Open Access
ARTICLE
Selecting the Technology of Sodium Silicate Modified Poplar with the Highest Performance by Fuzzy Orthogonal Method
1
College of Materials Science and Engineering, Central South University of Forestry and Technology, Changsha, 410004, China
2
College of Furniture and Art Design, Central South University of Forestry and Technology, Changsha, 410004, China
* Corresponding Authors: Ping Li. Email: ; Yingfeng Zuo. Email:
Journal of Renewable Materials 2023, 11(5), 2399-2415. https://doi.org/10.32604/jrm.2023.026656
Received 18 September 2022; Accepted 28 November 2022; Issue published 13 February 2023
Abstract
Sodium silicate modification can improve the overall performance of wood. The modification process has a great influence on the properties of modified wood. In this study, a new method was introduced to analyze the wood modification process, and the properties of modified wood were studied. Poplar wood was modified with sodium silicate by vacuum-pressure impregnation. After screening using single-factor experiments, an orthogonal experiment was carried out with solution concentration, impregnation time, impregnation pressure, and the cycle times as experimental factors. The modified poplar with the best properties was selected by fuzzy mathematics and characterized by SEM, FT-IR, XRD and TG. The results showed that some lignin and hemicellulose were removed from the wood due to the alkaline action of sodium silicate, and the orderly crystal area of poplar became disorderly, resulting in the reduction of crystallinity of the modified poplar wood. FT-IR analysis showed that sodium silicate was hydrolyzed to form polysilicic acid in wood, and structural analysis revealed the formation of Si-O-Si and Si-O-C, indicating that sodium silicate reacted with fibers on the wood cell wall. TG-DTG curves showed that the final residual mass of modified poplar wood increased from 25% to 67%, and the temperature of the maximum loss rate decreased from 343°C to 276°C. The heat release and smoke release of modified poplar wood decreased obviously. This kind of material with high strength and fire resistance can be used in the outdoor building and indoor furniture.Graphic Abstract
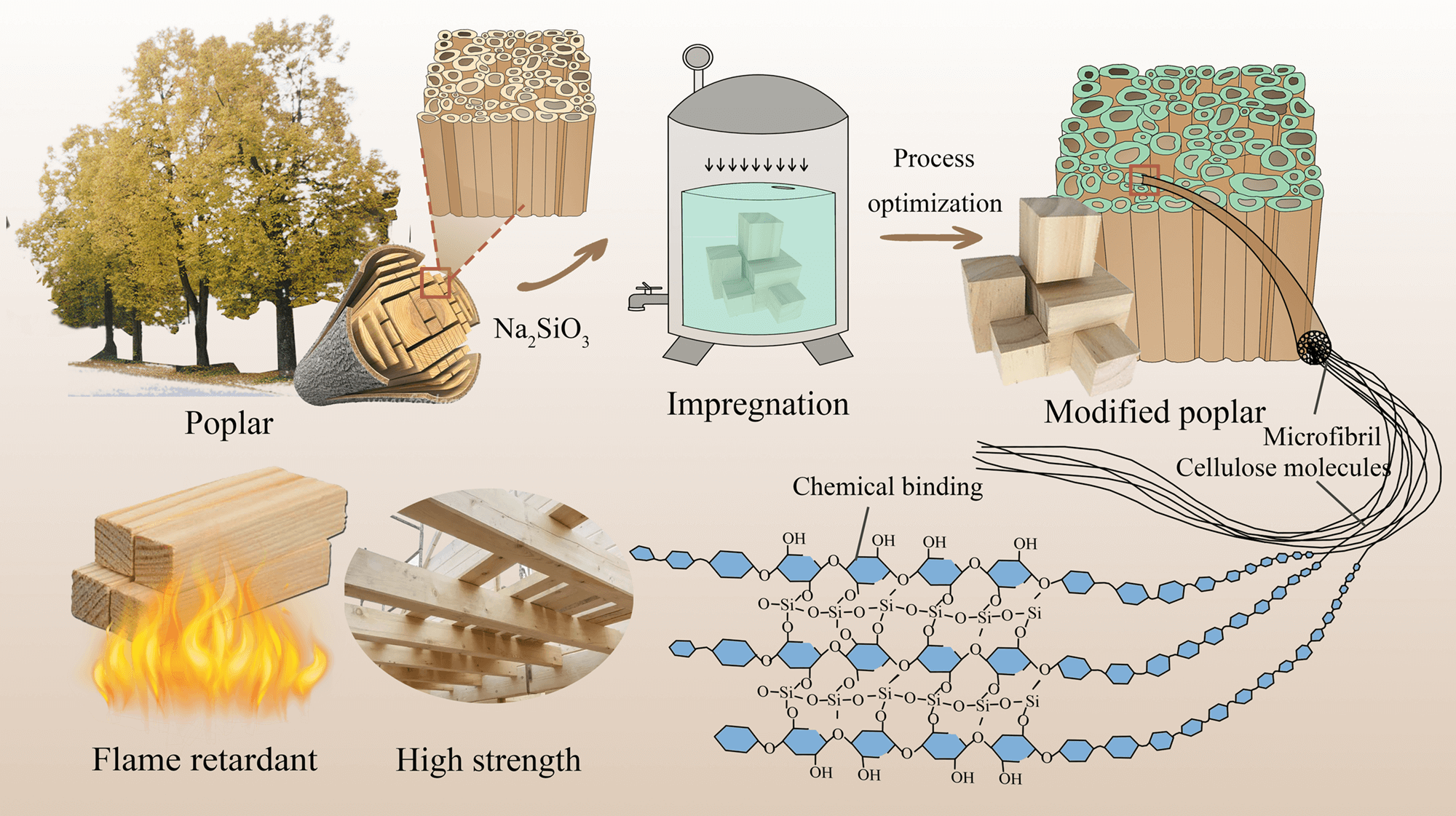
Keywords
The afforestation area in China has exceeded 6.7 × 106 hm2, the largest in the world [1]. Poplar has characteristics of fast growth, strong adaptability, easy processing and management. It is suitable for afforestation and positively impacts the ecological environment [2,3]. However, soft texture, poor dimensional stability, flammability, and perishable limit its use [4,5].
