Open Access
ARTICLE
Hydration Characteristics and Mechanical Properties of Cement-Based Materials Modified by Calcined Zeolite and Montmorillonite
1
Faculty of Materials Science and Chemistry, Key Laboratory of Geological Survey and Evaluation of Ministry of Education, China
University of Geosciences, Wuhan, 430074, China
2
Key Laboratory of Advanced Building Materials of Anhui Province, Anhui Jianzhu University, Hefei, 230022, China
3
Guangxi Key Laboratory of New Energy and Building Energy Saving, Guilin University of Technology, Guilin, 541004, China
4
Key Laboratory of Road Structure and Materials of Ministry of Transport, Chang’an University, Xi’an, 710064, China
5
University of Southern Queensland, Centre for Sustainable Agricultural Systems, Toowoomba, QLD, 4350, Australia
6
State Key Laboratory of Silicate Materials for Architectures, Wuhan University of Technology, Wuhan, 430070, China
7
Key Laboratory for Green & Advanced Civil Engineering Materials and Application Technology of Hunan Province, College of Civil
Engineering, Hunan University, Changsha, 410082, China
* Corresponding Authors: Ping Duan. Email: ; Yingcan Zhu. Email:
Journal of Renewable Materials 2023, 11(5), 2191-2208. https://doi.org/10.32604/jrm.2023.025197
Received 27 June 2022; Accepted 02 September 2022; Issue published 13 February 2023
Abstract
Montmorillonite and clinoptilolite zeolite were used as representative materials to prepare calcined clay-cement binary cementitious materials in order to study the effect of calcination treatment on the activation of clay minerals and the activity difference between layered and framed clays in this research. The influence of different calcined clay content (2%, 4%, 6%, 8%, 10%) on the fluidity, compressive strength, microstructure, phase change, and hydration heat of cement-based materials were analyzed. The calcined clay improves the fluidity of cement-based materials as compared with the uncalcined group. The addition of calcined montmorillonite (CMT) improves the development of mechanical strength, and the optimal compressive strength reaches 85 MPa at 28 days with 8% CMT. However, the activity of calcined clinoptilolite zeolite (CZL) is weak with few reaction sites, which slightly reduced the mechanical strength as compared to the blank sample. The addition of CMT changes the microscopic morphology of hydration products such as C-S-H and C-A-H, leading to the formation and transformation of ettringite in the early stage. It promotes the gradual polymerization of Si-O bonds into SiO-Si bonds simultaneously, which accelerates the early hydration process. However, CZL acts mainly as a filling function in the cementitious system. In brief, CMT as an admixture can improve the mechanical properties of cement, but CZL has little effect. This work provides a guideline for the applications of calcined clay in cement, considering the influence of clay type on workability and mechanical strength.Graphic Abstract
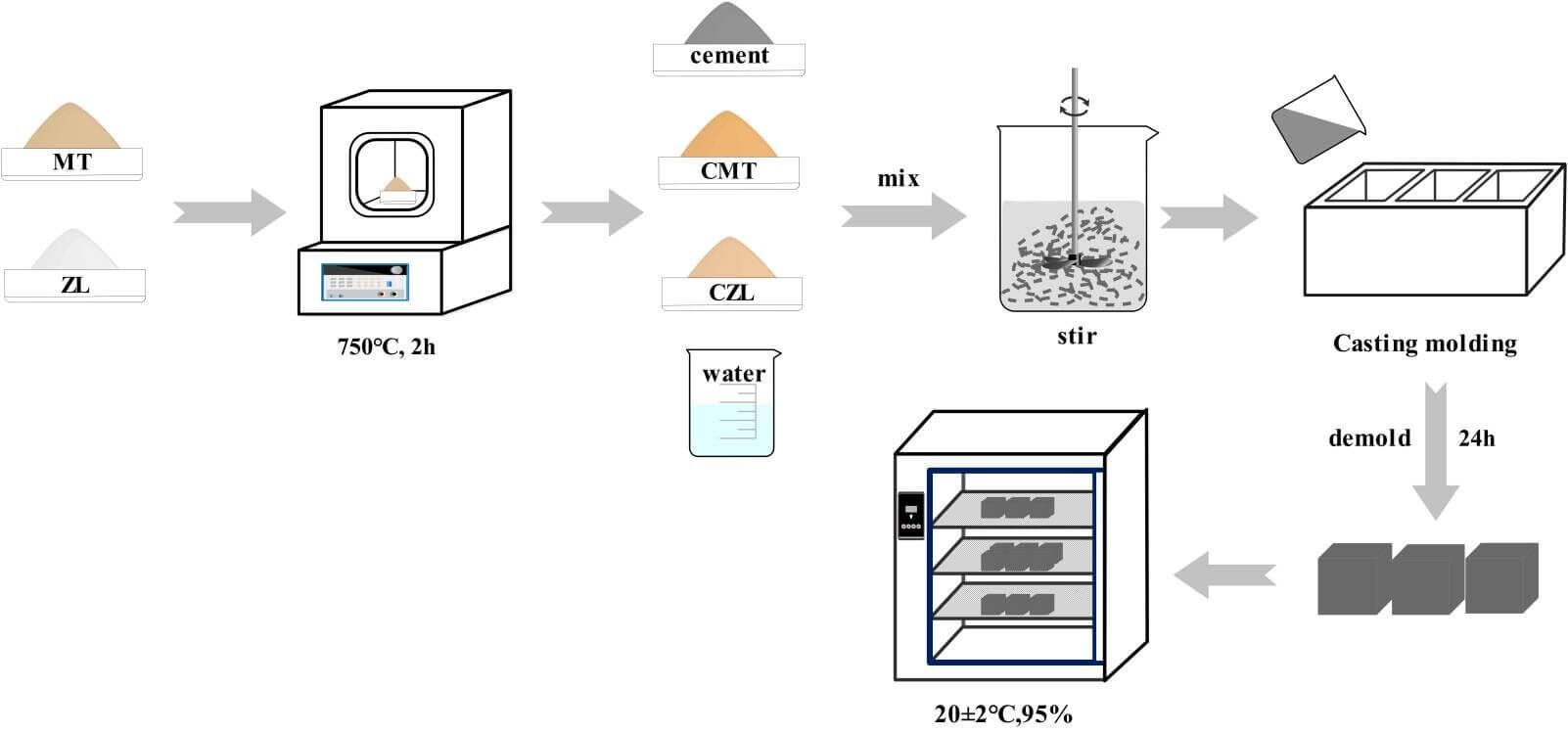
Keywords
Cement is the most widely used building material with the highest output because of its low cost and mature production technology. However, due to the demand for production technology, a large amount of carbon dioxide is emitted during cement production. Each ton of Portland cement clinker will emit about 0.8 tons of CO2, and the carbon emissions of the cement production industry account for about 5%–7% of greenhouse gases [1,2]. In order to reduce the carbon emissions in the production process, the following methods can be adopted to find environmentally friendly low-carbon cementitious materials. First and foremost is to modify the process during cement production and improve the energy utilization efficiency. What is more, using clean energy is one of the methods for cement production. Moreover, reducing the amount of cement clinker by adding supplementary cementitious materials can also decrease carbon emissions during cement production. The final method is to use the new low-carbon cementitious materials to replace traditional cement clinker. The path of adding supplementary cementitious materials to cement has made great progress in recent years.
