Open Access
ARTICLE
Water Absorption Capacity and Coating Adhesion on Thermally Modified and Not-Modified Spruce Wood (Blue Stained or Free of Blue Stained)
1
Key Lab of State Forest and Grassland Administration on “Wood Quality Improvement & High Efficient Utilization”, School of
Forestry & Landscape Architecture, Anhui Agricultural University, Hefei, 230036, China
2
Faculty of Technical Engineering, Department of Wood Science and Technology, University of Bihać, Bihać, 7700, Bosnia and
Herzegovina
3
Department of Natural Resources and Earth Science, Shahrekord University, Shahrekord, 64165478, Iran
4
Biotechnical Faculty, Department of Wood Science, University of Ljubljana, Ljubljana, 1501, Slovenia
* Corresponding Author: Mohsen Bahmani. Email:
(This article belongs to the Special Issue: Special Issue in Celebration of JRM 10 Years)
Journal of Renewable Materials 2023, 11(12), 4061-4078. https://doi.org/10.32604/jrm.2023.043657
Received 08 July 2023; Accepted 18 August 2023; Issue published 10 November 2023
Abstract
This study aimed to investigate the water absorption capacity of thermally modified and non-modified spruce and blue-stained spruce wood. The wettability of wood depends on various factors, including its type, density, porosity, and surface treatment. Wood can swell and become distorted when exposed to water or humidity, impacting its structural integrity. Hence, it is crucial to consider the water and water vapour uptake in the wood when choosing materials for applications that are likely to be exposed to moisture. Various moisture absorption tests were conducted to assess water absorption capacity, including short-term and long-term water absorption and water vapour absorption. The results showed a significant difference in the long-term exposure to water, which was related to the density of the wood. The study examined the influence of thermal treatment on the physical properties of wood and observed significant variations in mass change due to coating, indicating differences in adhesion among different wood types. Vacuum-treated blue-stained Norway spruce demonstrated higher adhesion (5%–15%) compared to air-treated samples. Furthermore, cohesion tests revealed lower cohesion force in blue-stained Norway spruce (approximately 20%–30%) compared to Norway spruce. The study also used industry-standard tests to investigate the adhesion and cohesion of nano-coatings on wood surfaces. The results provided valuable information on the properties of coatings applied to wood, which is vital in protecting and decorating wood while also providing preventive protection against wood pests, weathering, and mechanical influences. Wood modification in vacuum involves subjecting the wood to a low-pressure environment to remove air and moisture, allowing for deeper and more uniform penetration of treatment chemicals. In contrast, wood modification in air relies on the natural circulation of air to facilitate the absorption of chemical treatments, without the need for a vacuum chamber.Graphic Abstract
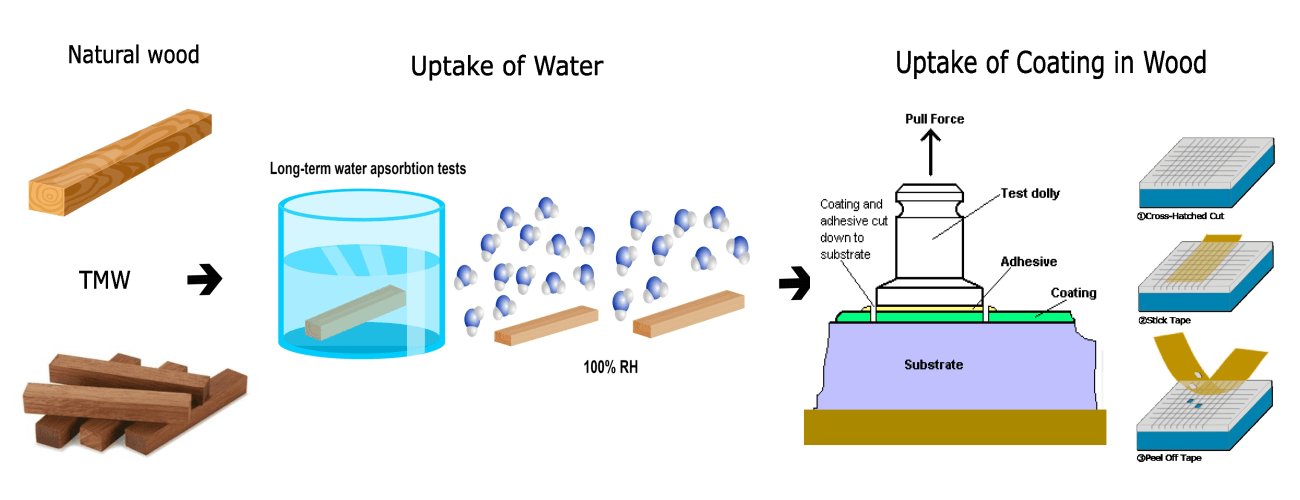
Keywords
Wood is one of the most essential building materials. The use of wood outdoors and its exposure to various abiotic and biotic parameters lead to its decomposition [1–3]. The function of a wooden structure is influenced by numerous parameters that should be considered, including wood species, environmental conditions, wood durability, application of biocides, and design and construction methods employed [4]. In addition to the inherent durability of the material, the moisture content and temperature conditions inside the wood, i.e., the climate of the material, are the most critical factors that affect the ability of fungi to decompose wood [5]. Various solutions are used to achieve the desired service life of wood, such as using different biocidal materials, different wood processing processes, proper design, and domestic or imported durable wood species [6]. Based on the exposure of the wood itself, additional protection can be applied with specific design measures, which is of great importance. However, if this is not sufficient or possible, a more durable material should be used. Permanent materials can be chosen from the group of naturally permanent types of wood (a limited number of species in Europe); wood treated with biocides or modified wood [7]. Spruce wood is one of the most important materials in Central Europe. However, the spruce has been under severe pressure due to climate changes [8]. Thus there are vast quantities of spruce that the bark beetles have attacked. This wood is frequently infested by blue stain fungi, which reduces the economic value of the wood [9]. The study [10] investigated the influence of different temperatures of thermal modification on changes in the essential chemical components of wood and the effect of these changes on the colour of the wood and its physical and mechanical properties.
