Open Access
ARTICLE
Mechanical Performance Analysis of Rubber Elastic Polymer-Polyurethane Reinforced Cement-Based Composite Grouting Materials
1 School of Civil Engineering and Architecture, Zhejiang University of Science and Technology, Hangzhou, 310023, China
2 Zhejiang–Singapore Joint Laboratory for Urban Renewal and Future City, Hangzhou, 310023, China
3 School of Mechanics, Civil Engineering and Architecture, Northwestern Polytechnical University, Xi’an, 710072, China
* Corresponding Authors: Chunhui Cao. Email: ; Xu Long. Email:
Journal of Polymer Materials 2025, 42(1), 255-275. https://doi.org/10.32604/jpm.2025.062081
Received 09 December 2024; Accepted 17 February 2025; Issue published 27 March 2025
Abstract
The ongoing operation of subway systems makes existing tunnels vulnerable to deformations and structural damage caused by adjacent foundation pit construction. Such deformations-manifesting as horizontal displacement, heightened lateral convergence, and internal force redistribution-may significantly compromise subway operational safety. Grouting remediation has become a widely adopted solution for tunnel deformation control and structural reinforcement. Developing optimized grouting materials is crucial for improving remediation effectiveness, ensuring structural integrity, and maintaining uninterrupted subway operations. This investigation explores the substitution of fine mortar aggregates with 0.1 mm discarded rubber particles at varying concentrations (0%, 3%, 6%, 9%, 12%, and 15%). Experimental parameters included three water-cement ratios (0.65, 0.70, and 0.75) with constant 4% WPU content. Mechanical properties including compressive strength, flexural strength, and compression-to-bending ratio were evaluated across specified curing periods. Material characterization employed Fourier Transform Infrared Spectroscopy (FTIR) spectroscopy for molecular analysis and Scanning Electron Microscopy (SEM) for microstructural examination. Results indicate optimal toughness at 0.70 water-cement ratio with 6% rubber content, meeting mechanical pumping specifications while maintaining structural performance.Keywords
China’s underground transit infrastructure development has accelerated significantly in recent years, with subway systems constituting the primary focus of urban rail expansion. However, as the subway systems operate, existing tunnels inevitably experience deformation and damage when disturbed by surrounding foundation pit projects, including horizontal deformation, increased lateral convergence, and changes in internal forces, which can adversely affect the normal operation of the subway when severe [1,2]. This operational challenge has driven critical research into advanced grouting materials development, particularly for enhancing deformation remediation technologies [3,4]. Among emerging solutions, the waterborne polyurethane (PU)-enhanced cement-based materials and rubberized cement matrices are gaining prominence in geotechnical applications owing to their superior mechanical performance and environmental adaptability.
Murali et al. [5] evaluated rubber aggregate substitution in fiber-reinforced grouted aggregate rubberized concrete (FRGARC), testing three water-cement ratios. Their findings revealed an inverse correlation between rubber content and compressive strength, while impact resistance showed marked improvement. Zhu et al. [6] systematically investigated grout performance determinants, identifying optimal parameters at 0.7 water-cement ratio with 70% slag and 30% rubber particle content for balanced flowability and mechanical performance. Jiang et al. [7] developed polyurethane-modified mortar (PUM) with 0.25 mm crumb rubber (0%, 5%, 10%, and 15%), demonstrating optimal mechanical enhancement and pore structure refinement at 5% substitution. Li et al. [8] identified energy dissipation mechanisms in rubber-modified WPU concrete through particle shrinkage/expansion and interfacial friction, significantly improving damping characteristics. Lu et al. [9] formulated a rubberized grouting sealant using porous sand, PVA fibers, and cement, observing direct correlation between rubber content and composite toughness enhancement. Zhu et al. [10] optimized composite formulations through systematic testing (mix design, uniaxial compressive strength tests, permeability) incorporating fly ash, recycled tire rubber, and clay components. Albano et al. [11] documented inverse relationships between workability and both rubber content (%) and particle size reduction in cementitious systems, while Topçu et al. [12] established proportional slump increase with volumetric rubber powder substitution.
Recent advances in polyurethane-modified cementitious systems demonstrate significant performance enhancements. Zheng et al. [13] demonstrated that waterborne polyurethane (WPU) incorporation improves cementitious material flexibility and adhesion, with WPU-only interfacial pretreatment achieving 100% bond strength enhancement. Li et al. [14] developed a WPU-cement hybrid grout using micronized cement, establishing a novel permeability assessment protocol for repair composites. Post-curing evaluations by Hussain et al. [15] revealed 28-day PU-cement composites showing 23%–41% strength increases across compression, flexure, and tension parameters, with exceptional concrete substrate adhesion. Tang et al. [16] introducing cationic polyurethane (PUC) to mitigate early-stage brittleness while enhancing cement matrix ductility. Gadea et al. [17] mixed cement with varying amounts of PU, fine aggregates, and water to produce several grades of mortar. They concluded that increasing the PU content reduces the density and mechanical properties of the mortar but enhances its workability and permeability. Gao et al. [18] further optimized PU-aggregate-cement ratios, demonstrating PU mortar’s 48.9% compressive and 10.9% flexural strength superiority over plain PU-cement systems. Zhang et al. [19] incorporated PU into cement mortar materials, which prevented the propagation of microcracks in the matrix and enhanced the deformability, toughness, and impact resistance of the matrix. Ummin et al. [20] altered the roughness and interface agent of the bond between WPU concrete and cement concrete. They found that the splitting tensile strength of the bonded specimens was consistently positively correlated with the roughness of the bonded interface.
Contemporary research confirms that composite modification with WPU and rubber particulates demonstrates substantial enhancement in cementitious grout performance, particularly in crack mitigation and rheological optimization. Furthermore, no studies have been reported on their application in operational tunnel grouting reinforcement control. This highlights the urgent need for experimental investigations focused on composite materials specifically designed for the operational tunnel environment. This study proposes a PU-rubber enhanced cement-based composite material, using waste rubber particles at varying content levels of 0%, 3%, 6%, 9%, 12%, and 15% to replace fine aggregates in the mortar, with a fixed PU content of 4%. Three water-to-cement ratios (0.65, 0.70, and 0.75) were set, and the mechanical properties of the new cement mortar samples at different curing ages were systematically tested. Based on the experimental results, the mix ratio of the grouting materials was optimized, and the best grouting correction material formulation was determined. This study provides scientific recommendations for material selection and mix ratio optimization in tunnel grouting correction projects.
