Open Access
ARTICLE
Development of a Novel Extrusion Process for Preparing Rice Straw/LLDPE Composites
Key Laboratory of Bio-Based Material Science and Technology (Ministry of Education), Material Science and Engineering College, Northeast Forestry University, Harbin, 150040, China
* Corresponding Author: Weihong Wang. Email:
(This article belongs to the Special Issue: Bio-based/Degradable Materials towards A Sustainable Future)
Journal of Renewable Materials 2023, 11(3), 1123-1135. https://doi.org/10.32604/jrm.2022.023959
Received 19 May 2022; Accepted 25 May 2022; Issue published 31 October 2022
Abstract
Straw utilization is a key issue related to agricultural production and air pollution control. In this study, a novel extrusion process was proposed to improve the physical and mechanical properties of the straw-reinforced linear low-density polyethylene (LLDPE) composite. Instead of crushing the straw and mixing it with plastic matrix, the new method mixes straw with plastic matrix in its original form. The intact long rice straws were parallelly spread on the LLDPE film and then rolled up together into a prefabricated roll. The rolls experienced three extrusion processes as follows: (1) twin-screw melting, cooling and crushing, single-screw extruding; (2) twin-screw melting and single-screw extruding; (3) directly single-screw extruding. The testing results showed that the straw/LLDPE composite (with a ratio of 6:4) prepared by Method (2) exhibited optimized properties. Characterization by scanning electron microscopy indicated that the damage to rice straw fibers was relatively minor, the orientation of long fibers was good, and the binding of fibers with the LLDPE matrix was excellent in this case. The results of dynamic mechanical testing (DMA), differential scanning calorimetry (DSC) and thermogravimetric (TG) analysis demonstrated that composites prepared by the new process exhibited significantly improved thermal stability and energy storage modulus, compared with those prepared by conventional processes (e.g., extruded straw particles/LLDPE composite). The new proposed method yielded significantly enhanced mechanical properties while reducing dust pollution.Keywords
As a large agricultural country, China is characterized by extremely abundant crop straw resources. Traditionally, straw is used as domestic fuel, organic fertilizer, or livestock forage [1]. Owing to the huge population migration from rural to urban areas over the past decades, the consumption of straw has experienced fundamental changes. This results in large quantities of straw being discarded in the fields. Meanwhile, crop straw utilization is limited by high recycling costs and a low level of industrialization development. As a result, illegal straw burning has been observed despite repeated banning, causing severe environmental pollution and waste of biomass resources [2,3]. Additionally, linear low-density polyethylene (LLDPE) has been widely applied in agriculture [4]. It is a hemicrystalline thermoplastic plastic with high weather resistance, good tear resistance, and excellent toughness. However, LLDPE has a short service life (3–4 months) and generates significant waste, causing serious harm to the environment and soil [5].
Composites prepared using wood fibers and plastic matrix are characterized by good performance [6–8] and have been widely applied in building materials, packaging, landscaping, and automobiles [9–12]. Thus, preparation of composites with good performances [13–16] by adding straw fibers into a thermoplastic polymer matrix might be a keyway of increasing crop straw utilization. Wang et al. [17] used wheat straw particles and HDPE as raw materials to prepare straw fiber/HDPE composites by hot pressing; Chen et al. [18] prepared a composite material by extrusion molding using the production of plastic benzylated wheat straw (BWS) and wheat straw particle as raw materials; Chai et al. [19] prepared a wheat straw/PLA composite with wheat straw particle, and polylactic acid as raw materials; Zabihzadeh et al. [20] prepared a composite with crushed rice straw and low-density polyethylene as raw materials. These composites presented better mechanical properties than their matrices. In most cases (both in lab experiments and practical application) of straw/plastic composite preparation, straw is crushed into fine particles and then blended with plastic pellets, followed by extrusion molding. This process is limited by severe damage to the straw and dust pollution. Additionally, the reinforcing role of long fibers is not exploited. In order to homogeneously mix long fibers and plastic matrix and fluently feed them into extenders, previous studies in our group developed a new extrusion process for preparing a composite consisting of long bamboo fiber bundles and plastic matrix and fluently feeding them into extenders. Specifically, long bamboo bundles were rolled up with PP film and sent into a single-screw extruder. Compared with conventional extruded bamboo powder/PP composites, the composites prepared by the proposed method contained bamboo fibers with large lengths and exhibited significantly enhanced mechanical properties [21]. After that, long rice straw/LLDPE composites were prepared in a similar way [22] and the optimized extruding temperature was determined. Nevertheless, the process and compounding mechanism have not been thoroughly investigated.
