Open Access
ARTICLE
Effect of Tetramethylurea (TMU) on Polysulfone Membrane Performance for Atrazine-containing Wastewater Treatment
Department of Chemical Engineering, Sardar Vallabhbhai National Institute of Technology, Surat, Gujarat, India
* Corresponding Author: e-mail:
Journal of Polymer Materials 2023, 40(3-4), 317-328. https://doi.org/10.32381/JPM.2023.40.3-4.12
Abstract
Tetramethylurea (TMU) is a good solvent for organic substances and has received little attention as compared to other solvents. The TMU is a polar solution and is one of the molecules with an amphiphilic character. In the present work, an attempt has been made to use TMU as an additive in the preparation of nanofiltration membranes to improve the hydrophilicity of the membrane. The polysulfone membrane has been modified by incorporating different concentrations of TMU (0, 0.5, and 1 wt.%) in order to check the rejection of atrazine in water. This study aim is to optimize the conditions to enhance the flux and the rejection of atrazine. It was observed that the rejection of atrazine was enhanced when feed pH changed to acidic and with increasing the evaporation time. The prepared membranes were subjected to different analyses, such as contact angle measurement, FTIR, porosity, and mean pore size. The effect of the coagulation bath, evaporation time, and pH on the atrazine rejection was also studied. Membrane with 0.5 wt.% TMU shows maximum rejection of atrazine at the operating pressure of 15 kgf /cm2Keywords
Pesticides ultimately end up in soils when sprayed in the atmosphere, and then they are washed away due to rainwater reaching water bodies. The movement of pesticides depends on the solubility of pesticides in water and the adsorption capacities of soil. Low levels of pesticides may not show toxicity problems, but they have chronic effects on reproductive health and can cause cancer, fetal damage, neurologic and immunologic disorders[1].
Pesticides control living organisms like insects, fungi, weeds, and micro-organisms and interfere in the food chain by destroying plant life, affecting living organisms like human beings and animals. It is very important to control water quality as different pesticides have different decaying periods and are lethal to the environment even at low concentrations, unlike heavy metals. Nanofiltration (NF) is a promising technique for treating wastewater and drinking water, and it differs from the reverse osmosis separation process as it rejects multivalent and organic compounds and allows other molecules to pass. The nominal weight cut-off of the nanofiltration membrane is 100-1000 Da, and pesticides have molecular weight cut-off of 100. Hence nanofiltration is an efficient technology to retain pesticides depending upon the nature of the solute and membrane[2]. Nanofiltration membrane has substituted reverse osmosis membrane due to low energy consumption and high water flux[3],[4]. The ions in nanofiltration are separated by a combination of electrical and size effects of ultrafiltration and ion interaction mechanisms in reverse osmosis[5]. The nanofiltration membranes are finely porous and asymmetric membranes with pore sizes of 1-5 nm. NF membrane's typical pure water flux range is 20-200 L/m2h in the pressure range of 7-30 atm[6].
Atrazine is one of the most commonly used herbicides to control the broad leaf weeds in farming, which is frequently discovered in groundwater and surface water due to moderate solubility in water, long half-life (30-100 days), and high mobility. Atrazine has carcinogenic effects even at low concentrations, and it also acts as an endocrine disruptor that induces complete feminization of amphibians like Xenopus laevis, which can cause risk to human health[7]. Hence higher removal of atrazine is urgently needed, and NF can be considered a prominent solution.
Polysulfone is a popularly used polymer to manufacture polymeric membranes owing to its properties like excellent compaction resistance, mechanical strength, chemical & thermal resistance, and stability in a wide pH range from 2 to 12. Due to its hydrophobic nature, polysulfone membrane has been a hurdle in water treatment as hydrophobicity contributes to reduce permeability and causes fouling[8]. These membranes have high solubility in a broad range of polar solvents[9]. Hence attempts have been made to reduce the hydrophobicity of the membrane.
