Open Access
REVIEW
Workability and Durability of Concrete Incorporating Waste Tire Rubber: A Review
School of Water Conservancy Engineering, Zhengzhou University, Zhengzhou, 450001, China
* Corresponding Author: Juan Wang. Email:
(This article belongs to the Special Issue: Sustainable Concrete with Recyclable Materials)
Journal of Renewable Materials 2023, 11(2), 745-776. https://doi.org/10.32604/jrm.2022.022846
Received 29 March 2022; Accepted 19 May 2022; Issue published 22 September 2022
Abstract
Environmental problems caused by waste tires are becoming increasingly prominent. There is an urgent need to find a green way to dispose of waste tires, and scholars have made considerable efforts in this regard. In the construction industry, rubber extracted from waste tires can be added to concrete to alleviate environmental problems to a certain extent. As a new building material, rubber concrete has superior properties compared to ordinary concrete and has been widely used in many fields. Numerous studies have been conducted worldwide to investigate the effect of waste tire rubber on the performance of concrete. It has been reported that the addition of waste tire rubber has a significant influence on the performance of concrete. Workability influences the hardened performance of rubber concrete, especially the durability. Based on the current research results, the workability and durability of concrete manufactured with waste tire rubber, including water absorption and permeability, carbonation resistance, chloride ion permeability resistance, and freeze-thaw resistance, are summarized in this paper. It is concluded that the addition of waste tires has a negative effect on the workability of concrete. In terms of durability, concrete exhibits better chloride ion penetration resistance and frost resistance, with a higher water absorption rate, and lower anti-permeability and carbonation resistance owing to the addition of waste tire rubber.Keywords
With the rapid development of the automobile industry and transportation, hundreds of millions of waste tires are produced worldwide. Cars bring great convenience to people’s lives, but they also cause a series of ecological and environmental problems including exhaust pollution, noise pollution, and waste tire accumulation. According to statistics, approximately 1 billion useless tires are discarded from motor vehicles every year, with the alarming potential of rising to 1.2 billion by the end of 2030 [1]. The tire manufacturing industry exists worldwide, with more than 160 manufacturers, and is widely distributed in 45 countries [2]. In the early stages, the number of recycled rubber tires in China was very small. The recovery utilization rate was only 5%, which is 3% lower than that in other countries. Most of them are refurbished and used to produce recycled rubber and rubber powder. In addition, some tires accumulate for a long time as degradation is difficult, resulting in the formation of a “black pollution” source. It is well known that waste rubber is a type of polymer material that is difficult to degrade under natural conditions. Therefore, a harmless method for treating waste rubber is urgently required, and it has become a hot topic for researchers. The storage of waste tires is common, causing a serious burden on the ecological environment on which human beings depend for survival. Some of the abandoned waste tires are incinerated, resulting in the production of harmful ingredients, which further aggravates the environmental pollution [3]. Fig. 1 shows the crushed scrap tire. Some of the scrap tires are used as fuel; however, they have no advantages over other fuels. People have long been aware that the production mode, use, and disposal of tires is unsustainable. Therefore, there is an urgent need to find a reasonable recycling method to solve this problem. With the development of environmental protection concept, it is necessary to use waste materials to substitute cement and natural aggregate in concrete. For example, some waste solids can be used to prepare geopolymer to replace the bonding material of cement [4–7]. And then geopolymer can be used to replace cement to fabricate green mortars or concretes [8–11]. Also, it has been previously shown that rubber particles or rubber powder can be used to partially replace the natural aggregate in concrete after recycling waste tires using certain methods. This has become a hot research topic for many scholars [12]. Waste tires can also be used for road and embankment subgrade fillings [13]. Although waste tire rubber offers a great market potential as an alternative material for coarse and fine aggregates of concrete, its disadvantages cannot be ignored because it makes the bond property in the cement matrix poor; this is undoubtedly a major challenge for concrete, which requires relatively high mechanical properties [14]; moreover, the durability may also be affected [15].
Figure 1: Crushed rubber from waste tire. Adapted with permission from reference [1], Copyright © 2018, Elsevier B.V.
Currently, concrete is one of the most important civil engineering materials. Concrete has the characteristics of rich raw materials, a low price, and a simple production process; therefore, it is increasingly being used. However, its production consumes a large amount of natural aggregates every year, with the mining of a large amount of resources resulting in great pressure on natural resources. Waste tire rubber particles can be used as a replacement for sand and stone aggregates in concrete. This yields the advantages of environmental protection, energy saving, and emission reduction. Compared with common concrete, the resulting rubber concrete has good characteristics in terms of deformation performance, crack resistance, energy absorption, and toughness. In addition, rubber concrete is better than ordinary concrete in terms of impact resistance, fatigue cracking resistance, freezing resistance, erosion resistance, noise reduction, and sound insulation.
Many studies have shown that rubber concrete exhibits better ductility, fatigue resistance, and impact resistance than ordinary concrete [16]. Rubber concrete is widely used in various applications such as road engineering, deck pavements, railway sleepers, and airport runways. Research on the application of rubber powder in concrete began in the 1980s. Since then, rubber concrete has been used in more research and engineering applications in Europe and North America. Studies on and applications of this new material began in the late 1990s, and some progress has been made in mechanical performance, durability, and impact resistance. In addition, the effects of rubber material size (rubber powder, rubber fiber, rubber dust), percentage of rubber content (instead of fine and coarse aggregates), and pretreatment of rubber particles with water and NaOH were studied. Concrete structures experience a series of durability problems after 20 to 30 years of use, such as cracking, frostbite, carbonation, and chloride ion erosion [17,18]. The durability of concrete structures has a great influence on their safety, which depends on the durability of concrete materials to a great extent. Therefore, research on the durability of concrete manufactured with waste tire rubber is of great significance.
In summary, the application of waste tire rubber particles in concrete can not only resolve the problem of pollution but also improve the frost resistance and chloride ion permeability of concrete. It is necessary to summarize the related research on the workability and durability of concrete manufactured with waste tire rubber, especially the latest related research results, in order to break new ground in the preparation of green concrete and promote the further application of waste tire rubber in concrete. Therefore, studies on the workability and durability of rubber concrete are summarized in this paper. The review conducted in this study will be of great significance for further research and application of concrete manufactured with waste tire rubber.
2.1 Effect of Rubber Content on Workability
The introduction of tire rubber particles into concrete mixtures adversely affects the workability of the concrete. The influence can be attributed to two effects of rubber particles on concrete. One is water absorption, rubber particles porous, can absorb free water, reduce slump. The other is the effect of air entraining, rubber particles can increase the content of gas inside concrete, improve liquidity [19–24]. Table 1 shows the slump of RC with varying RA size and content. When the rubber admixture reaches 40% of the total volume, the slump is reduced by 185 mm [19]. As shown in Fig. 2, when no fly ash is added, the rubber content increases from 0% to 25%, and the slump flow decreases from 700 to 525 mm. However, when the rubber content is fixed, the increase in fly ash content leads to an increase in the slump. The negative impact of waste rubber particles on the fluidity of concrete can be attributed to their lower unit weight, which is lower than that of natural aggregates (sand). The uneven surface of the particles increases the friction between the mixture and the particles, resulting in a higher coefficient of friction [22,25]. The slump was reduced by 120 mm when 30% of the weight of the fine aggregates was replaced with waste rubber powder [26]. At the highest replacement rate (25%), the slump increased with an increase in fly ash content. The addition of fly ash improves the workability of the self-compacting rubber concrete. Fly ash particles are spheres that flow with low friction, resulting in good flowability [27]. Dahmardeh et al. [22] found that glass particles can slightly improve the ease of self-compacting concrete; however, the improvement is small. The replacement of sand with 30% rubber resulted in a slump reduction of approximately 125 mm, which was 80% of that of the control group [23]. The rubber surface contains impurities, such as dust, which take up part of the free water in the mixing process [24,28].
Figure 2: Slump flow with different contents of crump rubber and fly ash. Adapted with permission from reference [20], Copyright © 2010, Springer
As shown in Fig. 3, the slump and unit weight of rubber powder concrete decrease with an increase in the rubber content [21]. Further addition of silica fume with a filling effect increased the unit mass [29]. Gesoglu et al. [30] observed a similar trend. In addition, they concluded that the addition of silica fume decreased the compatibility as well as the rubber particles, regardless of whether the water–cement ratio was 0.4 or 0.6. The results of Choudary et al. [31] also showed the same trend as above in the case of rubber functional gradient concrete. Khalid et al. [32] first combined recycled concrete fine aggregates and fine rubber particles to replace sand. The former was at a 60% replacement rate, and the latter at a 1.5% replacement rate. This group of specimens showed the smallest slump values, which decreased by approximately 21% compared with the control group without the addition of recycled concrete fine aggregate with rubber fines. Because the surface of the recycled concrete fine aggregate is rough and uneven, when its substitution rate increases to 60%, more friction naturally occurs between the particles in the fine aggregate, which reduces the slump of the concrete. In the fresh state, the workability tends to remain constant or increase as the amount of rubber increases [33].
Figure 3: Slump and unit weight with different crump rubber content. Adapted with permission from reference [21], Copyright © 2008, Elsevier B.V.
As shown in Fig. 4, in addition to rubber, Steyn et al. [36] investigated the effects of plastic and glass on the workability of concrete. In Fig. 4, RAC represents rubber aggregate concrete; PAC represents plastic aggregate concrete, and GAC represents glass aggregate concrete. The results show that plastic and glass can also reduce the workability of concrete, however the reduction is not as much as that of rubber. Ramdani et al. [37] reported that the simultaneous incorporation of rubber aggregates and glass powder was beneficial for the workability. Because the glass powder fills the voids between the particles, water can be released from the voids, and a new pore structure is formed. The unit weight of geopolymer concrete with added light expanded clay (75% replacement of coarse aggregate) was 17% lower than that of the control group without the light expanded clay [27]. Othman et al. [38] investigated the effects of eggshell powder on the rheological properties of concrete. As shown in Fig. 5, the effect of eggshell powder on the slump was not as great as that of tire powder. In the case of no eggshell powder, the slump value at 5% rubber powder replacement rate decreased by approximately 13%. However, when the eggshell powder replacement rate was 15%, the slump value was 0 with an increase in rubber content.
Figure 4: Influence waste aggregate have on concrete slump. Adapted with permission from reference [36], Copyright © 2021, Elsevier B.V.
Figure 5: Slump of rubber concrete with different contents of eggshell. Adapted with permission from reference [38], Copyright © 2021, Elsevier B.V.
