Open Access
REVIEW
A Review of the Advances Made in Improving the Durability of Welded Wood against Water in Light of the Results of African Tropical Woods Welding
1 Laboratory of Forest Resources and Wood Valorization, University of Douala, P.O. Box. 2701, Douala, Cameroon
2 Laboratory of Mechanics, University of Douala, P.O. Box. 2701, Douala, Cameroon
3 CETELOR, University of Lorraine, P.O. Box. 21042, Epinal, France
4 ENSTIB-LERMAB, University of Lorraine, P.O. Box. 21042, Epinal, France
5 Laboratory of Energetics and Thermal and Mass Transfers, El Manar University of Tunis, Tunis, Tunisia
* Corresponding Authors: Jean Jalin Eyinga Biwôlé. Email: ; Antonio Pizzi. Email:
(This article belongs to the Special Issue: Renewable and Biosourced Adhesives-2021)
Journal of Renewable Materials 2023, 11(3), 1077-1099. https://doi.org/10.32604/jrm.2023.024079
Received 23 May 2022; Accepted 03 August 2022; Issue published 31 October 2022
Abstract
Wood plays a major role in the production of furniture and wooden structures. Nevertheless, in this process, the massive use of adhesives and plural connectors remains a definite problem for health and the environment. Therefore, wood welding is a breakthrough in this respect. This paper reviews the applications of wood welding in furniture and construction and then examines advances in improving the durability of welded wood against water. Our contribution also highlights the need to join African tropical woods using the rotational friction welding technique. According to our results, these woods present interesting chemical singularities, which could provide solutions to the water vulnerability of the welded wood. Moreover, the use of such a joining method would first free the Cameroonian furniture industry from the chemical industry, secondly position it at the forefront of new eco-design trends and thirdly make it competitive with other countries in the Central African sub-region. These works enrich the long and rich bibliography on the technique of wood welding, which has long been conspicuous by its absence of tropical woods.Keywords
Nowadays, the development of a sustainable society promoting the use of recyclable materials and the understanding of environmental issues is a major challenge for our civilization [1,2]. In this perspective, the furniture and construction industry must be given increased attention, especially in developing countries where wood resources are a major concern [3].
In furniture and building applications, assembly is the basis for any architectural arrangement of wooden work [4]. It can be achieved using fasteners (metal or plastic) or adhesives [5,6]. Synthetic adhesives, commonly used in woodworking, are usually of petrochemical origin. Not only do they require relatively long curing times, but they also represent a source of health problems and environmental contamination [7–9]. For this reason, the optimization of wood joints using new environmentally friendly techniques in furniture and construction (Fig. 1) is of paramount importance [10]. In this perspective, history reveals that the first rotary friction welding process was established in 1891 by Bevington to shape and weld the ends of two tubes; subsequently, thermoplastic resin joining techniques were implemented in the plastic and automotive industry in the 1940s in this way Henning made the first joints with plastic materials [3]. Since then, these techniques have also spread to the manufacture of wood products such as glued laminate floors, using polypropylene or nylon placed between the surfaces to be joined. The polymerization of these resins can be obtained by a linear or circular friction process. However, these resins, which are derived from petrochemicals, have the ecological disadvantages already mentioned above, whether during their implementation, during their use or at the end of the product’s life. Conversely, it is now possible to join different materials, such as steel and aluminum, wood and aluminum, using these techniques [11]. Based on the results of work undertaken in the last few decades, the ability to join two pieces of wood without the use of an exogenous connector has emerged as an important technological innovation in the field of construction and furniture [1,12]. The first attempts to join wood by friction only began in the 1990s [13,14]. Suthoff et al. [13] in Germany documented the first work on friction welding of wood and patented the process. In this study and a subsequent patent, Suthoff et al. [14] established that wood parts can be joined in an inert atmosphere or vacuum by oscillating frictional motion. Several other works [1,6,15–30] carried out mainly with temperate woods, including common spruce (Picea abies L. Karst.) and beech (Fagus sylvatica L.), were undertaken largely on small pieces, but much larger specimens (Fig. 2) were also used [31–40]. At the same time, attempts have been made to adapt other types of wood, aluminum, metal, and plastic welding to small parts, such as ultrasonic and micro-motion welding techniques [11,41]. Some authors have also suggested that it would be possible to join wood parts with a wooden dowel using rotary friction welding. To this end, pioneering studies by Pizzi et al. [15] used rotary friction welding to secure two pieces of wood with wooden dowels, and the process was found to provide effective lignofixation between the wooden dowel and the pre-drilled wood. Subsequently, further work has shown that the disadvantage of being too flexible was present in softwood structural members joined by welding. An improvement of the mechanical behavior of these wood-wood connections was necessary. This improvement could be achieved by increasing the contact areas to transmit most of the forces [42]. Then, a heat transfer model was also developed for wood dowel welding and was found to be robust in predicting the temperature increase and its trends in the weld as a function of time, its decrease after friction welding stops, and the spread and decay of the heat generated by the weld to areas of the wood substrate progressively further away from the weld line [43]. In addition, a hybrid version of the linear and rotary methods, called orbital or circular welding, has also been developed but provides lower quality joints [44].
Figure 1: House made of solid wood panels (Nur Holz) without glue or chemical treatment [40]
Figure 2: Some life-size assemblies of wooden parts with dowels: (a) The work is fast, clean and precise after planning and brushing the visible faces of the panels, (b) The manufacture of a “Nur Holz” panel is the assembly of wooden lamellas held by threaded and screwed beech dowels [40], (c) Four-layer beam with 20 dowels held in clamps during construction [36]
The refinement and limitations of this innovative joining technique have been the subject of much research. This paper provides a thematic review (Table 1) of wood welding applications in furniture and construction and then examines the advances made to improve the natural durability of the welded wood against water. In addition, it explores the large-scale implementation of welding of African tropical woods, which have long been underrepresented in this field of research.
2 Retrospective of Wood Welding Work
Wood welding is a joining technique based on the melting and flowing of wood fiber wall constituents, primarily lignin and hemicelluloses [4,6,45,46]. During the friction of the two pieces of wood together, the melting of amorphous polymers results from the high temperatures (over 180°C) reached between 4 and 5 s at the interface [15]. This leads to the formation of entanglement of fibers that are locally highly compressed and where the melting of the intercellular, middle lamella lignin and hemicelluloses produces, after solidification under load, adhesion of the parts together, forming a high-density composite at the interface [6]. The resulting welded joint consists of a molten lignin-based polymer matrix [47]. The high temperatures reached during friction lead to the formation of furfural. Although it is not the main contributor to the weld, it is not produced in abundance. The contribution of this hydrophobic carbohydrate derivative to chemical bonding with lignin during welding is very small. Nevertheless, after melting, furfural contributes to the solidification phase of the resulting weld joint by maintaining compressive stress [6,15]. In addition, the temperature generated during the welding process is substantially correlated with the optimal welding parameters and wood anatomy [4,47]. Four different types of oscillating friction motion are typically used for wood welding, as shown in Fig. 3. In the first case (Fig. 3a), a pair of specimens are placed in a friction machine that simultaneously applies (i) transverse motion at a given frequency and (ii) pressure orthogonal to the welding plane. The parameters to be optimized include a linear amplitude frequency for a given time (t), a compression force, and finally, a pressure hold time of 5 s after the friction stops. With regards to the second case (Fig. 3b), the friction movements in orbital and circular welding are similar. In the case of orbital friction welding, the motion is elliptical, so the force and velocity are sinusoidal [44]. In the third case (Fig. 3c), the motion is circular; the velocity and frictional force are constant during the process. Finally, in the fourth case (Fig. 3d), the connection is obtained either (i) by inserting cylindrical dowels into holes smaller than the diameter of the dowel (Pizzi et al. [15], Kanazawa et al. [17]) or (ii) by inserting dowels whose ends have been previously tapered, but this time without prior drilling of the support [19].
