/C5GC00943J. [Google Scholar] [CrossRef]
6. Ramesh Babu, N. G., Anitha, N., Hema Kalai Rani, R. (2010). Recent trends in biodegradable products from. Biopolymers, 9, 30–34. [Google Scholar]
7. Averous, L., Laurichesse, S. (2014). Chemical modification of lignins: Towards biobased polymers. Progresses in Polymer Science, 39, 1266–1290. DOI 10.1016/j.progpolymsci.2013.11.004. [Google Scholar] [CrossRef]
8. Meister, J. (2002). Modification of lignin. Journal of Macromolecular Science Part C–Polymer Reviews, 42, 235–289. DOI 10.1081/MC-120004764. [Google Scholar] [CrossRef]
9. Kord, B., Sheikholeslami, A., Najafi, A. (2016). A study on creep behavior of a wood flour-polypropylene nanoclay hybrid composite. Iranian Journal of Wood and Paper Industries, 7(1), 1–12. [Google Scholar]
10. Kühnel, I., Podschun, J., Saake, B., Lehnen, R. (2015). Synthesis of lignin polyols via oxyalkylation with propylene carbonate. Holzforschung, 69(5), 531–538. DOI 10.1515/hf-2014-0068. [Google Scholar] [CrossRef]
11. Xue, D., Xue, B., Tang, R., Shen, C., Li1, X. et al. (2021). Synthesis of reprocessable lignin-based non-isocyanate poly(imine-hydroxyurethane)s networks. ACS Applied Materials & Interfaces, 6(1), 1–9. [Google Scholar]
12. Hu, S., Li, Y. (2014). Two-step sequential liquefaction of lignocellulosic biomass by crude glycerol for the production of polyols and polyurethane foams. Bioresource Technology, 161(6), 410–415. DOI 10.1016/j.biortech.2014.03.072. [Google Scholar] [CrossRef]
13. Rokicki, G., Piotrowska, A. (2002). A new route to polyurethanes from ethylene carbonate, diamines and diols. Polymer, 43, 2927–2935. DOI 10.1016/S0032-3861(02)00071-X. [Google Scholar] [CrossRef]
14. Kihara, N., Endo, T. (1993). Synthesis and properties of poly(hydroxyurethane)s. Journal of Polymer Science, Part A, 31, 2765–2773. DOI 10.1002/pola.1993.080311113. [Google Scholar] [CrossRef]
15. Kihara, N., Kushida, Y., Endo, T. (1996). Optically active poly(hydroxyurethane)s derived from cyclic carbonate and L-lysine derivatives. Journal of Polymer Science, Part A, 34, 2173–2179. DOI 10.1002/(SICI)1099-0518(199608)34:11<2173::AID-POLA10>3.0.CO;2-C. [Google Scholar] [CrossRef]
16. Tomita, H., Sanda, F., Endo, T. (2001). Structural analysis of polyhydroxyurethane obtained by polyaddition of bifunctional five-membered cyclic carbonate and diamine based on the model reaction. Journal of Polymer Science, Part A, 39, 851–859. DOI 10.1002/1099-0518(20010315)39:6<851::AID-POLA1058>3.0.CO;2-3. [Google Scholar] [CrossRef]
17. Tomita, H., Sanda, F., Endo, T. (2001). Polyaddition behavior of bis(five-and six-membered cyclic carbonate)s with diamine. Journal of Polymer Science, Part A, 39, 860–867. DOI 10.1002/1099-0518(20010315)39:6<860::AID-POLA1059>3.0.CO;2-2. [Google Scholar] [CrossRef]
18. Tomita, H., Sanda, F., Endo, T. (2001). Model reaction for the synthesis of polyhydroxyurethanes from cyclic carbonates with amines: Substituent effect on the reactivity and selectivity of ring-opening direction in the reaction of five-membered cyclic carbonates with amine. Journal of Polymer Science, Part A, 39, 3678–3685. DOI 10.1002/pola.10009. [Google Scholar] [CrossRef]
19. Birukov, O., Potashnikova, R., Leykin, A., Figovsky, O., Shapovalov, L. (2009). Advantages in chemistry and technology of non-isocyanate polyurethane. Journal of Scientific Israel-Technology Advances, 11, 160–167. [Google Scholar]
20. Figovsky, O., Shapovalov, L. (2002). Features of reaction amino-cyclocarbonate for production of new type polyurethanes. Macromolecular Symposia, 187, 325–332. DOI 10.1002/1521-3900(200209)187:1<325::AID-MASY325>3.0.CO;2-L. [Google Scholar] [CrossRef]
