Open Access
REVIEW
Research and Application Progress of Straw
1 College of Civil Engineering, Nanjing Forestry University, Nanjing, 210037, China
2 Joint International Research Laboratory for Bio-Composite Building Materials and Structures, Nanjing Forestry University, Nanjing, 210037, China
3 Department of Furniture, Design and Habitat Brno, Mendel University in Brno, Brno, 61300, Czech Republic
4 University College London, London, WC1E, 6BT, UK
5 University of Naples Federico II, Naples, 80133, Italy
6 Lianyungang Baolisen Industrial Co., Ltd., Lianyungang, 222500, China
* Corresponding Author: Haitao Li. Email:
(This article belongs to the Special Issue: Bio-Composite Materials and Structures-2021)
Journal of Renewable Materials 2023, 11(2), 599-623. https://doi.org/10.32604/jrm.2022.022452
Received 10 March 2022; Accepted 27 May 2022; Issue published 22 September 2022
Abstract
Straw is a general term for the stem and leaf parts of mature crops, and is a multi-purpose renewable biomass energy resource in the agricultural ecosystem. The prospect of comprehensive utilization of straw has become broad with the development of agricultural production, the advancement of science and technology, and the improvement of the level of agricultural mechanization. The comprehensive utilization of straw plays an important role in enhancing the sustainable development ability of agricultural economy and improving the current situation of comprehensive utilization of agricultural resources in my country. This paper briefly combs the development history of straw and the prospect and current situation of comprehensive utilization, and expounds the separation technology of straw components, straw man-made panels, straw concrete, straw returning technology and oyster mushroom cultivation. It focuses on the description of the component separation technology of straw and the manufacturing process of straw-based panels. The different separation methods and separation effects of cellulose, hemicellulose and lignin were introduced in detail, and the static yield strength (MOR), internal bonding strength (IB) and water absorption thickness of several common straw-based panels were compared and studied (TS). Finally, it summarizes the benefit analysis of the comprehensive utilization of straw by scholars from the perspective of economics, and summarizes the corresponding measures based on their own views.Keywords
The growing shortage of materials used in furniture production (wood) forces us to look for alternative sources [1–4]. New trends in material management are based on the principles of a circular economy, and concepts such as recycling, eco-design, bioeconomy and upcycling are being increasingly implemented in production processes [5,6]. There is a whole range of materials that combine these concepts. Some companies monitor the condition of these materials and allow them to stay in the life cycle by finding a suitable application for them [7–9]. This way, new types of materials whose properties are significantly different from those of original materials (wood) are entering production systems. Here it is necessary to focus attention on the correct identification and quantification of material characteristics [10–14].
Crop straw usually refers to the remaining part of wheat, rice, corn, rape, cotton, reed and other crops after harvesting the fruit. It is mainly divided into two categories: grain crop straw and economic crop straw [15]. The corn straw bundle is shown in Fig. 1. China is a big agricultural country with abundant agricultural crop resources. China’s rice output was 213 million tons in 2021, and the planting area accounted for about 25.44% of the worlds [16]. At the same time, China is also the largest rapeseed producer in the world, with rapeseed planting area and total output value accounting for 30% of the world [17]. The world’s crop straw production is also huge, and it is an important biomass raw material. The estimated global supply was 4.41 billion tons in 2019, and by 2025 it is expected to provide 4.8 billion tons of supply per year [18].
Figure 1: Corn straw bundle [15]
Straw can be absorbed and utilized by livestock such as cattle and sheep due to the high crude fiber content (30%–40%) and nutrient-rich cellulose, hemicellulose and lignin [19–22]. Physical treatment, chemical treatment and biological treatment [23–26] are usually used to treat crop straw to improve the nutritional value of straw and reduce the waste of straw feed resources, so as to achieve the goal of green economy and sustainable development. At the same time, straw-based wood-based panels also have good mechanical properties, and have received extensive attention in the use of building materials. The comprehensive utilization of crop straw resources is of great significance for promoting farmers’ income increase, environmental protection, resource conservation and sustainable development of the world’s agricultural economy [27]. More and more scholars have carried out comprehensive and in-depth research on the comprehensive utilization of straw.
This paper summarizes the comprehensive utilization and prospects of straw, and focuses on the performance of straw-based panels. The comprehensive utilization of straw is mainly concentrated in agriculture, and the industrial application is still relatively scarce at this stage. It is hoped that this will provide help and reference for the research and application of straw industrialization, and will be popularized in building structures as soon as possible.
2 Status of Comprehensive Utilization of Straw
China is a big grain producing country, producing more than 500 million tons of grain every year. At the same time, a large amount of straw is also produced. More than 200 million tons of straw rot or burn in vain in China every year because of people’s different consumption concepts and lifestyles [28]. According to relevant reports [29], the average annual output of agricultural straw reaches 1.14 billion tons. Most of the straw resources are used in abandoned or incinerated in situ except for a small part used in papermaking and board processing. Burning straw not only occupies land, but also produces a lot of dust and carbon dioxide. It will cause serious damage to the local ecological environment. How to learn from the practice and experience of comprehensive utilization of straw in other countries and do a good job in the utilization of crop straw in China has become an urgent agricultural development problem to be solved.
As the world’s energy shortage and environmental pollution problems have become increasingly prominent, the direct combustion of straw to obtain thermal energy has been banned. The Chinese government has issued a series of policies to guide the people to comprehensively utilize straw, including straw feed [30], straw returning to fields [31,32], straw energy use [33] (direct combustion power generation and bio gasification use) and straw papermaking [34], and have achieved remarkable results. The percentage of straw consumed by various straw utilization methods to the total straw is shown in Fig. 2. Shahryari et al. [35] conducted solid fermentation of wheat straw, and the experimental results showed that the fermented wheat straw could remove part of hemicellulose, phytic acid and lignin, which is beneficial to be used as animal feed.
Figure 2: Distribution of straw utilization ratio
3 Component Separation Technology of Crop Straw
The component separation of crop straw [36,37] is the premise to realize the high-value utilization of each component. Sun et al. [38] summarized their phased achievements in the separation and high-value utilization of wood and non-wood components, including the conversion of cellulose into fuel ethanol and the separation and modification of hemicellulose. Zhao et al. [39] summarized the research status and development of straw component separation technology from cellulose, hemicellulose, lignin and total component separation. There are differences in the proportion of the three components in different plant fiber raw materials. Even in the same plant, the differences in the three main components will be caused by the different growth stages and growing environments. In general, the cellulose content of wood is higher than the hemicellulose and lignin content of wood, while the content of hemicellulose in corn stover is relatively high [40]. Chen et al. [41] used a combination of steam explosion and ethanol extraction to effectively separate components from wheat straw and prepare regenerated cellulose membranes.
The application of cellulose in straw is mostly for pulping and papermaking or for producing fuel ethanol [42]. Researchers begin to explore the ways to improve the utilization value of plant cellulosic biomass and tried to convert it into fuel or various high value-added chemicals through combustion technology, bioconversion technology and thermochemical conversion technology [43]. The separation of cellulose generally adopts physical methods with relatively simple principles and will not cause damage to the environment. However, physical methods generally have high energy consumption and poor separation effect, so they are rarely used alone [44]. The treatment of cellulose with organic alcohols or organic acids such as methanol and ethanol are called the organic solvent method. In order to obtain a better treatment effect during the treatment process, a small amount of acid or alkali is often added as a catalyst [45,46].
As one of the most promising green reagents in recent years, ionic liquids have been widely used in the dissolution, separation and regeneration of cellulose. However, the high toxicity of ionic liquids has been criticized [47]. Therefore, deep eutectic solvents (DES) with the advantages of low toxicity, biodegradability, low price, and easy preparation are favored by many researchers. Francisco et al. [48] took the lead in treating wheat straw with DES, and found that DES has good solubility for lignin and hardly dissolves cellulose, so the selective separation of cellulose and lignin can be achieved according to the difference in solubility.
3.2 Separation of Hemicellulose
The separation method of hemicellulose is relatively complicated. The traditional separation method is the alkaline method, which has the advantage of less damage to cellulose and can be used for the extraction of pulp and paper and other high value-added chemicals [49]. Some scholars [50] adopted the environmental protection method of alkaline hydrogen peroxide to separate hemicellulose on the basis of the traditional alkaline method. The principle of this type of method is that the free radicals in cellulose can oxidize the lignin structure, thereby forming hydrophilic groups to break the chemical bonds between the lignin molecular units, and finally realize the separation of cellulose. The decomposition of hemicellulose also includes hot water pretreatment [51] and mixed organic solvent extraction [52]. Most of the mixed organic solvent extraction methods are used with the aid of steam explosion to obtain high yields of hemicellulose [53]. Yan et al. [54] isolated hemicellulose by microwave-assisted acid hydrolysis and boiling method using cooked rice straw as raw material, and found that there are abundant xylem structures in hemicellulose. Hemicellulose is mostly used to produce xylose or xylitol.
