Open Access
ARTICLE
MALDI ToF Investigation of the Reaction of Soy Protein Isolate with Glutaraldehyde for Wood Adhesives
1 Yunnan key Laboratory of Wood Adhesives and Glue Products, College of Material Science and Engineering, Southwest Forestry University, Kunming, 650224, China
2 International Joint Research Center for Biomass Materials, Southwest Forestry University, Kunming, 650224, China
3 Université de Lorraine LERMAB-ENSTIB, 27 rue Philippe Seguin, Epinal, 88000, France
* Corresponding Authors: Hong Lei. Email: ; Xuedong Xi. Email:
(This article belongs to the Special Issue: Renewable and Biosourced Adhesives-2021)
Journal of Renewable Materials 2023, 11(3), 1439-1450. https://doi.org/10.32604/jrm.2022.023535
Received 05 May 2022; Accepted 28 May 2022; Issue published 31 October 2022
Abstract
Soy protein adhesives are currently a hot research topic in the wood panels industry for the abundant raw material reserves, reasonable price and outstanding environmental features. But their poor water resistance, low bonding strength and intolerance to mold are major drawbacks, so that proper modification before use is essential. Glutaraldehyde is one of the more apt cross-linking agents for soybean protein adhesives, which can effectively improve the bonding strength and water resistance of the adhesive. Equally, glutaraldehyde is also an efficient and broad-spectrum fungicide that can significantly improve the anti-fungal properties of a soy protein adhesive. In the work presented here, matrix assisted laser desorption ionization (MALDI-ToF) mass spectrometry and Fourier transform infrared spectroscopy techniques were used to analyze the reaction mechanism of glutaraldehyde cross-linking soybean protein. The results confirmed the reaction of the aldehyde group with amino groups of the side chains and the amide groups of the peptide linkages constituting the skeletal chain of the protein. The laboratory plywood and particleboard bonded with glutaraldehyde-soy bean protein adhesives were prepared to determine the adhesive bonding properties, the dry strength, 24 h cold water soaking wet strength and 3 h hot water (63°C) wet strength of plywood were 2.03, 1.13 and 0.75 MPa, respectively, which satisfied the requirements of industrial production.Graphical Abstract
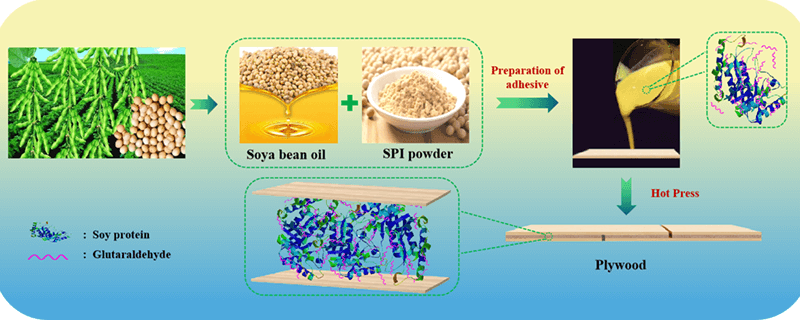
Keywords
Soy protein adhesives as a bio-based wood adhesive are currently a hot research topic in the wood composites industry, for their excellent environmentally friendly properties, abundance of raw materials, and low prices. Actually, in the 1930s soy bean protein adhesives were widely used in the industrial production of plywood in the USA. However, due to their low bonding strength, poor corrosion resistance and water resistance, it has been replaced by some synthetic resin adhesives with better bonding properties derived from petrochemical products, such as urea-formaldehyde (UF), phenol-formaldehyde (PF) and melamine-formaldehyde (MF) resins [1,2]. But since toxicity and carcinogenicity formaldehyde has inevitably been used as a raw material for the preparation of these synthetic resins, so that their glued products have a problem of formaldehyde emission. In recent decades, environmental protection issues have attracted considerable attention for the non-renewability of synthetic raw materials from petroleum resources. Thus, environmentally friendly wood adhesives from renewable biomass resources have entered in focus, and a lot of research work has been carried out on them [3]. Among them, soy protein adhesives have once again become a hot research topic.
