Open Access
ARTICLE
Tin Slag Polymer Concrete Strengthening by Basalt and Aramid Fiber Reinforced Polymer Confinement
1 Structural Performance Materials Engineering (SUPREME), Faculty of Mechanical &
Automotive Engineering Technology, Universiti Malaysia Pahang, Pekan, Pahang, Malaysia.
2 Department of Mechanical Engineering, Polytechnic Sultan Haji Ahmad Shah (POLISAS),
25350 Semambu, Kuantan, Pahang, Malaysia.
3
School of Chemical and Energy Engineering, Faculty of Engineering, Universiti Teknologi
Malaysia (UTM), 81310 UTM Skudai, Johor Bahru, Johor, Malaysia.
4
Centre for Advanced Composites (CACM), Universiti Teknologi Malaysia, Skudai, Johor, Malaysia.
5* Institute of Mechanical Engineering, Saveetha Institute of Medical and Technical Sciences
(SIMATS), Chennai -602105, Tamil Nadu, India.
6
Department of Mechanical Engineering, Sri Ramakrishna Engineering College, Coimbatore
641022, Tamil Nadu, India.
7 Department of Mechanical Engineering, Prince Sattam bin Abdulaziz University, Al-Kharj
11942, Saudi Arabia.
8 Department of Mechanical Engineering, Newcastle University in Singapore, Singapore.
9
Faculty of Science, Agriculture & Engineering, Newcastle University, Newcastle Upon Tyne
NE17RU, United Kingdom.
10 Department of Mechanical Engineering Education, Universitas Negeri Yogyakarta,
Yogyakarta, 55281, Indonesia.
* Corresponding Author: e-mail:
Journal of Polymer Materials 2022, 39(3-4), 241-253. https://doi.org/10.32381/JPM.2022.39.3-4.5
Abstract
This study investigates the potential of Tin Slag Polymer Concrete (TSPC) strengthening through confinement using basalt fiber reinforced polymer (BFRP) and aramid fiber reinforced polymer (AFRP) confinement. TSPC short cylindrical column samples have been wrapped with BFRP and AFRP in a single layer (30 mm overlap) using Sikadur-330 epoxy and final samples were coded as TSPC-UC, TSPC-BF and TSPC-AF for unconfined, BFRP and AFRP for confined respectively. After curing for 30 days at room temperature, compressive test has been performed to know the strength, modulus, strain, fracture energy and failure modes of unconfined and confined TSPC. Test result shows that AFRP confinement (114.24 MPa) provide more upsurge in strength enhancement compared to BFRP (81.52 MPa). Fracture energy value of TSPC-AF (821.18 J) is higher than TSPC-BF (538.66 J), but compressive modulus of TSPC-AF (3.23 GPa) is lower than TSPC-BF (4.32 GPa). In addition, yield stress value of TSPC-AF (80.71 MPa) is higher than TSPC-BF (57.21 MPa). Moreover, stress-strain curve and failure mode has shown that TSPC-AF exhibit higher degree of brittleness compared to TSPC-BF. Finally, it is noticed that there are some similarities in strength augmentation of TSPC amid BFRP and glass fiber reinforced polymer (GFRP) as well as between AFRP and carbon fiber reinforced polymer (CFRP) confinement.Keywords
Polymer concrete is a particulate composite material which applied polymeric resins instead of cement in conventional concrete material as composite matrix. In general, fiber reinforced polymer (FRP) composites and particulate reinforced polymer composites were widely employing polyester resins as the matrix due to its high level of resources availability.[1] This thermosetting resin is preferred in industries owing to its economic price, ease of processing, better mechanical characteristics and its excellent resistance to solvent due to its cross-linking three dimensional network.[2-4] The fabrication cost is also less due to minimum handling requirements owing to its ability to cure at room temperature. On addition of catalyst such as Methyl Ethyl Ketone Peroxide (MEKP) to the polyester, the cross-linking of polymer chain in the polyester starts which sets the entire resin in a three dimensional structure. Unsatisfactorily, the polyester cured matrix having cross-linking of polymer chains in its structure that exhibit sufficient strength and stiffness at ambient curing temperature possesses unacceptable fracture resistance.[5] Fortunately, it is understood that reinforcement of polyester with rubber and particulate fillers can sufficiently raise the toughness of the light weight polyester composite system.[6] Conversely, the reinforcement of rubber elements to the polyester composite system diminishes the strength and stiffness on comparing with neat polyester or particulate reinforced polyester composite. It is also evident that the strength and stiffness of the polyester composite system improved on reinforcing with rigid filler particulates such as alumina and silica without affecting its glass transition temperature.[7-9] On the other hand, the reinforcement of rubber particulates to the polyester composite system possesses better toughness compared to the rigid filler particulates reinforced polyester composites.
