Open Access
ARTICLE
Rheological Study on Blend Solutions of Non-mulberry Silk Fibroin and Gelatin Biopolymers
1
Discipline of Paint Technology, Department of Paint Technology, Mahamaya Polytechnic of
Information Technology, Chail Kaushambi, Uttar Pradesh, India.
2 Department of Paint Technology, School of Chemical Technology, Harcourt Butler Technical
University, Kanpur, India.
3
Discipline of Polymer Science and Chemical Technology, Department of Applied Chemistry,
Delhi Technological University, Shahbad Daulatpur, Delhi, India.
* Corresponding Author:
Journal of Polymer Materials 2023, 40(3-4), 205-214. https://doi.org/10.32381/JPM.2023.40.3-4.6
Abstract
In current research work, we have studied the blending effect of non-mulberry silk fibroin (10% weight/volume basis) and gelatin (20% weight/volume basis) in formic acid. Several blends as SF10G0, SF2G8, SF3G7, SF5G5 and SF0G10 have been made and their rheological behaviour was investigated. The blend solutions were subjected to a steady shear rheological study in the variety of range of shear rates, namely 0.01–500 sec-1 and the viscosities of blend solutions were noticed to decrease in comparison to pure silk solution. The frequency sweep was employed in dynamic rheological tests to determine complex viscosity of these solutions from range of angular sweep 0.1–100 rad/sec. The consistent shear-thinning behaviour was noted for all the blends. The difference in numerical values of shear and complex viscosities indicated disobedience of Cox-Merz rule. Such analysis can be utilised for tailoring the properties of solution prior to processing them to create a versatile range of materials.Keywords
Polymer solutions with the capacity to change their properties while in the solution state can be used to create materials with desired properties, and rheological studies are among the most extensively used approaches to study such alterations. Rheological analysis of polymer solutions can be used to fine-tune the process parameters that will be employed to create new materials.
Silk comes from silkworms and is a natural biopolymer. It has unique properties, such as being the strongest, having a high crystallinity, having good mechanical strength, being biocompatible, biodegradable, non-toxic, antibacterial, antioxidant, UV resistant, non-immunogenic, and readily available. There are two primary constituents of silk: 1. Fibroin (70-80%), 2. Sericin (20-30%). The fibroin, silk's structural centre, is widely popular for its toughness, thermal stability, and biodegradability. The sericin component acts as an adhesive, allowing fibroins to stick together. There are two types of silk. 1) the mulberry (Bombyx mori) and 2) the non-mulberry (wild silk worms such as A. mylitta, A. assamensis, P. ricini, etc.). Due to its poor solubility in common solvents, processing non-mulberry silk is significantly more challenging than mulberry silk. It contains arginine-glycine-aspartate (RGD) amino acid sequence, which encourages cell adhesion and proliferation, may be advantageous in biomedical applications.[1] Non-mulberry silk is being investigated as a natural biomaterial for use in various biotechnological and biomedical applications.[2] After numerous attempts, researchers finally found a solvent that could dissolve non-mulberry silk fibroin, such as ionic liquids.[3] Hydrogen bonds of non-mulberry silk are destroyed during dissolution, altering its structural arrangements, and affecting their physiological properties. For the purpose of recovering and enhancing physiological properties such as mechanical strength, flexibility, and biodegradability, other polymers such as chitosan, elastin, polyvinyl alcohol, etc. are blended with silk fibroin.[4] The physiological characteristics of the final products made from silk fibroin blends were the focus of the majority of research on biocompatibility, biodegradability, cell recognition.[5-7] However, little attention has been paid to the characteristics of blend solutions that can influence the characteristics of the final product. There are very few reports on rheological tests of mulberry silk fibroin.[3, 8]
Gelatin is produced from animal tissues, such as skin, muscles, and bones, after collagen is partially hydrolysed. Given its biocompatibility, biodegradability, water solubility, non-immunogenicity, and affordability, gelatin is one of the practical options for blending with non-mulberry silk fibroin.[9] Gelatin has arginine-glycine-aspartate (RGD) sequences, which allow it to bind to cells.[10-13] Both the polymers are come under category of biopolymers and at the same time both have RGD sequence which favours biomedical and tissue engineering applications. Furthermore, upon blending of these two polymers an upgraded class of material is created with combine properties than either of the pure polymers alone. Rheological analysis may shed light on the viability of their blending before giving a shape to silk fibroin/gelatin blend solutions in material form.