Thermal wood modification enhances dimensional stability and provides an eco-friendly alternative to biocidal treatments [11–16]. Wood’s main drawbacks, such as low dimensional stability and biological durability, stem from its cell wall polymers, primarily due to abundant hydroxyl groups (OH) [17,18]. Chemical or thermal modification can transform inferior softwood species into superior products [19–21], aiming to create a material with safe disposal and reduced environmental risks compared to unmodified wood.
Wood modification can alter its structure, with the goal of enhancing properties like durability and dimensional stability. Commonly, wood modification reduces moisture content through thermal or chemical processes, affecting its cellulose, hemicellulose, and lignin components [22–27]. Recent publications highlight the increasing adoption of wood modification in Europe, recognizing it as a sustainable approach to improve wood performance [28–31]. Various methods, including thermal treatments, have been extensively studied [32–39]. In a study [40], softwood’s dimensional stability improved with higher temperature and processing time. Wood’s performance in ground contact is not significantly enhanced by thermal modification [41]. Thermal modification’s increased fungal durability does not result from the formation of new substances [42]. Experimental studies on thermally modified wood samples have investigated influential parameters, focusing on bending and tensile strength [2,43,44]. Eucalyptus wood was modified to evaluate its mechanical properties [5,45], and the influence of thermal treatment on Pierre ex Heckel wood’s properties was examined in another study [46].
On the other hand, thermally modified wood also has some drawbacks, such as reduced wettability, increased surface roughness and decreased adhesion of coatings. Therefore, coating adhesion tests are important to evaluate the performance of coatings on thermally modified wood. Manufacturers and contractors can ensure that their coatings will provide the desired protection and longevity on this unique material by performing coating adhesion testing on thermally modified wood. The primary objective of this research is to investigate the effect of water immersion on specific wood types and evaluate the impact of different levels of modification. This objective involves studying how the selected wood species behave regarding water absorption, leaching, and other water-related properties and analysing how different modification levels, such as thermal treatments, affect their effect on water immersion characteristics. The findings of this study will contribute to a better understanding of the water performance of the selected wood types and provide insights into the effectiveness of different levels of modification in altering their effect on water immersion properties. The respective manuscript aims to test the possibility of using blue-stained wood for thermal modification. Thermal modification diminishes the blue staining, as a darker colour characterises the thermally modified wood.
The samples of Norway Spruce (Picea abies (L.) H. Karst) and blue-stained Norway spruce for this study were from the area of Ljubljana, Slovenia State. Planks were air-dried to reduce the moisture content and then machined into the required dimensions in the direction parallel to the grain with a circular saw using the CEN EN 84 [47]. Radial grain wood specimens were selected for this study by obtaining samples from the cross-section of a tree trunk, following a radial line originating from the center of the tree and extending to the outer edge, thus intersecting the growth rings, which are visible concentric circles when a cross-section is taken after cutting down the tree. The samples were oven dried at 103 ± 2°C until a constant mass was achieved. After that, the mass and dimensions of the samples were measured to determine the moisture content of the samples. Blue-stained samples were obtained from bark beetle-damaged trees. Part of the spruce and blue-stained spruce samples were thermally modified at two different temperatures, one in a vacuum and the other in the air.
2.2 Thermal Modification Process
The thermal modification was performed according to a commercial process (Silvapro®, Silvaprodukt, Ljubljana, Slovenia), with an initial vacuum in the first step of the treatment [10]. After the samples were placed in a vacuum reactor, a vacuum of about 95% was achieved in the chamber, where the absolute pressure was approximately 0.05 bar. The heating of the samples goes through seven phases (45°C, 90°C, 110°C, 140°C, 160°C, 185°C, 200°C, and 220°C), where the samples are heated to maximum temperatures (200°C, 220°C) and treated with maximum process duration times (TMD) of 3 h. The samples are then cooled over the next 12 h, re-dried at a temperature of 103°C, and weighed. After that, the samples were removed from the furnace and cooled in a silica gel desiccator. After that, mass and dimensions were determined to determine the mass change.
The second part of the samples, wrapped in aluminium foil, underwent a thermal modification process in the presence of air at high temperatures of 200°C and 220°C, with a maximum process duration of 3 h. The aluminum foil was used to protect the sample during the thermal modification process in the chamber due to elevated temperatures, ensuring its integrity and stability, while the heat treatment was intended to change the properties of the sample. High temperatures of 200°C and 220°C can significantly impact the material’s properties. This impact can include changes in structure, crystal lattice, density, and chemical reactions within the material. The presence of air during the thermal modification process can further affect changes in the material’s properties, such as oxidation or reduction. The maximum temperature of 3 h suggests that the sample was exposed to high temperatures for a certain period, which can result in significant changes in the material’s properties.
The results of this thermal modification process on the sample wrapped in aluminium foil can provide information on changes in the material’s properties after exposure to high temperatures and air, compared to thermal modification processes in a vacuum. Semi-radially oriented samples, which were carefully selected to capture a combination of radial and tangential characteristics, were precisely sawn to the dimensions of 15 mm × 25 mm × 50 mm (width × thickness × length) for scientific analysis. This orientation choice allows for a comprehensive investigation into wood properties that may exhibit variations based on the sample’s intermediate positioning between purely radial and tangential orientations. Samples were free of growth anomalies. Ten samples were prepared per material for test water-performance tests. Control samples of spruce wood and blue-stained spruce served as reference material and were not modified (Table 1).
We determined the average density of the oven-dry wood samples for each tested species by precisely weighing the samples and calculating their volume. The dimensions of the samples were measured as 15 mm × 25 mm × 50 mm (length × width × thickness) using appropriate tools such as callipers or rulers. After obtaining the mass and volume values, we employed a specific equation to calculate the average density. The equation used was based on scientifically accepted standards, ensuring accurate and reliable results. Wood density is a fundamental parameter that provides valuable insights into its physical characteristics and properties. It plays a crucial role in various scientific and practical applications, including predicting wood performance in different environments, understanding wood behavior during processing or manufacturing, and assessing the suitability of different wood species for specific uses. To ensure comparability, we focused on the density of oven-dried wood to avoid the influence of reduced hygroscopicity in thermally modified wood samples treated at different intensities.