Research on soy protein adhesives is more focused on improving their bonding properties and water resistance. To achieve this, some researchers have used acid/base pairs to hydrolyse soy protein molecules to expose more active functional groups hence to have a better reaction [4–6]. In addition, the use of microwave treatment [7], nanomaterial modification [8], graft copolymerisation [9–11] bio-nanotechnology modification [12–14] and cross-linked blending modification have also been reported. Of these, cross-linking modification has been heavily studied due to its simple process and significant modification effect. Moreover, there are many cross-linking modifiers that can be used for soy protein gums, such as formaldehyde, glyoxal, furfural, polyethyleneimine, epoxy resin, etc. [15,16]. Glutaraldehyde is a highly reactive, low-volatility aldehyde which is also one of the suitable soy protein cross-linking modifiers. In fact, the reports on reactions of soy protein isolate (SPI) and of gluten protein isolate with glutaraldehyde to prepare plywood adhesives have been described in the literature [17–19]. Glutaradehyde crosslinks proteins by reacting mainly with the side chains amino groups of some amino acid residues intermolecularly and intramolecularly and increasing the protein chains molecular entanglement [18]. Reaction with the amide groups of the skeletal peptide chain of the protein could also take place. The adhesive properties of the glutaraldehyde cross-linked soy protein and gluten protein were enhanced with an improvement in water resistance and strength being reported.
While the applied results for plywood adhesives of such proteins have been presented what has not been investigated are the oligomers that are progressively formed by the reaction of the protein with glutaraldehyde to define how the reaction advances towards cross-linking. Therefore, in this work, we investigated the reaction of soy protein isolate with glutaraldehyde using MALDI-ToF and FTIR to illustrate the reaction mechanism involved. In addition to this, the prepared soy protein-glutaraldehyde adhesive was used to bond plywood and particleboard, thus to again verify its feasibility for practical application.
Soy protein isolate (BR) was obtained from Yuanye Biotechnology Co., Ltd., Shanghai, China. Glutaraldehyde (AR), Formic acid (85% in water) and Sodium hydroxide pellets (95%) were brought from Shanghai Macklin Biochemical Co., Ltd., Shanghai, China.
2.2 Preparation of Soy Protein-Glutaraldehyde Adhesives
Soy protein isolate was prepared in a 25% solids content liquid, then to mix 5%, 7.5%, 10% and 20% glutaraldehyde by weight on soy protein isolate quality, named as SPG1, SPG2, SPG3, SPG4 respectively, their corresponding viscosities were 413, 635, 770, 957 mPa⋅s. Moreover, based on the formulation of SPG1, the effect of pH value on the performance of the adhesives was studied, and the adhesives under the conditions of pH = 5, 7, 9, 11 were prepared and named SPG-5, SPG-7, SPG-9, SPG-11, the viscosity of them were 417, 949, 1291 and 1940 mPa⋅s, respectively.
2.3 Matrix Assisted Laser Desorption Ionization (MALDI-ToF) Mass Spectrometry.
A solidified SPG1 sample for matrix assisted laser desorption ionization time-of-flight (MALDI-ToF) analysis was prepared by first dissolving 5 mg of samples soy protein isolate alone and reacted with 5% by weight of glutaraldehyde at 120°C, in 1 mL of a 50:50 v/v acetone/water solution. Then 10 mg of this solution is added to 10 μL of a 2, 5-dihydroxy benzoic acid (DHB) matrix. The locations dedicated to the samples on the analysis plaque were first covered with 2 μL of a NaCl solution 0.1 M in 2:1 v/v methanol/water, and predried. Then 1 μL of the sample solution was placed on its dedicated location and the plaque is dried again. MALDI-ToF spectra were obtained using an Axima-Performance mass spectrometer from Shimadzu Biotech (Kratos Analytical Shimadzu Europe Ltd., Manchester, UK) using a linear polarity-positive tuning mode. The measurements were carried out making 1000 profiles per sample with 2 shots accumulated per profile. The spectrum precision is of +1 Da.
Fourier transform infra-red (FTIR) analysis with a Shimadzu IRAffinity-1 spectrometer was used to confirm the relevant structures present. The reference spectrum used a potassium bromide tablet (ACS, ACROS Organics) as blank. An equivalent potassium bromide tablet in which was mixed 5% w/w of the powdered samples for analysis. A 32 scans transmission spectrum at a 2.0 resolution was then obtained.