In the present article, this study is continued. The long rice straw/plastic film rolls experienced different processes before hardening into their final form. First, long rice straws were rolled using LLDPE thin films to obtain pre-fabricated rolls, which were then processed by three methods to develop straw/LLDPE composites: (1) twin-screw melting, cooling, and crushing; (2) twin-screw melting and single-screw extruding; (3) directly single-screw extruding. The performances of the composites were evaluated, and the principle of performance improvement was analyzed. An optimized extrusion process for preparing high-performance straw/LLDPE composites has been developed. This study would greatly contribute to the effective utilization of straw resources and facilitate the utilization of abandoned agricultural films.
Rice straws (length = 70∼90 cm, bulk density = 0.035 g/cm3) were purchased from Yanshou County, Harbin, China. LLDPE films (thickness = 0.01 mm, density = 0.923 g/cm3) were purchased from Shanghai Runwen Packaging Material Co., Ltd. (Shanghai, China). Maleic anhydride-grafted polyethylene (MAPE, grafting ratio = 0.9%, density = 0.92 g/cm3) powder was purchased from Nantong Rizhisheng Fine Chemical Co., Ltd. (Nantong, China).
2.2 Preparation of Rice Straw/LLDPE Composite
After drying (moisture content < 3%), rice straws were laid in parallel on LLDPE film. Then, MAPE powder was homogeneously dispersed on the rice straws. LLDPE film and straws were rolled up together into pre-fabricated rolls. Finally, the rice straw/LLDPE composites were prepared using pre-fabricated rolls by three different processes.
(1) The rolls were fed into the twin-screw extruder. They were brought into the extruder tube by the rotation of a twin-screw to generate a molten composite mixture. Once being cooled to room temperature, the mixture was crushed into granules, which were then sent to the single-screw extruder to prepare the rice straw/LLDPE composite (named as Process 1, compounding-crushing-single screw extrusion composite).
(2) The rolls were fed into the twin-screw extruder and generated a molten composite mixture. Without crushing into granules, the cooled mixture was sent to the single-screw extruder to prepare a rice straw/LLDPE composite (named as Process 2, compounding-single screw extrusion composite).
(3) The rolls were directly fed into the single-screw extruder. The composite was extruded into a rice straw/LLDPE composite (named as single Process 3, single screw extrusion composite).
The control rice straw/LLDPE composite was prepared by conventional extrusion method. First, dried rice straw particle (20–40 mesh), LLDPE pellets, and MAPE powder were mixed in a high-speed mixer, followed by a process similar to method (1). After compounded with the twin-screw extruder, the mixture was cooled and granulated. The granules were sent to the single-screw extruder to prepare rice straw particle/LLDPE composite (named as Control Process, straw particle composite).
The four composites had identical formulations: the mass proportion of rice straw, LLDPE film, and MAPE powder was 60%, 37%, and 3%, respectively. The cross-section size of the extruded lumber was 40 mm (W) × 4 mm (T). The processing temperatures of the single/twin-screw extruder were set at 135°C, 140°C, 140°C, 135°C, respectively, at each stage.
2.3 Performance Testing and Characterization
2.3.1 Size of Rice Straw Fibers in the Composite
Composite samples were immersed in a container containing xylene and heated in an oil bath at 130°C for 3 h. Then, the extracted fibers were dispersed in a 0.1% ethanol solution, followed by filtration and drying. The fibers were characterized by a polarizing microscope and the length of each fiber was measured by Image J. Each group gave 200 fibers for statistics of size distribution.
Dumbbell tensile specimens (length = 165 mm, width = 13 mm, thickness = 4 mm) were prepared and tested for tensile performance according to GB/T 1040.2-2006 Plastic Tensile Performance Measurement. The gauge distance was 50 mm and the loading rate was 5 mm/min. Each group consisted of six specimens.
