Open Access
ARTICLE
Flexible Biofoams Based on Furanics and Fatty Acids Esterified Tannin
1
LERMAB, University of Lorraine, Blvd des Aiguillettes, Nancy, 54000, France
2
Department of Wood and Fiber Industries, Faculty of Forestry and Environment, Universiti Putra Malaysia, Serdang, Selangor,
43400, Malaysia
3
Institute of Tropical Forestry and Forest Products (INTROP), Universiti Putra Malaysia, Serdang, Selangor, 43400, Malaysia
4
CETELOR, University of Lorraine, Epinal, 88000, France
* Corresponding Authors: Christine Gerardin. Email: ; Antonio Pizzi. Email:
Journal of Renewable Materials 2023, 11(10), 3625-3645. https://doi.org/10.32604/jrm.2023.030373
Received 03 March 2023; Accepted 25 May 2023; Issue published 10 August 2023
Abstract
Water repellant, flexible biofoams using tannin esterified with various fatty acid chains, namely lauric, palmitic and oleic acids, by reaction with lauryl chloride, palmitoyl chloride, and oleyl chloride were developed and their characteristics compared with the equivalently esterified rigid biofoams. Glycerol, while initially added to control the reaction temperature, was used as a plasticizer yielding flexible biofoams presenting the same water repellant character that the equivalent rigid foams. Acetaldehyde was used as the cross-linking agent instead of formaldehyde, as it showed a better performance with the esterified tannin. The compression results showed a significant decrease of the Modulus of Elasticity (MOE) of the flexible foams in relation to that of the rigid foams, confirming their flexible character. The lauryl- and palmitoyl-esterified biofoams presented similar mechanical properties, while the oleyl-esterified biofoam presented different mechanical and morphological result not really showing the expected flexibility. Both the esterified rigid and flexible tannin-based biofoams showed good water resistance and their sessile drop contact angle analysis as a function of time confirmed this characteristic. Scanning Electron Microscope (SEM) analysis showed the flexible foams to present a higher proportion of closed cells than the rigid foams. Conversely, the cells depth of the flexible foams was lower than that of the rigid foam. As regards their thermal resistance, the flexible foams showed a slight loss of mass compared to the rigid ones without glycerol. Both types of foams presented much lower surface friability of non-esterified rigid foamsKeywords
Tannins are a complex class of natural polyphenols that are widely distributed in plant species, including fruits, vegetables, and trees. Due to their unique chemical structure [1], tannins, especially commercial condensed flavonoid tannin extracts have been used for a number of different applications in biomaterials science [2,3]. Tannins have been used as binders to create composites either alone [4] with other renewable materials, such as lignin [5] and proteins such as soy [6–8]. They have unique properties, including high mechanical strength and low flammability, making them suitable for use in the production of insulation materials. Their addition to composites can enhance their thermal stability and flame resistance, further increasing their potential as insulation materials [9]. Moreover, tannin-based composites are biodegradable, making them a more sustainable alternative to traditional insulation materials.
Tannins have been shown to possess excellent thermal stability and can be easily modified to enhance their performance as insulation materials. In addition, tannins are abundantly available in nature and can be extracted using sustainable methods, making them a promising candidate for the development of eco-friendly insulation materials [2,3,10,11]. One promising application is in the development of insulation foams [12–14]. Rigid tannin foams are typically produced through reacting furfuryl alcohol, another biosourced material [15] with tannins in the presence or absence of aldehydes and with or without a blowing agent [12,16] or by the formation of non-isocyanate polyurethanes foams for both condensed flavonoid tannins [17–20] and hydrolysable tannins [1,21]. The reaction leads to the formation of a crosslinked polymer network, which imparts rigidity and mechanical strength to the foam. These foams are typically used in applications such as fire and acoustic insulation [3,13,22], with also applications in hydroponics [23].
Conversely, flexible tannin foams have been reported by incorporating plasticizers or other additives into the tannin reaction mix. The plasticizers reduce the crosslinking density of the foam and increase its flexibility, making it suitable for use in other applications [24,25].
Tannin-based biofoams, however, also exhibit some limitations, such as friability, low water repellency and their somewhat inadequate compatibility with hydrophobic compounds. Therefore, to overcome these limitations and improve the properties of tannin biofoams, researchers have developed various methods to modify them, including their esterification with a fatty acid [26]. Recently rigid foams presenting lower friability and increased water repellence have been obtained by adding to tannin-furanic foams a relatively small proportion of tannin, the flavonoid units of which were esterified by either lauroyl, or palmitoyl or oleyl chlorides [27] to obtain structures of the type:
With n = 12 (lauroyl), 16 (palmitoyl) and 18 (oleyl). The esterification with fatty acids of condensed tannins can be achieved through various methods, such as esterification [26–29], amidation, or transesterification, which results in the formation of amphiphilic molecules with both hydrophilic and hydrophobic properties. This modification enhances the emulsifying and dispersing properties of tannins, as well as their solubility and compatibility with hydrophobic compounds, making them suitable for use in various applications, such as coatings, adhesives, and bio-forms.
