Open Access
ARTICLE
Electroless Deposition of Cu Using Dopamine as Flexible Conductive Materials
College of Mechanical Engineering, University of South China, Hengyang, 421001, China
* Corresponding Author: Zhitao Hu. Email:
Journal of Polymer Materials 2025, 42(1), 125-140. https://doi.org/10.32604/jpm.2024.059636
Received 13 October 2024; Accepted 25 November 2024; Issue published 27 March 2025
Abstract
With the rapid development of flexible wearable electronic products, their application fields and demands are increasing, posing new challenges to flexible conductive materials. This paper selected flexible polydimethylsiloxane (PDMS) as the substrate. In order to enhance the adhesion between the substrate and the metal coating, dopamine and silanization were used to co-modify its surface. A conductive layer of metallic copper is deposited on its surface using an inexpensive, easy-to-use electroless plating technique. By optimizing the process conditions, it is found that a uniform copper layer of about 0.6 μm can be formed on the surface of the substrate by electroless plating at a constant temperature of 45°C for 30 min with a conductivity of 5556 S/cm. The relative resistance changes under different deformation conditions, and the I-V curve of the LED circuit is not very different. Therefore, this paper prepared a flexible conductor with excellent electrical conductivity, high coating adhesion, and good electrical stability under large-scale deformation.Keywords
The field of polymer materials has seen a significant expansion in recent years, with polydimethylsiloxane (PDMS) emerging as a key player due to its unique properties such as biocompatibility, flexibility, and chemical stability [1]. PDMS has found applications in various domains, including microfluidics, sensors, and energy storage devices. However, the inherent hydrophobicity and non-stick nature of PDMS pose challenges for its direct use in certain applications, particularly those requiring adhesive properties or electrical conductivity [2]. To address these limitations, surface modification techniques have been developed to enhance PDMS functionality [3,4].
In this study, we focus on the modification of PDMS substrates to improve their adhesive and conductive properties through a series of chemical treatments. The literature has shown that dopamine-based surface modification can render PDMS surfaces more hydrophilic and adhesive. Furthermore, the introduction of silane coupling agents, such as aminopropyltriethoxysilane (APTES), has been demonstrated to enhance the surface’s adhesion and bonding strength. The combination of these modifications with metal deposition, specifically copper and copper-palladium alloy, has been explored for applications in flexible electronics and conductive interconnects.
The preparation process of PDMS substrates involves multiple steps, including cleaning, surface activation, and metal deposition. Ultrasonic cleaning in absolute ethanol and water is a common preliminary step to remove any contaminants from the PDMS surface. The use of Tris-HCl buffer with dopamine allows for the formation of a polydopamine layer on the PDMS surface, which can then be further functionalized with APTES. This process not only improves the surface’s hydrophilicity but also introduces amine groups that can complex with metal ions, facilitating subsequent metal deposition.
The literature also highlights the importance of silver activation in the metal deposition process. Silver ions have been used as catalysts for the reduction of metal ions and the growth of metal nanoparticles on modified PDMS surfaces [5]. Two common silver activators are employed in this study: one based on silver nitrate and another utilizing polyvinylpyrrolidone (PVP) as a stabilizing agent. These activators are crucial for the uniform deposition of copper and the subsequent formation of a copper-palladium alloy, which enhances the electrical conductivity and durability of the PDMS substrates.
The electrochemical performance of the modified PDMS substrates is evaluated through oxygen evolution reaction (OER) and methanol oxidation reaction (MOR) tests. These tests are essential for assessing the catalytic activity of the metal-deposited PDMS surfaces. Additionally, the mechanical flexibility and electrical conductivity of the copper-plated PDMS are tested under various deformation conditions, which is critical for applications in flexible electronics and wearable devices [6,7].
This paper presents a comprehensive study on the modification and characterization of PDMS substrates for enhanced adhesive and conductive properties. The results contribute to the understanding of PDMS surface modification and its implications in the development of flexible and functional polymer materials [8].
2 Materials and Experimental Section
Polydimethylsiloxane (PDMS, 0.65 cSt (25°C), Aladdin, Shanghai, China), copper sulfate pentahydrate (CuSO4· 5H2O, ≥98.0%, Aladdin), formaldehyde (HCHO, ≥98.0%, Aladdin), disodium EDTA dihydrate (C10H14N2Na2O8·2H2O, ≥99.0%, Aladdin), sodium hydroxide (NaOH, ≥98.0%, Macklin, Shanghai, China), ethylene glycol (C2H6O2, ≥98.%, Aladdin), methanol (CH3OH, ≥99.5%, Aladdin), ethanol (C2H5OH, ≥99.5%, Aladdin), sodium borohydride (NaBH4, ≥98.0%, Aladdin), ammonium persulfate, ((NH4)2S2O8, ≥98.0%, Aladdin) polyvinylpyrrolidone K30 ((C6H9NO)n, Aladdin), tris(hydroxymethyl) aminomethane (C4H11NO3, ≥99.9%, Aladdin), dopamine hydrochloride (C8H12ClNO2, ≥98%, Aladdin), (3-Aminopropyl)triethoxysilane (C9H23NO3Si, ≥99.9%, Aladdin), potassium sodium tartrate tetrahydrate (C4H4O6KNa·4H2O, ≥99.9%, Aladdin), hydroxide potassium (KOH, ≥95.0%, Macklin), silver nitrate (AgNO3, ≥99.0%, Aladdin).
2.2 Experimental Instruments and Test Instructions
The experimental equipment used in this study, along with their manufacturers and model numbers, are listed in Table 1.
