Open Access
REVIEW
A Brief Review of Surface Modification of Carbonyl Iron Powders (CIPs) for Magnetorheological Fluid Applications
A School of Integrative Engineering, Chung-Ang University, Seoul, Republic of Korea.
B Bavarian Center for Battery Technology (BayBatt) and Department of Chemistry, University
of Bayreuth, Universitätsstraße 30, 95447 Bayreuth, Germany.
C Department of Molecular Science and Technology, Ajou University, Suwon 16499,
Republic of Korea.
* Corresponding Authors: e-mail:,
,
Journal of Polymer Materials 2023, 40(3-4), 191-204. https://doi.org/10.32381/JPM.2023.40.3-4.5
Abstract
Magnetorheological fluids (MRFs) is a smart fluid system that exhibits swift and reversible alterations in their rheological characteristics when exposed to an external magnetic field. MRFs are used for applications in various areas, including automotive systems, robotics, aerospace, and civil engineering. The performance of MRFs depends on the behavior of the dispersed magnetic particles, necessitating thoughtful consideration of particle traits to optimize fluid performance. Carbonyl Iron Powders (CIPs), high purity iron (>98%) reduced from penta carbonyl iron, are widely employed in MRFs due to their exceptional magnetic characteristics. Nevertheless, the innate surfaces of CIPs tend to conglomerate, leading to compromises in fluid stability and rheological performance. To overcome the challenges, an intensive research has been devoted to advancing surface modification techniques that augment the dispersion, stability, and overall functionality of MRFs based on CIPs. This review describes the comprehensive approach to surface modification of CIPs for highly stable MRFs. We discuss the various surface modification methodologies that have been explored to optimize the behavior of carbonyl iron-based MRFs. Coating techniques, surfactant functionalization, magnetic coatings, and emerging approaches such as nanocoatings and electrochemical modification are also summarized. Moreover, insights into potential applications and future prospects of these modified MRFs are provided.Keywords
Magnetorheological fluids (MRFs) are smart materials that have gained significant attention due to their unique ability to undergo rapid and reversible shifts in their rheological characteristics upon exposure to an external magnetic field (Fig. 1)[1-3]. This distinctive behavior emanates from the interplay between magnetic particles suspended within the fluid and the applied magnetic field. MRFs find utility across diverse industries, ranging from automotive shock absorbers[4-7] that dynamically adapt suspension attributes to civil engineering dampers[2, 4] that heighten structural stability during seismic occurrences.
Fig. 1.: Operation mechanism of MRF system. Reproduced from ref.[1] under the Creative Commons Attribution 4.0 International (CC BY 4.0) License).
At the heart of MRF performance lies the nature of the dispersed magnetic particles[3, 4, 8]. Among these particles, carbonyl iron powders (CIPs) stand out due to their exceptional magnetization saturation, heightened magnetic susceptibility, and fast response speed to external magnetic fields[9]. However, the integration of CIPs presents challenges originating from the inherent traits of these particles. In their unaltered state, CIPs exhibit a tendency to aggregate, resulting in quick sedimentation and hindering the uniform dispersion required for consistent rheological behavior[10-12].
Fig. 2 shows an overview of stable CIP-based MRF system. The resolution to these challenges resides within the realm of surface modification techniques. These strategies aim to engineer particle surfaces to mitigate aggregation propensities and enhance compatibility within the carrier fluid. Through the customization of the surface chemistry and morphology of CIPs, researchers can achieve high dispersion stability, optimized yield stress, and an enhanced capacity to control rheological properties. Although there are many studies on the applications of MRF to various devices, there is a lack of systematic overview and discussion about surface treatment of CIPs in MRF system. Therefore, this comprehensive review extensively explores various methodologies of surface modification that have been investigated to optimize the behavior of CIP-based MRFs. Notably, this review discussed the various materials to stabilize the CIPs in MRFs, which will provide critical perspective for the highly stable MRF system for futuristic devices.