There are works reporting successful modification of tannins using fatty acids grafting such as oleic acid [27,29], stearic acid [29], and lauric acid [27] and palmitic acid [26,27], which have resulted in improved hydrophobicity and dispersing properties, enhanced thermal stability, and better compatibility with hydrophobic compounds. Furthermore, the degree of modification and the type of fatty acid used can be tailored to suit specific applications, making fatty acid-grafted tannins a promising avenue for developing new materials with improved properties.
The main unresolved problem in extending the applicability of these foams is the lack of the coupling of the fatty acid esterification technology with the flexibility technology due to the addition of plasticizers. The coupling of these two technologies would allow easier fitting foams for applications such as thermal insulation to steam or water pipes, as well as more adaptable acoustic insulation fitting to a number of different surface geometry. The work presented here does then aim to combine fatty-acid esterification of a commercial condensed flavonoid tannin extract by adding glycerol to obtain flexible, water-repellant, non-friable, fire-resistant flexible bio foams and to compare their characteristics with those of rigid tannin-based foams both with and without fatty acids esterification.
This research is divided into two parts:
(1) Preparation of esterified tannin that is involved in the reaction between the flavonoid’s groups and a fatty acid compound such as oleoyl chloride and palmitoyl chloride in a solvent. Previous work had determined how synthesizing the grafting of the tannin with the fatty acids [27].
(2) The conception of water-repellant tannin-based bioforms. Their formulations are indicated in Table 1.
Mimosa (Acacia mearnsii formerly mollissima, de Wildt) tannin extract as the main structural compound of this work was supplied by Silva Chimica (St. Michele Mondovi’, Italy). Furfuryl alcohol was purchased from Acros Organics (Geel, Belgium). Para-toluene-sulphonic acid (pTSA), diethyl ether, acetaldehyde, glutaraldehyde and glycerol were purchased from Sigma-Aldrich (St. Louis, MO, USA). Lauroyl chloride, oleoyl chloride and palmitoyl chloride were acquired from Alfa Aesar (Kandal, Germany). Chloroform was obtained from Merck (Darmstadt, Germany).
2.2 Tannin Oil-Grafting Method
Tannin oil-grafting was performed by modifying how it was done in previous work [27]; a commercial extract of mimosa tannin, 5 g, was placed in a reaction flask of 250 mL, 80 g of chloroform was added, and then 3.75 g of fatty acid chloride.
The reaction was left for at least 16 h while maintaining the temperature below 40°C and then evaporated. This procedure gives an esterified tannin that doesn’t have to be washed by a solvent and it can be used directly afterward.
Each esterified mimosa tannin extract was mixed with furfuryl alcohol. Then, the non-esterified mimosa tannin extract was added and mixed with acetaldehyde (99% solution) and water. For the flexible foams, glycerol was added at this stage and mixed rapidly. Last, a 65% water solution of the catalyst para-toluene-sulfonic acid (pTSA). The blowing agent then added was diethyl ether, and the mix was vigorously stirred for 40 s. The rigid foam was obtained rapidly and the flexible foam acquired its final structure within 2–3 min. 24 h were then allowed to eliminate by evaporating from the foam the trapped blowing agent residue. The formulations used are shown in Table 1.
2.4 Characterization of Tannin-Based Foam
First, some properties such as apparent density, induction time (min), and the absorption resistance time of a drop of water on the surface of a foam have been registered. The bulk density was calculated as each sample’s weight/volume ratio of a sample of the dimension of 30 mm × 30 mm × 30 mm.
The induction time is the time necessary to complete the foaming procedure.
2.4.2 Scanning Electron Microscopy (SEM) Analysis
The foams were analyzed by scanning electron microscope (SEM, Hitachi TM-3000) (Milexia, Paris, France). To determine their morphology and microscopic structure. 0.5 cm2 was the cross-section used for all the specimens. A gold palladium thin layer was then applied to the foam surface of the foams to improve image definition.
This analysis was carried out to compare the effect of different types of esterified tannin on the foams cell structure, and additionally to observe the differences between the rigid and flexible foams.
2.4.3 Resistance to Compression
Three foam specimens of 30 mm × 30 mm × 20 mm size for each case were prepared and their compression strength parallel to foam growth was tested by an Instron 4301 (Elancourt, France) rig at a compression rate of 2.0 mm·min−1. At least three samples were tested for each foam.
Three samples of 30 mm × 30 mm × 20 mm were placed under 10 cycles of compression at a strain of 10%, 20%, and 40%. The Modulus of Elasticity (MOE), strain, and stress values were calculated and compared to observe the different behavior of rigid and flexible foams.
2.4.4 Contact Angle Measurement
The foams water wettability was determined by their contact angles, as well as their maintenance as a function of time. A Krüss Gmb (Villebon-sur-Yvettes, France) CCD camera high resolution video measuring equipment was utilized for the purpose. The specimens were placed on the flat sample-holder of the equipment and the same size droplets of 20 microliters were added by micropipette on the foam sample surfaces to ensure reproducibility. The angles outline of the water drops were determined by the video system by measuring them during 180 s. Each drop accounted for 60 images. This yielded the variation trend as a function of the time of the water contact angle.