To assess thermal modification, we measured the percentage of mass loss (% ML) using the oven-drying method. After thermal treatment at 103°C for 24 h, the samples were weighed before and after modification to determine % ML. Determining % ML is crucial in evaluating the effects of thermal modification. It involves calculating the difference in mass before and after modification and expressing it as a percentage using Eq. (1). This equation accounts for the initial mass of the sample and is commonly used in such studies.
(1)
Explained as: ML (%) is the mass loss; mo (g) is the oven-dry mass of specimens before the treatment; mt (g) is the oven-dry mass of specimens after the thermal treatment.
The oven-drying method is a widely used and standardized approach to measure mass loss resulting from thermal modification in research and testing. It offers reproducible results, making it a valuable tool for assessing the level of modification or degradation that occurs due to thermal treatment.
Accurate measurement of mass loss is essential in understanding the impact of thermal modification on material properties, including changes in chemical composition, moisture content, and dimensional stability. This information is crucial for evaluating material performance and suitability for specific applications, particularly in wood or biomaterials science, where thermal modification is frequently utilized to enhance specific properties or functionalities.
2.5.1 Long-Term Water Uptake Test with Drying Process above Freshly Activated Silica Gel
The long-term water uptake of the specimens was assessed using the ENV 1250-2 (CEN, 1994) [48] leaching procedure, a standardised method for evaluating the water absorption characteristics of materials. Before the test, the specimens were subjected to oven-drying at a specific temperature of 103 ± 2°C for 24 h to ensure they were oven-dry. The oven-dry wood blocks were carefully weighed to determine their oven-dry mass, which serves as the baseline for measuring the water uptake. To conduct the test, the oven-dried wood blocks were placed in a glass jar and positioned with masses to prevent them from floating in the water (Fig. 1). A precise amount of distilled water, typically 100 g, was added to each specimen to initiate the water uptake. The specimens were left in the jar for designated time intervals, such as 1, 4, 8, and 24 h, to allow for water absorption.
Figure 1: Long-term water absorption tests
After each time interval, the specimens were removed from the jar, and their masses were measured again to determine the change in mass due to water uptake. The difference in mass between the initial oven-dry mass and the mass after each time interval provides the measure of water uptake by the specimens. This change in mass is used to calculate the moisture content of the samples, which is a critical parameter in evaluating the water absorption behaviour of the wood. This analysis used ten spruce and blue stained spruce type samples and five control spruce wood samples to ensure statistical accuracy and reliability. The ENV 1250-2 [48] leaching procedure is a widely recognised method for studying the long-term water uptake of materials. It provides valuable information on the moisture behaviour of wood, which is vital for understanding its durability, dimensional stability, and performance in various environmental conditions.
2.5.2 Water Vapour Uptake in a Water-Saturated Atmosphere
We needed ten samples of each material with dimensions of 50 mm × 25 mm × 15 mm (60 samples) and one glass chamber to conduct the test. At the bottom of each chamber, we placed a low aluminium container into which we poured distilled water to the top and placed a steel stand with holes. They allow air to circulate in the chamber and between samples. At the edge of the chamber, just below the top, we installed a fan, closed the chamber with a lid, sealed it with stretch film, and connected it with a fan to allow air to circulate. This setup created a climate with almost 100% relative humidity (Fig. 2).
Figure 2: Tests for water vapour absorption in an atmosphere saturated with water
The wood samples were first dried for 24 h in a Kambič dryer, at 103°C, to oven dry state, then cooled in a desiccator for 10 min, and their mass (m0) was measured. The weighed samples were then loaded onto steel shelves in the chambers and exposed to 100% RH. After 24 h, the masses of all samples were weighed again and again exposed to the climate. The samples were then weighed once a week until balanced. Balanced measurement was determined based on changes in sample mass, i.e., if the mass differences were more significant than 1% of the previous ones, this meant that balancing was still in progress. Equilibrium moisture content in the sample was achieved after six weeks of exposure to air conditioning, then dried for 24 h in a container with silica gel and last measured their masses.
At the end of the test, we calculated the average final moisture content for individual materials after 24 h and four weeks of exposure (Eqs. (2) and (3)).
(2)
(3)
-final moisture content of the samples after 24 h of exposure to 100% RH (%)
-final moisture content of the samples after four weeks of exposure to 100% RH (%)
-sample mass after 24 h of exposure (g)
-sample mass after four weeks of exposure (g)
-the mass of oven-dry sample (g)
This research evaluated the coating adhesion on hand-applied wood samples using commercial acrylic Belinka lasur for wood. The experiment used six wood samples of each wood type (500 mm × 25 mm × 15 mm). The samples were first weighed using an analytical balance with a precision of ±0.001 g, and the coated samples were weighed again. After the coating application, the samples were allowed to dry for 15 days under ambient conditions (temperature of 20 ± 2°C and relative humidity of 50 ± 5%). The difference in mass between the two measurements was calculated and recorded as the mass change due to the lasure coating. The test was performed in six replicates for each wood type, and the results were expressed as the mean mass change in grams.
The adhesion of a coating to wood was evaluated using the EN 2409 standard [49]. In this method, a unique cutting tool was used to create a grid pattern of cross-cut incisions on the radial surface of the wood samples to evaluate the coating adhesion. The incisions were made at a 90-degree angle to each other, resulting in a grid of squares approximately 1 mm in size. Care was taken to ensure that the incisions penetrated the coating and wood substrate. After the incisions were made, the samples were cleaned using a soft brush to remove debris or loose coating. A strip of adhesive tape was applied to the sample and rubbed down firmly using a finger or a roller to ensure good contact between the tape and the coating. The tape was then quickly and firmly pulled off the sample in a single motion at an angle of approximately 180 degrees to the surface. The degree of adhesion was evaluated by visually examining the grid pattern and recording the number of squares from which the coating had been removed. The adhesion was scored on a scale of 0 to 5, where 0 indicates no coating removal, and 5 indicates complete coating removal from all squares in the grid. The test was performed in triplicate for each sample, and the results were expressed as the mean adhesion score. The EN 2409 standard [49] provides a reliable and reproducible method for evaluating the adhesion of coatings to wood substrates. It is widely used in the industry and provides a valuable tool for comparing the adhesion properties of different coatings and wood substrates.
