Open Access
REVIEW
Effect of Recycled Aggregate and Slag as Substitutes for Natural Aggregate and Cement on the Properties of Concrete: A Review
1 School of Water Conservancy Engineering, Zhengzhou University, Zhengzhou, 450001, China
2 Yellow River Laboratory, Zhengzhou University, Zhengzhou, 450001, China
3 College of Civil Engineering, Chongqing University, Chongqing, 400045, China
* Corresponding Author: Yuanxun Zheng. Email:
(This article belongs to the Special Issue: Sustainable Concrete with Recyclable Materials)
Journal of Renewable Materials 2023, 11(4), 1853-1879. https://doi.org/10.32604/jrm.2023.024981
Received 31 May 2022; Accepted 09 August 2022; Issue published 01 December 2022
Abstract
Using recycled aggregate (RA) and slag instead of natural aggregate (NA) and cement can reduce greenhouse gas emissions (GHGE) and achieve effective waste recovery. In recent years, RA has been widely used to replace NA in concrete. Every year, several researchers conduct investigations on the mechanical performance and durability of recycled aggregate concrete (RAC). Due to the loose and porous material properties of RA, the mechanical properties and durability of RAC, such as strength, carbonation resistance, permeability resistance and chloride ion penetration resistance, are greatly reduced compared with natural aggregate concrete. In contrast, concrete containing slag instead of NA and cement generally improved the strength of concrete and reduced the internal porosity of materials. Herein, we discuss the effects of RA and slag on the workability, compressive strength, splitting tensile strength, ultrasonic pulse velocity (UPV) value, and elastic modulus of concrete. The relationships between the compressive strength and the splitting tensile strength, UPV value, and elastic modulus are discussed, and the optimal substitution method is proposed. In addition, various equations for calculating the compressive strength of concrete based on performance factors related to the compressive strength are summarized.Keywords
Concrete is a composite material composed of a binder (i.e., cement paste) and aggregates (i.e., sand, crushed stones, or gravel) [1]. These raw materials are non-renewable resources, and their mining and production processes have an adverse impact on the environment [2–4]. In recent years, owing to the impacts of climate change, significant attention has been devoted to reducing greenhouse gas emissions (GHGE) from various industries. According to one estimate, more than 25% of the global GHGE can be attributed to construction activities [5]. Concrete is one of the most widely used building materials in the world, with approximately 25 billion tons consumed annually, making it one of the main sources of GHGE in construction [6]. Therefore, a significant amount of research has been conducted to reduce GHGE during the production and preparation of raw materials and concrete. Flower et al. [7] recorded GHGE data from typical concrete manufacturing plants. The percentage of GHGE that can be attributed to each component of concrete is shown in Table 1. As shown, cement has the highest GHGE, followed by coarse and fine aggregates. The GHGE of the other raw materials is almost negligible compared to that of concrete, and is not listed in the table.
Flower et al. [7] stated that replacing cement with ground granulated blast furnace slag (GGBFS) can reduce GHGE by 22%. Nanayakkara et al. [8] revealed that compared to traditional concrete, alkali-activated slag–natural aggregate concrete and alkali-activated slag–recycled aggregate concrete have 43.5% and 52% lower GHGE, respectively. Therefore, GHGE can be reduced by replacing traditional concrete materials with materials that have lower carbon emissions; for example, by replacing natural aggregate (NA) and cement with recycled aggregate (RA) and slag, respectively.
The aggregates formed by crushing, grading, and mixing waste concrete in a certain proportion are called RA. Concrete prepared using RA is called recycled aggregate concrete (RAC). Globally, over 10 billion tons of construction waste are generated annually, most of which is disposed in landfills [9], which severely impacts the environment. By increasing the recycling and reuse of construction waste, environmental pollution can be reduced and construction raw material resources can be saved. Numerous studies have demonstrated that RA can successfully substitute natural coarse and fine aggregates, and provide the performance required for normal structural concrete [10,11]. Nevertheless, RA has significantly lower performance than NA in some aspects [12]. For example, the apparent and bulk densities of RA are lower than those of NA, whereas its crush index and water absorption are higher. Therefore, the use of RA affects the workability, mechanical performance, and durability of concrete. Tran et al. [13] investigated the difference in performance between concrete containing 100% recycled coarse aggregates and concrete containing natural coarse aggregates, and observed that the slump, compressive strength, splitting tensile strength, and elastic modulus of the RAC were 32.1%, 9.1%, 7.6%, and 6.4% lower, respectively, than those of the natural aggregate concrete. Tangchirapat et al. [14] replaced NA with RA, and observed a similar reduction in performance. In general, the performance of RAC degrades more noticeably as RA substitution increases.
RA extracted from waste concrete that is crushed and sieved by a grinder is generally composed of 65%–70% natural coarse and fine aggregates and 30%–35% old cement paste [15]. However, several internal cracks occur in the RA during the crushing process. Consequently, the crushed RA has high absorption and low density and strength. The strength of RAC is affected by various factors, including the RA quality, replacement ratio, type of RA, water–cement ratio, etc.
Based on the results obtained by numerous researchers, it can be concluded that the strength reduction in RAC is lessened as RA quality increases [16,17]. The quality of RA depends on the treatment method and degree of the aggregates. Common treatment methods include mechanical [18], chemical [19,20], and biological [21,22] treatments. The purpose of these treatments is to remove or enhance the old mortar attached to the surface of the RA, thereby enhancing its quality. The compressive strength of RAC decreases with the increase in the RA replacement ratio [23,24], and the reduction in strength can be as high as 40%. The strength reduction also varies based on the type of concrete used with RA. Poon et al. [15] performed strength tests on RAC prepared using ordinary concrete (OC) and high–performance concrete (HPC), and observed that compared to the ordinary RAC, the compressive strength of the high–performance RAC was closer to that of natural aggregate concrete.
To reduce the performance gap between RAC and natural aggregate concrete, certain admixtures can be added to RAC for specific engineering applications. The mechanical properties and durability of RAC can be greatly improved by adding grinding waste glass at a sub-micron level [25], a certain amount of fly ash [26,27] and slag [28,29] instead of cement. However, compared with the directly recovered slag, the grinding process of broken glass will generate a certain amount of additional greenhouse gases. Meanwhile, the composition of fly ash materials from different sources varies greatly, and the initial strength of the materials after incorporation is not high. Therefore, this paper mainly discusses the strengthening effect of green sources and high strength slag on recycled aggregate concrete.
Slag is a partially vitreous by-product of ore smelting processes. Steel slag and blast furnace slag are some examples of slag. Steel slag is a by-product of converting iron ore to steel [30]. Globally, 50 million tons of steel slag are produced every year [31]. Based on the steelmaking process, slag can be classified as pretreatment slag, ladle furnace slag (LFS), electrical arc furnace slag (EAFS), basic oxygen furnace slag (BOFS), and casting residue [32]. Table 2 summarizes the chemical composition of BOFS and EAFS [33]. Owing to the high content of CaO in slag, it is a suitable substitute material for concrete. However, steel slag also contains free-CaO [30], which can be detrimental to the volumetric stability of concrete if the free-CaO content exceeds 2% [34]. The volume stability decreases as the free-CaO reacts with water to form calcium hydroxide, increasing the volume by up to 98% [35]. However, as the steel slag ages, the probability of expansion or collapse gradually decreases [36]. Steel slag can be aged by exposing it to outdoor air for at least three months [34] or by immersing it in water, which increases the aging rate [34].
Steel slag can either be ground into a powder to serve as a partial substitution material for cement [37], or can be directly used as coarse or fine aggregates [38]. Chen et al. [38] observed the microscopic morphology (Fig. 1) of limestone and steel slag aggregate (SSA) using backscattered electron–scanning electron microscopy (BSE–SEM). As shown in Fig. 1, the surface texture of the SSA is rougher and has several micropores, which improves its ability to combine with cement paste, whereas the surface of the limestone is smoother and has fewer micropores. Faleschini et al. [39] prepared concrete with 100% EAFS aggregates. Experiments revealed that the EAFS aggregates improved the quality of the interfacial transition zone (ITZ) in the concrete. In summary, slag provides better performance than NA owing to either its physical properties or the microscopic properties of the products formed by its reactions with the concrete mixture. Consequently, the tensile strength and splitting tensile strength of concrete mixed with slag are higher than those of natural aggregate concrete.
Figure 1: Microscopic morphologies of limestone and SSA [38]. Adapted with permission from [32], Copyright © 2020, Elsevier B.V.
The effects of partially or totally substituting NA and cement with RA and slag on the working performance of fresh concrete and the compressive strength, elastic modulus, ultrasonic pulse velocity (UPV) value, and splitting tensile strength of hardened concrete are summarized herein. The variation in the relative compressive strength (RCS) with various replacement ratios reflects the impact of the replacement ratio on the compressive strength of the concrete. RCS can be calculated as:
RCS=CS1/CS2 (1)
where, RCS is the relative compressive strength, CS1 is the compressive strength of the concrete after replacement, and CS2 is the compressive strength of the concrete before replacement.
RCS is introduced because the source, RA particle size, and water–cement ratio used by different researchers can vary significantly. Consequently, the compressive strengths obtained using the same replacement ratio are not comparable. As the RCS data compares the compressive strengths of concrete before and after replacement, it can be directly compared across different research and test groups, and clearly reflects the relationship between the compressive strength and the replacement ratio.
How to improve the mechanical properties and durability of RAC has been a research hotspot for many scholars. Many researchers have made a lot of achievements in improving the performance of RA itself and the influence of some active materials on the performance of RAC. This paper summarizes a large number of research results of previous researchers on the specific effects of RA on the workability, compressive strength, splitting tensile strength, elastic modulus, and UPV value of concrete, and the effects of different alternative forms of slag on the performance of RAC. Combined with economic feasibility and environmental awareness, the best alternative form of slag to improve the performance of RAC has been put forward. This paper also compares some formulas related to the compressive strength of RAC and verifies the applicability of the formulas to a certain extent, which provides further theoretical support for the structural application of RAC.
RA usually has higher water absorption than NA. The water absorption values of NA and RA measured in various studies are compared in Fig. 2. As shown, the water absorption of RA is more than twice that of NA. This can be attributed primarily to the old mortar that adheres to the RA [15,40]. The water absorption of different kinds of steel slag also differs from that of limestone aggregate. Studies have shown that when steel slag is used as fine aggregate, its water absorption is higher than that of NA [41], whereas when steel slag is used as coarse aggregate, its water absorption is lower than that of NA [42,43]. Therefore, concrete composed of RA and steel slag instead of NA does not have the same workability as normal aggregate concrete. In general, the workability of concrete is determined using the slump test.