Supplementary cementitious materials (SCMs) are siliceous, aluminum-siliceous, and calcium-aluminum-siliceous powders used as mixtures to partially replace Portland cement in concrete. Adding supplementary cementitious materials to concrete cannot only significantly reduce carbon dioxide emissions but also improve the mechanical properties and durability of concrete [3]. Clay mineral materials have more advantages as supplementary cementitious materials due to their wide distribution of raw materials, low price and easy availability, simple production process, and other factors [4]. For a long time, natural clay minerals have been regarded as inert components in cement systems, which is not contribute to the mechanics and durability of concrete [5]. Heat treatment is a common method to improve the activity of clay minerals. Calcination is a method of heating clay to a specific temperature in order to dehydroxylation. In dehydroxylated clay minerals, the bonding coordination number of aluminum atoms on octahedral plates decreases, making them more reactive. Kaolinite is commonly used as an alkali-activated clay mineral, which is also the supplementary cementitious material of concrete. After high-temperature calcination, the structure of metakaolin (MK) is no longer a repeating unit but more reactive, which has a wide range of applications in the fields of alkali excitation and auxiliary cementing materials [6,7]. Generally, the dehydroxylation of kaolinite occurs at a range of 650°C–700°C [8,9].
However, the cost of metakaolin is relatively high, and the calcination of other types of clay minerals is widely concerning. The dehydroxylation principle of montmorillonite and zeolite is similar to that of kaolinite. There have been studies on adding montmorillonite and zeolite as supplementary cementitious materials to cement. He et al. [10] studied the chemical solubility of untreated and calcined (730°C, 830°C, and 930°C) soda-lime montmorillonite before and after the reaction with Ca(OH)2 in simulated cement pore solution. It indicates that the montmorillonites are fairly good pozzolanic materials and calcination substantially improves their pozzolanic activity. Kaminskas et al. [11] used hexane extraction method and thermal extraction method to treat montmorillonite clay which is a waste product in the bleaching process, and its possibility as supplementary cementitious material for Portland cement has been discussed. Montmorillonite waste calcined at 600°C has good pozzolanic reaction. Its content can reach 15% without reducing the compressive strength of the sample. Alujas et al. [12] prepared geopolymer with 40% kaolin and 40% montmorillonite and found it played a pozzolanic reaction, filling effect and promoting early cement hydration in the cementitious system. Elert et al. [13] found that the dissolution of expansive clay minerals in limestone treated with magnesium-rich lime was considerably limited. C-(A)-S-H phase formed and initially cemented clay particles in this reaction. Oh et al. [14] modified montmorillonite to study its dispersion in cement-based materials. The filling effect and nano-modified materials can improve the mechanical properties and durability of the specimens. Chen et al. [15] found that it was feasible to partially replace zeolite as cement. When the zeolite substitution rate is 5%, both the fluidity of the cementitious system and the strength increase significantly. However, the fluidity will decline when the addition rate of zeolite is over 5%. When the clay is calcined at 700°C–900°C, dehydroxylation occurs, and amorphous silicoaluminate is formed, which improves the pozzolanic activity [16]. Adding calcined clay into cement-based materials can not only reduce carbon emissions in cement production but also improve mechanical properties and durability due to its pozzolanic activity, which can lead to secondary hydration reaction [17,18]. Therefore, calcined clay has a wider application as supplementary cementitious material [19]. Clay can decompose at lower calcination temperatures and release less CO2, which can reduce carbon emissions [2,20]. The structure of montmorillonite and zeolite was destroyed after calcination, and the hydroxyl group was removed, which improved the activity in theory and could be used as cementitious materials.
At present, calcined clay has been studied widely as an admixture in cement. Adding calcined clay to cement as an admixture can not only reduce cement consumption, save energy, and reduce emissions but also improve the properties of the mixture due to its outstanding pozzolanic activity. It is found that there are few studies on 2:1 type minerals such as montmorillonite and frame minerals such as zeolite added in cement. Therefore, this paper takes montmorillonite and zeolite as representative materials to study the influence of mineral clay with different structures on hydration and mechanical properties of cement-based materials and explore the feasibility of montmorillonite and zeolite as supplementary cementitious materials.
