Open Access
ARTICLE
Physio-Mechanical Characterization of Recycled Polyethylene Terephthalate and Soda-Lime Glass Waste Composite for Roof Tile Application
1 Department of Materials & Metallurgical Engineering, University of Ilorin, Ilorin, 234031, Nigeria
2 Smart Manufacturing Research Institute & School of Mechanical Engineering, Universiti Teknologi MARA (UiTM), Shah Alam, 40450, Malaysia
3 Department of Mechanical Engineering, University of Ilorin, Ilorin, 234031, Nigeria
4 Laboratory of Applied Chemistry and Environment, Faculty Technology, University of El-Oued, El Oued, 39000, Algeria
* Corresponding Author: Yusuf Olanrewaju Busari. Email:
Journal of Polymer Materials 2024, 41(3), 117-129. https://doi.org/10.32604/jpm.2024.055895
Received 09 July 2024; Accepted 02 September 2024; Issue published 30 September 2024
Abstract
The research paper focuses on manufacturing composite materials from waste polyethylene terephthalate (PET) reinforced with soda-lime glass to provide a lightweight, less brittle, and high rust resistance when exposed to hazardous environment. In developing nations such as Nigeria, there is a significant surge in the volume of bottled water and other packaging materials used in households, leading to a rapid accumulation of biodegradable waste, that presents concerns such as the creation of landfills and health issues. PET are thermoplastic polymer that can be melted and shaped into various objects. This study involves the incorporation of soda lime glass with recycled PET with various weight proportions to create a composite for roof tile application. The processing phases encompass the gathering of discarded PET and glass, purification, fragmentation, glass treatment, composite fabrication, and physio-mechanical and microstructural characterization. The utilization of soda lime glass in the recycling of plastics led to the creation of cost-effective and efficient roof tile composites, while also decreasing environmental pollution. The density of the composite tile varied between 1.000242–1.600259 g/cm3 with 20 wt.% filler having the lowest density. The water absorption ranged from 0.12%–0.79%. Mechanical characterization results revealed that the hardness and tensile strength increased with increasing wt.% of reinforcement (soda-lime glass) with the highest values being 271 HBN and 12 N/mm2 (peak) at 60 and 50 wt.% filler (soda-lime glass), respectively. The composite samples had similar impact strength which varied between 70–74 J. Fourier Transform Infrared (FTIR) analysis reveals the occurrence of chemical and mechanical improvement during the recycling process. The composites exhibited promising properties from the research and revealed that the addition of the reinforcement largely improves the properties.Keywords
The global construction industry is facing increasing costs and resource demands, while plastic waste poses a significant environmental threat due to its non-biodegradable nature and pollution through incineration and landfill. Waste glass and polyethylene terephthalate (PET) bottles are consistently present in nearly all waste streams, often polluted with mixed-colour sources of varying compositions. Consequently, over 60% of these wastes are discarded in landfills and marine bodies causing sustainability. With 46 million tonnes of glass packaging in 2012 and 52 million tonnes of flat glass (mostly for buildings and automobiles) in 2009, the global market for glass packaging in containers accounted for about 85% of global output [1]. The global glass manufacturing market size was estimated at USD 106.44 billion in 2021. Nevertheless, with the emergence of new technologies in the glass production business, the degree of glass utilization has greatly grown to encompass solar panels, lighting applications, shelves, windows, appliances, and fiber optic cables. Glass waste originates from two sources: manufacturing firms that discard pieces that do not fit technical criteria or specialized retailers that sell glasses and accessories [2].
Matrix recycling is emerging as the most promising method for mitigating plastics’ environmental consequences, particularly in end-of-life management [3]. The recycling process of PET and soda-lime glass significantly influences their properties and suitability for composite applications. Recycled PET (R-PET) can be effectively used as a filler in various composite materials, enhancing their mechanical properties. The transition from a linear economy to a circular economy model for managing recycled PET and soda-lime glass waste offers significant environmental, economic, and social benefits. The circular economy emphasizes reuse, recycling, and regeneration of materials, reducing waste and conserving resources. Recycling PET bottles through methods like mechanical downcycling, closed-loop glycolysis, and upcycling can minimize greenhouse gas emissions and enhance material circularity [4,5]. Recycling soda-lime glass can reduce carbon dioxide emissions by 5%, contributing to sustainable development and cost savings in raw materials [6]. Overall, adopting a circular economy model for PET and soda-lime glass waste not only mitigates environmental impacts but also promotes sustainable industry practices and economic resilience.
