Open Access
ARTICLE
Effect of Selective Laser Sintering Polyamide-12 Powder as a Filler in Glass Fiber Reinforced Epoxy Composites
Central Institute of Petrochemicals Engineering & Technology (CIPET), School for Advanced Research in Polymers (SARP)-ARSTPS, Research & Development, Chennai, 600032, India
* Corresponding Author: Subbiah Rajkumar. Email:
Journal of Polymer Materials 2024, 41(3), 131-141. https://doi.org/10.32604/jpm.2024.055989
Received 10 March 2024; Accepted 16 April 2024; Issue published 30 September 2024
Abstract
In this study, the Polyamide-12 (PA-12) powdered material in the Selective Laser Sintering (SLS) process has been incorporated as the filler in the composite material to enhance its properties. The PA-12 powder has been made into a form of filament and is primarily used in the Fused Deposition Modelling (FDM) process. The PA-12 has been used with epoxy resin and glass fiber with different proportions. The characterization of materials, including the validation of the presence of PA-12 filler with epoxy, has been evidenced using Fourier Transform Infrared Spectroscopy (FTIR), Differential Scanning Calorimetry (DSC), and Thermogravimetric Analysis (TGA) identification methods. The mechanical characteristics of the 3 wt% PA-12 filled composite material showed increased tensile stress compared to other unfilled and 1 wt% filled materials. The contact angle of the 1 wt% PA-12 filler showed good agreement with improving the hydrophobic characteristics of the composite material. The rate of burning in the Horizontal position showed good results for the overall materials with self-extinguishing behavior. The morphological results of the glass fiber with epoxy and PA-12 filler showed better interference resulting in enhancing the mechanical characteristics than that of without fillers.Keywords
The continual advancements in specially blended additive manufacturing materials have expanded their applicability across various domains. The method for reusing used SLS PA-12 powder to enhance reusability has been studied to ease the disposal of waste SLS powder in landfills. Used PA-12 powder presents significant environmental concerns due to micro-particle grains, posing environmental hazards and causing global environmental setbacks. Many researchers are focused on sustainable development with used polymeric materials, which are in high demand to address the issue of disposing of used plastic materials in additive manufacturing processes [1]. This study also aims to effectively utilize PA-12 powder while enhancing composite properties. In one research study, Danuta’s investigation revealed notable improvements in mechanical and thermo-mechanical properties, attributed to the incorporation of both powder and fiber fillers into the epoxy matrix [2].
Generally, fillers improve the properties of fiber-reinforced composites, influencing their strength, heat resistance, and friction properties. This highlights the various uses of fillers in engineering, emphasizing their role in improving interfacial adhesion, water resistance, and other desired properties [3]. Sunil et al. investigated the materials used for the SLS technology for various applications. The materials used for SLS vary depending on the end usage applications, especially for biomedical implants and prostheses. The current research focuses on the Polyamide-12 material used in the SLS technology and it has been identified as one of the superior materials compared to other plastic materials due to its high strength, fire retardant, and fatigue characteristics, further, the waste materials also have the similar characteristics and it can be reprocessed for the future applications [4].
Gomes et al. validated the reuse of the SLS PA-12 powder in the same process. Although the characteristics of the material change on every cycle, post-processing methods of the PA-12 powder improvised the output of the SLS printed components [5]. The PA-12 powder was subjected to extremely high temperatures inside the chamber for the printing which caused the material to slightly shift to a new orientation in the molecular weight. The possibility percentage of the used and fresh PA-12 powder in the SLS manufacturing were maintained in the ratio of 67% and 33%, respectively [6,7]. Türk et al. studied how temperature affects PA12 mechanical properties. They found that as temperature increases, PA12 shows lower stress yields, increased elongation, and significant changes in tensile stiffness and strength [8]. The change in the properties such as surface finish, minimal melt flow rate, and shrinkage factors impulses in addition of more fresh powder in each SLS build, which results in better quality of the 3D printed components. The unused powder is not only considered a wastage but a threat to the environment. Feng et al. examined the reusability of the PA-12 powder for Fused Deposition Modeling (FDM). The mechanical properties of the reused PA-12 material showed 85%–95% of the virgin SLS PA-12 powder [9].
