Open Access
ARTICLE
Recovery of Pure Water, Salicylic Acid Crystals, and Paracetamol using PVDF-MWCNT Membranes by Membrane Distillation-crystallization
1 Department of Chemical Engineering, Sardar Vallabhbhai National Institute of Technology, Surat-395007, Gujarat, India.
* Corresponding Authors: e-mail: ;
Journal of Polymer Materials 2022, 39(3-4), 307-323. https://doi.org/10.32381/JPM.2022.39.3-4.9
Abstract
Membrane distillation-crystallization (MDC) is presented as a novel technique in the treatment of waste concentrated water which produces valuable crystals along with pure water. In the present study, multi-walled carbon nanotubes (MWCNT)/polyvinylidene fluoride (PVDF) flat sheet membranes were prepared via the wet phase inversion method and applied in MDC for the treatment of pharmaceutical waste. The pure and modified membrane surface properties are characterized with the help of SEM, FTIR, and contact angle measurement. The present work reported the effect of MWCNT content and feed temperature on the MDCperformance and measured pure water flux and pharmaceutical compounds recovery. The observed maximum permeate flux and crystal recovery for Salicylic acid system was 5.5 kg/m2 h and 50%, respectively for PVDF+0.5% CNT membrane and 5 kg/m2 h and 48%, respectively for pure PVDF. Also, for paracetamol system it was 3.9 kg/m2 h and 41% for PVDF +0.5% CNT membrane and 3.5 kg/ m2h and 38% for pure PVDF. Obtained results show that MDC has good potential in treating pharmaceutical waste.Keywords
Most pharmaceutical drugs have the potential to contaminate water resources due to their toxic nature. These drugs have several negative impacts on the environment. Salicylic acid (SA) is a major pharmaceutical intermediate used in the production of most anti-inflammatory drugs. Similarly, paracetamol is a widely used active pharmaceutical ingredient (API) in the manufacturing of medicines. In recent years, the increased demand for drugs and medicines led to the generation of high volumes of pharmaceutical wastewater. The wastewater needs proper treatment before disposing into the environment[1],[2]. Many membrane separation techniques such as ultrafiltration (UF), nanofiltration (NF), and reverse osmosis (RO) have been used for industrial wastewater treatment and to recover potable water from them. Recently, membrane distillation-crystallization (MDC) has become an alternative method for the reclamation of freshwater with crystalline products from its concentrated waste solution. Membrane distillation (MD) is a membrane-based separation technology used to treat concentrated waste, salt solutions, etc., to get pure water permeation. This technique provides a potential solution to handle challenges associated with industrial wastewater and limited clean water resources[3],[4]. MD is a temperature-driven separation process, and only water vapor can pass through the membrane. This process is actually driven by the vapor pressure difference developed across the membrane, which is generated due to the temperature gradient of streams flowing across the membrane [5]. In MD, the feed solution does not heat upto its boiling point; therefore, it becomes a cost-effective process. Moreover, it has become much more attractive due to its operational potential to use renewable energy sources, viz., geothermal energy, solar energy, or substandard industrial heating sources[6]. At the same time, the cold energy required for the vapor condensation can be utilized from the vaporization of liquefied natural gas (LNG) using a vaporizer[7].
The membrane distillation (MD) is a temperature driven membrane separation process with low thermal energy requirement and nearly 100% salt rejection capability. In DCMD, one of the configurations of MD, the hot feed solution comes in immediate touch of the membrane surface. The feed solution's vapors pass through the membrane's pores and get condensed on the downstream side. DCMD is used chiefly to concentrate fruit juices[5],[8],[9]. The DCMD configuration has been widely used in desalination and wastewater treatment. MD has been found to be a suitable method to treat radioactive wastes, in which pure water is collected on permeate side[10].