The most commonly used method for lignin separation in the market is the thioamide hydrolysis method proposed by Lapierre et al. [55], which can better improve the degradation selectivity of lignin.
Some researchers [56] also proposed a method for the direct separation of lignin by virtue of the environmentally friendly, efficient and specific characteristics of biotechnology. Chistyakov et al. [57] pointed out that hydrolyzed lignin can produce activated carbon, and used lignin to prepare carbon adsorption materials. Such methods are widely used in various fields such as water and air treatment, pharmaceuticals and solvent recovery.
Table 1 summarizes the separation methods of the three types of elements and the corresponding separation effects of each method.
According to the basic skeleton of lignin (as shown in Fig. 3) [58], some scholars proposed to use high-boiling alcohols such as ethylene glycol, 1,3-butanediol, and 1,4-butanediol as solvents to separate lignin. This method can obtain high yield of lignin without using catalyst, and the solvent can be recycled [59]. Scholars [60] summarized the separation methods of lignin, and the results are shown in Table 2.
Figure 3: Basic skeleton of lignin [58]
To sum up, crop straw is rich in resources, and the traditional treatment method pollutes the environment and wastes resources. Combining with the actual situation of crop straws in various places, a corresponding comprehensive utilization plan is adopted to develop an efficient and low-cost separation method to realize the separation of cellulose, hemicellulose and lignin, which has attracted much attention. The various utilizations of straw in the following are based on three main components, so as to realize the high-value utilization of each component.
Studies have shown that the composition of straw is similar to that of bamboo [61–64] and wood [65,66]. Therefore, it can be considered as an alternative raw material for wood and bamboo [67–69]. Straw products mainly include wheat straw particleboard, straw MDF, wheat straw fiberboard, grass-wood composite MDF, soft straw board, lightweight composite wall material, straw charcoal, straw plastic composite material [70]. The industrial production of straw-based panels started in the late 1990s [71], which can be used in furniture, decoration and other building materials, and can effectively solve the contradiction between wood supply and demand and the problems caused by waste and incineration of agricultural straws.
Straw-based panels are made of straw or wood and straw mixed in a certain proportion as raw materials, adding resin adhesive, and integrating physical, chemical, electrical, mechanical, hydraulic and other technical principles. Plate products obtained through paving, pre-pressing, hot-pressing, post-sawing treatment, curing treatment, surface treatment and other processes [72,73]. The two kinds of straw-based panels are shown in Fig. 4.
Figure 4: Two kinds of straw-based panels [72]
With the joint efforts of some scientists in the United States and Europe at the beginning of the 20th century, the production of wood-based panels using economic crops such as bagasse and hemp stalks as raw materials has been developed to varying degrees [74]. Then in 1970, the symposium on non-wood wood-based panels hosted by the United Nations Industrial Development Organization officially opened the curtain of research on straw-based panels [75].
Rowell [76] of the Madison Forest Products Laboratory in the United States conducted chemical composition analysis and performance comparison of the fibers of 20 kinds of straw plants, and believed that it is feasible to use them to composite with other materials to manufacture wood-based panels. Loxton et al. [77] conducted an in-depth study on the properties of particleboards made from agricultural residues using UF, PF and MDI, respectively. The results show that the waxy and siliceous layers on the surface will affect the bonding performance of the adhesive, so the surface should be pretreated and the manufacturing process should be improved. Jin [78] used corn stalk as raw material to conduct experimental research on the adhesive ratio and preparation process parameters of straw-based panels, which provided a reference for improving the performance of straw-based panels and improving the production process. The filling and forming process of corn stover wood-based panels are shown in Fig. 5.
Figure 5: Pressing process of straw-based panel [78]
Sören et al. [79] used wheat straw as raw material and a mixture of urea melamine formaldehyde (UMF) and urea melamine benzaldehyde (UMPF) resin as binder to prepare high-performance medium density fiberboard (MDF). Its preparation process is shown in Fig. 6.
Figure 6: Schematic diagram of straw fiber preparation in MDF test workshop [79]
In the figure: (1) hammer mill; (2) dry screen; (3) pretreatment screw; (4) conveyor belt; (5) feed screw; (6) preheater (distiller); (7) fiber separator (refiner); (8) discharge pipe; (9) dryer; (10) fiber discharge port (cyclone).
Straw-based panels have the characteristics of light weight, high strength, thermal insulation, sound insulation, excellent fire resistance and no pollution to the environment, and are widely used in furniture, flooring [80] (as shown in Fig. 7), interior decoration and building walls and other fields.
Figure 7: Veneer reinforced double straw core composite structure [80]
Halvarsson et al. [81] also tried to make fiberboard by a method without adding binder, which is roughly the same as the above method. The straw is subjected to steam, hot water and sulfuric acid treatment before fiber separation, and the fiber is added during the fiber separation process. Ferric chloride and hydrogen peroxide are used to oxidize and activate wheat straw fibers, so that the performance of fiberboard can be improved.
Straw-based panels can be mainly divided into three categories: straw particleboard, straw fiberboard and straw oriented board. A series of physical and chemical treatments such as grinding, hot pressing and adding anti-corrosion materials [82] are applied to the raw straw and finally processed into furniture, floor and building materials and applied to life. The manufacturing properties and applications of straw-based panels are shown in Fig. 8.
Figure 8: Manufacturing properties and applications of straw-based panels [82]
Naima et al. [83] designed a single-board reinforced double-straw core composite structural floor substrate. The floor leather material of this composite structure can not only endow the floor with good surface properties, but also prevent edge chipping during processing. Zhang et al. [84] studied the influence of the hot-pressing process of wheat straw particleboard on the basic properties of the finished product. The test results show that when the hot-pressing temperature is 150 degrees Celsius, and the pressed wheat straw particleboard with a density of 0.75 g/cm3 can meet the requirements of class A particleboard superior quality. The hot pressing process curve is shown in Fig. 9. Zhang et al. [85] used wheat straw as raw material and modified UF as adhesive to produce homogeneous particleboard. The test results show that this method is feasible. Within a certain range, the MOR and IB values of wheat straw homogeneous particleboard increase with the increase of its density, and the mechanical properties can meet the requirements.
Figure 9: Hot pressing process curve [85]
Mo et al. [86] used isocyanate (MDI), urea-formaldehyde (UF), soy protein isolate (SPI) and soy flour (SF) to chemically treat wheat straw to study its mechanical properties. The test results show that MDI particleboard has the best mechanical properties and water resistance among the four adhesives. Although the mechanical properties of soy-based adhesive are not as good as MDI resin, it is environmentally friendly and can be used in places where mechanical strength requirements are not strict. Table 3 shows the mechanical properties of several adhesive-treated wheat straw boards.
Xu et al. [87,88] used modified isocyanate adhesives to press straw particleboards in the laboratory and tested the static bending strength, elastic modulus, internal bonding strength and water absorption thickness expansion ratio of the boards. The results show that the flexural performance of straw particleboard meets the requirements of wood particleboard when the density exceeds 0.75 g/cm3. The straw particleboard will deform obviously under the action of water when the amount of glue is 5%. Density can effectively control short-term water swelling, but only an increase in water repellent and sizing amount can give the board long-term dimensional stability. Xu et al. [89] also used isocyanate (MDI) to make single-layer (KPB1) and three-layer (KPB3) kenaf stalk particleboards to explore the related mechanical properties of the two types of straw-based panels. The test results show that the static yield strength, internal bonding strength and elastic modulus of KPB3 are higher than those of KPB1, and the three-layer structure of the wood-based panel optimizes the end-face density distribution of the board and has the best comprehensive performance.
Xing et al. [90] used UF glue to make lightweight soybean straw particleboard, and analyzed the influence of board density, glue amount, hot pressing time and other factors on board performance. The test results show that the static yield strength and internal bonding strength of the board reach the maximum, and the thickness expansion rate of water absorption is the minimum when the temperature reaches 160 degrees Celsius. The mechanical properties of the light bean straw particleboard under different conditions are shown in Table 4.
