Open Access
ARTICLE
Investigation of the Damping Abilities of Sheep Wool Reinforced Expanded Polystyrene Core Layer Composites at Different Energies
1 Faculty of Technology, Department of Automotive Engineering, Afyon Kocatepe University, Afyon, 03200, Turkey
2 Faculty of Technology İnstitute of Science, Afyon Kocatepe University, Afyon, 03200, Turkey
* Corresponding Author: İbrahim Yavuz. Email:
Journal of Polymer Materials 2024, 41(1), 1-14. https://doi.org/10.32604/jpm.2024.052279
Received 28 March 2024; Accepted 28 May 2024; Issue published 21 June 2024
Abstract
In this study, natural fiber reinforced polymer foam core layered composites were produced for the automotive industry. Sheep wool was used as natural fiber. Polymer foam with a single layer XPS foam structure was used as the core material. XPS foams and fibers are bonded to the upper and lower sides of the foams with the help of resin. Samples were produced with one and two layers on both sides, with a total of two and four layers. Production was carried out using the vacuum bagging method using the manual laying method. After the production was completed, it was cut to dimensions in accordance with the standards and experiments were carried out. Compression tests, three-point bending tests and low-speed impact tests were carried out to analyze the energy absorption capabilities of the produced samples. As a result of the experiments, it was determined that the samples with a total of two floors provided better performance than the samples with a single layer. In the impact tests, rebound occurred in the double-layered samples in the 10 J impact tests, and punctures or stabbings were detected in the 20 J tests.Keywords
Highlights
• As the number of fiber layers increases, the energy absorption ability is better.
• As the impact energy increases, the deformation in the material increases.
• The porous core material is effective in absorbing energy.
• Mechanical properties are directly proportional to the number of layers.
The word “composite” is generally the combination of two or more separate materials on a macroscopic scale, and “composite material” means a structural unit used in various engineering applications, each of whose material components have different thermal, mechanical, electrical, magnetic, optical and chemical properties [1–3]. Flexibility in engineering materials according to their usage areas [4], lightness impact resistance, high corrosion resistance [5], bending strengths, energy absorption [6–8] and thermal resistance [9,10] features such as are sought. To meet this need, new composite materials have begun to be developed and their usage areas are becoming more widespread day by day.
Advanced composites are subjected to mechanical testing in different directions to determine their suitability for a particular design. In general, it is possible to express these tests as tensile, compression, shear, impact and fatigue tests [11–14]. It is possible to divide composite materials into classes such as their structures, components and application areas. According to the method of obtaining, they are grouped as artificial and natural fibers [15,16]. Artificial fibers are fiber types such as glass fiber, carbon fiber, kevlar (aramid) and boron fiber [15,16]. Glass, carbon and aramid fiber-based composites are more demanded than others in the aerospace, defense, automotive, wind energy and pipe manufacturing industries [17,18]. It is the use of natural fiber composites instead of or as a component of traditional materials (artificial fibers). Thus, to promote the use of environmentally friendly and sustainable materials and to reduce the negative environmental effects of synthetic materials.
Natural fibers can be examined in two parts: plant and animal [19–21]. For example, plant materials such as jute, cotton, linen and wool [22,23] fibers of animal origin such as sheep, goat wool, silkworm, natural fiber [24,25] it is considered. Plant fibers are widely used in the textile industry [26]. For example, fibers obtained from plants such as cotton, hemp and flax are used in fabric production [27–30]. Animal fibers are natural fibers obtained from animals. It is used in various applications in the composite industry. These fibers offer various advantages, especially in fields such as textile, construction and automotive [31]. Animal fibers are used in the automotive industry in car seats, steering wheel coverings and other interior design elements due to their durability, soft texture and aesthetic appearance. It reduces noise by using wool insulation in areas such as the engine compartment, door panels and ceiling [32–35]. Today, studies are carried out in different fields with sheep wool. Some of these are on sheep wool fiber-concrete composites. They found that using sheep wool has potential benefits in many areas, such as reducing weight, improving thermal insulation, fire resistance, noise reduction and can help reduce the environmental impact of concrete production, as well as improving its energy absorbing properties [36–39].
