Open Access
ARTICLE
MUF Resins Improved by Citric Acid as Adhesives for Wood Veneer Panels
1 Department of Forestry Engineering, Faculty of Technology, University of Brasilia, Brasília, Brazil
2 LERMAB, University of Lorraine, Nancy, France
3 SeniorPost-Doctoral Internship, LERMAB-ENSTIB, University of Lorraine, Epinal, France
4 Yunnan Key Laboratory of Wood Adhesives and Glue Products, College of Material Science and Engineering, Southwest Forestry University, Kunming, China
5 International Joint Research Center for Biomass Materials, Southwest Forestry University, Kunming, China
* Corresponding Author: Antonio Pizzi. Email:
(This article belongs to the Special Issue: Renewable and Biosourced Adhesives-2021)
Journal of Renewable Materials 2023, 11(2), 539-553. https://doi.org/10.32604/jrm.2022.024971
Received 15 June 2022; Accepted 18 July 2022; Issue published 22 September 2022
Abstract
This article presents the first applied results of using citric acid in combinations with a melamine-urea-formaldehyde (MUF) resin for bonding wood veneers. The chemical reactions involved are shown based on a MALDI ToF analysis of the reaction of the MUF resin with citric acid. The preliminary results of the physical and mechanical properties of the LVL prepared are also presented. Veneers from Populus sp were used to manufacture 5-layer laminated veneer lumber (LVL) of small dimensions. Five combinations of the amount of citric acid, MUF spread rate and pressing parameters were tested. LVL bonded with 20% of citric acid + 100 g/m2 of MUF, hot-pressed using a 3-step process with maximum 1.5 MPa of pressure yielded the board with better dimensional stability and mechanical properties. It could be concluded that citric acid in combination with MUF can be used for bonding wood veneer and the research should be continued to study further the parameters involved and to enhance the results.
Graphic Abstract
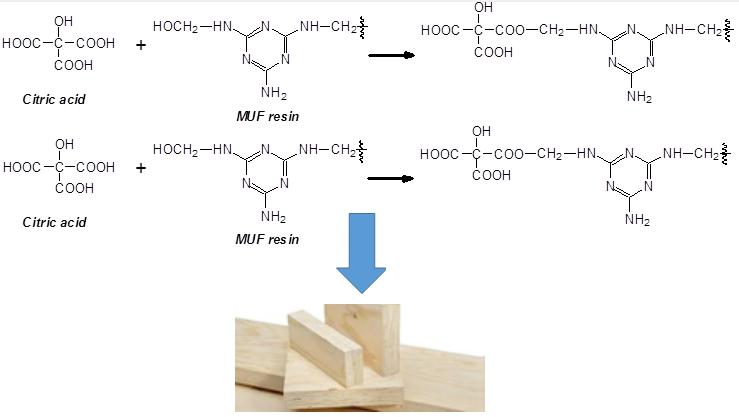
Keywords
Melamine-urea-formaldehyde (MUF) adhesives are one of the main thermosetting wood adhesives used to bond a variety of wood panels and other lignocellulosic materials [1]. Several systems have been reported both for upgrading their performance as well as to decrease the proportion of the expensive melamine while conserving their performance characteristics at a lower cost [2–9]. Thus, any new system that may improve any of these two aspects merits attention. Recently an interesting system was reported using citric acid for bonding wood panels or other wood joints. After the original research group discovering the effect of citric acid [10] several authors have shown the potential of this natural product to bind particleboards using several types of biomass [11–13], to bond wide flat wood surfaces such as LVL and plywood [14] as well as to markedly improve the water resistance of wood-welded joints [15].
Recent work has shown that the reaction of citric acid with wood occurs with both lignin and carbohydrate constituents of wood. The reactions occurring are esterifications between the carboxylic acid functions of citric acid and the numerous aromatic and aliphatic hydroxyl groups of the main wood constituents [14], while lignin rearrangements also contribute to the improvements in water resistance [15]. Based on these considerations it was interesting to apply citric acid to a traditional thermosetting adhesive for wood panels to see if its addition would improve somewhat its performance. The idea was based on the disponibility of alcohol groups on UF, MUF resins and PF resols, in the form of the hydroxymethyl groups abundant in such resins, to react with citric acid during curing of the adhesive. Among these thermosetting resins the one chosen for reaction with citric acid was the MUF because such a resin presents a more complex system in which a number of different reactions may occur. Thus, the work presented here is also aimed at further studying and clarifying what does occur at the chemical level when citric acid reacts with a thermosetting resin adhesive for wood panels, such as plywood and LVL, to evaluate the improvements, if any, in MUF performance in bonding, and to present preliminary results of LVL bonded with this system.
