Open Access
REVIEW
Recycling Carbon Resources from Waste PET to Reduce Carbon Dioxide Emission: Carbonization Technology Review and Perspective
1 Faculty of Printing, Packaging Engineering and Digital Media Technology, Xi’an University of Technology, Xi’an, 710048, China
2 School of Materials Science and Engineering, Jingdezhen Ceramic Institute, Jingdezhen, 333403, China
3 Environmental Resources and Material Industry Technology Research Institute of Zhongzhao Construction Groups, Guangzhou, 510623, China
4 Research Institute, Transfar Chemicals Group, Hangzhou, 311215, China
5 Key Laboratory of Auxiliary Chemistry and Technology for Chemical Industry, Ministry of Education, Shaanxi University of Science and Technology, Xi’an, 710021, China
6 Shaanxi Collaborative Innovation Center of Industrial Auxiliary Chemistry and Technology, Shaanxi University of Science and Technology, Xi’an, 710021, China
* Corresponding Author: Xing Zhou. Email:
Journal of Renewable Materials 2023, 11(5), 2085-2108. https://doi.org/10.32604/jrm.2023.025032
Received 18 June 2022; Accepted 13 September 2022; Issue published 13 February 2023
Abstract
Greenhouse gas emissions from waste plastics have caused global warming all over the world, which has been a central threat to the ecological environment for humans, flora and fauna. Among waste plastics, waste polyethylene terephthalate (PET) is attractive due to its excellent stability and degradation-resistant. Therefore, merging China’s carbon peak and carbon neutrality goals would be beneficial. In this review, we summarize the current state-of-the-art of carbon emission decrease from a multi-scale perspective technologically. We suggest that the carbon peak for waste PET can be achieved by employing the closed-loop supply chain, including recycling, biomass utilization, carbon capture and utilization. Waste PET can be a valuable and renewable resource in the whole life cycle. Undoubtedly, all kinds of PET plastics can be ultimately converted into CO2, which can also be feedstock for various kinds of chemical products, including ethyl alcohol, formic acid, soda ash, PU, starch and so on. As a result, the closed-loop supply chain can help the PET plastics industry drastically reduce its carbon footprint.Graphic Abstract
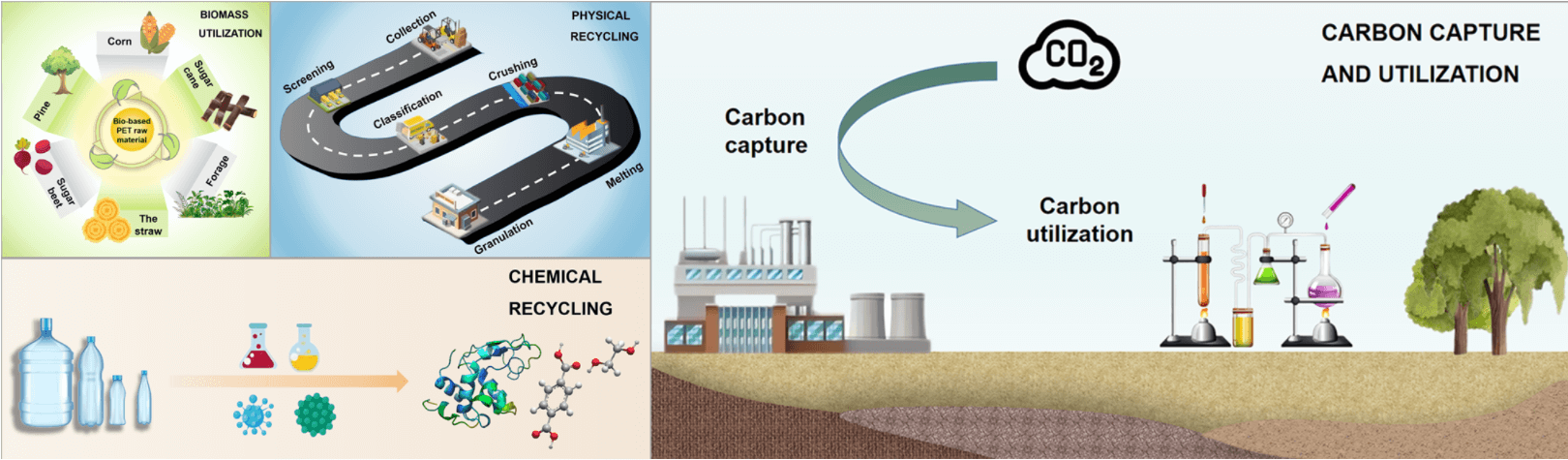
Keywords
Abbreviations Table
PET | polyethylene terephthalate |
MEG | monoethylene glycol |
GHG | greenhouse gas |
PLA | polylactic acid |
CLSC | closed-loop supply chain |
PBS | poly (butylene succinate) |
SCC | social cost of carbon |
PBAT | polyadipate/butylene terephthalate |
CF | Carbon footprint |
PHA | polyhydroxyalkanoate |
LCA | life cycle assessment |
MOF | metal organic frameworks |
VOCs | volatile organic chemicals |
PC | (poly) carbonates |
PP | polypropylene |
PU | polyurethane |
BHET | Bis (2-hydroxyethyl) terephthalate |
MHET | Monohydroxyethyl terephthalate |
FA | formic acid |
PS | polystyrene |
PM | particulate matter |
LDPE | low density polyethylene |
R-PET | recycled polyethylene terephthalate |
TPA | 1,5-trans polypentene rubbe |
EG | ethylene glycol |
TBAI | tetrabutylammonium iodide |
TBA+ | tetrabutylammonium cation |
DEG | 2-(2-hydroxyethoxy)ethanol |
TEG | 2,2-(ethylenedioxy)diethanol |
PG | 1,2-propanediol |
DMT | dimethyl terephthalate |
Owing to the announcement of reaching peak emissions by 2030 and carbon neutrality by 2060, China has planned a number of policies to achieve these goals in industries [1]. This has attracted a great deal of attention to achieving the goals academically from the technology level due to the central threat of global warming from greenhouse gas (GHG) emissions, such as carbon dioxide (CO2). To evaluate the influence of carbon emissions, the social cost of carbon (SCC) is proposed by characterizing how the additional CO2 emissions affect future economic outcomes by changing the climate. It is predicted that electricity consumption will increase substantially in emerging tropical economies due to global warming. When the global average surface temperature increases by 1°C, the global annual electricity consumption will increase by about 4.5 exa-joules (7% of current global consumption), while every direct consumption of other fuels will decrease by about 11.3 exa-joules (7% of current global consumption) [2]. For most countries, carbon peak (carbon emission reaches the peak, referring to the process that the annual carbon dioxide emission of a region or industry reaches the highest value in history) and carbon neutrality (the 2.0°C goal corresponds to the positive balance of CO2 emissions) are phased goals [3], which can be achieved as scheduled by employing technologies of fossil fuel mining and transportation, plastic refining and manufacturing, management of plastic waste, and deep decarbonization of energy industry, etc. In China, we will strive to stably keep the proportion of manufacturing and carbon emission intensity of traditional industries such as steel, non-ferrous, petrochemical, chemical, paper and cement. The main expectation is to reduce energy consumption, which is an inevitable requirement for achieving the goal of carbon peak and carbon neutrality. Especially in plastics and waste plastics management, urban plastic wastes have caused serious damage to the environment in China. It is necessary to reduce the production and use of plastic at the source, namely petroleum resources. Strategies to mitigate the employment of plastics include alternative plastic products, recycling and utilization of plastic wastes, and exchange of fossil carbon feedstock [4].
The following measures have been carried out to decrease fossil-based plastics, as well as GHG emissions. First, it involves aggressively supporting the reduction in plastic production, which includes encouraging eco-friendly plastic product design and minimizing the usage of disposable plastic goods. Second, there is a significant need to expedite the standardized recycling and disposal of plastic waste. This includes developing a system for the collection, transportation, and disposal of waste in rural areas, improving the effectiveness of recycling, and raising the bar for the safe disposal of plastic waste. Thirdly, there is a strong effort being made to remove plastic waste from important locations, including rivers, lakes, seas, tourist attractions, and rural regions. The categories of technology and procedures are primarily the key questions in the field for achieving these aims with carbon peaks [5–10].
Polyethylene terephthalate (PET), the main type of thermoplastic polyester from fossils, is one of the most multifunctional plastics with wide application in spinning, printing, food, package industry and electronic fields [11]. The consumption of PET accounts for 8.4% of global plastics consumption of 367 million tons in 2020, which are mainly bottles for water, soft drinks, juices, cleaners, etc. [12]. Most of the PET products are wasted in landfills, incinerators, and into rivers and oceans. Thus, one of the emergency measures should be laid to carbon peak emission of waste PET. PET is a potential resin that is suitable for the CLSC model and clean production [13]. The closed-loop supply chain (CLSC) model is supposed to be a promising pathway to achieving the goal of carbon peak emission. The achievement of CLSC model mainly depends on circular technologies, including (1) recycling of waste PET in physical and chemical processes, (2) biomass utilization for alternative products, and (3) carbon capture and utilization to end the life cycle of waste PET [4,14–16].
In this review, the pathway to reach carbon peak emissions and carbon neutral for PET plastics is illustrated in the form of CO2. It is suggested that the combination of recycling, biomass utilization, and carbon capture and utilization for PET plastics can be the desirable strategy to achieve the goals. To the best of our knowledge, there is little literature to summarize the carbon peak emissions and carbon neutral for PET plastics from the aspect of materials science. We assume that there are mainly two novel contributions of this review: (1) The focus on carbon peaking emissions is specifically shifted from the national level to the technological level, which supplies the controlled methods to reach carbon peak emissions and carbon neutral for PET plastics. (2) Alternative materials are firstly summarized to replace PET in different areas, as well as the closed-loop recycling of waste PET.
2 The Carbon Resources in Waste PET
Daily consumed plastics, which account for more than 90% of all plastic items in industries including building, medicine, packaging, automobiles, etc., mainly originated from petroleum derivatives [17]. It suggests that the main components of plastics are polymer chains consisting of carbon and hydrogen elements. These are the main components of most applied materials, especially organic materials. It indicates that the carbon resources can be reused to produce virgin materials, such as polymers, composites and even fuel gases. Unfortunately, the vast scale of waste plastics is landfilled and burned down in both developed and developing countries, resulting in the huge wasting of resources [18]. It is indicated that the PET recycling ratio has increased 37.9% to 55.5% due to the PET banning from landfill in Italy [19]. The main disposal methods of waste PET include landfill, mechanical recovery, chemical recovery, heat treatment, and biodegradation [19–22]. The various treatment methods are shown in Table 1. As one of the major components in municipal solid wastes, PET can be also a promising feedstock source for engineering materials [23]. The fixed carbon accounts for 7.77%–13.17%, and the carbon-based gases take up 86.83%–91.75% when waste PET is pyrolyzed under a temperature around 500°C [24]. The key point is how to complete the transformation of the carbon resources in the used PET plastics into valuable components. Apart from physical recycling processes, the CO2 emission from waste PET is mainly captured and stored by vegetation, as depicted in Fig. 1. Furthermore, some processes have been developed to introduce PET wastes (including transparent and colored PET) and their degradation products as raw materials for the preparation of highly valuable products [25,26].
