Open Access
ARTICLE
Impact on Mechanical Properties of Surface Treated Coconut Leaf Sheath Fiber/Sic Nano Particles Reinforced Phenol-formaldehyde Polymer Composites
1
Department of Mechanical Engineering, Sri Ramakrishna Engineering College
(Autonomous), Coimbatore, Tamil Nadu, India.
2
Department of Mechanical Engineering, Mohan Babu University (MBU), Tirupati, Andhra
Pradesh, India.
3 Mechanical and Mechatronics Engineering, Faculty of Engineering, Sohar University, Sohar,
Sultanate of Oman.
4* Institute of Mechanical Engineering, Saveetha School of Engineering, Saveetha Institute of
Medical and Technical Sciences (SIMATS), Chennai- 602105, Tamil Nadu, India.
5
Department of Information Technology, University College of Engineering, Nagercoil, Tamil
Nadu, India.
6
Department of Mechanical Engineering, College of Engineering in Al-Kharj, Prince Sattam
Bin Abdulaziz University, Al-Kharj, Saudi Arabia.
* Corresponding Author: e-mail:
Journal of Polymer Materials 2023, 40(1-2), 71-82. https://doi.org/10.32381/JPM.2023.40.1-2.6
Abstract
Several agro-wastes are rich in natural fibers and finds scope to be used as reinforcement in composite industry. These natural fibers have some advantages over man-made fibers, including low cost, light weight, renewable nature, high specific strength and modulus, and availability in various forms worldwide. In this paper, the effect of surface modification of leaf sheath coconut fiber (LSF) (an agro-waste) reinforced in phenol formaldehyde matrix composites with silicon carbide (SiC) nano particles as filler material were investigated for its mechanical characteristics. The investigation portrays that coconut LSF (CLSF) modified with potassium permanganate reinforced polymer composite with SiC nano particles as filler material exhibited 18.86%, 22.54%, 10.72% and 15.43% higher tensile, flexural, hardness and impact characteristics respectively compared to the unmodified CLSF reinforced polymer composite. The results reveal that the surface modification treatment considerably increased the mechanical characteristics of the composite.Keywords
The properties of plant fibers depend not only on the type of plant, the location where it is grown, the age of plant and the extraction method used, but also on the fiber structure, microfibrillar angle, fiber (cell) dimensions and chemical composition. The elementary unit of the cellulose macromolecule is hydro-D-glucose, which contains three alcohol hydroxyls (-OH)[1]. These hydroxyl groups form hydrogen bonds within the macromolecule itself (intermolecular) and between other cellulose macromolecules (intermolecular). Therefore, all plant fibers are hydrophilic in nature; their humidity reaches 8–13%[2]. In addition to cellulose, plant fibers contain various natural substances, especially hemicelluloses, lignin, pectins and waxes. The elementary fibers of plant fibers are connected to each other by lignin, which acts as glue. The content of lignin in plant fibers affects their structure, properties and morphology[3]. In general, the tensile strength and Young’s modulus of fibers increases with increase in cellulose content.
Studies on green composites of soy-based matrix/pineapple leaf fiber composite fabrication and property evaluation were performed[4]. In this study, they performed tests on fabricated composites and the composites were promising to use for structural applications. The effects of fiber loading and polyesteramide-grafted glycidyl methacrylate (PEA-g-GMA) as compatibilizer on morphology and physical properties of bio-composite were evaluated. Mechanical properties including tensile properties, flexural properties and impact strength of the biocomposites increased with increase in fiber content and presence of compatibilizer[5]. Scanning electron microscopic studies shows that fiber dispersion in the matrix deteriorated the strength with increase in fiber content but improved with the addition of compatibilizer. The addition of compatibilizer also reduced the water absorption characteristics. The improved mechanical properties of composites in the presence of compatibilizer corresponds to the interactions between the hydroxyl groups of pineapple leaf and the epoxy groups in PEA-g-GMA[6].