Scanning Electron Microscope (SEM)
Scanning electron microscope is the main instrument for microstructure analysis. It is often combined with energy dispersive X-ray spectroscopy (EDS) for elemental analysis and is widely used in materials, metallurgy, mineralogy and biology. In this study, a field emission scanning electron microscope (SU70) produced by Hitachi was used, along with an accompanying X-ray spectrometer, to analyze the surface morphology, coating thickness and element content of the material. In order to prevent the local charge caused by poor sample conductivity from affecting the secondary electron imaging, all test samples were sprayed with gold before the test, and the processing time was 60 s.
X-ray Diffractometer (XRD)
The X-ray diffractometer is mainly used for phase identification and can accurately determine the crystal structure of materials. This study used the SmartLab series multi-function X-ray diffractometer from Rigaku Corporation, with a testing angle range of 10° to 90° and a testing speed of 10°/min, to analyze whether metallic silver particles were produced after plasma treatment during the silver ion catalysis stage under a focused beam.
Fourier Transform Infrared Spectrometer (FT-IR)
The Fourier Transform Infrared Spectrometer is a non-dispersive infrared absorption spectrometer, and infrared spectroscopy is mainly used for qualitative analysis of chemical bonds and functional groups in molecules, also known as molecular vibration-rotation spectra. This study used a Fourier Transform Infrared Spectrometer (Nicolet 6700) produced by Thermo Fisher Scientific, mainly to compare the changes in vibration peak positions and heights in the infrared spectra before and after dopamine and silane modification of the PDMS substrate, and to analyze the grafting situation of functional groups.
Contact Angle Meter
The contact angle meter is mainly used to measure the contact angle between liquids and solids to evaluate the wetting performance of the solid interface to the liquid. In this study, a contact angle meter (CSCDIC-350) manufactured by Dongguan Shengding Precision Instrument Co., Ltd. was used. By adding 6 μL of deionized water droplets to the PDMS substrate interface and observing and measuring the angle between the droplet and the solid interface after the droplet stabilizes, the change in hydrophilicity of the material before and after dopamine modification was tested.
Adhesion Tester
The adhesion tester, also known as the cross-cut tester, is manufactured according to ISO2409-1992 and is suitable for GB/T9286-98, BS 3900E6/ASTM D3359. The tape used is the Scotch600 series produced by 3M Company. In this study, the coating was grid-patterned and penetrated to evaluate the adhesion effect of the coating separation from the PDMS substrate, thereby assessing the changes in adhesion before and after dopamine and silane modification.
Electrical and Electrochemical Performance Testing
The insulation resistance tester used in this study is the VC480C+ series tester produced by Shenzhen WeiXite Technology Co., Ltd., which is used to measure the change in relative resistance under different stretching conditions. The four-point probe surface resistivity tester produced by Signatone was used to determine the sheet resistance and conductivity of the PDMS substrate after chemical copper plating. Subsequently, the CHI600E series electrochemical workstation produced by Shanghai Chenhua Instruments Co., Ltd. was used to test its electrochemical performance under different conditions of oxygen evolution reaction (OER) and methanol electrocatalytic oxidation (MOR), as well as the I-V characteristic curves of the LED circuit under different bending angles. During the electrochemical performance testing, a Cu-PDMS electrode (working electrode), a platinum plate (counter electrode), and a Hg/HgO electrode (1M KOH solution) [reference electrode] were used as a conventional three-electrode system, and a 0.5 M/L methanol solution and a 1 M/L potassium hydroxide solution without methanol were used as the electrolyte, respectively.
The PDMS prepolymer and curing agent were thoroughly mixed in a weight ratio of 10:1 and put into a vacuum desiccator to degas to remove air bubbles, and then the mixture was dropped into pre-cleaned polypropylene plates and sugar cubes and spin-coat on the screw groove, and then carry out the second degassing treatment to remove the bubbles generated again during the transfer process, and let it stand at room temperature for half an hour, then put it into an oven at 80°C for more than 2 h, and after it is fully cured, carefully peel off the PDMS film and spiral PDMS, and dissolve the sugar cubes in deionized water. Finally, the fabricated PDMS substrate is cut into the desired size to obtain PDMS flat film, spring-like PDMS, and sponge-like PDMS. The specific preparation process is shown in Fig. 1 below.
Figure 1: Schematic diagram of the preparation process of PDMS substrate (a) PDMS flat film; (b) sponge PDMS; (c) spring PDMS
The PDMS prepolymer and curing agent are fully mixed with a mass ratio of 10:1 and then put into the vacuum dryer for the first step of vacuuming to remove the bubbles in the PDMS mixture. Then the mixture is dropped onto the pre-cleaned polypropylene plate, sugar block and screw groove [9], and the second step is to vacuum and stand at room temperature for half an hour for the second degassed treatment, to remove the bubbles generated again during the transfer process, and then bake in the oven at 80°C for more than 2 h, after it is fully cured. The PDMS film and spiral PDMS were carefully removed to obtain the PDMS flat film and spring-shaped PDMS. The cured sugar block was dissolved in deionized water for the third step, and finally removed and dried in the fourth step to obtain spongy PDMS. The PDMS base was cut to the required size, and finally the PDMS plane film, spring PDMS and sponge PDMS were obtained [10]. The specific preparation process is shown in Fig. 1a–c.