Other studies have arrived at the opposite conclusion that the workability increased with the increase in rubber content [29,39–41]. As can be seen from Fig. 6, the workability of the mixture receiving rubber crumbs (A) and the mixture coated with rubber crumbs (C) increased by approximately 17% and 22%, respectively compared to the control at the 15% substitution level (R); however, the addition of silica fume (C + SF) reduced the slump substantially by 56% to 78%. Youssf et al. [27] found that when silica fume was used as a substitute for slag, compatibility was reduced by up to 65%. In a study by Nagarajin et al. [29], silica fume similarly reduced the compatibility of concrete, both treated and untreated with modified clay, and the untreated concrete had better compatibility than the treated one because the use of modified clay changed the rubber material from hydrophobic to hydrophilic. The slump values of steel pipe concrete increased by 11, 25, and 45 mm over the reference group at substitution rates of 10%, 20%, and 30%, respectively, and the effect became more pronounced with higher content [40]. Tummala et al. [42] used M-sand and rubber powder as raw materials in a 20% admixture. Workability increased from 120 mm for the reference group to 142 mm, an increase of approximately 18%. With the addition of steel fibers, the workability of geopolymer concrete decreased, which is contrary to the trend of a surge with increasing rubber content [43]. Alsaif et al. [24] believed that steel fibers are more prone to agglomeration and are therefore detrimental to compatibility. For long hollow blocks and bricks, the slump increased linearly with increasing rubber content from 20% to 40%, with a maximum increase of 476% [44].
Figure 6: Slump of rubber concrete with different admixtures. Adapted with permission from reference [39], Copyright © 2014, Elsevier B.V.
The presence of rubber improved the workability of the composite binder ground polymer mortar, but the effect was not significant. The mixes with the highest rubber content (30%) had an average 5% higher flow diameter over the reference group mixes, and the mixes with a lower rubber content (20%) had an average 8% higher flow diameter over the reference group mixes [35]. The workability of light-rubber concrete with ordinary silicate cement was not as good as that of light-rubber concrete with geopolymers, with the former being approximately 56% lower than the latter. This is because the latter matrix requires little water, and the water glass in it acts as a lubricant, thus increasing the flowability of the geopolymer concrete [27]. The effect of a high-efficiency water-reducing agent on concrete and the ease of concrete was particularly obvious in the 1.0% water-reducing agent admixture, where the slump increased by approximately 183% compared with the control group without a water-reducing agent [45]. This finding was also supported by Mendis et al. [46]. The workability improved with the addition of admixtures, regardless of a high rubber dust content (40%) or similar content (30% and 40%). However, in the study conducted by Moustafa et al. [23], slump values fluctuated slightly at 150 mm when the proportion of the efficient water-reducing agent was changed. When the content of rubber particles does not exceed 40%, the mixing of slag powder and rubber particles results in the composite-modified self-compacting concrete having a better compatibility than the standard self-compacting concrete [47]. When rubber replaced 20% of the sand of geopolymer concrete, the compatibility was improved by 9%. By combining rubber with light expanded clay aggregates, the compatibility was improved by approximately 31% [27]. Hunag et al. [48] also believed that light aggregates could improve slump.
2.2 Effect of Rubber Particle Size and Treatment Process on Workability
The workability of rubber concrete with a large particle size is also high [6,34]. As shown in Fig. 7, the slumps of rubber particles with a particle size of 3 mm (CRA) were 6 and 8 mm, which are larger than those with particle sizes of 0.5 mm (CRB) and 0.3 mm (CRC). However, it was approximately 17% lower than that in the control (REF). The smaller the rubber particles, the more likely they are to absorb water, probably because the presence of the alkali exciter increases the surface roughness of the rubber particles [35]. At low rubber admixtures, the slump of concrete with 5–10 mm rubber particles was larger than that of 2–5 mm, but as the admixture increased to 40%, the slump of the coarser-grained self-compacting rubber concrete was approximately 50 mm lower than that of the finer group, as can be seen from Fig. 8. Youssf et al. [49] found that the slump values decreased by approximately 33% and 14% when using 40 mesh and 30 mesh rubber powder, respectively, instead of sand. However, the slump values when using 1–3 mm and 2–5 mm rubber powder increased by approximately 33% and 43%, respectively, compared to the control group without rubber powder. This indicates that the coarser rubber particles are superior to the interstitial rubber particles in terms of compatibility because the surface area of the coarse rubber particles is relatively small, increasing the moisture content of the concrete mix. However, the slump value for rubber particle size 2.36–4.75 mm was approximately 75% and 50% higher than those for particle sizes 1.18–2.36 mm and 0.3–1.18 mm, respectively (12.5% replacement of sand) [33]. Although the addition of crumb rubber (CR) and powder rubber (PR) both adversely affect the workability, the effect of PR is not as significant as that of CR [50].
Figure 7: Slump of all the mixes adapted with permission from reference [34], Copyright © 2015, Elsevier B.V.
Figure 8: Slump flow. Adapted with permission from reference [6], Copyright © 2019, American Society of Civil Engineers
In addition, the rubber grinding process affects the workability. At the same replacement rate (10%), the crash rate obtained by mechanically ground tire aggregates was approximately 6 mm lower than that obtained by replacing natural tire aggregates produced by cryogenic technology. This is because mechanically ground fine tire aggregates have a higher specific surface area and roughness [51]. The different orders of mixing methods also affect compatibility [49], such as when rubber is added to water from the beginning of the mix as against when it is added and then mixed dry or wet with other materials. The slump value of rubber concrete treated with a 50% NaOH solution was approximately 15% higher than that under a 10% concentration treatment. Gracia et al. [33] found that the compatibility under all three surface treatments, hydration, oxidation sulfonation, and hydrogen peroxide, was not as good as that of untreated concrete. The slumps of rubber concrete modified by SBL and EA were 300% and 33% higher than those of the reference rubber concrete and reference concrete, respectively [28].
3.1 Water Absorption and Water Permeability
Numerous studies have shown that rubber concrete exhibits a higher water absorption rate than ordinary concrete [3,45,48,52,53]. Table 2 presents the water absorption and water permeability of RC with varying RA size and content. This is because of the presence of open pores and capillaries in rubber granular concrete that can easily absorb water; thus, the water absorption capacity of rubber concrete is higher [48,54]. Previous studies have found that the water absorption of rubber fibers is similar to that of fine and coarse aggregates, with a difference of only 0.1% [55]. The depth of water permeability of concrete after adding 10% rubber granules (1–4 mm) increased by approximately 56% compared to normal concrete without rubber [45]. This may be due to the coarser gradation of rubber grains than that of pure sand, which affects the pore structure of concrete and provides a path for water to move inside the concrete [45]. Although the water absorption of rubber particles is weaker than that of sand, the water absorption of geopolymer rubber concrete is increased by 34% owing to the fact that the use of rubber results in a large number of voids in the concrete matrix because of the poor adhesion between the other pastes and rubber and hence the higher water absorption [27,53]. Youssf et al. [27] tested the effect of lightweight expanded clay aggregate (LECA) on the water absorption of geopolymer concrete. When combined with rubber, the respective effects were fully exploited, and the water absorption rate increased by 93%. Silva et al. [56] found no significant change in the water absorption of paving stones after replacing sand with tire rubber. The average water absorption of the concrete paving blocks prepared in this manner was below 6%.
In general, as the rubber content increases, the water absorption of concrete increases [54,57–59]. A rubber replacement rate of 5.5% resulted in a water absorption rate that was 68% higher than that of the control group. The fine nature of rubber powder leads to the creation of internal cracks and voids with an increase in porosity [59]. This was confirmed by Turatsinze et al. [60]. Additionally, the treatment of rubber concrete in acidic or alkaline solutions affects its water absorption. As shown in Fig. 9, for water and NaOH solutions at both 15% and 30% contents, concrete treated with NaOH solution always absorbs more water than that treated with water, and both are higher than the control value of 6.96% [53]. The bonding of the surface of the rubber granules with the cement paste was improved after treatment with NaOH solution, the porosity of the interfacial region with the cement matrix was reduced, and the microstructure of the concrete was improved [45]. Marques et al. [61] found no significant reduction in the water absorption of rubber concrete treated with aqueous NaOH solution. The water absorption of rubber concrete treated with a calcium hydroxide solution was reduced by 11% and increased again after treatment with an acetic acid solution. Acid and alkali treatments can hydrolyze some components into water-soluble anions, reducing the number of polar components and decreasing the absorption value [62]. When the rubber content is too high (40% replacement rate), too many pores lead to water leakage, and the permeability cannot be measured accurately [48].
Figure 9: Water absorption of all the specimens. Adapted with permission from reference [53], Copyright © 2019, Elsevier B.V
Some studies have concluded that an increased rubber content can inhibit water absorption [26,63]. As shown in Fig. 10, when the content of rubber powder was 10% of the weight of fine aggregate, the water absorption of rubber concrete was reduced by approximately 29% compared to normal concrete, and the water resistance was improved. In the study by Youssf et al. [58], the rubber content increased from 0% to 10%, and the water absorption decreased from 3.1 to 3.0. The porosity of the mixture decreased, and the water absorption was weakened owing to the filling effect of the rubber particles.
Figure 10: Influence of rubber powder content on water absorption. Adapted with permission from references [26,58], Copyright © 2017, Elsevier B.V.
As shown in Fig. 11, compared to the sample without recycled tire crumb (RTC), the water absorption at all three times decreased as the RTC increased from 10% to 30%, and the water absorption increased with time. The hydrophobic properties of rubber may explain this phenomenon [63]. Rubber reduced the permeability coefficient of pervious concrete, and when fine-grained rubber-modified pervious concrete was used, the permeability coefficient decreased by 18% when the admixture amount was increased to 8% because the porosity was reduced [64]. This observation was confirmed by Gesoglu et al. [65], who found that rubber granules with a particle size of 4 mm reduced the permeability coefficient by 45% and 68% at replacement ratios of 10% and 20%, respectively. In the studies by Zhang et al. [66] and Rezaifar et al. [67], a moderate amount of rubber content improved the water resistance, and above a certain level, the impermeability deteriorated. Si et al. [68] found that the water resistance was the best when the rubber content was 35%.
Figure 11: Water absorption after immersion into water vs. rubber content. Adapted with permission from reference [63], Copyright © 2017, Elsevier B.V.
In addition, as the rubber particle size increased, the water absorption of concrete also gradually increased, and the impermeability was weakened [66]. Su et al. [34] found that the permeability of rubber concrete with a diameter of 3 mm was approximately 170% higher than that of rubber concrete with diameters of 0.3 and 0.5 mm. Small rubber particles (1 mm) had a greater effect on the agglomerate pore space than large rubber particles (4 mm) [65]. Girskas et al. [54] believed that the finer the rubber particles, the higher is the water absorption value. Liu et al. [64] considered that a change in the rubber particle size had little effect on the permeability coefficient of permeable concrete. For plastic concrete, it is difficult for rubber particles to play a role in its permeability, and the water–cement ratio has a greater effect on it [69]. However, some scholars have observed different trends. Thomas et al. [70,71] found that the water absorption rate of rubber dust particles of three different sizes first decreased and then increased, as shown in Fig. 12 When the rubber dust content was less than 7.5%, it exhibited good water resistance. Similarly, Wang et al. [72] observed the same trend when rubber waste with different particle sizes was mixed with foam concrete. When the waste rubber content exceeded 3%, the water resistance deteriorated. The reason for this decrease is that rubber dust particles of a smaller size can fill the pore structure inside the rubber concrete.
