Open Access
REVIEW
Advancements and Challenges in Enhancing Thermal Stability of Lithium-Ion Battery Separators: Review on Coating Materials, High-Temperature Resistant Materials and Future Trends
1 Qiushi College, Beijing Institute of Technology, Beijing, 102488, China
2 National Engineering Research Center of Flame Retardant Materials, School of Materials Science & Engineering, Beijing Institute of Technology, Beijing, 100081, China
3 Research Center for Mine Ventilation Safety and Occupational Health Protection of National Energy Group, Guoneng Shendong Coal Group Co., Ltd., Ordos, 017209, China
* Corresponding Author: Ye-Tang Pan. Email:
(This article belongs to the Special Issue: Grafting to and from Polymer Nanocomposites blends for Coating, Energy and Environmental Applications)
Journal of Polymer Materials 2025, 42(1), 33-55. https://doi.org/10.32604/jpm.2025.062352
Received 16 December 2024; Accepted 27 February 2025; Issue published 27 March 2025
Abstract
The thermal stability of lithium-ion battery separators is a critical determinant of battery safety and performance, especially in the context of rapidly expanding applications in electric vehicles and energy storage systems. While traditional polyolefin separators (PP/PE) dominate the market due to their cost-effectiveness and mechanical robustness, their inherent poor thermal stability poses significant safety risks under high-temperature conditions. This review provides a comprehensive analysis of recent advancements in enhancing separator thermal stability through coating materials (metal, ceramic, inorganic) and novel high-temperature-resistant polymers (e.g., PVDF copolymers, PI, PAN). Notably, we critically evaluate the trade-offs between thermal resilience and electrochemical performance, such as the unintended increase in electronic conductivity from metal coatings (e.g., Cu, MOFs) and reduced electrolyte wettability in ceramic coatings (e.g., Al2O3). Innovations in hybrid coatings (e.g., BN/PAN composites, gradient-structured MOFs) and scalable manufacturing techniques (e.g., roll-to-roll electrospinning) are highlighted as promising strategies to balance these competing demands. Furthermore, a comparative analysis of next-generation high-temperature-resistant separators underscores their ionic conductivity, mechanical strength, and scalability, offering actionable insights for material selection. The review concludes with forward-looking perspectives on integrating machine learning for material discovery, optimizing interfacial adhesion in ceramic coatings, and advancing semi-/all-solid-state batteries to address both thermal and electrochemical challenges. This work aims to bridge the gap between laboratory innovations and industrial applications, fostering safer and more efficient lithium battery technologies.Keywords
The global shift toward carbon neutrality has propelled the rapid growth of electric vehicles (EVs) and renewable energy storage systems, with lithium-ion batteries (LIBs) serving as their cornerstone technology. The global electric vehicle market is projected to sustain rapid growth, with substantial market potential [1]. As the core power source of new electric vehicles, lithium batteries are the key point of research for major electric vehicle manufacturers. However, frequent incidents of spontaneous combustion in electric vehicles have raised widespread concerns about the safety of lithium batteries [2]. Therefore, while improving the energy storage capacity and endurance of lithium batteries, it is essential to prioritize their safety and stability, as these directly relate to the overall safety of the vehicle. Consequently, there is a significant demand for lithium batteries that seamlessly integrate energy storage, power output, and safety performance. The battery separator, as a key component of lithium batteries, plays the role of isolating positive and negative electrodes and conducting ions [3]. At the same time, the separator significantly impacts the thermal stability of lithium batteries [4,5]. Designing separators with excellent thermal stability can improve the safety performance of the battery and reduce the occurrence of accidents [6]. At the same time, it can also meet the market demand for electric vehicles with excellent performance and high safety, improving the acceptance of new energy vehicles in society so as to promote energy conservation and emission reduction to promote the policies on carbon peaking and carbon neutrality.
Traditional separators, predominantly composed of polymers, are pivotal in ensuring the normal operation of lithium batteries. In order to improve the thermal stability of the separator and improve the flame retardant performance of the separator, a variety of methods can be used. Among them, it is a common method to prepare the coating by a variety of materials and modify the separator [7]. By analyzing the thermal stability and other properties of the traditional separator, this paper summarizes the effects of new coating materials on the properties of the separator, prospects the new high temperature resistant separator materials, and further discusses the possibility of its application in the lithium battery separator to improve the safety performance of electric vehicles [8–11].
This analysis chart presents statistical data on the publication time, quantity, and proportion of literature regarding corresponding separator coating materials and new high-temperature separators (derived from the Science Direct database). According to incomplete statistics, research on various coating materials and new high-temperature-resistant separators has shown a steadily increasing trend year by year. This growth has been particularly notable since 2015, with the pace nearly doubling after 2021. This is closely related to the improvement of battery technology and the popularization of battery technology in life in recent years, and the promotion of green and environmentally friendly new energy technologies. It can be seen in Fig. 1a that studies on metal coatings are higher than the two types, among which Metal-Organic Framework (MOF) is the research hotspot of metal coatings in recent years (Fig. 1c). In 2021–2024, related studies account for 80.5% of the total research on MOF coatings, and in 2024, an increase of about 54.8% compared with 2023. In the studies related to ceramic coatings (Fig. 1b), Al2O3 accounts for nearly half of the highest proportion. At present, more studies have developed to Cr2O3 ceramics and various ceramic mixing types, such as Al2O3-TiO2 [12]. Si3N4 ceramics are more commonly used in fuel cell separators. Among other inorganic materials (Fig. 1e), graphene is the most widely studied, accounting for about 81.5% of the total; especially in the past four years, related studies accounted for about 44.6%. Currently, graphene coatings are also being combined with other related coating materials, such as MOF materials, to further improve the performance of the separator [13,14]. The research on boron nitride (BN) separator started late, and it can be a major research direction in the future. Among the new high-temperature-resistant materials (Fig. 1d), electrospinning and physical blending are the two most common techniques. The application of the latter began about ten years earlier than the former, and its research and application scope is broader than that of separators currently modified using the physical blending method.
Figure 1: (a) 2001–2024 Number of literatures on coatings. (b) 2001–2024 The proportion of various ceramic coating materials. (c) 1927–2024 The proportion of literature on MOF materials. (d) 2001–2024 Number of literature on new high temperature resistant separators. (e) 2001–2024 Proportion of other inorganic coating materials
In recent years, improving the thermal stability of battery separators has become crucial for enhancing both battery safety and performance. Significant progress has been made in the development of new coating materials, nanomaterials, and high-temperature-resistant materials [15]. For example, advanced materials like Metal-Organic Frameworks (MOFs), ceramic coatings, and graphene have shown promising improvements in thermal stability and flame-retardant properties. However, despite the promising laboratory results, one of the major challenges is scaling these materials for large-scale production while maintaining cost-effectiveness and stability.
While thermal stability in separators has advanced, several key challenges remain. One of these is finding the right balance between the separator’s high-temperature resistance and its ionic conductivity. Another challenge is optimizing coating thickness and uniformity, which is crucial to ensure that the separator does not negatively affect the overall performance of the battery. Thus, future research must focus on overcoming these challenges by improving material properties, manufacturing techniques, and reducing costs for broader adoption [16,17].
The main goal of this review is to provide a detailed overview of recent advancements in the thermal stability of battery separators, focusing on the role and potential applications of new coating materials. The paper also highlights the challenges currently faced in the field and suggests potential future research directions. By addressing these issues, this review aims to provide valuable insights into improving separator performance, which will contribute to advancing battery materials and technologies, ultimately improving the safety and efficiency of electric vehicles.
2 Thermal Stability of Battery Separators
The thermal stability of a lithium battery separator refers to its capacity to maintain physical and chemical integrity under high-temperature conditions, thereby preventing internal short circuits and thermal runaway. It is a key factor influencing battery safety, performance maintenance, and lifespan extension.
2.1 Analysis of the Thermal Stability of Traditional Polymer Separators
Polyolefins such as polypropylene (PP) and polyethylene (PE) are currently the most widely used materials for lithium battery separators in the market. They are favored for their high porosity, excellent insulating properties, relatively stable mechanical performance, and low cost [18–20]. However, polyolefin separators have relatively poor thermal stability. They tend to shrink significantly at high temperatures, which may cause internal short-circuits in the battery, ultimately leading to fires or even explosions [21]. In practical production, a PP/PE/PP “sandwich” structure is often employed to improve thermal stability, but its effectiveness remains limited [22,23]. Therefore, there is an urgent need to identify high-performance materials to address the issue of poor thermal stability in polyolefin separators. One fast and efficient approach is to introduce a coating structure on the separator [24].
