Open Access
ARTICLE
Self-Cross-Linked Tannin-Aminated Tannin Surface Coatings for Particleboard
1
LERMAB, I.U.T. Hubert Curien, University of Lorraine, Épinal, 88000, France
2
LERMAB-ENSTIB, University of Lorraine, Epinal, 88000, France
* Corresponding Authors: Bengang Zhang. Email: bengang ; Antonio Pizzi. Email:
Journal of Renewable Materials 2023, 11(12), 4097-4121. https://doi.org/10.32604/jrm.2023.029761
Received 07 March 2023; Accepted 14 April 2023; Issue published 10 November 2023
Abstract
Aminated tannins were prepared by reacting mimosa condensed tannin extract with ammonia yielding the substitution of many, if not all of the tannin hydroxyl groups with –NH2 groups. A tannin-aminated tannin (ATT) particleboard coating was then prepared by reacting raw tannin extract with aminated tannin extract and thus cross-liking the two by substituting tannin’s hydroxyl groups with the –NH2 groups on the aminated tannin to form –NH-bridges between the two. The resulting particleboard coating gave encouraging results when pressed at 180°C for 3 min. Conversely, the system in which tannin was reacted/cross-liked with urea (ATU) by a similar amination reaction did not perform as well as the ATT system, and this even when a higher curing temperature and longer hot press time were used. In particular its water repellence was worse probably due to the presence of urea and such a system lower reactivity. Nonetheless, substituting the tannin –OHs with the urea –NH2 groups appeared to also take place. ATT gave better results than ATU as regards water repellence and mechanical resistance as shown by the cross cut test. The ATT system was shown to be between 95% and 98% biosourced. The difference appeared to be due, by TMA analysis, to the much faster formation of the ATT hardened network leading to a better cross-linked polymer coating. The chemical species formed for both the ATT and ATU system were studied by MALDI ToF and CP MAS 13C NMR.Keywords
Surface coatings for particleboard and wood in general are a very important business area for the wood and wood panels industry. This field is dominated by the melamine based resins [1–5]. Melamine-formaldehyde or melamine-urea-formaldehyde resins [6–10] are the main exponents of this class of resins. Their advantages for coatings are in their good rate of pressing, transparent or white color and their excellent mechanical performance [11]. Melamine is obtained by the trimerization of urea, thus, it can even be considered biosourced like a number of other biosourced materials [12] thus a material to still consider in future. However, melamine, for all its great advantages, is also relatively expensive and its greatest drawback today is that it still uses formaldehyde in the formation of the coating resin. Interesting approaches to substitute formaldehyde such as melamine-glyoxal [13] and melamine-dialdehyde starch [14] to remedy this problem have been published but at this stage or they are still too new or they have not as yet retained the attention of the industry concerned.
Tannin-based resins, as all biobased resins, have gained a marked increase in interest with researchers in recent years. Tannin-based resins, on top of the considerable body of research literature on such a subject, have already been used industrially for many years as wood panel adhesives [15,16]. Their use as coatings, although of interest, has been limited to the commercialization of metal primers for metal surfaces [17]. Notwithstanding the plethora of articles on wood adhesives using tannins as raw material, as regards coatings for wood and wood panels while a number of articles can be found in the literature, these are still relatively scarce [18–23]. These have taken a number of different approaches, varying from the early essays on direct application of mimosa or quebracho tannin hardened by paraformaldehyde applied directly or through impregnated paper on particleboard [18], to the more modern tannin-furanic systems without formaldehyde also applied directly or through impregnated paper on particleboard [19–21], to the even more recent use of both hydrolysable and condensed tannins used as non-isocyanate polyurethane (NIPU) surface coatings on solid wood [22,24]. However with what being said, what is really needed is a biosourced coating that is entirely based on a single biosourced material. This is the reason why this article adopts the approach of considering a single material of biological origin, through a simple transformation of part of this biosourced material. In this case, tannin was the chosen material.
A reasonably recent finding thus, has promise for a further approach in using these biomaterials as surface finishes for wood or wood panels, an approach even higher in percentage of biosourced materials used. Tannin react very readily with ammonia and amines [23,25–27], and such reaction products can be sought for coatings applications. This reaction that can be either by substitution of just one –OH of the tannin with an –NH2 group [23] or up to being comprehensive of the total substitution of all the tannin –OH groups [26,27] could be used for surface coatings according to two different types of approach. Such approaches do not even use any aldehyde, not even the non-volatile non-toxic aldehydes generated from biosourced materials as proposed in adhesives [28,29] and used successfully at laboratory level for tannin-carbohydrate adhesives and other products [29–31].
