Open Access
ARTICLE
Properties and Hydration Mechanism of Cementitious Materials Prepared from Calcined Coal Gangue
School of Materials and Engineering, Xi’an University of Architecture and Technology, Xi’an, 710055, China
* Corresponding Author: Hui Li. Email:
Journal of Renewable Materials 2023, 11(3), 1223-1236. https://doi.org/10.32604/jrm.2022.022893
Received 30 March 2022; Accepted 26 May 2022; Issue published 31 October 2022
Abstract
The preparation of cementitious materials by replacing part of the cement with activated coal gangue is of great significance to the cement industry in terms of carbon reduction and coal-based solid waste utilization. For this paper, cementitious material was prepared by firing activated coal gangue under suspension conditions and batching it with limestone powder using Inner Mongolia coal gangue as raw material. The optimal ratio was determined by testing the strength changes of the cementitious material at 3, 7, and 28 days of hydration, and the hydration process and mechanism were explored by combining the pore structure, heat of hydration, chemical composition, phase composition, and microscopic morphological characteristics of the hydration products. The results showed that the active materials formulated from activated gangue and limestone powder can be used to prepare cementitious materials with good performance at the level of 30%–50% replacement of cement. The optimal ratio was 30% replacement of cement, and the mass ratio of calcined gangue to limestone powder was 2:1. The 3 days compressive strength of this ratio was 28.8 MPa, which was only slightly lower than that of cement. However, the 28 days compressive strength of samples reached 67.5 MPa, which was much higher than that of the reference cement. In the hydration of this cementitious material, not only does the activated coal gangue react with the Ca(OH)2 formed by hydration to form C–S–H gel, but CaCO3 also participates in the reaction to form a new phase of carbon aluminate, and the two effects together promote the development of the later strength of the samples. This paper can provide a reference for carbon reduction in the cement production process and comprehensive utilization of coal gangue.Keywords
Coal gangue is a solid waste produced in coal mining and production, due to the lack of effective comprehensive utilization technology coal gangue is mainly disposed of in stockpiles, not only occupying extensive land but also leading to serious environmental pollution [1–5]. Coal gangue with kaolinite as the main component, also known as coal series kaolinite, which is activated and calcined to prepare metakaolin that can be used as auxiliary cementitious material, can not only replace part of the cement but also significantly improve the durability and late strength [6–10]. Cement production emits substantial CO2 and other greenhouse gases, thus, gangue can be applied to cement production both to achieve the effective use of coal gangue and to reduce the carbon emissions of cement industry production [11–14]. Therefore, the research on the resource utilization technology of coal gangue in cement is of great practical significance.
At present, the preparation of activated coal gangue mainly adopts the method of calcining lumpy materials in a stacked state, and the calcination time is generally as long as 2–6 h, which not only exhibits high energy consumption but also causes the unstable quality of the product [15–19]. Suspension calcination technology is a new process used for gangue calcination in recent years. In this process due to the full contact transfer between material and airflow, as well as the high reaction efficiency, the calcination time and energy consumption are reduced, thus avoiding the problem of the reduced activity of activated coal gangue. The application of activated coal gangue in cement is usually as a mineral admixture. The amount of admixture is usually less than 15%–20% [20–22] leading to the limitation in the comprehensive utilization of coal gangue. In recent years, Karen Scrivener and Dhandapani et al. [20,23–25] proposed a cementitious material system that combines calcined clay and limestone powder to achieve comparable performance to pure silicate cement at a level of 45% total replacement of cement. In fact, both calcined clay and calcined coal series kaolinite can be used to prepare metakaolin with high activity, hence, it is theoretically feasible to use calcined coal gangue to replace clay to prepare cementitious materials. Liu et al. [26] studied the effect of coal gangue with low kaolinite content on the mechanical properties of cement, and the results showed that for binders with Calcined coal gangue and limestone, the replacement level can reach 30% (20% Calcined coal gangue and 10% limestone). Therefore, studies on using the suspended calcination technology for the preparation of metakaolin by calcination of coal series kaolinite, along with the subsequent preparation of cementitious materials through batching with limestone powder, are beneficial for both the utilization of coal-based solid waste and the carbon reduction of the cement industry in China.