Zhang et al. [91] studied the effect of fly ash content in cement on the performance of wheat straw board. The results showed that the main properties of the cement-wheat straw board decreased with the increase of fly ash content. The reason is that silicon and aluminum in fly ash can react with calcium hydroxide released from Portland cement under the action of water to form cementitious materials such as calcium silicate and calcium aluminate. However, if the amount of fly ash is large, it will affect the coagulation and hardening reaction of cement, thereby affecting the performance of cement wheat straw board.
Wang et al. [92] studied the effect of different cement additions on the properties of isocyanate (MDI) and urea-formaldehyde resin (UF) straw particleboard, especially the effect on the water absorption thickness expansion rate of the board. The results show that with the increase of cement addition, the water absorption thickness expansion rate of the board decreases. The water absorption thickness expansion rate of the straw particle board made of urea-formaldehyde resin adhesive reaches the highest when the cement addition amount reaches 10%.
Table 5 lists the mechanical performance parameters of different types of straw-based panels, including construction technology, density (ρ), static yield strength (MOR), internal bond strength (IB), and two-hour water absorption thickness swelling ratio (TS). The following conclusions can be drawn based on these statistical results:
(1) The main pressing method of straw-based panels is hot pressing, and the temperature of hot pressing also has a certain influence on the mechanical properties of the panels.
(2) The static yield strength and internal bonding strength of wheat straw particleboard are significantly higher than those of straw particleboard and kenaf straw particleboard under the same density. And the static yield strength of wheat straw particleboard reaches 31.2 MPa, which is much higher than the international standard of 14 MPa. The two-hour water absorption thickness swelling ratio is similar, and both are lower than the international standard 8. It shows that these types of straw-based panels all meet the requirements of high-quality products.
(3) Several mechanical property parameters of the light bean straw particleboard are lower than the international standard. This type of straw-based board solves the shortcomings of using a lot of materials and being self-heavy, but the mechanical properties cannot meet the requirements, and the specific application has limitations.
(4) The properties of cement straw particle board and cement wheat straw board are very different. Because the construction process of cement wheat straw board is cold pressing, the parameters in all aspects are relatively low. Therefore, the optimization and innovation of the hot-pressing process can be considered in the production process of straw-based panels.
To sum up, some progress has been made in the research and application of straw-based wood-based panels, and its production cost has gradually approached that of ordinary wood-based panels. Therefore, its application prospect in construction is considerable. However, the research on the preparation and modification mechanism of straw-based panels and their popularization and application is not deep enough. Author believes that there is still a lot of room for improvement in the research of straw-based wood-based panels in view of this.
Plant straw is rich in cellulose, hemicellulose and lignin, and its fiber structure is compact and has good toughness and tensile strength. Fig. 10 shows the microstructure of straw fibers. The unique material composition and microstructure of plant straw is a good choice for the development of functional building materials [93–96].
Figure 10: Effect of various factors on thermal diffusivity in moist and dry state [94]
Wei [93] explored the influencing factors of the thermal diffusivity of magnesium phosphate cement-based straw concrete through experiments. The test results show that the increase of the content of straw fiber can greatly reduce the thermal diffusivity and improve the thermal insulation performance. The increase of fly ash content can also improve the thermal insulation performance of straw concrete. The thermal diffusivity in wet and dry conditions is shown in Fig. 10.
Fig. 11 shows the microstructure of jute stalk fiber.
Figure 11: Microstructure of jute stalk fiber [94]
Parviz et al. [97] found that the gray matter obtained by incinerating rice husks contained relatively high activity of free silicon, and defined the activity of gray matter as a kind of gray matter that does not have or has less adhesiveness. But it will react with calcium hydroxide to form a sticky gel under certain conditions.
Biricik et al. [98] found that if the processed straw powder and straw strips (as shown in Fig. 12) were incinerated under low temperature conditions, the ash content of silica could reach 73%, and it had a certain pozzolanic activity. Adding it into concrete can improve the compression resistance of concrete. At the same time, different straw particle sizes have different effects on the mechanical properties of concrete.
Figure 12: Straw powder and straw strips [98]
Some scholars have found that injecting carbon dioxide gas during the mixing process can better improve the compatibility of fibers and cement, and improve the durability of concrete [99]. Farooqi et al. [100] found that centrifugal accelerated treatment of straw fibers can effectively improve the compatibility with cement and improve the internal structure of concrete. There have been many advances in the research of straw concrete, but the key point that hinders the development of straw concrete is that the plant straw contains a lot of hemicellulose, sugar and other substances, which are easy to be precipitated during the concrete mixing process.
Sun et al. [101] used corn straw to prepare a new type of energy-saving and environmentally friendly concrete, and designed mulching pretreatment. The test showed that the precipitation of sugar in the straw was effectively blocked after the treatment, and the molding of the concrete was ensured. Saraswathy et al. [102] pointed out that the compressive strength of concrete increased with the increase of the content of rice husk ash through the experimental study of rice husk ash concrete. The tensile strength of rice husk ash concrete showed a downward trend when the content of rice husk ash exceeded.
Feng et al. [103] studied the mechanical properties of concrete by adding highland barley straw ash (HBSA) to the concrete. The test results show that the content of HBSA affects the compressive strength of concrete by affecting the microstructure of concrete. The concrete with 15% HBSA had the strongest mechanical properties because the addition of HBSA changed the composition of hydration products and optimized the pore structure of the concrete.
Zhang et al. [104] carried out the incorporation of straw ash into reinforced concrete structures to study the compressive strength and corrosion resistance of concrete. The schematic diagram of the test is shown in Fig. 13.
Figure 13: Schematic diagram of the test [104]
The test results show that the bonding ability of steel bar and concrete will increase with the increase of straw ash content, and the compressive strength will also increase. The corrosion resistance of concrete will also increase. The straw ash concrete under the microscope structure is shown in Fig. 14.
Figure 14: Microstructure of straw ash concrete [104]
To sum up, the key to the development of straw concrete is to solve the problem of compatibility between straw fibers and cement. Although certain treatment methods have been proposed at present, there are still problems such as complicated processes, labor-intensive and material-intensive, unsuitable for large-scale production and certain toxic and side effects of the added chemicals. How to improve the compatibility of fiber and cement will still be the focus and difficulty of straw concrete research in the future.
6 Application of Oyster Mushroom Cultivation
Making full use of crop straw can not only realize the recycling of agricultural resources, but also reduce the degree of environmental pollution in rural areas. The straw fungus industry has obvious economic benefits, social benefits and ecological benefits, and also has the advantages of high efficiency, quick effect, low technical requirements and low cost. It is an important model of circular agriculture [105].
Nikolay et al. [106] found that adding straw powder to a petri dish can accelerate the absorption of selenium by mushrooms, thereby improving the vitality and yield of mushroom species. The growth process of oyster mushroom can be divided into four stages, which are the growth stage, the coral stage, the forming stage and the mature stage.
Luo et al. [107] used grape cuttings as the main raw material for cultivating oyster mushrooms, and used the method of bottle planting to prepare 7 formulas for cultivating oyster mushrooms by changing the proportion of grape cuttings in the medium. The test results showed that the different contents of grape twigs had different effects on the growth rate and biological efficiency of oyster mushroom mycelium. The mushrooms cultivated have the best taste, the highest yield, and the biological efficiency can reach 89.5% when the raw materials are 78% grape branches, 20% bran, 1% gypsum and 1% superphosphate. Therefore, it is feasible to cultivate oyster mushrooms with grape branches as the main raw material.
Singh et al. [108] designed to study its effect on mushroom yield by adding different kinds of straw raw materials to the petri dish. The specific test process is shown in Fig. 15. The test results show that the wheat straw added with wheat bran is the best substrate for the growth of oyster mushroom, the highest yield per pack can reach 91.9%, and the growth cycle and ripening time are also shortened.
Figure 15: Production of mushrooms [108]. (a) Saw dust + Wheat Bran (b) Wheat straw + Wheat Bran (c) Paddy straw + Wheat Bran (d) Saw dust (e) Wheat straw (f) Paddy straw
Che et al. [109] used pepper stalks as the raw material for cultivating oyster mushrooms. The result showed that oyster mushrooms cultivated with pepper stalks had the advantages of fast mycelium growth, short production cycle, low bacterial bag pollution rate and high biological efficiency. It shows that the pepper stalk can completely replace the sawdust for the production of oyster mushroom, and it will be an ideal new material for the production of oyster mushroom.
Zhang et al. [110] studied the yield of oyster mushroom grown on rice straw and wheat straw. The test results showed that the yield of oyster mushrooms grown on wheat straw was 10% higher than that of rice straw. At the same time, the ground straw material can reduce the growth cycle of mushrooms, but the yield of mushrooms will decrease when the straw is crushed into too small particles.
