Open Access
ARTICLE
Quasi-Static and Low-Frequency Dynamic Mechanical Analysis Characterization of Graphene Nanoplatelets/Glass Fabric/Bisphenol-A-Based Epoxy Nanocomposites
1 Centre of Excellence in Digital Manufacturing, Department of Mechanical Engineering, Rajalakshmi Engineering College, Chennai, 602015, India
2 Department of Management Studies, Rajalakshmi Engineering College, Chennai, 602105, India
* Corresponding Author: Venkateshwaran Narayanan. Email:
Journal of Polymer Materials 2024, 41(3), 105-116. https://doi.org/10.32604/jpm.2024.056744
Received 30 July 2024; Accepted 05 September 2024; Issue published 30 September 2024
Abstract
Glass fabric/polymer composites are widely used in various industrial applications due to their lightweight, exceptional strength, and fatigue resistance. Graphene nanoplatelets, a recently developed type of carbon material, stand out as unique nanofillers due to their 2D quantum confinement and expansive surface area within a polymer matrix. These features make them more effective than traditional carbon nanofillers at enhancing a range of properties. In this study, 3-weight % of graphene nanoplatelets with epoxy resin were used for investigation by varying sonication durations (0, 20, 40, and 60 min) using an ultrasonic bath sonicator. The laminates were made using the hand layup technique followed by compression molding to reduce the void content. Mechanical and dynamic mechanical characteristics of the fabricated nanocomposites were investigated. Tensile strength, Tensile modulus, and Flexural modulus were increased by 12.63%, 10.76%, and 32.55%, respectively, when the sonification duration was 40 min. The dynamic mechanical analysis at 1, 5, and 10 Hz frequencies to study the viscoelastic behavior of samples. From dynamic mechanical analysis, the sample with a 40-min sonication duration was observed to have better properties than the other samples.Keywords
A wide variety of materials have been utilized in the design and manufacturing of numerous engineering applications. These materials vary from those that have been available for centuries (copper, cast iron, brass) to those that have only recently been developed (composites, ceramics, high-performance steel, etc.) [1,2]. A composite material comprises two or more synergistic microconstituents that differ in physical form or chemical composition. Their main advantage is that they combine the properties of their substances, resulting in mechanical behavior that is superior to that of the initial materials [3–5]. Suitable glass fiber orientation and compositions resulted in the desired characteristics and functionality of Glass Fiber Reinforced Polymer (GFRP) composites comparable to steel, with larger tensile strength than aluminum and lower relative density than steel [4,6]. The polymer composites are reinforced with nanofillers as platelets with thicknesses of the order of 10–9 m. Because of the longer interfacial area between the nanofillers and the polymers, polymer nanocomposites have distinct physical and mechanical properties. Various nanofillers added are Graphene, Graphene Oxide, Carbon nanotubes, etc. Graphene nanoplatelets comprise layered 2-D graphene sheets with excellent electrical, thermal, and mechanical properties [7]. Graphene nanoplatelets are newly developed carbon materials. Graphene nanoplatelets are unique nanofillers because of their 2D quantum confinement and high surface area in a polymer matrix, making them superior to conventional carbon nanofillers in their capacity to adjust most properties [1,8]. The mechanical performance of fiber-reinforced epoxy composites was improved when GnPs were included into the polymer matrix [9,10].
Carbon nanomaterials have been recognized for developing massive agglomerates because of their large surface area and significant van der Waals forces. Therefore, dispersing these substances in a viscous media, such as in polymer solutions is a difficult task. Poor dispersion of carbon nanomaterials diminishes their effectiveness as reinforcement by reducing crosslinking density and causing nanoparticle slippage under load. This results in a decline in the composite properties compared to the neat matrix [11]. The dispersal method has a major impact on the structure of GnPs leading to the development of residual strains and defects in composites [12]. Sonication is one of the most frequent methods for dispersing graphene nanoparticles. The sonication method is widely used in two forms: sonication bath and probe sonication; it changes the morphology of the graphene, giving it a wrinkled application [9,13,14]. Dynamic mechanical analysis is one of the most efficient methods for investigating the mechanical characteristics of materials, as it allows for the study of rheology at various temperatures, frequencies, or loadings. These experiments in practice can determine storage modulus, loss modulus, Tan D, and glass transition temperature (Tg). Many amorphous polymers are hard and stiff below this temperature but soften once they reach it [15,16]. In this work, an attempt was made to study the dynamic mechanical analysis of GnPs/GFRP composite by varying the sonication durations in the preparation of the GnPs reinforced epoxy resin, and 3 weight % of GnPs was taken for various sonication durations because of its better mechanical properties [17].