The first reaction is the amination of the tannin, this reaction being already known [26,27].
Once the aminated tannin is obtained, there are two options to make it undergo the polycondensation reaction. Of the two approaches for coating one is based on the reaction on urea cross-linking aminated tannin by tannin deamination, a reaction already used very recently for other biomaterials [32,33] as shown in Scheme 1.
Scheme 1: ATU
The second option is to continue the amine substitution of other flavonoids –OH groups by the amine groups already fixed on the aminated tannin (Scheme 2). The first step of such reaction has already been observed and studied for other applications [26,27].
Scheme 2: ATT
It is these two approaches that have been tested in the research presented here to try to see if a surface coating for particleboard could be developed in this manner.
Commercial mimosa tannin extract form the bark of Acacia mearnsii (De Wild), supplied by Silva Chimica (St. Michele Mondovi, Italy) was used. It contained 80%–82% of actual phenolic flavonoid materials, 4%–6% of water, 1% of amino and imino acids, the remainder being monomeric and oligomeric carbohydrates, in general residual oligomes of cleaved hemicelluloses.
The ammonium hydroxide solution (25%) and urea (99.5%, ACS reagent) were both from Sigma-Aldrich (St. Louis, Missouri, USA). Distilled water was obtained in our laboratories.
2.2 Preparation of Aminated Tannins
10 g of mimosa tannin was dissolved in 10 mL of a 25 wt.% aqueous solution of ammonia. The solution was stirred during 1 h, and then it became very viscous and was left 1 day in a fume hood at room temperature. The resultant dry solid was washed with water (Dissolve solid tannins in water) and dried at 90°C. The dried solids are aminated tannins, which are ground for later use.
2.3 Reaction of Ammoniated Tannins with Raw Tannins (Named as ATT)
2 g aminated tannin +2 g raw tannin +4 g H2O. TMA (Thermomechanical analysis) was tested after stirring for 30 min. MALDI ToF was tested after drying in an oven at 120°C for 2 h. The coating is hot pressed at 180°C for 3 min on a particleboard substrate.
2.4 Reaction of Ammoniated Tannins with Urea (Named as ATU)
2 g aminated tannin +2 g urea +4 g H2O. TMA was tested after stirring for 30 min. MALDI ToF was tested after drying in an oven at 120°C for 2 h. The coating is hot pressed at 210°C for 3 min on a particleboard substrate.
The samples were subjected to an adhesion test by the cross-cut test according to French (European) standard NF EN ISO 2409 [27]. For this, the hardened surface finishes were cut through to the particleboard substrate with a razor blade in order to produce edges from which the coating may then be lifted. The cutting pattern consisted of a 10 × 10 grid of vertical and horizontal cuts spaced at 1 mm × 1 mm. A strong adhesive tape was then applied over the cut area and tightly pressed. The tape was then rapidly pulled off. This operation was repeated three times. Finally the surface finishes were examined to determine the number of blocks removed, this constituting an evaluation of the coating adhesion.
The contact angles of a drop of water on the two types of surface finishes cured at different temperatures were tested and compared to the same for an untreated surface of uncoated samples from the same particleboard. The contact angle of the treated and untreated board surfaces was obtained from the water drop being placed on the surface with a syringe and measured with an EasyDrop contact angle apparatus, using a drop shape analysis software (Krüs GmbH, Hamburg, Germany).
2.6 Thermomechanical Analysis (TMA)
30 mg of the coatings prepared were applied to beech wood strips, with dimensions of 21 mm3 × 5 mm3 × 1.1 mm3, and stacked together to form two-ply samples. The relationship of modulus of elasticity (MOE) against temperature was recorded by TMA (Mettler Toledo 40, Zurich, Switzerland) following the method of three-points bending on a span of 18 mm exercising a force cycle of 0.1/0.5 N on the specimens with each force cycle of 12 s (6 s/6 s) at a heating rate 10°C/min in the range 30°C–250°C [34], and the relevant curves of modulus of elasticity (MOE) against temperature were registered.