Additionally, combining R-PET with date palm fibers in unsaturated polyester (UP) composites enhances thermal behavior at high temperatures, although the flexural strength may decrease due to non-uniform filler distribution [7]. On the other hand, recycled soda-lime glass, when used as a filler in polytetrafluoroethylene (PTFE) composites, affects the dielectric, mechanical, and thermal properties. Increasing the volume fraction of recycled soda-lime glass reduces tensile strength but improves moisture absorption and density, with the lowest coefficient of thermal expansion observed at higher filler content [8]. Furthermore, using recycled PET as a matrix for glass fiber-reinforced virgin PET composites can significantly enhance crystallization kinetics and mechanical properties, making the material suitable for automobile applications [9,10]. Overall, the recycling process not only provides an environmentally friendly solution but also tailors the properties of PET and soda-lime glass for specific composite applications, enhancing their performance and expanding their utility in various engineering fields.
Despite their excellent mechanical and thermal qualities, PET composites have a low impact strength, limiting their use in a variety of applications. Numerous studies have demonstrated that the addition of various copolymers can significantly improve the impact strength of virgin and recycled PET [11,12]. These properties include PET being lightweight, cheap, non-corrosive, and non-biodegradable. It also has other properties which are low density, low moisture absorption, good creep, and chemical resistance [13]. Soda lime glass is valued for its affordability, chemical stability, and robust physical characteristics such as hardness, adaptability, and the unique feature of being recycled through multiple times of melt and reshaping without significantly losing quality [1,14]. The increasing demand for materials used in building construction due to population growth has brought about the exploration of low-cost and economical ways of manufacturing these materials.
The roof covering is made of steel, concrete, aluminum, ceramic, and others which is a crucial element of a building’s design since it provides all-around security while providing protection from the elements such as rain, sun, bad weather, etc., and contribute to the character of our townscapes from every angle [15,16]. However, the material has their various challenges ranging from noise, high expansion rate, corrosion, density, carbonization, etc. [17,18]. The utilization of polystyrene-based matrix composite as roof or pavement tiles has become prevalent with the integration of various reinforcements resulting in exceptional fracture toughness characteristics with excellent melt temperature on microcell diameter and density during injection molding [19]. Roof tiles made from plastic composite have some advantages as compared to traditional roof tiles such as low water absorption, high flexural resistance, low specific weight, and excellent resistance to hail and freezing [20].
The composite tiles offer a novel method for recycling waste plastic material in a sustainable and cost-effective manner, both in our daily lives and business. This can be utilized to construct structures that are lightweight, corrosion-resistant, chemically resistant, cost-effective to produce, have an extended lifespan, and, most importantly, address the societal problem of plastic waste [21]. An experimental investigation was conducted to examine the properties of roof tiles made from a combination of sand and recycled PET in different proportions. The results indicate that these plastic composite tiles exhibit excellent strength and absorbency, making them suitable for use in roof tiles [22]. This study explores the possibility of using glass as a substitute for natural aggregates in the construction industry, specifically roofing tiles. The focus is on addressing environmental concerns and analyzing the economic viability of this application. Additionally, the study aims to further develop post-consumer markets for recycled polymers and waste glasses by promoting recycling and reducing the use of landfills.
Recycled Polyethylene Terephthalate (R-PET) with 0.91 g/cm3 density sourced from the waste water bottle containers as classified [23] accumulated within the University of Ilorin, which lies between latitude 8.4799°N and longitude 4.5418°E, Ilorin, Nigeria was washed with water, cleaned, dried and shredded into flakes. Soda-lime glass (in broken form) from industrial waste is characterized by its green color, which helps block ultraviolet light to preserve the quality of the beverages. The green tint is achieved by adding iron oxides during the glass manufacturing process and reuse as reinforcing fillers provides thermal insulation in addition to its irregular and micrometric predominant presence of Na, Si, and Ca elements [24]. The soda-lime glass particles were produced by manual crushing, hammer milling, and 70 h ball milling in line with sieved to get a particular range of particle size which was 100 microns as seen in Fig. 1a.