The laboratory made melamine-urea-formaldehyde (MUF) resin was prepared according to the following steps: 300 g of formaldehyde (37% in water) was put in a beaker and the pH was adjust to 9, and then the first load of urea (74 g) and melamine (20 g) was added and the temperature was increase to 90°C. When the solution reached 90°C the pH was again adjusted to 5–5.5 and kept for 40 min. Afterwards the pH was adjusted to 8.5 and the second load of melamine (63 g) was added and the reaction was kept for 60 min. Then, the temperature of the solution was reduced to 60°C, pH adjusted to 8 before adding the second load of urea (19,59 g) and the reaction was maintained for further 20 min. The resin was cooled in ice and kept in the refrigerator up to the time to be used.
The M: U:F molar ratios are identical for all samples tested.
2.2 Veneers and Their Treatment
Twenty veneers (moisture content (MC) = 10.3%; ρ = 449 kg/m3) measuring 400 mm × 400 mm × 2–3 mm from poplar (Populus sp) were selected, weighted and measured. A citric acid/water solution (50:50) was prepared and sprayed on the one surface of the veneers at spread rate about 20% or 10% based on the veneer’s weight and then they were oven dried at 60°C for 6 h. Afterward the veneers were separated in two groups, and 40 citric acid treated veneers (400 mm × 200 mm × 2–3 mm) were prepared.
2.3 Laminated Veneer Lumber (LVL) preparation
The assembling of the LVL panels was done so that citric acid (CA) treated veneer surface faced the opposite veneer surface covered with the MUF. Five combinations based on citric acid amount, MUF spread rate, and pressing parameters were tested. Thus, two amount of CA (10% and 20%) and two spread rates of MUF (75 or 100 g/m2) were tested and the panels were then hot-pressed using a 1- to 4-step schedules at 180°C. Theses schedules were applied aiming at the consolidation and densification of the board during the same operation using a Joos Lap 150 (Pfalzgrafenweiler, Germany) laboratory hot press.
Bending properties (Modulus of rupture (MOR) and modulus of elasticity (MOE)), compression parallel to the grain strength (fc,0) and glue-line shear strength (fgv,0) at dry conditions was determined according EN408+A1 (2012) and EN314-1 (2005) [16–18]. These tests were done using an INSTRON 4467 universal testing machine. Because of the dimensions of the board the fc,0 width was 25 mm, but the length was kept as six times the board thickness. Thickness swelling and water absorption (TS/WA) tests were measured according to ASTM D1037 (2012) procedures [19], but the dimension of the samples was changed: 25 mm × 25 mm × thickness. Permanent thickness swelling (PTS) and equilibrium moisture content (EMC) were determined according to methods already published [20].
2.5 Cross Polarization-Magic Angle Spinning Nuclear Magnetic Resonance (CP-MAS 13C NMR) Spectra
The MUF resin + 20% by weight of citric acid were hardened in the oven at 103°C for 2 h. The MUF control and the citric acid+MUF resin-bonded wood joints obtained were analyzed by solid state CP MAS 13C NMR. The hardened resins were reduced to powder. The spectra were obtained on a Brüker Avance 400 MHz spectrometer at a carbon resonance frequency of 100.6 MHz. The impulse duration at 90° was of 4 microseconds. The rotor was spun at 12 kHz on a double-bearing 4 mm Bruker probe. The cross-polarization contact time was 1 ms and a ramp 100% was used with a continuous wave decoupling. The number of scans was from 4000 to 10000. The spectrum of the MUF sample treated with 20% of citric acid for 2 h at 103°C is reported. The spectrum of the hardened MUF control alone is not reported as being identical to the MUF + citric acid one.
