Open Access
REVIEW
Research Progress of Tung Oil/UV Photocomposite Curing Material
1 College of Mechanical Engineering and Mechanics, Xiangtan University, Xiangtan, 411105, China
2 State Key Laboratory of Utilization of Woody Oil Resource, Hunan Academy of Forestry, Changsha, 410000, China
3 Hunan Xiangchun Agricultural Technology Co., Ltd., Changsha, 410000, China
* Corresponding Authors: Qiquan Lin. Email: ; Aihua Zhang. Email:
(This article belongs to the Special Issue: Renewable Biomass as a Platform for Preparing Green Chemistry)
Journal of Renewable Materials 2023, 11(4), 1661-1686. https://doi.org/10.32604/jrm.2023.023669
Received 09 May 2022; Accepted 18 July 2022; Issue published 01 December 2022
Abstract
Tung oil (TO)/ultraviolet (UV) photo-composite curing material possesses the characteristics of low curing temperature, low material shrinkage and low environmental pollution. Accordingly, this material must be developed and utilized with the conjugated double bonds contained in the long chain of the main structure (α-tung acid) molecules in the refined TO. The aforementioned material can be chemically modified using a variety of chemical methods to develop a new TO-based UV photocurable material due to its unique chemical properties. This work reviews the research progress of TO/UV photo-composite curing materials in recent years. Firstly, the chemical structure and application of TO and UV Photocatalysis Technology were briefly introduced. Secondly, the research status of novel TO/UV photo-composite curing materials developed by the Diels-Alder reaction was discussed. The method and curing effect of the UV curing system constructed by other chemically modified TO were also discussed. Thereafter, the application of TO in industrial production is introduced from four directions: the application of TO in biodiesel, the application in synthetic resin, the application in self-healing coating and microcapsules and other applications. Finally, the research and application prospects of TO/UV photo-composite curing materials were presented.Keywords
Nomenclature
Term 1 | Interpretation 1 |
Term 2 | Interpretation 2 |
e.g., | |
Ø | Porosity |
S | Skin factor |
New biomass energy is gradually becoming an essential strategic concern in the field of resources and energy in various countries due to the depletion of global petrochemical resources. Woody oil, a significant renewable biomass energy, has gradually replaced traditional petrochemical products and has become the raw material for producing many chemical products. Woody oils come in various types, and their fatty acid chains typically contain some functional groups that can provide them special chemical properties, such as conjugated double bonds, ester groups and hydroxyl groups [1,2]. For example, castor oil has numerous hydroxyl groups, and flax oil and tung oil (TO) exhibit unsaturated double bonds. Over the years, the constant advancements of woody oil have introduced various new application fields of woody oil and a range of novel derivatives. These new fields and products continue to compensate for the scarcity of many non-renewable resources in social development. China is rich in woody oil-based resources. In the past few years, researchers have carried out a lot of basic research on the biomass materials of some natural renewable resources, such as soybean oil, castor oil and TO. These renewable resources have long become a hot spot in the research of biomass materials. TO, a rich and unique woody oil in China, has high development and production value. TO has a higher chemical activity than other woody oils because of its unique multi-chain conjugated triene structure. Over the years, researchers have mainly carried out anti-corrosion paint or chemical grafting on TO to fabricate low molecular weight polymers. Most of them are processed and utilized by thermal curing technology [3]. The thermal curing technology uses more chemical reagents and consumes more energy during the reaction process than the Stereo Lithography Appearance (SLA) light curing technology, which does not fulfill the requirements of green development in the current ecological environment. Meanwhile, the development of photosensitive materials is the core of SLA technology. Based on the above background, the combination of renewable TO with an efficient and environmentally friendly ultraviolet (UV) curing technology can effectively open up a green application road for TO. The research progress of new UV curing materials based on TO was introduced in detail due to the basic research of TO and its derivatives.
TO is a plant of the genus Aleurites in Euphorbiaceae, which is the seed of Vernicia fordii (Hemsl.) Airy Shawy is pressed to obtain refined vegetable oil. TO has been used for thousands of years as a protective coating for wood and is commonly utilized in varnish [4], resin [5,6], polyurethane [7] and other aspects. TO is characterized by fast drying speed, light specific gravity, good gloss, strong adhesion, acid resistance, heat resistance, rust resistance, corrosion resistance, and non-conduciveness [8,9]. Moreover, TO has an economic value, high application value of degradable biomass resources in biodiesel [10–12], tougheners [13], self-healing coatings [14–19], self-healing microcapsules [20–24], solubilizes [25], adhesives [26], films [27], soaps, and pesticides. TO is used as the main raw material for the manufacture of grease paint, such as alkyd resin paint, epoxy resin paint, and phenolic resin paint modifier. For example, tung oleic acid and epoxy resin E-20 or E-12 reaction can produce growth, medium and short oil degree of epoxy resin for electrical insulation metal primer, equipment plant anti-corrosion and so on. This material has good weather and corrosion resistance, white drying, strong adhesion to metals and other advantages. TO-modified unsaturated polyester (UPR) has good air drying. It overcomes the defect that the surface of general unsaturated polyester products or coatings cannot be dried due to the resistance of O2 in the air, and it can be used in fibre-reinforced polymers (FRP), coatings and atomic ash basal resin. Under alkaline conditions, TO-modified phenolic resin and cotton or wood pulp cellulose paper made of laminate material, the product has high heat resistance, low water absorption, excellent insulation properties, high mechanical strength and easy processing performance, and it can be applied to the coated board industry. In addition, TO has good cardboard waterproof performance, and it is widely used in construction [28], coatings, inks, ships, cardboard [29,30] and nano composite materials [31], furniture wood [32] and other aspects.
The main chemical component of TO is triglyceride [33]. TO mainly contains carbon double bonds, an ester group [34]. The structural formula is shown in Fig. 1, and the structural basis for chemical reactions includes Diels-Alder (D-A) reaction [35,36], Foucault alkylation reaction [37] and transesterification reaction. Berhoic acid is an unsaturated long-chain fatty acid with three conjugated double bonds, and it is systematically named 9,11,13-octadecatrienoic acid. According to the difference in the spatial configuration of the three double bonds, the α-niamic acid of the tung acid and the β-niamic acid of the cis, trans, trans-configuration of the α-niacin and the trans, trans, trans-configuration of the tung acid can be identified by infrared, ultraviolet, Raman and other means to identify the conjugate structure, spatial configuration and number and position of the double bonds [38]. In addition, the chemical properties of α-niacin acid are relatively active, and it is easy to isomerize into β-niamic acid under heating conditions.
Figure 1: Chemical structure of the triglyceride in tung oil
The structural formula of berhoic acid is shown in Fig. 2.
Figure 2: Molecular formula of berhoic acid
China has long been at the forefront of the world in terms of TO production and exportation. According to the data from China’s National Bureau of Statistics, the output of TO seeds in China reached more than 450,000 tons in 2018. The annual statistics of China Customs in 2017 indicated that the exportation volume of China’s tung tree was more than 6000 tons, and the export trade volume was as high as US $1.9 million. In comparison with the data in 2016, the export volume increased by approximately 45% and the trade volume by 30%. However, a majority of China’s export and processing trade products at present are mainly low-cost crude oil, and the yield and quality between plants vary, resulting in a significant impact on the yield and quality of TO [39]. Given the foregoing, efficient processing and utilization of TO to improve its valorization potential and economic benefits are challenges that must be addressed at this time.
TO refers to a type of dry oil. It is also a type of vegetable oil that is rich in unsaturated fatty acids. It may self-oxidize at room temperature or heat to achieve drying and curing [40]. The self-oxidation mechanism of unsaturated oil was in the initial stage of the reaction, wherein the allyl position on fatty acid chain α-H was easily removed by hydrogen extraction reaction to generate free radicals, which reacted with oxygen to form hydroperoxides [41]. These hydroperoxides were unstable and easy to be decomposed to form stable alkoxy radicals. In particular, metal driers can also be used to promote the formation and decomposition of hydroperoxides. Finally, the free radical in the system initiates oxidative polymerization, which further increases the molecular weight of the system so as to realize curing [42]. Raw and boiled TO were widely used as protective coatings for a long time. Boiled TO was made by boiling Raw TO at a high temperature. TO chemically changed and increased its chemical activity at high temperatures. Accordingly, the cured film of cooked TO has good heat and corrosion resistance [43]. When boiled TO is used as an anti-corrosion material for wood. It can maintain excellent gloss and play a good moisture-proof role. Consequently, cooked TO was one of the important coatings for the protection of ancient Chinese buildings and cultural relics.
TO has conjugated double bonds and is prone to undergo oxidative polymerization. The result showed that TO cannot only cure and cross-link at room temperature but also undergo free radical polymerization and cationic polymerization under UV light [44,45], especially in light curing coatings [46,47]. When the additional amount of TO was 20%, adding 50% epoxy resin, 25% active diluent, acryl morpholine, 5% three aryl sulphur salt and 1% free radical photo initiator, benzoin two ethers, the film prepared by UV curing had a gel rate of 93.25% and excellent mechanical properties [48]. In addition, TO can be used to make plastics [49], biodiesel [50], microcapsules and other materials. TO can also be used as the matrix of resin modification and mixed with other raw materials to prepare TO-based coatings by chemical modification [51]. Wang et al. [52] prepared hydroxyl derivatives from TO. Subsequently, TO-based waterborne polyurethane with excellent water resistance, thermal properties and mechanical properties was prepared through the reaction with toluene diisocyanate (TDI) and polyester polyol, and dihydroxymethylpropionic acid (DMPA) as chain extender. In conclusion, TO has been widely used in paint and other related fields [53]. Majority of these applications use high-temperature heating and chemical modifications to induce TO to participate in curing, whilst only a select few studies have been conducted on curing with an environmentally-friendly and efficient UV light [54].