The used SLS powder has been utilized as a filament for the Fused Deposition Modeling (FDM) process for printing plastic components. The scope of usage for the PA-12 has been improvised for the improvement of composite materials by using SLS powder as a filler. Kishi et al. evaluated the effects of adding PA-12 particles in epoxy, which improved the fatigue characteristics compared to the pure epoxies [10]. The current study highlights the reuse of the PA-12 powder for improving the mechanical and water absorption characteristics of the GFRP composites. The proportion of mixing the PA-12 material to the epoxy resin with and without the fiber has also been studied.
Hand-layup process was used for manufacturing the sheet. The 300 mm3 × 300 mm3 × 4 mm3 square cavity plate was manufactured with 4 ejector pins for preparing the specimen as per the specific percentage of PA-12 filler mat with glass fiber and epoxy.
2.1 Preparation of the Fiber Mat
An E-glass fabric of 300 GSM was used as a fiber which was procured from Go Green Composites, Chennai, TamilNadu, India. The mat was procured in the form of roll and the mat has been trimmed with the cutting scissors in to a square mat of 200 mm2 × 200 mm2. The fabric was pretreated up to 110°C at hot air oven for 2 h to remove the moisture. The thickness of the specimen was maintained 3 to 5 mm for the testing, 3 mats of 1.3 mm thickness each with an overall thickness of 3.9 mm were trimmed and prepared for fabrication.
2.2 Preparation of the Matrix with the Reused PA-12 Filler
The epoxy resin has been used as a matrix for composite preparation. The Epoxy resin of grade Araldite LY-556 with the hardener HY-951 were used in the ratio of 1:10 proportion. Initially, the overall volume of the cavity inside the mold has been calculated and accordingly, the resin and the filler, weight of the filler has been taken up to 3 wt% from the overall weight of the resin. The resin is stirred well before the addition of the filler (PA-12). The volume of the mold has been measured as 540 cm3, the required quantity of epoxy has been weighed and stirred continuously using an overhead stirrer, and finally sonicated. The PA-12 filler was added and stirred continuously for 30 min at 60°C and sonicated for one hour to avoid agglomeration of the PA-12 particles to the epoxy resin. The hardener of 1 wt% has been added to the resin. The resin weight has been calculated as 0.396 kg for pure epoxy content and poured over the mold. The poured resin has been allowed to cure for 24 h at room temperature. Similarly, the mat has been prepared with glass fiber and epoxy resin and allowed to cure. After curing the sample has been removed using the ejector pins from the mold. The prepared mat and epoxy sheet have been trimmed using water jet machining for further analyzing the mechanical properties.
2.3 Fourier Transform Infrared Spectroscopy (FTIR)
Fourier Transform Infrared Spectroscopy (FTIR) spectra were noted using Thermo Fisher Scientific Inc., Waltham, MA, USA model no Nicolet 6700 making the spectrum range of the machine from 500 to 4000 cm−1 with a resolution of 4 cm−1.
2.4 Differential Scanning Calorimeter (DSC)
The Differential Scanning Calorimeter data were drawn using M/s. Perkin Elmer model DSC 4000. The rate of heating and cooling was maintained at 10°C/min under a nitrogen environment. The peaks were examined using the data collected from the machine.
2.5 Thermogravimetric Analysis (TGA)
The Thermo gravimetric Analysis (TGA) was analyzed using the M/s. TA Instruments model number of TGA 55, the test has been carried out at 10°C/min under a nitrogen environment. The test has been used to determine the percentage of volatile content in the material and also thermal degradation.
