Open Access
ARTICLE
Acrylic Finished Leather Upgraded with Thermoplastic Polyurethane Filament using 3D Printing – A New Generation Hybrid Leather of Synthetic and Natural Polymer
a
Department of Leather Technology, Anna University, Chennai.
b
Department of Chemistry, College of Engineering Guindy Campus, Anna University, Chennai.
c
CLRI-Regional Centre Kanpur
d
Inorganic & Physical Chemistry Laboratory
e Polymer Science & Technology
f
Centre for Human & Organisational Resources
Development. CSIR-Central Leather Research Institute, Adyar, Chennai.
* Corresponding Authors: e-mail: ,
Journal of Polymer Materials 2023, 40(1-2), 33-45. https://doi.org/10.32381/JPM.2023.40.1-2.3
Abstract
Leather manufacturing process involves a lot of waste disposal which pollutes environment, some of the processes are inevitable. In the present investigation, 3D printing technology was used to reduce the wastage and to cover defective regions in leather. The present study focuses on synthesis of acrylic binder using emulsion polymerization technique. These binders were analysed for solid content for better optimisation of the amount of binder to be utilised for finishing operation. The experimental binder was prepared with 26% solids. Particle size and thermogravimetric analyses were carried out to understand the size and shape of the particles and their thermal resistance. These binders were used for leather finishing and the performance of leather was studied. Surface morphology changes of leathers were studied using Scanning Electron Microscopy (SEM). Wet and dry rub fastness, finish film adhesion, light fastness and organoleptic properties were studied and found to be superior compared with control leathers. The acrylic finished leather with minor defects was taken for 3D printing and designed using Thermoplastic Polyurethane (TPU) as filament. The acrylic finished leather shows good adhesion for TPU and it results in numerous designs in short duration. The new additive was added to leather using 3D printing technology to produce a tailor-made valuable design without any waste disposal and chemical discharge. This invention may convert the rejected waste leather into valuable material and lead to the new generation hybrid leather for use.Keywords
The leather industry is a high priority industrial sector for many countries[1]. Defects in leather are inevitable due to the damage caused by the injury, diseases and insect bites on animal skin. Leather is categorized into four types based on the quality, full grain, top grain, genuine leather and corrected grain[2]. The buyers demand the high-quality leather and secondary but the other two either go for a low price or rejected after finishing. The economic loss and environmental concern due to rejection of finished leather must be addressed.
In leather processing, one metric ton of raw hide can be converted to only 200kg of tanned leather and 200–250 kg of tanned leather waste. Apart from that 190–350 kg of untanned waste which means just 20% of the raw material becomes finished leather[3].
The leather processing involves many tedious steps like tanning, dyeing, finishing etc., large number of machineries, manpower and chemicals were employed. Apart from all these processes, if the leather seems to be defective by any means all the efforts failed to meet the demand.
3D printing and additive manufacturing is the new technique to design rejected leather precisely on the defected surface. The rejected leather can be made valuable by incorporating unique or customizable designs on leather. The new and unique designs were achieved with the help of CAD software.
In the present study finishing was achieved using acrylic polymers. Acrylic polymers are class of coating materials used for their exceptional performance properties in numerous areas, for example ceramic industry for green machining of ceramics,[4]optical,[5] optical fibres, microelectronics,[6] cement industry,[7] textile,[8] paper,[9] paint industry,[10] electronic,[11] medical,[12] glass,[13] automotive coating,[14] floor polishes,[15] dental,[16] nano composites,[17] adhesives,[18] printing,[19] ink,[20] rubber[21] and wet-end and finishing of leather[22]. Acrylics binders impart excellent weather resistance, water resistance due to their strong carbon-carbon bonds[23]. Aqueous based acrylics are cleaner alternatives for solvent borne coating binders. Acrylic binders confer superior thermo mechanical properties which are best suitable for their use in hostile environmental conditions.