Wood modification can change the structure or composition of wood by physical, chemical or biological methods to enhance the overall properties of fast-growing wood for more efficient utilization. Silicate has a wide range of sources and is low-cost, non-toxic and harmless. Compared with other inorganic modifiers such as montmorillonite, water-soluble silicate solution is easily immersed into wood [6]. Silicon compounds, a soluble alkali silicate, are widely used in wood modification which is an environmentally friendly and low-cost inorganic modifier. It can improve the mechanical properties and flame retardancy of wood. [7–9]. Bao et al. impregnated poplar with sodium silicate and investigated its surface wettability and surface-free energy. Modification treatment created hydrophilic groups (e.g., hydrogen bonds, free hydroxyl groups) on the wood surface to improve the surface wettability and surface free energy of poplar wood [10]. Kuai et al. prepared densified wood with high strength and excellent dimensional stability by removing lignin with sodium silicate [7]. Liu et al. used heat treatment and impregnated sodium silicate solution to modify poplar wood and found that when the modulus of sodium silicate was 3.3, the dimensional stability of the poplar sample was highest, and the bending strength, elastic modulus, hardness and impact toughness of modified wood were significantly improved [11]. Nguyen et al. treated Poplar and radiata pine woods with an aqueous solution containing styrene-acrylic copolymer dispersion and sodium silicate. The bending strength, elasticity modulus, compressive strength, surface hardness, tensile strength, and shear strength of the composite modified wood were improved up to 83.9%, 82.3%, 72.7%, 48.3%, 38.4%, and 53.1%, respectively [12]. Kačíková et al. demonstrated that wood modifications using sodium silicate and nanoparticle systems have potentially enhanced flame retardant properties [13].
Different impregnation methods can alter the impregnation effect of sodium silicate [14]. With the appropriate modification method, the performance of fast-growing wood can be better than that of natural wood [15,16]. We used a new analytical method to optimize the modification process to obtain high-strength, flame retardant modified poplar. This work studied the effects of different sodium silicate impregnation processes on the properties of poplar wood and identified the most efficient impregnation process. Single-factor experiment, orthogonal experiment, and fuzzy mathematical analysis were used to explore the effects of different impregnation treatments on the main properties of poplar. The optimum technological conditions were used to prepare modified poplar wood with uniform impregnation, good mechanical properties, and good flame retardancy. The results of this work provide a theoretical basis for the optimization of technological parameters of poplar wood modification.
Fast-growing poplar (Populus tremula) was cultivated in Chenzhou, Hunan province. According to national standards, GB/T 1929-2009, GB/T 1931-2009, GB/T 1936.1-2009, and GB/T 1941-2009, samples were prepared 20 × 20 × 300 mm3 (R × T × L), 50 × 50 × 70 mm3 (R × T × L), 20 × 20 × 30 mm3 (R × T × L), or 20 × 20 × 20 mm3 (R × T × L) in size. The selected specimens were smooth, without decay or scarring. The modulus of the sodium silicate solution was 1.9, 2.5 and 3.4, the solid content was 42%, 44% and 46%, and the pH was 12. Silicate solution was purchased from Hunan Hetang Chemical Co., Ltd. (Changsha, China). Ultrapure water was prepared in the lab.
2.2 Preparation of Impregnated Modified Poplar Wood
For the preparation of impregnated wood, 10 pieces of each experimental material were selected, put into the impregnation tank (impregnation tank: 50 L, Changsha Juchuang Technology Co., Ltd., Changsha, China), and the vacuum was adjusted to −0.1 MPa and held for 30 min. The pressure in the impregnation tank was used to suck in the sodium silicate solution until the wood was completely immersed. After 5 min, the pressure relief valve was opened to slowly restore the pressure to normal pressure. The sodium silicate solution in the tank was discharged, and the experiment material was removed. The surface of the wood samples was cleaned with ultrapure water. After air-drying the surface of the samples, the samples were then aged for 24 h, put into an oven for gradient drying, and then put into a drying dish to cool to room temperature. The process flow chart is shown in Fig. 1.
Figure 1: Process flow of poplar modification
2.3 Single Factor Experiment and Orthogonal Experiment Design
The effects of sodium silicate modulus, sodium silicate concentration, impregnation pressure, impregnation time, and cycle times on the impregnation of poplar wood were investigated by single factor experiment. The factors and levels of the single-factor experiment were designed as follows: the sodium silicate modulus values were 1.9, 2.5 and 3.4; the sodium silicate concentrations were 10%, 20%, 30%, and 40%; the impregnation pressure values were 0.1, 0.3, 0.5, and 0.7 MPa; the impregnation times were 1, 2, 3, and 4 h; and the number of cycles was 2, 4, 6, and 8. On the basis of single-factor experiments, sodium silicate concentration (A), impregnation time (B), impregnation pressure (C), and cycle times (D) were screened for the orthogonal experiment. An experimental table of four factors and four levels of L16(45) was used to optimize the process of sodium silicate modification of poplar wood, as shown in Table 1.