Figure 3: Movements, velocities and forces in four different types of frictional welding: (a) Linear friction, (b) Orbital friction, (c) Circular friction and (d) Rotary friction welding [26]
For this purpose, the use of a variable speed automatic drill is essential. Among the parameters to be optimized are the speed of rotation, the depth of the pre-drilled hole and the ratio between the diameter of the pre-drilled hole and the diameter of the dowel and the rate of insertion of the dowel in the predrilled wood substrate [46]. Several analyses have been performed, including qualitative and quantitative. The studies by Pizzi et al. [15], Kanazawa et al. [17], and Leban et al. [16] were visualized and confirmed by mapping the densification of the weld interface using scanning electron microscopy and X-ray microdensitometry. These measurements included different species of wood as well as different orientations of the specimens during welding [18,48]; for example, in the four images in Fig. 4 taken at different magnifications. In Fig. 4a, intact tracheids can be seen in the upper-left portion of the image as well as in the right portion. Similarly, in the lower-left portion of the image, one can see the molten material that makes up the welded joint in which a fiber bundle torn off when the joint was opened is immersed. Next, in Fig. 4b, intact tracheal cells can be seen immersed in molten polymer magma as well as heavily immersed tracheal cells clinging to the substrate. Fusion occurred very locally at the medial lamella of the tracheal cells, the most lignin-rich (Fig. 4c) but also a fusion of hemicelluloses, in particular, xylans contributing to the formation of the polymer melt [6,15,18,49]. The welded joint is thus composed of an entanglement of cells immersed in a matrix of an amorphous intercellular material composed mainly of lignin but also of hemicelluloses (Fig. 4d). In parallel, densitometric profiles quantitatively describing the densification of interface joints resulting from the friction welding process were studied (Fig. 5). These parameters were the joint width, and the maximum density achieved given the average density of each specimen [50]. Simultaneously, Fig. 6 shows experiments performed in orbital welding to determine the influence of optimal parameters [51].
Figure 4: Welded joints visualized at various magnifications: (a) Welded joint in which the molten material constituting the binder of the weld joint is observed, in which a bundle of fibers torn off during the opening of the joint is immersed, (b) Welded joint consisting of intact fibers while at the top one observes molten wood and a strongly curved tracheid fiber whose surface shows a melting facies, (c) Welded joint consisting of a curved fiber inserted in support of the material which has melted, (d) Welded joint consisting of tracheids whose wall has melted. This illustrates the highly localized nature of fusion [50]
Figure 5: The wooden nail experiment: effect of spruce ring width on beech wood nail insertion illustrated in terms of wood densification and the shape of the inserted part of the nail [50]
Figure 6: Classification of the process into different phases (I–VI) by means of the progression of the friction coefficient as a function of the interfacial temperature (exemplary for a sample of Norwegian spruce welded with a welding pressure PN = 0.78 MPa and a frequency of 130 Hz) and of the characteristic points S, E1, I, P, E2, F. The graph is valid only for orbital welding [26]
The chemical and physical reactions of welding have been studied. Indeed, during welding, the thermal energy of friction is used to soften the wood constituents, which are lignin and hemicelluloses. In the work of Stamm et al. [27], Stamm et al. [25], the formation of the “molten” material was examined using chemistry and spectroscopy to better understand the thermal reactions, thermal decomposition, and alteration of the wood constituents during the welding process between 420°C and 440°C. Their results revealed that hemicelluloses were degraded in substantial amounts while cellulose remained fairly stable. Lignin also underwent unique changes, as evidenced by an increase in the number of free phenolic groups and a decrease in typical phenol-propane bonds. They also found furan derivatives in the volatile components of the gaseous emissions, primarily the hemicelluloses. They determined that the main reactions in the friction zone that led to cross-linking of the “molten” contact material were interactions between furfural and other furan derivatives with lignin. Gfeller et al. [6], Pizzi et al. [15], Ganne-Chédeville et al. [19], and Kanazawa et al. [17] studied this material and found that the critical chemical changes affecting the polymeric elements of the wood during friction welding occur within 5, 6 s and then slows down or stop. The welded area of the wood was extensively studied by FTIR and CP-MAS 13C NMR, which revealed dehydration and an apparent increase in cellulose crystallinity. Some degradation of hemicellulose was observed, as well as the production of furfural. The degradation of cellulose is quite slow. The percentage of lignin in the fused interface increases in both analytical methods.
The internal rearrangement of lignin causes self-condensation, which persists during the welding process. The wood begins to carbonize after six seconds of welding, and the cross-linking of the lignin network increases. Ganne-Chédeville et al. [19] proposed to control the temperature variation at the interface in order to produce the frictional energy necessary for the reaction of furfural and other furan derivatives with lignin and to obtain good adhesion between the two pieces of wood [20,21]. In addition, the gases emitted during wood welding were determined by Py-GC/MS and by gas chromatography coupled with a thermal conductivity detector and a flame ionization detector (GC-TCD/FID) [30,52]. It has also been clearly established that thermal melting degrades hemicelluloses and affects the lignin polymer by depolymerization [4,10,15,49]. In contrast, pyrolytic gas chromatography-mass spectrometry (Py-GC/MS), attenuated total reflection Fourier transform infrared spectroscopy (ATR-FTIR), and X-ray photoelectron spectroscopy (XPS) has been used to explain thermochemical changes during wood welding. To date, the wood welding joining technique has reached a good technological level not only in the furniture industry but also in structural applications. Contrary to what one might think, the mechanical strength of welded wood is compromised when subjected to high moisture: its ability to resist pull-out decreases with increasing moisture content. This can be attributed to the hygroscopic nature of wood and the open, penetrable structure of the fibers and molten composite matrix that forms, which stresses the welded joint and causes cracking [53,54]. Nevertheless, understanding the hygroscopic nature of treated wood can help mitigate the effects of progressive shrinkage and swelling of welded wood [55,56]. The poor natural water resistance of welded wood, meanwhile, can be demonstrated for furniture and construction. In recent years, work to improve this drawback has been developed through four main approaches.
2.1 Optimization by Thermal Modification and Chemical Treatments of Wood
According to this approach, heat treatment is used as both an effective and environmentally friendly way to improve the hygroscopic nature and biological durability of wood because it increases its dimensional stability by reducing water absorption [28,56–58]. Nevertheless, the high temperatures involved cause a reduction in the mechanical properties of the wood. The unwanted disintegration of the wood cell wall is the cause of this decrease [28,56,59]. On the other hand, Haller et al. [60] investigated the effects of laser irradiation on wood in terms of structural, chemical, and physical characteristics and determined the laser parameters that prevent pyrolysis and melting of wood. Subsequently, Sandberg [61], Johansson et al. [62] observed a melted surface when treating aged pine and spruce samples with UV laser ablation [63,64]. Bianchi et al. [65] described an attempt to fabricate a glued spruce slat panel by linear friction welding. This process was an interesting alternative to the usual technology of hot pressing with glue, but it had disadvantages, such as the high amount of volatile products by thermal decomposition of the wood and the fact that the maximum achievable mechanical characteristics obtained were below the current standards. The micro-level phenomena that occur during friction welding were also found to have an interesting interaction with laser wood treatment. In contrast, Pizzi et al. [55] showed that acetylated low molecular weight organosolv lignin from wheat straw and depolymerized low sulfur organosolv lignin from wood significantly improved the water resistance and mechanical performance of spin welded joints. However, the ductility of the joints was proved in mechanical tests and attributed to the interpenetration of the elastic network of acetylated lignin into the stiffer composite network of the welded joint. Today, still the best method to improve the water-resistance of wood welding, both linear and rotational, is to use rosin as a waterproofing system of the interface, as this is applied in thin-film melts and is water-repellant impeding water to reach the welded interface [66,67]. In fact, this natural method was first derived from the soldering of loblolly pine which is naturally rich in rosin, which upon increasing the temperature during soldering melted and migrated to the interface, making it impermeable [68].
2.2 Optimization by Parameters Related to the Structure and Chemical Composition of Wood
According to this approach, the natural water durability of welded wood is shown to be substantially related to the amount and type of extractives it contains, particularly because some extractives have a low affinity for water, resulting in low water uptake in the welded zone [67–70]. Eyinga Biwôlé et al. [70] stated that this durability is also closely correlated with polyphenol content. In the same way, that lignin acts as a protective barrier against water penetration into the material and hemicelluloses as a bonding agent between the cellulose fibrils and the lignin matrix, these elements have a major effect on the adhesion of the welds [6,15]. Other authors show that welded joints are less sensitive to moisture when heartwood is used due to its increased extractive content and that increasing the moisture contact angle leads to decreased water absorption and swelling of the welded joint [53,62,71]. In contrast, a multi-species arrangement by high-speed rotation-induced wood dowel welding significantly improves water resistance. Stamm et al. [27] formed a multi-layered wood element consisting of alternating spruce and beech with eight 6 mm thick laminations. The experiment showed that this element could be used instead of a laminated wood beam or a glued wood panel element.
2.3 Optimization through Optimal Welding Parameters
In this approach, some authors show that vibration frequency, insertion speed, pressure, grain orientation, short displacement, and short welding time improve the water-resistance of the welded joints [4,12,29,47,72,73]. On the other hand, the type of linear or rotational welding also seems to improve this resistance. Some authors have demonstrated that a zigzag pattern of dowels spin-welded at the interface of a butt joint between two wood planks (Fig. 7) yields strong joints capable of withstanding a 2-h immersion in boiling water, as well as subsequent oven drying [17,55]. Extensive studies of fracture mechanics on linear welded wood were conducted [74]. Also noteworthy are the extensive optimization studies conducted by Segovia et al. [75,76] and Segovia et al. [77] on all types of furniture joints.