2.6 Matrix Assisted Laser Desorption Ionization Time-of-Flight (MALDI-TOF) Analysis
The MUF resin + 20% by weight of citric acid were hardened in the oven at 110°C. The samples were then treated with a NaCl solution (1.5 µl of a 0.1 M) in a methanol/water mixture (1:1) to increase ion formation, and a drop placed on the MALDI target (3 mm diameter) steel plate and dried. The samples and the matrix were then mixed in equal amounts, and 1.5 µl of the resulting slurry was placed on the MALDI target and dried at 40°C for 2 h before being analysed. A matrix of 2,5-dihydroxy benzoic acid was used. Red phosphorous (500–3000 Da) was used as reference for spectrum calibration. Finally, after evaporation of the solvent, the MALDI target was introduced into the spectrometer.
The spectra were recorded on a KRATOS AXIMA Performance mass spectrometer from Shimadzu Biotech (Kratos Analytical Shimadzu Europe, Ltd., Manchester, UK). The irradiation source was a pulsed nitrogen laser with a wavelength of 337 nm. The length of one laser pulse was 3 ns. Measurements were carried out using the following conditions: polarity-positive, flight path-linear, 20 kV acceleration voltages, 100–150 pulses per spectrum. The delayed extraction technique was used applying delay times of 200–800 ns. The software MALDI-MS was used for the data treatment. The oligomers can appear in the spectra either corresponding to their molecular weight or to their molecular weight +23 Da of the Na+ ion derived from the NaCl used as enhancer. The spectra precision is of ±1 Da.
The CP MAS 13C NMR of the MUF + citric acid in Fig. 1 does not really show anything more than a very polymerized MUF resin. Thus, the rather wide shoulder at 174–175 ppm represents unreacted and monosubstituted triazine. The peak at 166 ppm is due to the sum of tri-substituted and multi-substitited triazine and of unreacted urea. The peak at 158–159 ppm belongs to disubstituted and trisubstituted urea.
Figure 1: 13C NMR of the MUF + citric acid resin
The small shoulder at 80 ppm is due to the free formaldehyde in the system. The 73–74 ppm peak is representative of branched methylene ether linkages between amine and/or amide groups and the 53–54 ppm peak of the –CH2OH group linked to urea or melamine, such as
Thus, nothing much can be gleaned of the role of citric acid out of the NMR spectrum.
In the case of the MALDI ToF spectra of the MUF resin control just a number of species formed by copolymerized urea and melamine with formaldehyde are present as expected (Table 1) (Appendix 1: Figs. 2a–2f) [21–23]. The situation is very different in the reaction of MUF with citric acid (Appendix 2: Figs. 3a and 3b). On the MALDI ToF spectra first of all a series of peaks starting at 199 Da that increases in alternate steps of 162 Da and 175/176 Da can be noticed. This series is represented by the peaks at 199 Da-361 Da-536 Da-698 Da-874 Da-1036 Da-1212 Da-1373 Da-1549 Da and so on.
At first this seems as an alternation of two residues alternating, namely a monoreacted citric acid residue the MW of which is 175 Da and a residue such as –O-CH2-U-CH2-U the MW of which is 162 Da. This explanation is only partially true, some of such reaction products do exist but their presence is likely to be rather limited. This is so, as the possibility of reaction of –O-CH2-U-CH2-U is quickly exhausted unless it is further reacted with formaldehyde, and this cannot be the case as then the repeating motive would not anymore be 162 Da but higher due to the presence of a further –CH2- group. Thus, the possibility for this may anyhow exist as an alternation of a –O-CH2-U-CH2-U residue and of a –O-CH2-U-CH2-U-CH2+ residue reacted with formaldehyde released by either methylene ether bridges or still free in the resin mixture causing it. It must be clearly pointed out that direct reaction of the –NH2 of urea, an amide, with a carboxylic acid is not possible, thus such route of polymerization is quickly precluded at the lower molecular weights of condensation.
