Open Access
ARTICLE
Experimental Study and Failure Criterion Analysis of Rubber Fibre Reinforced Concrete under Biaxial Compression-Compression
1 Department of Civil and Airport Engineering, Nanjing University of Aeronautics and Astronautics, Nanjing, 210016, China
2 College of Civil Engineering, Yancheng Institute of Technology, Yancheng, 224051, China
3 Department of Civil and Airport Engineering, Nanjing University of Aeronautics and Astronautics, Nanjing, 210016, China
4 College of Civil Engineering, Yancheng Institute of Technology, Yancheng, 224051, China
5 Department of Civil and Airport Engineering, Nanjing University of Aeronautics and Astronautics, Nanjing, 210016, China
6 Department of Civil Engineering, School of Mechanics and Engineering Science, Shanghai University, Shanghai, 200444, China
* Corresponding Author: Peiwei Gao. Email:
Journal of Renewable Materials 2023, 11(4), 2055-2073. https://doi.org/10.32604/jrm.2022.023612
Received 05 May 2022; Accepted 04 July 2022; Issue published 01 December 2022
Abstract
In order to examine the biaxial compression-compression properties of rubber fibre reinforced concrete (RFRC), an experimental study on RFRC under different lateral compressive stresses was carried out by considering different rubber replacement rates and polypropylene fibre contents. The failure modes and mechanical property parameters of different RFRC working conditions were obtained from the experiment to explore the effects of rubber replacement rate and polypropylene fibre content on the biaxial compression-compression properties of RFRC. The following conclusions were drawn. Under the influence of lateral compressive stress, the biaxial compression-compression failure mode gradually developed from a columnar pattern to a flaky pattern, suggesting that the incorporation of rubber and polypropylene fibres into the concrete resulted in a significant change in the development of cracks. For different rubber replacement rates and polypropylene fibre contents, the vertical compressive stress exhibited the same developing trend under the influence of lateral compressive stress. Specifically, the lateral compressive stress imposed the minimum effect on the vertical compressive stress when the rubber replacement rate and polypropylene fibre content were 20% and 0.4%, respectively, and imposed the maximum effect when the rubber replacement rate and polypropylene fibre content were 20% and 0%, respectively. With the increase of rubber replacement rate, the vertical peak stress was significantly reduced, which implies that an appropriate amount of polypropylene fibres can increase the vertical peak stress to a certain extent. Then, the biaxial compression-compression mechanism of RFRC was analysed from the microscopic level by using scanning electron microscope (SEM). Meanwhile, based on Kupfer’s biaxial compression-compression failure criterion and the octahedral stress space, a biaxial compression-compression failure criterion for RFRC was proposed, which was proven to have good applicability. The research results of this study provide important theoretical basis for the engineering application and development of RFRC.Keywords
Owing to a high deformation capacity and strong energy dissipation ability, rubber particles play a role of solid air-entraining agent in concrete to improve its frost resistance. Meanwhile, the bridging effect of polypropylene fibre in concrete can effectively inhibit the development and expansion of concrete cracks. By organically combining the advantages of rubber concrete and polypropylene fibre concrete, a novel type of concrete called rubber fibre reinforced concrete (RFRC) is formed, whose properties including impact resistance, toughness and frost resistance are significantly improved [1,2]. Moreover, since the rubber used in rubber concrete is usually derived from waste rubber tires, RFRC plays a positive role in promoting environmental protection by recycling waste resources. Therefore, comprehensive research on RFRC has an important scientific value and a great engineering application prospect [3].
To date, the research on the mechanical properties of rubber concrete and polypropylene fibre concrete is mostly carried out by focusing on the rubber or fibre physical properties, the concrete mix ratio, the loading method, and so on so forth. For example, Eldin et al. [4] carried out an experimental study on the compressive and tensile mechanical properties of concrete by considering different rubber replacement rates and rubber particle sizes. Their results suggested that the tensile and compressive properties of rubber concrete were significantly weakened while the deformation capacity was gradually improved with the increase of rubber replacement rate and the increase of rubber particle size. Topcu et al. [5] examined the deformation characteristics of rubber concrete and reported that the plastic deformation capacity and ductility of concrete were effectively improved by incorporating an appropriate amount of rubber into the concrete mixture. Through experimental analysis, Song et al. [6] found that an appropriate amount of polypropylene fibres could improve the compressive strength, tensile strength and impact resistance of concrete, and had a certain inhibitory effect on the initiation and development of early shrinkage cracks. Yao et al. [7] carried out experimental research on the compressive, splitting and flexural mechanical properties of low-mix fibre-reinforced concrete, and proposed the equations to calculate the maximum strength and flexural toughness of concrete under the action of different fibre mixtures. Li et al. [8] examined the dynamic mechanical properties of rubber concrete by considering different rubber replacement rates and proposed a model equation for describing the compressive peak stress dynamic increase factor under the coupling action of rubber replacement rate and strain rate. Ai et al. [9] carried out an experimental study on the dynamic mechanical properties of RFRC by considering the effects of rubber replacement rate and polypropylene fibre content and then proposed the action mechanisms of rubber and polypropylene fibres on the dynamic mechanical properties of concrete under compression.