The combination of MD and crystallization unit becomes a hybrid process called membrane distillation-crystallization (MDC). It offers a potential solution to the treatment of wastewater and concentrated streams with complete recovery of pure water and the generation of valuable crystals. By this means, MDC mitigates the problem of secondary disposal[11],[12]. Edwie and Chung[13] used simultaneous membrane distillation-crystallization (SMDC) to recover clean water and salt from brine at various feed temperatures. Martinez et al.[14] treated pharmaceutical waste stream to recover crystals of 1-(15-bromo-fur-2-il)-2-nitroethane with the help of MDC, wherein the crystals were recovered at various stages by varying process operating conditions. Jensen et al.[15] have used various configurations of MD with a crystallization unit to recover LiCl crystals by treating their saturated solution. Different polymorphic forms of LiCl crystals were obtained at different operating conditions. Chen et al.[11] have shown the application of MDC in brine treatment and obtained pure NaCl crystals with complete recovery of pure water. Balis et al.[16] worked on cascading (six-tray) crystallizer-membrane distillation system to treat three different brine solutions. The crystal growth was enhanced by the extended mesh area and achieved higher water and salt recovery as compared to the MD system alone. Yadav et al.[17] synthesized a nanocomposite membrane using TiO2 nanoparticles and found higher water flux and high purity salt when tested on the MDC process using tannery released wastewater. Srivastava & Murthy[18] modified the PVDF membrane with hexagonal boron nitride and poly-ethylene glycol to get higher permeate flux using MDC for brine treatment. Zhao et al. incorporated the ultrasound in MDC system and observed increase water recovery and reduces the membrane fouling[19].
As MDC functions on saturated feed solutions, hence it is more challenging in comparison with the normal MD technique. Moreover, heat and mass transfer effects are much dominating in the case of MDC. The present technology of MDC limits its industrial implementation; a few factors like membrane fouling, low permeation flux, membrane wettability, etc., affect the commercialization of MDC. Thus, to overcome these issues, the membranes to be used in MDC process must possess optimum thickness, high porosity, high liquid entry pressure, and high hydrophobicity[20],[21]. There are conventional membrane materials used in MDC process, which include polytetrafluoroethylene (PTFE), polyethylene (PE), polypropylene (PP), and polyvinylidinefluoride (PVDF). The membranes made from these materials show high mechanical and thermal stability with better chemical resistance[22]. Several researchers are reported the enhanced membrane properties by incorporating additives in membrane structure or by designing nature-inspired super-hydrophobic membrane[23]–[25]. Mene and Murthy[26] incorporated acetone and LiCl into PVDF membranes to check the performance of MDC to recover pure water as permeate and sodium chloride crystals from concentrated brine in addition to varied operating parameters.
At present, the combination of nanotechnology and separation processes has led to a promising solution to modify membrane properties. For example, a multi-walled carbon nanotube (MWCNT) is a fascinating choice to enhance membrane performance because of its physical and chemical properties such as improved thermal stability, sturdiness, increased porosity and hydrophobicity [27-29]. Compared with conventional MD membranes, MWCNT in polymer matrices helps in reducing the operating conditions of the MD technique by improving pure water fluxes considerably[30]. In addition, the MWCNT has the tendency to form bundles with strong internal forces of Van der Waals between tubes and inner membrane layers[31],[32].
In the existing study, experiments were performed on MDC using flat sheet PVDF membranes, while the wet phase inversion method was adopted to synthesize membranes. MWCNT was used as a modifying agent to prepare PVDF membranes. The resulting membranes were used in MDC for the treatment of pharmaceutical wastes containing salicylic acid and paracetamol. Considerable enhancement in the permeate flux and total crystal recovery has been observed in cases of MWCNT incorporated membranes.
The PVDF was provided by Sigma Aldrich, Lyon, France. The solvent N,N dimethylformamide (DMF, e”99.5%) was taken from Rankem Ltd., Thane, India. The MWCNT with a purity of 98% was supplied by M/S. Ottokemi, Mumbai, India. Salicylic acid was brought from Finar Ltd., Ahmedabad, India. Paracetamol was supplied by Swapnroop Drugs and Pharmaceuticals, Aurangabad, India. The deionized (DI) water utilized during the experimental study was produced from Millipore unit.