2.4 Properties and Characterization
2.4.1 Weight Percentage Gain (WPG)
The experiment materials before and after modification were put into a drying oven at 103°C ± 2°C, dried to absolute drying, and then the absolute dry mass of untreated poplar wood Wc and modified poplar wood WT were obtained. The calculation using Eq. (1), as
WPG=WT−WCWC×100% (1)
Wood hardness was measured according to national standard GB/T 1941-2009, “Wood hardness experimental method.” The pressing speed was 3~5 mm/min uniform speed, the pressing depth was 5.64 mm, and the load reading was accurate to 10 N.
Wood bending strength was measured according to national standard GB/T1936-2009, “Wood flexural strength experimental method.” Briefly, the specimen size was 300 × 20 × 20 mm3, the indenter and bearing radius of curvature were 30 mm, and the distance between supports was 240 mm.
Wood along grain compressive strength was measured according to national standard GB/T1935-2009, “Wood along grain compressive strength experiment method.” Briefly, the specimen size was 30 × 20 × 20 mm3, with the length along the grain direction, uniform speed loading was used, and sample failure time was 1.5~2.0 min.
2.4.3 Fourier Transforms Infrared (FT-IR) Spectroscopic Analysis
Samples of poplar wood were put into a wood mill and pulverized, and particles less than 0.074 mm in diameter were collected. The wood particles were evaluated using a Bruker Vertex 70 FT-IR spectrophotometer (FT-IR, Bruker Corp., Billerica, MA, USA) using an infrared spectrum that ranged from 400 to 4000 cm−1.
2.4.4 X-Ray Diffraction (XRD) Analysis
The crystallinity index of the samples was measured by X-ray diffractometer at a voltage of 36 kV and a current of 20 mA. The angle 2 θ of the sample ranged from 5° to 40°, with a scanning speed of 4° per minute. The calculation formula of crystallinity was as Eq. (2) [17]:
Crl=I002−IamorphI002×100% (2)
where I002 is the maximum diffraction peak intensity of the main crystallization peak 002 (a.u.). Iamorph is diffraction peak intensity at 2 θ angle of 18° (a.u.) and Crl is crystallinity (%).
2.4.5 Scanning Electron Microscopy (SEM)
After gold spraying treatment, standard samples of poplar were fixed on the platform with conductive adhesive. The end face and longitudinal face of poplar were scanned and observed using a scanning electron microscope (FEI Quanta 200) at a voltage of 20 kV.
2.4.6 Thermal Gravimetric Analysis (TGA)
An appropriate amount of wood powder was put into a micro crucible and tested with a 209 F3 TGA (Netzsch Instruments North America, Burlington, MA, USA). The experimental conditions were air atmosphere and heating from room temperature to 750°C at a heating rate of 10 °C/min.
3.1 Single Factor Experiment Process Analysis
Fig. 2 shows the effect of sodium silicate modulus and sodium silicate concentration on modified poplar. Figs. 2a and 2d show that the WPG increase with the increase of the modulus and concentration of sodium silicate within the experimental range. Sodium silicate hydrolyzed in water generated NaOH and H2SiO3 precipitation. The larger the modulus of sodium silicate, the higher the concentration of sodium silicate, the higher the SiO2 content in sodium silicate solution, and the more H2SiO3 can be fixed in wood. Therefore, the WPG of modified poplar wood was positively correlated with the modulus and concentration of sodium silicate. At higher concentration of sodium silicate, the trend of increasing WPG slowed because the fluidity of the solution became worse after the increase of solid content, the permeability of the wood decreased, and there was greater resistance of sodium silicate into the wood. At the same time, the increase of WPG increased the density of wood, so the resistance of wood to external stress increased, and some mechanical properties were further enhanced. As shown in Figs. 2b–2f, the compressive strength and hardness of the modified poplar wood increased with the increase of modulus and concentration. However, the larger the sodium silicate modulus, the harder it is to dissolve the solid sodium silicate in water and the larger its molecular volume. The modulus of sodium silicate is generally between 1.5 and 3.5, so 3.4 was used as the maximum value in this experiment.
Figure 2: Effects of modulus and concentration of sodium silicate on properties of modified wood. (a) Effect of sodium silicate modulus on WPG, (b) Effect of sodium silicate modulus on bending strength and compressive strength, (c) Effect of sodium silicate modulus on hardness, (d) Effect of sodium silicate concentration on WPG, (e) Effect of sodium silicate concentration on bending strength and compressive strength, (f) Effect of sodium silicate concentration on hardness
Alkaline substances in sodium silicate solution will decompose poplar cellulose, hemicellulose and other components, which will affect the bending strength of modified poplar wood [18]. The larger the modulus of sodium silicate is, the less the content of NaOH is, the weaker the alkalinity is, and the smaller the damage degree to wood components is. Therefore, the greater the modulus, the greater the integrity of cellulose chain in wood, the greater the mutual restriction between wood fibers, and the higher the bending strength of the modified wood. Fig. 2e shows that the bending strength of modified wood continuously decreased with the increase of solution concentration. This is because when the concentration of sodium silicate solution was large, the alkalinity is enhanced, the decomposition ability of wood components was improved, and the cellulose molecular chain was disintegrated. When external pressure generated, the cellulose chain was difficult to slip and directly break. The effect of sodium silicate concentration on the property enhancement trend of the modified poplar wood was comprehensively analyzed. The optimum solution concentration was 40%.
