Open Access
ARTICLE
Preparation of Phase Change Concrete Using Environmentally Friendly Materials and Its Performance Study
1 Shandong Key Laboratory of Civil Engineering Disaster Prevention and Mitigation, Shandong University of Science and Technology, Qingdao, 266590, China
2 College of Civil Engineering and Architecture, Shandong University of Science and Technology, Qingdao, 266590, China
* Corresponding Author: Qianqian Lu. Email:
# These authors contribute equally to this paper and should be considered as co-first author
(This article belongs to the Special Issue: Sustainable Concrete with Recyclable Materials)
Journal of Renewable Materials 2023, 11(5), 2417-2431. https://doi.org/10.32604/jrm.2023.025443
Received 12 July 2022; Accepted 25 August 2022; Issue published 13 February 2023
Abstract
The control of carbon emissions and energy conservation, and environmental protection are hot spots of global concern. In this paper, phase change paraffin wax is applied to porous materials for adsorption and storage, and nature’s eco-friendly materials are selected as the porous matrix to propose an eco-friendly phase change concrete using eco-friendly materials as raw materials. It was obtained that the strength of the phase change concrete utilizing environmentally friendly materials was 25.4% to 36.8% lower than that of ordinary concrete, while some of the phase change light aggregates were found to produce slip damage with the cement paste in the damage study. By constructing a small-sized test room for thermal properties, we obtained a phase change concrete that utilizes environmentally friendly materials to control the temperature better than the commonly studied phase change concrete, with a peak temperature drop of up to 2.6°C in the phase change test room compared to the normal test room and a delay in the peak temperature.Keywords
Currently, the building industry accounts for more than 30% of global energy consumption, and its energy consumption is concentrated in the use phase of buildings, using the application of temperature-controlled equipment to maintain people’s comfort, consume energy and release carbon dioxide. Reducing the energy consumption of buildings is very important, and therefore, a new building concept is proposed-passive energy generation and conversion in buildings using solar, thermal and radiant energy.
Phase change materials (PCM) are used in buildings and belong to the development direction of green buildings [1,2]. The processing of building raw materials makes buildings more energy-saving and environmentally friendly. Phase-change building materials belong to the interdisciplinary subject of civil engineering and material physics and have broad research directions [3,4]. Min et al. [5] proposed the adsorption of octadecane phase change material based on graphite nanoflakes as a sizing material, and a new sizing phase change material (SSPCM) was prepared using the vacuum impregnation method to obtain a new sizing phase change material (SSPCM), and it was studied that the compressive strength and elastic modulus of concrete decreased with increasing content of SSPCM, and the decrease in compressive strength and elastic modulus was linearly proportional to the mass fraction of SSPCM in concrete. Fang et al. [6] devoted themselves to the preparation of phase change paraffin and carbon-based phase change composites. The high-performance paraffin carbon matrix composites were obtained to provide ideas for improving the stability of stone and thermal wax cycle stability rings in the future. Phase change concrete is widely used in the walls and slabs of buildings, which has a more important significance to the development of the low-carbon direction of the construction industry. In the process of phase change concrete research, many researchers in the development of concrete found that the addition of phase change materials in the concrete will make the mechanical properties of the concrete material to varying degrees of degradation. Cabeza et al. [7] conducted an experimental study on the mechanical properties of phase change concrete and found that the compressive and tensile strengths of the concrete were reduced to varying degrees when the phase change material was added to the wall, but it enabled the building to produce a heat passive system. Xu [8] used ceramic pellets as a carrier for phase change material adsorption and applied the prepared pellets to the building envelope, which largely reduced the leakage problem of phase change material by encapsulating the surface of ceramic pellets, and finally produced a new building envelope structure of phase change energy storage concrete. Wang et al. [9] prepared paraffin/vitrification phase change concrete using clay glass particles as a carrier and wrapped the surface of clay vitrification particles with triethylenetetramine, and concluded that paraffin/vitrification phase change concrete is more effective in blocking heat transfer phenomenon than ordinary concrete by temperature-time curve analysis. Zhang et al. [10] applied phase change materials to concrete blocks in winter conditions and conducted a comparison between air-conditioned rooms and non-air-conditioned rooms under phase change concrete block application, respectively, for air-conditioned rooms, the total heat dissipation in phase change concrete block rooms was 45% lower than that in ordinary concrete blocks, and for non-air-conditioned rooms, the average indoor temperature in phase change concrete block rooms was higher