Another study was reported on structural characterization of coconut leaf sheath fiber (CLSF) reinforcement[7]. They performed tests on coconut palm leaf sheath fibers. FTIR and chemical analysis showed a reduction in hemicellulose content by alkaline treatment of fibers[8]. X-ray diffraction revealed an increase in fiber crystallinity upon alkali treatment. It was found that the thermal stability of fibers increases slightly with alkaline treatment. The tensile properties of these fibers were also increased by alkaline treatment.
Further, study on the morphology and surface properties of Henequen fiber modified by electron beam (EB) was investigated[9]. Morphological and topological properties were performed and the roughness irradiated by electron beam (EB) with different intensities was investigated using SEM and AFM. EB irradiation is used to modify the surface of natural fibers and the surface properties of henequen fiber were also changed by EB irradiation. After the impurities were removed, small pores with a size of 110 μm were formed. Stronger EB irradiation leads to streaking with obvious height differences between doses of 10 kGy to 100 kGy due to removal of the P layer and exposure of the S layers.
Studies on artichoke (Cynara cardunculus L.) fibers as potential reinforcement of composite structures were investigated[10]. Scanning electron microscopy, chemical composition and mechanical properties tests were performed. The mechanical properties of these fibers were evaluated by tensile tests of individual fibers and the results were analyzed using the Weibull distribution. The thermal degradation behavior was fully investigated using TGA and DTG curves. Their stalks can be recovered to extract the fibers creating an industrial chain, highly localized with advantages in terms of environmental and social impacts and costs.
Furthermore, the study of dispersion, morphological and mechanical properties of flax fibers were performed[11]. The dispersion of fiber widths manifests itself as both inter-filament dispersion and intra-filament dispersion. The intra-filament variance alone is sufficient to explain the inter-filament variance. The dispersion of mechanical properties of flax fibers is apparently not caused by the dispersion of morphological characteristics. They are believed to be caused mainly by the variation in cellulose content between individual fibers as well as the random location and size of defects along each fiber.
The observations from literature reveal that the researchers have reported the effect of different natural fiber reinforcements and fillers on the mechanical characteristics of polymer composites. Very few researchers have attempted to know the effect of reinforcing surface modified natural fibers and eco-friendly filler material combination on the mechanical characteristics of polymer composites. Even in those investigations the surface modification of natural fibers was limited to a single chemical treatment process. This limits the comparison of influence of different chemical treatment process on natural fibers and SiC nano particles reinforcement on the mechanical properties of polymer composites. In this paper, CLSF treated with stearic acid, silane, potassium permanganate and benzoyl peroxide individually. They were reinforced in phenol formaldehyde matrix to form polymer composites with SiC nano particles as filler material. These polymer composites were characterized mechanically to know its suitability to be employed in any suitable industrial applications.
The coconut palm (Coco’s nucifera) is a member of the palm family (arecaceae). CLSFs is obtained from the coconut palm; it acts as the supporting structure of each coconut palm leaf. The fibers of the sheath of coconut leaves occur in the form of a mat. The coconut sheath is grown at the same time as the leaf. The coconut palm is native to coastal areas of South east Asia (Malaysia, Indonesia, and the Philippines), tropical Pacific islands, and westward to coastal India, Sri Lanka, East Africa, and tropical islands in the Indian Ocean. Although the fibers come from many parts of coconut trees that are used, the sheath fibers are left as a huge waste. In this work, we will use this material for chemical processing analysis. The coconut leaf sheath were collected from farms and soaked in water for 48 h. Then they were washed in running water to separate the CLSF from other impurities.
CLSFs are obtained from coconut trees by hand picking from agricultural farms. Then the CLSF is thoroughly washed with tap water and then cut to standard dimensions[12]. It is then dried for one day in sun to remove all the moisture content present in the CLSF. Later, a certain amount of CLSFs were immersed for 24 h in a 5% concentration of stearic acid[13]. After 24 h, CLSFs were taken out from the stearic acid solution and dried in the sunlight. Then, several CLSFs were immersed in 5% silane concentration for 24 h[14]. After 24 h, the CLSFs were taken out from the silane solution and dried in sunlight. Some amount of CLSFs was immersed in 5% concentration of potassium permanganate for 24 h[15]. After 24 h, the CLSFs were taken out from the potassium permanganate solution and dried in sunlight. A few CLSFs were immersed in a 5% concentration of benzoyl oxide for 24 h[16]. After 24 h, the CLSFs were taken out from the solution of benzoyl peroxide and dried in sunlight.