Alkyl acrylate monomers give soft and flexible polymers. In leather finishing, because of their high-performance and remarkable properties such as good film forming, weatherability, light fastness, abrasion resistance, good wet and dry rub fastness, adhesion, thermal resistance, resistance to solvents, grease, oil, acid, water and alkali,[24,25] acrylic materials are favoured compared to other polymers. Acrylic films will give good elongation, tensile, tear strength, cut through resistance, exceptional print retention and good flexing[26,27]. They also provide good covering for upgradation of low-grade leathers and improves the surface feel and lustre.
Finish film coated using currently available conventional acrylic binder are prone to yellowing upon ageing. Stability issues during storage are another concern. Film cracking upon ageing, high cost, inferior elasticity and low temperature resistance are few other problems with conventional acrylic binders[28]. Hence, there is a need for sustainable acrylic finishing systems which are non-toxic, nonflammable, and renewable. Have good UV resistance to degradation and improved anti-soiling. Product should be economical with high performance qualities. Also ease of production, handling and simpler application process, good shelf-life, durable, non-yellowing, clear/ transparent film formation are some of the desirable qualities of a good quality leather binder.
In the present study, acrylic binders were prepared and applied on leather as finishing agent. Different monomers were used for preparation of these binders and compared with commercially available acrylic binder. The performance characteristics were compared and evaluated through a systematic validation process for their finish film adhesion, rub fastness, light fastness, tensile strength, percentage elongation, thermal resistance, miscibility and leather application. Finished leathers resistance towards different solvents, alkali and acids were also analysed for understanding the durability and colour change. 3D printer was used to design acrylic finished leather, the filaments were checked for compatibility and finally TPU is selected as filament for printing on top of the leather. TPU shows good adhesion to leather and it retains the properties of leather.
Acrylic Acid (AA) (>99% pure), Lauryl Acrylate (LA) (>99% pure), Methyl Methacrylate (MMA) (>99% pure), 2 Ethyl Hexyl Acrylate (2-EHA) (>99% pure), Potassium persulfate (KPS) (>99% pure), surfactant Sodium dodecyl sulfate (SDS) (>99% pure) were purchased from Sigma Aldrich. Commercial acrylic (control) binder was purchased from Stahl India Private Limited. Distilled water is used for synthesis and analysis. Rejected leather after finishing, TPU filament.
Initially, 0.15 gm of SDS is dissolved in 46.46 ml of deionised water and stirred well by vertex stirrer for 5 minutes. Then the monomers MMA (9.25 gm), 2-EHA (10.25 gm), LA (10 gm) and AA (0.25 gm) were added with 23.23 ml of SDS dissolved deionised water. Then 0.15 gm of potassium per sulfate is dissolved in 23.23 ml of deionised water. In a 250 ml 3 neck round bottom flask, SDS dissolved deionised water (26.26g) is added and stirred at 300 RPM and the temperature of the oil bath was gradually increased to 85°C. From each neck, KPS solution and SDS emulsified monomer mixture was added slowly to the reaction vessel. The reaction was carried out in nitrogen atmosphere. Solutions of monomer and initiator were added in duration of 45 min. Further, the reaction was continued for another two hours after completion of addition of monomers and initiator. At the end of the reaction, temperature is lowered to 40°C and 5 ml of 5% KOH solution is added to neutralise the unreacted monomers. A small part of the solution is dried and used for analysis of the binder and checked for the film forming ability.
2.3 Analysis of Synthesised Acrylic Binder
Solid content analysis was carried out by measuring initial weight sample and was noted as W1, and was taken in a silica crucible (weight was noted as W2) and heated in a hot air oven at 105°C for 3h. Crucible was cooled to room temperature and weight was measured as final weight (W3). Solid content of the synthesised acrylic binder was analysed using differential weight measurement.
(1)
Thermogravimetric analysis was carried out for the synthesised binder to understand the material weight loss due to heating. The instrumentation was carried out using Q50 instrument (TA Instruments) and the temperature was ramped from 25 to 800°C and the analysis data was collected.
Particle size measurement was analysed and Dynamic Light Scattering (DLS) technique was employed to measure hydrodynamic sizes of the synthesised binder, the average diameter was measured. The particle size was analysed using Zetasizer Nano ZS (Malvern Instruments Ltd.).