2.7 Matrix Assisted Laser Desorption Ionization Time of Flight (MALDI ToF) Mass Spectrometry
The samples (4 mg/mL) were dissolved in water/acetone (50/50 by volume) and the solutions were added to the matrix solution of 10 mg/mL in acetone. 2,5-dihydroxy benzoic acid was used as the matrix to ease placing the sample on the sample-holder plate. Red phosphorus was used for instrument calibration (LaserBio Labs, Valbonne, France). A concentrated solution of 10 mg/ml of sodium chloride (NaCl) in distilled water was mixed to the matrix to enhance ion formation. The sample was added into the matrix solutions and was divided into three parts of the matrix solution. Three parts of the sample solution and a part of NaCl solution; 0.5 to 1 µL were put on the MALDI target. The MALDI target was placed into the spectrometer after solvent evaporation. The peaks in the spectrum can present themselves at the actual molecular weight of the chemical species or increased by 23 Da, this being the molecular weight of the Na+ linked to the molecule from the NaCl added to the matrix to facilitate the flight of heavier oligomers. Sometime both forms of the same species, with and without Na+ can be present in the same spectrum. The MALDI-TOF spectra were recorded on an AXIMA Performance instrument (Shimadzu Scientific Instruments; Manchester, UK). The irradiation source was a pulsed nitrogen laser with 3-ns intervals at a wavelength of 337 nm. The measurements were carried out using the following conditions: polarity: positive; flight path: linear; mass: high (20-kV accelerating voltage) and 100 to 150 pulses per spectrum. The delayed extraction technique was used to apply delay times of 200 to 800 ns. The ion gate was set at 0, 500 and 1000 Da, respectively. The spectra are exact at +1 Da.
2.8 Cross Polarization Magic Angle Spinning Carbon 13 Nuclear Magneting Resonance (CP-MAS 13C NMR) Spectrometry
Solid state CP-MAS (cross-polarisation/magic angle spinning) 13C NMR spectra of the oven-dried solids of the reaction of tannin with ammonia were recorded on a Bruker MSL 300 spectrometer at a frequency of 75.47 MHz. Chemical shifts were calculated relative to tetramethyl silane (TMS). The rotor was spun at 4 kHz on a double-bearing 7 mm Bruker probe. The spectra were acquired with 5 s recycle delays, a 90° pulse of 5 μs and a contact time of 1 ms. The number of transients was 3000.
An example of the application of ATT and ATU as a directly applied coating on particleboard is given in Fig. 1. This was subjected first of all to the sessile drop test and its evolution as a function of time. The results of this are shown in Fig. 2 that clearly indicates that the ATT system gives a better water repellence than the ATU system. This is most likely due to the presence of urea that may tend to absorb water more easily than the ATT structures. A further indication of the better performance of the ATT coatings than the ATU one is clearly given by the TMA results (Fig. 3), where the rate of curing of the ATT resin is definitely faster than that of the ATU system. This is clear as the ATT coatings does increase in strength much more rapidly and at much lower temperature than the ATU one, and it reaches a definitely higher value of the MOE, and this is faster than for the ATU. All this indicates that the ATT reactions of cross-linking are faster, require less energy, and yield a better cross-linked coating, hence of better performance. This conclusion is also supported by the results of the cross-cutting test (Fig. 4), where the ATT coatings detaches much less traces of material from the surface on which it has been applied, an indication of better curing of the coatings itself and of a tighter surface structure of the ATT coating. The color variation of the coated board surfaces in relation to the original color of the particleboard substrate are shown in Fig. 5.
Figure 1: Particleboard panels coated with ATT (left), and with ATU (right)
Figure 2: Sessile drop contact angle as a function of time for ATT and ATU coatings on particleboard
Figure 3: TMA of ATT and ATU coatings showing the rate of curing of each of the two finishes
Figure 4: Cross-cut test for ATU and ATT coatings on particleboard
Figure 5: Surface color comparison before and after coating
High temperatures can definitely cause degradation of the material. However, in this work, TMA is mainly used to understand the curing temperature and curing rate of the material, while TGA is mainly used to explain the pyrolysis of the material at high temperature (the maximum temperature of the material can reach 650°C–700°C). This study did not address thermal degradation content, so TG was not tested.
