Open Access
ARTICLE
Hybrid Epoxy Composites Reinforced with Coconut Sheath and Basalt Fibres: Enhancing Mechanical and Thermal Performance for Sustainable Applications
1 Department of Chemistry, Dhanalakshmi Srinivasan Engineering College, Perambalur, 621212, India
2 Department of Chemistry, School of Advanced Sciences, Kalasalingam Academy of Research and Education, Krishnankoil, 626126, India
3 School of Chemical Engineering, Yeungnam University, Gyeonsan, 38541, Republic of Korea
4 Department of Chemical and Materials Engineering, National Yunlin University of Science and Technology, Douliu, 64002, Taiwan
5 Department of Computational Biology, Saveetha School of Engineering, Saveetha Institute of Medical and Technical Sciences, Saveetha University, Chennai, 602105, India
* Corresponding Authors: Balamurugan Rathinam. Email: ; Vanaraj Ramkumar. Email:
Journal of Polymer Materials 2024, 41(4), 207-218. https://doi.org/10.32604/jpm.2024.057901
Received 30 August 2024; Accepted 12 November 2024; Issue published 16 December 2024
Abstract
The present study focuses on sustainable biopolymer composites created from coconut sheath and basalt fibres, which are biodegradable, environmentally benign, and have low carbon footprints. High specific strength, superior mechanical performance, reduced weight, and improved thermal stability are all displayed by these materials. Four hybrid epoxy composites (C1–C4) were produced utilizing five stacking sequences and compression moulding, demonstrating that hybridization considerably enhances mechanical characteristics. The hybrid and pure basalt fibre composites have larger storage moduli than untreated coconut sheath fibre-reinforced epoxy (2.1 GPa). The greatest glass transition temperature (Tg) for C4 has been determined to be 118°C. These low-cost, non-toxic composites provide environmentally friendly options for use in the electronics, packaging, automotive, and construction sectors.Graphic Abstract
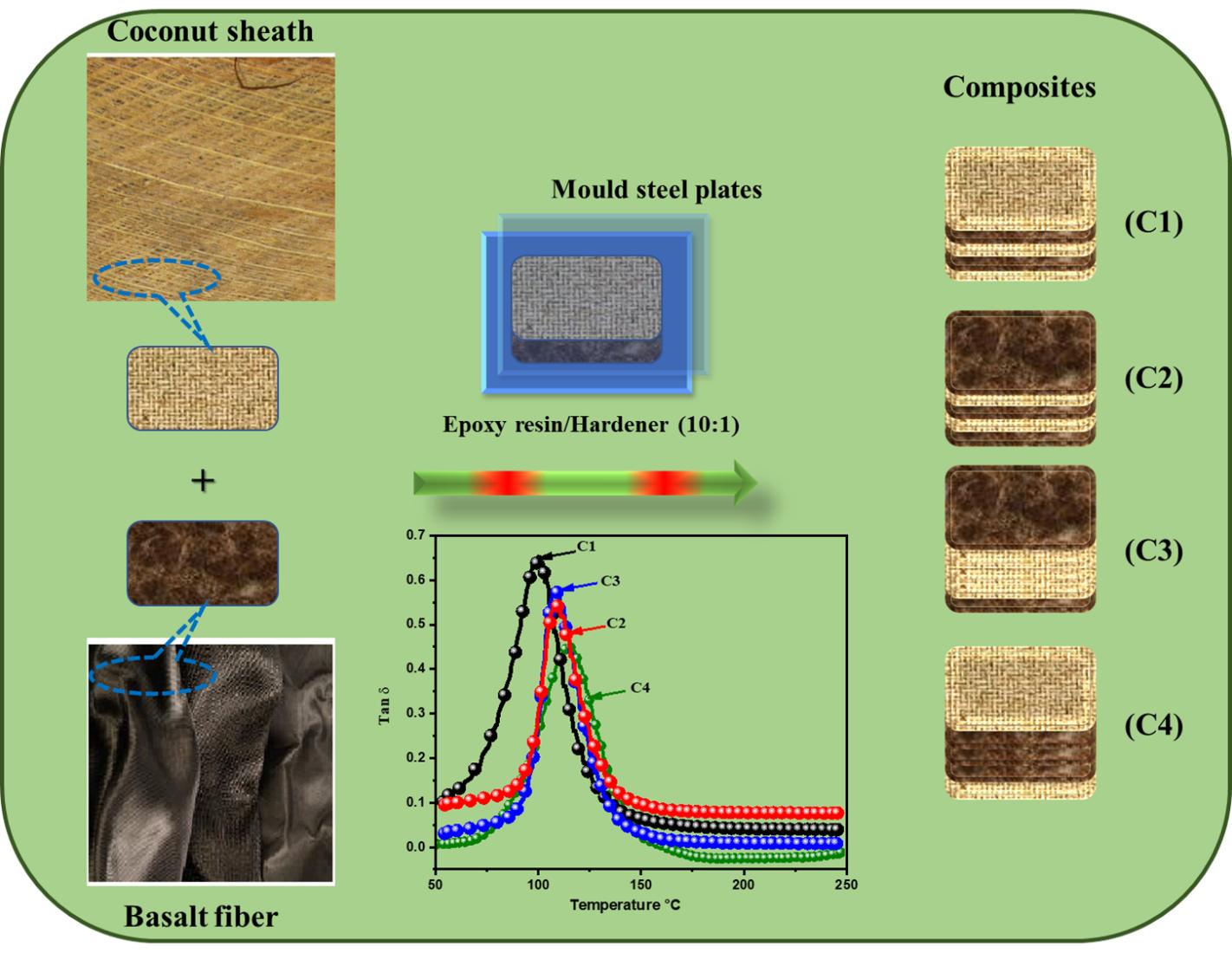
Keywords
In recent decades, there has been an increase in the research area of eco-friendly fibre-reinforced polymer (FRP) composites that use natural fibre as reinforcement due to their low cost, biodegradability, low environmental impact, non-hazardous, good acoustic insulation properties, low density, non-abrasive, high strength to weight ratio, and renewability [1–3]. Abaca, cotton, ramie, pineapple leaf, palm fibre, banana, agave, flax, hemp, jute, wool, silk, cotton, sisal, kenaf, and bagasse are all often used as reinforcing materials [4,5]. While there are many benefits, there are also drawbacks. For example, hydrophilicity, poor wettability with resin-matrix, discontinuous short fibres, highly variable mechanical properties, and weak interfacial bonding decreased the mechanical and thermal properties, which limited their use in construction, aerospace, and nautical environments [6,7]. Natural fibre composites’ qualities have been improved by surface treatment techniques such as silane, isocyanate, alkali, acid, and acid salt; nevertheless, these techniques also degrade the original characteristics of the fibres and alter their chemical composition [8–10]. Synthetic and natural materials were