Open Access
ARTICLE
Phosphorus Containing Rubber Seed oil as a Flame Retardant Plasticizer for Polyvinyl Chloride
1 Yellow River Conservancy Technical Institute, Kaifeng, 475004, China
2 Henan Engineering Technology Research Center of Green Coating Materials, Kaifeng, 475004, China
* Corresponding Author: Hongying Chu. Email:
(This article belongs to the Special Issue: Renewable Biomass as a Platform for Preparing Green Chemistry)
Journal of Renewable Materials 2023, 11(4), 1731-1743. https://doi.org/10.32604/jrm.2022.024160
Received 28 May 2022; Accepted 18 July 2022; Issue published 01 December 2022
Abstract
The application of phthalate plasticizers has been restricted around the world due to their poor migration and potential harm to the human body. Hence, producing functional bio-based plasticizers via exploiting clean and reusable resources meets the satisfaction of current demands. In this study, flame-retardant rubber seed oil-based plasticize (FRP) was prepared via epoxidation reaction and ring opening addition reactions, which was used as a flame-resistant plasticizer for polyvinyl chloride to replace petroleum-based phthalate plasticizer. When DOP was replaced with FRP, the torque of PVC blends increased from 11.4 to 18.4 N⋅m, the LOI value increased from 24.3% for PVC-FRP-0% to 33.1% for PVC-FRP-20. The THR value diminished from 39 MJ/m2 (pertaining to PVC-FRC-0) to 22 MJ/m2 Tg increased from 23°C to 47°C, the weight loss of plasticized PVC blends significantly reduced from 22.6% to 2.8% in leaching tests. The study provided a new way to prepare flame retardant plasticizer using rubber seed oil as raw material.Graphic Abstract
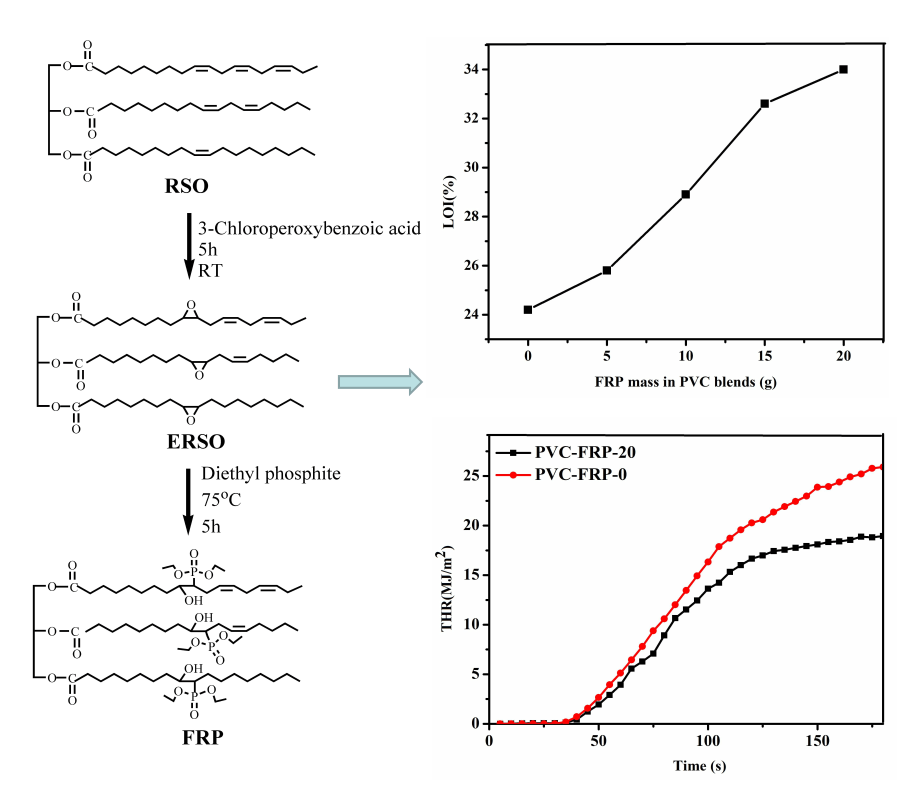
Keywords
Nomenclature
DOP | Dioctyl Phthalate |
FRC | Flame-retardant rubber seed oil-based plasticizer |
PVC | Polyvinyl chloride |
RSO | Rubber seed oil |
LOI | Limiting oxygen index |
ERSO | Epoxy rubber seed oil |
HRR | Heat release rate |
THR | Total heat release (THR) |
Td | Temperature at 5% weight loss |
T10 | Temperature at 10% weight loss |
T50 | Temperature at 50% weight loss |
Tg | Glass transition temperature |
Plasticizer has been widely used in the processing of polymers such as polyvinyl chloride (PVC) plastics. The most studied, most abundant, and perhaps most well-known plasticizers that are also emerging contaminants are phthalate plasticizer. The phthalate plasticizer derived from petroleum is the most widely used plasticizer in industrial production, but its application is increasingly limited in view of its potential menace to the surrounding environment even human health [1–3]. With the increasingly stringent global environmental protection regulations, environmental protection and safety have become a significant trend in the development of the plasticizer industry. Bio-based plasticizers specially used in the fields of medicine or health equipment, packaging, as well as environmentally friendly plasticizers with enhanced mechanical properties have been continuously developed [4–8]. Many bio-based plasticizers have been reported including isosorbide [9], cardanol [10–12], castor oil [13–15], lactic acid [16,17], and many kinds of vegetable oils [18–20].