Ahmad et al.[1] studied the rejection of atrazine on four commercial membranes NF90, NF270, NF200, and DK. The authors found that the rejection of atrazine is enhanced by increasing the pH of the feed solution. The studies showed that NF90 is a more appropriate nanofiltration membrane for the rejection of atrazine as compared to NF270, NF200, and DK. Bodalo et al.[10] also studied the rejection coefficient of atrazine and permeate fluxes of various nanofiltration membranes like NF-99, NF-97, Desal-5-DL, and Desal-5-DK for separating atrazine from water at various operating conditions like concentration of feed, pressure, and pH of feed. NF99 and NF97 showed higher rejection of atrazine as compared to DK and DL. Krishnan et al.[11] studied the removal of atrazine–fulvic acid from water using different polymeric membranes incorporated with Bi2WO6 nanoparticles. The rejection efficiency observed was highest for cellulose acetate membrane, followed by PVDF, polyetherimide (PEI), and polysulfone (PSF). This is because of the strong bonding of nanoparticles with the CA membrane compared to other hybrid membranes.
The reduction of transport properties of ultrafiltration membrane for the mixture of atrazine and humic substances as feed at pH 7, the flux decreases and hence atrazine rejection increases[12]. Agbekodo et al.[13] also reported very high separation efficiency of atrazine depending on the concentration of natural organic matter in the water to be treated. Devitt et al.[14] observed that the rejection of atrazine increases with the relative concentration of dissolved oxygen matter (DOM) and atrazine in water. The separation efficiency of atrazine from aqueous solution depends on factors such as the type of organic matter and dissolved (or total) organic concentration (DOC or TOC), which was much better when the feed solution to be treated contained humic substances. A further increase in organic carbon concentration from 9.5 g C/m3 resulted in a decrease in aqueous phase atrazine removal[15]. Currently, researchers are working on exploring the performance of the nanofiltration membrane modified by different additives[16],[17]. Parvizian et al.[17] studied the polyethersulfone (PES) nanofiltration membranes performance made up of different concentrations of oleic acid - TiO2 nanoparticles. Results show the highest pure water flux with 0.05wt.% nanoparticles containing membrane due to increasing the hydrophobicity of the membrane with the addition of nanoparticles. Lasisi et al.[18] prepared a novel nanofiltration membrane using terephthalic acid (TPA) as an additive and tested for acid wastewater. The modified membrane shows good water permeability and salt rejection as compared to the pristine membrane. Hu et al.[19] prepared the nanofiltration PES membrane through crosslinking method for salt or dye removal. The results show excellent dye removal with a 99% water flux recovery ratio.
Due to the lack of hydrogen bridges comprising hydrogen on amide nitrogen, tetramethylurea (TMU), one of the urea derivatives, is liquid at room temperature and acts as a hydrogen bond acceptor. TMU is soluble in water and in all common organic solvents in all proportions, and solubility is 1 gram in 25 ml of water at 20°C[20]. The surface of this molecule comprises 4 lipophilic methyl groups that shield the carbonyl oxygen to a large extent[20]. TMU molecules do not form strong intermolecular hydrogen bonds, but dipole-dipole coupling through C=O bonds could occur only in liquid TMU, and that's the reason it is in the liquid state[21]. The Methyl group may not always show its hydrophobic character as it is hydrophobic based on the thermodynamic properties of amphiphilic aqueous solutions. The TMU is a polar solution and is one of the molecules with an amphiphilic character. Tetramethylurea ((CH3)2N)2 CO) is one of the examples which possess amphiphilic characteristics as well as the N-methyl group (-N-CH3)[21]. In this work, different concentrations of tetramethylurea have been added as filler to prepare the different membranes, and pure water flux and rejection of atrazine were studied. Simultaneously, the effect of the coagulation bath, evaporation time, and pH on the atrazine rejection was also studied.
Polysulfone (PSF) (442.52 g/mol) was purchased from Sigma Aldrich, India, N, N dimethylformamide (DMF with purity ≥99.5%) was used as a solvent, and obtained from Rankem Ltd., Tetramethylurea was procured from Sigma Aldrich. Methanol was acquired from TCI Analytics, atrazine (≥70 wt.%) was bought from Heranba Industries Limited, and HCl (30 wt.%) was purchased from Finar Chemicals. The distilled water was taken from Millipore (Elix, Bangalore, India).