Montmorillonite powder was derived from Kangtai Mineral Products Processing Plant, Lingshou County, Shijiazhuang, Hebei Province, with a white appearance. Zeolite was obtained from Shijiazhuang Lingshou Ou Meiya Mineral Products Co., Ltd. (China), which has a light green appearance. Both montmorillonite and zeolite were calcined in a muffle furnace at 750°C for 2 h to obtain the calcined montmorillonite (CMT) and calcined zeolite (CZL). The ordinary Portland cement (OPC) was supplied from Huaxin Cement Co., Ltd. (China), with a specific surface area of 336 m2/kg and a relative density of 3100 kg/m3. The chemical composition of the powder is shown in Table 1. The powder polycarboxylate superplasticizer used in the experiment was from Shanghai Chenqi Environmental Protection Raw Material Wholesale Factory. In addition, the Physicochemical properties of raw materials are shown in Fig. 1.
Figure 1: Physicochemical properties of raw materials: (a) Appearance of CMT; (b) Appearance of CZL; (c) SEM image of CMT; (d) SEM image of CZL; (e) Particle size distribution of OPC, CMT and CZL; (f) XRD result
2.2 Sample Preparation and Characterization
Calcined clay and cement are drily mixed according to the certain mix ratio in Table 2, and tap water is mixed evenly to prepare CMT-OPC and CZL-OPC binary cementitious material. To test the fluidity, the slurry was prepared by gradually increasing the content of calcined clay (1% to 5%) with a water-binder ratio of 0.29 and a 1% polycarboxylate superplasticizer. The flow test for specimen workability was carried out in accordance with ASTM standards [21]. The mixing slurry was injected into the truncated cone mold (upper diameter Φ36 mm, lower diameter Φ60 mm, and height 60 mm). The truncated cone mold was raised, so the maximum diameter of the paste flowed on the glass plane was measured to represent the fluidity. An isothermal calorimeter (TA/TAMAIR-8) was used to test the hydration heat evolution of the cementitious system at 25°C. Ten grams of the slurry were extracted into a sealed bottle and placed in an inside isothermal calorimeter to measure the heat release response according to ASTM C305 standard.
Then the fresh paste was cast into 40 mm × 40 mm × 40 mm molds and vibrated for 30 s. All test specimens were cured at 25°C for 24 h and demolded. The samples were then placed in a standard curing chamber at 25°C and 95% relative humidity for 3, 7, and 28 days, respectively. The sample preparation process is shown in Fig. 2. It is noteworthy that curing is an important factor for specimen mechanical strength development. In order to better observe the phase change of calcined clay in cement, 20% calcined clay CMT/CZL was added for XRD analysis.
Figure 2: Specimen preparation process
The mechanical properties of samples were tested at 3, 7, and 28 days. The test specimen of 40 mm × 40 mm × 40 mm was placed in the center of the universal testing machine’s press plate (YAW4605), with a loading rate of 5 kN/min. Each measurement was repeated three times, and their mean value was reported. After the compressive tests, the broken pieces were collected and hand-ground in an agate mortar for about 15 min with an appropriate amount of ethyl alcohol. The fine ground powder was then washed with distilled water several times to remove excess impurities. The powder was then filtered and dried. The morphology images of specimens were obtained by a Hitachi SU8000 (Japan) scanning electron microscope (SEM). To analyze hydration products, the dried powder samples were mixed with potassium bromide (1/100 mass ratio), pressed into sheets for Fourier transform infrared (FTIR), and used the analysis of Nicolet iS50 Fourier transform infrared spectroscopy. Spectral scanning was recorded in the range of 4000–450 cm−1. XRD patterns of 2θ = 5°∼70° were obtained to evaluate the crystalline phase of the samples.
The influence of calcined clay on the flow performance of cementitious materials was compared with uncalcined clay, as shown in Fig. 3a. When MT is added to the cement-based material, the fluidity of cement slurry is greatly reduced, even just 1% dosage. This is related to the high affinity of the polycarboxylate superplasticizer to the aluminum silicate layer in the MT structure (Fig. 3b). This affects the further dispersion of the polycarboxylate superplasticizer in the cementitious system, thereby greatly reducing the fluidity [22]. In the CMT-OPC system, the fluidity of the slurry decreases significantly as compared to the OPC system. However, as compared to the MT-OPC system, the fluidity of the CMT-OPC system is much higher. This can be attributed to the crystal structure of CMT after high-temperature calcination is destroyed, and its adsorption effect of polycarboxylate superplasticizer is greatly reduced [23]. Noted with the increase of CMT, the fluidity of cement slurry decreases.
Figure 3: (a) Flow properties of different calcined clays (b) Schematic diagram of adsorption of water-reducing agent between MT particle layers (c) crystal structure of ZL
The fluidity of the cementitious system mixed with 1% ZL/CZL is better than that of pure cement paste. Since zeolite maintains a three-dimensional shape before and after calcination, it is conducive to slurry fluidity. In addition, zeolite filled the gap between cement particles, which reduced the water requirement for filling the internal gap, and increased the water used to provide slurry fluidity. However, when the addition of ZL/CZL is over 1%, the fluidity of the slurry decreases to varying degrees. This may be the absorption of a water-reducing agent by the pore structure of the zeolite. As shown in Fig. 3c, in the calcination process of zeolite, adsorption water, pore water, and crystal water are removed successively, and the crystal structure will be destroyed. The holes formed after calcination will absorb water-reducing agents and water, thus reducing the fluidity. However, the adverse effect of CZL on fluidity is lower than that of ZL, which indicates that calcination has a great influence on zeolite structure. Natural zeolite has strong porosity and a large internal surface area, which has a great influence on workability. Studies have shown that natural zeolite, after calcination reduces zeolite porosity, thereby reducing viscosity and yield stress, while calcination also contributes to dehydroxylation of impurities present in zeolite and helps to reduce water demand [24].
Fig. 4a shows the compressive strength of the specimens with different CMT dosages at different ages. After curing for 3 days, the compressive strength of the sample mixed with calcinated montmorillonite is slightly lower than that of the blank group. Probably because CMT is less reactive than cement clinker, and it acts as an inert component in the early reaction [25]. After curing for 7 days, the compressive strength of the experimental group is almost the same as that of the blank group. After 28 days of curing, the maximum compressive strength of the specimen can reach 85 MPa when CMT content is 8%. It suggests that the addition of CMT can improve the later strength of cement-based materials.