21. Camara, F., Benyahya, S., Besse, V., Boutevin, G., Auvergne, R. et al. (2014). Reactivity of secondary amines for the synthesis of nonisocyanate polyurethanes. European Polymer Journal, 55, 17–26. DOI 10.1016/j.eurpolymj.2014.03.011. [Google Scholar] [CrossRef]
22. Blattmann, H., Fleischer, M., Bähr, M., Mülhaupt, R. (2014). Isocyanate-and phosgene-free routes to polyfunctional cyclic carbonates and green polyurethanes by fixation of carbon dioxide. Macromolecular Rapid Communications, 35, 1238–1254. DOI 10.1002/marc.201400209. [Google Scholar] [CrossRef]
23. Xi, X., Pizzi, A., Delmotte, L. (2018). Isocyanate-free polyurethane coatings and adhesives from mono- and Di-saccharides. Polymers, 10, 402. DOI 10.3390/polym10040402. [Google Scholar] [CrossRef]
24. Xi, X., Wu, Z., Pizzi, A., Gerardin, C., Lei, H. et al. (2019). Non-isocyanate polyurethane adhesive from sucrose used for particleboard. Wood Science and. Technology, 53(2), 393–405. DOI 10.1007/s00226-019-01083-2. [Google Scholar] [CrossRef]
25. Xi, X., Pizzi, A., Gerardin, C., Du, G. (2019). Glucose-based non-isocyanate polyurethane biofoams. Journal of Renewable Materials, 7(3), 301–312. DOI 10.32604/jrm.2019.04174. [Google Scholar] [CrossRef]
26. Xi, X., Pizzi, A., Gerardin, C., Lei, H., Chen, X. et al. (2019). Preparation and evaluation of glucose based non-isocyanate polyurethane self-blowing rigid foams. Polymers, 11, 1802. DOI 10.3390/polym11111802. [Google Scholar] [CrossRef]
27. Chen, X., Li, J., Xi, X., Pizzi, A., Zhou, X. et al. (2020). Condensed glucose-tannin-based NIPU BioFoams of improved fire retardancy. Polymer Degradation and Stability, 175, 109121. DOI 10.1016/j.polymdegradstab.2020.109121. [Google Scholar] [CrossRef]
28. Beneš, H., Paruzel, A., Hodan, J., Trhlíková, O. (2018). Impact of natural oil-based recycled polyols on properties of cast polyurethanes. Journal of Renewable Materials, 6(7697–706. [Google Scholar]
29. Chen, X., Xi, X., Pizzi, A., Fredon, E., Zhou, X. et al. (2020). Preparation and characterizatuon of condensed tannin non-isocyanate polyurethane (NIPU) rigid foams by ambient temperature blowing. Polymers, 12, 750. DOI 10.3390/polym12040750. [Google Scholar] [CrossRef]
30. Chen, X., Pizzi, A., Xi, X., Zhou, X., Fredon, F. et al. (2021). Soy protein isolate non-isocyanates polyurethanes (NIPU) wood adhesives. Journal of Renewable Materials, 9(6), 1045–1057. DOI 10.32604/jrm.2021.015066. [Google Scholar] [CrossRef]
31. Sahmim, W., Boer, F. D., Chapuis, H., Obonou-Akong, F., Pizzi, A. et al. (2022). Feasibility study of the synthesis of isocyanate-free polyurethanes from catechin. Journal of Renewable Materials, 10(5), 1175–1184. DOI 10.32604/jrm.2022.016365. [Google Scholar] [CrossRef]
32. Chen, X., Pizzi, A., Fredon, F. C., Gerardin, C., Zhou, X. et al. (2022). Low curing temperature tannin-based non-isocyanate polyurethane (NIPU) wood adhesives: Preparation and properties evaluation. International Journal of Adhesion and Adhesives, 112, 103001. DOI 10.1016/j.ijadhadh.2021.103001. [Google Scholar] [CrossRef]
33. Azadeh, E., Chen, X., Pizzi, A., Gerardin, C., Gerardin, P. et al. (2022). Self-blowing non-isocyanate polyurethane foams based on hydrolysable tannins. Journal of Renewable Materials, 10(12), 3217–3227. DOI 10.32604/jrm.2022.022740. [Google Scholar] [CrossRef]
34. Yamada, T., Ono, H., (1999). Rapid liquefaction of lignocellulosic waste by using ethylene carbonate. Bioresource Technology, 70(1), 61–67. DOI 10.1016/S0960-8524(99)00008-5. [Google Scholar] [CrossRef]
35. American Society for Testing and Materials. ASTMD 8036-16, PA (2016). Standard test methods for polyurethane raw materials: Determination of dimer ratio in pure MDI, ASTM International, West Conshohocken. [Google Scholar]