Phenol formaldehyde (PF) resins include synthetic thermoset resins that are obtained by reacting phenols with formaldehyde. Sometimes the precursors include other aldehydes or another phenol. Phenolic resins are mainly used in the production of printed circuit boards. However, they are better known for making molded products including pool balls, lab plates, and as coatings and adhesives[17]. In form of bakelite, they are the oldest commercial synthetic resin.
A 3 mm thickness mould of size 300 mm × 150 mm was used to fabricate the CLSF/SiC/PF composites. The composites were fabricated as designated in Table 1 with the composition of 40 wt.% fiber, 3 wt.% SiC and 57 wt.% PF. Initially the mould was cleaned and the inner surface of the mould was coated with releasing agent. Then the CLSFs were evenly distributed in the mould. The resin prepared with 98:2 proportion with the hardener mixed with 3 wt.% of SiC nano particles were poured into the mould to wet the evenly distributed fibers[18]. A roller was used to remove the air traps within the mould. Then the mould was closed and loaded into the compression moulding machine. Force was applied using compression moulding machine on the mould until it is completely closed and held for 24 h. After the prescribed curing time the mould was opened and the composite plates were ejected from the mould. The same procedure was adapted for fabricating surface modified CLSF reinforced polymer composites.
Tensile, flexural, impact and hardness test were carried out as per ASTM standards. ASTM D3039 standard was adhered to carry out tensile test on the composite specimens[19]. On conducting flexural test on the composite specimens ASTM D790 standard were followed. Similarly, while interrogating the hardness characteristics of composites ASTM D785-98 standard were adhered. Finally, on investigating the impact characteristics of composites ASTM D256-10 standard was followed[20]. In order to understand the failure pattern of composites under loads, the tensile failure cross-section of the composites was viewed under scanning electron microscope (SEM).
Figure 1 presents the tensile characteristics of CLSF/SiC/PF composites. The addition of raw and treated CLSF along with SiC nano particles to PF to develop polymer composites significantly improved the tensile characteristics of polymer composite. The inclusion of SiC nano particles in the polymer composite highly improved the stress distribution in the polymer composite when subjected to tensile loads[21]. Moreover, the interaction between the CLSFs and the PF in the polymer composite were also enhanced by the presence of SiC nano particles by ensuring proper transmission of stress to the CLSFs when the developed polymer composites were subjected to tensile loads.
Fig. 1.: Tensile characteristics of CLSF/SiC/PF composites
The reinforcement of CLSFs and SiC nano particles improved the tensile strength of the polymer composite by 87.32% compared to neat PF. Maximum tensile strength is witnessed for the composite specimen E as 68.29 MPa in which the reinforced CLSFs were treated with potassium permanganate. This is owing to the rougher surface of CLSFs treated with potassium permanganate before reinforcement which enhanced the interaction with the PF resulting in better tensile characteristics. The CLSF subjected to different chemical treatments increased the cellulose weight percentage of the fibers when reinforced in PF matrix exhibited better tensile characteristics with SiC nano particles. Moreover, the addition of SiC nano particles reduced the voids thereby enhancing the interaction between the CLSF and PF matrix in the composite leading to better tensile characteristics. Tensile stress-strain curve of CLSF/SiC/PF composite sample E with maximum tensile strength is shown in Figure 2.
Fig. 2.: Tensile stress-strain curve of CLSF/SiC/PF composite sample E
Figure 3 presents the flexural characteristics of the CLSF/SiC/PF composites. The addition of raw and treated CLSF along with SiC nano particles to PF to develop polymer composites significantly improved the flexural characteristics of polymer composite[22]. The insertion of SiC nano particles in the polymer composite highly upgraded the stress distribution in the polymer composite when subjected to flexural loads. Moreover, the interaction between the CLSFs and the PF in the polymer composite were also enhanced by the presence of SiC nano particles by ensuring proper transmission of stress to the CLSFs when the developed polymer composites were subjected to flexural loads[23].