2.6 Rate of Burning in Horizontal Position
The rate of burning in horizontal burn test has been carried out as per ASTMD 635 for determining the burn rate characteristics of the material. The specimen size of 125 mm × 13 mm × 3 mm was used for determining the flammability characteristics. The test has been carried out using a Bunsen burner flame with a specimen holder. The edge of the samples has been lit using the Bunsen flame and the burning time has been estimated using a stop clock. The rate of the burning has been calculated for the specimens.
2.7 Morphological Observation using Scanning Electron Microscope (SEM)
The Morphological characterization were done using JSM–IT800, JEOL make Tokyo, Japan. The fractured sample were sputtered using gold and the surface topology were determined for the material.
The contact angle analysis was carried out using contact angle meter Holmarc-HO-IAD-CAM-01B with the sessile drop method. The substrate holder is used for placing the specimen and a drop of water has been dropped over the specimen. LED based diffused lighting mechanism captures the image of the drop for measuring the contact angle.
The current research highlights the improvement of the mechanical properties of the glass fiber reinforced composites with the used SLS-PA-12 powder. The effect of addition of the used nylon powders to the epoxy resin with and without glass fiber has been analyzed and detailed in the following section.
The Fourier Transform Infrared Spectroscopy (FTIR) analysis was carried out to check the chemical structure of the material. The IR of the samples with the PA-12 blend is shown in Fig. 1, stretching vibration of C = O at 1612 cm−1 and N-H bonds were shown in the box with a peak of 3250 to 3300 cm−1. From the graph, the increase in the PA-12 shows a slight bump in the 1 and 3 wt% PA-12 filler [11]. The epoxy resin samples were found in the vibration of 1612 cm−1 of the epoxy ring and 2965 cm−1 due to the presence of the aromatic protons [12]. The FTIR spectrum of the different samples proved the presence of PA-12 and Epoxy. Although the peaks of the epoxy have shown in different samples, the processing was carried out by handlay-up process, The presence of the epoxy with glass fiber shows a reduced peak value, due to the feeble quantity of the resin content.
Figure 1: Fourier transform infrared spectroscopy (FTIR) spectra of the samples
The Differential Scanning Calorimeter (DSC) analysis was carried out for the samples with PA-12 filler. Fig. 2A represents the DSC graph of the samples. The content of PA-12 sample with 3 wt% shows the melting range at 175°C to 189.3°C, but the actual melting temperature of the PA-12 as per the data sheet as per the SLS printing machine is 176 o thus proving the presence of PA-12 [13]. Fig. 2B represents the DSC graph of the GF+epoxy as cured in the range of 80.39°C. The actual melting range of the epoxy was in the range of 75°C, this may be due to a change in the glass transition temperature which increases due to the number of days after curing [14].
Figure 2: (A). DSC findings of 3 wt% Polyamide-12 filler with glass fiber. (B). DSC findings of unfilled glass fiber reinforced polymer
3.1.3 Thermogravimetric Analysis (TGA)
The Thermo gravimetric Analysis (TGA) was carried out for the unfilled GF epoxy and the 3 wt% filled PA-12 materials for analyzing the decomposition temperature of the samples. Fig. 3 shows the TGA graph of the filled and unfilled samples. The unfilled Glass fiber with epoxy starts decomposition (Ti) at 280°C and reaches up to 450°C [15]. The PA-12 filled GFRP samples showed slightly higher decomposition temperatures of 309°C and 317°C with an increase in the PA-12 filler proportion. The final decomposition temperature has slightly increased due to the epoxy value [16]. From the results it has been witnessed that the addition of PA-12 filler has altered the decomposition temperature (Ti) of the composite materials.