Figure 2: Water absorption of NA and RA [44–50]
2.1 Influence of RA on the Workability of Concrete
Regardless of whether RA replaces coarse or fine aggregates, the working performance of RAC is lower than that of natural aggregate concrete. Several factors affect the working performance of RAC, including the water–cement ratio, temperature, and time. These factors have a comparable impact on natural aggregate concrete. The RAC with smaller water–binder ratio, higher mixing temperature and longer mixing time will exhibit worse fluidity for the fresh mixture.
Under specific conditions of the water–cement ratio, time, and concrete temperature, the RA replacement ratio has a significant influence on the workability of the RAC. The change rule of the slump reduction rate for three different kinds of RA with the variation in the replacement ratio is shown in Fig. 3. As shown, as the RA replacement ratio increases, the slump of the RAC gradually decreases. The slump reduction rate after 100% replacement is almost 20%. Malešev et al. [51] prepared RAC with 50% and 100% RA and achieved similar slump reduction results. In particular, the concrete slump decreased by 31% at a replacement ratio of 100%. These results indicate that the slump of RAC with a high RA replacement ratio is low. Furthermore, Topçu et al. [52] revealed that the concrete slump decreases significantly above a replacement ratio of 50%.
Figure 3: Relationship between reduction rate of slump and replacement ratio of RA [47]. Adapted with permission from [41], Copyright © 2008, ACI
The decrease in the slump of RAC occurs primarily owing to the high absorption of RA. The higher water absorption decreases the quantity of mortar, which affects the slump [53,54]. Therefore, reducing the water absorption of RA can reduce the decrease in the workability of RAC. Sim et al. [55] concluded that the water absorption of recycled fine aggregate is higher than that of recycled coarse aggregate. Considering recycled coarse aggregate, Savva et al. [44] and Kou et al. [46] revealed that the larger the aggregate particle size, the lower its water absorption.
Low workability increases the porosity and decreases the density of concrete, which is detrimental to its strength and durability. To obtain the same workability as that of natural aggregate concrete, most researchers either add more water [56,57] or use a certain amount of superplasticizer [58] in RAC. Furthermore, RA can also be pretreated to reduce its water absorption. Pretreatment primarily serves to remove or improve the old mortar attached to the RA. Wang et al. [59] and Lu et al. [60] used carbonization technology to improve the old mortar and soaked the RA in acetic acid to remove the old mortar. Tam et al. [61] used different pre-soaking treatment methods to remove the old mortar, and observed that the water absorption of the treated RA was lower than that of the untreated RA. Most researchers treat RA by soaking it followed by surface drying to reduce its water absorption. Wang et al. [62] revealed that the fluidity of RAC containing RA treated using the microbial carbonate precipitation method was 11.6% higher than that of untreated RAC.
2.2 Influence of Slag on the Workability of RAC
Steel slag can replace natural coarse aggregate, natural fine aggregate, and cement in concrete mixtures. Based on the type of replacement, steel slag has different effects on the slump of concrete. In general, when steel slag replaces aggregates, the slump of the concrete mixture decreases with the increase in the replacement ratio. Choi et al. [34] prepared concrete with 50% and 100% steel slag coarse aggregate. The experimental results revealed that as the steel slag replacement ratio increased, the slump gradually decreased. Notably, the decrease in slump was independent of the type of mineral admixture. Therefore, replacing aggregates with steel slag has negative effects on RAC. Sharba [41] used 15%, 25%, 35%, and 45% steel slag and RA to replace natural fine and coarse aggregates, respectively. The results indicated that as the replacement ratio increased, the slump of the mixture gradually decreased, owing to the high absorption of the steel slag and RA.
In contrast, when steel slag powder replaces cement, at a certain substitution rate, the slump of the mixture increases with the increase in the replacement ratio. Therefore, adding steel slag powder to RAC instead of cement has a positive effect. Pan et al. [63] prepared self-compacting concrete by replacing NA and cement with 30% recycled coarse aggregate and different steel slag powder replacement ratios, respectively. The results demonstrated that the slump initially decreases and then increases with the increase in the steel slag powder replacement ratio. The concrete performance remains unchanged at a replacement ratio of 0%–10% and the slump gradually decreases; at a replacement ratio of 10%–50%, the slump gradually increases. This increase in slump may be attributed to the reduction in the volume and size of voids owing to the presence of the steel slag powder [64]. This also explains the decrease in slump at a replacement ratio of 10%. Nevertheless, the negative effect of 30% RA on the slump of the concrete mixture may outweigh the positive effect of the steel slag powder.
Besides steel slag powder, concrete prepared using GGBFS also has good workability. Amer et al. [65] prepared concrete using alkali-activated GGBFS instead of cement. The experimental results indicated that as the replacement ratio of GGBFS increased, the concrete slump gradually decreased. This is because the high cement content increases the speed of the hydration reaction, shortens the setting time, and reduces the slump of the concrete mixture. In addition, increasing the water–cement ratio can also increase concrete slump. As the water–cement ratio increases, the concentration of the alkali solution decreases, slowing down the polymerization reaction. Majhi et al. [66] used recycled coarse aggregate and different replacement ratios of GGBFS to replace NA and cement, respectively, and observed that the resulting concrete had good workability.
The influences of RA and slag on the workability of concrete are significant when both RA and slag are used as replacement materials. Based on various studies, the best approach is to use RA instead of NA, with a coarse aggregate replacement ratio of less than 50%, and steel slag powder or GGBFS instead of cement. Before replacement, the RA should be pretreated to improve its quality. These measures can ensure that the resulting RAC has satisfactory workability.
3.1 Influence of RA on Compressive Strength of RAC
The safety and stability of a concrete structure depend primarily on the compressive strength of the concrete [67,68]. The quality of the RA, replacement ratio, moisture content, type of RA, and water–cement ratio impact the compressive strength of RAC. The quality of the RA has the strongest influence on compressive strength. The density of concrete prepared using high quality RA is higher than that using low quality RA. The higher the density of the RAC, the higher its compressive strength. The microstructure of the ITZ between recycled coarse aggregate from OC and the RAC matrix and that between recycled coarse aggregate from HPC and the RAC matrix are shown in Fig. 4. The Fig. 4(a) represents ITZ between recycled coarse aggregate from ordinary concrete and RAC matrix, and Fig. 4(b) represents ITZ between recycled coarse aggregate from high–performance concrete and RAC matrix. As shown, the ITZ in Fig. 4a is denser and less porous than that in Fig. 4b. The microscopic images also reveal why more water is required to prepare RAC with the requisite fluidity than that required to prepare natural aggregate concrete. Tangchirapat et al. [14] revealed that the water absorption of RA is 12–13 times that of NA.
Figure 4: Microscopic images of interface transition zone [15]. Adapted with permission from [12], Copyright © 2004, Elsevier B.V.
The RA extracted from waste concrete that is subsequently crushed and sieved by a grinder is generally composed of 65%–70% natural coarse and fine aggregates and 30%–35% old cement paste [15]. Owing to the presence of the old cement mortar, the aggregate has high water absorption and porosity and low density, thereby resulting in a low compressive strength [69–71]. Owing to the high absorption of the RA, the water–cement ratio around the aggregates decreases significantly; the incomplete hydration around these aggregates and the higher porosity of the RA increase the stress in the RAC around these aggregates, thereby reducing its strength [72].
3.1.1 Influence of RA Quality on Compressive Strength of RAC
The quality of RA has a significant effect on the compressive strength of RAC. The higher the quality of RA, the higher the compressive strength of RAC. Fig. 5 depicts the experimental results of the studies listed in Table 3, and compares the compressive strengths of RAC samples prepared by various researchers using treated and untreated RA. As shown, the compressive strength of the treated RAC is higher than that of the untreated RAC. By selecting a proper RA treatment process, it is possible to obtain RAC with a compressive strength that is almost equal to that of natural aggregate concrete. Therefore, to minimize the reduction in the compressive strength of RAC, the quality of the RA should be as high as possible. The quality of the RA can be improved either by removing the adhesive old mortar or by strengthening it. The methods used by various researchers to treat RA are described and listed in Table 3. Owing to its simplicity, the most popular RA treatment method is mechanical grinding, wherein RA and water are rotated in a concrete drum to remove the loosely bonded mortar on the surface of the RA through contact between individual RA particles and that between the RA and the drum wall. However, mechanical grinding increases the number of internal cracks in the RA, which further reduces the compressive strength of the RAC.
Figure 5: Comparison of compressive strengths of RAC containing treated and untreated RA. Adapted with permission from [44], Copyright © 2021, MDPI, [45], Copyright © 2021, Elsevier B.V., [48], Copyright © 2021, Elsevier B.V., [61], Copyright © 2007, Elsevier B.V., [62], Copyright © 2017, Elsevier B.V., and [73], Copyright © 2004, American Society of Civil Engineers
3.1.2 Influence of Replacement Ratio of RA on Compressive Strength of RAC
The replacement ratio of RA also affects the compressive strength of RAC. The higher the RA replacement ratio, the lower the compressive strength of RAC. According to Majhi et al. [74], the decrease in compressive strength can be attributed to the decrease in the density of the RAC owing to the gaps left by the filtration of soluble calcium hydroxide. However, in some cases, a low RA replacement ratio increases the compressive strength of concrete [75,76]. This is because the addition of RA improves the grain gradation of concrete [77]. Furthermore, some unreacted cement particles may also adhere to the RA, thereby increasing the cementitious material content in the mixture [78]. This phenomenon is very rare.
The variation in RCS owing to the replacement of natural coarse aggregates with recycled coarse aggregates, considering different replacement ratios, are shown in Fig. 6. As shown, when natural coarse aggregates are replaced by recycled coarse aggregates, the RCS of the RAC decreases by as much as 40% compared to the strength of the original concrete. This is consistent with the research results of Younis et al. [79]. Based on the data from references [23,80–82] shown in Fig. 6, at an RA replacement ratio of 0%–50%, the reduction in the concrete compressive strength is less than 20% and is not evident. This was confirmed by Barhmaiah et al. [23]. However, the experimental data corresponding to [83] in Fig. 6 differ significantly from the rest of the data: first, the compressive strength decreases significantly even at a low RA replacement ratio; second, as the replacement ratio increases from 30% to 40%, the RCS suddenly decreases. The reasons for this behavior are: (1) the type of concrete used to prepare the RAC in [83] was self-compacting concrete, which differs from that used in the other studies; and (2) the porosity of the mixture increased considerably when the RA replacement ratio increased from 30% to 40%, decreasing the compactness of the concrete and ultimately reducing its compressive strength. Nevertheless, the RA replacement ratio is only one factor that affects the compressive strength of RAC.