Fig. 2.: An overview of stable CIP-based MRF system. Reproduced from ref.[15, 20, 22, 42] under the Creative Commons Attribution 4.0 International (CC BY 4.0) License).
2.1 Techniques for Surface Modification
The pursuit of enhancing CIP-based MRF performance through surface modification has engendered various strategies that bestow desirable attributes upon particle surfaces[10-14]. There are various methods to modify CIP surface including techniques[4, 10-12], such as, surfactant functionalization[6, 10-12, 15], magnetic coatings[4, 6], or nanocomposite coatings[4, 9].
Hetero-coating techniques have emerged as a potential method for enhancing dispersion and stability within MRFs[2, 6]. CIPs are coated by polymeric materials such as polydimethylsiloxane (PDMS), polyurethane, or polyacrylate that forms hetero interface[2, 4, 16, 17]. The hetero-layers form a physical barrier around particles, curbing particle-particle interactions and facilitating suspension within the fluid medium (Fig. 3)[17]. Silane coupling agents (SCAs) are another coating technique that has been employed to enhance particle-matrix interactions through chemical bonding[2, 6, 12]. SCAs house functional groups like amino, epoxy, or hydroxyl that can react with metal oxide surfaces to form strong covalent bonds. This not only advances dispersion but also imparts supplementary functionalities to particle surfaces. Inorganic coatings including silica, alumina, and titania have also showed promise in elevating the compatibility of CIPs with the surrounding fluid[18, 19]. Solgel processing or chemical vapor deposition (CVD) are used to form the coating that have been shown to forestall aggregation and sedimentation[20, 21].
Fig. 3.: Hetero-coating on CIPs: (A) with PMMA (Reproduced from ref.[17] under the Creative Commons Attribution 4.0 International (CC BY 4.0) License)), and (B) with gelatin (Reproduced from ref.[22] under the Creative Commons Attribution 4.0 International (CC BY 4.0) License)).
Various nanoscale coatings can be applied on the surface of CIPs to improve their performance and functionality in MRFs[2-4, 6, 9]. MRFs are smart materials that can change their viscosity and rheological properties under an external magnetic field. They have many applications in damping, braking, clutches, and haptic devices[23, 24]. CIPs are the most commonly used magnetic particles in MRFs due to their high saturation magnetization, low cost, and easy availability[17, 25]. However, CIPs hold drawbacks, such as poor dispersion stability, low corrosion resistance, and high eddy current losses at high frequencies[3, 5]. Functional coatings enables to overcome these limitations by enhancing the dispersion and magnetorheological response of CIPs, as well as providing additional functionalities, such as thermal stability, electrical conductivity, or microwave absorption[26, 27]. Graphene oxide (GO), graphite, silica (SiO2), and metal oxides are widely used materials for the coating (Fig. 5)[4, 26, 28-31].
GO is a nanosheet of carbon atoms that has excellent mechanical strength and electrical conductivity, making it a suitable material for creating stable and uniform coatings on the particle surfaces (Fig. 4A)[28]. By depositing GO nanosheets on the CIP particles, a 2D network is formed that reduces the interparticle interactions and prevents aggregation[32, 33]. This improves the dispersion stability and reduces the viscosity of the MRFs. Moreover, GO nanosheets can enhance the magnetic response of the CIPs by providing a conductive surface that facilitates the alignment of the particles under a magnetic field. GO nanocoatings can also improve the corrosion resistance and thermal stability of the CIPs by acting as a protective barrier against oxidation[32, 33]. Graphite have outstanding mechanical properties and provide a conductive surface that enhances the magnetic response of the particles (Fig. 4B)[29]. By incorporating graphite on the particle surfaces, not only the dispersion of the particles is improved, but also the electrical connectivity between them is increased, leading to a higher shear thickening behavior under magnetic fields. Graphite can also improve the thermal stability and microwave absorption of the CIPs by increasing their specific surface area and creating multiple scattering centers for electromagnetic waves[29]. SiO2 is also widely used for CIPs due to its low cost, easy availability, and good compatibility with various solvents (Fig. 4C)[30]. Metal oxides also provide various functionalities to the CIPs by coating their surfaces (Fig. 4D)[31, 32]. Metal oxides also enhance the magnetorheological response of the CIPs by increasing their dielectric constant and reducing their eddy current losses[31, 32]. Electrophoretic deposition (EPD) uses an electric field to deposit charged particles from a stable colloidal suspension onto a conductive substrate[34-36]. EPD has been used to deposit nanocoatings on CIPs for MRF applications, as well as for other purposes, such as creating magnetic composites, thermoelectric devices, biomedical implants, and radar and microwave absorbing materials[37, 38]. Polymers are formed by EPD on CIP surface for improving their dispersion stability and corrosion resistance (Fig. 5)[8]. Some examples of polymers that have been used to coat CIPs by EPD are polyvinyl alcohol (PVA), polyethylene glycol (PEG), polyacrylic acid (PAA), polyaniline (PANI), and polyethyleneimine (PEI)[8, 37, 38].