The experimental matrix comprised four constituent phases: Portland cement (PO 42.5) forming the cementitious base, WPU as the polymeric modifier, 0.1 mm granulated rubber particles serving as the elastomeric reinforcement, and standard quartz sand constituting the fine aggregate fraction.
The PO 42.5 ordinary Portland cement was used in this study. This cement meets the requirements of the standard “General Portland Cement” (GB175-2020). The chemical composition and basic performance indicators of the cement are presented in Tables 1 and 2, respectively.
The WPU used in this study is cationic WPU, distinguished by the incorporation of cationic functional groups, specifically quaternary ammonium salts (−NR4+), into its molecular structure. These cationic groups are introduced during the prepolymer synthesis stage using hydrophilic chain extenders containing cationic moieties, which react with isocyanate groups to form prepolymers. The cationic groups are then neutralized by adding basic substances such as triethanolamine (TEA), leading to the formation of cationic WPU dispersions. The positive charges of the cationic WPU create electrostatic attractions with negatively charged mineral particles in the soil, thereby strengthening the bond between the grout, soil, and tunnel structure. The fundamental properties of the WPU material used in this experiment are presented in Table 3.
Waste tire rubber particles, processed and produced in Chengdu, Sichuan, have a particle size of 0.1 mm, an apparent density of 785 kg/m3, and the chemical composition is shown in Table 4.
Ordinary river sand was used as the fine aggregate, with its grading curve meeting the specifications for natural sand in Zone II. The sand has a fineness modulus of 2.77, a maximum particle size of 2.36 mm, and an apparent density of 2650 kg/m3.
The material property testing instruments used in this experiment include a standard sieve shaker, a cement mortar mixer, a cement mortar vibration table, an electronic balance, a 40 mm × 40 mm × 160 mm standard mold, a temperature-controlled water curing box, a compressive strength testing machine, and a motorized flexural testing machine. The specific instrument parameters and models are listed in Table 5, and photographs of some of the equipment are shown in Fig. 1.
Figure 1: Photographs of test instruments: (a) standard sieve shaker, (b) cement mortar mixer, (c) cement mortar vibrating table, (d) vibration table, (e) cement mortar samples, (f) constant temperature water curing box, (g) electric flexural testing machine, (h) compression testing machine
Research about shield tunnel construction grouting materials shows that slurry performance depends mainly on water-to-binder ratio and binder-to-sand ratio as well as swelling ratio. Research shows that water-to-binder ratio indicates the mass proportion between water and binder material while binder-to-sand ratio describes the ratio between binder content and aggregate material and swelling ratio demonstrates the ratio between bentonite content and water content. Shield tunnel construction practices use grout with water-to-binder ratios between 0.6 to 0.9 while sand-cement ratios exist between 0.45 and 0.75 and swelling ratios remain under 0.4 [21]. The experimental procedures establish mix proportion adjustments following recommended standards which permit the investigation of rubber particle content (rubber particles to fine aggregates mass ratio) with water-to-binder ratio along with WPU content on slurry performance. The experiment applies rubber particles as a substitute for fine aggregates according to replacement ratios of 0%, 3%, 6%, 9%, 12%, and 15% based on two previous studies and scholarly works [22]. The water-to-binder ratio has three defined gradients which measure at ratios of 0.65, 0.70, and 0.75. The researchers adopted 4% WPU as their constant additive level through initial experiments which tested WPU amounts from 2% to 8% because this concentration provided optimal performance for composite materials. A mechanical properties enhancement of 4% WPU outperformed other WPU levels to improve the microstructure quality of these materials. Further investigations about the behavior of composite materials with 4% WPU were conducted as this dosage proved optimal for assessments. Bentonite addition to cement-based materials improves mixture uniformity and construction workability for grouting and filling applications that get benefit from enhanced flowability along with plasticity. Preliminary experiments together with existing literature review [23,24] led the authors to choose a 5% bentonite content as providing adequate performance results without raising production expenses or affecting material properties. The information regarding experimental groups and mix design appears in Table 6.
2.3.2 Mixing and Molding Procedures
Specimen Preparation and Molding Protocol: the dry constituents (cement, fine sand, rubber particles, and bentonite) were precisely weighed and initially blended in dry form. Following 30 s of low-speed mixing, WPU was introduced to the mixture, with continued blending for an additional 30-s interval. Pre-measured experimental water was subsequently incorporated, accompanied by another 30 s of low-speed agitation prior to mixer shutdown. During a 30 s pause in operations, residual materials adhering to the mixer blades and internal surfaces were systematically scraped back into the mixing vessel using a spatula. The mixture underwent final homogenization through 60 s of high-intensity mechanical agitation. Pre-lubricated triple molds (40 mm × 40 mm × 160 mm dimensions) were firmly mounted on the vibrating table. The prepared slurry was deposited in two distinct phases. Approximately 300 g of slurry was rapidly dispensed into each mold cavity. A trowel facilitated even distribution along the mold’s longitudinal axis to ensure complete cavity occupation. Gentle compaction using a smoothing blade enhanced material density while achieving surface planarization, followed by 60 controlled vibration cycles. The second layer of slurry was then added following the same procedure as the first layer. However, during the compaction and spreading of the sample, care was taken to avoid contacting the already compacted slurry. After leveling the second layer, the vibrating table was activated again to vibrate the slurry 60 times. During each vibration, a piece of cotton gauze, wetted with water and wrung dry, was placed over the sample to prevent slurry splatter during the vibration process.
Once the vibration process was complete, the molds were taken off the vibrating table and placed on a flat surface. Any excess slurry on the specimen surface was leveled using a scraper. Beginning at one end of the specimen, the scraper was held at an approximately 90° angle and slightly tilted in the direction of scraping. The scraper was then moved slowly along the specimen’s length in a horizontal sawing motion toward the opposite end. Further leveling was conducted as needed, depending on the slurry requirements. After leveling, a wrung-out damp cloth was used to clean any residual glue mortar from the specimen surface and outer walls. The specimens were subsequently numbered, wrapped in plastic, and allowed to cure for 1 to 2 days before demolding and further curing. Specimens were demolded 1 to 2 days after pouring. Extreme care was taken during the demolding process to prevent specimen damage. Tools like rubber hammers were used to gently extract the specimens from the molds. After removal, the specimens were immediately placed in a curing chamber maintained at 20°C ± 1°C, ensuring full water submersion. During the curing period, up to 50% of the water was replaced as necessary. Upon completing the designated underwater curing duration, the specimens were taken out, marking the end of the specimen preparation process. The specimen preparation process is illustrated in Fig. 2.