2.2 Coating Materials Improving the Thermal Stability of Polymer Separators
Modifying separators through coating structures typically involves two approaches: coating methods [25] and grafting methods [26–28]. The coating method is straightforward, highly versatile, and widely used for ceramic coatings [29–32]. The grafting method enables the coating material to grow directly on the polymer separator without increasing the separator’s thickness, thus minimizing the impact on the overall size of the battery. Technically simple and cost-effective, this method is ideal for large-scale industrial production. Common coating materials include metals, inorganic substances, ceramics, and others. Fig. 2 shows common materials and their related structures. Each coating material has its own advantages and is widely applied in different fields. Table 1 summarizes detailed information on surface modification of polyolefin separators reported in the literature.
Figure 2: Related layer materials and their structures
Copper (Cu) is a common metal coating. Lee et al. fabricated a Janus-type membrane (PE/CuTF) by coating a Cu thin film (CuTF) on one side of a traditional polymer separator, which effectively prevents membrane shrinkage. After heat treatment at 140°C for 20 min, the shrinkage rate was 16%, which is related to the resistance to thermal shrinkage provided by the Cu coating. Additionally, it enhances the electronic conductivity of the separator [33]. Liu et al. coated magnesium (Mg) on one side of the separator to improve thermal stability and suppress the growth of lithium dendrites, which can damage the separator. Zinc (Zn) and silver (Ag) have also been reported to have similar properties, offering potential for metal coatings [34].
MOFs, which are porous materials composed of clusters linked by metal ions or organic ligands, possess a large surface area and high porosity, making them advantageous as coating materials for lithium battery separators [23,35,36]. As early as 2013, MOFs were applied to separator materials [37]. However, due to the presence of flammable groups and limited thermal stability that are inherent in MOFs, they are often modified for use as separator coating materials [38–41]. As shown in Fig. 3a, it is a schematic diagram of the MOF coating in the battery.
Figure 3: (a) Illustrating the process of synthesizing Ni-HHTP MOF. Adapted with permission from Reference [46]. 2024, Elsevier B.V. (b) Nd2O3-C/KB separator battery structure. Adapted with permission from Reference [48]. 2024, Elsevier B.V
While Cu and MOF coatings improve thermal stability, they may increase electronic conductivity, leading to undesired electron leakage and accelerated lithium dendrite growth [42–44]. Strategies such as optimizing coating thickness (<50 nm) and hybridizing MOFs with insulating polymers (e.g., PVDF) can mitigate these risks while preserving ionic conductivity [45].
Kim et al. utilized conductive 2D metal-organic frameworks to create Nickel-hexahydroxytriphenylene (Ni-HHTP)@SP composite coating material, which was applied to PE separators to form functional separators. Fig. 3a illustrates the synthesis process of Ni-HHTP MOF. In various stability tests, including coating integrity, dimensional stability, and thermal shrinkage, these separators demonstrated excellent thermal properties and elasticity. At 150°C for 30 min, PE exhibits almost complete shrinkage, while the shrinkage rate of Ni-HHTP@SP separator is 13% (Table 1, No. 5), indicating an improvement in its thermal stability [46]. Song et al. incorporated a 3D porous network channel into the PP separator (rGO/Polyvinylidene Fluoride (PVDF) @PP), which significantly enhanced its thermal stability. After treatment at 120°C for 30 min, the separator showed only a 7% shrinkage rate (Table 1, No. 6), in contrast to the 70% shrinkage rate observed for PP under the same conditions. However, the maximum degradation temperature of the PVDF@PP separator showed only a slight improvement compared to the PP separator, with a difference of just about 3°C. Overall, its thermal stability surpassed that of the PP separator [36,47]. Pan et al. constructed a mixed structure of graphene/layered double hydroxide (LDH) using MOF as a precursor, forming Reduced Graphene Oxide@Layered Double Hydroxide (rGO@LDH), which enhanced the application of MOFs in battery separators. This material exhibited excellent thermal stability, as rGO@LDH promotes the formation of carbides at high temperatures, thereby suppressing shrinkage and degradation of the separator under elevated temperatures. This material also represents a flexible application of 3D structures [36,41].
Hao et al. applied an Nd-MOF coating to create the Nd2O3-C/KB separator. Fig. 3b shows the structural diagram of a battery with the Nd2O3-C/KB separator. It begins to deform only at 120°C, indicating that it can better withstand high-temperature conditions compared to conventional PP/PE separators [48].
Ceramic coatings are widely used in lithium battery separators due to their high temperature resistance and excellent insulating properties. Among them, Al2O3-based ceramics are the most commonly applied [49].
Yu et al. applied a coating of alumina nanoparticle—modified Polyimide (PI) microspheres to modify PP separators (PP@PI), which exhibited good thermal stability. Within the temperature range from room temperature to 150°C, the separator showed no significant changes in size or color. After heat treatment at 150°C for 30 min, the separator with 12% PI content exhibited only a 5% shrinkage (Table 1, No. 7). Moreover, as shown in Fig. 4a, the thermal stability of the modified separator gradually increases with the number of PI microspheres. It has been reported that at 150°C, the PP matrix in PP@PI melts, causing the composite membrane to form a non-porous structure. This characteristic imparts a thermal shutdown function to the separator during battery operation. Therefore, PP@PI holds great potential for practical industrial applications [50]. Lee et al. also tested an Al2O3/PI coating, which exhibited only a 13% shrinkage rate after exposure to 150°C for 30 min (Table 1, No. 8). In comparison, the PP separator showed a 53% shrinkage rate, demonstrating the best performance. However, the adhesive between the ceramic and the polymer significantly affects the thermal stability of the separator [51]. Ravi et al. utilized Lithium Lanthanum Titanate (LLTO)-defective perovskite particles as a coating material to fabricate a PE separator (GCS). After exposure to 130°C for 30 min, the separator exhibited only a 1.6% thermal shrinkage rate, compared to a 16.3% shrinkage rate for PE under the same conditions (Table 1, No. 9), indicating a significant improvement. This demonstrates the coating material’s excellent thermal performance [52]. Shi et al. applied an Al ceramic layer combined with carboxymethyl cellulose (CMC) and styrene-butadiene rubber (SBR) as adhesives to coat PE separators, creating a new CCS membrane. This separator exhibited improved overall thermal stability due to the flexibility and high-temperature resistance of SBR [53]. As shown in Fig. 4b,c, no significant shrinkage of the separator was observed at 130°C. Furthermore, as the thickness of the coating increases, the thermal stability of the separator also improves [29]. Polyurethane (PU) is another polymer separator material with excellent properties. Cheng et al. used electrospinning technology to form PU nanofibers embedded with Al ceramics to create the PUC separator, which further enhanced the thermal stability of the separator (Fig. 4d). No significant shrinkage was observed after heat treatment at 150°C for 30 min (Table 1, No. 13) [54].
Figure 4: (a) PP@PI. Adapted with permission from Reference [50]. 2022, Elsevier B.V. (b) Thermal shrinkage (%) of PE separator and CCS membrane. Adapted with permission from Reference [29]. 2014, Elsevier B.V. (c) Thermal shrinkage (%) of PE separator and CCS membrane at high temperature for 0.5 h (130°C, 145°C, 145°C, 145°C). Adapted with permission from Reference [29]. 2014, Elsevier B.V. (d) Flow chart of preparation of PUC separator. Adapted with permission from Reference [54]. 2022, Elsevier Ltd.
Ceramic materials are relatively cost-effective and environmentally friendly, making them an advantageous choice for coating materials. However, their adhesion to the separator at high temperatures is prone to instability, potentially leading to detachment. This could significantly impact the battery’s safety and stability. This is an area in which future improvements in the application of ceramic materials are needed. Furthermore, ceramic coatings enhance thermal resistance but may reduce electrolyte wettability due to surface hydrophobicity [55–57]. Incorporating hydrophilic binders (e.g., CMC-SBR) or plasma treatment improves interfacial compatibility, balancing thermal and electrochemical performance [58].
2.2.3 Other Inorganic Coatings
Graphene is currently one of the most commonly used materials for separator coatings among inorganic coatings, primarily due to its excellent thermal stability [59–61]. Park et al. developed GES separators by combining graphene and a Cu coating with PP separators. In thermal shrinkage tests, images showed significant shrinkage of the PP separator, while the graphene-enhanced separator (GES) exhibited minimal changes (Fig. 5b), demonstrating improved thermal stability attributed to the graphene structure in GES [18,62]. Graphene coatings, despite excellent thermal conductivity, can hinder Li+ transport due to dense layer stacking. Introducing nanopores or combining with ionic liquid-modified polymers (e.g., BN/PAN composites) enhances ion permeability without compromising thermal stability.