A bidirectional glass fiber mat of 360 g/m2 was used as reinforcement in this study. The matrix material, bisphenol-A-based epoxy resin (LY556) with 1.15 to 1.20 g/cm3 density at 25°C and hardener (HY951) with 0.95 to 1.05 g/cm3 density at 25°C was used to fabricate the laminates. The glass fabric, resin, and hardener were purchased from Javanthee Enterprises, Chennai, India. In addition, with bisphenol-A-based epoxy resin, the GnPs (grade C-300) with 300 m2/g surface area, relative density of 2 to 2.25 g/cm3, particle size of less the 2 µm in length, and few nm thickness were added to satisfy the base of the nanocomposite. The graphene nanoplatelets (GnPs) were purchased from Sigma-Aldrich Chemicals Private Limited, Banglore, Karnataka, India.
2.2.1 Fabrication of Graphene nanoplatelets/Glass fabric/Epoxy nanocomposite
Graphene nanoplatelets (GnPs) reinforced epoxy resin was prepared with 3 wt% GnPs. Initially, after adding GnPs to the epoxy resin, a mechanical stirrer was used for 25 min to improve the homogeneity of the nanoparticles in the polymer resin [10]. Agglomeration can still happen at the nanoparticle-resin interface, even after mechanical stirring. Because of the weak interface between GnPs and epoxy, no transfer of load to the nanofiller is possible. Because of this, nanofillers act as stress concentrators, which results in nano-mechanical composites being less effective. To enhance the dispersion of nanoparticles in the resin, sonication was used here. Sonication is the process of sending sound waves of high frequency through a combination of discrete elements to blend them [18]. So, the GnPs added epoxy resin is prepared through a sonication process. Sonication reduces the size of the clusters when the GnPs are mixed into the matrix material [19,20]. Here, a sonication bath was employed so that the present research work can be easily adapted to large-scale industries. In this study, the Sonication duration for preparing GnPs reinforced resin was varied as 0, 20, 40, and 60 min. The other parameters in the sonication bath, such as power and frequency, were kept at 100 W and 28 KHz, respectively. As per the manufacturer’s recommendation, the prepared GnPs/epoxy resin was combined with the hardener at a weight ratio of 10:1. Then, a mechanical stirrer was used to mix the resin for 5 min to ensure homogeneity. Four-layer bidirectional E-glass fabric of 360 m2/g was used as reinforcement for the laminate preparation. The hand layup method was used to fabricate the laminates, which were then subjected to a compressive load of 5 kg to improve compaction. The laminates were kept at ambient temperature for 24 h to allow for drying and bonding [21]. The diagrammatic representation for the preparation of the resin, laminate fabrication, pictorial representation of the inner structure, and testing specimens preparation is illustrated in Fig. 1. Here, the GnPs are homogenously distributed into the glass fabric/epoxy nanocomposites.
Figure 1: Illustration of GnPs/glass fabric/Epoxy nanocomposite fabrication
a) GnPs of 3 percentage weight ratio to epoxy is measured.
b) Mechanical stirring of the GnPs added resin for 25 min at 200 rpm.
c) Sonication of GnPs mixed resin at various durations like 20, 40 and 60 min.
d) Mixing of hardener into the sonicated resin and manual stirring for 5 min.
e) Fabrication of 4-layer bidirectional glass fiber (360 gsm) with GnPs mixed resin by using Hand Layup Technique.
f) The pictorial representation of the inner structure of the GnPs/glass fabric/epoxy laminates is illustrated.
g) Specimens for Mechanical Characterization and Dynamic Mechanical Analysis.