Review on previous studies in polymer concretes indicate that it possesses superior properties compared to cement concrete materials in terms of improved strength, rapid curing time, low cured shrinkage, excellent adhesion to most surfaces, resistance to chemicals as well as corrosions, excellent damping properties, low water absorbability and it also has the ability to be cast into complex shape.[10-12] Recently, tin slag (TS) has been applied as aggregates in polymer concrete resulting in a new material namely tin slag polymer concrete (TSPC). In a study, Faidzal et al.,[13] have reveal that TSPC with uniform fine aggregates (<1 mm) and 70:30 aggregate to resin ratio has achieved optimum compressive strength (58 MPa). Then, Shakil and Hassan [14] have reported the studies between glass fibers reinforced polymer (GFRP) and carbon fiber reinforced polymer (CFRP) confinement on TSPC column specimen. The CFRP confinement has provided better strength enhancement compared to GFRP. The study shows that percentage of strength enhancement efficiently occurs on the first layer of confinement with 84.78% for GFRP and 128.06% for CFRP confinement while the second layer of confinement only shows 41.16% for GFRP and 45.43% for CFRP confinement.
Later, the study continued with the application of CFRP wrapping in multiple layers on TSPC to investigate optimum number of confinement layers by the same research group. The results shows that the strength enhancement on TSPC column specimens under compressive load efficiently occurred at 1 layer of confinement (103%). The consecutive confinement layer from 1 to 2 layers (14.9%) or 2 to 3 layers (13.6%) has provided relatively low strength enhancement. Then, a study by Abdullah [15] has indicated that TSPC with 1 layer of GFRP and CFRP confinement enhanced the compressive strength to 51.18% and 103.04%. So far, the studies on strength enhancement of TSPC under compression by FRP confinement has provided two major findings which is the effectiveness of confinement layer occur at the first layer of FRP wrapping. Another finding is that only GFRP and CFRP has been employed in the study of TSPC strengthening by FRP confinement.
Brief review on TSPC strengthening study has indicated that the strengthening process has been performed using GFRP and CFRP confinement only. Till now, there was no information found on TSPC strengthening with the application of other FRP materials which are commonly applied as conventional concrete strengthening material such as basalt fiber reinforced polymer (BFRP) and aramid fiber reinforced polymer (AFRP) confinement. Baasankhuu et al., [16] has stated that glass, carbon, and aramid fiber have been long used as FRP material in concrete structure strengthening, while basalt fiber is a relatively new in concrete structure strengthening. Previously, according to Ouyang et al.,[17] a study on retrofitting square concrete column through BFRP jacketing has successfully enhanced strength and ductility of the structure. Besides, there were also studies by Jongvivatsakul et al.,[18] and Talikoti et al., [19] on concrete structure strengthening using AFRP jacketing which has proven to increase strength and durability of the structure. All of these studies present similar approach in concrete structure strengthening that may be applied for TSPC strengthening to further analyze its performance.
In this study, the compressive behavior of unconfined TSPC and TSPC confined with single layer of BFRP and AFRP material was investigated. Fine tin slag in the ratio of 70:30 with orthopthalic polyester was mixed and molded to form compression test specimens as per ASTM standards (short cylindrical column). These specimens were confined with single layer of BFRP and AFRP material by wrapping separately using epoxy as FRP matrix and binders with hand lay-up technique. These confined polymer concretes were tested for its compressive properties and compared with unconfined TSPC. TSPC confined with single layer of BFRP and AFRP material may reduce the brittleness and enhanced the load carrying capacity of the TSPC. The purpose of this study is to observe the compressive strength, stress versus strain curve, compressive modulus, yield stress, failure modes and fracture energy to investigate the potential of TSPC confined with single layer of BFRP and AFRP material in comparison with unconfined TSPC, GFRP and CFRP confinement as report in previous studies.