All the membranes used in the experimental work were synthesized with the help of PVDF polymer by dissolving it in dimethylformamide (DMF) with the addition of the required amount of MWCNT at a temperature of 50 °C. The dope solution consists of 20 wt.% PVDF, 80 wt.% DMF and the concentration of MWCNT was varied from 0 to 0.5wt.%. The prepared dope solution was then stirred constantly at the rate of 300 rpm for 12 hours to confirm uniformity. Then it was poured on a polyester nonwoven fabric support at room temperature and kept in contact with air for around 20s, and instantly submerged in a coagulation bath for a period of 24 hours to ensure the phase inversion and next, washed with distilled water to take out the traces of solvent and added MWCNT. In the end, the solvent residue was completely evaporated by drying the membranes overnight.
2.3. Membrane Characterization
According to our previous work mentioned in Mene et al.[26], contact angle measurements were done to check membrane hydrophobicity. Similarly, details of other analyses like membrane porosity, pore size measurement, membrane thickness, membrane morphology, Fourier transform infrared spectroscopy (FTIR), and crystal characterization was described in our previous work [26].
Experiments were performed in a laboratory-scale setup shown elsewhere[26]. Batch operation mode was used to operate membrane distillation-crystallization setup in which the permeate stream recirculated in counter-current modeacross the membrane module. The permeate stream at this stage is a mixture of deionized water and the feed solution. A plate-and-frame type membrane system was used, which includes two compartments, one for the permeate side and the other for the feed side, shown elsewhere[26]. The membrane, having an active surface area of 45 cm2, is compressed within two compartments of the membrane system. Two circulating pumps were used to flow hot concentrated feed solution and cold water stream through the membrane system in a counter-current manner. A 3.0 L volume of feed and cold permeate were maintained initially. The chiller maintained the 288 K temperature of permeate, and the feed side temperature of 333 K to 348 K was maintained with the help of a hot water bath. The temperatures are examined through a digital thermometer with the controller. There is a formation of the vapor-liquid interface at the membrane surface, and the generated vapors are diffused through the membrane pores and get condensed at the cold permeate section. This process continues till the feed solution gets saturated, and subsequently, crystallization starts in the feed tank. The normal atmospheric conditions are maintained in the crystallization tank during the operation.
The aqueous solutions of salicylic acid (3 g/L) and paracetamol (12g/L) under normal atmospheric conditions were taken as feed and heated in the water bath at the temperature range of 333 K to 348 K with the aid of an electric immersion coil. The feed flow rate was maintained at 0.8 L/min and was circulated by a diaphragm pump. The permeate DI water, circulated with another diaphragm pump with a flow rate of 0.5 L/min, cooled to the 288 K temperature. When the steady-state is achieved, the pure water flux (PWF) is calculated by measuring the permeate flux weight hike after every five hours of time span. The following formula was used to calculate the flux value:
Here, w2-w1 is the permeate flux hike and is measured by subtracting the final permeate weight from the initial weight, A is the effective membrane area, and Δt is the operation time interval.
The percentage recovery of crystalline product in each case was determined by using equation (2):
3.1. Surface morphology by SEM and contact angle
The effect of MWCNT used as an additive in the preparation of PVDF membrane was studied to check membrane performance and its modification effect on permeation. Changes in the morphology of the membrane because of the incorporation of MWCNT can be observed from SEM images in Figures 1, 2, and 3. Two modified membranes were prepared using 20 wt.% PVDF, DMF solvent for both the membrane and 0.25 wt.% and 0.5 wt.% MWCNT, respectively. The pure PVDF contains only 20 wt.% PVDF and DMF solvent. Experimental results confirm that the permeate flux and crystal recovery from MWCNT incorporated membranes were greater than the pure PVDF membranes. Different properties of prepared membranes can be observed in Table 1.
