Open Access
ARTICLE
Effect of Bio-Based Organic‒Inorganic Hybrid Hydrogels on Fire Prevention of Spontaneous Combustion of Coals
State Key Laboratory of Fire Science, University of Science and Technology of China, Hefei, 230026, China
* Corresponding Authors: Xin Wang. Email: ; Yuan Hu. Email:
Journal of Renewable Materials 2023, 11(12), 3991-4006. https://doi.org/10.32604/jrm.2023.029888
Received 13 March 2023; Accepted 10 May 2023; Issue published 10 November 2023
Abstract
To solve the fire accidents caused by coal combustion, this work prepared four hybrid hydrogel materials using bio-based polymers, flame retardants, and inorganic materials. Compared to pure water and 3.5 wt% MgCl2 solution, the as-prepared hydrogel presents good fire prevention performance. In addition, it is found that CO and CO2 are not produced by coal when the pyrolysis temperature is lower than 200°C. During low-temperature pyrolysis, CO is more likely to be produced than CO2, indicating inadequate pyrolysis behavior. At the same time, the addition of fire-preventing hydrogel can not only decrease the maximum CO2 concentration before the critical temperature but also prolong the corresponding time. In addition, based on the cone calorimeter test, the inhibition effects of pure water, magnesium chloride solution, and four hybrid hydrogels on heat release behavior are evaluated. It is demonstrated that different dosages of different hydrogels affected the fire prevention effect. Phosphorous-modified cellulose/silica and carrageenan/DMMP/vermiculite composite hydrogels have the weakest fire prevention effect at 20 g, which is weaker than that of water. However, the fire prevention effect of carrageenan/ DMMP/vermiculite composite hydrogels exceeded that of water at 40 and 60 g. Additionally, the fire prevention effect of the sodium alginate/sepiolite/ammonium polyphosphate composite hydrogel is most significant in common tests, attributed to the intumescent flame retardant system.Graphic Abstract
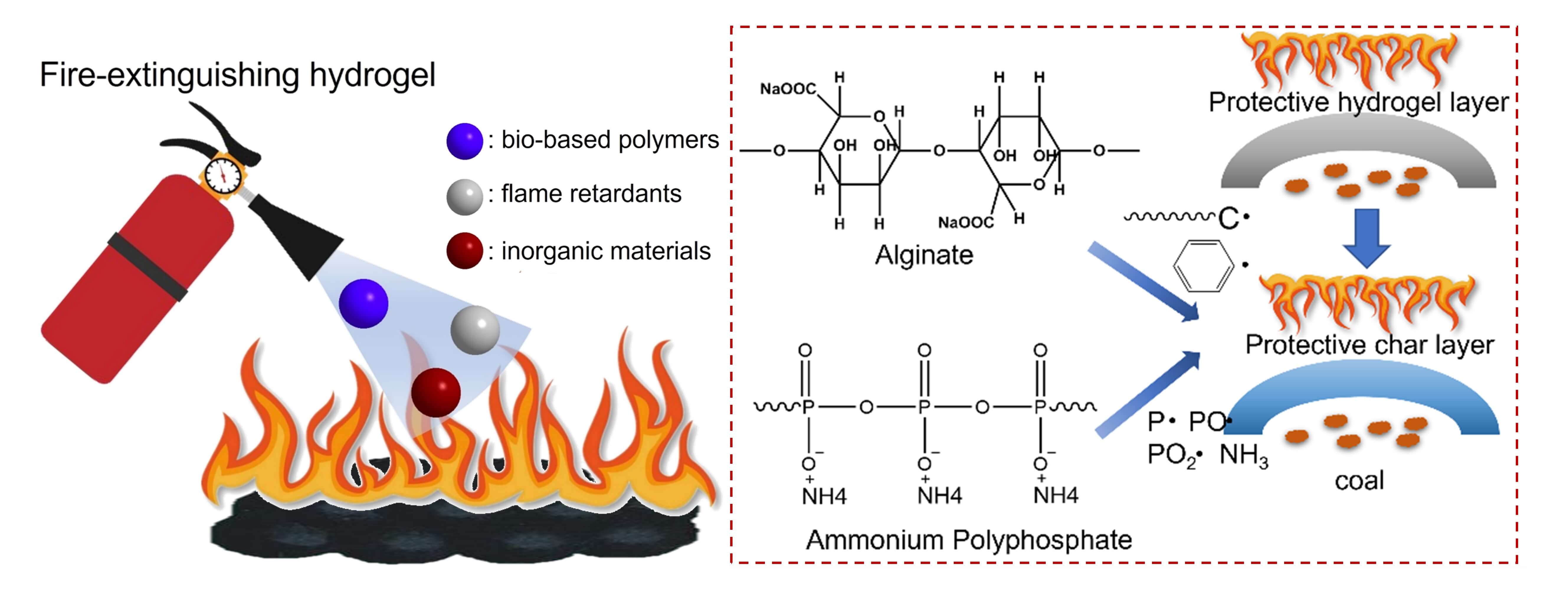
Keywords
Coal is a crucial strategic resource that has played a significant role in supporting the livelihoods of individuals and the growth of industries worldwide. However, the frequent occurrence of spontaneous combustion incidents in coal mines presents a significant threat to the safety of coal production [1]. The primary concentration of spontaneous combustion incidents is found in the goaf’s coal loss zone, making the prevention and control of air leakage in the goaf a crucial task in mitigating the risk of spontaneous combustion. To prevent spontaneous coal combustion, various techniques, such as grouting, colloid injection, three-phase foam injection, aerosol inhibitors, pressure-equalizing fire prevention, solidification of foam, and air leakage blocking, have been employed both domestically and internationally [2]. Despite these efforts, current fire prevention and extinguishing materials suffer from several limitations, including poor plugging effects with yellow mud irrigation, difficulties in recycling cement mortar, and inadequate strength and shelf life of ordinary gel plugging materials [3]. It is therefore imperative to develop more effective mine fire prevention and extinguishing materials to control existing fire areas and prevent new fires from occurring.