Figure 5: (a) Schematic illustration for the preparation of BN-Separator and the assembly of Li|NCM811 full-cell. Adapted with permission from Reference [35,63]. 2021, Science Press and Dalian Institute of Chemical Physics, Chinese Academy of Sciences. Published by ELSEVIER B.V. and Science Press. 2023, Published by Elsevier B.V. (b) Photographs of the PP separator and GES captured after high-temperature exposure. Adapted with permission from Reference [62]. 2024, Elsevier Ltd. (c) Pictures showing the thermal shrinkage of PE separator (left) and SnO2 coated PE separator (right) after heating at (A) 120°C, (B) 130°C, and (C) 140°C for 0.5 h. Adapted with permission from Reference [64]. 2018, Elsevier B.V
It is well-known that BN has higher thermal conductivity and excellent electrochemical stability with lithium metal compared to other metal compounds [35]. Zhang et al. found that BN coatings could enhance the thermal stability of polyolefin membranes, particularly in terms of resistance to thermal deformation. Fig. 5a shows the preparation of the BN separator and its application in the battery. The BN-modified separator maintains its structural integrity without deformation at 120°C (Table 1, No. 11) and begins to show slight shrinkage only at 140°C, which is attributed to the superior high-temperature resistance of BN nanosheets [63].
Xiang et al. developed a nanoscale SnO2 particle coating, which offers a significant advantage over traditional ceramic coatings such as alumina due to its nanoscale morphology, which can be easily tailored by adjusting synthesis conditions. The SnO2-coated separator exhibited excellent thermal stability, showing no significant deformation at 130°C (Table 1, No. 12) and only minor deformation at around 140°C. Fig. 5c shows the thermal shrinkage of PE separator (left) and SnO2 coated PE separator (right) under exposure to different high temperatures [64].
Currently, MOF coatings have high application costs and complex preparation processes. Although their structures are diverse and tunable, the regulation of pore structure during the preparation process is a significant challenge, which severely impacts the overall performance. Single-metal coatings also encounter challenges such as high costs and demanding application technology requirements. Ceramic coatings still face issues with insufficient adhesion, and their thickness is difficult to control. Additionally, the binder used in these coatings can have a significant impact on the overall performance of the membrane. However, inorganic coatings, apart from ceramic coatings, are rarely applied to improve the thermal stability of membranes. These coatings have lower preparation difficulty and application costs, making them a potential coating option for future applications. Table 1 summarizes most of the separator coatings mentioned in this study, along with their modified properties, serving as a reference for comparison. The separator thickness does not significantly affect the thermal stability; however, it is an important consideration for battery applications. Excessive separator thickness can severely impact the battery’s efficiency, size, safety, and other factors. This presents a key challenge for coated and modified separators currently being developed.
While coatings significantly improve thermal stability, their impact on electrochemical performance must be carefully evaluated. For instance, excessive coating thickness (>30 μm) can increase interfacial resistance, reducing rate capability. Additionally, non-uniform coatings may create localized hotspots during cycling [65]. Advanced characterization techniques, such as in situ electrochemical impedance spectroscopy (EIS) and synchrotron X-ray tomography, are critical for optimizing coating architectures to ensure homogeneous ion flux and mechanical integrity under operational conditions [66].
2.3 New High-Temperature Resistant Separator Materials
Although several high-performance coating materials are available for modifying traditional polyolefin separators, the thickness of the coating itself and the adhesion between the coating and the separator can significantly affect the safety performance of the battery [67]. Consequently, some high-temperature-resistant polymer materials have been employed in separator fabrication [68–72]. Examples include PVDF copolymers, PI, polyacrylonitrile (PAN), polyethylene terephthalate (PET), polyether ether ketone (PEEK), polyvinyl alcohol, and various cellulose copolymers [73–75]. These materials typically have high glass transition temperatures or high melting points, which are shown in Table 2, and are often manufactured using technologies such as electrospinning, pre-irradiation grafting, inversion-phase techniques, and phase separation.
Electrospun PVDF nanofibers were among the earliest used as high-temperature resistant polymers for battery separators. Choi et al. manufactured this separator and used it as a Lithium-Ion Battery (LIB) separator, improving its performance through heat treatment [25]. PAN (polyacrylonitrile) is a membrane material with high thermal resistance and excellent compatibility with electrolyte solutions [76–78]. However, pure PAN membranes have slight mechanical deficiencies. To address this, Dong et al. prepared PAN/cellulose composite membranes by blending PAN with cellulose, significantly improving their performance. As shown in Fig. 5E, compared to PP membranes, the composite membranes with various cellulose contents exhibit no noticeable changes at high temperatures ranging from 180°C to 210°C. The shrinkage rate of the PAN membrane is 2.78%, while that of the PAN/cellulose (5%) composite membrane is 1.39%. In contrast, PAN/cellulose (10% and 15%) composite membranes show no thermal shrinkage. As the temperature increases, the color of the PAN membrane and composite membranes turns yellow and darkens, which is attributed to the oxidation of -CN groups in PAN at high temperatures [79]. Although PAN membranes demonstrate good thermal stability in standard oven tests, Zhao et al. observed in a 4.2 V CR-2032 button-cell thermal oven experiment that PAN membranes performed well at 120°C. However, when the temperature reached 150°C, the battery experienced a short circuit due to the shrinkage caused by the adhesion of expanded PAN fibers [80]. Polyimide (PI) is another commonly used polymer for membrane fabrication, known for its excellent thermal stability and self-extinguishing properties, attributed to the rigid aromatic rings in its structure [81]. Researchers have also introduced ether bonds, polar groups, and other modifications to the PI structure to further enhance its membrane performance. For example, Zhang et al. developed membranes using PI containing ether bonds, which reduced the inherent rigidity of PI due to the flexibility of the ether bonds, thereby improving the thermal stability of the membranes [82]. Similarly, Wang et al. incorporated both ether bonds and trifluoromethyl (-CF3) groups into the PI structure, which not only enhanced thermal stability but also improved the electrolyte wettability of the membranes, leading to further improvements in their overall performance [83].
Among single high-temperature resistant polymer separators, the sandwich electrospinning membrane has been widely studied. Angulakshml et al. created a Poly (vinylidene fluoride-co-hexafluoropropylene) (PVDF-HFP)/(Polyvinyl Chloride (PVC))/Poly (vinylidene fluoride-co-hexafluoropropylene) (PVDF-HFP) structure using electrospinning, which remains relatively stable in a nitrogen atmosphere at around 230°C (Table 2, No. 12) [84]. Wu et al. constructed a composite polyimide/poly (vinylidene fluoride) (PVDF)/polyimide separator using electrospinning. This separator not only provides thermal shutdown functionality to reduce battery thermal imbalance and combustion at high temperatures but also exhibits excellent thermal stability, with no significant deformation at 150°C (Table 2, No. 11). (Fig. 6d). At 170°C, the PVDF nanofibers melt to form a non-porous layer, achieving thermal shutdown functionality. Fig. 6a shows illustrations and cross sectional Scanning Electron Microscope (SEM) images of the PI/PVDF/PI separator before and after the high temperature melt and shutdown behavior of the PVDF nanofibers layer [85].
Figure 6: (a) Illustrations and cross sectional SEM images of the PI/PVDF/PI separator before and after the high temperature melt and shutdown behavior of the PVDF nanofibers layer. Adapted with permission from Reference [85]. 2015, Elsevier Ltd. (b) The Thermogravimetric Analysis (TGA) curves. (i) corresponding Derivative Thermogravimetric (DTG) curves. (ii) of relevant membranes. Adapted with permission from Reference [86]. 2020, Elsevier Ltd. (c) Photographs of PP, PVDF and composite PET/PVDF membrane. (i) before and (ii) after exposure to 150°C for 30 min. Adapted with permission from Reference [87]. 2015, IOP Publishing Ltd. (d) (i–vi) Optical photos of PP and PI/PVDF/PI separators before and after the thermal treatments for 2 h. (i) before the thermal treatment. (ii) 90°C. (iii) 160°C. (vi) 180°C. The data inserted in (ii–vi) represent the shrinkage percentages and the red arrows are machining directions for the PP separator. (v–viii) Optical photos of the singlelayer PVDF nanofibers separators and PI nanofibers separators before and after the thermal treatments for 2 h. (v) before the thermal treatment. (vi) 90°C for the thermal treatment temperature. (vii) 160°C and (viii) 180°C for the thermal treatment temperature. Adapted with permission from Reference [85]. 2015, Elsevier Ltd. (e) Images of different separators after heat treatment at 180°C, 200°C, 210°C and 220°C. Adapted with permission from Reference [79]. 2021, The Author(s), under exclusive licence to Springer-Verlag GmbH Germany, part of Springer Nature
Compared to the electrospinning method for improving high-temperature polymer materials, physical blending is also a fast and efficient approach. Generally, electrospinning is also considered a part of physical blending. By blending two or more materials with complementary properties, it is possible to effectively enhance the thermal stability of the separator while reducing production costs. For example, Cai et al. developed a 3D thermally crosslinked PVDF-HFP/PI separator structure, which exhibited excellent thermal stability with no significant shrinkage at 200°C (Table 2, No. 13) (Fig. 6b). The thermal weight loss comparison shows that its pyrolysis occurs at approximately 565°C (Fig. 6b–i) and is quickly extinguished during combustion testing [86]. Wu et al. demonstrated that the composite PET/PVDF separator showed no significant deformation at 150°C (Table 2, No. 14), whereas PP and PVDF exhibited noticeable changes, as shown in Fig. 6c. This is attributed to the stronger high-temperature resistance of PET, which results in better thermal stability [87].