Figure 1: The vegetation and carbonization paths for waste PET recycling
Notably, the abundant carbon resources from PET can be a great promising feedstock for carbon nanomaterials, as illustrated in Fig. 1 [27–30]. The production of activated carbon from waste PET is one of the most promising ways to accomplish recycling PET in high value [31]. The activated carbon materials can be obtained under the function of alkali agents with carbonation and activation processes. The produced carbon materials can be an adsorbent candidate for water decontamination with cheap cost, large scale, and chemical stability (such as eliminating radioactive metals, methylene blue dyes, etc.) [32–34]. Moreover, functional carbon materials with unique micro- or nano-structures can also be obtained by using different precursors from waste PET, including hierarchical porous carbon for symmetric supercapacitors [35], carbon nanofibers for multifunctional surfaces [31], carbon nanotubes [36], magnetic carbon nanomaterials [37], graphene [38], etc., as shown in Fig. 1. The recycling of waste PET for the preparation of active carbon materials has been proven to be a significant way to convert waste PET into high-value-added products [39]. For example, El Essawy et al. [40] prepared graphene from waste PET bottles through the thermal dissociation process, which presents relatively high surface area and micropore volumes. The results suggest that the graphene shows the significant adsorption of methylene blue and acid blue 25, indicating great potential application in water purification areas. Furthermore, the graphene can be used to prepare 3D sponge nitrogen-doped graphene by mixing urea through a one-step method. The prepared composite presents outstanding performance, such as the specific capacitance of 405 F/g at 1 A/g, the energy density of 68.1 W⋅h/kg, the high maximum power density of 558.5 W/kg, as well as the appropriate cyclic stability with capacitance retention of 87.7% after 5000 cycles at 4 A/g with high charge/discharge duration. It holds promise in energy storage applications due to the cost-effective and environmentally friendly method of reducing waste PET [41]. Due to the abundance of carbon resources and the simplicity of the methods, it is possible to achieve carbon peak emission by repurposing waste PET as micro-or nanomaterials.
3 Analysis of the Carbon Recycling/Carbon Footprint of PET
Carbon footprint (CF), which is a significant single-issue impact assessment method belonging to life cycle assessment (LCA), is commonly employed to evaluate the pressure caused by human activities (including manufacture processes and consumer products) on the natural environment. It reflects the quantification impact of an activity on the environment. CF can be evaluated by equivalent carbon dioxide (kg CO2eq) emissions directly [42]. For the CF of PET bottles, it can be calculated by the sum of the CF in materials fabrication (CFmaterials), energy consumption (CFenergy), and transportation (CFtransportation), as depicted in Eq. (1).
CF materials are the CF of the packaging materials, such as PET resin, glue, labels, and printing materials. CF energy is the CF from energy consumption during the manufacturing process of the materials and packaging. CF transportation is the CF of the transportation for packaging products.
The average CF of PET bottle is 3.37 × 10−1 kg CO2eq per functional unit (1.5 L). According to Eq. (1), three main resources contribute to the carbon footprint content. The CF materials account for 1.98 × 10−1 kg CO2eq (59% CF) due to packaging processes, 46% of which are produced from PET bottles. CF transportation is 8.81 × 10−2 kg CO2eq (26% of the CF) and CF energy is 5.1 × 10−2 kg CO2eq (15% of the CF). When the usage of PET is limited, it is suggested the GHG emissions reduction by 163.5 kg CO2eq (per year, 2 L) [43].
To clearly show the decreased CO2 emissions of the waste plastics, a study was conducted to compare the production of resins by using waste and virgin plastics. As one of the largest plastic producers in Asia, Malaysia is selected as the studied region. The consumed raw materials, chemicals, water, and energy were evaluated as CO2. It suggests that 0.84 kg CO2/kg resins are produced for all kinds of plastics products. The value is significantly lower than 2 kg CO2/kg resins of virgin plastic resins production. Notably, the CO2 emissions are mainly from electricity consumption, solid waste generation and diesel consumption, which account for 73.8%, 23.3% and 2.3%, respectively [44].
4 The Methods to Reduce Carbon Dioxide Emission of Waste PET
It is assumed that circular technologies, including physical and chemical recycling, biomass utilization, and carbon capture and utilization, can be the most promising way to achieve the goal of accomplishing the peak carbon dioxide emissions for waste polymers, as depicted in Fig. 2 [2,4]. According to reducing the consumption of fresh carbon-based polymers, circular technologies can achieve net-zero emission plastics. In this way, the amount of carbon can be immobilized from the perspective of consumption.
Figure 2: Feedstock supply and waste treatment of the circular carbon pathway for wind-based electricity production with 7 g of CO2-equiv per kWh. The corresponding values represent the of carbon reduction (million tons of C) of the methods [4]
The physical recycling technology is known as mechanical recycling technology, which can be the most effective way with the highest reusing ratio of 100%. Waste polymers are primarily reused directly by blending with other materials to prepare composites, such as virgin polymers, concrete, pitch, etc. However, the performance of the obtained composites is commonly adequate, which is not suitable for the situation with high requirements. Chemical recycling can be the most effective way of producing feedstock with adjustable properties. The degradation of waste polymers produces various kinds of oligomers, diols, and other compounds in low molecular weight with reactivity. The main methods are hydrolysis, alcoholysis, glycolysis, aminolysis, ammonolysis, pyrolysis and so on. Biomass utilization and carbon capture and utilization are assumed to significantly incinerate waste plastics [4]. Although the carbon content in biomass is abundant, corresponding to petroleum-based plastics, the produced CO2 can be captured and reused directly in the form of hydrogen and carbon monoxide mixture. The main difference in the pathway for emission of CO2 between the biomass and fossil resins can be that the biomass can generate CO2 and energy immediately via a green process, while the fossil resins need over millennia [4,18]. Thus, biomass can offset the primary source of CO2 from the incineration and the production of waste plastics.
The saved waste gas emission of the manufacturing products from the recycling process and from virgin materials is listed in Table 2. It is obvious that the employment of recycling PET can significantly decrease the emission of the gases of CO2, CH4, NOx, volatile organic chemicals (VOCs), SOx, and fine particulate matter (PM). Thus, recycling waste PET is greatly essential for carbon emission peak.
Recycled polymers can be obtained from waste packaging plastics via physical recycling processes, including co-extrusion, hot-press, melting mixture, etc. For this strategy, waste packaging plastics are totally mixed with virgin resins to obtain composites with no emission of carbon waste (especially greenhouse gas (GHG)).
It is reported that more than 60% of waste plastics are treated in landfills all over the world because it is the most direct, simple, and effective means of treating solid waste [55]. However, the drawbacks are also obvious, such as space load and pollution of soil and water [56,57]. The plastics in the soil release a small number of harmful components into the groundwater after natural aging and degradation, causing water pollution. Furthermore, landfill leads to land desertification and seriously endanger the survival of soil organisms. Mechanical recovery involves the collection, screening, classification, crushing, melting and granulation of waste PET [58]. This method is nearly harmless to the environment and relatively inexpensive. Recycled PET is predominantly used to renew PET. Nevertheless, the inclusion of chemicals, contaminants, and other things will diminish the performance of recycled PET. To solve this problem, a number of studies have improved the properties of recycled PET by adding fillers, fibers, additives, coupling agents, stabilizers, and other types of polymers to meet the standards of industrial applications [59,60].
Furthermore, owing to the stability and highly sensitive to the alkaline environment of PET, the reuse of PET is good for the performance of concrete, such as flexural toughness, impact resistance and workability [61]. A series of researches have presented that the addition of recycling PET can improve the tensile strength of the building materials, as well as decrease GHG emissions. Maalouf et al. studied the CF of insulating layers in buildings façades by using three sustainable materials, including natural resources, hemp-concrete, and recycled polyethylene terephthalate (R-PET). CF assessment was performed by employing the façades located in France and Italy [42]. It suggested that the R-PET façade presented the most performing solution among the three materials in all the scenarios, which performed less electricity consumption, as well as less GHG emitting. Thus, the utilization of R-PET for preparing building materials is of great promise, with significant energy efficiency by decreasing environmental impact [62,63]. Schaefer et al. recycled waste PET to replace cement for preparing durable and sustainable concrete with significantly lower CF [61]. They indicated that the irradiated waste PET (highest addition amount of 100 kGy) contributed to the compressive strength compared with the nonirradiated waste PET.
Chemical recycling can reduce the emission of CO and CO2, resulting in the reduction of the carbon footprint of both thermoplastics and thermoset plastics [24]. It is reported that the CLSC model can evaluate CO2 emissions of producing PET under the chemical recycling pathway. During the chemical recycling process, the CO2 generation and energy consumptions are only 0.0391 tons and 1033.284 MJ, respectively. It suggested that 79% less energy and 73% less CO2 can be achieved during the production of PET [64].
For the PET plastics, the essence of chemical recovery of PET is the cleavage of ester bonds to obtain monomers, oligomers or polyols. These monomer units can be used to synthesize new PET, as well as other polymers. According to the many solvents employed, chemical recovery techniques can be categorized as hydrolysis, alcoholysis, aminolysis, glycolysis, amination, and so on [65–69]. Specific recovery methods and research progress are illustrated in detail in Section 4. In addition, heat treatment is a typical waste management technique, which can be classified as pyrolysis or incineration. Pyrolysis is a kind of thermochemical conversion under high temperature and non-oxygen atmosphere, which can be carried out directly or under the function of a catalyst [70]. Incineration is ultimately aimed at recovering energy. Whereas air pollution caused by incineration, such as soot particles, various harmful and toxic gases have a great impact on human health. Moreover, one of the promising methods is to use carbon-based fuel derived from waste plastics to reduce greenhouse gas emissions [71]. Biodegradation technology, eco-friendly and economically feasible, is gradually becoming a hot research point in the field of plastic waste management. The microorganism is the driving force of PET degradation. Researchers have found that many kinds of enzymes from bacteria and other organisms have shown the potential to degrade PET, among which PETase from ideonella sakaiensis has the most prominent hydrolysis effect on PET [72–74]. The current technical problem for biodegradation lies in the high accuracy requirements of microbial cultivation, maintenance, and enzyme extraction [75]. Moreover, the enzyme activity and stability are also the biggest obstacles to its technical popularization [76].
(1) Hydrolysis
Waste PET can be degraded into TPA and EG via the hydrolysis process. According to the different pH values in the water medium, it can be divided into neutral hydrolysis, acid hydrolysis, and alkaline hydrolysis [77]. Neutral hydrolysis often resorts to mechanical agitation and external forces. The temperature is controlled above the melting point of PET. Grause et al. [78] reported early research on the recovery of TPA and EG from waste PET through a fluidized bed reactor. Unfortunately, at 450°C, the highest yield of TPA is only 72%, and 22%–27% of TPA remains in the oligomer. In addition, the yield of EG is less than 10%. A large number of studies have expounded that acidic/alkaline reagents, catalysts and auxiliary technologies can enhance the hydrolysis kinetics of PET to achieve the effect of reducing the reaction temperature, shortening the reaction time, and increasing the yield of TPA and EG [79,80]. Paliwal et al. [81] proposed the use of a tetrabutylammonium iodide (TBAI) phase transfer catalyst with 190 W ultrasound supports to accelerate alkaline hydrolysis of PET. The phase transfer catalyst acts as a bridge here, connecting the inorganic and organic phases to facilitate molecular transportation. The specific PET alkali hydrolysis kinetics is shown in Fig. 3. The lipophilicity of tetrabutylammonium cation (TBA+) can attract OH− ions to the outer surface of PET. The OH− group acts as a nucleophilic to attack PET breaking into TPA and EG. Owing to hydrogen bonding, TPA and EG are subsequently transferred to the water phase. The experimental results are impressive. The reaction temperature is reduced to 90°C, and the reaction rate is increased by nearly 31% (compared to unassisted catalysis). The hydronium ion provided by the acid and alkali reaction conditions makes the ester group easier to hydrolyze. However, considering the economic and safety issues of strong acids and strong bases, using recyclable acid and base catalysts to hydrolyze PET in neutral pH media is an effective and practicable option.