By becoming widespread in the industrial sector of animal fibers, the country creates added value for the development of animal husbandry, as well as increasing the production capability in manufacturing. It is thought that one of these areas of use can provide impact absorption in vehicles with composite material reinforced with natural fibers. For this reason, the study tried to examine the energy absorption ability of natural fiber polymer foam core layer composites. In the study, sheepwool was used as the fiber and XPS foam layer was preferred.
The aim of the current study is to examine the mechanical properties of pure sheep wool fabric through experiments. In our country, the fibers clipped from sheep grown are obtained from naturally produced material that is turned into fabric. The chopped sheep wool in fiber form is shown in Fig. 1a, and the sample made into fabric is shown in Fig. 1b. Composites were created by combining sheep wool fabric with epoxy-based materials.
Figure 1: Sheep wool (a) Raw sheared form from sheep (b) Fabric form
The average technical characteristics of the wool of some sheep breeds raised in our country are shown in Table 1.
Sheep wool is a natural material used in various applications in the automotive industry. This soft, durable and insulating natural fiber is used to make some auto parts and interiors [34]. For this reason, it was preferred to be used in the study.
As the layer material, 20 mm thick XPS material complying with TS EN 13164 + A1 and En 13163 standards was preferred. They are foam-based materials, which are a closed-cell material with low density and high rigidity [41]. The properties of XPS foam are given in Table 2.
This material has low moisture absorption, compressibility, compressive creep, dimensional stability at a certain temperature, thermal conductivity and the ability to be shaped by heat. Additionally, its chemical resistance is quite good. Light and rigid layers of this type are commonly used as core materials. Layered foams are used in many areas, especially bumpers, in the automotive industry [44]. Safety is an important factor in automobiles. Thanks to their impact absorption properties, XPS foams can help protect passengers by dissipating energy during a crash [45].
The manual laying method is used in many areas in technical studies in the manufacturing of composite materials. Parts produced by hand-laying method have features such as high strength, low weight and chemical resistance. Reinforcement material in the form of fiber or fabric is placed on the mold by orientation. For sample production, MGS LR 285 epoxy resin and LH 285 epoxy hardener were mixed in appropriate proportions. The matrix material with polymeric resin is applied on top of the reinforcement material. After the application layers were completed, the resin was left in a vacuum atmosphere until it cured using the vacuum bagging method. The curing process was waited for approximately two hours at room temperature.
Vacuum bagging is an effective method used to optimize resin and air flow in the production of composite materials. This method allows the desired vacuum level to be created initially via the vacuum pump. Vacuum method: Thanks to the vacuum applied to the resin injection lines, the resin spreads homogeneously to fill all gaps. It removes air bubbles and allows them to come out. Once these steps are completed, the vacuum pump is turned off. Afterwards, the resin dispensing lines are clamped to ensure that the resin is kept in the desired areas [46,47].
Vacuum bagging method is a technique used in the production of composite materials. This method aims to achieve a higher material quality by eliminating air gaps between the resin and the sheepswool fabric. The application of the method is shown in Fig. 2. In sample production, the core material and fibers are combined with resin and a brush (Fig. 2a). In the study, the materials were cured at room temperature for 2 h under 20 bar pressure using the vacuum bagging method (Fig. 2b). The cured samples were prepared by cutting (Fig. 2c) the impact sample to 100 mm × 100 mm (Fig. 2d) using the precision cutting method using a jig saw.
Figure 2: XPS sheep wool sample production process visual
The findings were examined in three main parts. Three samples were used for all tests and graphs were drawn by taking the arithmetic average.
Impact test is a method used in material testing. It is used to examine the behavior of the material against impacts [48,49]. It is a testing method that applies a controlled impact to a material sample to understand how the material behaves under impact energy. While low-speed impact experiments are used to evaluate the deformation and energy absorption capacity of the material [50], high-speed impact experiments are generally used to study the behavior of the material against fracture and cracking [51]. Instron/Ceast 9350 device was used in impact experiments. Fig. 3 shows the impact test device used in the tests.