2.2.2 Mechanical Characterization
In this investigation, a computerised Universal Testing Machine with a 50 kN load cell was used. In accordance with the ASTM 3039/3039M standard [22], with the following dimensions: 126 mm × 13 mm × 1.8 mm using a water jet machine. The test was conducted with a test speed of 2 mm/min with a gauge length of 50 mm. End tabs were used since the specimen thickness was less than 2 mm, as recommended by the ASTM Standard. As per the ASTM D790-03 std [23], flexural testing specimens were cut with the following dimensions: 126 mm × 13 mm × 1.8 mm using water jet machining. With a span length of 52 mm, the 3-point flexural test was conducted at a test speed of 2 mm/min.
2.2.3 Dynamic Mechanical Analysis (DMA)
This analysis primarily uses the storage modulus, loss modulus, and loss factor to identify the viscoelastic properties of a material. It characterizes the relation between stress and strain in the elasticity area. The mechanical properties like tensile strength, flexural strength, tensile modulus, and flexural modulus were studied for the various GnP percentages with various sonication durations, and from the observations, it is decided that the laminate with 3% GnPs will have optimal mechanical characteristics in comparison with other combinations [17]. The dynamic mechanical analysis of Graphene nanoplatelets (GnPs)/GFRP composite was performed with a HITACHI DMA7100 machine. In this study, four samples with 3% graphene nanoplatelets and the time spent for the sonication during the preparation of the GnPs/epoxy resin were taken as 0, 20, 40, and 60 min. The rectangular specimens for DMA were prepared as per ASTM D5023 std. and taken for analysis [24]. The specimens were tested in three-point bending mode by varying the temperature range from 25°C to 160°C at 1, 5, and 10 Hz frequencies.
By varying the sonication period, composites with glass fabric and GnPs reinforcement were produced. The samples were examined in accordance with ASTM standards. The study that looked at how the duration of the sonication affected the composite’s viscoelasticity is discussed below.
3.1 Tensile and Flexural Behaviour of Graphene Nanoplatelets/Glass Fabric/Epoxy Composites
Fig. 2 presents the Stress-Strain curves from tensile testing, offering a visual depiction of the material’s response under tension. These curves elucidate critical mechanical properties such as elasticity, yield strength, and ultimate tensile strength. Analyzing these graphs helps in assessing the material’s suitability for various engineering applications. Fig. 3 illustrates the impact of sonication duration on the mechanical behaviour of the 3% GnPs/glass fabric/Epoxy nanocomposites. The process of sonication is instrumental in improving the bonding between GnPs and the matrix material. Tensile strength progressively rises to 12.63% as the sonication duration increases from 0 to 40 min, and the pattern reverses from 40 to 60 min sonication duration. In general, higher dispersion of nanofillers inside the polymer matrix is achieved with longer sonication periods. There’s usually a maximum duration for sonication, after which excessive sonication can cause filler agglomeration or damage, which could reduce mechanical qualities. As the sonication time increases from 0–40 min, the agglomerates of the nanofiller are broken down to ease the dispersion of the fillers [25]. Better dispersion creates more effective load transfer channels, which can improve mechanical qualities like modulus and tensile strength. The primary reason for this improvement is that the load transfer and stress distribution are more effectively achieved due to improved dispersion and interfacial adhesion between the nanofillers and the polymer matrix. Better dispersion can increase the strength of the composites by lowering the possibility of weak spots and stress concentrations in the material. Because of their large surface area and significant van der Waals forces, GnPs tend to aggregate into large clusters with an increase in duration beyond an optimum value [26,27]. Sonication initially helps in reducing the agglomeration till 40 min of sonication, and the GnPs begin to be fractured with longer sonication. Tensile modulus progressively rises up to 14.35% with the increase in sonication duration from 0 to 60 min. Flexural strength gradually decreases to 12.05% when the sonication duration increases from 0 to 60 min. Sonication modifies the surface morphology of GnPs, which in turn affects the flexural properties of nanocomposites. During sonication, the surface structure of GnPs is transformed from planer to wrinkled [12,20]. Due to the wrinkled surface, there are areas of significant tension concentration when a vertical bending force is applied. As the duration of sonication increases, the wrinkly surface of GnPs becomes sharper, resulting in a decrease in flexural strength. Flexural modulus increases up to 32.55% with the progressive rise in sonication duration from 0 to 40 min, and the pattern reverses from 40 to 60 mm sonication duration. A similar kind of observation was also observed in various studies [28,29].
