Open Access
ARTICLE
Naturally Nitrogen-Doped Biochar Made from End-of-Life Wood Panels for SO2 Gas Depollution
1
Research Forest Institute (Institut de Recherche sur les Forêts, IRF), University of Québec in Abitibi-Témiscamingue (UQAT),
Rouyn-Noranda, QC J9X 5E4, Canada
2
Technology Center for Industrial Waste (Centre Technologique des Résidus Industriels, CTRI), College of Abitibi-Témiscamingue
(Cégep de L’Abitibi-Témiscamingue), Rouyn-Noranda, QC J9X 5E5, Canada
3
École D’ingénieur de Sfax, Université De Sfax, Sfax, 3038, Tunisia
* Corresponding Author: Flavia Lega Braghiroli. Email:
(This article belongs to the Special Issue: Renewable Nanostructured Porous Materials: Synthesis, Processing, and Applications)
Journal of Renewable Materials 2023, 11(11), 3807-3829. https://doi.org/10.32604/jrm.2023.029454
Issue published 31 October 2023
Abstract
Reconstituted wood panels have several advantages in terms of ease of manufacturing, but their shorter life span results in a huge amount of reconstituted wood panels being discarded in sorting centers yearly. Currently, the most common approach for dealing with this waste is incineration. In this study, reconstituted wood panels were converted into activated biochar through a two-step thermochemical process: (i) biochar production using pilot scale fast pyrolysis at 250 kg/h and 450°C; and (ii) a physical activation at three temperatures (750°C, 850°C and 950°C) using an in-house activation furnace (1 kg/h). Results showed that the first stage removed about 66% of the nitrogen from the wood panels in the form of NO, NH3, and trimethylamine, which were detected in small amounts compared to emitted CO2. Compared to other types of thermochemical conversion methods (e.g., slow pyrolysis), isocyanic acid and hydrogen cyanide were not detected in this study. The second stage produced activated biochar with a specific surface area of up to 865 m2 /g at 950°C. The volatile gases generated during activation were predominantly composed of toluene and benzene. This two-step process resulted in nitrogen-rich carbon in the form of pyrrolic and pyridinic nitrogen. Activated biochars were then evaluated for their SO2 retention performance and showed an excellent adsorption capacity of up to 2140 mg/g compared to 65 mg/g for a commercial activated carbon (889 m2 /g). End-of-life reconstituted wood panels and SO2 gas are problematic issues in Canada where the economy largely revolves around forestry and mining industries.Graphic Abstract
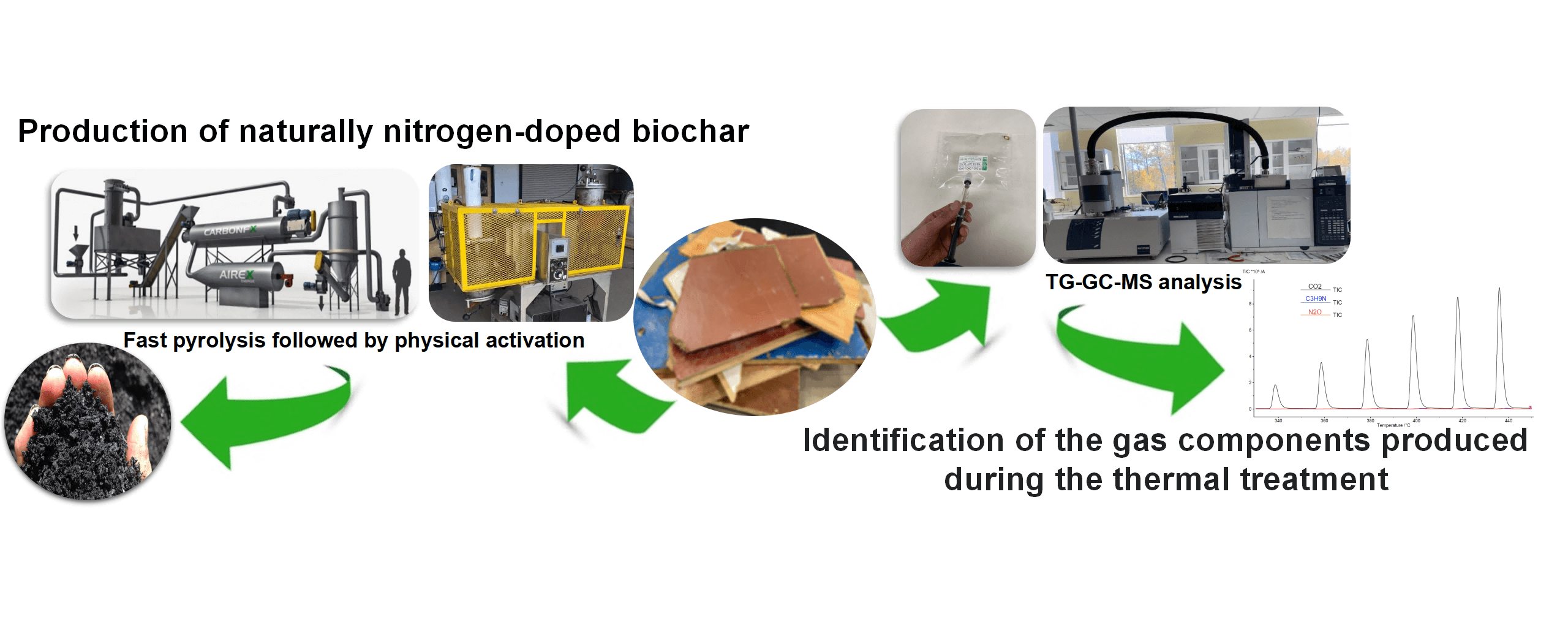
Keywords
Cite This Article
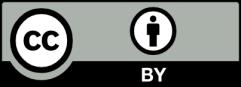
This work is licensed under a Creative Commons Attribution 4.0 International License , which permits unrestricted use, distribution, and reproduction in any medium, provided the original work is properly cited.