hybridized to conquer these shortcomings and maximize the benefits of each [11–13]. Research revealed that the flax fibre hybrid with basalt fibre was chemically equal to E glass, but because of the manufacturing technique, it produced fewer particles and was less irritating than the latter. It also had better rigidity and resilience to moisture. Natural fibre was thought to be a combination of synthetic fibres like glass [13] carbon [14] and aramid [15]. Variations in the percentage of natural fibre improved the mechanical characteristics of hybrid polymer composites consisting of glass and fibres from nature [16], such as sisal/glass, kenaf/glass [17] and jute/glass [18–20]. Recently, naturally occurring materials have been employed as reinforcing agents, one of which being basalt fibre derived from volcanic rock generated from lava [21]. Pyroxene and plagiocene are two of basalt’s key minerals [22,23]. Silica is the primary component of basalt, followed by alumina [24,25]. The Moscow Research Institute in Russia was the first to create basalt fibre, which is less expensive than glass and carbon fibre [23,24]. Biopolymer composites are increasingly utilized in the consumer goods, packaging, automotive, and aerospace industries due to their versatility and appeal. Their high mechanical strength, lightweight nature, and eco-friendly attributes position them as a compelling alternative to traditional composites, offering both performance and sustainability benefits. Biopolymer composites, with their ecologically friendly properties and renewable supply, represent a significant advancement in material research. Their mechanical properties, including their low weight, superior mechanical performance, and biodegradability, make them ideal for a variety of applications in consumer goods, packaging, automotive, and aerospace industries. These materials offer significant benefits to the environment and lessen the demand for fossil fuels because they are biodegradable and compostable. The hybridization of various fibres, such as coconut sheath and basalt, might result in composites with specialized characteristics for specific purposes. The arrangement of the reinforcing fibres inside the polymer matrix is one of the key elements that affect how well these hybrid composites work. The arrangement or order of the fibre layers is referred to as the “stacking sequence,” and it has a direct impact on the composite’s mechanical properties, thermal stability, and stress distribution. Prior research has demonstrated that the mechanical characteristics of hybrid composites, such as their strength-to-weight ratio, impact resistance, and general durability, may be considerably enhanced by optimizing the stacking sequence.
A survey of the literature reveals a severe dearth of knowledge about the usage of coconut sheath and basalt fibre as reinforcing elements in epoxy matrices. By examining the impacts of different stacking configurations of these fibres inside an epoxy matrix, our work fills that knowledge gap. Furthermore, the mechanical, thermal, and dynamic mechanical properties of the resultant composites have been comprehensively investigated. Scheme 1 illustrates of the work’s methodology.