Figure 4: Compressive strength of samples at different curing ages (a) CMT-OPC (b) CZL-OPC
The reasons why calcined montmorillonite clay can provide strength are as follows [26]: 1) Due to the small particle size of clay minerals, it has a filling effect that fills the pores of cement-based materials after hydration; 2) The crystal structure of CMT after calcination is destroyed and the pozzolanic reaction is increased. After 750°C calcination of montmorillonite, the hydroxyl group in the lamellar structure is removed, and the crystal structure is destroyed to obtain a pozzolanic reaction. In the presence of water, CMT reacts with free hydrated calcium hydroxide (CH) during OPC hydration [27]. This results in additional complementary cementitious compounds such as calcium silicate hydrate (C-S-H), calcium aluminate hydrate (C-A-H), and calcium and aluminum silicate hydrate (C-A-S-H) [28].
The compressive strength of CZL-OPC samples increases with the growth of curing age (Fig. 4b). This is similar to the findings of Kocak et al. [29]. This may be related to that zeolite raw material is mottled and impure, which contains a large number of stable mineral components as inert components in the system, making the performance of the CZL group inferior to that of the blank group on the whole [30]. However, with the further development of the hydration process in the later stage, the active component produced by calcined zeolite plays a supplementary role as cementing material to promote the further hydration reaction [31].
The microstructure of CMT in cement matrix can be observed by scanning electron microscopy and energy spectrum analysis. Although most of the CMT is covered by cement hydration products, CMT fillers can be identified from Figs. 5a, 5b of the circle shape and spectral component analysis. The lamellar CMT exists as fine particles in the hydration product, and no obvious aggregation phenomenon is found, but it is uniformly dispersed. As shown in Fig. 5d, the chemical composition of CMT is very similar to that of cement clinker through EDS analysis. The high pozzolanic reaction produced by CMT is related to that CMT consumes CH in the cement matrix to form a compact hydration product structure.
Figure 5: The SEM images of the CMT-OPC specimen and the role of CMT in matrix
As shown in Figs. 6a, 6b, the single particles of CZL are covered and surrounded by hydration products, and there is a small number of fine hydration products on the surface. The reason is that the introduction of CZL can provide additional reaction sites [32]. As shown in Fig. 6d, the chemical composition of CZL is similar to that of hydration products by energy spectrum [33].
Figure 6: The SEM images of the CZL-OPC specimen and the role of CZL in the matrix
In order to investigate the influence of CMT and CZL addition on hydration products in the cementitious system, the microscopic morphology of hydration products of the blank sample (A0), CMT 10% dosage (M10), and CZL 10% dosage (Z10) at different stages were analyzed. With the growth of curing time, all samples showed an evolutionary process from loose granular structure to dense network structure, which was similar to the traditional hydration process of OPC.
There were needle-like hydration products in A0 at 3 d (Fig. 7a), which were mainly calcium silicate hydrate (C-S-H) and a small amount of ettringite hydration products. In comparison, the hydration products of M10 and Z10 (Figs. 7d and 7g) at the same curing condition showed more network structure.
Figure 7: The SEM images of blank group (A0) at curing (a) 3 d (b) 7 d (c) 28 d, CMT 10% dosage (M10) group (d) 3 d (e) 7 d (f) 28 d, and CZL 10% dosage (Z10) group (g) 3 d (h) 7 d (i) 28 d
At 7 d, the hexagonal CH can be found in the microscopic morphology of A0 (Fig. 7b), and the disordered needle-like structure has largely disappeared, resulting in a more solidification and dense structure. However, no obvious hexagon CH was found in M10 and Z10 (Figs. 7e and 7h). This is because the addition of CMT and CZL can react with CH in cement hydration products to generate hydration products such as C-S-H [34].
After curing for 28 days, the tricalcium silicate in cement clinker has been substantially involved in the hydration process. All A0, M10, and Z10 (Figs. 7c, 7f, and 7i) groups showed compact structure. However, the OPC group showed a trend of local orientation after curing for 28 days, resulting in some cracks. The hydration products of the CMT group are denser and tend to be a whole. Because CMT consumes CH in the cement matrix, it generates more compact hydration products such as C-S-H [35]. The CZL group also tends to be a whole, but the transition region is more obvious, which explains the reason why the mechanical strength is lower than that of pure cement paste [10].
The hydration products with large particle sizes contribute to the strength development of the macroscopic matrix, and the less micro-crack in the matrix, the higher compressive strength is. Compared with the blank group, the microstructure of micro-hydration products of CMT in the experimental group was refined, with more C-S-H and other major hydration products, and its network structure was more compact with fewer micro-cracks [36]. This resulted in a significant improvement in compressive strength in the experimental group, which was confirmed in 28 days compressive strength data. Compared with the blank group, the microstructure of CZL hydration products in the experimental group was uniformly refined, but the transition region was more obvious. It explains why the strength of the experimental group declined compared with the blank group. The reasons are as follows: The crystal structure of zeolite used in the experiment is special, and the calcination temperature does not reach the excitation degree, so the volcanic ash reaction is low. And the amount of non-bridging oxygen in the zeolite is less, so the active sites provided to the matrix are less. Finally, the large particle size of raw material leads to a less prominent physical filling effect [11].