3 Introduction to UV Photocatalysis Technology
Photocatalysis refers to the process of using light as a source of energy. The photocatalyst absorbs a certain range of wavelengths of energy, converts the ground state to the excited state, and triggers a series of chemical reactions to generate new compounds or change them into intermediates to catalyze the progress of the reaction.
The UV curing technology (UV curing) is a type of advanced material surface treatment technology that was developed in the 1960s. This technology typically employs high-energy ultraviolet light (325 nm) as a curing energy source. The photo initiator in the liquid system absorbs a certain range of ultraviolet wavelengths of light energy, initiates cracking to produce free radicals or cationic radicals and triggers a series of chain chemical reactions between the system containing unsaturated double bonds, epoxy groups, vinyl ethers. Accordingly, the liquid materials with reactive activity were rapidly cross-linked and polymerized, and a new technology that instantly solidifies into solid materials is developed [55]. This technology has been widely used in printing, packaging, advertising, building materials, electronics, communications, home appliances, automotive, aerospace and other industries because of its fast curing, energy saving, environmental protection, economy, wide applicability, and other characteristics.
3.2 Characteristics of UV Light Curing
The UV light curing technology was characterized as a 5E green environmental protection industrial new technology, that is:
• Efficiency (fast curing rate, can be cured in a few seconds to tens of seconds, or even as fast as 0.1 s to complete the curing);
• Energy (room temperature curing, this technology is only used to excite the photo initiator excitation of radiation energy and does not need high-temperature heating; its energy consumption is only between one-tenth to one-fifth of the heat curing product);
• Enabling (light curing products can be applied to a variety of matrix materials, such as paper, wood, plastic, metal, leather, stone and glass; some heat-sensitive materials, such as electronic components, are also suitable; their scope of application is also extensive, such as wood, anti-corrosion, electronics and construction);
• Ecology (traditional coatings can reduce viscosity because they contain volatile organic compounds, the majority of which are carcinogenic; the light curing products are in line with green environmental protection because they basically do not contain volatile solvents; most of the active diluents used are compounds with high boiling points; during curing, they can participate in cross-linking polymerization and become part of the cross-networked structure thereby greatly reducing environmental pollution and harm to the human body);
• Economy (light curing products have high production efficiency, low energy consumption, low equipment investment, small construction footprint and smooth flow-through production; and the cost of processing pollution is relatively low due to their low pollution).
Although UV coatings have many advantages, they also have certain shortcomings: the UV paint curing speed is fast, they are cured into a film within a few tenths of a second, their film-forming shrinkage rate is large, and the internal stress is correspondingly high, resulting in poor coating adhesion. In addition, UV may cause certain damage to the human body. UV radiation converts oxygen in the air into ozone, causing headaches and fatigue.
3.3 Composition of the UV Light Curing System
The main component in the UV curing system includes photo initiators, reactive diluents (also known as monomers or functional monomers), reactive oligomers (oligomers), pigment fillers and various additives.
(1) Photo initiators can be divided into two categories: the first category is the photo initiator of free radical types, such as acetophenone, benzophenone, thiazone and benzother; the second other category is the photo initiator of the ionic type, mainly cationic type, such as aromatic diazole salts, ferrocene aromatic hydrocarbon complexes, iodine salts and sulfur [56,57]. The cationic photo initiator is the most representative of the gilded salt photo initiator, and it is important because it is not affected by the inhibition of oxygen, and can be quickly polymerized and cured. Meanwhile, the cationic photo initiator has the advantages of small volume shrinkage, strong adhesion, fast curing speed, good depth curing, low toxicity and other advantages in recent years [58]. In addition, free radicals and cationic intercompatibility have certain advantages; free radicals can promote cation polymerization and further enhance the depth and strength of curing [59,60]. Furthermore, the cationic photo initiator is involved in the ring-opening polymerization reaction. Accordingly, many monomers that could not have polymerization, such as cyclic vinyl ethers and oxygen compounds, can undergo photopolymerization reactions [61], greatly broadening the application scope of light-curing materials.
(2) Reactive diluent, commonly referred to as monomers or functional monomers, is an organic small molecule substance that contains polymerizable functional groups. It is mainly used to dissolve the solid components in the light curing system (such as photo initiators) and adjust the system viscosity. The reactive diluent can be divided into monofunctional, bifunctional and polyfunctional groups according to the number of functional groups contained in its molecules.
(3) Reactive oligomer, also known as photosensitive resin, is a relatively low molecular weight photosensitive material with different high curing activities of the reactive group, such as a variety of unsaturated double bonds, hydroxyl and epoxy groups. In the various components of the light curing system, oligomer is the most important body, and its performance determines the main performance of the cured product; the selection and design of oligomers are the most important steps in the light curing product formula [62].
(4) Pigmen is a colored substance with a fine powder that is evenly dispersed in the binder of the coating or ink and coated on the surface of the substrate to produce a color layer, thereby presenting a certain color. Additives are used to improve the performance of photosetting coatings and inks in manufacturing, construction, transportation and storage. The additives commonly used are defoamers, levelling agents, dispersants, matting agents [63].
4 Study on the TO/UV Photo-Composite Curing Material
4.1 Study on Catalyst-Free UV Curing of TO
According to reference [64], TO was affected by oxygen concentration during light curing. Under normal temperature and heating conditions, TO could not be solidified into a film without oxygen. The free radical photoinitiator could not solidify TO into a film isolated from oxygen with UV light. Meanwhile, the cationic photoinitiator can solidify TO into a film. The effect of oxygen was mainly due to TO’s tendency to undergo a hydrogenation reaction after being exposed to light. The free radical formed after dehydrogenation forms hydroperoxide with oxygen, promoting the oxidative polymerization of TO and curing. Some results showed that TO could form a large number of free radicals and initiate the polymerization of double bonds and other UV curing components under the environment of aerobic and UV light irradiation. Further analysis showed that the cross-linking reaction (double bond and free radical) and oxidative polymerization of TO mainly occurred during photopolymerization (on the α-H). The mechanism of the polymerization is shown in Fig. 3.
Figure 3: A schematic showing the mechanism of UV-induced polymerization of tung oil [64]
The results showed that the cured film formed by direct UV curing of TO would produce wrinkles on the surface, which were primarily caused by the rate difference in the curing process, and the curing of the surface and bottom layers was not synchronous, resulting in rate difference. The UV curing material obtained by chemical modification has excellent film-forming properties by mixing TO with epoxy acrylate (EA) and adding measured acryloyl morpholine, triaryl sulfonium salt and benzoin dimethyl ether (PI-BDK). The scanning electron microscopic observation of the cured material showed that the surface of the composite UV curing film is glossy and smooth. The main reason is that EA promotes the reaction at the bottom of the coating, eliminating the previous rate difference. Accordingly, the combination of epoxy acrylate and TO can improve the UV curing effect of TO. Physical blending was conducted in the experiment to maintain the original chemical structure of TO. The operation is simple, and the product can be directly used without any chemical change. This method provides a new idea for the application of TO in the field of UV curing coatings. Zhang et al. [65] found that TO has light curing activity and can achieve light and curing times under ultraviolet light irradiation much faster than the thermal curing and room temperature curing of TO. Meanwhile, TO was affected by the oxygen concentration during light curing. Under normal temperature and heating conditions, TO cannot be cured into a film without oxygen. Under UV light, TO cannot be solidified into a film without oxygen and free radical photo initiators. Meanwhile, cationic photo initiators can promote TO to cure into a film. Epoxidation of TO refers to the reaction of TO with epoxylating reagents under certain conditions, forming an oxygenated ternary ring in the position of double bonds. However, other side reactions may occur during the reaction, such as open ring and acidolysis. TO treated with epoxidation can be reacted with a variety of amine compounds to open the ring and prepare TO-based polyols containing functional groups, such as amino or hydroxyl groups, in the structure. Cao et al. [66] developed a new epoxy modified TO water-based insulation paint, which uses a closed hexamethylene diisocyanate as a curing agent. Zhao [67] prepared methyl tungate by two steps using TO as a raw material: firstly utilizing p-methylbenzenesulfonic acid as a catalyst and tetrahydrofuran as a solvent and synthesizing methyl tungate through the transesterification reaction of TO and methanol; and secondly employing concentrated sulfuric acid as the catalyst, with the H2O2 solution and glacial acetic acid as then oxidants. Methyl oxytung acid was then prepared.
In the catalyst-free reaction system, the directly cured film will have certain problems, such as size and smoothness. The influence of the side reaction products in the reaction must be considered. In the follow-up work, the experimental factors, such as reaction substrate and oxygen conditions, must be taken into account.
4.2 Study on the D–A Modified TO/UV Photo-Composite Curing Material
The D–A reaction, also known as the Diene addition reaction, refers to a compound with a conjugated olefin structure reacting with an olefin or alkyne compound to form a hex acyclic ring structure. The D–A reaction can occur with the dipolefins with the double bond structure because a long molecular chain of TO has a structure of trans-anti-conjugate double bonds [68].
Every long chain contains three conjugated double bonds because TO is an unsaturated triglyceride with three long chains. Thus the D–A reaction in which TO participates is a complex process.