Rubber seed oil (RSO) is extracted from rubber seed. The main component of RSO is triglyceride [5,21]. Bio-based plasticizer from RSO can be synthesized via esterification, epoxidation, and halogenation hydrolyzation reactions. Not only can the polar groups inside, including ester groups and ether groups, enhance the compatibility of plasticized PVC materials, but they also optimize physical property of PVC products in some respects [22,23]. Thus, reactions on RSO are carried out in order for the bio-based plasticizers synthesis, which can be taken as a promising and strategic research.
In this study, the rubber seed oil with rich reserves, wide sources and low price was selected as the raw material. The rubber seed oil was modified by epoxidation and ring opening addition reaction to synthesize the bio-based plasticizer products, which were used to replace the petroleum-based phthalate plasticizer; The mechanical properties, thermal properties, processability, flame-retardancy and extraction resistance of plasticized PVC blends were studied. The effect of partial substitution of the prepared oil-based plasticizer for phthalate plasticizers is studied to reduce the dependence of the plastic additives industry on petrochemical products.
Dioctyl phthalate (DOP, 98%), diethyl phosphite (99%), N-hexane (97%), toluene (98%), triphenyphosphine (95%), dichloromethane (99%), ethyl acetate (99%), calcium stearate (Zn 10%–12%) and sodium chloride (99.5%) were bought from Aladdin reagent (Shanghai) Co., Ltd. (China). S-1100 PVC resin (no additives) was provided by Jinling Chemical Industry Co. (Nanjing, China). Rubber seed oil (RSO) was provised by Kuming Jinning Chemical Industry Co., Ltd. (China).
2.2 Synthesis of Epoxy Rubber Seed Oil (ERSO)
RSO was dissolved in dichloromethane and put in the a round bottom flask, which was put in the ice bath. 3-Chloroperoxybenzoic acid was dropped in the mixture (mole ratio of double bonds to 3-Chloroperoxybenzoic acid is 1:0.5). The reaction was kept stirring for 5 h at room temperature to obtain the raw product. The obtained raw product was dissolved in dichloromethane and washed with brine and distilled water, then dried by anhydrous magnesium sulfate (MgSO4) and purified using silica gel column chromatography to obtain ERSO.
2.3 Synthesis of Flame-Retardant Rubber Seed Oil-Based Plasticizer (FRP)
ERSO (20 g) was dissolved in toluene (16 g), all of which were blended in a three-necked round-bottom flask. The mix of diethyl phosphate (6 g), triphenyphosphine (0.02 g) and toluene (16 g) were also put in the flask within 40 min at room temperature. Then, a 4 h-stir at 75°C was carried out. The reaction mixture was dropped to room temperature with sodium hydroxide (NaOH) solution and washed until pH = 7. FRP was obtained via removing water by rotary-evaporation, after a 3-time-wash through distilled water. The synthesis of FRP was showed in Fig. 1.
Figure 1: Synthesis of FRP
2.4 Preparation of FRP-Plasticized PVC Blends
FRP-Plasticized PVC blends were prepared by melt processing and the formulations were illustrated in Table 1. Then, further extrusion into strips like dumbbell or rectangular was necessary for subsequent tests.