This paper draws on the calcined clay and limestone cementitious composites system proposed by Karen Scrivener et al. [27] to replace calcined clay with coal gangue from the Junger mine in Inner Mongolia as raw material, and the rapid calcination technology developed by Xi’an University of Architecture and Technology was used to stimulate its activity, which was mixed into cement together with limestone powder to replace part of the cement. The influence mechanisms of the ratio of calcined coal gangue and limestone powder on the mechanical properties of cementitious materials were studied, and the hydration process was investigated by pore structure analysis, the heat of hydration, chemical analysis, physical phase analysis, and morphological analysis [28]. Compared with calcined clay and limestone cementitious composites systems, it is more energy-saving. The results of the study provide a new method for the comprehensive utilization of coal gangue.
Calcined coal gangue: The coal gangue from the Junger mine in the Inner Mongolia Autonomous Prefecture was crushed and ground until it could pass through the 80 μm square hole sieve. The coal gangue powder was calcined in suspension at 800°C to prepare the activated coal gangue used in the experiment and then stored in sealed conditions. An X-ray fluorescence spectrometer (S4 PIONEER Bruker, Germany) was used for the elemental analysis of the metakaolin products, and the results are shown in Table 1. An X-ray diffraction analyzer (D/MAX 2200, Rikagu, Japan) was used for the physical phase analysis of the coal gangue and calcined coal gangue, and the results are shown in Fig. 1. The analysis results showed that the main mineral phases of uncalcined coal gangue are kaolinite phase and boehmite phase. After rapid calcination, the kaolinite phase and boehmite phase disappear, and the kaolinite phase is completely transformed into metakaolin. The dissolution rate of active silica and aluminum was used as an indicator to characterize the product activity, and the potassium fluorosilicate volumetric method and the spectrophotometric method were used for analysis [29,30]. The analysis results showed that the calcined coal gangue had a good activity with 69.83% dissolution of active SiO2 and 78.91% dissolution of active Al2O3.
Figure 1: XRD patterns of coal gangue and calcined coal gangue
Cement: The reference cement produced by Anhui Conch Cement Plant was used. An X-ray diffraction analyzer (D/MAX 2200, Rikagu, Japan) was used for the physical phase analysis of the cement, and its XRD pattern is shown in Fig. 2.
Figure 2: XRD patterns of cement
As shown in Fig. 2, the main mineral phases in cement were C3S, C2S, and C4AF, along with a small amount of gypsum.
Limestone powder: The calcium carbonate reagent (analytical purity) produced by Tianjin Damao Chemical Reagent Factory was used; it was a white powder, odorless and tasteless, with CaCO3 content greater than 99%.
Water: The water used in this experiment was ordinary tap water.
Proportioning design: Three formulations with 1:1, 2:1, and 3:1 ratios of calcined coal gangue and limestone powder were adopted for 10 groups of experiments (including 1 group of blank experiments) under three levels of cement blending of 50%, 60%, and 70%. Further formulations with 10%, 15%, 20%, 25%, and 30% calcined coal gangue in the single mix were also investigated. The specific proportions of the formulations are shown in Table 2.
Mechanical strength test: According to the GB/T 17671-1999 Cement Sand Strength Test Method, the compressive strength was measured at 3 days, 7 days, and 28 days.
Analysis of hydration products: The cement specimens were formed with a fixed water–cement ratio of Z = 0.4, placed in a standard curing chamber at a temperature of 20°C and air humidity of 96%, and cured by extracting the broken pieces from the middle part of the specimens and soaking them in anhydrous ethanol for 48 h to terminate hydration for the strength determination at 3 days, 7 days, and 28 days. The specimens were taken out and dried in a vacuum oven for 8 h and then placed in sealed bags for pore structure analysis, chemical composition analysis, XRD analysis, and SEM-EDS analysis.
First, this part investigated the effect of mixing only calcined coal gangue on the strength of cementitious materials. The changes in compressive strength of the gelling material at 3, 7, and 28 days with different amounts of calcined coal gangue are shown in Fig. 3. The addition of calcined coal gangue led to a significant decrease in the 3-day compressive strength, approximately 30%–40% reduction compared to reference cement. This is because calcined coal gangue is hardly involved in the reaction at the early stage of hydration of cementitious materials, and the mechanical strength is mainly provided by cement at this time, whereby a greater amount of calcined coal gangue addition leads to a greater loss of strength. As hydration progresses, calcined coal gangue reacts with Ca(OH)2 produced by cement hydration to form a gel, thus gradually exerting strength, accordingly, the contribution of calcined coal gangue to the mechanical strength of cementitious materials is mainly reflected in the middle and late stages of hydration. Fig. 3 shows that the incorporation of calcined coal gangue led to the 7-day compressive strength being comparable to that of cement. For the 28-day strength of the cementitious material, the maximum compressive strength was obtained at a doping rate of 15%, and the addition of calcined coal gangue with a mixing rate of 25% increased the mechanical strength of the cementitious material, however, further increasing the mixing rate led to a decrease in the compressive strength of the cementitious material.