Table 2 summarizes the properties of several novel high-temperature resistant polymers. Their primary characteristic is the combination of excellent thermal stability with the ability to maintain a stable separator thickness. In comparison to coating modification methods, these materials offer enhanced stability, lower cost, and greater suitability for industrial production and application in batteries.
Table 3 summarizes key parameters of next-generation high-temperature-resistant separators, including thermal shrinkage, ionic conductivity, mechanical strength, and scalability
In today’s rapidly advancing technological landscape, lithium batteries, known for their high energy density, long cycle life, and relatively low self-discharge rate, have found widespread application in electric vehicles, energy storage systems, and various portable electronic devices. Meanwhile, the ongoing development and widespread use of lithium batteries have heightened the demands for improved performance and safety. Among these, the separator, as a key component of lithium batteries, significantly impacts their thermal stability, which is a crucial factor affecting the safety of lithium batteries. The thermal stability of the separator directly influences the battery’s performance and reliability in overheating conditions. Insufficient thermal stability of the separator may lead to performance degradation in high-temperature environments and could even trigger thermal runaway reactions, posing threats to battery lifespan and safety. Through various studies, the thermal stability of separators has been continuously improved and can be significantly enhanced by using various coating materials and special techniques. Table 4 compares different coating materials and separator materials, listing their advantages, disadvantages, current status, and directions for improvement.
3.1 Current Status of Each Separator in Actual Production
Traditional polyolefin separators (PP and PE) have long dominated the lithium battery separator market. They offer high porosity, good insulation properties, relatively stable mechanical performance, and low cost, which provide significant economic advantages in large-scale production and commercial applications. However, their poor thermal stability is a notable concern, leading to substantial safety risks during use and limiting their application in real-world production and life scenarios. The PP/PE/PP sandwich structure has been used to improve this issue, but it still does not fundamentally solve the problem of poor thermal stability.
The thermal stability of separators can be improved by adding coating structures. Common coating materials include metals, ceramics, and inorganic substances. Metal coatings such as MOFs (Metal-Organic Frameworks) and their modifications can enhance separator thermal stability. However, MOFs themselves have flammable groups and insufficient thermal stability, so they are often used as coating materials after modification. In practical production, there are many challenges. The processes are complex, involving multiple chemical reactions and precise control conditions, which leads to high production costs. Their compatibility with existing battery production processes is poor, making it difficult to integrate them seamlessly into large-scale production workflows. Long-term stability is yet to be validated, and more practical research requires to improve these issues [88,89].
Ceramic coatings, such as alumina ceramics, are widely used due to their high-temperature resistance and good insulation properties. The PP@PI separator has good thermal stability and strong safety, while Lithium Lanthanum Titanate (LLTO)-defective perovskite particle coatings significantly reduce the thermal shrinkage of PE separators. However, the adhesive between the ceramic and polymer has a major impact on the separator’s thermal stability. If the adhesive properties are poor, it can fail in high-temperature environments, causing the ceramic coating to peel off and severely compromising battery safety and stability.
Among inorganic coatings, graphene is one of the most widely used materials for separator coatings. Its excellent thermal stability allows it to effectively improve the thermal performance of the separator. Some inorganic coating materials can also improve the thermal stability of polyolefin films. For example, GES separators have better thermal stability than PP separators, and BN-modified separators maintain structural integrity at 120°C. While inorganic coatings are still relatively limited in their application for improving separator thermal stability, they are a promising option that warrants further research and development in the future.
Some new high-temperature-resistant materials have been applied in separator production due to their ability to withstand high temperatures, along with various manufacturing technologies such as electrospinning, pre-irradiation grafting, phase inversion and phase separation, and physical blending. Although these separators show good thermal stability, their application in actual production is still limited, and it will take some time before they are widely adopted.
3.2 Future Outlook: Potential Research Directions
3.2.1 Some Possible Research Directions Based on Diaphragms and Coatings Are Considered
There are some following research directions that could be considered.
Research on improving the thermal stability of polyolefin separators requires continuous in-depth exploration. On one hand, discovering more high-performance materials remains a key task. Efforts should be made to actively identify materials with superior thermal stability, better compatibility with polyolefin separators, and lower costs, fundamentally addressing the insufficient thermal stability of traditional polyolefin separators. On the other hand, further optimizing the performance of existing coating materials is a crucial pathway to enhancing the overall performance of separators [90,91].
For metal coatings, in-depth studies on modification methods are necessary. By employing innovative chemical modification techniques or composite strategies, it may be possible to enhance thermal stability while reducing costs. For example, exploring simpler, more efficient, and cost-effective MOF modification methods, or investigating the potential for composites with other inexpensive materials, could optimize performance and lower production costs [92,93].
For ceramic coatings, improving the performance of adhesives is a pressing issue. Enhancing the adhesive’s properties to strengthen its bonding with separators at high temperatures is critical for ensuring thermal stability. This can involve developing new high-temperature-stable adhesives or modifying existing ones to improve their bonding strength with both the separator and the ceramic coating under high-temperature conditions. This ensures a tight bond between the ceramic coating and separator in extreme high-temperature environments, preventing delamination.
This also involves studying the relationship between the chemical structure and performance of adhesives. Through molecular design and material optimization, it is possible to develop adhesives that meet the requirements for high-temperature and high-strength bonding. Additionally, research on the interfacial interactions between ceramic coatings is also needed.
3.2.2 Semi-Solid State Batteries and All-Solid State Batteries
Integrating electrolytes and separators, or even eliminating separators to manufacture solid-state batteries, including semi-solid-state batteries (SSSBs) or all-solid-state batteries (ASSBs), has become the main development trend nowadays due to the higher energy density and better thermal stability of these solid-state batteries [94–96].
ASSBs have high safety, with no flammable and easily leakable liquid components. They possess relatively high energy density, flexible structures, and can be fabricated into thin-film or flexible forms. However, the current technology is not yet fully mature and is still in the research and development stage. There are challenges such as low conductivity of electrolytes, dendrite growth, poor cycling performance and low rate performance. There are also difficulties regarding interfaces [97]. The high price of solid electrolytes (SEs), immature production lines, and additional stack pressure equipment create obstacles to the scale-up of ASSBs [98,99]. In recent years, however, scholars have devoted a great deal of research efforts to understand the interfacial behaviors of all-solid-state batteries and explore strategies, investigating various types of all-solid-state batteries, including solid-state lithium batteries, lithium-sulfur batteries, etc. [99]. Nowadays, some researchers are mainly focusing on constructing advanced SE and improving interfacial compatibility to solve the practical application problems of current all-solid-state lithium batteries (ASSLBs). Moreover, some specific properties of ASSLBs, such as flexibility and non-flammability, have also been exploited [97].
For solid-state batteries, SSSBs represent an important transitional stage. SSSBs have relatively good safety, with reduced liquid components, which lower the risks of combustion and leakage. They have relatively high energy density, improved utilization rates of cathode and anode materials, mature manufacturing processes that are similar to those of liquid lithium batteries, and are easy to scale up for production [100]. They also have high conductivity, low resistance, and enhanced power density [98,101]. However, they also face obstacles such as the encapsulation of solid electrolyte membranes and electrode materials. Nevertheless, some researchers have already developed a free-standing single-ion conductive semi-solid polymer electrolyte (PBSIL), which promotes the rapid transport of lithium ions through the fixation of lithium ion transport and anions, and the battery has long-term stability [102]. Moreover, SSSBs are regarded by many domestic battery companies as a transitional stage from liquid batteries to solid-state batteries and can be considered for use in the new energy vehicle industry [103]. Although SSSBs are an intermediate route, the goal of improving safety can only be achieved when the proportion of added liquid is significantly reduced. And for safety reasons, the liquid components can only be used as interfacial agents to maintain a low liquid fraction, and the solid/liquid interface needs to have chemical stability [98]. Research has found that thin separators (<60 μm) and thick cathodes (>4 mAh/cm2) are helpful for improving energy density. It is also necessary to explore technologies such as microstructure optimization and dry calendering with different shear forces to reduce the porosity of cathode composites. Some experiments have achieved in-situ polymerization and solidification of liquid components, allowing the liquid to initially act as a “self-healing” additive and ensuring sufficient contact between electrodes after polymerization [98].