Figure 7: Schematic representation of (a) Zigzag dowel insertion scheme in the wood substrate and (b) Insertion angles of dowels in the substrate [45]
2.4 Optimization through Treatments with Natural Extracts
In this approach, pioneering studies have proven the effectiveness of some environmentally friendly natural additives. Vaziri et al. [54] tested the effect of wollastonite on the water resistance of welded pine specimens using the Wilhelmy plate method with multiple cycles. The results of this study show a significant decrease in water absorption and swelling within a welding time of 5 s. Segovia et al. [5] treated beech dowels with sunflower oil. The major result of this study showed that the use of sunflower oil provides better water resistance for the welded joint. Using time-of-flight matrix-assisted laser desorption ionization analysis, Eyinga Biwôlé et al. [78] identified non-leachable oligomers in Padauk extracts, justifying the improved natural water durability of welded beech. Wieland et al. [79] found that the use of natural tannins and furfural, through self-condensation and polymerization, somewhat improves the water resistance of welded beech, common spruce, oak, and mixed spruce/beech. Citric acid has recently been presented as a binder for wood and has been shown to react readily with temperature, lignin, and carbohydrates in the wood [80]. According to Del Menezzi et al. [81], its main contribution was to improve the water resistance of wood joints. Subsequently, Amirou et al. [82] showed that the use of citric acid at different percentages (Fig. 8) on spruce wood also markedly improves the resistance of welded joints during frequent short and long-term water exposure. In addition, the use of a combination of waterproofing rosin and joint formers by Pizzi et al. [67] showed that treatment of welded joints in a 25% rosin solution in ethanol significantly improves joint strength in an outdoor environment. Underwater immersion, welded dowel joints show acceptable strength at more than 500 days. Mansouri et al. [66] treated welded joints with high-temperature molten rosin from pine wood. The results of this study showed exceptional tensile and shear strength of the joints after 200 days of immersion in cold water.
Figure 8: Comparison by superposition of CP-MAS 13C-NMR spectra of treated (40% citric acid) and untreated (0% citric acid) samples [82]
In summary, it is clear that these multiple techniques have so far been insufficient to qualify an external product without protection. Furthermore, these attempts at improvement have been much more focused on natural extracts from temperate woods and crops, while natural extracts from tropical woods have been largely relegated to the background. It would be appropriate to use their natural substances from leaves, bark, and sawdust to improve the water-resistance of welded wood.
3 Wood Socio-Economic Impact and the Local Furniture Industry in Cameroon
Central African countries, including Cameroon, are home to significant forestry potential that contributes significantly to local economies [83]. Cameroon’s forests contain more than 300 species, of which about 80 are currently exploited commercially [84,85]. In addition, local timber resources are the second largest export product after oil and contribute about 2.7% of the country’s gross domestic product [86–88]. The turnover of the individual artisanal sawmilling sector on the national market and the markets of neighboring countries is approximately 98 606 320.80 $, while that of the community artisanal exploitation is estimated at approximately 1 535 924 $. The total annual net financial benefits generated by artisanal timber exploitation in Cameroon are estimated at 17 263 785.76 $. Cerutti et al. [89] have produced recent estimates of annual artisanal sawmilling production in Cameroon (Table 2). Meanwhile, Table 3 shows the evolution of log production and industrial processing in Cameroon from 2012 to 2017. We observe a 109% increase in annual industrial sawlog production over this period.
According to Lescuyer et al. [90], local wood consumption is about 755 000 m3 per year, of which, more than 90% of this volume is in the form of boards, formwork, and rafters, intended for use in construction. This local wood consumption is also used to supply a wide range of items targeted to meet the needs of urban consumers in local markets [91–93]. The five most locally consumed species, accounting for about 70% of local sales, are Ayous (Triplochyton scleroxylon), which is by far the most consumed with 35% of sales; followed by Movingui (Distemonanthus benthamianus), Iroko (Milicia excelsa), Sapelli (Entendrophragma cylindricum) and Bilinga (Nauclea diderichii) [85]. Despite this, in Cameroon, most local industries are still subject to primitive use of wood material with rudimentary tools and very limited technology, which does not facilitate standardization [85].
To ensure the structuring of this sector, the Cameroonian government has made international commitments, particularly within the framework of the Voluntary Partnership Agreement on Forest Law Enforcement, Governance and Trade (VPA FLEGT) process with the European Union, in order to preserve access to this traditional market for its legal exports of wood products [94]. In this perspective, the commitments made by Cameroon at the international level have required numerous adjustments and constraints at the national level and for stakeholders in the timber sector. These include: (1) the decision to create the regional committee for the sustainable industrialization of the timber sector in the Congo Basin; (2) the regulation on the attributions, organization and functioning of the regional committee for the sustainable industrialization of the timber sector in the Congo Basin; (3) the decision to ban the export of timber in the form of logs by all countries of the Congo Basin, as of January 01, 2022; (4) the decision to create special economic zones for the establishment of 1st, 2nd and 3rd transformation industries of timber; (5) the regulation on the development of forest plantations; (6) the regulation designating the International Higher School of Agriculture and Wood Trades (IHSAWT) as a sub-regional university institution dedicated to vocational training in the timber sector as stipulated in the final press release of the meeting of sectoral ministers for the validation of the institutional and regulatory framework for the implementation of the strategy for the sustainable industrialization of the timber sector in the Congo Basin of September 18 2020. This legal framework of the Economic and Monetary Community of Central Africa (EMCCA) zone will necessarily boost the industrial sector of Central Africa in full mutation thanks to the reinforcement and the development of the industrial exploitation of wood for the benefit of the protection of the natural resources of the region. Also, in order to ensure optimal use of wood and to justify the interest of numerous research projects, sufficient knowledge of its properties and assembly techniques seems indispensable in a context marked by rudimentary practices [95]. Indeed, in Cameroon and the sub-region, carpenters, joiners and cabinet makers generally produce construction and interior design works and furniture from elementary components, wood pieces or wood by-products. The cutting and assembly of these components are usually done using shop equipment, either manually, using portable power tools or stationary machine tools. The joining method used differs from one work to another, depending on various technical parameters such as nature, dry or wet environment and mechanical strength, but also on aesthetic requirements and the need for investment [96]. To understand the theory of wood adhesion and its limitations, several avenues of research are explored. The theory of wood adhesion and its limitations are the subjects of several lines of research, particularly in wood welding technology, which is not an isolated case of classical gluing.
4 Exploratory Analysis and Innovative Nature of the Tropical Wood Welding Context in Cameroon
The technique of gluing solid wood by mechanical friction was not known in the Cameroonian context before our work. Indeed, most of the research on this subject has focused on temperate woods by examining more precisely the thermal degradation of wood due to temperature rise, the chemical components of the melted material, and the structure of the welded joint [73]. In contrast, very few studies have been devoted to African tropical woods. In this context, the introduction of this new joining method makes it possible to consider the elimination of the extensive use of adhesives and connectors in favor of the exclusive use of wood for joining. At the same time, the application of such a method opens new perspectives in this field and represents an important qualitative leap towards products of high environmental quality obtained in a much more productive way. The key points that justify this important breakthrough are: (1) Previously, no innovation allowed for a massive reduction in the use of adhesives and connectors in the furniture and construction sector in Cameroon. It is now possible to eliminate potentially toxic products such as formaldehyde-based compounds or vinyl and acrylics that are volatile, toxic, and currently present in products on the market. (2) The time to assemble wood parts by welding is particularly fast compared to any other gluing method that involves glue drying time. The resulting increase in productivity is an advantage that will benefit the wood material for the uses mentioned above. (3) This is the first time in Central Africa that a rapid assembly method using welded wooden dowels has been developed, with strength comparable to that of joints assembled with conventional means and without the use of glue [6,8,15,17]. In addition, this implementation is within the reach of everyone, thanks to the large DIY market. Finally, it should be noted that African tropical woods, due to their exceptional characteristics, generally present a high percentage of extractive substances in their structures, which reinforces their interest in a valorization perspective insofar as, the extracted molecules can be used as natural colorants, antiseptic substances, antioxidants, wood protection agents and active principles for medicine, perfumery, and pharmacy [84,78,97–99]. In addition, a better knowledge of the extractive substances responsible for the natural durability of these woods may allow optimal use of the welded wood.