Fine tin slag (TS) of size less than 1 mm was procured from M/s. Malaysia Smelting Corporation, Berhad, Malaysia. Orthopthalic polyester, MEKP and epoxy-Sikadur-330 was supplied by M/s Covai Polymers Pvt Ltd, Coimbatore, India. Unidirectional BFRP of 300 gram per-square meter (gsm) and AFRP 200 gsm sheets were purchased from M/s. Sathyam Fibertex Pvt Ltd, Coimbatore, India. All the chemicals and materials used are of analytical grade and were used as such for compression test specimen preparation without any further processing.
The TSPC sample has been fabricated by casting the mixture of TS with matrix (Orthopthalic polyester and 2% MEKP) in the ratio 70:30 into 50 mm polyvinyl chloride pipe as specimen mold.[13] After curing for 3 days at room temperature, the specimen was demolded and cut to 100 mm length to make 50 mm diameter and 100 mm height cylindrical TSPC specimens.[20] Then for confinement, the test samples were prepared based on the review by Manda et al.,[10] which provided a summary of previous study on FRP confinement material on cylindrical concrete material. All the confinements were made with single layer wrapping of BFRP and AFRP confinement.
BFRP and AFRP wrapping on TSPC has been made by cutting FRP cloth to 100 mm × 187 mm based on TSPC specimen size to wrap with 30 mm overlap. The wrapping procedure was adapted from previous studies by Talikoti et al.,[19] and Diab et al.,[21]. The wet epoxy-Sikadur-330 prepared by mixing epoxy and hardener in the ratio 4:1 was applied on both side of BFRP and AFRP material before being wrapped around the TSPC. The specimen was cured for 30 days at room temperature according to Sikadur-330 manufacturer recommendation. The confinement was made on TSPC by hand lay-up process in accordance with the method adopted by Yang et al., [17] Figure. 1 show the entire wrapping process on TSPC and finish samples. All the samples were prepared based on ASTM C 579-01 standards for polymer concrete compressive test.[22] Table 1 lists the summary of samples designation based on confinement material specification.
Figure 1. TSPC confinement (a) BFRP wrapping; (b) AFRP wrapping; (c) Unconfined TSPC; (d) TSPC with BFRP confinement; (e) TSPC with AFRP confinement
Mechanical testing was performed based on ASTM C 579-01 standard test method for polymer concrete's compressive strength. The testing machine employed is Shimadzu 1000 kN universal testing machine. The compression test specimen was placed in the middle of the bottom pressure plate to ensure the even dissemination of load and uniaxial compressive load was applied by top pressure plate.[23] The loading rate of compressive load was 1mm/min.
3.1 Mechanical characteristics of TSPC
Table 2 presents the test results for compressive strength, compressive strain and compressive modulus of both confined and unconfined TSPC compression test specimens. The maximum load and deformation for TSPC-UC is 116.22 KN, 2.997 mm, for TSPC-BF, 160.06 KN, 3.356 mm and for TSPC-AF, 224.31 KN, 6.654 mm respectively. The increase in compression characteristics of the confined TSPC sample is owing to the support offered by the confinement to the composite sample when subjected to compressive loads. The data shows that maximum load increases with the application of BFRP confinement on TSPC and further increases with AFRP confinement, both followed by maximum deformation measured.[24] The reason is that failure of TSPC is delayed due to the confinement effect from BFRP and AFRP wrapping on TSPC. According to Sahu et al.,[25] AFRP confinement shows better performance as all are well known that AFRP generally has higher tensile strength compared to BFRP.
From Table 2, the maximum compressive strength for TSPC-UC is 59.19 MPa for TSPC-BF, 81.52 MPa and for TSPC-AF, 114.24 MPa respectively. Based on these findings, the percentage of strength enhancement is 45.63 % for confinement with BFRP and 82.51 % for AFRP confinement with respect to TSPC. These values are a little bit lower compared to the performance of GFRP and CFRP confinement as previously report by Shakil and Hassan[14], Hassan et al.,[20] and Abdullah[15]. However, the finding has indicated that in terms of maximum strength, GFRP and BFRP confinement provide nearly alike act, while CFRP confinement has almost similar performance with AFRP confined composite sample.