Fig. 4.: CIPs with (A) GO [28], (B) graphite [29], (C) SiO2[30], and (D) metal oxides[31]. Reproduced from ref.[28-31] under the Creative Commons Attribution 4.0 International (CC BY 4.0) License.
Fig. 5.: TEM images of CIPs with polymeric coating deposited by EPD: (A) bare CIP, (b) CIP with thin layer and (c) CIP with thick layer. Reproduced from ref.[8] under the Creative Commons Attribution 4.0 International (CC BY 4.0) License.
2.1.2 Surfactant Functionalization
Surfactants have emerged as versatile agents for altering surface properties of CIPs[6, 10-12, 15]. The molecules possess hydrophilic and hydrophobic segments, enabling them to adsorb onto particle surfaces and establish a repulsive barrier between particles[2, 39]. Both ionic and non-ionic surfactants have been explored, each offering specific advantages in terms of stability and dispersion.
Amphiphilic molecules, characterized by hydrophilic and hydrophobic groups, have also been scrutinized to enhance particle dispersion by concurrently fostering compatibility with the carrier fluid and preventing particle aggregation[2, 9]. For example, polyethylene glycol (PEG) is a hydrophilic polymer that has been used to modify the surface of CIPs (Fig. 6A)[40]. PEG-coated CIPs have been shown to exhibit improved dispersion stability in water-based carrier fluids[40].
Fig. 6.: (A) (fig. parts are usually indicated by small letters, e.g (a)) CIP with PEG (Reproduced from ref.[40] under the Creative Commons Attribution 4.0 International (CC BY 4.0) License)), (B) Chemical structure of CTAB and SDS.
Cationic surfactants such as cetyltrimethylammonium bromide (CTAB) improve the dispersion stability of CIPs in water-based carrier fluids[3,4,8,339]. CTAB is a cationic surfactant that contains a positively charged head group and a long hydrophobic tail (Fig. 6B). The positively charged head group can adsorb onto negatively charged particle surfaces, while the long hydrophobic tail can extend into the surrounding fluid medium, forming a protective layer around particles. Anionic surfactants such as sodium dodecyl sulfate (SDS) have also been investigated for improving the dispersion stability of CIPs in silicone oil[3,4,8,9,39]. SDS is an anionic surfactant having a negatively charged head group and a long hydrophobic tail (Fig. 6B). The negatively charged head group attaches to positively charged particle surfaces, and the long hydrophobic tail in the surrounding fluid medium protect particles.
Magnetic coatings are also widely used for surface modification of CIPs[18,20,25]. By depositing magnetic materials onto particle surfaces, a magnetic “shell” is formed on CIP surface that not only stabilizes particles within the fluid but also amplifies their magnetic interactions[18,20,25]. Extensive exploration has been conducted on magnetic polymer coatings, wherein polymers incorporated with magnetic nanoparticles are deposited onto CIPs[3,4,19,20,25]. The dual-functional approach not only heightens dispersion stability but also augments the magnetic response of particles, contributing to more efficient operation in rheological properties under magnetic fields[2-4]. Hence, the application of a direct deposition method for magnetic materials onto particle surfaces offers a dual benefit – it improves magnetic performance and effectively mitigates dispersion challenges. Iron oxide nanoparticles have emerged as a favorable choice for magnetic coatings, primarily due to their exceptional magnetization properties and biocompatibility. (Fig. 7)[25].