Figure 2: Mortar mixing process flowchart
3.1 Properties of Grouting Materials
3.1.1 Infrared Spectroscopy Analysis
The grouting composite materials prepared were analyzed using a Fourier Transform Infrared Spectrometer (Thermo Fisher Scientific Nicolet iS20, Waltham, MA, USA) in attenuated total reflection mode, scanned within the range of 400–4000 cm−1, with a resolution of 4 cm−1 and 32 scans.
In the infrared spectra of samples with different rubber contents, as shown in Fig. 3, a broad peak appears at 3418 cm−1, which corresponds to the stretching vibration of hydroxyl groups in bound water. Additionally, the absorption peak in the range of 3400–3500 cm−1 corresponds to the N-H stretching vibration, a characteristic peak of amino groups in WPU. The absorption peak at 3695 cm−1 is attributed to the stretching vibration of free −OH groups. Studies have shown that hydroxyl groups in WPU form hydrogen bonds with Ca2+ ions in the cement matrix. This hydrogen bonding alters the hydroxyl vibration frequency, leading to shifts in peak position and intensity in the infrared spectrum. This indicates that WPU enhances its bonding strength with the cement matrix, thereby improving the overall mechanical properties of the material. Wang et al. [25] investigated the effect of waterborne epoxy resin on cement-based grouting materials and found that it enhances the interaction between cement particles, thereby increasing both the strength and fluidity of the grouting material. However, this study reveals that WPU not only physically embeds itself within the cement matrix but may also influence the vibration mode of Si-O bonds through chemical crosslinking reactions, thereby enhancing the overall strength and durability of the material. The absorption peak at 533 cm−1 corresponds to the bending vibration of Si-O bonds, which are the primary structural bonds in the cement matrix. The introduction of WPU alters the environment of Si-O bonds in the cement matrix. Through physical embedding or chemical crosslinking, it affects the vibration mode of Si-O bonds, leading to changes in peak position and intensity. This suggests that WPU interacts with Si-O bonds in the cement matrix, thereby enhancing the mechanical properties of the composite material. Lu et al. [9] studied the flowability and mechanical properties of an innovative rubber concrete and found that increasing the rubber content improved toughness but could reduce compressive strength at high concentrations. The distinction of this study lies in maintaining a fixed WPU content while optimizing the rubber substitution ratio to ensure both flowability and excellent mechanical properties. Additionally, the peak at 2920 cm−1 is primarily attributed to the stretching vibration of C-H bonds, associated with the −CH2- and −CH3 groups in WPU. When rubber particles undergo crosslinking reactions with WPU and the cement matrix, the vibration mode of C-H bonds may change, resulting in alterations in peak intensity and position. Similarly, the peak at 1485 cm−1 corresponds to the stretching vibration of C=C bonds, typically associated with unsaturated groups in WPU. Since the unsaturated groups in rubber can undergo copolymerization or crosslinking reactions with those in WPU to form a network structure, this crosslinking alters the vibration mode of C=C bonds, leading to changes in the peak characteristics. The stretching vibration peak of C=O bonds is observed at 1640 cm−1, mainly attributed to the -CONH- groups in WPU. The active groups in rubber (such as carboxyl and amino groups) can chemically react with the -CONH- groups in WPU, forming stronger chemical bonds. This chemical reaction alters the vibration mode of C=O bonds, indicating the formation of an effective crosslinked structure among rubber, WPU, and the cement matrix, thereby improving the overall mechanical properties and durability of the composite material. Compared to the clay-cement composite grouting material proposed by Zhang et al. [26], this study introduces a WPU-rubber reinforced cement-based composite material, optimizing the effects of different water-cement ratios and rubber substitution ratios on material properties, providing scientific guidance for tunnel grouting improvements.
Figure 3: Infrared spectra of cement mortar samples with rubber and WPU incorporation: A1 represents a rubber content of 3%; A3 represents a rubber content of 9%; A5 represents a rubber content of 15%
3.1.2 Scanning Electron Microscope Observation
The surface morphology of the grouting paste specimens was analyzed using a FEI Scios 2 HiVac instrument (USA). The sample preparation process was as follows: cube samples, precisely cut to dimensions of 6 mm × 6 mm × 3 mm, were sequentially labeled and soaked in anhydrous ethanol for 12 h to halt the hydration reaction. The samples were then placed in an electric hot air oven at 60°C for 24 h for drying and dehydration. Given the high insulating properties of cement-based composites, a thin gold film was sputter-coated onto the sample surfaces using a metal sputtering device to enhance electrical conductivity and prevent electron beam charging. The sputtering process lasted 60 s, producing a film thickness of approximately 10 nm. The samples were subsequently mounted onto metal stubs using conductive adhesive. Finally, the vacuum was set to 270 Pa, the accelerating voltage to 15 kV, and the resolution to 1.0 nm before conducting observations.
The scanning electron microscope was operated in low vacuum mode to enhance the interaction between the electron beam and the sample surface while effectively minimizing charge accumulation on the sample surface. During operation, the accelerating voltage was set to 15 kV to allow moderate penetration into the sample’s internal structure while preserving the resolution of surface morphology. The working distance was optimized to 10 mm to enhance image clarity and improve signal collection efficiency. To observe the interface morphology of rubber particles, WPU, and the cement matrix, the magnification was set to 500. During image acquisition, a Secondary Electron Detector was employed to precisely capture the surface morphological features of the samples, ensuring the requirements for microstructural analysis were met. Fig. 4 presents an SEM image of the cement mortar at a localized magnification.