Fig. 3.: Flexural characteristics of CLSF/SiC/PF composites
The reinforcement of CLSFs and SiC nano particles improved the flexural strength of the polymer composite by 82.79% compared to neat PF. Maximum flexural strength is witnessed for the composite specimen E as 78.83 MPa in which the reinforced CLSFs were treated with potassium permanganate. This is owing to the rougher surface of CLSFs treated with potassium permanganate before reinforcement which enhanced the interaction with PF resulting in better flexural characteristics. The CLSF subjected to different chemical treatments reduce the amorphous contents and consequently improve the cellulose wt.% of CLSF. This improves the crystalline and mechanical characteristics of CLSF. These CLSFs when reinforced in PF matrix along with SiC nano particles as filler material result in better flexural characteristics. It is observed that the enhancement of crystalline and mechanical characteristics of CLSF is optimal for potassium permanganate treatment which is reflected in CLSF/SiC/PF composite specimen E.
Fig. 4 presents the impact characteristics of the CLSF/SiC/PF composites. The addition of raw and treated CLSF along with SiC nano particles to PF to develop polymer composites significantly improved the impact characteristics of the polymer composite. The insertion of SiC nano particles in the polymer composite highly upgraded the stress distribution in the polymer composite when subjected to impact loads[24].
Fig. 4.: Impact characteristics of CLSF/SiC/PF composites
Moreover, the interaction between the CLSFs and the PF in the polymer composite were also enhanced by the presence of SiC nano particles by ensuring proper transmission of stress to the CLSFs when the developed polymer composites were subjected to impact loads.
The reinforcement of treated CLSFs and SiC nano particles in PF improved the impact strength of the polymer composite by 15.05% compared to the polymer composite with untreated CLSFs and SiC nano particles as reinforcement. Maximum impact strength is witnessed for the composite specimen E as 6.88 J/cm2 in which the reinforced CLSFs were treated with potassium permanganate. This is owing to the rougher surface of the CLSFs treated with potassium permanganate before reinforcement which enhanced the interaction with the PF resulting in better impact characteristics. Moreover, the addition of SiC nano particles as filler material reduces the voids and resists crack propagation when the CLSF/SiC/PF composites were subjected to impact loads. This consequently boosts the impact strength of the developed composite. On the other hand, the optimal treatment of CLSF by potassium permanganate improved the interfacial characteristics between the CLSF and PF matrix in the CLSF/SiC/PF composites resulting in better impact characteristics.
Figure 5 presents the hardness characteristics of the CLSF/SiC/PF composites. The incorporation of raw and treated CLSF along with SiC nano particles to PF to develop polymer composites significantly improved the hardness characteristics of the polymer composite. The addition of SiC nano particles in the polymer composite highly favoured the compact packing of the polymer composite resulting in higher hardness characteristics[25]. Moreover, the interaction between the CLSFs and the PF in the polymer composite were also enhanced by the presence of SiC nano particles by ensuring very smaller number of voids which also tend to improve the hardness characteristics of developed composite.
Fig. 5.: Hardness characteristics of CLSF/SiC/PF composites
The reinforcement of CLSFs and SiC nano particles improved the hardness of polymer composite by 16.07% compared to neat PF. Maximum hardness is witnessed for the composite specimen E as 69 HRRW in which the reinforced CLSFs were treated with potassium permanganate. This is owing to the compact packing of the CLSFs treated with potassium permanganate before reinforcement with PF and SiC nano particles which enhanced the hardness characteristics of composite. The reduction of voids in the CLSF/SiC/PF composites due to the presence of SiC lead to compact packing of the composites and result in better hardness characteristics. Moreover, the apt surface roughness of the CLSFs treated with potassium permanganate when reinforced in PF matrix along with SiC nano particles as filler material further contribute to the compactness of the composite resulting in maximum hardness for the CLSF/SiC/PF composite specimen E.