Put the PDMS substrate into absolute ethanol and water for ultrasonic cleaning for 15 min, and then put the PDMS substrate into Tris-HCl buffer (2 mg of dopamine per ml, pH 8.5), Placed on a magnetic stirrer in the dark and stirred for more than 12 h. After the reaction, the substrate was cross-washed with ethanol and water twice and placed in a vacuum drying oven at 40°C for vacuum drying. The dopa-modified PDMS substrate was soaked in anhydrous ethanol (95%) solution containing 2%wt APTES for 30 min. Then dry in an oven at 110°C for 20 min [11].
The following two commonly used and chemically stable silver activators are used in this paper:
1. Add 0.17 g of silver nitrate to a mixed solution of 10 g of ethanol and ethylene glycol (the weight ratio of the two is 2:1), and place it on a magnetic stirrer to stir for more than 20 min until the silver nitrate is completely dissolved. The solution becomes clear and transparent, and it is formulated to obtain a colourless and clear silver ion catalytic liquid. Then, the sponge-like PDMS was completely immersed in the silver ion catalytic solution, stirred on a magnetic stirrer for 3 min, and immediately after the timing was over, the sample was clipped out and placed in a plasma cleaner for 3 min. Repeat this operation twice so that both sides of the substrate undergo plasma treatment, and finally wash twice with water and ethanol alternately. Put it into a 40°C vacuum drying oven for vacuum drying for two to four hours, and then put it into the copper plating solution for copper plating.
2. First, 0.315 g of polyvinylpyrrolidone K30 (PVP) was added to 10 mL of ethylene glycol and sonicated for 20 min to make the PVP evenly dispersed. Then 0.17 g of silver nitrate was weighed and added to 10 mL of ethylene glycol. It was dissolved under constant temperature magnetic stirring at 30°C. Then, the uniformly dispersed PVP ethylene glycol solution was added to the silver nitrate solution and kept at 30°C under constant temperature stirring for 20 min to fully mix the two. Finally, 20 mL of ethylene glycol solution containing 0.1 g of sodium borohydride (NaBH4) was prepared and added to the above-mixed solution at an average rate of 55 drops/min. The nano-silver activation solution was obtained by reacting at 30°C under constant magnetic stirring for one hour. Then, the nano-silver activation solution was kept at a constant temperature of 50°C, and the PDMS flat film and the spiral PDMS were completely immersed in the silver activation solution for 6 min. Immediately after the timing, the sample was clamped out, and the silver activation solution was rinsed with deionized water. Then, it was placed in the copper plating solution for copper plating [12,13].
The copper plating solution is prepared from two A and B solutions and is currently being used. First, 15 g/L sodium hydroxide (NaOH), 15 g/L potassium sodium tartrate (KNaC4H4O6.4H2O), 15 g/L copper sulfate pentahydrate (CuSO4.5H2O) and 20 g/L Disodium EDTA-2Na (EDTA-2Na) was added to the aqueous solution in order and mixed, placed on a magnetic stirrer and stirred until clear and transparent to obtain copper plating solution A, and liquid B is an aqueous solution containing 0.95% formaldehyde (HCHO). Before starting the reaction, keep liquid A at a constant temperature, pour liquid B into liquid A, put in the sample after mixing, and take it out after a certain reaction time. Wash twice with water and ethanol alternately, and put it into a vacuum drying oven at 40°C for vacuum drying. In order to improve the electrochemical performance of the copper-plated samples, the copper-plated samples were put into 6 mL of palladium chloride solution (concentration of 10 Mm/L). The reaction was carried out at room temperature for 24 h. After the reaction, the obtained product was washed twice with water and ethanol and then placed in a vacuum drying oven at 40°C to vacuum dry and form a copper-palladium alloy [9,14].
After the PDMS substrate to be modified is put into the reaction solution during the dopamine self-polymerization reaction, the dopamine monomer can adhere to the surface of the PDMS substrate through the catechol group and gradually self-polymerize to form a dense polydopamine film, the polydopamine film has rich functional groups [15,16], such as hydroxyl and amino groups, so it has strong bonding properties, APTES can undergo a dehydration condensation reaction with the exposed hydroxyl groups of the polydopamine layer, uniformly disperse on the PDMS surface, and expose amino groups that can be linked to silver ions [5,17]. Therefore, the copper plating layer can also be uniformly deposited on the surface of the PDMS substrate after the subsequent electroless copper plating reaction. The specific process is shown in Fig. 2, in which the reaction mechanism of the polydopamine layer and the silane coupling agent is reported by Yuan et al. [18].
Figure 2: Dopamine and silylation modification principle: (a) Dopamine monomer self-polymerizes on the surface of PDMS to form polydopamine; (b) APTES hydrolysis; (c) polydopamine and APTES hydrolysis product hydroxyl condensation
Fig. 3 shows the appearance and morphological changes of PDMS at different reaction stages during electroless copper plating on the surface of PDMS substrate. Fig. 3a–c shows the detailed preparation processes of Cu-PDMS flat film, spongy Cu-PDMS and spring-like Cu-PDMS, respectively. In this paper, the polydimethylsiloxane substrates of different stages are named PDMS, PDA-PDMS, APTES-PDMS, Ag+-PDMS, and Cu-PDMS, respectively. It can be seen from the figure that the surface of PDA-PDMS modified by dopamine is uniformly covered with a layer of brown film, namely polydopamine; however, the surface of Ag+-PDMS after plasma treatment has a metallic lustre, which may be because some silver ions are reduced to the silver element by plasma during the treatment [19].