Figure 1. Membrane cross-section: (a) Pure PVDF; (b) with 0.25% MWCNT; (c) with 0.5% MWCNT
Figure 2. Enlarged cross-section: (a) Pure PVDF; (b) with 0.25% MWCNT; (c) with 0.5% MWCNT
Figure 3. Membrane surface: (a) pure PVDF; (b) with 0.25%MWCNT; (c) with 0.5% MWCNT
SEM technique was used to observe changes in the morphology of pure and MWCNT blended PVDF membranes. Figures 1, 2, and 3 show SEM images of the surface, cross-section, and inner structures of pure PVDF, PVDF with 0.25% MWCNT and PVDF with 0.5% MWCNT membranes respectively. It can be deduced from the figures that the incorporation of different wt.% of MWCNT surely altered the porous structure of membranes in comparison with the membranes prepared with the help of pure PVDF polymer. Therefore, variations can be observed in the pores and porosity of the membrane. The blended membranes obviously show improved surface morphology than the pure ones, and PVDF with 0.5% MWCNT blend membranes shows bigger pores and higher porosity than pure PVDF and PVDF with 0.25% MWCNT blend membranes. This may be due to the complex interaction of MWCNT with solvent and water during the phase inversion process. Furthermore, because of fast mass transformation formation of larger pore channels occurs.
Cross-sectional images of the membranes are compared, as represented in Figure 1. The figures also show that the skin layer and finger-like porous sub-layer, along with asymmetric porous structure, also exist. Figures 1 and 2 show the wider finger-like pores from MWCNT blended membranes compared to pure PVDF membranes. These results depict that incorporating MWCNT plays a crucial role in the preparation of membrane because of its surface structure properties. Figure 3 depicts the SEM images of the membrane surface, and it indicates that MWCNT remained well dispersed in the PVDF membranes. Cross-sectional images confirm a typical asymmetric structure with a thin dense upper layer and a porous sub-layer and elongated finger-like pores across the membrane thickness. These finger structured pores are emerged during the phase inversion operation and due to the presence of MWCNT[32],[33].
The wetting properties of the membrane surface depend upon the surface energy and surface roughness. The consequence of different concentrations of MWCNT on the hydrophobicity of the prepared flat sheet membrane was investigated. Figure 4 shows the contact angle (CA) measurement of pure PVDF and MWCNT blend membranes. The pure PVDF membrane exhibit a CA of 105°, which agrees with other, reported studies. While membranes with 0.25 and 0.5 wt.% MWCNT shows the CA value of 115° and 121°, respectively, which are larger than the pure PVDF membrane, and this observed change is due to the hydrophobic properties of MWCNT[32].
Figure 4. Contact angle: (a) pure PVDF; (b) with 0.25% MWCNT; (c) with 0.5% MWCNT
The chemical compositions of the pure PVDF and modified membranes were analyzed using FTIR spectra, as shown in Figures 5(a) and 5(b), respectively. The observed peak at 3389 cm-1 proves the asymmetric vibration, and at 2935 cm-1 supports the symmetric vibrations of PVDF. Four different peaks were observed in the FTIR analysis in Figure 5(a) and 5(b), which denotes four polymorphs (α, β, γ, and δ) of PVDF. The reported values in the literature of α phase (855 and 976 cm-1), β phase (470 cm-1), and γ phase (430 cm-1), respectively. The C-O bond shows a peak at 1155 cm-1, and 1400 cm-1 represents the bonding of C=C, which is evident of the presence of CNT in membranes. The typical C=O bond shows a major absorption at 1733 cm-1, which validates the existence of oxidized CNT in the membrane[26],[33]–[36].
Figure 5. FTIR image of: (a) pure PVDF; (b) modified PVDF with MWCNT
3.3. Performance of MDC for salicylic acid and paracetamol systems
Experiments were performed on aqueous salicylic acid (SA) and paracetamol solution separately to check the performance of the MDC process with respect to time. The feed side flow rate and temperature were maintained at 0.8 L min-1 and 343 K, respectively, while the permeate side flow rate and temperature were maintained at 0.5 L min-1 and 293 K, respectively, in each case for 50 h of the experiment. The water permeation flux with respect to time is plotted in Figure 6.