The situation is very different in the case of melamine. The –NH2 of melamine is aminic (not amidic) hence the possibility of reaction of a carboxylic acid with an amine is possible. However, this is only possible at elevated temperatures, to form the carboxylic acid amide –CO-NH-. Thus, as shown in the structures in Table 2 and Appendix 2: Figs. 3a and 3b the –COOH groups of citric acid can react with both the –NH2 of melamine to form an amide bridge, as well as on the –CH2OH formed by reaction of formaldehyde with urea and melamine to form an ester bridge –COOCH2-NH-.
The structures shown in Table 2 indicate that both of these reactions do occur. Thus, for example structure I represented by the peak at 535 Da comprises both esterification with citric acid of the –CH2OH group of a UF oligomer as well as the bridge formed by reaction with one of the amine groups of melamine.
IAs well as longer oligomers derived by this mix of reactions such as structure II in which two citric acid residues are present.
II
The set of reactions occurring then being:
(1) -COOH + H2N- → -CONH- + H2O
(2) -COOH + HOH2C- → -COOH2C- + H2O
(3) 2 R-NH2 + HCHO → 2 R-NH-CH2OH → 2 R-NH-CH2-NH-R’ + H2O
Both reactions do occur otherwise several of the peak’s present cannot be explained at all. It must be clearly pointed out that the melamine can react only at high temperature with the acid and the fact that the resin systems was hardened at 103°C for 2 h contributed to this reaction. In LVL and plywood bonding practice the max temperature at the veneers interface is at max 120°C when the press temperature is high, but only for a few minutes, indicating that the ester bridges may be predominating. Conversely, under the LVL pressing conditions used, at the first interface near the hot press platens the temperature will be much higher, in excess of 180°C, rendering possible also the formation of amide bridges by direct reaction of melamine.
Scheme 1 indicates the 5 types of reactions occurring when using MUF and citric acid together as thermosetting wood binders.
Scheme 1: Schematic representation of the 5 reactions occurring on wood when using a combination of a MUF resin and citric acid as binders
To conclude, the system MUF +20%citric acid is composed of a very complex set of reactions. Thus, the normal MUF oligomers formed by reaction with formaldehyde, in these spectra are represented by the peaks at 197 Da, 712 Da and 897/898 Da (see Table 1, MUF alone). Superimposed to these amide bridges formation and ester bridges formation occur, with the former occurring exclusively with melamine, and the latter occurring with the methylol groups on either urea or melamine. In the MALDI spectra at hand it seems that the esters form preferentially on the methylol groups carried on the urea resin as none of this involving melamine has been observed, although their presence cannot be excluded. It is for this mix of reactions that interpretation of the MALDI spectra is particularly difficult.
Finally, superimposed to the above reactions must be added the already well defined reactions of citric acid with the wood constituents on the wood surface, namely citric acid ester bridges in between wood polysaccharides, such as hemicelluloses and cellulose, citric acid bridges in between lignin units and between lignin and wood carbohydrates as well, these reactions having already been described in detail [14,15].
The conditions of preparation and the applied results of the LVL laboratory panels prepared are shown respectively in Tables 3–5. The conditions of preparation thus, relative proportions of MUF solids to citric acid solids, and the different sets of pressing schedules used, expressed as minutes of pressing at a given pressure, are shown in Table 3. The conditions of application of cases T4 to T8 were set from previus work on LVL using citric acid alone as binder [14].
It can be observed that the glue line shear strength of all differently pressed LVL panels exceeds the minimum required by EN-314-2 (1 N/mm2) [18]. Additionally, the modulus of rupture (MOR) was rather different from case to case with T6 showing bending strength on edge comparable to values reported in the literature [24]. The modulus of elasticity (MOE) values in Table 4 are similar to what found in the literature for cases T6 and T7, but lower for the other cases [24].
