Open Access
ARTICLE
Characterization of Curing and Bonding of Wood with Adhesive Mixtures of Liquefied Wood and Hexamethylenediamine
1
Department of Wood Science and Technology, Biotechnical Faculty, University of Ljubljana, Ljubljana, 1000, Slovenia
2
Department of Wood Science and Technology, Faculty of Forestry and Wood Technology, Mendel University in Brno,
Brno, 613 00, Czech Republic
* Corresponding Author: Jure Žigon. Email: -lj.si
(This article belongs to the Special Issue: Characterization of the Curing of Bio-Based Adhesives)
Journal of Renewable Materials 2023, 11(2), 991-1001. https://doi.org/10.32604/jrm.2022.023584
Received 04 May 2022; Accepted 25 July 2022; Issue published 22 September 2022
Abstract
Various crosslinking agents can be added to the formulations of natural-based adhesives for wood bonding in order to achieve better durability and higher strength of the formed joints. In the present study, the effect of hexamethylenediamine (HMDA) addition on the performance of liquefied wood (LW) adhesive for wood bonding is investigated. Differential scanning calorimetry showed the improved thermal stability and crosslinking of the LW adhesive with HMDA. The intensified presence of amide linkages (C–N bonds) was found in LW+HMDA with attenuated total reflection Fourier transform infrared spectroscopy. Analysis of the bonded joints using an automated bonding evaluation system showed that a higher press temperature resulted in stronger bonds for both types of adhesives. Moreover, the addition of HMDA to LW adhesive improved the bond strength of the joints and accelerated the crosslinking of the adhesive. However, with a tensile shear strength of (6.76 ± 2.16) N × mm−2 (for LW) and (6.89 ± 2.10) N × mm−2 (for LW+HMDA), both adhesives were found to be unsuitable for interior non-structural use. In addition, the acidity of LW resulted in relatively high wood failure (70%) in the adhesive joints tested. Improved crosslinking of LW with HMDA was reflected in improved resistance of LW+HMDA adhesive joints to water degradation. In conclusion, HMDA is a promising additive for improving the adhesive performance of LW adhesives.Keywords
In the search for a replacement for the polluting petroleum-based adhesives used in wood bonding, researchers have developed many interesting solutions in recent decades. Substitutes based on natural resources, such as tannin, lignin, proteins, carbohydrates, starch, and others [1], have been extensively studied, and many have been reported to be very promising in terms of their mechanical and physical properties [2]. Another natural substitutes for synthetic adhesives intended for bonding wood are liquefied lignocellulosic materials [3]. Liquefied wood (LW) has been successfully used several times as a raw component for the synthesis of LW-based adhesives [4,5], as an additive to commercially available synthetic resins [6,7], or as an independent wood-bonding agent [8,9]. When used independently, the cross-linked polymer structure of LW is formed by physical (elimination of solvent and water) and chemical (condensation reaction between the depolymerized cellulose and aromatic derivatives of lignin) phenomena occurring at high temperatures (180°C and above) [8]. Many phenolic hydroxyl (–OH) groups and alcoholic –OH groups confer high reactivity to LW [5]. The use of LW as an independent component in wood bonding brings many positive aspects, such as the general substitution of unsustainable synthetic binders [10] and consequently lower free formaldehyde emissions [11]. However, the main drawbacks of the bindings prepared with independent LW are their relatively low mechanical properties (shear strength of maximum 7 N × mm−2), which fall short of standard requirements [12], and the inability of LW bindings to persevere in humid or wet environments [9]. For example, Ugovšek and co-authors [13] unsuccessfully attempted to achieve better durability and higher tensile-shear strength of LW bonds by adding a condensed tannin from Norway spruce wood to the adhesive formulation, while Jiang and co-authors [14] improved the water-sorption of particleboards by using partially liquefied bark as the main binder instead of LW. Pan and co-authors [15], reported that the temperature and cooking method for preparing LW could also affect the water resistance of compression-molded wood-based composites bonded with LW. Another approach to improve the resistance of LW bondlines to degradation by elevated relative humidity is the addition of a hardener. As reported by Lin and co-authors [16] in 1995, the addition of hexamine (hexamethylenetetramine, (CH2)6N4) helps improve the flexural properties of LW-based moldings.