Figure 6: 28-d RCS of RAC [23,80–85]
Various factors that affect the compressive strength must be considered while preparing RAC to achieve the required structural strength. In general, as the RA replacement ratio increases, the strength of RAC decreases. However, even at the same replacement ratio, the eventual reduction in strength can differ considerably. This is because the low compressive strength of RAC is related to the high absorption of RA [77]. The absorption varies based on the pretreatment method. In addition, RA can be obtained from concrete with diverse water–cement ratios, which has a significant effect on the performance of the RA [86]. The compressive strength of RAC is also related to the water–cement ratio of concrete, which is also the case with natural aggregate concrete. Qasrawi [87] prepared concrete using recycled coarse aggregate and determined that the compressive strength of RAC gradually decreases with the increase in RA content. However, the high water–cement ratio of RAC decreases the reduction in compressive strength at a constant RA replacement ratio. As shown in Fig. 7, with a low water–cement ratio and high RA replacement ratio, the reduction in the compressive strength of the RAC is approximately 25%. In contrast, the reduction in the compressive strength of RAC with a high water–cement ratio and low RA replacement ratio is less than 5%, which is almost equal to the strength of the control concrete. This is consistent with the conclusions of Chen et al. [88].
Figure 7: Compressive strength reduction [77]. Adapted with permission from [77], Copyright © 2003, Informa UK Limited
3.1.3 Influence of Type of RA on Compressive Strength of RAC
The compressive strength and ultimate strength of RAC also vary with the type of RA. Table 4 lists the compressive strengths of concrete samples prepared using different types of RA. RA (a), RB (b), and RC (c) are derived from three types of concrete with increasing compressive strengths [73]. The mixed aggregates comprised crushed concrete, glass, masonry, etc. As shown, although the RA replacement ratios are the same, the compressive strengths of the RAC samples differ significantly based on the type of RA. When RA derived from high–strength concrete is used to prepare RAC, the reduction in strength is lower. Furthermore, the particle size of the RA also affects the compressive strength of the RAC. The reduction in the compressive strength of RAC containing recycled coarse aggregate is lesser than that containing recycled fine aggregates [89].
3.2 Influence of Slag on Compressive Strength of Concrete
Slag is often referred to as a supplementary cementitious material (SCM) owing to its pozzolanic activity [90]. Studies have shown that it can enhance the strength and durability of concrete [91]. The application of slag varies based on its particle size. Slag with finer particle size, such as GGBFS, steel slag power, and alkali-activated slag, can be used as a substitute for cement. Coarse slag such as steel slag can be used as an aggregate substitute. SSA can have different effects on the compressive strength of RAC based on the type of aggregate substituted. Replacing NA with SSA usually increases the compressive strength of concrete. As SSA has a rougher surface texture and more micropores than limestone, it promotes cement slurry bonding [38]. The compressive strength of concrete is affected both positively and negatively when SSA is used as fine aggregate instead of NA. As SSA is stronger than NA and has a rougher surface than NA, the bonding strength with the cement slurry increases. However, the addition of SSA increases the porosity of the concrete, and owing to its high angularity, steel slag requires more cement to cover its surface, which reduces the strength of the concrete [92]. These positive and negative effects have a competitive effect, resulting in an overall increase or decrease in strength.
The use of steel slag instead of coarse aggregate generally improves the compressive strength of RAC. The RCS of concrete prepared by various researchers using different steel slag replacement ratios is shown in Fig. 8. As shown, the compressive strength of concrete increases when natural coarse aggregates are replaced with steel slag. As the replacement ratio increases, the strength increment increases. The maximum strength increment relative to the control group was approximately 40%. Notably, thus far, the use of slag has not been reported to have any adverse effects [101].
Figure 8: Relative compressive strength changes in 28-d RCS [37,42,93–100]
In addition to using steel slag to replace natural coarse aggregates, it can also be used to replace natural fine aggregates and cement. The amount of steel slag that replaces fine aggregate is an important factor of the resulting strength enhancement. Based on the results obtained by Papayianni et al. [97], Pellegrino et al. [94], and Qasrawi et al. [102], the threshold value of steel slag that can replace fine aggregate is 50%; above this threshold, the steel slag has a negative impact on concrete strength. In contrast, Roslan et al. [101] partially replaced cement with EAFS and observed that the compressive strength of concrete increased with the increase in the EAFS replacement ratio. However, the early strength of the EAFS concrete was not as good as that of the control concrete; similar findings were reported by Amer et al. [65]. This behavior can be attributed to a lack of cement in the concrete mixture, which delays the hydration process, resulting in a minimal amount of initial calcium hydroxide (Ca(OH)2) formation. As the concrete ages, the amount of Ca(OH)2 increases and reacts with the EAFS and steel sludge to form additional calcium silicate gel (C-S-H), which increases the concrete strength [101]. Therefore, when slag is used to replace cement, the replacement ratio must be determined based on the needs of the project. To obtain an ideal early strength, the slag replacement ratio or the water–cement ratio must be reduced; this increases the cement content, accelerating the rate of the hydration reaction, and increasing the content of the early hydration products. This is contrary to the strength development rule applied when SSA is used as the replacement. Nguyen et al. [103] stated that the compressive strengths of concrete containing SSA at 7 and 28 d were approximately 55%–66% and 69%–73%, respectively, of that at 365 d. This indicates the strength development of concrete containing SSA primarily occurs during the early stages.
Not all types of steel slag or slag enhance the strength of concrete. Brand et al. [93] observed that for the same replacement ratio, the compressive strength of concrete containing EAFS increased by 4.8%, whereas that containing BOFS decreased by 13.0%. Therefore, most researchers use EAFS. Considering the material composition, the free CaO content in BOFS is higher than that in EAFS. A high free CaO content reduces the hydration reaction, thereby reducing the compressive strength of concrete. Liu et al. [37] replaced concrete with different ratios of steel slag powder and discovered that the compressive strength of concrete decreased with the increase in the steel slag powder replacement ratio. Papayianni et al. [95] also arrived at the same conclusion. This happens because the addition of steel slag powder increases the proportion of hardened pastes with pores larger than 50 nm. In addition to steel slag, the concrete strength can also be increased by using ferrochrome slag [104] and blast furnace slag [100] instead of aggregates.
3.3 Influence of Slag on Compressive Strength of RAC
RAC often has a lower compressive strength than natural aggregate concrete. Its compressive strength varies based on the type and amount of slag added to it. When steel slag is used to replace NA, it may not always improve the compressive strength of RAC. Anastasiou et al. [105] discovered that the compressive strength of concrete was reduced by 26.1% after 28 d when 100% RA and steel slag were used instead of natural fine and coarse aggregates. However, compared to natural aggregate concrete, the compressive strength of RAC decreased by 18.1% after 365 d, considerably alleviating the reduction in strength. Although the positive effects of SSA on the compressive strength of RAC are not evident initially, they can be detected as the concrete ages. Qasrawi [87] discovered that when NA was replaced with RA and steel slag in a ratio of 2:3, the resulting concrete had higher compressive strength than natural aggregate concrete. Therefore, when NA is simultaneously replaced by RA and steel slag, a satisfactory compressive strength can be obtained by selecting an appropriate mixture ratio of the two. In addition, as far as possible, the RA replacement ratio should not exceed 50%.
When steel slag is added to RAC instead of cement, the compressive strength of the RAC does not necessarily increase with the increase in steel slag. Pan et al. [63] prepared self-compacting concrete with 30% RA instead of NA and used different steel slag powder replacement ratios instead of cement. After curing for 28 d, the reduction rate of the compressive strength of the RAC varied with the steel slag powder replacement ratio, as shown in Fig. 9. The compressive strength of RAC increased by 7.2% compared with the control group when the cement was replaced by 10% steel slag powder. When the replacement amount of steel slag powder changed from 20% to 50%, the compressive strength of RAC decreased gradually, and the strength reduction rate reached up to 42.7%. The compressive strength of the RAC was higher than that of the control group only when the steel slag powder replacement ratio was relatively low. Moreover, the higher the steel slag powder replacement ratio was used, the greater the decrease in strength was observed. The hydration products of steel slag powder with low content can fill pores, so the compressive strength of RAC will be improved. However, the research results of Wang et al. [106] indicate that the dormant period of a steel slag-cement composite binder is longer than that of a cement binder. Moreover, the higher steel slag content will result in a longer dormant period. Therefore, the 28-day compressive strength of RAC prepared with a high content of steel slag powder instead of cement decreases gradually with the increase of steel slag power.
Figure 9: Compressive strength reduction with increase in steel slag replacement ratio. Adapted with permission from [54], Copyright © 2019, Elsevier B.V.
The compressive strength of RAC can be increased by using GGBS [107,108]. However, the increase in strength is not evident initially. This is because the hydration reaction with GGBS is slow and the hydration products are few, with most GGBS particles acting as a filler. Majhi et al. [74] did not find C-S-H gel and ettringites in the SEM images of early stage RAC containing GGBS. The early strength of RAC can be improved by using alkali-activated slag aggregates as the alkali solution promotes the rate of the hydration reaction [109].
Splitting tensile strength is an extremely important strength index for concrete as it determines the formation and development of cracks on the tensile side of flexural members [110]. The addition of RA negatively influences the splitting tensile strength of concrete, whereas the addition of slag has a positive influence. Therefore, slag can be added to RAC to maximize the use of RA and reduce solid waste.
The factors affecting the splitting tensile strength of RAC include the RA replacement ratio and type of RA. The relationship between the splitting tensile strength of RAC and the RA replacement ratio is illustrated in Fig. 10. As shown, the splitting tensile strength decreases as the replacement ratio increases. At a replacement ratio of 100%, the splitting tensile strength decreases by approximately 40%, which is comparable to the reduction in compressive strength. This decrease in the splitting tensile strength can be attributed to the decrease in the bond strength between the RA and the mortar. Savva et al. [44] analyzed the impacts of recycled coarse and fine aggregates on the splitting tensile strength of concrete at the same replacement ratio. As shown in Fig. 11, recycled fine aggregate has a smaller impact on the splitting tensile strength of concrete compared to that of recycled coarse aggregate.