Figure 3: Impact test device and samples produced for testing
In the study, the impact resistance of impact test samples with XPS core material with two different layer thicknesses, single and double, was experimentally examined. The dimensions of the impact samples were determined as 100 mm × 100 mm in width and length according to the ASTM D7766 standard [12]. Impact samples were made ready by cutting using the precision cutting method. Although sample thicknesses vary depending on the layer, 2-layer ones were measured as 22 mm and 4-layer ones were measured as 24 mm.
3.1 Single and Double Layer XPS Impact Test
Damage images on the upper and lower surfaces of single and double-layer sheep wool natural fiber test samples after impact are shown in the figure. In the figure, it is clearly seen that the damage area differs in samples with single and double layers under 10 and 20 J impact energy. When the post-impact damage areas for 10 and 20 J in single-layer XPS samples are compared, it is seen that the bottom and top surface damage areas of these two samples are the same. At 10 J impact energy, 16 mm damage is observed on the front surface of the monolayer and 19 mm damage is observed on the back surface of the fiber and core material. At 20 J impact energy, 12 mm damage is observed on the front surface of the single layer and 14 mm damage is observed on the back surface of the fiber and core material. It can be seen that under 10 J energy, smaller damage occurred on the upper surfaces of the double-layer XPS sample than the others, and there was no damage on the lower surface. However, at 20 J impact energy of the same sample, fiber breaks and core material damage are observed on the upper and lower surfaces. At an impact energy of 10 J, no damage is observed on the front surface of the double layer and 12 mm on the back surface. At an impact energy of 20 J, 20 mm damage is observed on the front surface of the double layer and 24 mm damage is observed on the back surface of the fiber and core material. Fig. 4 shows the damage caused to the samples as a result of the impact test.
Figure 4: XPS sample damage images as a result of the impact test
Fig. 5 shows the force-deformation graph of single and double layer samples with XPS core at 10 J energy. It was determined that at an energy value of 10 J, the upper layer of the double-layer sample was pierced, it could not advance to the lower layer and it bounced back as the foam absorbed the energy. In the single-layer sample, it completely pierced the top layer, damaged the core foam and remained stuck in the foam. While it resists a force of approximately 1500 N in the two-layer sample, it is around 800 N in the single-layer sample. The deformation was determined to be approximately 9 mm in the double-layer sample, and the deformation reached up to 12 mm in the single-layer samples.
Figure 5: Force-deformation graph of single and double layer samples with XPS core material as a result of 10 J impact energy
Fig. 6 shows the force-deformation graph of single and double-layered samples with XPS core as a result of 20 J energy. As a result of the impact test, the first layer of the double-layer samples was completely pierced and the striking tip reached the second layer and stuck into the sample. The downward descent in the force graph is a result of the foam absorbing energy. Approximate deformation is around 16 mm and the maximum force reached up to 2500 N. In single-layer samples, the striking tip penetrated both layers. The advancement amount of the striking tip inside the sample is approximately 25 mm, and the maximum force resistance is around 500 N, as seen in the graph in Fig. 8.
Figure 6: Force-deformation graph of single and double layer samples with XPS core material as a result of 20 J impact energy
In Fig. 7, the deformations of single-layer samples with XPS foam core under 10 and 20 J energy are compared. When the graph was examined, it was determined that the striking tip penetrated the single-layer samples under 20 J energy. The maximum force is around 600 N and the striking tip completely pierces the sample and the advancement amount is determined as 25 mm. In the test samples performed under 10 J energy, the tests resulted in stabbing. In the experiments, the maximum force was around 900 N and the deformation was determined as 12 mm.
Figure 7: KY-T-XPS force-deformation graph under 10 and 20 J impact energy
In Fig. 8, the deformations of double-layer samples with XPS foam core under 10 and 20 J energy are compared. In XPS 20 experiments, the test resulted in stabbing in the sample. It was determined that at an energy value of 10 J, the upper layer of the double-layered sample was pierced, it could not advance to the lower layer and it bounced back as the foam absorbed the energy. In 20 J experiments, the maximum force was around 2500 N and the deformation was determined as 16 mm. In 10 J experiments, the sample resisted a force of approximately 1500 N and the deformation was determined to be approximately 9 mm.
