Open Access
ARTICLE
Study on Organic Fluorine Modified Cationic Acrylic Resin and its Application in Cathodic Electrodeposition Coatings
School of Chemical Engineering, Zhejiang University of Technology, Chaowang Road, Hangzhou, Zhejiang Province, China
* Corresponding Author: e-mail:
Journal of Polymer Materials 2023, 40(3-4), 157-164. https://doi.org/10.32381/JPM.2023.40.3-4.3
Abstract
The organic fluorine modified/containing cationic acrylic resin is prepared via solution polymerization technique using hexafluorobutyl methacrylate (HFMA) along with butyl acrylate (BA), methyl methacrylate (MMA), styrene (St), dimethylaminoethyl methacrylate (DMAEMA) and hydroxy propyl methacrylate (HPMA) as the comonomers, proprylene glycol monomethyl ether (PGME) as the solvent, and 2, 2-Azo-bis-iso-butyronitrile (AIBN) as the initiator. The synthesized resin in which fluorine atom is introduced into the polymer chains. The cathodic electrodeposition (CED) coatings were prepared by mixing the synthesized resin and blocked isocyanate. The influence of the amount of organic fluorine on the resin and the resultant CED coatings is investigated in detail. In view of the appearance and hydrophobicity of the film, the optimum amount of organic fluorine is obtained, which is 12.0%. The hydrophobicity and the acid and alkaline resistance properties of the coating film are improved when the organic fluorine monomer is introduced into the resin.Keywords
Cathodic electrode position (CED) coatings have been widely used in industries nowadays to overcome the main drawbacks of anodic electrodeposition coatings, such as substrate dissolution and film discolouration. Presently, applications of the CED coating have been expanded from the base coat to the decorative coat. Acrylic CED coatings are mainly used in the electrodeposition finishing for high demand of exterior decorative and weather resistance, such as hardware, accessories, office furniture and so on[1-7]. However, acrylic CED coatings have poor water resistance, weather resistance and solvent resistance, and cannot meet the new demand of high-end products, which limits further development of such coatings. Fluorinated polymers are expected to be adopted in specific coatings to achieve outstanding advantages, such as high chemical and photochemical resistance, low surface tension and low refractive index. At present, there are some reports on fluorinated CED coatings. Wang et al. synthesized the fluorinated cationic Cathodic Electrodepositing (CED) resins by copolymerization of several acrylic monomers including Zonyl[8]. They also synthesized water-dispersible cationically modified diisocyanates TIb and TId blocked by n-butanol (BAO) and 3,5-dimethylpyrazole (DMP) for cathode electrodepositing (CED) coating curing by introducing cationic triethanolamine (TEOA) into isophorone diisocyanate (IPDI)[9]. Chen et al. prepared cationic fluorinated acrylic resin by solution polymerization of dodecafluoroheptyl methacrylate, butyl acrylate, methyl methacrylate, dimethylaminoethyl methacrylate and methacrylic acid initiated by 2, 2/- azo-bis-iso-butyronitrile in a solvent of butyl cellosolve. The resultant resin was neutralized with acetic acid[10]. In addition, Wang et al. also synthesized the cationic fluorinated acrylic ester resin for cathodic electrodepositing (CED) coating and cationic blocked-diisocyanate TId by the polymerization of isophorone diisocyanate (IPDI), cationic triethanolamine (TEOA), ZonylTM and some other acrylic ester monomers, with 3, 5-dimethylpyrazole (DMP) as the blocking agent[11]. However, the organic fluorine such as hexafluorobutyl methacrylate and some cheap monomers such as styrene, which are used to prepare the cationic acrylic resin, are seldom reported in the open literatures.
In this paper, the fluorinated acrylate resin is synthesized via solution polymerization technique using fluorinated monomer like hexafluorobutyl methacrylate and other functional monomers. Then, the fluorinated CED coatings are prepared by mixing the resultant resin and blocked isocyanate. The emphasis is put in the present work to observe the influence of organic fluorine on the resin and the resultant CED coatings.