4.1 Natural Durability of Welded Wood against Water
Eyinga Biwôlé et al. [70] used rotary friction welding to test the natural cold water durability of welded joints of three African tropical kinds of wood, namely iroko (Milicia excelsa W.), light wood of the Moraceae family with an average density of 12% of 650 kg/m3, moabi (Baillonella toxisperma P.), heavy wood of the Sapotaceae family whose average density at 12% is 850 kg/m3 and padauk (Pterocarpus soyauxii Taub), a medium-heavy wood of the Fabaceae family whose average density at 12% is 775 kg/m3. The work consisted in determining the extractives content of each wood by successive extractions. During these extractions, dichloromethane provided a higher extractive yield compared to methanol, which provided a lower yield for all species. The explanation would be the low polarity of dichloromethane which at least partially removes fatty and terpene compounds, while the high polarity of methanol solubilizes phenolic compounds [84]. The highest proportion of extractives was then obtained with padauk (7.60% dichloromethane extractives) and the lowest proportion with moabi (0.20% methanol extractives). The total extractive concentration of the three species studied ranged from 12.98% for iroko to 18.16% for padauk, while the highest total extractive contents were 17.36% for moabi and 18.16% for padauk, respectively. The determination of polyphenol contents was also the subject of phytochemical screening, at the end of which a high presence of polyphenols was found in the extractives of padauk and iroko. In contrast, moabi showed a low presence of these. Based on the results of the delamination tests for each species for 0- and 30-day immersion, it is clear that padauk wood showed better resistance to the cold-water immersion test. This finding was in agreement with that of Ganier et al. [69] and those from the study of antioxidant activities, total phenolic contents, and chemical compositions of extractives (Table 4) of four Cameroonian kinds of wood padouk (Pterocarpus soyauxii Taub), tali (Erythrophleum suaveolens), moabi (Baillonella toxisperma) and movingui (Distemonanthus benthamianus) [84]. Conversely, the low water resistance of moabi wood after 30 days of cold-water immersion was also effective despite its high extractive content. This differential behavior can be explained by its low polyphenol content which was found to be a determining factor [70,84]. At the same time, iroko wood, with a lower extractives content, showed exceptional water resistance due to the perfect entanglement of the fibers during the welding process and to the very strong inhibitory activity of oligomers of the stilbene class such as chlorophorin [C24H28O4] at 379 Da without Na+, tyrosinase [C20H32N2O] at 402 Da with Na+, and geranyl-trihydroxy-stilbene at 364 Da which remains insensitive to water. Furthermore, the revelation and slow leaching at 381 Da without Na+ of geranyl tetrahydroxy stilbene, cudraxanthose I [C23H24O6] at 380 Da, and neocyclomorusin [C25H24O7] at 377 Da in its extractives is an additional reason to justify the water stability of its soldered joints. In addition, other authors show that this durability is attributed to highly antifungal extractives and individual components acting synergistically in the heartwood, as well as to the relationship between wood properties and extractives [57,100–102]. Also, from an environmental perspective, the discovery of natural and hydrophobic constituents in these woods would elucidate their defense processes, which would be one of the best approaches to protect these woods from attack and preserve structures [103]. We can also observe a significantly different tensile strength of the welded samples between the three species studied at 0 and 30 days of cold-water immersion for a significance level α = 0.05. At the same time, the pairwise Student’s t-test reveals equality of the average strength between iroko and moabi at 0 days of immersion and between iroko and padauk at 30 days of immersion in contrast to the average of padauk and moabi at 0 and 30 days of immersion, respectively. Furthermore, from these findings, it is clear that of the 30 respective samples of each species tested, 23 moabi samples and 1 iroko sample have a delamination rate (percentage of welded joint openings) greater than 10% with zero tensile strength. In comparison, all padauk samples have a delamination rate of more than 10% with zero tensile strength. This would be evidence of the influence of structure, which is strongly correlated with the size and percentage of several wood tissues, such as vessels, axial parenchyma, fibers, and rays, which are the main pathways for water flow in these woods, as shown by Manga Begono et al. [104] on the case of sapelli (Entandrophragma cylindricum), sipo (Entandrophragma utile), and kosipo (Entandrophragma candollei). It also appears that the welding conditions could have an impact on this behavior. These results agree with the literature.
The illustrations in Fig. 9 provide a comparison of the samples affected by water during the immersion period. There is a significant attenuation of color in moabi due to cold water immersion compared to iroko and padauk woods. Furthermore, in Fig. 9d, the presence of micro-openings is much more visible in moabi samples than in iroko (Fig. 9b) and padauk (Fig. 9f). Understanding these phenomena requires analysis of the MALDI-TOF/MS spectra of the three kinds of wood previously selected for this study because of (1) their strong economic interest in the Cameroonian context, (2) their good wood quality as seen through their physicomechanical properties, (3) the availability of these woods in the forests, which guarantees their promising future in the manufacturing industry.
Figure 9: Photographs of the contact area between the welded dowel and the substrate: (a) Iroko welded joint before the immersion test, (b) Iroko welded joint after the immersion test, (c) African pearwood welded joint before the immersion test, (d) African pearwood welded joint after the immersion test, (e) Padauk welded joint before the immersion test. (f) Padauk welded joint after the immersion test. The circles around the joints refer to the welded joints of the three species before and after 30 days of immersion in cold water, respectively [70]
In the assignment of the padauk peaks, we find the structure of the molecules that can be leached, those that are partially but not fully leached, and those that are not leached at all. Another minor point to note is that the disappearance after 30 days of cold water leaching of the two relatively small peaks at 536 and 698 Da shows two possible effects on the hemicellulos’s fragments present, namely that the so-called lignin-hemicelluloses complexes can be hydrolyzed in water for the lignin-xylan and lignin-glucomannan bonds. It is possible that water hydrolysis can cleave the bonds between hemicelluloses and lignin fragments. The two peaks could well represent 2-glucuronic acid at 536 Da, and 3-Glucuronic acid at 698 Da, thus small hemicellulose fragments. The peak at 536 Da is a fragment of xylan composed of two glucose and a glucuronic acid side chain. The peak at 698 Da, which is a xylose-xylose-MeGlucuronic acid-conyferyl alcohol fragment of a lignin-xylan carbohydrate complex in which the benzyl ester bond between the methyl glucuronic acid side chain of xylan is still linked to a lignin-conyferyl alcohol unit, thus a fragment of the structure produced. Glucuronic acid is often a product of oxidative degradation of glucose, as described by Fengeland et al. [105] and Delmotte et al. [106]. This effect, although present, is minor, and, in general, cellulose, hemicelluloses, and lignin do not appear to be affected by a 30-day immersion in cold water. The major effect is the relationship with the leaching of the following single molecules identified from the MALDI-TOF/MS peaks of padauk. Also, the analysis of MALDI-TOF/MS spectra shows that stigmasterol and betulinic acid are absent from moabi extracts after 30 days of immersion in cold water. Nevertheless, squalene at 410 Da and lignans assigned to peaks 358 and 441 Da respectively are not affected by water, unlike betulinic acid at 642 Da which disappears under the influence of moisture. Finally, the peaks of the MALDI-TOF/MS spectra of iroko wood indicate that resveratrol = 3, 5, 4′-trihydroxy stilbene at 250 Da with the chemical formula [C14H12O3], a potent antioxidant of the flavonoid class acting as an important barrier against physical degradation is strongly affected upon contact with water.
4.2 Improvement of the Natural Durability of Welded Wood against Water
The low natural water-resistance of welded wood remains a major concern in wood welding technology to this day. Therefore, heat treatment is used as an effective and environmentally friendly method to increase the dimensional stability of wood by decreasing its water absorption. It is then shown that the natural water durability of welded wood is strongly correlated with its structure and chemical composition, especially because some extractives have a low affinity for water, resulting in low water absorption in the weld area. It is also worth noting the effectiveness of some environmentally friendly natural additives, such as wollastonite, sunflower oil, citric acid, and rosin, in waterproofing the welded joint upon contact with moisture, as demonstrated by Eyinga Biwôlé et al. [78] in improving the water-resistance of welded wood with padauk extracts. The tensile strengths obtained for samples treated at 0, 2, and 4 h of cold-water immersion were 2.34, 1.56 and 0.86 KN, respectively. In addition, MALDI-TOF/MS analysis in the mass/charge range of 50–1000 revealed an abundance of molecules with aromatic methoxy groups that leach slowly in cold water, such as santaline B at 596 Da and santaline A at 583 Da which has an additional-CH3 group.
According to the results of the analysis of variance, tensile strength and immersion time in cold water show a significant interaction. On the other hand, it appears that the treatment with Padauk extracts strongly contributes to the satisfactory result in terms of efficiency and yield. These results were confirmed by the statistical analysis of the interaction between the groups at the significance level of 0.05. The treatment had a significant impact on both non-immersed specimens in group 2 and immersed specimens in group 4, indicating that there are only modest statistical differences between groups and none within each of the groups studied. X-ray densitometry confirmed high weld line densification of treated specimens and peripheral densification of 762.74 kg/m3 compared to 754.60 kg/m3 of untreated specimens (Fig. 10). In addition, a logarithmic transformation of the displacement vs. tensile force equation inferred a maximum weld joint relaxation rate of 95% during the tensile test in the mm range.