Scheme 1: Flow chart of the current research work
Triethylenetetramine (HY 951) and epoxy resin (LY 556) were bought from Sigma-Aldrich, St. Louis, MO, USA. The densities of epoxy resin and triethylenetetramine were 1.15–1.20 g/cm3 and 0.97–0.99 g/cm3, respectively (This was taken from the test report provided by the manufacturer). The basalt fibres (GSM-300) were obtained from NICKUNJ, Mumbai, India. The coconut sheath fibres were obtained from local agricultural resources (Tanjore area, Tamil Nadu, India).
The tensile test is used to determine the stress-strain behaviour of an epoxy-based stacking of various layers of coconut sheath/basalt fibre-reinforced composites. A tensile test was performed on a UTM machine (Model H10K-S, Tinius Olsen, San Diego, CA, USA) with a crosshead speed of 5 mm/min, in accordance with ASTM standard D3039. Five samples were obtained for every test, and the outcomes were averaged. There are 115 mm separating the grips. The flexural strength of the epoxy-based composites is ascertained using the 3-point bending test. An Instron testing machine was used to study flexural qualities by ASTM D790-10 standard (Aberdeen, UK), with a cross-head speed of 5 mm/min. A span length of 50 mm was maintained for the testing. Each test was conducted with five samples, and the average of the results was calculated. To assess the energy required to fracture the specimens, an impact test was performed on the epoxy-based composites. The impact test followed ASTM D256-10 standards and was carried out using an Izod impact tester. Unnotched specimens were used for this test. As with the previous tests, five samples were used for each trial, and the average results were recorded. The Dynamic Mechanical Analysis (DMA) of polymeric composite materials is one of the most effective methods for assessing material damping behaviour, which is directly related to molecular structure. Using an SII Nanotechnology, Model DMS-6000 (Seiko Instruments Inc., Chiba, Japan) in a three-point bending configuration, at a temperature range of 25–300°C and an operating frequency of 1 Hz, the dynamic mechanical characterization of the epoxy-based composites was achieved. Morphological observations were conducted using a scanning electron microscopy (SEM) by S4800 (Hitachi, Tokyo, Japan) equipment. The raw, treated coconut sheath fibre surfaces and epoxy-based composite fracture surfaces (photomicrographs) were collected from the specimens produced following the tensile, flexural, and impact tests, which were coated with gold powder. The TGA test is used to determine how much weight loss occurs as a result of temperature. TGA of neat epoxy matrix and their composites was performed by Thermo gravimetric analysis-Thermal Analyzer NETZSCH STA 409 PC (TA instruments, Burlington, NJ, USA) at 10°C per minute heating rate (from 0 to 800°C) with a constant flow of nitrogen to predict percentage weight loss, char yield formation, and thermal degradation temperature. For every thermogravimetric analysis, 5 mg samples were employed.
Four distinct types of composites were made using two distinct fibres (basalt and coconut fibre) and epoxy resin. For every composite, about five layers of fibres were employed and the schematic representation was given in Fig. 1. The composite C1 was created by combining basalt fibre with epoxy resin. Create the hybrid composites, coconut fibres, and basalt were incorporated alternately. The hybrid composite C2 was created by layering basalt fibre on the top and bottom of the composite. With coconut fibre layered on top and bottom of the composite, the hybrid composite, C4, was created. Three layers of coconut fibres were stacked between basalt fibres to create the hybrid composite or C3.
Figure 1: Schematic representation of the preparation of composite materials (C1–C4)
In this study, two rectangular steel mould plates, each measuring 220 mm × 220 mm, were used to fabricate coconut sheath and basalt fibre-reinforced epoxy composites. Beads with a thickness of 4 mm were placed over the mould plates. Before pouring the uncured epoxy resin mixture onto the mould surface, the plates were thoroughly cleaned, dried, and treated with a releasing agent such as silicone spray. The coconut sheath and basalt fibres, selected with dimensions of 210 mm × 210 mm, were prepared for layering. Five layers of basalt fibre were used to determine the required amount of epoxy resin. The epoxy resin and hardener were mixed in a 10:1 ratio and stirred to form a homogeneous mixture. The epoxy resin mixture was then poured onto the mould plates and manually spread over the basalt fibres before placing each layer. This process was repeated for all five layers of basalt fibre. Once the layers were positioned, the mould plates were sealed and placed in a compression moulding machine. A pressure of 4 MPa was applied for 24 h to allow the composites to cure at room temperature. After curing, the basalt fibre-reinforced epoxy composites were weighed to determine the final epoxy resin content. The same procedure was followed for fabricating the different stacking sequences of the coconut sheath/basalt fibre-reinforced epoxy composites. The resulting fibre volume fractions for the composites were as follows: C1 = 0.53, C2 = 0.55, C3 = 0.57, and C4 = 0.63.