Several studies published in recent years have presented hexamethylenediamine (HMDA, C6H16N2) as another potential component to improve the adhesion and water resistance of natural-based adhesives. HMDA is a solid, colorless, water-soluble organic compound mainly used for the preparation of nylon 66 and in adhesive resins [17]. HMDA is a kind of multi-amine compound, and these amine groups can react with the functional groups of adhesive resins, leading to their improved the binding properties [18]. In this way, Saražin and co-authors [19] synthesized a non-isocyanate polyurethane (NIPU) wood adhesive from organosolv lignin and HMDA, which exhibited satisfactory mechanical properties. The study by Arias and co-authors [20] found that NIPU made from kraft lignin, soy protein, and tannins with the addition of HMDA are promising candidates for the production of alternatives to formaldehyde-based wood panels. Xi and co-authors [21] succeeded in producing particleboard glued with NIPU adhesive from sucrose with excellent properties and three-layer plywood glued with soy protein isolate-based polyamides [22], both with the addition of HMDA as an adhesive crosslinker. The formation of amide linkages in the adhesive mixtures of soy protein isolate-based polyamides was confirmed with different analytical techniques, which might happen also in the adhesive mixtures of LW and HMDA.
The findings from the literature inspired the authors of this to combine pure LW with HMDA as a crosslinker. The HMDA was used in order to improve the adhesive properties of LW and the resistance of the adhesive joints to degradation by increased relative humidity. The liquefaction of wood was carried out according to the known procedure [9]. The curing kinetics of adhesives was monitored by differential scanning calorimetry (DSC), while the cured adhesives were chemically characterized by Fourier transform infra-red (FTIR) spectroscopy. Finally, the performance of the LW-based adhesives for wood bonding was evaluated using the standardized tensile-shear strength test and the automated adhesive bonding evaluation system (ABES), which has not been used for this purpose before.
The LW was obtained by liquefying the sieved particles of the wood of the tree of heaven (Ailanthus altissima (Mill.) Swingle), with a maximum size of 0.237 mm; 200 g of the oven-dried (103°C, 24 h) wood particles were placed in a three-neck glass reactor containing 600 g of ethylene glycol (Honeywell, Charlotte, USA) and 18 g of 96% sulfuric acid (KEMIKA d.d., Zagreb, Croatia). The glass reactor was immersed in an oil bath heated to 180°C and equipped with a water condenser. The liquefaction process was carried out in 120 min with mechanical stirring (500 min–1). The liquefied product was decanted into a glass, diluted with a mixture (4:1) of 1,4-dioxane and distilled water, and filtered through paper filter disks (grade 388, Sartorius, Göttingen, Germany) to remove the insoluble parts. The mixture of 1,4-dioxane and water was evaporated at 55°C under vacuum (10 mbar) using a rotavapor apparatus (R-210, Büchi Labortechnik AG, Flawil, Switzerland) and vacuum pump (PC 3003 Vario, Vaccubrand GmbH & Co. KG, Wertheim, Germany). Next, ethylene glycol was evaporated from the liquefied product at 120°C and 10 mbar using the same equipment. Evaporation was stopped when the gravimetric ratio between wood and ethylene glycol reached approximately 1:1. This study used the liquefied final product as the first adhesive mixture.
The LW+HMDA adhesive represented the mixture of LW and 70% HMDA (Sigma-Aldrich, St. Louis, USA) in the ratio of 100:6 weight units, as suggested by Saražin and co-authors for NIPU adhesive [19]. A fresh mixture of LW+HMDA was prepared before each characterization.
The basic properties of liquid LW and LW+HMDA adhesives are presented in Table 1.
2.2 Differential Scanning Calorimetry
A DSC 1 high-pressure differential scanning calorimeter (Mettler Toledo, Columbus, USA) was used to study the physical transitions and chemical reactions that occur during the curing of adhesives. An empty aluminum 40 μL reference pan and a pan containing the LW or LW+HMDA sample (7 mg) were placed in a high-pressure cell of the DSC instrument. The heat flux during curing of the analyzed sample was monitored in the temperature range of 25°C to 320°C with a heating rate of 10°C × min–1 in a dynamic nitrogen atmosphere with a gas flow rate of 50 mL × min–1 at atmospheric pressure (1 bar). Three replicates of each adhesive were analyzed with DSC.