2.5 Preparation of the Plywood
Poplar 3-ply plywood panels (2 mm veneers thickness) bonded with soy protein-glutaraldehyde adhesives for 5 min at 150°C at 0.80 MPa after a closed assembly time of 10 min. The spread rate was 220 g/m2 double glue line. The panels were conditioned at ambient condition for 2 days before being cut into samples. For testing shear strength, the panels were cut into 100 mm × 25 mm samples according to GB/T 17657-2013, the size of the glued area of the test specimen is 25 mm × 25 mm, with ten samples being tested dry, ten samples tested wet after soaking in room temperature water for 24 h and ten samples tested wet after soaking in 63°C hot water for 3 h. Fig. 1 shows the preparation process of the protein adhesive and its application for plywood bonding.
Figure 1: Schematic representation for the preparation of soybean protein adhesive and its using for plywood bonding
2.6 Preparation of the Particleboard
Three identical monolayer particleboards of 350 × 310 × 10 mm3 size were prepared. The adhesive solids load was 10% on bone-dry wood particle. The panels were pressed with a pressure of 5 MPa for 10 min, the hot pressing temperature was 180°C. The prepared particleboard were conditioned at an indoor ambient condition for 2 days. After sanding the panel surface, the boards were cut to 50 mm × 50 mm for the tests of dry internal bond (IB) strength, and water absorption thickness expansion ratio. At least three samples were tested for each test according to China National Standard GB/T 17657-2013.
The MALDI ToF peaks relative to species formed by reaction of glutaraldehyde on SPI are shown in Fig. 2. Before assigning these results what is needed is to compare Fig. 2 with Fig. 3, this latter outlining the MALDI ToF spectra of SPI alone. By this comparison, the following peaks appear in Fig. 2 that are not present in the spectra of SPI alone in Fig. 3, namely: 237, 255, 316, 358, 399, 441, 522, 581, 638, 659, 675, 758, 874, 891, 965, 1056, 1212, 1297 and 1485 Da. The assignment shown in Table 1 could be gleaned by the reported molecular weights of soy amino acids and by their relative frequency [20].
Figure 2: MALDI ToF spectra of the product of the reaction of SPI + 5% glutaraldehyde at 120°C. (a) 60 to 300 Da range. (b) 300 to 600 Da range. (c) 600 to 900 Da range. (d) 900 to 1600 Da range
Figure 3: MALDI ToF spectra of the SPI alone treated at 120°C. (a) 50 to 100 Da range. (b) 150 to 500 Da range
From the assignments in Table 1 several conclusions can be drawn, Aspartic acid, glutamic acid, arginine and leucine are more present in line with their higher proportion in soy protein. Second, the interpretations in Table 1 are only indicative, two classes of compounds being present, namely (i) those in which each amino acid is linked by a glutaraldehyde bridge to another aminoacid, as is the case for example for the species assigned to the peaks at 638, 659 Da and the smaller molecular weight species in Table 1. (ii) The species in which glutaraldehyde bridges occur linking short aminoacid oligomers that are fragment of the soy protein. For example all the species from 758 to 1485 Da are indicated in the table with glutaraldehyde bridges between two single aminoacids, but the other aminoacids have been linked to just one aminoacid, when in reality the oligomer does contain glutaraldehyde bridges but these are most likely between short protein oligomers. Thus, for example while the peak at 874 Da is interpreted in the table as:
Arginine–G–Arginine–G–Arginine–Glycine–Aspartic ac
This is most likely not the case, as it most likely to be:
Arginine–Aspartic ac.–G–Arginine–Glycine G–Arginine
Or other mixes of aminoacids enchainement, this being the case for all the higher molecular weight peak species.
A further point from Table 1 is that as the molecular weight of the species increases so does the number of interpretations possible, the peak at 1212 Da being a particularly clear example of this.
Lastly, unreacted aldehyde groups belonging to the glutaraldehyde are still present, although in a minority of cases. This is the case of the species from 237 to 316 Da, and 399, 522 and 1297 Da.