Figure 8: KY-C-XPS force-deformation graph under 10 and 20 J impact energy
3.2 Sheep Wool Layered Composite Compression Test Results
ASTM C393-00 standard was used when applying this test method. According to this standard, the load applied to the samples advances 1 mm/min with the moving jaw [52,53]. Samples prepared in accordance with the standard were subjected to compression testing along their edges in the SHMADZU AUTOGRAPH AG-100 universal testing device. Images during sample testing are shown as in Fig. 9.
Figure 9: XPS sheep wool (a) Before the compression test (b) After the compression test
Compression testing of porous materials is a testing method used to evaluate how the material behaves under pressure. This test helps determine the amount of energy the material absorbs and its mechanical properties. The area under the compression test graph is an indicator of energy absorption. Similar to the data obtained in the impact tests, it was observed that the compressive strength of the two-layer samples was better than the single-layer ones.
Fig. 10 shows the XPS single and double layer force-deformation graph. When the graph is examined, when the compression test results on XPS core composite materials are examined, it is seen that the plastic destruction values are approximately 2200 N in XPS double layer samples and 1300 N in XPS single layer samples. Although the curves continued parallel to each other, they decreased slightly and continued horizontally, similar to the compression curves of porous structures. Due to the closure of the pores after approximately 50% deformation, the force increased and the experiment was terminated.
Figure 10: XPS single and double layer compression test force-deformation graph
3.3 Effect on Three Point Bending Strength
Three-point bending tests were examined in a single category, namely layer thickness. The samples were prepared in dimensions of 180 mm × 30 mm × 23 mm and 1 mm/min was selected as the device advance speed. In order to detect the breakage of the substrate in the experiments, a deformation of approximately 30 mm was applied to the samples (ASTM D790) [54]. Three samples from each layer were tested and the average of the results was taken and force-deformation graphs were drawn. Depending on the wool single-layer double-layer configuration shown in Fig. 11, the behavior of the beam under bending is shown in phase 3. When Fig. 11 is examined, separations and breaks in the core material and fiber layers were observed during the tests.
Figure 11: Compression test of XPS sheep wool sample (a) Single layer sample (b) Double layer sample
Fig. 12 shows the force-deformation graphs obtained from three-point bending tests of XPS single layer and XPS double layer For XPS-filled sheepwool, three separate test samples were used for each two layers. XPS single layer samples experienced first layer fracture with a deformation of approximately 8 mm and withstood a force of approximately 200 N. On the other hand, XPS double layer samples experienced first layer fracture with a deformation of approximately 12 mm and withstood a force of approximately 360 N. Based on these data, it is seen that XPS double layer samples have higher strength than XPS single layer samples.
Figure 12: XPS force-deformation graph
• In this study, tests were carried out to determine the mechanical properties of sheep’s wool fabric with XPS polytrene foam material in three configurations by performing single and two-layer compression, three-point and impact tests. To examine the impact behavior, tests were performed at two different energy values of 10 and 20 joules. In compression tests, the compressive strength of single and double layer samples increased by 70% more, while it was doubled between layers.
• In impact tests, sinking occurred in single-layer samples under 10 J impact energy. It was concluded that rebound occurred in the double-layer test samples under the same energy. In impact tests, punctures occurred in single-layer samples under 20 J impact energy. It was observed that under the same impact energy, stabbing occurred in the double-layer test samples.
• It has been concluded that the strength of the core and surface material increases as the layer thickness increases. As the layer thickness decreases, the strength of the material decreases. It can be concluded that the layer thickness of the material and the strength are directly proportional.
• As a suggestion to the study, composite material production can be improved by using different artificial fibers or different core structures instead of the natural fibers used in this study for future studies. This evaluation can provide insights into how these materials perform under various conditions relevant to impact resistance automotive applications.
• By identifying the most suitable combinations of fibers and polymers, the study could help develop composite materials with improved mechanical performance, lightweight potential and cost-effectiveness. Other researchers may investigate different types of natural fibers, polymer matrices, and processing techniques to optimize the properties of composites for automotive use.
Acknowledgement: The authors extend gratitude to all individuals who contributed to the completion of this study.
Funding Statement: The authors received no specific funding for this study.