Holland et al. studied the rheological characteristics of non-mulberry silk for frequency sweep and steady shear viscosity. They reported that non-mulberry silk behaves like a viscoelastic fluid in dynamic oscillatory and shear thinning in steady shear analysis[14]. Kokol et al. investigated the rheological properties of gelatine hydrogels and discovered that when gelatine concentration increased from 5 to 10% in Milli-Q water, the material exhibited a transition from a viscoelastic fluid to a solid. Shear thinning behaviour is respective of concentration[15]. Very limited literatures are available yet so it is almost unexplored area in respect of non-mulberry silk and gelatin blends. A research work on biomedical application of their blends was found which is reported by Batra and Purwar[16]. They prepared blend films and studied structural, thermal, and bio-degradable properties of the same. Though rheological study plays a crucial role in product fabrication process, it is left untouched which made the importance of rheological study of non-mulberry silk fibroin and gelatin blends.
In the present study, steady shear rheological experiments were used to examine the rheological behaviour of pure as well as blends of silk fibroin and gelatin. The resulting curves demonstrate how the shear viscosity of solution and its shear rate relate to one another. Dynamic rheological experiments were used to measure the complex viscosity of pure polymeric solutions and their blend solutions. All these investigations were done to learn more about the characteristics of pure solutions of silk fibroin and gelatin, as well as those of their blends.
Non-mulberry silkworm cocoons of grade Antheraea mylitta were supplied by the Central Silk Board in Son Bhadra, Uttar Pradesh, India. BMIMAC (1-butyl-3-methylimidazolium acetate), an ionic liquid, was provided by Sigma Aldrich. Gelatin bacteriological grade polymer (average M.W. 20000 g mol-1) and Slide-A-Lyzer dialysis flask (20K MWCO, 250 mL) were supplied by Thermo Scientific, India. Lab grade formic acid with a 98% purity was provided by Loba Chemie Pvt. Ltd. in India. Milli-Q water was used to dialyze the silk fibroin ionic solution
2.2 Preparation of stock solutions for non-mulberry silk fibroin, gelatin, and their blends
To eliminate the sericin component of Antheraea mylitta silkworm cocoons, it was first degummed. In degumming process, the cocoons were divided into small pieces and heated twice for 30 minutes at 100°C in distilled water containing 0.02 M NaHCO3. To remove any remaining sericin, the fibroin was subjected to two washes with distilled water. The degummed silk fibers were dried overnight in oven at 60°C[17]. The degummed silk fibers were utilised to make a solution in BMIMAc ionic solution, which was then dialyzed for a week against milli Q water. To produce fully dry silk fibers, this aqueous solution of silk fibroin was dried at 100°C. Formic acid was used to prepare stock solutions of dried silk fibroin (10% w/v) SF10G0 and gelatin (20% w/v) SF0G10. These stock solutions were then used to create various desired blend solutions with blend ratios of 50:50, 30:70, and 20:80 (based on weight basis), such as SF5G5, SF3G7, and SF2G8, respectively.
Modular Compact Rheometer (MCR 302) by Anton Paar was used to measure the rheological parameters of all the prepared blend solutions at 25°C, including shear viscosity and complex viscosity. All the experiments were carried out using concentric parallel plates PP40 (diameter of 40 mm) with gap of 0.70 mm. Steady shear rheology tests with shear rates ranging from 0.1 to 500 sec-1 were used to measure the viscosities of all the blends. The studies on dynamic shear rheology were done with frequencies ranging from 0.1 to 100 rad/sec to determine complex viscosity at various strain levels for various solutions.
3.1 Rheological analyses of solutions of silk fibroin/gelatin under steady shear condition
At a temperature of 25°C, the steady shear profiles of solutions containing a blend of silk fibroin and gelatin were examined, as depicted in Fig. 1. The SF10G0 solution had the highest viscosity and the SF0G10 solution had the lowest in the shear rate range (0.1-500 s-1), meaning that SF10G0 had the most polymeric chain entanglement and SF0G10 had the least. Similar behavior in silk[18] and in gelatin[19] were reported. When these two were blended, it was observed that the blend viscosity varied depending on which polymeric component was used. Because higher silk fibroin content provides more entangled chains, the blends with higher silk fibroin composition (SF5G5) had a higher viscosity as well as more entangled than blend solutions with more gelatin content (SF3G7, SF2G8) and found less entangled.
Fig. 1.: Shear rheological plots of pure and blends, prepared with silk fibroin and gelatin stock solutions at 25°C with various blending ratios (a) SF10G0, (b) SF5G5, (c) SF3G7, (d) SF2G8 and (e) SF0G10.