Figure 4: SEM images of the fracture surface of the sample: (a) baseline cement mortar, (b) contains 3% rubber particles, (c) contains 6% rubber particles, (d) contains 9% rubber particles, (e) contains 12% rubber particles, (f) contains 15% rubber particles
As shown in Fig. 4a, the microstructure of the cement mortar indicates that cement particles react with water to form calcium silicate hydrate (C-S-H) gel, leading to a relatively uniform structure. As seen in Fig. 4b–c, the surface of the cement mortar matrix containing rubber particles and WPU is covered with a substantial amount of hydration products, forming a new structural composition. Simultaneously, the polymer membrane structure expands, while the hydration products gradually bridge and integrate with the polymer membrane, increasing the material’s density. This suggests that cohesive forces have formed between the rubber, WPU, and the cement mortar matrix. These cohesive forces contribute to bridging effects during crack propagation and facilitate the formation of a three-dimensional network structure within the cement mortar matrix, significantly enhancing the sample’s flexural toughness. When the rubber content is in the range of 9% to 12%, the porosity of the cement matrix increases significantly, indicating that the excess rubber particles are in a free state within the matrix. Since waste rubber particles are inherently hydrophobic and lack hydrophilic groups on their surface, their interfacial bonding with the cement matrix is relatively weak. As a result, the bonding interface is more susceptible to damage, ultimately leading to a reduction in the overall strength of the mortar. When the rubber content reaches 15%, a large number of foam voids appear inside the specimen, with intact and undamaged edges. These foam voids primarily originate from trace amounts of water remaining on the aggregate surface during the WPU curing process. Additionally, carbon dioxide gas, which was not released in time during the reaction, becomes trapped inside the matrix, forming a pronounced porous structure. This phenomenon is consistent with the findings of Pham et al. [27], who observed that the interfacial bonding strength of rubber-cement composites plays a crucial role in determining the durability and mechanical properties of the material. In particular, enhancing interfacial bonding strength can effectively improve the material’s resistance to chemical erosion, especially in acidic or sulfate-rich environments.
The flowability of grouting materials represents their ability to disperse within tunnel structures, and sufficient flow performance is essential for ensuring compatibility with mechanical pumping requirements. In this study, flowability tests were conducted following the Test Protocol for Polymer-Modified Cement Mortar (DLT5126-2021). This standard outlines specific requirements for testing conditions, operational procedures, and implementation guidelines, making it suitable for assessing the flow performance of WPU rubber-enhanced cement-based grouting materials. The experimental procedure is outlined as follows: First, thoroughly stir the grout until it is uniformly mixed. Pour it into a clean grout mold, filling it up to two-thirds of the mold’s height, and use a steel tamping rod to tamp from the outer edge toward the inner edge 15 times to ensure uniform distribution. Next, continue pouring the grout until it rises 2 cm above the mold, then tamp from the outer edge toward the inner edge 10 times. Then, use a scraper to level the surface and remove any excess grout that has overflowed. Finally, carefully lift the mold, set the tapping frequency to once every 25 s, tap five times in total, and immediately activate the flowability measurement device. Once the tapping process is completed, measure the maximum diameter of the grout in two perpendicular directions using a vernier caliper. The average of these two measurements is recorded as the flowability of the grout. The entire test must be completed within six minutes to maintain accuracy. Field test images are presented in Fig. 5.
Figure 5: Flowability field test experiment diagram: (a) pouring the slurry into the grout mold, (b) measuring the maximum diameter of the grout
Analysis of Fig. 6 indicates that both the water-to-cement ratio and rubber particle content significantly influence the grout’s flow performance. As the water-to-cement ratio increases, the grout’s expansion diameter progressively grows. Specifically, when rubber particles replace 12% of fine aggregates by mass, the expansion diameters for groups C4, B4, and A4 are 263, 246, and 225 mm, respectively, reflecting increases of 16.9% and 9.3% compared to group A4. This occurs because, at a constant rubber content, the water required for hydration and polymer gel reactions remains unchanged. As the water-to-cement ratio rises, the presence of excess non-reactive water creates a lubricating layer between particles, reducing interparticle friction and enhancing grout dispersion and flowability. Additionally, the expansion diameter of the grout shows a “first increasing, then decreasing” trend with respect to the proportion of rubber replacing fine aggregates. At a W/C ratio of 0.70, the expansion diameter of group B2 reaches 248 mm, which is 1.37 and 1.42 times greater than that of groups B0 and B5, respectively. It is inferred that rubber particle incorporation reduces grout viscosity through a lubricating effect and enhances particle distribution uniformity, thereby improving flowability. However, when rubber incorporation exceeds 12%, interparticle friction and agglomeration increase significantly, causing higher grout viscosity and a reduced expansion diameter, which negatively impacts flowability and hinders grout mobility. In summary, when the rubber content is below 3%, the slurry exhibits low flowability, with a spread diameter of less than 220 mm. Conversely, when the rubber content exceeds 12%, viscosity increases sharply, leading to a significant decline in flowability. Tudin et al. [28] found that as the water-binder ratio increases and the replacement rate of rubber particles rises, the fluidity of the slurry improves, but its density, compressive strength, and flexural strength decrease. This study further quantifies the specific impact of the rubber particle replacement rate on the spread diameter of the slurry and indicates that when the replacement rate exceeds 12%, the fluidity of the slurry begins to decline. When rubber particles replace 6% to 12% of fine aggregates, the slurry demonstrates optimal flowability, with a spread diameter of 244–248 mm. This ensures sufficient flowability while preventing excessive slurry viscosity, aligning with industry standards. Compared to other formulations, the B2–B4 groups provide the best balance between flowability and uniformity. Therefore, at a water-to-cement ratio of 0.70, the optimal formulation includes a rubber particle content of 6% to 12%, ensuring compliance with mechanical pumping requirements while maintaining uniform slurry distribution, making it well-suited for practical engineering applications.
Figure 6: Relationship diagram of flowability of composite grout
3.2 Study on the Mechanical Properties of Grouting Materials
Based on the material proportions specified in the design scheme, the required materials are precisely weighed in sequence, thoroughly mixed, compacted, and then poured into 40 mm × 40 mm × 160 mm three-part molds to create specimens for subsequent flexural and compressive strength testing [29]. After molding, the specimens are cured under standard conditions at a temperature of 20 ± 2°C and a relative humidity of ≥95%. Following demolding, the specimens remain under the same curing conditions for predetermined durations of 3, 7, and 28 days. The detailed procedures for specimen molding, preparation, and curing are illustrated in Fig. 7.
Figure 7: Detailed process of specimen molding, preparation, and curing
For each mix ratio of the cement-based samples, three specimens of identical dimensions were prepared for flexural strength testing. Multiple repeated tests were conducted to ensure the reliability of the experimental results and the statistical validity of the data. The final flexural strength values were determined by averaging the results of the three tests and calculating the standard deviation to assess the stability and reproducibility of the test results. The flexural strength of the hardened samples was measured using the DKZ-6000 electric flexural testing machine. The non-cast surface of the specimen was positioned facing upward at the center of the fixture, with a 100 mm span between the two support points. A three-point loading method was employed, with a loading rate of 50 N/s. The final flexural strength of the material was determined using Eq. (1):
Rf=1.5FfL/b3(1)
where Rf is the flexural strength, measured in megapascals (MPa); Ff is the load applied at the center of the prism at the point of fracture, measured in newtons (N); L is the distance between the supporting cylinders, measured in millimeters (mm); and b is the side length of the square cross-section of the prism, also measured in millimeters (mm).