Figure 3: Changes in the appearance and morphology of PDMS in different reaction stages (a) PDMS flat film; (b) sponge-like PDMS; (c) spring-like PDMS
3.2 Wettability and Function Group Analysis
In order to confirm the formation of the hydrophilic dopamine layer on the surface of PDMS substrate and the increase of hydroxyl content, we tested the change of contact angle before and after PDMS substrate modification [20,21], as shown in the contact angle test diagrams in Fig. 4a,b, The hydrophilicity of the PDMS substrate surface modified by dopamine was improved, and the contact angle decreased from 113° ± 1° to 95° ± 1°. This further confirmed the formation of a polydopamine film on the surface of the PDMS substrate and the increase in the hydroxyl content [22,23]. In order to further confirm the existence of hydroxyl and amino groups on the modified PDMS surface, infrared spectrum analysis was carried out. As shown in Fig. 4c, by comparing the infrared vibration peaks of PDMS, PDA-PDMS, and APTES-PDMS, it can be found that the modified PDMS substrate has a broad peak in the range of 3000–3500 cm−1. The formation of this broad peak is due to the increase of hydroxyl groups; the vibration peaks near 1508 and 1630 cm−1 are exactly the band positions of the secondary amine in the infrared spectrum, which correspond to the groups shown in the reaction principle one by one, combined with the brown film formed on the surface of PDA-PDMS and the contact angle analysis, it can be seen that it is indeed polydopamine. Therefore, it was proved that dopamine and APTES formed a covalent bond with the PDMS substrate and successfully grafted on the surface of the PDMS substrate. Fig. 4d is the X-ray diffraction pattern of Ag+-PDMS after plasma treatment. Diffraction peaks appear at four different positions with 2Theta of 38.11°, 44.28°, 64.43°, and 77.47°, which correspond to the silver in the metallic state at (111), (200), (220) and (311), respectively. This result confirms the formation of elemental silver on the surface of the PDMS substrate [24]. Also, it confirms that the metallic lustre of Ag+-PDMS in the change of appearance and morphology is silver.
Figure 4: (a) Contact angle images of the PDMS; (b) contact angle images of the PDA-PDMS; (c) fourier transform infrared spectra of PDMS, PDA-PDMS, and APTES-PDMS; (d) XRD peaks of Ag+-PDMS after plasma treatment
3.3 Electroless Copper Plating Process
In order to find the most suitable reaction time and temperature, copper-plated samples were prepared from 10 to 35 min and 30°C to 55°C in this paper. From Fig. 5a1–a5, it can be seen from the SEM images under different copper plating times that the electroless plating time is too short, and the copper layer is too thin. It cannot completely cover the surface of the PDMS substrate, and the continuity is poor. With the increase of the electroless copper plating time, the copper layer gradually covered the entire surface until the time increased to 30 min, and the resistance value did not change significantly after continuing to prolong the reaction time [25]. Therefore, the optimal copper plating time was determined to be 30 min [26]. At the same time, as shown in Fig. 5b, by comparing the average resistance of each sample at the same distance (1.3 cm), the optimal reaction temperature for electroless copper plating is 45°C [27–29].
Figure 5: SEM images of different copper plating times (45°C) (a1) 10 min; (a2) 15 min; (a3) 20 min; (a4) 25 min; (a5) 30 min; (a6) double formaldehyde; (b) relative average resistance change at different copper plating temperatures
After finding the best reaction conditions, this paper also did experiments on the effect of different silanization modification times and different formaldehyde dosages on the effect of copper plating [30]. After testing, it was found that the resistance value of the three-time silanization modification was the lowest, which was 80 mΩ, and the atomic percentage of the copper element was as high as 67.23%, which was 6.3 percentage points higher than that of the one-time silanization sample [31]. However, the copper layer is easy to peel off, and its resistance changes greatly after a few days of placement. The possible reason is that the increase in silanizations will cause the PDMS surface groups to generate clusters [32]. Although it is easy to complex more silver ions in subsequent reactions and then chemically deposit metallic copper, the content of metallic copper increases, which the percentage of copper atoms can prove, but the bonding force with the substrate will decrease. Therefore, it showed excellent electrical conductivity initially but was not long-lasting.
In contrast, the conductivity and stability of the copper-plated samples modified by one-time silanization were the best. It can be seen from (a6) in Fig. 5 that increasing the amount of reducing agent formaldehyde will make the coverage of the copper layer lower [33]. The possible reason is that the increase of the reducing agent concentration will cause the reaction to become too intense so that most of the copper ions are reduced to copper elements in the solution but not deposited on the surface of the PDMS substrate [34].
As can be seen from the surface morphology of Fig. 6a1,a2, copper is uniformly and tightly attached to the surface of the PDMS substrate in the form of particles, without any gaps, so that the PDMS substrate constitutes a connected conductor. EDS spectrum of Fig. 6b,c shows that the copper plating layer’s copper atomic percentage accounts for up to 60.93% of the three main elements of copper oxycarbon, and the average thickness of the copper layer is 0.6 μm, which provides a theoretical basis for its electrical [35]. At the same time, the average resistance of the conductor at a distance of 1.3 cm is around 0.2 Ω, its square resistance is 1499.6 mΩ, and the conductivity is 5556 S/cm measured by a four-probe surface resistance tester.
