Open Access
ARTICLE
Preparation and Characterization of Self-crosslinked Acrylate Emulsified with Environmentally Friendly Surfactants
School of Chemical Engineering, Zhejiang University of Technology, Hangzhou No. 18, Chaowang Road, Hangzhou, Zhejiang Province, P. R. China.
* Corresponding Author: e-mail:
Journal of Polymer Materials 2023, 40(1-2), 47-58. https://doi.org/10.32381/JPM.2023.40.1-2.4
Abstract
The self-crosslinking polyacrylate latex was prepared via the semi-continuous seed emulsion polymerization technology that methyl methacrylate(MMA) and butyl acrylate (BA)were used as the main monomers and hexafluorobutyl methacrylate (HFMA) and monobutylitaconate (MBI) were used as the modified monomers and glycidyl methacrylate (GMA) was used as the crosslinked monomer which were emulsified with the environmentally friendly mixed surfactant of the isomeric triethylene (9) ether (E-1309) and the lauryl polyoxyethylene ether sulfosuccinate disodium salt (MES-30). The resultant latex and its film is characterized by Fourier transform infrared spectroscopy (FTIR), differential scanning calorimeter (DSC), laser particle sizer, contact angle determinator. The comparison of thermal stability between the resultant latex and conventional latex is carried out via the thermogravimetric analyzer (TGA). Factors, which have an influence on the properties of the resultant latex and the emulsion polymerization, are studied in detail. Results indicate that the thermal decomposition temperature of the latex film was increased from 336.9 °C to 370.1 °C The contact angle of the latex film is 82.9 ° owing to the introduction of GMA and MBI.Keywords
Acrylate latex is prepared by emulsion polymerization of the main raw materials of acrylates or methacrylates, which has the characteristics of good weather resistance, good film-forming properties, excellent mechanical properties and other characteristics. There is rich sources of raw materials with low cost also. Thus, it has been widely used in many fields such as coatings, pressure-sensitive adhesives, waterproof fabrics and so on[1–7]. The conventional acrylate latex has no cross-linked network structure, resulting in its poor water resistance, pollution resistance and high and low temperature resistance, which limit its further application and development[8]. Due to the presence of self-condensing or condensation groups in the molecules, the thermoplastic acrylic latex can be effectively converted into thermoset latex, which the cross-linkage of the polymer forms a spatial three-dimensional network structure and its film has greatly improved in terms of thermal stability, cross-linked degree, solvent resistance and mechanical properties[9,10]. However, the cross-linked monomer is hydrophilic and the single introduction makes the water resistance of the coating worse. Usually, the hydrophobicity, water resistance, thermal stability and other properties of the latex film can be improved via introduction of organic fluorine and silicone modified monomers[11–14].
At present, the traditional surfactant such as alkylphenol ethoxyethylene ether, which is used as the emulsifiers in the emulsion polymerization, resides in the latex and is less biodegradable and bioaccumulative. The residual surfactant has a negative influence on the properties and environment[15,16]. For the environmentally friendly surfactant, it is easy to be biodegradable and does not contain APEO, which has no effect on the biological endocrine system and do not cause ecological harm[17–19]. The study on environmentally friendly surfactants gradually replacing traditional surfactants has attracted great attention[20,21]. In this study, the mixed environmentally friendly surfactants of lauryl polyoxyethylene ether sulfosuccinate disodium salt (MES-30, seen in Scheme 1) and isomeric triacolpolyoxyethylene (9) ether (E-1309) are used as the emulsifiers to prepare the novel self-crosslinked acrylate latex, which have not been reported in the open literatures. The emphasis was put in the present work on factors which have on the properties of the resultant latex and the emulsion polymerization. The specific synthetic pathway is shown in Scheme 2.
Scheme 1: Structural formula of MES-30
Scheme 2: Synthetic route of acrylate latex
MMA and BA, which were chemically pure, were bought from Shanghai Aladdin Biochemical Technology Co. Ltd. (China). MES-30 and E-1309, which were industrial grade, were purchased from Hubei Chuxing Chemical Co. Ltd. (China) and Nantong Chenrun Chemical Co. Ltd. (China), respectively. MBI and GMA, which were chemically pure, were obtained from Shanghai Macklin Biochemical Technology Co. Ltd. (China). HFMA, which was industrial grade which was purchased from Harbin Xuejia Fluorine Silicon Chemical Co. Ltd. (China). KPS, which was analytically pure, was supplied by Shanghai Chemical Reagents (China). The deionized water was distilled in our laboratory.