Figure 2: Stress-Strain curves of the 3 wt% GnPs/GFRP laminate prepared using various sonication duration (a) 0 min, (b) 20 min, (c) 40 min and (d) 60 min
Figure 3: Effect of sonication duration on the mechanical properties of the 3 wt% GnPs/GFRP laminate
3.2 Dynamic Mechanical Analysis
An essential tool for characterising polymer nanocomposites is dynamic mechanical analysis or DMA. It evaluates mechanical characteristics such as viscoelasticity, damping, and stiffness, revealing the effects of nanofillers on overall performance. It assesses filler dispersion, an essential component of reinforcing effectiveness. Given that these composites behave differently depending on the environment, DMA is essential for measuring characteristics at various temperatures and frequencies.
3.2.1 Effect of Sonication Duration on Storage Modulus (E′)
Storage modulus (E′) represents the ability of the polymer material to store energy during the loading cycle and is related to the stiffness of the material. Fig. 4 illustrates the effect of temperature on the storage modulus for the sample of 3% GnPs at 1, 5 and 10 Hz frequencies. The storage modulus (E′) plot has four distinct regions (Glassy, Transition and rubbery and finally the viscoelastic) as the temperature rises. The composite structure is extremely rigid in the first stage because the molecules are tightly packed together. In the second stage, it was observed that polymeric chain motion occurs above the glass transition temperature (Tg) in the second glass transition phase, resulting in a lower storage modulus (E′). The movement in the polymeric chain will influence the stiffness and reinforcement/matrix bonding. In the third stage, due to the increased polymeric chain movement at the elevated temperature, there was no significant variation in E′ (rubbery plateau) [30]. Because most of the polymer chains freeze at lower temperatures (>60), stiffness significantly decreases in glassy regions of the composites, where E′ has its peak value [31]. Furthermore, it was noticed that E′ increased as the frequency increased from 1 to 10 Hz. Sonication has a significant influence, as evidenced by the rise in E′ at all frequencies. A dramatic decrease in storage modulus for the composites above the Tg was observed in the transition region. This could increase the molecular mobility caused by composite softening, which reduces stiffness at higher temperature [32]. In the elastic zone, where long polymer chain movement occurs, a smaller change of frequency can possibly be identified at elevated temperatures. At its lowest value, E′ was nearly constant. The frequency could become ineffective because it is unable to influence the motion of polymer chains at higher temperatures. Storage modulus rises with frequency in the following sequence in all cases: E10Hz > E5Hz > E1Hz. The rise in storage modulus with frequency was observed because polymer composite segments have less relaxation time for increasing the frequency. An additional cause for this outcome could be that the movement of polymer chains is lesser at higher frequencies, which increases stiffness, i.e., storage modulus [32,33]. Further, from the plot, the increase in the sonication time up to 40 min increases the crosslinking, which attribute to the increase in storage modulus values [34].
Figure 4: Effect of sonication duration on storage modulus of 3 wt% GnPs/GFRP laminate at (a) 1 Hz (b) 5 Hz (c) 10 Hz
The effectiveness coefficient (C) of nanofillers was calculated to check the adhesion effectiveness and can be represented below:
C=E′G/E′R(Composite)E′G/E′R(Resin)
where E′G and E′R are the storage modulus values in the glassy and rubbery region, respectively. The C value was calculated at the c and 100°C. Table 1 shows the maximum value of C obtained for the samples without sonification, and the lowest value is observed for 40 min of sonication time. The lower the value of C, the better the adhesion between filler and matrix. It is significant to note that the packing of the polymer chains and the strength of the intermolecular forces are the main factors influencing modulus in the glassy state [33]. This shows that an increase in the sonication duration of up to 40 min increases the interface and, thereby, the modulus.