Figure 6: Cu-PDMS at (a1) 10 μm; (a2) SEM topography of 2 μm; (b) SEM corresponding energy spectrum; (c) thickness of copper layer at 2 μm scale
Using a 100-grid knife to cut and penetrate the coating in a grid pattern, and divide the four 1 × 0.6 cm2 substrates into 60 equal areas (6 × 10, each small grid is 1 mm). Then the coating surface is tightly glued with 3M tape, and then it is peeled off, and the adhesion effect of the coating separating from the substrate is observed after a single adhesion test of the coating and the substrate. As can be seen from Fig. 7 the adhesion between the untreated PDMS substrate and the coating treated only with dopamine or silanization is not good, which is not conducive to practical application. However, the PDMS substrate modified by dopamine and silanization has high adhesion between the coating and only a little surface copper layer peeling off. At the same time, the ultrasonic washing method was also used to compare the weight change of the substrate before and after ultrasonic washing for 30 min, the weight loss rate of the co-modified PDMS substrate was calculated to be about 0.3%, both of which proved that the dopamine and silanization modification can significantly improve the bonding force between the silver coating and the PDMS substrate surface [36].
Figure 7: Digital photos of the substrate (before the test)-tape-substrate (after test) (a) PDMS; (b) only dopamine-modified PDMS; (c) silanized-modified PDMS only; (d) PDMS modified with dopamine and silanization
3.4 Electrochemical Performance
It can be seen from Fig. 8a that the onset potential of Cu-PDMS in the electrocatalytic oxygen uptake reaction is around 1.55 voltage vs. reversible hydrogen electrode (V vs. RHE). In contrast, the onset potential of the electrocatalytic MOR is around 1.35 V vs. RHE [37,38]. Then, the current density of the electrode rises sharply. At the same time, it can be seen from the figure that the MOR potential at the same current density is small, and the current density at the high potential is large, which proves that the MOR activity of copper hydroxide is higher than that of OER [39]. Subsequently, to roughly compare the electrochemical area of the electrodes, this paper uses the electric double-layer method for comparison [40]. The relationship between the current density difference of the electrode material and the scan rate is calculated by the cyclic voltammetry curve, and it can be seen that the electric double-layer capacitance value is proportional to the electrode’s electrochemical active surface area (ECSA) [39]. Therefore, we can see that the electrochemically active surface area of the Cu-PDMS electrode is small, so we need to increase the electrochemically active surface area of the electrode. In this paper, the method of ion replacement is used to form a copper-palladium alloy on the surface of the electrode [41,42]. It can be seen from the physical image that the surface of the electrode is covered with a layer of silver-white metallic lustre. Combined with the energy spectrum, it can be seen that the palladium ions successfully pass through the copper particles to form a copper-palladium alloy. By comparing Fig. 8e, it can be seen that the electrochemically active surface area of Cu-Pd-PDMS electrode is significantly higher than that of Cu-PDMS, which enhances the catalytic performance of the electrode [43].
Figure 8: (a) Comparison of oxygen evolution reaction (OER) and methanol oxidation reaction (MOR) properties of Cu-PDMS; (b) Physical image and energy spectrum of Cu-Pd-PDMS; (c, d) Cyclic voltammetry curves of Cu-PDMS and Cu-Pd-PDMS measured in the region of 0.91–1.02 V vs. RHE; (e) Double layer charging current densities of Cu-PDMS and Cu-Pd-PDMS samples
The as-prepared Cu-PDMS film is a conductor interconnect to light up a light-emitting diode (LED). The I-U characteristic curves of the LED circuit are measured in four different twisted states: the original state twisted at 90°, twisted at 180°, and twisted at 270° to evaluate the electrical stability of Cu/PDMS film. As shown in Fig. 9b, the I-V characteristic curves under different twisted morphologies almost overlap, and the maximum current reaches 19.2 mA; the small bulb can emit light normally, and the brightness has almost no change, which proves that the resistance of the Cu-PDMS sponge-like sample hardly changes at all. Fig. 9c shows the SEM morphology after distortion. There are few fracture surfaces and good continuity on the surface, indicating that the material has excellent anti-distortion effect. At the same time, in order to test the change of resistance value under different stretching ratios, we also adopted the Cu-PDMS substrate with spring structure, stretched from the original state (2 cm) to 10 times (20 cm), and measured its resistance. As can be seen from Fig. 9d,g, conductor resistance slightly increases and electrical performance decreases with the continuous increase of tensile ratio [44]. However, the relative resistance change rate remained within 0.4, proving that the silver-copper layers were still connected and not completely broken [45]. Fig. 9h shows the relative resistance change of 5000 cycles under 800% tensile state, indicating that the combined modification of dopamine and silanization can effectively improve the stability of the resistance change of the flexible copper electrode [46,47]. The resistance value can still change in a stable range under multiple tensile deformation.
Figure 9: (a1–a4) The effect diagrams of Cu-PDMS in the original state, twisted at 90°,180° and 270° as a conductor interconnection to light up LED dots; (b) I-V characteristic curves of LED circuits under different deformation conditions; (c) SEM morphology of Cu-PDMS conductor; (d); relative resistance changes of the prepared springs under different tensile conditions; (e) the original state (2 cm) resistance of the spring; (f) the effect of lighting up the LED dots as conductor interconnections; (g) I–V characteristics of LED circuit under different deformation conditions; (h) Normalized resistance of spring-like Cu-PDMS with different cycles under 800% tensile deformation
In this paper, silver catalysis was used to electroless copper plating on the surface of PDMS, and the preparation process was optimized. Then, the modification results, coating adhesion, and conductor properties were studied using various characterization methods. The main conclusions are as follows: The PDMS substrate was co-modified by polydopamine and silanization. The surface of the PDMS substrate was found to contain a large number of hydroxyl and aminopropyl groups by the analysis of the apparent morphology, contact Angle changes, and infrared spectroscopy, and the coating was tightly adsorbed on the PDMS substrate compared with that before modification. In the process of electroless plating and process optimization, it is concluded that the conductor with excellent performance can be prepared at 45°C for 30 min, and the best silanization modification is once. The optimal dosage of reducing agent formaldehyde is 0.95% of copper plating solution B. Subsequently, through a variety of characterization methods, it was measured that the average thickness of the coating of the conductor was 0.6 μm, the conductivity was 5556 S/cm, and the relative change value of the resistance and the I-V curve of the LED circuit almost did not change under the condition of large proportion of stretching and bending, proving that the prepared sample had good conductivity. And it can still maintain excellent electrical properties under large proportion deformation.