2.4.5 Thermogravimetric Analysis (TGA)
A thermogravimetric (TGA) analysis was performed by TGA/DSC1-TMA/SDTA 84Xe instrument from Mettler Toledo (Viroflay, France) equipped with a STARe v.11 fr System program. This analysis was realized to measure the foam’s thermal stability. Ten milligrams (±1.00 mg) of each sample powder were placed in an alumina crucible (the exact mass was automatically weighed by the instrument) followed by heating the sample at a temperature rate of 25°C up to 600°C.
3.1 FTIR Result of Oil-Grafted Tannin
The characterization by FTIR of oil-grafted tannin has been reported in recent research [27] as the three oil-grafted tannins showed almost the same results; the FTIR of the tannin grafted with acid lauroyl chloride has been studied in this research work (Fig. 1). In the spectrum of the grafted tannin sharp peak at 1740 cm−1 appears. This is the stretching peak of C = O groups indicating the esterification of tannin by the fatty acids. Conversely, for unreacted lauroyl chloride and lauric acid, these peaks appear at 1802 and 1700 cm−1, respectively this being the stretch bands for the carboxylic acid C = O. The tannin spectrum peak at 1616.12 cm−1 belongs to the tannin aromatic moieties C–H vibration [30,31].
Figure 1: Comparison of FTIR spectra of mimosa tannin, lauric acid, and fatty acid-grafted tannin using lauroyl chloride
The tannin grafting mechanism is shown in Fig. 2. The tannin used was a commercial tannin extract, thus it contained a minor percentage of carbohydrates oligomers either linked to the phenolic part of the tannin [32] or free [33], derived from the fragmentation of hemicelluloses in the extraction process. As a consequence, the esterification with fatty acid chlorides occurred both on the hydroxyl groups of the tannin as well as on some hydroxyl groups of the carbohydrates fraction. The species illustrated in Scheme 1 were identified doing the esterification of tannins for rigid foams [27].
Figure 2: Schematic visualization of the esterification of a commercial condensed tannin extract
The initial observation for the two series of foams is shown in Tables 2 and 3.
In all the modified foams, flexible and rigid ones, the lengths of time taken for water absorption and wettability have increased, indicating that water repellency is much improved when a percentage of the tannin is esterified with a fatty acid. The density increases slightly with the addition of glycerol. The induction time increases with the addition of glycerol because as the addition of the glycerol has reduced the temperature, the induction time for completing the foaming has increased and the flexible foams are smaller than the rigid foams. This could be attributed to the diminution of temperature and energy of foaming.
In the two series of foam, the modified foam with oleyl-grafted tannin shows a cell structure slightly different from the other modified foams but the glycerol addition has markedly increased this difference and the water repellency of the flexible foam. The foam modified with an oleyl-grafted tannin showed the smaller size cells than the rigid-modified foam grafted with the same fatty acid. Elastic foams appear visually less brittle than rigid foams.
The unmodified foam STD without glycerol is very brittle and the temperature of the reaction did not allow it to complete the procedure of foaming correctly, but the addition of glycerol made it less fragile. Another point important in this work is the quantity of acetaldehyde as a cross-linker agent. The classic formulation to prepare tannin furanic foams with formaldehyde indicated 3.7 g of acetaldehyde for 15 g of tannin but this proportion crushed the structure of the cell and a part of the foam was useless and destroyed. For this reason, the quantity of acetaldehyde was decreed to 2.5–3 g for 15 g of tannin.
3.3 Scanning Electron Microscopy (SEM) Analysis
The microstructure and micromorphology of the various foams were observed by SEM. The foam specimens SEM images include unmodified foams (STD.R and STD.F, Fig. 3), modified rigid foams with fatty acid-grafted tannin (C12-R. C16-R, C18-R), and flexibly modified foam (C12-F, C16-F, C18-F). All these were compared.
Figure 3: Comparison between unmodified foams without (STSD.R) and with glycerol (STD.F)
The comparison between the unmodified foams (STD.R and STD.F) shows the change in the size and form of the structure of the cell in the foam with glycerol. The cells of foams with a high proportion of glycerol are stronger than the foam without or with a small proportion of glycerol. In the foam STD-R which contains 1.5 g of glycerol, the holes are bigger and the wall structure of the cells seems weaker than the cells in the STD-F which contains more quantity of glycerol.
The cells in the unmodified foam with the glycerol are the same or slightly bigger than the foam STD.R but the cells are closer. Both foams were fragile and brittle but they have shown a result different in reaction with oil-grafted tannins.
In the second step, the water-repellant foams including rigid and semi-flexible ones were compared and the results are presented in Fig. 4. The foams containing glycerol appear to have cells slightly bigger than the rigid foams. But the cells have a somewhat closer structure (Fig. 4).
Figure 4: Comparison between rigid (C12,16,18-R) and flexible (C12,16,18-F) fatty acid-grafted tannin foams. (C12-R): Rigid lauric acid-grafted foam; (C12-F): flexible lauric acid-grafted foam. (C12-R): Rigid palmitic acid-grafted foam; (C12-F): flexible palmitic acid-grafted foam. (C12-R): rigid oleic acid-grafted foam; (C12-F): flexible oleic acid-grafted foam
3.4 Compression Resistance and Module Elasticity
The test of compression has been carried out to observe the flexibility comportment of flexible foams and to have a comparison between the rigid and flexible foams.