Figure 3: The mechanism of the phase transfer catalyst in the alkaline hydrolysis of PET. Reproduced from [81]
(2) Alcoholysis
Waste PET can be converted to oligomers, diols, and phthalate derivatives through the alcoholysis process. For this pathway, monomers of PET are commonly obtained, which can be used as raw materials for polymer synthesis, especially PET. During the reaction process, dimethyl terephthalate (DMT) easily reacts with EG under catalysis, which reduces the monomer yield [82,83]. Therefore, the loss can be reduced by separating the product or controlling the amount of the catalyst. In recent years, supercritical fluids have manifested a strong attraction to PET depolymerization. Supercritical methanol (Tc = 512.3 K, Pc = 8.09 MPa) and ethanol (Tc = 836 K, Pc = 7.7 MPa) are frequently used in PET alcoholysis [84,85]. Yang et al. [86] explored the process conditions of supercritical methanol depolymerization of PET in the early stage. It was reported that the optimal parameters were 533∼543 K of temperature, 9.0∼11.0 MPa of pressure, 40∼60 min and the weight ratio of methanol to PET is in the range of 6∼8. The alcoholysis process can be carried out at the temperature of 180°C–250°C with free CO2 emission. However, it needs high pressure to obtain degradation products, and this process is only applicable to plastics without dyes [87].
(3) Glycolysis
Glycolysis uses diols (EG, DEG, TEG, PG, etc.) to depolymerize PET into oligomers and monomers (BHET, MHET, EG) under the action of the catalyst. It is the most widely used PET recycling technology with many controllable factors, and a high recycling rate can be obtained by optimizing the depolymerization process. Presently, there are numerous studies on PET glycolysis, with catalysts playing a crucial role. Without a catalyst, the glycolysis rate of PET is very low, and it is nearly impossible to completely depolymerize PET into a BHET monomer, according to kinetic studies [88]. Nabid’s group [67] opened up a new path for PET glycolysis by using γ-Fe2O3/nitrogen-doped graphene bifunctional catalyst. On the one hand, the functional groups of the catalyst can form hydrogen bonds with ethylene glycol to enhance the glycolysis activity of PET. On the other hand, it will act on the carbonyl oxygen of PET to make the chain more easily broken (shown in Fig. 4 for the catalytic mechanism). The yield of BHET obtained by this method under normal pressure is almost 100%. In addition, the reaction temperature is lower than that of Aguado’s, the dual-function catalyst has super paramagnetism and is recyclable. After 5 cycles, the catalyst activity hardly changes.
Figure 4: Reaction mechanism of PET glycolysis catalyzed by γ-Fe2O3/n doped graphene bifunctional catalyst. Reproduced from [67]
Even waste PET can be employed as a feedstock for the preparation of construction materials, such as concrete, glass fibers, etc. [89]. Our previous work implies that waste PET can be degraded into nanofiber-based white fillers. These fibers devote to the enhancement of the mechanical performance of polymer composites [26]. Beckham et al. transformed waste PET bottles into renewable unsaturated polyesters, which can be mixed with glass fibers to produce usable products with high performance. The LCA results suggest that the recycled PET specifications can save feedstock energy as high as 80% potentially. Therefore, the recycled can be the ideal replacement of the virgin PET, as well as the remainder of the polymer backbone in composites [90]. It is reported that various kinds of glycols can be used to degrade waste PET, such as ethylene glycol, diethylene glycol, propylene glycol, butylene glycol, dipropyleneglycol, etc. The glycolysis process contributes most to the degradation of waste PET with controlled degradation products. The only key problem is the slow reaction in the absence of a catalyst during this process [25,87].
(4) Biodegradation
PET and enzymes exhibit a typical substrate binding mechanism. The ester groups of PET molecular chains are guided to specific active areas on the surface of the enzyme, where they are attacked by nucleophiles and broken apart [73]. PET hydrolase has an open surface structure that can accommodate hydrophobic polymers with a high molecular weight [91]. In this structure, PET interacts with the active regions of the enzyme. Typically, enzymes attack the fluid amorphous portion of PET. This portion of the chain is flexible, and the intermolecular force is low, which facilitates its precise interaction with the ester bond [92].
Since the found of the PETase hydrolase (Ideonella sakaiensis 201-F6), attention to the enzyme degradation of waste PET has been attracted largely [93]. Using highly thermally stable IsPETase variants to improve the degradation activity of PET is an effective path [76]. The researchers found two main candidate structures based on the key structural characteristics affecting the low-temperature stability of the protein. One is the central β gene sheet in the protein structure. The destruction of this structure seriously affects the thermal stability of IsPETase. The other is the connecting loop part of β6-β7, which has poor stability and can be enhanced by introducing hydrogen bonds. Several constructed PETase variants have higher thermal stability and enzymatic activity than PETase, which is an important step toward large-scale recycling of PET.
Enzymes for hydrolyzing PET are not limited to extracellular lipase and cutinase, and esterases also show activity on low-molecular chain polyesters. Unlike the water-insoluble substrate that lipase acts on, the substrate that esterase acts on is a water-soluble short-chain ester [94]. Bacillus subtilis p-nitrobenzylesterase (BsEstB) has been proven to hydrolyze film-like PET and produce TPA and MHET monomers [95]. BsEstB realizes the surface functionalization of PET here, which is reflected in the generation of a large number of hydroxyl and carboxyl groups, thereby increasing the surface hydrophilicity. Furthermore, the esterase also has MHET binding sites, which can realize the transformation of the inhibitory product MHET. In comparison to lipase and cutinase, esterase has a low activity temperature and harsh substrate-binding conditions. Therefore, PET degradation is unlikely to occur.
Utilizing PHL7, a metagenomic polyester hydrolase, it is possible to recycle amorphous PET waste with a minimal carbon footprint. This breakdown mechanism yields 91 mg of terephthalic acid per hour per mg of PHL7. The resulting terephthalic acid can be used to prepare virgin PET with a low carbon footprint and great efficiency [96].
For the recycling of waste PET plastics, chemical recycling and biodegradation technologies can be the best choices in terms of sustainability, environmental protection, and economy. The chemical recycling process leads to the formation of polymer raw materials (monomers) or fillers, which neither impose an additional burden on the environment nor require additional resources (monomers) to produce PET [51,52]. Biodegradation technologies have little environmental stress and are economical as well as effective. Thus, the following sections will focus on the biodegradation processes and chemical recycling of waste PET.
Bio-based materials are attractive due to the abundant resources from nature, the benefits of reduced CF, and increased resource efficiency. They are either biobased or biodegradable or with both of the two characteristics [97]. Bioplastics have been one of the most important bio-based materials because of the heavy environmental pollution and waste of carbon resources from petroleum-derived plastics. As to PET plastics, the non-biodegradable bio-based PET that is derived from renewable resources partially accounts for the market of ca. 57% [98]. Under the function of microbial breakdown, the non-biodegradable bio-based PET can reduce CF during manufacture as well as boost resource efficiency. In this sense, bio-based PET can be a highly promising replacement for numerous durable and long-lasting PET plastic items made from fossil fuels. Thus, biomass, which should be pretreated with suitable modification techniques including hydrolysis, fermentation, filtration and so on, can be a biological source to produce bio-based PET. The bio-based PET chemically corresponds to the petrochemical counterparts with partially bio-based components, such as the feedstock of monoethylene glycol (MEG) originating from ethanol from sugarcane or corn starch. In this case, PET resins can be obtained by the reaction between MEG and fossil-based terephthalic acid. The commercial bio-based PET and the feedstocks, such as MEG and TPA from renewable resources, have been simultaneously developed from biomass (mainly sugar and starch), as shown in Fig. 5. According to the bio-synthesis process, the first PET bottle (PlantBottle™) appeared at the World Expo in Milan by Coca-Cola [99]. Furthermore, bio-based PET plastics can be degraded by the novel bacterium, namely Ideonella sakaiensis 201-F [93].
Figure 5: The scheme for preparing fully and the main feedstocks of bio-based MEG and TPA monomers from sugar and starch. Reproduced from [100]
During the preparation procedure depicted in Fig. 5, bioethanol can be obtained in different forms. This is a promising development for ethanol-based chemical products and the reduction of GHG levels. For example, Song et al. prepared a series of bio-based chemical agents by destructing lignin structures in waste bamboo. Xylose and bioethanol were obtained with high efficiency, followed by the successful separation of both products. It supports an alternative pathway that presents the co-production of xylulose and xylitol at low cost, as well as the high-value-added byproducts [101].
Besides the non-degradable bio-based plastics from biomass, degradable plastic is a key material to replace existing plastics and reduce GHG emissions. The most attractive biodegradable plastics are polylactic acid (PLA), poly (butylene succinate) (PBS), PBAT (polyadipate/butylene terephthalate), and polyhydroxyalkanoate (PHA). It is reported that bio-based biodegradable plastics account for 44.6% of the bioplastics market, in which the PLA is 18.7%, PBS is 4.1%, and PHA is 1.7% [102]. Among them, PLA and PBAT are the mainstream products in the field of degradable plastics.
At present, the top three degradable plastics are starch-based composites, PLA and PBAT. Starch is a natural material with defects in performance, and the scope of use is very limited. PLA possesses unique hardness and transparency, and PBAT has the lowest cost as soft material. Owing to the synthesis controlling, the PLA and PBAT can be the most promising bio-polymers. PLA is predominantly utilized for biodegradable straws, while PBAT is predominantly used for biodegradable plastic bags according to their properties [30,103]. Compared to bio-PE and PE, a garbage bag made from PBAT/starch blends has the lowest environmental impact [104]. In addition, PLA has the lowest influence on climate change compared to PLA-based composite films, PLA, PET, and PP, in terms of energy recovery at the end of life [105]. Although the bio-polymers are biodegradable, CO2 emission remains a major environmental concern. It is uncertain whether biodegradable plastics can assist lower the carbon footprint of plastics. Commonly, plants are utilized in the creation of bio-based biodegradable polymers, despite the fact that plants can absorb CO2 through photosynthesis [106]. It has been found that biodegradable plastics can promote metabolic pathways in anaerobic sediments on the seafloor, leading to the decomposition of organic carbon buried in the ocean. This has the potential to impact carbon sequestration in coastal ecosystems, diminishing their capacity to moderate climate change [106,107]. In addition, around 0.02% of the world’s arable land is used to produce bio-based plastics. Up to 5% of arable land will be needed when plastic manufacture is entirely based on biomass [107]. Therefore, the use of land for the production of bio-based plastics should also be concerned. Notably, CO2 emission of bio-based plastics is not always lower than that of traditional plastics. It is reported that the CO2 emission of a PLA clamshell container is higher than that of PS plastics and lower than that of PET. Additionally, PLA composites emit somewhat more CO2 than LDPE composites. Similar results are observed for PHA and PLA in terms of CO2 emission [108]. It is a fact that most bio-based plastics contain similar chemical compounds to fossil-based plastics. Consequently, most bio-based polymers exhibit the same issues as fossil-based plastics [109]. We conclude that one of the best merits of bio-polymers can be bio-degradation in nature instead of decreasing carbon emission.