Figure 12: Water absorption with different rubber particle sizes. Adapted with permission from reference [71], Copyright © 2016, Elsevier B.V.
The depth of water permeability of rubber concrete (at 10% substitution) at water-reducer dosages of 0.75% and 1.0% was significantly lower than that of the reference group without a water reduced by approximately 48% and 58%, respectively, and the initial surface absorption rate of concrete in the first 10 min was significantly higher at any substitution level of the water reducer compared to that of the unadulterated rubber control group [45]. Pham et al. [53] found that an increase in rubber aggregates would lead to an increase in the surface absorption rate, regardless of whether water treatment or NaOH solution treatment was used. This phenomenon is related to the theory of particle accumulation and the pore structure. The water absorption rate of rubber treated with 25% NaOH was reduced by 41% [68]. Marques et al. [61] found that the difference in the water absorption of mortar between NaOH-treated and untreated rubber was only 1%. As shown in Fig. 13, the longer the exposure time of the specimen, the higher the water absorption value [4].
Figure 13: Water absorption of acid attacked specimens. Adapted with permission from reference [4], Copyright © 2016, Elsevier B.V.
In addition, the water–cement ratio affects the impermeability. With three water–cement ratios, the water absorption of the combination of rubber ash and rubber fibers was lower than that of rubber ash replacing part of the fine aggregate, which improved the permeability of concrete [57]. At a constant amount of sand replaced by rubber fibers (25%), the water–cement ratio was reduced to 0.35 from 0.55, with a 19.6% improvement in the permeability depth [52]. Gesoglu et al. [73] found that the amount of fly ash admixture also affects the water absorption capacity of concrete. The addition of silica fume increased the water absorption of geopolymer lightweight rubber concrete by 86% [27]. The replacement of cement with silica fume reduced the water immersion depth of concrete [52].
The carbonation resistance of concrete is an important durability indicator. Carbonation is mainly the reaction of alkaline substances in cement and CO2 in the air, which reduces the alkaline nature of concrete and destroys the structure. Many studies have reported that rubber concrete is less resistant to carbonation. Table 3 shows the carbonation resistance of RC with varying RA size and content. Luhar et al. [74] studied the carbonation depth of geopolymer concrete and ordinary concrete, which was higher than the initial value under three levels of rubber content (10%, 20%, 30%) and seven exposure times (14, 21, 28, 35, 42, 49, 56 days). Notably, in ordinary concrete, when the rubber content exceeds 10%, the carbonation depth shows a decreasing trend but still does not fall below the initial value. As shown in Fig. 14, the addition of rubber strips reduces the carbonation resistance of concrete, whereas the addition of silica fume significantly improves the carbonation resistance of concrete [75]. Xie et al. [76] found that the addition of rubber and silica fume reduced the carbonation depth in steel fiber concrete production.
Figure 14: Carbonation depth of rubber shreds concrete. Adapted with permission from reference [75], Copyright © 2020, John Wiley & Sons, Inc.
Many scholars have found that the addition of rubber to concrete reduces its carbonation resistance. Because the void volume between the rubber aggregate and cement paste increases, the carbonation depth of the matrix increases, and the carbonation resistance deteriorates after the addition of rubber sand [77]. When 15% of the natural coarse aggregate was replaced with rubber, the carbonation depth reached its peak, and it increased by approximately 46% on the 91st day [51]. Mohd Nasir et al. [45] studied the influence of water reducer content on the carbonation capacity of concrete and found that when rubber powder was substituted for fine aggregates, NaOH and water-treated rubber had a significant influence on the carbonation depth of lightweight concrete, as shown by the increase in water reducer content. As shown in Fig. 15, the average carbonation depth of the 30% NaOH-pretreated and 30% water-treated rubber specimens increased by 329% and 414%, respectively, compared to the control group at 28 days. The average carbonation depth of the rubber concrete treated with water was higher than that of the rubber concrete treated with the same amount of NaOH, regardless of the exposure time of 14 days or 28 days [53]. Pham et al. [53] found that the correlation coefficient between the carbonation depth of lightweight rubber concrete and the rubber content was high; the higher the rubber content, the deeper the carbonation depth. Yu et al. [78] investigated the effect of three different rubber particle sizes on the carbonation resistance of concrete, and the results showed that the resistance to carbonation decreases with increasing rubber content at any particle size.
Figure 15: Depths of carbonation after 14 and 28 days of CO2 exposure. Adapted with permission from reference [53], Copyright © 2019, Elsevier B.V.
Some researchers have found that rubber concrete has a better ability to resist the carbonation energy. In geopolymer concrete with rubber particles replacing 20% of the volume of sand, the carbonation depth was reduced by 17.2% compared to the geopolymer concrete without rubber; however, replacing 75% of the volume of stone with light expanded clay would increase the carbonation depth of geopolymer rubber concrete because the volume of light expanded clay is larger than that of concrete stone [27]. When using tire rubber powder with a 5% replacement ratio as a sand filler, the amount of eggshell powder replacing cement was increased from 0% to 15%, and the carbonation depth decreased by 40%, indicating that eggshell powder has a better filling effect than cement to stop the deep penetration of CO2 [81]. However, other scholars have presented opposite views [74,80,82]. Similarly, the carbonation resistance of self-compacting rubber concrete is better than that of ordinary concrete. As presented in Fig. 16, the carbonation depth of self-compacting concrete at various exposure durations increases with increasing rubber content. Thus, it is suitable for outdoor reinforced concrete structures but is not recommended for marine structures [80]. After testing a section of a gravel rubber concrete bridge deck in Tianjin, China, Zhu et al. [82] concluded that the carbonation resistance is also better than that of ordinary concrete. Another study considered that, because the acid resistance band of the sample is not an obvious boundary line, its carbonation resistance depth cannot be measured accurately and effectively, and a variety of methods should be proposed to evaluate this performance [78].
Figure 16: Depths of carbonation for different exposure periods. Adapted with permission from reference [80], Copyright © 2021, John Wiley & Sons, Inc.
Thomas et al. [70] found that in the case of a water–cement ratio of 0.3, when the content of rubber scraps was 2.5%–12.5%, the carbonation depth was smaller than the control. The reason for this decrease may be that the rubber scraps were not as large as the replaced fine aggregate; however, the carbonation depth gradually increased and was higher than that of the control group. A similar trend of an initially decreasing and subsequently increasing depth is shown in Fig. 17. The carbonation depth of the concrete decreased by 2 mm when the rubber addition was less than 20% and the exposure time was 24 h. The carbonation depth of concrete increased by 2 mm when the amount of rubber added exceeded 20% until 60%, and then the carbonation depth increased to 11.3 mm, because the porosity was low when the amount of rubber added was small and high when the amount of rubber added was large [83]. The carbonation depth of geopolymer light rubber concrete increased significantly with increasing slag content, and then decreased with increasing slag content because the addition of slag reduced the volume of pores permeated by CO2 [27].
Figure 17: Carbonation depth after 24 h in the chamber. Adapted with permission from reference [83], Copyright © 2020, IOP Publishing
Some researchers have found that, as the rubber particle size increases, the carbonation depth increases [51,71]. Yu et al. [78] found that the carbonation resistance of rubber concrete with a 60–80 mesh size was better than that of specimens made with a 30–40 mesh size and 2–4 mm particle size, for the same exposure time and rubber content. This further expounds that the empty joint inside rubber concrete is equivalent to providing a smoother channel for CO2 to enter the interior. Conversely, if the pores in the concrete are fewer and closer to each other, the carbonation depth will be correspondingly smaller. The carbonation depth of concrete increases with an increase in the rubber replacement rate, and the depth at 91 and 28 days is greater than that on the 7th day, which indicates that the carbonation depth increases with age [51]. Scholars have found that the carbonation resistance of concrete improves when the water–cement ratio is relatively low. Gupta et al. [55] studied the carbonation depth of concrete when the water–cement ratio was 0.35, 0.45, and 0.55, and found that when the rubber ash content was 5%, the carbonation depth at the water–cement ratio of 0.55 was deeper than that at the water–cement ratio of 0.35. Similarly, the minimum carbonation depth of cement mortar with recycled tire rubber fibers added at a 0.56 water–cement ratio was reduced by approximately 1/3; however, the carbonation resistance of the mortar with the water–cement ratio of 0.51 progressively worsened with the incorporation of rubber fibers, as shown in Fig. 18 [84]. The carbonation depth of rubber cement concrete with a high water–cement ratio (0.5) was larger than that of rubber cement concrete with a low water–cement ratio (0.4). The reason for the reduced carbonation resistance of the rubber cement concrete with a high water–cement ratio may be the increase in the internal pore size of the concrete with the increasing of water–cement ratio. The carbonation performance of the concrete is affected by a lot of factors, including carbonation time and rubber doping, which are also related to the size of the rubber particle.
Figure 18: Carbonation depth of mortar with W/C = 0.51 and W/C = 0.56. Adapted with permission from reference [84], Copyright © 2019, Elsevier B.V.
3.3 Chloride Ion Permeability Resistance
In marine environments, the durability of road and bridge concrete is severely affected by chloride erosion. Therefore, tests on the chloride permeability resistance of rubber concrete play a very important role in its application. The presence of rubber inhibits chloride ion migration. Table 4 describes the chloride ion permeability of RC with varying RA size and content. Han et al. [85] found that the incorporation of waste rubber was effective in reducing the chloride ion diffusion coefficient, using an electric acceleration method with ultrasonic detection. The chloride ion diffusion coefficient at a 20% replacement rate of rubber for sand was reduced by approximately 26% compared to the reference group, which effectively alleviated the corrosion of the reinforcing steel. The same conclusion was obtained using rubber powder with particle sizes ranging from 0.15 mm to 1.9 mm mixed with rubber fibers of width 2–5 mm and length 20 mm, with a decrease in the chloride ion diffusion coefficient of approximately 22% (25% substitution rate) [86].