In general, all the studies mentioned above applied the uniaxial loading method while examining the mechanical properties of rubber concrete or polypropylene fibre concrete. However, in practical engineering, concrete structures are usually subjected to a multiaxial stress state, so analysis of the mechanical properties of concrete merely based on uniaxial loading has deficiencies in understanding the actual structural safety and rational use of concrete. In view of this, comprehensive research on the multiaxial mechanical properties of concrete is of great scientific significance [10–12]. With respect to multiaxial mechanical properties of ordinary concrete, researchers usually focused on the influencing factors including multiaxial loading mode, lateral stress effect and loading history, for the purpose of developing the corresponding failure criterion and constitutive model [13]. For the multiaxial mechanical properties of RFRC, Xu et al. [14] examined its biaxial compression-compression properties by using specimens of the same strength grade but with different rubber replacement rates. By analysing the effect of rubber replacement rate on the biaxial compression-compression properties of RFRC, the authors established the corresponding failure criterion. Yu et al. [15] carried out an experimental study on the compression-shear multiaxial mechanical properties of RFRC by considering different rubber replacement rates and further analysed the influence of the coupling effect of axial compression ratio and rubber replacement rate on the shear mechanical properties. Zhang et al. [16] studied the compression-shear multiaxial mechanical properties of RFRC by considering 4 different mix ratios. Based on the analysis of the action mechanisms of rubber and polypropylene fibres in shear mechanical properties, the authors proposed the corresponding failure criterion. So far, the existing literature on the multiaxial mechanical properties of RFRC has only addressed the compression-shear loading mode, while reports on the mechanical properties of RFRC under other multiaxial loading modes are very rare. In order to dig deep into the multiaxial mechanical properties of RFRC and provide the experimental basis for establishing the corresponding mechanical model, more comprehensive research on the multiaxial mechanical properties of RFRC is needed.
This paper mainly aimed to examine the biaxial compression-compression properties of RFRC with different rubber replacement rates and polypropylene fibre contents. The failure modes and mechanical property parameters of RFRC under different working conditions were obtained from the experiment, which were used to analyse the influence of rubber, polypropylene fibres and lateral compressive stress on the vertical compressive stress and deformation parameters of RFRC and to reveal the corresponding stress mechanism. Meanwhile, based on Kupfer’s biaxial compression-compression failure criterion and the octahedral stress space, a biaxial compression-compression failure criterion for RFRC was proposed. The research results of this study provide important theoretical basis for the engineering application and development of RFRC.
In this paper, an experimental study was carried out on the biaxial compression properties of RFRC by considering the influencing factors of rubber replacement rate and polypropylene fibre content. The raw materials of RFRC mainly include cement, water, fine aggregates, coarse aggregates, rubber, and polypropylene fibres. Their specifications are as follows: cement (ordinary Portland cement P.O 42.5); fine aggregates (apparent density 2650 kg/m3); coarse aggregates (apparent density 2580 kg/m3, particle size 4–16 mm); rubber (particle size 2–5 mm, apparent density 1270 kg/m3, bulk density 820 kg/m3, tensile strength > 15 MPa, elongation at break > 500%); polypropylene fibres (length 19 mm, diameter 0.1 mm, tensile strength 322 MPa, elastic modulus 4.9 GPa). According to the conclusions reported in the related earlier studies [8,16] on the mechanical properties of rubber concrete and RFRC, the following working conditions were considered in this paper: 0% polypropylene fibre content and 0% rubber replacement rate (C-0%–0%); 0% polypropylene fibre content and 10% rubber replacement rate (C-0%-10%); 0% polypropylene fibre content and 20% rubber replacement rate (C-0%−20%); 0.2% polypropylene fibre content and 10% rubber replacement rate (C-0.2%−10%); and 0.4% polypropylene fibre content and 20% rubber replacement rate (C-0.4%−20%). The content of rubber was determined by replacing fine aggregates with equal volume of rubber particles, while the content of polypropylene fibres was determined by mixing fibres into the concrete mixture based on the mass ratio to the original mass of concrete mixture. In this paper, the C-0%−0% specimen (i.e., ordinary concrete) had a designed compressive strength of 30 MPa. The mix ratios of various RFRC specimens were then determined according to the “Specification for mix proportion design of ordinary concrete (JGJ55–2011)” and the predetermined admixture ratios mentioned above (see Table 1). Part of the raw materials used for preparing RFRC is shown in Fig. 1.