RSO, ERSO and FRP were respectively illustrated through Fourier transform infrared spectrometer (FT-IR) (Nicolet 6700), with the chosen wavelength between 4000 and 500 cm−1.1H nuclear magnetic resonance (1H NMR) spectrums were presented with the solvent of CDCl3 and internal standard of tetramethylsilane (TMS), respectively. Combustion tests were carried out according to GB/T 2406.1-2008. The FRP-modified PVC samples were designed into 80 mm × 10 mm × 4 mm. FTT200 cone calorimeter was used to analyze the combustion properties of samples that were cut into 100 mm × 100 mm× 2 mm, and ISO-5660 standard procedures would be referenced. The thermogravimetric analysis (TGA) was detected with surrounding N2 in the flow rate of 50 mL/min. The heating rate of PVC blends was set to 10 °C/min from the beginning of 50°C to the final 600°C. The leaching tests related to plasticizers were examined in term of ASTMD1239-98 with N-hexane as the chosen solvent. The PVC blends were submerged into solvents at the temperature of 30°C for one week. Thereafter, the samples were removed and the surface solvent was wiped off. Then further drying was conducted at 50°C for whole day. The migration rate was calculated in term of the following Eq. (1):
Thereinto, W1 and W2 represent the front and rear weight, respectively.
In addition, the tensile rate of electronic tensile testing machine was set to 20 mm/min, and the dynamic mechanical analysis (DMA) was brought into effect to investigate the specific glass transition temperature (Tg), from −80°C to 100°C at a heating speed of 3 °C/min. Limiting oxygen index (LOI) values were measured on a JF-3 oxygen index measuring instrument.
FTIR spectra of RSO, ERSO and FRP were shown in Fig. 2. The characteristic peaks around 3007 cm−1 were associated with -CH=CH- in RSO [24,25]. As Compared with the spectra of ERSO, the characteristic peak of CH=CH- vanished, opposite to the -C-O-C vibration which could be observed at approximately 972 and 1062 cm−1. All mentioned indicated that the -C=C- double bonds were converted into epoxy groups [26,27]. The peak at 1032 cm−1 was attributed to -P-O-CH- symmetric bending vibration, and -OH was observed at 3470 cm−1 in the FT-IR of FRP. The epoxy group at 972 and 1062 cm−1 cannot be observed in the FT-IR of FRP [28,29], which means that the reaction between P-OH and ERSO was accomplished.
Figure 2: FT-IR of RSO, ERSO and FRP
The 1H NMR spectrums pertaining to RSO, ERSO and FRP are exhibited in Fig. 3. The strong peak at δ = 5.28 ppm is attributed to the protons of -CH=CH- in RSO [25,26]. When epoxidation was finished, the peak at δ = 5.28 ppm became weak in the 1H NMR spectrum of ERSO, because the epoxidation reaction was not complete, and an emerged peak at 2.95–3.20 ppm was assigned to protons on the epoxy groups of ERSO [26,27], which indicated that some -CH=CH- bonds of RSO were converted into epoxy groups. In the 1H NMR spectrum of FRP, a new proton signal of -P-O-CH2- appeared at δ = 2.3 ppm [28,29], and the protons signals in the 5.28 ppm associated with -C-O-C- bonds showed weaker than ERSO, which indicated that chemical structure of FRP contains phosphate groups, which indicated that FRP was synthesized successfully.
Figure 3: 1H NMR of RSO, ERSO and FRP
3.2 Performance of Plasticized PVC Blends
The melting behavior was confirmed in the Haake chamber by gathering the processing data during the mix. Fig. 4 presents the torque values relevant to the proportion of plasticizer for the 5 min processing time. When more DOP was replaced with FRP, the torque of PVC blends increased from 11.4 to 18.4 N⋅m, respectively, corresponding to PVC-FRP-0 and PVC-FRP-20. In other words, 61% augmentation could be achieved, showing disadvantages in conduction of thermoplastic processing pertains to PVC blends.