Figure 1: Composite preparation (a) material sorting and grinding (b) weighting and melting (c) mechanical mixing (d) mold samples
The composite production process flow is depicted in Fig. 1. The R-PET plastic was washed thoroughly to remove impurities, then shredded for an easy melting process loaded into a metallic pot, and placed on a gas burner. The soda-lime glass was pulverized in two stages. Firstly, it was milled with a locally made electrically motorized hammer mill machine to get a coarse glass particle. The coarse glass particle was further milled in a ball mill machine to get a fine particle. The fine glass particle was sieved to obtain a particle size of 100 microns particle size. Fig. 1b depicts the glass particles varied from 20 to 60 wt.% with respect to PET plastics using a mold with five different samples as designed in Table 1. It was subjected to an elevated temperature of about 260°C (melting temperature of PET plastic) which was maintained to avoid excessive entrapment of gases. The mixing was carried out at 110°C and 40 rpm for 10 min by a HAAKE internal mixer (HBI System 90, Chicago, MI, USA) [25] as presented in Fig. 1c. This was done to ensure an ideal dispersion and distribution of the particles. A mold of 120 mm × 120 mm × 3 mm was utilized to cast the composite slabs, with foil paper employed as the mold release agent. The cast composite samples were cured at room temperature for 24 h before conducting physical, mechanical, and morphological characterization as depicted in Fig. 1d.
2.2 Physical Property Test of the Composite
The mass of the samples was recorded using the water displacement method as per the ASTM D4052 standard. A predetermined volume of water was obtained using a measuring cylinder with a capacity of 250 ml. A single sample piece was submerged in the measuring cylinder, and the resulting increase in water level was measured and recorded. The composite volume is calculated by subtracting the initial known volume of water from the water containing the sample. Eq. (1) depicts the density of a particular piece of composite by dividing its mass by its volume. The identical technique was executed for all the other composites to acquire their densities, with a total of five specimens being utilised in each sample to calculate an average.
2.2.2 Water Absorption and Thickness Swelling Tests
The test sample with 60 by 60 by 10 mm3 in accordance with ASTM D570-22 standard [26]. The samples were dried using by using an oven, they were then cooled and the weight of each sample was measured. Five samples from each combination were selected and subjected to a drying process in an oven for 24 h at 100 ± 3°C. The weight and thickness of dried specimens were measured with a precision of 0.001 g and 0.001 mm, respectively. Subsequently, the specimens were submerged in distilled water for one week and maintained at 22 ± 2°C. The weight and thickness of the specimens were measured following the removal of surplus water from their surface. The alteration in weight is documented and employed to compute the percentage water absorption with Eq. (2):
Also, the value of the thickness swelling performed to investigate the increasing thickness with time due to moisture (water) absorption. The samples were taken out and dry clean after every 7 days and measure the dimensional changes with vernier calliper with the least count of 0.01 mm according to equation using the Eq. (3) [27,28].
The porosity of the samples was determined by soaking the samples in a bath of water and oil. Mass of the samples before and after soaking were determined and recorded. Porosity of the samples was calculated using the formula below; where m1 is the mass of brick before soaking, m2 mass of brick after soaking, ρ is the density of the liquid mix and V is the volume of the sample in Eq. (4).
2.3 Mechanical Testing of the Composite
Hardness values of the composites was determined by Brinell hardness testing machine, using a hardened steel ball indenter load of 100 kgf [29]. Two different moulds were prepared for tensile and impact testing. The composite samples were shaped into dumbbell form for tensile tests, following the ASTM D638 guidelines. The experiments were conducted with a consistent 0.5 mm/min strain rate. The IZOD impact test was performed on composite samples using a fully instrumented Avery Denison test machine, following the ASTM D256-93 guidelines. This approach was used to measure the strength of composite samples under sudden load applications. The tests were conducted using three identical specimens, and the results presented are the average values obtained from testing all the composite samples.
2.4 Analysis of Composite Using Optical Microscopy and Fourier Transform Infrared Spectroscopy
The morphology of the composites was examined using an optical microscope (XL 30, Philips, Eindhoven, Netherlands). The analysis was conducted at a magnification of 200×. Changes in chemical structures and functional groups was characterized using ASTM E1252-98 (2013) with FTIR spectrometer (Perkin Elmer Spectrum 400, Waltham, MA, USA) using a resolution of 4 cm−1 over the spectral range of 4000–650 cm−1.
3.1 Physical Properties of the Composite
The density results obtained from the water displacement analysis of the particle-reinforced composite samples provide valuable insights into the composition and structural characteristics of each material. Table 2 shows the density kept on increasing with an increase in weight composition of soda-lime glass which is in line with composite material made from recycled materials [30]. PET80:G20 shows the lowest density which was 1.000242 g/cm3 and kept increasing up to the composition of PET50:G50. The density value is implying that even with a higher glass content, the particle glass still contributes to maintaining a relatively low density far from the traditional roofing tiles [31]. The fourth sample containing an equal mix by wt.%, displays a significantly higher density of 1.600259 g/cm3 which was even higher than that of PET40:G60 which had a higher proportion of glass. This result indicates that at a balanced composition, the composite material gains considerable mass and density. However, all the samples exhibited a lower density as compared to traditional roofing tile materials such as clay, asphalt shingles, ceramic, and Aluminium [32].