Although significant progress has been made, research on the thermal stability of lithium battery separators still has a long way to go. Further experimental studies are required to better understand the performance of different separator materials and designs in practical applications. Future research should also consider the overall thermal management of the battery system, as the thermal stability of the separator is only a part of the system’s overall thermal stability. We need to develop a comprehensive thermal management strategy to ensure optimal battery performance under various environmental conditions. Furthermore, future research must prioritize multifunctional separator designs that harmonize thermal resilience with electrochemical efficiency. For instance, hybrid coatings combining ceramics with flexible polymers (e.g., Al2O3/PU) or gradient-structured MOF composites could simultaneously suppress thermal shrinkage and enhance Li+ transport. Additionally, machine learning-driven material discovery and scalable manufacturing techniques (e.g., roll-to-roll electrospinning) will accelerate the transition from lab-scale innovations to industrial applications.
In conclusion, as lithium battery technology is widely used in fields such as new energy vehicles and energy storage systems, the research on the thermal stability of lithium battery separators is becoming increasingly important. We look forward to further developments and breakthroughs in this area.
Acknowledgement: None.
Funding Statement: This work was financially supported by Beijing Institute of Technology Student Innovation Training Program (BIT2024LH013). We would like to thank the China Association for Science and Technology (CAST) for supporting this research through the 2024 “Soaring Wings” University Student Science and Technology Volunteer Service Project (XMSB20240923022).
Author Contributions: Haoran Li: Writing—original draft, Methodology, Investigation. Yayou Xu: Writing—review & editing, Investigation. Zihan Zhang: Writing—review & editing, Investigation, Data curation. Feng Han: Formal analysis, Investigation, Data curation. Ye-Tang Pan: Writing—review & editing, Methodology, Funding acquisition, Conceptualization. Rongjie Yang: Supervision, Methodology. All authors reviewed the results and approved the final version of the manuscript.
Availability of Data and Materials: All data generated or analyzed during this study are included in this published article.
Ethics Approval: Not applicable.
Conflicts of Interest: The authors declare no conflicts of interest to report regarding the present study.
Abbreviations
MOF | Metal-Organic Framework |
PP | Polypropylene |
PE | Polyethylene |
PVDF | Polyvinylidene Fluoride |
Ni-HHTP | Nickle-hexahydroxytriphenylene |
PI | Polyimide |
PAN | Polyacrylonitrile |
rGO@LDH | Reduced Graphene Oxide@Layered Double Hydroxide |
PET | Polyethylene terephthalate |
PEEK | Poly-ether-ether-ketone |
CMC | Carboxymethyl cellulose |
SBR | Styrene-butadiene rubber |
-CF3 | Trifluoromethyl |
LIB | Lithium-Ion Battery |
PVC | Polyvinyl Chloride |
SEM | Scanning Electron Microscope |
TGA | Thermogravimetric Analysis |
DTG | Derivative Thermogravimetry |
PMIA | Polymethacrylimide |
PAEK | Polyaryletherketone |
PSA | Polysulfonamide |
LLTO | Lithium Lanthanum Titanate |
References
1. Du J, Ouyang M, Chen J. Prospects for Chinese electric vehicle technologies in 2016–2020: ambition and rationality. Energy. 2017;120(8):584–96. doi:10.1016/j.energy.2016.11.114. [Google Scholar] [CrossRef]
2. Duan J, Tang X, Dai H, Yang Y, Wu W, Wei X, et al. Building safe lithium-ion batteries for electric vehicles: a review. Electrochem Ener Rev. 2020;3(1):1–42. doi:10.1007/s41918-019-00060-4. [Google Scholar] [CrossRef]
3. Rana S, Kumar R, Bharj RS. Current trends, challenges, and prospects in material advances for improving the overall safety of lithium-ion battery pack. Chem Eng J. 2023;463(6):142336. doi:10.1016/j.cej.2023.142336. [Google Scholar] [CrossRef]
4. Zhang X, Sun Q, Zhen C, Niu Y, Han Y, Zeng G, et al. Recent progress in flame-retardant separators for safe lithium-ion batteries. Energy Storage Mater. 2021;37(44):628–47. doi:10.1016/j.ensm.2021.02.042. [Google Scholar] [CrossRef]
5. Wang J, Cai W, Mu X, Han L, Wu N, Liao C, et al. Construction of multifunctional and flame retardant separator towards stable lithium-sulfur batteries with high safety. Chem Eng J. 2021;416(29):129087. doi:10.1016/j.cej.2021.129087. [Google Scholar] [CrossRef]
6. Tong B, Li X. Towards separator safety of lithium-ion batteries: a review. Mater Chem Front. 2024;8(2):309–40. doi:10.1039/D3QM00951C. [Google Scholar] [CrossRef]
7. Zhou H, Liu P. Designing polymer coatings for lithium metal protection. Nanotechnology. 2022;33(11):112501. doi:10.1088/1361-6528/ac3fe2. [Google Scholar] [PubMed] [CrossRef]
8. Liao C, Mu X, Han L, Li Z, Zhu Y, Lu J, et al. A flame-retardant, high ionic-conductivity and eco-friendly separator prepared by papermaking method for high-performance and superior safety lithium-ion batteries. Energy Storage Mater. 2022;48(4):123–32. doi:10.1016/j.ensm.2022.03.008. [Google Scholar] [CrossRef]
9. Wang J, Cai W, Mu X, Han L, Wu N, Liao C, et al. Designing of multifunctional and flame retardant separator towards safer high-performance lithium-sulfur batteries. Nano Res. 2021;14(12):4865–77. doi:10.1007/s12274-021-3446-4. [Google Scholar] [CrossRef]
10. Nitou MVM, Tang M, Niu Y, Pang Y, Wan Z, Mawuli SE, et al. Separator with active coating for fast and stable Li-ion batteries. J Power Sources. 2024;602:234406. doi:10.1016/j.jpowsour.2024.234406. [Google Scholar] [CrossRef]
11. Xu E, Mo L, Zhou Y, Cheng Z, Li P, Tian X, et al. Promoted Li salt dissociation and ion transport of a high-dielectric coating film enable superior lithium battery. Appl Energy. 2025;377(5):124750. doi:10.1016/j.apenergy.2024.124750. [Google Scholar] [CrossRef]
12. Li Y, Liu X, Ren D, Hsu H, Xu G-L, Hou J, et al. Toward a high-voltage fast-charging pouch cell with TiO2 cathode coating and enhanced battery safety. Nano Energy. 2020;71:104643. doi:10.1016/j.nanoen.2020.104643. [Google Scholar] [CrossRef]
13. Sun X, Lin T, Hou Y, Hou B, Pan Y, Yang R. MOFs with hierarchical nanostructures towards future functional polymers. Nano Mate Sci. 2025. doi:10.1016/j.nanoms.2024.12.008. [Google Scholar] [CrossRef]
14. Sun X, Pan Y-T, Wang W, Yang R. Surface modification of MOFs towards flame retardant polymer composites. RSC Appl Interf. 2025;2(1):14–24. doi:10.1039/D4LF00252K. [Google Scholar] [CrossRef]
15. Shi M, Gao S, Shang L, Ma L, Wang W, Liu G, et al. Lab-on-fiber sensors with Ag/Au nanocap arrays based on the two deposits of polystyrene nanospheres. Polymers. 2023;15(20):4107. doi:10.3390/polym15204107. [Google Scholar] [PubMed] [CrossRef]
16. Zhang L, Li X, Yang M, Chen W. High-safety separators for lithium-ion batteries and sodium-ion batteries: advances and perspective. Energy Storage Mater. 2021;41:522–45. doi:10.1016/j.ensm.2021.06.033. [Google Scholar] [CrossRef]
17. Chen Y-S, Chang W-H, Kuo T-Y, Chang J-K, Su Y-S. Enhancing the performance of metallic lithium anode in batteries through water-resistant and air-stable coating. J Energy Storage. 2024;82(2021):110532. doi:10.1016/j.est.2024.110532. [Google Scholar] [CrossRef]