C+B+C+B+C = This stacking sequence taking as composite 1 (C1)
B+C+B+C+B = This stacking sequence taking as composite 2 (C2)
B+C+C+C+B = This stacking sequence taking as composite 3 (C3)
C+B+B+B+C = This stacking sequence taking as composite 4 (C4)
3.1 Surface Morphological Characteristics of the Composites
The SEM pictures displayed in Fig. 2a–d depict the fracture surface of the composite consisting of epoxy resin, coconut sheath fibre, and basalt fibre following tensile measurement. Fig. 2a depicts the shattered surface of the composite consisting of pure basalt fibre and epoxy resin (C4). Fig. 2b,d depicts the cracked surface of hybrid composites comprised of basalt fibre and coconut sheath fibre with epoxy resin (C1–C3 composites). The SEM images of the pure basalt fibre composites revealed no signs of void formation during fibre pull-out. Due to the high tensile modulus of basalt fibre, the fibres exhibited acute, trapezoidal, and cylindrical fracture patterns. Additionally, because basalt fibre and epoxy resin have excellent wettability, the interaction between the two materials was not compromised. As a result, the tensile, flexural, and impact strength values of the basalt fibre epoxy composite C4 were significantly higher. In contrast, the SEM analysis of the C1 composite showed noticeable fibre pull-out from the resin matrix, leading to the formation of voids. This reduced the fibre-matrix contact area, ultimately weakening the composite’s overall mechanical performance. This is obvious from the SEM pictures (Fig. 2b). The mechanical characteristics of the C1 composite were thus not as good as those of the C2 and C4 composites. The coconut sheath fibre’s SEM picture (Fig. 2c) reveals larger pores. C2 composite has less vacancy because it contains more basalt fibre, which adds to its strong tensile, flexural, and impact strengths.
Figure 2: Tensile fractured FE-SEM surface images of (a) C4 composite (b) C1 composite (c) C2 composite (d) C3 composite
In the C3 composite, the coconut sheath fibres were nearly destroyed due to significant fibre pull-out, while the basalt fibres sustained only minor damage. This can be attributed to the higher concentration of coconut sheath fibre and resin matrix, while the basalt fibre content was minimal, being present only in the top and bottom layers of the composite. The reduced percentage of basalt fibre negatively affected the mechanical properties of the composites. The tensile, flexural, and impact characteristics of hybrid composites are influenced by the sequence in which the fibres are arranged. Since basalt fibre possesses superior mechanical properties compared to coconut sheath fibre, the C3 composite demonstrated better mechanical performance than the C1 composite. This improvement is particularly noticeable when basalt fibres are placed in the outer layers, with coconut sheath fibres stacked between them. Additionally, excellent fibre-to-resin adhesion was observed, minimizing crack propagation throughout the composite. The strong interfacial interaction between the fibres and matrix contributed to proper adhesion, thereby enhancing the overall mechanical properties of the composites.
3.2 Thermogravimetric Analysis (TGA)
Fig. 3 depicts the thermal stability of composites made of basalt fibre and coconut sheath fibre with epoxy resin, as evaluated by TGA analysis. The hybrid composites consisting of basalt and coconut sheath fibres showed a 10% temperature degradation (T10) of 426°C for C2 and 438°C for C4. In terms of thermal stability, the pure basalt fibre composite C4 is superior to hybrid composites. This is because pure basalt fibre composites have large concentrations of iron oxides, alumina, and silica. When compared to untreated coconut sheath fibre reinforced epoxy (UTCSE) composites, C2 and C4 composites have stronger thermal stability due to the instability of the coconut sheath fibre, which has a higher cellulose, hemicellulose, and lignin content. Similarly, the char yield values of the hybrid composite C2 and basalt fibre composite (C4) were determined to be 44.1% and 51.8%, respectively (Fig. 3). The addition of basalt fibre to the hybrid composite boosts the composite’s heat stability and char yield.
Figure 3: TGA thermogram of C2 and C4 composites
3.3 Mechanical Properties of C1, C2, C3 and C4 Composites
The tensile, flexural and impact strengths of C1, C2, C3 and C4 composites are shown in Table 1. Tensile strengths of C1, C2, C3, and C4 composites were measured and found to be 96.76, 125.70, 104.25, and 182.50 MPa, respectively. The untreated coconut sheath fibre-reinforced epoxy composite (UTCSE composite) had a tensile strength of 48.35 MPa. The hybrid composites (C1–C3) had a better tensile strength than the untreated coconut sheath fibre composite (UTCSE composite), although it was lower than that of the pure basalt fibre composite (C4 composite), owing to the basalt fibre’s high stiffness. The tensile strength of the hybrid composite C2 was discovered to be 29.90% more than that of the hybrid composite C1, 18.77% greater than that of the hybrid composite C3, and 159.97% greater than that of UTCSE. The tensile strength of pure basalt fibre composite C4 was found to be 45.18% greater than the hybrid composite C2, and 277.45% higher than UTCSE. The high tensile strength of the basalt fibres was the cause of the hybrid composites’ high tensile strength.