Secondly, the water absorption result highlights the excellent water-resistant properties of PET70:G30 composite exhibiting the lowest water absorption rate of all the samples 0.12%. The majority of PET composition in samples with PET70:G30 and PET60:G40 had the highest water absorption rate of 0.72% and 0.79% respectively which can be used for pavement tiles. The utilization of PET plastic and increasing fine aggregate such as glass as reinforcement increases the water absorption resistance rate [22,33]. The problems that moisture causes in buildings have advanced significantly. However, the sample with PET40:G60 water absorption rate would start to decrease because generally, glass has a lower water absorption as compared to PET plastic. The samples produced had a relatively lower absorption as compared to conventional roof tile materials such as clay tile, asphalt shingle, and ceramics tiles with water absorption of 10%, 1%, and 5%, respectively [20,34].
Thirdly, the porosity test in Table 2 depicts that sample PET40:G60 with the highest glass composition particle displayed the lowest porosity of 0.04%. This is because of the volume fraction of the reinforcement used enhancing the packing density and minimizing gaps thereby reducing the chances of porosity occurring. Samples PET70:G30 and PET50:G50 displayed the highest porosity of 0.75% and 0.78%, respectively. The presence of pores affects mechanical properties such as strength, toughness, and stiffness [35]. The porosity was influenced by the processing condition during the production of the composite material such as stirring continuously which helps to get rid of the trapped gases [16].
Lastly, the samples exposed to the ambient environment and the thickness swell percentage results are recorded in Table 2. PET80:G20 having the least amount of particle glass reinforcement showed an extremely low swell percentage of 0.0008% as compared to the other samples. The result suggests that the material has excellent resistance to swelling when exposed to a high-temperature environment. The high PET content likely contributed to the resistance. It could be observed that the swell value increased with an increase in particle glass. PET50:50 swell of 0.115%. The result indicates that an increase in the composition of particle glass increases the swell rate up to 0.705% as seen in PET40:G60. The higher amount of particle glass in PET plastic may have reduced the effective glass transition temperature, increasing the composite’s susceptibility to swelling. research has established that thickness swelling minimizes interfacial adhesion [28,36].
3.2 Result of Mechanical Testing of the Composite
Fig. 2 shows the tensile properties of the compositions, it was observed that at 50 wt.% of glass and PET (PET50:G50), loading, the maximum tensile strength of the composite was 12 MPa and the minimum tensile strength was 4.06 MPa when the weight of glass is 20% matrix which is greatly close to the traditional roof tiles [20,32]. PET50:G50 can withstand the highest stress at yield, the composite material starts to undergo permanent deformation and might have been influenced by greater interfacial bonding between the matrix and the reinforcement. The tensile strength is affected by the distribution and dispersion of the particles in the matrix [37]. PET40:G60 tensile strength decreased because of glomeration because the most reinforced constituent is a particle. Reinforced agglomerations happened thus causing dispersion problems in PET, which led to a decrement in tensile strength [38].
Figure 2: Tensile strength for samples
From the results obtained in Table 3, it was observed that the fine aggregate glass has a significant effect on the hardness properties of composite. The hardness Brinell number average value of the samples increased with increase in particle glass which is in line with studies in literature [39]. The rapid rise in hardness value was seen at 60 wt.% glass as seen PET40:G60 with a hardness value of 271 HBN. The hardness of a composite material increases with an increase in particle size being added to the matrix. Similarly, the impact resistance average value in Table 3 depicts that highest sample PET40:G60 exhibited the highest impact strength value of 74 J which may be the effect of toughening of the composite due higher percentage of particle glass could have acted as crack arrester, preventing the propagation of crack and enhancing the material’s ability to absorb energy during impact [40]. On the other hand, PET70:G30 had the lowest impact energy value of 70 J. Furthermore, other samples were within the same range which could be adjudged to the fact that addition of reinforcement up to 6% increases the impact energy strength but above that, the impact resistance begins to reduce and hardness increase.