Hydrogel materials, as one type of significant polymer material, possess a unique three-dimensional network structure and hydrophilic polymer chains, allowing them to absorb and retain substantial amounts of water [4]. Beyond their remarkable water absorption and retention properties, hydrogel materials also exhibit good biocompatibility, temperature sensitivity, and pH responsiveness, among other distinctive characteristics [5,6]. As a result of these advantages, hydrogel materials have seen rapid development and widespread use in various areas, including drug delivery, tissue engineering, health care, and hygiene products [7]. Furthermore, hydrogel materials have been identified as an important class of fire-preventing materials. However, the use of pure hydrogels as fire-extinguishing materials is limited by issues such as low melting point, high viscosity, and poor liquidity [8]. Hence, further chemical modification of hydrogel-based fire-extinguishing materials is necessary to enhance fire prevention and extinguishing performance. Despite this, there is a scarcity of studies on inorganic–organic hybrid hydrogel materials for fire prevention [9]. It is thus imperative to prepare a hybrid hydrogel with superior performance, low cost, high water absorption, and high fire prevention performance.
Fire-preventing and fire-extinguishing hydrogel materials combine the properties of plugging, cooling, resistance, and consolidation of water [10]. By drilling, a colloidal solution can be gelled at the designated location and applied to the surface of high-temperature coal, thereby inhibiting the supply of oxygen and reducing the temperature [11,12]. The composition and ratio of raw materials in different colloidal materials will result in varying fire prevention performance and application conditions. In addition, the underlying mechanism of action is similar [10]. Essentially, when the hydrogel materials are introduced into high-temperature areas, the water within some un-gelled materials will be rapidly vaporized, leading to a quick reduction in coal surface temperature. The residual solids after the evaporation of water will form an insulation layer, preventing coal from coming into contact with oxygen. Meanwhile, another portion of the slurry will solidify into a colloid as the temperature decreases and cover the surface of the coal, isolating oxygen and inhibiting the spontaneous combustion of coal until the fire subsides. As reported in previous literature, our research group has prepared three kinds of hydrogel-based fire-extinguishing agents, presenting desirable effects on the extinguishing of wood combustion [13,14]. In these works, it was revealed that phosphorus-containing flame retardants and inorganic layer materials can promote the fire-extinguishing effect of bio-hydrogels [13–15].
Therefore, this study aimed to improve the fire-extinguishing effect in current hydrogel-based materials through the application of molecular design, interface control, and other methods. The combination of synergistic flame-retardant principles and nanocomposite technology was employed to design and produce high-performance hydrogel-based fire-extinguishing materials that were then modified with inorganic nanoparticles to broaden their range of applications. The physical properties of inorganic–organic hybrid hydrogel materials, including fire safety, water absorption, and fluidity, were studied. Meanwhile, the impact of the functional modification on the fire resistance and physical-chemical properties of the hybrid hydrogel materials was explored. The relationship between the chemical structure, composition, and fire prevention performance of hybrid hydrogel materials was analyzed. Meanwhile, the goal of preparing a hybrid hydrogel material with superior fire prevention performance and low cost was achieved.
In this study, four hydrogels were used as presented in Table 1: (1) Hydrogel A comprised of 1 wt% phosphorous-modified cellulose, 1 wt% fumed silica and 98 wt% water; (2) Hydrogel B made of 2 wt% sodium alginate, 2 wt% sepiolite, 1 wt% water-soluble ammonium polyphosphate (APP) and 95 wt% water; (3) Hydrogel C consisting of 1 wt% carrageenan, 2 wt% dimethyl methyl phosphate (DMMP), 4 wt% vermiculite and 93 wt% water; and (4) Hydrogel D comprised of 1 wt% sodium polyacrylate, 1 wt% polyacrylamide, 2 wt% montmorillonite (DK4) and 1 wt% water-soluble APP and 95 wt% water. The preparation methods of hydrogels A, B and C were performed according to previous works reported by our groups [9–11]. The coal was mixed with water of varying qualities and aqueous solutions containing magnesium chloride, as well as the four hydrogels, through mechanical stirring.
2.1.1 Preparation of Hydrogel A
The synthesis of phosphorous-modified cellulose was conducted by adding 8.05 g of 9,10-dihydro-9-oxa-10-phosphoxanthine-10-oxide and 22.72 g of methylcellulose (MC) into a round-bottomed flask fitted with a mechanical stirrer. A total of 1.38 g of potassium carbonate and 200 mL of DMF were added to the mixture, which was then stirred at 100°C for 12 h. The unreacted monomers and DMF were subsequently removed through vacuum filtration. The final product was obtained by drying the synthesized material to a constant weight in a vacuum oven at 70°C.
2.1.2 Preparation of Hydrogel B
The required quantities of sodium alginate, water-soluble APP, and sepiolite were mixed with 93% water in a beaker. The mixture was stirred dramatically until a homogenously dispersed solution was achieved.