Figure 3: Effect of calcined coal gangue content on the mechanical strength of cementitious materials
Next, this part used calcined coal gangue and limestone powder mixed with cement, the strength of several groups of samples with cement contents of 50%, 60%, and 70% are shown in Fig. 4, Fig. 5, and Fig. 6, respectively.
Figure 4: Compressive strength for specimens with 30% replacement of cement
Figure 5: Compressive strength for specimens with 40% replacement of cement
Figure 6: Compressive strength for specimens with 50% replacement of cement
As shown in Fig. 4, the 3-day, 7-day, and 28-day compressive strengths of the reference cement specimens were 32.0 MPa, 41.0 MPa, and 48.0 MPa, respectively. After incorporation of calcined coal gangue and limestone powder, the compressive strength of the cementitious material generally decreased slightly at 3 days because the hydrate reaction between calcined coal gangue and Ca(OH)2, which led to a slight loss of early strength after replacing part of the cement. With the extension of the curing age, the calcined coal gangue and limestone powder participated in hydration to gradually develop the strength, and the compressive strength of the cementitious material at 7 and 28 days generally exceeded that of the reference cement. At the age of 7 days, the compressive strength of the cementitious material exceeded the 41 MPa of the reference cement, with the compressive strength of the C2 and C3 sample groups reaching more than 47 MPa. At the late stage of hydration after 28 days, the compressive strength was much higher than that of the reference cement, with the highest being group C2, which reached 67 MPa, an increase of 63.41% compared with the compressive strength of the reference cement. As a reference, Antoni et al. [31] used calcined clay together with limestone powder to replace cement, and the 7-day and 28-day strengths of the cementitious materials prepared under the same conditions as C2 were 40 MPa and 55 MPa, respectively. Although the 28-day compressive strength of C3 was lower compared to C2, it was still higher than that of the reference cement. The cementitious material formulated with calcined coal gangue and limestone powder at the level of 30% cement replacement generally achieved better performance than the reference cement.
As shown in Fig. 5, the compressive strength of the cementitious material formulated with calcined coal gangue and limestone powder at the level of 40% replacement of cement was significantly lower compared to the reference cement after 3 days of hydration. The compressive strength of formulation group B1 was also slightly lower than the reference cement at 7 days of curing age, but the compressive strength of groups B2 and B3 increased. The compressive strengths of groups B1, B2, and B3 were all above 50 MPa at 28 days, reaching a level comparable to or even better than the reference cement. The optimal ratio for these mixes of test conditions was group B3, which had a compressive strength of 54.8 MPa at 28 days. Fig. 3 shows that the cementitious material prepared from calcined coal gangue and limestone powder in suspension also achieved comparable performance to the baseline cement at the level of 40% replacement.
Fig. 6 shows that when the percentage of replacement cement was increased to 50%, the compressive strength of the cementitious material after 3 days of hydration did not show any further decrease. The compressive strengths of A1 at 7 and 28 days of hydration were 38.5 and 42.5 MPa, respectively, which were lower than the reference cement but still achieved a rating of 42.5 MPa. In groups A2 and A3, the performance of the cementitious material was comparable to that of the reference cement, achieving a compressive strength >48.6 MPa at 28 days. Compared with the results of the experiments with 40% cement replacement, the performance of the cementitious material did not decrease significantly despite the increased replacement.
In summary, the cementitious materials prepared by batching calcined coal gangue in suspension and limestone powder could generally obtain comparable or even better performance indices than cement in the range of 30%–50% cement replacement, this method is better than mixing only calcined gangue to replace cement. When the proportion of replacement cement was 40% or more, the compressive strength of this cementitious material system was almost the same or even better than that of cement at 7 and 28 days, whereas the compressive strength at 3 days was significantly lower than that of cement. Various proportions could obtain the ideal performance index, indicating that the cementitious material system has wide applicability.