Acknowledgement: This work was financially supported by the Natural Science Foundation of Hunan Province. Sincere thanks to the University of South China for providing experimental conditions and other facilities.
Funding Statement: This work was financially supported by the Natural Science Foundation of Hunan Province (Grant No. 2021JJ40463).
Author Contributions: Jinliang Luo: Methodology, Validation, Investigation, Resources, Data Curation, Writing—Review & Editing, Visualization. Zhitao Hu: Methodology, Supervision, Writing—Review & Editing. Dongliang Li: Investigation, Writing—Review & Editing, Validation. Yang Li: Investigation, Methodology, Writing—Original Draft. Miaojiao Wang: Methodology, Data Collection, Investigation. Xiaomin Kang: Investigation, Validation, Writing—Review & Editing. All authors reviewed the results and approved the final version of the manuscript.
Availability of Data and Materials: The datasets generated and analyzed during the current study are available from the corresponding author on reasonable request.
Ethics Approval: Not applicable.
Conflicts of Interest: The authors declare no conflicts of interest to report regarding the present study.
References
1. Park H, Kim S, Lee J, Lee I, Bontapalle S, Na Y, et al. Organic flexible electronics with closed-loop recycling for sustainable wearable technology. Nat Electron. 2024;7(1):39–50. doi:10.1038/s41928-023-01078-9. [Google Scholar] [CrossRef]
2. Zhang W, Miao J, Zuo X, Zhang X, Qu L. Weaving a magnificent world: 1D fibrous electrodes and devices for stretchable and wearable electronics. J Mater Chem C. 2022;10(38):14027–52. doi:10.1039/D2TC02524H. [Google Scholar] [CrossRef]
3. Rong Q, Lei W, Liu M. Conductive hydrogels as smart materials for flexible electronic devices. Chemistry. 2018;24(64):16930–43. doi:10.1002/chem.201801302. [Google Scholar] [PubMed] [CrossRef]
4. Sun J, Sun R, Jia P, Ma M, Song Y. Fabricating flexible conductive structures by printing techniques and printable conductive materials. J Mater Chem C. 2022;10(25):9441–64. doi:10.1039/D2TC01168A. [Google Scholar] [CrossRef]
5. Wu C, Tang X, Gan L, Li W, Zhang J, Wang H, et al. High-adhesion stretchable electrode via cross-linking intensified electroless deposition on a biomimetic elastomeric micropore film. ACS Appl Mater Interfaces. 2019;11(22):20535–44. doi:10.1021/acsami.9b05135. [Google Scholar] [PubMed] [CrossRef]
6. Dehkharghani AMF, Divandari M. Investigation of electroless copper plating on polyurethane foam, as an initial step of open cell foam production process. Trans Inst Met Finish. 2015;93(4):186–9. doi:10.1179/0020296715z.000000000248. [Google Scholar] [CrossRef]
7. Fritz N, Koo H-C, Wilson Z, Uzunlar E, Wen Z, Yeow X, et al. Electroless deposition of copper on organic and inorganic substrates using a Sn/Ag catalyst. J Electrochem Soc. 2012;159(6):D386–92. doi:10.1149/2.099206jes. [Google Scholar] [CrossRef]
8. Cai D, Neyer A. Polydimethylsiloxane (PDMS) based optical interconnect with copper-clad FR4 substrates. Sens Actuators B-Chem. 2011;160(1):777–83. doi:10.1016/j.snb.2011.08.062. [Google Scholar] [CrossRef]
9. Chen D, Xu L, Liu H, Yang J. Rough-surfaced bimetallic copper-palladium alloy multicubes as highly bifunctional electrocatalysts for formic acid oxidation and oxygen reduction. Green Energy Environ. 2019;4(3):254–63. doi:10.1016/j.gee.2018.09.002. [Google Scholar] [CrossRef]
10. Won Y, Kim A, Yang W, Jeong S, Moon J. A highly stretchable, helical copper nanowire conductor exhibiting a stretchability of 700%. NPG Asia Mater. 2014;6(9):e132. doi:10.1038/am.2014.88. [Google Scholar] [CrossRef]
11. Zhang S, Zheng H, Miao X, Zhang G, Song Y, Kang X, et al. Surprising nanomechanical and conformational transition of neutral polyacrylamide in monovalent saline solutions. J Phys Chem B. 2023;127(46):10088–96. doi:10.1021/acs.jpcb.3c06126. [Google Scholar] [PubMed] [CrossRef]
12. Huang JH, Shih PS, Renganathan V, Grӓfner SJ, Chen YA, Huang CH, et al. Development of high copper concentration, low operating temperature, and environmentally friendly electroless copper plating using a copper—glycerin complex solution. Electrochim Acta. 2022;425:140710. [Google Scholar]
13. Moon Y-S, Lee J-H. Fabrication of Sn-Cu bump using electroless plating method. J Microelectron Packag Soc. 2008;15(2):17–21. doi:10.1016/j.electacta.2022.140710. [Google Scholar] [CrossRef]