Figure 3: TGA results of the samples with and without filler
The tensile testing has been performed using the Instron multi-axial torsion machine with a cross-head speed of 2 mm/min for determining the tensile strength and tensile modulus. The stress strain curve for the filled and the unfilled PA-12 filler has been shown in Fig. 4. The stress-strain curve clearly shows that 3 wt% of PA-12 filled composite material showed higher tensile strength compared to unfilled and 1 wt% of PA12 filled materials. Fig. 5A,B shows the tensile strength and tensile modulus of the samples with different filler proportions. From Fig. 5A, the 1 and 3 wt% PA-12 filled GFRP composites showed incremental values compared to the unfilled GFRP. The tensile results has been clearly resembling the increase in addition of the fillers to the matrix has drastically reduced the overall stress value with a slight increase in the strain. The addition of the fiber improved the mechanical strength making the material brittle with a steep curve with reduced strain value. The enhancement of the filler to the matrix and the fiber has shown better strength compared to the presence of fiber and without fiber of different filler percentages.
Figure 4: Stress strain curve for the samples
Figure 5: (A). Tensile strength of the Polyamide-12 filled samples (B). Tensile modulus of the Polyamide-12 filled samples
The water absorption characteristics of the PA-12 filler material to the GFRP composites has been measured using the contact angle meter. The overall contact angle of the individual variant has been showed in Fig. 6.
Figure 6: Contact angle measurement of the used SLS Polyamide-12 filled GFRP composites
The sample was placed on the specimen holder of the instrument. A droplet of 5 to 8 µL was carefully placed on the sample by raising the table until the droplet touched the specimen. The initial sample, consisting of an epoxy matrix with PA-12 filler, exhibited a contact angle of 93.26°, which was higher than those of the other two variants. The increased contact angle may be attributed to the absence of fabric, which slightly absorbs water due to micro-holes in the specimen. The 1 wt% PA-12-filled specimen with fabric showed a slight reduction in contact angle to 92.30°, while the 3 wt% PA-12-filled specimen exhibited a contact angle of 91.91°. This reduction of approximately 1° to 1.5° indicates a decrease in the hydrophobic characteristics of the material. The reduction in contact angle in the 3 wt% filler specimen may be due to the higher filler content, which could increase water absorption, making the material slightly more water-absorbent. The filler added to the matrix and fabric alters the water absorption characteristics, leading to a decreased contact angle. These results clearly indicate that the addition of filler increases the water absorption characteristics of the PA-12-filled GFRP to some extent. However, all three variants exhibit contact angles above 90°, confirming that the material remains hydrophobic.
4.3 Rate of Burning and Morphological Characteristics
4.3.1 Rate of Burning in Horizontal Position
The rate of burning characteristics of the material has been carried out using ASTM D635. The test data of the burn test is shown in Table 1. This shows the increase in the PA-12 increased the linear burn rate of the samples. This slight increment in the burn rate may be due to the addition of the PA-12 filler. The linear burn rate of the unfilled showed better results compared to the filled samples with no flame dripping on the cotton. The addition of the PA-12 fillers may originate the flame from the basic epoxy matrix, enhancing the burn rate to some extent.
The rate of burning has been carried for determining the flame retardant characteristics of the material. From the Fig. 7A, the unfilled glass fiber with epoxy, shows the flame tends to extinguish itself with a small lit at the edge emitting black smoke. In Fig. 7B, the PA-12 filled GFRP, which shows the flame has started rapidly with the flame with black smoke.
Figure 7: Rate of burning of (A). Pure epoxy with unfilled sample (B). Glass fiber with epoxy with 3 wt% Polyamide-12 filler
The Morphological characteristics of the GFRP with epoxy and PA-12 filler has been shown in Fig. 8. The Fig. 8A shows the fiber matrix interface showing the dispersion of the PA-12 filler to the GFRP material. In addition to the matrix the PA-12 filler has also been mixed with the composite material.