2.3 Attenuated Total Reflection Fourier Transform Infrared Spectroscopy
The cured compounds of LW and LW+HMDA adhesives from DSC analysis were chemically characterized with Spectrum Two attenuated total reflectance FTIR (ATR-FTIR) spectrometer (PerkinElmer Inc., Waltham, USA). Three samples of the cured LW and LW+HMDA adhesives were pressed onto the LiTaO3 detector and scanned (16 scans) in a wavelength range from 600 cm–1 to 4000 cm–1 with a resolution of 0.5 cm–1. In addition, the pure liquid HMDA was analyzed with ATR-FTIR. The relevant absorption bands were interpreted using Spectrum software (version 10.5.3, PerkinElmer Inc., USA).
2.4 Evaluation of Bonding Performance
2.4.1 Automated Bonding Evaluation System Test
The development of bond strength of LW and LW+HMDA adhesives in a lap joint was evaluated using ABES (Adhesive Evaluation Systems, Corvallis, Oregon, USA) in accordance with ASTM D7998-19 standard [25]. Beech (Fagus sylvatica L.) wood veneers with a thickness of 0.84 mm were cut into strips with dimensions of (117 × 20) mm. The LW and LW+HMDA adhesives were applied manually with a spatula on one veneer strip’s overlapping area [(20 × 5) mm]. The application rate of the adhesives ([200 ± 10] g × m–2) was controlled with a precision balance. The bonded pairs of veneer strips were placed in the hot press of ABES and pressed together at 1.2 N × mm–2 for (20, 40, 60, 80, 100, 120, 180, 240, 300, and 600) s. The pressing temperatures were (120, 140, 160, 180, and 200)°C. The elapsed pressing time was followed by 5 s cooling with compressed air. Finally, the tensile shear strength of the bonded joint was determined at a loading rate of 1 kN × s–1 using a computer-controlled and pneumatically driven system. Five measurements were performed at each pressing time and temperature.
Each of the sample sequences tested with ABES at a defined pressing time and pressing temperature was modeled into a three-parametric logistic function (Eq. (1)) with nonlinear regression using SPSS Statistic software (IBM, Armonk, USA):
where τ(t) [N × m–2] is the shear strength of the adhesive bond, t [s] is the pressing time, β [N × m–2] determines the upper asymptote of the shear strength, κ determines the slope of the curve, and γ [s] determines the time at which maximum growth occurs.
2.4.2 Tensile-Shear Strength Test
The adhesive performance of LW and LW+HDMA was also evaluated using a tensile-shear strength test described in the standards EN 205 [26] and EN 12765 [27]. Beech wood lamellae conditioned to 10% moisture content with a length of 600 mm, a width of 135 mm, and a thickness of 5 mm were used as the substrate. Two two-layer assemblies were bonded with each adhesive mixture (200 g × m–2) using a conventional hot press at 180°C for 15 min. Twenty single-lap joint specimens with a length of 150 mm and a width of 20 mm were cut from the bonded assemblies one day after the completion of bonding and stored in a climatic chamber (20 ± 2°C, relative humidity of 65 ± 5%) for 7 days (conditioning procedure C1). Half of the specimens were additionally immersed in cold (20 ± 5°C) water for 24 h (conditioning procedure C2). Finally, the tensile-shear strength of the lap joints was determined using a Z005 universal testing machine (ZwickRoell GmbH & Co. KG, Ulm, Germany).
DSC analysis of LW and LW+HMDA showed no significant difference in thermograms between the two adhesives (Fig. 1). The curing process of LW determined by DSC can be interpreted similarly to a study by Ugovšek et al. [12]. The DSC curve of LW showed two endothermic signals; the first endothermic signal appeared at 100°C and indicated the evaporation of water from the LW sample, while the second endothermic signal appeared at 185°C and indicated the evaporation of the solvent (ethylene glycol) from the LW sample. After the complete evaporation of water and ethylene glycol from the LW sample, the solidification of the sample occurred at about 235°C. At higher temperatures, decomposition of the LW sample occurred. The presence of HMDA in LW caused no other reaction that could be indicated by DSC but shifted the main endothermic peaks to higher temperatures. The signal of water evaporation was shifted to 102°C, the signal of ethylene glycol evaporation was shifted to 198°C, and the solidification of LW+HMDA occurred at about 246°C. These results indicate better cross-linking and, consequently, the higher thermal stability of LW+HMDA adhesive than of pure LW [28,29]. However, both types of the adhesive seem to cure with physical reactions (evaporation of water and ethylene glycol), since the occurrence of the chemical reactions between LW and LW+HMDA adhesive mixtures could not be confirmed with DSC results.