Six cow crust leathers were cut into 15 × 15 cm pieces (A, B- 3 pieces each) and were finished using the synthesised acrylic binder according to the procedure mentioned in the Table 1.
The finished leathers both control and experiment were analysed for changes on surface morphology and cross section using SEM analysis. The images were taken using Phenom-Pro SEM instrument. Prior to the imaging samples were cut into 1 × 1 cm sections and mounted on aluminium stubs and analysis was carried out at 25°C. Physical Testing of sampling was done according to standard procedure[29]. Tensile strength,[30] tear strength[31] and grain crack[32] were measured as per the standard procedures. Values reported were average of four samples. Strength properties of the crust leathers were measured using an INSTRON universal testing machine. Dry and wet rub fastness,[33] Light fastness (ISO 105-B01:1994), finish film adhesion,[34] was measured according to standard procedures. Leathers resistances towards acid, alkali and solvents were analysed to understand surface colour fading due to soiling by different chemicals. Hence, colour fastness due to water spotting[35] was carried out and 10% solutions of different acids (formic acid, acetic acid, sulphuric acid) and alkalis (sodium hydroxide, sodium bisulphite) were prepared and spotting test was carried out. Also, leathers were subjected to treatment of different solvents (methanol, ethanol, isopropyl alcohol, dichloromethane and acetone) and the colour changes were monitored and the leathers were rated by visual assessment. Organoleptic properties of finished leather were evaluated for their covering, colour, gloss, tackiness and plate release capability. These are some of the important properties of finish leathers to be evaluated for binder application for leather finishing. The ratings were given based on perception of the experienced leather technologists. The ratings were given from 0–10, higher values represent better properties.
The leather found defective after finishing was cut into 25 × 25cm was positioned in the bed by replacing the plate and the nozzle was adjusted and calibrated. The printer was loaded with TPU filament. Image to be printed on the leather was input from the software to the printer. The co-ordinates were adjusted to get the better design on the surface of leather.
3.1 Characterization of Acrylic Binders
From Table 2, Solid content of the acrylic binder was analysed to measure the active matter present in the synthesised binder and compared with control sample and solid content was around 26% and 22% w/w basis. The measurement of solid content was necessary to optimise the binder quantity to be utilised for leather finishing. The pH value of the material is an important parameter to check the compatibility of the binder with other chemical mixed in the finish formulation. The pH value of the control and experimental binder was set to 3.5. The visual appearance of the control binder was slightly yellow while the experimental binder was white to transparent liquid. The storage of the binders was checked for six months and the binders were stable without any layer formations or hardening when stored in an air tight container. Film forming ability of binders were tested by casting films and the films were continuous, stretchy and transparent in nature, while control binder-based films were transparent but were light-yellow in colour and experimental binders were completely transparent.
Particle size of the control and experimental binder were analysed and from Fig. 1, the size distribution of the particles in the experimental binder were in the range of 50–250nm while the particles of the control binder were distributed widely in the range of 30–600nm. This shows the broader spread of different sized particles in the control compared to experimental binder. The advantage of the system containing near identical sized particles is that the binder can effectively disperse the pigment, waxes and other finishing agents for making season without coagulation.
Fig. 1: Particle size analysis of acrylic binders
Thermogravimetric analyses of the binders were carried out to understand the polymers ability to withstand heat without deformation or weight loss. From Fig. 2, the first weight loss of the control was noticed below 100°C and experimental binder was beyond 100°C, while at 317°C the weight loss of both the binders were at 5.4% and the second weight loss was noted at 430°C with control and experimental binder at 80 and 90%. Though at higher temperatures above 430°C, the ability to withstand heat by the experimental polymer was less than control, the general practice of leather plating and embossing is carried out at temperatures not more than 150°C. Hence, the synthesised experimental binder can be compared to the control which can withstand temperatures as high as 200°C.
Fig. 2: Thermogravimetric analysis of acrylic binders
3.2 Characterization of Finished Leather
The crust leathers were finished using the season formulation consisting of water (750 parts), acrylic binder (150 parts both control and experiment) and pigment (100 parts) to make up to the volume of 1000 parts. The season was sprayed using compressed air gun at pressure of 30 psi. After application of 4 cross coats, the leathers (A, B) were plain plated using hydraulic press at a temperature of 80°C and pressure at 80 bar.