Figure 10: Density profiles: (a) Untreated beech, (b) Treated beech [78]
5 Conclusion and Development Prospects
The expected impact of our work, as well as the perspectives of its development, can be described as follows: (1) the introduction in the DIY industries and markets of the Central African sub-region and Cameroon in particular of solid wood products reconstituted by rotary and linear friction requiring no synthetic glue from petrochemicals and presenting no emission of volatile organic compounds, (2) the provision of these same industries and DIY markets of a significant gain in competitiveness resulting from the saving of glues and the reduction of assembly time, (3) about enforceable government measures related to the local development of the wood industry in the Central African sub-region and Cameroon in particular, the implementation of wood welding technology is of great interest to small and medium-sized enterprises, as dowel joints can be made with already available tools. In addition, due to the low water resistance of welded wood, welded joints can be reinforced with adhesives based on natural and ecological resins. However, to have a real impact on the furniture and construction market, the physical-mechanical properties, including the color of the welded interface and the mechanical strength of the welded structural elements, need to be fully analyzed and compared to those of wood assembled by conventional means. In this regard, African tropical woods are positioned with some confidence given their exceptional characteristics. Finally, in a global context marked by strong competition of wood with other construction materials, we will opt for a strategy of application of our results. As such, all our results will be published progressively. Also, the diffusion of this innovation will be accessible to any entrepreneur and will not be limited by any pressure group. Moreover, in case of success, the necessary developments that will accompany the industrial transfer of this innovation in Cameroon will constitute a favorable framework for exchanges between researchers and industrialists.
Acknowledgement: The authors express their gratitude to The Laboratory of Study and Research on Wood Materials (LERMAB) of The University of Lorraine for the common scientific framework that made this work possible.
Funding Statement: The authors did not receive specific funding for this review.
Conflicts of Interest: The authors declare that they have no conflicts of interest to report regarding this review.
References
1. Ganne-Chédeville, C., Duchanois, G., Pizzi, A., Pichelin, F., Properzi, M. et al. (2008b). Wood welded connections: Energy release rate measurement. Journal of Adhesion Science and Technology, 22(2), 169–179. DOI 10.1163/156856108X306939. [Google Scholar] [CrossRef]
2. Dourado, N., Pereira, F. A. M., Lousada, J. L., de Moura, M. F. S. F. (2019). Experimental and numerical analyses of wood boards joining using wood-pin connectors. Construction and Building Materials, 222, 556–565. DOI 10.1016/j.conbuildmat.2019.06.179. [Google Scholar] [CrossRef]
3. Sandberg, D., Haller, P., Navi, P. (2013). Thermo-hydro and thermo-hydro-mechanical wood processing: An opportunity for future environmentally friendly wood products. Wood Material Science and Engineering, 8(1), 64–88. DOI 10.1080/17480272.2012.751935. [Google Scholar] [CrossRef]
4. Rodriguez, G., Diouf, P., Blanchet, P., Stevanovic, T. (2010). Wood-dowel bonding by high-speed rotation welding—Application to two Canadian hardwood species. Journal of Adhesion Science and Technology, 24(8–10), 1423–1436. DOI 10.1163/016942410X501025. [Google Scholar] [CrossRef]
5. Segovia, C., Zhou, X., Pizzi, A. (2013). Wood blockboards for construction fabricated by wood welding with pre-oiled dowels. Journal of Adhesion Science and Technology, 27(5–6), 577–585. DOI 10.1080/01694243.2012.690616. [Google Scholar] [CrossRef]
6. Gfeller, B., Zanetti, M., Properzi, M., Pizzi, A., Pichelin, F. et al. (2003). Wood bonding by vibrational welding. Journal of Adhesion Science and Technology, 17(11), 1573–1589. DOI 10.1163/156856103769207419. [Google Scholar] [CrossRef]
7. Belleville, B., Stevanovic, T., Cloutier, A., Pizzi, A., Salenikovich, A. (2013a). Production and properties of wood-welded panels made from two canadian hardwoods. Wood Science and Technology, 47(5), 1005–1018. DOI 10.1007/s00226-013-0554-7. [Google Scholar] [CrossRef]
8. Belleville, B., Stevanovic, T., Pizzi, A., Cloutier, A., Blanchet, P. (2013b). Determination of optimal wood-dowel welding parameters for two North American hardwood species. Journal of Adhesion Science and Technology, 27(5–6), 566–576. DOI 10.1080/01694243.2012.687596. [Google Scholar] [CrossRef]
9. Sotayo, A., Bradley, D., Bather, M., Sareh, P., Oudjene, M. et al. (2020). Review of state of the art of dowel laminated timber members and densified wood materials as sustainable engineered wood products for construction and building applications. Developments in the Built Environment, 1, 100004. DOI 10.1016/j.dibe.2019.100004. [Google Scholar] [CrossRef]
10. Sun, Y., Royer, M., Diouf, P., Stevanovic, T. (2010). Chemical changes induced by high-speed rotation welding of wood—Application to two Canadian hardwood species. Journal of Adhesion Science and Technology, 24(8–10), 1383–1400. DOI 10.1163/016942410X500990. [Google Scholar] [CrossRef]
11. Xie, Y., Huang, Y., Meng, X., Li, J., Cao, J. (2020). Friction stir spot welding of aluminum and wood with polymer intermediate layers. Construction and Building Materials, 240, 117952. DOI 10.1016/j.conbuildmat.2019.117952. [Google Scholar] [CrossRef]
12. Mansouri, H., Omrani, P., Pizzi, A. (2009). Improving the water resistance of linear vibration-welded wood joints. Journal of Adhesion Science and Technology, 23(1), 63–70. DOI 10.1163/156856108X335595. [Google Scholar] [CrossRef]
13. Suthoff, B., Schaaf, A., Hentschel, H., Franz, U. (1996). Verfahren zum reibschweiβartigen fügen von holz (Method for joining wood). Patent DE, 196(20), 273. [Google Scholar]
14. Suthoff, B., Kutzer, H. (1997). Verfahren zum reibschweibartiartigen verbinden von holz [Method for joining wood]. Offenlegungungsschrift DE, 19746(782), A1. [Google Scholar]
15. Pizzi, A., Leban, J. M., Kanazawa, F., Properzi, M., Pichelin, F. (2004). Wood dowel bonding by high-speed rotation welding. Journal of Adhesion Science and Technology, 18(11), 1263–1278. DOI 10.1163/1568561041588192. [Google Scholar] [CrossRef]
16. Leban, J. M., Pizzi, A., Wieland, S., Zanetti, M., Properzi, M. et al. (2004). X-ray microdensitometry analysis of vibration-welded wood. Journal of Adhesion Science and Technology, 18(6), 673–685. DOI 10.1163/156856104839310. [Google Scholar] [CrossRef]
17. Kanazawa, F., Pizzi, A., Properzi, M., Delmotte, L., Pichelin, F. (2005). Parameters influencing wood-dowel welding by high-speed rotation. Journal of Adhesion Science and Technology, 19(12), 1025–1038. DOI 10.1163/156856105774382444. [Google Scholar] [CrossRef]
18. Properzi, M., Leban, J. M., Pizzi, A., Wieland, S., Pichelin, F. et al. (2005). Influence of grain direction in vibrational wood welding. Holzforschung, 59, 23–27. DOI 10.1515/HF.2005.004. [Google Scholar] [CrossRef]
19. Ganne-Chédeville, C., Pizzi, A., Thomas, A., Leban, J. M., Bocquet, J. F. et al. (2005). Parameter interactions in two-block welding and the wood nail concept in wood dowel welding. Journal of Adhesion Science and Technology, 19(13–14), 1157–1174. DOI 10.1163/156856105774429037. [Google Scholar] [CrossRef]