2.1.3 Preparation of Hydrogel C
A ternary hydrogel material composed of carrageenan, vermiculite and DMMP was synthesized using the one-pot method. The components were precisely weighed and added to water, and a uniform hydrogel was obtained through vigorous mechanical agitation accompanied by sonication for 1 h.
2.1.4 Preparation of Hydrogel D
A composite hydrogel material was prepared by the one-pot method with the composition of 1% sodium polyacrylate, 1% polyacrylamide, 2% DK4, and 1% water-soluble APP in 95% water. The ingredients were accurately weighed and added to water, and the mixture was subjected to intense mechanical agitation accompanied by sonication for 1 h.
The concentration and type of combustion gases were determined using a Fourier transform infrared (FTIR) detector from the United Kingdom. The measurements were conducted under various temperatures and formula ratios. The heat release rate and total heat release of drying hydrogel materials were evaluated using a micro calorimeter. In addition, the fire hazards of coal mixed with hydrogel-based fire-preventing materials are evaluated by cone calorimeter tests.
3.1 Analysis of Gas Generated by Combustion of 20 g Coal
The results from Fig. 1 indicate that the concentrations of carbon monoxide (CO) and carbon dioxide (CO2) generated during coal combustion are negligible when the temperature is below 200°C. At temperatures above 200°C, an increase in temperature results in an advanced generation of CO and CO2, with a concurrent increase in the maximum concentration of these combustion by-products. This implies that higher temperatures result in more intense coal combustion and a corresponding rise in the concentration of CO and CO2. The times corresponding to the maximum concentrations of CO at 250°C and 300°C are close. However, a slightly delayed phenomenon is presented at 350°C. Meanwhile, the time corresponding to the maximum concentration of CO2 is slightly promoted with increasing temperature. This suggests that the process of coal combustion is relatively consistent and that the times of peak CO and CO2 concentrations are nearly the same. The CO and CO2 release behaviors of 20 g coal were further investigated with a mixture of 90 g pure water and 90 g 3.5 wt% MgCl2 solution (Figs. 2 and 3). The production rules of CO and CO2 in 20 g coal mixed with 90 g pure water and 90 g 3.5 wt% MgCl2 solution are similar to those in pure 20 g coal, including time and temperature. However, the addition of pure water and 3.5 wt% MgCl2 solution obviously changed the concentrations of CO and CO2. For example, the highest concentrations of CO and CO2 at 350°C in pure 20 g coal are close to 3000 ppm and 1.80%, respectively. Obvious reductions were presented in the CO concentration of 20 g coal mixed with 90 g pure water and 90 g 3.5 wt% MgCl2 solution, as confirmed by a CO concentration of ~2300 ppm. In addition, incorporating pure water and 3.5 wt% MgCl2 solution cannot reduce the CO2 concentration. CO2 concentrations close to 1.85% are presented in three samples combusted at 350°C. These phenomena indicate that CO2 is the main product of coal combustion, similar to previous literature [16].
Figure 1: Concentration of (a) CO and (b) CO2 produced by combustion of 20 g coal at different temperatures
Figure 2: Concentration of (a) CO and (b) CO2 produced by combustion of 20 g coal added with 90 g water at different temperatures
Figure 3: Concentration of (a) CO and (b) CO2 produced by combustion of 20 g coal with 90 g 3.5 wt% MgCl2 solution at different temperatures
According to Fig. 4, the concentrations of CO and CO2 generated by the mixture combustion prepared by 20 g coal and 90 g hydrogel C are also investigated. The maximum concentration of CO2 at 350°C is obviously decreased, close to 1.70%. The same addition of pure water or 3.5 wt% MgCl2 solution is not capable of presenting a similar suppression effect on CO2 release. Meanwhile, the maximum concentration of CO is reduced to ~1650 ppm, much lower than the results of pure water and 3.5 wt% MgCl2 solution. Obviously, the suppression effect on CO and CO2 release is attributed to 90 g of hydrogel C. A control experiment investigating the CO and CO2 release behaviors of 20 g of coal mixed with 45 g of 3.5 wt% hydrogel C was carried out to confirm this view. The maximum CO and CO2 concentrations in this sample are up to 2250 ppm and 2.0%, respectively. Compared to 90 g 3.5 wt% hydrogel C, the concentrations of CO and CO2 are all slightly increased, indicating a weaker suppression effect in 45 g hydrogel C. Meanwhile, the CO and CO2 concentrations of 20 g coal mixed with 45 g hydrogel C are much lower than those of pure coal, close to those of 20 g coal mixed with 90 g water and 90 g 3.5 wt% MgCl2 solution. These results indicate that, compared to pure water and 3.5 wt% MgCl2 solution, hydrogel C is a superior fire-preventing material. The good fire-extinguishing effect in hydrogel C may be due to the flame retardant effect of P and S and the barrier function of vermiculite [17,18].