Butyl acrylate (BA), methyl methacrylate (MMA) and styrene (St), which were chemically pure grade, are obtained from Wulian Chemical Plant, Shanghai, China. They were purified further by distillation under reduced pressure prior to use. Hexafluorobutyl methacrylate (HFMA), which was industrial grade, was purchased from Harbin Xeogia Fluorine-Silicon Material Co. Ltd. (China). Dimethylaminoethyl methacrylate (DMAEMA), which was also industrial grade, was bought from Fushun Anxin Chemical Co. Ltd. (China). Hydroxy propyl methacrylate (HPMA) was industrial grade and purchased from Beijing Eastern Acrylic Chemical Technology Co. Ltd. (China). Acetic acid, which was analytically pure grade, was obtained from Hangzhou Chemical Reagent Co. Ltd. (China). Ethyl acetate, acetone and isopropanol, which were analytically pure grade, were purchased from Shuanglin Chemical Reagent Company, Hangzhou, China. Proprylene glycol monomethyl ether (PGME) and aliphatic blocked isocyanate crosslinker, which were industrial grade, were gifts from Anji Wanguo Coatings Co. Ltd., Huzhou, China. 2, 2-Azo-bis-iso-butyronitrile (AIBN), which was chemically pure grade, was purchased from Shanghai No.4 Reagent & H.V. Chemical Co. Ltd., Shanghai, China. Deionized water was manufactured in our laboratories, which is offered by Hangzhou Yajie Environmental Protection Equipment Co., Ltd.(China).
The resin was prepared by the solution polymerization technique. 27.00 g of PGME, which was used as the solvent, was added into the reactor which was equipped with a dropping funnel and a condenser under the condition of agitation. The solvent in the reactor was heated to 80°C inside water bath. 0.72 g of organic fluorine monomer, 60.00g of mixed monomers, which composed of BA, MMA, St, HPMA and DMAEMA and 1.00 g of initiator were dripped into the reactor slowly within the range of 3.5 and 4.0 hours. At the same time the reaction temperature was raised to 90°C. Another 0.20g of initiator solution, which was dissolved 9.00g of PGME, was dripped. Then 2.20g of acetic acid was added into the reactor quickly after the mixed monomers were dripped completely. Finally, the reaction lasted for another 2 hours to improve the conversion rate of mixed monomers. The product was cooled to 65 °C and discharged. Thus, the resin was obtained.
2.3 Preparation of CED Coatings and its Film
The synthesized resin was mixed with isocyanate curing agent, which was proprylene glycol monomethyl ether (PGME) and aliphatic blocked isocyanate, and deionized water at a mass ratio of 60:21:371. The emulsion was prepared by stirring in the dispersive machine with a rotational speed and dispersive time of 800 r/minand 30 min, respectively. The solid content was determinedto be about 10%. Conductivity and pH of the emulsion were determined. The film was prepared by the following electrodeposition device, which was shown in Figure 1.The power supply was switched onto for electrodeposition coating when the voltage was 60 Vand electrophoresis time was 80 s, which was changed to 80 V, 30–60 s later, respectively. Then the power supply was cut off and the cathode plate was taken out. The floating paint on the sample surface was rinsed off with running water as soon as possible, then with deionized water and finally dried properly. The temperature of the oven was set to160°C in advance and the sample was baked for 30 min after electrophoresis washing. The sample after baking was taken out and cooled for 24 h. Thus, the film of the electrodeposition coating was obtained.