The difference in the chloride diffusion coefficient between using a fixed content of rubber ash (10%) in combination with rubber fibers and rubber ash alone was not significant [55]. The total charge of the samples was also measured, and it was concluded that the total charge of rubber concrete was low at any level of high-efficiency water-reducing agent admixture, which indicated that the water-reducing agent had little effect on chloride ion penetration, and the key influencing factor was still rubber [45]. The total charge of rubber concrete without a water reducer was only 1/4 of the total charge of ordinary concrete, as shown in Fig. 19. This is attributed to the fact that the resistance of rubber reduces the current of the internal microporous connection [3]. In a study by Onuaguluchi et al. [39], rubber powder was pretreated with limestone powder, and by measuring the resistivity of the concrete surface, it was found that the difference in charge between coated and uncoated limestone powder was not significant, but the charge decreased substantially with the addition of silica fume. Although the addition of rubber leads to a decline in the mechanical properties, the chloride penetration resistance has been recognized by many scholars to be enhanced. Rubber concrete can be used in important situations where the mechanical properties required are not very high, but an improved chloride ion penetration resistance is necessary [87]. Si et al. [68] found that the presence of rubber degrades the total volume of permeable pores, thereby reducing the chloride ion absorption capacity.
Figure 19: Chloride penetration resistance of concretes. Adapted with permission from reference [45], Copyright © 2021, Informa UK Limited
However, in the study of Li et al. [90], the chloride ion diffusion coefficient was found to increase with an increase in the rubber substitution rate because the existence of cracks reduced the chloride ion penetration resistance. Alsaif et al. [25] also found that the penetration depth of chloride ions increased constantly. The penetration depth of chloride ions would be deeper under the condition of a dry-wet cycle, but lower than that of chloride ions in saturated concrete, because chloride ions would be absorbed by capillary attraction in saturated concrete. Han et al. [85] demonstrated the migration mechanism of a chloride ion using a molecular dynamics model, which was bound to the rubber chain without forming a chemical bond on the rubber surface. The process of chloride ions entering concrete is a combination of diffusion and absorption [25].
The water–cement ratio is also an important factor affecting chloride ion penetration. As shown in Fig. 20, the effective chloride ion diffusion coefficient was reduced by 57% at a water–cement ratio of 0.50 with a rubber substitution ratio of 10%. For a water–cement ratio of 0.35, the increase in rubber content does not have a significant effect on the effective chloride ion diffusion coefficient. Even at the maximum substitution ratio (20%), the effective chloride ion diffusion coefficient was only 22% lower than that of the control group. The comparison shows that a smaller water–ash ratio has a better effect on the inhibition of chloride ion penetration, and the extension of the duration of the wet maintenance period can alleviate the degree of chloride ion penetration [30]. Gupta et al. [55] studied three water–cement ratios of 0.35, 0.45, and 0.55, and found that the chloride ion diffusion coefficient at the water–cement ratio of 0.55 was significantly higher than that of the concrete at the lower water–cement ratios, whether rubber ash was used alone or in combination with rubber fiber. An appropriate amount of silica fume can improve the resistance to chloride ion migration; even if the rubber content is high, the effect of silica fume can be observed [30,39,88]. The ultrafine particle size of silica fume can provide a good filling effect. The gap between the cement slurry and aggregate particles can be filled with silica fume, and the microstructure becomes denser.
Figure 20: Effective chloride ion diffusion coefficients of rubberized concrete. Adapted with permission from reference [88], Copyright © 2015, Open Academic Journals Index
As shown in Fig. 21, the addition of fly ash also affected the amount of charge transferred by the self-compacting rubber concrete. The specimens with a curing age of 90 days had a stronger resistance to chloride ion erosion than those with a curing age of 28 days. Bravo et al. [51] also arrived at similar conclusions: the chloride ion permeability after curing for 91 days was lower than that after curing for 28 days. This phenomenon is attributed to the fact that the long-term reaction of fly ash in the mixture makes the pore structure of concrete denser, which makes it difficult for chloride ions to enter, resulting in a very low chloride ion permeability rate.
Figure 21: Charge passed with different rubber contents. Adapted with permission from reference [73], Copyright © 2011, Elsevier B.V.
The addition of rubber with a specific content range can help concrete resist chloride ion penetration [3,70]. As presented in Fig. 22, the depth of chloride ion penetration was reduced by 2 mm after the specimen was immersed in an NaCl solution for 28 days, where the rubber admixture was less than 7.5%. This reduction was due to the impermeability and non-absorbency of the rubber particles, which did not allow the passage of chloride ions. Some studies attributed the decrease to the uncertain test error during the production of concrete specimens, resulting in a lower chloride ion diffusion [51]. The subsequent increase in dosage also gradually increased the penetration depth, which finally exceeded that of the control group. This increase was due to the lack of filler inside the concrete, which created opportunities for chloride penetration. The penetration depth of the specimen increased with increasing soaking time (salt solution with a constant rubber content) [70]. For water–cement ratios of 0.4, 0.45, and 0.5, the depth of chloride ion penetration decreased and then increased with the rubber content [3].
Figure 22: Depth of chloride penetration with different rubber contents. Adapted with permission from reference [70], Copyright © 2015, Elsevier B.V.
Zhu et al. [89] studied the chloride ion attack resistance of rubber powder concrete at different temperatures and found that the concrete structure was less susceptible to chloride ion attacks at temperatures below 20°C. At five admixtures of 5%, 10%, 15%, 20%, and 30%, the chloride diffusion coefficients of rubber concrete modified by the silane coupling agent and carboxylated butadiene rubber were all lower than those of untreated concrete by 32.3%, 35.2%, 15.6%, 14.2%, and 13.9%, respectively, because the polymer modifier made the microstructure denser and made it more difficult for chloride ions to penetrate [90]. Liu et al. [91] found that the pretreatment of rubber powder with six modifiers could achieve good durability after replacing 20% of fly ash.
When rubber concrete contains a considerable amount of water, the building structure undergoes freezing and melting cycles or even damage. Therefore, it is particularly important to study the freezing resistance of rubber concrete for its application in a low-temperature environment. The incorporation of rubber improves the freeze-thaw resistance of concrete [68,91,92]. Table 5 shows the freeze-thaw resistance of RC with varying RA size and content. The total and effective porosity of concrete increases with the addition of rubber, thereby improving the freeze-thaw resistance of concrete products. The mass of fine aggregates replaced by waste rubber powder was increased from 0% to 30%, and the mass loss rate was reduced by 77.8% and 90.5% at 25 and 50 sub-cycles, respectively [26]. In the study by Gonen et al. [92], the abrasive effect was further enhanced by adding 3% NaCl to the pool, in addition to the freezing and dissolution cycles of the specimens in water. As shown in Fig. 23, even with a small rubber content (0.5%), the decrease in the mass loss was significant, almost 1/3. When the tire addition rate was 4%, the mass loss was reduced by 82% on average.
Figure 23: Lost weight with different rubber contents. Adapted with permission from reference [92], Copyright © 2018, Elsevier B.V.
The higher the rubber admixture, the better the freeze-thaw resistance of pervious concrete [64,93]. In geopolymer concrete, the rubber admixture increased from 0% to 20% under the effect of 25 freeze-thaw cycles, the relative dynamic modulus (RDM) of elasticity increased by 125%, and the mass loss decreased by 71.7%. However, the amount of fly ash replaced by slag increased from 0% to 70%, with a 70.2% decrease in the RDM of elasticity, a 413% increase in mass loss, and very poor frost resistance [94]. The freeze-thaw resistance was improved by 89.2% and 27.5% when the rubber powder was blended at 20 wt% and the rubber powder particle sizes were 2–4 mm and 4–6 mm, respectively [54]. The incorporation of tire rubber particles enhanced the freeze-thaw cycle resistance of the two concrete levels [95].
In contrast, a rubber content that is too high negatively affects freezing resistance. When the replacement level exceeds a certain level (5% of the total admixture), the improvement in freeze-thaw resistance is not significant [91]. As shown in Fig. 24, the change in RDM is not exaggerated when the rubber content in the concrete is below 25%. The reason for the increase in the RDM of elasticity during the first 246 cycles is that the stiffness of the rubber aggregate was small, and its immediate addition reduced the stiffness of the concrete mixer and reduced the extent to which it changed as the rubber aggregate admixture changed. Several scholars have proposed solutions for the rubber overload problem. Alsaif et al. [99] added a mixture of artificial and recycled tire steel fibers to rubber concrete to enhance its freeze-thaw resistance, greatly reducing the negative impact of a large amount of rubber on freeze-thaw resistance. Luo et al. [100] found that the effect of steel fibers on the mass loss rate was opposite to that on the relative dynamic elastic modulus, with a positive effect on the mass loss rate (decreasing with the increase in steel fiber content) and a negative effect on the relative dynamic elastic modulus. Nehdi et al. [95] found that the addition of recycled tire steel wire offset the negative impact of rubber particles on the mechanical properties of two-stage concrete and improved the freeze-thaw resistance because the addition of recycled tire steel wire inhibited the development of cracks during the freeze-thaw cycle.
Figure 24: Relative dynamic modulus after different freeze-thaw cycles. Adapted with permission from reference [68], Copyright © 2017, Elsevier B.V.
The freeze-thaw resistance also increases with a decrease in the rubber particle size [64,93,101]. The rate of compressive strength loss caused by the addition of fine rubber particles to pervious concrete is lower than that of coarse rubber particle concrete, as shown in Fig. 25 [64]. After 300 freeze-thaw cycles, the mass loss rate of the fine rubber crumb was found to be lower than that of the slightly coarser tire crumbs and rubber crumbs concrete at both 10% and 20% substitution ratios. The large specific surface area of smaller rubber particles creates more micropores inside the concrete, which provides sufficient room for expansion of the cement paste during freezing [93]. Richardson et al. [102] tested the mass loss of rubber concrete with five different particle sizes, and found that the mass loss of specimens with rubber particle sizes <0.5 mm was the smallest under 70 freeze-thaw cycles, and was consistently lower than 2250.0 g. Small rubber particles entrain more air, which provides freeze-thaw protection. For the 0.50% and 1% rubber admixtures, the mass loss of the sample with a maximum particle size of 1 mm was greater than that of the sample with a maximum particle size of 2 mm [92].
Figure 25: Compressive strength loss ratio under freeze-thaw cycles. Adapted with permission from reference [64], Copyright © 2018, MDPI (Basel, Switzerland)
Rubber granules treated with NaOH have better freeze-thaw resistance [68,94]. As can be seen from Fig. 24, the rubber concrete pretreated with NaOH of 95%–98% purity has an overall smaller RDM than both normal concrete and untreated rubber concrete in the range of 15%–50% of admixture, which indicates that the use of NaOH pretreatment can enhance the adhesion between rubber and cement paste and prevent the extension of internal microcracks [68]. In addition, Pham et al. [103] compared mortar made of styrene-butadiene-type copolymer-coated rubber aggregates with ordinary mortar and rubber mortar not treated with copolymers and found that the mass loss, mechanical properties, durability factors, and other related indices were better than those of the two control groups. This advantage makes rubber mortar more durable under frost conditions. It is suggested that rubber concrete can be used as road concrete for cold weather and even freezing areas, and that rubber mortar can be maintained in seawater with high-strength cement and sulfate-resistant cement to resist seawater erosion [104].