3.3 Optical Microscopy and Fourier Transform Infrared (FTIR) Spectroscopy
The micrograph of the samples depicts reinforcement was dispersed evenly to a great extent as seen in Fig. 3. To support the interpretation of the mechanical results, a morphological study has been performed. Fig. 4 shows optical micrographs of the produced materials at the same enlargements (×200). The dark patches represent the matrix PET and the light patches are the particle soda-lime glass serving as reinforcement which dominance kept on increasing as the wt.% of particle glass was increased. The PET80:G20 micrograph depicts greater dispersal of the PET fraction and their potential interfacial bonding with the PET chain. The combination of RPET with a greater proportion of soda-lime glass composites enhances hardness and impact strength due to uniform reinforcement distribution as seen in the PET 40:G60 sample. Moreover, The FTIR spectra of PET plastic and soda-lime glass composite are shown in Figs. 4–6, respectively. The spectrum exhibited characteristic peaks associated with both PET and soda-lime glass. The peak of the C-H bending vibration is around 720 cm−1 which also decreases as the PET ratio decreases which is in line with the PET peak around 725 cm−1 observed in microplastics PET [41]. The corresponding PET peak includes C-H stretching vibrations, C=O stretching (carbonyl) vibrations, which appear strongly at 1638 cm−1, and C-O-C stretching vibrations. Additionally, peaks 1000 cm−1, associated with the Si-O stretching vibrations of soda-lime glass were observed. The relative intensity of these peaks provided insight into the composition of the composite, with higher intensities indicating a greater concentration of specific functional groups as found in similar studies [36,42,43]. The spectra of the PET80:G20 and PET70:G30 reveal similar trends PET60:G40, PET50:G50, and PET40:G60 revealed polymeric absorption bands with lower intensities than later composites. It implies that there has been compatibilization between the surface of the soda lime glass reinforcement and the RPET, therefore giving strong adhesion between the matrix and filler.
Figure 3: Microstructure at 200× (a) PET80:G20 (b) PET70:G30 (c) PET60:G40 (d) PET50:G50 (e) PET40:G60
Figure 4: FTIR spectrum of PET80:G20
Figure 5: FTIR spectrum of FTIR spectrum of PET60:G40
Figure 6: FTIR spectrum of PET40:G60
The worldwide market for composite roof tiles is growing rapidly since there is a rising need for long-lasting, visually appealing, and eco-friendly roofing materials. Market expansion is driven by increasing construction activity, widespread acceptance of green building techniques, and strict laws on sustainable building materials. Product innovation, technological advances, and the expansion of distribution channels will drive anticipated market growth in the upcoming years. The composite roof tiles market is anticipated to expand significantly to attract carbon credit. Polymer composite consisting of recycled polyethylene terephthalate plastic and soda-lime glass was successfully produced with different weight percentages of R-PET plastic and soda-lime glass with uniform microns size were utilized for this research. The following conclusion can be drawn:
· Physical characterization of the composite samples revealed that the density, water absorption, and swell increase with the increase in reinforcement.
· Microstructural examination of the composite showed that the reinforcement (soda-lime glass) was largely dispersed evenly.
· Mechanical characterization showed that the samples with higher composition of reinforcement possessed a better hardness and tensile strength. The impact strength of the samples was merely influenced by the varying composition with all samples having an almost similar impact strength value.
· Diverting waste PET plastic and soda-lime glass from landfills and repurposing them for building materials contribute to a reduction in the environmental impact of waste disposal and the extraction of biodegradable resources.
· The transformation of industrial ecosystems to a circular economy model can also provide competitive advantages such as higher productivity, better resource utilization, and market growth while delivering social, financial, and environmental benefits in developing countries.
The best recycling techniques for certain applications are essential for the evolution of sustainable recycling technology. Further studies of processing temperature or other manufacturing factors that can affect the efficiency in market scale such as melt flow index of the polymer-based composite. The investigation of thermal fluctuations and degradation for extended periods can substantially enhance an in-depth understanding of the mechanical properties.
Acknowledgement: The authors acknowledge staff of Analytical Services at Federal Institute of Industrial Research, Oshodi (FIIRO) for their collaborative efforts in characterisation and analysis of samples.
Funding Statement: The authors received no specific funding for this study.
Author Contributions: The authors confirm contribution to the paper as follows: data collection: Issah Sadiq Ibrahim, Rachael Oluwatoyosi Idowu, Hassan Kobe lbrahim, Kabir S. Ajao; analysis and interpretation of results: Yusuf Olanrewaju Busari, Norliana Mohd Abbas, James Obafemi Adegbola; draft manuscript preparation: Yusuf Olanrewaju Busari, Abdallah Reghioua, Yusuf Lanre Shuaib-Babata. All authors reviewed the results and approved the final version of the manuscript.