The bending performance of the composite samples was measured by the three-point bending method according to GB/T 1449-2005 Fiber-Reinforced Plastic Bending Performance Testing. The bending test speed was 2 mm/min, the span was 64 mm, and the specimen size was L 80 mm × W 13 mm × T 4 mm. Each group consisted of six specimens.
The impact ductility of the composite samples was measured according to GB/T 1451-2005 Simply Supported Beam Test Method for Impact Ductility of Fiber-Reinforced Plastics. The size of a notchless specimen was L 80 mm × W 13 mm × T 4 mm. The impact energy was 2 J and the pendulum speed was 2.9 m/s. Each group consisted of six specimens.
The rice straw/LLDPE composite was characterized by scanning electron microscopy (SEM). The specimens were broken in a brittle way after being frozen with liquid nitrogen, and the section was sprayed with gold. The accelerating voltage was set at 12.5 kV.
2.3.6 Dynamic Mechanical Test (DMA)
The mechanical properties of composites as a function of temperature were investigated by DMA. The testing temperature was in the range of −35°C–120°C, the heating rate was 3 °C/min, and the size of the sample was 35 mm long, 14 mm wide, and 4 mm thick. and the testing frequency was 1 Hz. Samples were loaded in tension under an N2 environment during the entire process.
2.3.7 Differential Scanning Calorimetry (DSC)
The composites were investigated by DSC. The samples were cooled from room temperature to −80°C and then heated to 200°C at a rate of 10 °C/min. The correlation of enthalpy changes of samples induced by changes in physical and chemical properties with temperature was determined. The samples were tested in an N2 environment during the entire process.
The samples were heated from room temperature to 600°C at a rate of 10 °C/min. The mass variation during this process was measured by a TG analyzer. The entire testing process was performed under a nitrogen atmosphere.
3.1 Morphology of Fibers in the Rice Straw/LLDPE Composites
Fig. 1a shows the size distributions of the fibers retained in the composites prepared by Process 1. The straw experienced twin-screw extrusion, crushing into particles and single-screw extrusion. Compared with the other two long-fiber composites, the proposed composite exhibited maximum reduction of rice straw size. Fibers with lengths of 40–60 μm dominated, followed by those with lengths of 20–40 and 60–80 μm; each ratio of these fibers exceeded 20%. As shown in Fig. 1a, this extrusion process caused severe damage to the original straw as most were teared into particles with short length to diameter ratio.
Figure 1: Fiber length distribution and morphology of fibers in rice straw/LLDPE composites prepared by Process 1 (a), Fiber length distribution and morphology of fibers in rice straw/LLDPE composites prepared by Process 2 (b), Fiber length distribution and morphology of fibers in rice straw/LLDPE composites prepared by Process 3 (c)
Fig. 1b shows that more than 45% of fibers have lengths of 50–100 μm, and more than 25% of fibers have lengths of 100–150 μm in the composite prepared by Process 2. As is known, the length reduction of rice straw fibers decreased if no crushing step was involved after twin-screw extrusion. This extrusion process caused relatively minor damage to rice straw fibers, and most fibers maintained a slender shape; large-sized fibers can also be seen from the perspective of composite appearance (Fig. 2c). Hence, the absence of crushing helps to maintain fiber size.
Figure 2: Rice straw/LLDPE composites prepared by four different extrusion molding processes: (a) Control Process; (b) Process 1; (c) Process 2; (d) Process 3
Composites prepared by only single-screw extrusion (Process 3) exhibited significantly larger sized fibers and some rice straw segments maintained their original morphology (Fig. 2d). Fibers with sizes of 100–150 μm dominated, followed by those with sizes of 150–250 μm; each category accounted for more than 20% (Fig. 1c). As observed, this extrusion process caused minimum damage to rice straw and most of them maintained relatively large aspect ratios and widths (Fig. 1c).
As observed, both twin-screw extrusion and granulation caused damage to the morphology of rice straw. Direct extrusion of pre-fabricated roll can maintain the morphology and size of straw to the greatest extent, thus theoretically exhibiting maximum reinforcement. However, the physical and mechanical properties of the composites are also affected by the plasticization of the LLDPE matrix and its combination quality with rice straw.