As shown in Fig. 8a–c, after rubber incorporation, the 28-day flexural strength of Groups A and C generally decreases, whereas Group B demonstrates the smallest reduction in flexural strength compared to the baseline mortar and exhibits greater stability. In Group B, specimens with 3% rubber incorporation exhibit flexural strengths of 5.77, 7.13, and 7.31 MPa at 3, 7, and 28 days, respectively, reflecting increases of 3.59%, 21.26%, and 6.56%. This improvement is attributed to PU promoting the formation of cement hydration products. Tang et al. [16] reported that cationic PU enhances cement hydration, likely due to the positive charges in PU adsorbing onto the surfaces of cement particles and hydration products, thereby facilitating reactions between PU, hydration ions, and hydration products. Additionally, a small amount of rubber powder exhibits excellent deformation properties. The incorporation of rubber powder reduces the matrix rigidity and enhances its deformation capacity, thereby improving flexural strength [30]. When the rubber incorporation reaches 12%, the material’s flexural strengths at 3, 7, and 28 days are 4.92, 5.45, and 6.53 MPa, respectively, corresponding to reductions of 11.67%, 7.31%, and 4.81% compared to the reference mortar without rubber. The incorporation of PU has, to some extent, enhanced the slurry’s elasticity and crack resistance. However, an excessive amount of rubber particles replaces a significant portion of the effective aggregate in the cement matrix, hindering the cement hydration reaction and thus restricting the material’s early strength development. This observation aligns with the findings of Grinys et al. [31]. Although strength limitations exist, this study has successfully enhanced the crack resistance of cement slurry and identified an optimal rubber incorporation level and mix ratio. The optimal water-to-cement ratio is 0.70, with an ideal rubber particle content between 3% and 9%. Additionally, Turatsinze et al. [32] studied the synergistic effect of rubber particles and steel fibers, finding that their combination enhances the crack resistance of cement mortar. This study further validates the reinforcing effect of WPU combined with rubber particles and analyzes the flexural strength under different water-to-cement ratios, selecting an optimal grouting material suitable for tunnel reinforcement applications. Haruna et al. [33] investigated the role of WPU grouting materials in concrete repair and found that WPU exhibits excellent fluidity and mechanical properties. However, their study did not explore the composite reinforcing effect of rubber particles and WPU. In contrast, this study focuses on the grouting reinforcement requirements of tunnel engineering, proposing an optimized mix ratio for WPU-rubber reinforced cement-based composites, providing a scientific basis for practical engineering applications.
Figure 8: Flexural strength values at different curing ages: (a) flexural strength values of specimens with a water-to-cement ratio of 0.65 at 3 d, 7 d, and 28 d curing ages, (b) flexural strength values of specimens with a water-to-cement ratio of 0.70 at 3 d, 7 d, and 28 d curing ages, (c) flexural strength values of specimens with a water-to-cement ratio of 0.75 at 3 d, 7 d, and 28 d curing ages
The strength of grouting materials is closely linked to their permeability resistance, durability, and aging resistance. High compressive strength directly influences the performance and effectiveness of grouting materials [34–36]. The compressive strength test is conducted in strict accordance with the Cement Mortar Strength Test Method (ISO Method) (GB/T17671-2021). After curing to the designated testing age, the three fractured blocks from the flexural strength test are retained for compressive strength testing. The non-cast surface of each fractured block is positioned as the compressed face in the compressive testing fixture, with a loading rate of 2400 ± 200 N/s applied continuously and uniformly until the specimen reaches complete failure. The compressive strength test results are presented in Fig. 9. The final compressive strength of the material is determined using Eq. (2):
Rc=Fc/A(2)
where Rc is the compressive strength, measured in megapascals (MPa); Fc is the maximum load at failure, measured in newtons (N); and A is the loaded area, measured in square millimeters (mm2).
Figure 9: Compressive strength values at different curing ages: (a) compressive strength values of samples with a water-to-cement ratio of 0.65 at 3 d, 7 d, and 28 d, (b) compressive strength values of samples with a water-to-cement ratio of 0.70 at 3 d, 7 d, and 28 d, (c) compressive strength values of samples with a water-to-cement ratio of 0.75 at 3 d, 7 d, and 28 d
As shown in Fig. 9a,c, when the rubber content ranges from 9% to 15%, the compressive strength decreases significantly. This occurs because at higher rubber contents, rubber particles fail to establish effective chemical bonds with cement hydration products, leading to weak interfacial bonding and, consequently, a decline in the material’s mechanical properties. This finding aligns with previous studies, which indicate that as rubber content increases, adhesion between cement mortar and rubber particles weakens, ultimately reducing compressive strength [37]. The incorporation of rubber particles can indeed result in a slight reduction in compressive strength. This is attributed to the “softening” effect introduced by rubber particles, which causes the material to undergo greater deformation under compressive loads. However, this does not mean that the incorporation of rubber lacks practical benefits. On the contrary, rubber particles substantially enhance the material’s toughness. Moreover, the presence of rubber particles improves the composite material’s impact resistance and energy absorption capacity. A study by Li et al. [8] found that rubber incorporation significantly enhances the damping ratio of WPU cement-based composites. In practical applications, rubber particles can effectively absorb energy when materials experience external impacts or vibrations, thereby minimizing crack formation and propagation and extending the material’s service life. This effect is especially prominent under dynamic loads or extended fatigue loading conditions. While rubber particles may slightly reduce flexural strength, this trade-off is generally acceptable, as the advantages of improved toughness and energy absorption outweigh the drawbacks. In Group B, the water-to-cement ratio ensures adequate cement hydration, maintaining a balanced chemical reaction between rubber particles and the cement matrix, which facilitates the formation of cement hydration products. Therefore, the water-to-cement ratio in Group B is optimal for improving the performance of cement-based materials.