By contrast, these degradable polymers open up a new cycle from waste plastics to plastic raw materials, reducing soil damage and energy assumption. In addition, the degraded productions can be used as fertilizers, CO2 and water through composting processes, which contributes to the cultivation of sugar- or starch-containing crops. These can be converted into organic molecules for the production of bio-polymers through fermentation and chemical processes. As with fossil raw materials, the entire process forms a degradable cycle to dramatically reduce CO2 emissions. Notably, the improvements regarding biomass utilization should also be carefully balanced with comprehensive environmental impacts, such as GHG emissions, terrestrial acidification, water eutrophication and even marine environment, etc.
4.3 Carbon Capture and Utilization
Carbon capture and utilization strategies offer a promising method for reducing GHG emissions and fossil resource depletion. Owing to the abundance of carbon in plastics, waste plastics can be released as carbon-based gases, primarily carbon monoxide (CO) and carbon dioxide (CO2). Thus, in order to reduce the carbon emissions peak from plastics, it is believed that two factors are crucial. Firstly, the recycling and transformation of waste plastics into carbon-based materials of high efficiency should be noted. Secondly, facile technologies for carbon capture should be developed. It is suggested that carbon capture and utilization can be the optimal approaches to reducing carbon emissions and the employment of fossil resources. It can achieve the two goals specifically by capturing and utilizing CO2 [110].
Carbon capture and storage technologies are promising strategies to reduce CO2 emissions in the atmosphere significantly. For all the carbon capture and storage technologies, carbon capture has become a feasible pathway for humans due to the natural photosynthesis with plants. The abundant CO2 in the atmosphere supplies a big meal for plants with large above-ground surfaces of leaves. Thus, researchers have developed artificial photosynthesis technologies to capture carbon from waste incineration [110–112]. For the purpose of capturing carbon dioxide, Wala et al. heated plastic trash with potassium acetate (as a catalyst) to produce a carbon adsorbent with holes between 0.7 and 1.4 nm. By reversibly capturing CO2 from post-combustion sources like flue gas, the protocol presented here increases and leverages the value of PW products and offers a potential solution to two environmental problems: PW and growing atmospheric CO2 levels [112]. In addition, Yang et al. developed a series of artificial photosynthesis nanomaterials to accomplish carbon capture and transformation into value-added chemicals [113–115]. A technique that mimics natural photosynthesis using carbon dioxide, water, and solar energy has both theoretical and practical relevance. In natural photosynthesis, carbon dioxide is first converted to common biochemical building blocks in large quantities utilizing the energy of the sun, and then it is used to construct complex combinations of molecular compounds that constitute biomass. By creating a biocompatible light-capture nanowire array, Liu et al. [113] have investigated an artificial photosynthetic scheme and demonstrated that a hybrid semiconductor nanowire bacterial system could reduce carbon dioxide at neutral pH to a wide range of chemical targets, including fuels, polymers, and complex drug precursors. Besides, chemical absorption methods, including liquid-phase and solid-phase sorbents, membranes, and ionic liquids, have also been used to capture CO2 [116]. Furthermore, the main promising commercial ways for post-combustion CO2 capture are amine solvents, oxyfuel combustion, and calcium looping technologies [117].
The physical absorption process has also been attractive by using metal-organic frameworks (MOF) nanomaterials, zeolites and active carbon materials, etc. [118], which has been summarized elsewhere in detail [117]. Therefore, the purpose of the carbon capture technology for recycling PET waste is to repurpose these wastes. Transformation of discarded PET into efficient microporous carbons may be the most prevalent approach for CO2 capture [119,120]. According to the previous work [121], there is a large proportion of overlap with the carbon utilization for capturing CO2. It is identified that waste PET bottles-to-CO2 adsorbent strategy is able to achieve negative CO2 emission and thus accomplish an environmentally-friendly route to close the carbon loop. Furthermore, it is suggested that the life cycle implications of water resource depletion can be reduced by more than 25 percent by recycling PET into new products. It has the potential to reduce CO2 emissions indirectly. It is proposed that biomass can directly absorb CO2 in a controlled manner. The biomass gasification (mainly CO2) can be captured experimentally, such as Rectisol process [4]. Then, the captured CO2 can be significantly converted to methanol via the thermal hydrogenation process directly. The obtained methanol can be a feedstock for various kinds of chemical agents, such as ethylene, propylene, benzene, toluene, etc.
PET waste can be converted into solids, liquids, and gases, which can be quantified as CO2 throughout the carbon utilization process. Thus, this section will focus on the utilization of carbon from waste PET in the form of CO2. Some significant progress has been gained in the utilization of CO2 from waste. The capture and utilization of CO2 from waste incineration can contribute to the assay of crops and algae [116]. In this way, the desirable goal of net-zero emission of CO2 from plastics can be achieved in combination with recycling, as depicted in Fig. 6. Technologically, CO2 is mainly from the air with the resources of plastics, which can be captured and conversed into products. Apart from the direct use of CO2, the main transformations of them are chemical products, solid inorganic carbonates and biomass, as shown in Fig. 6. The CO2 captured by vegetation can generate valuable natural materials, such as wood products, increased plant yields, biofuel and bio-derived chemicals [122]. These products are consumed by humans in daily life, which can be transformed again into CO2 following by capture of biomass and artificial capture technologies in the ecosphere stated above. Thus, the closed-loop recycling formed with only the key problem of conversion rate in these processes.
Figure 6: Lifecycle of carbon dioxide reuse with main classes of CO2 sources and partial utilization pathways
So far, two main ways are artificially developed for carbon utilization of CO2 in the carbon capture and utilization strategy, including physical and chemical processes. For the physical process, CO2 is mainly used as a medium material (Fig. 6), including the inert gas in the areas of refrigerant, as extinguishant and modified atmosphere packaging for food preservation, and as the dispensing agent in the carbonation of beverages [110].
For the chemical process, CO2 can be applied in the preparation of inorganic and organic materials under the function of catalysis (mainly homogeneous, heterogeneous, enzymatic agents) and reaction environments (such as photochemical, electrochemical, thermochemical, etc.) inspired by the natural photosynthesis [122]. The inorganic materials are mainly calcite and hydrotalcite, and the organic materials are mainly urea, methanol, salicylic acid and cyclic carbonates, etc. [110,123]. These chemical monomers are accessible to prepare polymers and then plastic products in a closed cycle. It is suggested that the production of several polymers is experimentally possible, such as (poly)carbonates (PC), polyol, polypropylene (PP), polyurethane (PU) and so on [110]. For example, it indicates that the utilization of CO2 for preparing polyurethane can reduce the amounts of fossil resources significantly, according to the life-cycle-assessment (LCA) of CO2-based PU [124].
CO2 can be applied to preparing soda ash products via NaOH route by capturing CO2 from a power plant. It suggests that the cost of CO2 capture can be offset by the soda ash price of 18 $/t. This process supports significant sustainability promising for CO2 utilization due to the less parasitic energy requirements and low initial capital cost [125]. It is notable and arousing that CO2 can be used as feedstock for preparing starch by a cell-free process, according to Cai et al. [126]. They developed a hybrid system, the namely chemoenzymatic system with spatial and temporal segregation, in which CO2 is reduced to methanol under the function of an inorganic catalyst firstly and then significantly converted to three and six carbon sugar units by enzymes, and lastly to polymeric starch. It is able to produce amylose or amylopectin at a rate of 22 nanomoles of CO2 per minute per milligram of total catalyst, which presents about 8.5-fold higher rate than starch synthesis in maize. It is a high-worthy work for the utilization of CO2.
CO2 can be used to synthesize formic acid (FA) with high efficiency. The result illustrates that GHG emissions can be reduced by 97%–132% (1.43–1.95 kg of CO2eq per kg of pure FA). Meanwhile, the fossil resources can be saved by 69%–94% (0.56–0.78 kg oil eq. per kg of pure FA). It concluded that clean production could be conducted by improving energy efficiency and introducing renewable electricity sources during the CO2-based FA production process [127–130]. It is noted that CO2 is suitable for preparing several high-value chemical compounds. This is potentially the most promising method for reducing CO2 emissions at both the beginning and end of the CO2 life cycle. It is the most effective means of achieving carbon peak and carbon neutrality. The key problem is how to recycle the abundant CO2 into a large amount of useful products in environmental processes with high efficiency. According to the previous works [131–133], catalyst technologies can be the key to solving these problems for CO2 recycling.
In summary, we review the paths to achieving a carbon peak for waste PET. Waste PET has been a significantly attractive resource since the globally agreed policy instruments have increased recently, especially for the goals of carbon peak and carbon neutral in China. The optimism path for achieving these goals lays in the net-zero carbon emission PET plastics, including the mixture processes of recycling, biomass utilization, and CO2 capture and utilization.
For the recycling process, physical recycling can be more effective than chemical recycling. The life cycle impacts of water resource depletion can decrease by over 25% by converting waste PET into fresh PET products physically. Nevertheless, chemical recycling presents particular advantages. Waste PET can be transformed into high-valuable products, whether by chemical degradation or carbonized, which enhances the monetary incentive in recycling plastics. Moreover, the degradation products of waste PET can be recycled into another sustainable life cycle with low CO2 emissions. In a word, owing to the huge assumption of PET plastics as bottles, fibers, membranes and even micro-particles, recycling waste PET becomes an extremely way to reduce the emission of the gases of CO2, CH4, NOx, VOCs, SOx, and PM, as well as decrease energy assumption. The vital point lies in the recycling efficiency (100%) of waste PET for both physical and chemical processes. Notably, the PETase hydrolase was firstly and significantly extracted from a bacterium (Ideonella sakaiensis 201-F6) by Yoshida et al. [134], which provided a better solution for the biodegradation of waste PET with low carbon emission. The enzyme uses PET as the only carbon source and has higher binding characteristics than PET. It not only maintains enzyme activity under mild conditions but also has degradability for high crystallinity PET [135–138].
For the biomass utilization process, to reduce the carbon emission in PET, the most promising way can be biomass utilization instead of petroleum-based PET in plastic products, considering the mechanical properties. The bio-based polymers, such as bio-PET, PLA, PGA, PHA, etc., can be alternatives for PET from petroleum resources. These bio-polymers can endow plastics with degradability in nature, while the CO2 emission is higher than that of PS, LDPE, etc., according to LCA. The prepared bio-PET from a feedstock of biomass is a promising way to reduce CO2 emission by decreasing the byproducts and energy consumption.
The carbon capture and utilization processes are the ending lifecycles of the carbon emission and the beginning lifecycle of the carbon resources from wastes PET. These processes enhance the availability of waste PET as a resource, as well as provide the chance for CO2 utilization to achieve net-zero emission PET plastics. It is widely believed that CO2 can be feedstock for various kinds of chemical products, including ethyl alcohol, formic acid, soda ash, PU, starch and so on. This can be the most efficient strategy to complete CO2 recycling.
Despite considerable progress in carbon peak for recycling waste PET and its derivatives, there are challenges that remain to be solved so that waste PET can be 100% recycled and the CO2 emission can be controlled and reused. Here we outline several proposed solutions presented as follows:
1. The circular carbon economy with low energy consumption, operational costs, and environmental well-being should be carried out to redesign plastics production systems.
2. The degradation efficiency should be improved for the chemical degradation of waste PET, as well as the reusing efficiency of the degradation products. These degradation products must be used as raw materials in preparing chemical agents or polymers as much as possible.
3. The biocatalytic degradation of PET provides a “green way” for waste management, which shows a high degree of adaptation to PET. Yet, enzyme activity, low thermal stability, and long cycle should be improved in future works.
4. The CO2 capture and utilization technologies need to be further developed, including CO2 capture materials and process design and CO2 utilization methods. The CO2 utilization efficiency also should be improved in two ways. The first one can be the improvement of the utilization amount of CO2. The other one is to expand the kinds of products from CO2.