The parallel compression strength (fc,0) values of T5, T6 and T7 are instead were similar or higher than those found in the literature for LVL bonded with synthetic resins. Kurt et al. [25] produced poplar phenol-formaldehyde (PF)-bonded LVL and they found fc,0 values between 46.4 N/mm2 and 57.98 N/mm2. Rahayu et al. [26] performed a comprehensive study about the utilization of new poplars cultivars to produce LVL bonded with polyvinyl acetate. In general, the modulus of rupture (MOR) ranged between 47.4 and 64.8 N/mm2, while the modulus of elasticity (MOE) from 7250 to 10312 N/mm2. Bal [27] found MOR ranged from 79.9 to 90.5 N/mm2 whereas the MOE ranged from 8362–9185 N/mm2 for non-reinforced poplar PF resin-bonded LVL. Recently, Wang et al. [28] also evaluated the properties of PF-bonded poplar LVL and found 66.1 N/mm2 for MOR and 5433 N/mm2 for MOE. The values presented here are also between the range presented by the Forest Products Laboratory [29] for MOE (4900–12500 N/mm2) and MOR (33.8–88.2 N/mm2) for the experimental cases T5, T6 and T7, with T6 performing in general better that the other two.
The thickness swelling is lower for T6 and T7 but slightly higher for T5, while the water absorption is lower than usually found in the literature for LVL [27] for all the three experimental cases. Probably the main reason of this variation is the level of pressure applied. This pressure was chosen to allow with the same operation both con for T5 consolidation and densification of the LVL board to improve its mechanical properties. The density of the LVL billet before pressing was about 478 kg/m3 while the density of the consolidated LVL was between 586 and 641 kg/m3 for the T5,T6 and T7, meaning densification ratios of respectively 20.6% (T6), 34.5% (T5) and 25.1% (T7). The less dense bond lines of T6 due to its lowest densification ratio indicates why its thickness swelling and its water absorptions are lower. It is also remarkable that the T6 case at its lower densification ratio is superior to the others in almost all the different values of mechanical performance. It means that while certain level of compression stresses are always introduced in these assemblies, it is the multistep pressing schedule at lower pressures that appears to be one of the determinant factors on the mechanical performance of the final LVL. Equally the MOE and MOR values of T5 being higher than for T4 and for T7 being higher than T8 are due to the longer pressing time at equal pressure for the first period of the pressure cycle without this being followed by other cycles afterwards, namely 20 min for T5 and T7 against just 5 min for T4 and T8. For a sequence of multiple press conditions during the whole press cycle, the results of T8 being markedly better than those of T4 is due to the lower percentage of citric acid added. This indicates that as variations of pressure are introduced during the LVL pressing too high a proportion of citric acid is likely to decrease MOE and MOR due to the acid hydrolysis, hence damage of the wood constituents on the wood substrate surface. The key application parameters when coupling a traditional synthetic adhesive like a MUF with citric acid for bonding wood are then: the pressure, not excessively high, and not too much varied as in T6 (just varied twice); to use a single pressure throughout when using a relatively high proportion of citric acid, as for T5 and T7 to avoid excessive proportion of residual unreacted citric acid leading to excessive substrate hydrolysis damaging the carbohydrate constituents of the wood substrate surface; finally, in long sequences of pressure variations, as in T4 and T8, a lower proportion of citric acid yields better results as the substrate damage by hydrolysis is minimized by the lower quantity of acid used.
The reaction of citric acid with a MUF adhesive to bond wood veneers showed that reactions of citric acid with the MUF resin does occur. This is additional to the already observed esterifications between the carboxylic acid functions of citric acid and the numerous aromatic and aliphatic hydroxyl groups of the main wood constituents, in both the lignin and the carbohydrate constituents of wood. The reactions occurring are esterifications between the carboxylic acid functions of citric acid and the CH2OH group of methylolated UF oligomers as well as the bridges formed by reaction with some of the amine groups of melamine. These results confirm that under the conditions used for wood panel pressing the hypothesis of citric acid reacting with the resins used, here a MUF resin, do occur. Such esterifications may well occur with all hydroxyl-carrying compounds as shown in recent work with citric acid plus sugars [12,13]. The applied results on bonding wide flat wood surfaces such as veneers to obtain LVL panels or plywood have shown that citric acid has great potential to upgrade the performance of existing wood adhesives for wood veneers. The pressure applied during the hot-pressing, and the cycle of pressure variation might both have a very important role on the success of such a process for the particular type of panels studied in this work.
Funding Statement: The LERMAB-ENSTIB is financed under the scheme of Laboratory of Excellence ARBRE by the French Agence Nationale de la Recherche (ANR).
Conflicts of Interest: The authors declare that they have no conflicts of interest to report regarding the present study.