3.2 Load-deformation characteristics of TSPC
The failure behavior of the composite samples is found to be different based on the observations from stress versus strain curve, compressive modulus, yield stress and fracture energy. Figure 2 shows the stress versus strain curve of the composite samples that undergone compressive test. The confinement effect can be explained by the response of each composite sample from the beginning of compressive loading application up to fracture[26-29]. Initially, on starting the load, all samples inconsistently showed linear or non-linear response but neglected due to testing error until a clear linear elastic behavior is observed. The linear behavior describes the elastic modulus of each sample.[30] The elastic modulus of each sample where TSPC-UC with 2.84 GPa, TSPC-BF with 4.32 GPa and TSPC-AF with 3.23 GPa revealed that TSPC-BF has highest resistance to elastic deformation followed by TSPC-AF and TSPC-UC.
Figure 2. Stress versus strain graph of the compression test
Also, it can be observed that TSPC-UC reaches its yield strength first at 41.41 MPa followed by TSPC-BF at 57.21 MPa and then TSPC-AF at 80.71 MPa as observed in Figure 3. This phenomenon indicate that BFRP and AFRP confinement has efficiently strengthened the TSPC by delaying the conversion from elastic to plastic behavior of the confined samples compared to unconfined TSPC through yield stress value modification.[31,32] For FRP confinement, even the elastic modulus of TSPC-AF (3.23 GPa) is lower than TSPC-BF (4.32 GPa), the yield stress measurement of TSPC-AF (80.71 MPa) is higher, meaning that AFRP confinement is more effective in providing larger percentage of TSPC strength enhancement compared to BFRP confinement. After the composite test samples crosses its yield stress, the behavior start to change from linear to non-linear behavior. This situation indicates that the response towards compressive loading start to exchange from elastic to plastic behavior whereas after yield point, the permanent deformation will occur instead of stretchable deformation in elastic region.[33]
Figure 3. Yield stress for every test samples
Then the strength of each samples continue to increase in order to resists the rise in compressive load and at this state, the samples are in hardening condition.[34] After reaching the maximum strength TSPC-UC at 59.19 MPa, TSPC-BF at 81.52 MPa and TSPC-AF at 114.24 MPa, each sample start to soften. The slopes and shapes of softening curve describes the failure pattern of composite samples.[35,36] Softening curve of TSPC-UC has the lowest slope showing that the fracture will occur gradually. TSPC-BF softening curve has two distinct shapes whereas at first the curve goes down linearly before the non-linear portion and a downward slope is formed until fracture occurs. Here, the first condition may be characterized as debonding that occur on the adhesive layer between TSPC and BFRP confinement while the second condition is gradual softening until fracture occur.[37] Differently, TSPC-AF provide the highest downward slope on its softening curve representing that the strength loss occurs rapidly in relation to small compressive strain. This situation will cause sudden fracture of the composite sample and this type of softening curve generally exhibit high degree of brittle failure.[38]
To explain further on the fracture of the samples, Figure 4 shows the fracture energy for each of the composite test samples, TSPC-UC, TSPC-BF and TSPC-AF. Fracture is a state where test sample exhibit separation either by progressive crack formation or immediate crushing. The energy required to cause this separation is called fracture energy measured in kilo newton meter (kN.m) or Joule (J). Fracture energy for TSPC-UC is 354.31 J which describes that the energy required to cause the elimination of test sample resistance towards compressive load.[39] Under strain softening, test samples still resists the load but in gradually decreasing strength manner. To enumerate the confinement effectiveness through fracture energy measurement, in the case of TSPC-BF, the fracture energy increases to 538.66 J and for TSPC-AF, fracture energy increased to 821.18 J. The percentage of fracture energy enhancement with BFRP confinement is 52% while with AFRP confinement; the enhancement of fracture energy has achieved 132%. These variations have paved way for explaining the modification of fracture energy of TSPC through FRP confinement.[40,41]
Figure 4. Fractured Energy for every test samples
Failure modes of the composite test samples are presented in Figure 5, 6 and 7. TSPC-UC failure mode consist of both cracking and crushing failure. From Figure 5, a longitudinal shear crack and crushing has been observed. This failure mechanism indicates that TSPC is a brittle material.[42]
Figure 5. Failure modes of Unconfined TSPC (TSPC-UC)
Figure 6. Failure modes of TSPC with AFRP confinement (TSPC-BF)
Figure 7. Failure modes of TSPC with AFRP confinement (TSPC-AF)
Figure 6 depicts the failure modes of TSPC-BF where the rupture of BFRP confinement has been identified. The top side of TSPC-BF also reveals debonding between BFRP and TSPC and the BFRP breaks in uniform vertical direction in the lower portion of the TSPC-BF. In addition to that, debonding failure does not occur on the lower portion but shear crack formation of TSPC core can be seen clearly in the same direction of BRFP rupture.