3.2.2 Effect of Sonication Duration on Loss Modulus (E′′)
When comparing various systems at the same strain amplitude, the loss modulus E″ is a measurement of the energy lost as heat per cycle of sinusoidal deformation. It is the imaginary portion of the complex modulus and shows the viscous reaction of the materials as a result of the motion of the composite’s molecules. Loss modulus is the viscous response of the material and is more sensitive to the molecular movement. Fig. 5 illustrates the effect of temperature on the E” for the sample of 3% GnPs at various frequencies. At higher temperatures, the loss modulus curves reach a maximum and afterwards begin to decline, indicating that the polymer chains can move freely. Fig. 6 shows that at temperatures below the glass transition, the loss modulus peak values decrease with increasing sonication duration. Also, it was observed that with an increase in time, the loss modulus plot also broadens till 40 min of sonication time, and then it starts to narrow down. This broadening of the plot increases the glassy region because the fibres’ surrounding matrix differs physically from the remainder of the matrix, fibre, matrix, and immobilized polymer layer matrix [35]. Tg of viscous material is also a very useful parameter. Tg values derived from the highest peak of E′′(T) plot at various frequencies can be seen; E″ rises until it reaches its Tg and then goes down. E′′ increases as frequency increases. Additionally, as the frequency increased, the peak of the E″(T) plot was shifted to a higher temperature with a higher Tg value. Tg value increase with frequencies could explain the lower mobility of polymer chains at higher frequencies. Furthermore, the flow duration of the composite materials was shorter at high frequencies, increasing the value of E″. These findings are consistent with previous findings [36]. The loss modulus curve widening indicates a larger order range. A more widespread or elevated glass transition behaviour could result from improved limitations on the amorphous phase. Different physical states in the matrix around the fibre prevent molecules from moving freely, similar to an interlayer effect, which causes additional transitions.
Figure 5: Effect of sonication duration on loss modulus of 3 wt% GnPs/GFRP laminate at (a) 1 Hz (b) 5 Hz (c) 10 Hz
Figure 6: Effect of sonication on TanD of 3 wt% GnPs/GFRP laminate at (a) 1 Hz (b) 5 Hz (c) 10 Hz
3.2.3 Effect of Sonication Duration on Loss Factor (TanD)
The loss factor (TanD) is the proportion of scattered and stored energy, i.e., TanD = E″/E′. The greater the Tan delta peak, the more and more energy is lost, resulting in significant non-elastic deformation, and it is also related to the impact resistance of the material. When the reinforcement is incorporated into a matrix, damping is influenced. Because of the increased viscoelastic energy dissipation in the matrix material, shear stress concentrations at the reinforcement ends are mostly to blame. A further explanation might be the fibre’s elasticity. The TanD vs temperature of the sample with frequencies of 1, 5, 10 Hz is depicted in Fig. 6. In the sample without sonication, the value of Tg can be observed from the highest peak of the TanD plot at different frequencies. When the frequencies increase, the TanD value increases, and the Tg value increases. The Fig. 6 shows the damping properties of the nanocomposite, TanD is proportional to the ratio of energy dissipated to energy stored, called the loss tangent or damping factor. The decrease in loss factor values indicates an improvement in the interfacial bonding of composite materials. The interface adhesion decreases as the damping at the interfaces increases. The fibre primarily controls the strain such that there is less strain at the interface, which is thought to be the more dissipative part of the composite. The plot shows that the loss factor value decreases with an increase in the sonication duration. Also, observed that the sonication process widen the plot until 40 min duration. Hence, in a composite reinforced with nano fillers, inefficient packing occurs at lower sonication duration. As a result, there are more matrix-rich areas, which makes it simpler for the bonding to break at the interface. The adjacent fillers and fibres will stop the growth of cracks when the fibres are packed closer together. The polymer system’s nature can be inferred from the tan delta peak’s magnitude. The glass transition temperature without sonication is 80°C, and the Tg value slowly increases with the increase in the sonication time and reaches a maximum of 90°C at 40 min sonication due to enhanced interface bonding due to the proper distribution of the filler in the matrix [32]. Sonication also increases the crosslinking between the molecules, and the addition of fillers restricts the free movement of it. Further increasing the duration of sonication to 60 min results in the creation of hot spots and has a plasticising effect. Other than those of the constituents, the molecular movements in the interfacial area typically contribute to the material’s damping [24].