The reaction types are roughly divided into three categories:
(1) TO acts as a pro-dipene and conjugate dienes between molecules D–A reaction;
(2) TO, as a dipienogen, reacts with another conjugated D–A;
(3) TO acts as a conjugated diene and reacts with other dipienogens.
The conjugated double bond in the triglyceride of TO can easily undergo the D–A addition reaction with dienophiles and addition reaction with dienophiles containing different active groups, which can produce TO D–A composite products with distinct types of properties to develop a variety of D–A modified TO-based UV curing materials. Thanamongkollit et al. [69] prepared the alkyd resin by trimethylol triacrylate with TO and tung oleic acid monoglyceride by D–A addition reaction to prepare two types of photocurable resins UVTO and UVTA. Then, two resins were added to the photo initiator to create a photo-curing resin. They also studied the curing process with a light differential thermal analyser. The results showed that the introduction of the three double bonds of the TO-based conjugate improves the addition rate of the D–A reaction and shortens the curing time. Wutticharoenwong et al. [70] synthesized three types of TO-modified active diluents, namely, TOMAS, TOF and TOTAE through the D–A reaction and combined them with drying agents, humectants and long oleic alkyd resins to obtain a variety of modified alkyd resins. The results showed that the addition of three types of TO modified active diluents reduced the viscosity of the alkyd resin and reduced the amount of organic solvent in the alkyd resin and improved the pencil hardness, tensile strength and heat resistance of the coating film. Liu et al. [71] used TO as an active toughener to synthesize TO-based bicyclopentadiene unsaturated polyester resin (DCPD-UPR-TO) by D–A reaction and bicyclopentadiene unsaturated resin. They then used styrene to obtain the thermoset polymer by free radical polymerization cross-linking reaction. The experiments showed that the impact strength and tensile failure strain of DCPD-UPR-TO reached the maximum 373% and 875%, respectively, when the amount of TO was added at 20%. The hardness and flexibility of the polymer reach a flat equilibrium value when the amount of TO is added at 10%. Li [72] compounded and modified the five derivatives of TO with unsaturated polyester resin. The study showed that the hardness and adhesion of the UPR coating film modified by the five TO-based derivatives were significantly improved compared with those of the unmodified UPR. Meanwhile, the TO derivative tung oleic acid had better compatibility with UPR, and the flexibility, tensile strength and impact resistance of the coating film were greatly improved. Yang et al. [73] synthesized a new type of UV photocurable vinyl ester resin through a series of reactions such as D–A reaction of laurene and TO, glycidyl esterification reaction and open-ring esterification.
The D–A reaction, which is one of the most important means of forming carbon bonds in organic chemical synthesis, is commonly used in modern organic synthesis. The reaction has rich stereochemical properties and occupies an important proportion in various basic synthesis studies.
4.2.1 Modification of TO by D–A Addition Reaction Used Maleic Anhydride
Maleic anhydride, is a D–A reaction with conjugated double bonds in TO. The main methods of synthesizing TO anhydride are emulsification heating method [74] and microwave method [75]. New composites can be effectively developed by introducing anhydride groups with high chemical activity into TO through D–A reaction.
Huang et al. [76] used D–A reaction to obtain two types of TO maleic anhydride (MAT1 and MAT2), as shown in Fig. 4. After the two composites were obtained, they were reacted with hydroxy acrylate HEA and PETA under the action of catalyst. Then, glycidyl acrylate (GMA) was added to the reaction. The reaction process is shown in Fig. 5. Next, darocur 1173 photo initiator and 1,6-hexanediol diacrylate (HDDA) diluent were added to obtain HG-MAT and PG-MAT composites. The FTIR images before and after UV light irradiation confirmed that the composites were cured after UV light irradiation. The UV curing kinetics and film thermodynamic properties of the HG-MAT and PG-MAT composites were characterized by photo DSC and TG. The characterization results showed that the two composites have fast film-forming speed and excellent thermal stability, and the thermogravimetric temperature is more than 358°C.
Figure 4: Synthesis and theoretical structure of MAT1 and MAT2 [76]
Figure 5: Synthesis and theoretical structure of HG-MAT and PG-MAT [76]
Huang et al. [77] explored another synthesis path of composites constructed by mat and TO base. Firstly, piperazine-1,4 dicarboxylic acid bis-(2-hydroxyethyl) ester (PCD) and isophorone diamine-1,4 dicarboxylic acid bis-(2-hydroxyethyl) ester (ICD) was synthesized by the reaction of piperazine and isophorone diamine with ethylene carbonate (EC). Then, PCD and ICD were esterified with two configurations of mat, and the obtained product was reacted with GMA to obtain GMA-PCDMAT and GMA-ICDMATUV light curing matrixes, respectively, as shown in Fig. 6. Thereafter, 68% (mass ratio) of the light curing resin, 2% (mass ratio) of Darocur-1173 photoinitiator and 30% (mass ratio) of HDDA constituted the synthesis path of the light curing material. The UV curing kinetics and film thermodynamic properties of the two composites were characterized by photo DSC and TG. The results showed that the introduction of the non-cyanate polyurethane (NIPU) structure (PCD and ICD) greatly enhanced the thermal stability of the membrane and the degree of cross-linking between substances. Zhang et al. [78] modified the mat with hydroxyethyl methacrylate (HEMA), and compounded the modified product (HEMA-MAT) with a resin, photo initiator and light curing monomer to obtain a new TO UV curing material. They also measured the emulsification critical micelle concentration (CMC) of the system. The results showed that the HEMA-MAT composites not only have excellent UV curing properties, but also can be used as emulsifier of acrylic esters. Li et al. [79] studied boric acid and TO modified phenolic resins. Boric acid firstly reacted with phenol, and then with TO and formaldehyde to form a resin. The reaction is expressed in Fig. 7.
Figure 6: Synthesis and structure of GMA-PCDMAT and GMA-ICDMAT [76]
Figure 7: Boric acid, tung oil modified phenolic resin [79]
4.2.2 Modification of TO by Other Dienophile D–A Addition Reactions
Rosin, a natural substance like TO, has special functional groups (conjugated double bonds and carboxyl groups) and high chemical reaction activity. Rosin and TO can be used as conjugated doublets or dienes in D–A addition reaction system. Some studies have shown that the unique ring structure of rosin can reduce the stress generated in the curing process of buffer film and smoothens the surface of the buffer film after curing. Wu et al. [80] used the above-mentioned characteristics to modify TO with rosin. After hydroquinone was added into the container, D–A reaction occurred between TO and rosin in different proportions to obtain a TO rosin D–A product, as shown in Fig. 8. The UV curing material system of TO rosin was composed of epoxy acrylate, isobornyl acrylate, 1,6-hexanediol diacrylate and Irgacure-184 photo initiator. When the mass ratio of rosin to TO is 1:3, the composites with low volume and shrinkage could be obtained and have good thermal stability.
Figure 8: Idealized diels-alder addition reaction scheme between rosin and tung oil [81]
Thanamongkollit et al. [69] used the unique D–A reaction of trimethylolpropane trimethylacrylate (TMPTMA) with TO to obtain TO based phenolic resin (UVTO) in an oxygen-free environment. UVTO was evenly mixed with 10% TPGDA and 5% Irgacure-2100 photoinitiator to obtain a TO-based phenolic resin UV curing composite. This study based on TO and incorporates TMPTMA with multi-functional groups. The composite system can promote the cross-linking and curing of TO under UV light. This method also strengthens the hardness and wear resistance of TO based composite coating.
4.3 Study on the Transesterification-Modified TO/UV Curing Material
The main component of TO is triglyceride oleate, which contains three ester groups. This structure has a good basis for transesterification reaction and is also an excellent raw material for transesterification reaction. When alcohol is used as the solvent in the reaction system, the other two ester bonds are partially replaced or removed so as to convert the large molecular weight triester into a monoester with small molecular weight and space resistance, thus improving the reaction activity. Liu et al. [81] used TO and methanol as raw materials and NaOH as catalyst and prepared methyl tungate by transesterification reaction. They then used silver silica gel column nitrate to carry out gradient elution of methyl berlate, separation and purification and obtain a pure methyl berlate. The products were analyzed and characterized by infrared and UV. The results showed that the purity of methyl berlate was as high as 95%. Lianhua et al. [82] used TO and methanol as raw materials, solid acids as catalysts and fixed-bed reactors. They discussed the effects of the molar ratio, temperature and spatial velocity of methanol to oil on the esterification of TO. Thanamongkollit et al. [69] proposed UV curing system of TO based alkyd resin. Firstly, the transesterification reaction of TO and glycerol catalyzed by lead(IV) oxide was carried out to obtain glycerol monotung oleate. Subsequently, the alkylated monoTO is esterified with phthalic anhydride to obtain TO alkyd. The structural formula is shown in Fig. 9. Finally, UVTA was obtained through the D–A reaction between TO alkyd and TMPTMA monomer. The process is shown in Fig. 10. They used 1H NMR and 13C NMR to characterize the structure of UVTA and photo DSC to study the UV curing kinetics of UVTA. Moreover, they compared the photo DSC analysis curves of UVTA and UVTO mentioned earlier. The results showed that UVTA has better performance than UVTO in terms of light curing speed and efficiency. The alkyd resin prepared by traditional method contains more hydroxyl and carboxyl groups, resulting in poor water resistance and thermal stability. The TMPTMA active crosslinker has a rapid curing property because of its high double bond content. It also has low viscosity and volatility. The crosslinker is commonly used in the curing field because of its excellent characteristics. Thanamongkollit et al. modified a TO-based alkyd resin with TMPTMA. The research results showed that the modified resin had been greatly strengthened in terms of cross-linking density and curing time. The long-chain conjugated triene bond of the TO-based alkyd could also react with highly active pentaerythritol tetra acrylate at 150°C to form a highly polymerizable alkyd resin. TO-based alkyd plastics with excellent mechanical properties are also synthesized. The storage modulus of the plastics can reach 3.19 GPa and the glass transition temperature is 55°C. These studies provide new ideas and methods for the research of TO-based alkyd resin UV curing materials.