Figure 4: Concentration of (a) CO and (b) CO2 produced by combustion of 20 g coal with 90 g hydrogel C at different temperatures
3.2 Analysis of Gas at 250°C, 300°C, and 350°C
Fig. 5 shows that at 250°C, the concentrations of CO and CO2 produced by 20 g coal combustion are the highest. After adding water, MgCl2 and hydrogel, the concentrations of CO and CO2 produced by coal combustion decreased accordingly. Among them, the concentrations of CO and CO2 produced by coal combustion are ranked as follows: coal >90 g water >45 g 3.5% gel >90 g 3.5% MgCl2 and 90 g hydrogel C. At the same time, the time sequence of coal combustion to produce CO and CO2 is coal <45 g 3.5% hydrogel C <90 g water <90 g 3.5% MgCl2 <90 g hydrogel C. The addition of additives greatly reduces the concentrations of CO and CO2 produced by coal combustion. At the same dosage, the effect of hydrogel C is slightly better than that of the 3.5 wt% MgCl2 solution. The further increase in combustion temperature also brings a shorter time for CO and CO2 release (Figs. 6 and 7). For example, the time corresponding to the maximum CO2 concentration is near 75 min in 20 g coal mixed with 90 g 3.5 wt% MgCl2 or 90 g hydrogel C. However, the increase in heating temperature to 300°C from 250°C decreases the time corresponding to the maximum CO2 concentration to 50 min. Meanwhile, the temperature increase obviously promotes the release of CO and CO2, presenting a twofold increase in maximum concentration. Interestingly, the heating temperature of 350°C does not increase the maximum concentration of CO2 in 20 g pure coal compared to that of 300°C. This result indicates that 20 g pure coal has been burned fiercely near 300°C and that higher temperatures do not contribute to the further combustion of 20 g pure coal [15]. Nevertheless, obvious increases in CO2 release are presented in other samples, and the maximum concentration of CO2 is close to 1.75% (from 300°C to 350°C). These results indicate that a further temperature increase will suppress the fire-extinguishing effect of hydrogel C.
Figure 5: Concentration of (a) CO and (b) CO2 produced by combustion of 20 g coal with different fire extinguishing agents at 250°C
Figure 6: Concentration of (a) CO and (b) CO2 produced by combustion of 20 g coal with different fire extinguishing agents at 300°C
Figure 7: Concentration of (a) CO and (b) CO2 produced by combustion of 20 g coal with different fire extinguishing agents at 350°C
The above research and analysis show that coal hardly burns at temperatures below 200°C. With a heating temperature of ~250°C, the degree of coal combustion increased with increasing temperature. Below 300°C, the addition of pure water and 3.5 wt% MgCl2 solution will inhibit coal combustion, and the effect of 3.5 wt% MgCl2 solution is better than that of pure water. In addition, a heating temperature of 300°C does not increase the CO2 concentration of pure coal, demonstrating that a complete combustion process occurs below 300°C [19]. Meanwhile, the maximum CO2 concentration at 350°C is similar in different samples. This result indicates that the combustion process of all samples at 350°C is complete. It was also found that the addition of hydrogel C and 3.5 wt% MgCl2 can delay the release of CO and CO2 even with a heating temperature of 350°C, showing a desirable suppression effect [20].
3.3 Cone Calorimeter Test of Coal with 20 g of Hydrogel
The cone calorimeter test is a widely used technical approach to study the combustion behaviour of materials and can obtain a large amount of combustion-related data, including the heat release rate (HRR), average heat release rate (avHRR), peak heat release rate (PHRR), total heat release (THR), and total smoke release (TSP) [21–23]. The PHRR value of coal reaches 70 kW/m2 (Fig. 8 and Table 2). In addition, the order of PHRR of 20 g coal with 20 g different additives is hydrogel A (110.0 kW/m2) > hydrogel C (94.3 kW/m2) > water (82.6 kW/m2) > hydrogel D (76.9 kW/m2) > hydrogel B (56.2 kW/m2). Among them, the PHRR of coal with 20 g hydrogel B is 56.2 kW/m2, which is 49% lower than that of coal with 20 g hydrogel A and 32% lower than that of coal with 20 g water. This shows that 20 g hydrogel B can present the best effect on preventing coal combustion, effectively reducing the heat release and inhibiting coal combustion. The fire prevention effect of water and hydrogels is hydrogel B > hydrogel D > water > hydrogel C > hydrogel A. Even, the fire prevention effect of hydrogel A and hydrogel C is worse than that of water. Meanwhile, the order of THR size is hydrogel A (25.22 MJ/m2) > water (20.92 MJ/m2) > hydrogel C (17.82 MJ/m2) > hydrogel B (17.03 MJ/m2) > hydrogel D (16.21 MJ/m2) (Fig. 8). The minimum THR value of coal with 20 g of hydrogel D is 16.21 MJ/m2, which is 36% lower than that of coal with 20 g hydrogel A and 23% lower than that of coal with 20 g water. The THR of coal with 20 g hydrogel B is decreased by 32% and 19% compared with coal with the addition of 20 g hydrogel A and 20 g water, respectively.
Figure 8: (a) HRR, (b) THR and (c) TSP curves of 20 g coal with 20 g fire extinguishing agents
The order of avHRR size is hydrogel C (41.3 kW/m2) > hydrogel A (40.0 kW/m2) > hydrogel D (40.0 kW/m2) > water (34.0 kW/m2) > hydrogel B (31.2 kW/m2). In general, hydrogel B shows the best effect on inhibiting coal combustion, simultaneously reducing PHRR, THR, and avHRR. The fire prevention effect of hydrogel D is also desirable, effectively reducing the PHRR and THR. However, the suppression effect of hydrogels A and C is worse than that of pure water. The order of TSP values is hydrogel A (8410.0 m2/m2) > water (8041.4 m2/m2) > hydrogel B (6041.3 m2/m2) > hydrogel C (3616.4 m2/m2) > hydrogel D (242.9 m2/m2). Among them, the lowest TSP of coal with the addition of 20 g hydrogel D is 242.9 m2/m2, far lower than that of coal with other additives.