Figure 10: Changes in relative splitting tensile [47,49,58,111–113]
Figure 11: Splitting tensile strength of strength RAC at different replacement ratios [44]. Adapted with permission from [44], Copyright © 2021, MDPI
Mavroulidou et al. [114] analyzed the splitting tensile strength of concrete prepared by replacing cement with alkali-activated GGBS. They revealed that the splitting tensile strength of the resulting concrete was 19.9%–31.7% higher than that of the control concrete. Qi et al. [115] prepared concrete by replacing cement with different ratios of SSA. As the SSP replacement ratio increased, the splitting tensile strength gradually increased by approximately 10%. Maslehuddin et al. [43] prepared concrete with different SSA replacement ratios instead of NA. They discovered that as the SSA replacement ratio increased, the splitting tensile strength of the prepared concrete gradually increased. Almusallam et al. [42] arrived at the same conclusion by using 100% steel slag instead of NA, and achieved a strength increase of 27%. Therefore, slag can replace cement and the coarse and aggregates in concrete without significantly affecting the splitting tensile strength.
Qin et al. [116] investigated the change in the splitting tensile strength of concrete containing RA and slag. As shown in Fig. 12, the splitting tensile strength of concrete decreases with the increase in the RA replacement ratio and increases with the increase in the slag replacement ratio. However, a high slag replacement ratio also negatively influences the strength of the concrete. Nevertheless, the splitting tensile strength of the RAC containing RA and slag was satisfactory compared to that of the control concrete (the dotted line in the figure represents the splitting tensile strength of the control concrete). Therefore, the addition of slag to RAC can improve its splitting tensile strength even with an RA replacement ratio of 100%. The active SiO2 and Al2O3 in slag can react with the hydration product Ca(OH)2 of cement, resulting in secondary hydration in RAC. More gel materials are created as a result of secondary hydration. These gel materials will optimize the internal interface transition zone, enhance the bond strength between aggregates, and eventually increase the splitting tensile strength of RAC. However, when excessive slag is mixed into RAC, there is not enough Ca(OH)2 in the matrix to hydrate with extra slag. Excess slag is used to fill the pores. This is the cause of the decreased splitting tensile strength of RAC when more than 20% slag is included [116].
Figure 12: Splitting tensile strength with simultaneous substitution using RA and slag. Adapted with permission from [103], Copyright © 2019, Qin et al. [116]
Although there is a close correlation between the compressive and tensile strengths of RAC, this correlation is not entirely positive. Numerous researchers have proposed various prediction equations to describe the relationship between the compressive and splitting tensile strengths, as shown in Table 5. Khan et al. [117] used the data acquired by substituting NA with recycled coarse aggregate to derive Eq. (2); Arioglu et al. [118] and Bhanja et al. [119] proposed Eqs. (3) and (4), respectively; Larrard et al. [120] proposed Eq. (5), which is applicable regardless of the age of the concrete; Khoshkenari et al. [121] used RA instead of NA and derived Eq. (6) from test data. These test data were also used to verify the accuracy of Eqs. (3)–(5). The results revealed that Eqs. (3) and (4) had an error of approximately 3%, whereas the average error of Eq. (5) was approximately 12%. As these errors are within the acceptable range, these equations can be used to predict the splitting tensile strength of concrete based on its compressive strength.
The elastic modulus represents the capacity of concrete to withstand deformation under compression. To some extent, it reflects the compactness and strength of the concrete. Therefore, when RA and slag are used in concrete, their effect on the elastic modulus must be analyzed.
The elastic modulus of concrete is influenced by the elastic modulus of the coarse aggregate in the concrete [122]. Consequently, RA and slag can affect the elastic modulus of concrete. In general, RA decreases the elastic modulus of concrete, whereas slag increases it. According to Jacintho et al. [123], as the RA replacement ratio increases, the elastic modulus of RAC decreases. With an RA replacement ratio of 50%, the elastic modulus of the concrete decreased by 25.3%. The decrease in the elastic modulus of RAC can be attributed to the presence of the old mortar on the RA, which is characterized by a weak binding interface; in addition, the porosity of recycled concrete aggregate is low [124]. Occasionally, the addition of RA may increase the elastic modulus of concrete. Nanayakkara et al. [8] studied the variation in the elastic modulus of alkali-activated slag concrete before and after using 100% recycled coarse aggregate. The results revealed that the elastic modulus of the concrete decreased by 5.9% after aggregate replacement. The difference in the degree of the reduction in elastic modulus can be attributed to the unhydrated cement attached to the RA, which promotes the hydration of the alkali-activated slag concrete and increases the density of the interface microstructure.
The addition of slag increases the elastic modulus of concrete. Soldado et al. [125] discovered that the elastic modulus of concrete increased by 6.5% when slag was used instead of cement. Gholampour et al. [126] revealed that the addition of 100% recycled fine aggregate decreases the elastic modulus of concrete by 21.7%, whereas the elastic modulus of concrete containing 50% recycled fine aggregate and 35% GGBFS increases by 1.2%. El-Hawary et al. [127] used recycled coarse aggregate instead of NA, which decreases the elastic modulus. However, the addition of GGBS increased the elastic modulus above that of the control concrete. This increase in the elastic modulus of concrete primarily occurs because the addition of slag fills the pores in the concrete, thereby increasing its density [34]. However, when excess slag is added, it has a negative effect on the elastic modulus of concrete. The variation in the elastic modulus of RAC with the amount of cement replaced by slag is illustrated in Fig. 13. As is shown, the positive effect of slag on the elastic modulus of concrete has a certain content threshold. When the content of the added slag exceeds this threshold, the elastic modulus of RAC gradually will decrease as the slag replacement ratio increases. The dormant period of a steel slag-cement composite binder is longer than that of a cement binder. Moreover, the RAC with higher steel slag content needs a longer dormant period [106].
Figure 13: Variation in elastic modulus of RAC with slag replacement ratio [63,128]
The elastic modulus of concrete is closely linked to its compressive strength. Studies have shown that the elastic modulus of concrete is positively correlated with its strength. However, the conventional equation to express the relationship between the compressive strength and the elastic modulus of concrete is not applicable to RAC. Table 6 lists the equations proposed by various researchers to express the relationship between the compressive strength and the elastic modulus of RAC. El-Hassan et al. [124] proposed Eq. (7) based on the RA and steel fiber dosage, wherein RCA represents the percentage replacement of RA and SF represents the volume fraction of steel fiber; Yuan et al. [129] also proposed Eq. (8) for the relationship between compressive strength and elastic modulus of concrete containing RA and steel fiber, wherein λm represents the volume fraction of steel fiber, ra represents the percentage replacement of RA and d1 , d2 represent the regression coefficients of the elastic modulus. Park et al. [122] used a significant amount of test data to derive Eq. (9), wherein R represents the correction factor, which is related to the quality and replacement quantity of RA, σ represents the compressive strength of RAC and γ represents the mass of a unit volume of the RAC; Tošić et al. [130] proposed Eq. (10), wherein kE accounts for the type of aggregate and αRA represents the ratio between the mass of RA and the total aggregate mass in RAC.
UPV is a popular non-destructive and indirect approach used to measure the compressive strength of concrete. The UPV value has a good correlation with the compressive strength of concrete. Furthermore, it can also be used to evaluate the uniformity of the concrete and detect defects.
The UPV value is determined based on the ITZ characteristics of the concrete and the aggregate density. As illustrated in Fig. 14, the UPV value decreases with the increase in the RA replacement ratio [89]. This is because the voids and cracks in the concrete also increase with the increase in the RA replacement ratio [124]. The decrease in the UPV value can be attributed primarily to the high porosity and weak ITZ of the RAC [131]. The UPV value is also related to the curing conditions and type of RA used in the RAC. Cho et al. [132] revealed that the UPV value of concrete varies based on whether it is subjected to air curing or standard curing. Revilla-Cuesta et al. [89] stated that the use of excessive recycled fine aggregate leads to a higher predicted UPV value when the compressive strength of the concrete is measured using UPV. Consequently, when the compressive strength of the concrete exceeds 60 MPa, the compressive strength predicted by the UPV value is slightly overestimated [133]. Nanayakkara et al. [134] used UPV to evaluate the uniformity and defects in concrete and revealed that concrete containing slag and RA had excellent long–term performance. With time, the material quality improved, the strength increased, and the porosity decreased.
Figure 14: Ultrasonic pulse velocity of RAC with slag replacement ratio [89]
Table 7 demonstrates the relationships between the UPV value and the compressive strength of concrete proposed by various researchers. Revilla-Cuesta et al. [89] proposed different formulae based on the range of the UPV values. Saha et al. [135] clarified the relationship between the compressive strength, density, water–cement ratio, and UPV value of concrete; ρ represents the density and ω represents the water–cement ratio of concrete. El-Hassan et al. [124] established a relationship between the compressive strength and the UPV value of concrete, and Hong et al. [136] proposed a formula for the relationship between the UPV value and the compressive strength of high–strength concrete. The four formulas are all highly correlated functions that have been fitted from a large amount of experimental data. Eqs. (10), (13) and (14) directly present the relationship between compressive strength and UPV value without considering the characteristics of the concrete itself. After comparative analysis, the deviation between the three formulas is obvious, which is obviously not universal. Compared with the other three formulas, the relationship between the compressive strength and UPV value of RA given by Eq. (14) limits the density and water–binder ratio of materials, and the applicability of the formula is obviously improved. Therefore, the RAC prepared for different materials needs to adopt appropriate formulas to show the relationship between UPV value and compressive strength.
After reviewing 136 studies, the following conclusions are drawn:
(1) Slag added to RAC can improve its workability. When RA and slag are added to the concrete, the best approach is to use RA instead of NA, with a coarse aggregate replacement ratio of less than 50%, and steel slag powder or GGBFS instead of cement. Before replacement, the RA should be pretreated to improve its quality.
(2) When slag aggregate and RA replace natural aggregate together, the replacement amount of RA should not exceed 50%. The proportion of natural aggregate replaced by RA and slag aggregate is the key to the high compressive strength of concrete. In order to obtain a high early compressive strength of RAC, the proportion of steel slag powder replacing cement should be kept at about 10% or GGBFS should be used instead of cement.