Figure 4: The torque data of plasticized PVC blends
FRP contains many flame-resistant phosphate groups, which could be used as a alternative to DOP as the flame-resistant plasticizer. The flame-resistance of plasticized PVC blends was conducted by the LOI tests and the variation with regard to FRP content was described in Fig. 5. When DOP was replaced with FRP in plasticized PVC blends, the LOI value increased from 24.3% for PVC-FRP-0% to 33.1% for PVC-FRP-20. Only the latter one exhibited greater value than 26.0%, to a certain extent, displaying self-blackout capacity. Generally, FRP is not suitable to be considered as a preferable flame retardant plasticizer in the PVC blends [30,31].
Figure 5: LOI data for plasticized PVC blends
PVC chemical structure contains a large amount of chlorine, which makes it hard to burn. However, it will combust and release much heat when PVC products plasticized with DOP, being blended into PVC. Fig. 6 showed the heat release rate (HRR) curves of plasticized PVC blends. There exists a notable difference in HRR curves between PVC-FRC-0 and PVC-FRC-20. Almost all HRR curve of PVC-FRC-0 is higher than PVC-FRC-20, which indicats that PVC-FRC-0 released heat faster than PVC-FRC-20. Once ignited, PVC-FRC-0 produced flammable volatiles and released a lot of heat. However, the PPVC-FRC-20 was harder to burn than PVC-FRC-20. Thermal degradation of phosphate ester groups containing FRP produces a large amount of phosphoric acid and polyphosphate [31–33], which can promote carbon formation by removing water from FRP. The char residue will block heat transfer and the pyrolysis process. In addition, the total heat release (THR) curves of plasticized PVC blends were shown in Fig. 7. It can be found that the whole THR curve of PVC-FRC-0 was higher than PVC-FRC-20, which indicated that PVC-FRC-0 released more heat than PVC-FRC-20. The THR value decreased from 39 MJ/m2 (pertaining to PVC-FRC-0) to 22 MJ/m2 (pertaining to PVC-FRC-20) when 20 phr DOP was replaced with FRP in the plasticized PVC blends. All mentioned above revealed that FRP had capacity of improving the flame retardancy.
Figure 6: HRR curves of plasticized PVC blends
Figure 7: Total heat released of FRP-plasticized PVC blends
The thermogravimetric loss data of plasticized PVC blends with different mass of plasticizers were shown in the Figs. 8 and 9, and Table 2. As is demonstrated in the Fig. 8, the degradation temperature (Td: Temperature at 5% weight loss) of PVC blends increased with more DOP replaced by FRP, from the initial content of 5% FRP. When PVC blends plasticized with 40 phr DOP, Td is 252°C, while the Td reached 272°C when PVC blends plasticized with 20 phr DOP and 20 phr FRP. In addition, the temperature at 10% weight loss (T10) and the 50% one (T50) showed the same increasing trend when DOP was replaced with FRP. This indicated that FRP can improve thermal stability of PVC blends. All plasticized PVC blends presented 3 stages in N2 with regard to thermal degradation curves. None of the samples illustrated conspicuous weight loss until approaching 150°C. At stage one (from 150°C to 320°C), the weight loss process could be ascribed to the FRP migration together with the PVC dechlorination [34,35]. The temperature range belonging to the second stage was 320°C–450°C, which is mainly understood as the conversion process of conjugated olefins to aromatics. Finally curves between 450°C and 600°C corresponding to the fact that polyenes were cracked into olefin, as the third stage came out [34,35]. FRP had a considerable effect on preventing the weight loss of plasticized PVC blends. There exist numerous polar groups in plasticizer molecules that form hydrogen bonds with α-H of the PVC chain, deferring the PVC dechlorination [36,37].
Figure 8: TGA curves of FRP-plasticized PVC blends
Figure 9: DTG curves of FRP-plasticized PVC blends
Tg partly mirrors the plasticizing property of the plasticizers. Fig. 10 shows the DMA curves of plasticized PVC blends containing different masses of FRP. Each curve has only a single peak, corresponding to a homogeneous system. It has been reported that the Tg value of the original PVC is approximately 85.8°C, indicating that adding DOP or FRP to PVC can prominently reduce the Tg value. When DOP was replaced with FRP gradually, Tg increased from 23°C to 47°C, which indicated that plasticized ability of FRP was lower than DOP.