Fig. 3 shows the effects of impregnation pressure, impregnation time, and cycle times on the properties of modified poplar wood, as seen from panels Figs. 3a and 3d, the WPG of the modified wood increased with the increase of impregnation pressure and impregnation time. Because wood is a porous material, the greater the external power provided, the more easily sodium silicate can soak into the wood. When the impregnation pressure increased from 0.5 to 0.7 MPa, the external force was no longer the main factor affecting the modification effect, and the increasing trend of WPG slowed. Fig. 3d shows that the increasing trend of WPG of modified poplar decreased after soaking for more than 3 h, indicating that the poplar wood was nearly saturated after soaking for about 3 h, so the WPG of poplar was not affected by further soaking time.
Figure 3: The effects of impregnation pressure, impregnation time, and cycle times on the properties of modified wood. (a) Effect of impregnation pressure on WPG, (b) Effect of impregnation pressure on bending strength and compressive strength, (c) Effect of impregnation pressure on hardness, (d) Effect of impregnation time on WPG, (e) Effect of impregnation time on bending strength and compressive strength, (f) Effect of impregnation time on hardness, (g) Effect of cycle times on WPG, (h) Effect of cycle times on bending strength and compressive strength, (i) Effect of cycle times on hardness
Figs. 3b–3f show that the compressive strength and hardness of the modified poplar wood also increased with the increase of impregnation pressure and impregnation time, indicating that the greater the pressure and the longer the time, the more chemicals entered the wood. Sodium silicate filled into the weak structure of wood, and played a supporting and reinforcing role in enhancing the mechanical strength of poplar. However, Figs. 3b and 3c show that the bending strength of modified poplar decreased with the increase of impregnation pressure and impregnation time. When more sodium silicate solution entered the wood, alkalinity increased the damage of wood fiber. With the increased decomposition time of cellulose and hemicellulose in alkaline environment, the integrity of cellulose chain decreased, resulting in the reduction of wood toughness. Comprehensive analysis showed that the optimal impregnation pressure was 0.5 MPa and the optimal impregnation time was 3 h.
Next, the effects of different cycle times were tested. Poplar wood was modified by the vacuum-pressure impregnation method. The WPG, bending strength, compressive strength, and hardness of the modified poplar wood was tested after different cycle times and the results are shown in Figs. 3g–3i. As can be seen from the figure, with the increase of the cycle times, except for bending strength, the other properties first increased and then decreased. The results showed that the appropriate adjustment of cycle times could enhance the permeability of wood, improve the impregnation rate, and improve the mechanical properties, but the effective impregnation time of wood was shortened with more cycles, altering the effect of the modification. The results show that four cycles gave the best modification effect.
The results of the single-factor experiments identified the optimal parameters for best modification effects as follows: impregnation time of 3 h, impregnation pressure of 0.5 MPa, modulus of sodium silicate of 3.4, 40% concentration of sodium silicate, and four cycles.
3.2 Optimization Results and Analysis of Fuzzy Orthogonal Process
3.2.1 Results and Analysis of Orthogonal Experiment Design
The results of the single factor test show that when the modulus of sodium silicate was 3.4, the effect was the best. Since the modulus values of sodium silicate range between 1.5 and 3.5, the modulus of sodium silicate was not varied in the orthogonal experiment. The orthogonal experiment was carried out with factors of sodium silicate concentration (A), impregnation time (B), impregnation pressure (C), and the cycle times (D). An orthogonal experiment table with four factors and four levels L16(45) was constructed and used to optimize the sodium silicate modification of poplar with WPG, bending strength, compressive strength and hardness as evaluation indexes. Tables 2 and 3 show the results of orthogonal design and analysis.
It can be seen from Tables 2 and 3 that the physical and mechanical properties of poplar modified by sodium silicate were improved to different degrees, with different effects of different factors. The factors affecting the WPG and radial hardness of the modified poplar wood were in the order of A > C > D > B, and the optimum combinations were A4C4B3D1 and A4C4D4B2, respectively. However, the order of influencing factors on bending strength, compressive strength, end hardness, and bastard hardness were A > C > B > D, with optimum combinations of A2B1C3D1, A4C4B4D3, A4C4B3D1 and A3C4D4B4, respectively. Overall, the results show that sodium silicate concentration and impregnation pressure have the greatest influence on the properties of modified poplar wood.
Orthogonal experiment can analyze the optimal process of multiple factors for one index, and fuzzy mathematics can be used to obtain the optimal process of multiple factors for multiple indexes. Firstly, each index value was fuzzified, and the precision of the index in the orthogonal experiment was mapped to a fuzzy subset and fuzzified. Then, the corresponding set of fuzzy membership degree was found by this transformation [19]: Take the experimental factors as the objects of evaluation, and let their set be X = {X1, X2, … , Xn}, where: X1 is the solution concentration, X2 is the impregnation time, X3 is the impregnation pressure, and X4 is the cycle times.