Funding Statement: The authors acknowledge the financial support provided by the Key R&D Program of Shaanxi Province (No. 2022SF-168); Xi’an Programs for Science and Technology Plan (Nos. 2020KJRC0090 and 21XJZZ0045); Xi’an Beilin District Programs for Science and Technology Plan (No. GX2247); the Outstanding Chinese and Foreign Youth Exchange Program of China Association for Science and Technology (CAST) in 2019; the Opening Project of Shanxi Key Laboratory of Advanced Manufacturing Technology (No. XJZZ202001); the Scientific Research Project of Shaanxi Education Department (No. 20JS108); Open Foundation of Key Laboratory of Auxiliary Chemistry and Technology for Chemical Industry, Ministry of Education, Shaanxi University of Science and Technology (No. KFKT2021-01) and Shaanxi Collaborative Innovation Center of Industrial Auxiliary Chemistry and Technology, Shaanxi University of Science and Technology (No. KFKT2021-01).
Conflicts of Interest: The authors declare that they have no conflicts of interest to report regarding the present study.
References
1. Fang, K., Li, C., Tang, Y., He, J., Song, J. (2022). China’s pathways to peak carbon emissions: New insights from various industrial sectors. Applied Energy, 306, 118039. DOI 10.1016/j.apenergy.2021.118039. [Google Scholar] [CrossRef]
2. Rode, A., Carleton, T., Delgado, M., Greenstone, M., Houser, T. et al. (2021). Estimating a social cost of carbon for global energy consumption. Nature, 598(7889), 308–314. DOI 10.1038/s41586-021-03883-8. [Google Scholar] [CrossRef]
3. Wang, Y., Guo, C., Chen, X., Jia, L., Guo, X. et al. (2021). Carbon peak and carbon neutrality in China: Goals, implementation path and prospects. China Geology, 4(4), 720–746. DOI 10.31035/cg2021083. [Google Scholar] [CrossRef]
4. Meys, R., Kätelhön, A., Bachmann, M., Winter, B., Zibunas, C. et al. (2021). Achieving net-zero greenhouse gas emission plastics by a circular carbon economy. Science, 374(6563), 71–76. DOI 10.1126/science.abg9853. [Google Scholar] [CrossRef]
5. Zhou, X., Li, Y., Fang, C. Q., Li, S. J., Cheng, Y. L. et al. (2015). Recent advances in synthesis of waterborne polyurethane and their application in water-based ink: A review. Journal of Materials Science & Technology, 31(7), 708–722. DOI 10.1016/j.jmst.2015.03.002. [Google Scholar] [CrossRef]
6. Zhou, X., Fang, C. Q., Li, Y., An, N. L., Lei, W. Q. (2016). Preparation and characterization of Fe3O4-CNTs magnetic nanocomposites for potential application in functional magnetic printing ink. Composites Part B: Engineering, 89, 295–302. DOI 10.1016/j.compositesb.2015.11.041. [Google Scholar] [CrossRef]
7. El Essawy, N. A., Gouda, M. H., Ali, S. M., Salerno, M., Mohy Eldin, M. S. (2020). Effective elimination of contaminant antibiotics using high-surface-area magnetic-functionalized graphene nanocomposites developed from plastic waste. Materials, 13(7), 1517. DOI 10.3390/ma13071517. [Google Scholar] [CrossRef]
8. El Essawy, N. A., Konsowa, A. H., Elnouby, M., Farag, H. A. (2017). A novel one-step synthesis for carbon-based nanomaterials from polyethylene terephthalate (PET) bottles waste. Journal of the Air & Waste Management Association, 67(3), 358–370. DOI 10.1080/10962247.2016.1242517. [Google Scholar] [CrossRef]
9. Schmidt, S., Laner, D., Eygen, E. V., Stanisavljevi, N. (2020). Material efficiency to measure the environmental performance of waste management systems: A case study on pet bottle recycling in Austria, Germany and Serbia. Waste Management, 110, 74–86. DOI 10.1016/j.wasman.2020.05.011. [Google Scholar] [CrossRef]
10. Darzi, R., Dubowski, Y., Posmanik, R. (2022). Hydrothermal processing of polyethylene-terephthalate and nylon-6 mixture as a plastic waste upcycling treatment: A comprehensive multi-phase analysis. Waste Management, 143, 223–231. DOI 10.1016/j.wasman.2022.03.002. [Google Scholar] [CrossRef]
11. Ingrao, C., Lo Giudice, A., Bacenetti, J., Tricase, C., Dotelli, G. (2015). Energy and environmental assessment of industrial hemp for building applications: A review. Renewable & Sustainable Energy Reviews, 51, 29–42. DOI 10.1016/j.rser.2015.06.002. [Google Scholar] [CrossRef]
12. PlasticsEurope (2021). Plastics-the Facts 2021. https://plasticse urope.org/knowledge-hub/plastics-the-facts-2021/. [Google Scholar]
13. Schaefer, C. E., Kupwade-Patil, K., Ortega, M., Soriano, C., Büyüköztürk, O. (2018). Irradiated recycled plastic as a concrete additive for improved chemo-mechanical properties and lower carbon footprint. Waste Management, 71, 426–439. DOI 10.1016/j.wasman.2017.09.033. [Google Scholar] [CrossRef]
14. Zhou, X., Su, J., Wang, C. X., Fang, C. Q., He, X. Y. (2020). Design, preparation and measurement of protein/CNTs hybrids: A concise review. Journal of Materials Science & Technology, 46, 74–87. DOI 10.1016/j.jmst.2020.01.008. [Google Scholar] [CrossRef]
15. Zhang, Q. Y., Wu, R. Q., Zhou, Y. H., Lin, Q. L., Fang, C. Q. (2022). A novel surface-oxidized rigid carbon foam with hierarchical macro-nanoporous structure for efficient removal of malachite green and lead ion. Journal of Materials Science & Technology, 103, 15–28. DOI 10.1016/j.jmst.2021.07.012. [Google Scholar] [CrossRef]
16. Sandru, M., Sandru, E. M., Ingram, W. F., Deng, J., Stenstad, P. M. (2022). An integrated materials approach to ultrapermeable and ultraselective CO2 polymer membranes. Science, 376(6588), 90–94. DOI 10.1126/science.abj9351. [Google Scholar] [CrossRef]
17. Liu, Z., Liu, W., Walker, T. R., Adams, M., Zhao, J. (2021). How does the global plastic waste trade contribute to environmental benefits: Implication for reductions of greenhouse gas emissions? Journal of Environmental Management, 287, 112283. DOI 10.1016/j.jenvman.2021.112283. [Google Scholar] [CrossRef]
18. Jehanno, C., Alty, J. W., Roosen, M., Meester, S. D., Dove, A. P. (2022). Critical advances and future opportunities in upcycling commodity polymers. Nature, 603(7903), 803–814. DOI 10.1038/s41586-021-04350-0. [Google Scholar] [CrossRef]
19. Cimini, A., Moresi, M. (2018). Mitigation measures to minimize the cradle-to-grave beer carbon footprint as related to the brewery size and primary packaging materials. Journal of Food Engineering, 236, 1–8. DOI 10.1016/j.jfoodeng.2018.05.001. [Google Scholar] [CrossRef]
20. Raheem, A. B., Noor, Z. Z., Hassan, A., Abd Hamid, M. K., Samsudin, S. A. (2019). Current developments in chemical recycling of post-consumer polyethylene terephthalate wastes for new materials production: A review. Journal of Cleaner Production, 225, 1052–1064. DOI 10.1016/j.jclepro.2019.04.019. [Google Scholar] [CrossRef]
21. Koshti, R., Mehta, L., Samarth, N. (2018). Biological recycling of polyethylene terephthalate: A mini-review. Journal of Polymers and the Environment, 26(8), 3520–3529. DOI 10.1007/s10924-018-1214-7. [Google Scholar] [CrossRef]
22. Cot, S., Leu, M. K., Kalamiotis, A., Dimitrakis, G., Sans, V. (2019). An oxalate-bridged binuclear iron (iii) ionic liquid for the highly efficient glycolysis of polyethylene terephthalate under microwave irradiation. Chempluschem, 84(7), 786–793. DOI 10.1002/cplu.201900075. [Google Scholar] [CrossRef]
23. Najafi, S. K. (2013). Use of recycled plastics in wood plastic composites–A review. Waste Management, 33(9), 1898–1905. DOI 10.1016/j.wasman.2013.05.017. [Google Scholar] [CrossRef]
24. Al-Salem, S. M., Antelava, A., Constantinou, A., Manos, G., Dutta, A. et al. (2017). A review on thermal and catalytic pyrolysis of plastic solid waste (PSW). Journal of Environmental Management, 197, 177–198. DOI 10.1016/j.jenvman.2017.03.084. [Google Scholar] [CrossRef]
25. Diaz-Silvarrey, L. S., McMahon, A., Phan, A. N. (2018). Benzoic acid recovery via waste poly (ethylene terephthalate) (PET) catalytic pyrolysis using sulphated zirconia catalyst. Journal of Analytical and Applied Pyrolysis, 134, 621–631. DOI 10.1016/j.jaap.2018.08.014. [Google Scholar] [CrossRef]
26. Asensio, M., Esfandiari, P., Núñez, K., Silva, J. F., Marques, A. et al. (2020). Processing of pre-impregnated thermoplastic towpreg reinforced by continuous glass fibre and recycled PET by pultrusion. Composites Part B: Engineering, 200, 108365. DOI 10.1016/j.compositesb.2020.108365. [Google Scholar] [CrossRef]
27. Zhou, X., Fang, C. Q., Yu, Q., Yang, R., Xie, L. et al. (2017). Synthesis and characterization of waterborne polyurethane dispersion from glycolyzed products of waste polyethylene terephthalate used as soft and hard segment. International Journal of Adhesion and Adhesives, 74, 49–56. DOI 10.1016/j.ijadhadh.2016.12.010. [Google Scholar] [CrossRef]
28. Zhou, X., Deng, J. R., Fang, C. Q., Yu, R. E., Lei, W. Q. et al. (2020). Preparation and characterization of lysozyme@carbon nanotubes/waterborne polyurethane composite and the potential application in printing inks. Progress in Organic Coatings, 142, 105600. DOI 10.1016/j.porgcoat.2020.105600. [Google Scholar] [CrossRef]
29. Zhou, X., Deng, J. R., Yang, R., Zhou, D., Fang, C. Q. et al. (2020). Facile preparation and characterization of fibrous carbon nanomaterial from waste polyethylene terephthalate. Waste Management, 107, 172–181. DOI 10.1016/j.wasman.2020.03.041. [Google Scholar] [CrossRef]
30. Zhou, X., Deng, J. R., Fang, C. Q., Yu, R. E., Lei, W. Q. et al. (2020). Additive manufacturing of CNTs/PLA composites and the correlation between microstructure and functional properties. Journal of Materials Science & Technology, 60, 27–34. DOI 10.1016/j.jmst.2020.04.038. [Google Scholar] [CrossRef]
31. Zhou, X., Wang, C. X., Fang, C. Q., Yu, R. E., Li, Y. G. et al. (2019). Structure and thermal properties of various alcoholysis products from waste poly(ethylene terephthalate). Waste Management, 85, 164–174. DOI 10.1016/j.wasman.2018.12.032. [Google Scholar] [CrossRef]