14. Nurmukhametova AT, Belov RN, Sultanova ED, Vorob’ev VV, Osin YN, Burilov VA, et al. Amino-modified silica-supported copper-palladium alloy. Synthesis and use in selective hydrogenation of disubstituted nitroarenes in a flow micro reactor. Russ J Org Chem. 2019;55(1):1–6. doi:10.1134/s1070428019010019. [Google Scholar] [CrossRef]
15. Liu J, Yao Y, Li X, Zhang Z. Fabrication of advanced polydimethylsiloxane-based functional materials: bulk modifications and surface functionalizations. Chem Eng J. 2021;408:127262. doi:10.1016/j.cej.2020.127262. [Google Scholar] [CrossRef]
16. Lee H, Dellatore SM, Miller WM, Messersmith PB. Mussel-inspired surface chemistry for multifunctional coatings. Science. 2007;318(5849):426–30. doi:10.1126/science.1147241. [Google Scholar] [PubMed] [CrossRef]
17. Xiao X, Wang W, Chen J, Jia L. Polydopamine-coated open tubular column for the separation of proteins by capillary electrochromatography. J Sep Sci. 2015;38(16):2893–9. doi:10.1002/jssc.201500315. [Google Scholar] [PubMed] [CrossRef]
18. Li Y, Sa R, Yan Y, Wang W, Ning N, Tian M. Functionalization on poly-p-phenylene terephthamide fiber using bioinspire dopamine deposition and silane coupling agentd. China Rubber Ind. 2016;2016(631):5–12. doi:10.1007/s11426-015-5533-4. [Google Scholar] [CrossRef]
19. Zhang H-B, Chen Q. Recent progress of non-thermal plasma material surface treatment and functionalization. Acta Phys Sin. 2021;70(9):16–32. doi:10.7498/aps.70.20202233. [Google Scholar] [CrossRef]
20. Nagy N. Contact angle determination on hydrophilic and superhydrophilic surfaces by using r–θ-type capillary bridges. Langmuir. 2019;35(15):5202–12. doi:10.1021/acs.langmuir.9b00442. [Google Scholar] [PubMed] [CrossRef]
21. Prakash CGJ, Raj CC, Prasanth R. Fabrication of zero contact angle ultra-super hydrophilic surfaces. J Colloid Interface Sci. 2017;496:300–10. doi:10.1016/j.jcis.2017.01.007. [Google Scholar] [PubMed] [CrossRef]
22. Qiu Z, Wu B, Miao H, Yang Y, Wang Z, Wu M, et al. Rapid deposition of polydopamine on textile-based materials via solvent-assisted methodology. Mater Lett. 2023;333:133549. doi:10.1016/j.matlet.2022.133549. [Google Scholar] [CrossRef]
23. Zhao S, Golestani M, Penesyan A, Deng B, Zheng C, Strezov V. Antibiotic enhanced dopamine polymerization for engineering antifouling and antimicrobial membranes. Chin Chem Lett. 2020;31(3):851–4. doi:10.1016/j.cclet.2019.05.057. [Google Scholar] [CrossRef]
24. Zhang F-T, Xu L, Chen J-H, Zhao B, Fu X-Z, Sun R, et al. Electroless Deposition metals on poly(dimethylsiloxane) with strong adhesion as flexible and stretchable conductive materials. ACS Appl Mater Interfaces. 2018;10(2):2075–82. doi:10.1021/acsami.7b15726. [Google Scholar] [PubMed] [CrossRef]
25. Kang X, You G, Liu J, Fu G, Liu D, Zou Y, et al. An insight in the role of dopamine acted in the electroless deposition process using atomic force microscopy based single molecule force spectroscopy. Surf Interfaces. 2024;50:104495. doi:10.1016/j.surfin.2024.104495. [Google Scholar] [CrossRef]
26. Chen H, Liu G, Xu C, Hou X, Liu Y. Copper@carbon fiber composites prepared by a simple electroless plating technique. Mater Lett. 2016;173:211–3. doi:10.1016/j.matlet.2016.03.055. [Google Scholar] [CrossRef]
27. Koo H-C, Lightsey C, Kohl PA. Affect of anneal temperature on all-copper flip-chip connections formed via electroless copper deposition. IEEE Trans Compon Packag Manuf Technol. 2012;2(1):79–84. doi:10.1109/TCPMT.2011.2176492. [Google Scholar] [CrossRef]
28. Wang X. Bottom-up filling in electroless plating with an addition of JGB-RPE. Russ J Electrochem. 2014;50(5):438–43. doi:10.1134/S1023193514050103. [Google Scholar] [CrossRef]
29. Zan L, Liu Z, Yang Z, Wang Z. A synergy effect of 2-MBT and PE-3650 on the bottom-up filling in electroless copper plating. Electrochem Solid State Lett. 2011;14(12):D107–9. doi:10.1149/2.018112esl. [Google Scholar] [CrossRef]
30. Li S, Scheiger JM, Wang Z, Dong Z, Welle A, Trouillet V, et al. Substrate-independent and re-writable surface patterning by combining polydopamine coatings, silanization, and thiol-ene reaction. Adv Funct Mater. 2021;31(50):2107716. doi:10.1002/adfm.202107716. [Google Scholar] [CrossRef]
31. Yu M, Kang X, Qian L. Interactions between monovalent cations and polyethylene glycol: a study at micro level. Colloids Surf A Physicochem Eng Asp. 2024;680:132731. doi:10.1016/j.colsurfa.2023.132731. [Google Scholar] [CrossRef]