Further, Figure 7 depicts the failure modes of TSPC-AF. Clearly, experimental results has indicated that the failure of TSPC-AF occur with explosion as AFRP confinement which consumed a huge amount of energy (821.18 J) to cause separation of AFRP as explained previously.[43-45] The ruptures of AFRP also occurs in the lower portion of the TSPC-AF in a sudden manner. The rupture also causes the confinement material to spread out as witnessed in Figure 9(c). The observation of such phenomenon is due to the stronger bond between TSPC core and AFRP confinement in the TSPC-AF.[46]
Enhancement of compressive strength of TSPC has been studied by confining it with BFRP, AFRP and the results were compared with unconfined TSPC. Compressive strength for TSPC-BF has increased as much as 45.63 % and TSPC-AF has 82.51% of strength enhancement compared to TSPC-UC. Moreover, other than maximum compressive strength enhancement, the failure behaviors analysis based on stress versus strain curve, compressive modulus, fractured energy and failure mode has distinguished the different effects of confinement by BFRP and AFRP wrapping on TSPC. It can be concluded that AFRP confinement (114.24 MPa) has provide larger strength enhancement compared to BFRP (81.52 MPa). This enhancement is also in line with fracture energy value (AFRP, 821.18 J and BFRP, 538.66 J) but compressive modulus of TSPC-AF (3.23 GPa) is lower than TSPC-BF (4.32 GPa). However, yield stress value of TSPC-AF (80.71 MPa) and TSPC-BF (57.21 MPa) shows that TSPC-AF resist permanent deformation up to a higher strain compared to TSPC-BF. In addition to that, stress-strain curve and failure mode has shown that TSPC-AF exhibit higher degree of brittle failure compared to TSPC-BF. The overall results obtained for the TSPC-AF exhibited optimum conditions in all aspects making it well suit for diverse applications.
Acknowledgement: The authors are grateful to the Universiti Teknologi Malaysia under the collaborative research grant (CRG UTM – RDU192311) and Universiti Malaysia Pahang (PGRS210339).
References
1. F. Gapsari, A. Purnowidodo, Putu H. Setyarini, S. Hidayatullah, Suteja, H. Izzuddin, R. Subagyo, M. R. Sanjay, S. Siengchin, Polym. Comp. 43, 1147 (2022). [Google Scholar]
2. K. Karthik, J. Udaya Prakash, J. S. Binoj, B. Brailson Mansingh, Polym. Comp. 43, 6096 (2022). [Google Scholar]
3. C. Vijay, F. Ahmad, J. Reinf. Plast. Comp. 39, 572 (2020). [Google Scholar]
4. Jidong Li, Ying Bi, Binhui Zhao, Liwu Zu, Qing Yang, Shanshan Cong, Polym. Comp. 43, 955 (2022). [Google Scholar]
5. S. Sand Chee, M. Jawaid, M. T. H. Sultan, Othman. Y. Alothman, L. Chuah Abdullah, Comp. Part B: Engg. 163, 165 (2019). [Google Scholar]
6. B. Brailson Mansingh, J. S. Binoj, Z. Q. Tan, W. W. Leong Eugene, T. Amornsakchai, S. Abu Hassan, Kheng Lim Goh, Polym. Comp. 43, 6051 (2022). [Google Scholar]