Figure 6. Effect of time on permeate flux: (a) Salicylic acid system; (b) Paracetamol system
The visual connection of permeation flux with time, as depicted in Figure 6, shows satisfactory water permeability through pure PVDF and modified membranes at the initial phase of the experiment. With the passage of time, concentration of feed solution was increased, resulting in the generation of tiny crystals which deposit on the membrane surface. In MDC, as the preheated feed solution travels through the membrane unit, it is partially converted to vapor. Under the vapor pressure gradient, generated water vapors are capable of passing through the membrane pores with the effect of the temperature gradient formed across the membrane. A lot of factors play essential roles in the process, such as surface area of the membrane, feed concentration, inlet feed temperature, flow rate of the feed solution, and capability to remove condensed water. The diffusion rate of vapor and vapor pressure are affected by an important parameter, i.e., temperature. Higher vapor pressure is caused by higher temperatures and increases exponentially with temperature as per the Antoine's equation, and the diffusion coefficient as a function of temperature is explained by the Arrhenius equation[37]. A higher diffusion coefficient shows more vapor transport through the membrane pore, which consequently gives higher permeation fluxes.
The presence of MWCNT in the membrane alters the diffusion coefficient and porosity, pore size, and shape factor-like modified membrane geometric features. These parameters will enhance the selective movement of water vapors in the MDC process. However, MWCNT is extremely hydrophobic; hence the probability of wetting a pore with liquid becomes significantly less and leading to more pure vapor transportation. Knudsen diffusion transport mechanism is assumed to be followed across the membrane's pores. Due to the higher adsorption and desorption properties of MWCNT, it is probable that they permit water vapor molecules to follow the pattern of surface diffusion, in which the molecules of water are transported from one site to another by the surface interaction; hence, total water transport can be increased by this mechanism. The MWCNT also provides a different pathway for fast transport of mass through diffusion along with their smooth surface[38].
Furthermore, with the passage of time, permeation flux decreases due to the fouling of the membrane; this was found on the surface of the membrane. Consequently, this changes the membrane hydrophobicity and wettability. This effect is higher for the pure PVDF as compared to the MWCNT modified membranes, and in the case of the paracetamol system, it might be due to the strong interaction between membrane and crystals of paracetamol. In reality, this is one of the unwanted parameters in an MDC process.
3.4. Effect of feed temperature on permeation flux and crystal recovery for SA and paracetamol system
Feed temperature is a key factor in the MDC process. At higher temperatures, water molecules have a greater tendency to evaporate fast. This causes quick vapor molecules diffusion through the pores of membranes at higher temperatures. Figures 7a and 8a show the average pure water fluxes for SA and paracetamol at different feed inlet temperatures, respectively. At the same time, Figures 7b and 8b show the effect of feed temperature on percentage crystal recovery for SA and paracetamol, respectively. The changes in the feed temperature and vapor pressure are directly proportional; therefore, by increasing the feed temperature, the driving force of the process increases, which ultimately improves the water flux. Moreover, MWCNT blend membranes show higher fluxes due to MWCNT, which causes a change in the membrane structure. However, the concentration of nonvolatile components (SA and paracetamol) increases with high permeation flux, and the high value of flux is because of the rising feed inlet temperature. This effect will result in faster supersaturation and will cause a higher recovery of crystalline products.
Figure 7. Effect of feed temperature on: (a) permeate flux; (b) Crystal recovery for Salicylic acid system
Figure 8. Effect of feed temperature on: (a) Permeate flux; (b) Crystal recovery for Paracetamol system
It is evident that MWCNT possesses very high thermal conductivity, and the MWCNT as a membrane modifying agent can be of more interest due to its excellent thermal properties[34]. MWCNT can reduce the temperature gradient in the membrane pores as they generally present in the membrane pores, hence reducing condensation and allowing more water vapors to pass through the membrane's pores.
3.5. Characterization of crystallized product
In the current research work, the crystals generated in the crystallization tank were detected with the aid of a microscope attached to a LED lamp and a camera. Salicylic acid crystallizes in the form of needles in all solvents but forms peculiar hollow tubes with square cross-sectional areas from water. The morphology of the paracetamol crystals obtained shows a needle-like structure representing the mixture of monoclinic and orthorhombic forms of paracetamol[39],[40].