Figure 1: Part of the raw materials used for preparing RFRC
2.2 Loading Plan and Equipment
In this paper, the biaxial compression-compression properties of RFRC were examined by considering the influencing factors of rubber replacement rate, polypropylene fibre content and lateral compressive stress. Specifically, the lateral compressive stress was set to 0, (1/15) × fc, (2/15) × fc, (3/15) × fc, (4/15) × fc, (5/15) × fc, (6/15) × fc, (7/15) × fc and (8/15) × fc, where fc refers to the uniaxial compressive strength of RFRC under different mix ratios. The biaxial compression-compression loading was implemented by applying the lateral compressive stress with the load-controlled method first, at the loading rate of 0.8 MPa/min. After reaching the specified lateral compressive stress value, vertical load began to apply with the displacement-controlled method until specimen failure, at the quasi-static loading strain rate of 10–4/s. Upon completion of lateral compressive stress loading, the collection of load and displacement data was initiated for various working conditions. During the loading process, the combination of PTFE plastic films (3 layers) and mechanical butter was used to reduce the friction on the confining compression surface of the concrete specimen, in order to control the impact caused by friction on the experimental results [10]. In view of the randomness characteristics of concrete, 3 specimens were prepared for each loading condition in order to obtain the average value for analysis.
For the test equipment, a true tri-axial instrument equipped with independent hydraulic loading devices, load sensors and displacement sensors in each of the three directions was used to achieve biaxial compression-compression loading. The maximum load of the hydraulic loading device in each direction can reach 100 tons and the maximum displacement can reach 140 mm. The precision of the load sensors and displacement sensors can meet the measurement requirements of this paper. Fig. 2 illustrates the loading equipment and loading method.
Figure 2: Loading equipment and loading method
3 Analysis of Experimental Results
According to the biaxial loading plan described in the earlier section, the failure modes of RFRC under different lateral compressive stresses were obtained, which were used to analyse the effects of rubber, polypropylene fibres and lateral compressive stress on the failure mode of RFRC. In view of space limit, the working conditions corresponding to 0, (3/15) × fc, (6/15) × fc and (8/15) × fc were selected for comprehensive analysis, as shown in Fig. 3.
Figure 3: The biaxial compression-compression failure modes of RFRC
Fig. 3 shows the biaxial compression-compression failure modes of RFRC. When the rubber replacement rate and polypropylene fibre content remained constant, the failure mode gradually developed from a columnar pattern to a flaky pattern with the increase of lateral compressive stress, and the brittleness of the specimen reflected in the failure mode was gradually weakened. Under uniaxial vertical compressive stress, tensile strain was formed on the lateral surface. When the tensile strain reached the ultimate tensile strain, the specimen would fail with a columnar pattern as shown in Fig. 3. When the lateral compressive stress was small, the failure mode looked similar to that under the uniaxial loading condition. When the lateral compressive stress was large, compressive strain would be formed on the lateral surface in the lateral compressive stress direction, and tensile strain would be formed only on the lateral surface in the non-loading direction. Consequently, a flaky pattern failure mode was developed. The rubber replacement rate and polypropylene fibre content had little effect on the changing trend of the biaxial compression-compression failure mode under the influence of lateral compressive stress.
For specimens not containing rubber, there were a small number of cracks formed upon biaxial compression-compression failure with a relatively large crack size, exhibiting a developing trend penetrating the specimen towards the oblique direction. With the increase of rubber replacement rate, the integrity of the specimen after failure was improved, the crack size was gradually reduced, and the number of cracks was significantly increased. When rubber and polypropylene fibres were mixed into the concrete, the plastic characteristics of the specimen were obviously strengthened. In general, the developing trend and physical characteristics of the cracks of RFRC were similar to those of ordinary concrete, while differences mainly existed in the working conditions with non-zero lateral compressive stress: the compressive failure mode of specimens containing polypropylene fibres presented two main cracks in the oblique direction, which were accompanied by lots of small cracks and the pulling-out of some polypropylene fibres.
According to the biaxial loading plan in this paper, the load and deformation data of RFRC under different working conditions was obtained by the load sensors and displacement sensors, which were used to derive the biaxial compression-compression stress-strain curves, as shown in Figs. 4 and 5.
Figure 4: Vertical compressive stress-strain curves of RFRC under biaxial compression-compression
Figure 5: Lateral compressive stress-strain curves of RFRC under biaxial compression-compression
Fig. 4 shows the vertical compressive stress-strain curves of RFRC under biaxial compression-compression. For different rubber replacement rates, polypropylene fibre contents and lateral compressive stresses, the developing trends of the compressive stress-strain curves were basically the same, all showing good continuity and smoothness. The vertical compressive stress-strain curve of RFRC can be divided into the elastic stage, the elastic-plastic stage and the declining stage. It can be seen from the declining stage that, with the increase of rubber replacement rate and polypropylene fibre content, the plastic deformation capacity of RFRC was gradually increased, and the ductility characteristics were significantly improved. From the overall trend analysis, with the increase of rubber replacement rate, the vertical compressive stress was gradually decreased, while the vertical peak strain was significantly increased. The vertical compressive stresses of rubber-fibre concrete were obviously affected by lateral compressive stresses, which were higher than those under uniaxial compression.