FTIR analysis can provide more information about the hydration products of cementitious systems. As shown in Fig. 8a, the absorption peak of C2S is about 999 cm−1, and the absorption peak of sulphoaluminate is about 1110 cm−1. The peak of sulphoaluminate disappears gradually with the hydration reaction (Fig. 8a), which is consistent with the mechanism of the cement hydration process. In the early hydration process, ettringite (AFt) is the main hydration product. The absorption peak corresponding to -OH in CH is about 3640 cm−1, the stretching vibration peak of H2O is about 3420 cm−1, and the bending vibration peak is about 1643 cm−1. In addition, ettringite also corresponds to asymmetric stretching vibration with absorption peak SO42− at about 1110 cm−1. During the progress of the hydration reaction, this peak gradually disappeared, which was due to the transformation of AFt to AFm in the later hydration process [37]. The absorption peaks of 900–1000 cm−1 and 874 cm−1 correspond to the stretching vibration of Si-O in silicate. The absorption peak at 1424 cm−1 corresponds to carbonate, which may be caused by the inevitable carbonization reaction during sample preparation or hydration.
Figure 8: IR spectra of hydration products (a) OPC (b) CMT-OPC (c) CZL-OPC
The introduction of CMT did not significantly affect hydration product types. As shown in Fig. 8b, with the increase of CMT dosage and the growth of curing age, the main change is that the absorption peak near 1110 cm−1 gradually disappears. It indicates that the introduction of CMT contributes to the generation of AFt in the early stage and the transformation in the later hydration process. When hydration reaction time and CMT dosage increase, the absorption peak of 900–1000 cm−1 tends to migrate to the high wave segment. That states Si-O bond gradually polymerized into a Si-O-Si bond from the side, and the degree of polymerization of the Si-O tetrahedron in C-S-H increased [37].
The introduction of CZL did not significantly affect the type of hydration products [38]. As shown in Fig. 8c, the absorption peak around 900–1000 cm−1 tends to migrate to the high wave segment with the increase in hydration reaction time and CZL dosage. This also indicates that the Si-O bond gradually polymerized to Si-O-Si bond, and the degree of polymerization of Si-O tetrahedron in C-S-H increased, which may also be affected by the existence of high polymerization Si-O-Si bond in CZL [39].
The mineral composition of the OPC includes tricalcium silicate (C3S), dicalcium silicate (C2S), tricalcium aluminate (C3A), tetra calcium aluminoferrite (C4AF), and other minerals (Fig. 9a). Gypsum and other components react with C3A and generate Ettringite (AFt) when they contact with water, while C3S and C2S react with water and generate CH, C-S-H gel, and other products. It is generally believed that the chemical reaction of C2S gradually becomes prominent after 28 days, and the matrix strength of the sample in the early stage is mainly affected by the C-S-H and generated by the hydration of C3S. The main crystal hydration products in the hydration process are AFt, hydrotalcite, CH, inert quartz (unreacted), and unreacted clinker. As the curing time increases, it can be found that the diffraction peak of hydration products such as CH becomes more obvious, while the diffraction peak of cement clinker components such as C3S gradually weakens. This indicates that the raw cement materials had been consumed in the hydration process, causing hydration products to increase, and ettringite (AFt) will be transformed into monohydrate calcium sulphoaluminate (AFm).
Figure 9: Phase analysis of hydration products (a) OPC (b) CMT-OPC (c) CZL-OPC
Fig. 9b shows the phase analysis of hydration products with different dosages of CMT after curing for 3, 7, and 28 days. The hydration products have negligible change after adding CMT, which is similar to the results of other calcined clay introduced into OPC [40]. However, the addition of CMT provides additional chemical active components such as SiO2 and Al2O3 [41]. In the highly alkaline environment, SiO2, Al2O3, and other hydration products will produce additional C-S-H, C-A-H, and other hydration products. And the CH had been consumed, promoting the reaction of cement clinker, which is beneficial to the strength development of the sample. In order to further characterize the hydration product composition of CMT-OPC, sample M20 with the CMT dosage of 20% was prepared in this test. From the phase analysis diagram of hydration products at different ages, no new crystal hydration products were generated. It can be concluded that the addition of CMT into cement is not changing the type of hydration products. But it can promote the early chemical reaction of OPC clinker due to the large consumption of CH and other components in the matrix [42]. A growing hump in the XRD patterns is observed with increasing dosage of CMT, which indicates that more hydration products with irregular network structures such as C-S-H gel are generated.
In order to further characterize the hydration product composition of CZL-OPC, sample Z20 with the zeolite dosage of 20% was prepared for this test. As CZL is introduced without adding new chemical components, the hydration products do not change significantly (Fig. 9c). It is similar to the results of other calcined clay minerals introduced into OPC [40], but there are inert components such as anhydrite. Studies have shown that feldspar minerals may form hydrotalcite minerals after carbonization when they are added to cement [43]. Combined with the previous analysis, the introduction of CZL provides SiO2, Al2O3, and other components, but its chemical reaction activity is not prominent.
3.6 The Heat of Hydration Analysis
The early hydration heat stage of the cement-based cementitious material system can be divided into 5 stages, among which the performance of acceleration and deceleration is always the focus. The hydration heat curves of CMT-OPC and CZL-OPC systems are similar to those of OPC systems (Fig. 10). The exothermic rate curve of hydration heat during the acceleration period is related to the formation of ettringite, C-S-H, and other hydration products by clinker reaction. With the increase in CMT dosage, the induction period is shortened, and the hydration peak in the acceleration period reaches earlier. That means the peak point in the acceleration period moves forward and is lower than that in the A0 group. These trends indicate that the increase of CMT content is helpful in accelerating the hydration rate of the cementitious system. This is because C-S-H and other hydration products can be extra generated on the surface of CMT, and active SiO2, Al2O3, and other components provided by CMT participate in the hydration process, making the system reach the reaction peak earlier. The results are similar to those of Kaminskas et al. [11], who suggested that the pozzolanic reaction of montmorillonite was not dependent on its calcination treatment. However, the addition of CMT reduces the clinker composition, and its heat release rate is diluted, resulting in a lower peak value. The addition of CMT will also play a filler effect and provide an additional shear effect. That increases the water-cement ratio of cement clinker, making the hydration void space larger, which is conducive to the precipitation of hydration products [17]. As shown in Fig. 10a, there is no acromion corresponding to aluminate salinization. At the later stage of the reaction, not all hydrates are in thermodynamic equilibrium.