To sum up, the traditional culture medium for oyster mushroom cultivation has high quality and high biological efficiency, but the production cost is also high. Predecessors have done a lot of exploration in combination with the characteristics of crop straw to improve agricultural economic benefits. The cultivation of oyster mushrooms using different types of crop straws as medium raw materials has achieved certain results, but this is far from enough. Whether more different types of crop straws can be excavated and utilized or several kinds of crop straws with different textures can be mixed to replace the traditional culture material needs further research and discussion in the future.
7.1 The Main Ways of Returning Straw to the Field
Straw returning technology is an effective means to maintain soil organic matter content, increase biological activity, improve soil physical properties, and increase nutrient availability [111,112].
There are two ways of straw returning to the field, including direct returning and indirect returning [113]. The direct return to the field is relatively simple, convenient and fast, which can greatly reduce the labor and the effect of increasing production is also good. In recent years, farmers have mainly returned straw directly to the field. The commonly used methods of returning straw to the field include mulching and no-tillage, crushing and pressing, and direct cover. In some areas, straw is indirectly returned to the field through high-temperature composting, belly-crossing, and circle-returning. Turning and returning to the field [114] means that the crop straws are mechanically pulverized, spread evenly in the field, and then ploughed, and directly pressed into the soil, so that the nutrients of the straw can be fully retained in the soil. Straw mulching refers to crushing the straw and covering it directly on the surface, which can reduce the evaporation of soil water and increase the content of soil organic matter after rotting, but this will bring inconvenience to irrigation and seriously affect the planting of crops. Fig. 16 shows straw particles.
Figure 16: Straw particles [114]
7.2 Effect of Straw Returning to the Field
Wu et al. [115] found that the degradation of organic pollutants in paddy fields was affected by water-soluble soil organic matter (WSOM). It was concluded that the photosensitive effect of WSOM could be adjusted by straw returning technology through spectral and steady-state photodegradation tests, thereby increasing the concentration of WSOM to degrade organic pollutants.
Zhang et al. [116] conducted a straw returning experiment in the Loess Plateau. The experiment was divided into three groups. The schematic diagram of the specific test is shown in Fig. 17. The first group had no straw at the bottom, the second group had full straw laying at the bottom, and the third group had half straw laying at the bottom. Each group had nitrogen fertilizer at the bottom of the experimental farmland. The experimental results show that the combination of laying straw at the bottom and nitrogen fertilizer can improve the soil water and heat conditions, and improve the water use efficiency, nitrogen absorption efficiency and corn yield. It can be concluded that straw returning technology is an effective measure for the sustainable development of farmland in semi-arid areas.
Figure 17: Three types of farmlands [116]
Liu et al. [117] took rape straw as the research object and targeted the rice yield in the current season, and found that the rice yield of all treatments with rape straw was increased. Liu found that straw returning to the field can significantly increase the yield of rice and wheat by taking the rice-wheat double-cropping system as the research object, and using Meta analysis to collect and organize the literature for nearly 20 years. Returning rice straw to the field significantly reduced wheat yield in the lower reaches of the Yangtze River, while in the middle and upper reaches of the Yangtze River, returning rice straw to the field significantly increased wheat yield. In the Yangtze River Basin, the return of wheat straw to the field significantly increased rice yield [118].
Studies have shown that returning straw to the field can increase the sequestration of soil organic carbon. The research of Mitchell et al. [119] believed that the return of straw to the field leads to the excitation effect of existing soil organic carbon, which offsets the soil organic carbon derived from straw. Zhang et al. [120] believed that although straw returning to the field would increase the loss of the original organic carbon in the soil through the excitation effect of organic carbon, and the straw returning to the field played an important role in increasing the soil organic carbon storage. Straw-derived SOC gains outweighed SOC losses, and leading to an increase in the net accumulation of SOC after straw addition [121]. The net effect of straw returning on soil organic carbon sequestration was closely related to fertilization. Organic carbon sequestration was highest in NPK-fertilized soils and lowest in unfertilized soils [122].
In summary, straw returning to the field can not only promote the nutrient absorption of crops, but also improve the nutrient structure of the soil and reduce the loss of soil water and increase the organic matter in the soil. Straw returning to the field can also provide better breeding conditions for microorganisms. Improving the biological activity of the soil by increasing the number of microorganisms in the soil, but also pay attention to the prevention of diseases and insect pests. There will be some differences in the thinking of straw returning to the field according to different soil environments, but the overall impact on crop yield is still positive.
Straw is the stem and leaf part of mature crops, most of which are discarded and burned at will. Such behavior not only causes air pollution, but also wastes the effective use of renewable resources and affects the ecological environment. In response to this problem, various scholars have carried out a lot of research and exploration from the aspects of technology and application, and the effect is remarkable. Cellulose, hemicellulose and lignin are separated from the fractional technology of straw and these substances are reused. Straw is used in combination with agriculture, industry and construction, which not only protects the environment but also effectively solves the problem of energy shortage. At the same time, it can also alleviate the problem of energy shortage in rural areas, and crop straw can further promote agricultural development as a fertilizer. The maturity of straw-based wood-based panel technology provides a new industrial development idea for reducing the deforestation of forest wood resources and protecting the ecological environment. The construction of civilization system has played a positive role.
In general, scholars attach great importance to the research on the comprehensive utilization of straw, and have continuously achieved corresponding results. This also points out the direction for the comprehensive utilization of straw, and also allows us to see the broad prospects for the utilization of straw resources.
However, scholars’ research on comprehensive utilization of straw has not yet formed a systematic and complete system. The research mainly focuses on agriculture, and the economic aspect is relatively small, and the knowledge of other disciplines is not well combined with the comprehensive utilization of straw. In general, the analysis is not systematic and complete. Therefore, we can consider in-depth understanding of the characteristics and mechanical properties of different crop straws, and optimize more scientific and reasonable straw crushing and returning devices or straw recycling devices. According to the internal elements of straw, straw-based wood-based panels with better performance are manufactured, and strive to be applied to building structures as soon as possible. Providing economic support and hardware environment for the comprehensive utilization and sustainable development of crop straw. Promoting the application of the results actively, and constantly update and improve in practice.
Funding Statement: The research work presented in this paper is supported by the National Natural Science Foundation of China (Nos. 51878354 & 51308301), the Natural Science Foundation of Jiangsu Province (Nos. BK20181402 & BK20130978), and Qinglan Project of Jiangsu Higher Education Institutions. Any research results expressed in this paper are those of the writer(s) and do not necessarily reflect the views of the foundations.
Conflicts of Interest: The authors declare that they have no conflicts of interest to report regarding the present study.