Fig. 5 shows the lateral compressive stress-strain curves of RFRC under biaxial compression-compression. As the lateral displacement sensors might be subjected to a certain degree of deviation caused by the damage of the specimen during the measurement process, the developing trend of the stress-strain curve appeared to be unstable. When the lateral compressive stress was small, tensile strain was formed in the lateral compressive stress direction, while when the lateral compressive stress was large, compressive strain was formed in the lateral compressive stress direction. This changing trend is consistent with that of the failure mode of RFRC under the influence of lateral compressive stress.
The peak stress data was extracted from the vertical compressive stress-strain curve of RFRC as shown in Fig. 4, which was used to analyse the effects of rubber, polypropylene fibres and lateral compressive stress on the vertical peak stress under biaxial compression-compression, as shown in Figs. 6 and 7.
Figure 6: Lateral compressive stress and vertical peak stress of RFRC
Figure 7: Vertical peak stress of rubber, fibre and RFRC
Fig. 6 shows the lateral compressive stress and vertical peak stress of RFRC. For the specimen C-0%−0%, the uniaxial compressive peak stress was 25.94 MPa, while the vertical peak stress was increased to the interval of 29.44−32.27 MPa (increased by 12.48%−24.42%) under the influence of lateral compressive stress. For the specimens C-0%−10%, C-0%−20%, C-0.2%−10% and C-0.4%−20%, the uniaxial compressive peak stress was 19.69, 16.45, 18.80, and 17.34 MPa, respectively, while the vertical peak stress was increased to the interval of 22.88−25.56 MPa (maximum increase of 29.83%), 19.50–22.01 MPa (maximum increase of 33.81%), 22.90–25.03 MPa (maximum increase of 33.14%) and 19.43–21.30 MPa (maximum increase of 22.85%), respectively, under the influence of lateral compressive stress. When the lateral compressive stress ratio was lower than 0.2, the vertical peak stress of RFRC showed a gradually increasing trend with the increase of lateral compressive stress ratio. When the lateral compressive stress ratio was higher than 0.2, the vertical peak stress tended to show a stable developing trend with the increase of lateral compressive stress ratio. This trend was observed in all specimens with different rubber substitution rates and polypropylene fibre contents. The action mechanism can be explained as follows. The action of lateral compressive stress effectively improves the interaction between coarse aggregates, and at the same time, suppresses the development of initial damage inside the specimen. Therefore, as the lateral compressive stress increases, the vertical compressive stress shows a gradually increasing trend. When the lateral compressive stress is large, the specimen will be subjected to a high degree of damage under the action of lateral compressive stress. Coupled with the effect of lateral compressive stress in strengthening the interaction between coarse aggregates, eventually, the vertical peak stress shows a relatively stable developing trend as the lateral compressive stress increases under a large lateral compressive stress. According to the general trend analysis above, for specimens not containing polypropylene fibre, the increase in vertical compressive stress under the influence of lateral compressive stress was gradually increased with the increase of rubber substitution rate. When the polypropylene fibre content was 0.2%, the specimen C-0.2%−10% had a higher increase in the vertical compressive stress than C-0%−10% under the influence of lateral compressive stress. When the polypropylene fibre content was 0.4%, the specimen C-0.4%−20% had a lower increase in the vertical compressive stress than C-0%−20% under the influence of lateral compressive stress. Among all the specimens, C-0.4%−20% had the lowest increase in the vertical compressive stress under the influence of lateral compressive stress.
In this paper, the elastic modulus was calculated based on the stress-strain curves obtained from the uniaxial compression test of RFRC under different mixing conditions. The elastic modulus of C-0%−0%, C-0%−10%, C-0%−20%, C-0.2%−10% and C-0.4%−20% was 14.67, 9.99, 6.73, 8.19 and 6.23 GPa, respectively. The tensile peak stress of RFRC under different mixing conditions was obtained by the splitting tensile test, and the tensile peak stress of C-0%−0%, C-0%−10%, C-0%−20%, C-0.2%−10% and C-0.4%−20% was 1.445, 0.986, 0.8075, 1.14 and 1.02 MPa, respectively. With the increase of rubber replacement rate, the elastic modulus and tensile peak stress were gradually reduced. After incorporating an appropriate amount of polypropylene fibres into the concrete, the tensile peak stress was gradually increased, and the increasing range was higher than that under the compressive loading method. Polypropylene fibre at an appropriate amount can effectively exert its bridging effect, and this bridging effect is more obvious under the tensile loading mode than under compression mode. Therefore, the incorporation of polypropylene fibres has a stronger improving effect on the tensile peak stress than on the compressive peak stress.