Fig. 1.: Electrodeposition devices (1: Dc power, 2: pH meter, 3: Conductivity meter, 4: Stirrer, 5: Anode plate, 6: Cathode plate)
Conductivity was tested with a digital conductivity meter (DDS-11A, China). The absorbance of diluted resin aqueous solution was measured by UV-visible spectrophotometer. The dilution ratio was 1000 and the peak value appeared when λ = 259 nm. The abs value at this time was A. The transmittance is calculated as follows: T (%) = 10-A; where T was transmittance; A was the abs value. A moderate amount of the CED coatings was taken into the 10ml sample tube and placed symmetrically in the centrifuge. The rotation speed was adjusted to 1000-4000r/min for 20min. After that, the sample was taken out and the phenomenonof precipitation and stratification were observed to evaluate the mechanical stability of the CED coatings. The resin sample was placed in an oven at 105°C and baked for 6 h to constant weight m1. The sample was taken out and placed in 200 ml deionized water for 48h. After that, the sample was taken out and weighed m2 to calculate water absorption via the following equation:.
3.1 Influence of Amount of Organic Fluorine on Transmittance and Water Absorption
The effect of amount of organic fluorine on transmittance and water absorption is presented in Figure 2. It shows that with the increase of organic fluorine amount, the light transmittance of resin aqueous solution showed a downward trend, i.e. the water solubility of resin became worse, which was caused by the strong hydrophobicity of the organic fluorine group in the polymer. Furthermore, the more organic fluorine is and the worse hydrophobicity is. The water absorption of the right side of the figure also has a similar trend because fluorine atoms of the modified polymer tend to be arranged on the outside of the molecule and enriched in the surface layer of the coating film, forming a water-repellent layer, which increases the repulsion effect on water molecules, making it difficult to penetrate into the polymer molecule, resulting in good water resistance of the coating film.
Fig. 2.: Effects of amount of organic fluorine on transmittance and water absorption (a: Transmittance; b: Water absorption)
3.2 Effect of Organic Fluorine on Solution of CED Coatings
Influence of the amount of the organic fluorine on the appearance and mechanical stability of the CED coatings is shown in Table 1. Table 1 indicates the increased amount of the organic fluorine has a negative effect on the appearance and mechanical stability of the CED coatings. This phenomenon can be explained by the fact that the water solubility of acrylic polymer is decreased with the increased amount of organic fluorine and the water solubility of resin is closely related to the stability of emulsion. During the course of forming the emulsion system, the particles are formed, which suspended in water to form emulsion when resin molecules are wrapped in curing agent molecules to form particles. Thus, the water solubility of resin becomes worse, which will cause resin particles to be difficult to suspend and result in emulsion stratification. Effect of the amount of the organic fluorine onp H and conductivity of the CED coatings is given in Figure 3. It shows that the deterioration of resin water solubility will lead to the decrease of the ion number of the paint solution and the conductivity while the pH of the paint solution is related to the stability of the emulsion. However, the lower pH will reduce the degree of ionization hydrolysis of the cationic resin and parts of resins cannot be dispersed in water, resulting in precipitation in the emulsion.
Fig. 3.: Effects of amount of organic fluorine on pH and conductivity (a: pH; b: conductivity)
3.3 Influence of Organic Fluorine on Appearance and Acid and Alkali Resistance of Film of CED Coatings
Effect of organic fluorine on appearance and acid and alkali resistance of film of CED coatings is presented in Table 2. Table 2 shows that a small number of pinholes appear in the paint film when the amount of organic fluorine is 15%. This may be caused by the fact that too much organic fluorine makes the conductivity of the CED coatings decreases, which has a negative influence on film properties of CED coatings and leads to the unstable structure of the cured film, resulting in pinhole phenomenon. Furthermore, form Table 2, it can be found that the acid and alkaline resistance of the film can be improved obviously with the increased amount of organic fluorine. This is due to the special function of fluorine atom, which can protect the molecular chain and improve the acid and alkaline resistance.