In Group B, samples with 3% rubber content exhibited compressive strengths of 31.87, 33.88, and 34.51 MPa at 3, 7, and 28 days, respectively, reflecting increases of 18.56% and 33.97% at 3 and 7 days, followed by a 7.21% decrease at 28 days. This is attributed to the moderate incorporation of rubber particles, which enhanced the material’s toughness and crack resistance when combined with the cement matrix. However, over time, the rubber particles inhibited the cement hydration reaction, and alterations in the internal structure of the material resulted in a decrease in compressive strength. When the rubber content reached 9%, the compressive strength at 28 days was only 32.58 MPa, representing a 12.40% reduction compared to the reference mortar without rubber. At a 9% rubber content, the rubber particles occupied a greater volume, restricting the formation of cement hydration products. This inhibition constrained the strength development of the cement matrix, ultimately causing a reduction in compressive strength. Excessive rubber content results in weak interfacial bonding between rubber particles and the cement matrix, leading to an irregular internal structure and a decline in compressive strength, findings that align closely with Jiang’s research [38]. In conclusion, while some compressive strength is sacrificed, the large-scale use of waste rubber remains feasible and continues to meet specific engineering requirements [39]. Thus, the optimal water-to-cement ratio is 0.70, with a rubber particle content ranging from 3% to 6%.
Ordinary cement mortar is mostly a heterogeneous brittle material, with defects such as poor toughness and insufficient bonding strength. When a material is able to adapt well to deformation, it indicates that the material has excellent toughness. Currently, toughness of materials is evaluated using indicators such as the compressive-to-flexural strength ratio (crush-to-bend ratio), elastic modulus, and impact toughness. This study primarily uses the compressive-to-flexural strength ratio to investigate the material’s flexibility. The compressive-to-flexural strength ratio is the ratio of compressive strength to flexural strength under static load. The magnitude of the ratio can characterize the amount of deformation caused when the specimen fails under load. The smaller the ratio, the better the material’s flexibility [40,41].
As illustrated in Fig. 10, the compression ratio of Group A mortar gradually increases as the rubber content rises, indicating a decrease in mortar flexibility with rubber incorporation. In contrast, the compression ratios of Group B and Group C mortar remain stable, with Group B displaying an overall decreasing trend, suggesting that mortar materials with this water-cement ratio exhibit enhanced ductility and superior mechanical properties. In Group B, the compression ratios of mortar with 3% rubber content at 3, 7, and 28 days were 4.27, 4.29, and 4.55, respectively, reflecting reductions of 22.48%, 20.11%, and 19.18%. When the rubber content increased to 9%, the compression ratios at 3, 7, and 28 days rose to 4.55, 4.63, and 4.71, representing increases of 6.56%, 7.93%, and 3.52% compared to the mortar with 3% rubber. In Group B materials, the compression ratio increased significantly after the addition of 9% rubber particles, suggesting that the hydrophobic nature of rubber particles and the hydrophilic properties of cement hydration products lead to weak interfacial bonding. This effect becomes more pronounced at higher rubber contents, where the interfacial bonding between rubber particles and cement hydration products is notably weak. Liu et al. [42] conducted X-ray diffraction analysis to examine the effect of rubber dosage on cement mortar hydration reactions. The results revealed that with increasing rubber content, the levels of C3S, C2S, C3A, and C4AF in the rubber concrete samples gradually increased. Conversely, the concentration of Ca(OH)2 and amorphous substances progressively declined. These findings suggest that rubber incorporation partially suppressed the cement hydration reaction, leading to a slight reduction in material toughness. Therefore, the optimal water-cement ratio is 0.70, with a rubber particle content ranging from 3% to 6%, ensuring both mechanical performance and enhanced toughness. This provides a scientific basis for material selection and mix ratio optimization in tunnel grouting reinforcement projects.
Figure 10: Compression ratio at different curing ages: (a) compression ratio of samples with a water-to-cement ratio of 0.65 at 3 d, 7 d, and 28 d, (b) compression ratio of samples with a water-to-cement ratio of 0.70 at 3 d, 7 d, and 28 d, (c) compression ratio of samples with a water-to-cement ratio of 0.75 at 3 d, 7 d, and 28 d
This study seeks to address the existing shortcomings in the mechanical performance evaluation of WPU and rubber-enhanced cement-based grouting composites. The following conclusions have been drawn:
(1) Flowability test results indicate that with a water-cement ratio of 0.70 and a rubber particle content of 6% to 12%, the grout achieves a flow diameter of 244–248 mm, satisfying the mechanical pumping and crack-filling requirements for tunnel reinforcement projects.
(2) According to the flexural strength test results, the optimal water-cement ratio for the grouting material is 0.70, with a rubber particle content ranging from 3% to 9%. The compressive strength test results also confirm that the optimal water-cement ratio remains 0.70, with a rubber particle content of 3% to 6%. Likewise, compression ratio test results indicate that the most suitable water-cement ratio is 0.70 with a rubber content of 3% to 6%.
(3) The ideal mix ratio for the grouting material is a water-cement ratio of 0.70 and a rubber particle content of 6%, which improves the material’s flexibility while ensuring good mechanical properties and overall stability.
Acknowledgement: The authors like to express the deepest gratitude and appreciation for the assistance and support received throughout the completion of this research paper.
Funding Statement: This work was supported by the National Natural Science Foundation of China, Grant Nos. 42477185, 41602308, the Zhejiang Provincial Natural Science Foundation of China, Grant No. LY20E080005, the Zhejiang Province University Students Science and Technology Innovation Program, Grant No. 0201310P28, the PostGraduate Course Construction Project of Zhejiang University of Science and Technology, Grant No. 2021yjskj05, and the Zhejiang University of Science and Technology Graduate Research and Innovation Fund, Grant No. 2023yjskc10.
Author Contributions: The authors confirm contribution to the paper as follows: study conception and design: Baoping Zou, Jiahao Yin, Xu Long; data collection: Jiahao Yin; analysis and interpretation of results: Baoping Zou, Jiahao Yin, Chunhui Cao; draft manuscript preparation: Jiahao Yin, Xu Long. All authors reviewed the results and approved the final version of the manuscript.
Availability of Data and Materials: The data that support the findings of this study are available from the corresponding author.
Ethics Approval: Not applicable.
Conflicts of Interest: The authors declare no conflicts of interest to report regarding the present study.
