Open Access
ARTICLE
A Primary Study on Mechanical Properties of Heat-Treated Wood via in-situ Synthesis of Calcium Carbonate
1
Key Lab of State Forest and Grassland Administration on “Wood Quality Improvement & High Efficient Utilization”, School of
Forestry & Landscape Architecture, Anhui Agricultural University, Hefei, China
2
Department of Wood Science and Technology, Faculty of Technical Engineering, University of Bihać, Bihać, Bosnia and
Herzegovina
3
Department of Natural Resources and Earth Science, Shahrekord University, Shahrekord, Iran
* Corresponding Author: Demiao Chu. Email:
(This article belongs to the Special Issue: Functionalization of Wood and Bamboo-Based Materials)
Journal of Renewable Materials 2023, 11(1), 435-451. https://doi.org/10.32604/jrm.2022.023214
Received 15 April 2022; Accepted 26 May 2022; Issue published 10 August 2022
Abstract
This study aims to improve the value of fast-growing wood and extend the heat-treated wood utilization using inorganic calcium carbonate (CaCO3) crystals via an in-situ synthesis method. CaCl2 and Na2CO3 solutions with a concentration ratio of 1:1 were successively introduced into the thermally modified poplar wood obtained by steam heat treatment (HT) at 200°C for 1.5 and 3 h, resulting in the in-situ synthesis of CaCO3 crystals inside the heat-treated wood. The filling effect was best at the concentration of 1.2 mol/L. CaCO3 was uniformly distributed in the cell cavities of the heat-treated wood, and some of the crystals were embedded in the fissures of the wood cell walls. The morphology of CaCO3 crystals was mainly spherical and rhombic polyhedral. Three main types of CaCO3 crystals were calcite, vaterite, and aragonite. The HT of poplar wood at 200°C resulted in degrading the chemical components of the wood cell wall. This degradation led to reduced wood mechanical properties, including the surface hardness (HD), modulus of rupture (MOR), and modulus of elasticity (MOE). After CaCO3 was in-situ synthesized in the heat-treated wood, the HD increased by 18.36% and 16.35%, and MOR increased by 14.64% and 8.89%, respectively. Because of the CaCO3 synthesization, the char residue of the 200°C heat-treated wood samples increased by 9.31% and the maximum weight loss rate decreased by 19.80%, indicating that the filling with CaCO3 cannot only improve the mechanical properties of the heat-treated wood but also effectively enhance its thermal stability.Graphic Abstract
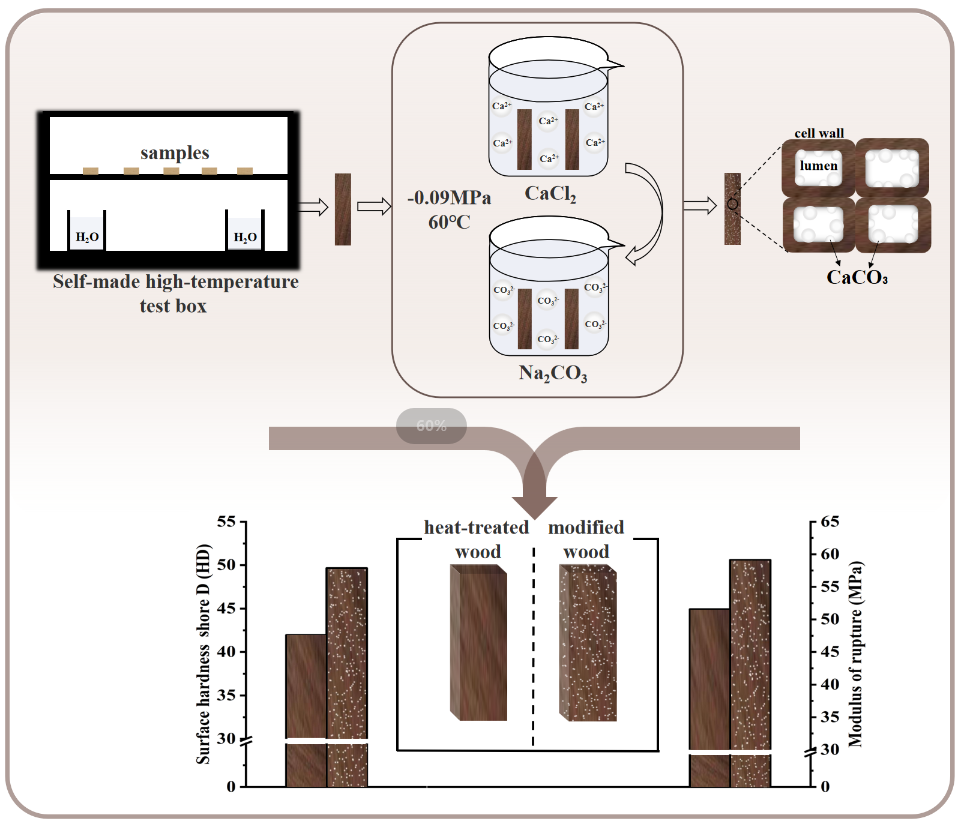
Keywords
Cite This Article
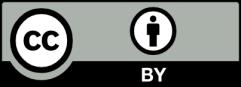
This work is licensed under a Creative Commons Attribution 4.0 International License , which permits unrestricted use, distribution, and reproduction in any medium, provided the original work is properly cited.