The cohesion testing of the nano-coating on the wood surface was performed according to the EN 24624 standard [50]. The samples had dimensions of 500 mm × 25 mm × 15 mm for each type of wood, and the testing was conducted on three samples per wood type. The sample preparation involved sanding the sample’s surface with sandpaper with 240 grit abrasive material. After sanding, the samples were thoroughly cleaned of dust and other impurities. To conduct the cohesion test, the samples were fixed in a sample holder that contained a cylindrical steel attachment. Nano-coatings were applied on top of the attachment according to the manufacturer’s instructions and left to dry for the recommended time. After drying, the samples were placed in a cohesion testing machine, and the testing began. The attachment was placed on the sample during the testing, so the coating was sandwiched between two steel plates. The system was then subjected to a specific force until the coating was detached from the wood. The forces applied were gradually increased, with force measurements being taken using sensors and software connected to the cohesion testing machine. All force values were recorded on a computer during testing. The results of the cohesion test are expressed in the force required to detach the coating from the wood, expressed in MPa.
On average, ten replicates were used for most of the tests. Statistical analysis of the data obtained was conducted using Microsoft Excel with the Analyse-it for Microsoft Excel 4.90 add-on, a software tool developed by Analyse-it Software, Ltd., based in Leeds, United Kingdom. The student’s t-test, a commonly used statistical method for comparing the means of two groups, was employed to verify the difference between the thermal and control samples statistically. The student’s t-test is a parametric test that assesses whether the means of two groups are significantly different from each other based on the assumption that the data follows a normal distribution. In this case, the test was used to determine whether there was a statistically significant difference between the thermal and control samples.
The density of the samples used in the research was calculated by determining the mass and volume of the samples in an oven-dry state. The median density of the Norway spruce samples was the highest among all the investigated samples, with a value of 0.42 g/cm3. On the other hand, the blue-stained Norway spruce samples, subjected to thermal treatment in a vacuum at 220°C, exhibited the lowest density among all the investigated samples, with a value of 0.294 g/cm3 (Fig. 3). Statistical analysis was conducted further to investigate the differences in density between the various samples. The statistical analysis results revealed significant density differences among all the study’s samples. The statistical analysis likely involved appropriate statistical tests, such as analysis of variance (ANOVA) or posthoc tests, to determine the significance of the observed differences in density. The findings suggest that the thermal treatment, specifically the vacuum treatment at 220°C, had a notable impact on the density of the Blue stained Norway spruce samples compared to the untreated and the other investigated samples.
Figure 3: Densities of wood samples modified in vacuum and air of Norway spruce and Blue stained Norway spruce
3.2 Statistical Assessment of Mass Loss
The mass loss (ML) measurements were recorded to assess the effects of thermal treatment on the samples. Among the investigated samples, the lowest ML was observed in spruce samples subjected to vacuum treatment at 200°C, with a recorded ML of 3.3%. On the other hand, the highest ML was recorded in blue-stained Norway spruce wood samples, which underwent thermal treatment at a temperature of 220°C, with a recorded ML of 10%. Comparing the ML values between blue-stained Norway spruce and spruce samples, it was observed that blue-stained Norway spruce exhibited slightly higher ML than spruce samples, regardless of whether the treatment was conducted in a vacuum in the presence of air (Table 1). These findings indicate that the thermal treatment at higher temperatures, specifically 220°C, resulted in a more significant mass loss in the blue-stained Norway spruce samples compared to the spruce samples.
The observed mass losses of the samples in this study are consistent with the findings reported in the literature [51]. The degradation of hemicellulose and lignin is expected to occur primarily at the temperature used in the thermal treatment, as cellulose tends to be more resistant to thermal degradation than hemicellulose and lignin [52]. One surprising observation was that higher mass losses were determined in vacuum-modified wood than wood modified under ambient conditions (wrapped in foil). This difference can be attributed to the fact that the pressure during the vacuum modification process was lower than the ambient pressure. This pressure difference likely influenced the reaction kinetics and resulted in removing degradation products from the wood during the vacuum treatment. In contrast, in the samples wrapped in foil, the degradation products remained close to the wood, leading to condensation and polymerisation of the degradation products within the modified wood. This difference in the behaviour of degradation products between vacuum-modified wood and wood modified under ambient conditions could contribute to the observed differences in mass losses between the two treatments. These findings suggest that the pressure conditions during the thermal modification process can impact the extent of mass loss in wood samples, with vacuum treatment resulting in higher mass losses than treatment under ambient conditions. This provides valuable insights into the complex interactions between pressure, temperature, and reaction kinetics during wood modification processes and highlights the need to carefully consider process parameters to achieve desired modifications in wood properties.
Water immersion has been identified as another important factor influencing the service life of wood in outdoor applications [53]. Wood with better water exclusion efficacy has longer service life than wood with lower water exclusion efficacy, regardless of comparable durability. Therefore, various effects of water immersion tests were performed on spruce and blue-stained spruce species in thermally modified and controlled wood samples. There were no statistically significant differences in the samples observed between different types of spruce samples. The uptake of water increases with increasing immersion time. Reference spruce wood uptakes 33.27% of water after the first hour of immersion, and the uptake gradually increases to 90.91% after seven days of immersion. Comparable uptakes were determined at blue-stained wood as well. However, the uptakes were slower initially, but the final value was comparable (Table 2). On the other hand, thermal modification considerably reduced water uptake. For example, after the first hour of immersion, the MC of thermally modified wood, at 220°C, uptakes five times less water than non-modified wood. Even after seven days of immersion, the MC of modified wood was still lower than that of reference wood species. A comparable trend was observed in specimens modified at both temperatures and procedures. The influence of temperature was noticed in the first periods of immersion and became less significant after seven days of immersion (Table 2). This proves that the effect of water immersion of thermally modified blue stained wood is comparable to the reference modified wood. The same effect of water immersion of modified wood has already been reported for non-discoloured wood [39,54], but has not been reported for blue-stained wood (Table 2).