than that in ordinary concrete block rooms 2.45°C. Vinh et al. [11] investigated the potential of polymer concrete walls containing microencapsulated phase change materials for application in buildings under different environmental conditions. Two types of microencapsulated phase change concrete walls were tested over one year, and it was found that the application of such walls could significantly reduce the annual electricity consumption for heating/cooling. A quantitative tool was developed to design MPCM concrete walls according to different environmental requirements. Shen et al. [12] used ceramic particles as a porous matrix for phase change material adsorption to obtain a kind of concrete with shaped phase change material with paraffin wax adsorbed in ceramic particles, and the concrete mixed with phase change ceramic particles has a great improvement in thermal storage and temperature control capacity and can achieve both thermal performance and economic performance gains at the same time. Qu et al. [13] obtained that the thermal conductivity of concrete specimens decreased, and the thermal storage capacity increased after the addition of phase change materials by conducting partial phase change foam concrete specimen tests in the wall. Tu et al. [14] produced a phase change concrete wall to reduce the degree of influence of outdoor ambient temperature changes on indoor temperature, and the study obtained a phase change wall with small thermal conductivity and better thermal performance. It was found that the phase change concrete slab layer in the wall, when positioned close to the outdoors, can give full play to its heat absorption capacity. González et al. [15] used phase change materials to achieve thermal energy storage in heating floors through radiant heat by filling the macroscopic capsules with phase change materials. The experiments were designed to set the position of the heating pipes, as well as the variables of the width of the pipes and the air temperature as well as the surface temperature of the pipes were tested. The conclusion obtained from the tests is that the heat storage of the radiant floor with phase change material can reach 243%, and the curing time is more than 24 h, which ensures the continuity of the heating time.
The application of phase change materials in civil construction has controlled energy consumption to a great extent. How phase change materials are incorporated into concrete is a very good research direction, and direct incorporation methods, porous matrix augmentation method, microencapsulation method, etc., have appeared. At the same time, the application of environmentally friendly materials began to receive attention [16–18]. Many researchers choose environmentally friendly materials from nature as carriers, such as coral aggregates and volcanic rocks. Volcanic rocks produced by a large number of extinct volcanoes in the Pacific Rim and a large amount of coral aggregate obtained from seaside cities are reused as recyclable waste in nature, and resources are used rationally while playing a green and low-carbon utility.
The environmentally friendly phase change concrete in this paper is mainly used for walls and floor slabs. Phase change concrete refers to the addition of phase change materials to ordinary concrete. Among the raw materials, the cement is P-O 42.5 ordinary silicate cement produced by Qingdao Shanshui Company, China., and polycarboxylic acid high-efficiency water reducing agent is used. The fine aggregate is ordinary river sand, whose properties are shown in Table 1. The particle size of coarse aggregate is chosen between 5–20 mm, where the bulk density of crushed stone is 1340 kg/m3, and the crushing index is 7.12%. The shale ceramic granules are from the lightweight shale ceramic granules produced in Zhengzhou, Henan Province (China), which is a porous and lightweight material made from natural rocks. The volcanic rock is selected from the Changbai Mountain area in Yanbian Province, Jilin Province (China), and the coral aggregate is from the coral reefs in the Yellow Sea waters, the properties of which are shown in Table 2.
The composition is a solid alkane, which is a white or light yellow translucent solid. It has a melting point of about (28 ± 2°C), latent heat of phase change of 206.2 J/g, a specific heat capacity of 3.52 J/g*K, and thermal conductivity of 0.21 W/m*K. The advantages of solid alkanes are low cost, non-toxicity, non-corrosiveness, good thermal cycling properties, and small phase change volume [19,20].
Phase change concrete is prepared by mixing porous matrix and phase change materials by high-temperature adsorption to make the phase change coarse aggregates. It is mixed into the concrete [21], and the lightweight porous matrix such as shale vitriol, volcanic rock and coral aggregate needs to be cleaned and rinsed with a high-pressure water gun to clean the impurities within the pores. After cleaning, the light porous matrix was sent to an electric blast drying chamber which should be set at 60°C. After drying, the porous substrate is removed and cooled to room temperature. Different adsorption environmental conditions have different degrees of influence on the adsorption rate of absorbent porous substrates, including natural adsorption, high-temperature adsorption and negative pressure adsorption. In this experiment, paraffin wax adsorption under high temperature heating conditions was used, and the paraffin wax impregnated on the porous substrate was heated with a water bath.