18. Ding H, Ge J, Zhang T, He C, Zhang H, Mohamad Ali B, et al. Thermally stable poly-aromatic solid electrolyte coated polyethylene membrane as high-performance lithium-ion battery separator. J Power Sources. 2024;602:234355. doi:10.1016/j.jpowsour.2024.234355. [Google Scholar] [CrossRef]
19. Arora P, Zhang Z. Battery separators. Chem Rev. 2004;104(10):4419–62. doi:10.1021/cr020738u. [Google Scholar] [PubMed] [CrossRef]
20. Zhu L, Ding G, Han Q, Yang X, Xie L, Cao X. Review—recent developments in safety-enhancing separators for lithium-ion batteries. J Electrochem Soc. 2021;168(10):100524. doi:10.1149/1945-7111/ac2dca. [Google Scholar] [CrossRef]
21. Liu Z, Peng Y, Meng T, Yu L, Wang S, Hu X. Thermal-triggered fire-extinguishing separators by phase change materials for high-safety lithium-ion batteries. Energy Storage Mater. 2022;47:445–52. doi:10.1016/j.ensm.2022.02.020. [Google Scholar] [CrossRef]
22. Choi J, Kim PJ. A roadmap of battery separator development: past and future. Curr Opin Electrochem. 2022;31:100858. doi:10.1016/j.coelec.2021.100858. [Google Scholar] [CrossRef]
23. Hou B, Pan Y-T, Song P. Metal-organic frameworks as promising flame retardants for polymeric materials. Microstructures. 2023;3(4):2023039. doi:10.20517/microstructures.2023.37. [Google Scholar] [CrossRef]
24. Cao J, Pan Y-T, Vahabi H, Song J-I, Song P, Wang D-Y, et al. Zeolitic imidazolate frameworks-based flame retardants for polymeric materials. Mater Today Chem. 2024;37(1):102015. doi:10.1016/j.mtchem.2024.102015. [Google Scholar] [CrossRef]
25. Lu W, Yuan Z, Zhao Y, Zhang H, Zhang H, Li X. Porous membranes in secondary battery technologies. Chem Soc Rev. 2017;46(8):2199–236. doi:10.1039/C6CS00823B. [Google Scholar] [PubMed] [CrossRef]
26. Shi J-L, Fang L-F, Li H, Zhang H, Zhu B-K, Zhu L-P. Improved thermal and electrochemical performances of PMMA modified PE separator skeleton prepared via dopamine-initiated ATRP for lithium ion batteries. J Membr Sci. 2013;437:160–8. doi:10.1016/j.memsci.2013.03.006. [Google Scholar] [CrossRef]
27. Jeon H, Jin SY, Park WH, Lee H, Kim H-T, Ryou M-H, et al. Plasma-assisted water-based Al2O3 ceramic coating for polyethylene-based microporous separators for lithium metal secondary batteries. Electrochim Acta. 2016;212:649–56. doi:10.1016/j.electacta.2016.06.172. [Google Scholar] [CrossRef]
28. Gwon S-J, Choi J-H, Sohn J-Y, Ihm Y-E, Nho Y-C. Preparation of a new micro-porous poly(methyl methacrylate)-grafted polyethylene separator for high performance Li secondary battery. Nuclear Instrum Meth Phy Res Sec B: Beam Interact Mat Atoms. 2009;267(19):3309–13. doi:10.1016/j.nimb.2009.06.117. [Google Scholar] [CrossRef]
29. Shi C, Zhang P, Chen L, Yang P, Zhao J. Effect of a thin ceramic-coating layer on thermal and electrochemical properties of polyethylene separator for lithium-ion batteries. J Power Sources. 2014;270:547–53. doi:10.1016/j.jpowsour.2014.07.142. [Google Scholar] [CrossRef]
30. Cheng Q, He W, Zhang X, Li M, Song X. Recent advances in composite membranes modified with inorganic nanoparticles for high-performance lithium ion batteries. RSC Adv. 2016;6(13):10250–65. doi:10.1039/C5RA21670Bc. [Google Scholar] [CrossRef]
31. Hwang Y, Kim M. Effect of a polypropylene separator with a thin electrospun ceramic/polymer coating on the thermal and electrochemical properties of lithium-ion batteries. Polymers. 2024;16(18):2627. doi:10.3390/polym16182627. [Google Scholar] [PubMed] [CrossRef]
32. Shin W-K, Kannan AG, Kim D-W. Effective suppression of dendritic lithium growth using an ultrathin coating of nitrogen and sulfur codoped graphene nanosheets on polymer separator for lithium metal batteries. ACS Appl Mat Interf. 2015;7(42):23700–7. doi:10.1021/acsami.5b07730. [Google Scholar] [PubMed] [CrossRef]
33. Lee H, Ren X, Niu C, Yu L, Engelhard MH, Cho I, et al. Suppressing lithium dendrite growth by metallic coating on a separator. Adv Funct Mater. 2017;27(45):1704391. doi:10.1002/adfm.201704391. [Google Scholar] [CrossRef]
34. Liu Y, Xiong S, Wang J, Jiao X, Li S, Zhang C, et al. Dendrite-free lithium metal anode enabled by separator engineering via uniform loading of lithiophilic nucleation sites. Energy Stor Mater. 2019;19:24–30. doi:10.1016/j.ensm.2018.10.015. [Google Scholar] [CrossRef]
35. Wu N, Wang J, Liao C, Han L, Song L, Hu Y, et al. A flame retardant separator modified by MOFs-derived hybrid for safe and efficient Li-S batteries. J Energy Chem. 2022;64:372–84. doi:10.1016/j.jechem.2021.05.001. [Google Scholar] [CrossRef]
36. Song X, Lei X, Tian T, Yu T, Zhu H, Zhang Z, et al. Constructing 3D porous network channel on PP-based separator to achieve homogeneous deposition of lithium ions for lithium metal battery. Electrochim Acta. 2024;499:144568. doi:10.1016/j.electacta.2024.144568. [Google Scholar] [CrossRef]
37. Huo J, Marcello M, Garai A, Bradshaw D. MOF-polymer composite microcapsules derived from Pickering emulsions. Adv Mater. 2013;25(19):2717–22. doi:10.1002/adma.201204913. [Google Scholar] [PubMed] [CrossRef]
38. Song K, Hou B, Ur Rehman Z, Pan Y-T, He J, Wang D-Y, et al. “Sloughing” of metal-organic framework retaining nanodots via step-by-step carving and its flame-retardant effect in epoxy resin. Chem Eng J. 2022;448(10):137666. doi:10.1016/j.cej.2022.137666. [Google Scholar] [CrossRef]
39. Hou B, Zhang W, Lu H, Song K, Geng Z, Ye X, et al. Multielement flame-retardant system constructed with metal POSS-organic frameworks for epoxy resin. ACS Appl Mat Interf. 2022;14(43):49326–37. doi:10.1021/acsami.2c14740. [Google Scholar] [PubMed] [CrossRef]
40. Huang G, Pan Y-T, Liu L, Song P, Yang R. Metal-organic frameworks and their derivatives for sustainable flame-retardant polymeric materials. Advan Nanocompos. 2025;2(4):1–14. doi:10.1016/j.adna.2024.10.001. [Google Scholar] [CrossRef]
41. Wang R, Zhang X, Yuan M, Wang D-Y, Zhang J, Pan Y-T. Fire retardancy of epoxy composites: a comparative investigation on the influence of porous structure and transition metal of metal-organic framework. Compos Commun. 2024;51(43):102087. doi:10.1016/j.coco.2024.102087. [Google Scholar] [CrossRef]
42. Rubin EB, Chen Y, Chen R. Optical properties and thermal stability of Cu spinel oxide nanoparticle solar absorber coatings. Sol Energy Mater Sol Cells. 2019;195(10):81–8. doi:10.1016/j.solmat.2019.02.032. [Google Scholar] [CrossRef]
43. Yuan N, Sun W, Yang J, Gong X, Liu R. Multifunctional MOF-based separator materials for advanced lithium-sulfur batteries. Adv Mater Interfaces. 2021;8(9):2001941. doi:10.1002/admi.202001941. [Google Scholar] [CrossRef]
44. Phung J, Zhang X, Deng W, Li G. An overview of MOF-based separators for lithium-sulfur batteries. Sustain Mater Technol. 2022;31(25):e00374. doi:10.1016/j.susmat.2021.e00374. [Google Scholar] [CrossRef]
45. Park J, Kwon YJ, Yun J, Bae JW, Lee MJ, Zhang K, et al. Fluorine-rich modification of self-extinguishable lithium-ion battery separators using cross-linking networks of chemically functionalized PVDF terpolymers for highly enhanced electrolyte affinity and thermal-mechanical stability. J Mater Chem A. 2024;12(4):2011–23. doi:10.1039/D3TA06261A. [Google Scholar] [CrossRef]
46. Kim D, Park Y, Nam KW. Inhibiting polysulfide shuttle and enhancing polysulfide redox: conductive 2D metal-organic framework coated separators for lithium-sulfur batteries. J Alloys Comp. 2024;1009:176812. doi:10.1016/j.jallcom.2024.176812. [Google Scholar] [CrossRef]
47. Pan Y-T, Wan J, Zhao X, Li C, Wang D-Y. Interfacial growth of MOF-derived layered double hydroxide nanosheets on graphene slab towards fabrication of multifunctional epoxy nanocomposites. Chem Eng J. 2017;330:1222–31. doi:10.1016/j.cej.2017.08.059. [Google Scholar] [CrossRef]