Fig. 7 illustrates the influence of rubber and fibre on the vertical peak stress of RFRC. When the lateral compressive stress was 0, the vertical peak stress of C-0%−0%, C-0%−10%, C-0%−20%, C-0.2%−10% and C-0.4%−20% was 25.94, 19.69, 16.45, 18.80 and 17.34 MPa, respectively. For specimens not containing polypropylene fibres, the vertical peak stress showed a gradually decreasing trend with the increase of rubber replacement rate, and the maximum decrease was 36.58%. When the rubber replacement rate was 10%, the vertical peak stress of C-0.2%−10% was 18.80 MPa, which was 4.52% lower than that of C-0%−10%. When the rubber replacement rate was 20%, the vertical peak stress of C-0.4%−20% was 17.34 MPa, which was 5.41% higher than that of C-0%−20%. From the overall trend analysis, the vertical peak stress of C-0%−0%, C-0%−10%, C-0.2%−10%, C-0.4%−20% and C-0%−20% all showed a gradually decreasing trend, which was basically not affected by the lateral compressive stress. Since the bearing capacity of rubber is much lower than that of river sand and the contact between rubber and mortar is weaker, the vertical compressive stress of RFRC is gradually reduced with the increase of rubber replacement rate. When the polypropylene fibre content is at a moderate level, polypropylene fibres can play an effective role of bridging so as to improve the overall strength of concrete. When the polypropylene fibre content is too high or too low, the fluidity of the concrete mixture will be weakened due to the incorporation of polypropylene fibres, and more initial damage will be formed. Thus, the bridging effect of polypropylene fibres in the concrete mixture will be inhibited to a certain extent, so that the vertical compressive peak stress will be reduced accordingly.
The vertical strain value and lateral compressive strain value corresponding to the peak stress (i.e., peak strain) were extracted from the stress-strain curves of RFRC under biaxial compression-compression as shown in Figs. 4 and 5, which were used to analyse the influence of rubber, polypropylene fibres and lateral compressive stress on the peak strain of RFRC, as shown in Figs. 8 and 9.
Figure 8: Vertical peak strain of RFRC under biaxial compression-compression
Figure 9: Lateral peak strain of RFRC under biaxial compression-compression
Fig. 8 shows the vertical peak strain of RFRC under biaxial compression-compression. When the lateral compressive stress was 0, the vertical peak strain of C-0%−0%, C-0%−10%, C-0%−20%, C-0.2%−10% and C-0.4%−20% was 2120, 2563, 2848, 2980 and 3616 με, respectively. For specimens not containing polypropylene fibres, the vertical peak strain was significantly increased with the increase of rubber replacement rate, and the maximum increase reached 34.34%. When the rubber replacement rate was 10%, the vertical peak strain of C-0.2%−10% was increased by 16.27%. When the rubber replacement rate was 20%, the vertical peak strain of C-0.4%−20% was increased by 26.97%. For working conditions under different lateral compressive stress values, the vertical peak strain of RFRC was gradually increased with the increase of rubber replacement rate and polypropylene fibre content. Under the action of lateral compressive stress, the vertical peak strain of RFRC was higher than that under uniaxial compression, and the vertical peak strain showed a gradually increasing trend, which was observed in all the specimens with different rubber replacement rates and polypropylene fibre contents. The underlying mechanism for this developing trend is mainly related to the strong deformation capacity of rubber and the action of polypropylene fibres in the concrete.
Fig. 9 shows the lateral peak strain of RFRC under biaxial compression-compression. It can be seen that the developing trend of lateral peak strain under the influence of rubber replacement rate and polypropylene fibre content was basically similar to that of the vertical peak strain mentioned above. When the lateral compressive stress was low, the peak strain in the lateral compressive stress direction became tensile strain. As the lateral compressive stress increased, the tensile strain was gradually decreased. When the lateral compressive stress increased to (5/15) × fc, the peak strain in the lateral compressive stress direction changed from tensile strain to compressive strain. As the lateral compressive stress increased, the lateral peak strain of RFRC was gradually increased, which is consistent with the developing trend of the biaxial compression-compression failure mode under the influence of lateral compressive stress.
In this paper, the microscopic morphologies at the interfaces between mortar and coarse aggregates, between mortar and rubber, and between mortar and polypropylene fibres were obtained by using scanning electron microscope (SEM) to examine the microscopic mechanism of RFRC with different mix ratios, as shown in Fig. 10.
Figure 10: Apparent properties at the various interfaces of RFRC
Fig. 10 shows the apparent properties at the interfaces between each component of RFRC. For the specimen not containing rubber particles and polypropylene fibres, the interface between the mortar and coarse aggregates exhibited a better bonding performance. When the specimen was mixed with rubber particles, the contact interface between the mortar and rubber was relatively weak. As it can be seen, compared with specimens containing 0.2% fibres, there were more voids at the contact interface between the mortar and fibres in specimens with 0.4% fibres, indicating that the contact interface between the mortar and fibres was less compact.