Figure 8: Morphological images of the tested Polyamide-12 filled sample (A). Fiber matrix interface (B). Interference of the filler inside the matrix and the fiber
The tested specimen has been witnessed for the morphological study for visualizing the detailed internal structure after failure. The red spotted region from a different SEM image denotes the filled debris of the epoxy and the PA-12 interfaced entity. The Fig. 8B denotes the de bossed structure of the PA-12 filler after testing. The interface of the PA-12 with the matrix was found to normal due to the reduced interfacial shear stress. The percentage of the filler added to the matrix was considerably low and there might be chances of agglomeration of the fillers during the mixing or during curing of the matrix. Ultimately from the literatures the PA-12 has a high rate of interfacial bonding strength to the glass fiber [17].
The addition of PA-12 filler to the glass fiber-reinforced epoxy resin significantly enhances the composite’s properties like thermal stability and mechanical properties. The Fourier Transform Infrared Spectroscopy (FTIR) confirms the presence of PA-12 and epoxy, with varying peaks indicating structural modifications. The mechanical results of the PA-12 filled material show better results for 3 wt% incorporation of PA-12 where the tensile strength of 99.82 MPa and modulus of 9202.07 MPa are observed which show superior results compared to other samples. Additionally, the contact angle measurement of approximately 90° for the 1 wt% PA-12 filler signifies its inherent hydrophobic nature. In terms of the rate of burning in the horizontal orientation, the unfilled material displayed a higher range, while all materials showcased self-extinguishing properties with zero flame dripping. Overall, these results highlight the effectiveness of the PA-12 filler in improving the mechanical properties of the composite material. The improvements in mechanical strength and a notable increase in hydrophobicity suggest the promising potential of PA-12 filler for tailored composite material applications.
Acknowledgement: The authors like to express the deepest gratitude and appreciation for the assistance and support received throughout the completion of this research paper. The authors take this opportunity to acknowledge the contributions of the individuals and institutions who have played a significant role in successfully completing this research.
Funding Statement: The authors received no specific funding for this study.
Author Contributions: The author confirms contribution to the paper as follows: study conception and experimentation, Ravikumar Karthikeyan; interpretation of results, Subbiah Rajkumar; draft preparation, Balasundaram Ravi. All authors reviewed the results and approved the final version of the manuscript.
Availability of Data and Materials: The datasets generated during and/or analyzed during the current study are available from the corresponding author on reasonable request.
Ethics Approval: Not applicable.
Conflicts of Interest: The authors declare that they have no conflicts of interest to report regarding the present study.
References
1. Mägi P, Krumme A, Pohlak M. Recycling of PA-12 in additive manufacturing and the improvement of its mechanical properties. Key Eng Mater. 2016 Feb 21;674:9–14. doi:10.4028/www.scientific.net/KEM.674.9. [Google Scholar] [CrossRef]
2. Matykiewicz D. Hybrid epoxy composites with both powder and fiber filler: a review of mechanical and thermomechanical properties. Materials. 2020 Apr 11;13(8):1802. doi:10.3390/ma13081802. [Google Scholar] [PubMed] [CrossRef]