Figs. 4a and 4b shows the infrared spectra analysis results of the solid SPG1, SPG2, SPG3 and SPG4 resins. It is indicated that the broad peak around 3300 cm−1 corresponds to bound N–H and O–H groups. The peak observed at about 2930 cm−1 is attributed to C-H stretching vibrations of methyl groups in protein adhesives. The peaks of several adhesives at these positions are consistent, and even the peaks intensity show basically no differences. Obviously, the absorption peak which was observed at 1657, 1542 and 1242 cm−1 in the figure belong to C=O stretching vibration (amide I), N–H bending vibration (amide II), N–H in plane and C–N stretching vibration (amide III) [21], respectively. Combined with Fig. 4b, it is evident that the N–H stretching vibration absorption peak of the adhesive SPG4 at 1542 cm−1 is the weakest one. This is due to SPG4 adhesive containing more glutaraldehyde which by reacting with amino groups causes that more N–H groups are consumed [22]. It is worth clarifying that the aldehyde can reacts with the amino groups of the side chains such as arginine and lysine, and can also react with the amide groups of the peptide linkages constituting the skeletal chain of the protein. Certainly, AMINO groups of the side chains are more reactive than that the AMIDE groups of the skeletal chain of the protein, but what cannot be excluded is that the second reaction is also likely to happen, as they are =N–H group hence still reactive as urea is. The C-O stretching vibration of hydroxyl groups bonded to carbon atoms is at 1052 cm−1 [23]. It clearly appears that SPG4 has a stronger absorption peak than the other three adhesives, which means that the SPG4 adhesives contain a higher proportion of C–O structures. This is attributed to the addition reaction of glutaraldehyde to the amino groups to produce hydroxyl groups [24–26].
Figure 4: Infrared spectrum test results of the SPG1, SPG2, SPG3, and SPG4 resins
3.2 Bonding Performance of Adhesives
Fig. 5a shows the dry shear strength of the boards prepared with SPG adhesive and the wet bond strength after soaking in cold water for 24 h or in 63 ± 2°C hot water for 3 h. Compared to neat soy protein adhesive (SP), it can be seen from the figure that all SPG adhesives show a good dry shearing strength, as these are all higher than the standard requirement of China National Standard GB/T9846-2015 (≥0.7 MPa). The more satisfactory result is that the SPG1 adhesive, hence with the lower proportion of glutaraldehyde, has the best bonding performance compared to the other two resins. In particular, its 24-h cold water immersion strength and 3-h 63°C hot water strength are 1.11 and 0.78 MPa, respectively, which meets the standard requirements. However, excessive use of glutaraldehyde will cause the 3 h 63°C hot water strength of the plywood glued by the synthetic adhesive to decrease. This can be observed in SPG3’s 3 h 63°C hot water strength of 0.69 MPa. This may be due to the excessive addition of glutaraldehyde resulting in an excessively high viscosity of the adhesive and the reduction of its ductility on the surface of the plywood veneers [27,28]. This can be detected during the preparation of the adhesive, also as shown in the part of preparation of soy protein-glutaraldehyde adhesives.
Figure 5: (a) Shear strength of plywood showing the effect of glutaraldehyde addition on the properties of soy protein-glutaraldehyde adhesive (b) The effect of different pHs on the properties of soy protein-glutaraldehyde adhesive
Fig. 5b shows the effect of pH values of 5, 7, 9, 11 on the properties of soy protein-glutaraldehyde adhesive, such as the dry shear strength of the plywood prepared with the adhesive and their 24 h cold water strength as well as their wet bond strength after immersion in hot water at 63 ± 2°C for 3 h. As can be seen from the figure, all SPG resins show a good dry shearing strength, as they are all higher than the standard requirement of China National Standard GB/T9846-2015 (≥0.7 MPa). In addition, a more noteworthy feature is that SPG-9 and SPG-11 resins have the best bonding properties, compared to the other two resins. The dry shear strength of its bonded plywood is as high as 2.59 and 2.03 MPa respectively, which is much higher than the standard requirement (≥0.7 MPa). At the same time, the 24-h cold water immersion wet strengths of the two resins were 1.11 and 1.13 MPa, respectively. This means that the SPG-9 and SPG-11 resins have excellent water resistance. Even more satisfying, their 3-h hot water strength also meets the standard requirement of 0.7 MPa or higher. Furthermore, by comparing weakly acidic and alkaline conditions, it appears that the plywood bonded with the SPG adhesive has better dry strength and wet shear strength under alkaline than acidic conditions [29]. This indicates that the bonding performance of the SPG adhesive is greatly affected by the pH value, and it will bond better under alkaline conditions, with its water resistance also being enhanced.