The results of pore size distributions and pore characteristics of reference cement and C2 samples at 3 days and 28 days are summarized and presented in Fig. 7 and Table 3, respectively. It can be seen that the porosity of both the cement and this cementitious material decreases as the hydration reaction proceeds, which promotes the development of its strength. At 3 days of hydration, the porosity of the C2 sample is larger than that of cement, so its strength is lower than that of the reference cement. At 28 days, with the active silica and alumina in the calcined coal gangue participating in the hydration, its porosity has become smaller than that of cement. At the same time, the mixing of calcined gangue and limestone powder also refines the pore size structure and reduces its average pore diameter.
Figure 7: Pore size distribution
Fig. 8 shows the rate of heat evolution and cumulative heat amount of the reference cement and C2 samples. It can be seen that the hydration exothermic reaction is mainly concentrated in the age of 3 days, and the exothermic peaks of the cement and C2 samples are respectively 3.6 mW/g and 0.0027 mW/g, the first exothermic peak occurred at 9.12 and 8.8 h, respectively. In the early stage of hydration, the mixing of calcined coal gangue and limestone powder had a dilution effect on cement hydration, which eventually leads to a lower exothermic peak and delays its arrival at the peak, so the early strength was lower than that of the reference cement. As hydration proceeds, the rate of heat of hydration of the C2 sample exceeded that of the reference cement, at which time calcined gangue and limestone powder participated in the hydration reaction and gradually promoted the development of strength. It can also be seen from the cumulative heat curve that the total exothermic heat of the two types of cement at 3 days differs greatly, but as the reaction proceeds, the exothermic heat of this cementitious material has approached that of the reference cement, which is consistent with the strength analysis results.
Figure 8: Normalized heat flow and cumulative heat
3.4 Structure and Morphology of Hydration Products
As shown in Fig. 9a, the main crystalline phases in the hydration products of pure cement were ettringite, calcium hydroxide, and C3S, C2S, and C4AF that were not yet hydrated. In contrast, the cementitious material system consisting of calcined coal gangue, limestone powder, and cement showed a distinct CaCO3 diffraction feature, which was introduced by limestone. The main products formed in the early stage of hydration were calcium hydroxide and ettringite. The diffraction peaks of monocarbo-aluminate and hemicarbo-aluminate appeared obviously after 7 days of hydration, while the diffraction peaks of calcium hydroxide and calcium carbonate weakened, indicating that some CaCO3 participated in the hydration reaction to generate carbon aluminate with the active aluminum in calcined coal gangue, thereby increasing the total volume of hydration products. The formation of calcium carbonate stabilizes ettringite and reduces the void fraction of cementitious materials, thus promoting the development of cementitious material strength [32,33]. After 28 days of hydration, the intensity of the diffraction peaks of carbon aluminate in the hydration products of the cementitious material was significantly enhanced compared to 7 days, indicating a continuous increase in the involvement of limestone powder in the hydration, consistent with the study by Antoni et al. [31].
Figure 9: XRD patterns of hydration products of cement and C2 cementitious materials
Fig. 10 shows a comparison of the hydration products of cement and C2 cementitious materials after 3, 7, and 28 days of hydration, while Figs. 11–13 show the results of energy spectrum analysis in the regions A, B, and C in Fig. 7, respectively.
Figure 10: SEM images after hydration for 3, 7, and 28 days
Figure 11: Energy spectrum analysis of area A
Figure 12: Energy spectrum analysis of area B
Figure 13: Energy spectrum analysis of area C
The cement hydration products were denser than C2 cementitious material at 3 days. Both hydration processes produced needle-like ettringite and a large number of flakes-like products from the cementitious material. According to the energy spectrum analysis in Fig. 8, it can be seen that the main elements were Ca, O, etc. Due to the addition of limestone powder, the main element should have been CaCO3.
The structure of the cementitious material was relatively dense after 7 days of hydration, and several lattice-like products were generated, The energy spectrum analysis in Fig. 9 shows that the main elements were Ca, Si, and O, which were judged to be C–S–H gels [34]. The C–S–H gel mainly originated from the cement’s hydration, as well as the secondary hydration reaction of calcined coal gangue with Ca(OH)2. In addition, a small amount of Al was derived from the active Al2O3 in calcined coal gangue.