Fig. 7.: CIPs with iron oxide magnetic shell (Scale bar is 3 ìm). Reproduced from ref.[25] under the Creative Commons Attribution 4.0 International (CC BY 4.0) License.
3.1 Hybrid Surface Modifications
A difficult problem for modifying the surfaces of CIPs in MRFs is to make sure that the particles are stable and well-dispersed in different liquids and situations. To solve this problem, researchers are trying new methods that use more than one technique together to get better results. (Fig. 8)[41]. An example of such an approach is the synergic fusion of polymer coatings and surfactant functionalization[2,3,17, 32,42]. Organic materials can coat the particles with thin layers that act as a physical barrier, stopping them from sticking together and forming clumps.
Fig. 8.: CIP with polymer hybrid coating: (A) bare CIP and (B) CIP with coating. Reproduced from ref.[41] under the Creative Commons Attribution 4.0 International (CC BY 4.0) License.
Amphiphilic molecules can change the surface chemistry of the particles, making them repel each other and dissolve better in different liquids. By using both organic materials and amphiphilic molecules to coat the particles, a better way is achieved that makes the particles more stable and dispersed in various conditions.[2, 3, 17, 32, 42]. The interaction between polymer coatings and surfactants can affect how the particles behave, so they have to be compatible with each other. For example, some surfactants can stop the polymer coatings from forming or sticking to the particles[2, 3, 17, 32, 42]. Therefore, choosing compatible pairs and adjusting their amounts are important for getting the best stability and performance.
Another example of a hybrid approach for surface modification is the use of magnetic hybrid coatings, which consist of magnetic nanoparticles and conventional coatings[6,18,26, 30]. Magnetic nanoparticles are nanosized particles that have high magnetic properties, such as high saturation magnetization and coercivity[4,43]. Conventional coatings are non-magnetic materials that improve the stability and dispersion of the particles, such as polymers, ceramics, or metals[2,3,17,32,42]. By depositing magnetic nanoparticles onto CIP particles that are coated with conventional coatings, a hybrid structure is created that combines both magnetic response and stability[2,3,17,32,42]. The hybrid particles exhibit superior yield stress and adjustable rheological characteristics, making them ideal candidates for applications that require both mechanical strength and magnetic responsiveness (Fig. 9)[44]. For example, the hybrid particles can be used in MRFs for damping, braking, or clutching systems that need to adjust their viscosity and stiffness under external magnetic fields[44]. To get a good combination of magnetic improvement and coating stability, careful control over the materials and methods of coating is needed.[2,3,17,32,42]. For instance, some factors that need to be considered are the size, shape, composition, distribution, and orientation of the magnetic nanoparticles, as well as the type, thickness, uniformity, and adhesion of the conventional coatings[19].
Fig. 9.: CIP with magnetic hybrid coating. Reproduced from ref. [44] under the Creative Commons Attribution 4.0 International (CC BY 4.0) License.
4 Multi-Scale Modeling and Simulation
The performance of MRFs depends on how the particles interact with each other at the small scale and how the fluid behaves at the large scale. A way to model this is to use different kinds of simulations that show different parts of the system[45]. Molecular dynamics (MD) simulations can predict how the particles interact with each other based on their surface chemistry and morphology[45-47]. Continuum mechanics can describe how the bulk fluid behaves under different conditions and external forces[45, 48]. Magnetic field simulations can analyze how the particles respond to magnetic fields and how they affect the rheological properties of the fluid[45]. The models can provide insights into how various modification strategies influence the final characteristics of MRFs, such as viscosity, yield stress, and shear thinning[45-47]. The ability to anticipate the complex interaction between surface chemistry, particle morphology, and magnetic response enables the rational design of modified MRF formulations that are tailored to specific applications[45-47].