Let the set of evaluation indexes be U = {u1, u2, … , um}, where U1 is the weight gain rate, U2 is the bending strength, U3 is compressive strength, U4 is the end hardness, U5 is the radial hardness, U6 is the bastard hardness.
Let the judgment set be V = {v1, v2, … , vs}, where, the judgment set for the ith index ui of the Xj factor is Ri = (ri1, ri2, … , ris), Ri ϵ V, rij ϵ [0,1], so Ri is a fuzzy subset on V and represents the eigenvector of Xj. Therefore, for a single factor Xj, the judgment set of “m” index can be represented by a judgment matrix R:
R=[R1R2R3]=[r11r12…r1sr21r22…r2srm1rm2…rms]
where “rij” represents the membership degree of the ith index ui on the jth rating vi, i = 1, 2, … , m, j = 1, 2, … , s. This concretely represents the index value of fuzzification under a test condition. The horizontal mean of the observed index was transformed into the corresponding rij.
The results of the orthogonal experiment in Table 2 were converted into the degree of membership of the evaluation. The membership degree contained the contribution rate of a level test condition of a certain factor to an evaluation index, where the greater the value, the greater the contribution to the index. However, this contribution rate was fuzzy, so the horizontal mean value of each factor had to be calculated and then fuzzified. To do this, the ratio of the average value of each level in each factor to the sum of the level average values for the factor was determined. If the total contribution value of a factor to an index is T, then:
T=t1+t2+t3+t4
where t1, t2, t3, and t4 represent the average values of each level, and the evaluation membership degree ri can be calculated by the membership function uR:
uR=tiT
All calculation results are listed in Table 4.
Each evaluation object Xj in the table satisfies normalization for the evaluation subset of any evaluation index, that is: ∑&j=1rij=1 .
3.2.3 Fuzzy Comprehensive Evaluation
Fuzzy comprehensive evaluation is carried out in the space composed of the evaluation object including the experimental factor set X, the evaluation index set U, and the evaluation matrix R, that is, the evaluation space S, S = (X, U, R). R is in essence, a fuzzy relation between set U and set V, so we can consider R as a fuzzy converter that can map the fuzzy subset A on U to B on V, where A and B are the preimage and image of the mapping, respectively.
The comprehensive evaluation of the multi-factor experiment was composed of the comprehensive evaluation of each single factor, and the fuzzy comprehensive evaluation B of each factor was a fuzzy subset of V, so the evaluation result needs to be obtained by the synthesis operation of fuzzy matrix as Eq. (3):
B=A∘R (3)
The symbol “ ∘ ” in the formula is called the fuzzy matrix multiplication operator, and represents a synthesis operation. A is the weight vector of the evaluation index, and A ϵ U is a fuzzy subset on the evaluation index U, A = (a1, a2, … , am). B is the evaluation result vector, and B ϵ V is a fuzzy subset on the evaluation set V, B = (b1, b2, … , bs). The final conclusion of the evaluation was ranked in B to select the best.
When judging different factors, different converters R were used in the same judging space. Here, each element in comprehensive evaluation B was solved according to the fuzzy matrix multiplication rule, where bi was Eq. (4):
bi=maxmin(aj,rij)=f=1Vm(ajj=1Λsrij) (4)
Before the evaluation of impregnation process parameters, the weight vector A of index was established. The weight coefficient can be set according to different needs. The WPG directly reflects the filling effect. Modified poplar wood is usually used in furniture products, wooden handicrafts, and structural parts, so there may be higher requirements for load-bearing and elastic properties of the modified poplar wood. We determined the weight coefficients of the six indexes as a1 = 0.40, a2 = 0.26, a3 = 0.28, a4 = 0.20, a5 = 0.18, and a6 = 0.18. The weight vector A was used as the common criterion for each object, where A = (0.35, 0.29, 0.30, 0.20, 0.18, 0.18). The steps of comprehensive evaluation of each factor are shown using X1 (solution concentration) as an example:
The evaluation vectors of the four levels of solution concentration on the experiment indexes u1, u2, u3, u4, u5 and u6 were:
u1=(0.084,0.187,0.302,0.426)u2=(0.069,0.317,0.300,0.314)u3=(0.069,0.301,0.309,0.320)u4=(0.053,0.238,0.320,0.390)u5=(0.222,0.247,0.265,0.266)u6=(0.211,0.233,0.281,0.275)
Thereby forming a fuzzy evaluation matrix R1 for X1:
R1=[0.0840.1870.3020.4260.0690.3170.3000.3140.0690.3010.3090.3200.0530.2380.3200.3900.2220.2470.2650.2660.2110.2330.2810.275]
According to fuzzy evaluation Eqs. (3) and (4), it can be concluded that:
B1=(0.35,0.29,0.30,0.20,0.18,0.18)∘[0.0840.1870.3020.4260.0690.3170.3000.3140.0690.3010.3090.3200.0530.2380.3200.3900.2220.2470.2650.2660.2110.2330.2810.275]
= (0.18,0.30,0.302,0.35)
There, b1 = (0.35 Λ 0.084) V (0.29 Λ 0.069) V (0.30 Λ 0.069) V (0.20 Λ 0.053) V (0.18 Λ 0.222) V (0.18 Λ 0.211)
= 0.084 V 0.069 V 0.069 V 0.053 V 0.18 V 0.18 = 0.18
The results of normalized processing gave B1 = (0.159, 0.265, 0.267, 0.309).