32. Fuks, L., Herdzik-Koniecko, I., Rogowski, M. (2021). Carbon obtained from waste polyethylene terephthalate (PET) containers as potential sorbent of radionuclides from the contaminated aqueous solutions. International Journal of Environmental Science and Technology, 18(11), 3527–3538. DOI 10.1007/s13762-020-03102-3. [Google Scholar] [CrossRef]
33. Djahed, B., Shahsavani, E., Naji, F. K., Mahvi, A. H. (2016). A novel and inexpensive method for producing activated carbon from waste polyethylene terephthalate bottles and using it to remove methylene blue dye from aqueous solution. Desalination and Water Treatment, 57(21), 9871–9880. DOI 10.1080/19443994.2015.1033647. [Google Scholar] [CrossRef]
34. Torrik, E., Nejati, E., Soleimani, M. (2014). Economic pre-feasibility study for physical conversion of polyethylene terephthalate wastes to activated carbon. Asia-Pacific Journal of Chemical Engineering, 9(5), 759–767. DOI 10.1002/apj.1822. [Google Scholar] [CrossRef]
35. Liu, X. G., Wen, Y. L., Chen, X. C., Tang, T., Mijowska, E. (2020). Co-etching effect to convert waste polyethylene terephthalate into hierarchical porous carbon toward excellent capacitive energy storage. Science of the Total Environment, 723, 138055. DOI 10.1016/j.scitotenv.2020.138055. [Google Scholar] [CrossRef]
36. Bazargan, A., McKay, G. (2012). A review-synthesis of carbon nanotubes from plastic wastes. Chemical Engineering Journal, 195, 377–391. DOI 10.1016/j.cej.2012.03.077. [Google Scholar] [CrossRef]
37. Gong, J., Chen, X., Tang, T. (2019). Recent progress in controlled carbonization of (waste) polymers. Progress in Polymer Science, 94, 1–32. DOI 10.1016/j.progpolymsci.2019.04.001. [Google Scholar] [CrossRef]
38. Luong, D. X., Bets, K. V., Algozeeb, W. A., Stanford, M. G., Kittrell, C. et al. (2020). Gram-scale bottom-up flash graphene synthesis. Nature, 577(7792), 647–651. DOI 10.1038/s41586-020-1938-0. [Google Scholar] [CrossRef]
39. Wei, S. H., Kamali, A. R. (2020). Dual-step air-thermal treatment for facile conversion of PET into porous carbon particles with enhanced dye adsorption performance. Diamond and Related Materials, 107, 107914. DOI 10.1016/j.diamond.2020.107914. [Google Scholar] [CrossRef]
40. El Essawy, N. A., Ali, S. M., Farag, H. A., Konsowa, A. H., Elnouby, M. et al. (2017). Green synthesis of graphene from recycled PET bottle wastes for use in the adsorption of dyes in aqueous solution. Ecotoxicology and Environmental Safety, 145, 57–68. DOI 10.1016/j.ecoenv.2017.07.014. [Google Scholar] [CrossRef]
41. El Essawy, N. A., El Nady, J., Wazeer, W., Kashyout, A. B. (2019). Development of high-performance supercapacitor based on a novel controllable green synthesis for 3D nitrogen doped graphene. Scientific Reports, 9, 1129. DOI 10.1038/s41598-018-37369-x. [Google Scholar] [CrossRef]
42. Maalouf, C., Ingrao, C., Scrucca, F., Moussa, T., Bourdot, A. et al. (2018). An energy and carbon footprint assessment upon the usage of hemplime concrete and recycled-PET façades for office facilities in France and Italy. Journal of Cleaner Production, 170, 1640–1653. DOI 10.1016/j.jclepro.2016.10.111. [Google Scholar] [CrossRef]
43. Botto, S., Niccolucci, V., Rugani, B., Nicolardi, V., Bastianoni, S. (2011). Towards lower carbon footprint patterns of consumption: The case of drinking water in Italy. Environmental Science & Policy, 14(4), 388–395. DOI 10.1016/j.envsci.2011.01.004. [Google Scholar] [CrossRef]
44. Rahim, R., Raman, A. A. A. (2017). Carbon dioxide emission reduction through cleaner production strategies in a recycled plastic resins producing plant. Journal of Cleaner Production, 141, 1067–1073. DOI 10.1016/j.jclepro.2016.09.023. [Google Scholar] [CrossRef]
45. Le, D. K., Leung, R. I. H., Er, A. S. R., Zhang, X. W., Tay, X. J. (2019). Applications of functionalized polyethylene terephthalate aerogels from plastic bottle waste. Waste Management, 100, 296–305. DOI 10.1016/j.wasman.2019.09.031. [Google Scholar] [CrossRef]
46. Park, S. H., Kim, S. H. (2014). Poly (ethylene terephthalate) recycling for high value added textiles. Fashion and Textiles, 1(1), 1–17. DOI 10.1186/s40691-014-0001-x. [Google Scholar] [CrossRef]
47. Yang, L., Gao, J., Liu, Y., Zhuang, G. Q., Peng, X. W. (2021). Biodegradation of expanded polystyrene and low-density polyethylene foams in larvae of tenebrio molitor linnaeus (Coleoptera: TenebrionidaeBroad versus limited extent depolymerization and microbe-dependence versus independence. Chemosphere, 262, 127818. DOI 10.1016/j.chemosphere.2020.127818. [Google Scholar] [CrossRef]
48. Cakic, S. M., Ristic, I. S., Cincovic, M. M., Nikolic, N. C., Ilic, O. Z. (2012). Glycolyzed products from PET waste and their application in synthesis of polyurethane dispersions. Progress in Organic Coatings, 74(1), 115–124. DOI 10.1016/j.porgcoat.2011.11.024. [Google Scholar] [CrossRef]
49. Abdelaal, M. Y., Sobahi, T. R., Makki, M. S. I. (2011). Chemical transformation of pet waste through glycolysis. Construction and Building Materials, 25(8), 3267–3271. DOI 10.1016/j.conbuildmat.2011.03.013. [Google Scholar] [CrossRef]
50. Tawfik, M. E., Eskander, S. B. (2010). Chemical recycling of poly(ethylene terephthalate) waste using ethanolamine. Sorting of the end products. Polymer Degradation and Stability, 95(2), 187–194. DOI 10.1016/j.polymdegradstab.2009.11.026. [Google Scholar] [CrossRef]
51. Imran, M., Kim, B. K., Han, M., Cho, B. G., Kim, D. H. (2010). Sub- and supercritical glycolysis of polyethylene terephthalate (PET) into the monomer bis(2-hydroxyethyl) terephthalate (BHET). Polymer Degradation and Stability, 95(9), 1686–1693. DOI 10.1016/j.polymdegradstab.2010.05.026. [Google Scholar] [CrossRef]
52. Sinha, V., Patel, M. R., Patel, J. V. (2010). PET waste management by chemical recycling: A review. Journal of Polymers and the Environment, 18(1), 8–25. DOI 10.1007/s10924-008-0106-7. [Google Scholar] [CrossRef]
53. Barth, M., Oeser, T., Wei, R., Then, J., Schmidt, J. et al. (2015). Effect of hydrolysis products on the enzymatic degradation of polyethylene terephthalate nanoparticles by a polyester hydrolase from thermobifida fusca. Biochemical Engineering Journal, 93, 222–228. DOI 10.1016/j.bej.2014.10.012. [Google Scholar] [CrossRef]
54. Cudjoe, D., Wang, H., Zhu, B. (2021). Assessment of the potential energy and environmental benefits of solid waste recycling in China. Journal of Environmental Management, 295, 113072. DOI 10.1016/j.jenvman.2021.113072. [Google Scholar] [CrossRef]
55. Yadav, V., Sherly, M. A., Ranjan, P., Tinoco, R. O., Boldrin, A. et al. (2020). Framework for quantifying environmental losses of plastics from landfills. Resources Conservation and Recycling, 161, 104914. DOI 10.1016/j.resconrec.2020.104914. [Google Scholar] [CrossRef]
56. Salem, Z., Hamouri, K., Djemaa, R., Allia, K. (2008). Evaluation of landfill leachate pollution and treatment. Desalination, 220(1–3), 108–114. DOI 10.1016/j.desal.2007.01.026. [Google Scholar] [CrossRef]
57. Wang, D., Tang, Y. T., Long, G., Higgitt, D., He, J. et al. (2020). Future improvements on performance of an EU landfill directive driven municipal solid waste management for a city in England. Waste Management, 102, 452–463. DOI 10.1016/j.wasman.2019.11.009. [Google Scholar] [CrossRef]
58. Maris, J., Bourdon, S., Brossard, J. M., Cauret, L., Fontaine, L. et al. (2018). Mechanical recycling: Compatibilization of mixed thermoplastic wastes. Polymer Degradation and Stability, 147, 245–266. DOI 10.1016/j.polymdegradstab.2017.11.001. [Google Scholar] [CrossRef]
59. Cavalieri, F., Padella, F. (2002). Development of composite materials by mechanochemical treatment of post-consumer plastic waste. Waste Management, 22(8), 913–916. DOI 10.1016/S0956-053X(02)00084-3. [Google Scholar] [CrossRef]
60. van Bruggen, E. P. A., Koster, R. P., Picken, S. J., Ragaert, K. (2016). Influence of processing parameters and composition on the effective compatibilization of polypropylene-poly(ethylene terephthalate) blends. International Polymer Processing, 31(2), 179–187. DOI 10.3139/217.3124. [Google Scholar] [CrossRef]
61. Ugduler, S., van Geem, K. M., Denolf, R., Roosen, M., Mys, N. et al. (2020). Towards closed-loop recycling of multilayer and coloured PET plastic waste by alkaline hydrolysis. Green Chemistry, 22(16), 5376–5394. DOI 10.1039/d0gc00894j. [Google Scholar] [CrossRef]
62. Zhang, L. Y., Li, Y. G., Zhang, W., Xi, K., Kim, K. H. et al. (2021). The potential of microplastics as adsorbents of sodium dodecyl benzene sulfonate and chromium in an aqueous environment. Environmental Research, 197, 111057. DOI 10.1016/j.envres.2021.111057. [Google Scholar] [CrossRef]
63. Shen, Y. B., He, J. L., Xie, Z. X., Zhou, X., Zhang, C. Q. et al. (2019). Synthesis and characterization of vegetable oil based polyurethanes with tunable thermomechanical performance. Industrial Crops and Products, 140, 111711. DOI 10.1016/j.indcrop.2019.111711. [Google Scholar] [CrossRef]
64. Chavez, R., Sharma, M. (2017). Profitability and environmental friendliness of a closed-loop supply chain for PET components: A case study of the mexican automobile market. Resources Conservation and Recycling, 135, 172–189. DOI 10.1016/j.resconrec.2017.10.038. [Google Scholar] [CrossRef]
65. Zhou, L., Lu, X. M., Ju, Z. Y., Liu, B., Yao, H. Y. (2019). Alcoholysis of polyethylene terephthalate to produce dioctyl terephthalate using choline chloride-based deep eutectic solvents as efficient catalysts. Green Chemistry, 21(4), 897–906. DOI 10.1039/c8gc03791d. [Google Scholar] [CrossRef]