The magnitude of the adsorption rate of a porous matrix depends on both internal and external factors. Internal factors are related to the pore size and pore density of the matrix itself, while external factors are related to the temperature and time of the adsorption process. The too high porosity of the material itself leads to the low strength of the material, while too low porosity leads to low adsorption rate. The experimental temperature was 80°C (Fig. 1a) and the adsorption time was 2 h. Different porous polymers have different adsorption rates, as shown in Fig. 1b.
Figure 1: Adsorption test
The temperature control performance of environmentally friendly phase change concrete mainly depends on the properties of the concrete material itself and the admixture of phase change materials. The pore distribution and size of the three porous matrices were studied separately. The adsorption capacity of the surface microstructure was analyzed according to the properties of the materials themselves, and the surface microstructure of the aggregates was obtained using microscopic techniques (Fig. 2). Shale ceramic granules are made by high-temperature firing, and their pores are irregular, so they are not uniformly distributed. The size of the pores is determined by the firing time and other reasons, and the pores have a certain adsorption capacity. The pores of volcanic rocks are mostly round pores, continuously distributed on the surface, with large pore depth and no communication between pores. The porous matrix can adsorb paraffin through the adsorption force generated by capillary force. The coral aggregate has uniform pore distribution, large space and interpenetration within the pores, which is conducive to the storage of phase change materials, but the capillary force is small, and the coral aggregate is more prone to liquid leakage than shale vitrified and volcanic rocks. The comparative analysis of microscopic characterization shows that coral aggregate has the highest adsorption rate and the largest storage capacity for phase change paraffin, and the higher porosity leads to lower strength. Shale ceramic granules and volcanic rocks have lower adsorption rates than coral aggregates but higher material strengths than coral aggregates.
Figure 2: Microscopic pores
For the study and analysis of the three porous matrices, the adsorption rate of the three porous light aggregates was mostly at about 15%. Observing the cross-section of the phase change aggregates, as in Fig. 3, it was found that the distribution of phase change paraffin in the porous light aggregates was relatively uniform, which could ensure the uniform occurrence of the phase change process in the pores to a certain extent.
Figure 3: Comparison of paraffin adsorption
The phase change coarse aggregate is obtained by adsorption of paraffin wax from a porous matrix. The phase change paraffin wax in the pores is prone to leakage during the phase change process and reduces the heat storage capacity of the material, so the surface of the phase change coarse aggregate was encapsulated. The epoxy resin and the curing agent are mixed thoroughly to obtain an epoxy resin gel, which is uniformly wrapped around the surface of the phase change coarse aggregate material.
Different types of concrete were made into 100 mm × 100 mm × 100 mm cubic compressive specimens (Fig. 4). The insulated box model YH-60B was cured for 28 d under standard curing conditions in a constant temperature and humidity curing box. We chose TYE-3000 pressure testing machine to test the compressive strength of different types of specimens at 3 d, 7 d, 14 d and 28 d.
Figure 4: Cube compressive strength test
Through the preparation of concrete, the specific process operation is shown in Fig. 5. The crushed stone in ordinary concrete is replaced by porous shale vitriol, volcanic rock, and coral aggregate by equal volume [22–24], with 50% and 30% replacement ratio, respectively, as shown in Table 3.
Figure 5: Preparation process of phase change material concrete
3 Research on Mechanical Properties of Concrete with Environmentally Friendly Phase Change Materials
Cube compressive strength test is carried out according to the regulations [25]. Through the test, it is found that the change of the strength of the concrete with the addition of light aggregate is consistent with the change of the strength of the ordinary concrete for 28 d. For phase change lightweight aggregate concrete, the strength changes in the early stage are large, and the change in the later stage is slow, and the early strength is high. The main reason is that although the encapsulation of epoxy resin improves the strength of the aggregate, it makes the surface of the aggregate smooth, and the ability to work with the cement slurry is reduced.
The effect of phase change lightweight aggregate on the strength of concrete was studied, and the concrete mixed with phase change aggregate was compared with the concrete mixed with ordinary aggregate, and it was found that the strength of phase change lightweight aggregate concrete decreased by 25.4%∼36.8% (Fig. 6).