Figure 9: The synthesis route of tung oil alkyd [69]
Figure 10: The synthesis of UV-curable tung oil alkyd(UVTA) system from tung oil alkyd [69]
Chittavanich et al. [83] developed and applied the above UVTA composite system to the field of colored coatings. A UV curable TO-based alkyd yellow paint was prepared by mixing caterpillar yellow pigment with UVTA, photoinitiator, dispersion additive and silicone additive. The analysis on the physical properties of the coating indicated that the addition of monomer makes the coating not only have good flexibility, but also have excellent impact resistance and adhesion.
Although the transesterification has certain advantages, such as reduced viscosity of the reaction system, improved reactivity, mild reaction conditions and fast reaction speed, higher requirements are also imposed for the quality of raw materials and oils before exchange. A solid acid catalyst must be used to pre-esterify vegetable oil with a high acid value, and biodiesel should be prepared by exchanging alkali-catalytic esters.
4.4 Study on the TO-Based Hyperbranched UV Photo-Solidification Material
Hyperbranched polymers (HBPS) are chain structured polymers composed of many tree branches [84], and they are widely used in biomedical materials [85] and other areas. The main characteristics of HBPS are compact structure, many branches, low viscosity and ability to combine various active functional groups.
Mirshahi et al. [86] showed that HBPS improved the light curing level and conversion of monomers and oligomeric systems. HBPS also increased the cross-linking density of UV curing system and the glass transition temperature in the UV curing coatings. Zhou et al. [87] explored the TO based hyperbranched UV curing material composite system. Firstly, they used tung acid methyl ester as reaction raw material to prepare epoxy tung acid methyl ester, and reacted it with diethanolamine under UV light to prepare TO-based polyol. The TO-based polyols were reacted with isophorone diisocyanate (IPDI) and HEMA under the catalysis of dibutyltin dilaurate to obtain TO based hyperbranched polyurethane acrylate. Finally, a certain amount of the above products, monomers and photo initiators were mixed in a certain proportion to develop TO based hyperbranched UV curing materials. The results showed that the thermal stability and elongation at break of the film formed by the UV curing system are comparable to the commercial No. 2665-3. This result indicated that TO-based hyperbranched UV curing materials are expected to replace traditional petroleum based materials [88].
5 Research on the Application of TO in Industrial Production
TO has undergone some chemical modifications and can be applied to various aspects, such as biodiesel [89,90], resins, coatings, construction, preservatives and foams [91].
5.1 Application of TO in Biodiesel
Biodiesel [92] is a synthetic oil converted from biomass materials, generally chemically converted from vegetable oils, which as a biomass material, with non-toxic, harmless, low exhaust emissions, sustainable use and other characteristics, is a substitute for traditional petrochemical diesel, so it has attracted more and more attention and attention. At present, the four main methods for preparing biodiesel are as follows: physical, chemical, biological, and chemical-physical methods. Biodiesel prepared from TO-based biomaterials is characterized by high flash point, good fluidity, safe use and low sulphur content, indicating that it meets the requirements of green development and has extremely broad application prospects [93]. Zhao et al. [94] prepared TO-based biodiesel by transesterification reaction between TO and methanol, and the optimal reaction conditions were as follows: the molar ratio of TO and methanol was 1:6, the amount of catalyst NaOH was 1.0% of the quality of TO, the optimal temperature of the reaction was 30°C, the optimal reaction time was 20 min, and the average conversion rate was 82.8%.
5.2 Application of TO in Resin
Based on the characteristics of the molecular structure of TO, it is modified via addition, substitution, polycondensation and other reactions to synthesize TO-based polymer resin materials [95,96]. Polyurethane (PU) is a type of polymer that contains NHCOO repeating structural units; It is an isocyanate (monomer) isocyanate and polyhydroxy compound that is generated after a series of polymerization reactions to obtain polymer materials; PU resin modified with TO as the matrix can be applied to coatings, adhesives, preservatives [97]. The double bond is firstly hydroxylated into a polyol with TO as the raw material. The alcohol reaction with triethanolamine is then carried out, and the rigid polyurethane is prepared as a nucleus, which improves its flexibility and increases its elongation at break. Epoxy resin is an oligomer that contains two or more epoxy groups in the molecular structure, characterized by a plurality of active epoxy groups in the molecular chain and located at the end of the molecular chain. Epoxy resin can also be in the middle or exhibit a ring-like structure. After epoxidation modification, TO can improve its curing activity, achieve self-crosslinking curing and can be used as a curing agent [98]. TO is an important curing agent for manifold alkali-based epoxy resins. The synthetic reaction formula is shown in Fig. 11. The phenolic skeleton structure further improved the heat deformation temperature and the shortcomings of the resin itself with insufficient heat and corrosion resistance. The curing speed can be altered by adjusting the dosage of the ratio, and the epoxy resin can be cured in normal temperature, low temperature (0°C–5°C), humidity and underwater environment. However, some shortcomings persist, such as fast resin curing speed, uneven internal stress distribution, large brittleness of resin cured matter, weak adhesion, and limited application. To overcome this defect, TO with many long flexible carbon chains, which can be substituted with phenol as a modifier, participates in the structure of the curing agent, increasing its molecular weight, reducing sensitivity to water and vapour, and improving the brittleness of the epoxy resin cured and the flexibility, resulting in higher adhesion. According to organic chemistry, olefins with conjugated double bonds are prone to Fourier substitution reaction. The phenol aromatic ring on the phenol hydroxyl ortho position, one of the three active hydrogen positions in the position can be electrophilic substitution reaction with the double bond under the action of an acid catalyst. After the introduction of flexible long-chain compound TO with conjugated double bond, the remaining two active hydrogen positions, can still react with aldehydes and amines Manicheher. The specific reaction formula is shown in Fig. 12. The product obtained by the reaction steps greatly improves the brittleness and flexibility of the resin cured substance and has lower toxicity, higher mechanical strength and better adhesion characteristics compared with the usual low-grade lapfruites. Fu’s substitution reaction of phenol and TO is extremely sensitive to water. The water content in the reaction system exceeds 3.7%, which will prevent the reaction from proceeding. In addition, this reaction was extremely fast. The absorption peak on the infrared spectrum of the conjugated double bond of active hydrogen and TO on the phenol ortho-paradectron disappears 15 min after the start of the reaction, and a new absorption peak of the substitution product appears. Under heating conditions, the phenolic resin itself can be directly cured. The phenolic alcohol in the phenolic resin can be dehydrated at high temperature to form a hypo-methyl quinone containing co-choke double bonds, which can be combined with the double bond in the TO coolimide D–A addition reaction to generate TO imide phenolic resin and curing under certain conditions to form a tung oleimide phenolic resin. Shang et al. [99] synthesized the inexpensive new bismaleimide (ABMI) as show in Fig. 13. Synthetic ABMI is less expensive.
Figure 11: Manich alkali-based epoxy resin synthesis reaction path
Figure 12: Manich alkali tung oleoresin synthesis reaction path
Figure 13: Chemical synthesis pathway of ABMI
5.3 Application of TO in Self-Healing Coating and Microcapsules
TO has become a promising self-healing core material due to its natural source and environmental friendliness. Moreover, TO contains a large number of unsaturated fatty acids, which can be hardened to form corrosion-resistant polymers under oxygen-containing conditions. Sharma et al. [100] modified the epoxy coating of steel bars by adding nano-clay and TO microcapsules, and the microcapsule-based epoxy coating demonstrated outstanding corrosion resistance performance.
Zhang et al. [24] used a microwave technology to obtain novel UV-curable oligomer (TMG) from renewable TO, and a biobased reactive diluent (MM) was derived from malic acid under ambient conditions. Afterward, a set of UV-curable coatings that contains a substantial number of hydroxyl and ester groups was prepared by photo-polymerizing the TMG oligomer with the MM diluent. The resulting coatings demonstrated a high bio-based content (49.2%–58.1%), good mechanical and thermal properties (e.g., Tg of 70.6°C–78.6°C) and excellent coating adhesion and flexibility. Furthermore, the TMG material containing 10% of MM demonstrated a crack repair efficiency of 92.5%, a welding efficiency of tensile strength up to 171.8%, a recycling efficiency of tensile strength up to 404.3% and a shape fixity ratio of 98.2%.
Wang et al. [101] used TO as the core material, and Ca–Al layered double hydroxides (LDH) as corrosion inhibitors to hybridize ethyl cellulose (EC) and the solvent evaporation method to prepare the microcapsules. The synthesis mechanism diagram is shown in Figs. 14 and 15. Ca–Al LDH was loaded on the surface of the hybrid microcapsules. The layered Ca–Al LDH was stabilized by using the physical preparation method of the microcapsules, and the chemical structure was not destroyed during the violent preparation of microcapsules. The result showed that the nanolayered Ca–Al LDH within the hybrid wall provided additional nucleation sites for cement hydration. The chlorine adsorption capacities of the cement paste doped with 3 and 6 wt% microcapsules were 14.7% and 26.7% higher than those of pure cement paste in SCPS, respectively. Moreover, the highest corrosion inhibition efficiency of the hybrid microcapsules in SCPS was 94.12%, and the corrosion inhibition efficiency of the self-healing microcapsules is less than 75%. The hybrid microcapsules improved the corrosion resistance in SCPS via the synergistic effect of self-healing and chlorine adsorption.