3. Ramesh M, Rajeshkumar LN, Srinivasan N, Kumar DV, Balaji D. Influence of filler material on properties of fiber-reinforced polymer composites: a review. e-Polymers. 2022 Nov 9;22(1):898–916. [Google Scholar]
4. Tiwari SK, Pande S, Agrawal S, Bobade SM. Selection of selective laser sintering materials for different applications. Rapid Prototyp J. 2015 Oct 19;21(6):630–48. doi:10.1108/RPJ-03-2013-0027. [Google Scholar] [CrossRef]
5. Gomes PC, Piñeiro OG, Alves AC, Carneiro OS. On the reuse of SLS polyamide 12 powder. Materials. 2022 Aug 10;15(16):5486. doi:10.3390/ma15165486. [Google Scholar] [PubMed] [CrossRef]
6. Zarringhalam H, Hopkinson N, Kamperman NF, De Vlieger JJ. Effects of processing on microstructure and properties of SLS Nylon 12. Mat Sci and Eng: A. 2006 Nov 5;435:172–80. [Google Scholar]
7. Dotchev K, Yusoff W. Recycling of polyamide 12 based powders in the laser sintering process. Rapid Prototyp J. 2009 May 29;15(3):192–203. doi:10.1108/13552540910960299. [Google Scholar] [CrossRef]
8. Türk DA, Brenni F, Zogg M, Meboldt M. Mechanical characterization of 3D printed polymers for fiber reinforced polymers processing. Mat & Des. 2017 Mar 15;118(3):256–65. doi:10.1016/j.matdes.2017.01.050. [Google Scholar] [CrossRef]
9. Feng L, Wang Y, Wei Q. PA12 powder recycled from SLS for FDM. Polymers. 2019 Apr 22;11(4):727. doi:10.3390/polym11040727. [Google Scholar] [PubMed] [CrossRef]
10. Kishi H, Matsuda S, Imade J, Shimoda Y, Nakagawa T, Furukawa Y. The effects of the toughening mechanism and the molecular weights between cross-links on the fatigue resistance of epoxy polymer blends. Polymer. 2021 May 3;223(20):123712. doi:10.1016/j.polymer.2021.123712. [Google Scholar] [CrossRef]
11. Li S, Yang Y, Zha X, Zhou Y, Yang W, Yang M. Nanoscale morphology, interfacial hydrogen bonding, confined crystallization and greatly improved toughness of polyamide 12/polyketone blends. Nanomaterials. 2018 Nov 8;8(11):932. doi:10.3390/nano8110932. [Google Scholar] [PubMed] [CrossRef]
12. Sahmetlioglu ER, Mart H, Yuruk H, Surme Y. Synthesis and characterization of oligosalicylaldehyde-based epoxy resins. Chem Pap. 2006 Feb;60(1):65–8. doi:10.2478/s11696-006-0012-1. [Google Scholar] [CrossRef]
13. Shirinbayan M, Montazeri A, Nouri Sedeh M, Abbasnezhad N, Fitoussi J, Tcharkhrtchi A. Rotational molding of Polyamide-12 Nanocomposites: modeling of the viscoelastic behavior. Int J Mater Forming. 2021 Jan;14(1):143–52. doi:10.1007/s12289-020-01558-9. [Google Scholar] [CrossRef]
14. Beura S, Sahoo SR, Thatoi DN, Mohanty UK, Chakraverty AP. Stability of GFRP composites with varied fractions of reinforcement exposed to ageing processes outdoors. Polymers and Polymer Composit. 2021 Nov;29(9):1485–94. doi:10.1177/0967391120973505. [Google Scholar] [CrossRef]
15. Mohan TP, Ramesh Kumar M, Velmurugan R. Thermal, mechanical and vibration characteristics of epoxy-clay nanocomposites. J Mater Sci. 2006 Sep;41(18):5915–25. doi:10.1007/s10853-006-0278-2. [Google Scholar] [CrossRef]
16. Zhu D, Ren Y, Liao G, Jiang S, Liu F, Guo J, et al. Thermal and mechanical properties of polyamide 12/graphene nanoplatelets nanocomposites and parts fabricated by fused deposition modeling. J Appl Polym Sci. 2017 Oct 15;134(39):45332. doi:10.1002/app.45332. [Google Scholar] [CrossRef]
17. Bernet N, Bourban PE, Maånson JA. On the characterization of wetting and adhesion in glass fiber-PA12 composites. J Thermoplastic Compos Mater. 2000 Nov;13(6):434–50. doi:10.1106/W3B4-CFKP-02VR-OXTE. [Google Scholar] [CrossRef]
Cite This Article
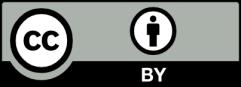
This work is licensed under a Creative Commons Attribution 4.0 International License , which permits unrestricted use, distribution, and reproduction in any medium, provided the original work is properly cited.