The TSP of coal with the addition of 20 g hydrogel D is 97% lower than that of coal with 20 g hydrogel A, 97% lower than that of coal with 20 g water, 96% lower than that of coal with 20 g hydrogel B, and 93% lower than that of coal with 20 g hydrogel C [24]. This result shows that the addition of hydrogel D can effectively suppress the smoke generated by coal combustion, presenting good smoke suppression performance [25,26]. The addition of hydrogels B and C also presents a certain degree of smoke suppression, while the fire prevention effect of hydrogel C is better than that of hydrogel B. In addition, the fire prevention effect of hydrogel A is worse than that of pure water (Table 1).
3.4 Cone Calorimeter Test of Coal with 40 g Hydrogel
The cone calorimetric results of 20 g coal with 40 g of different additives are presented in Fig. 9. The order of PHRR is hydrogel A (119.6 kW/m2) > water (92.1 kW/m2) > hydrogel C (80.1 kW/m2) > hydrogel B (77.9 kW/m2) > hydrogel D (60.8 kW/m2) (Table 3). Among them, the minimum PHRR of coal combustion presented by the addition of 40 g hydrogel D is 60.8 kW/m2, lower than that of coal added with 40 g hydrogel A (49%) and 40 g pure water (34%). This result shows that 40 g hydrogel D has the best suppression effect on coal combustion, effectively reducing the heat released from coal combustion and reducing the intensity of coal combustion. The fire prevention effect of additives is hydrogel D > hydrogel B > hydrogel C > water > hydrogel A. The order of THR is hydrogel A (23.12 MJ/m2) > water (21.22 MJ/m2) > hydrogel C (17.72 MJ/m2) > hydrogel B (14.58 MJ/m2) > hydrogel D (14.51 MJ/m2). The minimum THR of coal combustion is presented by adding 40 g hydrogel D, close to 14.51 MJ/m2. Meanwhile, the THR of coal combustion with 40 g hydrogel D is the same as that of coal with 40 g hydrogel B and lower than that of coal with 40 g hydrogel A (36%) and 40 g water (23%). The order of avHRR value is hydrogel A (49.0 kW/m2) > water (44.5 kW/m2) > hydrogel C (40.8 kW/m2) > hydrogel B (40.0 kW/m2) > hydrogel D (35.5 kW/m2). In general, coal added with hydrogel D has the best effect on inhibiting the combustion process, effectively reducing PHRR, THR and avHRR. The fire-extinguishing effect of hydrogel B is slightly less than that of hydrogel D. In addition, the fire-extinguishing effect of hydrogel C is worse but better than that of pure water. The fire-extinguishing effect of hydrogel A is worse than that of pure water. The order of TSP values is water (7375.9 m2/m2) > hydrogel C (1776.2 m2/m2) > hydrogel A (1059.7 m2/m2) > hydrogel D (779.8 m2/m2) > 40 g hydrogel B (595.2 m2/m2).
Figure 9: (a) HRR, (b) THR and (c) TSP curves of 20 g coal with 40 g fire extinguishing agents
Among them, coal with 40 g hydrogel B presents a TSP as low as 595.2 m2/m2, far lower than that of other samples containing other additives. Reductions of 92%, 66%, 44%, and 24% were presented compared with coal added with 40 g water, 40 g hydrogel C, 40 g hydrogel A, and 40 g hydrogel D. This result shows that the addition of hydrogel B can effectively inhibit smoke production with coal combustion. The addition of hydrogel D also presents a certain degree of smoke suppression but is slightly worse than the addition of hydrogel B. In summary, the addition of hydrogel A will not inhibit the combustion of coal but will promote the combustion of coal. The addition of hydrogel B can effectively inhibit coal combustion, reducing the combustion intensity and preventing smoke suppression. The addition of hydrogel C can properly prevent the combustion of coal and has certain smoke suppression, but the comprehensive effect is not good. The addition of hydrogel D can inhibit coal combustion and reduce the combustion intensity slightly better than that of hydrogel B. Hydrogel D has the best comprehensive performance.
3.5 Cone Calorimeter Test of Coal with 60 g Hydrogel
The heat release behaviors of 20 g coal with 60 g different additives are also investigated with a cone calorimeter test (Fig. 10). The order of PHRR values is hydrogel A (120.0 kW/m2) > water (105.5 kW/m2) > hydrogel D (64.2 kW/m2) > hydrogel C (27.2 kW/m2) > hydrogel B (27.2 kW/m2). The coal with 60 g hydrogel B presents a PHRR of 27.2 kW/m2, which is lower than that of the other samples. The reduction in PHRR of coal with 60 g hydrogel B is equivalent to that of 60 g hydrogel C, 77% lower than that of 60 g hydrogel A, and 74% lower than that of 60 g pure water. This result shows that 60 g hydrogels B and C have the best effect in effectively reducing the heat release behavior. The fire prevention effect of additives is hydrogel B and hydrogel C > hydrogel D > water > hydrogel A. The fire prevention effect of hydrogel A is worse than that of water. The order of THR is hydrogel A > hydrogel D (21.96 MJ/m2) > water (20.37 MJ/m2) > hydrogel C > hydrogel B (5.65 MJ/m2). The THR of coal added with 60 g hydrogel B presents reductions of 74% and 72% compared with coal added with 60 g hydrogel D and pure water. The fire prevention effect of 60 g hydrogel C in coal combustion is slightly worse than that of 60 g hydrogel B. The order of avHRR values is hydrogel A (47.2 kW/m2) > water (45.8 kW/m2) > hydrogel D (32.0 kW/m2) > hydrogel B (12.7 kW/m2). In general, hydrogel B has the best effect on inhibiting coal combustion, simultaneously reducing PHRR, THR and avHRR. The order of TSP values is hydrogel D (5693.6 m2/m2) > water (2999.8 m2/m2) > hydrogel B (402.9 m2/m2). Compared with coal added with 60 g hydrogel D and pure water, the TSP of coal added with 60 g B was decreased by 93% and 87%, respectively (Table 4). In summary, the addition of hydrogel A will not reduce the heat release from coal combustion. Hydrogel B can significantly suppress heat release and smoke formation compared to other hydrogels. The addition of hydrogel C will significantly inhibit heat release. Hydrogel D can hinder heat release, but it is not capable ofsuppressing smoke formation.