Figure 6 presents the morphological characteristics of the CLSF/SiC/PF composite specimen E. The composite specimen E with maximum mechanical characteristics undergone tensile failure whose cross-section was presented. The SEM images of the fractured surface helps to understand the failure pattern of the composites under loads[26]. The SEM image presents voids, fiber pull-outs, fiber breakage, filler ejection holes and matrix cracks. The presents of voids are due to the air traps during the fabrication of the composites. But it was minimum due to the presence of SiC nano particles as filler material and the better interaction between the CLSF and PF in the CLSF/SiC/PF composite specimen E. The fiber pull-outs and filler ejection holes represent the weaker interaction between the SiC nano particles and CLSF with the PF matrix[27]. Even these damages to CLSF/SiC/PF composite specimen E were caused at much higher loads compared to this category of materials. Fiber breakage is owing to the inability of the CLSF to withstand the loads. It is understood that any material will have its own yield point and failure which is showcased by the CLSF. Matrix crack indicate the inefficient stress transfer from the PF to the CLSF when the composite was subjected to loads.
Fig. 6.: SEM images of CLSF/SiC/PF composite specimen E
The CLSF/SiC/PF composites were fabricated and its mechanical characteristics were investigated for identifying its suitability for use in industrial applications. The study detailed the influence of SiC nano particles and chemical treatment of CLSF on the mechanical characteristics of the developed polymer composite. The composite specimen E with potassium permanganate treated CLSF reinforcement showed maximum mechanical characteristics. The composite specimen E exhibited tensile, flexural, impact and hardness characteristics of 68.29 MPa, 78.83 MPa, 6.88 J/cm2 and 69 HRRW respectively. It is supported by the failure pattern revealed through the SEM images. The obtained results of CLSF/SiC/PF polymer composites agree its use in structural supports.
Author Contributions: BBM.: Research design, data analysis, writing-reviewing and editing; KLN.: Conceptualization, Investigation, reviewing and editing; KCV.: Methodology, writing an original draft; JSB.: Original-Writing, Review and Editing; AR.: Review and Editing; AA.: Supporting Investigation and Reviewing; All authors have read and agreed to the published version of the manuscript.
Funding: No funding was provided for this work.
References
1. S. V. Prasad, R. Asthana. (2004). Trib. Lett, 17: 445. [Google Scholar]
2. B. Brailson Mansingh, J. S. Binoj, Suchart Siengchin, M. R. Sanjay. (2023). J App. Poly. Sci, 140: e53345. [Google Scholar]
3. M. Gerald Arul Selvan, J. S. Binoj, B. Brailson Mansingh, J. B. Sajin. (2023). J. Nat. Fib, 20: 2129897. [Google Scholar]
4. U. A. Hanan, S. A. Hassan, M. U. Wahit, J. S. Binoj, B. Brailson Mansingh, K. L. Goh. (2023). Poly. Comp, 44: 241. [Google Scholar]
5. K. Karthik, J. Udaya Prakash, J. S. Binoj, B. Brailson Mansingh. (2022). Poly. Comp, 43: 6096. [Google Scholar]
6. B. Brailson Mansingh, J. S. Binoj, Z. Q. Tan, W. W. L. Eugene, T. Amornsakchai, S. A. Hassan, K. L. Goh. (2022). Poly. Comp, 43: 6051. [Google Scholar]
7. J. S. Binoj, N. Manikandan, B. Brailson Mansingh, V. N. Anbazhagan, G. Bharathiraja, Suchart Siengchin, M. R. Sanjay, S. Indran. (2022). Fib. Polym, 23: 3207. [Google Scholar]