Graphene nanoplatelets (GnPs) reinforced glass fiber/bisphenol-A-based epoxy nanocomposite laminates with 3 wt% GnPs content (of epoxy) were developed. The sonication duration for the GnPs/bisphenol-A epoxy resin preparation varied: 0, 20, 40, and 60 min. Mechanical characterization revealed that a sonication duration of 40 min yielded the best results, demonstrating enhancements in the nanocomposite properties. Specifically, there was a 12.63% increase in tensile strength, a 10.76% increase in tensile modulus, and a 32.55% increase in flexural modulus. Dynamic mechanical analysis further supported these findings, indicating a beneficial effect of sonication; the highest improvements were noted in the storage modulus (E′) above the glass transition temperature (Tg) with 40 min of sonication. Additionally, the loss modulus curve became broader at this duration, suggesting improved adhesion at the interface, and the glass transition temperature shifted from 85.08°C to 93.39°C.
Acknowledgement: We extend our gratitude to the management of Rajalakshmi Engineering College for providing the necessary support and facilities to conduct the experimentation.
Funding Statement: The authors received no specific funding for this study.
Author Contributions: The authors confirm contribution to the paper as follows: Experimentation, result validation and draft report preparation: Santhanakrishnan Mamallan; Ideology, methods, results verification and validation: Venkateshwaran Narayanan; Verification of manuscript and final preparations: Canungo Bhimarao Ragotham. All authors reviewed the results and approved the final version of the manuscript.
Availability of Data and Materials: The datasets generated during and/or analyzed during the current study are available from the corresponding author on reasonable request.
Ethics Approval: Not applicable.
Conflicts of Interest: The authors declare that they have no conflicts of interest to report regarding the present study.
References
1. Yi X-S. An introduction to composite materials. In: Yi X-S, Du S, Zhang L, editors. Composite materials engineering, volume 1: fundamentals of composite materials. Singapore: Springer Singapore; 2018. p. 1–61. doi:10.1007/978-981-10-5696-3_1. [Google Scholar] [CrossRef]
2. Chen B, Li X, Li X, Jia Y, Yang J, Li C. Hierarchical carbon fiber-SiO2 hybrid/polyimide composites with enhanced thermal, mechanical, and tribological properties. Polym Compos. 2018;39:E1626–34. [Google Scholar]
3. Ye C, Wang YQ. Nonlinear forced vibration of functionally graded graphene platelet-reinforced metal foam cylindrical shells: internal resonances. Nonlinear Dyn. 2021;104(3):2051–69. doi:10.1007/s11071-021-06401-7. [Google Scholar] [CrossRef]
4. Yarlagaddaa J, Malkapuram R, Balamurugan K. Machining studies on various ply orientations of glass fiber composite. In: Arockiarajan A, Duraiselvam M, Raju R, editors. Advances in industrial automation and smart manufacturing. Singapore: Springer Singapore; 2021. p. 753–69. [Google Scholar]
5. Santos P, Silva AP, Reis PNB. The effect of carbon nanofibers on the mechanical performance of epoxy-based composites: a review. Polymers. 2024;16(15):2152.1–59. doi:10.3390/polym16152152. [Google Scholar] [PubMed] [CrossRef]
6. Ahmad F, Yuvaraj N, Bajpai PK. Effect of reinforcement architecture on the macroscopic mechanical properties of fiberous polymer composites: a review. Polym Compos. 2020;41(6):2518–34. doi:10.1002/pc.25666. [Google Scholar] [CrossRef]
7. Wang L, Wang W, Fu Y, Wang J, Lvov Y, Liu J, et al. Enhanced electrical and mechanical properties of rubber/graphene film through layer-by-layer electrostatic assembly. Compos Part B Eng. 2016;90:457–64. [Google Scholar]