The mechanism of RFRC under biaxial compression-compression can be explained as follows. When the lateral compressive stress is low, the action of lateral compressive stress inhibits the development of initial damage to a certain extent, which effectively strengthens the bite force between coarse aggregates, thereby increasing the vertical compressive stress. When the lateral compressive stress is high, the initial damage inside the specimen tends to develop; coupled with the bite force between coarse aggregates, the increase in vertical compressive stress will eventually become stable with the increase of lateral compressive stress [17]. The spacing between coarse aggregates directly affects the increase in vertical compressive stress under the influence of lateral compressive stress. When the specimen is mixed with rubber, the spacing between coarse aggregates will be effectively reduced under the action of lateral compressive stress due to a relatively high level of deformation capacity of rubber particles. Therefore, with the increase of rubber replacement rate, the effect of lateral compressive stress on the vertical peak stress of RFRC is gradually strengthened. When polypropylene fibres are mixed into the concrete mixture containing 10% rubber, the polypropylene fibres can effectively inhibit the development of micro-cracks during the loading process. When micro-cracks develop to the vicinity of coarse aggregates, the fibres will exert an inhibitory effect, so that the coarse aggregates will be able to play a strong bridging role. Eventually, the increase in vertical peak stress of RFRC under the influence of lateral compressive stress will be increased. For the specimen C-0.4%−20%, its microscopic morphology indicated that there were large voids between the mortar and polypropylene fibres. Due to the effects of rubber and polypropylene fibres, the initial damage inside the specimen was at a relatively high level. Under the action of lateral compressive stress, the initial damage would evolve in a connected and penetrating manner; consequently, the increase in vertical compressive stress at this working condition was reduced under the influence of lateral compressive stress.
4.2 Principal Stress Space Failure Criterion
Kupfer [18] proposed the concrete biaxial compression-compression failure criterion based on the test data of lateral compressive stress and vertical compressive stress, as shown in Eq. (1).
(1)
Eq. (1) can then be transformed into the expression of stress ratio, as shown in Eqs. (2)–(3) below:
(2)
(3)
where σZ is the vertical compressive stress under biaxial compression-compression (MPa); σX is the lateral compressive stress under biaxial compression-compression (MPa); fc is the peak stress under uniaxial compression (MPa); α is the stress ratio.
The test data of lateral compressive stress and vertical compressive stress of RFRC under 5 different mix ratios obtained in this paper was then compared with Kupfer’s biaxial compression-compression failure criterion, as shown in Fig. 11.
Figure 11: Comparison between the test data of compressive stress and Kupfer’s biaxial failure criterion
According to Fig. 11, the stress of C-0%−0% under biaxial compression-compression well conformed to Kupfer’s biaxial failure criterion. For the specimens C-0%−10%, C-0%−20% and C-0.2%−10%, Kupfer’s failure criterion appeared to be conservative relative to the test values, while for the specimen C-0.4% −20%, the test values appeared to be conservative relative to Kupfer’s failure criterion. The developing trends of vertical compressive stress under the influence of lateral compressive stress corresponding to different rubber replacement rates and polypropylene fibre contents were basically consistent with Kupfer’s failure criterion. Therefore, based on Kupfer’s failure criterion, the biaxial compression-compression failure criterion for RFRC was proposed in this paper, as shown in Eq. (4).
(4)
where, a and b are undetermined parameters. Considering the actual physical meaning of a, the value of a was set to 1.
Then, based on the test data of lateral compressive stress and vertical compressive stress corresponding to C-0%−10%, C-0%−20%, C-0.2%−10% and C-0.4%−20%, the biaxial failure criterion equation for RFRC was obtained by performing mathematical regression analysis on Eq. (4), as shown in Fig. 12.
Figure 12: Biaxial compression-compression failure criterion of RFRC
According to Fig. 12, the value of b for C-0%−10%, C-0%−20%, C-0.2%−10% and C-0.4%−20% was 3.97, 4.16, 4.17 and 3.44, respectively. The biaxial failure criterion for RFRC obtained from Eq. (4) has good applicability in quantitatively describing the developing trend of vertical compressive stress under the influence of lateral compressive stress, and is consistent with the qualitative analysis conclusions of this paper.
4.3 Octahedral Stress Space Failure Criterion
The criterion equation constituted by three-dimensional stress (i.e., σX, σY and σZ) has a hydrostatic compression axis equal to the included angle of each coordinate. The stress state of the hydrostatic compression axis conforms to σX = σY = σZ; the plane perpendicular to the hydrostatic compression axis is the plane π; and the normal stress and shear stress on plane π are σoct and τoct, respectively. The corresponding expressions are shown in Eqs. (5)–(6) [19].
(5)
(6)
In this paper, the concrete specimens were set under a biaxial compression-compression loading condition during the experiment, so σY = 0. Thus, Eqs. (5)–(6) can be simplified to Eqs. (7)–(8).