Figure 10: Exothermic rate curve and cumulative heat release curve (a) CMT-OPC (b) CZL-OPC
However, with the increase in CZL dosage, the hydration peak in the acceleration phase will not reach the peak point earlier (Fig. 10b). These trends indicate that the increase of CZL content has no obvious effect on accelerating the hydration rate of the cementitious system [44]. However, CZL substitutes the same amount of cement, resulting in a slow heat release rate and lower peak value.
Cumulative heat release can reflect the hydration degree of the whole cementitious system. The cumulative heat release for all mixtures is generally higher in the first few hours but lower than blank group A0 after 16 h (Fig. 10a). In general, a lower clinker phase number leads to a reduction in cumulative heat, which is important in preventing the early cracking of concrete [45].
Due to the good pozzolanic reaction, CMT can promote the early hydration reaction, making the hydration peak arrive early. While its shoulder peak during the deceleration period is not obvious. But the addition of CZL has no obvious effect on the induction stage, the acceleration stage, and the deceleration stage [46]. In general, the addition of different calcined clay minerals reduces the hydration cumulative heat of the system.
Based on the results and analysis, the following conclusions can be drawn:
1. The calcined clay improves the fluidity of the cementing material system compared with that before calcination. When CMT is added to cement, the fluidity is lower than cement paste; only 1% of CZL can improve fluidity, and other content of CZL reduces the fluidity.
2. CMT helps the development of mechanical strength because of its excellent pozzolanic activity. The optimal compressive strength reaches 85 MPa at 28 days with 8% CMT. The Filling effect and the pozzolanic reaction of calcined clay improve the strength of the matrix. However, when zeolite is added to the matrix, the strength of the cement paste is almost equal to that of pure cement paste.
3. The addition of CMT improves the microstructure of hydration products such as C-S-H and C-A-H. And its addition accelerates the formation of AFt in the early stage and the transformation of the hydration process in the later stage. CZL provides additional reaction sites and increases the degree of polymerization of Si-O tetrahedrons in C-S-H. But the effect on the early hydration process was not obvious, and the cumulative heat release was lower than that of blank group A0 after 16 h.
Acknowledgement: We thank the Faculty of Materials Science and Chemistry, China University of Geosciences, Wuhan 430074, China for providing experimental conditions and funding for this research.
Funding Statement: The research presented in this paper was supported by National Natural Science Foundation of China (Grant No. 52272031), the Fundamental Research Funds for the Central Universities, China University of Geosciences (Wuhan), and the Opening Fund of Guangxi Key Laboratory of New Energy and Building Energy Saving (Grant No. 19-J-22-2), Key Research and Development Program of Hubei Province (Grant No. 2020BAB065), Key Research and Development Program of Jiangxi Province (Grant No. 20201BBG71011), Fundamental Research Funds for the Central Universities, CHD (Grant No. 300102211506), Opening Fund of Key Laboratory of Advanced Building Materials of Anhui Province (Grant No. JZCL001KF).
Conflicts of Interest: The authors declare that there are no known competing financial interests or personal relationships that may affect the work of this paper.
References
1. Valentini, L., Contessi, S., Dalconi, M. C., Zorzi, F., Garbin, E. (2018). Alkali-activated calcined smectite clay blended with waste calcium carbonate as a low-carbon binder. Journal of Cleaner Production, 184, 41–49. DOI 10.1016/j.jclepro.2018.02.249. [Google Scholar] [CrossRef]
2. Krishnan, S., Emmanuel, A. C., Bishnoi, S. (2019). Hydration and phase assemblage of ternary cements with calcined clay and limestone. Construction and Building Materials, 222, 64–72. DOI 10.1016/j.conbuildmat.2019.06.123. [Google Scholar] [CrossRef]
3. Juenger, M. C. G., Snellings, R., Bernal, S. A. (2019). Supplementary cementitious materials: New sources, characterization, and performance insights. Cement and Concrete Research, 122, 257–273. DOI 10.1016/j.cemconres.2019.05.008. [Google Scholar] [CrossRef]
4. Shubbar, A. A., Sadique, M., Kot, P., Atherton, W. (2019). Future of clay-based construction materials–A review. Construction and Building Materials, 210, 172–187. DOI 10.1016/j.conbuildmat.2019.03.206. [Google Scholar] [CrossRef]
5. Nehdi, M. L. (2014). Clay in cement-based materials: Critical overview of state-of-the-art. Construction and Building Materials, 51, 372–382. DOI 10.1016/j.conbuildmat.2013.10.059. [Google Scholar] [CrossRef]
6. Siddique, R., Klaus, J. (2009). Influence of metakaolin on the properties of mortar and concrete: A review. Applied Clay Science, 43(3–4), 392–400. DOI 10.1016/j.clay.2008.11.007. [Google Scholar] [CrossRef]
7. Tafraoui, A., Escadeillas, G., Vidal, T. (2016). Durability of the ultra high performances concrete containing metakaolin. Construction and Building Materials, 112, 980–987. DOI 10.1016/j.conbuildmat.2016.02.169. [Google Scholar] [CrossRef]