Figure 10: DMA curves of FRP-plasticized PVC blends
Extraction resistance is an important quality in evaluating the migration property of plasticizers. The excellent extraction resistance can maintain the long-term stability of mechanical, thermal, electrical properties and flame-retardancy of plasticized polymer products, and prevent the potential threat to human health caused by the migration of plasticizers in the use of food and medical devices. Fig. 11 manifests the weight loss of plasticized PVC with DOP and FRP in N-hexane, the advantage of using N-hexane as solvent is that organic solvent can accelerate the migration of plasticizer, and then its migration performance can be evaluated in a short time [5]. With the gradual decrease of DOP and increase of FRP in PVC blends, the weight loss of plasticized PVC blends significantly reduced from 22.6% to 2.8%. FRP showed superior solvent extraction resistance than that of DOP. FRP with a larger relative molecular weight and higher branching degree has better migration resistance than DOP.
Figure 11: Migration property of FRP
The tensile test was conducted at the temperature of 25°C to appraise FRP’s plasticizing effect, with the detailed results being exhibited in Table 3. The affixion of plasticizer usually increases elongation at break and decreases the tensile strength of plasticized PVC materials. Furthermore, when DOP was replaced gradually with FRP, the elongation at break of plasticized PVC blends decreased from 450% to 19%, seeing an opposite trend to the tensile strength, from 12.3 to 28.9 MPa. The results indicated though the ester groups and phosphate groups in the structure of FRP have the lubrication effect on PVC chains, making plasticized PVC blends more flexible [38,39], but FRP showed a lower plasticizing effect than DOP.
In this study, phosphorus-containing rubber seed oil was prepared via epoxidation reaction and ring opening addition reactions, which was used as a flame-retardant polyvinyl chloride plasticizer to replace petroleum-based phthalate one. In plasticized PVC blends, the torque of PVC blends increased from 11.4 to 18.4 N⋅m after DOP was replaced by FRP at the content of 20 phr, which indicate the addition of FRP is unfavorable to the thermoplastic processing process. But the LOI value, at the same time, increased from 24.3% to 33.1%, and the THR data decreased from 39 to 22 MJ/m2, which indicated that FRP in the plasticized PVC blends reduced the flammability. As a result of hydrogen bond formation, with the coaction of α-H in PVC molecular chains and polar groups in plasticizers, the dichlorination of PVC will be intervened to delay. With the addition of DOP or FRP, PVC can significantly raise the Tg value from 23°C to 47°C. It means the plasticized ability of FRP was lower than DOP, though FRP still has the potential to be a flame retardant and secondary plasticizer for PVC materials. FRP with the larger relative molecular weight and higher branching degree has better migration resistance than DOP. When DOP was replaced gradually with FRP. In all, the bio-based plasticizer from RSO can be used as a flame-retardant plasticizer to partly replace DOP in PVC blends.
Funding Statement: This work was funded by the Science and Technology Project of Henan Province (202102310593) and Science and Technology Project of Kaifeng City (2002003).
Conflicts of Interest: The authors declare that they have no conflicts of interest to report regarding the present study.
References
1. Lee, I., Pälmke, C., Ringbeck, B., Ihn, Y., Gotthardt, A. et al. (2021). Urinary concentrations of major phthalate and alternative plasticizer metabolites in children of Thailand, Indonesia, and Saudi Arabia, and associated risks. Environmental Science & Technology, 55(24), 16526–16537. DOI 10.1021/acs.est.1c04716. [Google Scholar] [CrossRef]