Multi-scale modeling is a challenging task, as it demands a lot of computational power and advanced algorithms. To capture the interactions between the particles and the surface, the motion of the particles in a fluid medium, and the effects of the magnetic field, sophisticated computational methods are required. Furthermore, these models need to be compared with experimental data to ensure their validity and reliability. Hence, cooperation between computational scientists and experimental researchers is crucial for improving these models and developing a comprehensive framework for predicting MRF behavior
5 Applications and Future Prospects
The performance of MRFs based on CIPs depends largely on the surface modification techniques applied to the particles[2-4]. Surface modification affects the stability, yield stress, and controllability of the rheological properties of the MRFs. Improved stability prevents the particles from settling and clumping, ensuring consistent performance over time[2-4]. A key parameter for applications such as dampers and brakes is high yield stress, which is achieved by improving the particle dispersion and the formation of strong particle networks under magnetic fields. Moreover, tailored surface chemistry can result in controlled changes in rheological response, allowing precise tuning of fluid attributes in response to varying magnetic field intensities for various applications[3,4,9,10,12,13,15].
One of the areas where surface modification of CIPs has made a significant impact is automotive technology, especially in adaptive suspension systems (Fig. 9A)[49]. MRF-based shock absorbers dynamically adjust their suspension properties based on road conditions and driving behavior, providing smoother rides and improved handling[33]. The ability to adapt to changing road conditions in real-time enhances both comfort and safety, revolutionizing the driving experience.
Fig. 9.: MRF-based (A) damper [49] and (B) haptic systems [42]. Reproduced from ref. [42, 49] under the Creative Commons Attribution 4.0 International (CC BY 4.0) License.
The creation of MRF-based actuators and haptic devices is another field where surface modification and robotics have combined. (Fig. 9B)[6, 42]. Modified CIPs enable fine-tuned control of mechanical properties, allowing robotic systems to exert precise forces and mimic human touch[6, 42]. Applications range from soft robotics with shape-changing capabilities to haptic feedback devices that enhance the realism of virtual environments[6]. Such advancements in haptic technology open doors to enhanced human-machine interaction and immersive experiences.
MRF-based dampers also find practical use in civil engineering for structural stability and vibration control[6, 9]. Surface-modified CIP particles are integrated into dampers that adapt to dynamic loads, such as those experienced during earthquakes[6, 9]. The modified particles enable quick changes in fluid viscosity under magnetic fields, resulting in effective energy dissipation and reduced structural vibrations. Such dampers offer a promising solution for safeguarding critical infrastructure and ensuring the resilience of buildings in seismic zones[6, 9].
6 Challenges and Considerations
Some challenges are faced by surface modification techniques, despite their potential. The possible toxicity of some agents used for surface modification is one of the challenges, which may harm the environment and human health. Another challenge is the durability of modified particles within the fluid matrix, especially for applications that face changing conditions over long durations of time. A third challenge is the large-scale production of surface modification methods without losing performance or increasing costs. To address the environmental concerns of surface modification techniques, environmentally friendly materials have been developed[50, 51]. Green modification approaches aim to use less harmful chemicals, consume less energy, and generate less waste. Bio-based polymers, natural extracts, and environmentally benign precursors as surface modification agents are developed[50, 51].
In summary, the aim of surface modification of CIPs for MRFs is to change the surface properties of the magnetic particles to enhance the performance and functionality of MRFs. Table 1 shows a summary of different coating materials for CIP-based MRF system. MRFs are smart materials that can alter their viscosity and rheological properties when an external magnetic field is applied. MRFs have various applications in damping, braking, clutches, and haptic devices. CIPs are the most widely used magnetic particles in MRFs because they have high saturation magnetization, low cost, and easy availability. However, CIPs also have some limitations, such as low dispersion stability, poor corrosion resistance, and high eddy current losses at high frequencies. Surface modification techniques can help address these limitations by improving the dispersion and magnetorheological response of CIPs, as well as adding additional functionalities, such as thermal stability, electrical conductivity, or microwave absorption.