Figure 14: Preparation process and formation mechanism of microcapsule
Figure 15: Oxidation polymerization mechanism of tung oil
Wang et al. [102] used TO as a core, LDH as corrosion inhibitor and EC as a wall to synthesize the self-healing and corrosion resistance microcapsule (S/CMC). They found that microcapsules respond to microcracks in the coating by rapidly releasing the core material after cracking or slowly via slow-release pores to repair the coating microcracks. The LDH was embedded in the EC to form a stable 3D wall structure that could capture the chloride ion via the hybrid wall through surface adsorption and ion exchange, and the corrosion resistance of the epoxy resin coating was improved by S/CMC. The mechanism of synthesis is shown in Fig. 16.
Figure 16: Formation mechanism of S/CMC
Li et al. [103] used the in-situ polymerization method to prepare TO-loaded microcapsules, as shown in Fig. 17. The average diameter was approximately 105 μm. Microcapsules maintain a spherical shape with a core content of more than 80.0 wt%. Furthermore, the microcapsules exhibit excellent thermal stability. Dual functional coatings were prepared by incorporating TO-loaded microcapsules into epoxy. The self-healing and self-lubricating functions of the coatings were realized by the releasing of TO from the microcapsules under the scarp or wear condition. TO has excellent film-forming properties when it was contact with oxygen. Approximately 17.3% and 78.6% decreases were observed compared with pure epoxy. The self-healing and self-lubricating mechanisms are also discussed (Fig. 18).
Figure 17: The schematic of microencapsulation mechanism
Figure 18: Schematic diagram of self-healing mechanism
5.4 Application of TO in Other Aspects
With the continuous development of society, TO-based modified products and their application fields have expanded beyond their traditional coatings, varnishes and other manufacturing fields and are also widely used in the electronics industry, plastic industry, printing ink, rubber industry, polymer materials and other chemical industries [104]. TO can be used as a reactive diluent in resin synthesis to reduce the change in viscosity during the reaction [70] and as a composite material to participate in film-forming curing, improving its mechanodynamic and thermodynamic properties [105].
Wutticharoenwong et al. [106] used TO and unsaturated D–A reaction to prepare three reaction diluents, namely, methacryloyloxypropyl trimethoxysilane, methacrylic acid 2,2,2-trifluoroethyl ester and acrylate trialelyl ether, which were then formulated with thiol resin in a certain proportion to make a cured sample. The results showed that the viscosity of the alkyd resin was reduced to 70% with the addition of TO-based reactive diluent, and its drying and curing times were 1.8 times faster than those of the alkyd resin alone.
TO has UV curing activity and can be used as a matrix of the UV curing coating reaction. However, the film-forming effect of TO alone is poor and needs to be further improved. The conjugated double bonds contained in the molecular long chain of tung acid can be effectively improved by chemical modification in combination with the main structure of TO. After modification, TO may be coupled with the characteristics of other substances to construct UV curing materials with good film-forming quality, good mechanical properties and special properties.
TO/UV photo-composite curing products can be widely used in a variety of fields. For example, TO based waterborne hyperbranched resin has the characteristics of low viscosity and high solubility. The aforementioned product can be used as a raw material for the preparation of waterborne ink and mitigation of the generation of volatile organic solvents [107]. TO-based unsaturated resin has high strength and acid resistance and can be used to prepare corrosion-resistant FRP products [108]. The mechanical strength and electrical properties of TO could be improved by using phenolic resin. TO-based phenolic resin can also be used in wear-resistant materials [109]. In addition, the UV curing materials chemically modified by organic substances such as TO D–A and transesterification, are the most studied at present. Considering that the conjugated diene structure of TO can react with distinct dienophiles, and the ester group of TO can be trans esterified with different alcohols, modified products with a variety of functional groups and chemical properties can be created. Accordingly, a variety of UV curing materials can be developed. In summary, with the increasing depletion of global petrochemical resources, extensive research on TO-based UV curing materials can enrich the theoretical system of woody oil reaction, reduce the excessive dependence on fossil resources and prevent environmental pollution caused by petrochemical resources. Research on this aspect can broaden the application scope of woody oil and improve its practical value.
Some deficiencies persist in the field of woody oil-based UV curing. Firstly, woody oils barely exhibit strong material properties after chemical modification and polymerization and could not replace petrochemical polymerization products. Secondly, a certain gap can be observed between light and heat curing coatings in resistance and mechanical properties [110]. In summary, researchers need to further explore the construction of UV curing material system by modifying TO with inorganic materials. TO is expected to become the most changeable vegetable oil in the 21st century because of its long-chain structure of conjugated polyene triesters. The application of TO in UV curing materials has changed the traditional chemical research of multi-reagent and multi-pollution of vegetable oil and realized the goal of green chemical and carbon-neutral development of TO. Therefore, today, when environmental protection and energy conservation are advocated, more in-depth research on the development of TO in the field of UV curing should be carried out.
Funding Statement: This research was funded by Major Landmark Innovation Demonstration Project, 2019XK2002; Changsha Functional Oil Technology Innovation Center, KH2101007; Hunan Forestry Bureau Outstanding Training Research Project, XLK202108-2.
Conflicts of Interest: The authors declare that they have no conflicts of interest to report regarding the present study.
References
1. Zhang, C., Garrison, T. F., Madbouly, S. A., Kessler, M. R. (2016). Recent advances in vegetable oil-based polymers and their composites. Progress in Polymer Science, 71, 91–143. DOI 10.1016/j.progpolymsci.2016.12.009. [Google Scholar] [CrossRef]
2. Phalak, G., Patil, D., Vignesh, V., Mhaske, S. (2018). Development of tri-functional biobased reactive diluent from ricinoleic acid for UV curable coating application. Industrial Crops & Products, 119, 17–19. DOI 10.1016/j.indcrop.2018.04.001. [Google Scholar] [CrossRef]
3. Wang, Y., An, Q., Yang, B. (2019). Synthesis of UV-curable polyurethane acrylate modified with polyhedral oligomeric silsesquioxane and fluorine for iron cultural relic protection coating. Progress in Organic Coatings, 136, 105235. DOI 10.1016/j.porgcoat.2019.105235. [Google Scholar] [CrossRef]
4. Huang, J., Yuan, T., Yang, Z., Man, L., Hu, Y. et al. (2019). UV/thermal dual curing of tung oil-based polymers induced by cationic photoinitiator. Progress in Organic Coatings, 126, 8–17. DOI 10.1016/j.porgcoat.2018.10.022. [Google Scholar] [CrossRef]
5. Gaidukovs, S., Medvids, A., Onufrijevs, P., Grase, L. (2018). UV-light-induced curing of branched epoxy novolac resin for coatings. Express Polymer Letters, 12(10), 918–929. DOI 10.3144/expresspolymlett.2018.78. [Google Scholar] [CrossRef]
6. Yang, S., Fang, H., Li, H., Shen, F., Chen, X. et al. (2022). Synthesis of tung oil-based vinyl ester resin and its application for anti-corrosion coatings. Progress in Organic Coatings, 170, 106967. DOI 10.1016/j.porgcoat.2022.106967. [Google Scholar] [CrossRef]
7. Li, M., Li, S., Xia, J., Ding, C., Wang, M. et al. (2017). Tung oil based plasticizer and auxiliary stabilizer for poly(vinyl chloride). Materials & Design, 366–375. DOI 10.1016/j.matdes.2017.03.025. [Google Scholar] [CrossRef]
8. Cai, L. (1984). Some special uses of tung oil. Guizhou Chemical, 1(3), 24–33. [Google Scholar]