3.2 Mechanical Properties of Rice Straw/LLDPE Composite
Fig. 3 illustrates the effects of the extrusion process on the tensile performance, bending performance, and impact strength of the rice straw/LLDPE composite. Composites prepared by Process 2 exhibited optimized tensile strength (8.60 MPa) and bending strength (18.24 MPa). As mentioned earlier, Process 2 retained larger fibers with a higher aspect ratio in such composites compared to those composites prepared by Process 1 due to no crushing involved. Observed from the microstructure (Fig. 4c), it is found the fibers are closely bonded with LLDPE and well oriented in the composites, indicating a strong reinforcement.
Figure 3: Mechanical properties of rice straw/LLDPE composites prepared by extrusion molding: (a) tensile performance; (b) bending performance; (c) impact strength
Figure 4: Micro-morphologies of rice straw/LLDPE composites prepared by: (a) Control process, rice straw particle/LLDPE composite; (b) Process 1, twin screw compunding-crushing-single screw extrusion; (c) Process 2, twin screw compunding-single screw extrusion; (d) Process 3, single screw extrusion
In conventional extrusion processes, straw was in powder form and its fiber length was below the critical length. Hence, fibers serve as fillers instead of reinforcement in the composites [18–21]. Therefore, the rice straw powder/LLDPE composite exhibited relatively poor mechanical properties. Compared with the composites prepared by the other three processes, the composites prepared by single-screw extrusion (Process 3) exhibited the minimum tensile strength despite its maximum fiber length (Fig. 1c). This may be attributed to the short stay of the pre-fabricated roll inside the extruder, which leads to incomplete melting mixing with and wetting of straw fibers. As a result, rice straw fibers were heterogeneously distributed in the LLDPE matrix, resulting in degraded tensile performances. Same in the tensile case, Process 2 shows the greatest bending property (Fig. 3). The difference is that Process 3 shows greater bending property than Process 1 which is the control process. The larger size played the main role. Process 3 prepared the lumber with more long straw arranged parallel to the length direction (Fig. 2d). In bending property test, the stress direction was perpendicular to the length direction of the lumber. The long straw enhanced the flexural performance better than in tensile test. Thus, Process 3 shows bending resistance second only to Process 2.
The impact strength of composites improved significantly as the fiber length increased. This can be attributed to the larger contact area of long-fiber with LLDPE, extending its sliding paths in the matrix. Under impact stresses, long failure paths lead to increased energy consumption by fiber pulling out/fracturing, thus enhancing impact resistance. For Process 3, the weak binding interface and the void structure retained in the straw are conducive to the absorption of impact energy, so the impact strength of Process 3 is the largest.
3.3 Micro-Morphology of the Composites
The rice straw/LLDPE composite was characterized by SEM. As observed in Fig. 4a, straw particles were randomly distributed in the matrix and strongly bonded with the matrix in the straw particle/LLDPE composite. In the composite prepared by Process 1, several holes were left after breaking (Fig. 4b), suggesting that straw fibers were pulled out rather than broken and that reinforcement by fibers was not maximized. Fig. 4c shows a SEM image of the composite prepared by Process 2. As observed, rice straw fibers were homogeneously distributed and strongly bonded with the LLDPE matrix; fibers were fractured and most of them were well oriented. Additionally, such composites exhibited relatively large fiber sizes, suggesting that the absence of crushing leads to reduced damage to rice straw fibers. Well-oriented long fibers exhibited significant reinforcement in the composite, which is consistent with the trend of measured static mechanical properties (Fig. 3).
For Process 3 (Fig. 4d), despite the fact that straw fibers with relatively large sizes were retained, direct extrusion of the pre-fabricated roll leads to heterogeneous distribution and agglomeration of fibers in the matrix. Meanwhile, pores left in the matrix after fiber pulling out were observed, indicating poor interface binding between fibers and the LLDPE matrix. Nevertheless, long fibers interact with each other and the entangled structure extends pulling and sliding paths, resulting in the highest impact resistance of the straw/LLDPE composites.