20. Ganne-Chédeville, C., Properzi, M., Pizzi, A., Leban, J. M., Pichelin, F. (2006a). Parameters of wood welding: A study with infrared thermography. Holzforschung, 60, 434–438. DOI 10.1515/HF.2006.068. [Google Scholar] [CrossRef]
21. Ganne-Chédeville, C., Properzi, M., Pizzi, A., Leban, J. M., Pichelin, F. (2006b). Edge and face linear vibration welding of wood panels. Holz als Roh- und Werkstoff, 65(1), 83–85. DOI 10.1007/s00107-006-0125-9. [Google Scholar] [CrossRef]
22. Ganne-Chédeville, C., Duchanois, G., Pizzi, A., Leban, J. M., Pichelin, F. (2008a). Predicting the thermal behaviour of wood during linear welding using the finite element method. Journal of Adhesion Science and Technology, 22(12), 1209–1221. DOI 10.1163/156856108X323688. [Google Scholar] [CrossRef]
23. Ganne-Chédeville, C., Properzi, M., Leban, J. M., Pizzi, A., Pichelin, F. (2008c). Wood welding: Chemical and physical changes according to the welding time. Journal of Adhesion Science and Technology, 22(7), 761–773. [Google Scholar]
24. Stamm, B. (2006). Development of friction welding of wood: Physical, mechanical and chemical studies (Ph.D. Thesis). Ecole Federale Polytechnique de Lausanne, Switzerland. DOI 10.5075/epfl-thesis-3396. [Google Scholar] [CrossRef]
25. Stamm, B., Windeisen, E., Natterer, J., Wegener, G. (2006). Chemical investigations on the thermal behaviour of wood during friction welding. Wood Science and Technology, 40(7), 615–627. DOI 10.1007/s00226-006-0097-2. [Google Scholar] [CrossRef]
26. Stamm, B., Natterer, J., Navi, P. (2005a). Joining wood by friction welding. Holz als Roh- und Werkstoff, 63(5), 313–320. DOI 10.1007/s00107-005-0007-6. [Google Scholar] [CrossRef]
27. Stamm, B., Natterer, J., Navi, P. (2005b). Joining of wood layers by friction welding. Journal of Adhesion Science and Technology, 19(13–14), 1129–1139. DOI 10.1163/156856105774429046. [Google Scholar] [CrossRef]
28. Boonstra, M., Pizzi, A., Ganne-Chédeville, C., Properzi, M., Leban, J. M. et al. (2006). Vibration welding of heat-treated wood. Journal of Adhesion Science and Technology, 20(4), 359–369. DOI 10.1163/156856106776381758. [Google Scholar] [CrossRef]
29. Omrani, P., Pizzi, A., Mansouri, H., Leban, J. M., Delmotte, L. (2009c). Physico-chemical causes of the extent of water resistance of linearly welded wood joints. Journal of Adhesion Science and Technology, 23(6), 827–837. DOI 10.1163/156856108X396345. [Google Scholar] [CrossRef]
30. Omrani, P., Masson, E., Pizzi, A., Mansouri, H. (2009b). Emission gases in linear vibration welding of wood. Journal of Adhesion Science and Technology, 23(1), 85–94. DOI 10.1163/156856108X335612. [Google Scholar] [CrossRef]
31. Bocquet, J. F., Pizzi, A., Resch, L. (2006). Full-scale (industrial) wood floor using welded-through dowels. Journal of Adhesion Science and Technology, 20(15), 1727–1739. DOI 10.1163/156856106779024454. [Google Scholar] [CrossRef]
32. Bocquet, J. F., Pizzi, A., Despres, A., Mansouri, H. R., Resch, L. et al. (2007a). Wood joints and laminated wood beams assembled by mechanically-welded wood dowels. Journal of Adhesion Science and Technology, 21(3–4), 301–317. DOI 10.1163/156856107780684585. [Google Scholar] [CrossRef]
33. Bocquet, J. F., Pizzi, A., Resch, L. (2007b). Full-scale industrial wood floor assembly and structures by welded-through dowels. Holz als Roh- und Werkstoff, 65(2), 149–155. DOI 10.1007/s00107-006-0170-4. [Google Scholar] [CrossRef]
34. Belleville, B., Segovia, C., Pizzi, A., Stevanovic, T., Cloutier, A. (2011). Wood blockboards fabricated by rotational dowel welding. Journal of Adhesion Science and Technology, 25(20), 2745–2753. DOI 10.1163/016942410X537323. [Google Scholar] [CrossRef]
35. O’Loinsigh, C., Oudjene, M., Shotton, E., Pizzi, A., Fanning, P. (2012a). Mechanical behaviour and 3D stress analysis of multi-layered wooden beams made with welded-through wood dowels. Composite Structures, 94(2), 313–321. DOI 10.1016/j.compstruct.2011.08.029. [Google Scholar] [CrossRef]
36. O’Loinsigh, C., Oudjene, M., Ait-Aider, H., Fanning, P., Pizzi, A. et al. (2012b). Experimental study of timber-to-timber composite beam using welded-through wood dowels. Construction and Building Materials, 36, 245–250. DOI 10.1016/j.conbuildmat.2012.04.118. [Google Scholar] [CrossRef]
37. O’Loinsigh, C., Oudjene, M., Shotton, E., Pizzi, A., Fanning, P. (2012c). Mechanical behaviour and 3D stress analysis of multi-layered wooden beams made with welded-through wood dowels. Composite Structures, 94(2), 313–321. DOI 10.1016/j.compstruct.2011.08.029. [Google Scholar] [CrossRef]
38. Resch, L., Despres, A., Pizzi, A., Bocquet, J. F., Leban, J. M. (2006). Welding-through doweling of wood panels. Holz als Roh- und Werkstoff, 64(5), 423–425. DOI 10.1007/s00107-005-0090-8. [Google Scholar] [CrossRef]
39. Renaud, A. (2009). Minimalist Z chair assembly by rotational dowel welding. European Journal of Wood and Wood Products, 67(1), 111–112. DOI 10.1007/s00107-008-0264-2. [Google Scholar] [CrossRef]
40. Habitat Naturel (2009). Nur holz, solid panel without glue. http://www.habitatnaturel.fr/dossiers/11-Le-bois-lamellecroise--CLT/28-Nurholz-panneau-massifsans-colle/. [Google Scholar]
41. Tondi, G., Andrews, S., Pizzi, A., Leban, J. M. (2007). Comparative potential of alternative wood welding systems, ultrasonic and microfriction stir welding. Journal of Adhesion Science and Technology, 21(16), 1633–1643. DOI 10.1163/156856107782793258. [Google Scholar] [CrossRef]
42. Girardon, S. (2014). Amélioration des performances mécaniques des assemblages bois sur bois vissés par préparation des interfaces: Application à la réalisation d’éléments de structure (Ph.D. Thesis). University of Lorraine, Epinal, France. [Google Scholar]
43. Zoulalian, A., Pizzi, A. (2007). Wood-dowel rotation welding–A heat-transfer model. Journal of Adhesion Science and Technology, 21(2), 97–108. DOI 10.1163/156856107780437435. [Google Scholar] [CrossRef]
44. Pizzi, A. (2006). Recent developments in eco-efficient bio-based adhesives for wood bonding: Opportunities and issues. Journal of Adhesion Science and Technology, 20(8), 829–846. DOI 10.1163/156856106777638635. [Google Scholar] [CrossRef]
45. Omrani, P., Bocquet, J. F., Pizzi, A., Leban, J. M., Mansouri, H. (2007). Zigzag rotational dowel welding for exterior wood joints. Journal of Adhesion Science and Technology, 21(10), 923–933. DOI 10.1163/156856107781393910. [Google Scholar] [CrossRef]
46. Auchet, S., Segovia, C., Mansouri, H., Meausoone, P. J., Pizzi, A. et al. (2010). Accelerating vs constant rate of insertion in wood dowel welding. Journal of Adhesion Science and Technology, 24(7), 1319–1328. DOI 10.1163/016942409X12598231568384. [Google Scholar] [CrossRef]
47. Belleville, B., Amirou, S., Pizzi, A., Ozarska, B. (2017). Optimization of wood welding parameters for Australian hardwood species. BioResources, 12(1), 1007–1014. [Google Scholar]
48. Omrani, P., Mansouri, H., Pizzi, A., Masson, E. (2010). Influence of grain direction and pre-heating on linear wood welding. European Journal of Wood and Wood Products, 68(1), 113–114. DOI 10.1007/s00107-009-0349-6. [Google Scholar] [CrossRef]
49. Delmotte, L., Mansouri, H., Omrani, P., Pizzi, A. (2009). Influence of wood welding frequency on wood constituents chemical modifications. Journal of Adhesion Science and Technology, 23(9), 1271–1279. DOI 10.1163/156856109X433991. [Google Scholar] [CrossRef]
50. Michel, L. J., Pizzi, A., Properzi, M., Pichelin, F., Gelhaye, P. et al. (2005). Wood welding: A challenging alternative to conventional wood gluing. Scandinavian Journal of Forest Research, 20(6), 534–538. DOI 10.1080/02827580500432305. [Google Scholar] [CrossRef]