2.2 Preparation of Self-crosslinked Acrylic Latex
The self-crosslinked acrylic latex was prepared via the semi-continuous seeded emulsion polymerization. Firstly, 0.23 g of anionic surfactant MES-30, 0.67 g of nonionic surfactant E-1309 and 40.00 g of deionized water were added to the 250 ml four-neck flask, which was fixed to an iron stand and fitted with a reflux condenser, mechanical agitator and constant pressure drip funnel. The stirring speed of the agitator is controlled at about 230 r/min and the water bath is heated to 80 °C. Secondly, 0.15 g of KPS initiator was dissolved in 30.00 g of deionized water to form an initiator solution. 0.60 g of HFMA, 0.90 g of MBI, 0.90g of GMA, 13.8 g of MMA and 13.8 g of BA were mixed uniformly and used as the copolymerized monomers. When the temperature of the water bath reaches 80°C, 3.00 g of KPS initiator solution and 3.00 g of mixed monomer were added to the four-neck flask via two different the constant pressure droplet funnels within 15 min and then the temperature was kept constant for another 15 min. Thirdly, the rest of 27.15 g of initiator solution and 27.00 g of mixed monomers was slowly added dropwise to the reactor within 3 h. After all the dropwise additions were finished, the temperature of water bath was increased to 90°C and the reaction was maintained for another 45-60 min to further improve the monomer conversion rate. Finally, the mixture in the reactor was naturally cooled to about 40°C and the gel was separated by filtration with 100 mesh gauze. Thus, the novel self-crosslinked acrylate latex was obtained. The typical recipe of preparing the novel self-crosslinked acrylate latex was given in Table 1.
The conversion rate of the mixed monomers were determined by gravimetric method and calculated by the following equation:
where Y was the conversion rate; W2 was the weight of bottle and dry colloid; W1was the weight of colloid and bottle; W0 is the weight of weighing bottle; A is the weight percentage of chemicals excluding monomers; B is the weight percent of the total monomer. The coagulation percentage was calculated according to formula below:
Where, x was the water absorption; M0 and M1were the mass of wet film and dry film, respectively. The film of latex was obtained from coating the latex on a clean glass sheet and drying it for 2 h at 80 °C in an oven.
3.1 FTIR and DSC Analyses of Film of Resultant Latex
FTIR of the film of the resultant latex was shown in Figure 1. From Figure 1, it can be seen that 3515.6 cm-1 was the absorption peak of -OH, which indicated that the crosslinked monomer GMA had undergone a ring-opening reaction to form a hydroxyl group during the film formation process and another weak absorption peak nearby was the characteristic peak of the hydroxyl group in the modified monomer MBI. 2955.6 cm-1 and 2874.2 cm-1 were the C-H characteristic vibration absorption peaks of methyl and methylene groups. 1725.9 cm-1 was the carbon-based vibration peak due to the extremely large electric dipole moment of carbonyl groups. 1449.5 cm-1 and 1385.5 cm-1 were C-H bending vibration absorption peaks of methyl and methylene. 1235.6 cm-1 and 1142.6 cm-1 were the vibration peaks of C-O-C. The absorption peak at 841.8 cm-1 was the characteristic absorption peak in BA. The absorption peak at 753.8 cm-1 was the bending vibration of -CF3. Furthermore, there was no stretching vibration in the range of C=C of 1500-1700cm-1, which indicated that all the monomers were involved in the emulsion polymerization. Tg value had a very important reference value in the industrial application of the product, which determined the use of the polymer. In areas with lower temperatures, a lower Tg value of polymers was selected to resist cold climates and the product can be applied evenly and firmly to the surface of the matrix. Similarly, in areas with higher temperatures, higher Tg values were chosen[22]. The DSC curves of the resultant latex film were shown in Figure 2. From Figure 2, it can be found that the Tg of the polymer latex film was 13.53 °C, which was different from those of BA homopolymer (-54 °C) and MMA homopolymer (103°C)[23]. In addition, only one Tg was detected, which meant that all monomers were introduced into the polymerization and the latex was the random copolymer.
Fig. 1: FTIR of resultant latex film
Fig. 2: DSC of latex film
3.2 Determination of Amount of Initiator
The effect of initiator content on the monomer conversion and coagulation percentage was presented in Figure 3. From Figure 3, it can be seen that the conversion was increased first and then decreased with the increased amount of initiator. However, in comparison with the conversion, the coagulation percentage showed the opposite tendency with the increased amount of the initiator. These phenomena can be explained by the following facts. The free radical dissolved in the water phase was increased owing to the increased concentration of initiator. Thus, the probability that the radical diffused to the micelles was increased, which lead to more activation center and the increased value of the chain propagation. As a result, the conversion of mixed monomers was increased. When the amount of initiator was too large, the rate of polymerization reaction would be accelerated, which resulted in aggregating lots of heats in the reaction. Then the rate of the latex particles that collided with each other was accelerated, thus causing the particles to be agglomerated easily. Finally, the coagulation percentage was increased. The polymerization did not proceed well when the amount of the initiator was excessive. In Figure 3, it can be found that the conversion of mixed monomers was higher and the coagulation percentage was the minimum when the amount of initiator was 0.5%. Thus, the amount of the initiator was 0.5% in this study.