To test the application of soy protein-glutaraldehyde adhesives in particleboard bonding, these were prepared using the SPG1, 2 and 3 adhesives at pH 9 as shown in Fig. 6, and their performance results are shown in Table 2. Firstly, it can be seen from Table 2 that the particleboards prepared from SPG1, SPG2 and SPG3 showed little difference in density values between them, i.e., 0.71, 0.74 and 0.72 g/cm3, respectively. Secondly, all particleboards prepared from SPG resins showed good internal bond strengths, which were higher than the GB/T 9846-2015 standard requirements (≥0.4 MPa). Among them, the internal bond strength of particleboard prepared with SPG2 adhesive was as high as 0.78 MPa, its higher density possibly also contributing to it [30,31]. However, the internal bond strength of SPG3 was relatively lower at 0.59 MPa, which was mainly due to the large amount of glutaraldehyde added leading to the excessive viscosity of the adhesive [32]. This was shown in the adhesive preparation method, so that its ductility and penetration effect on the surface of the board was weakened, which eventually led to the poor bonding strength [33].
Figure 6: Particleboard prepared from SPG1, SPG2 and SPG3 resins
The reaction mechanism of glutaraldehyde as a cross-linking agent for soybean protein adhesive was studied by MALDI-ToF and FTIR analysis in this work. Two types of linkages form and can be present, namely (i) each amino acid is linked by a glutaraldehyde bridge to another amino acid, and (ii) glutaraldehyde bridges also occur linking short amino acid oligomers that are fragment of the soy protein. Cross-linking by addition reaction of aldehydes to amino groups occurred and produced hydroxyl group. In this research work, it’s also once again shown that the glutaraldehyde crosslinked soybean protein adhesive can be used for plywood and particleboard bonding. The panels prepared show good performance and are up to the requirements of industrial wood-based panels production.
Funding Statement: This work was supported by the National Natural Science Foundation of China (31660176), the Yunnan Provincial Natural Science Foundation (202201AU070222) and Scientific Research Fund Project of Yunnan Provincial Department of Education (2022J0490). This research was also financed by the ERA-CoBioTech Project WooBAdh (Environmentally-friendly bioadhesives from renewable resources) and by the Slovenian Ministry of Education. Science and Sport and the Slovenian Research Agency within the Framework of the Program P4-0015.
Conflicts of Interest: The authors declare that they have no conflicts of interest to report regarding the present study.
References
1. Pizzi, A., Papadopoulos, A. N., Policardi, F. (2020). Wood composites and their polymer binders. Polymers, 12(5), 1115. DOI 10.3390/polym12051115. [Google Scholar] [CrossRef]
2. Pizzi, A. (2016). Wood products and green chemistry. Annals of Forest Science, 73(1), 185–203. DOI 10.1007/s13595-014-0448-3. [Google Scholar] [CrossRef]
3. Luo, J., Luo, J., Yuan, C., Zhang, W., Li, J. et al. (2015). An eco-friendly wood adhesive from soy protein and lignin: Performance properties. RSC Advances, 5(122), 100849–100855. DOI 10.1039/c5ra19232c. [Google Scholar] [CrossRef]
4. Fan, B., Zhang, L., Gao, Z., Zhang, Y., Shi, J. et al. (2016). Formulation of a novel soybean protein-based wood adhesive with desired water resistance and technological applicability. Journal of Applied Polymer Science, 133(27), 1–10. DOI 10.1002/app.43586. [Google Scholar] [CrossRef]
5. Hettiarachchy, N. S., Kalapathy, U., Myers, D. J. (1995). Alkali-modified soy protein with improved adhesive and hydrophobic properties. Journal of the American Oil Chemists’ Society, 72(12), 1461–1464. DOI 10.1007/bf02577838. [Google Scholar] [CrossRef]