Bhavani et al. [97] modified geopolymer concrete with a 5% replacement of fly ash mass by natural zeolite combined with rubber powder (5% replacement of fine aggregate weight). The weight loss of the modified geopolymer concrete specimens after freeze-thaw cycles was 1.00%, and the weight loss of the control geopolymer concrete without natural zeolite and rubber was 1.44%. Nano-SiO2 and silanized rubber can improve the microstructure of concrete [105]. As shown in Fig. 26a, the hydration products of the control concrete were not only porous but also loose in structure, with a large number of C-H crystals owing to insufficient hydration of the cement. After adding 0.5% nano-SiO2, as shown in Fig. 26b, the compactness of the concrete was significantly higher than that of the control, with fewer lamellar crystals and pores. The microstructure of the concrete after the addition of 5% silanized rubber is shown in Fig. 26c, and the adhesion between the particles and concrete is enhanced. The microstructure of the concrete containing 5% silanized rubber and 3% nano-silica is shown in Fig. 26d. There were no larger pores and voids in the structure and almost no cracks on the boundary, which were the closest to each other, and the hydration products were evenly distributed.
Figure 26: Microstructure of concrete modified with nano-SiO2 and silanized rubber. Adapted with permission from reference [105], Copyright © 2021, MDPI (Basel, Switzerland)
Gum powder can be used as an air-entraining agent [98,105]. The difference in the dynamic modulus of elasticity under 200 freeze-thaw cycles is not significant when adding air-entraining agents alone compared to adding powder of three particle sizes alone, proving that adding powder does not provide better freeze-thaw resistance compared to adding air-entraining agents [98]. The dynamic modulus of elasticity under the second freeze-thaw cycle is not significantly different, which proves that the addition of powder does not yield better freeze-thaw resistance compared to the addition of air-entraining agents. When the air content was 4%, the best freeze-thaw performance was obtained for concrete with rubber aggregate and SiO2 [105]. PP (polypropylene) fibers can be replaced by recycled tire polymer fibers (RTPF), which does not damage the pumpability, but improves the freeze-thaw resistance [106].
As shown in Fig. 27, the compressive strength loss rates of the waste rubber powder group, waste rubber powder and silica fume compound groups, and silica fume only group were lower than those of the control group at different numbers of freeze-thaw cycles. This shows that the waste rubber powder, silica fume, and the waste rubber powder and silica fume compound modification all improved the frost resistance of the concrete. Although the improvement effect of compounding waste rubber powder and silica fume was better than that of rubber powder alone, it was not as good as that of silica fume. The composite effect is not the superposition of the properties of the two materials because the effects of waste rubber powder and silica fume on the mechanical properties are different [96].
Figure 27: Compressive strength loss rate after 50 freeze-thaw cycles. Adapted with permission from reference [96], Copyright © 2021
The coefficient of freezing expansion of rubber concrete appears in three different stages with an increase in the number of freeze-thaw cycles. The stage of decline was less than 100 cycles, the plateau stage was between 100 and 200 cycles, and the stage of increase was after 200 cycles [107]. The reason for the initial decline is that when the interface between the rubber powder and cement matrix is damaged by freeze-thaw, the porosity is higher and the bond is poor, which attracts a large amount of water to the gap between the rubber and cement interface. The slight change in the plateau is due to the fact that rubber is an elastomer [95], which can relieve ice crystallization pressure to a certain extent. The reason for the increase is that some of the water in the interstice of the freezing stage must return to the pores during thawing. Grinys et al. [101] studied the durability of styrene butadiene rubber (SBR) emulsion-modified concrete, where the freeze-thaw durability coefficient calculated using various parameters of concrete porosity can be conveniently used to predict the freeze-thaw resistance and durability of concrete. Some studies have suggested that multiple indices should be considered when evaluating the frost resistance of concrete [98].
4 Environmental Protection for Usage of Waste Tire Rubber in Concrete
With the deepening of the concept for green development, the reuse of waste materials has been paid more and more attention. In addition to that waste tire rubber can be used in concrete, municipal garbage, waste fiber and other solid wastes can also be used in the preparation of concrete [108]. The reuse of waste rubber tire can not only solve the pollution caused by its long-term storage to the environment, but also accord with the concept of green development. Waste tire rubber is mainly processed into three forms: pellet, powder and fiber [109]. Waste tire rubber can not only replace coarse aggregate and fine aggregate in concrete, but also replace cementite material or be used as admixture. In addition, rubber particles can also be pretreated by certain chemical and physical methods to achieve the required application effect and meet the requirements of engineering [110]. Addition of rubber can improve the sound absorption and heat insulation performance of concrete [111]. When the railway trains pass through the tunnels at high speed, and heavy trucks and tractors run on the roads, as well as flying helicopters and operating substations, there will be serious noise [112]. The damping coefficient measured in rubber concrete is higher than that of ordinary concrete, because the acoustic vibration is immediately suppressed and the sound quickly becomes smaller and absorbed when noise is generated [113]. Therefore, rubber concrete can be made into sound absorbing panels, which can be installed in residential areas or workplaces being affected by noise [114]. In addition, compared to the traditional aggregate, rubber has a lower thermal conductivity, so it has better thermal insulation performance [115].
Rubber concrete has achieved promising results as a new green building material. This study summarizes the workability and durability of rubber concrete and draws the following conclusions:
(1) The poor workability of rubber concrete is attributed to the lighter weight of the rubber particles and the larger friction between them and the mixture. In contrast, the hydrophobic properties of the rubber particles can improve the workability of concrete. In addition to the rubber content, the rubber particle size and rubber grinding process both affect the workability of the rubber. Coarse rubber has a better effect on improving the workability of concrete.
(2) The water absorption rate of rubber concrete is higher than that of ordinary concrete because holes and capillaries exist in rubber granular concrete that can easily absorb water. As the rubber content increases, the absorption rate of the concrete and permeability also increase gradually. With an increase in the rubber particle size, the impermeability of concrete decreases. The water–cement ratio is also an important factor that affects the impermeability of concrete.
(3) The carbonation resistance of rubber concrete is poor; however, it is better under certain special conditions. The reason for the decrease in the carbonation resistance of rubber concrete with a high water–cement ratio may be that the internal pore size of the concrete increases with an increase in the water–cement ratio. Under the same exposure time and rubber content, the carbonation resistance of the fine particle size rubber concrete is better than that of the coarse particle size rubber concrete.
(4) Rubber can inhibit the migration of chloride ions. Rubber particles are impermeable to water and do not absorb water, indicating that they do not allow the passage of chloride ions. Chloride ions are bound to the rubber chain. The wetting and drying cycles result in a deeper chloride penetration. Prolonging the wetting curing period can alleviate the penetration of chloride ions.
(5) The total porosity and effective porosity of concrete increase with the addition of rubber, which improves the freeze-thaw resistance of concrete products. A high rubber content can negatively affect freezing resistance, but it can be improved by adding fiber. Rubber particles treated with NaOH exhibit better freeze-thaw resistance.
Funding Statement: This study was supported by the financial support received from Program for Innovative Research Team (in Science and Technology) in University of Henan Province of China (Grant No. 20IRTSTHN009), National Natural Science Foundation of China (Grant Nos. U2040224, 52179145), and Natural Science Foundation of Henan (Grant Nos. 212300410018, 222300420081).
Conflicts of Interest: The authors declare that they have no conflicts of interest to report regarding the present study.
References
1. Sofi, A. (2018). Effect of waste tyre rubber on mechanical and durability properties of concrete–A review. Ain Shams Engineering Journal, 9(4), 2691–2700. DOI 10.1016/j.asej.2017.08.007. [Google Scholar] [CrossRef]
2. Kara De Maeijer, P., Craeye, B., Blom, J., Bervoets, L. (2021). Crumb rubber in concrete—The barriers for application in the construction industry. Infrastructures, 6(8), 116. DOI 10.3390/infrastructures6080116. [Google Scholar] [CrossRef]
3. Thomas, B. S., Gupta, R. C., Panicker, V. J. (2016). Recycling of waste tire rubber as aggregate in concrete: Durability-related performance. Journal of Cleaner Production, 112, 504–513. DOI 10.1016/j.jclepro.2015.08.046. [Google Scholar] [CrossRef]