Availability of Data and Materials: No data was used for the research described in the article.
Ethics Approval: Not applicable.
Conflicts of Interest: The authors declare that they have no conflicts of interest to report regarding the present study.
References
1. Favaro N, Ceola S. Glass cullet: sources, uses, and environmental benefits basic features of cullet. Am Ceramic Soc. 2021;II(4):1179–89. doi:10.1002/9781118801017.ch9.9. [Google Scholar] [CrossRef]
2. Cardoso de Souza-Dal Bó G, Bó MD, Bernardin AM. Reuse of laminated glass waste in the manufacture of ceramic frits and glazes. Mater Chem Phys. 2021;1–13. doi:10.1016/j.matchemphys.2020.123847. [Google Scholar] [CrossRef]
3. Ragaert K, Delva L, Van Geem K. Mechanical and chemical recycling of solid plastic waste. Waste Manag. 2017;69:24–58. doi:10.1016/j.wasman.2017.07.044. [Google Scholar] [PubMed] [CrossRef]
4. Ghosh T, Uekert T, Walzberg J, Carpenter AC. Comparing parallel plastic-to-X pathways and their role in a circular economy for PET bottles. Adv Sustain Syst. 2023;2300068:1–11. doi:10.1002/adsu.202300068. [Google Scholar] [CrossRef]
5. Alhazmi H, Shah SAR, Anwar MK, Raza A, Ullah MK, Iqbal F. Utilization of polymer concrete composites for a circular economy: a comparative review for assessment of recycling and waste utilization. Polymers. 2021;13(2135):1–39. doi:10.3390/polym13132135. [Google Scholar] [PubMed] [CrossRef]
6. Hsieh CL, Tsai WH. Towards carbon neutrality and circular economy in the glass industry by using the production decision model. Energies. 2023;16(22):1–18. doi:10.3390/en16227570. [Google Scholar] [CrossRef]
7. Habila T, Meftah Y, Maou S. Thermal and physical properties of hybrid composites made from used PET bottles and date palm fibers filled with unsaturated polyester. ASEAN J Chem Eng. 2023;23(1):94–102. doi:10.22146/ajche.82419. [Google Scholar] [CrossRef]
8. Alhaji I, Abbas Z, Zainuddin N, Ibrahim N, Khamis A, Lakin I. Recycled soda lime silica glass inclusion in polytetrafluoroethylene matrix as reinforcement for microwave substrate application. Materwiss Werksttech. 2022;53:1373–85. doi:10.1002/mawe.202200126. [Google Scholar] [CrossRef]
9. Volpe V, Lanzillo MS, Molaro A, Affinita G, Pantani R. Characterization of recycled and virgin polyethylene terephthalate composites reinforced with modified kenaf fibers for automotive application. Polym Compos. 2022;43(11):7724–38. doi:10.1002/pc.26866. [Google Scholar] [CrossRef]
10. Medeiros H, Santos GAV, Guedes BN, Santiago K, Brito K. A design process to define public challenges addressing SDGs. Revista de Administracao Publica. 2023;57(4). doi:10.1590/0034-761220230008x. [Google Scholar] [CrossRef]
11. Bocz K, Ronkay F, Decsov KE, Molnár B, Marosi G. Application of low-grade recyclate to enhance reactive toughening of poly(ethylene terephthalate). Polym Degrad Stab. 2021;185(109505):1–11. doi:10.1016/j.polymdegradstab.2021.109505. [Google Scholar] [CrossRef]
12. Van Kets K, Delva L, Ragaert K. Structural stabilizing effect of SEBSgMAH on a PP-PET blend for multiple mechanical recycling. Polym Degrad Stab. 2019;166:60–72. doi:10.1016/j.polymdegradstab.2019.05.012. [Google Scholar] [CrossRef]
13. Taiwo O, Abas NF. Mechanical properties and durability of PET waste aggregates in roof tiles production. Int J Recent Technol Eng. 2021;9(5):300–4. doi:10.35940/ijrte.E5303.019521. [Google Scholar] [CrossRef]
14. Andreola F, Barbieri L, Lancellotti I, Leonelli C, Manfredini T. Recycling of industrial wastes in ceramic manufacturing: state of art and glass case studies. Ceram Int. 2016;42(12):13333–8. doi:10.1016/j.ceramint.2016.05.205. [Google Scholar] [CrossRef]