9. Humar, M., Lesar, B. (2013). Efficacy of linseed- and tung-oil-treated wood against wood-decay fungi and water uptake. International Biodeterioration & Biodegradation, 85, 223–227. DOI 10.1016/j.ibiod.2013.07.011. [Google Scholar] [CrossRef]
10. Chen, Y., Chen, J., Chang, C. (2010). Biodiesel production from tung (Vernicia montana) oil and its blending properties in different fatty acid compositions. Bioresource Technology, 101(24), 9521–9526. DOI 10.1016/j.biortech.2010.06.117. [Google Scholar] [CrossRef]
11. Chen, Y., Chen, J., Luo, Y. (2012). Complementary biodiesel combination from tung and medium-chain fatty acid oils. Renewable Energy, 44, 305–310. DOI 10.1016/j.renene.2012.01.098. [Google Scholar] [CrossRef]
12. Manh, D., Chen, Y., Chang, C. (2012). Effects of blending composition of tung oil and ultrasonic irradiation intensity on the biodiesel production. Energy, 48(1), 519–524. DOI 10.1016/j.energy.2012.09.065. [Google Scholar] [CrossRef]
13. Agnol, L. D., Dias, F. T. G., Ornaghi Jr, H. L., Sangermano, M., Bianchi, O. (2021). UV-curable waterborne polyurethane coatings: A state-of-the-art and recent advances review. Progress in Organic Coatings, 154, 106156. DOI 10.1016/j.porgcoat.2021.106156. [Google Scholar] [CrossRef]
14. Soufeiania, L., Folientea, G., Nguyenb, T. Q. K., Nicolasa, R. S. (2020). Corrosion protection of steel elements in facade systems–A review. Journal of Building Engineering, 32, 101759. DOI 10.1016/j.jobe.2020.101759. [Google Scholar] [CrossRef]
15. Robuschi, S., Tengattini, A., Dijkstra, J., Fernandez, I., Lundgren, K. (2021). A closer look at corrosion of steel reinforcement bars in concrete using 3D neutron and X-ray computed tomography. Cement and Concrete Research, 144, 106439. DOI 10.1016/j.cemconres.2021.106439. [Google Scholar] [CrossRef]
16. Zhu, P., Hao, Y., Liu, H., Wang, X., Gu, L. (2020). Durability evaluation of recycled aggregate concrete in a complex environment. Journal of Cleaner Production, 273, 122569. DOI 10.1016/j.jclepro.2020.122569. [Google Scholar] [CrossRef]
17. Shevtsov, D. S., Zartsyn, I. D., Komarova, E. S. (2021). Relation between resistivity of concrete and corrosion rate of reinforcing bars caused by galvanic cells in the presence of chloride. Cement and Concrete Composites, 119, 104026. DOI 10.1016/j.cemconcomp.2021.104026. [Google Scholar] [CrossRef]
18. Ma, A., Wei, J., Wu, Y., Wu, Y., Zhao, W. (2021). A novel directional repairing rGO-Fe3O4/oil coating with magnetic driving for metal protection and self-healing. Chemical Engineering Journal, 421, 129597. DOI 10.1016/j.cej.2021.129597. [Google Scholar] [CrossRef]
19. Wang, X., Chen, Z., Xu, W., Wang, X. (2020). Fluorescence labelling and self-healing microcapsules for detection and repair of surface microcracks in cement matrix. Composites Part B: Engineering, 184, 107744. DOI 10.1016/j.compositesb.2020.107744. [Google Scholar] [CrossRef]
20. Wang, X., Zhang, C., Wang, K., Huang, Y., Chen, Z. (2021). Highly efficient photothermal conversion capric acid phase change microcapsule: Silicon carbide modified melamine urea formaldehyde. Journal of Colloid and Interface Science, 582, 30–40. DOI 10.1016/j.jcis.2020.08.014. [Google Scholar] [CrossRef]
21. Su, Y., Qiu, S., Yang, D., Liu, S., Zhao, H. et al. (2020). Active anti-corrosion of epoxy coating by nitrite ions intercalated MgAl LDH. Journal of Hazardous Materials, 391, 122215. DOI 10.1016/j.jhazmat.2020.122215. [Google Scholar] [CrossRef]
22. Du, W., Lin, R., Liu, Q. (2021). Investigation of isophorone diisocyanate microcapsules to improve self-healing properties and sulfate resistance of concrete. Construction and Building Materials, 300, 124438. DOI 10.1016/j.conbuildmat.2021.124438. [Google Scholar] [CrossRef]
23. Yamaç, Ö. E., Yilmaz, M., Yalçın, E., Kök, B. V., Norambuena-Contreras, J. et al. (2021). Self-healing of asphalt mastic using capsules containing waste oils. Construction and Building Materials, 270, 121417. DOI 10.1016/j.conbuildmat.2020.121417. [Google Scholar] [CrossRef]
24. Zhang, J., Huang, J., Zhu, G., Yu, X., Cheng, J. et al. (2021). Self-healing, recyclable, and removable UV-curable coatings derived from tung oil and malic acid. Green Chemistry, 23(16), 5875–5886. DOI 10.1039/D1GC01726H. [Google Scholar] [CrossRef]
25. Mantelli, A., Romani, A., Suriano, R., Diani, M., Colledani, M. et al. (2021). UV-assisted 3D printing of polymer composites from thermally and mechanically recycled carbon fibers. Polymers, 13(5), 726. DOI 10.3390/polym13050726. [Google Scholar] [CrossRef]
26. Lee, S., Kim, Y., Park, D., Kim, J. (2021). The thermal properties of a UV curable acrylate composite prepared by digital light processing 3D printing. Composites Communications, 26, 100796. DOI 10.1016/j.coco.2021.100796. [Google Scholar] [CrossRef]
27. Sangermano, M., D’anna, A., Marro, C., Klikovits, N., Liska, R. (2018). UV-activated frontal polymerization of glass fibre reinforced epoxy composites. Composites Part B: Engineering, 143, 168–171. DOI 10.1016/j.compositesb.2018.02.014. [Google Scholar] [CrossRef]
28. Zhao, Z., Liu, X., Kang, D., Xiao, Z., Dong, W. et al. (2022). Optimization of the subcritical butane extraction of tung Oil and Its mechanism analysis. Processes, 10(6), 1071. DOI 10.3390/pr10061071. [Google Scholar] [CrossRef]
29. Jianprasert, A., Monvisade, P., Yamaguchi, M. (2015). Combination of tung oil and natural rubber latex in PVA as water based coatings for paperboard application. MATEC Web of Conferences, 30, 03010. DOI 10.1051/matecconf/20153003010. [Google Scholar] [CrossRef]
30. Jianprasert, A., Monvisade, P., Yamaguchi, M. (2016). Surface improvement on water and oil affinities and absorption rate of PVA/tung oil-coated paperboard and fiberboard. Journal of Coatings Technology and Research, 13(2), 345–354. DOI 10.1007/s11998-015-9750-8. [Google Scholar] [CrossRef]
31. Cai, B. R., Cao, J. H., Liang, W. H., Yang, L. Y., Liang, T. et al. (2021). Ultraviolet-cured Al2O3-polyethylene terephthalate/polyvinylidene fluoride composite separator with asymmetric design and its performance in lithium batteries. ACS Applied Energy Materials, 4(5), 5293–5303. DOI 10.1021/acsaem.1c00804. [Google Scholar] [CrossRef]
32. Fang, S., Zhang, H., Zhang, B. (2014). A study of tung-oil-lime putty—A traditional lime based mortar. International Journal of Adhesion and Adhesives, 48, 224–230. DOI 10.1016/j.ijadhadh.2013.09.034. [Google Scholar] [CrossRef]
33. Lee, Y. C., Nobles, W. L. (1959). A chemical study of American tung oil. Journal of Pharmaceutical Sciences, 48(3), 162–165. [Google Scholar]
34. Wu, H., Xu, D., Zhou, Y., Gao, C., Guo, J. et al. (2020). Tung oil anhydride modified hemp fiber/polypropylene composites: The improved toughness, thermal stability and rheological property. Fibers and Polymers, 21(9), 2084–2091. DOI 10.1007/s12221-020-1157-1. [Google Scholar] [CrossRef]
35. Levine, S., Stevenson, H. J. R., Kabler, P. W. (1953). Qualitative studies of pneumococcal polysaccharides by infrared spectrophotometry. Academic Press, 45(1). DOI 10.1016/0003-9861(53)90405-6. [Google Scholar] [CrossRef]
36. Wang, M., Xia, J., Jiang, J., Li, S., Huang, K. et al. (2016). A novel liquid Ca/Zn thermal stabilizer synthesized from tung-maleic anhydride and its effects on thermal stability and mechanical properties of PVC. Polymer Degradation and Stability, 133, 136–143. DOI 10.1016/j.polymdegradstab.2016.08.010. [Google Scholar] [CrossRef]
37. Jorma, S., Kaarlo, K., Jouko, K. (1988). Kinetics of reactions between methyl and dimethyl-aminyl radicals formed in the flash photolysis of tetramethylhydrazine, tetramethylurea and tetramethyltetrazene in the gas phase. Journal of Photochemistry and Photobiology A: Chemistry, 43(1), 31–41. DOI 10.1016/1010-6030(88)80004-2. [Google Scholar] [CrossRef]
38. Xiao, L., Li, S., Wang, Y., Li, W., Chen, J. et al. (2021). Toughening epoxy resin by constructing π-π interaction between a tung oil-based modifier and epoxy. Industrial Crops and Products, 170, 113723. DOI 10.1016/j.indcrop.2021.113723. [Google Scholar] [CrossRef]
39. Zhang, Q., Wen, Z., Luo, K. (2020). Research progress in the biology of tung oil. Non-Wood Forest Research, 38(4), 238–245. [Google Scholar]
40. Seyferth, D. (1986). Organometallic chemistry reviews. Journal of Organometallic Chemistry, 301(1), 276–300. [Google Scholar]
41. Zuyev, B. M., Chistyakov, Y. V., Filippova, A. P., Arkhireyev, O. S. (1986). Studies on birefringence as a function of strain in cross-linked polymers under creep conditions. Pergamon, 28(10), 2472–2479. [Google Scholar]