Figure 1: Detected heat flow from curing kinetics monitoring of LW and LW+HMDA with DSC
The FTIR spectra shown in Fig. 2 reveal the chemical properties of the LW and LW+HMDA adhesives previously analyzed by DSC, and the chemical properties of pure HMDA crosslinker.
Figure 2: FTIR spectra acquired on cured LW and LW+HMDA
The LW sample exhibited some chemical components typical of wood composed of cellulose, hemicelluloses, lignin, and extractives, with carbonyl (C=O), OH, ester (RCOORʹ), and ethyl (CH2CH3) bonds, as well as carbon-hydrogen (C–H) bonds [30]. The broad peak in the spectra of pure LW, HMDA and LW+HMDA at about 3350 cm–1 corresponded to the OH groups, while the peaks at 2930 cm–1 and 2860 cm–1 were assigned to the CH2 and CH3 stretches, respectively. Moreover, especially the peak at 2930 cm–1 in LW+HMDA sample was intensified due to the presence of HMDA and increased proportion of CH2 groups [22]. The sharp peak found in LW at 1730 cm–1 indicates C=O stretching in non-conjugated ketones, aldehydes, and carboxyl (RCOOH) in xylan and hemicelluloses [31]. This peak was not detected in LW+HMDA adhesive and decreased notably, possibly due to the reaction between LW and HMDA [22], but the chemical reaction between LW and HMDA cannot be confirmed. The peak at 1595 cm–1 observed in LW was associated with the conjugated double bonds (C=C) or aromatic skeletal vibrations in lignin [32] and remained unchanged upon the addition of HMDA. HMDA exhibited the sharp peak at the same wavelength which corresponded to symmetrical and asymmetrical –NH deformation [33]. The same as for the peak at 1595 cm–1 in LW was true for the peak at 1450 cm–1, which signaled the asymmetric CH3 bending of the methoxyl groups (O–CH3) in the lignin structure [31]. In contrast, a shoulder peak at 1550 in LW+HMDA indicated the presence of secondary amides (N–H bonds) [34]. A bending vibration at about 1250 cm–1 was characteristic of the C–O–C groups of the ether linkages originating from the lignin in LW. The addition of HMDA to LW attenuated this peak. The enhanced peak at 1100 cm–1 signaled the stretching of amide group with C–N bonds originating from HMDA [35]. The peaks between 940 cm–1 and 760 cm–1 indicated the presence of aromatic double bonds in lignin [36], which were more evident in the LW sample.
3.3.1 Adhesive Bond Strength Development
The actual developments of the tensile-shear strength measured with ABES in the LW and LW+HMDA adhesive joints are shown in Figs. 3a and 3c. Based on these results, it was possible to construct the modeling curves for the evolution of the tensile-shear strength developments in adhesive joints, which are shown in Figs. 3b and 3d. The coefficients defining the shape of the modeled three-parametric logistic curves are listed in Table 2.
Figure 3: Actual (markings) and modeled (lines) developments of the tensile-shear strength in adhesive joints bonded with LW (a and b) and LW+HMDA (c and d)
For both adhesives, it has been shown that a higher pressing temperature results in stronger adhesive bonds. The higher the press temperature, the shorter the press time required to achieve maximum adhesion strength growth (γ value) or higher slope of the modeled curves (κ value). Moreover, for both adhesives, the highest strength values or their asymptotes (value of β) were obtained after a pressing time of 300 s, since increasing the pressing time to 600 s did not improve the bond strength anymore. In the case of the pure LW adhesive, the maximum tensile-shear strength of the bonded joint was (5.38 ± 0.30) N × mm–2. The addition of HMDA to the LW adhesive notably improved the bond strength of the joints, and this was true for all applied pressing temperatures. In addition, the pressing time required to achieve the maximum growth was reduced due to the accelerated cross-linking of the adhesive. The highest tensile-shear strength of (6.91 ± 0.26) N × mm–2 was found for LW+HMDA adhesive joints, pressed at 200°C for 600 s. In general, the ABES study showed that the press time should be no longer than about 200 s, regardless the type of adhesive mixture and the applied press temperature.