15. Akinwande AA, Adediran AA, Balogun OA, Adetula YV, Olayanju TMA, Agboola OO. Material selection for the production of roof tiles using digital logic method. IOP Conf Series: Mater Sci Eng. 2021;1107(1):12022. doi:10.1088/1757-899X/1107/1/012022. [Google Scholar] [CrossRef]
16. Topacio A, Eng M, Arkuino RC, Romano KV, Jayvee C. Development of hydrophobic composite roof tiles utilizing recycled plastic materials. Mater Eng Dev. 2018;6:1–3. [Google Scholar]
17. Roy K, Dani AA, Ichhpuni H, Fang Z, Lim JBP. Improving sustainability of steel roofs: life cycle assessment of a case study roof. Appl Sci. 2022;12(5943):1–20. doi:10.3390/app12125943. [Google Scholar] [CrossRef]
18. Furszyfer Del Rio DD, Sovacool BK, Foley AM, Griffiths S, Bazilian M, Kim J, et al. Decarbonizing the ceramics industry: A systematic and critical review of policy options, developments and sociotechnical systems. Renew Sustain Energ Rev. 2022;157:112081. doi:10.1016/j.rser.2022.112081. [Google Scholar] [CrossRef]
19. Ahmad M, Waseem M. Effects of injection molding parameters on cellular structure of roofing tiles composite. Mater Today: Proc. 2021;36:701–7. doi:10.1016/j.matpr.2020.04.751. [Google Scholar] [CrossRef]
20. Gaggino R, Kreiker J, Filippín C, Sánchez Amono MP, González Laría J, Peisino LE. The comprehensive comparison of thermal and physical-mechanical properties of the recycled rubber and plastic roofing tiles versus roofing tiles made with different traditional materials. Adv Civil Eng. 2018;2018:1–11. doi:10.1155/2018/7361798. [Google Scholar] [CrossRef]
21. Dhawan R, Bisht BMS, Kumar R, Kumari S, Dhawan SK. Recycling of plastic waste into tiles with reduced flammability and improved tensile strength. Process Saf Environ Prot. 2019;124:299–307. doi:10.1016/j.psep.2019.02.018. [Google Scholar] [CrossRef]
22. Bamigboye GO, Ngene BU, Ademola D, Jolayemi JK. Experimental study on the use of waste polyethylene terephthalate (PET) and river sand in roof tile production. J Phys: Conf Series. 2019;1378(4):1–10. doi:10.1088/1742-6596/1378/4/042105. [Google Scholar] [CrossRef]
23. Nováková K, Šeps K, Achten H. Experimental development of a plastic bottle usable as a construction building block created out of polyethylene terephthalate: testing PET(b)rick 1.0. J Build Eng. 2017;12:239–47. doi:10.1016/j.jobe.2017.05.015. [Google Scholar] [CrossRef]
24. Galvão ACP, Farias ACM, Mendes JUL. Characterization of waste of soda-lime glass generated from lapping process to reuse as filler in composite materials as thermal insulation. Ceramica. 2015;61(359):367–73. doi:10.1590/0366-69132015613591987. [Google Scholar] [CrossRef]
25. Liao H, Gao J, Liu C, Tao G. Rheological investigation on a polypropylene/low density polyethylene blending melt. J Polym Mater. 2024;41(1):45–54. doi:10.32604/jpm.2024.053021. [Google Scholar] [CrossRef]
26. ASTM D570–22. Standard test method for water absorption of plastics. West Conshohocken, PA, USA: American Society of Testing Materials; 2022. [Google Scholar]
27. Devapiriam R, Karthik S, Santhy K. Evaluation of mechanical and thermal properties of fabricated Sansevieria and Kaans fiber/Egg shell powder reinforced with polyester matrices. Pigm Resin Technol. 2022;51(6):692–9. doi:10.1108/PRT-07-2021-0076. [Google Scholar] [CrossRef]
28. Radzi AM, Sapuan SM, Jawaid M, Mansor MR. Water absorption, thickness swelling and thermal properties of roselle/sugar palm fibre reinforced thermoplastic polyurethane hybrid composites. J Mater Res Technol. 2019;8(5):3988–94. doi:10.1016/j.jmrt.2019.07.007. [Google Scholar] [CrossRef]
29. Chidhananda RS, Prakash SD, Nireeksha P, Reddy Mungara S. A study on hardness and thermal properties of fibre based particulate polymer composites. Mater Today: Proc. 2021;47:4495–501. doi:10.1016/j.matpr.2021.05.328. [Google Scholar] [CrossRef]