References
1. Zhang, Y., Gu, J., Tan, H., Zhang, Y., Zhu, L. et al. (2011). Straw based particleboard bonded with composite adhesives. BioResources, 6(1), 464–476. DOI 10.15376/biores. [Google Scholar] [CrossRef]
2. El-Kassas, A. M., Mourad, A. I. (2013). Novel fibers preparation technique for manufacturing of rice straw-based fiberboards and their characterization. Materials & Design, 50, 757–765. DOI 10.1016/j.matdes.2013.03.057. [Google Scholar] [CrossRef]
3. Belini, U. L., Tomazello Filho, M., Louzada, J. L. P. C., Rodrigues, J. C. D. C., Astolphi, J. R. S. (2012). Pilot study for MDF manufacture from sugarcane bagasse and eucalyptus fibers. European Journal of Wood and Wood Products, 70(4), 537–539. DOI 10.1007/s00107-011-0577-4. [Google Scholar] [CrossRef]
4. Çöpür, Y., Güler, C., Taşçıoğlu, C., Tozluoğlu, A. (2008). Incorporation of hazelnut shell and husk in MDF production. Bioresource Technology, 99(15), 7402–7406. DOI 10.1016/j.biortech.2008.01.021. [Google Scholar] [CrossRef]
5. Aisyah, H. A., Paridah, M. T., Sahri, M. H., Anwar, U. M. K., Astimar, A. A. (2013). Properties of medium density fibreboard (MDF) from kenaf (Hibiscus cannabinus L.) core as function of refining conditions. Composites Part B: Engineering, 44(1), 592–596. DOI 10.1016/j.compositesb.2012.02.029. [Google Scholar] [CrossRef]
6. Kirchherr, J., Reike, D., Hekkert, M. (2017). Conceptualizing the circular economy: An analysis of 114 definitions. Resources, Conservation and Recycling, 127, 221–232. DOI 10.1016/j.resconrec.2017.09.005. [Google Scholar] [CrossRef]
7. He, Y., Ding, Y., Mohrmann, S., Wang, Z. (2022). Experimental and finite element method study on dynamic characteristics of beam-column glulam frame structure. Advances in Structural Engineering, 13694332221107577. DOI 10.1177/13694332221107577. Published Online. [Google Scholar] [CrossRef]
8. Migliore, M., Talamo, C., Paganin, G. (2020). Construction and demolition waste. In: strategies for circular economy and cross-sectoral exchanges for sustainable building products, pp. 45–76. Cham: Springer. DOI 10.1007/978-3-030-30318-1_2. [Google Scholar] [CrossRef]
9. Deselnicu, D. C., Militāru, G., Deselnicu, V., Zăinescu, G., Albu, L. (2018). Towards a circular economy–a zero waste programme for Europe. International Conference on Advanced Materials and Systems (ICAMS), pp. 563–568. Romania, The National Research & Development Institute for Textiles and Leather-INCDTP. DOI 10.24264/icams-2018.XI.4. [Google Scholar] [CrossRef]
10. Sikora, A., Gaff, M., Németh, R. (2021). Properties of wood-based composites manufactured of densified beech wood in viscoelastic and plastic region force-deflection diagram (FDD). Reviews on Advanced Materials Science, 60, 702–718. DOI 10.1515/rams-2021-0053. [Google Scholar] [CrossRef]
11. Gaff, M., Kačik, F., Sandberg, D., Turčani, M., Niemz, P. et al. (2019). The effect of chemical changes during thermal modification of European oak and Norway spruce on elasticity properties. Composite Structures, 220, 529–538, DOI 10.1016/j.compstruct.2019.04.034. [Google Scholar] [CrossRef]
12. Gaff, M., Babiak, M., Kačik, F., Sandberg, D., Turčani, M. et al. (2019). Plasticity properties of thermally modified timber in bending–the effect of chemical changes during modification of European oak and Norway spruce. Composites Part B: Engineering, 165, 613–625. DOI 10.1016/j.compositesb.2019.02.019. [Google Scholar] [CrossRef]
13. Chen, S., Zhou, Y. H., Sarah, M. (2022). Acoustics performance research and analysis of light timber construction wall elements based on helmholtz metasurface. Journal of Renewable Materials, 10, 2791–2803. DOI 10.32604/jrm.2022.021531. [Google Scholar] [CrossRef]
14. Hysek Š., Gaff, M., Sikora, A., Babiak, M. (2018). New composite material based on winter rapeseed and his elasticity properties as a function of selected factors. Composites Part B: Engineering, 153, 108–116. DOI 10.1016/j.compositesb.2018.07.042. [Google Scholar] [CrossRef]
15. Cao, Z., Huang, Y., Hao, J. (2018). Multi-suitability comprehensive evaluation of crop straw resource utilization in China. Research of Environmental Sciences, 31(1), 179–186. DOI 10.1016/j.jclepro.2021.125958. [Google Scholar] [CrossRef]
16. Gu, X., Liu, K., Gao, J., Liu, L. J. (2022). Research progress on water-saving irrigation technology and its impact on rice yield. Hybrid Rice, 37(2), 7–13. DOI 10.16267/j.cnki.1005-3956.20210715.256. [Google Scholar] [CrossRef]
17. On the “l4th Five-Year Plan” Guidance on the comprehensive utilization of bulk solid waste (2021). National Development and Reform Commission of the People’s Republic of China. https://www.ndrc.gov.cn/xxgk/zcfb/tz/202103/t202103241270286.html. [Google Scholar]
18. Wang, M., Yin, C. X., Cheng, J. L. (2021). Application of AHP-FCE evaluation on the pulping and papermaking water pollution control technology. Journal of Forestry Engineering, 6(4), 107–113. DOI 10.13360/j.issn.2096-1359.202007017. [Google Scholar] [CrossRef]
19. van Soest, P. J., Robertson, J. B., Hall, M. B. (2020). Klason lignin is a nutritionally heterogeneous fraction unsuitable for the prediction of forage neutral-detergent fibre digestibility in ruminants. British Journal of Nutrition, 124(7), 693–700. DOI 10.1017/S0007114520001713. [Google Scholar] [CrossRef]
20. Wang, F., Kang, L., Ji, R., Liu, T., Yu, Q. et al. (2022). A novel magnetic carbon-based catalyst synthesized from reed straw and electric furnace dust for biodiesel production. Journal of Renewable Materials, 10(8), 2099–2115. DOI 10.32604/jrm.2022.018806. [Google Scholar] [CrossRef]
21. Liu, L., Ren, J. W., Liu, X. L. (2021). Properties and applications of lignosulfonate from wheat straw spent liquor pretreated by magnesium bisulfite. Journal of Forestry Engineering, 6(3), 93–99. DOI 10.13360/j.issn.2096-1359.202009019. [Google Scholar] [CrossRef]
22. Yang, S., Fu, Y. J., Yan, T. T. (2021). Effect of high temperature heat-treatment on the chemical properties of swietenia macrophylla. Journal of Forestry Engineering, 6(2), 120–125. DOI 10.13360/j.issn.2096-1359.202006016. [Google Scholar] [CrossRef]
23. Zhou, Y. H., Shen, Z. Y., Li, H. T. (2022). Study on in-plane shear failure mode of cross-laminated timber panel. Journal of Wood Science, 68, 36. DOI 10.1186/s10086-022-02045-2. [Google Scholar] [CrossRef]
24. Zhou, K., Li, H. T., Assima, D., Yang, D., Xiong, Z. H. et al. (2022). Slenderness ratio effect on the eccentric compression performance of chamfered laminated bamboo lumber columns. Journal of Renewable Materials, 10(1), 165–182. DOI 10.32604/jrm.2021.017223. [Google Scholar] [CrossRef]
25. Jian, B. Y., Cheng, K., Li, H. T., Mahmud, A., Zheng, X. Y. (2022). A review on strengthening of timber beams using fiber reinforced polymers. Journal of Renewable Materials, 10(8), 2073–2098. DOI 10.32604/jrm.2022.021983. [Google Scholar] [CrossRef]
26. Martelli-Tosi, M., Assis, O. B., Silva, N. C. (2017). Chemical treatment and characterization of soybean straw and soybean protein isolate/straw composite films. Carbohydrate Polymers, 157, 512–520. DOI 10.1016/j.carbpol.2016.10.013. [Google Scholar] [CrossRef]
27. Chen, Y. H., Tian, F. Y., Yan, Y. F., Song, Z. H., Li, F. D. et al. (2018). Existing problems and development suggestions of comprehensive utilization of crop straw. Chinese Journal of Agricultural Machinery, 39(2), 67–73. [Google Scholar]
28. Zhang, F., Zhang, L., Qi, C. S., Zhang, Y., Mu, J. (2017). Effects of pretreatment methods on the properties of corn straw wood-based panels. Journal of Beijing Forestry University, 39(9), 112–118. DOI 10.13332/j.1000-1522.20170069. [Google Scholar] [CrossRef]