2. Babich, M. A., Bevington, C., Dreyfus, M. A. (2020). Plasticizer migration from children’s toys, child care articles, art materials, and school supplies. Regulatory Toxicology and Pharmacology, 111, 104574. DOI 10.1016/j.yrtph.2019.104574. [Google Scholar] [CrossRef]
3. Demirtepe, H., Melymuk, L., Codling, G., Murínová, Ľ. P., Richterová, D. et al. (2021). Targeted and suspect screening of plasticizers in house dust to assess cumulative human exposure risk. Science of the Total Environment, 781, 146667. DOI 10.1016/j.scitotenv.2021.146667. [Google Scholar] [CrossRef]
4. Liu, D. K., Jiang, P. P., Nie, Z. X., Wang, H. Y., Dai, Z. D. et al. (2020). Synthesis of an efficient bio-based plasticizer derived from waste cooking oil and its performance testing in PVC. Polymer Testing, 90, 106625. DOI 10.1016/j.polymertesting.2020.106625. [Google Scholar] [CrossRef]
5. Zhang, Z. M., Jiang, P. P., Liu, D. K., Feng, S., Zhang, P. B. et al. (2021). Research progress of novel bio-based plasticizers and their applications in poly(vinyl chloride). Journal of Materials Science, 56(17), 10155–10182. DOI 10.1007/s10853-021-05934-x. [Google Scholar] [CrossRef]
6. Hao, Y. Y., Tian, A. P., Zhu, J., Fan, J. S., Yang, Y. (2020). Synthesis and evaluation of bio-based plasticizers from 5-hydroxymethyl-2-furancarboxylic acid for poly(vinyl chloride). Industrial & Engineering Chemistry Research, 59(40), 18290–18297. DOI 10.1021/acs.iecr.0c03356. [Google Scholar] [CrossRef]
7. Aouachria, K., Massardier, V., Benaniba, M. T., Belhaneche-Bensemra, N. (2019). Evaluation of the effects of acetyl tributyl citrate as bio-based plasticizer on the physical, thermal, and dynamical mechanical properties of poly(vinyl chloride)/polymethyl methacrylate blends. Journal of Vinyl and Additive Technology, 25(S1), E73–E82. DOI 10.1002/vnl.21646. [Google Scholar] [CrossRef]
8. Song, F., Jia, P. Y., Xia, H. Y., Zhang, M., Hu, L. H. et al. (2020). Rosin-derived poly(vinyl chloride) plasticizer: Synthesis, structure, and properties. Journal of Vinyl and Additive Technology, 26(2), 180–186. DOI 10.1002/vnl.21731. [Google Scholar] [CrossRef]
9. Jiang, Y. Y., Ren, L., Wu, G. H., Guo, W., Guan, X. F. et al. (2022). An environmentally sustainable isosorbide-based plasticizer for biodegradable poly(butylene succinate). Journal of Polymer Engineering, 42(4), 331–342. DOI 10.1515/polyeng-2021-0232. [Google Scholar] [CrossRef]
10. Briou, B., Caillol, S., Robin, J. J., Lapinte, V. (2019). Non-endocrine disruptor effect for cardanol based plasticizer. Industrial Crops and Products, 130, 1–8. DOI 10.1016/j.indcrop.2018.12.060. [Google Scholar] [CrossRef]
11. Greco, A., Ferrari, F., Maffezzoli, A. (2018). Thermal analysis of poly(lactic acid) plasticized by cardanol derivatives. Journal of Thermal Analysis and Calorimetry, 134(1), 559–565. DOI 10.1007/s10973-018-7059-4. [Google Scholar] [CrossRef]
12. Lee, S. J., Park, M. S., Shin, J. H., Kim, Y. W. (2018). Effect of the individual and combined use of cardanol-based plasticizers and epoxidized soybean oil on the properties of PVC. Polymer Degradation and Stability, 147, 1–11. DOI 10.1016/j.polymdegradstab.2017.11.002. [Google Scholar] [CrossRef]
13. Fu, Q. H., Long, Y. L., Gao, Y. Y., Ling, Y., Qian, H. et al. (2019). Synthesis and properties of castor oil based plasticizers. RSC Advances, 9(18), 10049–10057. DOI 10.1039/C8RA10288K. [Google Scholar] [CrossRef]
14. Feng, G., Jia, P., Zhang, L., Hu, L., Zhang, M. et al. (2015). Synthesis of a novel phosphorus-containing plasticizer based on castor oil and its application for flame retardancy of polyvinyl chloride. Korean Journal of Chemical Engineering, 32(6), 1201–1206. DOI 10.1007/s11814-014-0288-8. [Google Scholar] [CrossRef]