According to the above calculation method, B2 = (0.254, 0.251, 0.245, 0.250), B3 = (0.231, 0.251, 0.258, 0.260), B4 = (0.254, 0.251, 0.248, 0.247). Because b14 > b13 > b12 > b11, b21 > b22 > b24 > b23, b34 > b33 > b32 > b31, b41 > b42 > b43 > b44, the best process of impregnation modification was the combination of A4B1C4D1 under the condition of integrating the overall properties of poplar.
3.3 Study on Performance Enhancement Mechanism of Modified Poplar
Figs. 4a and 4b show the electron microscopic images of the end face and longitudinal face of unmodified poplar wood. There were many voids in the poplar. This is because the wood is a porous material, and poplar wood has ducts and many voids, resulting in loose density and poor mechanical strength. Figs. 4c and 4d show the electron microscopic images of the end face and longitudinal face of modified poplar wood. The sodium silicate was evenly and closely filled in the wood ducts and cell cavities, which increased the density of the wood and improved its mechanical strength. In order to further prove the improvement of mechanical strength of modified poplar, we did tensile test, the results showed that the tensile strength increased from 90.80 to 118.30 MPa, and increased by 30.29%, as shown in Fig. 3e. Fig. 4f shows the XRD images of poplar modified by different processes and unmodified poplar. The crystallization peaks of each curve scanning angle 2 θ at 15.5° and 22.7° correspond to the (101) and (002) crystal surfaces of wood cellulose, respectively [20]. The results for the unmodified poplar wood revealed larger fluctuation and higher peak value, with smaller fluctuation for the modified poplar wood. The peak and trough of the modified poplar did not shift, indicating that the crystal type did not change. According to Eq. (2), the relative crystallinity of unmodified poplar wood was 61.70%. After modification, the relative crystallinity decreased to 44.69%, 43.87%, 47.25% and 42.85%, respectively. This change is because the pH value of sodium silicate solution applied in this experiment was between 13 and 14. The alkaline treatment damaged the original structure of wood, removing some of the hemicellulose and lignin and causing the original ordered lignin to become disordered. At the same time, sodium silicate disturbed the neatly arranged microfibers in the crystallization zone during penetration and curing, decreasing the relative crystallinity of the modified poplar wood. Since the strength of cured sodium silicate was high, the decrease of crystallinity did not lead to the decrease of mechanical strength of poplar wood [21].
Figure 4: Electron microscopic image, tensile test, XRD spectrum, FT-IR spectrum and EDS of poplar before and after modification. (a) Electron microscopic image of unmodified poplar end face, (b) Electron microscopic image of unmodified poplar longitudinal section, (c) Electron microscopic image of modified poplar end face, (d) Electron microscopic image of modified poplar longitudinal section, (e) Tensile test of poplar before and after modification, (f) XRD spectrum of poplar before and after modification, (g) FT-IR spectrum of poplar before and after modification, (h–k) Energy spectrum of the cross-sectional fille
Fig. 4g shows FT-IR spectra of modified and unmodified poplar wood. The C=O stretching vibration peak on acetyl and carboxyl groups distinguished the characteristics of hemicellulose from other components and appeared near 1739 cm−1 for the unmodified poplar wood. The C=O stretching vibration peak intensity of the modified poplar wood decreased, indicating decreased content of hemicellulose. Sodium silicate can hydrolyze the wood cell wall and destroy hemicellulose [22]. In addition, there were small changes in the vibration of the benzene ring framework on lignin at 1593 cm−1 and the C-H bending vibration of lignin at 1425 cm−1 in the modified poplar wood, indicating that sodium silicate had little influence on lignin [23]. The characteristic peak of Si-O-Si appeared at 460 cm−1, indicating formation of the polysilicic acid network structure by the hydrolysis of sodium silicate in wood [24]. Si-O-C structure appears near 1040 cm−1, indicating that sodium silicate reacted with some free hydroxyl groups on the wood cell wall, forming a close chemical bond and explaining the improvement of the overall mechanical strength of modified poplar [25]. Figs. 4h–4k are the energy spectrum of the cross-sectional filler. C elements was uniformly distributed in wood as a cell wall skeleton. Most Si elements were distributed in the poplar tube holes, and some were filled around the cell walls of parenchyma cells and ray cells. In Fig. 4k, Na elements were concentrated on the tube walls, indicating that sodium silicate was impregnated into the wood cell walls, which proved the above conclusion.
Wood is a combustible material, so there is a need to improve the fire resistance of modified poplar. The poplar modified by sodium silicate exhibited improved flame retardancy. Figs. 5a and 5b show the TG and DTG curves of modified and unmodified poplar wood. From the TG curve, we can see that the trend of the two curves is basically the same. The poplar wood before and after the modification at 50°C~140°C began to lose weight, but the rate of weight loss was very small. This was because the water in the wood was constantly evaporating at this time, and the loss was water mass. Poplar at 140°C~200°C showed almost no mass loss, and at this stage the wood surface began to carbonize into a glass melting state. At 200°C~350°C, the mass loss rates of the two kinds of wood decreased rapidly. During this period, cellulose and other components in the wood were rapidly pyrolyzed and decomposed into CH4, CO, and CO2, which were volatilized until only incombustible inorganic salt components remained [21].