36. American Society for Testing and Materials. ASTMD 6579-11 (2020). Standard test methods for for molecular weight averages and molecular weight distribution of hydrocarbon, rosin and terpene resins by size-exclusion chromatography. [Google Scholar]
37. American Society for Testing and Materials. ASTMD 4662-08 (2012). Standard test methods for testing polyurethane Raw materials: Determination of acidity as acid number of polyols. [Google Scholar]
38. American Society for Testing and Materials. ASTM D 4274-21, PA (2021). Standard test methods for testing polyurethane Raw materials: Determination of hydroxyl numbers of polyols, ASTM International, West Conshohocken. [Google Scholar]
39. El-Mansouri, N., Salvado, J. (2007). Analytical methods for determining green. functional groups of various technical lignin. Industrial Crops and Products, 26, 116–124. DOI 10.1016/j.indcrop.2007.02.006. [Google Scholar] [CrossRef]
40. Nasar, A. S., Mitsutoshi, J., Kakimoto, M. (2003). Synthesis and properties of polyurethane elastomers crosslinked with amine-terminated AB2-type hyperbranched polyamides. European Polymer Journal, 39(9), 1201–1208. DOI 10.1016/S0014-3057(02)00370-1. [Google Scholar] [CrossRef]
41. Hu, L., Pan, H., Zhou, Y., Zhang, M. (2011). Methods to improve lignin reactivity as a phenol substitute and as a replacement for other phenolic compounds: A brief review. BioResources, 6, 3515–3525. DOI 10.15376/biores. [Google Scholar] [CrossRef]
42. Mohamad Ebrahim, M. N., Mohamad Yosof, N. N., Hashim, A. (2007). Comparison studies on soda lignin and soda anthraquinone lignin. The Malaysian Journal of Analytical Sciences, 11(1), 206–212. [Google Scholar]
43. El Mansouri, N. E., Yuan, Q., Huang, F. (2011). Study of chemical modification of alkaline lignin by the glyoxalation reaction. Bioresources, 6(4), 4523–4536. [Google Scholar]
44. Gosselink, R., Abächerli, A., Semke, H., Malherbe, R., Käuper, P. et al. (2004). Analytical protocols for characterisation sulphur-free lignin. Industrial Crops and Products, 19(3), 271–281. DOI 10.1016/j.indcrop.2003.10.008. [Google Scholar] [CrossRef]
45. Brodin, I., (2009). Chemical properties and thermal behaviour of kraft lignins. KTH, school of chemical science and engineering (CHE). Fibre and Polymer Technology, 17, 1654–1081. [Google Scholar]
46. Bayerbach, R., Nguyen, V., Schurr, U., Meier, D. (2006). Characterisation of the water insoluble fraction from fast pyrolysis liquids (pyrolytic ligninPart III. Molar mass characteristics by SEC, MALDI-TOF-MS, LDI-TOF-MS and Py-FIMS. Journal of Analytical Applied Pyrolysis, 77, 95–101. DOI 10.1016/j.jaap.2006.02.002. [Google Scholar] [CrossRef]
47. Rajendran, G. P., Mahadevan, V., Srinivasan, M. (1982). Synthesis and properties of polyester based polyurethanes. European Polymer Journal, 18(11), 953–956. DOI 10.1016/0014-3057(82)90081-7. [Google Scholar] [CrossRef]
48. Murayama, T., Nakano, Y., Murata, S. (2005). Polyester. USA: Patent Application Publication. 0038224 Al. [Google Scholar]
49. Allauddin, S., Jena, K. K., Mishara, A. K., Radhika, K. R., Narayan et al. (2012). Synthesis and characterization of benzaldehyde modified acetoacetylated polyesters for polyurethane/urea coatings. Progress in Organic Coatings, 75(1–2), 131–138. DOI 10.1016/j.porgcoat.2012.04.008. [Google Scholar] [CrossRef]
50. Cook, W. H. (1975). Glutarate-containing polyester polyols. methods of preparation and polyurethane compositions derived therefrom. United States Patent, 4,096,129. [Google Scholar]
51. Behrooz, R., Younesi Kordkheili, H., Kazemi Najafi, S. (2009). Using kraft lignin as a compatibilizer in wood plastic composites. Iranian Journal of Wood and Paper Science Researches, 26(3), 454–465. [Google Scholar]