In the Appendix are shown in Table A1 all the species formed in the ATT system. As the applied results for the ATU system were worse than for the ATT system, MALDI ToF spectra for the ATU system and the oligomer species assignments are only presented in the Appendix (Fig. A1 and Table A2). In the Appendix are also shown in Table A1 all the species formed in the ATT system.
Given the results reported it is worth to consider what does occur at the molecular level in the reaction of a condensed tannin with either ammonia or urea. As the better result is with the ATT coating this will be discussed first (Fig. 6). Mimosa tannin is mainly composed of robinetnidin, fisetinidin and catechin. There are, according to its origin also cases of flavonoid gallates, but these are unusual in this tannin and when they are present they are only in very small proportions/traces. In the MALDI ToF, dimers, trimers and tetramers of just flavonoid units are present (See Table A1). Dimers of the type already formed in the reaction of a flavonoid model compound with NH3 are clearly present as the 551 peak (with 23 Da of Na+), and also the open flavonoid form as the species at 617 Da that can be exclusively assigned to an open form of gallocatechin dimer partially aminated.
Figure 6: MALDI ToF mass spectra of the ATT coating
Notes: In Figs. 6A–6D respectively represent the MALDI spectra in the ranges of 0–1000, 0–500, 500–1000, and 1000–1500 Da, thus without the ion gate being applied for A and B, and with the ion gate set respectively at 500 Da (C), and 1000 Da (D).
Other open structure of the same type could be present such as those at 563 and 601 Da, but these can be also assigned to other types of flavonoid dimers.
Or structures in which the central nitrogen atom functions as a knot of tridimensional cross-linking such as in the structure at 840 Da (with Na+).
And linear structures such as the one at 905 Da (with Na+).
Equally structures where flavonoid dimers are linked to three dimensional or linear structures are found, such as those assigned for example to the peaks at 1177 Da.
And the linear one at 1192 Da.
The complete set of molecular structures identified are shown in Table A1.
The aminated tannin product obtained showed by CP-MAS 13C NMR (Fig. 6) shows some characteristics related to what already found previously with models [26,27]. Thus, on a flavonoid unit.
The peaks of C2’, C5’ and C6’ at 117 ppm are relatively lower that what observed in the spectrum of mimosa tannin alone (cf. Figs. 6–8). Equally relatively lower are the C3’ and C4’ peaks at 144–145 ppm, even if the small proportion of C=N-C bridges linking flavonoid units A-rings is superimposed in this peak. This shows that these carbons after reaction exist in a changed environment than that of mimosa tannin alone. While the peak at 144–145 ppm presents the shift characteristic of the C3’ and C4’ of a normal catechin flavonoid, this is much lower in the aminated tannin (Fig. 6) than on the unreacted tannin spectrum (Fig. 8) indicating that some of the B-ring –OH groups have also being substituted by –NH2 groups on the B-rings of flavonoid units. Consequently, it appears that several, although not all phenolic –OHs have undergone substitution mostly B-ring ones. The MALDI results are thus confirmed by these NMR shifts. It is then the extensive substitution by nitrogen causing cross-linking explaining tannin cross-linking. The unreacted tannin does not present a 166 ppm shift for the –C=N- bridge, shift that instead exists, although small, in the aminated tannin NMR (Fig. 7). As this peak is not present in the unreacted tannin spectrum (Fig. 8) this means that as for the catechin model the –C=N- bridge does also occurs in the tannin, but proportionally less [26,27]. However, the presence of this small peak is assigned to the double bond of the –C=N- bond which forms on the C9 of the A-ring in some of the open forms of the flavonoid units. The peak at 130–131 ppm is the one assigned to the C1’ of flavonoid units, while the 109 and 106 ppm are respectively assigned to ther interflavonoid C4–C6 and C4–C8 bond, and to the free C6 and C8 of the flavonoid unit A-rings.