8. King JA, Klimek DR, Miskioglu I, Odegard GM. Mechanical properties of graphene nanoplatelet/epoxy composites. J Appl Polym Sci. 2013;128(6):4217–23. [Google Scholar]
9. Arun S, Rama Sreekanth PS, Kanagaraj S. Mechanical characterisation of PMMA/SWNTs bone cement using nanoindenter. Mater Technol. 2014;29(sup1):B4–B9. doi:10.1179/1753555713Y.0000000111. [Google Scholar] [CrossRef]
10. Seretis GV, Kouzilos G, Manolakos DE, Provatidis CG. On the graphene nanoplatelets reinforcement of hand lay-up glass fabric/epoxy laminated composites. Compos Part B Eng. 2017;118(9):26–32. doi:10.1016/j.compositesb.2017.03.015. [Google Scholar] [CrossRef]
11. Tang LC, Wan YJ, Yan D, Pei YB, Zhao L, Li YB, et al. The effect of graphene dispersion on the mechanical properties of graphene/epoxy composites. Carbon N Y. 2013;60(5696):16–27. doi:10.1016/j.carbon.2013.03.050. [Google Scholar] [CrossRef]
12. Moriche R, Prolongo SG, Sánchez M, Jiménez-suárez A, Sayagués MJ, Ureña A. Composites: part B morphological changes on graphene nanoplatelets induced during dispersion into an epoxy resin by different methods. Compos Part B. 2015;72:199–205. doi:10.1016/j.compositesb.2014.12.012. [Google Scholar] [CrossRef]
13. Hu H, Gao Q, Tian G, Hong S, Zhao J, Zhao Y. The influence of topology and morphology of fillers on the conductivity and mechanical properties of rubber composites. J Polym Res. 2018;25(4):87. doi:10.1007/s10965-018-1478-6. [Google Scholar] [CrossRef]
14. Seretis GV, Theodorakopoulos ID, Manolakos DE, Provatidis CG. Effect of sonication on the mechanical response of graphene nanoplatelets/glass fabric/epoxy laminated nanocomposites. Compos Part B Eng. 2018;147:33–41. doi:10.1016/j.compositesb.2018.04.034. [Google Scholar] [CrossRef]
15. Zeltmann SE, Prakash KA, Doddamani M, Gupta N. Prediction of modulus at various strain rates from dynamic mechanical analysis data for polymer matrix composites. Compos Part B Eng. 2017;120(1):27–34. doi:10.1016/j.compositesb.2017.03.062. [Google Scholar] [CrossRef]
16. Mohana Krishnudu D, Sreeramulu D, Venkateshwar Reddy P. A study of filler content influence on dynamic mechanical and thermal characteristics of coir and luffa cylindrica reinforced hybrid composites. Constr Build Mater. 2020;251:119040. doi:10.1016/j.conbuildmat.2020.119040. [Google Scholar] [CrossRef]
17. Mamallan S, Narayanan V. Demystifying the role of graphene nanoplatelets percentage and sonication duration on the mechanical properties of the glass fabric/graphene nanoplatelets hybrid nano-composite. Polym Compos. 2022;43(11):8170–80. doi:10.1002/pc.26985. [Google Scholar] [CrossRef]
18. Seetharaman A, Narayanan V. Effect of aluminosilicate nanoclay on polyester composites’ static and dynamic mechanical properties. Polym Compos. 2022;43(10):7290–302. doi:10.1002/pc.26794. [Google Scholar] [CrossRef]
19. Wang Z, Fan J, Guo X, Ji J, Sun Z. Enhanced permittivity of negative permittivity middle-layer sandwich polymer matrix composites through conductive filling with flake MAX phase ceramics. RSC Adv. 2020;10(45):27025–32. doi:10.1039/D0RA03493B. [Google Scholar] [PubMed] [CrossRef]
20. Prolongo SG, Moriche R, Sánchez M, Ureña A. Advantages and disadvantages of the addition of graphene nanoplatelets to epoxy resins. Eur Polym J. 2014;61:206–14. doi:10.1016/j.eurpolymj.2014.09.022. [Google Scholar] [CrossRef]
21. Megahed M, Megahed AA, Agwa MA. Mechanical properties of on/off-axis loading for hybrid glass fiber reinforced epoxy filled with silica and carbon black nanoparticles. Mater Technol. 2018;7857(6):1–8. doi:10.1080/10667857.2018.1454022. [Google Scholar] [CrossRef]
22. ASTM. ASTM D3039/D3039M-17. Standard test method for tensile properties of polymer matrix composite materilas. Annu B ASTM Stand. 2017;1–13. doi:10.1520/D3039_D3039M-17. [Google Scholar] [CrossRef]