32. Gökaltun A, Kang YB, Yarmush ML, Usta OB, Asatekin A. Simple surface modification of poly(dimethylsiloxane) via surface segregating smart polymers for biomicrofluidics. Sci Rep. 2019;9(1):7377. doi:10.1038/s41598-019-43625-5. [Google Scholar] [PubMed] [CrossRef]
33. Bragaglia M, Paleari L, Mariani M, Nanni F. Sustainable formaldehyde-free copper electroless plating on carbon-epoxy substrates. J Mater Sci Mater Electron. 2024;35(10):707. doi:10.1007/s10854-024-12493-9. [Google Scholar] [CrossRef]
34. Vavra J, Ramona GPL, Dattila F, Kormanyos A, Priamushko T, Albertini PP, et al. Solution-based Cu+ transient species mediate the reconstruction of copper electrocatalysts for CO2 reduction. Nat Catal. 2024;7(1):89–97. doi:10.1038/s41929-023-01070-8. [Google Scholar] [CrossRef]
35. Hassanin H, Mohammadkhani A, Jiang K. Fabrication of hybrid nanostructured arrays using a PDMS/PDMS replication process. Lab A Chip. 2012;12(20):4160–7. doi:10.1039/c2lc40512a. [Google Scholar] [PubMed] [CrossRef]
36. Li W, Chen Y, Wu S, Zhang J, Wang H, Zeng D, et al. Preparing high-adhesion silver coating on APTMS modified polyethylene with excellent anti-bacterial performance. Appl Surf Sci. 2018;436:117–24. doi:10.1016/j.apsusc.2017.11.216. [Google Scholar] [CrossRef]
37. Fang Y-H, Liu Z-P. First principles Tafel kinetics of methanol oxidation on Pt(111). Surf Sci. 2015;631:42–7. doi:10.1016/j.susc.2014.05.014. [Google Scholar] [CrossRef]
38. Geng D, Lu G. Dependence of onset potential for methanol electrocatalytic oxidation on steric location of active center in multicomponent electrocatalysts. J Phys Chem C. 2007;111(32):11897–902. doi:10.1021/JP0709510. [Google Scholar] [CrossRef]
39. Kang X, Fu G, Fu X-Z, Luo J-L. Copper-based metal-organic frameworks for electrochemical reduction of CO2. Chin Chem Lett. 2023;34(6):107757. doi:10.1016/j.cclet.2022.107757. [Google Scholar] [CrossRef]
40. Wang J, Xu F, Jin H, Chen Y, Wang Y. Non-noble metal-based carbon composites in hydrogen evolution reaction: fundamentals to applications. Adv Mater. 2017;29(14):1605838. doi:10.1002/adma.201605838. [Google Scholar] [PubMed] [CrossRef]
41. Chen Y, Wang L, Wang W, Cao M. Enhanced photoelectrochemical properties of ZnO/ZnSe/CdSe/Cu2-xSe core-shell nanowire arrays fabricated by ion-replacement method. Appl Catal B-Environ. 2017;209:110–7. doi:10.1016/j.apcatb.2017.02.049. [Google Scholar] [CrossRef]
42. Gordienko MG, Palchikova VV, Kalenov SV, Lebedev EA, Belov AA, Menshutina NV. The alginate-chitosan composite sponges with biogenic Ag nanoparticles produced by combining of cryostructuration, ionotropic gelation and ion replacement methods. Int J Polym Mater Polym Biomater. 2022;71(1):34–44. doi:10.1080/00914037.2020.1798439. [Google Scholar] [CrossRef]
43. Connor P, Schuch J, Kaiser B, Jaegermann W. The determination of electrochemical active surface area and specific capacity revisited for the system MnOx as an oxygen evolution catalyst. Zeitschrift für Physikalische Chemie. 2020;234(5):979–94. doi:10.1515/zpch-2019-1514. [Google Scholar] [CrossRef]
44. Bi X, Huang Z, Yao M, Wang Z, Yu P, Jiang C. Highly conductive rubber-based electrode with a robust wrinkled mesh-like copper coating for stretchable triboelectric nanogenerator. Colloids Surf A Physicochem Eng Asp. 2024;700:134786. doi:10.1016/j.colsurfa.2024.134786. [Google Scholar] [CrossRef]
45. Miao J, Tian M, Qu L, Zhang X. Flexible, transparent and conductive wearable electronic skin based on 2D titanium carbide (MXene) ink. Carbon. 2024;222:118950. doi:10.1016/j.carbon.2024.118950. [Google Scholar] [CrossRef]
46. Srivastava V, Dubey S, Vaish R, Rajpurohit BS. Optimized fabrication of flexible paper-based PCBS with pencil and copper electroplating. Adv Mater Technol. 2024;2400688. doi:10.1002/admt.202400688. [Google Scholar] [CrossRef]
47. King MG, Baragwanath AJ, Rosamond MC, Wood D, Gallant AJ. Porous PDMS force sensitive resistors. Procedia Chem. 2009;1(1):568–71. doi:10.1016/j.proche.2009.07.142. [Google Scholar] [CrossRef]
Cite This Article
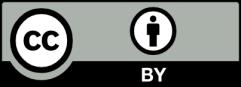
This work is licensed under a Creative Commons Attribution 4.0 International License , which permits unrestricted use, distribution, and reproduction in any medium, provided the original work is properly cited.