Figure 6: Comparison of compressive strength
The test methods of bond-slip capacity mainly consist of the pull-out test, beam anchor test, and strain gauge test of internal paste of reinforcement, and the pull-out test is chosen for the bond capacity test in this paper.
The standard cube specimen (150 mm × 150 mm × 150 mm) was used for this test. HRB400 reinforcement was set in the center of the specimen, and no hoop was set. The anchorage length of the reinforcement was 150 mm (Fig. 7). The type of reinforcement chosen therein is threaded reinforcement, and the bonding force includes adhesion, mechanical bite force and friction force. The test instrument was a WDW3300 microcomputer-controlled electronic universal testing machine (Fig. 8), which was used for the tensile test. The test blocks were fixed at the two ends of the anchor bar, and the distance between the rebar fixture and the test blocks were controlled and recorded. The loading speed was set to 1 mm/min so that a relatively smooth bond-slip curve could be obtained [26].
Figure 7: Pull-out test cube specimen
Figure 8: Pull-out test
The load was started to be applied without any significant displacement of the reinforcement. Continuing the loading, the sound of brittle cracking of concrete started. As the loading process continued, the concrete suddenly cracked and showed brittle damage with a clear sound when damaged. The damage mode of the phase change concrete was found to be splitting damage, as shown in Fig. 9a, and the bond sliding ultimate strength of PCM-CA4-50% concrete was reduced by about 9.06% compared to OR-CA2-50% concrete, as shown in Fig. 9b. The bond strength of phase-change coral concrete is lower than that of normal light-aggregate concrete. A large amount of phase change coral aggregate appeared at the edge of the damaged section of PCM-CA4-50%, and the smooth surface of phase change coarse aggregate reduced the friction force with cement paste during the damage process, which reduced the bond slip resistance, as shown in Fig. 9c.
Figure 9: Bond-slip test
Through the test of concrete strength under different variables, it can be found that the strength of phase change concrete has a certain law to follow. This is because in the preparation process of phase change aggregate, in order to prevent the leakage of phase change paraffin, epoxy resin is wrapped on the aggregate surface. When the epoxy resin is cured, the surface of the phase change aggregate will become very smooth, and the bond between the phase change aggregate and the mortar in the concrete will decrease, resulting in a decrease in strength.
The mechanical properties of phase change concrete cubic compressive test blocks were tested. Axial pressure was applied to the specimen blocks all the time, and cracks appeared without peeling off the concrete surface. The test blocks were continued to be loaded, and the damage pattern was found to be different from that of the normal coarse aggregate concrete specimens. The final damage of the concrete specimen blocks was due to the relative sliding between the resin wrapped around the surface of the phase change coarse aggregate and the concrete. Some of the phase change coarse aggregates were crushed, and most of the phase change light aggregates were intact, sliding with the cement paste and creating internal cracks. Thus, the strength of the phase change concrete was significantly reduced.
Coral aggregates are white and relatively more visible, see Fig. 10a. The phase change coral aggregate and ordinary coral aggregate were added to the concrete respectively, and the cubic compressive strength test data were analyzed, and it was found that the phase change coarse aggregate concrete strength decreased due to the smooth surface of the phase change aggregate. The phase-change aggregate is not easy to form a whole with the mortar, which reduces the bonding effect between them. By observing the test phenomenon, it can be seen that the damage cracks of the phase change concrete are irregular, and most of the internal cracks of the concrete block are along the surface of the phase change coarse aggregate. The coral aggregate is not stressed, and the aggregate is relatively complete, as shown in Fig. 10b. For ordinary coral aggregates, the failure phenomenon shows that during the concrete mixing process, due to the large pores of the coral aggregates and the rough surface of the aggregates, the coral aggregates are fractured or crushed when they are finally destroyed (Fig. 10c).
Figure 10: Destruction pattern
4 Study on Thermal Properties of Phase Change Concrete
We chose phase change concrete and ordinary concrete to build four downsized concrete test chambers [27,28]. The dimensions of the test room are 300 mm × 300 mm × 300 mm (L × B × H), the wall thickness is 30 mm, and the gap is filled by a sealant.