The phase inversion method was used for the preparation of the membrane using Polysulfone (PSF) polymer and dimethylformamide (DMF) as solvent. The PSF of 20 wt.% concentration was dissolved in DMF to prepare the dope solution and kept for magnetic stirring for converting into a homogenous solution. The magnetic stirrer was maintained at 180 rpm for 3 hrs., and at 60°C temperature. Then 0.5 wt.% and 1 wt.% TMU was mixed with DMF and kept for sonication for 40 min. After sonication, the solution becomes more homogenous and the obtained solution was combined with prepared dope solution and kept for stirring for 2 hrs. After 2 hrs. of magnetic stirring the solution was degassed for 20 min so that all the bubbles if present can be removed. The final dope solution was poured on a properly washed and dried glass plate, and the membrane was cast with the help of a doctor blade using a 150 μm casting knife. Then, this casted membrane was immersed in the coagulation non-solvent bath for 24 hrs at room temperature. After that membrane was washed with distilled water and dried in air to obtain a flat sheet of membrane. Table 1 shows the fabricated membrane types and their compositions.
2.2.1 Effect of Evaporation Time
It is advantageous to have a volatile solvent in the membrane casting solution to investigate the evaporation step's influence on the membrane's performance. During this step, solvent gets vaporized from the selective portion of the membrane skin layer; hence, polymer concentration varies at different locations. It is stated when evaporation is taking place due to the loss of volatile solvent, the concentration of polymer on the surface of the membrane increases, which leads to the formation of a denser layer on the surface, hindering the rate of exchange of non-solvent and solvent resulting in a delay in de-mixing when the membrane is immersed in coagulation bath[22]. Pure water flux decreases with a longer evaporation time, and rejection increases with a minimum evaporation time of 30 s before immersing the membrane in the non-solvent bath. It was found that 30 s is the optimum evaporation time for good membrane performance as after that, rejection is almost constant, but permeate decreases on longer evaporation time. For evaporation time greater than 100 s, macrovoids are suppressed, but the number of macrovoids is reduced without changing shape on shorter evaporation time[23]. The coagulation bath conditions also affect the membrane performance as reported by the Xu et al.[24]. The authors used glacial acetic acid (GAA) and ethanol as coagulation bath medium and observed the 25% (w/w) of ethanol in distilled water reveals optimum condition for the membrane's performance and improved fouling properties.
2.3 Characterization of Membrane
2.3.1 Contact Angle (CA) measurement
The equipment used for the CA measurement was goniometer, OCA20 Data Physics Instruments Ltd., Filderstadt, Germany[25]. A total five CAs are measured at different locations of the membrane and finally average of five CAs were taken.
2.3.2 Fourier transform infrared spectroscopy (FTIR)
The FTIR spectrometer (FTIR-8400S SHIMADZU) was used to depict the occurrence of the polysulfone and TMU functional groups in the prepared membrane.
The porosity (ɛ) of the membrane was calculated using gravimetric method. The details of the procedure is explain by Gupta and Murthy[25]. The membrane porosity (ɛ) was measured by Equation (1)[26]:
where, m1 is weight of the wet membrane (g) and m2 is the weight of dry membrane. ρw (1 g/cm3) is the water density and (ρp 1.24 g/cm3) is the polymer density.
The mean pore radius of membranes (rm) was calculated by Guerout–Elford–Ferry equation. The expression is given in Equation (2)[27]:
Here Q is pure water permeability (m3/s), η is the viscosity of water (0.00089 Pa.s), A denotes the nominal membrane area (m2), l is the membrane thickness (m), ɛ denotes the membrane porosity and ΔP be the operating pressure.
The thickness gauge meter supplied by Baker gauges India Private Limited used to compute the membrane thickness. During measurement, the two metal bezels sandwiches the membrane and dial gauge give the reading accordingly. Similarly, as CAs measurement, the membrane thickness was also measured at five different locations and the average was calculated.