3.4 Dynamic Mechanical Properties of Rice Straw/LLDPE Composites
According to Fig. 5, storage modulus (E′) of all composites decreased as the temperature increased. Among them, composites prepared by Process 3 exhibited minimum E′. This indicated the fact that single-screw extrusion alone leads to a degraded interfacial bonding strength between rice straw and the LLDPE matrix induced by incomplete melting mixing and fiber agglomeration [23]. Compared with the composites prepared by the other three processes, composite prepared by Process 2 exhibited maximum E′ under both low and high temperatures. This is consistent with the trend of measured tensile strength (Fig. 3a), demonstrating that the proposed process leads to optimized binding of straw fibers with LLDPE and the relatively long fibers serve as reinforcement in the composite (Fig. 1b). Loads applied to the straw/LLDPE composites can be effectively transferred to rice straw fibers via the strong interface so that the fibers effectively share the loads, which are reflected as large rigidity and increased energy storage modulus of the composite [24–26].
Figure 5: DMA curves of rice straw/LLDPE composites: (a) energy storage modulus; (b) loss factor
The loss factor (tanδ) of the composite is defined as the ratio of loss modulus and energy storage modulus. Among composites prepared using pre-fabricated roll, the composite prepared by Process 2 exhibited a minimum loss factor, indicating reduced inelastic deformation and increased rigidity (Fig. 5b); the composite prepared by Process 3 exhibited a maximum loss factor, indicating increased viscous deformation and good flexibility (Fig. 5c). Compared with long-fiber composites, rice straw particle/LLDPE composites exhibited maximum loss modulus and significant viscosity. Both of its E′ and tanδ shows increase in variation around 40°C, implying the small particles could not remain their reinforcement as good as other long straw fibers.
3.5 DSC of Rice Straw/LLDPE Composite
It can be found from Fig. 6 that LLDPE makes a small shift around 30°C and continues slowly until a large melting peak appears. Thus, at temperatures below 30°C, rice straw particle/LLDPE composites exhibited high E′, but quickly decreased while the temperature gone up. This decrease can be attributed to its small size of straw particles which has less inhibition on matrix deformation. As a result, the LLDPE characteristics were enhanced as the temperature increased.
Figure 6: DSC curves of rice straw/LLDPE composites prepared by extrusion molding
According to DSC curves (Fig. 6), melting peaks are present at 120.47°C, 122.55°C, 121.73°C, and 118.99°C in the spectra of composites prepared by the control process, Process 1, Process 2, and Process 3, respectively. These temperatures are close to the melting temperature of LLDPE (122.9°C), suggesting that the endothermic peaks of the composites in this region can be attributed to the melting of LLDPE [22].
Compared with composites prepared by other processes, composites prepared by Process 2 (Fig. 2c) exhibited broader and higher melting peaks and maximum enthalpy of melting. This can be attributed to the increased contact area of fiber and LLDPE caused by the relatively large size of rice straw fibers (Fig. 1b). There are micropores among fibers and between the fibers and the matrix (Fig. 4c), which affects heat transfer. In addition, fibers of Process 2 are homogeneously distributed in the composites and strongly bond with the LLDPE matrix, resulting in a strong inhibition. Hence, heat consumption during melting of the proposed composite increases, resulting in increased thermal resistance [27]. Followed by the composites prepared with Process 3 (Fig. 2d), it also exhibited relatively high melting enthalpy. This can be attributed to the presence of the largest fiber sizes, which remained in straw cavities and cell pores in the composites (Fig. 1c). These characteristics make the composite absorb and store more heat, impeding the melting of the LLDPE matrix. For conventional rice straw particle/LLDPE composite, it exhibited the lowest melting enthalpy (Table 1), which can be attributed to the crushing of long fibers into 40-mesh powder. As a result, fiber cavities and cell pores were damaged, and the powder could barely withstand the thermal stress. For this reason, the composite exhibited poor thermal stability.
Fig. 7 shows the DTG and TGA curves of LLDPE, rice straw particle, and long rice straw composites prepared by extrusion molding, respectively. As observed, LLDPE exhibits one degradation zone, while the rice straw/LLDPE composite exhibits three degradation zones. The first degradation zone of rice straw powder is below 100°C and it is dominated by the volatilization of water and other small molecules in straw fibers. The second degradation zone of rice straw particles is in the range of 280°C∼350°C and it is dominated by severe degradation. For the composites prepared by pre-fabricated roll, degradation at temperatures below 100°C is not significant, while the mass loss at 230°C∼380°C is significant. This can be attributed to the degradation of cellulose and hemicellulose that existed in rice straw fibers [28–30]. The third degradation zone is 380°C∼600°C and it is dominated by the degradation of LLDPE components.