3.4 Effect of Amount of Organic Fluorine on Contact Angle
The influence of the amount of organic fluorine on the contact angle of CED coatings is given in Figure 4. From Figure 4, it can be found that the contact angle of the film is increased gradually with the increased amount of organic fluorine when the amount of organic fluorine is less than 12%. This is caused by the fact that more fluorine atoms are enriched on the surface of the molecular chain, which reduces the surface energy and increases the hydrophobicity. However, when it is 15%, the contact angle is decreased somewhat, which is due to the high content of organic fluorine and the saturation of external fluorine atoms, making part of fluorine atoms migrate to the inner part of the molecule, and its characteristics are difficult to reflect, and the fluorine atomic groups cannot effectively reduce the surface energy. Figure 5 is the comparison of the contact angel of conventional resin and fluorinated resin. In Figure 5, it can be seen that with the addition of organic fluorine, the contact angle of the film is increased, which is attributed to the introduction of fluorinated monomer, the fluorinated groups of acrylate preferentially migrated and accumulated on the surface during the course of film forming. Thus, the surface energy of film is decreased, which leads to the increase of the hydrophobicity.
Fig. 4.: Influence of amount of organic fluorine on contact angle
Fig. 5.: Contact angel of conventional resin and fluorinated resin (a: contact angle of conventional resin 88.4°; b: contact angle of fluorinated resin101.4°).
The organic fluorine modified cationic acrylic resin is prepared via solution polymerization technology using hexafluorobutyl methacrylate (HFMA) along with other comonomers like BA, MMA, St, DMAEMA and HPMA, and PGME as solvent, and AIBN as the initiator. Thus fluorine atom is introduced into the polymer chains of the synthesized resin. Effects of amount of the organic fluorine on the CED coatings and their films are investigated in detail. In view of the appearance and hydrophobicity of the film, the optimum amount of organic fluorine is obtained, which is 12.0%. The hydrophobicity and the acid and alkaline resistance of the film are improved when the organic fluorine monomer is introduced into the synthesized resin.
References
1. T. K. Rout, P. P. Sahoo and D. Despande. (2006). Mater. Perform. 45:32. [Google Scholar]
2. J. Q. Hu, W. P. Tu and J. Q. Qu. (2002). J. South China Univ. Technol. (Nat. Sci.) 30:57. [Google Scholar]
3. C. H. Xu, Z. Q. Gong, W. T. Zhao and L. J.Chen. (2022). PPCJ Polym. Paint Colour J. 212:49. [Google Scholar]
4. Z. Q. Gong, W. T. Zhao and L. J. Chen. (2022). J Polym. Res. 29:303. [Google Scholar]
5. W. T. Zhao, S. S. Cao, X. L. Chen and L. J.Chen. (2021). PPCJ Polym. Paint Colour J. 211:48. [Google Scholar]
6. F. Padash, B. Dorff, W. J. Liu, K. Ellwood, B. Okerberg, S. Zawacky and J. N. Harb. (2019). Prog. Org. Coat. 133:395. [Google Scholar]
7. L. J. Chen, W. Li and W. Jiang. (2014). PPCJ Polym. Paint Colour J., 204:2. [Google Scholar]
8. T. Wang, S.G. Qi, B. Y. Ren and Z.Tong. (2007). Prog.Org.Coat. 60:132-139. [Google Scholar]
9. T. Wang, S. G. Qi, B. Y. Ren and Z Tong. (2008). J. Appl. Polym. Sci. 107:4036. [Google Scholar]
10. L. J. Chen, W. Li and W. Jiang. (2014). Pigm. Resin Technol. 43:251. [Google Scholar]
11. T. Wang, S. G. Qi, B. Y. Ren, Y. Zhu and Z.Tong. (2008). J. South China Univ. Technol. (Nat. Sci.) 36:111. [Google Scholar]
Cite This Article
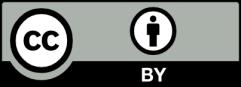
This work is licensed under a Creative Commons Attribution 4.0 International License , which permits unrestricted use, distribution, and reproduction in any medium, provided the original work is properly cited.