Figure 5: Comparison of the flame-retardant effect of modified and unmodified poplar. (a) TG curves, (b) DTG curves, (c) Heat release rate, (d) Total heat release, (e) Smoke production rate, (f) Total smoke production
TG and DTG curves show that the thermal stability of the modified poplar was significantly improved. Compared with the unmodified poplar, the mass loss rate of the modified poplar was much slower. The final residual quality of the modified poplar wood increased from 25% for the unmodified poplar wood to 67%, an increase of 168%. The maximum loss rate temperature was also reduced from 343°C to 276°C. This shows that the immersion of sodium silicate destroyed the structure of wood, reduced the combustible matter, and shortened the time of wood burning. The sodium silicate treatment removed some hemicellulose and lignin and replaced them in the wood. The mass loss rate of modified poplar wood was reduced because the wood was fixed with non-combustible sodium silicate crystals. In addition, the chemical reaction between sodium silicate and wood changed the composition of wood, so the overall flammability was reduced. In Figs. 5c–5f, it can be seen that the heat release rate and smoke production rate of modified poplar decreased significantly, and the peaks decreased from 279.74 kW/m2 and 0.12 m2/s to 206.69 kW/m2 and 0.08 m2/s, respectively. The time of the peak also moved back and slowed the rate of combustion. At the same time, the total heat release and total smoke release also decreased significantly. It showed that the modified poplar had obvious flame retardancy and smoke suppression effect.
In this experiment, poplar wood was modified by vacuum-pressure impregnation with sodium silicate. After single factor screening, the optimum process parameters of a single index were determined by orthogonal experimental analysis. The optimum process parameters were determined under different factors of multiple indexes by the fuzzy mathematics method: 40% solution concentration, 1 h impregnation time, impregnation pressure of 0.7 MPa, and two cycles. Sodium silicate can evenly fill the vessels and cell lumen, remove part of hemicellulose and lignin, and make the orderly crystallization area became disorderly, resulting in the reduction of the crystallinity of modified poplar wood. Sodium silicate can hydrolyze in wood to form polysilicic acid, which combined with the fibers on the cell wall of poplar wood to form Si-O-Si and Si-O-C structures. The pyrolysis process before and after the modification of poplar wood was nearly the same, with faster pyrolysis of modified poplar wood. The final residual mass of the modified poplar wood was 168% higher than that of the unmodified poplar wood, the maximum loss rate was advanced from 343°C to 276°C, and the flame retardancy was significantly improved. This work optimized the process of poplar modified by sodium silicate, and the fuzzy mathematics method was used for the analysis of orthogonal results to more easily determine the optimal parameters, which provided a new idea for future research.
Funding Statement: This work was financially supported by National Natural Science Foundation of China (32201485), Natural Science Foundation of Hunan Province, China (2022JJ40863), Scientific Research Project of Hunan Provincial Education Department, China (21B0238) and The Science and Technology Innovation Program of Hunan Province (2021RC4062).
Conflicts of Interest: The authors declare that they have no conflicts of interest to report regarding the present study.
References
1. Liu, S. Q., Bao, F. C. (1999). Current situation and development trends of research on wood properties, processing & utilization of poplar plantation in China. Chinese Journal of Wood Science and Technology, 13(3), 14–16. DOI 10.19455/j.mcgy.1999.03.004. [Google Scholar] [CrossRef]
2. Yue, K., Cheng, X. C., Wang, L. L., Chen, W. D., Wan, L. et al. (2016). Effect of modification on mechanical property and fire-retardant behavior of fast-growing poplar wood. Journal of Combustion Science and Technology, 22(4), 426–432. DOI 10.11715/rskxjs.R201509013. [Google Scholar] [CrossRef]
3. Yue, K., Chen, Q., Jia, C., Cheng, X. C., Tang, L. et al. (2018). Mechanical properties of industrial heat-treated wood. Journal of Fujian Agriculture and Forestry University (Natural Science Edition), 47(3), 361–366. DOI 10.13323/j.cnki.j.fafu(nat.sci.). 2018.03.015. [Google Scholar] [CrossRef]
4. Liu, Y. X., Zhao, G. J. (2010). Wood science. Beijing, China: China Forestry Publishing House. [Google Scholar]
5. Dong, Y. M., Liu, X. Y., Liu, R. H., Wang, W., Li, J. Z. (2020). Research progress and development trend of wood chemical cross-linking modification. China Forest Products Industry, 57(11), 10–14. DOI 10.19531/j.issn1001-5299.202011003. [Google Scholar] [CrossRef]
6. Furuno, T., Aono, S., Uehara, T. (1996). Mechanical properties of wood-mineral composites using the water glass-boron compound system. Journal of the Society of Materials Science Japan, 45(6), 687–693. DOI 10.2472/jsms.45.687. [Google Scholar] [CrossRef]