(3) The elastic modulus, UPV value and splitting tensile strength of RAC are positively correlated with its compressive strength. Many researchers have established many relations between them according to their own experimental results. When these relationships are used, bias can be greatly reduced by selecting relationships that include as many material properties as possible.
In conclusion, this paper summarizes the factors and mechanisms of RA and slag on concrete workability, compressive strength, splitting tensile strength, elastic modulus, and UPV value. The best alternative method for incorporating RA and slag into concrete has been identified. Some formulas related to the compressive strength of RAC are compared in this paper, and their applicability is verified to a certain extent. The author thinks that in order to obtain the wide application and recognition of RAC, the quality of RA should be divided into certain grades based on the material source, particle size, the content of old mortar, and other aspects, and this grade must be mutually transformed with the grade of natural aggregate. Secondly, the replacement amount of RA should be capped. Future research should not be limited to the mechanical properties of RAC, but more research should be done on its durability, so as to provide more data support for the application of RAC.
Funding Statement: The authors would like to acknowledge the financial support received from National Natural Science Foundation of China (Grant No. U2040224), Natural Science Foundation of Henan (Grant No. 212300410018), and Program for Innovative Research Team (in Science and Technology) in University of Henan Province of China (Grant No. 20IRTSTHN009).
Conflicts of Interest: The authors declare that they have no conflicts of interest to report regarding the present study.
References
1. Wang, L., Li, G. X., Li, X., Guo, F. X., Tang, S. W. et al. (2022). Influence of reactivity and dosage of MgO expansive agent on shrinkage and crack resistance of face slab concrete. Cement & Concrete Composites, 126, 104333. DOI 10.1016/j.cemconcomp.2021.104333. [Google Scholar] [CrossRef]
2. Thomas, J., Thaickavil, N. N., Wilson, P. M. (2018). Strength and durability of concrete containing recycled concrete aggregates. Journal of Building Engineering, 19, 349–365. DOI 10.1016/j.jobe.2018.05.007. [Google Scholar] [CrossRef]
3. Wen, C., Zhang, P., Wang, J., Hu, S. (2022). Influence of fibers on the mechanical properties and durability of ultra-high-performance concrete: A review. Journal of Building Engineering, 52, 104370. DOI 10.1016/j.jobe.2022.104370. [Google Scholar] [CrossRef]
4. Peng, Y. X., Tang, S. W., Huang, J. S., Tang, C., Wang, L. et al. (2022). Fractal analysis on pore structure and modeling of hydration of magnesium phosphate cement paste. Fractal and Fractional, 6(6), 337. DOI 10.3390/fractalfract6060337. [Google Scholar] [CrossRef]
5. Hong, J., Shen, G. Q., Feng, Y., Lau, W. S. T., Mao, C. (2015). Greenhouse gas emissions during the construction phase of a building: A case study in China. Journal of Cleaner Production, 103, 249–259. DOI 10.1016/j.jclepro.2014.11.023. [Google Scholar] [CrossRef]
6. Petek Gursel, A., Masanet, E., Horvath, A., Stadel, A. (2014). Life-cycle inventory analysis of concrete production: A critical review. Cement and Concrete Composites, 51, 38–48. DOI 10.1016/j.cemconcomp.2014.03.005. [Google Scholar] [CrossRef]
7. Flower, D. J. M., Sanjayan, J. G. (2007). Green house gas emissions due to concrete manufacture. The International Journal of Life Cycle Assessment, 12(5), 282–288. DOI 10.1065/lca2007.05.327. [Google Scholar] [CrossRef]
8. Nanayakkara, O., Gunasekara, C., Law, D. W., Xia, J., Setunge, S. (2021). Alkali-activated slag concrete with recycled aggregate long-term performance. Journal of Materials in Civil Engineering, 33(7), 04021167. DOI 10.1061/(ASCE)MT.1943-5533.0003773. [Google Scholar] [CrossRef]
9. Chen, K., Wang, J., Yu, B., Wu, H., Zhang, J. (2021). Critical evaluation of construction and demolition waste and associated environmental impacts: A scientometric analysis. Journal of Cleaner Production, 287, 125071. DOI 10.1016/j.jclepro.2020.125071. [Google Scholar] [CrossRef]
10. Zheng, Y., Zhuo, J., Zhang, P., Ma, M. (2022). Mechanical properties and meso-microscopic mechanism of basalt fiber-reinforced recycled aggregate concrete. Journal of Cleaner Production, 370, 133555. DOI 10.1016/j.jclepro.2022.133555. [Google Scholar] [CrossRef]
11. Limbachiya, M., Meddah, M. S., Ouchagour, Y. (2012). Performance of portland/silica fume cement concrete produced with recycled concrete aggregate. ACI Materials Journal, 109(1), 91–100. [Google Scholar]
12. Xiao, J., Li, J., Zhang, C. (2005). Mechanical properties of recycled aggregate concrete under uniaxial loading. Cement and Concrete Research, 35(6), 1187–1194. DOI 10.1016/j.cemconres.2004.09.020. [Google Scholar] [CrossRef]
13. Tran, D. V. P., Allawi, A., Albayati, A., Cao, T. N., El-Zohairy, A. et al. (2021). Recycled concrete aggregate for medium-quality structural concrete. Materials, 14(16), 4612. DOI 10.3390/ma14164612. [Google Scholar] [CrossRef]
14. Tangchirapat, W., Buranasing, R., Jaturapitakkul, C., Chindaprasirt, P. (2008). Influence of rice husk–bark ash on mechanical properties of concrete containing high amount of recycled aggregates. Construction and Building Materials, 22(8), 1812–1819. DOI 10.1016/j.conbuildmat.2007.05.004. [Google Scholar] [CrossRef]
15. Poon, C. S., Shui, Z. H., Lam, L. (2004). Effect of microstructure of ITZ on compressive strength of concrete prepared with recycled aggregates. Construction and Building Materials, 18(6), 461–468. DOI 10.1016/j.conbuildmat.2004.03.005. [Google Scholar] [CrossRef]
16. Phuong Trinh, B., Huynh Sang, L., Phan Phuong Uyen, N., Thanh Nam, L., Ngoc Thanh, N. et al. (2020). Effect of sodium-silicate treatment for recycled concrete aggregate on slump and compressive strength of concrete. ICSCEA 2019 Proceedings of the International Conference on Sustainable Civil Engineering and Architecture. Lecture Notes in Civil Engineering (LNCE 80), pp. 457–465. Ho Chi Minh City, Vietnam. [Google Scholar]
17. Atmajayanti, A. T., Saragih, G. C. D., Haryanto, Y. (2018). The effect of recycled coarse aggregate (RCA) with surface treatment on concrete mechanical properties. 4th International Conference on Rehabilitation and Maintenance in Civil Engineering (ICRMCE), pp. 01017. Solo Baru, Indonesia. [Google Scholar]
18. Zheng, Y., Zhang, Y., Zhuo, J., Zhang, P., Kong, W (2022). Mechanical properties and microstructure of nano-strengthened recycled aggregate concrete. Nanotechnology Reviews, 11(1), 1499–1510. DOI 10.1515/ntrev-2022-0077. [Google Scholar] [CrossRef]
19. Chen, K., Zhu, Z., Xue, T., Zhang, H., Wang, A. et al. (2021). Enhancement treatment of recycled concrete aggregate. Frontiers in Built Environment, 7, 739148. DOI 10.3389/fbuil.2021.739148. [Google Scholar] [CrossRef]
20. Zhan, B. J., Xuan, D. X., Zeng, W. L., Poon, C. S. (2019). Carbonation treatment of recycled concrete aggregate: Effect on transport properties and steel corrosion of recycled aggregate concrete. Cement & Concrete Composites, 104, 103360. DOI 10.1016/j.cemconcomp.2019.103360. [Google Scholar] [CrossRef]
21. Qiu, J. S., Tng, D. Q. S., Yang, E. H. (2014). Surface treatment of recycled concrete aggregates through microbial carbonate precipitation. Construction and Building Materials, 57, 144–150. [Google Scholar]
22. Liu, Z. W., Chin, C. S., Xia, J. (2021). Improving recycled coarse aggregate (RCA) and recycled coarse aggregate concrete (RCAC) by biological denitrification phenomenon. Construction and Building Materials, 301, 124338. [Google Scholar]
23. Barhmaiah, B., Leela Priyanka, M., Padmakar, M. (2021). Strength analysis and validation of recycled aggregate concrete. Materials Today: Proceedings, 37, 2312–2317. [Google Scholar]
24. Abedalqader, A., Shatarat, N., Ashteyat, A., Katkhuda, H. (2021). Influence of temperature on mechanical properties of recycled asphalt pavement aggregate and recycled coarse aggregate concrete. Construction and Building Materials, 269, 121285. [Google Scholar]
25. Nassar, R. U. D., Soroushian, P. (2012). Strength and durability of recycled aggregate concrete containing milled glass as partial replacement for cement. Construction and Building Materials, 29, 368–377. [Google Scholar]
26. Tangchirapat, W., Rattanashotinunt, C., Buranasing, R., Jaturapitakkul, C. (2013). Influence of fly ash on slump loss and strength of concrete fully incorporating recycled concrete aggregates. Journal of Materials in Civil Engineering, 25(2), 243–251. [Google Scholar]
27. Wang, L., Yu, Z. Q., Liu, B., Zhao, F., Tang, S. W. et al. (2022). Effects of fly ash dosage on shrinkage, crack resistance and fractal characteristics of face slab concrete. Fractal and Fractional, 6(6), 335. [Google Scholar]
28. Ann, K. Y., Moon, H. Y., Kim, Y. B., Ryou, J. (2008). Durability of recycled aggregate concrete using pozzolanic materials. Waste Management, 28(6), 993–999. [Google Scholar]