Experimental leathers confer superior film strength, good elasticity compared with control, good covering on low grade leathers, good film forming characteristics and clear film formation, since the film is clear it will be very easy for colour matching or in other words with very minimum quantity of pigment, the colour matching can be achieved easily. Since the experimental binder does not yellowing on ageing it can also be used for white leather finishing. Also, experimental binder showed good product stability over wide temperature range with good flow properties without solidification.
The surface and cross-sectional morphology of the control and experimental leathers were analysed to understand the morphological changes on the finished leather. From Fig. 3, the surface morphology of the control and experiment were examined and there was no considerable changes. No damages or variations noticed on surface as well as at hair roots. Upon examination of cross section, fibre alignment was compact for both the samples and no noticeable changes occurred upon finishing with control and experimental binders.
Fig. 3: Scanning electron microscopy analysis of finished leathers
The strength properties of control and experiment leathers were acceptable according to the upper leather norms. It can be seen from Table 3, there was a slight increase in tensile strength, while percentage elongation of the experimental leathers improved meaning that the leathers were slightly stretchy compared to control leathers. Due to increase in stretch, there was improvement in tear strength values as well for the experimental leathers. Finish film adhesion improved marginally for experimental leathers. Grain crack values qualified the norms for upper leathers for both control and experimental leathers.
The Rub fastness analysis of leathers (Table 4) gives the information about colour fading due to rubbing on leather. This is one of the important tests to understand the colour fading due while leather usage. Dry rub and wet rub fastness for control and experimental leathers coated with 4 cross coats were analysed. From Table 4, the dry rub fastness was similar for both control and experiment. Wet rub fastness was slightly lower for experimental leathers, while it can be observed that the performances of experimental leathers were on par with standard norms with upper leathers.
Leathers finished using experimental and control binders were evaluated for the film stability towards acid, alkali and different solvents. The main objective is to analyse the film degradation towards different chemicals. From Table 5, finish film resistance towards 10% solutions of acids such as formic and acetic acid solutions were observed to be good in case of both control and experiment leathers, while film tend to degrade with application of sulphuric acid solution in case of both the leathers. With respect to alkali, film tainting was moderate when sodium bisulphite solution was applied and complete degradation was observed when sodium hydroxide solution was applied on control and experimental leathers. Solvent resistance was analysed using water, methanol, ethanol, isopropyl alcohol, dichloromethane and acetone, there was slight degradation when dichloromethane and acetone were applied on control leathers while experimental leathers showed very slight degradation compared to control. No degradation of finish film was observed when water, methanol, ethanol and isopropyl alcohol were applied on surface of the leather. This shows the ability of leathers finished using experimental acrylic binder is very competitive for production of chemical resistant gloves and safety footwear.
The light fastness analysis was carried out for the leathers finished with control and experimental binders. Finished leathers were exposed to artificial light for about 72h and colour fading was analysed using grayscale. The value of colour fastness rating for finished leather is 4 and that of the control is also 4. It can be observed that the colour fading was negligible in case of control and experimental leathers (See Fig. 4). This shows the ability of the finished leathers resistance to colour fading due the exposure of light.
Fig. 4: Light fastness tested finished leathers (C-control, E-Experiment)
Organoleptic properties were analysed for understanding covering, colour, gloss, tackiness and plate release capability of the finished leathers. The visual assessment was carried out by the experienced leather technologists and was rated from 0–10. From Fig. 5, experimental leathers showed better covering and improved colour, this may be due to higher adhesion provided by the experimental binder. Tackiness and plate release capabilities of the experimental and control leathers were similar, making them suitable for high performance dust free leathers and printable leathers. The gloss was noted to be poor for both control and experimental leathers.