Figure 7: CP MAS 13C NMR spectrum of the ATT coating formed by condensation of tannin-aminated tannin
Figure 8: CP MAS 13C NMR spectrum of the unreacted mimosa tannin extract
Clear 40, 30, 22 and 18 ppm shifts also occur. The 40 and 30 ppm peaks are assigned to the free, unreacted C4 site of the flavonoid, the two belonging respectively to close and open flavonoid units. While it is not easy to explain the 18 and 22 ppm (–CH3 and –CH2-) peaks, the 40 ppm peak could also belong to a –C-N- (Fig. 7), present in the tannin spectrum, thus confirming multiamination and the previous structures. That multiamination has occurred is also confirmed by the shoulder at 65 ppm (Fig. 7) indication of the same type of –C-N- group observed for model compound reactions with amonia [26,27]. The existence of two different chemical environments for –C-N- groups is inferred by the two –C-N- shifts. This confirms multiamination. The two peaks at 71 and 78 ppm are assigned respectively to the flavonoid units C3 to which is linked an alcoholic –OH group, and to the to the carbohydrate oligomers from cleaved hemicelluloses that are always present in commercial tannin extracts. The peak at 175 ppm is assigned to the glucuronic acids also generated by the cleavage and hydrolysis pf hemicellulose. The presence of traces of quinones is inferred by the rather small 196–197 ppm shift and are the consequence of some residual phenolic –OHs being oxidized during reaction. One must notice however, that different spectra shifts are obtained by treating tannins with an alkali different than ammonia, for example sodium hydroxide, with the aminated tannin shifts not being present, as ascertain from previous work [35–38].
The results of a tannin-aminated tannin (ATT) particleboard coating obtained by the reaction of the two materials gave encouraging results. The aminated tannin was obtained by reaction of the raw tannin with ammonia. The system instead in which tannin was reacted/cross-linked with urea (ATU) did not perform to the same level of the ATT system, although tannin –OHs substitution with the urea –NH2 groups appeared to also take place. ATT gave better results than ATU as regards water repellence and mechanical resistance as shown by the cross cut test. The difference appeared to be due, by TMA analysis, to the much faster formation of the ATT hardened network leading to a better cross-linked polymer coating.
Examination by MALDI ToF of both systems and of ATT by CP MAS 13C NMR showed a variety of cross-linked species being formed in both systems.
Funding Statement: The LERMAB is supported by a grant of the French Agence Nationale de la Recherche (ANR) in the Ambit of the Laboratory of Excellence (Labex) ARBRE. This work was also supported by “The 111 Project (D21027)”.
Conflicts of Interest: The authors declare that they have no conflicts of interest to report regarding the present study.
References
1. Bader, K., Wippel, W., Kummer, M. (2002). Concentrated, stable aqueous melamine-formaldehyde resin composition. Eur. Patent Appl.PCT/EP 00 09749. [Google Scholar]
2. Golombek, J. (1991). Verfahren und Vorrichtung zum Prufen des Aushartungsgrades eines mit Reaktionsharz impragnierten Tragers. Eur. Patent Appl., EP 0 324 869 A1. [Google Scholar]
3. Kandelbauer, A., Teischinger, A. (2010). Dynamic mechanical properties of decorative papers impregnated with melamine formaldehyde resin. Holz als Roh- und Werkstoff, 68(2), 179–187. [Google Scholar]
4. Kandelbauer, A., Teischinger, A. (2009). On the warping behavior of particleboards coated with melamine formaldehyde resin impregnated papers. Holz als Roh- und Werkst, 67(4), 367–378. [Google Scholar]
5. Roberts, R. J., Evans, P. D. (2005). Effects of manufacturing variables on surface quality and distribution of melamine formaldehyde resin in paper laminates. Composites Part A–Applied science and Manufacturing, 36(1), 95–104. https://doi.org/10.1016/S1359-835X(04)00127-7 [Google Scholar] [CrossRef]