29. Han, L. J., Yan, Q. J., Liu, X. Y. (2002). China’s crop straw resources and their utilization status. Chinese Journal of Agricultural Engineering, 18(3), 87–91. [Google Scholar]
30. Wang, X. H., Feng, Z. M. (2004). Biofuel use and its environmental problems in rural areas of China. Journal of Nanjing Agricultural University, 27(1), 108–110 (in Chinese). [Google Scholar]
31. Zhao, X. L., Yuan, G. Y., Wang, H. Y. (2019). Effects of full straw incorporation on soil fertility and crop yield in rice-wheat rotation for silty clay loamy cropland. Agronomy, 9(3), 133. DOI 10.3390/agronomy9030133. [Google Scholar] [CrossRef]
32. Abdel-Mohdy, F. A., Abdel-Halim, E. S., Abu-Ayana, Y. M. (2009). Rice straw as a new resource for some beneficial uses. Carbohydrate Polymers, 75(1), 44–51. DOI 10.1016/j.carbpol.2008.06.002. [Google Scholar] [CrossRef]
33. Wang, X. D., Zhuang, J. J., Liu, B. Y., Li, S. S., Zhao, X. et al. (2020). Residue returning induced changes in soil organic carbon and the influential factors in China’s croplands, a meta-analysis. Journal of China Agricultural University, 25(8), 12–24 (in Chinese). [Google Scholar]
34. Nagpal, R., Bhardwaj, N. K., Mishra, O. P. (2021). Cleaner bio-pulping approach for the production of better strength rice straw paper. Journal of Cleaner Production, 318, 128539. DOI 10.1016/j.jclepro.2021.128539. [Google Scholar] [CrossRef]
35. Shahryari, Z., Fazaelipoor, M. H., Setoodeh, P. (2018). Utilization of wheat straw for fungal phytase production. International Journal of Recycling of Organic Waste in Agriculture, 7(4), 345–355. DOI 10.1007/s40093-018-0220-z. [Google Scholar] [CrossRef]
36. Song, Y., Wang, Z., Zhang, X., Zhang, R., Li, J. (2021). Synthetic process of bio-based phenol formaldehyde adhesive derived from demethylated wheat straw alkali lignin and its curing behavior. Journal of Renewable Materials, 9(5), 943. DOI 10.32604/jrm.2021.014131. [Google Scholar] [CrossRef]
37. Zheng, X. X., Zhao, Y. T., Pan, B. (2021). Extraction, distribution and composition of tannin in picea sitchensis. Journal of Forestry Engineering, 6(2), 108–113. DOI 10.13360/j.issn.2096-1359.202007026. [Google Scholar] [CrossRef]
38. Sun, R. C., Xu, F. (2008). Separation and high-value utilization of biomass components in agriculture and forestry. Bioindustry Technology, (1), 46–52. [Google Scholar]
39. Zhao, T., Hui, L. F., Liu, Z. (2012). Research status and development of lignocellulosic raw material component separation technology. Tianjin Paper, (4), 16–20. [Google Scholar]
40. Amarasekara, A. S., Owereh, O. S. (2009). Hydrolysis and decomposition of cellulose in brönsted acidic ionic liquids under mild conditions. Industrial & Engineering Chemistry Research, 48(22), 10152–10155. DOI 10.1021/ie901047u. [Google Scholar] [CrossRef]
41. Chen, H. Z., Liu, Z. H. (2014). Multilevel composition fractionation process for high-value utilization of wheat straw cellulose. Biotechnology for Biofuels, 7(1), 137. DOI 10.1186/s13068-014-0137-3. [Google Scholar] [CrossRef]
42. Passoth, V., Sandgren, M. (2019). Biofuel production from straw hydrolysates, current achievements and perspectives. Applied Microbiology and Biotechnology, 103(13), 5105–5116. DOI 10.1007/s00253-019-09863-3. [Google Scholar] [CrossRef]
43. Peralta-Yahya, P. P., Zhang, F., Del Cardayre, S. B. (2012). Microbial engineering for the production of advanced biofuels. Nature, 488(7411), 320–328. DOI 10.1038/nature11478. [Google Scholar] [CrossRef]
44. Bhatia, S. K., Jagtap, S. S., Bedekar, A. A. (2020). Recent developments in pretreatment technologies on lignocellulosic biomass, effect of key parameters, technological improvements, and challenges. Bioresource Technology, 300, 122724. DOI 10.1016/j.biortech.2017.12.026. [Google Scholar] [CrossRef]
45. Li, J., Zhang, S., Li, H. (2018). Cellulase pretreatment for enhancing cold caustic extraction-based separation of hemicelluloses and cellulose from cellulosic fibers. Bioresource Technology, 251, 1–6. DOI 10.1016/j.biortech.2017.12.026. [Google Scholar] [CrossRef]
46. Li, M. F., Yang, S., Sun, R. C. (2016). Recent advances in alcohol and organic acid fractionation of lignocellulosic biomass. Bioresource Technology, 200, 971–980. DOI 10.1016/j.biortech.2017.12.026. [Google Scholar] [CrossRef]
47. Leonowicz, A., Matuszewska, A., Luterek, J. (1999). Biodegradation of lignin by white rot fungi. Fungal Genetics and Biology, 27(2), 175–185. DOI 10.1006/fgbi.1999.1150. [Google Scholar] [CrossRef]
48. Francisco, M., van den Bruinhorst, A., Kroon, M. C. (2012). New natural and renewable low transition temperature mixtures (LTTMsScreening as solvents for lignocellulosic biomass processing. Green Chemistry, 14(8), 2153–2157. DOI 10.1039/c2gc35660k. [Google Scholar] [CrossRef]
49. Yuan, Z., Kapu, N. S., Beatson, R. (2016). Effect of alkaline pre-extraction of hemicelluloses and silica on kraft pulping of bamboo (Neosinocalamus affinis keng). Industrial Crops and Products, 91, 66–75. DOI 10.1016/j.indcrop.2016.06.019. [Google Scholar] [CrossRef]
50. Yan, X., Cheng, J. R., Wang, Y. T. (2020). Enhanced lignin removal and enzymolysis efficiency of grass waste by hydrogen peroxide synergized dilute alkali pretreatment. Bioresource Technology, 301, 122756. DOI 10.1016/j.biortech.2020.122756. [Google Scholar] [CrossRef]
51. Ma, X. J., Yang, X. F., Zheng, X. (2014). Degradation and dissolution of hemicelluloses during bamboo hydrothermal pretreatment. Bioresource Technology, 161, 215–220. DOI 10.1016/j.biortech.2014.03.044. [Google Scholar] [CrossRef]
52. Haimer, E., Wendland, M., Potthast, A. (2010). Controlled precipitation and purification of hemicellulose from DMSO and DMSO/water mixtures by carbon dioxide as anti-solvent. The Journal of Supercritical Fluids, 53(1), 121–130. DOI 10.1016/j.supflu.2010.02.009. [Google Scholar] [CrossRef]
53. Sun, X. F., Sun, R., Fowler, P., Baird, M. S. (2005). Extraction and characterization of original lignin and hemicelluloses from wheat straw. Journal of Agricultural and Food Chemistry, 53(4), 860–870. DOI 10.1021/jf040456q. [Google Scholar] [CrossRef]
54. Yan, L. C. (2017). Process research on the conversion of rice straw hemicellulose to xylose and xylitol. Sichuan, China: Southwest Jiaotong University. https://kns.cnki.net/KCMS/detail/detail.aspx?dbname=CMFD201702&filename=1017124990.nh. [Google Scholar]
55. Lapierre, C., Monties, B., Rolando, C. (1985). Thioacidolysis of lignin, comparison with acidolysis. Journal of Wood Chemistry and Technology, 5(2), 277–292. DOI 10.1080/02773818508085193. [Google Scholar] [CrossRef]
56. Chen, X., Li, H., Sun, S. (2018). Co-production of oligosaccharides and fermentable sugar from wheat straw by hydrothermal pretreatment combined with alkaline ethanol extraction. Industrial Crops and Products, 111, 78–85. DOI 10.1016/j.indcrop.2017.10.014. [Google Scholar] [CrossRef]
57. Chistyakov, A. V., Tsosikov, M. V. (2018). Methods for preparing carbon sorbents from lignin. Russian Journal of Applied Chemistry, 91(7), 1090–1105. DOI 10.1134/S1070427218070054. [Google Scholar] [CrossRef]
58. Chen, C., Li, H. T., Assima, D. (2022). Properties and applications of bamboo fiber—A current-state-of-the art. Journal of Renewable Materials, 10(3), 605–624. DOI 10.32604/jrm.2022.018685. [Google Scholar] [CrossRef]
59. N’diaye, S., Rigal, L. (2000). Factors influencing the alkaline extraction of poplar hemicelluloses in a twin-screw reactor, correlation with specific mechanical energy and residence time distribution of the liquid phase. Bioresource Technology, 75(1), 13–18. DOI 10.1016/S0960-8524(00)00032-8. [Google Scholar] [CrossRef]