In general, the results of the standardized tensile-shear strength test (Fig. 4) showed that both the LW and LW+HMDA adhesives used in this study were not suitable for interior non-structural use, as none of them reached the minimum tensile-shear strength value of 10 N × mm–2 prescribed by the EN 12765 standard (durability class C1) [27].
Figure 4: Tensile-shear strength and wood failure percentage of lap joints bonded with LW and LW+HMDA, measured after conditioning procedures C1 (20 ± 2°C, 65 ± 5%, 7 days) and C2 (additional immersion in cold (20 ± 5°C) water, 24 h)
The influence of the pressing temperature on the tensile-shear strength of specimens bonded with pure LW was studied in detail by Ugovšek et al. [9]. As simlilar as reported in their study, the highest average tensile-shear strength for an LW bonded joint after completion of the conditioning procedure C1 was (6.76 ± 2.16) N × mm–2. In this case, a relatively high wood failure (70%) indicates the degradation of wood in the bonded joint due to the acidity of pure LW (Fig. 5). This degraded wood tissue could represent the weakest point in the joint. After the samples bonded with LW were immersed in liquid water for another day (conditioning procedure C2), the adhesive joints remained together, but their strength was very low ([0.45 ± 0.38] N × mm–2). A high percentage of wood failure (60%) confirmed the degradation of the wood adherends by the LW adhesive already during the hot-pressing process. The reason for the higher strength values of the LW adhesive in the tensile-shear strength test compared to ABES could be due to the thinner wood adherents of the latter, where the carbonization of the wood tissue around the LW bondline was more prominent [37]. As Solt and co-authors suggest in their studies [38,39], another reason for the different strengths obtained in the tensile-shear strength test and with ABES could be a difference in the wood surface quality of solid wood and veneers, as well as the time between the pressing and testing steps.
Figure 5: The appearance of the lap joints bonded with LW and LW+HMDA adhesives, tested after different conditioning procedures
In contrast to the ABES results, the tensile-shear strength test showed that the addition of HMDA to LW did not improve the strength of the bonded joints. For the samples bonded with LW+HMDA conditioned by procedure C1, the strength values were very similar ([6.89 ± 2.10] N × mm–2) to those of pure LW. At the same time, the percentage of wood failure was notably lower (20%) here. The reason for these observations could be the accelerated and improved crosslinking of the LW+HMDA adhesive. In addition, the strong acidity of LW could also be mitigated by the added HMDA. However, when testing the bonded samples after conditioning procedure C2, it was found that HMDA improved the resistance of the LW adhesive bond to water degradation. Here, the samples bonded with LW+HMDA still exhibited some adhesion on average and achieved an average tensile-shear strength of (3.24 ± 1.21) N × mm–2. These results confirm the improved crosslinking and resistance of LW to water degradation after the addition of HMDA.
The overall research on bonding performance of LW and LW+HMDA adhesives revealed these types of adhesive mixtures as another promising alternative to synthetic-based adhesives for bonding wood. The future research should be focused on improvement of LW and LW+HMDA adhesives resilience in humid environment.
The effect of HMDA addition on the performance of pure LW as an independent adhesive for wood bonding was evaluated. In addition to the improved thermal stability of LW+HMDA adhesive, DSC analysis showed that HMDA caused the improved reactions in LW. A similar finding was confirmed by ATR-FTIR analysis of the cured LW and LW+HMDA adhesives; the possible interaction between LW and HMDA could be confirmed by the enhanced presence of amide linkages with C–N bonds in the LW+HMDA adhesive. Monitoring the evolution of adhesive strength development by ABES showed that higher pressing temperature resulted in stronger bonds in both adhesives. In addition, the HMDA in the LW adhesive notably improved the bond strength of the joints and accelerated the cross-linking of the adhesive. However, the tensile-shear strength test showed that both the LW and LW+HMDA adhesives were not suitable for interior non-structural use, as neither none of them met the standard requirements. The relatively high wood failure (70%) in the tested joints bonded with pure LW was related to the degradation of the wood in the adhesive joint by the acidic LW. The addition of HMDA to LW notably improved the resistance of the LW+HMDA adhesive joints to water degradation. It can be concluded that HMDA improves the bonding performance of LW, which could be further enhanced by optimizing the LW+HMDA adhesive formulation.