“Long-term water uptake test”, an ANOVA analysis was performed to determine if there were any statistically significant differences in water absorption between the different types of spruce samples. The analysis revealed no statistically significant differences between the samples (p > 0.005). The water uptake increased with increasing immersion time, but the differences between the spruce species were not statistically significant. Comparable uptakes were observed in blue-stained wood samples compared to the reference spruce wood (Table 2).
After exposing samples of different materials to a climate with approximately 100% relative humidity (RH), we monitored their equilibrium weekly by weighing their masses. Based on the change in mass, we determined whether the samples had already reached equilibrium (difference in mass smaller than 1%). The samples equilibrated (reached the final equilibrium moisture content) after four weeks of exposure to 100% climate. We calculated their average final moisture content (Eqs. (2) and (3)).
In reference, modified wood samples reached 24.4 % after four weeks of conditioning; the MC of blue-stained wood was lower and reached 19.5% only (Table 3). The thermal modification resulted in decreased wood moisture content. The final minimum moisture content of thermally modified samples (TM 220°C, vacuum) averaged 12.8% for blue-stained spruce samples, and the highest moisture content was achieved (19.8%). There was no significant difference between the modification in the vacuum and modification performed in the air noticed, as resolved from Table 3. Based on the results, we cannot confirm that different modification treatments and temperatures significantly affect the trend of moisture absorption in wood. However, the critical question is if the blue-stained wood is suitable for thermal modification. At all treatments, the equilibrium MC of blue-stained wood was lower than that of the reference wood species. For example, the MC of wood modified in a vacuum at 220°C was 15%, while the MC of blue-stained wood modified according to the same process was considerably lower (12.8%) (Table 3). The key question is, what is the explanation for this phenomenon? It might be associated with consuming simple sugars by blue-stain fungi, predominately as the structure of the main constituents of the wood (lignin, cellulose, hemicelluloses) are not affected by the blue-stain fungi [55]. For the “Water vapour uptake” test, an ANOVA analysis was conducted to assess the moisture absorption of the samples under different treatment methods and temperatures. The analysis indicated no statistically significant differences in moisture absorption between the treatment methods and temperatures (p > 0.005). The thermal modification significantly reduced the moisture content of the wood compared to the reference wood species. Additionally, blue-stained wood exhibited lower equilibrium moisture content than the reference wood species across all treatments. However, according to the ANOVA analysis, these differences were not statistically significant (Table 3).
3.4 Analysis of Properties of Coatings Applied to Wood
The results showed that the mass change due to the coating varied depending on the wood type. The coating had a more remarkable mass change on some wood types compared to others, indicating a difference in adhesion between the wood types (Table 4).
Table 5 presents data on the degree of adhesion for various wood samples and coating treatments (see Fig. 4).
Figure 4: Adhesion test on samples to assess the bonding strength of the materials
The degree of adhesion is expressed on a scale from 1 to 5, where 1 indicates adhesion of less than 5%, and 5 indicates adhesion of more than 65%. The first two rows show data for untreated Norway spruce and blue-stained Norway spruce, both with a degree of adhesion of 2 (5%–15%). The next four rows show data for Norway spruce and blue-stained Norway spruce thermally treated in a vacuum at 200 and 220 degrees Celsius. The adhesion for Norway spruce was 1 for 200 and 2 for 220 degrees, while the adhesion for blue-stained Norway spruce was 3 for both temperatures. The last four rows show data for samples that were thermally modified in air at temperatures of 200 and 220 degrees Celsius. The adhesion for Norway spruce was 2 for 200 degrees and 3 for 220 degrees, while the adhesion for blue-stained Norway spruce was 3 for 200 degrees and 4 for 220 degrees. Overall, the data suggest that thermal modification in a vacuum positively affects the adhesion of the coatings, particularly for blue-stained Norway spruce. Thermal modification in air also appears to have a positive effect, though to a lesser extent.
Fig. 5 shows the results of the cohesion test on various types of wood.
Figure 5: Cohesion test on samples to assess the bonding strength of the materials
The results (Fig. 6) show that Blue stained Norway spruce has a lower cohesion force than Norway spruce in both the C and 220°C vacuum-treated categories. The difference in cohesion force between Norway spruce and Blue stained Norway spruce is approximately 30% in both cases. In the 220°C vacuum-treated category, Blue stained Norway spruce has a slightly lower cohesion force than Norway spruce, with a difference of approximately 20%. In the air-treated category, the cohesion force of Blue stained Norway spruce is slightly higher than Norway spruce, with a difference of approximately 1%.
Figure 6: Adhesion test results
Several factors can contribute to the observed differences in cohesion between different wood species. One crucial factor is the wood’s anatomical structure, which can affect the mechanical properties of the wood, including its cohesion. For example, wood with higher density and a more compact cellular structure is generally more cohesive than wood with a lower density and a less compact cellular structure. Another important factor is the wood’s chemical composition, particularly the lignin, cellulose, and hemicellulose content. Lignin is a major component of wood that provides structural support and helps bind the wood fibres together, while cellulose and hemicellulose contribute to the wood’s overall stiffness and strength. Wood with higher lignin content generally has higher cohesion than wood with lower lignin content. It should be considered that the level of the blue stain damage is not uniform. The intensity of the blue staining depends on the duration of infestation, season, post-harvesting manipulation. Thus it would make sense to consider the influence of various stages of infestation on water and the overall performance of wood. In addition, we have exposed the modified and non-modified blue-stained wood to weathering to compare laboratory and field trials.