51. Stamm, B., Natterer, J., Windeisen, E., Wegener, G. (2005c). Thermal behaviour of polysaccharides in wood during friction welding. Holz als Roh- und Werkstoff, 63, 388–389. DOI 10.1007/s00107-005-0002-y. [Google Scholar] [CrossRef]
52. Omrani, P., Masson, E., Pizzi, A., Mansouri, H. R. (2008). Emission of gases and degradation volatiles from polymeric wood constituents in friction welding of wood dowels. Polymer Degradation and Stability, 93(4), 794–799. DOI 10.1016/j.polymdegradstab.2008.01.017. [Google Scholar] [CrossRef]
53. Vaziri, M., Karlsson, O., Abrahamsson, L., Lin, C. F., Sandberg, D. (2021). Wettability of welded wood-joints investigated by the wilhelmy method: Part 1. Determination of apparent contact angles, swelling, and water sorption. Holzforschung, 75(1), 65–74. DOI 10.1515/hf-2019-0308. [Google Scholar] [CrossRef]
54. Vaziri, M., Karlsson, O., Abrahamsson, L., Moghaddam, M. S., Sandberg, D. (2021). Wettability of welded wood-joints investigated by the wilhelmy method: Part 2. Effect of wollastonite additive. Holzforschung, 75(1), 79–86. DOI 10.1515/hf-2019-0310. [Google Scholar] [CrossRef]
55. Pizzi, A., Zhou, X., Navarrete, P., Segovia, C., Mansouri, H. et al. (2013). Enhancing water resistance of welded dowel wood joints by acetylated lignin. Journal of Adhesion Science and Technology, 27(3), 252–262. DOI 10.1080/01694243.2012.705512. [Google Scholar] [CrossRef]
56. Amirou, S., Pizzi, A., Delmotte, L. (2020). Investigations of mechanical properties and chemical changes occurring during welding of thermally modified ash wood. Journal of Adhesion Science and Technology, 34(1), 13–24. DOI 10.1080/01694243.2019.1659569. [Google Scholar] [CrossRef]
57. Zor, M. (2020). Water resistance of heat-treated welded iroko, ash, tulip, and ayous wood. BioResouces, 15(4), 9584–9595. DOI 10.15376/biores.15.4.9584-9595. [Google Scholar] [CrossRef]
58. Ruponen, J., Čermák, P., Rhême, M., Rautkari, L. (2015). Reducing the moisture sensitivity of linear friction welded birch (Betula pendula L.) wood through thermal modification. Journal of Adhesion Science and Technology, 29(22), 2461–2474. DOI 10.1080/01694243.2015.1069721. [Google Scholar] [CrossRef]
59. Esteves, B. M., Pereira, H. M. (2009). Wood modification by heat treatment: A review. BioResources, 4(1), 370–404. [Google Scholar]
60. Haller, P., Beyer, E., Wiedemann, G., Panzner, M., Wust, H. (2001). Experimental study of the effect of a laser beam on the morphology of wood surfaces. Proceedings of the First International Conference of the European Society for Wood Mechanics, Lausanne, Switzerland. https://www.researchgate.net/publication/237543545. [Google Scholar]
61. Sandberg, D. (1999). Weathering of radial and tangential wood surfaces of pine and spruce. Holzforschung, 53(4), 355–364. DOI 10.1515/HF.1999.059. [Google Scholar] [CrossRef]
62. Johansson, J., Sandberg, D. (2007). Preparation of wood with pulsed UV-laser ablation for characterisation of the wood structure. In: Navi, P., Guidoum, A. (Eds.Fracture mechanics and micromechanics of wood and wood composites with regard to wood machining, 3rd Symposium of Wood-Machining, pp. 191–194. Cost action E35, Lausanne, Switzerland. [Google Scholar]
63. Seltman, J. (1995a). Abtragen von holzoberflächen durch UV-bestrahlung. Holz als Roh- und Werkstoff, 53(2). [Google Scholar]
64. Seltman, J. (1995b). Freilegen der holzstruktur durch UV-bestrahlung. Holz als Roh- und Werkstoff, 53(4), 225–228. DOI 10.1007/s001070050076. [Google Scholar] [CrossRef]
65. Bianchi, S., Peña, M. I. P., Ganne-Chédeville, C., Pichelin, F., Sandberg, D. (2012). Softwood strand-boards manufacturing without adhesive using linear friction welding technology. COST Action FP0904 Workshop Current and Future Trends of Thermo-Hydro-Mechanical Modification of Wood, pp. 142–143. Nancy, France, Nancy University. [Google Scholar]
66. Mansouri, H. R., Pizzi, A., Leban, J. M., Delmotte, L., Lindgren, O. et al. (2011). Causes for the improved water resistance in pine wood linear welded joints. Journal of Adhesion Science and Technology, 25(16), 1987–1995. DOI 10.1163/016942410X544794. [Google Scholar] [CrossRef]
67. Pizzi, A., Mansouri, H. R., Leban, J. M., Delmotte, L., Pichelin, F. (2011). Enhancing the exterior performance of wood joined by linear and rotational welding. Journal of Adhesion Science and Technology, 25(19), 2717–2730. DOI 10.1163/016942411X556088. [Google Scholar] [CrossRef]
68. Vaziri, M., Lindgren, O., Pizzi, A., Mansouri, H. R. (2010). Moisture sensitivity of Scots pine joints produced by linear frictional welding. Journal of Adhesion Science and Technology, 24(8–10), 1515–1527. DOI 10.1163/016942410X501098. [Google Scholar] [CrossRef]
69. Ganier, T., Hu, J., Pizzi, A. (2013). Causes of the water resistance of welded joints of paduk wood (Pterocarpus soyauxii Taub.). Journal of Renewable Materials, 1(1), 79–82. DOI 10.7569/JRM.2012.634101. [Google Scholar] [CrossRef]
70. Eyinga Biwôlé, J. J., Biwole, A. B., Zobo Mfomo, J., Segovia, C., Pizzi, A. et al. (2022). Causes of differential behavior of extractives on the natural cold water durability of the welded joints of three tropical woods. Journal of Adhesion Science and Technology, 36(12), 1314–1331. DOI 10.1080/01694243.2021.1970318. [Google Scholar] [CrossRef]
71. Pizzi, A., Leban, J. M., Zanetti, M., Pichelin, F., Wieland, S. et al. (2005). Surface finishes by mechanically induced wood surface fusion. Holz Roh Werkst, 63(4), 251–255. DOI 10.1007/s00107-004-0569-8. [Google Scholar] [CrossRef]
72. Vaziri, M., Lindgren, O., Pizzi, A. (2011). Influence of weldling parameters on weldline density and its relation to crack formation in welded Scots pine joints. Journal of Adhesion Science and Technology, 25(15), 1819–1828. DOI 10.1163/016942410X525713. [Google Scholar] [CrossRef]
73. Gedara, A., Chianella, I., Endrino, J. L., Zhang, Q. (2021). Adhesiveless bonding of wood–A review with a focus on wood welding. BioResources, 16(3), 6448–6470. DOI 10.15376/biores.16.3.Gedara. [Google Scholar] [CrossRef]
74. Omrani, P., Mansouri, H., Duchanois, G., Pizzi, A. (2009). Fracture mechanics of linearly welded wood joints: Effect of wood species and grain orientation. Journal of Adhesion Science and Technology, 23(16), 2057–2072. DOI 10.1163/016942409X12526743387881. [Google Scholar] [CrossRef]
75. Segovia, C., Pizzi, A. (2009a). Performance of dowel-welded wood furniture linear joints. Journal of Adhesion Science and Technology, 23(9), 1293–1301. DOI 10.1163/156856109X434017. [Google Scholar] [CrossRef]
76. Segovia, C., Pizzi, A. (2009b). Performance of dowel-welded T-joints for wood furniture. Journal of Adhesion Acience and Technology, 23(16), 2073–2084. [Google Scholar]
77. Segovia, C., Renaud, A., Pizzi, A. (2011). Performance of dowel-welded L-joints for wood furniture. Journal of Adhesion Science and Technology, 25(15), 1829–1837. DOI 10.1163/016942410X525722. [Google Scholar] [CrossRef]
78. Eyinga Biwôlé, J. J., Pizzi, A., Zobo Mfomo, J., Segovia, C., Atangana, A. et al. (2022a). Padauk (Pterocarpus soyauxii Taub.) extracts: An ecological solution for improving the natural water durability of welded wood. Industrial Crops and Products, 180, 114711. DOI 10.1016/j.indcrop.2022.114711. [Google Scholar] [CrossRef]
79. Wieland, S., Shi, B., Pizzi, A., Properzi, M., Stampanoni, M. et al. (2005). Vibration welding of wood: X-ray tomography, additives, radical concentration. Forest Products Journal, 55(1), 84–87. [Google Scholar]