Author Contributions: Kenan Budak: Data curation (equal); formal analysis (equal); investigation (lead); methodology (lead). Ercan Şimşir: Supervision (supporting); writing—review and editing (supporting). İbrahim Yavuz: Conceptualization (lead); data curation (equal); formal analysis (lead); funding acquisition (lead); project administration (lead); resources (lead); supervision (lead); writing—original draft (lead); writing—review and editing (lead).
Availability of Data and Materials: Data will be made available on request.
Conflicts of Interest: The authors declare that he has no conflicts of interest to report regarding the present study.
References
1. Gaurav, Gohal H, Kumar V, Jena H. Study of natural fibre composite material and its hybridization techniques. Mater Today: Proc. 2020;26:1368–72. doi:10.1016/J.MATPR.2020.02.277. [Google Scholar] [CrossRef]
2. Yogeshwaran S, Natrayan L, Rajaraman S, Parthasarathi S, Nestro S. Experimental investigation on mechanical properties of Epoxy/graphene/fish scale and fermented spinach hybrid bio composite by hand lay-up technique. Mater Today: Proc. 2021;37:1578–83. doi:10.1016/J.MATPR.2020.07.160. [Google Scholar] [CrossRef]
3. Reddy Nagavally R. Composite materials-history, types, fabrication techniques, advantages, and applications. Int J Curr Res. 2016;8(9):37763–8. [Google Scholar]
4. Lim HR, Kim HS, Qazi R, Kwon YT, Jeong JW, Yeo WH, et al. Advanced soft materials, sensor integrations, and applications of wearable flexible hybrid electronics in healthcare, energy, and environment. Adv Mater. 2020;32(15):1901924. doi:10.1002/adma.201901924. [Google Scholar] [PubMed] [CrossRef]
5. Hemath M, Mavinkere Rangappa S, Kushvaha V, Dhakal HN, Siengchin S. A comprehensive review on mechanical, electromagnetic radiation shielding, and thermal conductivity of fibers/inorganic fillers reinforced hybrid polymer composites. Polym Compos. 2020;41(10):3940–65. doi:10.1002/pc.25703. [Google Scholar] [CrossRef]
6. Ha NS, Lu G. A review of recent research on bio-inspired structures and materials for energy absorption applications. Compos Part B: Eng. 2020;181:107496. doi:10.1016/j.compositesb.2019.107496. [Google Scholar] [CrossRef]
7. Kim S, Nasirov A, Pokkalla DK, Kishore V, Smith T, Duty C, et al. Compression and energy absorption characteristics of short fiber-reinforced 2D composite lattices made by material extrusion. Eng Rep. 2023; 5(12):e12701. doi:10.1002/ENG2.12701. [Google Scholar] [CrossRef]
8. Pandey A, Upadhyay AK, Shukla KK. Multi-objective optimization of geometrical parameters of composite sandwich panels with an aluminum honeycomb core for an improved energy absorption. Mech Compos Mater. 2023;59(1):45–64. doi:10.1007/S11029-023-10080-3/TABLES/14. [Google Scholar] [CrossRef]
9. Xu F, Bao D, Cui Y, Gao Y, Lin D, Wang X, et al. Copper nanoparticle-deposited graphite sheets for highly thermally conductive polymer composites with reduced interfacial thermal resistance. Adv Compos Hybrid Mater. 2022;5(3):2235–46. doi:10.1007/S42114-021-00367-1/FIGURES/10. [Google Scholar] [CrossRef]
10. Ruan K, Shi X, Guo Y, Gu J. Interfacial thermal resistance in thermally conductive polymer composites: a review. Compos Commun. 2020;22:100518. doi:10.1016/J.COCO.2020.100518. [Google Scholar] [CrossRef]
11. Massaq A, Rusinek A, Klosak M, Bahi S, Arias A. Strain rate effect on the mechanical behavior of polyamide composites under compression loading. Compos Struct. 2019;214(6):114–22. doi:10.1016/J.COMPSTRUCT.2019.01.101. [Google Scholar] [CrossRef]