4. Gao, Z., Zhang, P., Wang, J., Wang, K., Zhang, T. (2022). Interfacial properties of geopolymer mortar and concrete substrate: Effect of polyvinyl alcohol fiber and nano-SiO2 contents. Construction and Building Materials, 315, 125735. DOI 10.1016/j.conbuildmat.2021.125735. [Google Scholar] [CrossRef]
5. Liu, C., Huang, X., Wu, Y., Deng, X., Liu, J. et al. (2020). Review on the research progress of cement-based and geopolymer materials modified by graphene and graphene oxide. Nanotechnology Reveiws, 9(1), 155–169. DOI 10.1515/ntrev-2020-0014. [Google Scholar] [CrossRef]
6. Zhang, P., Kang, L., Zheng, Y., Zhang, T., Zhang, B. (2022). Influence of SiO2/Na2O molar ratio on mechanical properties and durability of metakaolin-fly ash blend alkali-activated sustainable mortar incorporating manufactured sand. Journal of Materials Research and Technology, 18, 3553–3563. DOI 10.1016/j.jmrt.2022.04.041. [Google Scholar] [CrossRef]
7. Zhang, X., Zhang, P., Wang, T., Zheng, Y., Qiu, L. et al. (2022). Compressive strength and anti-chloride ion penetration assessment of geopolymer mortar merging PVA fiber and nano-SiO2 using RBF–BP composite neural network. Nanotechnology Reviews, 11(1), 1181–1192. DOI 10.1515/ntrev-2022-0069. [Google Scholar] [CrossRef]
8. Wang, X., Zhang, C., Zhu, H., Wu, Q. (2022). Reaction kinetics and mechanical properties of a mineral-micropowder/metakaolin-based geopolymer. Ceramics International, 48(10), 14173–14181. DOI 10.1016/j.ceramint.2022.01.304. [Google Scholar] [CrossRef]
9. Zhang, P., Wang, K., Wang, J., Guo, J., Ling, Y. (2021). Macroscopic and microscopic analyses on mechanical performance of metakaolin/flyash based geopolymer mortar. Journal of Cleaner Production, 294, 5126193. [Google Scholar]
10. Xu, Z., Huang, Z., Liu, C., Deng, H., Deng, X. et al. (2021). Research progress on key problems of nanomaterials-modified geopolymer concrete. Nanotechnology Reviews, 10(1), 779–792. DOI 10.1515/ntrev-2021-0056. [Google Scholar] [CrossRef]
11. Zhang, P., Wang, K., Wang, J., Guo, J., Hu, S. et al. (2020). Mechanical properties and prediction of fracture parameters of geopolymer/alkali-activated mortar modified with PVA fiber and nano-SiO2. Ceramics International, 46(12), 20027–20037. DOI 10.1016/j.ceramint.2020.05.074. [Google Scholar] [CrossRef]
12. Assaggaf, R., Maslehuddin, M., Al-Osta, M. A., Al-Dulaijan, S. U., Ahmad, S. (2022). Properties and sustainability of treated crumb rubber concrete. Journal of Building Engineering, 51, 104250. DOI 10.1016/j.jobe.2022.104250. [Google Scholar] [CrossRef]
13. Roychand, R., Gravina, R. J., Zhuge, Y., Ma, X., Youssf, O. et al. (2020). A comprehensive review on the mechanical properties of waste tire rubber concrete. Construction and Building Materials, 237, 117651. DOI 10.1016/j.conbuildmat.2019.117651. [Google Scholar] [CrossRef]
14. Eldin, N. N., Senouci, A. B. (1993). Rubber-tire particles as concrete aggregate. Journal of Materials in Civil Engineering, 5(4). DOI 10.1061/(ASCE)0899-1561(1993)5:4(478). [Google Scholar] [CrossRef]
15. Wang, L., Guo, F., Yang, H., Wang, Y. (2021). Comparison of fly ash, PVA fiber, MgO and shrinkage-reducing admixture on the frost resistance of face slab concrete via pore structural and fractal analysis. Fractals, 29(2), 2140002. DOI 10.1142/S0218348X21400028. [Google Scholar] [CrossRef]
16. Xiao, F. P., Zhao, W. B., Amirkhanian, S. N. (2009). Fatigue behavior of rubberized asphalt concrete mixtures containing warm asphalt additives. Construction and Building Materials, 23(10), 3144–3151. DOI 10.1016/j.conbuildmat.2009.06.036. [Google Scholar] [CrossRef]
17. Wang, L., Lu, X., Liu, L., Xiao, J., Zhang, G. et al. (2022). Influence of MgO on the hydration and shrinkage behavior of low heat portland cement-based materials via pore structural and fractal analysis. Fractals, 6(1), 40. [Google Scholar]
18. Wang, L., Luo, R., Zhang, W., Jin, M., Tang, S. (2021). Effects of fineness and content of phosphorus slag on cement hydration, permeability, pore structure and fractal dimension of concrete. Fractals, 29(2), 2140004. DOI 10.1142/S0218348X21400041. [Google Scholar] [CrossRef]
19. Gregori, A., Castoro, C. (2021). Modelling mechanical properties and bond behaviour of rubbercrete. Construction and Building Materials, 305, 124735. DOI 10.1016/j.conbuildmat.2021.124735. [Google Scholar] [CrossRef]
20. Güneyisi, E. (2009). Fresh properties of self-compacting rubberized concrete incorporated with fly ash. Materials and Structures, 43(8), 1037–1048. DOI 10.1617/s11527-009-9564-1. [Google Scholar] [CrossRef]
21. Batayneh, M. K., Marie, I., Asi, I. (2008). Promoting the use of crumb rubber concrete in developing countries. Waste Management, 28(11), 2171–2176. DOI 10.1016/j.wasman.2007.09.035. [Google Scholar] [CrossRef]
22. Dahmardeh, S. R., Moghaddam, M. S. S., Moghaddam, M. H. M. (2019). Effects of waste glass and rubber on the SCC: Rheological, mechanical, and durability properties. European Journal of Environmental and Civil Engineering, 25(2), 302–321. DOI 10.1080/19648189.2018.1528891. [Google Scholar] [CrossRef]
23. Moustafa, A., ElGawady, M. A. (2015). Mechanical properties of high strength concrete with scrap tire rubber. Construction and Building Materials, 93, 249–256. DOI 10.1016/j.conbuildmat.2015.05.115. [Google Scholar] [CrossRef]
24. Alsaif, A., Koutas, L., Bernal, S. A., Guadagnini, M., Pilakoutas, K. (2018). Mechanical performance of steel fibre reinforced rubberised concrete for flexible concrete pavements. Construction and Building Materials, 172, 533–543. DOI 10.1016/j.conbuildmat.2018.04.010. [Google Scholar] [CrossRef]
25. Alsaif, A., Bernal, S. A., Guadagnini, M., Pilakoutas, K. (2018). Durability of steel fibre reinforced rubberised concrete exposed to chlorides. Construction and Building Materials, 188, 130–142. DOI 10.1016/j.conbuildmat.2018.08.122. [Google Scholar] [CrossRef]
26. Liu, M. L., Zhang, G. D., Ding, Y. F., Wei, L., Wang, Y. et al. (2016). Research on properties of the concrete with waste rubber powder. Materials Science Forum, 852, 1443–1449. DOI 10.4028/www.scientific.net/MSF.852.1443. [Google Scholar] [CrossRef]
27. Youssf, O., Elchalakani, M., Hassanli, R., Roychand, R., Zhuge, Y. et al. (2022). Mechanical performance and durability of geopolymer lightweight rubber concrete. Journal of Building Engineering, 45, 103608. DOI 10.1016/j.jobe.2021.103608. [Google Scholar] [CrossRef]
28. Chen, Z., Li, L., Xiong, Z. (2019). Investigation on the interfacial behaviour between the rubber-cement matrix of the rubberized concrete. Journal of Cleaner Production, 209, 1354–1364. DOI 10.1016/j.jclepro.2018.10.305. [Google Scholar] [CrossRef]
29. Nagarajan, C., Shanmugasundaram, P. (2021). Effect of modified clay treated crumb rubber and silica fume on the properties of concrete. Structure Concrete, 1–13. DOI 10.1002/suco.202100085. [Google Scholar] [CrossRef]
30. Gesoğlu, M., Güneyisi, E. (2007). Strength development and chloride penetration in rubberized concretes with and without silica fume. Materials and Structures, 40(9), 953–964. DOI 10.1617/s11527-007-9279-0. [Google Scholar] [CrossRef]
31. Choudhary, S., Jain, A., Chaudhary, S., Gupta, R. (2021). Development of functionally graded concrete using rubber fiber. Materials Science Forum, 1019, 62–72. DOI 10.4028/www.scientific.net/MSF.1019.62. [Google Scholar] [CrossRef]
32. Khalid, F. S., Saaidin, S. H., Shahidan, S., Othman, N. H., Irwan, J. M. et al. (2020). Performance of concrete containing fine recycled concrete aggregate (FRCA) and fine crumb rubber (FCA) as partial sand replacement. Materials Science and Engineering, 917, 012017. [Google Scholar]
33. García, E., Villa, B., Pradena, M., Urbano, B., Campos-Requena, V. H. et al. (2021). Experimental evaluation of cement mortars with end-of-life tyres exposed to different surface treatments. Crystals, 11(5), 552. DOI 10.3390/cryst11050552. [Google Scholar] [CrossRef]
34. Su, H. L., Yang, J., Ling, T. C., Ghataora, G. S., Dirar, S. (2015). Properties of concrete prepared with waste tyre rubber particles of uniform and varying sizes. Journal of Cleaner Production, 91, 288–296. DOI 10.1016/j.jclepro.2014.12.022. [Google Scholar] [CrossRef]
35. Abdelmonim, A., Bompa, D. V. (2021). Mechanical and fresh properties of multi-binder geopolymer mortars incorporating recycled rubber particles. Infrastructures, 6, 146. DOI 10.3390/infrastructures6100146. [Google Scholar] [CrossRef]
36. Steyn, Z. C., Babafemi, A. J., Fataar, H., Combrinck, R. (2021). Concrete containing waste recycled glass, plastic and rubber as sand replacement. Construction and Building Materials, 269, 121242. DOI 10.1016/j.conbuildmat.2020.121242. [Google Scholar] [CrossRef]
37. Ramdani, S., Guettala, A., Benmalek, M. L., Aguiar, J. B. (2019). Physical and mechanical performance of concrete made with waste rubber aggregate, glass powder and silica sand powder. Journal of Building Engineering, 21, 302–311. DOI 10.1016/j.jobe.2018.11.003. [Google Scholar] [CrossRef]
38. Othman, R., Chong, B. W., Jaya, R. P., Mohd Hasan, M. R., Al Bakri Abdullah, M. M. et al. (2021). Evaluation on the rheological and mechanical properties of concrete incorporating eggshell with tire powder. Journal of Materials Research and Technology, 14, 439–451. DOI 10.1016/j.jmrt.2021.06.078. [Google Scholar] [CrossRef]
39. Onuaguluchi, O., Panesar, D. K. (2014). Hardened properties of concrete mixtures containing pre-coated crumb rubber and silica fume. Journal of Cleaner Production, 82, 125–131. DOI 10.1016/j.jclepro.2014.06.068. [Google Scholar] [CrossRef]
40. Abendeh, R., Ahmad, H. S., Hunaiti, Y. M. (2016). Experimental studies on the behavior of concrete-filled steel tubes incorporating crumb rubber. Journal of Constructional Steel Research, 122, 251–260. DOI 10.1016/j.jcsr.2016.03.022. [Google Scholar] [CrossRef]