80. Umemura, K., Ueda, T., Munawar, S. S., Kawai, S. (2012). Application of citric acid as natural adhesive for wood. Journal of Applied Polymer Science, 123(4), 1991–1996. DOI 10.1002/app.34708. [Google Scholar] [CrossRef]
81. Del Menezzi, C., Amirou, S., Pizzi, A., Xi, X., Delmotte, L. (2018). Reactions with wood carbohydrates and lignin of citric acid as a bond promoter of wood veneer panels. Polymers, 10, 833. DOI 10.3390/polym10080833. [Google Scholar] [CrossRef]
82. Amirou, S., Pizzi, A., Delmotte, L. (2017). Citric acid as waterproofing additive in butt joints linear wood welding. European Journal of Wood and Wood Products, 75(4), 651–654. [Google Scholar]
83. Mfomo, J. Z., Biwolé, A. B., Fongzossie, E. F., Ekassi, G. T., Hubert, D. et al. (2020). Carbonization techniques and wood species influence quality attributes of charcoals produced from industrial sawmill residues in Eastern Cameroon. Bois & Forets des Tropiques, 345, 65–74. [Google Scholar]
84. Saha, J. B. T., Abia, D., Dumarçay, S., Ndikontar, M. K., Gérardin, P. et al. (2013). Antioxidant activities, total phenolic contents and chemical compositions of extracts from four Cameroonian woods: Padouk (Pterocarpus soyauxii Taubbtali (Erythrophleum suaveolensmoabi (Baillonella toxispermaand movingui (Distemonanthus benthamianus). Industrial Crops and Products, 41, 71–77. DOI 10.1016/j.indcrop.2012.04.012. [Google Scholar] [CrossRef]
85. Atyi, E., Lescuyer, G., Ngouhouo, P. J. (2013). Étude de l’importance économique et sociale du secteur forestier et faunique au Cameroun: Rapport final. https://agritrop.cirad.fr/573085/. [Google Scholar]
86. Georges, B. J., Evariste, F., Achille, B., Joseph, Z. M., Moise, N. A. et al. (2022). Synergistic effect of jatropha curcas seed oil and sodium tetraborate treatment on wood resistance to fungal attacks: Case of ayous (Triplochiton scleroxylona high value commercial wood species in tropical Africa. Wood Material Science & Engineering, 17(3), 186–191. [Google Scholar]
87. Mounguengui, S., Saha Tchinda, J. B., Ndikontar, M. K., Dumarçay, S., Attéké, C. et al. (2016). Total phenolic and lignin contents, phytochemical screening, antioxidant and fungal inhibition properties of the heartwood extractives of ten Congo basin tree species. Annals of Forest Science, 73(2), 287–296. [Google Scholar]
88. Cerutti, P. O., Tacconi, L. (2008). Forests, illegality, and livelihoods: The case of Cameroon. Society and Natural Resources, 21(9), 845–853. [Google Scholar]
89. Cerutti, P. O., Lescuyer, G. (2011). The domestic market for small-scale chainsaw milling in Cameroon: Present situation, opportunities and challenges. CIFOR Occasional Paper No. 61, pp. 38. Bogor, Indonesia, Center for International Forestry Research (CIFOR). [Google Scholar]
90. Lescuyer, G., Cerutti, P. O., Tsanga, R. (2016). Contributions of community and individual small-scale logging to sustainable timber management in Cameroon. International Forestry Review, 18(1), 40–51. DOI 10.1505/146554816819683744. [Google Scholar] [CrossRef]
91. Lescuyer, G., Tal, M. (2016). Intra-African trade of timber: The Cameroon-Chad case in 2015. IITO, CIFOR. DOI 10.13140/RG.2.1.2940.5845. [Google Scholar] [CrossRef]
92. Lescuyer, G., Atyi, R. E., Cerutti, P. (2009). Consommations nationales de bois d’œuvre en afrique centrale : Un enjeu majeur pour la gestion forestière durable. The World Forestry Congress XIII, Buenos Aires, Argentina. [Google Scholar]
93. Assembe-Mvondo, S. (2009). Sustainable forest management practice in Central African states and customary law. International Journal of Sustainable Development & World Ecology, 16(4), 217–227. DOI 10.1080/13504500903031709. [Google Scholar] [CrossRef]
94. Hiolhiol, F., Assembe-Mvondo, S. (2020). Etat des lieux des acteurs du secteur privé de la filière forêt-bois au cameroun. Mentions Légales. GFBC-Groupement de la Filière Bois au Cameroun. [Google Scholar]
95. Groutel, E. (2019). Pour un positionnement forestier responsable dans le bassin du Congo-premisses d’une politique environnementale commune ? NIMEC (UPRES-EA 969) IAE, Caen, France. DOI 10.13140/RG.2.2.30502.37448. [Google Scholar] [CrossRef]
96. Aguilera, L. A. A. (2000). Optimisation des conditions de coupe pour l’usinage du bois : Application de la méthode Couple Outil Matière au défonçage des panneaux de fibres de densité moyenne. CRAN-Centre de Recherche en Automatique de Nancy. [Google Scholar]
97. Tchinda, J. B. S., Pétrissans, A., Molina, S., Ndikontar, M. K., Mounguengui, S. et al. (2014). Study of the feasibility of a natural dye on cellulosic textile supports by red padouk (Pterocarpus soyauxii) and yellow movingui (Distemonanthus benthamianus) extracts. Industrial Crops and Products, 60, 291–297. DOI 10.1016/j.indcrop.2014.06.029. [Google Scholar] [CrossRef]
98. Oke-Altuntas, F., Kapche, G. D. W. F., Nantchouang Ouete, J. L., Demirtas, I., Koc, M. B. et al. (2016). Bioactivity evaluation of cudraxanthone I, neocyclomorusin and (9βh)-3β-acetoxylanosta-7, 24-diene isolated from Milicia excelsa Welw. C. C. Berg (Moraceae). Medicinal Chemistry Research, 25(10), 2250–2257. DOI 10.1007/s00044-016-1670-3. [Google Scholar] [CrossRef]
99. Tchamadeu, M., Dzeufiet, P., Nana, P., Nouga, C. K., Tsofack, F. N. et al. (2011). Acute and sub-chronic oral toxicity studies of an aqueous stem bark extract of Pterocarpus soyauxii Taub (Papilionaceae) in rodents. Journal of Ethnopharmacology, 133(2), 329–335. DOI 10.1016/j.jep.2010.09.035. [Google Scholar] [CrossRef]
100. Hart, J. (1989). The role of wood exudates and extractives in protecting wood from decay. In: Natural products of woody plants, pp. 861–880. Springer Series in Wood Science. DOI 10.1007/978-3-642-74075-6. [Google Scholar] [CrossRef]
101. Schultz, T., Harms, W., Fisher, T., McMurtrey, K., Minn, J. et al. (1995). Durability of angiosperm heartwood: The importance of extractives. Berlin, Germany: Walter de Gruyter. [Google Scholar]
102. Eyinga Biwôlé, J. J., Zobo Mfomo, J., Pizzi, A., Segovia, S., Abessolo, D. et al. (2022b). Iroko wood (M. excelsa Welw. C. C. Berga good candidate for highspeed rotation-induced wood dowel welding: An assessment of its welding potential and the water resistance of the welded joints. International Journal of Adhesion and Adhesives (in Press). [Google Scholar]
103. Amusant, N., Moretti, C., Richard, B., Prost, E., Nuzillard, J. M. et al. (2007). Chemical compounds from Eperua falcata and Eperua grandiflora heartwood and their biological activities against wood destroying fungus (Coriolus versicolor). Holz als Roh- und Werkstoff, 65(1), 23–28. DOI 10.1007/s00107-006-0120-1. [Google Scholar] [CrossRef]
104. Manga Bengono, D. M., Jean Gaston, T., Joseph, Z. M., Evariste, F. F., Armand, F. L. et al. (2022). Sorption behaviour of three african tropical woods (Sapelli, sipo, kosipo) with similar anatomical structures from Cameroon. International Wood Products Journal, 13(3), 194–202. DOI 10.1080/20426445.2022.2073075. [Google Scholar] [CrossRef]
105. Fengel, D., Wegener, G. (1989). Wood chemistry, ultrastructure, reactions. Berlin, Germany: Walter de Gruyter. [Google Scholar]
106. Delmotte, L., Ganne-Chedeville, C., Leban, J. M., Pizzi, A., Pichelin, F. (2008). CP-MAS, 13C NMR and FTIR investigation of the degradation reactions of polymer constituents in wood welding. Polymer Degradation and Stability, 93, 406–412. DOI 10.1016/j.polymdegradstab.2007.11.020. [Google Scholar] [CrossRef]
Cite This Article
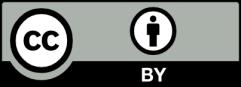
This work is licensed under a Creative Commons Attribution 4.0 International License , which permits unrestricted use, distribution, and reproduction in any medium, provided the original work is properly cited.