References
1. Chen Y, Tao J, Zhou J, Yao H, Zhang W, Deng Y. Quantitative evaluation of driver's distance and speed perception characteristics in tunnel and safety facility optimization. J Imaging Sci Technol. 2023;67(4):1–8. doi:10.2352/J.ImagingSci.Technol.2023.67.4.040405. [Google Scholar] [CrossRef]
2. Zou B, Yin J, Liu Z, Long X. Transient rock breaking characteristics by successive impact of shield disc cutters under confining pressure conditions. Tunn Undergr Space Technol. 2024;150:105861. doi:10.1016/j.tust.2024.105861. [Google Scholar] [CrossRef]
3. Long X, Mao M, Su T, Su Y, Tian M. Machine learning method to predict dynamic compressive response of concrete-like material at high strain rates. Defence Technol. 2023;23:100–11. doi:10.1016/j.dt.2022.02.003. [Google Scholar] [CrossRef]
4. Long X, Mao M, Lu C, Li R, Jia F. Modeling of heterogeneous materials at high strain rates with machine learning algorithms trained by finite element simulations. J Micromech Mol Phys. 2021;6(1):2150001. doi:10.1142/S2424913021500016. [Google Scholar] [CrossRef]
5. Murali G, Poka L, Parthiban K, Haridharan MK, Siva A. Impact response of novel fibre-reinforced grouted aggregate rubberized concrete. Arab J Sci Eng. 2019;44(10):8451–63. doi:10.1007/s13369-019-03819-5. [Google Scholar] [CrossRef]
6. Zhu X, Zhang W, Wang Y, Lv W, Ma C. Diffusion mechanism of solid waste product utilization pulping and fracture network grouting. Constr Build Mater. 2023;408(6):133571. doi:10.1016/j.conbuildmat.2023.133571. [Google Scholar] [CrossRef]
7. Jiang W, Zhu H, Haruna SI, Zhao B, Shao J, Yu Y. Effect of crumb rubber powder on mechanical properties and pore structure of polyurethane-based polymer mortar for repair. Constr Build Mater. 2021;309(3):125169. doi:10.1016/j.conbuildmat.2021.125169. [Google Scholar] [CrossRef]
8. Li C, Zhang W, Sun G, Li Y, Zhang Y. Research on damping properties and microscopic mechanism of polyurethane cement-based composites. Constr Build Mater. 2023;365(3):130137. doi:10.1016/j.conbuildmat.2022.130137. [Google Scholar] [CrossRef]
9. Lu Y, Li C, Zhang X, Huang X, Zhao Z. A workability characterization of innovative rubber concrete as a grouting material. Materials. 2022;15(15):5319. doi:10.3390/ma15155319. [Google Scholar] [PubMed] [CrossRef]
10. Zhu X, Zhang Q, Zhang W, Shao J, Wang Z, Wu X. Experimental study on the basic properties of a green new coal mine grouting reinforcement material. ACS Omega. 2020;5(27):16722–32. doi:10.1021/acsomega.0c01626. [Google Scholar] [PubMed] [CrossRef]
11. Albano C, Camacho N, Reyes J, Feliu JL, Hernández M. Influence of scrap rubber addition to Portland I concrete composites: destructive and non-destructive testing. Compos Struct. 2005;71(3):439–46. doi:10.1016/j.compstruct.2005.09.037. [Google Scholar] [CrossRef]
12. Topçu İ.B, Sarıdemir M. Prediction of rubberized concrete properties using artificial neural network and fuzzy logic. Constr Build Mater. 2008;22(4):532–40. doi:10.1016/j.conbuildmat.2006.11.007. [Google Scholar] [CrossRef]
13. Zheng H, Pang B, Jin Z, Liu S, Zhang Y, Bi J, et al. Mechanical properties and microstructure of waterborne polyurethane-modified cement composites as concrete repair mortar. J Build Eng. 2024;84:108394. doi:10.1016/j.jobe.2023.108394. [Google Scholar] [CrossRef]
14. Li C, Bai J, Jiang Y, Xiao H, Wang W, Xu F. Investigating the seepage control and plugging capabilities of polyurethane-cement composites: a comprehensive study on material properties. Constr Build Mater. 2024;416(41):135191. doi:10.1016/j.conbuildmat.2024.135191. [Google Scholar] [CrossRef]
15. Hussain HK, Liu G, Yong Y. Experimental study to investigate mechanical properties of new material polyurethane-cement composite (PUC). Constr Build Mater. 2014;50(5):200–8. doi:10.1016/j.conbuildmat.2013.09.035. [Google Scholar] [CrossRef]
16. Tang J, Liu J, Yu C, Wang R. Influence of cationic polyurethane on mechanical properties of cement based materials and its hydration mechanism. Constr Build Mater. 2017;137(12):494–504. doi:10.1016/j.conbuildmat.2016.12.162. [Google Scholar] [CrossRef]
17. Gadea J, Rodríguez A, Campos PL, Garabito J, Calderón V. Lightweight mortar made with recycled polyurethane foam. Cement Concr Compos. 2010;32(9):672–7. doi:10.1016/j.cemconcomp.2010.07.017. [Google Scholar] [CrossRef]
18. Gao H, Liu L, Yang W, Dong Y, Liu H. Experimental study on mechanical properties of polyurethane-based composites. Case Stud Constr Mater. 2024;21:3907. doi:10.1016/j.cscm.2024.e03907. [Google Scholar] [CrossRef]
19. Zhang X, Fang H, Du M, Shi M, Zhang C. Experimental study on the mechanical properties of the fiber cement mortar containing polyurethane. Adv Mater Sci Eng. 2021;2021(1):1. doi:10.1155/2021/9956897. [Google Scholar] [CrossRef]
20. Ummin O, Li Y, Li K, Chen Y, Jia H, Zuo J. Influence of surface roughness and interfacial agent on the interface bonding characteristics of polyurethane concrete and cement concrete. J Build Eng. 2024;91:109596. doi:10.1016/j.jobe.2024.109596. [Google Scholar] [CrossRef]
21. Wang T, Hong J, Liao C, Liu J. Experimental research of rubberized concrete. Concrete. 2009; 2009(1):67–9. doi:10.3969/j.issn.1002-3550.2009.01.019. [Google Scholar] [CrossRef]
22. Zheng H, Pang B, Jin Z, Zhang Y, Hou D, Bi J, et al. Durability enhancement of cement-based repair mortars through waterborne polyurethane modification: experimental characterization and molecular dynamics simulations. Constr Build Mater. 2024;438:137204. doi:10.1016/j.conbuildmat.2024.137204. [Google Scholar] [CrossRef]