42. Korshak, V. V., Sosin, S. L., Slonimskii, G. L., Askadskii, A. A., Zakharkin, L. I. et al. (1986). Synthesis and copolymerization of 4-(1â·2-o-carboranyl) styrene with acryloyl ferrocene and study of the properties of the copolymers obtained. Pergamon, 28(2), 265–271. [Google Scholar]
43. Liu, C., Dai, Y., Wang, C., Xie, H., Zhou, Y. et al. (2013). Phase-separation dominating mechanical properties of a novel tung-oil-based thermosetting polymer. Industrial Crops & Products, 43(5), 677–683. DOI 10.1016/j.indcrop.2012.07.072. [Google Scholar] [CrossRef]
44. Ahmad, A., Alsaad, A., Al-Bataineh, Q. M., Al-Akhras, M. A. H., Albataineh, Z. et al. (2021). Synthesis and characterization of ZnO NPs-doped PMMA-BDK-MR polymer-coated thin films with UV curing for optical data storage applications. Polymer Bulletin, 78(3), 1189–1211. DOI 10.1007/s00289-020-03155-x. [Google Scholar] [CrossRef]
45. Wang, T., Liu, T., Ma, T., Li, L., Wang, Q. et al. (2018). Study on degradation of phosphorus and nitrogen composite UV-cured flame retardant coating on wood surface. Progress in Organic Coatings, 124, 240–248. DOI 10.1016/j.porgcoat.2018.08.017. [Google Scholar] [CrossRef]
46. Liang, B., Zhao, J., Li, G., Huang, Y., Yang, Z. et al. (2019). Facile synthesis and characterization of novel multi-functional bio-based acrylate prepolymers derived from tung oil and its application in UV-curable coatings. Industrial Crops & Products, 138, 111585. DOI 10.1016/j.indcrop.2019.111585. [Google Scholar] [CrossRef]
47. Man, L., Feng, Y., Hu, Y., Yuan, T., Yang, Z. (2019). A renewable and multifunctional eco-friendly coating from novel tung oil-based cationic waterborne polyurethane dispersions. Journal of Cleaner Production, 241, 118341. DOI 10.1016/j.jclepro.2019.118341. [Google Scholar] [CrossRef]
48. Yang, Z., Huang, J., Yuan, T. (2018). Study on light/heat dual curing of tung oil and its derivatives. Report Collection of the 19th China Radiation Curing Annual Conference 2018, vol. 5, pp. 75–78. [Google Scholar]
49. Wu, D., Chen, B., Sun, R., Liu, G. (2017). Thermal behavior and Raman spectral characteristics of step-heating perhydrous coal: Implications for thermal maturity process. Journal of Analytical and Applied Pyrolysis, 128, 143–155. [Google Scholar]
50. Qi, D. H., Yang, K., Zhang, D., Chen, B., Wei, Q. et al. (2017). Experimental investigation of a turbocharged CRDI diesel engine fueled with tung oil-diesel-ethanol microemulsion fuel. Renewable Energy, 113, 1201–1207. [Google Scholar]
51. Liu, R., Wu, Z., He, P., Fan, H., Huang, Z. et al. (2019). A self-standing, UV-cured semi-interpenetrating polymer network reinforced composite gel electrolytes for dendrite-suppressing lithium ion batteries. Journal of Materiomics, 5(2), 185–194. [Google Scholar]
52. Wang, Z., Wang, J., Gu, L. (2012). Synthesis and characterization of tung oil-based waterborne polyurethane. Paint & Coatings Industry, 42(7), 49–52. [Google Scholar]
53. Czachor-Jadacka, D., Pilch-Pitera, B. (2021). Progress in development of UV curable powder coatings. Progress in Organic Coatings, 158, 106355. [Google Scholar]
54. Liu, X., Bouxin, F. P., Fan, J., Budarin, V. L., Hu, C. et al. (2020). Recent advances in the catalytic depolymerization of lignin towards phenolic chemicals: A review. ChemSusChem, 13(17), 4296–4317. [Google Scholar]
55. Chemtob, A., Belon, C., Croutxe-Barghorn, C. (2011). Tandem cationic and sol-gel photopolymerizations of a vinyl ether alkoxysilane. Polymer Engineering & Science, 51(8), 1466–1475. [Google Scholar]
56. Zheng, X., Liu, J., Wang, K., Liu, R., Yuan, Y. et al. (2018). Preparation of polyimide/amino-modified reduced graphene oxide composite matrix and its application in UV-cured functionalized films. Progress in Organic Coatings, 124, 122–128. [Google Scholar]
57. Yu, Z., Cui, A., Zhao, P., Wei, H., Hu, F. (2018). Preparation and properties studies of UV-curable silicone modified epoxy resin composite system. Journal of Applied Biomaterials & Functional Materials, 16(1_suppl), 170–176. [Google Scholar]
58. Huang, J., Xiong, Y., Zhou, X., Yang, Z., Yuan, T. (2022). A novel polyfunctional polyurethane acrylate prepolymer derived from bio-based polyols for UV-curable coatings applications. Polymer Testing, 106, 107439. DOI 10.1016/j.polymertesting.2021.107439. [Google Scholar] [CrossRef]
59. Nan, X., Huang, Y., Fan, Q. (2016). Efficient visible photoinitiator with high-spectrum stability in an acid medium for free-radical and free-radical-promoted cationic photopolymerization based on erythrosine B derivatives. Journal of Applied Polymer Science, 133(10). DOI 10.1002/app.43035. [Google Scholar] [CrossRef]
60. Podsiadly, R., Podemska, K., Szymczak, A. M. (2011). Novel visible photoinitiators systems for free-radical/cationic hybrid photopolymerization. Dyes and Pigments, 91(3), 422–426. DOI 10.1016/j.dyepig.2011.05.012. [Google Scholar] [CrossRef]
61. Xiao, L., Liu, Z., Li, N., Li, S., Fu, P. et al. (2020). A hyperbranched polymer from tung oil for the modification of epoxy thermoset with simultaneous improvement in toughness and strength. New Journal of Chemistry, 44(39), 16856–16863. DOI 10.1039/C9NJ06373K. [Google Scholar] [CrossRef]
62. Mendes-Felipe, C., Barbosa, J., Gonçalves, S., Pereira, N., Costa, C. et al. (2020). High dielectric constant UV curable polyurethane acrylate/indium tin oxide composites for capacitive sensing. Composites Science and Technology, 199, 108363. DOI 10.1016/j.compscitech.2020.108363. [Google Scholar] [CrossRef]
63. Valentino, H. A. S., dos Reis, P. T. L., Gandini, A., Lacerda, T. M. (2021). Furfuryl alcohol/tung oil matrix-based composites reinforced with bacterial cellulose fibres. Cellulose, 28(11), 7109–7121. DOI 10.1007/s10570-021-03999-0. [Google Scholar] [CrossRef]
64. Huang, J., Yuan, T., Ye, X., Man, L., Zhou, C. et al. (2018). Study on the UV curing behavior of tung oil: Mechanism, curing activity and film-forming property. Industrial Crops & Products, 112, 61–69. DOI 10.1016/j.indcrop.2017.10.061. [Google Scholar] [CrossRef]
65. Zhang, L., Li, P., Yang, Z., He, Z., Zhou, W. (2020). Study on the photocuring activity of tung oil under ultraviolet light conditions. Functional Materials, 3(51), 3089–3095. [Google Scholar]
66. Cao, M., Wang, H., Cai, R. (2015). Preparation and properties of epoxy-modified tung oil waterborne insulation varnish. Journal of Applied Polymer Science, 132(45). DOI 10.1002/app.42755. [Google Scholar] [CrossRef]
67. Zhao, X. (2014). Chemical modification of tung oil and its application in epoxy resin. Tianjin University, China. [Google Scholar]
68. Biermann, U., Butte, W., Eren, T. (2007). Regio- and stereoselective Diels–Alder additions of maleic anhydride to conjugated triene fatty acid methyl esters. European Journal of Organic Chemistry, 2007(23), 3859–3862. DOI 10.1002/(ISSN)1099-0690. [Google Scholar] [CrossRef]
69. Thanamongkollit, N., Miller, K. R., Soucek, M. D. (2012). Synthesis of UV-curable tung oil and UV-curable tung oil based alkyd. Progress in Organic Coatings, 73(4), 425–434. DOI 10.1016/j.porgcoat.2011.02.003. [Google Scholar] [CrossRef]
70. Wutticharoenwong, K., Dziczkowski, J., Soucek, M. D. (2012). Tung based reactive diluents for alkyd systems:Film properties. Progress in Organic Coatings, 73(4), 283–290. DOI 10.1016/j.porgcoat.2011.03.017. [Google Scholar] [CrossRef]
71. Liu, C. G., Lei, W., Cai, Z. C. (2013). Use of tung oil as a reactive toughening agent in dicyclopentadiene-terminated unsaturated polyester resins. Industrial Crops & Products, 49, 412–418. DOI 10.1016/j.indcrop.2013.05.023. [Google Scholar] [CrossRef]
72. Li, N. (2014). Synthesis of tung oil derivatives and their research on modified unsaturated polyester resin. Central South University of Forestry and Technology, China. [Google Scholar]
73. Yang, X., Li, S., Xia, J. (2015). Novel renewable resource-based UV-curable copolymers derived from myrcene and tung oil: Preparation, characterization and properties. Industrial Crops & Products, 63, 17–25. DOI 10.1016/j.indcrop.2014.10.024. [Google Scholar] [CrossRef]
74. Wang, Q., Ye, Q., Luo, J., Xie, C., Liu, H. et al. (2022). Effects of tung oil composite regenerating agent on rheological properties and microstructures of reclaimed asphalt binder. Materials, 15(9), 3197. DOI 10.3390/ma15093197. [Google Scholar] [CrossRef]