(7)
(8)
According to the octahedral stress space and the related literature [19], the octahedral stress space failure criterion for RFRC with a three-parameter expression form was proposed, as shown in Eq. (9).
(9)
where, c, d and e are all undetermined parameters.
According to the biaxial compression-compression test data of RFRC with different rubber replacement rates and polypropylene fibre contents in this paper, the values of σoct and τoct were calculated by Eqs. (7)–(8). Then, mathematical regression was performed through Eq. (9), and the parameter values and expressions as shown in Table 2 and Fig. 13 were obtained.
Figure 13: Failure criterion of RFRC based on the octahedral stress space
According to Table 2 and Fig. 13, it can be seen that the biaxial compression-compression failure criterion for RFRC under different rubber replacement rates and polypropylene fibre contents proposed based on the octahedral stress space can well describe the developing trend of vertical compressive stress under the influence of lateral compressive stress.
In this paper, an experimental study was carried out on the biaxial compression-compression properties of RFRC with different rubber replacement rates and polypropylene fibre contents, and the effects of rubber, polypropylene fibres and lateral compressive stress on the biaxial compression-compression properties of RFRC were analysed comprehensively. In summary, the following conclusions were drawn:
Under the action of biaxial compression-compression, the failure mode of RFRC gradually developed from a columnar pattern under a low lateral compressive stress to a flaky pattern under a high lateral compressive stress. This developing trend was observed in all specimens with different rubber replacement rates and polypropylene fibre contents. As the rubber replacement rate increased, the integrity of the specimen upon compressive failure was improved, the crack size was decreased, and the number of cracks was increased. For specimens mixed with rubber and polypropylene fibres, when the lateral compressive stress was not zero, the compressive failure mode was mainly manifested as two penetrating cracks accompanied by lots of small cracks and the pulling-out of some polypropylene fibres.
With the increase of lateral compressive stress, the vertical compressive stress of RFRC showed an increasing trend first and then tended to stabilise under all working conditions, which means that the rubber replacement rate and polypropylene fibre content had little effect here. For the specimens C-0.4%−20%, C-0%−0%, C-0%−10%, C-0.2%−10% and C-0%−20%, the maximum increase in vertical compressive stress under the influence of lateral compressive stress was gradually increased. With the increase of rubber replacement rate, the vertical peak stress was significantly reduced. Therefore, polypropylene fibres at an appropriate amount can increase the vertical peak stress to a certain extent. Under the influence of rubber substitution rate and polypropylene fibre content, the vertical peak stress of RFRC showed the same developing trend under different lateral compressive stresses.
With the increase of lateral compressive stress, the vertical peak strain of RFRC showed a gradually increasing trend. The vertical peak strain under biaxial compression-compression was larger than that under uniaxial compression. With the increase of either rubber replacement rate or polypropylene fibre content, the vertical peak strain of RFRC was gradually increased and the plastic deformation capacity was significantly improved. The peak strain in the lateral compressive stress direction is directly related to the lateral compressive stress. The developing trend of peak strain in the lateral compressive stress direction can quantitatively reflect the changing trend of the biaxial compression-compression failure mode of RFRC under the influence of lateral compressive stress.
The SEM technology was used to analyse the microscopic morphology of RFRC for the purpose of revealing the biaxial compression-compression stress mechanism of RFRC. Based on Kupfer’s biaxial compression-compression failure criterion and the octahedral stress space, the biaxial compression-compression failure criterion for RFRC by considering different rubber replacement rates and polypropylene fibre contents was proposed, which was proven to have good applicability.
Funding Statement: This work was supported by the National 12th Five Year Plan of Science and Technology Support Project (2015 BAL02b02), National Spark Plan Project (2015 GA690045), Jiangsu Province “Six Talent Peaks” Team Project (XCL-CXTD−007).
Conflicts of Interest: The authors declare that they have no conflicts of interest to report regarding the present study.