Figure 10: (a) HRR, (b) THR and (c) TSP curves of 20 g coal with 60 g fire extinguishing agents
In summary, hydrogel B can effectively inhibit the combustion of coal, reduce the combustion intensity of coal, and inhibit the generation of smoke. The more hydrogel D is added, the worse the fire prevention effect is. Hydrogel D is composed of polyacrylate and polyacrylamide which are inflammable. Therefore, the higher loading of hydrogel D incorporation, the worse the fire protection. 20 g and 40 g of hydrogel C had no effect, but 60 g of hydrogel C had a good effect on inhibiting combustion. Hydrogel A has no fire prevention effect at all and is even weaker than water.
The water content of the four kinds of hydrogel materials was completely removed after being dried in an oven at 80°C. The combustion process and heat release behavior of four kinds of hydrogels were studied based on a micro calorimeter test (Fig. 11). Below 250°C, four kinds of hydrogels had slight heat release, which was due to the weak thermal stability of hydroxyl and acetate groups within the structure of the hydrogel material [27]. In addition, hydrogel A made of 1 wt% phosphorus-modified cellulose+1 wt% fumed silica+98 wt% water showed significantly earlier heat. This result shows that the thermal stability of phosphorus-modified cellulose is weaker than that of sodium alginate, sodium polyacrylate, and carrageenan. Compared with the high heat release peaks of hydrogels A, C, and D, hydrogel B only showed a relatively flat heat release curve, indicating that hydrogel B had high flame retardancy. The above phenomenon may be attributed to the potential intumescent flame retardant system [28]. Sodium alginate as a bio-based carbon-forming agent and ammonium polyphosphate (both as gas and acid sources) significantly promote the formation of a protective carbon layer. The two obvious heat release peaks in hydrogel D are due to the coexistence of sodium polyacrylate and polyacrylamide [29]. In the THR curves, hydrogel B had the best flame retardancy after being dried. A reliable flame retardancy mechanism is proposed. After being sprayed onto the surface of coal, the hydrogel first plays a fire extinguishing effect with the absorption of heat and evaporation of water. Then, sodium alginate decomposes into unsaturated carbon-based pyrolysis products to react with the thermal decomposition products of ammonium polyphosphate [30,31]. The reaction between unsaturated carbon-based pyrolysis products and phosphorus-containing free radicals will promote the formation of the char layer. Meanwhile, the NH3 from the thermal decomposition of ammonium polyphosphate will promote the swelling of the char layer and dilute the inflammable products (Fig. 12).
Figure 11: HRR and THR curves of four hydrogels after being dried
Figure 12: The fire suppression mechanism of hydrogel B
This study finds that under 200°C, coal cannot be ignited and produces CO and CO2. Above 250°C, there is an obvious CO and CO2 emission peak, demonstrating a critical heating temperature. At the same time, the temperature rise of the external heat source is conducive to the earlier release of CO and CO2. Compared with water and 3.5 wt% MgCl2 solution, hydrogel C has a better fire-extinguishing effect on coal combustion. A further increase to 350°C from 300°C will increase the maximum CO2 concentration in coal with additives; however, a similar phenomenon is not presented in pure coal. This result confirms that the critical heating temperatures for the complete combustion of pure coal and coal with additives are different, near 300°C and 350°C, respectively. Even with the same CO2 concentration at 350°C, the corresponding time for the peak value of CO2 concentration is effectively prolonged by the addition of hydrogel C. Meanwhile, the fire prevention effect of four hydrogels is also studied for coal combustion. Hydrogels composed of sodium alginate, water-soluble APP, and sepiolite present the highest fire suppression effect, showing a positive relation to additive increase. The MCC results from dried hydrogels indicate that the high suppression effect of hydrogel B can be attributed to the formation of an intumescent flame retardant system. Hydrogel B can effectively inhibit the combustion of coal, reduce the combustion intensity of coal, and inhibit the generation of smoke, presenting the most effective fire extinguishing performance.
Funding Statement: The authors acknowledge the National Key Research and Development Program of China (Grant No. 2017YFC0805900), the Fundamental Research Funds for the Central Universities (Grant No. WK2320000047) and the USTC Research Funds of the Double First-Class Initiative (Grant No. YD2320002004).
Conflicts of Interest: The authors declare that they have no conflicts of interest to report regarding the present study.