The research findings indicate that blue-stained wood, which bark beetles have damaged, is a viable and suitable source for thermal modification. The mass losses observed in thermally modified blue-stained wood are comparable to those of the reference materials. Moreover, thermally modified blue-stained wood’s long-term water absorption properties are comparable to modified reference wood’s, suggesting a similar effect of water immersion characteristics. Furthermore, all the modified wood species, including blue-stained wood, exhibit significantly improved effects of water immersion properties compared to non-modified materials. The sorption properties of blue-stained wood, both in its non-modified and modified state, are even better than those of the reference spruce wood. This phenomenon suggests that thermally modified blue-stained wood may perform even better than non-blue-stained wood in above-ground applications. These findings highlight the potential of using thermally modified blue-stained wood as a suitable material for various applications, especially regarding its effect on water immersion characteristics. The results suggest that the blue-stained wood, despite its damaged state, can be effectively modified and utilised as a viable alternative to non-blue-stained wood. It may even exhibit the superior effect of water immersion properties in specific applications. The research analysed the properties of coatings applied to different types of wood and found that the mass change due to the coating varied depending on the wood type, indicating a difference in adhesion between the wood types. Also suggests that thermal modification in vacuum and air positively affects the adhesion of coatings, particularly for blue-stained Norway spruce. The results of the cohesion test on various types of wood indicate that the wood’s anatomical structure and chemical composition, particularly the content of lignin, cellulose, and hemicellulose, are essential factors that can contribute to the observed differences in cohesion between different wood species.
Acknowledgement: The authors would like to express their gratitude to the Faculty of Technical Engineering in Bihać, Department of Wood Science, and the Biotechnical Faculty in Ljubljana, Department of Wood Science, for granting access to the laboratories. Their support and resources have played a pivotal role in conducting the research and crafting this paper.
Funding Statement: The authors received no specific funding for this study.
Author Contributions: Conceptualization, M.H. methodology, M.B., R.H.; validation, R.H., D.H.; formal analysis, M.H., R.H., L.F.; investigation, R.H, M.H., L.F., D.C.; resources, R.H., M.H., M.B., L.F.; data curation, R.H, M.B., L.F., M.H. and D.C.; writing—original draft preparation, R.H., M.B., M.H., L.F. and D.C.; writing—review and editing, R.H., M.B. and D.C.; visualisation, R.H., M.H.; supervision, M.H.; project administration, R.H. and M.B.; funding acquisition, R.H. and D.C.
Availability of Data and Materials: The data that support the findings of this study are available from the corresponding, upon reasonable request.
Conflicts of Interest: The authors declare that they have no conflicts of interest to report regarding the present study.
References
1. van den Bulcke, J., de Windt, I., Defoirdt, N., de Smet, J., van Acker, J. (2011). Moisture dynamics and fungal susceptibility of plywood. International Biodeterioration & Biodegradation, 65, 708–716. [Google Scholar]
2. Chu, D., Hasanagić, R., Hodžić, A., Kržišnik, D., Hodžić, D. et al. (2022). Application of temperature and process duration as a method for predicting the mechanical properties of thermally modified timber. Forests, 13, 217. [Google Scholar]
3. Hasanagić, R., Ganguly, S., Bajramović, E., Hasanagić, A. (2021). Mechanical properties changes in fir wood (Abies sp.linden wood (Tilia sp.and beech wood (Fagus sp.) subjected to various thermal modification process conditions. IOP Conference Series: Materials Science and Engineering, 1208, 012025. https://doi.org/10.1088/1757-899x/1208/1/012025 [Google Scholar] [CrossRef]
4. Isaksson, T., Brischke, C., Thelandersson, S. (2012). Development of decay performance models for outdoor timber structures. Materials and Structures, 46, 1209–1225. https://doi.org/10.1617/s11527-012-9965-4 [Google Scholar] [CrossRef]
5. Brischke, C., Rapp, A. O. (2008). Influence of wood moisture content and wood temperature on fungal decay in the field: Observations in different micro-climates. Wood Science and Technology, 42, 663–677. https://doi.org/10.1007/s00226-008-0190-9 [Google Scholar] [CrossRef]
6. Reinprecht, L. (2016). Wood deterioration, protection and maintenance. Oxford, UK: John Wiley & Sons, Ltd. https://doi.org/10.1002/9781119106500 [Google Scholar] [CrossRef]
7. Kutnik, M., Suttie, E., Brischke, C. (2014). European standards on durability and performance of wood and wood-based products—Trends and challenges. Wood Material Science & Engineering, 9(3), 122–133. https://doi.org/10.1080/17480272.2014.894574 [Google Scholar] [CrossRef]
8. Hanewinkel, M., Cullmann, D. A., Schelhaas, M. J., Nabuurs, G. J., Zimmermann, N. E. (2012). Climate change may cause severe loss in the economic value of European forest land. Nature Climate Change, 3, 203–207. https://doi.org/10.1038/nclimate1687 [Google Scholar] [CrossRef]