8. Y. Thooyavan, L. A. Kumaraswamidhas, R. Edwin Raj, J. S. Binoj, B. Brailson Mansingh. (2022). Engg. Fail. Analy, 136: 106227. [Google Scholar]
9. Y. Thooyavan, L. A. Kumaraswamidhas, R. Edwin Raj, J. S. Binoj, B. Brailson Mansingh. (2022). Polym. Comp, 43: 2574. [Google Scholar]
10. B. Brailson Mansingh, J. S. Binoj, V. N. Anbazhagan, S. A. Hassan, K. L. Goh, Suchart Siengchin, M. R. Sanjay, M. Mariatti, Y. C. Liu. (2022). J Appl. Polym. Sci., 139: e52245. [Google Scholar]
11. S. A. Hassan, J. S. Binoj, K. L. Goh, B. Brailson Mansingh, K. C. Varaprasad, M. Yazid Yahya, F. E. Che Othman, U. Ahmed, D. Nurhadiyanto, Mujiyono, A. P. Wulandari. (2022). Curr. Rese. Green Susta. Chem, 5: e100284. [Google Scholar]
12. B. Brailson Mansingh, J. S. Binoj, N. Manikandan, N. Prem Sai, Suchart Siengchin, Sanjay Mavinkere Rangappa, K.N. Bharath, S. Indran. (2022). Woodhead Publishing, 283. [Google Scholar]
13. J. B. Sajin, R. Christu Paul, J. S. Binoj, B. Brailson Mansingh, M. Gerald Arul Selvan, K. L. Goh, R. S. Rimal Isaac, M. S. Senthil Saravanan. (2022). Curr. Rese. Green Susta. Chem, 5: e100241. [Google Scholar]
14. B. Brailson Mansingh, J. S. Binoj, S. A. Hassan, M. Mariatti, Suchart Siengchin, M. R. Sanjay, K. N. Bharath. (2022). J Nat Fib, 19: 9373. [Google Scholar]
15. P. T. Saravanakumar, S. P. Arunkumar, B. Brailson Mansingh, P. Manoj Kumar, Ram Subbiah, Vimal Kumar Eswarlal. (2021). Mate Tod Proceed, 50: 1502. [Google Scholar]
16. B. Brailson Mansingh, J. S. Binoj, N. Prem Sai, S. A. Hassan, Suchart Siengchin, M. R. Sanjay, Y. C. Liu. (2021). Curr. Rese. Green Susta. Chem, 4: e100207. [Google Scholar]
17. B. Brailson Mansingh, J. S. Binoj, S. A. Hassan, M. Mariatti, Suchart Siengchin, M. R. Sanjay, Y. C. Liu, P. Saji Raveendran. (2021). Polym. Comp, 42: 6403. [Google Scholar]
18. B. Brailson Mansingh, P. Karuppuswamy. (2019). J Balk. Trib. Assoc, 25: 808. [Google Scholar]
19. B. Brailson Mansingh, K. S. Selvakumar, S. R. Vignesh kumar. (2015). IEEE Xplore, 15506381. [Google Scholar]
20. B. Brailson Mansingh, A. P. Arun Pravin. (2011). IEEE Xplore, 11834452. [Google Scholar]
21. B. Sachuthananthan, D. Raghurami Reddy, B. Brailson Mansingh, R. Vinoth. (2020). Intnl. J Advanc. Rese. Engg. Tech, 11: 2155. [Google Scholar]
22. B. Brailson Mansingh, P. Karuppuswamy. (2016). Asia. J. Rese. Soc. Sci. Human. 6: 1267. [Google Scholar]
23. K. S. Gnanadurai, B. Brailson Mansingh, J. Praveen Jebasingh, V. Ramana. (2015). Intnl. J Appl. Engg. Rese. 10: 411. [Google Scholar]
24. B. Brailson Mansingh, P. Karuppuswamy. (2015). Intnl. J Appl. Engg. Rese. 10: 5959. [Google Scholar]
25. B. Brailson Mansingh. (2010). Intnl. J Fluid. Engg, 2: 7. [Google Scholar]
26. B. Brailson Mansingh, J. S. Binoj, A. Amala Mithin Minther Singh, A. Sagai Francis Britto. (2023). J Appl. Poly. Sci, https://doi.org/10.1002/app.53591. [Google Scholar] [CrossRef]
27. B. Brailson Mansingh, J. S. Binoj, Z. Q. Tan, W. L. L. Eugene Wong, T. Amornsakchai, S. A. Hassan, K. L. Goh. (2023). J Polym. Environ, https://doi.org/10.1007/s10924-023-02758-5. [Google Scholar] [CrossRef]
Cite This Article
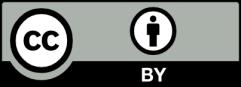
This work is licensed under a Creative Commons Attribution 4.0 International License , which permits unrestricted use, distribution, and reproduction in any medium, provided the original work is properly cited.