Acknowledgement: The authors acknowledge the financial support from the Slovenian Research Agency (research programs funding No. P4-0015, “Wood and Lignocellulosic Composites”, and No. P4-0430, “Forest-Wood Value Chain and Climate Change: Transition to Circular Bioeconomy”), and the ASFORCLIC project. This project has received funding from the European Union’s Horizon 2020 Research and Innovation Programme under Grant Agreement N°952314.
Funding Statement: The authors received no specific funding for this study.
Conflicts of Interest: The authors declare that they have no conflicts of interest to report regarding the present study.
References
1. Pizzi, A. (2006). Recent developments in eco-efficient bio-based adhesives for wood bonding: Opportunities and issues. Journal of Adhesion Science and Technology, 20(8), 829–846. DOI 10.1163/156856106777638635. [Google Scholar] [CrossRef]
2. Sarika, P. R., Nancarrow, P., Khansaheb, A., Ibrahim, T. (2020). Bio-based alternatives to phenol and formaldehyde for the production of resins. Polymers, 12(10), 2237. DOI 10.3390/polym12102237. [Google Scholar] [CrossRef]
3. Jiang, W., Kumar, A., Adamopoulos, S. (2018). Liquefaction of lignocellulosic materials and its applications in wood adhesives–A review. Industrial Crops & Products, 124, 325–342. DOI 10.1016/j.indcrop.2018.07.053. [Google Scholar] [CrossRef]
4. Kobayashi, M., Tukamoto, K., Tomita, B. (2000). Application of liquefied wood to a new resin system-synthesis and properties of liquefied wood/epoxy resins. Holzforschung, 54(1), 93–97. DOI 10.1515/HF.2000.014. [Google Scholar] [CrossRef]
5. Kishi, H., Akamatsu, Y., Noguchi, M., Fujita, A., Matsuda, S. et al. (2011). Synthesis of epoxy resins from alcohol-liquefied wood and the mechanical properties of the cured resins. Journal of Applied Polymer Science, 120(2), 745–751. DOI 10.1002/app.33199. [Google Scholar] [CrossRef]
6. Hassan, E. B., Kim, M., Wan, H. (2009). Phenol-formaldehyde-type resins made from phenol-liquefied wood for the bonding of particleboard. Journal of Applied Polymer Science, 112(3), 1436–1443. DOI 10.1002/app.29521. [Google Scholar] [CrossRef]
7. Esteves, B., Martins, J., Martins, J., Cruz-Lopes, L., Vicente, J. et al. (2015). Liquefied wood as a partial substitute of melamine-urea-formaldehyde and urea-formaldehyde resins. Maderas. Ciencia y Tecnología, 17(2), 277–284. DOI 10.4067/S0718-221X2015005000026. [Google Scholar] [CrossRef]
8. Wan, H., He, Z., Mao, A., Liu, X. (2017). Synthesis of polymers from liquefied biomass and their utilization in wood bonding. In: He, Z. (Ed.Bio-based wood adhesives: Preparation, characterization, and testing, pp. 239–259. USA: CRC Press. [Google Scholar]
9. Ugovšek, A., Šernek, M. (2013). Effect of pressing parameters on the shear strength of beech specimens bonded with low solvent liquefied wood. Journal of Adhesion Science and Technology, 27(2), 182–195. DOI 10.1080/01694243.2012.701529. [Google Scholar] [CrossRef]
10. Janiszewska, D., Frąckowiak, I., Bielejewska, N. (2016). Application of selected agents for wood liquefaction and some properties of particleboards produced with the use of liquefied wood. Drewno, 59(197), 223–230. DOI 10.12841/wood.1644-3985.C37.01. [Google Scholar] [CrossRef]
11. Kunaver, M., Medved, S., Cuk, N., Jasiukaitytě, E., Poljanšek, I. et al. (2010). Application of liquefied wood as a new particle board adhesive system. Bioresource Technology, 101(4), 1361–1368. DOI 10.1016/j.biortech.2009.09.066. [Google Scholar] [CrossRef]