Two methods have been used that include rupture and multicycling under certain strains.
All the foam were cut into 30 mm × 30 mm × 20 mm samples to observe the resistance against an applied force up to rupture. For this the foams were subjected to a 2KN force applied perpendicular to the 30 mm × 20 mm face at a displacement rate of 2 mm/min.
The elastic behavior of the foams was evaluated in the direction perpendicular using (Instron 4301, Elancourt, France) subjected to a 1 KN for each foam. 3 samples of 30 mm × 30 mm × 20 mm were subjected to 10 cycles of compression at strains of 10%, 20% and 40%. The Modulus of Elasticity was calculated on the basis of the relation between stress and strain value at the yield point using the following formula:
where: E = Modulus of Elasticity (Pa or MPa) and (σ) = stress (force per unit area, typically in N/m² or MPa); ε = strain (change in length per unit length, typically expressed as a decimal or a percentage). In the first step, the average strength of the rigid and flexible foams has been calculated (Figs. 5 and 6).
Figure 5: The average compression strength of the rigid unmodified and oil-grafted foams with the three different fatty acid chains
Figure 6: The average compression strength of the modified and flexible oil-grafted foams with the three different fatty acid chains
The comparison between the two classes of foams that include rigid and semi-flexible showed that the unmodified rigid foam using acetaldehyde has a nature more flexible than a rigid foam using formaldehyde. To have a standard value to compare the rigidity, an unmodified foam using formaldehyde has been prepared (STD-R-formaldehyde).
It must be noted that for both the rigid and the flexible foams there is some correlation between foam density and the foam resistance to compression. This correlation is not linear as the number of carbon atoms of the grafted ester increases, the density increases almost linearly while the resistance to compression increases much more sharply. This is evident from both Figs. 5 and 6. While the differences in density for the rigid foams grafted with the three fatty acids in Fig. 5 possibly contribute to somewhat partially justify the resistance to compression, this is not the case in Fig. 6 for the case of the flexible foam. Such an effect is particularly evident in Fig. 6 for the flexible foams where the differences in density of the three fatty acids grafted foams are really non-significant. It indicates that for both rigid and flexible foams, but particularly for the flexible foams, the length of the fatty acid chain contributes to the compression strength imparted to a tannin-furanic foam. The question is then, why the longer the fatty acid chain esterifying the tannin, the higher is the contribution of its length to the foam compression resistance? Firstly, what can possibly be advanced is that over the tannin-furanic covalent network formed in the foam is superposed also a strength contribution by a physical entanglement network due to the long chains of the fatty acid esters present. Second, the carbohydrate oligomer chains, linked or not to the tannin, that in general do not contribute to the strength of a tannin-furanic foam, being now partly esterified also contribute to the physical entanglement network formed and thus to the increase in strength.
The compression curve always shows an elastic failure with three regions, namely elastic deformation or linear elasticity, plateau, and densification (Fig. 7). However, the tensile stress-strain curve of a standard formaldehyde cross-linked tannin-furanic foam showed a fragile break [10]. Crack formation is always the result of an effect of the concentration of stress. This damages the material in either tension or compression. Tension, nonetheless, causes a far more rapid crack propagation causing tannin-furanic foams to be brittle in tension and elastic while being compressed. The first step can give information like stress, strain, and MOE at the yield point or the elastic region. The calculation and compression of the MOE and at the yield point make a difference between the rigidity of the foams. The foam with a smaller MOE is more elastic or flexible. The results of compression analysis for the rigid and flexible sample’s weight/volume ratios are shown in Tables 4 and 5.
Figure 7: Schematic figure to explain the elasticity calculation
As is shown in Table 4 and Fig. 8, the MOE of rigid foams using a hardener like formaldehyde is bigger than the foams using acetaldehyde. Indeed, the unmodified foam using acetaldehyde has neither a good structural composition nor mechanical resistance but by just substituting 8.33% of tannin with fatty-acid-grafted tannin, it is possible to obtain a foam with high water-repellent character and improvement of its cellular structure thus also improving its mechanical resistance.
Figure 8: Comparison between load at the yield point and MOE for unmodified and rigid oil-grafted foams
As is shown in Fig. 8, the oil-grafted foams with the three different fatty acid chains have influenced the increase of the MOE. Such a difference is even clearly noticeable to the eye.
In the second part of the project with the substitution of tannin with 8.3% fatty acid-grafted tannin and the addition of glycerol, a grafted foam with high water repellency and less rigidity has been obtained. This foam is indeed flexible and can stand up the pressure more than a rigid foam. This foam is flexible and did not crush as rigid foam under the pressure of compression, recovering its shape during the cyclic test (Table 5). Its elasticity is thus proven by the calculation the of MOE yield.
As is shown in Table 5 and Fig. 9, the MOE of the tannin foams to which fatty acids-grafted tannin, especially with lauric and palmitic acids is very low, in line with their increase in elasticity.