The microstructure of the cementitious material was denser after 28 days of hydration, The energy spectrum analysis in Fig. 10 shows that its major elements were Ca and O. In addition, the content of C and Al elements has increased, indicating that, in addition to unreacted CaCO3, hydrated carbon aluminate was generated, consistent with the XRD results. The formation of secondary hydration and carbon aluminate increased the content of hydration products in the material, thus increasing its strength.
In this paper, calcined coal gangue and limestone powder are mixed into cement to prepare cementitious materials. Determine the best ratio by strength analysis, and the hydration process and mechanism were explored by combining the pore structure, heat of hydration, chemical composition, phase composition, and microscopic morphological characteristics of the hydration products. The result is as follows:
(1) The cementitious material prepared by calcined coal gangue and limestone powder could generally meet and exceed the performance index of pure cement at the level of 30%–50% replacement. The incorporation of calcined coal gangue and limestone powder could reduce the early strength of the cementitious material, but could significantly improve the mid-and late-stage strength of the cementitious material. The cementitious material prepared by replacing 30% of the cement with a ratio of calcined coal gangue to limestone powder of 2:1 had the best performance, with its 28-day strength reaching 67.5 MPa, which was 1.4 times that of pure cement. If only calcined coal gangue is mixed, its maximum replacement level should not exceed 25%, as the early strength reduction is serious. This study focuses on its compressive strength, and other mechanical properties can be analyzed in the future.
(2) In the early stage of hydration, the addition of calcined coal gangue and limestone powder leads to a decrease in the hydration exothermic peak and delays its arrival at the peak, as hydration continues, the rate of heat of hydration will exceed that of the reference cement, while its exothermic heat amount also gradually approaches that of the reference cement.
(3) The mixing of calcined gangue and limestone powder will refine the pore structure of the cement and reduce its average pore diameter, while its porosity is significantly lower than that of the reference cement at 28 days of hydration.
(4) In the cementitious material system composed of calcined coal gangue, limestone powder, and cement, the early strength was mainly provided by cement. With the gradual participation of calcined coal gangue and limestone powder in the reaction, the structurally dense monocarbo-aluminate and hemicarbo-aluminate were formed, while the secondary hydration of calcined coal gangue and Ca(OH)2 was promoted to generate C–S–H gel, which significantly improved the mechanical properties of the cementitious material.
Funding Statement: This research was funded by the National Natural Science Foundation of China Projects (Grant No. 51672207).
Conflicts of Interest: The authors declare that they have no conflicts of interest to report regarding the present study.
References
1. Wu, R. D., Dai, S. B., Jian, S. W., Huang, J., Tan, H. B. (2021). Utilization of solid waste high-volume calcium coal gangue in autoclaved aerated concrete: Physico-mechanical properties, hydration products and economic costs. Journal of Cleaner Production, 278(3), 123416. DOI 10.1016/j.jclepro.2020.123416. [Google Scholar] [CrossRef]
2. Li, J., Wang, J. (2019). Comprehensive utilization and environmental risks of coal gangue: A review. Journal of Cleaner Production, 239(12–14), 117946. DOI 10.1016/j.jclepro.2019.117946. [Google Scholar] [CrossRef]
3. Peng, B., Li, X. (2018). Release and transformation characteristics of modes of occurrence of chlorine in coal gangue during combustion. Energy & Fuels, 32(9), 9926–9933. DOI 10.1021/acs.energyfuels.8b02019. [Google Scholar] [CrossRef]