15. Jia, P. Y., Zhang, M., Hu, L. H., Liu, C. G., Feng, G. D. et al. (2015). Development of a vegetable oil based plasticizer for preparing flame retardant poly(vinyl chloride) materials. RSC Advances, 5(93), 76392–76400. DOI 10.1039/C5RA10509A. [Google Scholar] [CrossRef]
16. Llanes, L. C., Clasen, S. H., Pires, A. T. N., Gross, I. P. (2021). Mechanical and thermal properties of poly(lactic acid) plasticized with dibutyl maleate and fumarate isomers: Promising alternatives as biodegradable plasticizers. European Polymer Journal, 142, 110112. DOI 10.1016/j.eurpolymj.2020.110112. [Google Scholar] [CrossRef]
17. Zhang, Z. M., Jiang, P. P., Liu, D. K., Feng, S., Leng, Y. et al. (2021). Synthesis of novel plasticizer ester end-capped oligomeric lactic acid and its plasticizing performance in poly(vinyl chloride). New Journal of Chemistry, 45(25), 11371–11379. DOI 10.1039/D1NJ01604K. [Google Scholar] [CrossRef]
18. Hosney, H., Nadiem, B., Ashour, I., Mustafa, I., El-Shibiny, A. (2018). Epoxidized vegetable oil and bio-based materials as PVC plasticizer. Journal of Applied Polymer Science, 135(20), 46270. DOI 10.1002/app.46270. [Google Scholar] [CrossRef]
19. Chu, H. Y., Li, H. B., Sun, X. Y., Zhang, Y. W. (2021). Synthesis of biomass-based plasticizer with excellent durability for high transparent polyvinyl chloride film. Journal of Vinyl and Additive Technology, 1, 1–7. DOI 10.1002/vnl.21851. [Google Scholar] [CrossRef]
20. Greco, A., Ferrari, F., Del Sole, R., Maffezzoli, A. (2018). Use of cardanol derivatives as plasticizers for PVC. Journal of Vinyl and Additive Technology, 24(S1), E62–E70. DOI 10.1002/vnl.21585. [Google Scholar] [CrossRef]
21. Jisieike, C. F., Betiku, E. (2020). Rubber seed oil extraction: Effects of solvent polarity, extraction time and solid-solvent ratio on its yield and quality. Biocatalysis and Agricultural Biotechnology, 24, 101522. DOI 10.1016/j.bcab.2020.101522. [Google Scholar] [CrossRef]
22. Chen, F., Zhang, F., Yang, S., Liu, H., Wang, H. et al. (2021). Investigation of pyrolysis kinetics, thermodynamics, product characteristics and reaction mechanism of rubber seed oil. Energy Conversion and Management, 244, 114535. DOI 10.1016/j.enconman.2021.114535. [Google Scholar] [CrossRef]
23. Bocqué, M., Voirin, C., Lapinte, V., Caillol, S., Robin, J. J. (2016). Petro-based and bio-based plasticizers: Chemical structures to plasticizing properties. Journal of Polymer Science Part A: Polymer Chemistry, 54(1), 11–33. DOI 10.1002/pola.27917. [Google Scholar] [CrossRef]
24. Abduh, M. Y., Iqbal, M., Picchioni, F., Manurung, R., Heeres, H. J. (2015). Synthesis and properties of cross-linked polymers from epoxidized rubber seed oil and triethylenetetramine. Journal of Applied Polymer Science, 132(40), 35–66. DOI 10.1002/app.42591. [Google Scholar] [CrossRef]
25. Huang, J., Zhang, J. S., Zhu, G. Q., Yu, X. X., Hu, Y. et al. (2021). Self-healing, high-performance, and high-biobased-content UV-curable coatings derived from rubber seed oil and itaconic acid. Progress in Organic Coatings, 159, 106391. DOI 10.1016/j.porgcoat.2021.106391. [Google Scholar] [CrossRef]
26. Okieimen, F. E., Pavithran, C., Bakare, I. O. (2005). Epoxidation and hydroxlation of rubber seed oil: One-pot multi-step reactions. European Journal of Lipid Science and Technology, 107(5), 330–336. DOI 10.1002/ejlt.200401126. [Google Scholar] [CrossRef]
27. Kantee, J., Kajorncheappunngam, S. (2017). Characterization of epoxidized rubber seed oil. Key Engineering Materials, 728, 295–300. DOI 10.4028/www.scientific.net/KEM.728.295. [Google Scholar] [CrossRef]