We ideally assume that the two concrete materials are homogeneous and the model uses a single physics setup. The solid heat transfer is selected for the phase change concrete physical field, and the transient solver type is selected. The concrete material is selected from the database, and convection phenomena are not considered. The solid heat transfer is selected for the physical field of normal concrete, the steady state is selected for the solver type, and the heat source is set to solar heat. The short side of the slab is set as insulation, and heat transfer is controlled as Z-directional conduction.
The isotherms and temperature fields were obtained in the test room under the action of the heat source (Fig. 11). The location of the test points in the laboratory is determined according to the requirement to select the median temperature as far as possible. The location of the monitoring points was determined from the isotherms, and the center of each wall was selected.
Figure 11: Room simulated temperature field
The test room uses an NTC (10 K/3435) temperature sensor placed in the center of each wall and roof covering outside the test room and inside the test room, numbering each of the five walls (A–E) as shown in Fig. 12. The heating device adopts carbon fiber heaters, using the heating device inside the room to control the temperature of the laboratory room from room temperature to 50°C, to create a temperature difference between inside and outside the test room.
Figure 12: Model test room
The thermal performance of phase change concrete was examined by the rate of temperature change inside the room, and the temperature control of the wall under temperature change was studied experimentally for each of the four types of concrete materials (OR-1, PCM-SC4-50%, PCM-CA4-50% and PCM-VR4-50%).
In comparison to Fig. 13, a test house was made with shale vitrified phase change concrete, coral aggregate phase change concrete, and volcanic stone phase change concrete to compare the temperature changes under the same temperature change conditions [29,30]. We conduct temperature tests through test walls in five directions: A, B, C, D, and E. Ensure that the mechanical properties meet the requirements of use. Since the size of the test room is smaller than the actual room, it can still be seen from the test results that there are differences in the temperature control capabilities of different types of concrete. Analysis of the test results: The differences between the test rooms are manifested in the peak temperature and the peak temperature delay phenomenon. The highest average temperature in the five directions of the test direction is the PCM-VR4-50% concrete test room. The difference in peak temperature between the PCM-VR4-50% test room and the PCM-SC4-50% test room is not obvious. Compared with the PCM -CA4-50% test room temperature difference is obvious. The peak temperature difference at the temperature measurement points B, D, and E can reach 2.6°C, while the temperature change slopes near the melting point are very different. The temperature began to drop, and the latent heat capacity of the internal phase change material of PCM-CA4-50% showed obvious, which made the temperature change in the temperature region before and after the adjacent melting point relatively obvious, and the temperature change rate slowed down. The phase change material has the most obvious effect, but the latent heat of the phase change material in PCM-VR4-50% concrete and PCM-SC4-50% concrete also plays a role.
Figure 13: Temperature change curve
We compare the indoor temperature changes of ordinary concrete and phase-change coral concrete. By raising the ambient temperature in the room through the internal heat source, the ordinary concrete test room shows a more obvious difference than the phase change concrete test room. The temperature change at the testing point in the phase change concrete test room is lower than the peak temperature in the ordinary concrete test room, and the rate of temperature increase, as well as the rate of temperature decrease, is smaller. The temperature variation of the test room of phase change coral aggregate concrete was compared with the test room of ordinary concrete, and the advantages of phase change coral aggregate concrete in terms of delaying the temperature peak and reducing the temperature peak were relatively obvious.
1. The compressive strength of the cube is tested and studied, and it is obtained that the strength of the cube after replacing 50% stone is 25.4%–36.8% lower than that of ordinary concrete, which meets the requirements of concrete construction strength.
2. The bond-slip test of typical coral aggregate concrete shows that the bond strength of phase change coral concrete is 9.06% lower than that of ordinary coral concrete. As a typical damage analysis of phase change coral aggregate concrete, the surface of the aggregate is coated with epoxy resin, and the surface of the aggregate is smooth. The damage presented in the damage section is that the phase change coral aggregate and concrete slip, and the crack between the phase change coral aggregate and concrete develops continuously, leading to the damage to concrete.
3. The peak temperature and peak occurrence time of OR-1, PCM-SC4-50%, PCM-VR4-50%, and PCM-CA4-50% were different under the influence of variable temperature heat sources. The peak temperature reduction time was 1.4∼2.6°C, and the peak temperature delay time was 5∼15 min. The results show that the phase change concrete with environment-friendly material as aggregate has better temperature control performance than ordinary phase change concrete.