8. Sperinck, S., Raiteri, P., Marks, N., Wright, K. (2011). Dehydroxylation of kaolinite to metakaolin—A molecular dynamics study. Journal of Materials Chemistry, 21(7), 2118–2125. DOI 10.1039/C0JM01748E. [Google Scholar] [CrossRef]
9. Hu, L., He, Z. (2020). A fresh perspective on effect of metakaolin and limestone powder on sulfate resistance of cement-based materials. Construction and Building Materials, 262, 119–847. DOI 10.1016/j.conbuildmat.2020.119847. [Google Scholar] [CrossRef]
10. He, C., Makovicky, E., Osbaeck, B. (1996). Thermal treatment and pozzolanic activity of Na- and Ca-montmorillonite. Applied Clay Science, 10(5), 351–368. DOI 10.1016/0169-1317(95)00037-2. [Google Scholar] [CrossRef]
11. Kaminskas, R., Kubiliute, R., Prialgauskaite, B. (2020). Smectite clay waste as an additive for portland cement. Cement and Concrete Composites, 113, 103710. DOI 10.1016/j.cemconcomp.2020.103710. [Google Scholar] [CrossRef]
12. Alujas, A., Fernández, R., Quintana, R., Scrivener, K. L., Martirena, F. (2015). Pozzolanic reactivity of low grade kaolinitic clays: Influence of calcination temperature and impact of calcination products on OPC hydration. Applied Clay Science, 108, 94–101. DOI 10.1016/j.clay.2015.01.028. [Google Scholar] [CrossRef]
13. Elert, K., Azañón, J. M., Nieto, F. (2018). Smectite formation upon lime stabilization of expansive marls. Applied Clay Science, 158, 29–36. DOI 10.1016/j.clay.2018.03.014. [Google Scholar] [CrossRef]
14. Oh, J. A., Zhuge, Y., Araby, S., Wang, R., Yu, H. et al. (2021). Cement nanocomposites containing montmorillonite nanosheets modified with surfactants of various chain lengths. Cement and Concrete Composites, 116, 103894. DOI 10.1016/j.cemconcomp.2020.103894. [Google Scholar] [CrossRef]
15. Chen, J. J., Ng, P. L., Kwan, A. K. H., Li, L. G. (2019). Lowering cement content in mortar by adding superfine zeolite as cement replacement and optimizing mixture proportions. Journal of Cleaner Production, 210, 66–76. DOI 10.1016/j.jclepro.2018.11.007. [Google Scholar] [CrossRef]
16. Ayati, B., Newport, D., Wong, H., Cheeseman, C. (2022). Low-carbon cements: Potential for low-grade calcined clays to form supplementary cementitious materials. Cleaner Materials, 5, 100099. DOI 10.1016/j.clema.2022.100099. [Google Scholar] [CrossRef]
17. Lothenbach, B., Scrivener, K., Hooton, R. D. (2011). Supplementary cementitious materials. Cement and Concrete Research, 41(12), 1244–1256. DOI 10.1016/j.cemconres.2010.12.001. [Google Scholar] [CrossRef]
18. Brigatti, M. F., Galán, E., Theng, B. K. G. (2013). Structure and mineralogy of clay minerals. In: Handbook of clay science, pp. 21–81. Amsterdam: Elsevier. [Google Scholar]
19. Ouellet-Plamondon, C., Scherb, S., Koberl, M., Thienel, K. C. (2020). Acceleration of cement blended with calcined clays. Construction and Building Materials, 245. DOI 10.1016/j.conbuildmat.2020.118439. [Google Scholar] [CrossRef]
20. Imbabi, M. S., Carrigan, C., McKenna, S. (2012). Trends and developments in green cement and concrete technology. International Journal of Sustainable Built Environment, 1(2), 194–216. DOI 10.1016/j.ijsbe.2013.05.001. [Google Scholar] [CrossRef]
21. Li, R., Lei, L., Sui, T., Plank, J. (2021). Approaches to achieve fluidity retention in low-carbon calcined clay blended cements. Journal of Cleaner Production, 311, 127770. DOI 10.1016/j.jclepro.2021.127770. [Google Scholar] [CrossRef]
22. Chen, G., Lei, J., Du, Y., Du, X., Chen, X. (2018). A polycarboxylate as a superplasticizer for montmorillonite clay in cement: Adsorption and tolerance studies. Arabian Journal of Chemistry, 11(6), 747–755. DOI 10.1016/j.arabjc.2017.12.027. [Google Scholar] [CrossRef]
23. Zhao, H., Yang, Y., Zhou, D., Shu, X., Ran, Q. (2021). Molecular dynamic simulations of montmorillonite contact with polycarboxylate superplasticizer at solid-liquid interface. Materials Today Communications, 28, 102538. DOI 10.1016/j.mtcomm.2021.102538. [Google Scholar] [CrossRef]
24. Seraj, S., Ferron, R. D., Juenger, M. C. G. (2016). Calcining natural zeolites to improve their effect on cementitious mixture workability. Cement and Concrete Research, 85, 102–110. DOI 10.1016/j.cemconres.2016.04.002. [Google Scholar] [CrossRef]
25. Luraschi, P., Gimmi, T., Van Loon, L. R., Shafizadeh, A., Churakov, S. V. (2020). Evolution of HTO and 36Cl−diffusion through a reacting cement-clay interface (OPC paste-na montmorillonite) over a time of six years. Applied Geochemistry, 119, 104581. DOI 10.1016/j.apgeochem.2020.104581. [Google Scholar] [CrossRef]
26. Alani, S., Hassan, M. S., Jaber, A. A., Ali, I. M. (2020). Effects of elevated temperatures on strength and microstructure of mortar containing nano-calcined montmorillonite clay. Construction and Building Materials, 263, 120895. DOI 10.1016/j.conbuildmat.2020.120895. [Google Scholar] [CrossRef]
27. Papatzani, S., Badogiannis, E. G., Paine, K. (2018). The pozzolanic properties of inorganic and organomodified nano-montmorillonite dispersions. Construction and Building Materials, 167, 299–316. DOI 10.1016/j.conbuildmat.2018.01.123. [Google Scholar] [CrossRef]
28. Laidani, Z. E. A., Benabed, B., Abousnina, R., Gueddouda, M. K., Kadri, E. H. (2020). Experimental investigation on effects of calcined bentonite on fresh, strength and durability properties of sustainable self-compacting concrete. Construction and Building Materials, 230, 117062. DOI 10.1016/j.conbuildmat.2019.117062. [Google Scholar] [CrossRef]