References
1. Manik, T. N., Nuki, S. A., Fauziyah, N. A., Mashuri, Zainuri, M. et al. (2021). Structure, dynamic-mechanical and acoustic properties of oil palm trunk modified by melamine formaldehyde. Journal of Renewable Materials, 9(9), 1647–1660. DOI 10.32604/jrm.2021.016089. [Google Scholar] [CrossRef]
2. Wazarkar, K., Sabnis, A. (2018). Development of cardanol-based polyol via click chemistry and crosslinking with melamine formaldehyde resin for coating applications. Journal of Renewable Materials, 6(4), 438–449. DOI 10.7569/JRM.2017.634159. [Google Scholar] [CrossRef]
3. Prestifilippo, M., Pizzi, A., Norback, H., Lavisci, P. (1996). Low addition of melamine salts for improved UF adhesives water resistance. Holz als Roh-und Werkstoff, 54, 393–398. [Google Scholar]
4. Zanetti, M., Pizzi, A. (2003). Low addition of melamine salts for improved MUF adhesives water resistance. Journal of Applied Polymer Science, 88, 287–292. [Google Scholar]
5. Zanetti, M., Pizzi, A., Beaujean, M., Pasch, H., Rode, K. et al. (2002). Acetals induced strength increase of MUF polycondensation adhesives. II. Solubility and colloidal state disruption. Journal of Applied Polymer Science, 86, 1855–1862. [Google Scholar]
6. Pizzi, A., Beaujean, M., Zhao, C., Properzi, M., Huang, Z. (2002). Acetals-induced strength increases and lower resin contents in MUF and other polycondensation adhesives. Journal of Applied Polymer Science, 84, 2561–2571. [Google Scholar]
7. Zanetti, M., Pizzi, A., Kamoun, C. (2003). Upgrading of MUF particleboard adhesives and decrease of melamine content by buffer and additives. Holz als Roh-und Werkstoff, 61, 55–65. [Google Scholar]
8. Kamoun, C., Pizzi, A., Zanetti, M. (2003). Upgrading of MUF resins by buffering additives–Part 1: Hexamine sulphate effect and its limits. Journal of Applied Polymer Science, 90, 203–214. [Google Scholar]
9. Zanetti, M., Pizzi, A. (2003). Upgrading of MUF resins by buffering additives–Part 2: Hexamine sulphate mechanisms and alternate buffers. Journal of Applied Polymer Science, 90, 215–226. [Google Scholar]
10. Umemura, K., Ueda, T., Munawar, S., Kawai, S. (2012). Application of citric acid as natural adhesive for wood. Journal of Applied Polymer Science, 123, 1991–1996. [Google Scholar]
11. Kusumah, S. S., Umemura, K., Oshioka, K. Y., Miyafuji, H., Kanajama, K. (2016). Utilisation of sweet sorghum bagasse and citric acid for manufacturing particleboard, I: Effects of predrying treatment and citric acid content on the board properties. Industrial Crops and Products, 84(9), 34–42. DOI 10.1016/j.indcrop.2016.01.042. [Google Scholar] [CrossRef]
12. Liao, R., Xu, J., Umemura, K. (2016). Low density sugarcane bagasse particleboard bonded with citric acid and sucrose: Effect of board density and additive content. BioResources, 11(1), 2174–2185. DOI 10.15376/biores.11.1.2174-2185. [Google Scholar] [CrossRef]
13. Widyorini, R., Nugraha, P., Rahman, M., Prayitno, T. (2016). Bonding ability of a new adhesive composed of citric acid-sucrose for particleboard. BioResources, 11(2), 4526–4535. DOI 10.15376/biores.11.2.4526-4535. [Google Scholar] [CrossRef]
14. Del Menezzi, C., Amirou, S., Pizzi, A., Xi, X., Delmotte, L. (2018). Reactions with wood carbohydrates and lignin of citric acid as a bond promoter of wood veneer panels. Polymers, 10(8), 833. DOI 10.3390/polym10080833. [Google Scholar] [CrossRef]
15. Amirou, S., Pizzi, A., Delmotte, L. (2017). Citric acid as waterproofing additive in butt joints linear wood welding. European Journal of Wood and Wood Products, 75(4), 651–654. DOI 10.1007/s00107-017-1167-x. [Google Scholar] [CrossRef]