Fig. 5: Organoleptic properties of the finished leather
3.3 3D Printing of Finished Leather
The defects found on leather after finishing is the common problem faced in the leather industry, though many methods have been employed to prevent the leather rejection, the economic loss due to the quality comprise cannot be managed. The sellers forced to reject and go for the primary or full grain leathers, it not only increases the discharge of waste but also the life of animals. The 3D printing technology is a boon for developing many new designs and to bring the artistic brain to picture with the help of software. In the present study TPU is used as the filament to mask the defected area in leather by design. The TPU is selected due to its flexibility and now a days this is used as a replacement for leather, it is an attempt to make a hybrid material with natural leather (collagen) and synthetic leather (TPU). The design is made convenient for printing using the software. The leather mounted on the bed is adjusted to escape the trapped air between the bed and leather to get even surface.
3.4 Application of 3D Printed Leather
The flexibility of the leather after complete printing was shown in Fig. 6A. The results suggests that the flexibility of the leather lasts even after building up design using TPU, hence this method can adopt to mask the defected area. The unique designs and the complicated designs will increase the price of the material which means the rejected material will become valuable material. The company logo and names can also draw on the defected surface, which looks more visible for the buyers and it also prevents the unwanted animal killing, solid waste and economic loss.
Fig. 6: (A) Flexibility of leather after printing and (B) Applications of 3D printed Leather
The retained flexibility of the leather after designing with TPU filament increases its application. Some of the applications are illustrated in Fig. 6B. It can be used to make pen stands, laptop cases and wallets.
In the present study we have shown successful synthesis and analysis of acrylic binder and its application in leather finishing. The finished leather was further taken for 3D printing using TPU filament. The experimental binders showed superior film forming capabilities, as the synthesised binder was transparent without any colouring. These types of binders are best suitable for finishing leathers with light colours. The adhesion capabilities were comparable with control binder. The particle size was distributed in a narrow range compared to control binder, which is very important characteristic to facilitate better dispersion of season chemicals. Thermal resistance of the experimental binder was up to 200°C, which means the leather finish film can withstand hot platting and other heat operations. Physical strength properties were on par with control leathers, also leathers showed better rub fastness values as well as light fastness. From the analysis of binder and finished leather testing data we can say that the synthesised acrylic binders showed superior qualities compared to control binders and can be used for 3D printing. The technology sometimes involves high temperature operation to get the desired design, the thermal resistance studies shows that the acrylic finished leather can meet the demand compared to control leather for 3D printing.
References
1. Md. Arafat Hossain, Mukta Rani Sarkar, Md. Farhad Ali and Uttam Kumar Roy. (2016). Univers. J. environ. Res. Technol. 6: 91. [Google Scholar]
2. Haftu Hailu, Hideki Tabuchi, Hiroshi Ezawa and Kassu Jilcha. (2017). Ind. Eng Manage. 6: 1. [Google Scholar]
3. N. M. Sivaram and Debabrata Barik in “Energy from toxic organic waste for heat and power generation”, Debabrata Barik (Eds). (2019). Woodhead Publishing Series in Energy, Ch. 5: p.55. [Google Scholar]