12. Bhujangrao T, Froustey C, Iriondo E, Veiga F, Darnis P, Mata FG. Review of intermediate strain rate testing devices. Metals. 2020;10(7):894. doi:10.3390/MET10070894. [Google Scholar] [CrossRef]
13. Liu Y, Meng J, Zhu L, Chen H, Li Z, Li S, et al. Dynamic compressive properties and underlying failure mechanisms of selective laser melted Ti-6Al-4V alloy under high temperature and strain rate conditions. Addit Manuf. 2022;54(7):102772. doi:10.1016/J.ADDMA.2022.102772. [Google Scholar] [CrossRef]
14. Şimşir E, Yavuz I, Erik Ç.M. Comparison of energies absorbed at different speeds of polymer materials used in vehicle bumpers. Konya J Eng Sci. 2021;4(9):2667–8055. doi:10.36306/konjes.932489. [Google Scholar] [CrossRef]
15. Alam MI, Maraz KM, Khan RA, Alam MI, Maraz KM, Khan RA. A review on the application of high-performance fiber-reinforced polymer composite materials. GSC Adv Res Rev. 2022;10(2):20–36. doi:10.30574/GSCARR.2022.10.2.0036. [Google Scholar] [CrossRef]
16. Rajak DK, Wagh PH, Linul E. A review on synthetic fibers for polymer matrix composites: performance, failure modes and applications. Materials. 2022;15(14):4790. doi:10.3390/MA15144790. [Google Scholar] [PubMed] [CrossRef]
17. Begum S, Fawzia S, Hashmi MSJ. Polymer matrix composite with natural and synthetic fibres. Adv Mater Process Technol. 2020;6(3):547–64. doi:10.1080/2374068X.2020.1728645. [Google Scholar] [CrossRef]
18. Elsheikh AH, Abd Elaziz M, Ramesh B, Egiza M, Al-qaness MAA. Modeling of drilling process of GFRP composite using a hybrid random vector functional link network/parasitism-predation algorithm. J Mater Res Technol. 2021;14(13):298–311. doi:10.1016/j.jmrt.2021.06.033. [Google Scholar] [CrossRef]
19. Karimah A, Ridho MR, Munawar SS, Adi DS, Ismadi DR, Subiyanto B, et al. A review on natural fibers for development of eco-friendly bio-composite: characteristics, and utilizations. J Mater Res Technol. 2021;13(10):2442–58. doi:10.1016/j.jmrt.2021.06.014. [Google Scholar] [CrossRef]
20. Jagadeesh P, Puttegowda M, Mavinkere Rangappa S, Siengchin S. A review on extraction, chemical treatment, characterization of natural fibers and its composites for potential applications. Polym Compos. 2021;42(12):6239–64. doi:10.1002/pc.26312. [Google Scholar] [CrossRef]
21. Keya KN, Kona NA, Koly FA, Maraz KM, Islam MN, Khan RA. Natural fiber reinforced polymer composites: history, types, advantages and applications. Mater Eng Res. 2019;1(2):69–85. doi:10.25082/MER.2019.02.006. [Google Scholar] [CrossRef]
22. Ahmed F, Mondal MIH. Introduction to natural fibres and textiles. Fundam Nat Fibres Text. 2021;7(5):1–32. doi:10.1016/B978-0-12-821483-1.00001-2. [Google Scholar] [CrossRef]
23. Rangasamy G, Mani S, Senathipathygoundar Kolandavelu SK, Alsoufi MS, Mahmoud Ibrahim AM, Muthusamy S, et al. An extensive analysis of mechanical, thermal and physical properties of jute fiber composites with different fiber orientations. Case Stud Therm Eng. 2021;28(5):101612. doi:10.1016/J.CSITE.2021.101612. [Google Scholar] [CrossRef]
24. Mann GS, Azum N, Khan A, Rub MA, Hassan MI, Fatima K, et al. Green composites based on animal fiber and their applications for a sustainable future. Polymers. 2023;15(3):601. doi:10.3390/POLYM15030601. [Google Scholar] [PubMed] [CrossRef]
25. Ramesh M, Deepa C, Rangappa SM, Siengchin S. Biocomposites reinforced with animal and regenerated fibers. Hybrid Fiber Compos. 2020;197–215. doi:10.1002/9783527824571.CH11. [Google Scholar] [CrossRef]