7. Kuai, B. B., Wang, Z. H., Gao, J. S., Tong, J. W., Zhan, T. Y. et al. (2022). Development of densified wood with high strength and excellent dimensional stability by impregnating delignified poplar by sodium silicate. Construction and Building Materials, 344(18), 128282. DOI 10.1016/j.conbuildmat.2022.128282. [Google Scholar] [CrossRef]
8. Pfeffer, A., Mai, C., Militz, H. (2012). Weathering characteristics of wood treated with water glass, siloxane or DMDHEU. European Journal of Wood and Wood Products, 70(1–3), 165–176. DOI 10.1007/s00107-011-0520-8. [Google Scholar] [CrossRef]
9. Liu, Q. Q., Du, H. J., Lyu, W. H. (2021). Physical and mechanical properties of poplar wood modified by glucose-urea-melamine resin/sodium silicate compound. Forests, 12(2), 127. DOI 10.3390/f12020127. [Google Scholar] [CrossRef]
10. Bao, X. D., Zhang, M. Y., Li, P., Lv, J. X., Yuan, G. M. et al. (2021). Investigating the surface wettability and surface free energy of sodium silicate-impregnated poplar wood. Wood Material Science & Engineering, 38(6), 1–10. DOI 10.1080/17480272.2021.1996454. [Google Scholar] [CrossRef]
11. Liu, M. L., Li, C. F., Liu, Y. L. (2019). Physical and mechanical properties of modified poplar wood by heat treatment and impregnation of sodium silicate solution. Wood Research, 64(1), 145–154. [Google Scholar]
12. Nguyen, T. T., Xiao, Z. F., Che, W. B., Trinh, H. M., Xie, Y. J. (2019). Effects of modification with a combination of styrene-acrylic copolymer dispersion and sodium silicate on the mechanical properties of wood. Journal of Wood Science, 65(1), 1–11. DOI 10.1186/s10086-019-1783-7. [Google Scholar] [CrossRef]
13. Kačíková, D., Kubovský, I., Eštoková, A., Kačík, F., Kmeťová, E. et al. (2021). The influence of nanoparticles on fire retardancy of pedunculate oak wood. Nanomaterials, 11(12), 3405. DOI 10.3390/nano11123405. [Google Scholar] [CrossRef]
14. He, L. H., Ma, L. F., Lin, P., Hu, T. Y., Ye, D. (2016). Principle and application of wood modification by microwave and vacuum impregnation. China Forest Products Industry, 43(11), 53–55. DOI 10.19531/j.issn1001-5299.2016.11.013. [Google Scholar] [CrossRef]
15. Chen, C., Cheng, R. X. (2014). Research progress in modified fast growing poplar wood. Forest Engineering, 30(5), 27–29. DOI 10.16270/j.cnki.slgc.2014.05.005. [Google Scholar] [CrossRef]
16. Wang, W. (2014). Fast-growing poplar wood modified with silica sol/VAE (Master’s Thesis). Central South University of Forestry and Technology, China. [Google Scholar]
17. Segal, L., Creely, J. J., Martin, A. E., Conrad, C. M. (1959). An empirical method for estimating the degree of crystallinity of native cellulose using the X-ray diffractometer. Textile Research Journal, 29(10), 786–794. DOI 10.1177/004051755902901003. [Google Scholar] [CrossRef]
18. Pan, X. Z., Bai, S., Liu, M. X., Li, C. F., Liu, Y. et al. (2020). Analysis on main components of poplar treated with sodium silicate. China Forest Products Industry, 57(10), 23–25. DOI 10.19531/j.issn1001-5299.202010005. [Google Scholar] [CrossRef]
19. Shen, B. X. (1989). Fuzzy comprehensive evaluation of the experimental design for the multi-target. Geomatics and Information Science of Wuhan University, 14(1), 57–65. [Google Scholar]
20. Toba, K., Yamamoto, H., Yoshida, M. (2013). Crystallization of cellulose microfibrils in wood cell wall by repeated dry-and-wet treatment, using X-ray diffraction technique. Cellulose, 20(2), 633–643. DOI 10.1007/s10570-012-9853-7. [Google Scholar] [CrossRef]
21. Zhou, Y., Li, P., Zhang, Y., Yuan, G. M., Wang, X. J. et al. (2020). Process optimization of sodium silicate reinforced Chinese fir wood based on respiratory impregnation. Materials Reports, 34(18), 18171–18176. DOI 10.11896/cldb.19090068. [Google Scholar] [CrossRef]
22. Liao, H. (2009). Study on modifying populus wood by silicates (Master’s Thesis). Northeast Forestry University, China. [Google Scholar]
23. Huang, Y. G., Li, G. Y., Chu, F. X. (2019). In situ polymerization of 2-hydroxyethyl methacrylate (HEMA) and 3-(methacryloxy) propyltrimethoxysilane (MAPTES) in poplar cell wall to enhance its dimensional stability. Holzforschung, 73(5), 469–474. DOI 10.1515/hf-2018-0139. [Google Scholar] [CrossRef]
24. Deng, Y. X., Guan, P. F., Zuo, Y. F., Wu, Y. Q., Yuan, G. M. et al. (2021). Preparation and properties of PVA-sodium silicate hybrid modified poplar with interpenetrating and cross-linking structure. Materials Reports, 35(10), 10221–10226. DOI 10.11896/cldb.20040043. [Google Scholar] [CrossRef]
25. Guan, P. F., Li, P., Wu, Y. Q., Li, X. G., Yuan, G. M. et al. (2022). Comparative study on the properties of inorganic silicate and organic phenolic prepolymer modified poplar wood by vacuum cycle pressurization. Journal of Renewable Materials, 10(9), 2451–2463. DOI 10.32604/jrm.2022.020459. [Google Scholar] [CrossRef]
Cite This Article
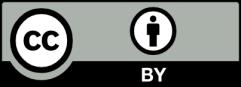
This work is licensed under a Creative Commons Attribution 4.0 International License , which permits unrestricted use, distribution, and reproduction in any medium, provided the original work is properly cited.