3.6. Effect of MWCNT concentration on crystal recovery
In the present research article MWCNTs are used to enhance the separation properties of the PVDF polymer matrix. The MWCNTs are a particular form of carbon nanotubes in which multiple single-walled carbon nanotubes are nested inside one another. The MWCNTs significantly increases the hydrophobicity properties, enhancing the phase separation characteristics and decreasing the interfacial tension. When such type of MWCNTs is used in polymer membranes, due to its unimodal characteristics, it develops a homogeneous reinforcement and traps the crystals of the different materials. In addition, the MWCNTs form an essential bridge between graphite fibers and a polymer matrix, in which some micrometer size small crystals are easily trapped in the cavities of MWCNTs, and the recovery of crystals increased. Furthermore, the MWCNTs not only increase the mechanical strength and thermal and electrical conductivity but also enhances the hydrophobicity properties of the membranes. The higher weight percent concentration of MWCNTs increases the amount of MWCNTs on both the rough and the smooth surface of membranes and, consequently, increases their hydrophobicity. However, the concentration of nonvolatile components (SA and paracetamol) increases with high permeation flux, and the high value of flux is because of the rising feed inlet temperature. This effect will result in faster supersaturation and will cause a higher recovery of crystalline products.
The MDC with MWCNT blend membranes is an emerging treatment method for concentrated waste solutions. PVDF membranes with flat geometry were successfully synthesized by the wet phase inversion method, and the same was used in the current study. The incorporation of MWCNT modified the membranes. The influences of membrane modification were studied by the incorporation of MWCNT in membranes. The modified membranes exhibited increased porosity and high hydrophobicity as compared to the pure PVDF membrane. The effects of feed temperature and MWCNT content on the MDC performance of MDC have been examined.
In the present study, pharmaceutically active compounds, salicylic acid, and paracetamol were treated successfully to obtain pure water and crystalline products. This method can also be useful for other waste solutions because it emphasizes the permeation of water only rather than the selective permeation of different solutes across the membrane system. Conventional MDC with pure hydrophobic membranes showed a lesser efficiency, but the incorporation of MWCNT resulted in a higher performance of membrane in terms of permeation flux and crystal recovery. The crystals generated in each case show geometry similar to the original crystals used in the experiments. From the results obtained, it can be concluded that the MDC is a prominent method to generate the value-added crystals with pure water recovery from the waste concentrated streams.
Conflict of Interest: The authors declare that there is no conflict of interest.
References
1. Ozyonar F, Aksoy S. Int J Electrochem Sci. (2016);11:3680-3696. [Google Scholar]
2. Meng M, He Z, Yan L, et al. J ApplPolym Sci. (2015);132(42):1-14. [Google Scholar]
3. Nejati S, Boo C, Osuji CO, Elimelech M. J Memb Sci. (2015);492:355-363. [Google Scholar]
4. Francis L, Ghaffour N, Al-Saadi AS, Amy G. Desalin Water Treat. (2015);55(10):2786-2791. [Google Scholar]
5. Alkhudhiri A, Darwish N, Hilal N. Desalination (2012);287:2-18. [Google Scholar]