Figure 7: (a) TGA curves of rice straw/LLDPE composite prepared by extrusion molding; (b) DTG curves of rice straw/LLDPE composite prepared by extrusion molding
The pyrolysis temperature of composites is significantly higher than that of rice straw, which can be attributed to the coating structure of LLDPE on rice straw. In addition, after experienced the thermal processing, part the small molecules in the rice straw have been pyrolyzed and volatilized. Compared with the unheated straw, the straw contained in the composite has better pyrolysis resistance. Compared with Process 1, involving crushing, Process 2 presented maximum initial decomposition and maximum thermal degradation temperatures (465.03°C). This can be attributed to the excellent interfacial binding and long rice straw fibers that remained (Fig. 1b), which led to increased contact area of fiber and matrix and the development of a compacted yet stabilized carbon layer on the LLDPE matrix. In this case, melting of the composites requires more thermal energy, resulting in inhibited pyrolysis. However, composites prepared by Process 3 still exhibited significantly high thermal stability at 0°C∼430°C. This can be attributed to the large rice straw fibers in the composites (Fig. 1c), which hinder heat flow or recombination of polymers in the matrix; complete cell pores and straw cavities favor energy storage. Therefore, this kind of composite exhibited high thermal stability.
In this study, rice straw/LLDPE composites were developed by extrusion molding with long rice straw as the reinforcement and LLDPE as the matrix. The rice straws were first rolled up with LLDPE film and then experimented with different extrusion processes. The mechanism of the extrusion molding process and its effects on composite performance were discussed. The following conclusions can be drawn:
(1) Extrusion molding of long-fibers was achieved by an extrusion molding process with a pre-fabricated roll as the raw material. Characterization by SEM revealed that twin-screw melt compounding-single-screw extrusion molding caused relatively minor damage to rice straw fibers and the long fibers with good orientation in the composite played a better reinforcing role. Indeed, composites prepared by the proposed process exhibited maximum tensile strength (8.60 MPa) and bending strength (18.24 MPa).
(2) Owing to twin-screw melt compounding-crushing–single screw extrusion process, straw were crushed into fine fibers, indicating severe damages. Hence, the absence of crushing helps to maintain the morphology and size of fibers.
(3) Direct single-screw extrusion of pre-fabricated roll caused minimal damage to rice straw and some straws even maintained their original morphology. This, however, did not result in the best mechanical performance.
(4) DMA curves indicated that composites prepared by twin-screw compounding and single-screw extrusion exhibited the highest energy storage modulus under both low and high temperatures, as well as a minimum loss factor, indicating reduced viscous deformation and increased rigidity. Composites prepared by single-screw extrusion of pre-fabricated rolls exhibited maximum loss factor, showing increased viscous deformation and good flexibility.
(5) DSC and TG curves revealed that processing methods involving no crushing can generate rice straw/LLDPE composites with high thermal stability. Additionally, a strong binding of long fibers with matrix is essential for excellent mechanical properties and thermal stability of rice straw/LLDPE composites.
Funding Statement: This research was supported by the Natural Science Foundation of China (No. 32071704).
Conflicts of Interest: The authors declare that they have no conflicts of interest to report regarding the present study.