12. Ugovšek, A., Sernek, M. (2013). Characterisation of the curing of liquefied wood by rheometry, DEA and DSC. Wood Science and Technology, 47(5), 1099–1111. DOI 10.1007/s00226-013-0565-4. [Google Scholar] [CrossRef]
13. Ugovšek, A., Budija, F., Kariž, M., Šernek, M. (2011). Content in liquefied wood and of the addition of condensed tannin on bonding quality. Drvna Industrija, 62(2), 87–95. DOI 10.5552/drind.2011.1039. [Google Scholar] [CrossRef]
14. Jiang, W., Adamopoulos, S., Hosseinpourpia, R., Žigon, J., Petrič, M. et al. (2020). Utilization of partially liquefied bark for production of particleboards. Applied Sciences, 10(15), 5253. DOI 10.3390/app10155253. [Google Scholar] [CrossRef]
15. Pan, H., Shupe, T. F., Hse, C. Y. (2009). Physical and mechanical properties of bio-composites from wood particles and liquefied wood resin. In: Shelly, J. R., Puettmann, M. E., Skog, K. E., Han, H. S. (Eds.Woody biomass utilization: Challenges and opportunities, pp. 43–46. USA: Forest Products Society. [Google Scholar]
16. Lin, L., Yoshioka, M., Yao, Y., Shiraishi, N. (1995). Physical properties of moldings from liquefied wood resins. Journal of Applied Polymer Science, 55(11), 1563–1571. DOI 10.1002/app.1995.070551107. [Google Scholar] [CrossRef]
17. Ashland, L. L. C. (2018). Product stewardship summary, Hexamethylenediamine. https://www.ashland.com/file_source/Ashland/Documents/Sustainability/rc%20hexamethylenediamine.pdf. [Google Scholar]
18. Hu, J., Feng, X., Liu, Z., Zhao, Y., Chen, L. (2017). Surface amine-functionalization of UHMWPE fiber by bio-inspired polydopamine and grafted hexamethylene diamine. Surface and Interface Analysis, 49(7), 640–646. DOI 10.1002/sia.6203. [Google Scholar] [CrossRef]
19. Saražin, J., Pizzi, A., Amirou, S., Schmiedl, D., Šernek, M. (2021). Organosolv lignin for non-isocyanate based polyurethanes (NIPU) as wood adhesive. Journal of Renewable Materials, 9(5), 881–907. DOI 10.32604/jrm.2021.015047. [Google Scholar] [CrossRef]
20. Arias, A., Entrena-Barbero, E., Feijoo, G., Moreira, M. T. (2022). Sustainable non-isocyanate polyurethanes bio-adhesives for engineered wood panels are revealed as promising candidates to move from formaldehyde-based alternatives. Journal of Environmental Chemical Engineering, 10(1), 107053. DOI 10.1016/j.jece.2021.107053. [Google Scholar] [CrossRef]
21. Xi, X., Wu, Z., Pizzi, A., Gerardin, C., Lei, H. et al. (2019). Non‐isocyanate polyurethane adhesive from sucrose used for particleboard. Wood Science and Technology, 53(2), 393–405. DOI 10.1007/s00226-019-01083-2. [Google Scholar] [CrossRef]
22. Xi, X., Pizzi, A., Gerardin, C., Chen, X., Amirou, S. (2020). Soy protein isolate‐based polyamides as wood adhesives. Wood Science and Technology, 54(1), 89–102. DOI 10.1007/s00226-019-01141-9. [Google Scholar] [CrossRef]
23. EN ISO 3251 (2019). Paints, varnishes and plastics-Determination of non-volatile-matter content (ISO 3251:2019). Brussels, Belgium: European Committee for Standardization. [Google Scholar]
24. EN ISO 2555 (2018). Plastics-Resins in the liquid state or as emulsions or dispersions-Determination of apparent viscosity using a single cylinder type rotational viscometer method (ISO 2555:2018). Brussels, Belgium: European Committee for Standardization. [Google Scholar]
25. ASTM D7998–19 (2019). Standard test method for measuring the effect of temperature on the cohesive strength development of adhesives using lap shear bonds under tensile loading. West Conshohocken, USA: ASTM International. [Google Scholar]
26. EN 205 (2016). Adhesives-wood adhesives for non-structural applications-Determination of tensile shear strength of lap joints. Brussels, Belgium: European Committee for Standardization. [Google Scholar]