4. The mechanical and thermal properties of the three types of phase change light aggregate concrete were tested and it was determined that phase change coral concrete was the most effective type of concrete.
Funding Statement: Thanks to the Shandong Science and Technology Development Project (2013YD02043) and Shandong University of Science and Technology Science and Technology Innovation Program for their support.
Availability of Data and Materials: The datasets used or analyzed during the current study are available from the corresponding author upon reasonable request.
Conflicts of Interest: The authors declare that they have no conflicts of interest to report regarding the present study.
References
1. Hassan, N., Mariah, B., Francisco, J., Marllory, L., Xu, X. H. et al. (2019). Recent developments in phase change materials for energy storage applications: A review. International Journal of Heat and Mass Transfer, 129, 491–523. DOI 10.1016/j.ijheatmasstransfer.2018.09.126. [Google Scholar] [CrossRef]
2. Wei, G. S., Wang, G., Xu, C., Ju, X., Xing, L. J. et al. (2018). Selection principles and thermophysical properties of high temperature phase change materials for thermal energy storage: A review. Renewable and Sustainable Energy Reviews, 81(2), 1771–1786. DOI 10.1016/j.rser.2017.05.271. [Google Scholar] [CrossRef]
3. Punniakodi, B. M. S., Senthil, R. (2022). Recent developments in nano-enhanced phase change materials for solar thermal storage. Solar Energy Materials and Solar Cells, 238, 111629. DOI 10.1016/j.solmat.2022.111629. [Google Scholar] [CrossRef]
4. Abhat, A. (1983). Low temperature latent heat thermal energy storage: Heat storage materials. Solar Energy, 30(4), 313–332. DOI 10.1016/0038-092X(83)90186-X. [Google Scholar] [CrossRef]
5. Min, H. W., Sumin, K., Hee, S. K. (2017). Investigation on thermal and mechanical characteristics of concrete mixed with shape stabilized phase change material for mix design. Construction and Building Materials, 149, 749–762. DOI 10.1016/j.conbuildmat.2017.05.176. [Google Scholar] [CrossRef]
6. Fang, G. H., Yu, M. H., Zhang, W. T., Meng, C., Tan, X. (2021). Research progress on thermal properties of paraffin/carbon-based composite phase change materials. New Chemical Materials, 49(11), 41–45+50. [Google Scholar]
7. Cabeza, L. F., Castellon, C., Nogues, M. (2006). Use of microencapsulated PCM in concrete walls for energy savings. Energy Build, 39(2), 113–119. DOI 10.1016/j.enbuild.2006.03.030. [Google Scholar] [CrossRef]
8. Xu, R. C. (2008). Pilot production of phase change energy storage concrete (Master Thesis). Chongqing University, China. [Google Scholar]
9. Wang, Q., Zhang, C. B., Ding, Z. Y., Liu, J. (2013). Study on the thermal properties of paraffin/ceramsite phase change concrete. Advanced Materials Research, 838–841, 91–95. [Google Scholar]
10. Zhang, W. W., Cheng, J. J., Zhang, Y., He, J. P. (2016). Study on the effect of composite phase change concrete blocks in Nanjing area for winter application. Concrete and Cement Products, 4, 66–71. [Google Scholar]
11. Vinh, D. C., Shima, P., Carlos, S. B., Anna, M. S., Tri, Q. B. et al. (2019). Thermal analysis of geopolymer concrete walls containing microencapsulated phase change materials for building applications. Solar Energy, 178, 295–307. DOI 10.1016/j.solener.2018.12.039. [Google Scholar] [CrossRef]
12. Shen, Y. L., Liu, S. L., Hu, H., Cai, J. Y., Zhang, Y. J. et al. (2020). Preparation and thermal properties of ceramic/paraffin-set phase change material concrete. China Building Metal Structure, 2, 54–57. [Google Scholar]
13. Qu, Y., Chen, J. Y., Liu, L. F., Xu, T., Wu, H. J. et al. (2020). Study on properties of phase change foam concrete block mixed with paraffin/fumed silica composite phase change material. Renewable Energy, 150, 1127–1135. DOI 10.1016/j.renene.2019.10.073. [Google Scholar] [CrossRef]
14. Tu, H., Zhang, H., Liu, L. H., Li, J., Sun, S. Q. (2021). Study on the heat transfer performance of phase change concrete walls. Energy Storage Science and Technology, 10(1), 287–294. [Google Scholar]