References
1. Amiri, M., Hatami, F., Golafshani, E. M. (2022). Evaluating simultaneous impact of slag and tire rubber powder on mechanical characteristics and durability of concrete. Journal of Renewable Materials, 10(8), 2155–2177. DOI 10.32604/jrm.2022.019726. [Google Scholar] [CrossRef]
2. Zhang, J. K., Xu, J. C., Liu, C. S., Zheng, J. (2021). Prediction of rubber fiber concrete strength using extreme learning machine. Frontiers in Materials, 7, 582635. DOI 10.3389/fmats.2020.582635. [Google Scholar] [CrossRef]
3. Tian, L., Qiu, L. C., Li, J. J., Yang, Y. S. (2020). Experimental study of waste tire rubber, wood-plastic particles and shale ceramsite on the performance of self-compacting concrete Journal of Renewable Materials, 8(2), 153–170. [Google Scholar]
4. Eldin, N. N., Senouci, A. B. (1993). Rubber-tire particles as concrete aggregate. Journal of Materials in Civil Engineering, 5(4), 478–496. DOI 10.1061/(ASCE)0899-1561(1993)5:4(478). [Google Scholar] [CrossRef]
5. Topcu, I. B. (2020). The properties of rubberized concretes. Cement and Concrete Research, 25(2), 304–310. DOI 10.1016/0008-8846(95)00014-3. [Google Scholar] [CrossRef]
6. Song, P. S., Hwang, S., Sheu, B. C. (2005). Strength properties of nylon- and polypropylene-fiber-reinforced concretes. Cement & Concrete Research, 35(8), 1546–1550. DOI 10.1016/j.cemconres.2004.06.033. [Google Scholar] [CrossRef]
7. Yao, W., Li, J., Wu, K. (2003). Mechanical properties of hybrid fiber-reinforced concrete at low fiber volume fraction. Cement & Concrete Research, 33(1), 27–30. DOI 10.1016/S0008-8846(02)00913-4. [Google Scholar] [CrossRef]
8. Li, F. R., Wu, Y. Y., Xie, X. H., Zhao, K., Yu, Z. P. (2021). Experimental study on the dynamic behavior of rubber concrete under compression considering earthquake magnitude strain rate. Journal of Civil Engineering and Management, 26(8), 733–743. DOI 10.3846/jcem.2020.13728. [Google Scholar] [CrossRef]
9. Ai, S. P., Tang, P. (2021). Compression dynamic behavior of rubber fiber reinforced concrete under action of earthquake magnitude. Journal of Building Materials, 10(5), 1002–1010. [Google Scholar]
10. Shang, H. S., Song, Y. P. (2006). Experimental study of strength and deformation of plain concrete under biaxial compression after freezing and thawing cycles. Cement and Concrete Research, 36(10), 1857–1864. DOI 10.1016/j.cemconres.2006.05.018. [Google Scholar] [CrossRef]
11. Yu, Z. P., Tang, R., Li, F. R., Hu, Y. L., Liu, G. Q. et al. (2021). Experimental study and failure criterion analysis on combined compression-shear performance of rubber concrete (RC) with different rubber replacement ratio. Construction and Building Materials, 288, 123105. DOI 10.1016/j.conbuildmat.2021.123105. [Google Scholar] [CrossRef]
12. Cui, J., Hao, H., Shi, Y. C., Zhang, X. H., Huan, S. (2019). Volumetric properties of concrete under true triaxial dynamic compressive loadings. Journal of Materials in Civil Engineering, 31(7), 04019126. DOI 10.1061/(ASCE)MT.1943-5533.0002776. [Google Scholar] [CrossRef]
13. Cao, Q., Lv, X. R., Wu, Z. M., Zhou, C. J., Wang, X. C. (2021). Failure criteria and constitutive model of polypropylene fiber-reinforced expansive self-consolidating concrete under biaxial loading. Journal of Materials in Civil Engineering, 33(12), 04021371. DOI 10.1061/(ASCE)MT.1943-5533.0004006. [Google Scholar] [CrossRef]
14. Xu, J., Niu, X. L., Yao, Z. Y. (2021). Mechanical properties and acoustic emission data analyses of crumb rubber concrete under biaxial compression stress states. Construction and Building Materials, 298, 123778. DOI 10.1016/j.conbuildmat.2021.123778. [Google Scholar] [CrossRef]
15. Yu, Z. P., Huang, Q., Xie, X. H., Xiao, N. (2019). Experimental study and failure criterion analysis of plain concrete under combined compression-shear stress. Construction and Building Materials, 179, 198–206. DOI 10.1016/j.conbuildmat.2018.05.242. [Google Scholar] [CrossRef]
16. Zhang, J. T., Yu, Z. P., Sun, X. J., Zhang, G. L., Pan, W. G. (2021). Experimental study and failure mechanism analysis of rubber fiber concrete under the compression-shear combined action. Advances in Materials Science and Engineering, 2021, 5554257. DOI 10.1155/2021/5554257. [Google Scholar] [CrossRef]
17. Geel, E. V. (1998). Behaviour of concrete in multiaxial compression. The Netherlands: Eindhoven University of Technology. [Google Scholar]
18. Kupfer, H. B. (1969). Behavior of concrete under biaxial stresses. Journal of the Engineering Mechanics Division Asce, 99(8), 853–866. [Google Scholar]
19. Rong, C., Shi, Q. X., Zhang, T., Zhao, H. C. (2018). New failure criterion models for concrete under multiaxial stress in compression. Construction and Building Materials, 161, 432–441. DOI 10.1016/j.conbuildmat.2017.11.106. [Google Scholar] [CrossRef]
Cite This Article
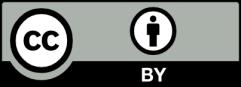
This work is licensed under a Creative Commons Attribution 4.0 International License , which permits unrestricted use, distribution, and reproduction in any medium, provided the original work is properly cited.