Figure 9: Comparison between load at the yield point and MOE for unmodified and flexible fatty acids grafted foams
The other point of interest is the decrease of elasticity with the length of the fatty acid chain. The character of the tannin foams with added fatty acid-grafted tannin with oleic acid is near to that of a rigid foam (0.011 MPa) as the MOE of an unmodified rigid foam (0.010 MPa) is even lower than that of a rigid foam modified with same fatty acid (0.033 MPa). The reasons for such behavior have been ascribed to the contribution of the superposed physical entanglement network formed by the fatty acid chains linked to both the phenolic part of the tannin extract and on the hemicelluloses oligomer fragments in it.
In Fig. 9, a comparison between unmodified, rigid, and flexible foams is shown. Actually, the semi-flexible foam rather than the rigid foam did not show a real yield or brittle point, and after several cycles of compression or a complete compression cycle, the foam keeps its shape and can return at 70% of its initial weight and dimension. A comparison between three fatty acid-grafted foams (rigid and flexible) has been registered and shown to prove the increase in rigidity with an increase in the length of the fatty acid chain used (Figs. 10 and 11).
Figure 10: Compression results of unmodified and rigid oil-grafted foams with three chains of fatty acid
Figure 11: Comparison between flexible fatty acid-grafted foams with three different fatty acid chains
Since the strain yield point in the rigid foams was observed to be around 10%–15%, and less than 10% for the semi-flexible foams, compression and, stress-strain cycles were studied at 10%, 20%, and, 40% strain to compare the effect of pressure on flexibility.
In the first step, the rigid foams like unmodified foam with or without glycerol (Fig. 12) and rigid fatty acid-grafted foams were studied and the role of glycerol in increasing flexibility has been shown (Figs. 13–15). Afterwards, cyclic compression tests were carried out to observe the behavior of the flexible foams.
Figure 12: Cyclic compression tests for the unmodified rigid foam (STD-R) without plasticizer and with glycerol plasticizer (STD-F)
Figure 13: Schematic differences at the level of the polymer network between rigid and flexible foams
Figure 14: 10 cycles strain-stress curves of rigid foams added with lauric acid -grafted tannin at 10%, 20% and 40% strain
Figure 15: 10 Cycles strain-stress curves of flexible foams with added lauric acid-grafted tannin at strains of 10%, 20% and 40%
The comparison between two rigid unmodified foams shows the increase in flexibility in the unmodified foam with glycerol, although this flexibility is even more remarkable in the semi-flexible oil-grafted foams. Glycerol is a so-called external plasticizer, in principle a plasticizer that does not react covalently with the covalent polymer network forming the foam cell walls. It interposes itself in the interspaces between polymer chains blocking or interrupting some of the covalent bonds and physical entanglements possible in the network during its forming stage. The fact that also some physical entanglement knots of the fatty acid chains can be prevented by the presence of glycerol can explain the improved flexibility of the esterified tannin extracts foams (Fig. 13). From Fig. 13, it is clear that the polymer network structure is more open due to the insertion of glycerol. This more open polymer network also contributes to the acquired flexibility of the foam.
The compression results of three oil-grafted foams were compared. The flexibility appears to decrease as a function of the increase in the fatty acid chain length. Thus, the foams with added oleic acid-grafted tannin (C18) showed lower flexibility compared to modified foams with lauric or palmitic acid. This only means that the oleic acid-based foam is still flexible but at a higher range of compression strength. It is in line with the higher compression strength observed, the longer is the chain of fatty acid esterifying the tannin extract.
In the present work, the behavior of foams with added flexible lauric acid-grafted tannin has been studied. As a control the compression of a rigid foam with added lauric acid-grafted tannin has also been studied.
The compression test was carried out at 10%, 20%, and 40% strain (Figs. 12, 14 and 15).
As the flexible foam with the added fatty acid-grafted tannin with chains of C12 and C16 showed, the cyclic compression results for the foam added of the lauric acid-grafted tannin is the one shown in this report (Figs. 12, 14, and 15).
The oil-grafted foam with oleyl-grafted tannin has shown results different from the other flexible foams. The cyclic compression result in these foams even containing the plasticizer indicated an almost rigid behavior (Fig. 16).
Figure 16: 10 cycles strain stress curves of flexible foams with added oleic acid-grafted tannin at strains of 10%, 20% and 40%
The comparison of foam water repellence has been made by the sessile drop test method by measuring the difference in contact angle of three tannin foams modified by adding tannin grafted with fatty acids of three different chain lengths. The rigid foams added of lauric acid-grafted tannin and palmitic acid grafted tannin showed an initial water contact angle of 120°, stabilizing then after 180 s to around 110°. The rigid foams added of oleic acid-grafted tannin also showed a water contact angle of 120° but this decreased nearer to 100° in 180 s. This might be due to the larger cell size compared to the other foams. Nonetheless, all three rigid foams added fatty acid-grafted tannin show both a much improved water repellency, water contact angle, and better contact angle stability than the rigid unmodified foam control (Fig. 17). This effect is due to two contributions, first by the water repellence imparted by the presence of the linked fatty acids and second by the decrease in hydrophilicity of the carbohydrate oligomers in the tannin extract as these too have been esterified with the fatty acid chains. The rigid unmodified foam shows an initial water contact angle of 52° decreasing rapidly down to around 10° after 180 s without appearing to stabilize.