The results showed that the flexural strengths of the composites C1, C2, C3, and C4 were 218.36, 278.60, 234.20, and 342.26 MPa, in that order. Flexural strength was much higher for pure basalt fibre composite C4 due to the basalt fibre’s high stiffness and minimal elongation [21,22]. C2 has the highest flexural strength of all the hybrid composites. In the C2 composite, the applied force was resisted by basalt fibre, while the remaining force was passed to the natural fibre via the resin matrix. When the fibre in the coconut sheath breaks, another layer of basalt resists the breakage, and so on. The basalt fibre lamina acts as a shield for the coconut sheath fibre, giving C2 better tensile and flexural strength than others. The impact strengths of Composites C1–C4 were measured and found to be 9.14, 13.93, 10.28, and 18.16 J/mm in that order. The impact strength of the hybrid composites C1–C3 was lower than that of the pure basalt fibre composite C4 because of the sliding of the two distinct fibre layers (coconut and basalt fibre). C2 offers the highest impact strength of any hybrid composite because it has top, middle, and bottom layers of basalt fibre. As load bearers, the basalt fibres withstand the force of impact. Fibre-matrix de-bonding, the combinational impact of void content, and fibre defects that contribute to the composites’ strength were some of the aspects that influenced the hybrid composites’ defect. The enhanced value of hybrid composite C2 stems from the creation of voids that are overpowered by the stiffness of the basalt fibres. Whereas the other two hybrid composites, C1 and C3, have lower values, this might be owing to the production of a significant number of voids, which causes debonding of the fibre matrix. The results suggest that the composite made from untreated coconut sheath fibre and epoxy resin exhibited tensile, flexural, and impact strengths of 48.35 MPa, 64.60 MPa, and 4.51 J/mm, respectively. The incorporation of basalt fibres, known for their stiffness, significantly improved all these properties in the hybrid composites.
3.4 Flame Retardancy of the Composites
Biopolymer composites can withstand ignition, slow the propagation of fire, and emit less heat when they come into contact with flames. “Flame retardancy” is the term used to describe this quality [2,3]. Biopolymer composites are materials made by adding various fillers or reinforcements to natural polymers, which are often derived from renewable resources, to improve their properties [11]. To increase their resistance to flames, they can be treated with different substances and materials. An indication of the composites’ flame retardancy assessment is the Limiting Oxygen Index (LOI) value. The char yield value(s) at 800°C from TGA analysis was utilized for the measurement of the LOI value using the van Krevelen and Hoftyzer equation, which is provided below.
where LOI is the Limiting Oxygen Index value and CY is the char yield determined by TGA analysis. The LOI values for hybrid composite C2 and pure basalt fibre composite C4 were 35.14 and 38.22, respectively. In general, the polymer’s LOI value should be more than 26, indicating that it is self-extinguishing and flame retardant. As the char yield value rises, the composite’s LOI value rises as well. Every composite that was made had a LOI value of more than 26, indicating strong flame retardancy.
3.5 Dynamic Mechanical Analysis (DMA)
Eco-friendly polymer composites’ “dynamic mechanical characteristics” describe how they react to changes in strain, temperature, and stress over time. Comprehending these attributes is crucial in evaluating the effectiveness, longevity, and possible uses of these environmentally beneficial substances [21,22]. Dynamic mechanical analysis was used to determine the storage modulus value (Fig. 4) and the damping behaviour (Tan δ) of the pure basalt fibre composite and hybrid composites (Fig. 5). The storage modulus and plots of Tan δ for the C1, C2, C3, and C4 composites are depicted in Fig. 4.