29. Yang, H., Zhang, S., Wang, L., Chen, P., Shao, D. et al. (2022). High-ferrite portland cement with slag: Hydration, microstructure, and resistance to sulfate attack at elevated temperature. Cement & Concrete Composites, 130, 104560. [Google Scholar]
30. Tsakiridis, P. E., Papadimitriou, G. D., Tsivilis, S., Koroneos, C. (2008). Utilization of steel slag for portland cement clinker production. Journal of Hazardous Materials, 152(2), 805–811. [Google Scholar]
31. Altun, I. A., Yılmaz, I. (2002). Study on steel furnace slags with high MgO as additive in portland cement. Cement and Concrete Research, 32, 1247–1249. DOI 10.1016/S0008-8846(02)00763-9. [Google Scholar] [CrossRef]
32. Yi, H., Xu, G., Cheng, H., Wang, J., Wan, Y. et al. (2012). An overview of utilization of steel slag. Procedia Environmental Sciences, 16, 791–801. DOI 10.1016/j.proenv.2012.10.108. [Google Scholar] [CrossRef]
33. Wu, X. Q., Zhu, H., Hou, X. K., Li, H. S. (1999). Study on steel slag and fly ash composite portland cement. Cement and Concrete Research, 29, 1103–1106. DOI 10.1016/S0008-8846(98)00244-0. [Google Scholar] [CrossRef]
34. Choi, S. Y., Kim, I. S., Yang, E. I. (2020). Comparison of drying shrinkage of concrete specimens recycled heavyweight waste glass and steel slag as aggregate. Materials, 13(22), 5084. DOI 10.3390/ma13225084. [Google Scholar] [CrossRef]
35. Hou, J., Lv, Y., Liu, J., Wu, Q. (2018). Expansibility of cement paste with tri-component f-CaO in steel slag. Materials and Structures, 51(5), 113. DOI 10.1617/s11527-018-1240-x. [Google Scholar] [CrossRef]
36. Lim, H. S., Lee, H. (2017). Experimental study on evaluation on volume stability of the electric arc furnace oxidizing slag aggregate. Journal of the Korea Institute for Structural Maintenance and Inspection, 21(2), 78–86. [Google Scholar]
37. Liu, J., Guo, R. (2018). Applications of steel slag powder and steel slag aggregate in ultra-high performance concrete. Advances in Civil Engineering, 2018, 1–8. DOI 10.1155/2018/1426037. [Google Scholar] [CrossRef]
38. Chen, X., Wang, G., Dong, Q., Zhao, X., Wang, Y. (2020). Microscopic characterizations of pervious concrete using recycled steel slag aggregate. Journal of Cleaner Production, 254, 120149. DOI 10.1016/j.jclepro.2020.120149. [Google Scholar] [CrossRef]
39. Faleschini, F., Brunelli, K., Zanini, M. A., Dabalà, M., Pellegrino, C. (2015). Electric arc furnace slag as coarse recycled aggregate for concrete production. Journal of Sustainable Metallurgy, 2(1), 44–50. DOI 10.1007/s40831-015-0029-1. [Google Scholar] [CrossRef]
40. Katz, A. (2003). Properties of concrete made with recycled aggregate from partially hydrated old concrete. Cement and Concrete Research, 33(5), 703–711. DOI 10.1016/S0008-8846(02)01033-5. [Google Scholar] [CrossRef]
41. Sharba, A. A. (2019). The efficiency of steel slag and recycled concrete aggregate on the strength properties of concrete. KSCE Journal of Civil Engineering, 23(11), 4846–4851. DOI 10.1007/s12205-019-0700-3. [Google Scholar] [CrossRef]
42. Almusallam, A. A., Beshr, H., Maslehuddin, M., Al-Amoudi, O. S. B. (2004). Effect of silica fume on the mechanical properties of low quality coarse aggregate concrete. Cement and Concrete Composites, 26(7), 891–900. DOI 10.1016/j.cemconcomp.2003.09.003. [Google Scholar] [CrossRef]
43. Maslehuddin, M., Sharif, A. M., Shameem, M., Ibrahim, M., Barry, M. S. (2003). Comparison of properties of steel slag and crushed limestone aggregate concretes. Construction and Building Materials, 17, 105–112. DOI 10.1016/S0950-0618(02)00095-8. [Google Scholar] [CrossRef]
44. Savva, P., Ioannou, S., Oikonomopoulou, K., Nicolaides, D., Petrou, M. F. (2021). A mechanical treatment method for recycled aggregates and its effect on recycled aggregate-based concrete. Materials, 14(9), 2186. DOI 10.3390/ma14092186. [Google Scholar] [CrossRef]
45. Wang, X., Yang, X., Ren, J., Han, N., Xing, F. (2021). A novel treatment method for recycled aggregate and the mechanical properties of recycled aggregate concrete. Journal of Materials Research and Technology, 10, 1389–1401. DOI 10.1016/j.jmrt.2020.12.095. [Google Scholar] [CrossRef]
46. Kou, S. C., Poon, C. S. (2012). Enhancing the durability properties of concrete prepared with coarse recycled aggregate. Construction and Building Materials, 35, 69–76. DOI 10.1016/j.conbuildmat.2012.02.032. [Google Scholar] [CrossRef]
47. Yang, K. H., Chung, H. S., Ashour, A. F. (2008). Influence of type and replacement level of recycled aggregates on concrete properties. ACI Materials Journal, 105, 289–296. [Google Scholar]
48. Kazmi, S. M. S., Munir, M. J., Wu, Y. F., Lin, X., Ahmad, M. R. (2021). Investigation of thermal performance of concrete incorporating different types of recycled coarse aggregates. Construction and Building Materials, 270, 121433. DOI 10.1016/j.conbuildmat.2020.121433. [Google Scholar] [CrossRef]
49. Younis, K. H. (2021). Metakaolin modified recycled aggregate concrete containing recycled steel fibers. Materials Today: Proceedings, 45, 4689–4694. [Google Scholar]
50. Sagoe-Crentsil, K. K., Brown, T., Taylor, A. H. (2001). Performance of concrete made with commercially produced coarse recycled concrete aggregate. Cement and Concrete Research, 31, 707–712. DOI 10.1016/S0008-8846(00)00476-2. [Google Scholar] [CrossRef]
51. Malešev, M., Radonjanin, V., Marinković, S. (2010). Recycled concrete as aggregate for structural concrete production. Sustainability, 2(5), 1204–1225. DOI 10.3390/su2051204. [Google Scholar] [CrossRef]
52. Topçu, İ. B., Şengel, S. (2004). Properties of concretes produced with waste concrete aggregate. Cement and Concrete Research, 34(8), 1307–1312. DOI 10.1016/j.cemconres.2003.12.019. [Google Scholar] [CrossRef]
53. Yaba, H. K., Naji, H. S., Younis, K. H., Ibrahim, T. K. (2021). Compressive and flexural strengths of recycled aggregate concrete: Effect of different contents of metakaolin. Materials Today: Proceedings, 45, 4719–4723. [Google Scholar]
54. Zhang, P., Gao, Z., Wang, J., Guo, J., Wang, T. (2022). Influencing factors analysis and optimized prediction model for rheology and flowability of nano-SiO2 and PVA fiber reinforced alkali-activated composites. Journal of Cleaner Production, 366, 132988. DOI 10.1016/j.jclepro.2022.132988. [Google Scholar] [CrossRef]
55. Sim, J., Park, C. (2011). Compressive strength and resistance to chloride ion penetration and carbonation of recycled aggregate concrete with varying amount of fly ash and fine recycled aggregate. Waste Management, 31(11), 2352–2360. DOI 10.1016/j.wasman.2011.06.014. [Google Scholar] [CrossRef]
56. Leite, M. B., Figueire do Filho, J. G. L., Lima, P. R. L. (2013). Workability study of concretes made with recycled mortar aggregate. Materials and Structures, 46(10), 1765–1778. DOI 10.1617/s11527-012-0010-4. [Google Scholar] [CrossRef]
57. Poon, C. S., Shui, Z. H., Lam, L., Fok, H., Kou, S. C. (2004). Influence of moisture states of natural and recycled aggregates on the slump and compressive strength of concrete. Cement and Concrete Research, 34(1), 31–36. DOI 10.1016/S0008-8846(03)00186-8. [Google Scholar] [CrossRef]
58. Tuyan, M., Mardani-Aghabaglou, A., Ramyar, K. (2014). Freeze–thaw resistance, mechanical and transport properties of self-consolidating concrete incorporating coarse recycled concrete aggregate. Materials & Design, 53, 983–991. DOI 10.1016/j.matdes.2013.07.100. [Google Scholar] [CrossRef]
59. Wang, D. C., Noguchi, T., Nozaki, T., Higo, Y. (2021). Investigation of the carbonation performance of cement-based materials under high temperatures. Construction and Building Materials, 272, 121634. DOI 10.1016/j.conbuildmat.2020.121634. [Google Scholar] [CrossRef]
60. Lu, Z., Tan, Q. H., Lin, J. L., Wang, D. C. (2022). Properties investigation of recycled aggregates and concrete modified by accelerated carbonation through increased temperature. Construction and Building Materials, 341, 127813. DOI 10.1016/j.conbuildmat.2022.127813. [Google Scholar] [CrossRef]
61. Tam, V. W. Y., Tam, C. M., Le, K. N. (2007). Removal of cement mortar remains from recycled aggregate using pre-soaking approaches. Resources, Conservation and Recycling, 50(1), 82–101. DOI 10.1016/j.resconrec.2006.05.012. [Google Scholar] [CrossRef]
62. Wang, J., Vandevyvere, B., Vanhessche, S., Schoon, J., Boon, N. et al. (2017). Microbial carbonate precipitation for the improvement of quality of recycled aggregates. Journal of Cleaner Production, 156, 355–366. DOI 10.1016/j.jclepro.2017.04.051. [Google Scholar] [CrossRef]
63. Pan, Z., Zhou, J., Jiang, X., Xu, Y., Jin, R. et al. (2019). Investigating the effects of steel slag powder on the properties of self-compacting concrete with recycled aggregates. Construction and Building Materials, 200, 570–577. DOI 10.1016/j.conbuildmat.2018.12.150. [Google Scholar] [CrossRef]
64. Sheen, Y. N., Le, D. H., Sun, T. H. (2015). Greener self-compacting concrete using stainless steel reducing slag. Construction and Building Materials, 82, 341–350. DOI 10.1016/j.conbuildmat.2015.02.081. [Google Scholar] [CrossRef]
65. Amer, I., Kohail, M., El-Feky, M. S., Rashad, A., Khalaf, M. A. (2021). Characterization of alkali-activated hybrid slag/cement concrete. Ain Shams Engineering Journal, 12(1), 135–144. DOI 10.1016/j.asej.2020.08.003. [Google Scholar] [CrossRef]