6. Wu, Z., Lei, H., Du, G. (2013). Disruption of soy-based adhesive treated by Ca(OH) and NaOH. Journal of Adhesion Science and Technology, 27(20), 2226–2232. DOI 10.1080/01694243.2013.768140. [Google Scholar] [CrossRef]
7. Jin, B., Zhou, X., Zheng, Z., Liang, Y., Chen, S. et al. (2020). Investigating on the interaction behavior of soy protein hydrolysates/β-glucan/ferulic acid ternary complexes under high-technology in the food processing: High pressure homogenization versus microwave treatment. International Journal of Biological Macromolecules, 150, 823–830. DOI 10.1016/j.ijbiomac.2020.02.138. [Google Scholar] [CrossRef]
8. Zhao, S., Wang, Z., Li, Z., Li, L., Li, J. et al. (2019). Core-shell nanohybrid elastomer based on co-deposition strategy to improve performance of soy protein adhesive. ACS Applied Materials & Interfaces, 11(35), 32414–32422. DOI 10.1021/acsami.9b11385. [Google Scholar] [CrossRef]
9. Wang, Z., Hua, Z., Huang, J., Ge, Z., Guo, J. et al. (2018). Improvement of the bonding properties of cassava starch-based wood adhesives by using different types of acrylic Iester. International Journal of Biological Macromolecules, 126, 603–611. DOI 10.1016/j.ijbiomac.2018.12.113. [Google Scholar] [CrossRef]
10. Liu, H., Li, C., Sun, X. (2015). Improved water resistance in undecylenic acid (UA)-modified soy protein isolate (SPI)-based adhesives. Industrial Crops and Products, 74(1), 577–584. DOI 10.1016/j.indcrop.2015.05.043. [Google Scholar] [CrossRef]
11. González, A., Igarzabal, C. I. A. (2017). Study of graft copolymerization of soy protein-methyl methacrylate: Preparation and characterization of grafted films. Journal of Polymers & the Environment, 25 (2), 214–220. DOI 10.1007/s10924-016-0797-0. [Google Scholar] [CrossRef]
12. Wang, Z., Zhao, S., Zhang, W., Qi, C., Zhang, S. et al. (2017). Bio-inspired cellulose nanofiber-reinforced soy protein resin adhesives with dopamine-induced codeposition of water-resistant interphases. Applied Surface Science, 478(6), 441–450. DOI 10.1016/j.apsusc.2019.01.154. [Google Scholar] [CrossRef]
13. Liu, H., Xie, W., Song, F., Wang, X., Wang, Y. (2019). Constructing hierarchically hydrophilic/superhydrophobic ZIF-8 pattern on soy protein towards a biomimetic efficient water harvesting material-science direct. Chemical Engineering Journal, 369, 1040–1048. DOI 10.1016/j.cej.2019.03.152. [Google Scholar] [CrossRef]
14. Wang, L., Liu, J., Zhang, W., Zhang, D., Li, J. et al. (2020). Biomimetic soy protein-based exterior-use films with excellent UV-blocking performance from catechol derivative acacia mangium tannin. Journal of Applied Polymer Science, 138(15), 1–10. DOI 10.1002/app.50185. [Google Scholar] [CrossRef]
15. Lépine, E., Riedl, B., Wang, X., Pizzi, A., Delmotte, L. et al. (2015). Synthesis of bio-adhesives from soybean flour and furfural: Relationship between furfural level and sodium hydroxide concentration. International Journal of Adhesion and Adhesives, 63, 74–78. DOI 10.1016/j.ijadhadh.2015.08.007. [Google Scholar] [CrossRef]
16. Hao, X., Fan, D. B. (2018). Preparation and characterization of epoxy-crosslinked soy protein adhesive. Adhesion Science and Technology, 32(24), 2682–2692. DOI 10.1080/01694243.2018.1517488. [Google Scholar] [CrossRef]
17. Charles, R., Frihart, L., Lorenz, F. (2019). Specific oxidants improve the wood bonding strength of soy and other plant flours. Journal of Polymer Science Part A: Polymer Chemistry, 57(9), 1017–1023. DOI 10.1002/pola.29357. [Google Scholar] [CrossRef]
18. Wang, Y., Mo, X., Sun, S., Wang, D. (2007). Soy protein adhesion enhanced by glutaraldehyde crosslink. Journal of Applied Polymer Science, 104(1), 130–136. DOI 10.1002/app.24675. [Google Scholar] [CrossRef]
19. Xi, X., Pizzi, A., Gerardin, C., Liao, J., Amirou, S. et al. (2021). Glutaradehyde-wheat protein-based adhesives for plywood. The Journal of Adhesion, 97(1), 88–100. DOI 10.1080/00218464.2019.1630821. [Google Scholar] [CrossRef]