Fig. 3: Effect of amount of initiator on conversion percentage and coagulation percentage
3.3 Influence of Mixed Emulsifier Amount on Properties of Latex and Emulsion Polymerization
The effect of the amount of emulsifier on properties of latex and emulsion polymerization was given in Table 2. During the course of the emulsion polymerization, it can be seen that the seeded emulsion prepared by the mixed emulsifiers appeared translucent blue. However, with the continuous addition of initiators and monomers, the appearance of the latex slowly changed from blue to milky white. The resultant latex had always been milky white and the increased amount of the mixed emulsifiers had no obvious influence on the appearance of the latex. Table 2 indicated that the amount of mixed emulsifier also had no obvious effect on the conversion percentage. This may be caused by the fact that the small molecule emulsifier was added into the system, which can reduce the surface tension of the system, thus reducing the interface energy and improving the stability of the latex. In addition, when the surfactant was adsorbed at the interface of the droplets, it can act as a barrier to prevent the droplets from gathering together. When ionic surfactant with charge was added, the droplets of the latex would repel each other because of the action of the same charge, so that the emulsification was improved, which caused the conversion percentage to be high. The influence of the amount of the emulsifier on the average particle size of latex and its distribution was given in Figure 4. Figure 4 showed that the average particle size of the latex was decreased with the increased amount of the emulsifier. This can be explained by the following fact. The oleophilic group in the emulsifier molecule extended inward and hydrophilic group extended into the water phase to form a micelle after the emulsifier was added to the reaction container. The organic monomer entered the micelle, reacted under the action of initiator and eventually formed latex particles. The greater the amount of emulsifier was, and the more micelles and the more latex particles were. In the case of a certain amount of monomers, the final latex particle size was smaller. In addition, the distribution of particle size was relatively narrow, indicating that the emulsion was relatively uniform. Of course, the larger amount of emulsifier may lead to the smaller particle size. However, the water resistance of the latex film would be decreased because of the hydrophilicity of the emulsifier. Thus, the amount of the emulsifier was 3.0% in this work, which the conversion percentage was higher, the average particle size was smaller, its distribution was uniformly and the stability of the latex was good.
Fig. 4: Average particle size and its distribution of latex (Amount of emulsifier of A, B and C was 1.0%, 3.0% and 6.0%, respectively)
TGA was used to investigate the thermal stability of modified acrylate films and the results were shown in Figure 5. Figure 5 indicated that the decomposing temperature of acrylate latex modified with GMA and HFMA was 372.97°C and the decomposing temperature of latex modified with GMA was 370.11°C and the decomposing temperature of latex without GMA and HFMA was 336.91°C.
Fig. 5: TGA of latex film (A: acrylate latex; B: GMA modified latex; C: GMA and HFMA modified latex)
The obvious increase of the thermal stability of the modified latex may be attributed to the cross-linked network, which can be formed by the crosslinkage of GMA. In addition, the fluorinated groups of acrylate preferentially migrated and accumulated on the surface during the course of film forming. Thus, the surface energy of film was decreased and the thermal stability of the modified latex was improved by the introduction of HFMA.
3.5 Contact Angle and Water Absorption of Latex Film
The water absorption rate and contact angle of the latex film were to reflect its hydrophobicity were shown in Table 3. Table 3 indicated that the contact angle of the latex film prepared by the mixed emulsifier was 82.9°C and the water absorption was 20.93%. After the introduction of cross-linked monomers, the contact angle of the latex film increased and the water absorption rate decreased, which was caused by the fact that the network structure formed after the self-crosslinking reaction and the distance between the polymer molecular chains became more compact, the surface energy of the material is reduced and the hydrophobicity of latex film was increased. With the addition of HFMA, the contact angle of the latex film was increased, which was attributed to the introduction of fluoride monomer, the fluorinated groups of acrylate preferentially migrated and accumulated on the surface during the course of film forming. Thus, the surface energy of film was decreased, which led to the increase of the hydrophobicity[24].