66. Majhi, R. K., Nayak, A. N., Mukharjee, B. B. (2018). Development of sustainable concrete using recycled coarse aggregate and ground granulated blast furnace slag. Construction and Building Materials, 159, 417–430. DOI 10.1016/j.conbuildmat.2017.10.118. [Google Scholar] [CrossRef]
67. Han, Q. Y., Zhang, P., Wu, J. J., Jing, Y. T., Zhang, D. et al. (2022). Comprehensive review of the properties of fly ash-based geopolymer with additive of nano-SiO2. Nanotechnology Reviews, 11(1), 1478–1498. DOI 10.1515/ntrev-2022-0092. [Google Scholar] [CrossRef]
68. Zhang, X. M., Zhang, P., Wang, T. Y., Zheng, Y., Qiu, L. H. et al. (2022). Compressive strength and anti-chloride ion penetration assessment of geopolymer mortar merging PVA fiber and nano-SiO2 using RBF-BP composite neural network. Nanotechnology Reviews, 11(1), 1181–1192. DOI 10.1515/ntrev-2022-0069. [Google Scholar] [CrossRef]
69. Butler, L., West, J. S., Tighe, S. L. (2011). The effect of recycled concrete aggregate properties on the bond strength between RCA concrete and steel reinforcement. Cement and Concrete Research, 41(10), 1037–1049. DOI 10.1016/j.cemconres.2011.06.004. [Google Scholar] [CrossRef]
70. Rahal, K. (2007). Mechanical properties of concrete with recycled coarse aggregate. Building and Environment, 42(1), 407–415. DOI 10.1016/j.buildenv.2005.07.033. [Google Scholar] [CrossRef]
71. Zheng, Y., Zhuo, J., Zhang, Y., Zhang, P. (2022). Mechanical properties and microstructure of nano-SiO2 and basalt-fiber-reinforced recycled aggregate concrete. Nanotechnology Reviews, 11(1), 2169–2189. DOI 10.1515/ntrev-2022-0134. [Google Scholar] [CrossRef]
72. Jalilifar, H., Sajedi, F. (2021). Micro-structural analysis of recycled concretes made with recycled coarse concrete aggregates. Construction and Building Materials, 267, 121041. DOI 10.1016/j.conbuildmat.2020.121041. [Google Scholar] [CrossRef]
73. Katz, A. (2004). Treatments for the improvement of recycled aggregate. Journal of Materials in Civil Engineering, 16(6), 597–603. DOI 10.1061/(ASCE)0899-1561(2004)16:6(597). [Google Scholar] [CrossRef]
74. Majhi, R. K., Nayak, A. N. (2019). Bond, durability and microstructural characteristics of ground granulated blast furnace slag based recycled aggregate concrete. Construction and Building Materials, 212, 578–595. DOI 10.1016/j.conbuildmat.2019.04.017. [Google Scholar] [CrossRef]
75. Fonseca, N., de Brito, J., Evangelista, L. (2011). The influence of curing conditions on the mechanical performance of concrete made with recycled concrete waste. Cement and Concrete Composites, 33(6), 637–643. DOI 10.1016/j.cemconcomp.2011.04.002. [Google Scholar] [CrossRef]
76. Etxeberria, M., Vázquez, E., Marí, A., Barra, M. (2007). Influence of amount of recycled coarse aggregates and production process on properties of recycled aggregate concrete. Cement and Concrete Research, 37(5), 735–742. DOI 10.1016/j.cemconres.2007.02.002. [Google Scholar] [CrossRef]
77. Bai, G., Zhu, C., Liu, C., Liu, B. (2020). An evaluation of the recycled aggregate characteristics and the recycled aggregate concrete mechanical properties. Construction and Building Materials, 240, 117978. DOI 10.1016/j.conbuildmat.2019.117978. [Google Scholar] [CrossRef]
78. Huang, J. G., Zou, C. Y., Sun, D., Yang, B., Yan, J. C. (2021). Effect of recycled fine aggregates on alkali-activated slag concrete properties. Structures, 30, 89–99. DOI 10.1016/j.istruc.2020.12.064. [Google Scholar] [CrossRef]
79. Younis, K. H., Pilakoutas, K. (2013). Strength prediction model and methods for improving recycled aggregate concrete. Construction and Building Materials, 49, 688–701. DOI 10.1016/j.conbuildmat.2013.09.003. [Google Scholar] [CrossRef]
80. Liu, S., Wei, X., Wang, W., Lu, S., Ma, F. (2014). Influence of recycled coarse aggregate on recycled concrete performance. Building Structure, 44(14), 17–20. [Google Scholar]
81. Peng, Q., Wang, L., Lu, Q. (2018). Influence of recycled coarse aggregate replacement percentage on fatigue performance of recycled aggregate concrete. Construction and Building Materials, 169, 347–353. [Google Scholar]
82. Luo, S., Ye, S., Xiao, J., Zheng, J., Zhu, Y. (2018). Carbonated recycled coarse aggregate and uniaxial compressive stress-strain relation of recycled aggregate concrete. Construction and Building Materials, 188, 956–965. [Google Scholar]
83. Panda, K. C., Bal, P. K. (2013). Properties of self compacting concrete using recycled coarse aggregate. Procedia Engineering, 51, 159–164. [Google Scholar]
84. Ali, R., Hamid, R. (2015). Workability and compressive strength of recycled concrete waste aggregate concrete. Applied Mechanics and Materials, 754–755, 417–420. [Google Scholar]
85. Wang, W., Ling, H., Wang, X. N., Xia, T., Wang, D. Z. et al. (2008). Experimental study on compressive strength of recycled aggregate concrete. Key Engineering Materials, 385–387, 381–384. [Google Scholar]
86. Behera, M., Bhattacharyya, S. K., Minocha, A. K., Deoliya, R., Maiti, S. (2014). Recycled aggregate from C&D waste & its use in concrete–A breakthrough towards sustainability in construction sector: A review. Construction and Building Materials, 68, 501–516. [Google Scholar]
87. Qasrawi, H. (2014). The use of steel slag aggregate to enhance the mechanical properties of recycled aggregate concrete and retain the environment. Construction and Building Materials, 54, 298–304. [Google Scholar]
88. Chen, H. J., Yen, T., Chen, K. H. (2003). The use of building rubbles in concrete and mortar. Journal of the Chinese Institute of Engineers, 26(2), 227–236. [Google Scholar]
89. Revilla-Cuesta, V., Skaf, M., Serrano-López, R., Ortega-López, V. (2021). Models for compressive strength estimation through non-destructive testing of highly self-compacting concrete containing recycled concrete aggregate and slag-based binder. Construction and Building Materials, 280, 122454. [Google Scholar]
90. Lothenbach, B., Scrivener, K., Hooton, R. D. (2011). Supplementary cementitious materials. Cement and Concrete Research, 41(12), 1244–1256. [Google Scholar]
91. Amran, Y. H. M., Alyousef, R., Alabduljabbar, H., El-Zeadani, M. (2020). Clean production and properties of geopolymer concrete; A review. Journal of Cleaner Production, 251, 119679. DOI 10.1016/j.jclepro.2019.119679. [Google Scholar] [CrossRef]
92. Wu, K., Hu, Y., Zhang, L., Su, Y., Han, J. et al. (2020). Quantitative evaluation of interfacial transition zone of sustainable concrete with recycled and steel slag as aggregate. Structural Concrete, 22(2), 926–938. DOI 10.1002/suco.202000135. [Google Scholar] [CrossRef]
93. Brand, A. S., Roesler, J. R. (2015). Steel furnace slag aggregate expansion and hardened concrete properties. Cement and Concrete Composites, 60, 1–9. DOI 10.1016/j.cemconcomp.2015.04.006. [Google Scholar] [CrossRef]
94. Pellegrino, C., Gaddo, V. (2009). Mechanical and durability characteristics of concrete containing EAF slag as aggregate. Cement and Concrete Composites, 31(9), 663–671. DOI 10.1016/j.cemconcomp.2009.05.006. [Google Scholar] [CrossRef]
95. Papayianni, I., Anastasiou, E. (2010). Production of high-strength concrete using high volume of industrial by-products. Construction and Building Materials, 24(8), 1412–1417. DOI 10.1016/j.conbuildmat.2010.01.016. [Google Scholar] [CrossRef]
96. Pellegrino, C., Cavagnis, P., Faleschini, F., Brunelli, K. (2013). Properties of concretes with black/oxidizing electric arc furnace slag aggregate. Cement and Concrete Composites, 37, 232–240. DOI 10.1016/j.cemconcomp.2012.09.001. [Google Scholar] [CrossRef]
97. Papayianni, I., Anastasiou, E. (2011). Concrete incorporating high-calcium fly ash and EAF slag aggregates. Magazine of Concrete Research, 63(8), 597–604. DOI 10.1680/macr.2011.63.8.597. [Google Scholar] [CrossRef]
98. Etxeberria, M., Pacheco, C., Meneses, J. M., Berridi, I. (2010). Properties of concrete using metallurgical industrial by-products as aggregates. Construction and Building Materials, 24(9), 1594–1600. DOI 10.1016/j.conbuildmat.2010.02.034. [Google Scholar] [CrossRef]
99. Chunlin, L., Kunpeng, Z., Depeng, C. (2011). Possibility of concrete prepared with steel slag as fine and coarse aggregates: A preliminary study. Procedia Engineering, 24, 412–416. DOI 10.1016/j.proeng.2011.11.2667. [Google Scholar] [CrossRef]
100. Praveen Kumar, K., Radhakrishna, Ramesh, P. S., Chethan Kumar, S. (2021). Properties of sustainable concrete with processed slag sand. In: Advances in sustainable construction materials, pp. 821–830. New Orleans, LA, USA. [Google Scholar]
101. Roslan, N. H., Ismail, M., Abdul-Majid, Z., Ghoreishiamiri, S., Muhammad, B. (2016). Performance of steel slag and steel sludge in concrete. Construction and Building Materials, 104, 16–24. DOI 10.1016/j.conbuildmat.2015.12.008. [Google Scholar] [CrossRef]
102. Qasrawi, H., Shalabi, F., Asi, I. (2009). Use of low CaO unprocessed steel slag in concrete as fine aggregate. Construction and Building Materials, 23(2), 1118–1125. DOI 10.1016/j.conbuildmat.2008.06.003. [Google Scholar] [CrossRef]
103. Nguyen, T. T., Phan, D. H., Mai, H. H., Nguyen, D. L. (2020). Investigation on compressive characteristics of steel-slag concrete. Materials, 13(8), 1928. DOI 10.3390/ma13081928. [Google Scholar] [CrossRef]