References
1. Chernetskiy, M. Y., Dekterev, A. A. (2011). Mathematical model for heat transfer and combustion in a pulverized coal flame. Combustion Explosion and Shock Waves, 47(3), 280–288. https://doi.org/10.1134/S001050821103004X [Google Scholar] [CrossRef]
2. Huang, Z. A., Xiao, S. L., Lu, W., Gao, Y. K., Zhang, Y. H. et al. (2018). Means of protecting materials from spontaneous coal combustion: Current developments, mechanisms, classifications, and prospects. International Journal of Materials and Structural Integrity, 12(1–3), 125–150. https://doi.org/10.1504/IJMSI.2018.093906 [Google Scholar] [CrossRef]
3. Cao, Q., Shen, J. J., Guo, W. J. (2020). Effects of foaming agent on properties of foamed gel. Advanced Composites Letters, 29. https://doi.org/10.1177/0963693519881649 [Google Scholar] [CrossRef]
4. Yu, Z., Liu, J., Suryawanshi, A., He, H., Wang, Y. (2021). Thermal insulating and fire-retarding behavior of treated cotton fabrics with a novel high water-retaining hydrogel used in thermal protective clothing. Cellulose, 105(15), 151903. https://doi.org/10.1007/s10570-021-03696-y [Google Scholar] [CrossRef]
5. Madhavikutty, A. S., Chandel, A. K. S., Tsai, C. C., Inagaki, N. F., Ohta, S. et al. (2023). pH responsive cationic guar gum-borate self-healing hydrogels for muco-adhesion. Science and Technology of Advanced Materials, 24, 2175586. https://doi.org/10.1080/14686996.2023.2175586 [Google Scholar] [PubMed] [CrossRef]
6. Matthiesen, I., Jury, M., Boroojeni, F. R., Ludwig, S. L., Holzreuter, M. et al. (2023). Astrocyte 3D culture and bioprinting using peptide functionalized hyaluronan hydrogels. Science and Technology of Advanced Materials, 24, 2165871. https://doi.org/10.1080/14686996.2023.2165871 [Google Scholar] [PubMed] [CrossRef]
7. Kirchmajer, D. M., Gorkin, R. I. I. I., Panhuis, M. I. H. (2015). An overview of the suitability of hydrogel-forming polymers for extrusion-based 3D-printing. Journal of Materials Chemistry B, 3(20), 4105–4117. https://doi.org/10.1039/C5TB00393H [Google Scholar] [PubMed] [CrossRef]
8. Huang, Y., Zhou, J., Sun, P., Zhang, L., Qian, X. et al. (2021). Green, tough and highly efficient flame-retardant rigid polyurethane foam enabled by double network hydrogel coatings. Soft Matter, 17(46), 10555–10565. https://doi.org/10.1039/D1SM01213D [Google Scholar] [PubMed] [CrossRef]
9. Yu, Z., Suryawanshi, A., He, H., Liu, J., Li, Y. et al. (2020). Preparation and characterisation of fire-resistant PNIPAAm/SA/AgNP thermosensitive network hydrogels and laminated cotton fabric used in firefighter protective clothing. Cellulose, 27(9), 5391–5406. https://doi.org/10.1007/s10570-020-03146-1 [Google Scholar] [CrossRef]
10. Illeperuma, W. R. K., Rothemund, P., Suo, Z., Vlassak, J. J. (2016). Fire-resistant hydrogel-fabric laminates: A simple concept that may save lives. ACS Applied Materials & Interfaces, 8(3), 2071–2077. https://doi.org/10.1021/acsami.5b10538 [Google Scholar] [PubMed] [CrossRef]
11. Kuznetsov, P. N., Fetisova, O. Y., Kuznetsova, L. I., Avid, B., Purevsuren, B. (2023). Insight into the key kinetic steps in the pyrolysis of coking and non-coking coals, characterization of the pyrolysis products. International Journal of Coal Science & Technology, 10, 316. https://doi.org/10.1007/s40789-023-00574-9 [Google Scholar] [CrossRef]
12. Zhu, G. Q., Hui, S. E., Niu, Y. Q., Kang, Y. Q., Lv, Y. (2023). Fast pyrolysis of pulverized coal at high temperatures and fuel nitrogen migration characteristics in a wire mesh reactor. Energy Sources Part A–Recovery Utilization and Environmental Effects, 45, 1551–1563. https://doi.org/10.1080/15567036.2023.2179693 [Google Scholar] [CrossRef]
13. Wang, C. Y., Shi, H., Wang, X., Song, L., Hu, Y. (2022). Carrageenan-vermiculite-dimethyl methyl phosphate ternary hybrid hydrogels for firefighting. Fire and Materials, 47(3), 400–410. https://doi.org/10.1002/fam.3105 [Google Scholar] [CrossRef]
14. Nabipour, H., Shi, H., Wang, X., Hu, X. M., Song, L. et al. (2022). Flame retardant cellulose-based hybrid hydrogels for firefighting and fire prevention. Fire Technology, 58(4), 2077–2091. https://doi.org/10.1007/s10694-022-01237-y [Google Scholar] [CrossRef]
15. Wang, C. Y., Shi, H., Wang, X., Song, L., Hu, Y. (2022). Alginate-sepiolite-ammonium polyphosphate ternary hybrid gels for firefighting in grain and cotton reserves. Journal of University of Science and Technology of China, 52(3), 8. https://doi.org/10.52396/JUSTC-2021-0181 [Google Scholar] [CrossRef]
16. Wang, H., Fan, C., Li, J., Zhang, Y., Sun, X. et al. (2023). Dynamic characteristics of near-surface spontaneous combustion gas flux and its response to meteorological and soil factors in coal fire area. Environmental Research, 217, 114817. https://doi.org/10.1016/j.envres.2022.114817 [Google Scholar] [PubMed] [CrossRef]