48. Hao Q, Qian X, Jin L, Zhang K, Zhao S, Li B. Application of Nd-MOF derived Nd2O3-C/KB and Nd2O3-C/CNT for lithium-sulfur battery separators. Coll Surf A: Physicochem Eng Asp. 2024;702:134948. doi:10.1016/j.colsurfa.2024.134948. [Google Scholar] [CrossRef]
49. Li H, Luo D, He J, Lin F, Wang H, Yu L, et al. Crystalline Al2O3 modified porous poly(aryl ether ketone) (PAEK) composite separators for high performance lithium-ion batteries via an electrospinning technique. CrystEngComm. 2020;22(9):1577–85. doi:10.1039/C9CE01557D. [Google Scholar] [CrossRef]
50. Yu J, Dong N, Liu B, Tian G, Qi S, Wu D. A newly-developed heat-resistance polyimide microsphere coating to enhance the thermal stability of commercial polyolefin separators for advanced lithium-ion battery. Chem Eng J. 2022;442:136314. doi:10.1016/j.cej.2022.136314. [Google Scholar] [CrossRef]
51. Lee Y, Lee H, Lee T, Ryou M-H, Lee YM. Synergistic thermal stabilization of ceramic/co-polyimide coated polypropylene separators for lithium-ion batteries. J Power Sources. 2015;294:537–44. doi:10.1016/j.jpowsour.2015.06.106. [Google Scholar] [CrossRef]
52. Muchakayala R, Yarramsetti S, Maram PS, Kalluri S, Ran F, Sangaraju S. Modified ceramic coated polyethylene separator—a strategy for using lithium metal as anode with superior electrochemical performance and thermal stability. J Energy Storage. 2023;68:107687. doi:10.1016/j.est.2023.107687. [Google Scholar] [CrossRef]
53. Yoshio M, Tsumura T, Dimov N. Silicon/graphite composites as an anode material for lithium ion batteries. J Power Sources. 2006;163(1):215–8. doi:10.1016/j.jpowsour.2005.12.078. [Google Scholar] [CrossRef]
54. Cheng C, Liu H, Ouyang C, Hu N, Zha G, Hou H. A high-temperature stable composite polyurethane separator coated Al2O3 particles for lithium ion battery. Compos Commun. 2022;33:101217. doi:10.1016/j.coco.2022.101217. [Google Scholar] [CrossRef]
55. Wu S, Ning J, Jiang F, Shi J, Huang F. Ceramic nanoparticle-decorated melt-electrospun PVDF nanofiber membrane with enhanced performance as a lithium-ion battery separator. ACS Omega. 2019;4(15):16309–17. doi:10.1021/acsomega.9b01541. [Google Scholar] [PubMed] [CrossRef]
56. Wang Z, Li X, Dong N, Liu B, Tian G, Qi S, et al. A novel Pe composite separator coated by ZrO2@Pi nanospheres enabling ultralight weight, highly-improved thermal dimensional stability, and wettability for advanced and safe li-ion battery. 2022. doi:10.2139/ssrn.4136291. [Google Scholar] [CrossRef]
57. Wang Z, Li X, Dong N, Liu B, Tian G, Qi S, et al. Novel ZrO2@Polyimde nano-microspheres-coated polyethylene separators for high energy density and high safety Li-ion battery. Mater Today Energy. 2022;30(3):101155. doi:10.1016/j.mtener.2022.101155. [Google Scholar] [CrossRef]
58. Mehta A, Vasudev H. Advancements in ceramic-coated metals: enhancing thermal spray coatings for improved performance in aerospace applications using surface treatments. Res Surf Interf. 2025;18:100387. doi:10.1016/j.rsurfi.2024.100387. [Google Scholar] [CrossRef]
59. Kumar P, Sarkar A, Jain P. Green synthesis of reduced graphene oxide nanosheet by using L-ascorbic acid and study of its cytotoxicity on human cervical cancer cell line. J Polym Mate. 2022;39(1–2):121–35. doi:10.32381/JPM.2022.39.1-2.8. [Google Scholar] [CrossRef]
60. Shivakumar H, Gurumurthy GD, Bommegowda KB, Parameshwara S. Study of galvanic charging-discharging properties of graphene nanoplatelets incorporated epoxy-carbon fabric composites. J Polym Mat. 2023;40(1–2):93–103. doi:10.32381/JPM.2023.40.1-2.8. [Google Scholar] [CrossRef]
61. Arun Kumar M, Jayakumari LS, Chandran R. Enhanced mechanical and electrical properties of styrene butadiene rubber nanocomposites with graphene platelet nano-powder. J Polym Mat. 2023;40(3–4):141–56. doi:10.32381/JPM.2023.40.3-4.2. [Google Scholar] [CrossRef]
62. Park M, Woo S, Seo J, Choi J, Jeong E, Kim PJ. Directing the uniform and dense Li deposition via graphene-enhanced separators for high-stability Li metal batteries. Electrochim Acta. 2024;495:144426. doi:10.1016/j.electacta.2024.144426. [Google Scholar] [CrossRef]
63. Zhang Q, Wang Z, Liu Y-G, Zhu B, Wu L, Mi R, et al. Homogeneous deposition of lithium ions enabled by BN coated separator for high-performance lithium-metal batteries. Surf Interfaces. 2023;43:103568. doi:10.1016/j.surfin.2023.103568. [Google Scholar] [CrossRef]
64. Xiang Y, Wang Z, Qiu W, Guo Z, Liu D, Qu D, et al. Interfacing soluble polysulfides with a SnO2 functionalized separator: an efficient approach for improving performance of Li-S battery. J Membr Sci. 2018;563:380–7. doi:10.1016/j.memsci.2018.06.004. [Google Scholar] [CrossRef]
65. Horváth DV, Tian R, Gabbett C, Nicolosi V, Coleman JN. Quantifying the effect of separator thickness on rate performance in lithium-ion batteries. J Electrochem Soc. 2022;169(3):030503. doi:10.1149/1945-7111/ac5654. [Google Scholar] [CrossRef]
66. Miranda D, Gonçalves R, Wuttke S, Costa CM, Lanceros-Méndez S. Overview on theoretical simulations of lithium-ion batteries and their application to battery separators. Adv Energy Mater. 2023;13(13):2203874. doi:10.1002/aenm.202203874. [Google Scholar] [CrossRef]
67. Bicy K, Gueye AB, Rouxel D, Kalarikkal N, Thomas S. Lithium-ion battery separators based on electrospun PVDF: a review. Surf Interfaces. 2022;31:101977. doi:10.1016/j.surfin.2022.101977. [Google Scholar] [CrossRef]
68. Wang F, Ke X, Shen K, Zhu L, Yuan C. A critical review on materials and fabrications of thermally stable separators for lithium-ion batteries. Adv Mater Technol. 2022;7(5):2100772. doi:10.1002/admt.202100772. [Google Scholar] [CrossRef]
69. Sun X, Li M, Ren S, Lei T, Lee SY, Lee S, et al. Zeolitic imidazolate framework-cellulose nanofiber hybrid membrane as Li-Ion battery separator: basic membrane property and battery performance. J Power Sources. 2020;454:227878. doi:10.1016/j.jpowsour.2020.227878. [Google Scholar] [CrossRef]
70. Peng K, Wang B, Ji C. A poly(ethylene terephthalate) nonwoven sandwiched electrospun polysulfonamide fibrous separator for rechargeable lithium ion batteries. J Appl Polym Sci. 2017;134(22):44907. doi:10.1002/app.44907. [Google Scholar] [CrossRef]
71. Zhu Y, Yin M, Liu H, Na B, Lv R, Wang B, et al. Modification and characterization of electrospun poly (vinylidene fluoride)/poly (acrylonitrile) blend separator membranes. Compos Part B: Eng. 2017;112:31–7. doi:10.1016/j.compositesb.2016.12.025. [Google Scholar] [CrossRef]
72. Park S, Son CW, Lee S, Kim DY, Park C, Eom KS, et al. Multicore-shell nanofiber architecture of polyimide/polyvinylidene fluoride blend for thermal and long-term stability of lithium ion battery separator. Sci Rep. 2016;6(1):36977. doi:10.1038/srep36977. [Google Scholar] [PubMed] [CrossRef]
73. Huang D, Liang C, Chen L, Tang M, Zheng Z, Wang Z. MOF composite fibrous separators for high-rate lithium-ion batteries. J Mater Sci. 2021;56(9):5868–77. doi:10.1007/s10853-020-05559-6. [Google Scholar] [CrossRef]
74. Miao Y-E, Zhu G-N, Hou H, Xia Y-Y, Liu T. Electrospun polyimide nanofiber-based nonwoven separators for lithium-ion batteries. J Power Sources. 2013;226:82–6. doi:10.1016/j.jpowsour.2012.10.027. [Google Scholar] [CrossRef]