9. Rep, G., Pohleven, F., Košmerl, S. (2012). Development of the industrial kiln for thermal wood modification by a procedure with an initial vacuum and commercialisation of modified Silvapro wood. In: Jones, D., Militz, H., Petrič, M., Pohleven, F., Humar, M. et al. (Eds.6th European conference on wood modification, pp. 11–17, Ljubljana, Slovenia: University of Ljubljana, Biotechnical Faculty, Department of Wood Science and Technology. [Google Scholar]
10. Nasir, V., Nourian, S., Avramidis, S., Cool, J. (2018). Prediction of physical and mechanical properties of thermally modified wood based on color change evaluated by means of “Group Method of Data Handling” (GMDH) neural network. Holzforschung, 73, 381–392. https://doi.org/10.1515/hf-2018-0146 [Google Scholar] [CrossRef]
11. Poncsak, S., Kocaefe, D., Younsi, R. (2010). Improvement of the heat treatment of jack pine (Pinus banksiana) using thermowood technology. European Journal of Wood and Wood Products, 69, 281–286. https://doi.org/10.1007/s00107-010-0426-x [Google Scholar] [CrossRef]
12. Kocaefe, D., Poncsak, S., Boluk, Y. (2008). Effect of thermal treatment on the chemical composition and mechanical properties of birch and aspen. BioResources, 3, 517–537. [Google Scholar]
13. Gunduz, G., Korkut, S., Aydemir, D., Bekar, I. (2009). The density, compression strength and surface hardness of heat treated hornbeam (Carpinus betulus L.) wood. Maderas. Ciencia y tecnología, 11(1), 61–70. https://doi.org/10.4067/s0718-221x2009000100005 [Google Scholar] [CrossRef]
14. Garcia, R. A., de Carvalho, A. M., de Figueiredo Latorraca, J. V., de Matos, J. L. M., Santos, W. A. et al. (2010). Nondestructive evaluation of heat-treated Eucalyptus Grandis hill ex Maiden wood using stress wave method. Wood Science and Technology, 46, 41–52. https://doi.org/10.1007/s00226-010-0387-6 [Google Scholar] [CrossRef]
15. Alrubaie, M. A. A., Lopez-Anido, R. A., Gardner, D. J., Tajvidi, M., Han, Y. (2019). Experimental investigation of the hygrothermal creep strain of wood-plastic composite lumber made from thermally modified wood. Journal of Thermoplastic Composite Materials, 33, 1248–1268. https://doi.org/10.1177/0892705718820398 [Google Scholar] [CrossRef]
16. Gaff, M., Kačík, F., Gašparík, M. (2019). Impact of thermal modification on the chemical changes and impact bending strength of European oak and Norway spruce wood. Composite Structures, 216, 80–88. https://doi.org/10.1016/j.compstruct.2019.02.091 [Google Scholar] [CrossRef]
17. Rowell, R. M. (2021). Understanding wood surface chemistry and approaches to modification: A review. Polymers, 13, 2558. https://doi.org/10.3390/polym13152558 [Google Scholar] [PubMed] [CrossRef]
18. Gérardin, P. (2015). New alternatives for wood preservation based on thermal and chemical modification of wood— A review. Annals of Forest Science, 73, 559–570. https://doi.org/10.1007/s13595-015-0531-4 [Google Scholar] [CrossRef]
19. Papadopoulos, A. N. (2010). Chemical modification of soild wood and wood raw material for composites production with linear chain carboxylic acid anhydrides: A brief review. BioResources, 5, 499–506. [Google Scholar]
20. Mantanis, G. I. (2017). Chemical modification of wood by acetylation or furfurylation: A review of the present scaled-up technologies. BioResources, 12(2), 4478–4489. https://doi.org/10.15376/biores.12.2.Mantanis [Google Scholar] [CrossRef]
21. Teng, T. -J., Mat Arip, M. N., Sudesh, K., Nemoikina, A., Jalaludin, Z. et al. (2018). Conventional technology and nanotechnology in wood preservation: A review. BioResources, 13(4), 9220–9252. https://doi.org/10.15376/biores.13.4.Teng [Google Scholar] [CrossRef]
22. Spear, M. J., Curling, S. F., Dimitriou, A., Ormondroyd, G. A. (2021). Review of functional treatments for modified wood. Coatings, 11(3), 327. [Google Scholar]
23. Esteves, B. (2009). Wood modification by heat treatment: A review. BioResources, 4(1), 370–404. [Google Scholar]
24. Jones, D., Sandberg, D., Goli, G., Todaro, L. (2019). Wood modification in Europe: A state-of-the-art about processes, products and applications. Florence, Italy: Firenze University Press. [Google Scholar]
25. Sandberg, D., Kutnar, A., Karlsson, O., Jones, D. (2021). Wood modification technologies. Principles, sustainability, and the need for innovation. Cambridge, UK: CRC Press. [Google Scholar]
26. Herrera-Díaz, R., Sepúlveda-Villarroel, V., Pérez-Peña, N., Salvo-Sepúlveda, L., Salinas-Lira, C. et al. (2017). Effect of wood drying and heat modification on some physical and mechanical properties of radiata pine. Drying Technology, 36, 537–544. [Google Scholar]
27. Korkut, S., Korkut, D. S., Kocaefe, D., Elustondo, D., Bajraktari, A. et al. (2012). Effect of thermal modification on the properties of narrow-leaved ash and chestnut. Industrial Crops and Products, 35, 287–294. [Google Scholar]
28. González-Penã, M. M., Curling, S. F., Hale, M. D. C. (2009). On the effect of heat on the chemical composition and dimensions of thermally-modified wood. Polymer Degradation and Stability, 94, 2184–2193. [Google Scholar]
29. González-Peña, M. M., Hale, M. D. C. (2009). Colour in thermally modified wood of beech, Norway spruce and Scots pine. Part 1: Colour evolution and colour changes. Holzforschung, 63, 385–393. [Google Scholar]
30. Hill, C. A. S., Jones, D. (1996). The dimensional stabilisation of Corsican pine sapwood by reaction with carboxylic acid anhydrides. Holzforschung, 50, 457–462. [Google Scholar]
31. Jebrane, M., Harper, D., Labbe, N., Sebe, G. (2011). Comparative determination of the grafting distribution and viscoelastic properties of wood blocks acetylated by vinyl acetate or acetic anhydride. Carbohydrate Polymers, 84, 1314–1320. [Google Scholar]