The self-crosslinked acrylate latex was successfully prepared by semi-continuous seeded emulsion polymerization of MMA, BA, HFMA, MBI and GMA which was initiated with KPS and emulsified with the environmentally friendly surfactants of E-1309 and MES-30. The optimal condition of preparing the latex is as follows: the amount of emulsifiers is 3.0%; the amount of initiator is 0.5%. The thermal stability and the water resistance of the film of the resultant latex are improved significantly. The result latex can be used as the binder of the high grade coatings and adhesives.
Conflict of interest: The authors do not have any conflict of interests to declare and there are no financial conflicts of interest.
References
1. J. Machotova, E. Cernoskova, J. Honzicek and J. Snuparek. (2018). Prog. Org. Coat. 120: 266. [Google Scholar]
2. X. B. Jiang, D. Zou, X. Z. Kong and X L Zhu. (2013). J. Polym. Res. 21: 125. [Google Scholar]
3. H. Y. Zhang, H. Q. Wang and H. Q. Wang. (2019). Research progress in polymerization methods of emulsion acrylic acid pressure sensitive adhesive, IOP Conference Series: Earth and Environmental Science, 384: 012141. [Google Scholar]
4. C. Fang, Q. M. Yan, Z. Z. Liu and Z. Lin. (2018). Int. J. Adhes. Adhes. 84: 387. [Google Scholar]
5. S. S. Cui. (2018). Preparation and application of modified polyacrylate polyester washless printing adhesive, Zhejiang Sci-Tech University. [Google Scholar]
6. W. Xu, Q. F. An, L. F. Hao, D. Zhang and M. Zhang, (2014) Fibers Polym. 15: 457. [Google Scholar]
7. J. Lin, C. Zheng, M. N. Zhu, Y. Z. Chen, P. P. Lu, Q. Liu, X. F. Cai, J. W. Zhuang, X. M. Cai and L. P. Liao. (2014). Polym. Adv. Technol. 26: 68. [Google Scholar]
8. M. Y. Cui, C. Liu, Q. Xu and R. H. Li. (2015). J. Adhes. Sci. Technol. 29: 1758. [Google Scholar]
9. S. Parvate and P. Mahanwar. (2018). J. Disper. Sci. Technol. 40: 519. [Google Scholar]
10. G. Tillet, B. Boutevin and B. Ameduri. (2011). Prog. Polym. Sci. 36, 191. [Google Scholar]
11. Y.L. Zhang, Q.F. An and Y. Yu. (2013). Coat. Ind. 43: 31. [Google Scholar]
12. T. C. Canak, E. Hamuryudan and I. E. Serhatli. (2013). J. Appl. Polym. Sci. 128: 1450. [Google Scholar]
13. F. Yang, Z. Wang and H.F. Liu. (2016). Silicone Mat. 30: 28. [Google Scholar]
14. M. A. Lutz and K. E. Polmanteer. (1979). J. Coat. Technol. 51: 37. [Google Scholar]
15. F.Y Li., T.B. Zhao and Y.J. Yang. (2018). J. Petrochem. Coll. 31: 13. [Google Scholar]
16. F. Y. Li, R.R. Hu, T.B. Zhao and Y. Yang. (2018). Fine Petrochem. Ind. 35: 26. [Google Scholar]
17. S. Niu. (2010). Synthesis and application of polyacrylate soap-free emulsion, Xi’an Polytechnic University. [Google Scholar]
18. Y. Liu. (2012). Research on pesticide environmentally friendly formulations based on green surfactants, Zhejiang University. [Google Scholar]
19. P. Wang. (2014). Fire Technol. 51: 503. [Google Scholar]
20. A. M. Fernandez, U. Held and A. Willing. (2005) Prog. Org. Coat. 53: 246. [Google Scholar]
21. X. L. Chen, S. S. Cao, W. T. Zhao and L. J. Chen. (2021). Polym. Paint Colour J. 211: 40. [Google Scholar]
22. F. Rietsch, D. Daveloose and D. Froelich. (1979). Polymer 17: 859. [Google Scholar]
23. M. H. Keshavarz, K. Esmaeilpour and H. Taghizadeh. (2016). J. Therm. Anal. Calorim. 126: 1787. [Google Scholar]
24. L. J. Chen and F. Q. Wu. (2011). J. Appl. Polym. Sci. 123: 1997. [Google Scholar]
Cite This Article
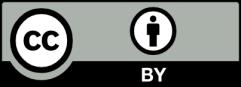
This work is licensed under a Creative Commons Attribution 4.0 International License , which permits unrestricted use, distribution, and reproduction in any medium, provided the original work is properly cited.