Some of the surface modification techniques that have been used for CIPs are coating techniques, surfactant functionalization, and magnetic coatings. Coating techniques involve applying a thin layer of another material on the particle surfaces, such as polymers, ceramics, or metals. The dispersion stability and corrosion resistance of CIPs are enhanced by introducing surface roughness and altering surface energy. In addition, the magnetorheological response of CIPs is improved by increasing their dielectric constant and reducing their eddy current losses. Moreover, coating techniques can provide additional functionalities to CIPs, such as thermal stability, electrical conductivity, or microwave absorption, depending on the coating material. Surfactant functionalization involves changing the surface chemistry of CIPs by attaching molecules that have both hydrophilic and hydrophobic parts, such as organic acids or salts. Surfactant functionalization can enhance the dispersion stability and solubility of CIPs by creating repulsive forces between them and improving their compatibility with different solvents. Surfactant functionalization also affect the magnetorheological response of CIPs by altering their surface charge and potential. Magnetic nanoparticles, such as iron oxide or cobalt ferrite, are placed on the particle surfaces by magnetic coatings. Magnetic coatings can enhance the magnetorheological response and microwave absorption of CIPs by increasing their magnetic properties, such as saturation magnetization and coercivity. Magnetic coatings can also enhance the dispersion stability of CIPs by creating magnetic attraction between them. By using these surface modification techniques for CIPs, researchers have achieved significant improvements in the stability, yield stress, and rheological properties of CIP-based MRFs. The progresses have enabled a wide range of applications in various sectors and created opportunities for further innovation, driven by the goals of enhancing performance, sustainability, and scalability. With the matures of technology, surface-modified MRFs will have a positive impact on industries, society, and the way we design and interact with materials.
Funding: This research was supported by the Chung-Ang University Research Grants in 2023.
Institutional Review Board Statement: Not applicable.
Informed Consent Statement: Not applicable.
Data Availability Statement: The datasets used and/or analyzed during the current study are available from the corresponding author upon reasonable request.
Acknowledgement: This research was supported by the Chung-Ang University Research Grants in 2023.
Conflicts of Interest: The authors declare that they have no competing interests.
Copyright statement: All the Fig. of this paper requires no copyright permission under the “Creative Commons Attribution 4.0 International (CC BY 4.0) License”.
References
1. H. Lu, L. Wang, L. Dai, H. Ding, Q. Zhang, X. Liu. (2020). Advances in Materials Science and Engineering, 701908. [Google Scholar]
2. M. Ashtiani, S.H. Hashemabadi, A. Ghaffari. (2015). Journal of Magnetism and Magnetic Materials, 374, 716-730. [Google Scholar]