29. Kocak, Y., Tascı, E., Kaya, U. (2013). The effect of using natural zeolite on the properties and hydration characteristics of blended cements. Construction and Building Materials, 47, 720–727. DOI 10.1016/j.conbuildmat.2013.05.033. [Google Scholar] [CrossRef]
30. Özen, S., Göncüoğlu, M. C., Liguori, B., de Gennaro, B., Cappelletti, P. et al. (2016). A comprehensive evaluation of sedimentary zeolites from Turkey as pozzolanic addition of cement-and lime-based binders. Construction and Building Materials, 105, 46–61. DOI 10.1016/j.conbuildmat.2015.12.055. [Google Scholar] [CrossRef]
31. Kaplan, G., Coskan, U., Benli, A., Bayraktar, O. Y., Kucukbaltacı, A. B. (2021). The impact of natural and calcined zeolites on the mechanical and durability characteristics of glass fiber reinforced cement composites. Construction and Building Materials, 311, 125–336. DOI 10.1016/j.conbuildmat.2021.125336. [Google Scholar] [CrossRef]
32. Florez, C., Restrepo-Baena, O., Tobon, J. I. (2021). Effects of calcination and milling pre-treatments on natural zeolites as a supplementary cementitious material. Construction and Building Materials, 310, 125–220. DOI 10.1016/j.conbuildmat.2021.125220. [Google Scholar] [CrossRef]
33. Uzal, B., Turanlı, L. (2012). Blended cements containing high volume of natural zeolites: Properties, hydration and paste microstructure. Cement and Concrete Composites, 34(1), 101–109. DOI 10.1016/j.cemconcomp.2011.08.009. [Google Scholar] [CrossRef]
34. Mohanty, S., Roy, N., Singh, S. P., Sihag, P. (2021). Strength and durability of flyash, GGBS and cement clinker stabilized dispersive soil. Cold Regions Science and Technology, 191, 103358. DOI 10.1016/j.coldregions.2021.103358. [Google Scholar] [CrossRef]
35. Perraki, T., Kontori, E., Tsivilis, S., Kakali, G. (2010). The effect of zeolite on the properties and hydration of blended cements. Cement and Concrete Composites, 32(2), 128–133. DOI 10.1016/j.cemconcomp.2009.10.004. [Google Scholar] [CrossRef]
36. Zhou, Y., Wang, Z., Zhu, Z., Chen, Y., Wu, K. et al. (2022). Influence of metakaolin and calcined montmorillonite on the hydration of calcium sulphoaluminate cement. Case Studies in Construction Materials, 16, e01104. DOI 10.1016/j.cscm.2022.e01104. [Google Scholar] [CrossRef]
37. Allahverdi, A., Maleki, A., Mahinroosta, M. (2018). Chemical activation of slag-blended portland cement. Journal of Building Engineering, 18, 76–83. DOI 10.1016/j.jobe.2018.03.004. [Google Scholar] [CrossRef]
38. Burris, L. E., Juenger, M. C. G. (2020). Effect of calcination on the reactivity of natural clinoptilolite zeolites used as supplementary cementitious materials. Construction and Building Materials, 258, 119988. DOI 10.1016/j.conbuildmat.2020.119988. [Google Scholar] [CrossRef]
39. Khandelwal, S., Rhee, K. Y. (2021). Effect of silane modified smectite clay on the hydration, intercalation of PCE superplasticizers, and mechanical strength of cement composites. Cement and Concrete Composites, 123, 104210. DOI 10.1016/j.cemconcomp.2021.104210. [Google Scholar] [CrossRef]
40. Wei, J., Gencturk, B. (2019). Hydration of ternary portland cement blends containing metakaolin and sodium bentonite. Cement and Concrete Research, 123, 105772. DOI 10.1016/j.cemconres.2019.05.017. [Google Scholar] [CrossRef]
41. Čėsnienė, J., Baltušnikas, A., Lukošiūtė, I., Brinkienė, K., Kalpokaitė-Dičkuvienė, R. (2018). Influence of organoclay structural characteristics on properties and hydration of cement pastes. Construction and Building Materials, 166, 59–71. DOI 10.1016/j.conbuildmat.2018.01.099. [Google Scholar] [CrossRef]
42. Borralleras, P., Segura, I., Aranda, M. A. G., Aguado, A. (2019). Influence of the polymer structure of polycarboxylate-based superplasticizers on the intercalation behaviour in montmorillonite clays. Construction and Building Materials, 220, 285–296. DOI 10.1016/j.conbuildmat.2019.06.014. [Google Scholar] [CrossRef]
43. Enríquez, E., Torres-Carrasco, M., Cabrera, M. J., Muñoz, D., Fernández, J. F. (2021). Towards more sustainable building based on modified portland cements through partial substitution by engineered feldspars. Construction and Building Materials, 269, 121334. DOI 10.1016/j.conbuildmat.2020.121334. [Google Scholar] [CrossRef]
44. Küçükyıldırım, E., Uzal, B. (2014). Characteristics of calcined natural zeolites for use in high-performance pozzolan blended cements. Construction and Building Materials, 73, 229–234. DOI 10.1016/j.conbuildmat.2014.09.081. [Google Scholar] [CrossRef]
45. Arora, A., Sant, G., Neithalath, N. (2016). Ternary blends containing slag and interground/blended limestone: Hydration, strength, and pore structure. Construction and Building Materials, 102, 113–124. DOI 10.1016/j.conbuildmat.2015.10.179. [Google Scholar] [CrossRef]
46. Tydlitát, V., Zákoutský, J., Černý, R. (2014). Early-stage hydration heat development in blended cements containing natural zeolite studied by isothermal calorimetry. Thermochimica Acta, 582, 53–58. DOI 10.1016/j.tca.2014.03.003. [Google Scholar] [CrossRef]
Cite This Article
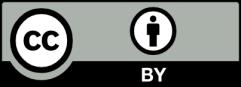
This work is licensed under a Creative Commons Attribution 4.0 International License , which permits unrestricted use, distribution, and reproduction in any medium, provided the original work is properly cited.