The experimental studies were carried out in a setup containing reciprocating pump of diaphragm type (mROY B-13), membrane test cell, pressure gauge and a needle valve. The experiments were conducted at a constant flow rate of 45 L/h and operating pressure of 5 kgf/cm2 to 25 kgf/cm2 using a cross-flow membrane test cell with a nominal area of 20.4 cm2. Atrazine (herbicide) dissolved in water was used as a feed with a 22 mg/L concentration. The pH of the feed was also reduced from 6.8 to 4. The feed solution prepared was distributed throughout the setup for a minimum of 30 minutes to collect the rejection data. Pure water flux (PWF) was calculated using the formula given in Equation (3)[28],[29]:
Here Jw is the PWF (L/m2.h), V is permeate volume collected in a time interval t (h). The feed and permeate concentrations were determined by UV-Vis Spectrophotometer by plotting the calibration curve using the wavelength at which there is maximum absorbance of atrazine. Percentage rejection (% R) was found using the Equation (4):
Here Cf and Cp are the concentration of atrazine at the feed and permeate side.
The contact angle is a crucial factor in determining a membrane's fouling characteristic. Low the contact angle, the more is the hydrophilicity of the membrane. Hydrophilicity is one of the major features affecting the membrane's flux and antifouling ability. In this experiment, we see that as we use tetramethylurea (TMU) as an additive to modify polysulfone membrane, the contact angle reduces from 96.2° to 79°. As the concentration of TMU was decreased from 1% to 0.5%, the contact angle reduced from 79° to 67°. This is shown schematically in Fig. 1.
Fig. 1.: Water contact angle of different membranes
The FTIR of pure polysulfone membrane with peaks in the range of 1000 to 1500 cm-1 and that of polysulfone membrane with peaks in the range of 500 to 1700 cm-1. FTIR peaks of prepared polysulfone membranes and TMA are tabulated in Tables 2 and 3; the graph is plotted in Figs. 2 and 3.
Fig. 2.: FTIR of pure polysulfone membrane
Fig. 3.: FTIR of polysulfone membrane with 0.5% TMU
Pure water permeability of different membranes with varied compositions of TMU was measured. Water permeation was augmented at 1 and 0.5 (wt.%) of TMU. Incorporating TMU as an additive for the preparation of modified membranes had two major effects on the properties of the membrane; increasing the concentration of TMU from 0 to 1 (wt.%) in membrane composition decreases the hydrophilicity of the membrane and changes the structure as well as the porosity of membrane. The contact angle recorded for different membranes with varied TMU concentrations validates that incorporating TMU improved the hydrophilicity of the membrane as compared to pure polysulfone membranes. As a result, the pure water flux of TMU integrated membrane was higher compared to pure polysulfone membrane. Even though 0.5 and 1 (wt.%) TMU-incorporated membranes showed better hydrophilicity, but their pure water flux was not the highest (Fig. 4).
Fig. 4.: Plot of PWP of different membranes at different Pressures
Pure water Permeability was compared at a fixed pressure of 10 kgf/cm2 at different membrane compositions as shown in Fig. 5. It was observed that the PWP of virgin polysulfone membrane was lowest as it is densely packed with the smallest pore size. As the concentration of TMU decreased from 1% to 0.5 (wt.%) hydrophilicity of the membrane and PWP increased. But on the other hand, when M2 membrane was compared with the M3 membrane, where the coagulation bath composition was methanol in water (1:4 wt.%) and evaporation time was increased from 5 s to 40 s pore size was found to be decreased, which resulted in a decrease in PWP.
Fig. 5.: PWP of different membranes at 10 kgf/cm2
3.4 Porosity and Mean Pore Radius
Porosity and mean pore radius for various membranes are tabulated in Table 4. As the concentration of TMU is decreased from 1 to 0.5 (wt.%), porosity increases, and the mean pore radius decreases. This is due to with decrease in the concentration of TMU, the hydrophilicity of the membrane increases. On the other hand, when at the same composition of membranes with 1 (wt.%) of TMU, coagulation bath conditions and evaporation time was increased, and voids shrank.
3.5 Effect of TMU Concentration on Rejection of Atrazine
Different parameters affect the retention of solute and rejection mechanisms in nanofiltration. The vital factors affecting the rejection of solute are its molecular size and weight, hydrophilicity or hydrophobicity, acid dissociation constant (Log Kow), and polarity. Similarly, the main membrane factors affecting rejection performance are its porosity, charge on the surface, membrane cut-off weight, and hydrophilicity/hydrophobicity. These parameters about membrane and feed solute are of great importance as they give a clear idea about the separation mechanism. Log Kow is deciding factor for validating the hydrophobicity or hydrophilicity of the membrane. Atrazine is hydrophobic in nature as its value of Log Kow =2.61; if Log Kow > 2, then it is hydrophobic. Due to the hydrophobic nature of atrazine, it tends to resist hydrophilic membranes[10], so with the decrease in the concentration of TMU from 1 to 0.5 (wt.%), the hydrophilicity increases; hence rejection increases. The rejection data for different membrane compositions are shown in Fig. 4.