Figure 4: Storage modulus of C1, C2, C3 and C4 composites
Figure 5: Tan δ of C1, C2, C3 and C4 composites
The storage modulus of the hybrid composites varied depending on the stacking sequences of basalt and coconut sheath fibres. For C1, composed of both fibres, the storage modulus was determined to be 4.9 GPa, while for C2 it was 5.6 GPa, and for C3 it was 5.1 GPa. In contrast, the pure basalt fibre composite C4 exhibited the highest storage modulus at 6.4 GPa. Among the hybrid composites, C2 had the highest value, whereas C1 had the lowest. The alternating placement of basalt and coconut sheath fibres in C1 and C2 contributed to their differing performance. The higher storage modulus of C2 was attributed to the stiffness of basalt fibres, which restrict the polymer chain’s mobility. Strong interfacial bonding between the fibres and the epoxy resin contributed to this enhanced performance. However, C3, where coconut sheath fibres were positioned between the basalt layers, exhibited slightly reduced interfacial contact, leading to a lower storage modulus of 5.1 GPa. The manufactured hybrid composites and pure basalt fibre composite had higher storage modulus values compared to the untreated coconut sheath fibre-reinforced epoxy composite (UTCSE, which had a storage modulus of 2.1 GPa). The glass transition temperature (Tg), where the tan δ curve reaches its peak, was found to be 96.5°C for C1, 104°C for C2, 99°C for C3, and 118°C for C4. As with the storage modulus, C2 had the highest Tg, while C1 had the lowest. The increased Tg in C2 was a result of the restricted mobility of the epoxy resin caused by the stiff basalt fibres, which also reduced the viscoelastic lag. This limited dissipation of vibrational energy across the matrix led to a lower tan δ value. All four composites had Tg values higher than the 84.1°C observed for UTCSE. The incorporation of both basalt and coconut sheath fibres in hybrid composites improved both the storage modulus and the glass transition temperature, demonstrating their potential for enhancing mechanical and thermal properties. Biopolymer composites are becoming more popular in a variety of industries, including consumer products, packaging, automotive, and aerospace, due to their lightweight design, strong mechanical qualities, and environmentally beneficial attributes [25–28]. Their attractiveness as a sustainable alternative to conventional composites arises from their renewable nature and low environmental effect. These materials have major advantages, including biodegradability, reduced dependency on fossil fuels, and a lesser environmental imprint. The combination of natural fibres with biopolymers improves mechanical and thermal qualities while preserving low density and an attractive look. Notwithstanding these advantages, issues like moisture sensitivity and thermal stability require more investigation. All things considered, biopolymer composites are a viable and sustainable substitute for traditional polymer composites, aiding in the shift to more ecologically friendly raw materials and production techniques [29,30].
This study investigates sustainable biopolymer composites derived from coconut sheath and basalt fibers, which are recognized for their biodegradability, low environmental effect, and low carbon footprint. High specific strength, higher mechanical qualities, reduced weight, and greater thermal stability are all displayed by these composites. Four hybrid epoxy composites (C1–C4) were created utilizing five distinct stacking sequences and compression molding techniques, demonstrating that hybridization considerably enhances mechanical properties. The hybrid and pure basalt fiber composites have larger storage moduli (up to 2.1 GPa) than the untreated coconut sheath fiber-reinforced epoxy. The composite C4 also had the greatest glass transition temperature (Tg), which was 118°C. Applications in the electronics, packaging, automotive, and construction sectors all benefit from these affordable, non-toxic composites. The mechanical parameters of the hybrid composites, notably the C2 variety, show potential increases in specific strength, tensile, flexural, and impact resistance when compared to untreated coconut sheath fiber composites. To put these results into perspective, a comparison with other widely used biopolymer composites demonstrates the C2 composite’s competitive advantage in terms of mechanical performance. C2’s improved qualities are likely due to its optimal stacking sequence and the synergistic interaction of coconut sheath and basalt fibers, which promotes load transmission and matrix reinforcement. This formulation provides a balanced gain in mechanical strength and durability, making it an excellent choice for long-term applications in sectors that require lightweight and high-strength materials.
Hybrid epoxy composites reinforced with basalt fibre and coconut sheath have been successfully developed using compression moulding. The integration of basalt fibre with coconut sheath in these hybrid epoxy composites shows promising results, presenting an eco-friendly and sustainable alternative to conventional reinforced polymer composites. Biopolymer composites offer notable advantages including biodegradability, reduced carbon footprint, and reliance on renewable resources that align well with the global focus on environmental responsibility and sustainability. These composites demonstrate impressive material properties, such as high specific strength, lightweight design, and excellent mechanical performance, while also ensuring non-toxicity and safe handling. The hybrid composites exhibit superior tensile, flexural, and impact strengths compared to composites reinforced with untreated coconut sheath fibre alone. Among the tested variations, the C2 composite displays the highest mechanical properties. These composites also offer economic advantages, including cost-effectiveness and potential support for local economies, enhancing their appeal for widespread use. The versatility and potential of biopolymer composites make them suitable for a range of applications across different industries. With ongoing research and development, these materials are likely to have a significant impact on material science, contributing to the advancement of a more sustainable and environmentally responsible society. This study underscores that combining basalt fibre with coconut sheath fibre and epoxy substantially enhances the mechanical properties of hybrid composites, making them viable for applications in construction and related fields.
Acknowledgement: The authors acknowledge Mayakrishnan Gopiraman, Shinshu University, Japan for the fruitful discussions for the biopolymer material as an edible coating application.
Funding Statement: Seong Cheol Kim greatly acknowledges the Basic Science Research Program through the National Research Foundation of Korea (NRF) funded by the Ministry of Education (2020R1I1A3052258) for financial support.