60. Liu, X. (2020). Research on separation and classification of corn straw components. South China University of Technology, Guangdong, China. DOI 10.27151/d.cnki.ghnlu.2020.004865. [Google Scholar] [CrossRef]
61. Tu, D. Y., Chen, C. F., Zhou, Q. F. (2021). Research progress of thermo-mechanical compression techniques for wood products. Journal of Forestry Engineering, 6(1), 13–20. DOI 10.13360/j.issn.2096-1359.202001036. [Google Scholar] [CrossRef]
62. Bowyer, J. L., Stockmann, V. E. (2001). Agricultural residues: An exciting bio-based raw material for the global panels industry. Forest Products Journal, 51(1), 10–21. [Google Scholar]
63. Assima, D., Li, H. T., Xiong, Z. H., Rodolfo, L. (2021). A review of mechanical behavior of structural laminated bamboo lumber. Sustainable Structures, 1(1), 000004. DOI 10.54113/j.sust.2021.000004. [Google Scholar] [CrossRef]
64. Su, J. W., Li, H. T., Xiong, Z. H., Rodolfo, L. (2021). Structural design and construction of an office building with laminated bamboo lumber. Sustainable Structures, 1(2), 000010. DOI 10.54113/j.sust.2021.000010. [Google Scholar] [CrossRef]
65. Felice, C. P., Di, C. A., Lamarucciola, N., Domenico, N. (2021). Experimental estimation of energy dissipated by multistorey post-tensioned timber framed buildings with anti-seismic dissipative devices. Sustainable Structures, 1(2), 000007. DOI 10.54113/j.sust.2021.000007. [Google Scholar] [CrossRef]
66. Zhou, Y. H., Huang, Y. J., Usama, S., Wang, Z. (2021). Research on dynamic characteristics test of wooden floor structure for gymnasium. Sustainable Structures, 1(1), 000005. DOI 10.54113/j.sust.2021.000005. [Google Scholar] [CrossRef]
67. Chen, G., Yin, M., Wu, X. Wang, Z., Jiang, H. (2021). Structural performance of laminated-bamboo lumber nailed connection. Wood Material Science & Engineering, 1–13. DOI 10.1080/17480272.2021.1983872. [Google Scholar] [CrossRef]
68. Chen, G., Wu, X. T., Jiang, H., Wang, Z. J., Yin, M. Y. (2022). Cyclic response of laminated bamboo lumber nailed connection: Theoretical modelling and experimental investigations. Structures, 35, 118–131. DOI 10.1016/j.istruc.2021.10.086. [Google Scholar] [CrossRef]
69. Meng, X. M., Zhang, D. B., Feng, P., Hu, N. (2021). Review on mechanical behavior of solar cells for building integrated photovoltaics. Sustainable Structures, 1(2), 000009. DOI 10.54113/j.sust.2021.000009. [Google Scholar] [CrossRef]
70. Zhou, D. G., Zhang, Y. (2007). The formation and development of my country’s crop straw material industry. Wood Industry, 1, 5–8. DOI 10.19455/j.mcgy.2007.01.002. [Google Scholar] [CrossRef]
71. Zhou, D. G., Zhang, Y., Yu, W. J. (2003). Manufacturing technology and industrialization of high- and medium-density rice-straw wood-based panels: Basic technology research. Forest Products Industry, 30(4), 17–21. DOI 10.19531/j.issn1001-5299.2003.04.005. [Google Scholar] [CrossRef]
72. Zhou, Y. H., He, Y. H., Shen, Z. Y. (2022). Research on dynamic and static test methods for evaluating the poisson’s ratio of oriented strand board. Journal of Renewable Material, 10(12), 3459–3476. DOI 10.32604/jrm.2022.021251. [Google Scholar] [CrossRef]
73. Chen, G., Yang, W., Zhou, T. (2021). Experiments on laminated bamboo lumber nailed connections. Construction and Building Materials, 269, 121321. DOI 10.1016/j.conbuildmat.2020.121321. [Google Scholar] [CrossRef]
74. Hse, C. Y., Shupe, T. F. (2002). utilization of agricultural waste for composite panels for composite panel. The 6th Pacific Rim Bio-Based Composites Symposium & Workshop on the Chemical Modification of Cellulosics, Portland. [Google Scholar]
75. Urve, K., Hele, J., Targo, K., Lembit, K. (2017). Assessment of durability of environmentally friendly wood-based panels. Energy Procedia, 132, 207–212. DOI 10.1016/j.egypro.2017.09.756. [Google Scholar] [CrossRef]
76. Rowell, R. M. (1996). Composites from agric-based resources. Proceedings of the Use of Recycled Wood and Paper in Building Applications. pp. 217–222, 7286. WI, USA, Madison, Forest Product Society. [Google Scholar]
77. Loxton, C., Hague, J. (1996). Utilization of agricultural crop materials in panel product. Proceedings of theUse of Recycled Wood and Paper in Building Applications. pp. 190–192, 7286. WI, USA, Madison, Forest Product Society. [Google Scholar]
78. Jin, G. G. (2019). Experiment on hot pressing molding parameters of corn straw wood-based panels. Shenyang Agricultural University, Liaoning, China. DOI 10.27327/d.cnki.gshnu.2019.001054. [Google Scholar] [CrossRef]
79. Sören, H., Håkan, E., Magnus, N. (2008). Properties of medium-density fibreboard (MDF) based on wheat straw and melamine modified urea formaldehyde (UMF) resin. Industrial Crops and Products, 28, 37–46. DOI 10.1016/j.indcrop.2008.01.005. [Google Scholar] [CrossRef]
80. Li, P., Zuo, Y. F., Wu, Y. Q., Zhao, X., Wang, J. (2019). Research progress on the manufacture and application of straw-based wood-based panels. Materials Review, 33(15), 2624–2630. [Google Scholar]
81. Halvarsson, S., Edlund, H., Norgren, M. (2009). Manufacture of non-resin wheat straw fibreboards. Industrial Crops and Products, 29, 437–445. DOI 10.1016/j.indcrop.2008.08.007. [Google Scholar] [CrossRef]
82. Shi, L. Y., Zhang, H. B., Li, Z. X. (2018). Analysis of moisture buffering effect of straw-based board in civil defence shelters by field measurements and numerical simulations. Building and Environment, (143), 366–377. DOI 10.1016/j.buildenv.2018.07.018. [Google Scholar] [CrossRef]
83. Naima, B., Dashnor, H., Brahim, I. (2017). Impact of fiber treatment on the fire reaction and thermal degradation of building insulation straw composite. Energy Procedia, 139, 544–549. DOI 10.1016/j.egypro.2017.11.251. [Google Scholar] [CrossRef]
84. Zhang, Y., Hua, D., Li, J., Liu, X. K. (2000). Research on the influence of hot-pressing process of wheat straw particleboard on the basic properties of finished products. Forest Products Industry, (2), 23–24. DOI 10.19531/j.issn1001-5299.2000.02.007. [Google Scholar] [CrossRef]
85. Zhang, Y., Hua, Y. K. (2001). Process research on modified UF wheat straw homogeneous particleboard. Forest Products Industry, (6), 15–18. DOI 10.19531/j.issn1001-5299.2001.06.005. [Google Scholar] [CrossRef]
86. Mo, X. Q., Cheng, E. Z., Wang, D. H., Sun, X. S. (2003). Physical properties of medium-density wheat straw particleboard using different adhesives. Industrial Crops and Products, (18), 47–53. DOI 10.1016/S0926-6690(03)00032-3. [Google Scholar] [CrossRef]
87. Xu, X. W., Wu, Q. L., Zhou, D. G., Zhou, X. Y. (2003). Study on modified isocyanate adhesive straw particleboard. Journal of Nanjing Forestry University (Natural Science Edition), (3), 21–25. [Google Scholar]
88. Xu, X. W., Wu, Q. L., Zhou, D. G., Zhou, X. Y. (2003). Moisture absorption characteristics of modified isocyanate straw particleboard. Forest Products Industry, (3), 18–21+52. DOI 10.19531/j.issn1001-5299.2003.03.005. [Google Scholar] [CrossRef]
89. Xu, X. W., Wu, Q. L., Zhou, D. G. (2004). Laboratory research on kenaf stalk particleboard (I)—the effect of slab structure on board properties. Forest Products Industry, (3), 28–31. DOI 10.19531/j.issn1001–5299.2004.03.008. [Google Scholar] [CrossRef]
90. Xing, C., Yin, S., Deng, Y. H. (1999). Research on the technology of light bean straw particleboard. Wood Industry, (6), 7–9. DOI 10.19455/j.mcgy.1999.06.002. [Google Scholar] [CrossRef]
91. Zhang, Y. (2000). Technology research of cement wheat straw board. Building Artificial Board, (1), 20–22. [Google Scholar]
92. Wang, J. B., Zhang, K. F., Zhang, T., Feng, T. T., Wu, C. (2018). Application of wheat straw in cement-based composite materials. Materials Review, 32(S1), 466–468+474. [Google Scholar]