3.6 Effect of Coagulation Bath and Evaporation time Over Rejection of Atrazine
On increasing the concentration of methanol in distilled water for the coagulation bath, pore size becomes more prominent and then shrinks, improving the hydrophilicity and antifouling property of the membrane. Using methanol as a coagulation bath component improved the hydrophilicity of the membrane and led to the enhanced rejection of the hydrophobic component atrazine. 25% (w/w) concentration of methanol in water is optimum for improved membrane performance. Hence we have used 25% (w/w) of methanol solution as coagulation bath resulting in increased rejection of atrazine. Pure water flux decreases with longer evaporation time, but there is a significant change in rejection only for 30 s of evaporation time before immersing the film in the coagulation non-solvent bath. It was studied that 30 s is the optimal evaporation time to study the membrane performance as rejection remains constant on further increasing the evaporation time. Also, the pores are suppressed on evaporation time of more than 100 s but on shorter evaporation time number of voids decreases without changing their shape.
3.7 Effect of pH on Rejection of Atrazine
Acidic hydrolysis is responsible for increasing hydrophilic sites at the membrane surface that ultimately increases permeate flux. Also, at low pH, due to hydration swelling of the membrane, pore size decreases, thus reducing the permeation of atrazine through the membrane. Here when the pH of the feed was changed from 6.8 to 4, the rejection of atrazine increased due to acidic hydrolysis, which causes hydration swelling of the membrane, shrinking the pore size and hence increases the rejection. Here M5 shows the rejection of the M4 membrane when feed pH changes from 6.8 to 4 as shown in Fig. 6.
Fig. 6.: Rejection study of atrazine of different membranes at 15 and 20 kgf/cm2
Nanofiltration is one of the efficient techniques due to its lower energy requirement as compared to other separation processes. Due to this feature, it has been used for treating wastewater and drinking water. Here atrazine used for rejection studies is hydrophobic, and the polysulfone membrane used is also hydrophobic. So tetramethylurea has been used as an additive to enhance the membrane's hydrophilicity and improve the rejection of atrazine. FTIR plot confirms the presence of TMU in the polysulfone membrane. As the concentration of TMU was varied from 1 to 0.5 (wt.%) in polysulfone, the hydrophilicity of the membrane was improved, and hence rejection was enhanced. Also, by changing the feed pH, the rejection of atrazine was increased slightly. Rejection of atrazine was enhanced from 0% to 15% by the following factors:
The concentration of TMU, used as an additive, was varied from 1 to 0.5 (wt.%) in polysulfone membrane, contact angle decreases from 96.2° (M1) to 67° (M4). The hydrophilicity of the membrane was observed to be improved, and hence rejection efficiency was enhanced.
During membrane formation, when the evaporation time of the membrane was increased from 5 s to 40 s, pores on the membrane shrink, reducing the pores' size. So, it also helps in improving rejection to some extent.
When methanol and water (in a ratio of 1:4 wt.%) were used as coagulation bath instead of distilled water, the hydrophilicity of the membrane was enhanced and improved the separation efficiency of the membrane.
As the pH of the feed containing atrazine was reduced from 6.8 to 4, due to acidic hydrolysis, there is hydration swelling of the membrane, which reduces the pore's size, hence reducing the permeation of atrazine through the membrane.