3. G. Bossis, S. Lacis, A. Meunier, O. Volkova. (2002). Journal of Magnetism and Magnetic Materials, 252, 224-228. [Google Scholar]
4. Y. J. Kim, J. S. Choi, J.-H. Yim. (2022). Journal of Materials Chemistry C 10(176687-6695. [Google Scholar]
5. J.-S. Oh, J.W. Sohn, S.-B. Choi. (2020). Actuators, 11(244. [Google Scholar]
6. F.D. Goncalves, J.-H. Koo, M. Ahmadian.(2006). The Shock and Vibration Digest 38, 203+. [Google Scholar]
7. B. Hwang, Y. Han, P. Matteini. (2022). Facta Universitatis, Series: Mechanical Engineering 20(3553-560. [Google Scholar]
8. M. Cvek, M. Mrlik, J. Sevcik, M. Sedlacik. (2018). Polymers, 10(121411. [Google Scholar]
9. H. Eshgarf, A. Ahmadi Nadooshan, A. Raisi. (2022). Journal of Energy Storage 50, 104648. [Google Scholar]
10. H. Lian, M. Xue, K. Ma, D. Mo, L. Wang, Z. Cui, X. Chen.(2022). Micromachines 13(81247. [Google Scholar]
11. M.N. Aruna, M.R. Rahman, S. Joladarashi, H. Kumar. (2019). Materials Research Express, 6(8086105. [Google Scholar]
12. H. Kim, N. Qaiser, B. Hwang. (2023). Facta Universitatis, Series: Mechanical Engineering, 21(151-61. [Google Scholar]
13. H. Ha, R. Thompson, P. Matteini, S.J. Yoo, B. Hwang. (2022). Colloid and Interface Science Communications, 48, 100625. [Google Scholar]
14. H. Ha, S. Müller, R.-P. Baumann, B. Hwang./ (2023). Facta Universitatis, Series: Mechanical Engineering Online First, DOI: https://doi.org/10.22190/FUME221126001H. [Google Scholar] [CrossRef]
15. H. Ha, R. Thompson, S. Lim, B. Hwang. (2022). Materials Letters, 322, 132513. [Google Scholar]
16. H. Ha, N. Qaiser, J.H. Jeong, K. Lee, B. Hwang. (2023). Journal of Natural Fibers 20(12128149. [Google Scholar]
17. D. Takahashi, A.V.S. Sainath, J. Ikeda, K. Budpud, T. Kaneko, M. Kawai, T. Mitsumata. (2021). Polymers, 13(3335. [Google Scholar]
18. J.S. Kumar, P.S. Paul, G. Raghunathan, D.G. Alex. (2019). International Journal of Mechanical and Materials Engineering, 14(113. [Google Scholar]
19. J. de Vicente, D.J. Klingenberg, R. Hidalgo-Alvarez. (2011). Soft Matter, 7(83701-3710. [Google Scholar]
20. M. Kumar, H.N. Singh Yadav, A. Kumar, M. Das. (2022). Journal of Micromanufacturing, 5(282-100. [Google Scholar]
21. G. Zhang, Z. Zhang, M. Sun, Y. Yu, J. Wang, S. Cai. (2022). Advanced Engineering Materials, 24(92101680. [Google Scholar]
22. T. Plachy, P. Rohrer, P. Holcapkova. (2021). Materials, 14(102503. [Google Scholar]
23. W. Zhu, X. Dong, H. Huang, M. Qi. (2019). Journal of Magnetism and Magnetic Materials, 491, 165556. [Google Scholar]
24. H. Prajapati, J. Shahanand, H. Nimkar, A. Lakdawala. (2020). Materials Today: Proceedings, 28, 40-44. [Google Scholar]
25. M.A. Portillo, G.R. Iglesias. (2017). Journal of Nanomaterials, 9026219. [Google Scholar]
26. M. Kumar, A. Kumar, R.K. Bharti, H.N.S. Yadav, M. Das. (2022). Materials Today: Proceedings, 56, A6-A12. [Google Scholar]
27. S.T. Shilan, S.A. Mazlan, Y. Ido, A. Hajalilou, B. Jeyadevan, S.-B. Choi, N.A. Yunus. (2016). Smart Materials and Structures, 25(9095025. [Google Scholar]
28. M. Liu, M. Zhang, J. Zhang, Y. Qiao, P. Zhai. (2021). Polymers, 13(111777. [Google Scholar]