28. Jia, P. Y., Hu, L. H., Zhang, M., Zhou, Y. H. (2016). TG-FTIR and TG-MS analysis applied to study the flame retardancy of PVC–castor oil-based chlorinated phosphate ester blends. Journal of Thermal Analysis and Calorimetry, 124(3), 1331–1339. DOI 10.1007/s10973-015-5199-3. [Google Scholar] [CrossRef]
29. Jia, P. Y., Zhang, M., Hu, L. H., Bo, C. Y., Zhou, Y. H. (2015). Synthesis, application, and flame-retardant mechanism of a novel phosphorus-containing plasticizer based on castor oil for polyvinyl chloride. Journal of Thermal Analysis and Calorimetry, 120(3), 1731–1740. DOI 10.1007/s10973-015-4540-1. [Google Scholar] [CrossRef]
30. Wu, Q., Zhang, Q., Zhao, L., Li, S. N., Wu, L. B. et al. (2017). A novel and facile strategy for highly flame retardant polymer foam composite materials: Transforming silicone resin coating into silica self-extinguishing layer. Journal of Hazardous Materials, 336, 222–231. DOI 10.1016/j.jhazmat.2017.04.062. [Google Scholar] [CrossRef]
31. Jia, P. Y., Zhang, M., Hu, L. H., Zhou, J., Feng, G. D. et al. (2015). Thermal degradation behavior and flame retardant mechanism of poly(vinyl chloride) plasticized with a soybean-oil-based plasticizer containing phosphaphenanthrene groups. Polymer Degradation and Stability, 121, 292–302. DOI 10.1016/j.polymdegradstab.2015.09.020. [Google Scholar] [CrossRef]
32. Estela, J. M., Cerdà, V. (2005). Flow analysis techniques for phosphorus: An overview. Talanta, 66(2), 307–331. DOI 10.1016/j.talanta.2004.12.029. [Google Scholar] [CrossRef]
33. Shen, K. K. (2019). Recent advances in boron-based flame retardants. In: Flame retardant polymeric materials. USA: CRC Press. [Google Scholar]
34. Jia, P. Y., Bo, C. Y., Hu, L. H., Zhang, M., Zhou, Y. H. (2016). Synthesis of a novel polyester plasticizer based on glyceryl monooleate and its application in poly(vinyl chloride). Journal of Vinyl and Additive Technology, 22(4), 514–519. DOI 10.1002/vnl.21468. [Google Scholar] [CrossRef]
35. Ning, X. J., Dang, H., Xu, R. S., Wang, G. W., Zhang, J. L. et al. (2022). Co-hydrothermal carbonization of biomass and PVC for clean blast furnace injection fuel production: Experiment and DFT calculation. Renewable Energy, 187, 156–168. DOI 10.1016/j.renene.2022.01.082. [Google Scholar] [CrossRef]
36. Chen, J., Nie, X. A., Jiang, J. C. (2020). Synthesis of a novel bio-oil-based hyperbranched ester plasticizer and its effects on poly(vinyl chloride) soft films. ACS Omega, 5(10), 5480–5486. DOI 10.1021/acsomega.0c00119. [Google Scholar] [CrossRef]
37. Chen, J., Liu, Z., Wang, K., Huang, J., Li, K. et al. (2019). Epoxidized castor oil-based diglycidyl-phthalate plasticizer: Synthesis and thermal stabilizing effects on poly(vinyl chloride). Journal of Applied Polymer Science, 136(9), 47142. DOI 10.1002/a 47142. [Google Scholar] [CrossRef]
38. Jia, P. Y., Zheng, M. R., Ma, Y. F., Feng, G. D., Xia, H. Y. et al. (2019). Clean synthesis of epoxy plasticizer with quaternary ammonium phosphotungstate as catalyst from a byproduct of cashew nut processing. Journal of Cleaner Production, 206, 838–849. DOI 10.1016/j.jclepro.2018.09.238. [Google Scholar] [CrossRef]
39. Wang, M., Wang, G. L., Xu, Y. F., Song, X. H., Bu, Q. (2022). Simultaneous improvement of the plasticization, mechanical and migration resistance properties of PVC materials by grafting ricinoleic acid-derived phosphate ester. Chemical Papers, 76(1), 351–359. DOI 10.1016/j.jhazmat.2017.04.062. [Google Scholar] [CrossRef]
Cite This Article
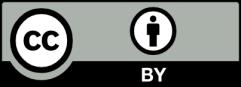
This work is licensed under a Creative Commons Attribution 4.0 International License , which permits unrestricted use, distribution, and reproduction in any medium, provided the original work is properly cited.