52. Ionescu, M. (2010). Chemistry and technology of polyols for polyurethanes, 2nd edition. UK: Rapra Technology Publisher. [Google Scholar]
53. Mahmood, N., Yuan, Z., Schmidt, J., Xu, C. (2013). Production of polyols via direct hydrolysis of kraft lignin: Effect of process parameters. Bioresource Technology, 139, 13–20. DOI 10.1016/j.biortech.2013.03.199. [Google Scholar] [CrossRef]
54. Perez-Arce, J., Centeno-Pedrazo, A., Labidi, J., Ochoa-Gómez, J. R., Garcia-Suarez, E. J. (2020). A novel and efficient approach to obtain lignin-based polyols with potential industrial applications. Polymer Chemistry, 11, 7362–7369. DOI 10.1039/D0PY01142H. [Google Scholar] [CrossRef]
55. Li, H., Shao, Q., Luo, H., Xu, J. (2016). Polyurethane foams from alkaline lignin-based polyether polyol. Journal of Applied Polymer Science, 133(14), 1–7. DOI 10.1002/app.43261. [Google Scholar] [CrossRef]
56. Cross, J. M., Hudson, G. A., Hixenbaug, J. C. (1975). Polyester polyols. United States Patent, 3,888,908. [Google Scholar]
57. Vogt, H. C., Patton, J. T. (1977). Process for the preparation of polyester polyols. United States Patent 4,018,815. [Google Scholar]
58. Huang, J., Fu, S., Gan, L. (2019). Structure and characterisics of lignin. In: Lignin chemistry and applications, pp. 25–50. ChemicalIndustry Press, Elsevier. [Google Scholar]
59. International Organization for Standardization, ISO14900. ICS: 83.080.10 (2017). Plastics-polyols for use in the production of polyurethane-determination of hydroxyl number. [Google Scholar]
60. Zhang, S., Wang, Z., Zhang, Y., Pan, H., Tao, L. (2016). Adsorption of methylene blue on organosolv lignin from rice straw. Procedia Environmental Sciences, 31(1), 3–11. [Google Scholar]
61. Chu, S., Subrahmanyam, A. V., Huber, G. W. (2013). The pyrolysis chemistry of a β-O-4 type oligomeric lignin model compound. Green Chemistry, 15(1), 125–136. DOI 10.1039/C2GC36332A. [Google Scholar] [CrossRef]
62. Kim, J. Y., Oh, S., Hwang, H., Kim, U. J., Choi, J. W. (2013). Structural features and thermal degradation properties of various lignin macromolecules obtained from poplar wood (Populus albaglandulosa). Polymer Degradation and Stability, 98, 1671–1678. DOI 10.1016/j.polymdegradstab.2013.06.008. [Google Scholar] [CrossRef]
63. Liu, Q., Wang, S., Zheng, Y., Luo, Z., Cen, K. (2008). Mechanism study of wood lignin pyrolysis by using TG-FTIR analysis. Journal of Analytical and Applied Pyrolysis, 82(1), 170–177. DOI 10.1016/j.jaap.2008.03.007. [Google Scholar] [CrossRef]
64. Jing, Z., Wang, X., Hu, J., Qian, L., Shen, D. et al. (2014). Thermal degradation of softwood lignin and hardwood lignin by TG-FTIR and Py-GC/MS. Polymer Degradation and Stability, 108, 133–138. DOI 10.1016/j.polymdegradstab.2014.06.006. [Google Scholar] [CrossRef]
65. Watkins, D., Nuruddin, M., Hosur, M., Tcherbi-Narteh, A., Jeelani, S. (2015). Extraction and characterization of lignin from different biomass resources. Journal of Material Research Technology, 4(1), 26–32. DOI 10.1016/j.jmrt.2014.10.009. [Google Scholar] [CrossRef]
66. Manara, P., Zabaniotou, A., Vanderghem, C., Richel, A. (2014). Lignin extraction from Mediterranean agro-wastes: Impact of pretreatment conditions on lignin chemical structure and thermal degradation behavior. Catalysis Today, 223, 25–34. DOI 10.1016/j.cattod.2013.10.065. [Google Scholar] [CrossRef]
Cite This Article
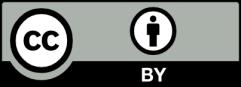
This work is licensed under a Creative Commons Attribution 4.0 International License , which permits unrestricted use, distribution, and reproduction in any medium, provided the original work is properly cited.