Figure 17: Comparison between rigid standard foam and rigid foams added of fatty acid-grafted tannin different chain lengths
The water contact angle measures for the flexible foams are shown in Fig. 18. The results showed an initial water contact angle of 120° decreasing down to 105° and stabilizing. The flexible foam in which glycerol was added but that was not added of any fatty acid-grafted tannin, namely STD-F, presented a much lower water repellency presenting an initial water contact angle of 79° decreasing in 180 s down to 50° without apparently stabilizing. Both the results of the rigid and flexible foams indicate that is the addition of the tannin grafted of the fatty acid chains that is the reason for the water repellence of both these types of tannin-based foams, the glycerol contributing only the flexibility of the foams to which it has been added.
Figure 18: Comparison between standard flexible foam and flexible foams added fatty acid-grafted tannin of different chain lengths
3.6 Thermogravimetric Analysis (TGA)
TGA was used to determine the cured resins’ thermal stability. The corresponding first derivate (DTG) and the TGA traces are shown in Figs. 19–21. Thermal degradation seems to occur in a number of phases as indicated in Fig. 19 by DTG curves of the rigid foams. Thus, in the 50°C–125°C, 175°C–250°C, and two zones between 280°C–550°C. The lower temperature phase weight loss is indicative of the water residues evaporating as well as some smaller impurities degrading [17,34]. The next phase indicates that some sort of degrading occurs in the links of tannin and fatty acids in the foam. The progressive degrading of the materials network formed occurs in the series of degradation phases in the 280°C and 550°C temperature range, both first the complete degradation of the linkages between tannin and furanic oligomers and finally, at the higher temperature, the tannin itself degrading. As condensed tannins are degraded at higher temperatures they are in general employed to improve adhesives and resins resistance to higher temperature. Bonds which are more stable, such as C-C and C-O, cleave in such a range of temperatures [17,34]. The DTG of the 4 foams with different fatty acids–grafted tannins added are very similar whatever the length of the fatty acid chain used.
Figure 19: Comparison of TGA and DTG weight curves as a function of time, between an unmodified rigid foam (STD-R) and rigid foams added of fatty acids-grafted tannin with fatty acid chains of three different kinds
Figure 20: Comparison of TGA and DTG curves weight curves as a function of time, between an unmodified flexible foam (STD-F) and rigid foams added of fatty acids-grafted tannin with fatty acid chains of three different kinds
Figure 21: Comparison of TGA and DTG between unmodified foams (STD-R, STD-F) and rigid (C12-R)and flexible (C12-F) lauric grafted-tannin foam
The behavior of the flexible foams with added different fatty acid-grafted chains (Fig. 20) also presents 5 zones of degradation. The first one is as for the rigid foams in the 50°C–125°C range, the reason for it being the same as for the rigid foams in Fig. 19. What changes mainly are the length of the second degradation stage that is markedly shorter, in the 125°C–230°C range (Fig. 20), with the first slope between 125°C and 150°C much shorter than the start of the degradation of the linkage between tannin and furanic oligomers observed for the rigid foams. The 125°C–150°C range corresponds to the start of the degradation of some tannin-fatty esters linkages, with the second portion namely the 150°C–230°C range corresponding to the degradation of the glycerol plasticizer present in the flexible foams. The fact that this zone peaks at 175°C which is the temperature of degradation of glycerol in the presence of oxygen [35] clearly indicates that this zone is the one representing the degradation of the glycerol in the flexible phones, explaining the absence of this peak in the rigid foams. In the 150°C–230°C stage degradation of the linkages of the fatty acids and between the tannin and the fatty acids portion of the foam still occurs, as shown by the slope in the rigid foams DTGA traces, and also exists in the flexible foams where it is masked by the more marked event of glycerol degradation. This stage is thus shifted to a slightly lower temperature range than for the rigid foams probably due to the influence of the presence of glycerol in the flexible foams. In this range of temperature, the standard flexible foam without fatty acids-modified tannin degrades relatively less than the ones modified with fatty-acid-esterified tannin added. This is an indication that the combination of glycerol and fatty acid-modified tannin accounts for a more evident degradation, with the C16 case appearing to be slightly more sensitive than the C12 and C18 cases (Fig. 20). The higher temperature stages appear to be similar to what observed for the rigid foams, for the same type of degradation.
The very different behavior in this temperature range between rigid and flexible foams is very much put into evidence in Fig. 21, where rigid and flexible lauric acid esterified foams are directly compared.
The flexible tannin-furanic biofoams developed by the addition of a small proportion of one or other type of three fatty acids-grafted tannins of chain length, of respectively C12, C16, and C18 carbons, and glycerol have shown to be water repellent as their equivalent rigid foams without the glycerol plasticizer. It is the glycerol that imparted the flexible character to the structure of the tannin-furanic foam but the small proportions of fatty-acid grafted tannins added yielded their water repellency. The use of acetaldehyde as a cross-linker rather than formaldehyde yielded an improved mechanical performance when the fatty acid-grafted tannins were added. The flexibility was determined by the decrease of the MOE of these foams under a 10 cycles compression test. Lauryl- and palmitoyl-esterified bio foams encourage similar mechanical properties. The oleyl-esterified bio foam instead showed a different compression behavior and morphology showing rigidity characteristics almost similar to rigid foam, and thus of much-decreased flexibility. The flexible foams appeared by SEM to present a somewhat lower proportion of holed cells with a smaller cell size than the rigid foams, and good instant as well as a function of time water repellency. Both types of foams presented much lower surface friability than non-esterified rigid foams.