32. Marfo, E. D., Wereko, E. Y., Larbi, K. O. (2017). Chemical modification of the tropical hardwood species, Celtis mildbraedii (ESA FUFUOto improve its durability. Journal of Wood Chemistry and Technology, 38, 51–56. [Google Scholar]
33. Kumar, A., Richter, J., Tywoniak, J., Hajek, P., Adamopoulos, S. et al. (2018). Surface modification of Norway spruce wood by octadecyltrichlorosilane (OTS) nanosol by dipping and water vapour diffusion properties of the OTS-modified wood. Holzforschung, 72, 45–56. [Google Scholar]
34. Gérardin, P. (2016). New alternatives for wood preservation based on thermal and chemical modification of wood—A review. Annals of Forest Science, 73, 559–570. [Google Scholar]
35. Rowell, R. M. (2014). Acetylation of wood—A review. International Journal of Lignocellulosic Products, 1(1), 1–27. [Google Scholar]
36. Sandberg, D., Kutnar, A., Mantanis, G. (2017). Wood modification technologies—A review. iForest, 10, 895–908. [Google Scholar]
37. Stamm, A. J. (1956). Thermal degradation of wood and cellulose. Industrial & Engineering Chemistry, 48, 413–417. https://doi.org/10.1021/ie51398a022 [Google Scholar] [CrossRef]
38. Hill, C. A. S. (2007). Wood modification: Chemical, thermal and other processes. West Sussex, UK: John Wiley & Sons. [Google Scholar]
39. Dirol, D., Guyonnet, R. (1993). The improvment of wood durability by retification process. The International Research Group on Wood Preservation_Section 4_Report Prepared for the 24 Annual Meeting, 40015, 1–11. [Google Scholar]
40. Mazela, B., Zakrzewski, R., Grzeskowiak, W., Cofta, G., Bartkowiak, M. (2003). Preliminary research on the biological resistance of thermally modified wood. Proceedings of the 1st European Conference on Wood Modification. Ghent. [Google Scholar]
41. Kamdem, D. P., Pizzi, A., Triboulot, M. C. (2000). Heat-treated timber: Potentially toxic byproducts presence and extent of wood cell wall degradation. Holz als Roh-und Werkstoff, 58, 253–257. [Google Scholar]
42. Kamdem, D. P., Pizzi, A., Jermannaud, A. (2002). Durability of heat-treated wood. Holz als Roh- und Werkstoff, 60, 1–6. https://doi.org/10.1007/s00107-001-0261-1 [Google Scholar] [CrossRef]
43. Hasanagić, R. (2022). Optimization of thermal modification of wood by genetic algorithm and classical mathematical analysis. Journal of Forest Science, 68, 35–45. https://doi.org/10.17221/95/2021-JFS [Google Scholar] [CrossRef]
44. Hasanagić, R. (2019). Thermal modified wood: A critical review. RIM 2019–Development and Modernisation of Production Sarajevo, 2566, 80–85. [Google Scholar]
45. Wentzel, M., Brischke, C., Militz, H. (2019). Dynamic and static mechanical properties of eucalyptus nitens thermally modified in an open and closed reactor system. Maderas. Ciencia y tecnología, 21(2). https://doi.org/10.4067/S0718-221X2019005000201 [Google Scholar] [CrossRef]
46. Wentzel, M., Fleckenstein, M., Hofmann, T., Militz, H. (2018). Relation of chemical and mechanical properties of eucalyptus nitens wood thermally modified in open and closed systems. Wood Material Science & Engineering, 14, 165–173. https://doi.org/10.1080/17480272.2018.1450783 [Google Scholar] [CrossRef]
47. CEN EN 84:1997—Wood Preservatives—Accelerated Ageing of Treated Wood Prior to Biological Testing—Leaching Procedure. https://standards.iteh.ai/catalog/standards/cen/78929b10-74af-4f84-9ea6-d4358d125139/en-84-1997 [Google Scholar]
48. CEN EN 1250-2:1994 (2004). Wood preservatives—Methods for measuring losses of active ingredients and other preservative ingredients from treated timber—Part 2: Laboratory method for obtaining samples for analysis to measure losses by leaching into water or synthetic sea water, European Committee for Standardisation: Brussels, Belgium. [Google Scholar]
49. EN ISO 2409:1994—Paints and Varnishes—Cross-Cut Test (ISO 2409:1992). https://standards.iteh.ai/catalog/standards/cen/d5644e75-4282-4c3f-a503-be585c2eebb7/en-iso-2409-1994 [Google Scholar]
50. EN 24624:1992—Paints and Varnishes—Pull-off Test (ISO 4624:1978). https://standards.iteh.ai/catalog/standards/cen/c2cbdbfc-90fb-45f4-9956-d651c3ae7173/en-24624-1992 [Google Scholar]
51. Iyiola, E. A., Ayanleye, S. O., Catherine, O., Olufemi, B., Faruwa, F. A. et al. (2019). Impact of thermal treatment on anatomical and mechanical properties of ricinodendron heudelotii wood. Journal of Scientific Research and Reports, 22(5), 1–8. https://doi.org/10.9734/jsrr/2019/v22i530101 [Google Scholar] [CrossRef]
52. Torniainen, P., Elustondo, D., Dagbro, O. (2016). Industrial validation of the relationship between color parameters in thermally modified spruce and pine. BioResources, 11(1), 1369–1381. [Google Scholar]
53. Meyer-Veltrup, L., Brischke, C., Alfredsen, G., Humar, M., Flæte, P. O. et al. (2017). The combined effect of wetting ability and durability on outdoor performance of wood: Development and verification of a new prediction approach. Wood Science and Technology, 51, 615–637. https://doi.org/10.1007/s00226-017-0893-x [Google Scholar] [CrossRef]
54. Esteves, B., Sahin, S., Ayata, U., Domingos, I., Ferreira, J. et al. (2021). Effect of heat treatment on shore-D hardness of some wood species. BioResources, 16, 1482–1495. [Google Scholar]
55. Irle, M. A., Barbu, M. C., Réh, R., Bergland, L., Rowell, R. M. (2012). Wood composites. In: Handbook of wood chemistry and wood composites, pp. 321. Boca Raton, FL, USA: CRC Press. [Google Scholar]
Cite This Article
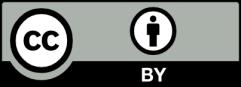
This work is licensed under a Creative Commons Attribution 4.0 International License , which permits unrestricted use, distribution, and reproduction in any medium, provided the original work is properly cited.