16. European Norm EN408+A1 (2012). Timber structures-Structural timber and glued laminated timber–Determination of some physical and mechanical properties. [Google Scholar]
17. European Norm. EN 314-1 (2004). Plywood-Bond quality-Test methods. [Google Scholar]
18. European Norm. EN 314-2 (2004). Plywood-Bond quality-Requirements. [Google Scholar]
19. American Society for Testing and Materials (2006). Standard test methods for evaluating properties of wood-base fiber and particle panel materials. [Google Scholar]
20. Del Menezzi, C. H. S., Tomaselli, I., Teixeira, D. E., Okino, E. Y. A., Santana, M. A. E. (2009). Thermal modification of consolidated oriented strandboards: Effects on dimensional stability, mechanical properties, chemical composition and surface color. European Journal of Wood and Wood Products, 67, 383–396. [Google Scholar]
21. Despres, A., Pizzi, A., Pasch, A., Kandelbauer, A. (2007). Comparative 13C NMR and MALDI-TOF of species variation and structure maintenance during MUF resins preparation. Journal of Applied Polymer Science, 106, 1106–1128. [Google Scholar]
22. Kandelbauer, A., Despres, A., Pizzi, A., Taudes, I. (2007). Testing by FT-IR species variation during MUF resins preparation. Journal of Applied Polymer Science, 106, 2192–2197. [Google Scholar]
23. Mercer, A. T., Pizzi, A. (1996). A 13C NMR analysis method for MF and MUF resins strength and formaldehyde emission from wood particleboard–Part 1: MUF resins. Journal of Applied Polymer Science, 61, 1687–1696. [Google Scholar]
24. Saviana, J., Sosa Zitto, M. A., Piter, J. C. (2009). Bending strength and stiffness of structural laminated veneer lumber manufactured from fast-growing Argentinean Eucalyptus grandis. Maderas: Ciencia y Tecnologia, 11, 183–190. [Google Scholar]
25. Kurt, R., Meric, H., Aslan, K., Çil, M. (2012). Laminated veneer lumber (LVL) manufacturing using three hybrid poplar clones. Turkey Journal of Agriculture and Forestry, 36, 237–245. DOI 10.3906/tar-1005-958. [Google Scholar] [CrossRef]
26. Rahayu, I., Denaud, L., Marchal, R., Darmawan, W. (2015). Ten new poplar cultivars provide laminated veneer lumber for structural application. Annals of Forest Science, 72(6), 705–715. DOI 10.1007/s13595-014-0422-0. [Google Scholar] [CrossRef]
27. Bal, B. C. (2016). Some technological properties of laminated veneer lumber produced with fast-growing poplar and eucalyptus. Maderas: Ciencia y Tecnologia, 18(3), 413–424. DOI 10.4067/S0718-221X2016005000037. [Google Scholar] [CrossRef]
28. Wang, J., Guo, X., Zhong, W., Wang, H., Cao, P. (2015). Evaluation of mechanical properties of reinforced poplar laminated veneer lumber. Bioresources, 10(4), 7455–7465. DOI 10.15376/biores.10.4.7455-7465. [Google Scholar] [CrossRef]
29. Forest Products Laboratory (2010). Wood handbook—Wood as an engineering material. General Technical Report FPL-GTR-190. Madison, Wisconsin: United States Department of Agriculture, Forest Service, Forest Products Laboratory. [Google Scholar]
Figure 2: MALDI ToF spectra of MUF resin in the (a) 20–200 Da range, (b) 200–400 Da range, (c) 400–600 Da range, (d) 600–800 Da range, (e) 800–1000 Da range, (f) 1000–2000 Da range
Figure 3: MALDI ToF spectra of MUF resin +20%citric acid in the (a) 100–800 Da range, (b) 800–1000 Da range
Cite This Article
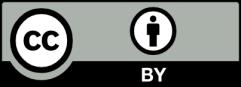
This work is licensed under a Creative Commons Attribution 4.0 International License , which permits unrestricted use, distribution, and reproduction in any medium, provided the original work is properly cited.