17. Sethurajaperumal, A., Manohar, A., Banerjee, A., Varrla, E., Wang, H. et al. (2021). A thermally insulating vermiculite nanosheet-epoxy nanocomposite paint as a fire-resistant wood coating. Nanoscale Advances, 3(14), 4235–4243. https://doi.org/10.1039/D1NA00207D [Google Scholar] [PubMed] [CrossRef]
18. Liang, Y., Yu, J., Peng, Z., Ai, P. (2013). Flammability and thermal properties of bitumen with aluminium trihydroxide and expanded vermiculite. Construction and Building Materials, 48, 1114–1119. https://doi.org/10.1016/j.conbuildmat.2013.07.074 [Google Scholar] [CrossRef]
19. Liang, W., Ning, X., Zhang, J., Li, Y., Niu, L. et al. (2022). Effect of ash on coal combustion performance and kinetics analysis. Combustion Science and Technology, 194(4), 785–800. https://doi.org/10.1080/00102202.2020.1786077 [Google Scholar] [CrossRef]
20. Cui, X. F., Zheng, W. J., Zou, W., Liu, X. Y., Yang, H. et al. (2019). Water-retaining, tough and self-healing hydrogels and their uses as fire-resistant materials. Polymer Chemistry, 10(37), 5151–5158. https://doi.org/10.1039/C9PY01015G [Google Scholar] [CrossRef]
21. Xu, Q., Jin, C., Jiang, Y. (2017). Compare the flammability of two extruded polystyrene foams with micro-scale combustion calorimeter and cone calorimeter tests. Journal of Thermal Analysis and Calorimetry, 127(3), 2359–2366. https://doi.org/10.1007/s10973-016-5754-6 [Google Scholar] [CrossRef]
22. Geschwindner, C., Goedderz, D., Li, T., Bender, J., Dreizler, A. et al. (2023). The effects of various flame retardants on the combustion of polypropylene: Combining optical diagnostics and pyrolysis fragment analysis. Polymer Degradation and Stability, 211, 110321. https://doi.org/10.1016/j.polymdegradstab.2023.110321 [Google Scholar] [CrossRef]
23. Soni, V., Dahiya, J. B. (2023). Synthesis and characterization of a novel P/N containing flame retardant and its effect on flame-retardancy, thermal and mechanical properties of epoxy/clay nanocomposites. High Performance Polymers. https://doi.org/10.1177/09540083231169166 [Google Scholar] [CrossRef]
24. Bin, C., Yang, L. (2022). Enhanced flame retardancy of rigid polyurethane foams by polyacrylamide/MXene hydrogel nanocomposite coating. International Journal of Molecular Sciences, 23(20), 12632. https://doi.org/10.3390/ijms232012632 [Google Scholar] [PubMed] [CrossRef]
25. Feng, X. M., Yang, H. Y. (2023). Boosting flame retardancy of thermoplastic polyurethane: Synergistic effect of nickel phosphide nanoparticles and molybdenum disulfide nanosheets. Journal of Vinyl & Additive Technology, 1–12. https://doi.org/10.1002/vnl.22001 [Google Scholar] [CrossRef]
26. Tan, Y. W., Xie, J. G., Wang, Z. Q., Li, K., He, Z. Y. (2023). Effect of halloysite nanotubes (HNTs) and organic montmorillonite (OMMT) on the performance and mechanism of flame retardant-modified asphalt. Journal of Nanoparticle Research, 25, 74. https://doi.org/10.1007/s11051-023-05697-3 [Google Scholar] [CrossRef]
27. Dong, W., Wang, Y., Huang, C., Xiang, S., Ma, P. et al. (2014). Enhanced thermal stability of poly(vinyl alcohol) in presence of melanin. Journal of Thermal Analysis and Calorimetry, 115(2), 1661–1668. https://doi.org/10.1007/s10973-013-3419-2 [Google Scholar] [CrossRef]
28. Dong, X., Nie, S., Liu, Z., Wang, D. Y. (2016). Study of the synergistic effect of nickel phosphate nanotubes (NiPO-NT) on intumescent flame retardant polypropylene composites. Journal of Thermal Analysis and Calorimetry, 126(3), 1323–1330. https://doi.org/10.1007/s10973-016-5681-6 [Google Scholar] [CrossRef]
29. Natkanski, P., Kustrowski, P., Bialas, A., Piwowarska, Z., Michalik, M. (2013). Thermal stability of montmorillonite polyacrylamide and polyacrylate nanocomposites and adsorption of Fe(III) ions. Applied Clay Science, 75–76, 153–157. https://doi.org/10.1016/j.clay.2013.02.002 [Google Scholar] [CrossRef]
30. Mateescu, M., Vlase, G., Budiul, M. M., Cernusca, B. D., Vlase, T. (2023). Preliminary study for preparation and characterization of medicated jelly based on Ibuprofen or Ambroxol. Journal of Thermal Analysis and Calorimetry, 148, 4601–4614. https://doi.org/10.1007/s10973-023-12052-0 [Google Scholar] [CrossRef]
31. Quan, Y. F., Shen, R. Q., Schweizer, C., Parajuli, P., Zhang, Z. R. et al. (2023). Synergistic effects of zeolitic imidazolate frameworks (ZIFs) with different transition metals on intumescent flame-retarded polypropylene composites: A comparative study. Journal of Materials Science & Technology, 155, 102–110. https://doi.org/10.1016/j.jmst.2023.01.015 [Google Scholar] [CrossRef]
Cite This Article
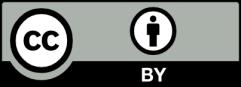
This work is licensed under a Creative Commons Attribution 4.0 International License , which permits unrestricted use, distribution, and reproduction in any medium, provided the original work is properly cited.