References
1. Xu, Z., Tang, Y., Wang, Q., Hao, H. (2021). Emergy based optimization of regional straw comprehensive utilization scheme. Journal of Cleaner Production, 297, 126638. DOI 10.1016/j.jclepro.2021.126638. [Google Scholar] [CrossRef]
2. Xin, W., Wei, C., Bin, C., Cheng, Y., Gang, T. et al. (2020). Does the prohibition on open burning of straw mitigate air pollution? An empirical study in Jilin Province of China in the post-harvest season. Journal of Environmental Management, 264,110451. [Google Scholar]
3. Guan, Y. N., Chen, G. Y., Cheng, Z. J., Yan, B. B., Hou, L. (2017). Air pollutant emissions from straw open burning: A case study in Tianjin. Atmospheric Environment, 171, 155–164. DOI 10.1016/j.atmosenv.2017.10.020. [Google Scholar] [CrossRef]
4. Rajen, M. P., Teresa, P. K., Nilesh, R. S., Salibi, L. L. (2019). Fundamentals of structure–property relationships in blown films of linear low density polyethylene/low density polyethylene blends. Journal of Plastic Film & Sheeting, 35(4), 401–421. [Google Scholar]
5. Aleksander, H., Mateusz, B., Jacek, A., Paulina, K., Adam, P. et al. (2020). Rotational molding of linear Low-density polyethylene composites filled with wheat bran. Polymers, 12(5), 1004. DOI 10.3390/polym12051004. [Google Scholar] [CrossRef]
6. Agnantopoulou, E., Tserki, V., Marras, S., Philippou, J., Panayiotou, C. (2012). Development of biodegradable composites based on wood waste flour and thermoplastic starch. Journal of Applied Polymer Science, 126(S1), E273–E281. DOI 10.1002/app.35420. [Google Scholar] [CrossRef]
7. Kazemi-Najafi, S., Nikray S. J., Ebrahimi, G. A. (2012). A comparison study on creep behavior of wood–plastic composite, solid wood, and polypropylene. Journal of Composite Materials, 46(7), 801–808. [Google Scholar]
8. Jin, K. K., Pal, K. (2010). Overview of wood-plastic composites and uses. In: Engineering materials, vol. 32. Berlin Heidelberg: Springer. [Google Scholar]
9. Dixit, S., Yadav, V. L. (2019). Optimization of polyethylene/polypropylene/alkali modified wheat straw composites for packaging application using RSM. Journal of Cleaner Production, 240, 118228. DOI 10.1016/j.jclepro.2019.118228. [Google Scholar] [CrossRef]
10. Riyajan, S. -A. (2020). A packaging material from a waste paper/sugar cane stalk composite: Preparation and properties. Food Packaging and Shelf Life, 26, 100568. DOI 10.1016/j.fpsl.2020.100568. [Google Scholar] [CrossRef]
11. Jiang, D., Jiang, D., Lv, S. S. C., Zhang, J. (2021). Effect of modified wheat straw fiber on properties of fiber cement-based composites at high temperatures. Journal of Materials Research and Technology, 14(15), 2039–2060. DOI 10.1016/j.jmrt.2021.07.105. [Google Scholar] [CrossRef]
12. Sun, E., Liao, G., Zhang, Q., Qu, P., Wu, G. et al. (2019). Biodegradable copolymer-based composites made from straw fiber for biocomposite flowerpots application. Composites Part B: Engineering, 165, 193–198. DOI 10.1016/j.compositesb.2018.11.121. [Google Scholar] [CrossRef]
13. Miedzianowska, J., Masłowski, M., Strzelec, K. (2019). Thermoplastic elastomer biocomposites filled with cereal straw fibers obtained with different processing methods-preparation and properties. Polymers, 11, 641. DOI 10.3390/polym11040641. [Google Scholar] [CrossRef]
14. Zabihzadeh, S. M. (2010). Influence of plastic type and compatibilizer on thermal properties of wheat straw flour/Thermoplastic composites. Journal of Thermoplastic Composite Materials, 1(6), 817–826. DOI 10.1177/0892705709353711. [Google Scholar] [CrossRef]
15. Uitterhaegen, E., Parinet, J., Labonne, L., Mérian, T., Ballas, V. et al. (2018). Performance, durability and recycling of thermoplastic biocomposites reinforced with coriander straw. Composites Part A: Applied Science & Manufacturing, 113, 254–263. [Google Scholar]