23. ASTM. ASTM D790-17. Standard test methods for flexural properties of unreinforced and reinforced plastics and electrical insulating materials. Annu B ASTM Stand. 2017;1–12. doi:10.1520/D790-17. [Google Scholar] [CrossRef]
24. ASTM. ASTM D5023-23. Standard test methods for plastics: dynamic mechanical properties: in flexure (Three-Point Bending) D5023-15. Annu B ASTM Stand. 2023;1–12. doi:10.1520/D5023-23. [Google Scholar] [CrossRef]
25. Gao Y, Jing HW, Chen SJ, Du MR, Chen WQ, Duan WH. Influence of ultrasonication on the dispersion and enhancing effect of graphene oxide-carbon nanotube hybrid nanoreinforcement in cementitious composite. Compos Part B Eng. 2019;164(2):45–53. doi:10.1016/j.compositesb.2018.11.066. [Google Scholar] [CrossRef]
26. Alasfar RH, Ahzi S, Barth N, Kochkodan V, Khraisheh M, Koç M, et al. A review on the modeling of the elastic modulus and yield stress of polymers and polymer nanocomposites: effect of temperature, loading rate and porosity. Polymers. 2022;14(3):360:1–31. doi:10.3390/polym14030360. [Google Scholar] [PubMed] [CrossRef]
27. Sheehan PE, Lieber CM. Friction between van der Waals solids during lattice directed sliding. Nano Lett. 2017;17(7):4116–21. [Google Scholar] [PubMed]
28. Mendes de Oliveira M, Forsberg S, Selegård L, Carastan DJ. The influence of sonication processing conditions on electrical and mechanical properties of single and hybrid epoxy nanocomposites filled with carbon nanoparticles. Polymers. 2021;13(23):4128:1–20. doi:10.3390/polym13234128. [Google Scholar] [PubMed] [CrossRef]
29. Nadiv R, Shtein M, Shachar G, Varenik M, Regev O. Optimal nanomaterial concentration: harnessing percolation theory to enhance polymer nanocomposite performance. Nanotechnology. 2017;28(30):305701. doi:10.1088/1361-6528/aa793e. [Google Scholar] [PubMed] [CrossRef]
30. Kuzak SG, Shanmugam A. Dynamic mechanical analysis of fiber-reinforced phenolics. J Appl Polym Sci. 1998;73:649–58. doi:10.1002/(SICI)1097-4628(19990801)73:53.0.CO;2-B. [Google Scholar] [CrossRef]
31. Gupta MK. Effect of frequencies on dynamic mechanical properties of hybrid jute/sisal fibre reinforced epoxy composite. Adv Mater Process Technol. 2017;3(4):651–64. doi:10.1080/2374068X.2017.1365443. [Google Scholar] [CrossRef]
32. Feng J, Guo Z. Effects of temperature and frequency on dynamic mechanical properties of glass/epoxy composites. J Mater Sci. 2016;51(5):2747–58. doi:10.1007/s10853-015-9589-5. [Google Scholar] [CrossRef]
33. Gupta MK. Effect of variation in frequencies on dynamic mechanical properties of jute fibre Reinforced epoxy composites. J Mater Environ Sci 2018;9(1):100–6. doi:10.26872/jmes.2018.9.1.12. [Google Scholar] [CrossRef]
34. Saba N, Jawaid M, Alothman OY, Paridah MT. A review on dynamic mechanical properties of natural fibre reinforced polymer composites. Constr Build Mater. 2016;106(3):149–59. doi:10.1016/j.conbuildmat.2015.12.075. [Google Scholar] [CrossRef]
35. Haris NIN, Hassan MZ, Ilyas RA, Suhot MA, Sapuan SM, Dolah R, et al. Dynamic mechanical properties of natural fiber reinforced hybrid polymer composites: a review. J Mater Res Technol. 2022;19(4):167–82. doi:10.1016/j.jmrt.2022.04.155. [Google Scholar] [CrossRef]
36. Gupta MK, Srivastava RK. Tribological and dynamic mechanical analysis of epoxy based hybrid sisal/jute composite. Indian J Engineer Materi Sci. 2016;23:37–44. [Google Scholar]
Cite This Article
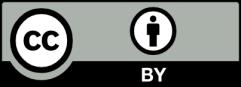
This work is licensed under a Creative Commons Attribution 4.0 International License , which permits unrestricted use, distribution, and reproduction in any medium, provided the original work is properly cited.