93. Wei, Y. Q. (2020). Experimental study on physical mechanics and thermal properties of plant straw concrete. Shanghai Jiaotong University, Shanghai, China. DOI 10.27307/d.cnki.gsjtu.2020.000942. [Google Scholar] [CrossRef]
94. Vavřínová, N., Stejskalová, K., Teslík, J., Kubenková, K., Majer, J. (2022). Research of mechanical and thermal properties of composite material based on gypsum and straw. Journal of Renewable Materials, 10(7), 1859. DOI 10.32604/jrm.2022.018908. [Google Scholar] [CrossRef]
95. Mahmud, A., Mohammad, J. H., Safat, A. D. (2021). Semi-rigid behaviour of stainless-steel beam-to-column bolted connections. Sustainable Structures, 1(1), 000002. DOI 10.54113/j.sust.2021.000002. [Google Scholar] [CrossRef]
96. Liang, R. F., Hota, G. (2021). Development and evaluation of load-bearing fiber reinforced polymer composite panel systems with tongue and groove joints. Sustainable Structures, 1(2), 000008. DOI 10.54113/j.sust.2021.000008. [Google Scholar] [CrossRef]
97. Parviz, S., Fadhel, A., Habibur, C., Ali, N., Ghulam, S. (2004). Cement-bonded straw board subjected to accelerated processing. Cement and Concrete Composites, 26, 797–802. DOI 10.1016/j.cemconcomp.2003.06.001. [Google Scholar] [CrossRef]
98. Bricik, H., AK, Z. F., Berktay, I. (1999). Study of pozzolanic properties of wheat straw ash. Cement and Concrete Research, 29, 637–643. DOI 10.1016/S0008-8846(98)00249-X. [Google Scholar] [CrossRef]
99. Sarigahuti, M., Shah, S. P., Vinson, K. D. (1993). Shrinkage cracking and durability characteristics of cellulose fiber reinforced concrete. ACI Material Journal, 90(4), 309–318. [Google Scholar]
100. Farooqi, M. U., Ali, M. (2019). Effect of pre-treatment and content of wheat straw on energy absorption capability of concrete. Construction and Building Materials, 224(10), 572–583. DOI 10.1016/j.conbuildmat.2019.07.086. [Google Scholar] [CrossRef]
101. Sun, J., Ma, J. S., Cai, H. Q. (2013). Experimental study on the preparation of pumice composite concrete with corn stalks. Concrete, 7, 138–143. [Google Scholar]
102. Saraswathy, V., Song, H. W. (2007). Corrosion performance of rice husk ash blended concrete. Construction and Building Materials, 21(8), 1779–1784. DOI 10.1016/j.conbuildmat.2006.05.037. [Google Scholar] [CrossRef]
103. Feng, C., Qiao, H. X., Li, Y. K., Shu, X. Y., Cui, L. J. (2022). Effect of highland barley straw ash admixture on properties and microstructure of concrete. Construction and Building Materials, 315, 125802. DOI 10.1016/j.conbuildmat.2021.125802. [Google Scholar] [CrossRef]
104. Zhang, Q., Li, Y. Z., Xu, L., Lun, P. Y. (2019). Bond strength and corrosion behavior of rebar embedded in straw ash concrete. Construction and Building Materials, 205, 21–30. DOI 10.1016/j.conbuildmat.2019.01.228. [Google Scholar] [CrossRef]
105. Matheus, R. I., Juan, D. V. C., Francisco, J., Gea, A., Diego, C. Z. (2018). Pleurotus spp. cultivation on brachiaria sp. straw treatment with alkaline water, oyster mushroom and substrate treatment. Brazilian Journal of Microbiology, 49, 64–67. DOI 10.1016/j.bjm.2018.06.003. [Google Scholar] [CrossRef]
106. Nikolay, S. N., Tejo, P., Poonam, B., Ranjana, P., Evgenii, D. et al. (2018). Selenium-rich mushrooms cultivation on a wheat straw substrate from seleniferous area in Punjab, India. Journal of Trace Elements in Medicine and Biology, 50, 362–366. DOI 10.1016/j.jtemb.2018.07.027. [Google Scholar] [CrossRef]
107. Luo, W. J., Meng, J. L., Qu, J. H. (2010). Cultivation experiment of oyster mushroom with grape cuttings. Journal of Shanxi Agricultural University (Natural Science Edition), 30(2), 146–149. DOI 10.13842/j.cnki.issn1671-8151.2010.02.014. [Google Scholar] [CrossRef]
108. Singh, S., Raj, C., Singh, H. K. (2021). Characterization and development of cultivation technology of wild split gill schizophyllum commune mushroom in India. Scientia Horticulturae, 289, 110399. DOI 10.1016/j.scienta.2021.110399. [Google Scholar] [CrossRef]
109. Che, J. H. (2018). A new type of material for cultivating oyster mushrooms-pepper stalks. Friends of Farmers’ Enrichment, (20), 135. [Google Scholar]
110. Zhang, R., Li, H., J, X., Fadel, J. G. (2002). Oyster mushroom cultivation with rice and wheat straw. Bioresource Technology, 82, 277–284. DOI 10.1016/S0960-8524(01)00188-2. [Google Scholar] [CrossRef]
111. Puttaso, A., Vityakon, P., Saenjan, P. (2011). Relationship between residue quality, decomposition patterns, and soil organic matter accumulation in a tropical sandy soil after 13 years. Nutrient Cycling in Agroecosystems, 89(2), 159–174. DOI 10.1007/s10705-010-9385-1. [Google Scholar] [CrossRef]
112. Wu, T., Zhao, X. Y., Liu, M. D., Zhao, J., Wang, X. M. (2023). Wheat straw return can lead to biogenic toluene emissions. Journal of Environmental Sciences, 124, 281–290. DOI 10.1016/j.jes.2021.08.050. [Google Scholar] [CrossRef]
113. Liu, W., Liu, Y., Liu, G. (2022). Estimation of maize straw production and appropriate straw return rate in China. Agriculture, Ecosystems & Environment, 328, 107865. DOI 10.1016/j.agee.2022.107865. [Google Scholar] [CrossRef]
114. Wang, Q., Chen, X., Yu, M. (2019). Research progress on the effect of straw returning on nitrogen cycling microorganisms and functional genes in paddy fields. Zhejiang Agricultural Journal, 31(2), 333–342. [Google Scholar]
115. Wu, D., Li, M., Du, L. (2022). Straw return in paddy field alters photodegradation of organic contaminants by changing the quantity rather than the quality of water-soluble soil organic matter. Science of the Total Environment, 821, 153371. DOI 10.1016/j.scitotenv.2022.153371. [Google Scholar] [CrossRef]
116. Zhang, M., Song, D., Pu, X. (2022). Effect of different straw returning measures on resource use efficiency and spring maize yield under a plastic film mulch system. European Journal of Agronomy, 2022(134), 126461. DOI 10.1016/j.eja.2022.126461. [Google Scholar] [CrossRef]
117. Liu, L., Wang, W., Zhou, R. (2015). The effect of rapeseed straw turnover on rice production in season. World Journal of Forestry, 4, 1–6. [Google Scholar]
118. Zhu, B. Y., Ma, N. N., Yu, D. G. (2017). Rwsponse of ricce and wheat cropping system to straw mulching: Based on meta-analysis. Journal of Nanjing Agricultural University, 40(3), 376–385. [Google Scholar]
119. Mitchell, E., Scheer, C., Rowlings, D. W. (2016). The influence of above-ground residue input and incorporation on GHG fluxes and stable SOM formation in a sandy soil. Soil Bioloy and Biochemistry, 101, 104–113. DOI 10.1016/j.soilbio.2016.07.008. [Google Scholar] [CrossRef]
120. Zhang, J., Hu, K., Li, K. (2017). Simulating the effects of long-term discontinuous and continuous fertilization with straw return on crop yields and soil organic carbon dynamics using the DNDC model. Soil Bioloy and Biochemistry, 165, 302–314. DOI 10.1016/j.still.2016.09.004. [Google Scholar] [CrossRef]
121. Wu, L., Zhang, W., Wei, W. (2019). Soil oraganic matter priming and carbon balance after straw addition is regulated by long-term fertilization. Soil Bioloy and Biochemistry, 135, 383–391. DOI 10.1016/j.soilbio.2019.06.003. [Google Scholar] [CrossRef]
122. Liu, C., Lu, M., Cui, J. (2014). Effects of straw carbon input on carbon dynamics in agricultural soils, a meta-analysis. Global Change Biology, 20, 1366–1381. DOI 10.1111/gcb.12517. [Google Scholar] [CrossRef]
Cite This Article
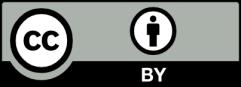
This work is licensed under a Creative Commons Attribution 4.0 International License , which permits unrestricted use, distribution, and reproduction in any medium, provided the original work is properly cited.