26. Jahandideh A, Ashkani M, Moini N. Biopolymers in textile industries. Biopolymers Their Ind Appl. 2021;214:193–218. doi:10.1016/B978-0-12-819240-5.00008-0. [Google Scholar] [CrossRef]
27. Vandepitte K, Vasile S, Vermeire S, Vanderhoeven M, van der Borght W, Latré J, et al. Hemp (Cannabis sativa L.) for high-value textile applications: the effective long fiber yield and quality of different hemp varieties, processed using industrial flax equipment. Ind Crops Prod. 2020;158:112969. doi:10.1016/J.INDCROP.2020.112969. [Google Scholar] [CrossRef]
28. Duque Schumacher AG, Pequito S, Pazour J. Industrial hemp fiber: a sustainable and economical alternative to cotton. J Clean Prod. 2020;268:122180. doi:10.1016/J.JCLEPRO.2020.122180. [Google Scholar] [CrossRef]
29. Kozlowski R, Muzyczek M. Hemp, flax and other plant fibres. Sustain Fibres Fashion Text Manuf. 2023;75–93. doi:10.1016/B978-0-12-824052-6.00017-2. [Google Scholar] [CrossRef]
30. Shuvo II. Fibre attributes and mapping the cultivar influence of different industrial cellulosic crops (cotton, hemp, flax, and canola) on textile properties. Bioresour Bioprocess. 2020;7(1):1–28. doi:10.1186/S40643-020-00339-1/FIGURES/22. [Google Scholar] [CrossRef]
31. Huda MK, Widiastuti I. Natural fiber reinforced polymer in automotive application: a systematic literature review. J Phys: Conf Ser. 2021;1808(1):012015. doi:10.1088/1742-6596/1808/1/012015. [Google Scholar] [CrossRef]
32. Mukhopadhyay SK, Partridge JF. Automotive textiles. Text Prog. 1999;29:1–2. doi:10.1080/00405169908688876. [Google Scholar] [CrossRef]
33. Bajwa DS, Bhattacharjee S. Current progress, trends and challenges in the application of biofiber composites by automotive industry. J Nat Fibers. 2016;13(6):660–9. doi:10.1080/15440478.2015.1102790. [Google Scholar] [CrossRef]
34. Arenas JP. Applications of acoustic textiles in automotive/transportation. In: Textile science and clothing technology. Singapore: Springer; 2016. p. 143–63. doi:10.1007/978-981-10-1476-5_7. [Google Scholar] [CrossRef]
35. Clark S. The design and prototyping of innovative sustainable material solutions for automotive interiors. UK: RoyalCollege of Art; 2018. [Google Scholar]
36. Alyousef R, Alabduljabbar H, Mohammadhosseini H, Mohamed AM, Siddika A, Alrshoudi F, et al. Utilization of sheep wool as potential fibrous materials in the production of concrete composites. J Build Eng. 2020;30(24):101216. doi:10.1016/j.jobe.2020.101216. [Google Scholar] [CrossRef]
37. Fantilli AP, Sicardi S, Dotti F. The use of wool as fiber-reinforcement in cement-based mortar. Constr Build Mater. 2017;139:562–9. doi:10.1016/j.conbuildmat.2016.10.096. [Google Scholar] [CrossRef]
38. Alyousef R. Enhanced acoustic properties of concrete composites comprising modified waste sheep wool fibers. J Build Eng. 2022;56(10):104815. doi:10.1016/j.jobe.2022.104815. [Google Scholar] [CrossRef]
39. Fiore V, di Bella G, Valenza A. Effect of sheep wool fibers on thermal insulation and mechanical properties of cement-based composites. J Nat Fibers. 2020;17(10):1532–43. doi:10.1080/15440478.2019.1584075. [Google Scholar] [CrossRef]
40. Koyuncu M, Tuncel E, Ferik A. Anadolu Merinosu, Kıvırcık, Türkgeldi koyunlarının yapağı verim ve özellikleri üzerine bir araştırma. Uludağ Üniv. Zir. Fak. Derg. 1996;12:101–8. [Google Scholar]
41. Mohamed M, Hussein R, Abutunis A, Huo Z, Chandrashekhara K, Sneed LH. Manufacturing and evaluation of polyurethane composite structural insulated panels. J Sandw Struct Mater. 2016;18(6):769–89. doi:10.1177/1099636215626597. [Google Scholar] [CrossRef]