66. Abdullah, M. M. S., Al-Lohedan, H. A. (2020). Novel amphiphilic gemini ionic liquids based on consumed polyethylene terephthalate as demulsifiers for Arabian heavy crude oil. Fuel, 266, 117057. DOI 10.1016/j.fuel.2020.117057. [Google Scholar] [CrossRef]
67. Nabid, M. R., Bide, Y., Fereidouni, N., Etemadi, B. (2017). Maghemite/nitrogen-doped graphene hybrid material as a reusable bifunctional catalyst for glycolysis of polyethylene terephthalate. Polymer Degradation and Stability, 144, 434–441. DOI 10.1016/j.polymdegradstab.2017.08.033. [Google Scholar] [CrossRef]
68. Meawad, A., Ibrahim, S. (2019). Novel bifunctional dispersing agents from waste PET packaging materials and interaction with cement. Waste Management, 85, 563–573. DOI 10.1016/j.wasman.2019.01.028. [Google Scholar] [CrossRef]
69. Lopez-Fonseca, R., Duque-Ingunza, I., de Rivas, B., Arnaiz, S., Gutierrez-Ortiz, J. I. (2010). Chemical recycling of post-consumer PET wastes by glycolysis in the presence of metal salts. Polymer Degradation and Stability, 95(6), 1022–1028. DOI 10.1016/j.polymdegradstab.2010.03.007. [Google Scholar] [CrossRef]
70. Lee, J., Lee, T., Tsang, Y. F., Oh, J. I., Kwon, E. E. (2017). Enhanced energy recovery from polyethylene terephthalate via pyrolysis in CO2 atmosphere while suppressing acidic chemical species. Energy Conversion and Management, 148, 456–460. DOI 10.1016/j.enconman.2017.06.026. [Google Scholar] [CrossRef]
71. Joshi, C. A., Jeffrey, R. S. (2019). Total generation and combustion emissions of plastic derived fuels: A trash to tank approach. Environmental Progress & Sustainable Energy, 39(5), e13151. DOI 10.1002/ep.13151. [Google Scholar] [CrossRef]
72. Chen, C. C., Dai, L. H., Ma, L. X., Guo, R. T. (2020). Enzymatic degradation of plant biomass and synthetic polymers. Nature Reviews Chemistry, 4(3), 114–126. DOI 10.1038/s41570-020-0163-6. [Google Scholar] [CrossRef]
73. Han, X., Liu, W. D., Huang, J. W., Ma, J. T., Zheng, Y. Y. et al. (2017). Structural insight into catalytic mechanism of PET hydrolase. Nature Communications, 8, 2106. DOI 10.1038/s41467-017-02255-z. [Google Scholar] [CrossRef]
74. Sangalang, A., Bartolome, L., Kim, D. H. (2015). Generalized kinetic analysis of heterogeneous PET glycolysis: Nucleation-controlled depolymerization. Polymer Degradation and Stability, 115, 45–53. DOI 10.1016/j.polymdegradstab.2015.02.012. [Google Scholar] [CrossRef]
75. Kawai, F., Kawabata, T., Oda, M. (2020). Current state and perspectives related to the polyethylene terephthalate hydrolases available for biorecycling. ACS Sustainable Chemistry & Engineering, 8(24), 8894–8908. DOI 10.1021/acssuschemeng.0c01638. [Google Scholar] [CrossRef]
76. Son, H. F., Cho, I. J., Joo, S., Seo, H., Sagong, H. Y. et al. (2019). Rational protein engineering of thermo-stable PETase from Ideonella sakaiensis for highly efficient PET degradation. ACS Catalysis, 9(4), 3519–3526. DOI 10.1021/acscatal.9b00568. [Google Scholar] [CrossRef]
77. Aguado, A., Martinez, L., Becerra, L., Arieta-araunabena, M., Arnaiz, S. et al. (2011). Chemical depolymerisation of PET complex waste: Hydrolysis vs. glycolysis. Journal of Material Cycles and Waste Management, 16(2), 201–210. DOI 10.1007/s10163-013-0177-y. [Google Scholar] [CrossRef]
78. Grause, G., Kaminsky, W., Fahrbach, G. (2004). Hydrolysis of poly(ethylene terephthalate) in a fluidised bed reactor. Polymer Degradation and Stability, 85, 571–575. DOI 10.1016/j.polymdegradstab.2003.10.020. [Google Scholar] [CrossRef]
79. Pellis, A., Gamerith, C., Ghazaryan, G., Ortner, A., Herrero, A. E. et al. (2016). Ultrasound-enhanced enzymatic hydrolysis of poly(ethylene terephthalate). Bioresource Technology, 218, 1298–1302. DOI 10.1016/j.biortech.2016.07.106. [Google Scholar] [CrossRef]
80. Park, R., Sridhar, V., Park, H. (2020). Taguchi method for optimization of reaction conditions in microwave glycolysis of waste PET. Journal of Material Cycles and Waste Management, 22(3), 664–672. DOI 10.1007/s10163-019-00958-7. [Google Scholar] [CrossRef]
81. Paliwal, N. R., Mungray, A. K. (2013). Ultrasound assisted alkaline hydrolysis of poly(ethylene terephthalate) in presence of phase transfer catalyst. Polymer Degradation and Stability, 98(10), 2094–2101. DOI 10.1016/j.polymdegradstab.2013.06.030. [Google Scholar] [CrossRef]
82. Genta, M., Goto, M., Sasaki, M. (2010). Heterogeneous continuous kinetics modeling of PET depolymerization in supercritical methanol. Journal of Supercritical Fluids, 52(3), 266–275. DOI 10.1016/j.supflu.2010.01.007. [Google Scholar] [CrossRef]
83. Tang, H., Li, N., Li, G. Y., Wang, A. Q., Cong, Y. et al. (2019). Synthesis of gasoline and jet fuel range cycloalkanes and aromatics from poly(ethylene terephthalate) waste. Green Chem, 21(10), 2709–2719. DOI 10.1039/c9gc00571d. [Google Scholar] [CrossRef]
84. Sako, T., Okajima, I., Sugeta, T., Otake, K., Yoda, S. et al. (2000). Recovery of constituent monomers from polyethylene terephthalate with supercritical methanol. Polymer Journal, 32, 178–181. DOI 10.1295/polymj.32.178. [Google Scholar] [CrossRef]
85. de Castro, R. N. E., Vidotti, G. J., Rubira, A. F., Muniz, E. C. (2006). Depolymerization of poly(ethylene terephthalate) wastes using ethanol and ethanol/water in supercritical conditions. Journal of Applied Polymer Science, 101(3), 2009–2016. DOI 10.1002/app.23748. [Google Scholar] [CrossRef]
86. Yang, Y., Lu, Y., Xiang, H., Xu, Y., Li, Y. (2002). Study on methanolytic depolymerization of PET with supercritical methanol for chemical recycling. Polymer Degradation and Stability, 75(1), 185–191. DOI 10.1016/S0141-3910(01)00217-8. [Google Scholar] [CrossRef]
87. Kazemi, M., Kabir, S. F., Fini, E. H. (2021). State of the art in recycling waste thermoplastics and thermosets and their applications in construction. Resources, Conservation and Recycling, 174, 105776. DOI 10.1016/j.resconrec.2021.105776. [Google Scholar] [CrossRef]
88. Eshaq, G., ElMetwally, A. E. (2016). (Mg-Zn)-Al layered double hydroxide as a regenerable catalyst for the catalytic glycolysis of polyethylene terephthalate. Journal of Molecular Liquids, 214, 1–6. DOI 10.1016/j.molliq.2015.11.049. [Google Scholar] [CrossRef]
89. Allen, R. D. (2019). Waste PET: A renewable resource. Joule, 3(4), 910. DOI 10.1016/j.joule.2019.04.002. [Google Scholar] [CrossRef]
90. Rorrer, N. A., Nicholson, S., Carpenter, A., Biddy, M. J., Grundl, N. J. et al. (2019). Combining reclaimed PET with bio-based monomers enables plastics upcycling. Joule, 3(4), 1006–1027. DOI 10.1016/j.joule.2019.01.018. [Google Scholar] [CrossRef]
91. Wei, R., Zimmermann, W. (2017). Biocatalysis as a green route for recycling the recalcitrant plastic polyethylene terephthalate. Microbial Biotechnology, 10(6), 1302–1307. DOI 10.1111/1751-7915.12714. [Google Scholar] [CrossRef]
92. Taniguchi, I., Yoshida, S., Hiraga, K., Miyamoto, K., Kimura, Y. et al. (2019). Biodegradation of PET: Current status and application aspects. ACS Catalysis, 9(5), 4089–4105. DOI 10.1021/acscatal.8b05171. [Google Scholar] [CrossRef]
93. Tournier, V., Topham, C. M., Andre, I., Duquesne, S., Marty, A. et al. (2020). An engineered PET depolymerase to break down and recycle plastic bottles. Nature, 580(7802), 216–219. DOI 10.1038/s41586-020-2149-4. [Google Scholar] [CrossRef]
94. Eberl, A., Heumann, S., Bruckner, T., Araujo, R., Cavaco-Paulo, A. et al. (2009). Enzymatic surface hydrolysis of poly(ethylene terephthalate) and bis(benzoyloxyethyl) terephthalate by lipase and cutinase in the presence of surface active molecules. Journal of Biotechnology, 143(3), 207–212. DOI 10.1016/j.jbiotec.2009.07.008. [Google Scholar] [CrossRef]
95. Ribitsch, D., Heumann, S., Trotscha, E., Acero, E. H., Greimel, K. et al. (2011). Hydrolysis of polyethylene terephthalate by p-nitrobenzylesterase from bacillus subtilis. Biotechnology Progress, 27(4), 951–960. DOI 10.1002/btpr.610. [Google Scholar] [CrossRef]
96. Sonnendecker, C., Oeser, J., Richter, P. K., Hille, P., Zhao, Z. et al. (2022). Low carbon footprint recycling of post-consumer PET plastic with a metagenomic polyester hydrolase. ChemSusChem, 15(9). DOI 10.1002/cssc.202101062. [Google Scholar] [CrossRef]
97. Zhou, X., Hao, Y. Y., He, X. Y., Zhou, D., Xie, L. et al. (2020). Protean morphology of waterborne polyurethane dispersion: An overview of nanoparticles from sphere to irregular elongated shape. Progress in Organic Coatings, 146, 105742. DOI 10.1016/j.porgcoat.2020.105742. [Google Scholar] [CrossRef]
98. Andreeßen, C., Steinbüchel, A. (2019). Recent developments in non-biodegradable biopolymers: Precursors, production processes, and future perspectives. Applied Microbiology and Biotechnology, 103(1), 143–157. DOI 10.1007/s00253-018-9483-6. [Google Scholar] [CrossRef]
99. Bioplastics Magazine (2015). Coca-Cola Introduced World’s First 100% Biobased PET Bottle. http://www.bioplasticsmagazine.com/en/news/meldungen/20150604_Coca-Cola.php. [Google Scholar]
100. Corinaldesi, V., Donnini, J., Nardinocchi, A. (2015). Lightweight plasters containing plastic waste for sustainable and energy-efficient building. Applied Microbiology and Biotechnology, 94, 337–345. DOI 10.1016/j.conbuildmat.2015.07.069. [Google Scholar] [CrossRef]
101. Song, Y. H., Lee, Y. G., Cho, E. J., Bae, H. J. (2020). Production of xylose, xylulose, xylitol, and bioethanol from waste bamboo using hydrogen peroxicde-acetic acid pretreatment. Fuel, 278, 118247. DOI 10.1016/j.fuel.2020.118247. [Google Scholar] [CrossRef]
102. Rahman, M. H., Bhoi, P. R. (2021). An overview of non-biodegradable bioplastic. Journal of Cleaner Production, 294, 126218. DOI 10.1016/j.jclepro.2021.126218. [Google Scholar] [CrossRef]