6. Drioli E, Ali A, Macedonio F. Desalination (2015);356:56-84. [Google Scholar]
7. Wang P, Chung T. Water Res. (2012);46(13):4037-4052. [Google Scholar]
8. Alves VD, Coelhoso IM. J Food Eng. (2006);74(1):125-133. [Google Scholar]
9. Gunko S, Verbych S, Bryk M, Hilal N. Desalination (2006);190(1-3):117-124. [Google Scholar]
10. Korolkov I V., Yeszhanov AB, Zdorovets M V., et al. Sep Purif Technol. (2019);227(April):115694. [Google Scholar]
11. Chen G, Lu Y, Krantz WB, Wang R, Fane AG. J Memb Sci. (2014); 450:1-11. [Google Scholar]
12. Zuo G, Wang R, Field R, Fane AG. Desalination (2011); 283:237-244. [Google Scholar]
13. Edwie F, Chung TS. ChemEng Sci. (2013); 98:160-172. [Google Scholar]
14. Brito Martínez M, Jullok N, Rodríguez Negrín Z, Van der Bruggen B, Luis P. ChemEng Res Des. (2014);92(2):264-272. [Google Scholar]
15. Quist-Jensen CA, Ali A, Mondal S, Macedonio F, Drioli E. J Memb Sci. (2016);505:167-173. [Google Scholar]
16. Balis E, Griffin JC, Hiibel SR. Sep Purif Technol. (2022);290:120788. [Google Scholar]
17. Yadav A, Singh K, Panda AB, Labhasetwar PK, Shahi VK. J Water Process Eng. (2021); 44:102393. [Google Scholar]
18. Srivastava A, Murthy ZVP. Mater Today Chem. (2021); 22:100545. [Google Scholar]
19. Zhao H, Lu M, Hu X, et al. Desalination (2022);531:115727. [Google Scholar]
20. Peng N, Widjojo N, Sukitpaneenit P, et al. ProgPolym Sci. (2012);37(10):1401-1424. [Google Scholar]
21. Kalla S, Piash KPS, Sanyal O. J Water Process Eng. (2022);46:102634. [Google Scholar]
22. Huo R, Gu Z, Zuo K, Zhao G. Desalination (2009);249(3):910-913. [Google Scholar]
23. Lu KJ, Zhao D, Chen Y, Chang J, Chung TS. npj Clean Water. (2020);3(1). [Google Scholar]
24. Lu KJ, Zuo J, Chung TS. J Memb Sci. (2017); 539:34-42. [Google Scholar]
25. Zhao D, Zuo J, Lu KJ, Chung TS. Desalination (2017); 413:119-126. [Google Scholar]
26. Mene NR, Murthy ZVP. Sep Sci Technol. (2019);54(3):396-408. [Google Scholar]
27. Fahmey MS, El-Aassar AHM, M.Abo-Elfadel M, Orabi AS, Das R. Desalination (2019);451:111-116. [Google Scholar]
28. Zhou R, Rana D, Matsuura T, Lan CQ. Sep Purif Technol. (2019); 217:154-163. [Google Scholar]
29. Balis E, Sapalidis A, Pilatos G, et al. Sep Purif Technol. (2019);224:163-179. [Google Scholar]
30. Goh PS, Ismail AF, Ng BC. Desalination (2013); 308:2-14. [Google Scholar]
31. Sanip SM, Ismail AF, Goh PS, Soga T, Tanemura M, Yasuhiko H. Sep Purif Technol. (2011);78(2):208-213. [Google Scholar]
32. Tijing LD, Woo YC, Shim WG, et al. J Memb Sci. (2016):502:158-170. [Google Scholar]
33. Silva TLS, Morales-Torres S, Figueiredo JL, Silva AMT. Desalination (2015):357. [Google Scholar]
34. Buonomenna MG, Macchi P, Davoli M, Drioli E. Eur Polym J. (2007);43(4):1557-1572. [Google Scholar]
35. Choi JH, Jegal J, Kim WN. J Memb Sci. (2006):284:406-415. [Google Scholar]
36. Bai H, Wang X, Zhou Y, Zhang L. Prog Nat Sci Mater Int. (2012);22(3):250-257. [Google Scholar]
37. Al-Obaidani S, Curcio E, Macedonio F, Di Profio G, Al-Hinai H, Drioli E. J Memb Sci. (2008);323(1):85-98. [Google Scholar]
38. Gethard K, Sae-Khow O, Mitra S. Sep Purif Technol. (2012);90:239-245. [Google Scholar]
39. Nordström FL, Rasmuson ÅC. J Chem Eng Data (2006);51(5):1775-1777. [Google Scholar]
40. Di Profio G, Tucci S, Curcio E, Drioli E. Chem Mater. (2007):19(10):2386-2388. [Google Scholar]
Cite This Article
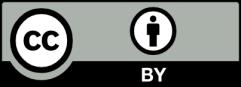
This work is licensed under a Creative Commons Attribution 4.0 International License , which permits unrestricted use, distribution, and reproduction in any medium, provided the original work is properly cited.