42. Luo S, Xie Q, Da LJ, Qiu R. Experimental study on thermal structure inside flame front with a melting layer for downward flame spread of XPS foam. J Hazard Mater. 2019;379(329):120775. doi:10.1016/j.jhazmat.2019.120775. [Google Scholar] [PubMed] [CrossRef]
43. Sadek E, Fouad NA. Finite element modeling of compression behavior of extruded polystyrene foam using X-ray tomography. J Cell Plast. 2013;49(2):161–91. doi:10.1177/0021955X13477436. [Google Scholar] [CrossRef]
44. Ellouze A, Jesson D, Ben Cheikh R. The effect of thermal treatment on the properties of expanded polystyrene. Polymer Eng Sci. 2020;60(11):2710–23. doi:10.1002/pen.25502. [Google Scholar] [CrossRef]
45. Masso-Moreu Y, Mills NJ. Impact compression of polystyrene foam pyramids. Int J Impact Eng. 2003;28(6):653–76. doi:10.1016/S0734-743X(02)00148-3. [Google Scholar] [CrossRef]
46. Yeole P, Herring C, Hassen A, Kunc V, Stratton R, Vaidya U. Improve durability and surface quality of additively manufactured molds using carbon fiber prepreg. Polym Compos. 2021;42(4):2101–11. doi:10.1002/pc.25962. [Google Scholar] [CrossRef]
47. Mujahid Y, Sallih N, Mustapha M, Abdullah MZ, Mustapha F. Effects of processing parameters for vacuum-bagging-only method on shape conformation of laminated composites. Processes. 2020;8(9):1147. doi:10.3390/pr8091147. [Google Scholar] [CrossRef]
48. Sadighi M, Alderliesten RC, Benedictus R. Impact resistance of fiber-metal laminates: a review. Int J Impact Eng. 2012;49:77–90. doi:10.1016/J.IJIMPENG.2012.05.006. [Google Scholar] [CrossRef]
49. Park SW, Xia Q, Zhou M. Dynamic behavior of concrete at high strain rates and pressures: II. Numerical simulation. Int J Impact Eng. 2001;25(9):887–910. doi:10.1016/S0734-743X(01)00021-5. [Google Scholar] [CrossRef]
50. Zhao Y, Yang Z, Yu T, Xin D. Mechanical properties and energy absorption capabilities of aluminium foam sandwich structure subjected to low-velocity impact. Constr Build Mater. 2021;273(7):121996. doi:10.1016/J.CONBUILDMAT.2020.121996. [Google Scholar] [CrossRef]
51. Ghiaskar A, Nouri MD. Numerical and experimental investigation of impact strength and fracture mechanism of Kevlar and Hemp elastomeric thin biocomposite laminate under high-velocity impact: a comparative study. Mater Today Commun. 2023;37:106935. doi:10.1016/J.MTCOMM.2023.106935. [Google Scholar] [CrossRef]
52. Sutherland LS, Soares CG. Impact resistance of cork-skinned marine PVC/GRP sandwich laminates. Thin-Walled Struct. 2022;180:109830. doi:10.1016/J.TWS.2022.109830. [Google Scholar] [CrossRef]
53. Khalili S, Khalili SMR, Farsani RE, Mahajan P. Flexural properties of sandwich composite panels with glass laminate aluminum reinforced epoxy facesheets strengthened by SMA wires. Polym Test. 2020;89(1):106641. doi:10.1016/j.polymertesting.2020.106641. [Google Scholar] [CrossRef]
54. Anand Raj MK, Muthusamy S, Panchal H, Mahmoud Ibrahim AM, Alsoufi MS, Elsheikh AH. Investigation of mechanical properties of dual-fiber reinforcement in polymer composite. J Mater Res Technol. 2022;18(6):3908–15. doi:10.1016/j.jmrt.2022.04.053. [Google Scholar] [CrossRef]
Cite This Article
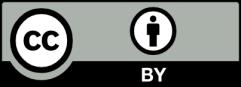
This work is licensed under a Creative Commons Attribution 4.0 International License , which permits unrestricted use, distribution, and reproduction in any medium, provided the original work is properly cited.