15. González, B., Prieto, M. M. (2021). Radiant heating floors with PCM bands for thermal energy storage: A numerical analysis. International Journal of Thermal Sciences, 162, 106803. DOI 10.1016/j.ijthermalsci.2020.106803. [Google Scholar] [CrossRef]
16. Zhang, X. G., Lin, X. Y., Wang, P., Yang, J. H., Wu, F. (2016). Analysis of the effect of recycled light aggregates replacing natural aggregates on the compressive strength of concrete. Concrete, 12, 64–67. [Google Scholar]
17. Katzer, J., Janusz, K., Tomasz, P. (2020). Influence of crimped steel fibre on properties of concrete based on an aggregate mix of waste and natural aggregates. Materials, 13(8), 1906–1906. [Google Scholar]
18. Saeid, G. B., Sohrab, S., Sahar, G., Vivian, W. T., Jorge, B. et al. (2019). Effect of crushed concrete waste’s maximum size as partial replacement of natural coarse aggregate on the mechanical and durability properties of concrete. Resources. Conservation & Recycling, 149, 664–673. DOI 10.1016/j.resconrec.2019.06.030. [Google Scholar] [CrossRef]
19. Phattharachai, P., Piti, S., Tanakorn, P. N., Thanongsak, I., Pitthaya, J. et al. (2019). Use of burnt clay aggregate as phase change material carrier to improve thermal properties of concrete panel. Case Studies in Construction Materials, 11, e00-242. [Google Scholar]
20. Ramakrishnan, S., Sanjayan, J., Wang, X. M., Alam, M., Wilson, J. (2015). A novel paraffin/expanded perlite composite phase change material for prevention of PCM leakage in cementitious composites. Applied Energy, 157, 85–94. [Google Scholar]
21. Kumar, C. S., Goyal, R. (2022). Study the effect of tiles aggregate waste as partial replace with natural aggregate in cement concrete. Materials Today: Proceedings, 51, 905–908. [Google Scholar]
22. GB/T 50080-2002. (2015). Standard for mechanical properties test methods of ordinary concrete. Beijing, China: China Construction Industry Press. [Google Scholar]
23. Luo, Y. (2021). Preparation and basic mechanical properties of fiber-reinforced self-compacting light-aggregate concrete (Ph.D. Thesis). Inner Mongolia University of Science and Technology, China. [Google Scholar]
24. Niu, J. G., Bian, Y., Liu, W. H., Li, J. J. (2020). Design method and experimental study of high-strength light-aggregate concrete ratio. Silicate Bulletin, 39(11), 3480–3487. [Google Scholar]
25. GB/T 50152-2012. (2015). Standard for test methods for concrete structures. Beijing, China: China Construction Industry Press. [Google Scholar]
26. Chen, Y. S., Zeng, S. H., Dong, F. Z., Li, X. Z. (2006). Experimental study on bond stress distribution of deformed steel bars in light aggregate concrete. Building Structures, 11, 100–102. [Google Scholar]
27. Wu, T. J. (2016). Study on the preparation and performance of paraffin phase change energy storage concrete. New Building Materials, 43(12), 91–93. [Google Scholar]
28. Li, M., Wu, Z. S., Chen, M. R. (2011). Preparation and properties of gypsum-based heat storage and preservation material. Energy and Buildings, 43(9), 2314–2319. DOI 10.1016/j.enbuild.2011.05.016. [Google Scholar] [CrossRef]
29. Li, M., Wu, Z. S., Kao, H. T. (2011). Experimental investigation of preparation and thermal performances of paraffin/bentonite composite phase change material. Energy Conversion and Management, 52(11), 3275–3281. DOI 10.1016/j.enconman.2011.05.015. [Google Scholar] [CrossRef]
30. Li, H. J., Ji, Z. J., Li, S. Q., Wang, J., Wang, J. C. et al. (2012). Test method for phase change temperature regulation performance of building materials. China: China Building Materials Research Institute. [Google Scholar]
Cite This Article
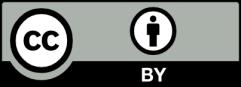
This work is licensed under a Creative Commons Attribution 4.0 International License , which permits unrestricted use, distribution, and reproduction in any medium, provided the original work is properly cited.