23. Malusis MA, McKeehan MD. Chemical compatibility of model soil-bentonite backfill containing multiswellable bentonite. J Geotech Geoenviron Eng. 2013;139(2):189–98. doi:10.1061/(ASCE)GT.1943-5606.0000729 2013/1/1. [Google Scholar] [CrossRef]
24. Zhang Z, Zhang C, Chen W, Li Q. Effect of bentonite mineral on properties of basalt fiber cementitious materials. Non-Metallic Mines. 2021;44(6):23–5. doi:10.3969/j.issn.1000-8098.2021.06.006. [Google Scholar] [CrossRef]
25. Wang Y, Wu J. Effects of polymer-curing agent ratio on rheological, mechanical properties and chemical characterization of epoxy-modified cement composite grouting materials. Polymers. 2024;16(18):2665. doi:10.3390/polym16182665. [Google Scholar] [PubMed] [CrossRef]
26. Zhang C, Yang J, Fu J, Ou X, Xie Y, Dai Y, et al. A new clay-cement composite grouting material for tunnelling in underwater karst area. J Cent South Univ. 2019;26(7):1863–73. doi:10.1007/s11771-019-4140-5. [Google Scholar] [CrossRef]
27. Pham N, Toumi A, Turatsinze A. Evaluating damage of rubberized cement-based composites under aggressive environments. Constr Build Mater. 2019;217(3–4):234–41. doi:10.1016/j.conbuildmat.2019.05.066. [Google Scholar] [CrossRef]
28. Tudin DZA, Rizalman AN. Effect of water-cement ratio on the properties of naoh-treated rubberized mortar. Key Eng Mater. 2020;6060:135–9. doi:10.4028/www.scientific.net/KEM.862.135. [Google Scholar] [CrossRef]
29. Mamallan S, Narayanan V, Ragothaman CB. Quasi-static and low-frequency dynamic mechanical analysis characterization of graphene nanoplatelets/glass fabric/bisphenol-a-based epoxy nanocomposites. J Polym Mater. 2024;41(3):105–16. doi:10.32604/jpm.2024.056744. [Google Scholar] [CrossRef]
30. Pi YL, Zhang WH, Zou WT, Zhang YS. Study on the mechanical behaviors and failure mechanism of polyurethane cement composites under uniaxial compression and tension. Arch Civ Mech Eng. 2022;22(1):18. doi:10.1007/s43452-021-00342-z. [Google Scholar] [CrossRef]
31. Grinys A, Balamurugan M, Augonis A, Ivanauskas E. Mechanical properties and durability of rubberized and glass powder modified rubberized concrete for whitetopping structures. Materials. 2021;14(9):2321. doi:10.3390/ma14092321. [Google Scholar] [PubMed] [CrossRef]
32. Turatsinze A, Granju JL, Bonnet S. Positive synergy between steel-fibres and rubber aggregates: effect on the resistance of cement-based mortars to shrinkage cracking. Cem Concr Res. 2006;36(9):1692–7. doi:10.1016/j.cemconres.2006.02.019. [Google Scholar] [CrossRef]
33. Haruna SI, Ibrahim YE, Han Z, Farouk AIB. Flexural response of concrete specimen retrofitted with PU grout material: experimental and numerical modeling. Polymers. 2023;15(20):4114. doi:10.3390/polym15204114. [Google Scholar] [PubMed] [CrossRef]
34. Long X, Su T, Lu C, Wang S, Huang J, Chang C. An insight into dynamic properties of sac305 lead-free solder under high strain rates and high temperatures. Int J Impact Eng. 2023;175(3):104542. doi:10.1016/j.ijimpeng.2023.104542. [Google Scholar] [CrossRef]
35. Long X, Hu Y, Su T, Iyela PM, Su Y, Yan W, et al. Thermomechanical constitutive behaviour of 3D printed biomimetic polymer material under high strain rates. Polym Test. 2024;134(6):108439. doi:10.1016/j.polymertesting.2024.108439. [Google Scholar] [CrossRef]
36. Manda M, Mrbm R, Sa H, Wahit M, Binoj J, Mansingh B, et al. Tin slag polymer concrete strengthening by basalt and aramid fiber reinforced polymer confinement. J Polym Mater. 2023;39(3–4):241–53. doi:10.32381/JPM.2022.39.3-4.5. [Google Scholar] [CrossRef]
37. Kang JF, Yan CX. Correlation of strength, rubber content, and water-cement ratio in roller compacted rubberized concrete. Adv Mater Res. 2011;243–249:1179–85. doi:10.4028/www.scientific.net/AMR.243-249.1179. [Google Scholar] [CrossRef]
38. Jiang Z, Tang C, Yang J, You Y, Lv Z. A lab study to develop polyurethane concrete for bridge deck pavement. Int J Pavement Eng. 2022;23(5):1404–12. doi:10.1080/10298436.2020.1804063. [Google Scholar] [CrossRef]
39. Ma H, Hu F, Ma J, Dong D. Experimental investigation on effect of particle size and dosage of rubber on mechanical properties of mortar. Sci Technol Eng. 2019;19(4):232–6. doi:10.3969/j.issn.1671-1815.2019.04.037. [Google Scholar] [CrossRef]
40. Yan J, Gao Y, Tang M, Ding N, Xu Q, Peng M, et al. Experimental study on the mechanical properties of recycled spiral steel fiber-reinforced rubber concrete. Buildings. 2024;14(4):897. doi:10.3390/buildings14040897. [Google Scholar] [CrossRef]
41. Jeemol PA, Mathew S, Reghunadhan Nair CP. Toughening of unsaturated polyester resin by blending with polyether telechelics. Dependency of toughening efficacy on end groups. J Polym Mater. 2022;39(1–2):111–20. doi:10.32381/JPM.2022.39.1-2.7. [Google Scholar] [CrossRef]
42. Liu L, Wang C, Liang Q, Chen F, Zhou X. A state-of-the-art review of rubber modified cement-based materials: cement stabilized base. J Clean Prod. 2023;392(5):136270. doi:10.1016/j.jclepro.2023.136270. [Google Scholar] [CrossRef]
Cite This Article
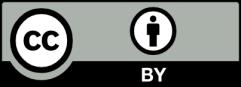
This work is licensed under a Creative Commons Attribution 4.0 International License , which permits unrestricted use, distribution, and reproduction in any medium, provided the original work is properly cited.