75. Chun S-J, Choi E-S, Lee E-H, Kim JH, Lee S-Y, Lee S-Y. Eco-friendly cellulose nanofiber paper-derived separator membranes featuring tunable nanoporous network channels for lithium-ion batteries. J Mater Chem. 2012;22(32):16618–26. doi:10.1039/c2jm32415f. [Google Scholar] [CrossRef]
76. Jiang W, Liu Z, Kong Q, Yao J, Zhang C, Han P, et al. A high temperature operating nanofibrous polyimide separator in Li-ion battery. Solid State Ion. 2013;232:44–8. doi:10.1016/j.ssi.2012.11.010. [Google Scholar] [CrossRef]
77. Cao L, An P, Xu Z, Huang J. Performance evaluation of electrospun polyimide non-woven separators for high power lithium-ion batteries. J Electroanal Chem. 2016;767:34–9. doi:10.1016/j.jelechem.2016.01.041. [Google Scholar] [CrossRef]
78. Shayapat J, Chung OH, Park JS. Electrospun polyimide-composite separator for lithium-ion batteries. Electrochim Acta. 2015;170:110–21. doi:10.1016/j.electacta.2015.04.142. [Google Scholar] [CrossRef]
79. Dong GX, Li HJ, Wang Y, Jiang WJ, Ma ZS. Electrospun PAN/cellulose composite separator for high performance lithium-ion battery. Ionics. 2021;27(7):2955–65. doi:10.1007/s11581-021-04073-2. [Google Scholar] [CrossRef]
80. Cho T-H, Tanaka M, Onishi H, Kondo Y, Nakamura T, Yamazaki H, et al. Battery performances and thermal stability of polyacrylonitrile nano-fiber-based nonwoven separators for Li-ion battery. J Power Sources. 2008;181(1):155–60. doi:10.1016/j.jpowsour.2008.03.010. [Google Scholar] [CrossRef]
81. Wang Q, Song W-L, Wang L, Song Y, Shi Q, Fan L-Z. Electrospun polyimide-based fiber membranes as polymer electrolytes for lithium-ion batteries. Electrochim Acta. 2014;132:538–44. doi:10.1016/j.electacta.2014.04.053. [Google Scholar] [CrossRef]
82. Zhang H, Lin C-E, Zhou M-Y, John AE, Zhu B-K. High thermal resistance polyimide separators prepared via soluble precusor and non-solvent induced phase separation process for lithium ion batteries. Electrochim Acta. 2016;187:125–33. doi:10.1016/j.electacta.2015.11.028. [Google Scholar] [CrossRef]
83. Wang H, Wang T, Yang S, Fan L. Preparation of thermal stable porous polyimide membranes by phase inversion process for lithium-ion battery. Polymer. 2013;54(23):6339–48. doi:10.1016/j.polymer.2013.09.036. [Google Scholar] [CrossRef]
84. Angulakshmi N, Stephan AM. Electrospun trilayer polymeric membranes as separator for lithium-ion batteries. Electrochim Acta. 2014;127:167–72. doi:10.1016/j.electacta.2014.01.162. [Google Scholar] [CrossRef]
85. Wu D, Shi C, Huang S, Qiu X, Wang H, Zhan Z, et al. Electrospun nanofibers for sandwiched polyimide/poly (vinylidene fluoride)/polyimide separators with the thermal shutdown function. Electrochim Acta. 2015;176:727–34. doi:10.1016/j.electacta.2015.07.072. [Google Scholar] [CrossRef]
86. Cai M, Yuan D, Zhang X, Pu Y, Liu X, He H, et al. Lithium ion battery separator with improved performance via side-by-side bicomponent electrospinning of PVDF-HFP/PI followed by 3D thermal crosslinking. J Power Sources. 2020;461:228123. doi:10.1016/j.jpowsour.2020.228123. [Google Scholar] [CrossRef]
87. Wu D, Huang S, Xu Z, Xiao Z, Shi C, Zhao J, et al. Polyethylene terephthalate/poly (vinylidene fluoride) composite separator for Li-ion battery. J Phy D: Appl Phy. 2015;48(28):285305. doi:10.1088/0022-3727/48/28/285305. [Google Scholar] [CrossRef]
88. Song K, Pan Y-T, He J, Yang R. Coordination bond cleavage of metal-organic frameworks and application to flame-retardant polymeric materials. Industr Chem Mat. 2024;2(4):556–70. doi:10.1039/D3IM00110E. [Google Scholar] [CrossRef]
89. Hu J, Pan Y-T, Zhou K, Song P, Yang R. A new way to improve the fire safety of polyurethane composites with the assistance of metal-organic frameworks. RSC Appl Poly. 2024;2(6):996–1012. doi:10.1039/D4LP00257A. [Google Scholar] [CrossRef]
90. Chen L, Gong Z, Fu Z. Study on organic fluorine modified cationic acrylic resin and its application in cathodic electrodeposition coatings. J Poly Mate. 2023;40(3–4):157–64. doi:10.32381/JPM.2023.40.3-4.3. [Google Scholar] [CrossRef]
91. Li X, Liu K, Dong N, Liu B, Tian G, Qi S, et al. A dendrite-blocking polyimide-meta-aramid separator with ultrahigh strength and thermostability for high-security lithium-ion battery. Chem Eng J. 2024;481(12):148525. doi:10.1016/j.cej.2024.148525. [Google Scholar] [CrossRef]
92. Sun X, Miao W, Pan Y-T, Song P, Gaan S, Ibarra LH, et al. Metal-organic frameworks: a solution for greener polymeric materials with low fire hazards. Adv Sustain Syst. 2025;9(2):2400768. doi:10.1002/adsu.202400768. [Google Scholar] [CrossRef]
93. Zhang J, Zhang X, Wang R, Wang W, Zhao H, Yang S, et al. Cyclodextrin-based host-guest hierarchical fire retardants: synthesis and novel strategy to endow polylactic acid fire retardancy and UV resistance. Carbohydr Polym. 2024;341:122313. doi:10.1016/j.carbpol.2024.122313. [Google Scholar] [PubMed] [CrossRef]
94. Takenaka N, Bouibes A, Yamada Y, Nagaoka M, Yamada A. Frontiers in theoretical analysis of solid electrolyte interphase formation mechanism. Adv Mater Deerfield. 2021;33(37):2100574. doi:10.1002/adma.202100574. [Google Scholar] [PubMed] [CrossRef]
95. Cheng X-B, Zhang R, Zhao C-Z, Wei F, Zhang J-G, Zhang Q. A review of solid electrolyte interphases on lithium metal anode. Adv Sci. 2016;3(3):1500213. doi:10.1002/advs.201500213. [Google Scholar] [PubMed] [CrossRef]
96. Yang D, Xu P, Xu C, Zhou Q, Liao N. Highly stable silicon oxycarbide all-solid-state batteries enabled by machined learning accelerated screening of oxides and sulfides electrolytes. J Colloid Interface Sci. 2025;677(3):130–9. doi:10.1016/j.jcis.2024.07.200. [Google Scholar] [PubMed] [CrossRef]
97. Lim H-D, Park J-H, Shin H-J, Jeong J, Kim JT, Nam K-W, et al. A review of challenges and issues concerning interfaces for all-solid-state batteries. Energy Storage Mater. 2020;25:224–50. doi:10.1016/j.ensm.2019.10.011. [Google Scholar] [CrossRef]
98. Huo H, Janek J. Solid-state batteries: from ‘all-solid’ to ‘almost-solid’. Natl Sci Rev. 2023;10(6):nwad098. doi:10.1093/nsr/nwad098. [Google Scholar] [PubMed] [CrossRef]
99. Lou S, Zhang F, Fu C, Chen M, Ma Y, Yin G, et al. Interface issues and challenges in all-solid-state batteries: lithium, sodium, and beyond. Adv Mater Deerfield. 2021;33(6):2000721. doi:10.1002/adma.202000721. [Google Scholar] [PubMed] [CrossRef]
100. Zhang Y, Zheng G, Yuan Z, Huang X, Long F, Li Y. Review on interfacial compatibility of solid-state lithium batteries. Ionics. 2023;29(5):1639–66. doi:10.1007/s11581-023-04952-w. [Google Scholar] [CrossRef]
101. Verma P, Maire P, Novák P. A review of the features and analyses of the solid electrolyte interphase in Li-ion batteries. Electrochim Acta. 2010;55(22):6332–41. doi:10.1016/j.electacta.2010.05.072. [Google Scholar] [CrossRef]
102. Zhang J, Zhu J, Zhao R, Liu J, Song X, Xu N, et al. An all-in-one free-standing single-ion conducting semi-solid polymer electrolyte for high-performance practical Li metal batteries. Ener Environ Sci. 2024;17(19):7119–28. doi:10.1039/D4EE02208D. [Google Scholar] [CrossRef]
103. Li H, Zhao H, Liu D, Li Z, Hu Q. Electro-thermal coupling modeling and heat generation decoupling analysis of semi-solid-state lithium-ion battery. Electrochim Acta. 2025;512(1):145455. doi:10.1016/j.electacta.2024.145455. [Google Scholar] [CrossRef]
Cite This Article
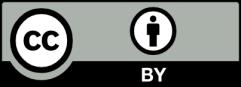
This work is licensed under a Creative Commons Attribution 4.0 International License , which permits unrestricted use, distribution, and reproduction in any medium, provided the original work is properly cited.