4. Zhang, J., Chen, T., Gao, X. (2021). Incorporation of self-ignited coal gangue in steam cured precast concrete. Journal of Cleaner Production, 292, 126004. DOI 10.1016/j.jclepro.2021.126004. [Google Scholar] [CrossRef]
5. Gao, H., Huang, Y., Li, W., Li, J., Ouyang, S. et al. (2021). Explanation of heavy metal pollution in coal mines of china from the perspective of coal gangue geochemical characteristics. Environmental Science and Pollution Research, 28(46), 65363–65373. DOI 10.1007/s11356-021-14766-w. [Google Scholar] [CrossRef]
6. Shekarchi, M., Bonakdar, A., Bakhshi, M., Mirdamadi, A., Mobasher, B. (2010). Transport properties in metakaolin blended concrete. Construction and Building Materials, 24(11), 2217–2223. DOI 10.1016/j.conbuildmat.2010.04.035. [Google Scholar] [CrossRef]
7. Li, D., Song, X., Gong, C., Pan, Z. (2006). Research on cementitious behavior and mechanism of pozzolanic cement with coal gangue. Cement and Concrete Research, 36(9), 1752–1759. DOI 10.1016/j.cemconres.2004.11.004. [Google Scholar] [CrossRef]
8. Lee, S., Moon, H., Hooton, R., Kim, J. (2005). Effect of solution concentrations and replacement levels of metakaolin on the resistance of mortars exposed to magnesium sulfate solutions. Cement and Concrete Research, 35(7), 1314–1323. DOI 10.1016/j.cemconres.2004.10.035. [Google Scholar] [CrossRef]
9. Dong, Q., Liu, D. Y., Peng, W. X. (2006). Effects of environmental and geological hazards of gangue hills and their stability analyses in Chongqing. The Chinese Journal of Geological Hazard and Control, 17, 97–101. [Google Scholar]
10. Cassagnabère, F., Mouret, M., Escadeillas, G., Broilliard, P., Bertrand, A. (2010). Metakaolin, a solution for the precast industry to limit the clinker content in concrete: Mechanical aspects. Construction and Building Materials, 24(7), 1109–1118. DOI 10.1016/j.conbuildmat.2009.12.032. [Google Scholar] [CrossRef]
11. Frías, M., de La Villa, R., Garcia, V., Martínez-Ramírez, R., Fernández-Carrasco, S. et al. (2018). New developments in low clinker cement paste mineralogy. Applied Clay Science, 166, 94–101. DOI 10.1016/j.clay.2018.09.009. [Google Scholar] [CrossRef]
12. Tironi, A., Trezza, M. A., Scian, A. N., Irassar, E. F. (2012). Kaolinitic calcined clays: Factors affecting its performance as pozzolans. Construction and Building Materials, 28(1), 276–281. DOI 10.1016/j.conbuildmat.2011.08.064. [Google Scholar] [CrossRef]
13. Cheng, S., Ge, K., Sun, T., Shui, Z., Chen, X. et al. (2021). Pozzolanic activity of mechanochemically and thermally activated coal-series kaolin in cement-based materials. Construction and Building Materials, 299(6), 123972. DOI 10.1016/j.conbuildmat.2021.123972. [Google Scholar] [CrossRef]
14. Guan, X., Chen, J., Zhu, M., Gao, J. (2021). Performance of microwave-activated coal gangue powder as auxiliary cementitious material. Journal of Materials Research and Technology, 14(7), 2799–27811. DOI 10.1016/j.jmrt.2021.08.106. [Google Scholar] [CrossRef]
15. Zhu, J. P., Zhang, J. W., Zhao, S. H., Zhao, S., Li, D. X. (2012). Influence of calcination temperature on activity of hydration properties of gangue. Proceedings of the Advanced Materials Research, 415, 1466–1469. [Google Scholar]
16. Peng, H., Cui, C., Cai, C. (2014). Research on influence of calcination temperature on metakaolin reactivity and its determination. Bulletin of the Chinese Ceramic Society, 33(8), 2078–2084. [Google Scholar]
17. Dong, L., Liang, X., Song, Q., Gao, G., Song, L. (2017). Study on Al2O3 extraction from activated coal gangue under different calcination atmospheres. Journal of Thermal Science, 26(6), 570–576. DOI 10.1007/s11630-017-0975-y. [Google Scholar] [CrossRef]
18. Zhang, Y., Ling, T. C. (2020). Reactivity activation of waste coal gangue and its impact on the properties of cement-based materials-A review. Construction and Building Materials, 234(1), 117424. DOI 10.1016/j.conbuildmat.2019.117424. [Google Scholar] [CrossRef]