Furthermore, the viscosity of pure silk fibroin solution reduced significantly as the shear rate was raised from 0.1 to 500 s-1. However, no such reduction was found in pure gelatin solution. There was evidence of higher uncoiling or disentanglement of polymeric chains in silk polymer when shear rate was increased than in gelatin polymer. The blend solutions, as expected, displayed a falling trend in viscosity that was intermediate to the pure polymeric solutions, with this tendency being more prominent in solutions with a higher silk content. Shear thinning is a viscosity reduction phenomenon generated by a high shear rate.[20]
3.2 Rheological behaviors of silk fibroin/gelatin blend solutions under dynamic shear condition
The frequency dependent complex viscosity for pure as well as their blends were examined at 25°C under dynamic shear profiles, as illustrated in Fig. 2. Within the applied frequency range (0.1-100 rad/sec-1) in predetermined % shear strains of blend solution as determined by amplitude sweep, (SF10G0=1%, SF5G5=1%, SF3G7=10%, SF2G8=10%, and SF0G10=10%) was maintained constant for the respective solution within the LVE region. SF10G0 solution had the highest complex viscosity, SF0G10 solution had the lowest, and SF2G8, SF3G7, and SF5G5 solutions were in between, as expected, like shear viscosity trends illustrated in Fig. 1.
Fig. 2.: Dynamic shear rheological curves of a solution of silk fibroin and gelatin at 25°C for various blending ratios
As shown in Fig. 3, the difference between complex viscosity and shear viscosity values of all blend solutions was higher at low frequencies than at high frequencies except SF2G8 solution. All curves moved closer to one another as the angular frequency increased except SF2G8 sample; also, the complex viscosity of SF0G10, SF2G8, and SF3G7 was constant at high frequencies resulted most of the chains were aligned and it indicates that the density of chain entanglement was high at low frequencies. The complex viscosity reduces as frequency rises, implying that chains align and the density of disentangled chains rises which indicates shear-thinning behaviour of all the blend solutions. In the literature,[21] the same behaviour was reported. Pure silk solution (SF10G0) showed the most shear-thinning, implying a random orientation and highly entangled state of silk polymeric chains, which detangle and become orientated under high frequency, resulting in a reduction in viscosity. Pure gelatin, on the other hand, has the least entangled or random orientation of chains, resulting in the least amount of shear thinning. When these two were blended, it was observed that the complex viscosity of blend solutions was varied depending on which polymeric component was used. Because higher silk fibroin content provides more entangled chains and the blend solution contains higher silk fibroin (SF5G5) shown a higher viscosity as compared with other blend solutions with higher gelatin composition (SF3G7, SF2G8) that are less entangled chains. These results confirmed our steady shear viscosity data. When the applied shear rate and angular frequency are equivalent, the Cox-Merz rule states that both the shear viscosity and complex viscosities should be numerically equal.
Fig. 3.: Diagram of η and η* for pure silk fibroin, gelatin and their blends with various blending ratios SF10G0 (b) SF5G5 (c) SF3G7 (d) SF2G8 (e) SF0G10.
A comparison of the complex and shear viscosity graphs that consider the viscous properties of pure and blends is displayed in Fig. 3. Shear viscosity and complex viscosity of pure silk fibroin and blend solutions showed an almost identical trend but in terms of numerically values it was found different, which contradicted the well-known Cox-Merz rule despite being studied under both constant and dynamic conditions. Pure gelatin solution curves only overlapped in terms of complex and shear viscosities, indicating agreement with the Cox-Merz rule, which failed in the other solutions. SF2G8 had a shear viscosity that was higher than its complex viscosity, but SF5G5 exhibited the exact opposite trend. At low frequencies (below the frequency of 1 rad/sec), complex viscosity was greater than shear viscosity in the case of SF3G7, whereas the opposite trend was observed at high frequencies. Different entanglement states of blend components might explain the Cox-Merz rule disagreement.[22] According to observations in the literature, the types of entanglement between polymeric chains in the solution affect the values of complex and shear viscosities.[23] Table 1 shows the comparative shear and complex viscosity results of all the solutions at low shear rates/frequencies and high shear rates/frequencies. This illustrates that both shear and complex viscosity have the same shear thinning patterns.
On an average basis, shear and complex viscosities were calculated at low and high shear rates and angular frequencies respectively. To calculate their values, five beginning points and five last points of shear/complex viscosities were taken at low and high shear rates/angular frequencies and averages were taken.