7. J. Naveen, M. Jawaid, E. S. Zainudin, Mohamed. T. H. Sultan, R. Yahaya, M. S. Abdul Majid, Comp. Struct. 219, 194 (2019). [Google Scholar]
8. J. S. S. Neto, R. A. A. Lima, D. K. K. Cavalcanti, J. P. B. Souza, R. A. A. Aguiar, M. D. Banea, J. Appl. Polym. Sci. 136, 47154 (2019). [Google Scholar]
9. U. Abdul Hanan, S. Abu Hassan, M. U. Wahit, J. S. Binoj, B. Brailson Mansingh, Kheng Lim Goh, Polym. Comp. (2022). https://doi.org/10.1002/pc.27041 [Google Scholar] [CrossRef]
10. Manda. M. S, Rejab. M. R. M, Hassan. S. A, Quanjin. M, Green Infrastructure, Springer, Singapore, (2022). https://doi.org/10.1007/978-981-16-6383-3_4 [Google Scholar] [CrossRef]
11. Bedi. R, Chandra. R, Singh. S. P, Indian Concrete Journal, 88, 47 (2014). [Google Scholar]
12. Asif, A., and Ansari, A. 2nd ICEST, College of Engineering, Teerthanker Mahaveer University, Moradabad India, April 12-13, 2013: 1. [Google Scholar]
13. Faidzal. M. M. Y, Hassan. S. A, Omar. B, Zakaria. K, Zaharuddin. M. F. A, J. of Built Environ. Tech. Engg. 5, 1 (2018). [Google Scholar]
14. Usaid Ahmed Shakil, Shukur Bin Abu Hassan, J. Mech. Behav. Mater. 29, 44 (2020). [Google Scholar]
15. Abdullah. K. F, (Thesis). School of Mechanical Engineering, Faculty of Engineering, Universiti Teknologi Malaysia, Skudai, Johor, Malaysia, 2021. [Google Scholar]
16. Baasankhuu. B, Choi. D, Ha. S, Intnl. J. Concr. Struct. Mater 14, 2150 (2020). [Google Scholar]
17. Ouyang. L. J, Gao. W. Y, Zhen. B, Lu. Z. D, J. Comp. Struct. 162, 294 (2017). [Google Scholar]
18. Jongvivatsakul. P, Thi, C. N, Tanapornraweekit. G, Bui. L. V. H, Songklanakarin J. Sci. Tech. 42, 637 (2020). [Google Scholar]
19. Talikoti, R. S, Kandekar, S. B, Fibers. 7, 11 (2019). [Google Scholar]
20. Hassan, S. A, Hanan, U. A, Yahya. M. Y, Wahit. M. U, J. Penelit. Karya. Ilmiah Lemb. Penel. Univer. Trisakti. 5, 2541 (2020). [Google Scholar]
21. Diab, S. H, Soliman, A. M, and Nokken. M. R, J. Constr. Build. Mate. 266, e120893 (2021). [Google Scholar]
22. Y. Thooyavan, L. A. Kumaraswamidhas, R. Edwin Raj, J. S. Binoj, B. Brailson Mansingh, Polym. Comp. 136, 106227 (2022). [Google Scholar]
23. V. Ganesan, V. Shanmugam, B. Kaliyamoorthy, S. Sanjeevi, S. Suresh Kumar, V. Alagumalai, Y. Krishnamoorthy, M. Försth, G. Sas, S. M. Javad Razavi, O. Das, Polymers. 13, 2471 (2021). [Google Scholar]
24. Kesavulu. A, Akash Mohanty, Polym. Comp. 43, 2711 (2022). [Google Scholar]
25. Sahu, N. P., Khande, D. K., Patel, G. C., Sen, P. K., and Bohidar, S. K, Intnl. J. Innov. Rese. Sci. Tech. 1, 2349 (2014). [Google Scholar]
26. Brailson Mansingh. B, Binoj. J. S, S. Abu Hassan, Mariatti. M, S. Siengchin, Sanjay. M. R, Bharath. K. N, J. Nat. Fib. 19, 9373 (2022). [Google Scholar]
27. S. Abu Hassan, J. S. Binoj, Kheng Lim Goh, B. Brailson Mansingh, K. C. Varaprasad, M. Yazid Yahya, F. E. Che Othman, U. Ahmed, D. Nurhadiyanto, Mujiyono, A. P. Wulandari, Cur. Rese. Gre. Sust. Chem. 5, e100284 (2022). [Google Scholar]