Funding Statement: The Malaysia–France Bilateral Research Collaboration Project Grant 2021 (MATCH 2021) funded this research work, MOHE-Fire-Resistant and Water-Repellent Tannin-Furanic-Fatty Acid Biofoams. The ANR (French Agence Nationale de la Recherche) funds the LERMAB within the ambit of the Labex (Laboratory of Excellence) ARBRE.
Conflicts of Interest: The authors declare that they have no conflicts of interest to report regarding the present study.
References
1. Azadeh, E., Pizzi, A., Gerardin-Charbonnier, C., Gerardin, P. (2023). Hydrolysable chestnut tannin extract chemical complexity in its reactions for non-isocyanate polyurethanes (NIPU) foams. Journal of Renewable Materials, 11(6), 2823–2848. https://doi.org/10.32604/jrm.2023.027651 [Google Scholar] [CrossRef]
2. Pizzi, A. (2019). Tannin-based biofoams-A review. Journal of Renewable Materials, 7(5), 477–492. https://doi.org/10.32604/jrm.2019.06511 [Google Scholar] [CrossRef]
3. Pizzi, A. (2019). Tannins: Prospectives and actual industrial applications. Biomolecules, 9(8), 344. [Google Scholar] [PubMed]
4. Zhang, B., Chen, X., Pizzi, A., Petrissans, M., Dumarcay, S. et al. (2023). Highly branched tannin-tris(2-aminoethyl)amine-urea wood adhesives. Polymers, 15(2), 890. [Google Scholar] [PubMed]
5. Pizzi, A. (2023). A review of soy-tannin gelling for resins applications. Journal of Renewable Materials, 11(1), 1–25. https://doi.org/10.32604/jrm.2022.023314 [Google Scholar] [CrossRef]
6. Ghahri, S., Pizzi, A., Hajihassani, R. (2022). A study of concept to prepare totally biosourced wood adhesives from only soy protein and tannin. Polymers, 14(6), 1150. [Google Scholar] [PubMed]
7. Sarazin, J., Poljansek, I., Pizzi, A., Sernek, M. (2022). Curing kinetics of tannin and lignin biobased adhesives by DSC and ABES. Journal of Renewable Materials, 10(8), 2117–2131. https://doi.org/10.32604/jrm.2022.019602 [Google Scholar] [CrossRef]
8. Navarrete, P., Pizzi, A., Tapin-Lingua, S., Benjelloun-Mlayah, B., Pasch, H. et al. (2012). Low formaldehyde emitting biobased wood adhesives manufactured from mixtures of tannin and glyoxalated lignin. Journal of Adhesion Science and Technology, 26(10–11), 1667–1684. [Google Scholar]
9. Celzard, A., Fierro, V., Amaral-Labat, G., Pizzi, A., Torero, J. (2011). Flammability assessment of tannin-based cellular materials. Polymer Degradation and Stability, 96, 477–482. [Google Scholar]
10. Tondi, G., Pizzi, A. (2009). Tannin-based rigid foams: Characterization and modification. Industrial Crops and Products, 29(2–3), 356–363. [Google Scholar]
11. Sánchez-Martín, J., Beltra-Heredia, J., Delgado-Regana, A., Rodriguez-Gonzalez, M. A., Rubio-Alonso, F. (2013). Optimization of tannin rigid foam as adsorbents for wastewater treatment. Industrial Crops and Products, 49, 507–514. [Google Scholar]
12. Meikleham, N., Pizzi, A. (1994). Acid and alkali-setting tannin-based rigid foams. Journal of Applied Polymer Science, 53, 1547–1556. [Google Scholar]
13. Lacoste, C., Basso, M. C., Pizzi, A., Celzard, A., Ella Bang, E. et al. (2015). Pine (P. pinaster) and quebracho (Schinopsis lorentzii) tannin based foams as green acoustic absorbers. Industrial Crops and Products, 67, 70–73. [Google Scholar]
14. Chen, X., Li, J., Essawy, H., Pizzi, A., Fredon, E. et al. (2022). Flame-retardant and thermally-insulating tannin and soybean protein isolate (SPI) based foams for potential applications in building materials. Construction and Building Materials, 315, 125711. [Google Scholar]
15. Delliere, P., Pizzi, A., Guigo, N. (2023). Structural differences on biobased polyfurfuryl alcohol generated by polymerization in water. Polymers, 15, 1745. [Google Scholar] [PubMed]
16. Basso, M. C., Giovando, S., Pizzi, A., Celzard, A., Fierro, V. (2013). Tannin/furanic foams without blowing agents and formaldehyde. Industrial Crops and Products, 49(12), 17–22. [Google Scholar]
17. Chen, X., Li, J., Xi, X., Pizzi, A., Zhou, X. et al. (2020). Condensed glucose-tannin-based NIPU BioFoams of improved fire retardancy. Polymer Degradation and Stability, 175(7), 109121. [Google Scholar]