16. Ning, H., Lu, N., Hassen, A. A., Chawla, K., Selim, M. et al. (2019). A review of long fibre-reinforced thermoplastic or long fibre thermoplastic (LFT) composites. International Materials Reviews, 65(3), 164–188. [Google Scholar]
17. Wang, W., Yuan, S., Bu, F., Li, G., Wang, Q. (2011). Wheat-straw-HDPE composite produced by the Hot-pressing method. Journal of Thermoplastic Composite Materials, 23(2), 251–261. DOI 10.1177/0892705710369081. [Google Scholar] [CrossRef]
18. Chen, J., Su, M., Ye, J., Yang, Z., Cai, Z. (2013). All-straw-fiber composites: Benzylated straw as matrix and additional straw fiber reinforced composites. Polymer Composites, 35(3), 419–426. [Google Scholar]
19. Chai, X., He, C., Liu, Y., Wang, G., Zhou, Y. et al. (2022). Degradation of wheat straw/polylactic acid composites by aspergillus Niger. Polymer Composites, 43(3), 1823–1831. DOI 10.1002/pc.26500. [Google Scholar] [CrossRef]
20. Zabihzadeh, M., Dastoorian, F., Ebrahimi, G. (2010). Effect of MAPE on mechanical and morphological properties of wheat straw/HDPE injection molded composites. Journal of Reinforced Plastics & Composites, 29(1), 123–131. DOI 10.1177/0731684408096426. [Google Scholar] [CrossRef]
21. Hao, J., Yi, X., Zong, G., Song, Y., Wang, W. et al. (2021). Fabrication of long bamboo fiber-reinforced thermoplastic composite by extrusion and improvement of its properties. Industrial Crops and Products, 173, 114–120. DOI 10.1016/j.indcrop.2021.114120. [Google Scholar] [CrossRef]
22. Zhang, L., Xu, H., Wang, W. (2020). Performance of straw/linear low density polyethylene composite prepared with film-roll Hot pressing. Polymers, 12(4), 860. DOI 10.3390/polym12040860. [Google Scholar] [CrossRef]
23. Wang, Y., Cao, J., Zhu, L. (2011). Stress relaxation of wood flour/polypropylene omposites omposites at room temperature. Wood and Fiber Science, 43(3), 262–270. [Google Scholar]
24. Tubbs, F. R. (1930). The effect of manorial deficiency upon the mechanical strength of barley straw. Annals of Botany, 44(173), 147–160. [Google Scholar]
25. Gowthaman, S., Kunigal, N. S., Larry, C. R. (2009). Anomalies, influencing factors, and guidelines for DMA testing of fiber reinforced composites. Polymer Composites, 30(7), 962–969. DOI 10.1002/pc.20641. [Google Scholar] [CrossRef]
26. Hassan, M. L., Fadel, S. M., El-Wakil, N. A., Oksman, K. (2012). Chitosan/rice straw nanofibers nanocomposites: Preparation, mechanical, and dynamic thermomechanical properties. Journal of Applied Polymer Science, 125(S2), E216–E222. DOI 10.1002/app.36606. [Google Scholar] [CrossRef]
27. Priya, S. P., Rai, S. K. (2005). Impact, compression, density, void content, and weight reduction studies on waste silk fabric/epoxy composites. Journal of Reinforced Plastics and Composites, 24(15), 1605–1610. DOI 10.1177/0731684405050401. [Google Scholar] [CrossRef]
28. Zhao, J., Dong, Z., Li, J., Chen, L., Bai, Y. et al. (2018). Ensiling as pretreatment of rice straw: The effect of hemicellulase and lactobacillus plantarum on hemicellulose degradation and cellulose conversion. Bioresource Technology, 266, 158–165. DOI 10.1016/j.biortech.2018.06.058. [Google Scholar] [CrossRef]
29. Zhao, Y., Qiu, J., Feng, H., Zhang, M., Lei, L. et al. (2011). Improvement of tensile and thermal properties of poly (lactic acid) composites with admicellar-treated rice straw fiber. Chemical Engineering Journal, 173(2), 659–666. DOI 10.1016/j.cej.2011.07.076. [Google Scholar] [CrossRef]
30. Qin, L., Qiu, J., Liu, M., Ding, S., Shao, L. et al. (2011). Mechanical and thermal properties of poly(lactic acid) composites with rice straw fiber modified by poly(butyl acrylate). Chemical Engineering Journal-Lausanne, 166(2), 772–778. DOI 10.1016/j.cej.2010.11.039. [Google Scholar] [CrossRef]
Cite This Article
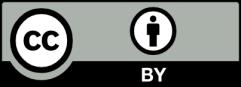
This work is licensed under a Creative Commons Attribution 4.0 International License , which permits unrestricted use, distribution, and reproduction in any medium, provided the original work is properly cited.