41. Lakusic, S. (2017). Flexural fatigue performance and mechanical properties of rubberized concrete. Journal of the Croatian Association of Civil Engineering, 69(11), 983–990. DOI 10.14256/JCE. [Google Scholar] [CrossRef]
42. Tummala, S., Raj, P. S., Satyanarayana, G. V. V., Sriharshavarma, M., Kosaraju, S. et al. (2020). Investigation on workability of M20 grade concrete with partial replacement of crumb rubber and M sand for fine aggregates and fly ash for cement. E3S Web of Conferences, 184(2), 01098. [Google Scholar]
43. Yeluri, S. C., Yadav, N. (2020). Mechanical properties of rubber aggregates based geopolymer concrete–A review. Materials Science and Engineering, 989, 012014. [Google Scholar]
44. Sodupe-Ortega, E., Fraile-Garcia, E., Ferreiro-Cabello, J., Sanz-Garcia, A. (2016). Evaluation of crumb rubber as aggregate for automated manufacturing of rubberized long hollow blocks and bricks. Construction and Building Materials, 106, 305–316. DOI 10.1016/j.conbuildmat.2015.12.131. [Google Scholar] [CrossRef]
45. Nasir, M., Abu Bakar, N. A., Safiee, N., Abdul Aziz, F. N. A. (2021). Permeation-durability properties of metakaolin blended concrete containing rubber. European Journal of Environmental and Civil Engineering, 1–16. [Google Scholar]
46. Mendis, A. S. M., Al-Deen, S., Ashraf, M. (2017). Behaviour of similar strength crumbed rubber concrete (CRC) mixes with different mix proportions. Construction and Building Materials, 137, 354–366. DOI 10.1016/j.conbuildmat.2017.01.125. [Google Scholar] [CrossRef]
47. Yang, S., Qi, B., Ai, Z., Cao, Z., He, S. et al. (2022). Mechanical properties and microcosmic properties of self-compacting concrete modified by compound admixtures. Journal of Renewable Materials, 10(4), 897–908. DOI 10.32604/jrm.2022.016653. [Google Scholar] [CrossRef]
48. Hunag, L. J., Wang, H. Y., Wu, Y. W. (2016). Properties of the mechanical in controlled low-strength rubber lightweight aggregate concrete (CLSRLC). Construction and Building Materials, 112, 1054–1058. DOI 10.1016/j.conbuildmat.2016.03.016. [Google Scholar] [CrossRef]
49. Youssf, O., Mills, J. E., Benn, T., Zhuge, Y., Ma, X. et al. (2020). Development of crumb rubber concrete for practical application in the residential construction sector–design and processing. Construction and Building Materials, 260, 119813. DOI 10.1016/j.conbuildmat.2020.119813. [Google Scholar] [CrossRef]
50. Ismail, M. K., Sherir, M. A. A., Siad, H., Hassan, A. A. A., Lachemi, M. (2018). Properties of self-consolidating engineered cementitious composite modified with rubber. Journal of Materials in Civil Engineering, 30(4), 04018031. DOI 10.1061/(ASCE)MT.1943-5533.0002219. [Google Scholar] [CrossRef]
51. Bravo, M., de Brito, J. (2012). Concrete made with used tyre aggregate: Durability-related performance. Journal of Cleaner Production, 25, 42–50. DOI 10.1016/j.jclepro.2011.11.066. [Google Scholar] [CrossRef]
52. Gupta, T., Chaudhary, S., Sharma, R. K. (2016). Mechanical and durability properties of waste rubber fiber concrete with and without silica fume. Journal of Cleaner Production, 112, 702–711. DOI 10.1016/j.jclepro.2015.07.081. [Google Scholar] [CrossRef]
53. Pham, T. M., Elchalakani, M., Hao, H., Lai, J., Ameduri, S. et al. (2019). Durability characteristics of lightweight rubberized concrete. Construction and Building Materials, 224, 584–599. DOI 10.1016/j.conbuildmat.2019.07.048. [Google Scholar] [CrossRef]
54. Girskas, G., Nagrockienė, D. (2017). Crushed rubber waste impact of concrete basic properties. Construction and Building Materials, 140, 36–42. DOI 10.1016/j.conbuildmat.2017.02.107. [Google Scholar] [CrossRef]
55. Gupta, T., Chaudhary, S., Sharma, R. K. (2014). Assessment of mechanical and durability properties of concrete containing waste rubber tire as fine aggregate. Construction and Building Materials, 73, 562–574. DOI 10.1016/j.conbuildmat.2014.09.102. [Google Scholar] [CrossRef]
56. Silva, F. M., Gachet Barbosa, L. A., Lintz, R. C. C., Jacintho, A. E. P. G. A. (2015). Investigation on the properties of concrete tactile paving blocks made with recycled tire rubber. Construction and Building Materials, 91, 71–79. DOI 10.1016/j.conbuildmat.2015.05.027. [Google Scholar] [CrossRef]
57. Ganjian, E., Khorami, M., Maghsoudi, A. A. (2009). Scrap-tyre-rubber replacement for aggregate and filler in concrete. Construction and Building Materials, 23(5), 1828–1836. DOI 10.1016/j.conbuildmat.2008.09.020. [Google Scholar] [CrossRef]
58. Youssf, O., Hassanli, R., Mills, J. E. (2017). Mechanical performance of FRP-confined and unconfined crumb rubber concrete containing high rubber content. Journal of Building Engineering, 11, 115–126. DOI 10.1016/j.jobe.2017.04.011. [Google Scholar] [CrossRef]
59. Bisht, K., Ramana, P. V. (2017). Evaluation of mechanical and durability properties of crumb rubber concrete. Construction and Building Materials, 155, 811–817. DOI 10.1016/j.conbuildmat.2017.08.131. [Google Scholar] [CrossRef]
60. Turatsinze, A., Garros, M. (2008). On the modulus of elasticity and strain capacity of self-compacting concrete incorporating rubber aggregates. Resources, Conservation and Recycling, 52(10), 1209–1215. DOI 10.1016/j.resconrec.2008.06.012. [Google Scholar] [CrossRef]
61. Marques, A. C., Akasaki, J. L., Trigo, A. P. M., Marques, M. L. (2008). Influence of the surface treatment of tire rubber residues added in mortars. Revista Ibracon de Estruturas e Materials, 1, 113–120. DOI 10.1590/S1983-41952008000200001. [Google Scholar] [CrossRef]
62. Muñoz-Sánchez, B., Arévalo-Caballero, M. J., Pacheco-Menor, M. C. (2016). Influence of acetic acid and calcium hydroxide treatments of rubber waste on the properties of rubberized mortars. Materials and Structures, 50, 75. DOI 10.1617/s11527-016-0912-7. [Google Scholar] [CrossRef]
63. Kashani, A., Ngo, T. D., Mendis, P., Black, J. R., Hajimohammadi, A. (2017). A sustainable application of recycled tyre crumbs as insulator in lightweight cellular concrete. Journal of Cleaner Production, 149, 925–935. DOI 10.1016/j.jclepro.2017.02.154. [Google Scholar] [CrossRef]
64. Liu, H., Luo, G., Gong, Y., Wei, H. (2018). Mechanical properties, permeability, and freeze–thaw resistance of pervious concrete modified by waste crumb rubbers. Applied Sciences, 8(10), 1843. DOI 10.3390/app8101843. [Google Scholar] [CrossRef]
65. Gesoğlu, M., Güneyisi, E., Khoshnaw, G., İpek, S. (2014). Investigating properties of pervious concretes containing waste tire rubbers. Construction and Building Materials, 63, 206–213. DOI 10.1016/j.conbuildmat.2014.04.046. [Google Scholar] [CrossRef]
66. Zhang, Y. M., Chen, S. X., Chen, B., Sun, W. (2006). Dry shrinkage, frost resistance and permeability of rubber included concrete. Key Engineering Materials, 302–303, 120–124. DOI 10.4028/www.scientific.net/KEM.302-303.120. [Google Scholar] [CrossRef]
67. Rezaifar, O., Hasanzadeh, M., Gholhaki, M. (2016). Concrete made with hybrid blends of crumb rubber and metakaolin: Optimization using response surface method. Construction and Building Materials, 123, 59–68. DOI 10.1016/j.conbuildmat.2016.06.047. [Google Scholar] [CrossRef]
68. Si, R., Guo, S., Dai, Q. (2017). Durability performance of rubberized mortar and concrete with NaOH-solution treated rubber particles. Construction and Building Materials, 153, 496–505. DOI 10.1016/j.conbuildmat.2017.07.085. [Google Scholar] [CrossRef]
69. Cheng, S. Z., Xu, S. J., Cong, R., Wang, K. L. (2012). Experimental study on mix design of plastic concrete with lower elastic modulus and higher impervious coefficient. Advanced Materials Research, 535–537, 1936–1939. DOI 10.4028/www.scientific.net/AMR.535-537.1936. [Google Scholar] [CrossRef]
70. Thomas, B. S., Gupta, R. C., Mehra, P., Kumar, S. (2015). Performance of high strength rubberized concrete in aggressive environment. Construction and Building Materials, 83, 320–326. DOI 10.1016/j.conbuildmat.2015.03.012. [Google Scholar] [CrossRef]
71. Thomas, B. S., Chandra Gupta, R. (2016). Properties of high strength concrete containing scrap tire rubber. Journal of Cleaner Production, 113, 86–92. DOI 10.1016/j.jclepro.2015.11.019. [Google Scholar] [CrossRef]
72. Wang, R., Gao, P., Tian, M., Dai, Y. (2019). Experimental study on mechanical and waterproof performance of lightweight foamed concrete mixed with crumb rubber. Construction and Building Materials, 209, 655–664. DOI 10.1016/j.conbuildmat.2019.03.157. [Google Scholar] [CrossRef]
73. Gesoğlu, M., Güneyisi, E. (2011). Permeability properties of self-compacting rubberized concretes. Construction and Building Materials, 25(8), 3319–3326. DOI 10.1016/j.conbuildmat.2011.03.021. [Google Scholar] [CrossRef]
74. Luhar, S., Luhar, I., Nicolaides, D., Gupta, R. (2021). Durability performance evaluation of rubberized geopolymer concrete. Sustainability, 13(11), 5969. DOI 10.3390/su13115969. [Google Scholar] [CrossRef]
75. Gupta, T., Siddique, S., Sharma, R. K., Chaudhary, S. (2020). Effect of aggressive environment on durability of concrete containing fibrous rubber shreds and silica fume. Structural Concrete, 22(5), 2611–2623. DOI 10.1002/suco.202000043. [Google Scholar] [CrossRef]
76. Xie, J., Fang, C., Lu, Z., Li, Z., Li, L. (2018). Effects of the addition of silica fume and rubber particles on the compressive behaviour of recycled aggregate concrete with steel fibres. Journal of Cleaner Production, 197, 656–667. DOI 10.1016/j.jclepro.2018.06.237. [Google Scholar] [CrossRef]
77. Rashad, A. M. (2016). A comprehensive overview about recycling rubber as fine aggregate replacement in traditional cementitious materials. International Journal of Sustainable Built Environment, 5(1), 46–82. DOI 10.1016/j.ijsbe.2015.11.003. [Google Scholar] [CrossRef]
78. Yu, Q., Wang, J. (2014). Experimental study on carbonation resistance of waste rubber concrete. Advanced Materials Research, 1065–1069, 1766–1769. DOI 10.4028/www.scientific.net/AMR.1065-1069.1766. [Google Scholar] [CrossRef]