Author Contributions: Conceptualization, writing—review & editing and funding acquisition: Subburayan Manickavasagam Suresh Kumar; software, data curation, project administration: Sundaravel Balachandran; validation, supervision: Seong Cheol Kim; resources,writing—original draft preparation, visualization & supervision: Balamurugan Rathinam; conceptualization, writing—original draft preparation & writing—review and editing: Vanaraj Ramkumar. All authors reviewed the results and approved the final version of the manuscript.
Availability of Data and Materials: The datasets generated and/or analyzed during the current study are available from the corresponding author on reasonable request.
Ethics Approval: Not applicable.
Conflicts of Interest: The authors declare that they have no conflicts of interest to report regarding the present study.
References
1. Fiore V, Calabrese L, Di Bella G, Scalici T, Galtieri G, Valenza A, et al. Effects of aging in salt spray conditions on flax and flax/basalt reinforced composites: wettability and dynamic mechanical properties. Compos B: Eng. 2016;93:35–42. doi:10.1016/j.compositesb.2016.02.057. [Google Scholar] [CrossRef]
2. Elanchezhian C, Vijaya Ramnath B, Ramakrishnan G, Rajendrakumar M, Naveenkumar V, Saravanakumar MK. Review on mechanical properties of natural fibre composites. Mater Today: Proc. 2018;5:1785–90. doi:10.1016/j.matpr.2017.11.276. [Google Scholar] [CrossRef]
3. Maiti S, Islam MR, Uddin MA, Afroj S, Eichhorn SJ, Karim N. Sustainable fibre-reinforced composites: a review. Adv Sustain Syst. 2022;6(11):2200258. doi:10.1002/adsu.202200258. [Google Scholar] [CrossRef]
4. Libonati F, Vellwock AE, Ielmini F, Abliz D, Ziegmann G, Vergani L. Bone-inspired enhanced fracture toughness of de novo fibre reinforced composites. Sci Rep. 2019;9(1):1–12. doi:10.1038/s41598-019-39030-7. [Google Scholar] [PubMed] [CrossRef]
5. Ahmed H, Rahaman Noyon MA, Uddin ME, Jamal M, Palaniappan SK. Biodegradable and flexible fibre-reinforced composite sheet from tannery solid wastes: an approach of waste minimization. Polym Compos. 2023;44(11):7545–56. doi:10.1002/pc.27644. [Google Scholar] [CrossRef]
6. Saba N, Paridah MT, Jawaid M. Mechanical properties of kenaf fibre reinforced polymer composite: a review. Constr Build Mater. 2015;76:87–96. doi:10.1016/j.conbuildmat.2014.11.043. [Google Scholar] [CrossRef]
7. Saba N, Paridah MT, Abdan K, Ibrahim NA. Effect of oil palm nano filler on mechanical and morphological properties of kenaf reinforced epoxy composites. Constr Build Mater. 2016;123:15–26. doi:10.1016/j.conbuildmat.2016.06.131. [Google Scholar] [CrossRef]
8. Özduman ZC, Oglakci B, Halacoglu Bagis DM, Aydogan Temel B, Eliguzeloglu Dalkilic E. Comparison of a nanofibre-reinforced composite with different types of composite resins. Polymers. 2022;15(17):3628. doi:10.3390/polym15173628. [Google Scholar] [PubMed] [CrossRef]
9. Sayam A, Rahman ANMM, Rahman MS, Smriti SA, Ahmed F, Rabbi MF. A review on carbon fibre-reinforced hierarchical composites: mechanical performance, manufacturing process, structural applications and allied challenges. Carbon Lett. 2022;32(5):1173–205. doi:10.1007/s42823-022-00358-2. [Google Scholar] [CrossRef]
10. Babu NK, Mensah RA, Shanmugam V, Rashedi A, Athimoolam P, Aseer JR. Self-reinforced polymer composites: an opportunity to recycle plastic wastes and their future trends. J Appl Polym Sci. 2022;139(46):53143. doi:10.1002/app.53143. [Google Scholar] [CrossRef]
11. Jawaid M, Khalil HPSA. Cellulosic/synthetic fibre reinforced polymer hybrid composites: a review. Carbohydr Polym. 2011;86:1–18. doi:10.1016/j.carbpol.2011.04.043. [Google Scholar] [CrossRef]
12. Dhakal HN, Zhang ZY, Guthrie R, MacMullen J, Bennett N. Development of flax/carbon fibre hybrid composites for enhanced properties. Carbohydr Polym. 2013;96:1–8. doi:10.1016/j.carbpol.2013.03.074. [Google Scholar] [PubMed] [CrossRef]
13. Ku H, Wang H, Pattarachaiyakoop N, Trada M. A review on the tensile properties of natural fibre reinforced polymer composites. Compos B Eng. 2011;42(4):856–73. doi:10.1016/j.compositesb.2011.01.010. [Google Scholar] [CrossRef]