6. Depres, A., Pizzi, A., Pasch, H., Kandelbauer, A. (2007). Comparative 13C-NMR and matrix-assisted laser desorption/ionization time-of-flight analyses of species variation and structure maintenance during melamine-urea–formaldehyde resin preparation. Journal of Applied Polymer Science, 106, 1106–1128. [Google Scholar]
7. Kandelbauer, A., Depres, A., Pizzi, A., Taudes, I. (2007). Testing by Fourier transform infrared species variation during melamine-urea–formaldehyde resin preparation. Journal of Applied Polymer Science, 106, 2192–2197. [Google Scholar]
8. Kirchgaessner, U., Niessner, M. (1992). Schnell penetrierende Aminoplastharzlosungen. German Patent Application DE 4117841A1. [Google Scholar]
9. Petek, P., Bottcher, A., Kandelbauer, A. (2006). Experimental design methods for the optimization of impregnation resins. Proceedings of the European Laminates Conference and Workshop, pp. 1–7. Prague, Czech Republic. [Google Scholar]
10. Pizzi, A. (1994). Advanced wood adhesives technology. New York: Marcel Dekker. [Google Scholar]
11. Kandelbauer, A., Petek, P., Medved, S., Pizzi, A., Teischinger, A. (2010). On the performance of a melamine-urea-formaldehyde resin for decorative paper coatings. European Journal of Wood and Wood Products, 68(1), 63–75. [Google Scholar]
12. Parmegiani, M., Noe, S., Santucci, R. (2003). Process for the production of melamine from urea, and particularly for the separation of melamine from off-gas. Patent WO2003080584A1. [Google Scholar]
13. Deng, S., Pizzi, A., Du, G., Lagel, M. C., Delmotte, L. et al. (2018). Synthesis, structure characterization and application of melamine-glyoxal adhesive resins. European Journal of Wood and Wood Products, 76(1), 283–296. [Google Scholar]
14. Zhang, B., Pizzi, A., Petrissans, M., Petrissans, A., Colin, B. (2023). A melamine-dialdehyde starch wood surface finish without formaldehyde. Journal of Renewable Materials, 11(2). https://doi.org/10.32604/jrm.2023.028888 [Google Scholar] [CrossRef]
15. Valenzuela, J., von Leyser, E., Pizzi, A., Westermeyer, C., Gorrini, B. (2012). Industrial production of pine tannin-bonded particleboard and MDF. European Journal of Wood and Wood Products, 70(5), 735–740. https://doi.org/10.1007/s00107-012-0610-2 [Google Scholar] [CrossRef]
16. Pizzi, A. (1979). Glue blenders effect on particleboard using wattle tannin adhesives. Holzforschung und Holzverwertung, 31(4), 85–86. [Google Scholar]
17. Matamala, G., Smeltzer, W. S., Droguetta, G. (2000). Comparison of steel anticorrosive protection formulated with, natural tannins extracted from acacia and from pine bark. Corrosion Science, 42(8), 1351–1362. https://doi.org/10.1016/S0010-938X(99)00137-7 [Google Scholar] [CrossRef]
18. Pizzi, A. (1979). Tannin-based overlays for particleboard. Holzforschung und Holzverwertung, 31(3), 59–61. [Google Scholar]
19. Abdullah, U. H., Pizzi, A., Zhou, X., Rode, K., Delmotte, L. et al. (2013). Mimosa tannin resins for impregnated paper overlays. European Journal of Wood and Wood Products, 71(2), 153–162. https://doi.org/10.1007/s00107-012-0652-5 [Google Scholar] [CrossRef]
20. Abdullah, U. H., Pizzi, A., Zhou, X. (2014). High pressure paper laminates from mimosa tannin resin. International Wood Products Journal, 5(4), 224–227. [Google Scholar]
21. Abdullah, U. H., Zhou, X., Pizzi, A., Merlin, A. (2013). A note on the surface quality of plywood overlaid with mimosa (Acacia mearnsii) tannin and melamine urea formaldehyde impregnated paper: Effects of moisture content of resin-impregnated papers before pressing on the physical properties of overlaid panels. International Wood Products Journal, 4(4), 253–256. [Google Scholar]
22. Thebault, M., Pizzi, A., Essawy, H., Baroum, A., Gvan Assche, G. (2015). Isocyanate free condensed tannin-based polyurethanes. European Polymer Journal, 67, 513–526. [Google Scholar]
23. Thebault, M., Pizzi, A., Santiago-Medina, F. J., Al-Marzouki, F. M., Abdalla, S. (2017). Isocyanate-free polyurethanes by coreaction of condensed tannins with aminated tannins. Journal of Renewable Materials, 5, 21–29. https://doi.org/10.7569/JRM.2016.634116 [Google Scholar] [CrossRef]