79. Dong, M., Elchalakani, M., Karrech, A., Yang, B. (2021). Strength and durability of geopolymer concrete with high volume rubber replacement. Construction ang Building Materials, 274, 121783. DOI 10.1016/j.conbuildmat.2020.121783. [Google Scholar] [CrossRef]
80. Mallek, J., Daoud, A., Omikrine-Metalssi, O., Loulizi, A. (2021). Performance of self-compacting rubberized concrete against carbonation and chloride penetration. Structural Concrete, 22(5), 2720–2735. DOI 10.1002/suco.202000687. [Google Scholar] [CrossRef]
81. Wei, C. B., Othman, R., Jaya, R. P., Doh, S. I., Li, X. F. et al. (2021). Properties of concrete with eggshell powder and tyre rubber crumb. Key Engineering Materials, 879, 34–48. DOI 10.4028/www.scientific.net/KEM.879.34. [Google Scholar] [CrossRef]
82. Zhu, H., Duan, F., Shao, J. W., Shi, W., Lin, Z. (2021). Material and durability study of a 10-year-old crumb rubber concrete bridge deck in Tianjin, China. Magazine of Concrete Research, 73(10), 499–511. DOI 10.1680/jmacr.19.00238. [Google Scholar] [CrossRef]
83. Vilches, J., Figueroa, J., Chamorro, L., Pina, C. (2020). Analysis of the carbonation in normal concrete with the addition of tire rubber aggregate. Environmental Earth Sciences, 503, 012069. [Google Scholar]
84. Gheni, A. A., Alghazali, H. H., ElGawady, M. A., Myers, J. J., Feys, D. (2019). Durability properties of cleaner cement mortar with by-products of tire recycling. Journal of Cleaner Production, 213, 1135–1146. DOI 10.1016/j.jclepro.2018.12.260. [Google Scholar] [CrossRef]
85. Han, Q., Wang, N., Zhang, J., Yu, J., Hou, D. et al. (2021). Experimental and computational study on chloride ion transport and corrosion inhibition mechanism of rubber concrete. Construction and Building Materials, 268, 121105. DOI 10.1016/j.conbuildmat.2020.121105. [Google Scholar] [CrossRef]
86. Gupta, T., Siddique, S., Sharma, R. K., Chaudhary, S. (2019). Behaviour of waste rubber powder and hybrid rubber concrete in aggressive environment. Construction and Building Materials, 217, 283–291. DOI 10.1016/j.conbuildmat.2019.05.080. [Google Scholar] [CrossRef]
87. Oikonomou, N., Mavridou, S. (2009). Improvement of chloride ion penetration resistance in cement mortars modified with rubber from worn automobile tires. Cement and Concrete Composites, 31(6), 403–407. DOI 10.1016/j.cemconcomp.2009.04.004. [Google Scholar] [CrossRef]
88. Noor, N. M., Hamada, H., Sagawa, Y., Yamamoto, D. (2015). Effect of crumb rubber on concrete strength and chloride ion penetration resistance. Jurnal Teknologi, 77(32), 171–178. [Google Scholar]
89. Zhu, H., Liang, J., Xu, J., Bo, M., Li, J. et al. (2018). Research on anti-chloride ion penetration property of crumb rubber concrete at different ambient temperatures. Construction and Building Materials, 189, 42–53. DOI 10.1016/j.conbuildmat.2018.08.193. [Google Scholar] [CrossRef]
90. Li, G., Wang, Z., Leung, C. K. Y., Tang, S., Pan, J. et al. (2016). Properties of rubberized concrete modified by using silane coupling agent and carboxylated SBR. Journal of Cleaner Production, 112, 797–807. DOI 10.1016/j.jclepro.2015.06.099. [Google Scholar] [CrossRef]
91. Liu, H. B., Wang, X., Jiao, Y., Sha, T. (2016). Experimental investigation of the mechanical and durability properties of crumb rubber concrete. Materials, 9(3), 172. DOI 10.3390/ma9030172. [Google Scholar] [CrossRef]
92. Gonen, T. (2018). Freezing-thawing and impact resistance of concretes containing waste crumb rubbers. Construction and Building Materials, 177, 436–442. DOI 10.1016/j.conbuildmat.2018.05.105. [Google Scholar] [CrossRef]
93. Gesoğlu, M., Güneyisi, E., Khoshnaw, G., İpek, S. (2014). Abrasion and freezing–thawing resistance of pervious concretes containing waste rubbers. Construction and Building Materials, 73, 19–24. DOI 10.1016/j.conbuildmat.2014.09.047. [Google Scholar] [CrossRef]
94. Zhang, B., Feng, Y., Xie, J., Lai, D., Yu, T. et al. (2021). Rubberized geopolymer concrete: Dependence of mechanical properties and freeze-thaw resistance on replacement ratio of crumb rubber. Construction and Building Materials, 310, 125248. DOI 10.1016/j.conbuildmat.2021.125248. [Google Scholar] [CrossRef]
95. Nehdi, M. L., Najjar, M. F., Soliman, A. M., Azabi, T. M. (2017). Novel eco-efficient two-stage concrete incorporating high volume recycled content for sustainable pavement construction. Construction and Building Materials, 146, 9–14. DOI 10.1016/j.conbuildmat.2017.04.065. [Google Scholar] [CrossRef]
96. Luo, G., Zhao, P., Zhang, Y., Xie, Z., Zhao, X. D. (2021). Performance evaluation of waste crumb rubber/silica fume composite modified pervious concrete in seasonal frozen regions. Advanced in Materials Science and Engineering, 2021, 1–10. DOI 10.1155/2021/1411185. [Google Scholar] [CrossRef]
97. Bhavani, S., Kumar, G. N., Reddy, M. S., Rayudu, E. S. (2021). Experimental study on geopolymer rubberized concrete using natural zeolite. Materials Science and Engineering, 1132, 012038. [Google Scholar]
98. Hora, M., Reiterman, P. (2016). Assessment of the air-entraining effect of rubber powder and its influence on the frost resistance of concrete. Romanian Journal of Materials, 46(3), 327–333. [Google Scholar]
99. Alsaif, A., Bernal, S. A., Guadagnini, M., Pilakoutas, K. (2019). Freeze-thaw resistance of steel fibre reinforced rubberised concrete. Construction and Building Materials, 195, 450–458. DOI 10.1016/j.conbuildmat.2018.11.103. [Google Scholar] [CrossRef]
100. Luo, T., Zhang, C., Sun, C., Zheng, X., Ji, Y. et al. (2020). Experimental investigation on the freeze-thaw resistance of steel fibers reinforced rubber concrete. Materials (Basel), 13(5), 1260. DOI 10.3390/ma13051260. [Google Scholar] [CrossRef]
101. Grinys, A., Augonis, A., Daukšys, M., Pupeikis, D. (2020). Mechanical properties and durability of rubberized and SBR latex modified rubberized concrete. Construction and Building Materials, 248, 118584. DOI 10.1016/j.conbuildmat.2020.118584. [Google Scholar] [CrossRef]
102. Richardson, A., Coventry, K., Edmondson, V., Dias, E. (2016). Crumb rubber used in concrete to provide freeze–thaw protection (optimal particle size). Journal of Cleaner Production, 112, 599–606. DOI 10.1016/j.jclepro.2015.08.028. [Google Scholar] [CrossRef]
103. Pham, N. P., Toumi, A., Turatsinze, A. (2019). Effect of an enhanced rubber-cement matrix interface on freeze-thaw resistance of the cement-based composite. Construction and Building Materials, 207, 528–534. DOI 10.1016/j.conbuildmat.2019.02.147. [Google Scholar] [CrossRef]
104. Topcu, İ. B., Demir, A. (2007). Durability of rubberized mortar and concrete. Journal of Materials in Civil Engineering, 19(2), 173–178. DOI 10.1061/(ASCE)0899-1561(2007)19:2(173). [Google Scholar] [CrossRef]
105. Fang, J., Zhao, L., Shi, J. (2021). Frost resistance and pore structure of concrete incorporated with rubber aggregates and Nano-SiO2. Materials, 14(5), 1170. DOI 10.3390/ma14051170. [Google Scholar] [CrossRef]
106. Baricevic, A., Pezer, M., Jelcic Rukavina, M., Serdar, M., Stirmer, N. (2018). Effect of polymer fibers recycled from waste tires on properties of wet-sprayed concrete. Construction and Building Materials, 176, 135–144. DOI 10.1016/j.conbuildmat.2018.04.229. [Google Scholar] [CrossRef]
107. Gou, Y. J., Zhang, L. H., Liu, C. B., Zhang, H. P., Wei, C. et al. (2021). Investigation of freeze-thaw mechanism for crumb rubber concrete by the online strain sensor. Measurement, 174, 109080. DOI 10.1016/j.measurement.2021.109080. [Google Scholar] [CrossRef]
108. Wen, P., Wang, C., Song, L., Niu, L., Chen, H. (2021). Durability and sustainability of cement-stabilized materials based on utilization of waste materials: A literature review. Sustainability, 13(21), 11610. DOI 10.3390/su132111610. [Google Scholar] [CrossRef]
109. Yadav, J. S., Tiwari, S. K. (2017). Effect of waste rubber fibres on the geotechnical properties of clay stabilized with cement. Applied Clay Science, 149, 97–110. DOI 10.1016/j.clay.2017.07.037. [Google Scholar] [CrossRef]
110. Siddika, A., Mamun, M. A. A., Alyousef, R., Amran, Y. H. M., Aslani, F. et al. (2019). Properties and utilizations of waste tire rubber in concrete: A review. Construction and Building Materials, 224, 711–731. DOI 10.1016/j.conbuildmat.2019.07.108. [Google Scholar] [CrossRef]
111. Corredor-Bedoya, A. C., Zoppi, R. A., Serpa, A. L. (2017). Composites of scrap tire rubber particles and adhesive mortar–noise insulation potential. Cement and Concrete Composites, 82, 45–66. DOI 10.1016/j.cemconcomp.2017.05.007. [Google Scholar] [CrossRef]
112. Fraile-Garcia, E., Ferreiro-Cabello, J., Defez, B., Peris-Fajanes, G. (2016). Acoustic behavior of hollow blocks and bricks made of concrete doped with waste-tire rubber. Materials, 9(12), 962. DOI 10.3390/ma9120962. [Google Scholar] [CrossRef]
113. Nadal Gisbert, A., Gadea Borrell, J. M., Parres García, F., Juliá Sanchis, E., Crespo Amorós, J. E. et al. (2014). Analysis behaviour of static and dynamic properties of ethylene-propylene-diene-methylene crumb rubber mortar. Construction and Building Materials, 50, 671–682. DOI 10.1016/j.conbuildmat.2013.10.018. [Google Scholar] [CrossRef]
114. Ghizdăveţ, Z., Ştefan, B. M., Nastac, D., Vasile, O., Bratu, M. (2016). Sound absorbing materials made by embedding crumb rubber waste in a concrete matrix. Construction and Building Materials, 124, 755–763. DOI 10.1016/j.conbuildmat.2016.07.145. [Google Scholar] [CrossRef]
115. Abdel Kader, M. M., Abdel-wehab, S. M., Helal, M. A., Hassan, H. H. (2019). Evaluation of thermal insulation and mechanical properties of waste rubber/natural rubber composite. Housing and Building National Research Center, 8(1), 69–74. [Google Scholar]
Cite This Article
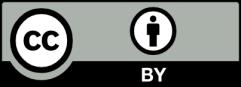
This work is licensed under a Creative Commons Attribution 4.0 International License , which permits unrestricted use, distribution, and reproduction in any medium, provided the original work is properly cited.