References
1. Ahmad AL, Tan LS, Abd. Shukor SR. (2008). J Hazard Mater. 154(1-3):633-638. [Google Scholar]
2. Ahmad AL, Tan LS, Shukor SRA. (2009). Chem Eng J. 147(2-3):280-286. [Google Scholar]
3. Cadotte J, Forester R, Kim M, Petersen R, Stocker T. (1988). Desalination. 70(1-3):77-88. [Google Scholar]
4. Gozálvez JM, Lora J, Mendoza JA, Sancho M. (2002). Desalination. 144(1-3):341-345. [Google Scholar]
5. Bowen WR, Welfoot JS, Williams PM. (2002). AIChE J. 48(4):760-773. [Google Scholar]
6. Shon HK, Phuntsho S, Chaudhary DS, Vigneswaran S, Cho J. (2013). Drink Water Eng Sci. 6(1):47-53. [Google Scholar]
7. Wu S, Li H, Li X, He H, Yang C. (2018). Chem Eng J. 353(June):533-541. [Google Scholar]
8. Homayoonfal M, Akbari A, Mehrnia MR. (2010). Desalination. 263(1-3):217-225. [Google Scholar]
9. Rezaee R, Nasseri S, Mahvi AH, et al. (2015). J Environ Heal Sci Eng. 13(1):1-11. [Google Scholar]
10. Bódalo A, León G, Hidalgo AM, Gómez M, Murcia MD, Blanco P. (2010). Desalin Water Treat. 13(1-3):143-148. [Google Scholar]
11. Krishnan SAG, Gumpu MB, Arthanareeswaran G, Goh PS, Aziz F, Ismail AF. (2023). Chemosphere. 311(P2):137016. [Google Scholar]
12. Majewska-Nowak K, Kabsch-Korbutowicz M, Dod M. (2002). Desalination. 145(1-3):281-286. [Google Scholar]
13. Agbekodo KM, Legube B, Dard S. (1996). Water Res. 30(11):2535-2542. [Google Scholar]
14. Devitt EC, Ducellier F, Cote P, Wiesner MR. (1998). Water Res. 32(9):2563-2568. [Google Scholar]
15. Majewska-Nowak K, Kabsch-Korbutowicz M, Dod M, Winnicki T. (2002). Desalination. 147(1-3):117-122. [Google Scholar]
16. Mahdavi H, Hosseini F. J Taiwan Inst Chem Eng. (2023);142(November 2022):104609. [Google Scholar]
17. Parvizian F, Ansari F, Bandehali S. (2020). Chem Eng Res Des. 156:433-441. [Google Scholar]
18. Lasisi KH, Zhang K. (2022). J Memb Sci. 644 (October 2021):120155. [Google Scholar]
19. Hu D, Li Y, Yan Z, Li S, Xu M, Wang C. (2022). J Ind Eng Chem. 112:348-357. [Google Scholar]
20. Lüttringhaus A, Dirksen HW. (1964). Angew Chemie Int Ed English. 3(4):260-269. [Google Scholar]
21. Mink J, Hajba L, Pápai I, et al. (2010). Appl Spectrosc Rev. 45(4):274-326. [Google Scholar]
22. Indra Sandipa, Biswas Ranjit. (2016). J Chem Sci. 128(5):753-761. [Google Scholar]
23. Hołda AK, Aernouts B, Saeys W, Vankelecom IFJ. (2013). J Memb Sci. 442:196-205. [Google Scholar]
24. Xu J, Tang Y, Wang Y, Shan B, Yu L, Gao C. (2014). J Memb Sci. 455:121-130. [Google Scholar]
25. Gupta N, Murthy ZVP. (2022). Mater Today Chem. 23:100685. [Google Scholar]
26. Park MJ, Phuntsho S, He T, et al. (2015). J Memb Sci., 493:496-507. [Google Scholar]
27. Li JF, Xu ZL, Yang H, Yu LY, Liu M. Appl Surf Sci. (2009);255(9):4725-4732. [Google Scholar]
28. Babu J, Murthy ZVP. (2017). Sep Purif Technol. 183:66-72. [Google Scholar]
29. Singh PS, Joshi S V., Trivedi JJ, Devmurari C V., Rao AP, Ghosh PK. (2006). J Memb Sci., 278(1-2):19-25. [Google Scholar]
30. Schafer M, Curran C. (1996). Inorg Chem. 5(2):265-268. [Google Scholar]
31. Giesbrecht E, Kawashita M. (1970). J Inorg Nucl Chem. 32:2461-2464. [Google Scholar]
Cite This Article
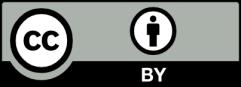
This work is licensed under a Creative Commons Attribution 4.0 International License , which permits unrestricted use, distribution, and reproduction in any medium, provided the original work is properly cited.