18. Chen, X., Xi, X., Pizzi, A., Fredon, E., Zhou, X. et al. (2020). Preparation and characterization of condensed tannin non-isocyanate polyurethane (NIPU) rigid foams by ambient temperature blowing. Polymers, 12(4), 750. [Google Scholar] [PubMed]
19. Chen, X., Guigo, N., Pizzi, A., Sbirrazzuoli, N., Li, B. et al. (2020). Ambient temperature self-blowing tannin-humins biofoams. Polymers, 12(11), 2732. [Google Scholar] [PubMed]
20. Chen, X., Li, J., Essawy, H., Pizzi, A., Fredon, E. et al. (2022). Flame-retardant and thermally-insulating tannin and soybean protein isolate (SPI) based foams for potential applications in building materials. Construction and Building Materials, 315(7), 125711. [Google Scholar]
21. Azadeh, E., Chen, X., Pizzi, A., Gerardin, C., Gerardin, P. et al. (2022). Self-blowing non-isocyanate polyurethane foams based on hydrolysable tannins. Journal of Renewable Materials, 10(12), 3217–3227. https://doi.org/10.32604/jrm.2022.022740 [Google Scholar] [CrossRef]
22. Lacoste, C., Basso, C., Pizzi, A., Laborie, M. P., Celzard, A. et al. (2013). Pine tannin-based rigid foams: Mechanical and thermal properties. Industrial Crops and Products, 43, 245–250. [Google Scholar]
23. Basso, M. C., Pizzi, A., Al-Marzouki, F., Abdalla, S. (2016). Horticultural/hydroponics and floral foams from tannins. Industrial Crops and Products, 87(6), 177–181. [Google Scholar]
24. Li, X., Pizzi, A., Cangemi, M., Fierro, V., Celzard, A. (2012). Flexible natural tannin-based and protein-based biosourced foams. Industrial Crops and Products, 37(1), 389–393. [Google Scholar]
25. Basso, M. C., Giovando, S., Pizzi, A. (2014). Composition for manufacturing an elastic tannin based foam material, and process thereof, World Patent Organization, patent WO2014117946A1. Assigned to silva chimica. [Google Scholar]
26. Rangel, G., Chapuis, H., Basso, M. C., Pizzi, A., Delgado-Sanchez, C. et al. (2016). Improving water repellency and friability of tannin-furanic foams by oil-grafted flavonoid tannins. BioResources, 11(3), 7754–7768. [Google Scholar]
27. Azadeh, E., Abdullah, U. H., Ali, N. B. M., Pizzi, A., Gerardin-Charbonnier, C. et al. (2022). Development of water repellent, non-friable tannin-furanic-fatty acids biofoams. Polymers, 14(22), 5025. [Google Scholar] [PubMed]
28. Grigsby, W. J., Bridson, J. H., Cole Lomas, C., Elliot, J. A. (2013). Esterification of condensed tannins and their impact on the properties of poly(lactic acid). Polymers, 5(2), 344–360. [Google Scholar]
29. Poaty-Poaty, B. (2009). Modification chimique d’antioxydants pour les rendre lipophiles: Application aux tannins (Ph.D. Thesis). University Henri Poincaré-Nancy I, Nancy, France. [Google Scholar]
30. Ping, L., Pizzi, A., Zhou, D. G., Brosse, N. (2012). Condensed tannins from grape pomace: Characterization by FTIR and MALDI TOF and production of environment friendly wood adhesive. Industrial Crops and Products, 40(14), 13–20. [Google Scholar]
31. Ricci, A., Olejar, K. J., Parpinello, G. P., Kilmartin, P. A., Versari, A. (2015). Application of fourier transform infrared (FTIR) spectroscopy in the characterization of tannins. Applied Spectroscopy Reviews, 50(5), 407–442. [Google Scholar]
32. Drovou, S., Pizzi, A., Lacoste, C., Zhang, J., Abdalla, S. et al. (2015). Flavonoid tannins linked to long carbohydrate chains—MALDI ToF analysis of the tannin extract of the African locust bean. Industrial Crops and Products, 67(13), 25–32. [Google Scholar]
33. Pizzi, A. (1983). Tannin-based adhesives. In: Pizzi, A. (Ed.Wood adhesives chemistry and technology. New York: Marcel Dekker. [Google Scholar]
34. Luo, J., Zhou, Y., Gao, Q., Li, J., Yan, N. (2020). From wastes to functions: A new soybean meal and bark-based adhesive. ACS Sustainable Chemistry and Engineering, 8(29), 10767–10773. [Google Scholar]
35. Qadariyah, L., Sumarno, M., Machmudah, S., Sasaki, M., Goto, M. (2011). Degradation of glycerol using hydrothermal process. Bioresource Technology, 102(19), 9267–9271. [Google Scholar] [PubMed]
Cite This Article
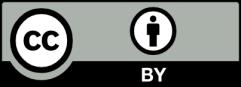
This work is licensed under a Creative Commons Attribution 4.0 International License , which permits unrestricted use, distribution, and reproduction in any medium, provided the original work is properly cited.