75. Liu, C., Liu, Z., Tisserat, B. H., Wang, R., Schuman, T. P. et al. (2015). Microwave-assisted maleation of tung oil for bio-based products with versatile applications. Industrial Crops & Products, 71, 185–196. DOI 10.1016/j.indcrop.2015.02.066. [Google Scholar] [CrossRef]
76. Huang, Y., Ye, G., Yang, J. (2015). Synthesis and properties of UV-curable acrylate functionalized tung oil based resins via Diels–Alder reaction. Progress in Organic Coatings, 78, 28–34. DOI 10.1016/j.porgcoat.2014.10.011. [Google Scholar] [CrossRef]
77. Huang, Y., Pang, L., Wang, H., Zhong, R., Zeng, Z. et al. (2013). Synthesis and properties of UV-curable tung oil based resins via modification of Diels–Alder reaction, nonisocyanate polyurethane and acrylates. Progress in Organic Coatings, 76(4), 654–661. [Google Scholar]
78. Zhang, H., Zhou, H., Wang, J. (2017). Synthesis, characterization and UV curable property of acrylate modified tung oil-based emulsifier. Chemical Industry & Engineering Progress, 36(10), 3860–3865. [Google Scholar]
79. Li, Y., Yao, J., Zhou, Y. (2005). Composite modified phenolic resins and their applications in friction materials. Non-Metallic Minerals, 28(4), 57–59. [Google Scholar]
80. Wu, J., Zhang, T., Ma, G., Li, P., Ling, L. et al. (2013). Synthesis of a tung oil–rosin adduct via the diels–alder reaction: Its reaction mechanism and properties in an ultraviolet-curable adhesive. Journal of Applied Polymer Science, 130(6), 4201–4208. [Google Scholar]
81. Liu, Y., Fu, C. (2015). Silver nitrate silica gel column gradient elution purification of methyl tungate. Journal of Jishou University, 36(1), 52–56. [Google Scholar]
82. Li, L. H., Lv, P. M., Luo, W., Wang, Z. M., Yuan, Z. H. (2010). Esterification of high FFA tung oil with solid acid catalyst in fixed bed reactor. Biomass and Bioenergy, 34(4), 496–499. [Google Scholar]
83. Chittavanich, P., Miller, K., Soucek, M. D. (2012). A photo-curing study of a pigmented UV-curable alkyd. Progress in Organic Coatings, 73(4), 392–400. [Google Scholar]
84. Yan, M., Lin, F. Y., Cochran, E. W. (2017). Dynamics of hyperbranched polymers derived from acrylated epoxidized soybean oil. Polymer, 125, 117–125. [Google Scholar]
85. Zhang, H., Zhao, T., Newland, B., Liu, W., Wang, W. et al. (2018). Catechol functionalized hyperbranched polymers as biomedical materials. Progress in Polymer Science, 78, 47–55. [Google Scholar]
86. Mirshahi, F., Bastani, S., Sari, M. G. (2016). Studying the effect of hyperbranched polymer modification on the kinetics of curing reactions and physical/mechanical properties of UV-curable coatings. Progress in Organic Coatings, 90, 187–199. [Google Scholar]
87. Zhou, C., Hu, Y., Yang, Z., Yuan, T., Huang, J. et al. (2018). Facile synthesis and characterization of urushiol analogues from tung oil via ultraviolet photocatalysis. Progress in Organic Coatings, 120, 240–251. [Google Scholar]
88. Andjelkovic, D. D., Larock, R. C. (2006). Novel rubbers from cationic copolymerization of soybean oils and dicyclopentadiene. 1. Synthesis and characterization. Biomacromolecules, 7(3), 927–936. [Google Scholar]
89. Shang, Q., Lei, J., Jiang, W. (2010). Properties of tung oil biodiesel and its blends with 0# diesel. Bioresource Technology, 101(2), 826–828. [Google Scholar]
90. Shang, Q., Lei, J., Jiang, W. (2012). Production of tung oil biodiesel and variation of fuel properties during storage. Applied Biochemistry and Biotechnology, 168(1), 106–115. [Google Scholar]
91. Mosiewicki, A. M., Casado, U., Marcovich, E. N. (2012). Moisture dependence of the properties of composites made from tung oil based polyurethane and wood flour. Journal of Polymer Research, 19. [Google Scholar]
92. Anand, M., Farooqui, A. S., Kumar, R. (2016). Optimizing renewable oil hydrocracking conditions for aviation bio-kerosene production. Fuel Processing Technology, 151, 50–58. [Google Scholar]
93. Chalapud, M. C., Herdt, M., Nicolao, E. S., Ruseckaite, R. A., Ciannamea, E. M. et al. (2020). Biobased particleboards based on rice husk and soy proteins: Effect of the impregnation with tung oil on the physical and mechanical behavior. Construction and Building Materials, 230, 116996. [Google Scholar]
94. Zhao, W. (2007). Experimental study on the conversion of tung oil into biodiesel. Northwest A & F University, China. [Google Scholar]
95. Soto, D. G., Marcovich, E. N., Mosiewicki, M. (2016). Flexible polyurethane foams modified with biobased polyols: Synthesis and physical-chemical characterization. Journal of Applied Polymer Science, 133(35), 43831. [Google Scholar]
96. Xiao, L., Huang, J., Wang, Y., Chen, J., Liu, Z. et al. (2019). Tung oil-based modifier toughening epoxy resin by sacrificial bonds. ACS Sustainable Chemistry & Engineering, 7(20), 17344–17353. [Google Scholar]
97. Noè, C., Hakkarainen, M., Sangermano, M. (2020). Cationic UV-curing of epoxidized biobased resins. Polymers, 13(1), 89. DOI 10.3390/polym13010089. [Google Scholar] [CrossRef]
98. Hu, H., Chen, M., Cao, M. (2021). TiO2 antifouling coating based on epoxy-modified tung oil waterborne resin. Polymers and Polymer Composites, 29(9_suppl), S521–S529. DOI 10.1177/09673911211011123. [Google Scholar] [CrossRef]
99. Shang, S., Zhou, Y., Wang, D., Wang, D. (2005). Study on heat resistance of tung oil phthalimine phenolic resin. Chemistry and Industry of Forest Products, 25, 27–30. [Google Scholar]
100. Sharma, N., Sharma, S., Sharma, S. K., Mehta, R. (2020). Evaluation of corrosion inhibition and self healing capabilities of nanoclay and tung oil microencapsulated epoxy coatings on rebars in concrete. Construction and Building Materials, 259, 120278. DOI 10.1016/j.conbuildmat.2020.120278. [Google Scholar] [CrossRef]
101. Wang, X., Zhu, J., Zou, F., Zhou, N., Li, Y. et al. (2022). Ca-Al LDH hybrid self-healing microcapsules for corrosion protection. Chemical Engineering Journal, 447, 137125. DOI 10.1016/j.cej.2022.137125. [Google Scholar] [CrossRef]
102. Wang, X., Zhu, J., Lei, Y., Lei, W. (2022). Synthesis and characterization of layered double hydroxides hybrid microcapsules for anti-corrosion via self-healing and chloride ion adsorption. Applied Clay Science, 221, 106481. DOI 10.1016/j.clay.2022.106481. [Google Scholar] [CrossRef]
103. Li, H., Cui, Y., Li, Z., Zhu, Y., Wang, H. (2018). Fabrication of microcapsules containing dual-functional tung oil and properties suitable for self-healing and self-lubricating coatings. Progress in Organic Coatings, 115, 164–171. DOI 10.1016/j.porgcoat.2017.11.019. [Google Scholar] [CrossRef]
104. Huang, K., Xia, J. (2008). Modification of tung oil and its derivatives in the application of high-molecular materials. Chemical Industry Progress, 27(10), 1588–1592. [Google Scholar]
105. Xiong, Z., Li, C., Ma, S. (2013). The properties of poly(lactic acid)/starch blends with a functionalized plant oil: Tung oil anhydride. Carbohydrate Polymers, 95(1), 77–84. DOI 10.1016/j.carbpol.2013.02.054. [Google Scholar] [CrossRef]
106. Wutticharoenwong, K., Soucek, D. M. (2010). Synthesis of tung-oil-based reactive diluents. Macromolecular Materials and Engineering, 295(12), 1097–1106. DOI 10.1002/mame.201000099. [Google Scholar] [CrossRef]
107. Smith, M., Payne, A., Edwards, K., Morris, S., Beckler, B. et al. (2015). Effect of microwave cure on the thermo-mechanical properties of tung oil-based/Carbon nanotube composites. Coatings, 5(3), 557–575. DOI 10.3390/coatings5030557. [Google Scholar] [CrossRef]
108. Ni, J., Feng, G., Meng, Z., Hong, T., Chen, Y. et al. (2018). Reinforced lubrication of vegetable oils with graphene additive in tapping ADC12 aluminum alloy. Springer London, 94(1), 1031–1040. DOI 10.1007/s00170-017-0952-3. [Google Scholar] [CrossRef]
109. Ng, W. S., Lee, C. S., Chuah, C. H., Cheng, S. F. (2017). Preparation and modification of water-blown porous biodegradable polyurethane foams with palm oil-based polyester polyol. Industrial Crops & Products, 97, 65. DOI 10.1016/j.indcrop.2016.11.066. [Google Scholar] [CrossRef]
110. Chen, M., Zhong, M. J., Johnson, J. A. (2016). Light-controlled radical polymerization: Mechanisms, methods, and applications. Chemical Reviews, 116(17), 10167. DOI 10.1021/acs.chemrev.5b00671. [Google Scholar] [CrossRef]
Cite This Article
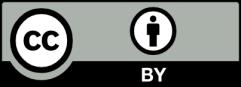
This work is licensed under a Creative Commons Attribution 4.0 International License , which permits unrestricted use, distribution, and reproduction in any medium, provided the original work is properly cited.