24. Byrne, C., D’Alessandro, O., Selmi, G. J., Romagnoli, R., Deyá, C. (2019). Primers based on tara and quebracho tannins for poorly prepared steel surfaces. Progress in Organic Coatings, 130, 244–250. [Google Scholar]
25. Hashida, K., Makino, R., Ohara, S. (2009). Amination of pyrogallol nucleus of condensed tannins and related polyphenols by ammonia water treatment. Holzforschung, 63(3), 319–326. https://doi.org/10.1515/HF.2009.043 [Google Scholar] [CrossRef]
26. Braghiroli, F., Fierro, V., Izquierdo, M. T., Parmentier, J., Pizzi, A. et al. (2012). Nitrogen-doped carbon materials produced from hydrothermally treated tannin. Carbon, 50(15), 5411–5420. https://doi.org/10.1016/j.carbon.2012.07.027 [Google Scholar] [CrossRef]
27. Braghiroli, F., Fierro, Pizzi, A., Rode, K., Radke, W. et al. (2013). Reaction of condensed tannins with ammonia. Industrial Crops and Products, 44(4), 330–335. https://doi.org/10.1016/j.indcrop.2012.11.024 [Google Scholar] [CrossRef]
28. Frihart, C. R., Pizzi, A., Xi, X., Lorenz, L. (2019). Reactions of soy flour and soy protein by non-volatile aldehydes generation by specific oxidation. Polymers, 11(9), 1478. https://doi.org/10.3390/polym11091478 [Google Scholar] [PubMed] [CrossRef]
29. Xi, X., Pizzi, A., Frihart, C. R., Lorenz, L., Gerardin, C. (2020). Tannin plywood adhesives by non-volatile aldehydes generation from specific oxidation of mono- and disaccharides. International Journal of Adhesion and Adhesives, 98, 102499. https://doi.org/10.1016/j.ijadhadh.2019.102499 [Google Scholar] [CrossRef]
30. Chen, X., Xi, X., Pizzi, A., Fredon, E., Du, G. et al. (2021). Oxidized demethylated lignin as a bio-based adhesive for wood bonding. Journal of Adhesion, 97(9), 873–890. https://doi.org/10.1080/00218464.2019.1710830 [Google Scholar] [CrossRef]
31. Xi, X., Pizzi, A., Lei, H., Chen, X., Zhang, B. et al. (2022). Environmental friendly chitosan adhesives for plywood bonding. International Journal of Adhesion and Adhesives, 112(2–3), 103027. https://doi.org/10.1016/j.ijadhadh.2021.103027 [Google Scholar] [CrossRef]
32. Li, T., Zhang, B., Jiang, S., Zhou, X., Du, G. et al. (2020). Novel highly branched polymer wood adhesive resin. ACS Sustainable Chemistry and Engineering, 8(13), 5209–5216. https://doi.org/10.1021/acssuschemeng.9b07732 [Google Scholar] [CrossRef]
33. Zhang, B., Chen, X., Pizzi, A., Petrissans, M., Dumarcay, S. et al. (2023). Highly branched tannin-tris(2-aminoethyl)amine-urea wood adhesives. Polymers, 15(2), 890. https://doi.org/10.3390/polym15040890 [Google Scholar] [PubMed] [CrossRef]
34. Kamoun, C., Pizzi, A., Garcia, R. (1998). The effect of humidity on cross-linked and entanglement networking of formaldehyde-based wood adhesives. Holz als Roh- und Werkstoff, 56(4), 235–243. https://doi.org/10.1007/s001070050309 [Google Scholar] [CrossRef]
35. Pizzi, A., Stephanou, A. (1992). Theory and practice of non-fortified tannin adhesives for particleboard. Holzforschung und Holzverwertung, 44(4), 62–68. [Google Scholar]
36. Pizzi, A., Stephanou, A. (1993). A comparative 13C NMR study of polyflavonoid tannin extracts for phenolic polycondensates. Journal of Applied Polymer Science, 50, 2105–2113. [Google Scholar]
37. Pizzi, A., Stephanou, A. (1994). A 13C NMR study of polyflavonoid tannin adhesives intermediates. I. Non-colloidal, performance-determining rearrangements. Journal of Applied Polymer Science, 51, 2109–2124. [Google Scholar]
38. Pizzi, A., Stephanou, A. (1994). A 13C NMR study of polyflavonoid tannin adhesives intermediates. II. Colloidal state reactions. Journal of Applied Polymer Science, 51, 2125–2130. [Google Scholar]
Appendix
Figure A1: Assignment of MALDI ToF analysis peaks to relevant structures of ATU surface coating
Cite This Article
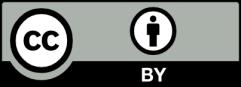
This work is licensed under a Creative Commons Attribution 4.0 International License , which permits unrestricted use, distribution, and reproduction in any medium, provided the original work is properly cited.