104. Bashkatov, N. N. (2020). Utilization of ferrochrome slag in concrete production. IOP Conference Series: Materials Science and Engineering, 966, 012053. DOI 10.1088/1757-899X/966/1/012053. [Google Scholar] [CrossRef]
105. Anastasiou, E., Georgiadis Filikas, K., Stefanidou, M. (2014). Utilization of fine recycled aggregates in concrete with fly ash and steel slag. Construction and Building Materials, 50, 154–161. DOI 10.1016/j.conbuildmat.2013.09.037. [Google Scholar] [CrossRef]
106. Wang, Q. A., Yan, P. Y., Han, S. (2011). The influence of steel slag on the hydration of cement during the hydration process of complex binder. Science China-Technological Sciences, 54(2), 388–394. DOI 10.1007/s11431-010-4204-0. [Google Scholar] [CrossRef]
107. El-Hawary, M., Al-Yaqout, A., Nouh, K. (2019). Durability of recycled aggregate concrete incorporating slag. Proceedings of the Institution of Civil Engineers-Waste and Resource Management, 172(4), 107–117. DOI 10.1680/jwarm.18.00025. [Google Scholar] [CrossRef]
108. Lin, S. K., Wu, C. H. (2021). Improvement of bond strength and durability of recycled aggregate concrete incorporating high volume blast furnace slag. Materials, 14(13), 3708. DOI 10.3390/ma14133708. [Google Scholar] [CrossRef]
109. Kathirvel, P., Kaliyaperumal, S. R. M. (2016). Influence of recycled concrete aggregates on the flexural properties of reinforced alkali activated slag concrete. Construction and Building Materials, 102, 51–58. DOI 10.1016/j.conbuildmat.2015.10.148. [Google Scholar] [CrossRef]
110. Zhang, P., Kang, L., Zheng, Y., Zhang, T., Zhang, B. (2022). Influence of SiO2/Na2O molar ratio on mechanical properties and durability of metakaolin-fly ash blend alkali-activated sustainable mortar incorporating manufactured sand. Journal of Materials Research and Technology, 18, 3553–3563. DOI 10.1016/j.jmrt.2022.04.041. [Google Scholar] [CrossRef]
111. Sadeghi-Nik, A., Berenjian, J., Alimohammadi, S., Lotfi-Omran, O., Sadeghi-Nik, A. et al. (2018). The effect of recycled concrete aggregates and metakaolin on the mechanical properties of self-compacting concrete containing nanoparticles. Iranian Journal of Science and Technology, Transactions of Civil Engineering, 43(S1), 503–515. [Google Scholar]
112. Duan, Z., Singh, A., Xiao, J., Hou, S. (2020). Combined use of recycled powder and recycled coarse aggregate derived from construction and demolition waste in self-compacting concrete. Construction and Building Materials, 254, 119323. DOI 10.1016/j.conbuildmat.2020.119323. [Google Scholar] [CrossRef]
113. Bahrami, N., Zohrabi, M., Mahmoudy, S. A., Akbari, M. (2020). Optimum recycled concrete aggregate and micro-silica content in self-compacting concrete: Rheological, mechanical and microstructural properties. Journal of Building Engineering, 31, 101361. DOI 10.1016/j.jobe.2020.101361. [Google Scholar] [CrossRef]
114. Mavroulidou, M., Shah, S. (2021). Alkali-activated slag concrete with paper industry waste. Waste Management & Research, 39(3), 466–472. DOI 10.1177/0734242X20983890. [Google Scholar] [CrossRef]
115. Qi, A., Liu, X., Wang, Z., Chen, Z. (2020). Mechanical properties of the concrete containing ferronickel slag and blast furnace slag powder. Construction and Building Materials, 231, 117120. DOI 10.1016/j.conbuildmat.2019.117120. [Google Scholar] [CrossRef]
116. Qin, Y., Chen, J., Li, Z., Zhang, Y. (2019). The mechanical properties of recycled coarse aggregate concrete with lithium slag. Advances in Materials Science and Engineering, 2019, 1–12. DOI 10.1155/2019/8974625. [Google Scholar] [CrossRef]
117. Khan, M. T., Jahan, I., Amanat, K. M. (2020). Splitting tensile strength of natural aggregates, recycled aggregates and brick chips concrete. Proceedings of the Institution of Civil Engineers-Construction Materials, 173(2), 79–88. DOI 10.1680/jcoma.18.00049. [Google Scholar] [CrossRef]
118. Arioglu, N., Girgin, Z. C., Arioglu, E. (2006). Evaluation of ratio between splitting tensile strength and compressive strength for concretes up to 120 MPa and its application in strength criterion. ACI Materials Journal, 103(1), 18–24. [Google Scholar]
119. Bhanja, S., Sengupta, B. (2005). Influence of silica fume on the tensile strength of concrete. Cement and Concrete Research, 35(4), 743–747. DOI 10.1016/j.cemconres.2004.05.024. [Google Scholar] [CrossRef]
120. Larrard, F. D., Malier, Y. (1992). Engineering properties of very high performance concretes. In: Malier, Y. (Ed.High performance concrete: From material to structure. London: E & FN Spon, Chapman and Hall. [Google Scholar]
121. Khoshkenari, A. G., Shafigh, P., Moghimi, M., Mahmud, H. B. (2014). The role of 0–2 mm fine recycled concrete aggregate on the compressive and splitting tensile strengths of recycled concrete aggregate concrete. Materials & Design, 64, 345–354. DOI 10.1016/j.matdes.2014.07.048. [Google Scholar] [CrossRef]
122. Park, W. J., Noguchi, T., Shin, S. H., Oh, D. Y. (2015). Modulus of elasticity of recycled aggregate concrete. Magazine of Concrete Research, 67(11), 585–591. DOI 10.1680/macr.14.00213. [Google Scholar] [CrossRef]
123. Jacintho, A., Cavaliere, I. S. G., Pimentel, L. L., Forti, N. C. S. (2020). Modulus and strength of concretes with alternative materials. Materials, 13(19), 4378. DOI 10.3390/ma13194378. [Google Scholar] [CrossRef]
124. El-Hassan, H., Medljy, J., El-Maaddawy, T. (2021). Properties of steel fiber-reinforced alkali-activated slag concrete made with recycled concrete aggregates and dune sand. Sustainability, 13(14), 8017. DOI 10.3390/su13148017. [Google Scholar] [CrossRef]
125. Soldado, E., Antunes, A., Costa, H., do Carmo, R., Julio, E. (2021). Influence of pozzolan, slag and recycled aggregates on the mechanical and durability properties of low cement concrete. Materials, 14(15), 4173. DOI 10.3390/ma14154173. [Google Scholar] [CrossRef]
126. Gholampour, A., Zheng, J., Ozbakkaloglu, T. (2021). Development of waste-based concretes containing foundry sand, recycled fine aggregate, ground granulated blast furnace slag and fly ash. Construction and Building Materials, 267, 121004. DOI 10.1016/j.conbuildmat.2020.121004. [Google Scholar] [CrossRef]
127. El-Hawary, M., Al-Yaqout, A., Elsayed, K. (2021). Freezing and thawing cycles: Effect on recycled aggregate concrete including slag. International Journal of Sustainable Engineering, 14(4), 800–808. DOI 10.1080/19397038.2021.1886374. [Google Scholar] [CrossRef]
128. Berndt, M. L. (2009). Properties of sustainable concrete containing fly ash, slag and recycled concrete aggregate. Construction and Building Materials, 23(7), 2606–2613. DOI 10.1016/j.conbuildmat.2009.02.011. [Google Scholar] [CrossRef]
129. Yuan, H., Zhu, L., Wang, X., Yang, H. (2022). Effect of microstructure on the mechanical properties of steel fiber-reinforced recycled concretes. Materials, 15(11), 4018. DOI 10.3390/ma15114018. [Google Scholar] [CrossRef]
130. Tošić, N., Torrenti, J. M., Sedran, T., Ignjatović, I. (2020). Toward a codified design of recycled aggregate concrete structures: Background for the new fib model code 2020 and eurocode 2. Structural Concrete, 22(5), 2916–2938. [Google Scholar]
131. Singh, N., Arya, S., Mithul Raj, M. (2019). Assessing the performance of self-compacting concrete made with recycled concrete aggregates and coal bottom ash using ultrasonic pulse velocity. Recycled Waste Materials, 32, 169–178. [Google Scholar]
132. Cho, Y. S., Baek, S. K., Lee, Y. T., Kim, S. H., Park, J. H. et al. (2013). Estimation of compressive strength of high-strength concrete with recycled aggregate using ultrasonic pulse velocity method. Advanced Materials Research, 680, 226–229. DOI 10.4028/www.scientific.net/AMR.680.226. [Google Scholar] [CrossRef]
133. Panesar, D. K., Chidiac, S. E. (2007). Ultrasonic pulse velocity for determining the early age properties of dry-cast concrete containing ground granulated blast-furnace slag. Canadian Journal of Civil Engineering, 34(5), 682–685. DOI 10.1139/l07-039. [Google Scholar] [CrossRef]
134. Nanayakkara, O., Gunasekara, C., Sandanayake, M., Law, D. W., Nguyen, K. et al. (2021). Alkali activated slag concrete incorporating recycled aggregate concrete: Long term performance and sustainability aspect. Construction and Building Materials, 271, 121512. DOI 10.1016/j.conbuildmat.2020.121512. [Google Scholar] [CrossRef]
135. Saha, A. K., Majhi, S., Sarker, P. K., Mukherjee, A., Siddika, A. et al. (2021). Non-destructive prediction of strength of concrete made by lightweight recycled aggregates and nickel slag. Journal of Building Engineering, 33, 101614. DOI 10.1016/j.jobe.2020.101614. [Google Scholar] [CrossRef]
136. Hong, S. U., Kim, S. H., Lee, Y. T. (2014). Estimation of compressive strength of recycled aggregate high strength concrete using ultrasonic pulse velocity. Key Engineering Materials, 605, 147–150. DOI 10.4028/www.scientific.net/KEM.605.147. [Google Scholar] [CrossRef]
Cite This Article
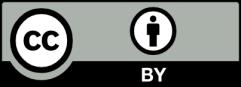
This work is licensed under a Creative Commons Attribution 4.0 International License , which permits unrestricted use, distribution, and reproduction in any medium, provided the original work is properly cited.