The rheological behaviour of pure as well as blend solutions of silk fibroin and gelatin in different ratios was studied by steady and dynamic shear tests. At rest (zero shear rate), the highest viscosity was found in the SF10G0 (neat silk fibroin) solution, while the lowest was found in the SF0G10 (neat gelatine) solution.
Furthermore, the viscosity of pure silk fibroin solution was seen to significantly decrease as the shear rate was increased, whereas such measurable reduction did not occur in case of pure gelatin solution. The viscosities of all the blends were observed between viscosities of those of pure solutions and displayed shear-thinning behaviour. According to curves of viscosity vs shear rate, it was found that gelatin, which had previously been observed to be non-Newtonian in its pure form, started to exhibit Newtonian behavior at high shear rates when silk fibroin solution was blended to it. Every other solution disobeyed from the Cox-Merz rule, apart from pure gelatin solution. Which could have been caused by differences in chain entanglement. The viscoelasticity of solutions can generally be altered by factors such as bend ratio, shear rate and angular frequency by which a desired product can be obtained with adjustable properties. In order to prepare new materials/products with customizable properties using silk fibroin and gelatine and their blends, the current study will aid in optimizing the processing parameters, such as shear rate and flow rates required for various techniques such as electrospinning, film casting, spin coating, etc.
Conflict of Interest: The authors state that they have no competing interests in this study.
References
1. S. Jasmine and B. B. Mandal. (2014). Woodhead Publishing Limited. [Google Scholar]
2. B.B. Mandal and S.C. Kundu. (2010). Acta Biomater, 360-371. [Google Scholar]
3. H.Y. Wang, Z.G. Wei and Y.Q. Zhang. (2020). Int. J. Biol. Macromol, 594-601. [Google Scholar]
4. A. Sionkowska. (2011). Prog. Polym. Sci. 1254-1276. [Google Scholar]
5. P. Bhattacharjee. (2015). Eur. Polym. J, 490-509. [Google Scholar]
6. D. Chouhan, B. Chakraborty, S.K. Nandi and B.B. Mandal. (2016). Acta Biomaterialia. [Google Scholar]
7. S.C. Kundu. (2016). Colloids Surfaces B Biointerfaces, 431-439. [Google Scholar]
8. X. Zhang and Z. Pan. (2020). J. Mater. Sci, 15350-15363. [Google Scholar]
9. C.S. Ki. (2005). Polymer, (Guildf) 5094-5102. [Google Scholar]
10. E. Hoch, C. Schuh, T. Hirth, G.E.M. Tovar and K. Borchers. (2012). J. Mater. Sci. Mater. Med, 2607-2617. [Google Scholar]
11. A. Mota. (2014). Cell J, 1-10. [Google Scholar]
12. Q. Xing. (2014). Sci. Rep, 1-10. [Google Scholar]
13. A.A. Aldana and G.A. Abraham. (2017). Int. J. Pharm, 441-453. [Google Scholar]
14. C. Holland, D. Porter and F. Vollrath. (2012). Biopolymers, 362-367. [Google Scholar]
15. V. Kokol, Y.B. Pottathara, M. Mihelèiè and L.S. Perše. (2021). Colloids Surfaces A Physicochem. Eng. Asp, 616. [Google Scholar]
16. R. Batra and R. Purwar. (2021). Polym. Int., 73-82. [Google Scholar]
17. Sreenivasa Reddy Perla and S Padmanabhan. (2019). International Journal of Research in Advent Technology, 184-192. [Google Scholar]
18. D. Keerl and T. Scheibel. (2014). Green Mater. 11-23. [Google Scholar]
19. L. Zhang, C. Qiao, Y. Ding, J. Cheng and T. Li. (2012). J. Macromol. Sci. Part B Phys. 747-755. [Google Scholar]
20. B.N. Singh, N.N. Panda, R. Mund and K. Pramanik. (2016). Carbohydr. Polym. 335-347. [Google Scholar]
21. E.V. Prut, T.I. Medintseva and O.P. Kuznetsova. (2021). 166-176. [Google Scholar]
22. K. Yasuda, R.C. Armstrong and R.E. Cohen. (1981). Rheol. Acta, 163-178. [Google Scholar]
23. S. Li, P. Jarvela and P. Jarvela. (2001). Polym. Eng. Sci. [Google Scholar]
Cite This Article
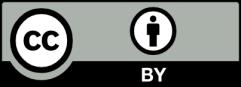
This work is licensed under a Creative Commons Attribution 4.0 International License , which permits unrestricted use, distribution, and reproduction in any medium, provided the original work is properly cited.