30. Seghiri M, Boutoutaou D, Kriker A, Hachani MI. The possibility of making a composite material from waste plastic. Energy Proc. 2017;119:163–9. doi:10.1016/j.egypro.2017.07.065. [Google Scholar] [CrossRef]
31. Gaggino R, Positieri MJ, Irico P, Kreiker J, Arguello R, Sánchez Amono MP. Ecological roofing tiles made with rubber and plastic wastes. Adv Mater Res. 2014;844:458–61. doi:10.4028/www.scientific.net/AMR.844.458. [Google Scholar] [CrossRef]
32. De Carvalho Gomes S, Zhou JL, Li W, Long G. Progress in manufacture and properties of construction materials incorporating water treatment sludge: a review. Resourc Conservat Recycl. 2019;145:148–59. doi:10.1016/j.resconrec.2019.02.032. [Google Scholar] [CrossRef]
33. Bamigboye GO, Nworgu AT, Odetoyan AO, Kareem M, Enabulele DO, Bassey DE. Sustainable use of seashells as binder in concrete production: prospect and challenges. J Build Eng. 2021;34:101864. doi:10.1016/j.jobe.2020.101864. [Google Scholar] [CrossRef]
34. Chaka KT, Ahmed FE, Zegeye LH, Worku BG. Compressive strength of floor tile composites from recycled PET reinforced with natural fibers. J Nat Fibers. 2023;20(1):1–15. doi:10.1080/15440478.2022.2146249. [Google Scholar] [CrossRef]
35. Benyathiar P, Kumar P, Carpenter G, Brace J, Mishra D. Polyethylene terephthalate (PET) bottle-to-bottle recycling for the beverage industry: a review. Polymers. 2022;14(12):1–29. doi:10.3390/polym14122366. [Google Scholar] [PubMed] [CrossRef]
36. Dos Santos Pereira AP, Da Silva MHP, Lima ÉP, Dos Santos Paula A, Tommasini FJ. Processing and characterization of PET composites reinforced with geopolymer concrete waste. Mater Res. 2017;20:411–20. doi:10.1590/1980-5373-mr-2017-0734. [Google Scholar] [CrossRef]
37. Agunsoye JO, Aigbodion VS. Bagasse filled recycled polyethylene bio-composites: morphological and mechanical properties study. Results Phys. 2013;3:187–94. doi:10.1016/J.RINP.2013.09.003. [Google Scholar] [CrossRef]
38. Radzi AM, Sapuan SM, Jawaid M, Mansor MR. Mechanical performance of Roselle/Sugar palm fiber hybrid reinforced polyurethane composites. BioResources. 2018;13(3):6238–49. doi:10.15376/biores.13.3.6238-6249. [Google Scholar] [CrossRef]
39. Agunsoye JO, Bello SA, Bamigbaiye AA, Odunmosu KA, Akinboye IO. Recycled ceramic composite for automobile brake pad application. J Res Phys. 2018;39(1):35–46. doi:10.2478/jrp-2018-0004. [Google Scholar] [CrossRef]
40. Monti M, Scrivani MT, Kociolek I, Larsen ÅG, Olafsen K, Lambertini V. Enhanced impact strength of recycled PET/glass fiber composites. Polymers. 2021;13(9):1–12. doi:10.3390/polym13091471. [Google Scholar] [PubMed] [CrossRef]
41. Seo JH, Shin Y, Gyu Song I, Lim J, Ok YS, Weon S. Atmospheric microplastics: challenges in site-and target-specific measurements. TrAC-Trends Anal Chem. 2024;178:117859. doi:10.1016/j.trac.2024.117859. [Google Scholar] [CrossRef]
42. Worku BG, Wubieneh TA. Mechanical properties of composite materials from waste poly(ethylene terephthalate) reinforced with glass fibers and waste window glass. Int J Polym Sci. 2021;2021(3320226):1–14. doi:10.1080/17518253.2023.2169081. [Google Scholar] [CrossRef]
43. Chen Z, Hay JN, Jenkins MJ. The thermal analysis of poly(ethylene terephthalate) by FTIR spectroscopy. Thermochim Acta. 2013;552(4):123–30. doi:10.1016/j.tca.2012.11.002. [Google Scholar] [CrossRef]
Cite This Article
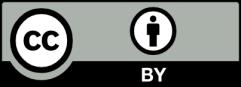
This work is licensed under a Creative Commons Attribution 4.0 International License , which permits unrestricted use, distribution, and reproduction in any medium, provided the original work is properly cited.