103. Zhou, X., Zhang, X., Wang, D., Fang, C. Q., Lei, W. Q. et al. (2020). Preparation and characterization of waterborne polyurethane/cellulose nanocrystal composite membrane from recycling waste paper. Journal of Renewable Materials, 8(6), 631–645. DOI 10.32604/jrm.2020.010176. [Google Scholar] [CrossRef]
104. Saibuatrong, W., Cheroennet, N., Suwanmanee, U. (2017). Life cycle assessment focusing on the waste management of conventional and bio-based garbage bags. Journal of Cleaner Production, 158, 319–334. DOI 10.1016/j.jclepro.2017.05.006. [Google Scholar] [CrossRef]
105. Benetto, E., Jury, C., Igos, E., Carton, J., Hild, P. et al. (2015). Using atmospheric plasma to design multilayer film from polylactic acid and thermoplastic starch: A screening life cycle assessment. Journal of Cleaner Production, 87, 953–960. DOI 10.1016/j.jclepro.2014.10.056. [Google Scholar] [CrossRef]
106. Sanz-Lázaro, C., Casado-Coy, N., Beltrán-Sanahuja, A. (2021). Biodegradable plastics can alter carbon and nitrogen cycles to a greater extent than conventional plastics in marine sediment. Science of the Total Environment, 756, 1–7. DOI 10.1016/j.scitotenv.2020.143978. [Google Scholar] [CrossRef]
107. Zheng, J., Suh, S. (2019). Strategies to reduce the global carbon footprint of plastics. Nature Climate Change, 9(7), 374–378. DOI 10.1016/j.scitotenv.2020.143978. [Google Scholar] [CrossRef]
108. Choi, B., Yoo, S., Park, S. I. (2018). Carbon footprint of packaging films made from LDPE, PLA, and PLA/PBAT blends in South Korea. Sustainability, 10(7), 2369. DOI 10.3390/su10072369. [Google Scholar] [CrossRef]
109. Niaounakis, M. (2019). Recycling of biopolymersethe patent perspective. European Polymer Journal, 114, 464–475. DOI 10.1016/j.eurpolymj.2019.02.027. [Google Scholar] [CrossRef]
110. van Heek, J., Arning, K., Ziefle, M. (2017). Reduce, reuse, recycle: Acceptance of CO2-utilization for plastic products. Energy Policy, 105, 53–66. DOI 10.1016/j.enpol.2017.02.016. [Google Scholar] [CrossRef]
111. Zhou, X., Li, M. Y., Wang, D., Fang, C. Q., Yu, R. E. et al. (2022). The construction of pyramid structure of micro aluminum oxide. Ceramics International, 48(6), 8733–8739. DOI 10.1016/j.enpol.2017.02.016. [Google Scholar] [CrossRef]
112. Algozeeb, W. A., Savas, P. E., Yuan, Z., Wang, Z., Kittrell, C. et al. (2022). Plastic waste product captures carbon dioxide in nanometer pores. ACS Nano, 16(5), 7284–7290. DOI 10.1021/acsnano.2c00955. [Google Scholar] [CrossRef]
113. Liu, C., Gallagher, J. J., Sakimoto, K. K., Nichols, E. M., Chang, C. J. et al. (2015). Nanowire–bacteria hybrids for unassisted solar carbon dioxide fixation to value-added chemicals. Nano Letters, 15(5), 3634–3639. DOI 10.1021/acsnano.2c00955. [Google Scholar] [CrossRef]
114. Kornienko, N., Zhang, J. Z., Sakimoto, K. K., Yang, P., Reisner, E. (2018). Interfacing nature’s catalytic machinery with synthetic materials for semi-artificial photosynthesis. Nature Nanotechnology, 13(10), 890–899. DOI 10.1038/s41565-018-0251-7. [Google Scholar] [CrossRef]
115. Cestellos-Blanco, S., Zhang, H., Kim, J. M., Shen, Y., Yang, P. (2020). Photosynthetic semiconductor biohybrids for solar-drivenbiocatalysis. Nature Catalysis, 3, 245–255. DOI 10.1038/s41929-020-0428-y. [Google Scholar] [CrossRef]
116. Bui, M., Adjiman, C. S., Bardow, A., Anthony, E. J., Boston, A. (2018). Carbon capture and storage (CCSThe way forward. Energy & Environmental Science, 11(5), 1062–1176. DOI 10.1039/C7EE02342A. [Google Scholar] [CrossRef]
117. MacDowell, N., Florin, N., Buchard, A., Hallett, J., Galindo, A. (2010). An overview of CO2 capture technologies. Energy & Environmental Science, 3(11), 1645–1669. DOI 10.1039/c004106h. [Google Scholar] [CrossRef]
118. Zhou, X., Hao, Y. Y., Li, Y. X., Peng, J. H., Wang, G. S. et al. (2022). MXenes: An emergent material for packaging platforms and looking beyond. Nano Select, 3(7), 1123–1147. DOI 10.1002/nano.202200023. [Google Scholar] [CrossRef]
119. Yuan, X., Lee, J. G., Yun, H., Deng, S., Kim, Y. J. (2020). Solving two environmental issues simultaneously: Waste polyethylene terephthalate plastic bottle-derived microporous carbons for capturing CO2. Chemical Engineering Journal, 397, 125350. DOI 10.1016/j.cej.2020.125350. [Google Scholar] [CrossRef]
120. Yuan, X., Li, S., Jeon, S., Deng, S., Zhao, L. et al. (2020). Valorization of waste polyethylene terephthalate plastic into N-doped microporous carbon for CO2 capture through a one-pot synthesis. Journal of Hazardous Materials, 399, 123010. DOI 10.1016/j.jhazmat.2020.123010. [Google Scholar] [CrossRef]
121. Wang, J. Y., Yuan, X. Z., Deng, S., Zeng, X. L., Yu, Z. et al. (2020). Waste polyethylene terephthalate (PET) plastics-derived activated carbon for CO2 capture: A route to a closed carbon loop. Green Chemistry, 22(20), 3836–3845. DOI 10.1039/d0gc01613f. [Google Scholar] [CrossRef]
122. Hepburn, C., Adlen, E., Beddington, J., Carter, E. A., Fuss, S. et al. (2019). The technological and economic prospects for CO2 utilization and removal. Nature, 575(7781), 87–97. DOI 10.1038/s41586-019-1681-6. [Google Scholar] [CrossRef]
123. Zheng, Y., Liu, H., Zhang, Y. (2020). Engineering heterostructured nanocatalysts for CO2 transformation reactions: Advances and perspectives. ChemSusChem, 13(23), 6090–6123. DOI 10.1002/cssc.202001290. [Google Scholar] [CrossRef]
124. von der Assen, N., Bardow, A. (2014). Life cycle assessment of polyols for polyurethane production using CO2 as feedstock: Insights from an industrial case study. Green Chemistry, 16(6), 3272–3280. DOI 10.1039/c4gc00513a. [Google Scholar] [CrossRef]
125. Yusuf, A., Giwa, A., Mohammed, E. O., Mohammed, O., Al Hajaj, A. et al. (2019). CO2 utilization from power plant: A comparative techno-economic assessment of soda ash production and scrubbing by monoethanolamine. Journal of Cleaner Production, 237, 117760. DOI 10.1016/j.jclepro.2019.117760. [Google Scholar] [CrossRef]
126. Cai, T., Sun, H. B., Qiao, J., Zhu, L. L., Zhang, F. (2021). Cell-free chemoenzymatic starch synthesis from carbon dioxide. Science, 373(6562), 1523–1527. DOI 10.1126/science.abh4049. [Google Scholar] [CrossRef]
127. Kang, D., Byun, J., Han, J. (2021). Evaluating the environmental impacts of formic acid production from CO2: Catalytic hydrogenation vs. electrocatalytic reduction. Green Chemistry, 23(23), 9470–9478. DOI 10.1039/d1gc02997e. [Google Scholar] [CrossRef]
128. Zhou, X., Fang, C. Q., He, X. Y., Wang, Y. Z., Yang, J. et al. (2017). The morphology and structure of natural clays from Yangtze river and their interactions with polyurethane elastomer. Composites Part A, 96, 46–56. DOI 10.1016/j.compositesa.2017.02.009. [Google Scholar] [CrossRef]
129. Wang, J., Wang, F. N., Duan, H. M., Li, Y., Xu, J. M. et al. (2020). Polyvinyl chloride-derived carbon spheres for CO2 adsorption. ChemSusChem, 13(23), 6426–6432. DOI 10.1002/cssc.202002230. [Google Scholar] [CrossRef]
130. Zhou, X., Fang, C. Q., Lei, W. Q., Su, J., Li, L. et al. (2017). Thermal and crystalline properties of waterborne polyurethane by in situ water reaction process and their potential application as biomaterial. Progress in Organic Coatings, 104, 1–10. DOI 10.1016/j.porgcoat.2016.12.001. [Google Scholar] [CrossRef]
131. Zhou, X., Deng, J. R., Wang, D., Fang, C. Q., Song, R. F. et al. (2020). Growth of polypyrrole conductive and integrated hybrids with lysozyme nanolayer and the thermal properties. Composites Part A, 137, 105975. DOI 10.1016/j.compositesa.2020.105975. [Google Scholar] [CrossRef]
132. Wang, C. X., Zhou, X., Wang, G. S., Wang, D., Fang, C. Q. et al. (2022). Preparation of lysozyme/carbon nanotube hybrids and their interactions at the nano-bio interface. Progress in Organic Coatings, 163, 106659. DOI 10.1016/j.porgcoat.2021.106659. [Google Scholar] [CrossRef]
133. Ross, M. B., de Luna, P., Sargent, E. H. (2019). Designing materials for electrochemical carbon dioxide recycling. Nature Catalysis, 2(8), 648–658. DOI 10.1038/s41929-019-0306-7. [Google Scholar] [CrossRef]
134. Yoshida, S., Hiraga, K., Takehana, T., Taniguchi, I., Yamaji, H. et al. (2016). A bacterium that degrades and assimilates poly(ethylene terephthalate). Science, 351(6278), 1196–1199. DOI 10.1126/science.aad6359. [Google Scholar] [CrossRef]
135. Knott, B. C., Erickson, E., Allen, M. D., Beckham, G. T., McGeehan, J. E. et al. (2020). Characterization and engineering of a two-enzyme system for plastics depolymerization. PNAS, 117(41), 25476–25485. DOI 10.1073/pnas.2006753117. [Google Scholar] [CrossRef]
136. Uekert, T., DesVeaux, J. S., Singh, A., Lamers, P., Beckham, G. T. et al. (2022). Life cycle assessment of enzymatic poly(ethylene terephthalate) recycling. Green Chemistry, 24(17), 6531–6543. DOI 10.1039/D2GC02162E. [Google Scholar] [CrossRef]
137. Brizendine, R. K., Erickson, E., Haugen, S. J., McGeehan, J. E., Beckham, G. T. et al. (2022). Particle size reduction of poly(ethylene terephthalate) increases the rate of enzymatic depolymerization but does not increase the overall conversion extent. ACS Sustainable Chemistry & Engineering, 10(28), 9131–9140. DOI 10.1021/acssuschemeng.2c01961. [Google Scholar] [CrossRef]
138. Bell, E. L., Smithson, R., Kilbride, S., Foster, J., Green, A. P. et al. (2022). Directed evolution of an efficient and thermostable PET depolymerase. Nature Catalysis, 5(8), 673–681. DOI 10.1038/s41929-022-00821-3. [Google Scholar] [CrossRef]
Cite This Article
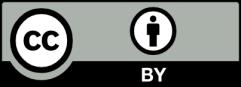
This work is licensed under a Creative Commons Attribution 4.0 International License , which permits unrestricted use, distribution, and reproduction in any medium, provided the original work is properly cited.