14. Vigneshwaran S, Sundarakannan R, John K, Joel Johnson RD, Prasath KA, Ajith S, et al. Recent advancement in the natural fibre polymer composites: a comprehensive review. J Clean Prod. 2020;277:124109. doi:10.1016/j.jclepro.2020.124109. [Google Scholar] [CrossRef]
15. AL-Oqla FM, Sapuan S. Natural fibre reinforced polymer composites in industrial applications: feasibility of date palm fibres for sustainable automotive industry. J Clean Prod. 2014;66:347–54. doi:10.1016/j.jclepro.2013.10.050. [Google Scholar] [CrossRef]
16. Rao H, Kumar M, Reddy G. Hybrid composites: effect of fibres on mechanical properties. Int J Biol Macromol. 2011;1:9–14. [Google Scholar]
17. Mishra S, Mohanty A, Drzal L, Misra M, Parija S, Nayak S. Studies on mechanical performance of biofibre/glass reinforced polyester hybrid composites. Compos Sci Technol. 2003;63:1377–85. doi:10.1016/S0266-3538(03)00084-8. [Google Scholar] [CrossRef]
18. Sule U. Studies on the properties of short okra/glass fibres reinforced epoxy hybrid composites. Int J Eng Sci Technol. 2013;204(2):260–5. [Google Scholar]
19. Braga RA, Magalhaes JrPAA. Analysis of the mechanical and thermal properties of jute and glass fibre as reinforcement epoxy hybrid composites. Mater Sci Eng C. 2015;56:269–73. doi:10.1016/j.msec.2015.06.031. [Google Scholar] [PubMed] [CrossRef]
20. Atiqah A, Maleque MA, Jawaid M, Iqbal M. Development of kenaf-glass reinforced unsaturated polyester hybrid composite for structural applications. Compos B Eng. 2014;56:68–73. doi:10.1016/j.compositesb.2013.08.019. [Google Scholar] [CrossRef]
21. Militky J, Kovacic V, Rubnerova J. Influence of thermal treatment on tensile failure of basalt. Eng Fract Mech. 2002;69(9):1025–33. doi:10.1016/S0013-7944(01)00119-9. [Google Scholar] [CrossRef]
22. Deak T, Czigany T. Chemical composition and mechanical properties of basalt and glass fibres–a comparison. Text Res J. 2009;79:645–51. doi:10.1177/0040517508095597. [Google Scholar] [CrossRef]
23. Morova N. Investigation of usability of basalt fibres in hot mix asphalt concrete. Constr Build Mater. 2013;47:175–80. doi:10.1016/j.conbuildmat.2013.04.048. [Google Scholar] [CrossRef]
24. Sim J, Park C, Moon DY. Characteristics of basalt fibre as a strengthening material for concrete structures. Compos B Eng. 2005;36:504–12. doi:10.1016/j.compositesb.2005.02.002. [Google Scholar] [CrossRef]
25. Prakash SO, Sahu P, Madhan M, Santhosh AJ. A review on natural fibre-reinforced biopolymer composites: properties and applications. Int J Polym Sci. 2022;1:7820731. doi:10.1155/2022/7820731. [Google Scholar] [CrossRef]
26. Sadasivuni KK, Saha P, Adhikari J, Deshmukh K, Ahamed MB, Cabibihan J. Recent advances in mechanical properties of biopolymer composites: a review. Polym Compos. 2019;41(1):32–59. doi:10.1002/pc.25356. [Google Scholar] [CrossRef]
27. Demirel A, Yılmaz E, Türk S, Çalışkan F. Preparation and investigation of porous chitosan/carbon nanotube biocomposite coating by space holder method. Diam Relat Mater. 2023;138:110217. doi:10.1016/j.diamond.2023.110217. [Google Scholar] [CrossRef]
28. Sukhova AA, Gofman IV, Skorik YA. Preparation and properties of chitosan-nanodiamond dispersions and composite films. Diam Relat Mater. 2019;98:107483. doi:10.1016/j.diamond.2019.107483. [Google Scholar] [CrossRef]
29. Santos NS, Silva MR, Alves JL. Reinforcement of a biopolymer matrix by lignocellulosic agro-waste. Procedia Eng. 2016;200:422–7. doi:10.1016/j.proeng.2017.07.059. [Google Scholar] [CrossRef]
30. Bari E, Sistani A, Morrell JJ, Pizzi A, Akbari MR, Ribera J. Current strategies for the production of sustainable biopolymer composites. Polymers. 2020;13(17):2878. doi:10.3390/polym13172878. [Google Scholar] [PubMed] [CrossRef]
Cite This Article
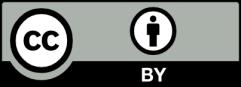
This work is licensed under a Creative Commons Attribution 4.0 International License , which permits unrestricted use, distribution, and reproduction in any medium, provided the original work is properly cited.