4. D. B. Rohini Kumar, M. Rami Reddy, V. N. Mulay and N. Krishnamurti. (2000). Eur. Polym. J. 36: 1503. [Google Scholar]
5. Ji Yun Kwon, Bong Gun Kim, Jung Yun Do, Jung-Jin Ju and Seung Koo Park. (2007). Macromol. Res. 15: 533. [Google Scholar]
6. Stefan Walheim, Erik Schaffer, Jurgen Mlynek and Ullrich Steiner. (1999). Science. 283: 520. [Google Scholar]
7. Seung- Wan Son and Jung Heum Yeon. (2012). Constr Build Mater. 37: 669. [Google Scholar]
8. Quing Bo Meng, Sung -ILLee, Changwoon Nah and Youn - Sik Lee. (2009). Prog. Org. Coat. 66: 382. [Google Scholar]
9. Samya, EI - Sherbiny, Fatma A. Morsy, Ayman M. Atta and Salwa A. Ahmed. (2014). J. surf. eng. mater. adv. Technol. 4: 140. [Google Scholar]
10. A. I. Hussain and H. E. Nasar. (2010). Nature and Science. 8: 94. [Google Scholar]
11. Fei Dong, Stephan, J. Meschter, Schinji Nozaki, Takeshi Ohshima, Takahiro Makino and Junghyun Cho. (2019). Polym. Degrad. Stab. 166: 219. [Google Scholar]
12. Frank Alifui - Segbaya and Roy George. (2018). Inventions. 3: 52. [Google Scholar]
13. Nil Acarali and Rabia oktay. (2018). Celal Bayar University Journal of Science, 14: 257. [Google Scholar]
14. Sal Lovano. (1996). Met. Finish. 94: 20. [Google Scholar]
15. Samane Mehravar, Konrad J. Roschmann, Paola Uribe Arocha, Bernd Reck, Amaia Agirre, Radmila Tomovska, Jose M. Asua and Nicholas Ballard. (2019). Prog. Org. Coat. 131: 417. [Google Scholar]
16. AncaVitalariu, Monica Tatarciuc, Odette Luca, Catalina Holban Cioloca, Bogdan Bulancea, Andra Aungurencei, Ovidiu Aungurencei, Gheorghe Raftu and Diana Diaconu Popa. (2019). Rev. Chim. 70: 591. [Google Scholar]
17. Massoud Malaki, YasserHashemzadeh and Alireza Fadaei Tehrani. (2018). Prog. Org. Coat. 125: 507. [Google Scholar]
18. Minh Canh Vu, Young Han Bae, Min Ji Yu, Won - Kook Choi, Md. Akhtarul Islam and Sung - Ryong Kim. (2019). J Adhes. 95: 887. [Google Scholar]
19. Tarun Kumar Agarwal, Christine Campagne and Ludovic Koehl. (2007). Int. J. Adv. Manuf. Technol. 101: 2907. [Google Scholar]
20. Xiang - Long Ma and Hui - Long Xia. (2009). J. Hazard. Mater. 162: 386. [Google Scholar]
21. H. J. Sue, E. I. Garcia Meitin, B. L. Burton and C. C. Garrison. (1991). J. Polym. Sci. B : Polym. Phys. 29: 1623. [Google Scholar]
22. Debasis Samanta, Murali Adhigan, Jaya Prakash Alla, Nagaraju Pentela and Ramakrishnan Ramesh, et al., (2013). RSC Adv. 3: 16626. [Google Scholar]
23. F. Schindler. (2003). J. Am. Leather Chem. Assoc. 98: 97. [Google Scholar]
24. E. Heidemann, K. G. Eduard Roether and Darmstadt. (1993). Polym. Int. 37: 149. [Google Scholar]
25. A. G. El’ Amma, J. J. Hodder and G. Ward. (1996). J. Am. Leather Chem. Assoc. 91: 237. [Google Scholar]
26. J. Hoefler and E. Nungesser. (2005) J. Am. Leather Chem. Assoc. 100: 54. [Google Scholar]
27. Raquel Rodriguez, Carolina de las Heras Alarcon, Piyasiri Ekanayake, Peter J. McDonald, Joseph L. Keddie, Maria J. Barandiaran and Jose M. Asua. (2008). Macromolecules. 41: 8537. [Google Scholar]
28. IUP 2 (2000). J. Soc. Leather Technol. Chem. 84: 303. [Google Scholar]
29. IUP 6. (2000). J. Soc. Leather Technol. Chem. 84: 317. [Google Scholar]
30. IUP 8. (2000). J. Soc. Leather Technol. Chem. 84: 327. [Google Scholar]
31. IUP 12. (2000). J. Soc. Leather Technol. Chem. 84: 347. [Google Scholar]
32. IUF 450. (1987). J. Soc. Leather Tech. Chem. 71: 24. [Google Scholar]
33. IUF 470. (1990). J. Soc. Leather Tech. Chem. 74: 155. [Google Scholar]
34. IUF 420. (1975). J. Soc. Leather Tech. Chem. 59: 99. [Google Scholar]
35. IUF 434. (1991). J. Soc. Leather Tech. Chem. 75: 30. [Google Scholar]
Cite This Article
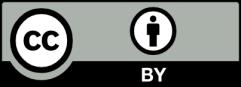
This work is licensed under a Creative Commons Attribution 4.0 International License , which permits unrestricted use, distribution, and reproduction in any medium, provided the original work is properly cited.