28. K. Yoganandam, P. Ganeshan, B. Nagarajaganesh, K. Raja, J. Nat. Fib. 17, 1706 (2020). [Google Scholar]
29. Brailson Mansingh. B, Binoj. J. S, S. Abu Hassan, M. Mariatti, S. Siengchin, M. R. Sanjay, Liu Yu Cheng, Saji Raveendran. P, Polym. Comp. 42, 6403 (2021). [Google Scholar]
30. S. Kumar, D. Zindani, S. Bhowmik, J. Mater. Engg. Perfor. 5, 17994230 (2020). [Google Scholar]
31. J. B. Sajin, R. Christu Paul, J. S. Binoj, B. Brailson Mansingh, M. Gerald Arul Selvan, Kheng Lim Goh, R. S. Rimal Isaac, M. S. Senthil Saravanan, Cur. Rese. Gre. Sust. Chem. 5, e100241 (2022). [Google Scholar]
32. Y. Thooyavan, L. A. Kumaraswamidhas, R. Edwin Raj, J. S. Binoj, B. Brailson Mansingh, Engg. Fail. Analy. 136, 106227 (2022). [Google Scholar]
33. M. Muralidharan, T. P. Sathishkumar, Jesus de-Prado-Gil, Rebeca Martínez-García, Polym.Comp. 43, 2396 (2022). [Google Scholar]
34. Brailson Mansingh, B, Binoj. J. S, Prem Sai. N, Shukur Abu Hassan, Suchart Siengchin, Sanjay. M. R, Liu Yu Cheng, Cur. Rese. Gre. Sust. Chem. 4, e100207 (2021). [Google Scholar]
35. S. S. Abhilash, D. L. Singaravelu, J. Indust. Text. 51, 285 (2020). [Google Scholar]
36. B. Brailson Mansingh, J. S. Binoj, V. N. Anbazhagan, Shukur Abu Hassan, Kheng Lim Goh, Suchart Siengchin, M. R. Sanjay, M. Mariatti, Y. C. Liu, J. Appl. Polym. Scie. 139, e52245 (2022). [Google Scholar]
37. V. Chaudhary, P. K. Bajpai, S. Maheshwari, Fib. Polym. 19, 403 (2018). [Google Scholar]
38. Forkan Sarker, MD Zulhash Uddin, Kazi Sowrov, Md Shakirul Islam, Amran Miah, Polym. Comp. 43, 1330 (2022). [Google Scholar]
39. Ameya Borkar, Andreas Hendlmeier, Zan Simon, James D. Randall, Filip Stojcevski, Luke C. Henderson, Polym. Comp. 43, 2408 (2022). [Google Scholar]
40. H. Junaedi, M. Baig, A. Dawood, E. Albahkali, Polymers, 12, 2851 (2020). [Google Scholar]
41. Chaudhary. V, Bajpai. P. K, Maheshwari. S, Fib. Polym. 19, 403 (2018). [Google Scholar]
42. Yashas Gowda. T. G, Vinod. A, Madhu. P, Kushvaha. V, Sanjay. M. R, Siengchin. S, Polym. Comp. 42, 1891, (2021). [Google Scholar]
43. Wenjing Song, Ke Guo, Zongze Li, Yunhui Zhao, Kongying Zhu, Xiaoyan Yuan, Polym. Comp. 43, 1136 (2022). [Google Scholar]
44. Huanhuan Dong, Guojie Zhang, Yang Jiang, Yong Zhang, Polym. Comp. 43, 1128 (2022). [Google Scholar]
45. Thooyavan. Y, Kumaraswamidhas. L. A, Raj. R. E, Binoj. J. S, Comp. Sci. Tech. 219, 109210 (2022). [Google Scholar]
46. Rashmi Ray, Sankar Narayan Das, Harish Chandra Das, Asutosh Das, Polym. Comp. 43, 1319 (2022). [Google Scholar]
Cite This Article
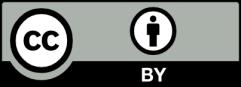
This work is licensed under a Creative Commons Attribution 4.0 International License , which permits unrestricted use, distribution, and reproduction in any medium, provided the original work is properly cited.