29. M.K. Shabdin, M.A. Abdul Rahman, S.A. Mazlan, Ubaidillah, N.M. Hapipi, D. Adiputra, S.A. Abdul Aziz, I. Bahiuddin, S.-B. Choi. (2019). Materials, 12(3391. [Google Scholar]
30. S.K.M. Jamari, N.A. Nordin, Ubaidillah, S.A.A. Aziz, N. Nazmi, S.A. Mazlan.(2020). Materials, 13(235317. [Google Scholar]
31. Z. Lin, H. Hu, Y. Dai, Y. Zhong, S. Xue. (2023). Nanomaterials, 13(3398. [Google Scholar]
32. G. Wang, Y. Ma, Y. Tong, X. Dong. (2017). Journal of Industrial and Engineering Chemistry, 48, 142-150. [Google Scholar]
33. S. Kumar, R. Sehgal, M.F. Wani, M.D. Sharma. (2020). Journal of Magnetism and Magnetic Materials, 579, 170852. [Google Scholar]
34. H. Salimkhani, P. Palmeh, A.B. Khiabani, E. Hashemi, S. Matinpour, H. Salimkhani, M.S. Asl. (2016). Surfaces and Interfaces, 5, 1-7. [Google Scholar]
35. J. Wu, J. Chen, Y. Zhao, W. Liu, W. Zhang. (2016). Composites Part B: Engineering 105, 167-175. [Google Scholar]
36. M. Farshad, F. Clemens, M. Le Roux. (2007). Journal of Thermoplastic Composite Materials, 20(165-74. [Google Scholar]
37. Z.W. Zhong. (2008). Materials and Manufacturing Processes, 23(5449-456. [Google Scholar]
38. J. Bernat, P. Gajewski, J. Kołota, A. Marcinkowska. (2023). Applied Sciences, 13(31651. [Google Scholar]
39. H. Yoon, R. Thompson, B. Hwang. (2023). Colloid and Interface Science Communications, 52, 100686. [Google Scholar]
40. R. Oriòaková, R. Gorejová, M. Petráková, Z.O. Králová, A. Oriòak, M. Kupková, M. Hrubovèáková, M. Podobová, M. Baláž, R.M. Smith. (2020). Materials, 13(184134. [Google Scholar]
41. J.H. Lee, Q. Lu, J.Y. Lee, H.J. Choi. (2019). Polymers, 11(2219. [Google Scholar]
42. E. Shokrollahi, A.A. Goldenberg, J.M. Drake, K.W. Eastwood, M. Kang. (2018). Actuators, 7(483. [Google Scholar]
43. Y. Seo, S. Ko, H. Ha, N. Qaiser, M. Leem, S.J. Yoo, J.H. Jeong, K. Lee, B. Hwang. (2022). Composites Science and Technology, 218, 109150. [Google Scholar]
44. Y. Fu, J. Yao, H. Zhao, G. Zhao, Z. Wan, Y. Qiu. (2018). Nanomaterials, 8(9714. [Google Scholar]
45. P. Pei, Y. Peng. (2022). Journal of Magnetism and Magnetic Materials, 550, 169076. [Google Scholar]
46. G. Liu, F. Gao, D. Wang, W.-H. Liao. (2022). Smart Materials and Structures, 31(4043002. [Google Scholar]
47. Q. Tan, L. Yuan, G. Liang, A. Gu. (2022). Applied Surface Science, 576, 151827. [Google Scholar]
48. A.E. Filippov, V.L. Popov. (2020). [Google Scholar]
49. M.H. Idris, F. Imaduddin, Ubaidillah, S.A. Mazlan, S.-B. Choi. (2020). Actuators, 9(116. [Google Scholar]
50. L. Shixu, Z. Jing, L. Jun, F. Jie, Y. Miao, Q. Song. (2021). Langmuir, 37(237176-7184. [Google Scholar]
51. F. Liang, L. Wang, H. Zhu, Q. Dong, Y. Zhang, J. Liu, S. Zhang, Z. Ye, Y. Zhang, X. Zhang, B. Liu. (2022). Water, 14(71118. [Google Scholar]
52. L.D. Gil, I.L. de Camargo, E.I. Gutiérrez - Velásquez, H.A. Colorado. (2023). Revista UIS Ingenierías, 22(21-14. [Google Scholar]
53. K.S. Sista, S. Dwarapudi. (2018). ISIJ International. 58(6999-1006. [Google Scholar]
Cite This Article
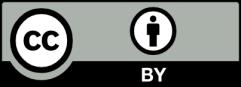
This work is licensed under a Creative Commons Attribution 4.0 International License , which permits unrestricted use, distribution, and reproduction in any medium, provided the original work is properly cited.