20. Yang, B., Yang, H., Li, J., Li, Z., Jiang, Y. (2010). Amino acid composition, molecular weight distribution and antioxidant activity of protein hydrolysates of soy sauce lees. Food Chemistry, 124(2), 551–555. DOI 10.1016/j.foodchem.2010.06.069. [Google Scholar] [CrossRef]
21. Zhang, W., Sun, H., Zhu, C., Wan, K., Zhang, Y. et al. (2010). Mechanical and water-resistant properties of rice straw fiberboard bonded with chemically-modified soy protein adhesive. RSC Advances, 8(27), 15188–15195. DOI 10.1039/C7RA12875D. [Google Scholar] [CrossRef]
22. Lin, Q., Chen, N., Bian, L., Fan, M. (2012). Development and mechanism characterization of high performance soy-based bio-adhesives. International Journal of Adhesion and Adhesives, 34, 11–16. DOI 10.1016/j.ijadhadh.2012.01.005. [Google Scholar] [CrossRef]
23. Chen, N., Lin, Q., Rao, J., Zeng, Q. (2010). Water resistances and bonding strengths of soy-based adhesives containing different carbohydrates. Industrial Crops and Products, 50(10), 44–49. DOI 10.1016/j.indcrop.2013.06.038. [Google Scholar] [CrossRef]
24. Rashid, S., Adnani, A., Ashraf, Q. F. (2015). Synthesis and application of formaldehyde free melamine glutaraldehyde amino resin as an effective retanning agent. Indian Journal of Chemical Technology, 22(1), 48–55. [Google Scholar]
25. Gen, F. C., Shan, B. L. (2004). Preparation and FTIR properties of amino compounds modified glutaraldehyde crosslinked chitosan resin activated with cyanuric chloride. Spectroscopy and Spectral Analysis, 24(11), 1315–1318. DOI 10.1016/j.jco.2003.08.015. [Google Scholar] [CrossRef]
26. Yan, E. K., Cao, H., Zhang, C., Lu, Q., Ye, Y. et al. (2015). Cross-linked protein crystals by glutaraldehyde and their applications. RSC Advances, 5(33), 26163–26174. DOI 10.1039/C5RA01722J. [Google Scholar] [CrossRef]
27. Amini, M., Hashim, R., Sulaiman, N. S. (2019). Formaldehyde-free wood composite fabricated using oil palm starch modified with glutardialdehyde as the binder. International Journal of Chemical Engineering, 2019(10), 1–9. DOI 10.1155/2019/5357890. [Google Scholar] [CrossRef]
28. Mohd, H. M. A., Rokiah, H., Nurul, S. S., Mazlan, M., Mohmad, N. M. et al. (2018). Study on dimensional stability of particleboard made using glutardialdehyde modified corn starch as the binder at various relative humidity. International Journal of Engineering & Technology, 7(2.15), 19–22. DOI 10.14419/ijet.v7i2.15.11191. [Google Scholar] [CrossRef]
29. He, Z., Chapital, D. C., Cheng, H., Dowd, M. K. (2014). Comparison of adhesive properties of water-and phosphate buffer-washed cottonseed meals with cottonseed protein isolate on maple and poplar veneers. International Journal of Adhesion and Adhesives, 50, 102–106. DOI 10.1016/j.ijadhadh.2014.01.019. [Google Scholar] [CrossRef]
30. Bacigalupe, A., Fernández, M., Eisenberg, P., Escobar, M. (2020). Greener adhesives based on UF/soy protein reinforced with montmorillonite clay for wood particleboard. Journal of Applied Polymer Science, 137(37), 49086–49086. DOI 10.1002/app.49086. [Google Scholar] [CrossRef]
31. Nicolao, E. S., Leiva, P., Chalapud, M. C., Ruseckaite, R. A., Ciannamea, E. M. et al. (2020). Flexural and tensile properties of biobased rice husk-jute-soybean protein particleboards. Journal of Building Engineering, 30, 101261–101261. DOI 10.1016/j.jobe.2020.101261. [Google Scholar] [CrossRef]
32. Amini, M. H. M., Hashim, R., Sulaiman, N. S., Hiziroglu, S., Sulaiman, O. et al. (2015). Glutardialdehyde modified corn starch-urea formaldehyde resin as a binder for particleboard making. Applied Mechanics and Materials, 754–755, 89–93. DOI 10.4028/www.scientific.net/AMM.754-755.89. [Google Scholar] [CrossRef]
33. Xi, X., Delmotte, L., Younesi-Kordkheili, H., Pizzi, A. (2018). Melamine–glyoxal–glutaraldehyde wood panel adhesives without formaldehyde. Polymers, 10(1), 22. DOI 10.3390/polym10010022. [Google Scholar] [CrossRef]
Cite This Article
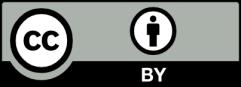