27. EN 12765 (2016). Classification of thermosetting wood adhesives for non-structural applications. Brussels, Belgium: European Committee for Standardization. [Google Scholar]
28. Zengin, H., Boztuğ, A., Basan, S. (2005). Poly(hepten-1-alt-maleic anhydride)-hexamethylenediamine conjugate: Synthesis and characterization of the thermal behaviour. Journal of Materials Science, 40(17), 4691–4693. DOI 10.1007/s10853-005-3927-y. [Google Scholar] [CrossRef]
29. Gao, Y., Yang, T., Wang, X., Xia, Y., Zhu, B. et al. (2021). Synthesis and characterization of poly(hexamethylene terephthalate/hexamethylene oxamide) alternating copolyamide (alt-PA6T/62). Journal of Applied Polymer Sicence, 138(5), e49773. DOI 10.1002/app.49773. [Google Scholar] [CrossRef]
30. Jiang, W., Hosseinpourpia, R., Biziks, V., Ahmed, S. A., Militz, H. et al. (2021). Preparation of polyurethane adhesives from crude and purified liquefied wood sawdust. Polymers, 13(19), 3267. DOI 10.3390/polym13193267. [Google Scholar] [CrossRef]
31. Li, G., Hse, C., Qin, T. (2015). Wood liquefaction with phenol by microwave heating and FTIR evaluation. Journal of Forestry Research, 26(4), 1043–1048. DOI 10.1007/s11676-015-0114-0. [Google Scholar] [CrossRef]
32. Pan, H., Shupe, T. F., Hse, C. Y. (2007). Characterization of liquefied wood residues from different liquefaction conditions. Journal of Applied Polymer Science, 105, 3739–3746. DOI 10.1002/(ISSN)1097-4628. [Google Scholar] [CrossRef]
33. Oprea, S., Vlad, S., Stanciu, A., Ciobanu, C., Macoveanu, M. (1999). Synthesis and characterization of poly(urethane-urea-acrylate)s. European Polymer Journal, 35(7), 1269–1277. DOI 10.1016/S0014-3057(98)00214-6. [Google Scholar] [CrossRef]
34. Saražin, J., Poljanšek, I., Pizzi, A., Šernek, M. (2022). Curing kinetics of tannin and lignin biobased adhesives determined by DSC and ABES. Journal of Renewable Materials, 10(8), 2117–2131. DOI 10.32604/jrm.2022.019602. [Google Scholar] [CrossRef]
35. Ryu, S. H., Sin, J. H., Shanmugharaj, A. M. (2014). Study on the effect of hexamethylene diamine functionalized graphene oxide on the curing kinetics of epoxy nanocomposites. European Polymer Journal, 52(73), 88–97. DOI 10.1016/j.eurpolymj.2013.12.014. [Google Scholar] [CrossRef]
36. Kunaver, M., Jasiukaityte, E., Čuk, N., Guthrie, J. T. (2010). Liquefaction of wood, synthesis and characterization of liquefied wood polyester derivatives. Journal of Applied Polymer Science, 115(3), 1265–1271. DOI 10.1002/app.31277. [Google Scholar] [CrossRef]
37. Ugovšek, A., Sever Škapin, A., Humar, M., Sernek, M. (2013). Microscopic analysis of the wood bond line using liquefied wood as adhesive. Journal of Adhesion Science and Technology, 27(11), 1247–1258. DOI 10.1080/01694243.2012.736854. [Google Scholar] [CrossRef]
38. Solt, P., van Herwijnen, H. W. G., Konnerth, J. (2019). Thermoplastic and moisture-dependent behavior of lignin phenol formaldehyde resins. Journal of Applied Polymer Science, 136(40), 48011. DOI 10.1002/app.48011. [Google Scholar] [CrossRef]
39. Solt, P., Konnerth, J., Gindl-Altmutter, W., Kantner, W., Moser, J. et al. (2019). Technological performance of formaldehyde-free adhesive alternatives for particleboard industry. International Journal of Adhesion and Adhesives, 94, 99–131. DOI 10.1016/j.ijadhadh.2019.04.007. [Google Scholar] [CrossRef]
Cite This Article
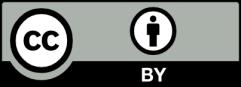
This work is licensed under a Creative Commons Attribution 4.0 International License , which permits unrestricted use, distribution, and reproduction in any medium, provided the original work is properly cited.