19. Cao, Z., Cao, Y., Dong, H., Zhang, J., Sun, C. (2016). Effect of calcination condition on the microstructure and pozzolanic activity of calcined coal gangue. International Journal of Mineral Processing, 146, 23–28. DOI 10.1016/j.minpro.2015.11.008. [Google Scholar] [CrossRef]
20. Dhandapani, Y., Sakthivel, T., Santhanam, M., Gettu, M., Pillai, R. G. (2018). Mechanical properties and durability performance of concretes with limestone calcined clay cement (LC3). Cement and Concrete Research, 107, 136–151. DOI 10.1016/j.cemconres.2018.02.005. [Google Scholar] [CrossRef]
21. Qin, L., Gao, X. (2019). Properties of coal gangue-Portland cement mixture with carbonation. Fuel, 245(7), 1–12. DOI 10.1016/j.fuel.2019.02.067. [Google Scholar] [CrossRef]
22. Zhao, Y., Qiu, J., Ma, Z., Sun, X. (2021). Eco-friendly treatment of coal gangue for its utilization as supplementary cementitious materials. Journal of Cleaner Production, 285, 124834. DOI 10.1016/j.jclepro.2020.124834. [Google Scholar] [CrossRef]
23. Scrivener, K., Martirena, F., Bishnoi, S., Maity, S. (2018). Calcined clay limestone cements (LC3). Cement and Concrete Research, 114(7), 49–56. DOI 10.1016/j.cemconres.2017.08.017. [Google Scholar] [CrossRef]
24. Maraghechi, H., Avet, F., Wong, H., Kamyab, H., Scrivener, K. (2018). Performance of limestone calcined clay cement (LC3) with various kaolinite contents with respect to chloride transport. Materials and Structures, 51(5), 1–17. DOI 10.1617/s11527-018-1255-3. [Google Scholar] [CrossRef]
25. Avet, F., Scrivener, K. (2018). Investigation of the calcined kaolinite content on the hydration of limestone calcined clay cement (LC3). Cement and Concrete Research, 107, 124–135. DOI 10.1016/j.cemconres.2018.02.016. [Google Scholar] [CrossRef]
26. Liu, Y., Ling, T. C., Wang, M., Wu, Y. Y. (2021). Synergic performance of low-kaolinite calcined coal gangue blended with limestone in cement mortars. Construction and Building Materials, 300(12), 124012. DOI 10.1016/j.conbuildmat.2021.124012. [Google Scholar] [CrossRef]
27. Li, H., Chen, Y., Xu, D. (2005). Preparing kaolin from coal waste by suspension calcining process. Fourth International Conference on Geopolymers, pp. 89–92. Saint-Quentin, France. [Google Scholar]
28. Xu, D. L., Wang, Z. E., Li, H., Song, H. X., Li, H. H. (2007). Study on suspension calcination technology of kaolin from coal measures. Non-Metallic Mines, 2, 45–47. [Google Scholar]
29. Qiu, G., Pang, S. (1989). Spectrophotometric determination of activated aluminium in soil using eriochrome cyanine R. Instrumental Anal, 8(4), 68–71. [Google Scholar]
30. Zhen, J., Zhou, T., Chen, X. (2007). Study on the reactivity and its fast determination method of metakaoline in synthesizing geopolymer. Bulletin of the Chinese Ceramic Society, 26(5), 887–900. [Google Scholar]
31. Antoni, M., Rossen, J., Martirena, F., Scrivener, K. (2012). Cement substitution by a combination of metakaolin and limestone. Cement and Concrete Research, 42(12), 1579–1589. DOI 10.1016/j.cemconres.2012.09.006. [Google Scholar] [CrossRef]
32. Liu, S., Yan, P. (2008). Hydration properties of limestone powder in complex binding material. Journal of the Chinese Ceramic Society, 36(10), 1401–1405. [Google Scholar]
33. Wang, D., Shi, C., Farzadnia, N., Shi, Z., Jia, H. (2018). A review on use of limestone powder in cement-based materials: Mechanism, hydration and microstructures. Construction and Building Materials, 181(6), 659–672. DOI 10.1016/j.conbuildmat.2018.06.075. [Google Scholar] [CrossRef]
34. Huang, Z. Y., Huang, Y. S., Liao, W. Y., Hua, N., Zhou, Y. (2020). Development of limestone calcined clay cement concrete in South China and its bond behavior with steel reinforcement. Journal of Zhejiang University–Science A, 21(11), 892–907. DOI 10.1631/jzus.A2000163. [Google Scholar] [CrossRef]
Cite This Article
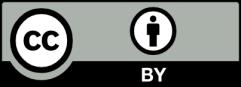
This work is licensed under a Creative Commons Attribution 4.0 International License , which permits unrestricted use, distribution, and reproduction in any medium, provided the original work is properly cited.